Сравнение двух вариантов механизации перегрузки тарно-штучных грузов автопогрузчик с консольной безблочной стрелой и козловой кран КК-6 со строповым захватом




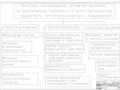
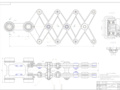
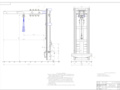
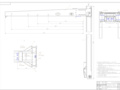
- Добавлен: 25.10.2022
- Размер: 3 MB
- Закачек: 0
Описание
Состав проекта
![]() |
![]() |
![]() ![]() ![]() |
![]() ![]() ![]() |
![]() ![]() ![]() ![]() |
![]() ![]() ![]() |
![]() ![]() ![]() ![]() |
![]() ![]() ![]() ![]() |
![]() ![]() ![]() ![]() |
![]() ![]() ![]() ![]() |
![]() ![]() ![]() ![]() |
![]() ![]() ![]() |
![]() ![]() ![]() ![]() |
![]() ![]() ![]() ![]() |
![]() ![]() ![]() |
![]() ![]() ![]() ![]() |
![]() ![]() ![]() ![]() |
Дополнительная информация
Безблочная стрела.docx
ТДС 14.04.02.01.00.000
ТДС 14.04.02.02.00.000
Механизм изменения вылета
ТДС 14.04.02.03.00.000
ТДС 14.04.02.04.00.000
Основание фермы.docx
ТДС 14.04.02.03.02.01.000
ТДС 14.04.02.03.02.02.000
ТДС 14.04.02.03.02.00.001
Схема склада.dwg

Техническая характеристика автопогрузчика
Годовые приведенные расходы
Себестоимость переработки груза
Площадь грузовой площадки
Вариант механизации перегрузки контейнеров автопогрузчиками
Наименование объекта (сооружения)
Единица тарно-штучного груза
Автомобиль КАМАЗ-53215
ФГБОУ ВО РГУПС каф ЭРМ
Механизм передвижения.docx
ТДС 14.04.02.02.01.000
ТДС 14.04.02.02.00.001
Болт специальный левый
Болт специальный правый
Безблочная стрела.dwg

Технические требования
Внутренние поверхности направляющих наружной
шаровые поверхности и поверхности цапф наружной рамы
перед установкой вкладышей смазать.
Разность размеров В после регулировки натяжения цепи мах 1
При установке грузоподъемника на раму шасси автопогрузчика
регулировать на 1-2 мм меньше размера Б между
торцами вкладышей после закрепления их в кронштейнах рамы
шасси равномерной установкой шайб на обе цапфы наружной рамы
*Размеры для справок.
При установке траверсы
масленки должны быть расположены спереди.
Техническая характеристика
Скорость подъема груза
Скорость изменения вылета
ТДС 14.04.02.00.00.000 ВО
мероприятия охрана труда.dwg

устранения вредных и опасных
Основные мероприятия для
производственных факторов
УСТРАНЯЮЩИЕ ВРЕДНЫЕ И ОПАСНЫЕ
ПРОИЗВОДСТВЕННЫЕ ФАКТОРЫ
Медицинский и профессиональный отбор работников
Лечебно-профилактическое обслуживание работников
Стажировка работника на рабочем месте
Проведение всех видов инструктажей по технике безопасности
Постоянный контроль руководящих кадров и ответственных лиц
Использование работниками спецодежды и защитных средств
Соблюдение всех требований Ростехнадзора к грузоподъемным механизмам
Соблюдение всех требований Ростехнадзора к грузовым канатам и стропам
участвующими в проведении погрузо-разгрузочных работ знаковой сигнализации
Создание регламентированной освещенности площадки и рабочего пространства
Эконом показатели.dwg

показатели вариантов
Основные экономические
представленных к сравнению
механизации с применением автопогрузчика составит 5407708 руб
Годовой экономический эффект от внедрения варианта
Экономические показатели сравниваемых вариантов механизации
Вариант механизации с применением крана КК-6
Вариант механизации с применением автопогрузчика
Капиталовложения на средства механизации
Капиталовложения на объекты склада
Суммарные капиталовложения
Годовые эксплуатационные расходы по перегрузке груза
Годовые эксплуатационные расходы по хранению груза на складе
Суммарные эксплутационные расходы
Себестоимость перегрузки груза
Себестоимость хранения груза
Суммарная себестоимость. рубт
Приведенные расходы на вариант
Ферма стрелы.dwg

несоостность поверхностей Д и Д
Непараллельность осей поверхностей Д и Д
Неперпендикулярность осей поверхностей Д и Д
Разность размеров Б и В мах 0
Неуказанные допуски сварных соединений
Надпись о грузоподъемности выполнять после окраски стрелы
с одной стороны консоли.
предохранив посадочные поверхности.
Сварку производить по контуру прилегания деталей. Электрод
Э-42 по ГОСТ 9467-75.
* Размеры для справок.
Неуказанные предельные отклонения размеров H14
Несоосность поверхностей Д и Д
ТДС 14.04.02.03.00.000 СБ
Основание фермы.dwg

при сварке в указанном месте обеспечить плавный
переход от поверхности П
Неперпендикулярность поверхности П
на длинне 1000 (для 2 х осей катков).
Несоосность поверхностей Д и Д
Неуказанные допуски сварных соединений
Брызги от сварки на поверхностях Д и Д
*Размеры для справок.
Сварку производить по контурам прилегания деталей.
Электрод типа Э-42 по ГОСТ 5264-80.
Неуказанные предельные отклонения размеров H14
ТДС 14.04.02.04.00.000 СБ
ТДС-5-242_Гульбин_ВКР_ПЗ.docx
«Ростовский государственный университет путей сообщения»
Кафедра «Эксплуатация и ремонт машин»
ДОПУСТИТЬ К ЗАЩИТЕ В ГАК
Зав. кафедрой ЭРМ к.т.н. доцент
05.01 – «Наземные транспортно-технологические средства»
(код и наименование специальности)
Механизация процесса перегрузки тарно-штучных грузов
(тема выпускной квалификационной работы)
ПОЯСНИТЕЛЬНАЯ ЗАПИСКА
к выпускной квалификационной работе
(шифр пояснительной записки)
Обучающийся гр. ТДС-5-242Д.И. Гульбин
Руководитель проектаР.В. Каргин
КонсультантА.Г. Хвостиков
научный сотрудникА.Н. Чукарин
Нормоконтроль А.С. Волохов
к.т.н. доцент В.Е. Зиновьев
на выпускную квалификационную работу по специальности
Обучающемуся Гульбину Д.И. группы ТДС-5-242 фак-та ДСМ
Выдано в 2 семестре 2020 2021 учебного года « 20» апреля 2021 г.
Тема выпускной квалификационной работы: «Механизация процесса перегрузки тарно-штучных грузов».
Исходные данные: Годовой грузооборот –120000 т.
Коэффициент складочности – 055. Тип груза – тарно-штучный ящики с товаром
Назначение грузового двора – прибытие груза выгрузка размещение отгрузка.
Предлагаемые к сравнению варианты механизации:
- козловой кран КК-6;
- автопогрузчик оснащенный специальным захватом;
Главный объект проектирования:
Участок грузового двора по перегрузке и хранению тарно-штучных грузов.
Автопогрузчик специальный захват в виде консольной стрелы.
лист Схема склада оснащенного автопогрузчиками
лист Технологические показатели сравниваемых вариантов механизации
лист Экономические показатели сравниваемых вариантов механизации
лист Безблочная стрела
лист Механизм передвижения крюка
лист Основание фермы
лист Мероприятия по разделу охрана труда
По научно-исследовательской части: Исследовать влияние основных качеств контактных поверхностей деталей на долговечность и эксплуатационные свойства соединений. Выявить доминирующие показатели качества поверхности деталей.
Задание по экономической части: Провести технико-экономические расчеты основных показателей сравниваемых вариантов механизации. Выбрать оптимальный вариант и определить экономический эффект от внедрения.
Задание по технике безопасности: Выполнить проверочный расчет устойчивости модернизированного погрузчика.
Охрана окружающей среды: Провести расчет объема вредных выбросов в атмосферу от дизельных двигателей погрузчиков.
Пояснительная записка содержит задание вводную и описательную части обоснование принятого варианта механизации трудоемких процессов и выбора оборудования материалы по технологии изготовления или ремонта деталей основные конструктивные и технико-экономические расчеты а также мероприятия по технике безопасности и охране окружающей среды.
График сроков выполнения разделов ВКР:
ПРИКРЕПЛЕННЫЕ КОНСУЛЬТАНТЫ:
Срок защиты «15» июня 2021 г.
РуководительР.В. Каргин
Выпускная квалификационная работа содержит 83 страницы пояснительной записки 21 рисунок 14 таблиц 34 источника литературы
ГРУЗОВАЯ ПЛОЩАДКА АВТОПОГРУЗЧИК ГРУЗОЗАХВАТНОЕ ПРИСПОСОБЛЕНИЕ БЕЗБЛОЧНАЯ СТРЕЛА РАСЧЕТ СЕБЕСТОИМОСТЬ КАПИТАЛОВЛОЖЕНИЯ ВЫБОР
При выполнении выпускной квалификационной работы широко применялся опыт производства погрузочно-разгрузочных работ в механизированных дистанциях. Использовались методики указания и рекомендации по решению организационных технических экономических и социальных вопросов при выполнении погрузочно-разгрузочных работ.
В работе описано устройство принцип работы погрузочно-разгрузочных машин и грузозахватных приспособлений. Рассмотрены организация технология и технико-экономические расчеты при выполнении погрузочных операций в сравнении с альтернативным вариантом.
Произведен проверочный конструкторский расчет навесного оборудования и грузоподъемника автопогрузчика рекомендованного к использованию для механизации процесса перегрузки тарно-штучных грузов. Рассмотрены мероприятия по охране труда и технике безопасности при проведении работ а также проектируемый объект подвергнут анализу с точки зрения охраны окружающей среды.
Организационно-технологический раздел9
1 Технология производства работ на грузовых дворах станций9
2 Характеристика перерабатываемого груза правила
его транспортировки и его хранения11
3 Расчет суточного грузооборота и определение емкости склада15
4 Выбор типа и марки погрузочно-разгрузочных машин
и грузозахватных приспособлений16
5 Компоновка склада оснащенного козловым краном КК-6 и определение его размеров19
6 Компоновка склада оснащенного автопогрузчиком
и определение его размеров23
7 Расчет времени цикла погрузочно-разгрузочной машины23
8 Расчет эксплуатационной производительности ПРМ и необходимого числа машин26
9 Расчет количества вагонов поступающих на склад
10 Определение числа автотранспорта обслуживающего
Конструкторский раздел32
2 Расчет поперечины37
Научно-исследовательский раздел.
Влияние основных качеств контактных поверхностей деталей на долговечность и эксплуатационные свойства соединений41
1 Основные показатели качества контактных поверхностей41
2 Выявление доминирующих параметров качеств контактных поверхностей и адгезии влияющих на прочность неподвижных соединений деталей собранных с применением полимерных уплотняющих составов49
Экономический анализ основных показателей сравниваемых вариантов механизации53
1 Определение полной себестоимости перегрузки 1 тонны груза суммарных капиталовложений приведенных годовых расходов при использовании кранов КК-653
2 Определение полной себестоимости перегрузки 1 тонны груза суммарных капиталовложений и приведенных годовых расходов при использовании автопогрузчика оснащенного безблочной стрелой59
3 Выбор оптимального варианта механизации63
Безопасность и экологичность решений проекта65
2 Охрана окружающей среды73
Список использованных источников81
Перевозочный процесс сопровождается как минимум двумя перегрузочными операциями: погрузкой груза в транспортное средство и выгрузкой из него. Участие в перевозке различных видов транспорта (железнодорожный автомобильный водный и воздушный) увеличивает число перевозочных операций и требует наличие складов для хранения грузов в ожидании транспортных средств.
Прямая смешанная перевозка грузов осуществляется обычно двумя видами транспорта например: железнодорожным - автомобильным речным - автомобильным морским - железнодорожным. При этом груз доставляется первым видом транспорта в так называемый пункт перевалки или грузовой терминал без хранения или с кратковременным хранением и последующей перегрузкой на другой вид транспорта. Типичным примером смешанной перевозки является обслуживание автотранспортными фирмами железнодорожных станций или морского (речного) порта транспортного узла. Признаками смешанной перевозки является наличие нескольких транспортных документов единой тарифной ставки фрахта схема последовательного взаимодействия участников транспортного процесса.
Смешанные комбинированная перевозка грузов отличается от прямой смешанной перевозки с использованием более двух видов транспорта. Использование смешанных (комбинированных) видов транспортировки часто обусловлено отправкой крупных партий груза непосредственно с завода - изготовителя на оптовую базу железнодорожным транспортом (с целью максимального снижения затрат) а развозка с оптовой базы в пункты розничной торговли - автомобильным.
На основе применения разнообразных укрупненных грузовых единиц сформировалась интермодальная технология перевозок грузов представляющая собой «межвидовое» сообщение (исходя из словосочетания intermodal где inter - меж между а modal - вид форма) при котором перевозка грузов осуществляется в грузовых модулях с обязательной ответственностью за всю перевозку одного перевозчика (оператора) независимо от количества используемых видов транспорта. Оплата за доставку груза производится по единой тарифной ставке. Действующие в настоящее время правовые нормы перевозки грузов в интермодальных сообщениях создавались в течение всего двадцатого столетия и только в 1995 году были опубликованы Правила Конференции ООН по торговле и развитию и Международной Торговой Палаты явившиеся синтезированным обобщением сложившихся на практике норм и правил.
Экономический эффект интермодальных перевозок по сравнению с перевозками неукрупненными грузовыми местами (т.е. россыпью) достигается путем:
– сокращения общего срока доставки грузов за счет автоматизации складских операций повышения производительности работ при загрузке и разгрузке подвижного состава транспорта возможности установления автоматизированного контроля за продвижением грузовых мест;
– экономии расходов за счет ускорения обработки подвижного состава при его загрузке выгрузке и при перевалочных и складских операциях а также за счет ускорения банковских процедур уменьшения числа расчетных операций повышения уровня сохранности грузов возможности применения высокопроизводительных перегрузочных средств.
Широкое развитие интермодальных технологий основано с одной стороны на достижениях научно-технического прогресса на транспорте и с другой - на необходимости снижения транспортных издержек в цене товара в условиях жесткой конкуренции на мировом экономическом пространстве.
Важнейшим направлением в перевозочном процессе является укрупнение и пакетирование грузов что даст возможность повысить производительность труда более чем в 25-3 раза и повысить сохранность груза.
На грузовых районах станций железных дорог погрузочно-разгрузочные работы в основном выполняются терминально-складскими комплексами в парке которых более 15000 подъемно- транспортных машин различных типов. Около 28 % парка машин составляют электропогрузчики. Они являются основными средствами механизации погрузочно-разгрузочных работ с тарно-штучными груза в крытых складах вагонах и на грузосортировочных площадках. Козловые краны составляют около 22% от общего парка подъемно-транспортных машин МЧ и выполняют около 45% общего объема механизированной переработки грузов. Особенно эффективно их использование на контейнерных площадках и для переработки тяжеловесных грузов (труб проката лесоматериалов и др.). В парке также имеются мостовые краны стреловые краны на железнодорожном ходу автомобильные передвижные краны и другие подъемно-транспортные машины и оборудование. Парк погрузочно-разгрузочных машин совершенствуется путем внедрения дистанционного и программного управления. Среди машин оснащенных таким управлением автоматические краны-штабелеры которые позволяют устанавливать пакеты грузов в соответствующие ячейки стеллажей склада без участия человека работы и манипуляторы которые обеспечивают полную автоматизацию выполнения погрузочно-разгрузочных и складских операций по штабелированию пакетированию упаковке передаче грузов с конвейера на конвейер и др.
Особенный интерес с учетом контеризации и укрупнения еденицы груза предсталяют работы с изучением технологий применения автопогрузчиков на прегрузочных работах с тарно-штучными грузами.
ОРГАНИЗАЦИОННО-ТЕХНИЧЕСКИЙ РАЗДЕЛ
1 Технология производства работ на грузовых дворах станций
Конкурентность железных дорог их стабильное финансовое положение зависит от качества обслуживания грузоотправителей и грузополучателей. По мнению американских специалистов «железная дорога должна представлять транспортные услуги обеспечивающие сохранность перевозимых грузов и их доставку в оговоренном количестве точно в срок (не раньше и не позже) и проданные по справедливой цене». На западных железных дорогах приоритетами в качестве перевозок являются:
–своевременность доставки грузов;
–обеспечение сохранности перевозок;
–быстрота реакции железных дорог на пожелание клиентуры;
–скорость доставки груза;
–возможность доставки груза «от двери до двери»;
–надежность перевозок;
–реализация полной цепочки транспортно-экспедиционного обслуживания включая таможенное оформление как во внутренних так и в международных перевозках;
–страхование грузов и банковское обслуживание;
–возможность получения информации о месте нахождения груза в любое конкретное время.
Одной из новых концепций является организация грузовых перевозок в постоянно сформированном поезде с «высадкой» и «посадкой» грузов на станциях по примеру доставки пассажиров.
При решении проблемы повышения качества грузовых перевозок важное значение имеет стратегический анализ и оценка маркетинговыми службами дороги текущей деятельности по обслуживанию клиентуры и потенциала ближайших конкурентов автомобильного транспорта в грузовых перевозках.
Механизированная дистанция погрузочно-разгрузочных работ – линейное предприятие которое выполняет погрузочно-разгрузочные работы на местах общего пользования и подчиняется непосредственно отделению железной дороги.
Технологический процесс работы механизированной станции направлен на решение основных задач: обеспечение круглосуточной погрузки – выгрузки вагонов и автомобилей на станциях с наименьшими затратами трудовых материальных и финансовых ресурсов; совершенствование системы организации погрузочно-разгрузочных работ повышение уровня механизации трудоемких процессов; содержание в технически исправном состоянии грузоподъемных машин и механизмов и полное их использование сокращение времени простоя вагонов и автомобилей под погрузкой-выгрузкой; концентрация выгрузки грузов на меньшем числе станций и специализация мест выгрузки на грузовых дворах; обеспечение при погрузке-разгрузке надлежащего складирования грузов и их сохранность; внедрение передовой технологии в организацию погрузочно-разгрузочных работ обеспечение своевременного ремонта грузоподъемных машин и механизмов; повышение производительности труда рентабельности и производства и снижение себестоимости переработки грузов.
Типовые технологии погрузочно-разгрузочных и складских работ разрабатывают для конкретных грузов на основе обобщения передовых методов работы и последних научно-технических достижений в смежных отраслях. При разработке типовой технологии учитывают основные физико-химические и механические характеристики грузов; габаритные размеры массу и конфигурацию грузов; условия размещения и хранения грузов в транспортных средствах а также в складах и на открытых площадках; перечень и характеристику имеющегося подъемно-транспортного складского и вспомогательного оборудования; количество и место рабочих участвующих в технологическом процессе; последовательность погрузки-выгрузки грузов в транспортные средства возможность совмещения погрузки и выгрузки; порядок формирования штабеля или установка на стеллажи; материальные и денежные затраты; условия обеспечения охраны и техники безопасности; условия обеспечения сохранности грузов при перегрузочных операциях.
2 Характеристика перерабатываемого груза правила его транспортировки и его хранения
Штучные грузы могут перевозиться в таре или без нее характеризуются габаритными размерами массой формой. Они принимаются к перевозке и сдаются по счету и массе. Перевозка их может осуществляться отдельными единицами груза (поштучно) или укрупненными грузовыми единицами (пакетами либо в контейнерах).
В зависимости от массы одного места различают грузы мелкоштучные и грузы большой массы – с массой одного места более 250 кг а для катно-бочковых – более 500 кг.
При перевозке мелкоштучные грузы нельзя объединять с грузами большой массы так как они входят в более низкий диапазон по массе но их нельзя относить также и к навалочным грузам так как погрузка и выгрузка их набрасыванием (навалом) без укладки приводит к порче груза и его потерям.
К категории мелкоштучных грузов относятся некоторые строительные товары частично продукция машиностроения (отдельные узлы и агрегаты машин запасные части) металлургической промышленности.
Основная же часть этой категории грузов перевозимых автотранспортом – это товары в таре и упаковке. В большинстве случаев это продукция легкой пищевой химической и других видов промышленности преимущественно товары народного потребления.
Условия перевозки погрузки и выгрузки таких грузов определяются не столько их наименованием сколько видом тары и упаковки массой и специальными требованиями указанными на маркировке. По виду тары различают мелкоштучные грузы:
ящичные – в ящиках деревянных фанерных из гофрированного картона и других материалов;
в полужесткой таре массой до 80 кг – в кипах прессованных с упаковкой из рогожи или упаковочной ткани с деревянными дощечками или планками с обвязкой металлической лентой или проволокой;
в мягкой таре – в рогожных кулях в тюках из упаковочной ткани мешках с массой одного грузового места 50–80 кг. В основном так перевозят сыпучие грузы (зерно крупа сахар мука и др.);
катные– в рулонах фанерных барабанах и бочках бидонах.
В зависимости от вида грузового места погрузка и выгрузка грузов могут выполняться вручную (для грузовых мест массой до 50 – 80 кг) или механизировано. В последнем случае грузовые места формируют в укрупненные грузовые единицы (УГЕ – пакеты либо контейнеры) и применяют соответствующие подъемно-транспортные машины. Способ загрузки подвижного состава зависит от свойств груза и оснащения погрузочно-разгрузочных пунктов средствами механизации.
В зависимости от величины партии груза перевозки тарно-штучных грузов могут выполняться:
- помашинными отправками (полнопартионные перевозки);
- мелкопартионными отправками.
При помашинных отправках как правило используется универсальный подвижной состав но при необходимости защиты груза от воздействий внешней среды либо для повышения гарантии сохранности грузов при перевозке может применяться крытый подвижной состав или фургоны. Перевозки выполняются по маятниковым или кольцевым маршрутам.
При мелкопартионных отправках обслуживаются клиенты как правило не имеющие оборудованных погрузочно-разгрузочных пунктов. Такие перевозки более целесообразно выполнять подвижным составом оборудованным погрузочно-разгрузочными приспособлениями: грузоподъемным задним бортом гидроподъемником и другими механизмами. Перевозки мелкопартионных отправок целесообразно выполнять по развозочно-сборным маршрутам.
При перевозке грузов большой массы (иногда их называют «тяжеловесные грузы») особое внимание уделяется размещению таких грузов на платформе подвижного состава. Особенно актуально это требование для грузов масса одного места которых сопоставима с грузоподъемностью транспортного средства так как в зависимости от размещения центра тяжести груза меняется нагрузка на оси автомобиля или автопоезда
Перевозка тарно-штучных грузов отдельными грузовыми местами (поштучно) неэффективна из-за значительных простоев подвижного состава под погрузкой и разгрузкой и соответственно низкой производительности труда как транспортников так и подразделений выполняющих погрузочно-разгрузочные работы. Вместе с тем перевозка грузов пакетами и в контейнерах за счет механизации грузовых операций позволяет значительно сократить простои подвижного состава ускорить продвижение грузов сократить их потери при транспортировке.
Несмотря на явные преимущества получаемые при перевозках укрупненными грузовыми единицами следует учитывать что перевозка пакетами связана с определенными сложностями:
- несоблюдением кратности размеров поддонов и кузова автомобиля. При перевозке грузов с небольшой объемной массой коэффициент использования грузоподъемности автомобиля может снижаться. Кроме того при установке пакетов в кузове транспортного средства между ними остаются пустоты которые необходимо заполнять порожней тарой либо другими подручными материалами во избежание смещений груза при транспортировке;
- ограничением высоты пакета его устойчивостью при перевозке автотранспортом. Чем больше высота пакета тем выше требования к его увязке и укладке груза. Для увязки пакета используют бандажи (при перевозке кирпича) термоусадочную пленку металлическую ленту и другие материалы. Пакеты формируют укладывая груз вперевязку (мешки ящики) «в елочку» (кирпич) либо другими способами позволяющими сформировать устойчивую грузовую единицу.
Наибольший экономический эффект от применения пакетного способа перевозок достигается если пакет следует без расформирования от мест производства непосредственно до мест потребления с перегрузкой средствами механизации.
Масса средств пакетирования не превышает 4–5 % массы перевозимого груза при применении поддонов при использовании других средств – меньше. Пакетные перевозки позволяют экономить на таре и упаковке если в качестве упаковочного материала применять термоусадочную пленку. При прямых автомобильных перевозках пакетный способ может быть преобладающим.
По условиям заданий и согласуясь с тематикой ВКР считаем что на участке грузового двора перегружаются тарно-штучные грузы относящиеся к товарам народного потребления. Упакованы в ящичную тару. Размеры транспортной и потребительской тары должны быть увязаны между собой и с размерами средств пакетирования транспортного складского оборудования. Типы масса брутто конструктивные особенности и область применения специальной тары согласно ГОСТ 30302-95 приведены в таблице 1.1 а размеры рымных узлов их расположение присоединительные размеры на рисунке 1.1 Допускаемая высота складирования 2 яруса.
Таблица 1.1 – Типы масса брутто конструктивные особенности и область применения специальной тары
Для штучных в том числе пакетированных а также тяжеловесных грузов не требующих укрытия при перевозке и хранении
Рисунок 1.1 – Общий вид тары размеры рымных узлов их расположение присоединительные размеры
3 Расчет суточного грузооборота и определение емкости склада
Определение среднесуточного грузооборота производим по формуле
где αн - коэффициент неравномерности поступления груза (αн=14);
Qгод – годовой грузооборот 120000 т;
D- число дней простоя участка (D=30 дней).
Для определения емкости участка используем следующее выражение
где Еск- количество груза которое находится на складе т;
Тхр- срок хранения ( Тхр =4 суток);
ск– коэффициент который учитывает то количество груза которое проходит через склад (ск = 055).
Еск=502·4·055=1104 т.
При определении количества операций производимых погрузочно-разгрузочной машиной используем формулу
где Коп - количество операций произведет специальная машина для погрузки и выгрузки груза.
Коп= 1 + 055 = 155.
и грузозахватных приспособлений
Стационарные погрузочно-разгрузочные пункты как правило оснащены высокопроизводительным подъемно-транспортным оборудованием чем обеспечивается сокращение продолжительности загрузки и разгрузки подвижного состава. В настоящей ВКР представляется интересным сравнить варианты механизации процесса перегрузки тарно-штучных грузов с использованием наиболее распространённых на сети железных дорог средствами механизации:
По справочной литературе [3] производим выбор погрузочно-разгрузочных машин для варианта механизации с использованием козлового крана выбираем козловой кран КК-6 который имеет следующую характеристику (таблица 1.2).
Таблица 1.2 – Техническая характеристика козлового крана КК-6
Высота подъема груза м
Рабочие скорости механизмов крана мс
передвижения тележки
Суммарная мощность установленных электродвигателей к Вт
Бурейский механический завод
Необходимо также произвести выбор погрузочно-разгрузочной машины для варианта механизации с использованием автопогрузчика. Выбор останавливаем на варианте применения автопогрузчика оснащенного безблочной стрелой для возможности производства работ с платформами и полувагонами.
Стрела на погрузчик безблочная применяется для подъема и транспортировки габаритных и негабаритных грузов при помощи строп и других приспособлений (рисунок 1.2). Устанавливается на каретку или на вилы погрузчика (рисунок 1.3). Монтаж и демонтаж данного оборудования занимает не больше 5 минут установку может осуществлять один человек.
По рекомендациям производителя компании «СпецМаш» выбор останавливаем на стреле со следующими техническими характеристиками (таблица 1.3).
Таблица 1.3 – Характеристика стрелы погрузчика
Количество такелажных положений
Рабочие длина L высота Н м
Расстояниегрузоподъемность
Рисунок 1.2 – Стрела безблочная Г-образная с креплением на каретку
Рисунок 1.3 – Стрела в сборе
Техническая характеристика данной погрузочно-разгрузочной машины приведена в таблице 1.4
Таблица 1.4 – Техническая характеристика автопогрузчика оснащенного консольной стрелой
Угол наклона рамы грузоподъемника
Габаритные размеры мм
Скорость подъема груза мс
Скорость передвижения погрузчика кмч
Мощность двигателя л.с
Для обоих средств механизации в качестве грузозахватного приспособления выбираем стандартный крюк и стропы.
5Компоновка склада оснащенного козловым краном КК-6 и определение его размеров
Грузовая площадка делится на секторы. Схема площадки должна обеспечивать подачу подвижного состава с наименьшим объемом маневровой работы а также удобные заезды автотранспорта при завозе и вывозе груза. У въезда на площадку вывешивают указатели ее специализации порядка завоза-вывоза.
Каждый кран работающий на площадке прикрепляют для обслуживания одного или двух направлений. Таким образом районы работы строго ограничены и краны не мешают друг другу. Между участками для различных направлений предусматривают промежуточные площадки предназначенные для установки грузов переходящих на другое направление.
Все погрузочно-разгрузочные операции с грузами выполняет крановая бригада под руководством приемосдатчика площадки. Приемосдатчик к моменту окончания подачи вагонов должен иметь план обработки грузовых мест в каждой подаче в целом и для каждого крана в отдельности. При работе кранов не оснащенных автоматическими захватами в состав бригады обязательно включается два стропальщика.
Площадка складирования тарно-штучных грузов должна быть размечена контрастной краской. На площадке грузы могут устанавливаться в два яруса по высоте. При установке во второй ярус должны учитываться условия удобства работы для отправки нижнего ряда до того как отправлен верхний. Площадка располагается в пролете крана под консолями – подъездные пути. Расстояние от оси подкранового рельса до первого контейнера составляет 1500 мм. Ширина автомобильной дороги составляет 4 – 6 м.
Козловыми кранами целесообразно обрабатывать вагоны и автомобили. При этом простой некоторых автомобилей несколько увеличивается но средний простой на площадке уменьшается.
Грузы должны укладываться так чтобы исключалась опасность их падения опрокидывания разваливания и обеспечивались доступность и безопасность их выемки при выдаче в производстве или при погрузке для отправки.
Каждая деталь каждый материал требует определенного способа укладки и хранения согласно правилам и нормам укладки на приобъектном складе в соответствии с ГОСТ 12.3.009-76.
Укладка грузов на погрузочно-разгрузочных площадках вплотную к стенам здания колоннам и оборудованию штабель к штабелю не допускается. Расстояние от груза и стены колонны должно быть не менее 1 м между грузом и перекрытием здания — не менее 1 м между грузом и светильником — не менее 05 м
Ширина склада определяется по компоновке и составляет 326 м (рисунок 1.4). Для определения длины склада необходимо учесть какое количество рядов груза размещается по длине склада. Так как в полете крана одновременно могут быть установлены 12 единиц груза с учетом двух ярусного размещения получаем что на разрезе склада размещается 24 единиц груза.
Для определения числа рядов по фронту работ используем формулу
где Zгр.мест – общее количество грузовых мест на участке.
По длине склада такелажные зазоры между рядами груза также составляют 02 м. Через 10 метров длины склада обустраиваем проход шириной 1 м .Таким образом длину склада определяем по формуле
Lск= Lряд· Nряд+ Lзаз· Nзаз+ Lраз· Nраз+ 2 Lзап
где Lряд – длина ряда 124 м;
Nряд – числа рядов груза 37 ряда;
Lзаз – длина зазора между рядами 02 м );
Nзаз – число зазоров 31 шт;
Lраз – длина технологических разрывов 1 м;
Nраз – число технологических разрывов по длине склада 5 шт;
Nраз – длина зон запаса с торцов склада под его развитие 15 м.
Lск = 124·37+02·31+1·5+2·15=87 м.
Площадь склада равна Fск = 2836 м2.
Рисунок 1.4 – Схема склада тарно-штучных грузов оснащенного козловым краном КК-6
6 Компоновка склада оснащенного автопогрузчиком и определение его размеров
При разработке компоновки склада для данного варианта механизации сохраняются общие принципы освещенные ранее в пункте 1.5 Компоновочное решение показано на рисунке 1.5 ширина склада составит Вск =50 м. На разрезе склада с учетом двух ярусного хранения одновременно можно разместить 56 единиц груза
тогда число рядов контейнеров по фронту работ составит
Длина склада составит.
Lск=16·1+8·01+9·5=62 м.
Площадь склада Fск = 3100 м2.
7Расчет времени цикла погрузочно-разгрузочной машины
Рабочим циклом погрузочно-разгрузочных машин называют время затрачиваемое на захват и перемещение одной порции груза и возврат машины в исходное положение. Наиболее точно время рабочего цикла можно определить хронометражным наблюдением. В общем случае оно складывается из времен отдельных операций по застропке отстропке подъему перемещению развороту опусканию груза скорректированных на коэффициент учитывающий совмещение некоторых операций [2].
7.1 Расчет времени рабочего цикла козлового крана КК-6
Время рабочего цикла определяется как сумма времени затрачиваемого для выполнения отдельных операций.
где t3 to – время на застропку и отстропку груза (t3=40 с; to=30 с);
ty – время установки захватного устройства над грузом и груза над штабелем.
φ – коэффициент учитывающий совмещение операций во времени козлового крана (φ =08);
Н – средняя высота подъема и опускания груза определяемая из компоновки м;
Vп – скорость подъема и опускания груза (из технической характеристики крана) мс;
- среднее расстояние перемещение крана вдоль фронта работ определяемое как 13 длины зоны обслуживания грузовой площадки (из компоновки склада) м;
Vkp – скорость передвижения крана (из технической характеристики крана мс;
LТ – среднее расстояние передвижения тележки крана (из технической характеристики крана) мс;
VТ – скорость передвижения тележки крана (из технической характеристики крана) мс;
Σt – суммарное время запуска и торможения механизмов крана (Σt=24 с);
tупр – суммарное время управления краном ( tупр=32 с).
7.2Расчет времени рабочего цикла автопогрузчика с консольной стрелой
Время рабочего цикла погрузчика определяем по формуле [2]
Тц=t3+2tраз+tгр+tбгр+tпод+tотс (1.5)
где t3 – время застропки груза (t3=40 с);
tраз – время разворота погрузчика (tраз=30 с);
tгр – время движения с грузом tгр=рт
где - расстояние перемещения ( =20 м);
tрт- время на разгон и торможения механизмов (tрт=15 с);
Vгр – скорость движения погрузчика Vгр=111 мс;
tбгр- время движения погрузчика без груза рассчитываем аналогично (V бгр=5 c );
tпод – время подъема и опускания груза
где Н- средняя высота подъема и опускания (Нср=18м);
Vпод – скорость механизма подъема (Vпод=027 мс);
tотс – время отстропки груза (tотс=40 с)
Тц=450+2·10+5+5+39+30=139 с.
8Расчет эксплуатационной производительности ПРМ и необходимого числа машин
8.1 Расчет эксплуатационной производительности ПРМ и необходимого числа машин при использовании козлового крана КК-6
Рассчитываем эксплуатационную производительность козлового крана используя формулу
где Gф - фактическая масса поднимаемого груза т;
в - коэффициент использования погрузочно-разгрузочной машины в течение смены (в=085);
Тц - продолжительность рабочего цикла с.
Необходимое минимальное количество погрузочно-разгрузочных машин для обслуживания грузового узла с заданным грузооборот определяется по формуле
где m – число смен 2 смены;
t – продолжительность смены 8 ч.
Следовательно для обслуживания проектируемого грузового двора необходимо склад оснастить двумя кранами КК- 6.
8.2Расчет эксплуатационной производительности и необходимого числа машин при использовании автопогрузчика
Эксплуатационная производительность погрузчика по формуле 1.6 составит
Минимально необходимое количество автопогрузчиков на складе для переработки заданного грузооборота (формула 1.7) составит
Принимаем 2 погрузчика.
Таким образом для обслуживания проектируемого грузового двора необходимо использовать два автопогрузчика оснащенных консольной стрелой.
9Расчет количества вагонов поступающих на склад ежесуточно
Количество вагонов поступающих на склад ежесуточно определяем воспользовавшись формулой [2]
где qв - номинальная грузоподъемность полувагона ( qв=65 т);
- коэффициент использования вагона по грузоподъемности (=055).
Необходимо 14 полувагонов грузоподъемностью 65 т.
Длина фронта погрузочно-разгрузочных работ принимается равной длине грузовой площадки полученной в результате компоновки контейнерной площадки с использованием козлового крана.
где - длина вагона по осям автосцепки (=1392 м);
nп - количество подач вагонов в сутки.
Из приведенного выражения определяем количество подач вагонов в сутки при варианте механизации козловым краном КК -6.
Следовательно будет произведено три подачи вагонов. время простоя одной подачи под погрузочно-разгрузочными операциями без учета времени на вспомогательные операции находят по формуле
Для варианта использования козлового крана КК -6
Суммарное время простоя подач в сутки должно удовлетворять условию
В данном случае 46·3 24 ч следовательно условие выполняется.
При использовании автопогрузчиков длина склада составляет Lск=62 м значит число подач вагонов составит
Следовательно необходимо вагоны разбить на 4 подачи. Время простоя подачи составит
Суммарное время простоя подач будет равно 23·4 = 92 часов что менее 24 часов следовательно расчеты проведены верно.
10Определение числа автотранспорта обслуживающего грузовой узел
В соответствии с родом груза и его габаритами для обслуживания контейнерной площадки выбираем автомобили марки ЗИЛ-5301[2].
Краткая характеристика автомобиля:
- грузоподъемность – 3 т;
- количество осей – 4;
- внутренние размеры кузова д × ш × в – 4100 × 2100× 2200 мм.
В данном случае коэффициент использования автомобиля по грузоподъемности при перевозке 2-х единиц груза г=083.
Количество автомобилей ежесуточно подаваемых на фронт погрузки и к складам подсчитывается по формуле
где qа - паспортная грузоподъемность автомобиля 3 т;
np - количество рейсов в сутки;
г - коэффициент использования автомобиля по грузоподъемности г=083.
Количество рейсов в сутки определяем следующим образом
где tP - продолжительность рейса ч;
T - количество часов работы в сутки ( Т=8 ч).
Продолжительность рейса определяется по формуле
Vk - средняя скорость движения (Vk=30 кмч).
Принимаем что для обслуживания проектируемого грузового узла в обоих случаях необходимо использовать 17 бортовых автомобилей марки ЗИЛ-5301.
Проведенные организационно-технические расчеты позволили спроектировать грузовые узлы для обоих вариантов механизации.
Установлено что необходимо использовать два автопогрузчика с консольной стрелой марки или два козловых крана КК-6.
Проведен расчет времени цикла и эксплуатационной производительности сравниваемых средств механизации. Рассчитаны основные параметры склада разработаны компоновочные решения.
Данные расчеты и выводы будут использованы для выбора оптимального варианта механизации и расчета экономических показателей.
КОНСТРУКТОРСКИЙ РАЗДЕЛ
В выпускной квалификационной работе исследуется возможность использования автопогрузчика с консольной стрелой при перегрузке ящичных тарно-штучных грузов. Поскольку стандартное навесное оборудование было заменено на консольную безблочную стрелу то возникает необходимость проведения проверочных конструкторских расчетов с целью подтверждения обоснованности предлагаемой модернизации.
Стрела представляет собой сварную конструкцию (рисунок 2.1) предназначенную для вертикального подъема и горизонтального перемещения грузов массой от 15 т до 5 т.
Консоль стрелы состоит из двух тонкостенных балок корытного профиля связанных между собой поперечинами. Коней консоли вварен в верхнюю поперечину и связан косынками со стойками (рисунок 2.1)
Под действием давления катков механизма передвижения крюка стрелы балки консоли испытывают общий и местный изгиб и стесненное кручение.
Расчетный изгибающий момент в защемлении консоли возникает при действии груза Q= 5 т на вылете 1220 мм и равен
где q – ускорение свободного падения (q=981 мс).
М=5000·122·981=59841 кН·см.
Для удобства подсчетов разбиваем сечение на части 1 2 и 3 (рисунок 2.2).
Момент инерции рассматриваемого сечения относительно оси изгиба х – х составит
где J1 J2 J3 – моменты инерции соответствующих частей относительно этой оси.
– вертикальные стойки;
Рисунок 2.1 – Схема стрелы погрузчика
Рисунок 2.2 – Сечение балки стрелы в защемлении
Участок рассматриваем как кольцевой
где J2 - момент инерции полукольца относительно его центральной оси
- площадь полукольца;
где D - наружный диаметр ( D=54 мм );
d - внутренний диаметр (d=30 мм);
y2=1005+ расстояние от оси х-х до центра тяжести полукольца;
Момент инерции сечения составит:
J=8125+2·630+1040=3115 см4;
Нормальные напряжения изгиба при условии что нагрузка распределена поровну между балками равны:
Нормальные напряжения изгиба с учетом коэффициентов перегрузки К1=11 и динамичности К2=13 равны
Напряжения местного изгиба определяются в сечении изображенном на рисунке 2.3
Рисунок 2.3 – Сечение балки стрелы
Напряжение местного изгиба определяются по отработанной методике. Согласно этой методике значения поперечных изгибающих моментов Му и продольных изгибающих моментов Мх в полке и стенке определяются по таблицам в зависимости от параметров hho Hb ρ= ab
Н – высота по средней линии профиля (2Н=198 мм);
h – толщина полки (h=12мм);
ho – толщина стенки (ho=12мм);
а – расстояние центра приложения нагрузки от середины стенки ( а=39мм);
вб длина участка на котором распределена нагрузка;
Q=12500 Н – реакция катка на полку.
Для сечения А-А принимаем следующее значение поперечного изгибающего момента.
Напряжения в изогнутом участке вычисляем согласно теории кривого бруса.
где М – изгибающий момент в сечении;
S – статистический момент сечения относительно нейтральной оси;
R- радиус кривизны этого волокна.
Рисунок 2.4 – Сечение А-А балки стрелы.
Сечение А-А имеет вид представленный на рисунке 2.4 значения для расчета следующие:
С=12мм – высота сечения;
Rвн = 15мм – радиус кривизны внутренних волокон;
Rн = 27 мм – радиус кривизны наружных волокон;
Rо =21мм – радиус кривизны оси;
r – радиус кривизны нейтрального слоя;
ZB =54 мм – расстояние внутренних волокон от нейтрального слоя;
ZB=66 мм – расстояние наружных волокон от нейтрального слоя.
Для сечения единичной длины площадь сечения будет равна:
Статистический момент относительно нейтральной оси составит:
S=F(Ro-r)=12(21-204)=0072 см³;
Напряжения во внутреннем волокне определяется как:
Местные напряжения изгиба с учетом коэффициентов перегрузки К1=11 и динамичности К2=13 равны
Gмах= K1·K2·G=11·13·1717=2455 МПа.
Материал стрелы – Ст 10×СнD ГОСТ 5058-65 допускаемые напряжения составляют:
На основании полученных данных можно сделать вывод что возникающие максимальные напряжения в контрольных сечениях балки стрелы не превышают допускаемых:
[Gт]=400мПа >Gмах=2455 МПа.
Поперечину рассматриваем как балку защемленную по краям. Поперечина находится под действием нагрузки Р соответствующей весу груза и крутящего момента
где - плечо силы Р (=122 см);
Р – действующая на стрелу сила (Р=50000 Н).
Расчетная схема эпюры изгибающих моментов и крутящих моментов представлены на рисунке 2.5.
Реакции опор А и В составят
Изгибающие моменты в опорах А и В определяются как
Определим геометрические характеристики сечения
Момент сопротивления изгиба поперечины составит
Максимальные напряжения изгиба равны
Рисунок 2.5 – Расчетная схема и эпюры изгибающих и крутящих моментов поперечины
Сечение поперечины имеет вид представленный на рисунке 2.6.
Рисунок 2.6 – Сечение поперечины
Касательные напряжения составят
Материал поперечины – Ст 3. Допускаемые напряжения составляют
На основании полученных результатов видно что Gмах=429 МПамах=705 МПа[GТ]=240МПа т.е. возникающие нагрузки не приведут к разрушению поперечины.
На основании проведенных в конструкторском разделе расчетов можно сделать вывод что предлагаемая модернизация автопогрузчика обоснована.
Возникающие напряжения в материале стрелы и направляющей грузоподъемника не приведут к их выходу из строя так как значительно ниже допускаемых напряжений. Так например максимальные напряжения в стреле не превышают 246 МПа а допускаемые 400 МПа.
НАУЧНО-ИССЛЕДОВАТЕЛЬСКИЙ РАЗДЕЛ
Влияние основных качеств контактных поверхностей деталей на долговечность и эксплуатационные свойства соединений
1 Основные показатели качества контактных поверхностей
В технике под поверхностью детали понимают наружный слой который по строению и физическим свойствам отличается от внутренних слоев. Совершенно справедливо утверждение российских и зарубежных ученых что качество поверхностного слоя субстрата в неподвижных соединениях деталей и узлах трения непосредственно влияет на долговечность и эксплуатационные средства изделия в целом. Особенно если фиксация неподвижного сопряжения достигается использованием полимерных и металлополимерных уплотняющих составов. Так как долговечность отдельных узлов и всей машины будет зависеть от прочности соединения то есть от адгезии полимерного слоя к субстрату которая в свою очередь напрямую зависит от качества поверхностного слоя субстрата.
Качество поверхности (рисунок 3.1) определяется ее герметическими характеристиками физико-химическими свойствами поверхностного слоя [13]. После механической обработки и различных видов воздействия на деталь поверхностные слои твердого тела имеют вид показанный на рисунке 3.2. в верхних слоях находятся молекулы адсорбированного газа паров воды и молекулы органического происхождения. В зависимости от их концентрации они могут образовывать моно или мульти молекулярные слои из однородных молекул хаотично ориентированных относительно друг друга. Под этим слоем находится слой молекул органического происхождения молекулярные цепи которых параллельны плоскости твердого тела. Этот слой граничит с поликристаллообразным слоем полярных молекул органического происхождения. Далее к поверхности субстрата залегают слои адсорбированных газов и паров воды причем слой паров воды непосредственно примыкает к слою окислов образованных в результате хемосорбции инородных молекул с материалом поверхностного слоя субстрата.
Рисунок 3.1 - Классификация параметров качества поверхностного слоя субстрата
Толщина данного слоя порядка 20 200 мкм и зависит от среды в которой проводилась механическая обработка субстрата. Под слоем окислов расположен сильно деформированный наклепанный слой материала субстрата который непосредственно граничит с основным материалом.
Обработка поверхностного слоя детали при изготовлении и других технологических операциях какой бы совершенной она ни была приводит к отклонению профиля поверхности от идеальной геометрической формы заданной чертежом. Данные отклонения принято называть погрешностью. С точки зрения причин возникновения погрешностей их разделяют на три категории:
- макрогеометрические отклонения;
- шероховатость поверхности;
- волнистость поверхности.
– слой различных адсорбированных молекул
– слой молекул органического происхождения;
– слой полярных молекул органического происхождения;
– слой адсорбированных газов;
– слой адсорбированных паров воды;
– слой пленок окислов;
– сильно деформированный слой материала субстрата;
– слой основного материала субстрата
Рисунок 3.2 – Модель поверхностного слоя твердого тела
Макрогеометрические отклонения – это погрешности в общей геометрии детали. Различают следующие виды отклонений:
- бочкообразность цилиндрических деталей;
- вогнутость цилиндрических деталей;
- конусность поверхности;
- непрямолинейность.
Поскольку в работе рассматриваются неподвижные сопряжения типа «вал-втулка» и «корпус-кольцо» в которых средний диаметр соединения соразмерим или превосходит длину контакта то в основном представляют интерес первые шесть отклонений. Причем их можно разбить на две группы относим бочкообразность вогнутость цилиндрических деталей и конусность поверхности. Во вторую группу объединяем некруглость овальность и огранку.
При анализе первой группы применительно к аспектам изучаемого вопроса можно сделать следующие выводы. Если значения данных погрешностей находятся в пределах нормы то они не окажут значительного влияния на процесс уплотнения зазора в соединении полимерным составом. Однако если их значения (или сумма значений) выходят за пределы допусков то может сложиться ситуация при которой часть поверхности субстрата будет чрезмерно покрыта составом тогда как в отдельных участках смачивание поверхности не произойдет совсем или состав нанесется в минимальном количестве. Неравномерное распределение полимерного слоя по поверхности субстрата в уплотняемом зазоре однозначно вызовет снижение прочности шва и системы в целом (рисунок 3.3).
Погрешности поверхности объединенные нами во вторую группу также окажут влияние на качество и процесс формирования уплотняющего полимерного шва. Как и в рассмотренном нами выше случае превышение отклонениями допускаемых значений может значительно ухудшить процесс смачиваемости полимером поверхности субстрата. В результате образуется неравномерный по толщине уплотняющий полимерный шов только в плоскости перпендикулярной осевым линиям цилиндрический деталей соединения. Это негативно скажется на стабильности полученных результатов сборки и прочности полимерного уплотняющего шва (рисунок 3.4 3.5). однако в данном случае можно улучшить равномерность распределения состава по поверхности субстрата проворачивая вал или кольцо (чередуя направление вращения) что позволит несколько нейтрализовать вредное влияние указанных факторов.
Рисунок 3.3 - Влияние величины зазора между стыкуемыми поверхностями на прочность уплотняющего слоя полимерного состава (УГ-7)
Рисунок 3.4 - Прочность при аксиальном сдвиге анаэробных материалов в соединениях типа «вал-втулка» в зависимости от зазора S
Рисунок 3.5 - Прочность при аксиальном сдвиге анаэробных составов фирмы «Локтайт» в соединениях типа «вал-втулка» в зависимости от зазора S
Шероховатость поверхности субстрата оказывает непосредственное влияние на прочность собранного соединения и уплотняющего шва. С одной стороны увеличение шероховатости способствует повышению реальной площадки контакта адгезива с субстратом в соединении (таблица 3.1 рисунок 3.6) а с другой препятствует равномерному и полному смачиванию поверхности субстрата полимерным составом. Кроме того во впадинах на поверхности субстрата если они чрезмерно глубокие скапливаются трудноудаляемые включения масел грязи и пузырьки воздуха которые также оказывают негативное влияние на прочность соединения снижая его на 30 40% (рисунок 3.7).
Волнистость поверхности субстрата представляет собой периодические микроотклонения от геометрической формы детали представляющие собой практические равные по размерам возвышения и впадины с шагом волны значительно превышающим его высоту. Различают продольную и поперечную волнистость. Возможная высота и длина волн при различных видах механической обработки поверхности субстрата приведены в таблице 3.2.
Аксиальное усилие Н×m
Удельное аксиальное усилие МПа
Таблица 3.1 Влияние площади контакта на прочность цилиндрических соединений (скользящая посадка шероховатость Rа=125) [17]
– материал АН-6В (ст.45зазор 025);
– материал АН-6В (ст.45 зазор 025)
Рисунок 3.6 - Зависимость механической прочности соединения от шероховатости поверхности
Рисунок 3.7 – Зависимость момента проворачивания деталей соединения относительно друг друга от содержания масла на поверхности этих деталей
Таблица 3.2 – Высота и длина волн на поверхности субстрата в зависимости от вида механической обработки
Фрезерование торцевое
Шлифование цилиндрическое
Возникает волнистость в результате неравномерности подачи при точении и шлифовании вынужденных колебаний системы «станок-приспособление-инструмент-деталь» и т.д. Высота волны является более важным с нашей точки зрения критерием так как от высоты зависят следующие параметры:
- фактическая протяженность несущей поверхности;
- объем пустот профиля;
- удельное давление.
Известно что в прессовых посадках чем меньше высота волны и ее шаг по поверхности субстрата тем больше фактическая площадь контакта. При использовании уплотняющих полимерных составов когда используются переходные и скользящие посадки роль волнистости в обеспечении неподвижности и работоспособности соединений деталей несколько снижается. Однако в литературе отсутствуют данные о положительном либо отрицательном влиянии данного вида погрешностей поверхности субстрата на качество сборки неподвижных соединений с использованием уплотняющих составов. Нам представляется интересным выявить какие виды волнистости размеры высоты волн и их длины существенно снижают прочность соединения либо ее повышают. Последующие экспериментальные работы будут направлены на установление определенных критериев по которым следует назначать волнистость различных деталей неподвижных соединений.
2 Выявление доминирующих параметров качеств контактных поверхностей и адгезии влияющих на прочность неподвижных соединений деталей собранных с применением полимерных уплотняющих составов
Для выявления доминирующих факторов качества контактных поверхностей и адгезии влияющих на прочность неподвижных соединений объединим представленный выше материал и рассуждения в виде блок-схемы (рисунок 3.8).
Очевидно что представленные в схеме показатели могут быть разбиты на группы по важности с точки зрения обеспечения качества соединения. Причем варьировать все показатели в условиях сборочного или ремонтного производства представляется затруднительным. Следовательно необходимо определить ряд факторов изменение которых возможно в условиях производства узлов и агрегатов различных машин и техники причем их изменение позволит добиться наилучшего качества неподвижных соединений.
Рисунок 3.8 – Факторы и показатели влияющие на качество неподвижного соединения деталей с применением полимерных уплотняющих составов
Проанализировав составленную схему с учетом выявленных требований можно сделать ряд выводов:
- как правило перечень уплотняющих полимерных составов выпускаемый химический промышленностью ограничен и стабилен. Изменение основных физико-механических характеристик состава в условиях производства не представляется возможным. Разработка новых составов производителями по заказу неизбежно вызовет удорожание себестоимости продукции;
- изменение материала субстрата и масштабного фактора соединения (размеров основных деталей образующих соединение) также не целесообразно так как не возможно без согласования с разработчиками проекта и потребует много времени и усилий;
- смачиваемость поверхности субстрата полимерным составом и фактическая площадь контакта напрямую зависит от качества поверхностного слоя субстрата вязкости полимерного состава и давления в соединении;
- качество поверхности субстрата по числу влияющих связей с другими показателями оказывается наиболее доминирующим показателем соединения;
- основные показатели качества поверхностного слоя субстрата с учетом большого количества механической и других видов подготовки поверхности могут легко варьироваться;
- изменение технологии производства или ремонта неподвижных соединений возможно осуществить в условиях массового производства без значительных затрат и удорожания себестоимости продукции.
Представлена модель поверхностного слоя субстрата после механической обработки. Рассмотрены основные параметры качества поверхностного слоя. Произведена их разбивка на группы (макрогеометрические отклонения шероховатость волнистость) по основным признакам и выполнен анализ каждой группы. Оценен вклад каждого показателя качества поверхности в прочность неподвижного соединения и качество адгезии. Выявлены наиболее перспективные направления дальнейших исследований.
Проведен анализ показателей качества неподвижного соединения деталей собранных с применением уплотняющих полимерных составов. Разработана блок-схема влияния данных показателей друг на друга. Выявлены доминирующие факторы и сделаны следующие выводы:
- как правило перечень уплотняющих полимерных составов выпускаемый химической промышленность ограничен и стабилен. Изменение основных физико-механических характеристик состава в условиях производства не представляется возможным разработка новых составов производителями по заказу неизбежно вызовет удорожание себестоимости продукции;
ЭКОНОМИЧЕСКИЙ РАСЧЕТ ОСНОВНЫХ ПОКАЗАТЕЛЕЙ СРАВНИВАЕМЫХ ВАРИАНТОВ МЕХАНИЗАЦИИ
Целью экономического расчета является выявление оптимального варианта механизации из сравниваемых:
- автопогрузчик оснащенный безблочной стрелой;
Базовым вариантом считаем механизацию переработки контейнеров с использованием козловых кранов. Для экономического анализа вариантов механизации эффективности принятого оборудования принимается система показателей которая характеризуется: эффективностью капитальных затрат издержками производства использованием основных фондов.
1 Определение полной себестоимости перегрузки 1 тонны груза суммарных капиталовложений приведенных годовых расходов при использовании кранов КК-6
Полная себестоимость переработки груза определяется по формуле [3].
где Сn – себестоимость перегрузки одной тонны груза рубт;
Сх – себестоимость хранения одной тонны груза на складе рубт.
Суммарные капиталовложения на вариант механизированной переработке груза составят:
где Км - капиталовложения на средства механизации руб.;
Кск - капиталовложения в складские сооружения руб.
Приведенные годовые расходы по варианту механизации составят:
где СΣ - годовые эксплуатационные затраты по перегрузке и хранению
ЕН – нормативный коэффициент экономической эффективности капитальных вложений ЕН= 015.
1.1 Расчет затрат на заработную плату работникам складской и механизированной бригады
Для определения затрат по заработной плате необходимо составить штатную ведомость (таблица 4.1 4.2).
Таблица 4.1 – Штатная ведомость работников механизированной бригады
Таблица 4.2 – Штатная ведомость работников складской бригады
Оклад работникам складской и механизированной бригады устанавливается согласно трудовым соглашениям коллективному договору и квалификации работника.
Годовые расходы на заработную плату определяются по формуле [2].
где - коэффициент начислений на заработную плату учитывающий отчисление премии 15 [3];
Σ С·PМ – фонд оплаты труда механизаторов за месяц 4559039 руб. (таблица 4.1).
=1512294720=5304960 руб.
Годовые расходы на заработную плату работникам складской бригады составят [3]:
где Σ С – фонд оплаты труда складских работников за месяц 12881268 руб. (таблица 4.2).
Зск = 15·12·288580=5194440 руб.
Необходимо обеспечить отчисление страховых взносов которые составляют 304 % от годового фонда оплаты труда работников механизированной и складской бригады.
где годовой фонд оплаты труда механизированной бригады;
=03045304960=161270784 руб.
где годовой фонд оплаты труда работников склада;
04·5194440=157910976 руб.
1.2 Расчет затрат на силовую и осветительную энергию
Годовые затраты на приобретение силовой энергии определяются по формуле [3].
где NΣ – суммарная мощность электродвигателей крана 542 кВт;
n – число кранов работающих на складе 2;
ТГ – количество часов работ всех механизмов в течение года.
где Qгод- годовой грузооборот 120000 т;
Коп – коэффициент увеличения погрузо-разгрузочных операций 155;
Пэксп – эксплуатационная производительность крана 18 тч;
nд – коэффициент использования двигателей по мощности 06 [3];
nВ – коэффициент использования двигателей по времени 07 [3];
nс – коэффициент учитывающий потери в производящих цепях 11 [3];
СЭ- стоимость промышленной электроэнергии 713158 руб. кВтч;
СЭ = 542·2·5167·06·07·11·713158=184542108 руб.
Затраты на смазочные и обтирочные материалы составляют 10% от суммы затрат СЭ
М=01·СЭ =01·184542108=18454211 руб.
Затраты на освещение территории склада составят [2]
ЭО= NСВ·СВ·mсв· nс·Cэ
где NСВ – мощность одного светильника типа Г220-1000 1 кВт [2];
ТСВ – время работ светильников в течении года для средней полосы России ТСВ=2920 [2];
mсв – общее количество светильников
где FСК – площадь спроектированного склада 2836 м2;
Е0 – норма освещенности 1м2 площади склада 10 лк [2];
n3 – коэффициент запаса 13 [3];
n2 – коэффициент учитывающий ослабление светового потока 05 [3];
f0 – световой поток ламп 18600 лм [2].
Округляем до ближайшего четного числа принимаем 4 светильников Г220-1000 для освещения склада.
Э0 =1·2920·4·11·713158=9162654 руб.
1.3 Расчет амортизационных отчислений на средства механизации и складских сооружений
Амортизационные отчисления на полное восстановление средств механизации составят:
где КМ – капиталовложения на приобретение средств механизации
КМ = К0· n (1+Δ1+Δ2)
где К0 – оптовая (цена) стоимость крана 6215000 руб.;
Δ1 – транспортные расходы 005 [3];
Δ2 – монтажные расходы 007 [3];
КМ = 6215000·2·(1+005+007)= 13921600 руб.
АМ – норма амортизационных отчислений на полное восстановление средств механизации 5% [2].
АМ = 13921600·001·5=696080 руб.
Затраты на содержание ремонт и техническое обслуживание машин и оборудования принимаем в размере 89 % от их фактической стоимости
=0089=0089 13921600=12390224 руб.
Амортизационные отчисления на полное восстановление складских объектов определяются по той же методике. Капиталовложения в объект склада определяется по формуле
где Кск – стоимость элементов склада руб;
Si – стоимость сооружения единицы объекта склада 16157 рубм2.
Кск=2836·16157=45821252 руб.
Амортизационные отчисления на восстановление складских объектов составят
Аск=45821252·3·001=137463756 руб.
Расходы на содержание и ремонт складских сооружений принимаем в размере 59 % от их фактической стоимости
=005945821252=270345387 руб.
1.4 Определение годовых эксплуатационных расходов на перегрузку и хранение грузов
Годовые эксплуатационные затраты по перегрузке груза механизированной бригадой оснащенной козловым краном КК-6 составят [3]
где П – прочие расходы принимаем 10 % от суммарных затрат
П=001(5304960+161270784+184542108+18454211+696080+
+12390224) =108827334 руб.
Остальные величины определены предыдущим расчетом. С учетом ранее представленной формулой затраты по перегрузке груза составят
СПЕР =5304960+161270784+184542108+18454211+696080+
+12390224+108827334 =1197100677 руб.
Себестоимость механизированной перегрузки груза составит [2]
Годовые эксплуатационные расходы по хранению груза на спроектированном складе составит [3]
где П – прочие расходы 10% от всех предыдущих затрат.
П= 01(5194440+157910976+9162654+137463756+270345387)=
СХР =5194440+157910976+9162654+137463756+270345387+
+109432677 =120375945 руб.
Себестоимость хранения груза на складе составит
Полная себестоимость переработки 1 тонны груза определенная по формуле 4.1
С = 9976+10032=20008 рубт.
Суммарные капиталовложения на вариант механизированной переработки груза составят (формула 4.2)
КΣ = КМ + ΣКСК =13921600+45821252=59742852 руб.
Суммарные затраты на переработку груза составят
СΣ = Спер + Схр =1197100677+120375945=2400860127 руб.
Приведенные годовые расходы по вариантам механизации составят (формула 4.3)
R= 2400860127+015·59742852=3297002907 руб.
2 Определение полной себестоимости перегрузки 1 тонны груза суммарных капиталовложений и приведенных годовых расходов при использовании автопогрузчика оснащенного безблочной стрелой
Полная себестоимость механизированной переработки 1 тонны груза суммарные капиталовложения на вариант механизации и приведенные годовые расходы определяются по формулам представленным в разделе 4.1 соответственно с учетом особенностей данного варианта механизации и данных последующих расчетов.
2.1 Расчет затрат на заработную плату работникам складской и механизированной бригад
Списочный состав работников механизированной бригады представлен в таблице 4.3.
Состав складской бригады режим работы и оклады возьмем с учетом данных таблицы 4.2.
Затраты по выплате заработной платы работникам складской и механизированной бригад в течение года составят
=1512257880=4641840 руб.
Страховые взносы работников соответствующих бригад составят
=03044641840=141111936 руб.
2.2 Расчет затрат на силовую и осветительную энергию
Расчет затрат на приобретение жидкого топлива ведем по формуле
ЭТ =n· Nр · ТГ · СТ · д ;
где NР – норма расхода топлива при работе автопогрузчика 47 кгмаш;
СТ – стоимость 1 кг топлива 4046 руб.;
ТГ – число часов работы машины в течении года
д – коэффициент использования двигателя по мощности 05.
ЭТ = 2·47 · 3444· 4046· 05 = 65491793 руб.
Затраты на смазочные и обтирочные материалы составят
М=01·Ст =01·65491793=6549179 руб.
Годовые затраты по освещению склада определяются аналогично первому варианту механизации
Принимаем для освещения склада 6 ламп типа Г220-1000.
Э0 = NСВ · ТСВ · mСВ · nс ·СЭ = 1·2920·6·11·713158=13743981 руб.
2.3 Расчет амортизационных отчислений на средства механизации и складские сооружения
Расчет ведем по методике описанной выше при расчете первого варианта механизации. Капиталовложения на средства механизации составят
КМ=К0· n (1+Δ1+Δ2) = 4549300·2(1+005+007)= 10190432 руб.
Амортизационные отчисления на полное восстановление средств механизации составят
АМ = КМ · 001 · АВ = 10190432· 001 · 189=192599165 руб.
Затраты на ремонт и восстановление средств механизации
=0089 10190432=90694845 руб.
Капиталовложения в объект склада с учетом стоимости сооружения объектов склада для работы автопогрузчиков (Si =10234 руб.) составят
Кск=3100·10234=31725400 руб.
Аск=31725400·3·001=951762 руб.
Расходы на содержание и ремонт складских сооружений будут равны
=0059317254002=18717986 руб.
2.2Определение годовых эксплуатационных расходов на перегрузку и хранение грузов
Годовые эксплуатационные затраты по перегрузке и хранению груза на складе определяются по методике описанной при экономическом расчете первого варианта механизации.
Годовые эксплуатационные затраты по перегрузке груза с применением автопогрузчика составят (формула 4.4):
П=01(4641840+141111936+65491793+6549179+192599165+
+90694845)= 96063092 руб.
СПЕР =4641840+141111936+65491793+6549179+192599165+
+90694845+ 96063092= 105669401 руб.
Себестоимость механизированной перегрузки груза составит
Годовые эксплуатационные затраты по хранению груза на складе будут равны
П = 001(5194440+157910976+13743981+951762+18717986)= =97345502 руб.
СХР =5194440+157910976+13743981+951762+18717986+
+97345502= 1070800519 руб.
Себестоимость хранения 1 тонны груза на складе составит
Полная переработка груза будет равна
Сп = 8806+8923=17729 руб т.
Суммарные капиталовложения на вариант механизации составят:
KΣ = KМ + ΣКСК = 10190432+31725400=41915832 руб.
Суммарные затраты на переработку груза составят
СΣ = Спер + Схр =105669401+1070800519=2127494529 руб.
Приведенные годовые расходы по вариантам механизации с применением кранов автопогрузчиков составят
R = CΣ + ЕН · КΣ =2127494529+015 ·41915832=2756232009 руб.
3 Выбор оптимального варианта механизации
Полученные в результате расчета данные по обоим вариантам механизации сводим в таблицу 4.4.
Таблица 4.4 – Результаты технико-экономических расчетов по обоим вариантам механизации
Время рабочего цикла ПРМ
Эксплуатационная производительность ПРМ
Капиталовложения на средства механизации
Капиталовложения в склад
Суммарные капиталовложения
Годовые эксплуатационные расходы по перегрузке груза
Годовые эксплуатационные расходы по хранению груза на складе
Суммарные эксплуатационные расходы
Себестоимость перегрузки
Себестоимость хранения
Полная себестоимость
Приведенные годовые расходы
Годовой экономический эффект достигнутый за счет внедрения материала механизации с применением модернизированного автопогрузчика оснащенного безблочной стрелой составит
Э = R - R =3297002907-2756232009=540770898 руб.
На основании проведенных расчетов установлено что по всем основным показателям вариант механизации с использованием автопогрузчиков превосходит вариант с козловым краном КК-6 (таблица 4.4).
Происходит снижение суммарных капиталовложений на 30 % годовых эксплуатационных затрат на 12 % себестоимости переработки на 11 %.
Основные затраты приходятся на содержание и эксплуатацию участка отгрузки. С целью снижения можно предположить следующие мероприятия:
- уменьшение численности персонала склада;
- уменьшение его размеров за счет снижения сроков ожидания отправки груза.
Данные мероприятия позволят повысить экономический эффект от внедрения.
БЕЗОПАСНОСТЬ И ЭКОЛОГИЧНОСТЬ РЕШЕНИЙ ПРОЕКТА
1.1 Общая характеристика и анализ потенциальных опасностей
и вредностей на участке грузового двора
Основным объектом проектирования является участок грузового двора для хранения тарно-штучных грузов открытого хранения. Анализ технологической последовательности переработки груза позволит выявить опасные или вредные производственные факторы возникновение которых возможно при выполнении каждой операции технологического процесса перегрузки ящичных штучных автопогрузчиками:
- травмирование персонала движущимися машинами и механизмами незащищёнными подвижными узлами и элементами;
- при эксплуатации подвижного состава механическое травмирование работников;
- потеря устойчивости штабелем груза и его обрушение;
- при разрыве грузовых стропов падение груза и травмирование персонала.
- при неисправности изоляции и заземления электрооборудования поражение электрическим током персонала.
К вредным производственным факторам следует отнести:
- повышенные уровни производственного шума;
- все работы производятся круглый год на открытом воздухе вследствие чего летом существует вероятность тепловых ударов а зимой обморожения;
- различные транспортно-технологические вибрации;
- недостаточная освещенность рабочего пространства в темное время суток и др.;
Негативное воздействие на работающих оказывает производственный шум. У рабочего работающего в условиях постоянного шума превышающего предельные уровни звукового давления наблюдается повышенная утомляемость замедленная скорость психических реакций снижение памяти возникают сердечнососудистые заболевания что может привести к профессиональным заболеваниям.
Воздействие шума уровнем свыше 75 дБ может привести к потере слуха - профессиональной тугоухости. При действии шума высоких уровней (более 140 дБ) возможен разрыв барабанных перепонок контузия а при еще более высоких (более 160 дБ) и смерть. Шум кроме того нарушает концентрацию внимания точность и координированность движений ухудшает восприятие звуковых и световых сигналов опасности и поэтому способствует росту травматизма. Нормируемые параметры шума на рабочих местах определяется ГОСТ 12.1.003 -83(89) СН 2.2.42.1.8.562 - 96.
Таблица 5.1 - Допустимые уровни звукового давления
Вид трудовой деятельности рабочее место
Уровни звукового давления дБ в октавных полосах со среднегеометрическими частотами Гц
Уровни звука и эквивалентные уровни звука дБ А
Постоянные рабочие места и рабочие зоны в производственных помещениях и на территории предприятия
Также негативное влияние на работников склада оказывают различные вибрации. Вибрация является одним из наиболее распространенных вредных производственных факторов воздействующих на работников. Под вибрацией понимают механические колебания упругих тел при частоте от 3 до 1000 Гц с амплитудами от 05 до 0003 мм.
По характеру воздействия на человека различают общую и локальную вибрации. При работе с ручными машинами вибрация которых имеет максимальный уровень энергии в высокочастотной области спектра (свыше 125 Гц) возникают сосудистые расстройства с наклонностью к спазму периферических сосудов и приводят к вибрационной болезни.
Различают гигиеническое и техническое нормирование вибраций. Гигиенические нормы ограничивают параметры производственной вибрации исходя из физиологических требований исключающих возможность возникновения вибрационной болезни. Гигиенические нормы производственной вибрации определяются ГОСТ 12.1.012 - 90 и СН 2.2.42.1.8.556 - 95.
Нормируемой величиной как для локальных так и общих вибраций является уровень виброскорости в октавных полосах частот которые представлены в таблице 5.2.
Таблица 5.2 - Гигиенические нормы вибраций
Допустимый уровень виброскорости дБ в октавных полосах со среднегеометрическими частотами Гц
Транспортно-технологическая
Подъемно-транспортные средства установки и рабочее оборудование на участке перегрузки и хранения грузов имеют электропривод. Поэтому всегда существует потенциальная опасность поражения работающих электрическим током.
Электрический ток проходя через организм человека производит термическое электрическое механическое и биологическое действия. Электрический ток даже небольшой величины (005 А) вызывает в организме серьёзные последствия (ожоги сильные судороги и боли затрудняет дыхание). Ток величиной 01А создаёт электрический удар который поражает весь организм в целом (легкие сердце нервную систему и останавливает дыхание). Наиболее опасным для жизни человека является ток промышленной частоты 50 Гц.
Для предупреждения поражения рабочих от электрического тока все токонесущие устройства имеют защитное зануление. Защитное зануление на участке применяется в связи с тем что для подвода электрической энергии к различным электроустановкам используется трёхфазная четырёхпроводная сеть с заземлённой нейтралью. Четвёртым проводником в этой сети служит нулевой защитный проводник что позволяет просто и надежно использовать эту схему электрозащиты.
Недостаточная освещенность рабочих мест возникающая в результате неправильного использования естественного и искусственного освещения грузовой площадки также может стать причиной травмирования рабочего из-за потери визуального контроля человеком своего положения в опасной зоне.
1.2 Разработка организационных и технологических мероприятий устраняющих опасные и вредные производственные факторы
Для предотвращения вышеуказанных вредных и опасных воздействий необходимо предусмотреть комплекс организационных и технических мероприятий для их устранения.
К организационным мероприятиям по устранению и предотвращению влияния опасных и вредных производственных факторов относятся мероприятия связанных с допуском к производству работ инструктажем по технике безопасности и контроль над соблюдением требований техники безопасности [6].
К техническим мероприятия относятся мероприятия связанные с поддержанием технических средств в исправном состоянии их контроль и испытания мероприятия по обеспечению электробезопасности использования системы сигнализации а также достаточная освещённость производственных площадей.
На грузовых дворах безопасность проведения перегрузочных операций регламентируется ГОСТ 12.3.009-76. Отдельные работники руководствуются соответствующими инструкциями например машинисты погрузчиков должны выполнять «Инструкцию по безопасному ведению работ для машинистов погрузчиков».
К производству работ допускаются лица прошедшие:
инструктаж по пожарной безопасности;
первичный инструктаж на рабочем месте;
инструктаж по электробезопасности на рабочем месте.
Заступая на дежурство водитель погрузчика тщательно осматривает машину особое внимание обращает на действие тормозов исправность грузоподъемника (рамы каретки захватных приспособлений) убеждается в отсутствии течи в соединениях маслопроводов гидросистем в прочности крепления звездочек и грузовых цепей пальцев цилиндров наклона рамы и др. Особое внимание обращается на регулировку тормозной системы. Педаль ножного тормоза имеет свободный ход 10 15 мм (до начала перемещения поршни главного тормозного цилиндра) и полный ход 90 95 мм. Малейший отказ тормозной системы снижает безопасность труда.
Во время перемещения погрузчика с грузом раму грузоподъемника следует отклонять назад. Это повышает устойчивость машины и исключает сползание груза с вил.
В связи с наличием на объекте значительного шума предусматривается использование системы знаковой сигнализации в установленном порядке. Предусматривается использование индивидуальных средств защиты (беруши шлемы наушники и т.п.) для снижения вредного воздействия данного производственного фактора на работающих.
Лица участвующие в проведении погрузо-разгрузочных работ должны знать знаковую сигнализацию. Сигнальщик одет в каску желтого цвета рукавицы брезентовые повязки на руках красного цвета и спецодежда.
Водитель выбирает скорость движения погрузчика в зависимости от состояния дороги типа и массы груза условий работы не допускать резких троганий торможений и поворотов погрузчиков. Реверсирование движений погрузчика следует производить только после полной остановки. Водитель погрузчика контролирует отсутствие совмещение операций по подъему-опусканию груза с передвижением погрузчика. Также контролируется нахождение людей под поднимаемым грузом. При смене грузозахватных приспособлений водитель должен соблюдать требования инструкции на оснастку и инструмент. Если из-за большого пакета или груза не видно дороги допускается передвижение электропогрузчика задним ходом но с низкой скоростью. Движение с грузом осуществляется на скоростях обеспечивающих безопасность обслуживающего персонала. У пересечений проездов поворотах в местах скоплений людей водитель снижает скорость машины и подает сигналы; водитель погрузчика контролирует отсутствие людей в зоне разворота машины. Если на пути движения электропогрузчика особенно с грузом на вилах встречаются мостки перекрывающие неровности пути то водитель обязан предварительно проверить прочность мостков затем уже переезжать их.
Работа погрузчика прекращается при скорости ветра превышающей допустимую для данного погрузчика при снегопаде дожде или тумане и в других случаях когда машинист плохо различает сигналы стропальщика или перемещаемый груз. При движении автотранспорта по территории контейнерной площадки скорость его движения не должна превышать 15 кмч. Переезды через железнодорожные пути оборудуются охраняемыми или специальными автоматическими шлагбаумами с сигнализацией.
При работе погрузчиков на открытых площадках опасным является воздействие сильного ветра. Ветровая нагрузка определяется при удельном давлении ветра 400 Нм2 для погрузчиков работающих в портах и 250 Нм2 для остальных погрузчиков.
Аналитически устойчивость погрузчиков рассчитывается аналогично расчету устойчивости кранов но с учетом специфики их устройства и эксплуатации.
Продольная устойчивость при штабелировании. Груз должен быть поднят на максимальную высоту. Положение грузоподъемника перпендикулярно плоскости опорной плоскости (рисунок 5.1)
Рисунок 5.1 – Схема к расчету устойчивости погрузчика
Требование продольной устойчивости при штабелировании можно получить уравнения моментов всех сил относительно ребра возможного опрокидывания.
где КШ – коэффициент запаса;
G0 - масса погрузчика без груза 10280 кг;
Q – масса груза 5000 кг;
- расстояние от ребра опрокидывания до центра тяжести
- расстояние от ребра опрокидывания до центра тяжести
h Н – соответственно высоты центра тяжести погрузчика и груза мм;
- угол наклона опорной плоскости град.
В данном случае =0 следовательно
С учетом известных значений получаем
С целью более полного изучения вопроса рассмотрим случай когда присутствует наклон опорной плоскости. Расчетная схема представлена на рисунке 5.2.
Этому случаю соответствует следующая расчетная модель:
- номинальный груз поднят на максимальную высоту;
- грузоподъемник перпендикулярен к опорной площадке;
- площадка наклонена к горизонтали на угол 2016.
Рисунок 5.2 – Расчетная схема
Коэффициент грузовой устойчивости
На схеме приняты следующие обозначения:
доп – дополнительный вылет центра тяжести шарнира стрелы за счет уклона площадки;
- перемещение центра тяжести погрузчика за счет уклона площадки;
точка О1 – центра тяжести шарнира стрелы когда грузоподъемник перпендикулярен к опорной поверхности а груз поднят на максимальную высоту;
точка О2 – центра тяжести стрелы когда грузоподъемник наклонен вперед на угол и груз поднят на максимальную высоту.
точка О – положение центра тяжести погрузчика.
погрузчик на уклоне в 16% т.к. тормозной момент .
Выполнен анализ проектируемой площадки по перегрузке тарно-штучных грузов определены основные вредные и опасные производственные факторы. Разработан ряд мероприятий по предотвращению или снижению воздействия этих факторов. Детально выполнен расчет устойчивости модернизированного погрузчика. В результате расчета установлено что потери устойчивости погрузчика в результате производства работ не наступит.
2 Охрана окружающей среды
2.1 Общая характеристика влияния работы грузового двора на окружающую среду
Участок на котором осуществляется комплексная механизация перегрузки штучных грузов предназначен для осуществления различных погрузочно-разгрузочных и складских операций. Хозяйство участка состоит из открытой площадки на которой перегрузка грузов производится одним автопогрузчиком. Площадка оборудована соответствующим путевым развитием: для подачи вагонов к месту погрузки и для перемещения автотранспорта вдоль разгрузочно-погрузочного фронта.
С учетом характера работ проектируемого объекта можно сделать вывод что при осуществлении производственной деятельности на окружающую среду будет оказываться вредное воздействие.
Проектируемый производственный объект как одна из сфер хозяйственной деятельности человека оказывает неблагоприятное воздействие на окружающую природную среду. В первую очередь это связано с большим количеством вредных веществ выделяющихся в атмосферу как двигателями перегрузочных и транспортных средств. [18].
Наиболее значимыми загрязнителями при этом являются сажа оксиды углерода серы и азота углеводороды свинец.
Антропогенная деятельность человека в производственном процессе проектируемого грузового двора приводит к загрязнению как поверхностных так и подземных источников воды. Основными источниками загрязнения гидросферы являются сбрасываемые сточные воды остатки топливо-смазочных материалов смываемые дождями с кузовов техники и подвижного состава. Данные загрязнители гидросферы способны вступать в химические реакции и образовывать более вредоносные комплексы [18-20].
При ремонте металлоконструкций автопогрузчика и складских сооружений происходит загрязнение выбросами от сварочных и окрасочных работ. В окружающую среду при сварке выбрасываются твердые частицы марганец и его соединения окислы хрома фториды фтороводород окись азота окись углерода. При окраске восстановленных узлов выделяются пары растворителей краски и т.д. Часть окрасочных материалов попадают в почву. [19].
Неблагоприятные воздействия на почву оказывает закрытие больших площадей бетоном и асфальтом. Такие покрытия препятствуя нормальному впитыванию дождевой воды в почву нарушают баланс грунтовых вод для земель находящихся как непосредственно под этим покрытием так и за его пределами. Кроме того при обильных дождях покрытия способствуют образованию более или менее значительных потоков смывающих плодородную почву и способствующих эрозии.
Основной источник электромагнитного воздействия на предприятии – электромагнитные поля от линий электропередач (ЛЭП).Отрицательные воздействия электромагнитных полей на человека и на те или иные компоненты экосистем прямо пропорционально мощности полей и времени облучения. Неблагоприятное воздействие электромагнитного поля создаваемого ЛЭП проявляется уже при напряженности поля равной 1000 Вм у человека нарушается эндокринная система обменные процессы функции головного и спинного мозга и др.
Кроме химических веществ выделяющихся в воздух перегрузочный транспорт проектируемого объекта создает так называемые энергетические загрязнения такие как шум и электромагнитные поля которые в некоторых случаях могут оказывать даже большее воздействие на окружающую среду чем вредные химические вещества.
С учетом выше сказанного можно сделать вывод что необходимо определять и постоянно контролировать объемы вредного воздействия проектируемого грузового двора на окружающую среду.
Для снижения вредного воздействия необходимо принять меры по охране окружающей среды в соответствии с Федеральным законом «Об охране окружающей среды» от 10.01.02г.№7-ФЗ [21].
Согласно статьи 45 [21] при эксплуатации автопогрузчиков оказывающих негативное воздействие на окружающую среду необходимо контролировать и соблюдать нормативы допустимых выбросов и принимать меры по обезвреживанию загрязняющих веществ в том числе их нейтрализации снижению уровня шума и иного негативного воздействия на окружающую среду.
Негативное воздействие на окружающую среду является платным. что указано в статье 16 Закона. Ответственность за загрязнение окружающей среды определяется согласно ст.75 [21].
Проведем расчеты выбросов от дизельных двигателей погрузчиков задействованных в перегрузочном процессе. В настоящее время отработана методика расчета выбросов по количеству топлива (фактически израсходованному за отчетный период или предполагаемому по нормам прогнозное). Система платежей за загрязнение среды выбросами от передвижных источников предусматривает проведение расчетов по фактически израсходованному топливу. При таких расчетах все объекты учета разбиваются на две большие группы: новые (после постройки) и остальные – прошедшие разные стадии технического обслуживания (четыре подгруппы).
При работе перегрузочной техники с дизельными двигателями образуются загрязняющие вещества поступающие в окружающие среду. Расчет выбросов этих веществ производится как от неорганизованных источников по удельному расходу топлива (тч) и коэффициентам эмиссии загрязняющих веществ (тт). Численные значения коэффициента эмиссии загрязняющих веществ в выбрасываемых отработанных газах техники занятой в перегрузочном процессе представлены в таблице 5.3.
Таблица 5.3 – Значения коэффициента эмиссии загрязняющих веществ в выбрасываемых отработанных газах техники занятой в перегрузочном процессе
Удельный расход топлива qуд тч
Коэффициенты эмиссии α (тт)
Погрузчик с безблочной стрелой оснащенный двигателем Д-180
Для проведения дальнейших расчетов необходимо определить годовой расход топлива G. Расчет ведем по формуле
где – продолжительность работы двигателя погрузчика.
где kоп - коэффициент увеличения погрузочно-разгрузочных операций 155;
Пэксп – эксплуатационная производительность погрузчика 27 тч;
n – численность погрузчиков на складе 2 шт.
G=00083444=2755 тгод.
Планируется на различных участках склада использование 2 однотипных погрузчиков с двигателями Д-180.
GΣ=2755·2=5510 тгод.
Выбросы i-го загрязняющего вещества Мi рассчитываем по формуле
Таким образом выбросы окиси углерода составят
МСО=01·5510=551 тгод.
Выбросы углеводородов равны
МСН=003·5510=1653 тгод.
Выбросы двуокиси азота равны
МNО=004·5510=2.204 тгод.
Выбросы сажи составят
МСАЖ=000155·5510=00854 тгод.
Выбросы сернистого ангидрида равны
МSO=002·5510=11 тгод.
Выбросы бенз(а)пирена
МБП=000000032·5510=0000018 тгод.
Основными направлениями снижения величины загрязнения окружающей среды являются: рациональный выбор технологических процессов для производства готовой продукции и ее транспортирования; использование средств защиты окружающей среды и поддержание их в исправном состоянии.
Полное решение проблемы уменьшения загрязнения воздуха выбросов от двигателей зависит в первую очередь от технических мероприятий касающихся повышения экологичности каждого двигателя и уменьшения токсичности выбросов. Это - долгосрочная программа требующая больших материальных затрат и времени. Определить целесообразность и достаточность тех или иных технических и организационных мероприятий по снижению выбросов объекта позволяет долгосрочный прогноз загрязнения воздуха с учетом информации о существующих уровнях загрязнения воздуха в городах и мероприятий по снижению выбросов [18].
В таблице 5.4 приведен перечень возможных мероприятий ведущих к снижению выбросов вредных веществ при эксплуатации дизельных двигателей погрузчиков.
Таблица 5.4 – Перечень мероприятий позволяющих улучшить токсические характеристики дизелей эксплуатируемых погрузчиков
Наименование предприятий
Эффективность мероприятий
Уменьшение угла опережения впрыска топлива
Увеличение содержания в выхлопе СО рост расхода топлива снижение на 5-7 % эффективной мощности
Предварительное насыщение топлива воздухом
Снижение выбросов сажи и СО соответственно на 70 и 30%
Рост выбросов NOX на 15%
Применение присадок синтетических спиртов
Снижение NOX на 30-40% CO на 40% SO2 на 15-20%
Усложнение конструкции двигателя
Применение каталитических нейтрализаторов
Снижение CO и углеводородов до 90%
Низкая эффективность на малых нагрузках
В целях защиты окружающей среды грузового двора от вредного воздействия производственной деятельности при использовании погрузчиков необходимо снижать расход топлива. Для этого необходимо осуществлять мероприятия по поддержанию технического состояния ДВС проверять работу топливных систем двигателей вовремя устранять неисправности в работе двигателей транспортных средств работающих на грузовом дворе.
В выпускной квалификационной работе проведено детальное сравнение двух вариантов механизации по основным технико-экономическим показателям. Сравнению подвергались автопогрузчик с консольной безблочной стрелой и козловой кран КК-6 со строповым захватом. Полученные значения убедительно свидетельствуют о преимуществе предлагаемого к внедрению средства механизации – автопогрузчика с безблочной стрелой. Его внедрение позволяет повысить производительность перегрузочных работ и повысить технологичность процесса перегрузки.
Внедрение разработанной технологии работ и модернизированного средства механизации позволяет получить годовой экономический эффект в размере 540770898 руб.
Проведенные конструкторские расчеты подтвердили возможность установки захвата на погрузчик. Изменение конструкции погрузчика не ухудшит эксплуатационные характеристики и качество работы погрузчика.
В научно-исследовательском разделе было исследовано влияние качества поверхностей сопрягаемых деталей на их эксплуатационною надежность и срок службы. Проведен поиск доминирующих показателей качества поверхностного слоя детали влияющих на адгезию и прочность собранного соединения.
Проведена экологическая оценка решений проекта и оценка уровня охраны труда и безопасности работ. Разработаны и предложены мероприятия проведение которых позволит снизить вред наносимый окружающей среде и персоналу проектируемого грузового двора.
Список использованных источников
Бойко Н.И Транспортно-грузовые системы и склады: Бойко Н.И. Чередниченко С.П. Учебное пособие для вузов. Ростов нД: Феникс 2007. - 400 с.
Бойко Н.И. Погрузочно-разгрузочные и складские работы: Бойко Н.И. Чередниченко С.П. Учебное пособие. - Ростов НД: РГУПС 2006. - 334 с.
Бойко Н.И. Транспортно-грузовые комплексы. Бойко Н.И. Хачкинаян А.Е. Дядечко Н.В. Механизация складских работ с насыпными грузами: Учебное пособие для вузов. - Ростов НД: РГУПС 2007. -218с.
Журавлев Н.П. Транспортно-грузовые системы: Журавлев Н.П. Маликов О.Б. Учебник для вузов. - М.: Маршрут 2006. - 368 с.
Комплексная механизация и автоматизация погрузочно-разгрузочных работ: Учебник для вузов ж.д. транспорта. А.А. Тимошин И.И. Мачульский и др.: под ред. А.А. Тимошина и И.И. Мачульского. - М.: Маршрут 2003. - 400 с.
Зиновьев В.Е. Особенности проведения погрузочно-разгрузочных и складских работ с различными грузами: Учебное пособие. - Ростов НД: РГУПС 2005. - 60 с.
Найденов Б.Ф. Объемные веса и удельные объемы грузов Справочник М. «Транспорт» 1971 г.
Макеева Ю.Н. Оптимизация вариантов механизации и автоматизации погрузочно-разгрузочных работ с применением ЭВМ» Ростов-на-Дону РГУПС 1984 г.
Вайсон А.А. Подъемно-транспортные машины М. «Машиностроение» 1989 г.
Гохберг М.М. Справочник по кранам М. «Машиностроение» том 1 1988 г.
Гохберг М.М. Справочник по кранам М. «Машиностроение» том 2 1988 г.
Бекасов В.И. Охрана труда в грузовом хозяйстве железных дорог .И. Бекасов М.Е. Лысенко В.А. Муратов М. «Транспорт» 1984 г.
Сибаров Ю.Г. Охрана труда в железнодорожном транспорте» М. «Транспорт» 1981 г.
Журнал «Библиотека инженера по охране труда» №5 2001 г.
Ушаков П.Н. Руководство по изучению Правил устройства и безопасности эксплуатации грузоподъемных кранов М. «Металлургия» 1979 г.
«Единые нормы амортизационных отчислений» М. «Дан Инфра-М» 2001 г.
Гарин В.М. Расчет платы за загрязнение окружающей среды» В.М. Гарин Т.А. Шатихина Учебное пособие РГУПС Ростов-на-Дону 2006 г.
Аксенов И.Я. Транспорт и охрана окружающей среды И.Я. Аксенов В.И. Аксенов М. «Транспорт» 1986 г.
Гарин В.М. Экология для технических вузов. В.М. Гарин И.А. Кленова В.И. Колесников Учебник Ростов-на-Дону «Феникс» 2001 г.
Новиков Ю.В. Экология окружающая среда и человек М. «Гранд» 1998 г.
Шабельский В.А Защита окружающей среды при производстве лакокрасочных покрытий. – Л.: Химия 2005. – 120 с.
Иванникова Т.Ф. Безопасность труда при нанесении лакокрасочных покрытий в машиностроении Иванникова Т.Ф. Фиалковская Т.А – М.: Машиностроение 2011. – 112 с.
Гирусов Э.В. Экология и экономика природопользования Под ред. Э.В. Гирусова – М.: ЮНИТИ 2007. – 591 с.
Росляков П.В. Методы защиты окружающей среды: учебник для вузов П.В. Росляков. – М.: Издательский дом МЭИ 2007. – 336 с.: ил.
Федеральный закон №7 «Об охране окружающей среды» от 10.01.2002 г.
Справочная система «Консультант плюс» .
Антоневич Э.Ф. Погрузочно-разгрузочные работы М. «Транспорт» 1972 г.
Падня В.А. Погрузочно-разгрузочные машины на железнодорожном транспорте справочник М. «Транспорт» 1972 г.
Козлов Ю.Т. Грузозахватные устройства справочник М. «Транспорт» 1980 г.
Бойко Н.И. Ресурсосберегающая технология ремонта транспортных средств анаэробными материалами и металлополимерными композициями Н.И. Бойко В.Е. Зиновьев учебное пособие Ростов-на-Дону РГУПС 2000 г.
Зиновьев В.Е. Применение металлополимерных композиций в ресурсосберегающих технологиях машиностроения. Монография. Ростов-на-Дону РГУПС 2010 г.
«Типовая инструкция для лиц ответственных за безопасное производство работ кранами» РД 10-34-93.
Подобед М.А. «Охрана труда комментарий к КЗОТ» М. «Приор» 2001 г.
Механизм передвижения крюка.dwg

СМ 14.04.06.02.00.000 СБ
Максимальный ход 2150*
Технические требования
*Размеры для справок
Неуказанные предельные отклонения размеров H14
При сборке все соединительные элементы смазать смазкой
Циатим-203 ГОСТ 8773-73
Соединительный элемент не показан
ТДС 14.04.02.02.00.000 СБ
НИР факторы влияющие на адгезиюdwg.dwg

Каф. ЭРМ гр. ТДС-5-242
оказывающие основное влияние
на адгезионную прочность и эксплуатационную
надежность металлополимерного соединения
поверхности субстрата
адгезива и субстрата
поверхности субстрата
упрочняющими элементами
металлополимерного соединения
Ферма стрелы.docx
ТДС 14.04.02.03.01.00.000
ТДС 14.04.02.03.02.00.000
ТДС 14.04.02.03.00.00.001
ТДС 14.04.02.03.00.00.002
ТДС 14.04.02.03.00.00.003
Схема работ по установке опор контактной сети.dwg

устранения вредных и опасных
Основные мероприятия для
производственных факторов
УСТРАНЯЮЩИЕ ВРЕДНЫЕ И ОПАСНЫЕ
ПРОИЗВОДСТВЕННЫЕ ФАКТОРЫ
Медицинский и профессиональный отбор работников
Лечебно-профилактическое обслуживание работников
Стажировка работника на рабочем месте
Проведение всех видов инструктажей по технике безопасности
Постоянный контроль руководящих кадров и ответственных лиц
Использование работниками спецодежды и защитных средств
Соблюдение всех требований Ростехнадзора к грузоподъемным механизмам
Соблюдение всех требований Ростехнадзора к грузовым канатам и стропам
участвующими в проведении погрузо-разгрузочных работ знаковой сигнализации
Создание регламентированной освещенности площадки и рабочего пространства
Технологич показатели.dwg

сравниваемых вариантов
Технологические показатели
- вариант механизации
с применением козлового крана КК-6
с применением автопогрузчика с безблочной стрелой
сравниваемых вариантов механизации
Площадь спроектированного
Задействованное количество
Время рабочего цикла
перегрузочных машин
Рекомендуемые чертежи
- 03.12.2014
- 12.06.2019