Проект механического участка по производству корпуса токосъемника




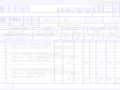
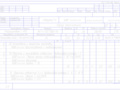
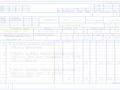
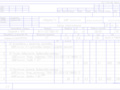
- Добавлен: 25.10.2022
- Размер: 5 MB
- Закачек: 0
Описание
Состав проекта
![]() |
![]() ![]() ![]() ![]() |
![]() ![]() |
![]() ![]() ![]() |
![]() ![]() |
![]() ![]() |
![]() ![]() |
![]() ![]() ![]() ![]() |
![]() |
![]() |
![]() ![]() |
![]() ![]() |
![]() ![]() |
![]() ![]() |
![]() ![]() |
![]() ![]() |
![]() ![]() |
![]() ![]() |
![]() ![]() |
![]() ![]() |
![]() ![]() |
![]() ![]() |
![]() ![]() |
![]() ![]() |
![]() ![]() |
![]() ![]() |
![]() ![]() |
![]() ![]() |
![]() ![]() |
![]() ![]() |
![]() ![]() |
![]() ![]() |
![]() |
![]() ![]() ![]() ![]() |
![]() ![]() ![]() ![]() |
![]() ![]() ![]() ![]() |
![]() ![]() ![]() ![]() |
![]() ![]() ![]() ![]() |
![]() ![]() ![]() ![]() |
![]() ![]() ![]() ![]() |
![]() ![]() ![]() ![]() |
![]() ![]() ![]() ![]() |
![]() ![]() ![]() ![]() |
![]() ![]() ![]() ![]() |
![]() ![]() ![]() ![]() |
![]() ![]() ![]() ![]() |
![]() ![]() ![]() ![]() |
![]() ![]() ![]() ![]() |
![]() ![]() ![]() ![]() |
![]() ![]() ![]() ![]() |
![]() ![]() ![]() ![]() |
![]() ![]() ![]() ![]() |
![]() ![]() ![]() ![]() |
![]() ![]() ![]() ![]() |
![]() ![]() ![]() ![]() |
![]() ![]() ![]() ![]() |
![]() ![]() ![]() ![]() |
![]() ![]() ![]() ![]() |
![]() ![]() ![]() ![]() |
![]() ![]() ![]() ![]() |
![]() ![]() ![]() ![]() |
![]() ![]() ![]() ![]() |
![]() ![]() ![]() ![]() |
![]() ![]() ![]() ![]() |
![]() ![]() ![]() |
![]() ![]() ![]() ![]() |
![]() ![]() ![]() ![]() |
![]() ![]() ![]() ![]() |
![]() ![]() ![]() ![]() |
![]() ![]() ![]() ![]() |
![]() ![]() ![]() ![]() |
![]() ![]() ![]() ![]() |
![]() ![]() ![]() ![]() |
![]() ![]() ![]() ![]() |
![]() ![]() ![]() ![]() |
![]() ![]() ![]() ![]() |
![]() ![]() ![]() ![]() |
![]() ![]() |
![]() ![]() |
![]() ![]() |
![]() ![]() |
![]() ![]() |
![]() ![]() |
![]() ![]() |
![]() ![]() |
![]() ![]() |
![]() ![]() |
![]() ![]() |
![]() ![]() |
![]() ![]() |
![]() ![]() |
![]() ![]() |
![]() ![]() |
![]() ![]() |
![]() ![]() |
![]() ![]() |
![]() ![]() |
![]() ![]() |
![]() ![]() |
![]() ![]() ![]() ![]() |
![]() |
![]() ![]() ![]() ![]() |
![]() |
![]() |
![]() |
![]() ![]() ![]() ![]() |
![]() ![]() |
![]() ![]() ![]() ![]() |
![]() |
![]() ![]() |
![]() |
![]() |
![]() ![]() ![]() ![]() |
![]() ![]() ![]() ![]() |
![]() ![]() ![]() ![]() |
![]() ![]() ![]() ![]() |
![]() ![]() ![]() ![]() |
![]() ![]() ![]() ![]() |
![]() ![]() ![]() ![]() |
![]() ![]() ![]() ![]() |
![]() ![]() ![]() ![]() |
![]() ![]() ![]() ![]() |
![]() ![]() ![]() ![]() |
![]() ![]() ![]() ![]() |
![]() ![]() |
![]() ![]() |
![]() ![]() |
![]() ![]() |
![]() ![]() |
![]() ![]() |
![]() ![]() |
![]() ![]() |
![]() ![]() |
![]() ![]() |
![]() ![]() |
![]() ![]() |
Дополнительная информация
спецификация12.dwg

Винт М4х10 ГОСТ Р 11738-84
Винт М6х20 ГОСТ Р 11738-84
Винт М6х30 ГОСТ Р 11738-84
Винт М8х26 ГОСТ Р 11738-84
Винт М8х30 ГОСТ Р 11738-84
Винт М6х26 ГОСТ Р 11738-84
Гайка М8 ГОСТ 5915-70
Гайка М20 ГОСТ 5915-70
Заклепка 5 ГОСТ 10299-80
Пружина ГОСТ 13165-67
Прокладка ГОСТ 8752-79
Уплотнение ГОСТ 8753-81
Шайба 8 ГОСТ 11371-72
Шайба 20 ГОСТ 11274-72
Штуцер прямой ГОСТ 16049-70
Дипломная записка.doc
2. Программа запуска эффективный фонд рабочего времени ..5
3. Задание на проектирование 6
ТЕХНОЛОГИЧЕСКАЯ ЧАСТЬ 7
1. Анализ технологичности детали ..7
2. Обоснование выбора заготовки 7
3. Технологический маршрут обработки и выбор баз ..10
4. Размерный анализ сборочной единицы .11
5. Расчет припусков на механическую обработку 14
6. Расчет режимов резания ..17
7. Техническое нормирование .26
8. Планировка участка .29
КОНСТРУКТОРСКАЯ ЧАСТЬ 33
1. Проектирование станочного приспособления 33
2. Проектирование контрольного приспособления 33
3. Проектирование режущего инструмента 37
ПРОИЗВОДСТВЕНЫЕ ВОПРОСЫ . ..44
1. Обоснование формы производства . 44
2. Расчёт количества рабочих мест .. 47
3. Расчёт календарно-плановых нормативов.. 48
4. Организация транспорта на участке 49
ЭКОНОМИЧЕСКАЯ ЧАСТЬ 51
ЭКОЛОГИЧЕСКАЯ ЧАСТЬ 70
СПИСОК ИСПОЛЬЗОВАННЫХ ИСТОЧНИКОВ .. .80
Машиностроение является ведущей отраслью народного хозяйства которая производит орудия труда. В связи с этим машиностроение должно находиться на высшем уровне по развитию на базе новейших достижений науки и техники.
В настоящее время улучшается структура парка металлообрабатывающего оборудования за счет увеличения выпуска высокопроизводительных специальных и агрегатных станков прогрессивного кузнечно-прессового оборудования автоматических линий.
Снижается удельная металлоемкость машин и оборудования за счет совершенствования конструкции машин широкого применения металла повышенной прочности фасонных профилей проката высокой точности конструктивных пластмасс замены технологических прессов основанных на резании металлов методами формообразования деталей.
В последнее время успешно решаются вопросы связанные с разработкой автоматизированного проектирования технологической подготовки производства и развитие гибких автоматизированных систем.
Появление станков с числовым программным управлением (ЧПУ) обеспечило при их универсальности высокую степень автоматизации обработки деталей повышение производительности труда и качества изготавливаемых деталей а так же позволило исключить изготовление большого количества оснастки.
Развитие и совершенствование станков с ЧПУ привело к появлению таких станков которые объединили в себе технологические возможности многих станков обычного использования.
1. Служебное назначение детали
Основное служебное назначение выпускаемого узла – обеспечение электрической связи потребителей электрической энергии вращающегося несущего винта с неподвижной электрической систеьой питания. Основными требованиями конструкции выпускаемого узла являются:
-постоянство выходных параметров электрической схемы.
По принципу работы токосъемник представляет собой систему со скользящими контактами между щетками и кольцами посредством которой питание током передается от неподвижного источника к вращающимся потребителям.
Корпус изделия является основной базовой деталью электромашины на которой базируются все остальные сборочные узлы и детали.
Корпус изготовляется из алюминиевого сплава АК7ч и имеет ряд специфических особенностей:
- корпус является тонкостенной деталью в результате чего возникает ряд трудностей при обработке на отдельных операциях;
- наличие массивных переходов по краям на торцах лап создает значительные трудности в получении заготовки;
-наличие глухих резьбовых отверстий затрудняет их обработку;
-корпус имеет жесткие требования для отверстий под посадочные места под подшипники а конструктивные особенности не позволяют обрабатывать их с одной установки;
-биение поверхностей относительно друг друга и перпендикулярность жестко ограничены до 005мм
Все перечисленные выше требования требуют внимательного подхода к каждой операции особенно при выборе установочных баз и режимов резания а также повышенные требования к точности зажимных приспособлений.
Программа запуска эффективный фонд рабочего времени
оборудования и обоснование типа производства
Определяем программу запуска по формуле:
где Nв – программа выпуска; Nв=10000 штук;
aос – процент отсева изделий по технологическим причинам
Тип производства определяем по коэффициенту серийности:
где r – такт поточной линии мин;
tшт.ср – среднее-штучное время по участку мин;
Такт поточной линии можно определить по формуле:
где Fд – эффективный фонд времени работы производственного
Для двухсменной работы принимаем Fд=4015 часов.
Среднее штучное время по участку определяем по формуле:
m – количество операций;
коэффициент серийности:
т.к. в нашем случае 5 кс 10 то производство средне серийное.
3 Задание на проектирование.
Проект механического участка по производству корпуса токосъемника.
Разработать технологический процесс механической обработки корпуса.
Технические условия на объект производства
корпус токосъемника должен соответствовать требованиям ТУ и конструкторской документации;
участок должен соответствовать и отвечать нормам техники безопасности. Допустимые нормы санитарно-гигиенических факторов по ГОСТ 12.1.005-83 допустимый уровень вибрации по ГОСТ 12.1.012-78 допустимый уровень шума по ГОСТ12.1.003-83 освещенность по СНиП I I 4-79.
заводские данные по проектируемому объекту:
-заводская программа выпуска 10000штук;
-базовый технологический процесс;
-трудоемкость изготовления щита.
ТЕХНОЛОГИЧЕСКАЯ ЧАСТЬ
1Анализ технологичности детали
Требование технологичности детали предусматривает такое проектирование которое при соблюдении всех эксплуатационных качеств обеспечивает минимальную трудоемкость изготовления детали минимальную материалоемкость и себестоимость детали без ущерба ее служебного назначения а также быстрого освоения серийного выпуска изделий на базе применения новых методов обработки.
Технологический анализ конструкции обеспечивает улучшение технико-экономических показателей разрабатываемого технологического процесса.
Деталь «Корпус» представляет собой отливку цилиндрической формы выполненную из АК7ч ГОСТ1583-93. Сплав хорошо обрабатывается и имеет высокие механические и антикоррозионные свойства.
Сплав относится ко 2-ой группе алюминиевых сплавов и применяется для изготовления сложных по конфигурации изделий. Отливка проста по конфигурации но требует стержневой формовки для образования внутренних полостей.
Конструкция детали имеет хорошие базовые поверхности.
В целом деталь является технологичной и это позволяет использовать прогрессивное оборудование и высокопроизводительные режимы обработки.
2.Обоснование выбора заготовки
Существует много способов получения заготовки:
литье под давлением:
литье по выплавляемым моделям.
Из этих способов два являются наиболее производительными и рациональными методами: это литье в кокиль и литье под давлением.
Литье под давлением по технологическим и экономическим показателям занимает ведущее место среди способов получения отливок т.к. при наибольшем приближении формы и размеров отливки к готовой детали высокой точности и чистоте поверхности этот способ обеспечивает и наиболее высокий уровень производительности труда возможность полной автоматизации технологического процесса.
Литьем под давлением изготавливают сложные тонкостенные отливки. Как правило детали полученные литьем под давлением не подвергают механической обработке за исключением посадочных мест. Прочность отливок при литье под давлением на 15-20% превышает прочность отливок из того же сплава изготовленных литьем в песчано-глинистые формы.
Пластичные свойства отливок несколько снижаются т.к. в процессе заполнения формы металлом воздух находящийся в форме и газы образующиеся от сгорания смазки создают газовоздушную пористость в добавление к тому количеству газов которое находится в металле в растворенном состоянии.
Газовоздушная пористость уменьшает плотность и герметичность отливок.
К недостаткам способа литья под давлением относятся:
-высокая стоимость пресс форм сложность и длительность изготовления;
- трудность выполнения отливок со сложными полостями и поднутрениями.
Учитывая эти недостатки и изучив конструкцию детали данный способ не дает возможности изготавливать деталь «Корпус» литьем под давлением. Другие способы получения заготовки являются не экономичными т.к. заготовки по внешнему виду не удовлетворяют требуемому качеству. Заготовка при этом имеет большие припуски на механическую обработку. Поэтому метод получения заготовки принимаем аналогичным существующему на данном предприятии – литье в кокиль.
Литье в кокиль экономически целесообразно применять в условиях серийного производства. Наибольшее распространение получили для литья в кокиль цветные сплавы имеющие более низкую температуру плавления и более высокую стойкость форм.
Сплавы для фасонного литья должны обладать высокой жидкотекучестью сравнительно небольшой усадкой малой склонностью к образованию горячих трещин и пористости в сочетании с хорошими механическими свойствами сопротивлением коррозии.
Этими свойствами обладают сплавы АК74 ГОСТ 1583-93.
Корпус выполняем из АК74 ГОСТ 1583-93 химический состав и механические свойства сплава АК74 представлены в таблице 2.1.
«Содержание элементов в % »
Вид термической обработки
Механические свойства
Принятому типу производства подбираю кокильную однопозиционную машину марки 5944.
Техническая характеристика
-размеры подкоккильных плит 630х500;
-минимальное расстояние между плитами . 500 мм;
-ход толкателей ..100мм;
-усилие раскрытия .10000н;
-время холостого цикла 15сек;
-производительность корпусов в час . 28 штук;
-масса получаемых отливок ..до 3 кг.
Данный способ получения заготовки совпадает с базовым проектом.
3. Технологический маршрут обработки и выбор баз
Корпус является основной базовой деталью на котором монтируются все остальные узлы .Конструкторскими базами являются посадочные места подшипниковых узлов и 146Н7 127F8.
Так как конструкция детали не позволяет обрабатывать все поверхности с одной установки то при проектировании техпроцесса нужны вспомогательные технологические базы. Анализируя конструкцию детали легко придти к выводу что наиболее удобной базой от которой нужно вести техпроцесс является сквозное отверстие 78. Технологический маршрут обработки представлен в таблице 2.2.
Технологический маршрут обработки
Наименование операции
Из технологического маршрута операции 005 и 010 являются подготовительными на них производится подготовка вспомогательных технологических баз. Чистовое растачивание конструкторских и сборочных баз вынесены на конечные операции 055 и 060 как наиболее трудоемкие и обработка которых производится на точных полуавтоматах.2.4 Размерный анализ сборочной единицы
Размерный анализ сборочной единицы является одним из мероприятий связанных с ее технологичностью. Проводя его проверяем технические требования на сборку а также допуски на входящие детали. Для нормальной работы токосъемника необходимо обеспечить зазор между корпусом и подшипником. Учитывая небольшое расстояние между подшипниками температурные деформации вала отбрасываем. Зазор находим из условия сборки узла. Во избежание заклинивания шариков необходимо чтобы зазор ³ 0.Для уточнения допуска выполним расчет размерных цепей.
Целью расчета является определение метода достижения точности замыкающего звена.
При выполнении размерного анализа учитываем положения ГОСТ 16319-80 «Расчет размерных цепей».
Для обеспечения нормальной работы узла токосъемника необходимо обеспечить минимальный зазор между корпусом токосъемника и торцом подшипника для исключения заклинивания тел качения в подшипниках.
Расчет размерных цепей:
Составляем схему размерной цепи и выявляем по ней увеличивающие и уменьшающие звенья (рис.2.2).
Увеличивающие А1 А2;
Номинальные размеры составляющих звеньев представлены в таблице 2.3.
Рис.2.2 Схема размерной цепи
Номинальные размеры составляющих звеньев
Предельные отклонения
Определяем поле допуска замыкающего звена
Определяем номинальный размер замыкающего звена А по формуле:
где - увеличивающее звено;
- уменьшающее звено;
Находим координату середины поля допуска замыкающего звена по формуле:
Определяем верхнее и нижнее предельные отклонения замыкающего звена
Таким образом при заданных номинальных размерах и предельных отклонениях составляющих размеров замыкающий размер должен быть выполнен
Проверочный расчет замыкающего звена
Вывод: Замыкающий размер рассчитан правильно
Точность замыкающего звена обеспечивается методом полной взаимозаменяемости.
Результаты расчетов представлены в графической части дипломного проекта.
5. Расчет припусков на механическую обработку
Расчет припусков на механическую обработку производим расчетно-аналитическим методом для отверстия корпуса . Технологический маршрут обработки отверстия состоит из двух переходов: чернового и чистового растачивания.
Суммарное значение и характеризующее качество поверхности литых заготовок выбираем по таблице (табл.27[1]). Заготовка получена литьем в кокиль класс точности 3 . Предварительное растачивание мкм мкм окончательное растачивание мкм мкм (таблица 6[1]).
Суммарное значение пространственных отклонений для заготовки данного типа определяем по формуле
где - коробление отверстия мкм;
- смещение отверстия в отливке мкм;
Коробление отверстия следует учитывать как в диаметральном так и в осевом его сечении следовательно:
где - диаметр и длина обрабатываемого отверстия;
- удельная кривизна заготовки на 1 мм =07(табл.30.[1]);
=-смещение отверстия в отливке мкм (табл.31.[1]);
Величина остаточного пространственного отклонения после чернового растачивания
Погрешность установки при предварительном растачивании
гдепогрешность базирования в самоцентрирующем патроне с базированием по торцу мкм(табл.36[1]);
- погрешность закрепления мкм (табл.40[1]);
Остаточная погрешность установки при чистовом растачивании
где=0 так как черновое и чистовое растачивание производится в одной установке;
Рассчитываем минимальные значения межоперационных припусков пользуясь основной формулой:
Минимальный припуск:
- под растачивание предварительное
- под растачивание окончательное
По результатам полученных данных заполняем таблицу 2.4.
Графа «Расчетный размер» (см. табл.2.4.) заполняется начиная с конечного (чертежного) размера последовательным вычитанием расчетного минимального припуска каждого технологического перехода.
Таким образом для чистового растачивания наибольший предельный размер а наименьший 780.
Для чернового растачивания наибольший предельный размер
Значения допусков каждого перехода принимаем по таблицам в соответствии с квалитетом точности того или иного вида обработки. Так для чистового растачивания допуск составляет 30 мкм (по чертежу). Для чернового растачивания ; допуск на отверстие в отливке 3–го класса точности по ГОСТ 1855-85 составляет мкм.
В графе «Предельный размер» наибольшее значение () получается по расчетным размерам округленным до точности допуска соответствующего перехода.
Наименьшие предельные размеры () определяются из наибольших предельных размеров вычитанием допусков соответствующих переходов. Так для окончательного растачивания наибольший предельный размер =78030 мм наименьший
Для заготовки наибольший =7607 мм =758 мм.
Минимальные предельные значения припусков равны разности наибольших предельных размеров выполняемого и предшествующего переходов а максимальное значение - разности наименьших предельных размеров. Тогда для окончательного растачивания получаем
Для предварительного растачивания получаем
Производим проверку правильности выполненных расчетов:
Полученные результаты сводим в таблицу 2.4
«Расчет припусков и предельных отклонений по технологическим переходам на обработку отверстия корпуса диаметром 78мм »
Тех. перех. обработ. отверст.
Пред.значен. припусков мкм
На основании данных расчета строим схему графического расположения припусков и допусков по обработке отверстия 78+0030 (см. рис.2.2.)
растачивания окончательного 78030 мм
растачивания окончательного 78 мм
растачивания окончательного 30 мкм
растачивания предварительного 7796 мм
растачивания предварительного 7780 мм
растачивания предварительного 160 мкм
на растачивание предварительное 2000 мкм
на растачивание предварительное 1890 мкм
на растачивание окончательное 200 мкм
на растачивание окончательное 70 мкм
Рис.2.2.Схема графического расположения припусков и допусков на обработку отверстия 78+0030
6.Расчет режимов резания
Режимы резания устанавливаемые при обработке деталей являются одним из главных факторов технологического процесса.
Режимы резания выбираются таким образом чтобы при наименьшей себестоимости данной технологической операции была достигнута наибольшая производительность труда. Данные по режимам резания вносим в операционную карту обработки ГОСТ 31404-86.
Операция 010 «Токарная с ЧПУ»
Обработка ведется на станке модели АТПР 2М12.Подрезать торец мм выдерживая диаметр мм резцом ВК8 2122-0053 ГОСТ 18800-73.
Выбираем подачу по таблице 12[3]
Корректируем с паспортными данными станка и принимаем
Определяем скорость резания:
где глубина резания мм;
период стойкости мин;
поправочный коэффициент на скорость резания.
Значение коэффициента и показателей степени выбираем по таблице 28[2].
Поправочный коэффициент определяется:
где коэффициент учитывающий влияние материала заготовки. Выбираем из таблицы 4 [2] ;
коэффициент учитывающий состояние поверхности. Выбираем из таблицы 5[2] ;
коэффициент учитывающий материал инструмента. Выбираем из таблицы 6[2] .
Определяем число оборотов шпинделя:
где скорость резания ммин;
диаметр обрабатываемого отверстия мм.
Корректируем с паспортными данными станка принимаем тогда действительная скорость резания.
где диаметр обрабатываемого отверстия мм;
частота вращения шпинделя (из паспортных данных);
Определяем силу резания:
действительная скорость резания ммин;
коэффициент учитывающий реальные условия резания.
Значения коэффициента и показатели степени выбираем из таблицы 22[2].
Определяем поправочный коэффициент
где поправочные коэффициенты учитывающие влияние
геометрических параметров режущей части инструмента; их произведение равно 1.
коэффициент учитывающий влияние качества обрабатываемого материала.
где показатель степени выбираем из таблицы 9 [2] .
Определяем эффективную мощность резания:
действительная сила резания ммин.
Проверяем достаточна ли мощность привода станка. Необходимо выполнить условие. Мощность на шпинделе станка
У станка АТПР 2М12 а .
Следовательно обработка возможна.
где L-величина перемещения резца мм ;
где -длина обработки мм =93 мм;
-величина врезания =0 мм;
- величина перебега мм =0;
Для обработки отверстия 30мм принимаем комбинированный инструмент сверло - зенковка из быстрорежущей стали Р6М5 3046.
Глубина резания при
Подача ммоб.(см. табл.25[2]). Корректируем по паспорту станка подачу и принимаем ммоб.
Определяем скорость резания
- постоянная (см. табл.28[2]);
- стойкость сверла мин(см.табл.30[2]);
; ; ; (см. табл.28.[2]);
Определяем частоту вращения шпинделя
Корректируем частоту вращения шпинделя по паспорту станка и принимаем
Определяем действительную скорость резания
Крутящий момент на шпинделе и осевую силу рассчитываем по формулам
где значения коэффициентов и показателей степеней (см. табл.32.[2]);
D –диаметр сверла мм D=30;
-коэффициент учитывающий фактические условия обработки зависит только от материала обрабатываемой заготовки и определяется выражением
Мощность резания (эффективная) кВт
где n- частота вращения инструмента обмин;
У станка МС12-250 а .
где L-величина перемещения сверла мм
где -длина обработки мм ;
-величина врезания мм. При одинарной заточке сверла
- величина перебега мм;
Для обработки отверстия 26 мм используем инструмент сверло из быстрорежущей стали Р6М5 26 мм.
. Глубина резания мм.
Подача ммоб. (см. табл.25[2]).
Корректируем по паспорту станка и принимаем ммоб.
Скорость резания определяем по формуле:
где -постоянная (см.табл.28[2]);
- диаметр сверла мм;
Корректируем частоту вращения шпинделя по паспорту станка и принимаем .
Крутящий момент на шпинделе.
где значения коэффициентов и показателей степеней (см. табл.22.[2]);
D –диаметр сверла мм D=26;
где n- частота вращения инструмента обмин
где -длина обработки мм ; При одинарной заточке сверла
-величина врезания мм;
- величина перебега мм;
7. Техническое нормирование
Определение норм времени на операцию 040 Многоцелевая с ЧПУ.
Определение времени на управление станком.
где - -время на включение и выключение станка мин ;
-время на открывание заградительного щита и закрывание мин ;
-время на включение пульта лентопротяжного механизма и выключение мин .
Получаем время на управление станком:
Определение времени на контрольные измерения:
где - время измерения детали в зависимости от измерительного инструмента и длины измеряемой поверхности мин.
Время активного наблюдения принимается равным 5% от времени цикла (согласно нормативов). Время цикла определяется на входе составления управляющей программы на станок в зависимости от режимов резания. Принимаем
где - основное время;
Получаем время активного наблюдения
Определяем время переходов
Время переходов принимается 015 мин на 1 метр пути.
Перекрываемое время занятости рабочего на данном станке
Определяем машинное свободное время
где - машинное свободное время мин.;
- машинное время или - основное время =593 мин;
Определяем время занятости рабочего.
Время на установку детали в специальное приспособление
где - время на установку детали в приспособление мин.;
- время на установку детали в приспособление в зависимости от способа крепления мин.
- коэффициент зависящий от вида обрабатываемого материала - для легких сплавов (карта 7[7]).
Время занятости рабочего
Определяем количество обслуживаемых станков при работе на станках-дублерах время которых равно или кратно свободному машинному времени и времени занятости рабочего по формуле:
где - коэффициент учитывающий возможные отклонения вспомогательного времени от принятых значений =08 (Табл.1[8]);
Получаем количество обслуживаемых станков:
Определяем штучное время:
где - штучное время мин.;
- оперативное время мин.;
- время технического обслуживания рабочего места мин.;
- время на отдых и личные надобности.;
- берется нормативное [8] 12% от .
Определяем подготовительно-заключительное время на партию деталей:
где - время на получение наряда чертежа режущего инструмента заготовки до начала и сдача их после окончания обработки партии =7 мин (карта 11 поз.1[7]);
- время на ознакомление с работой чертежом осмотр заготовки =2 мин (карта 11 поз.2[7]);
- время на инструктаж мастера =3 мин (карта 11 поз.3[7]);
Определяем норму выработки с одного станка за смену по формуле:
где - продолжительность смены мин;
8.Планировка участка
8.1. Расчет производственной площади
Расчет производственной площади определяется исходя из норм удельной площади и количества станков на линии.
где - количество станков
-удельная площадь на один станок;
- количество групп станков;
Определяем площадь занимаемую оборудованием:
Токарный станок с ЧПУ модели АТПР 2М12 1314м2 4 шт.;
Многоцелевой станок с ЧПУ модели МС 12-250 9 м2 4 шт.;
Вертикально-фрезерный станок с ЧПУ модели ФП-4 118м2 2 шт.;
Координатно-сверлильный станок модели КС12-500 55м2 3 шт.;
Токарный па модели 1А240П 204м2 2шт.;
Площадь контрольного места
где -площадь на одно рабочее место контролера принимаем =5м2;
n - количество рабочих мест;
Площадь участка для слесаря – наладчика принимаем
где - площадь участка для слесаря – наладчика принимаем 5м2;
n - количество рабочих мест n=1;
i -коэффициент использования площади i =13 175 принимаем
Площадь склада заготовок и готовой продукции принимаем
Площадь занимаемая рабочим местом мастера F= 6 м2.
Таким общая площадь участка с учетом всех проемов проездов проходов и складочных мест заготовок и деталей а также коэффициента R=22 с учетом удобства эксплуатации станков составляет
При проектировании механического участка предусмотрена возможность последовательного прохождения заготовки по стадиям обработки с учетом максимального использования рабочей площади с соблюдением требований охраны труда и техники безопасности. Планировка разработана с учетом нормального хода производства т.е. его равномерности поточности пропорциональности и возможности развития производства в перспективе его гибкости создании условий для высокопроизводительного труда работающих сокращения длительности его цикла с учетом допустимых нагрузок на пол и перекрытия.
Планировка поточной линии должна отвечать принципу прямоточности предусматривать возможность передачи деталей между рабочими местами по кратчайшему расстоянию. Для этого станки располагаем последовательно в соответствии с технологическими операциями обработки. Размещение оборудования осуществляем вдоль продольных пролетов. Применяем здание с сеткой колонн м. При планировании участка учитываем место для хранения заготовок и готовых деталей. Оборудование на участке расположено в два ряда.
Запас материалов должен быть невелик так как назначение его –обеспечение регулярного снабжения рабочих мест. Склад оборудован штабелером. Заготовки хранятся на стеллажах в таре.
На рабочих местах станочников устанавливаем тумбочки для хранения инструмента.
Цветовую отделку потолков стен балок и других частей здания а также технологического оборудования осуществляем преимущественно светлыми тонами обеспечивающими повышение освещенности рабочих мест за счет отраженного света от поверхности интерьера. В цехе для производственных рабочих и служащих предусматривается установка фонтанчиков с питьевой водой. В цехе имеются бытовые помещения с раздевалкой и душевой.
Планировка участка произведена с учетом требований техники безопасности и пожаропасности.
ПРОИЗВОДСТВЕННЫЕ ВОПРОСЫ
1 Обоснование формы организации производства
При серийном производстве могут быть две формы организации производства: поточная и непоточная.
А т. к. у нас корпуса четырех типоразмеров то организуем поточное производство. Поточное форма организации производства является передовой и прогрессивной при этой форме улучшаются все технико – экономические показатели.
Переход от изготовления одной детали к другой осуществляется с переналадкой части рабочих мест линии с изменением режимов резания и оснастки поэтому выбираем переменно – поточную линию.
Для такой линии необходимо определить частные такты:
Деталь представитель N1=10050 шт.; t1=3945мин;
Условные детали N2=20000 шт.; t2=4505мин;
N3=35000 шт.; t3=4852мин;
Определяем коэффициенты приведения:
Определяем приведенную программу:
Определяем условный такт
где h – допустимый коэффициент на переналадку линии
для крупносерийного производства h =(002 003);
Частные такты для каждой из деталей
r1 =K1×rу =1×301=301 мин;
r2 =K2×rу =114 ×301=343 мин;
r3 =K3×rу =1.23 ×301=370 мин;
Определяем действительный годовой фонд времени для детали
где См – число смен занятых на изготовление данной детали;
Тм – продолжительность смены Тм = 8 часов;
Определяем число смен:
где R – темп выпуска деталей в смену:
Определяем % времени от действительного годового фонда времени работы линии для детали представителя:
.3.2 Расчет количества рабочих мест и коэффициента загрузки
Расчетное количество рабочих мест на операции
Коэффициент загрузки на каждой операции:
Рассчитаем Срi и Кзi для первой операции:
Данные расчета для всех операций приводим в таблице 3.1
Количество и загрузка рабочих мест
Токарный с ЧПУ АТПР2М12
Многоцелевой с ЧПУ МС12-250
Верт.фрезерный с ЧПУ ФП-4
Коорд.-сверл. с ЧПУ КС12-500
Установка электрохимическая
Расчет количества рабочих мест с учетом совмещения операций представляем в таблице 3.2.
Расчет количества рабочих мест и рабочих
с учетом совмещения операций
Количество рабочих мест
Т. к. практически на всех операциях установлены станки с ЧПУ то необходимо учесть многостаночное обслуживание.
Количество станков которые может обслужить один рабочий можно найти по формуле:
где Тмаш =1033мин – машинное время;
Труч – время выполнения ручных приемов а также время наблюдения за работой станков и на переход от станка к станку
Труч =Тву +(1 05) мин (3.11)
гдеТву – вспомогательное время на установку и снятие детали;
Т. е. рабочий может обслужить сразу 4 станка.
Количество основных производственных рабочих определяем
из таблицы 3.2 учитывая что работа в две смены принимаем
3 Расчет календарно – плановых нормативов
)Предварительно определяем минимальный размер партии деталей
где a =(003 01) – коэффициент допускаемых потерь времени на
переналадку оборудования;
tпз – подготовительно – заключительное время принимаем наибольшее из всех операций равное 7.
) Среднесуточное потребление деталей штук
) Периодичность запуска партии деталей (ритм)
Необходимо принять по унифицированному ряду.
) Оптимальное количество деталей в партии штук
4 Организация транспорта на участке
Расчетное количество тележек [ 1 стр.375 ф. 278]
где Q – вес деталей транспортируемых в год кг
mз - масса заготовки mз = 23кг.
mдет – масса детали mдет =18кг.
Nз – программа запуска Nз = 10050 штук.
Q=10050 (23+1.8)=41205 (кг).
где i – среднее количество транспортных операций на одну деталь
(перевоз заготовок из склада в цех и перевоз готовых деталей на
склад готовой продукции) т. е. i =2.
q – средняя грузоподъемность тележки за один рейс q =150 кг;
F – номинальный годовой фонд времени работы тележки в одну
смену F =2070 часов.
m – количество смен m =2.
Кт – коэффициент использования тележки
где Кс =08 – коэффициент использования суточный;
Кг =075 – коэффициент использования номинальной
Vср =20 ммин – средняя скорость тележки;
tз =5 мин – время на загрузку тележки;
tз =4 мин – время на разгрузку тележки;
Определяем коэффициент загрузки тележки
Т.к. тележка загружена очень мало то она будет использоваться для перевозки грузов и на других участках.
1 Определение стоимости основных фондов участка
Стоимость основных фондов складывается из нескольких элементов
)Стоимость здания занимаемого участком
где Sу –площадь занимаемая участком м2; Sу =200 м2;
-цена одного м2 здания; =3000 руб;
Ссд =200×3000 =600000 (руб).
) Стоимость оборудования подсчитаем в таблице 4.1
Стоимость оборудования
ТокарныйсЧПУАТПР2М12
Вертикал.-фрезер.ФП-4
Координатно-сверл.КС12-500
Электрохимическая установка
) Стоимость производственного и хозяйственного инвентаря принимаем условно 3% от стоимости оборудования:
2 Расчет стоимости материала
Определяем стоимость заготовки:
где mз – масса заготовки: mз=23кг.
Цмет – цена 1 кг материала руб.
Деталь изготавливается из материала АК7ч ГОСТ 1583-93 стоимость 1 кг равнаЦмет=5225 (руб).
Т.к. деталь в процессе производства обрабатывается то имеются возвратные отходы (стружка) стоимость которых можно определить по формуле:
где mд – масса готовой детали; mд=18 (кг).
Цмет.отх. – цена отходов; Цмет.отх.=15 (руб).
3 Определение стоимости энергоресурсов
Годовой расход силовой энергии участка можно определить по формуле:
[ стр.377 ф.281] (4.5)
где Кс – коэффициент спроса; в среднем Кс=03;
- суммарная установленная мощность оборудования кВт;
Fэф – эффективный фонд работы оборудования Fэф=4015 ч;
hз – коэффициент загрузки оборудования по времени hз=08;
Определение стоимости силовой электроэнергии
где ЦЭ – цена 1 кВт×ч электроэнергии ЦЭ=125 руб
4 Определение численности ППП участка
Явочная численность основных производственных рабочих определена в п.3.3 Чоя= 12 человек.
Определяем списочное число основных производственных рабочих
где b – процент потерь номинального фонда рабочего времени
Численность вспомогательных производственных рабочих определяем укрупненно.
Для серийного производства (30 45)% от численности основных производственных рабочих.
Чв =110×040=45 человек
Принимаем 6 человек.
Полученные данные сведем в таблицу 4.3.
Численность вспомогательных производственных рабочих
по профессиям и сменам
В том числе по сменам
5 Расчет годового фонда заработной платы участка
5.1 Расчет заработной платы основных производственных рабочих
Для расчета заработной платы основных производственных рабочих принимаем повременно-премиальную систему оплаты труда.
) Расчет расценки на операцию:
где Сч – часовая тарифная ставка;
К – коэффициент изменения штучного времени в условиях
многостаночного обслуживания.
Произведем расчет для первой операции а для других операций данные расчета занесем в таблицу
Рабочий обслуживает 3 станка и К=0.48.
Сч.з=9352– четвёртый разряд
) Определяем тарифный фонд заработной платы:
где Nз – программа запуска шт;
Рсдi – сдельная расценка iой операции руб.
Данные расчетов сведем в таблицу 4.4.
) Определяем основную заработную плату основных производственных рабочих
гдеЗпр – премия (принимаем 80 % от Зтар);
Расчет годового тарифного фонда заработной платы
основных производственных рабочих
Зр.к. – районный коэффициент 15% от (Зтар+Зпр); Зр.к.=
Тогда основная зарплата:
Но учтем что на линии обрабатывается еще две детали а на изготовление детали представителя тратится всего 125% времени.
Тогда зарплата основная за год:
) Определяем дополнительную заработную плату:
) Определяем общий годовой фонд заработной платы:
) Определяем общий фонд заработной платы:
) Определяем среднемесячную зарплату
где Чр – численность рабочих сдельщиков на участке
5.2 Расчет заработной платы вспомогательных производственных
Принимаем для расчета повременно - премиальную систему оплаты труда.
На участке работают:
два контролера 4 разряда тарифная ставка Сч=9.352 руб;
два слесаря – ремонтника 4 разряда Сч=9352 руб;
) Определяем тарифный фонд заработной платы вспомогательных производственных рабочих
где Fэ – эффективный годовой фонд рабочего времени Fэ=1840 часов;
Расчет произведем для контролеров для слесарей и электромонтеров он будет аналогичен т.к. тарифная ставка у всех одинаковая расчет представим в таблице:
) Дальнейший расчет ведем по формулам
Принимаем премию 80% от Зтар
Районный коэффициент
Тогда основная зарплата
) Определяем дополнительную зарплату рабочих повременщиков:
)Определяем общий фонд зарплаты
)Определяем годовой фонд заработной платы с учетом премии из
) Определим среднемесячную заработную плату:
5.3 Расчет фонда оплаты труда ИТР участка
С учетом двух смен принимаем двух мастеров.
Принимаем для них контрактную систему оплаты труда
) Определяем оклад за год
где – месячный оклад мастера для 9 разряда Зм=2512руб.;
Ч - количество человек; Ч=2 чел.;
)Определяем годовой фонд зарплаты с учетом районного
) Определяем общий фонд оплаты труда ИТР
где Зфн – премия из фонда накопления принимаем 20-30% от Зосн.
)Определяем среднемесячную зарплату
Расчет зарплаты участка представляем в таблице 4.5
Фонд заработной платы всех работающих на участке
6 Составление сметы расходов на содержание и эксплуатацию оборудования
)Определяем расходы на амортизацию оборудования
С целью компенсации износа основных фондов используется система амортизационных отчислений их величина определяется на основе норм амортизации которые устанавливаются на один год.
Амортизация – это постепенное перенесение стоимости основных фондов на производимую продукцию.
Расчет амортизационных отчислений представим в таблице 4.6
Амортизационные отчисления
Сумма амортизационных
Верт.-фрезерный ФП-4
Коордю-сверлил.КС12-500
) Расходы на эксплуатацию оборудования
В данную статью входят:
а) затраты на силовую электроэнергию;
б) затраты на вспомогательные материалы.
Принимаем условно 10 тыс.руб. на один станок в год
т.е Звсп.мат.=10×16=160 (тыс.руб.)
в) Годовой фонд зарплаты ремонтников и наладчиков с начислениями
Итого на эксплуатацию оборудования:
Зэксп.обор.=1309600 +17540565+160000+2440757=188917135 (руб)
) Текущий ремонт оборудования
Принимаем условно 3% от стоимости оборудования
Зрем.обор.=Соб×003=11330×003=3399 (тыс.руб)
)Износ малоценных и быстроизнашивающихся инструментов
Принимаем условно из расчета 10 тыс.руб. на одного основного производственного рабочего
Зизн=14×10=140 (тыс.руб)
Принимаем условно 3% от суммы всех предыдущих статей
Зпроч.=(188917135 +339900+140000)×003=7107214 (руб)
Смету расходов представим в таблице 4.7
Смета расходов на содержание и эксплуатацию оборудования
Амортизация оборудования
Расходы на эксплуатацию оборудования
Текущий ремонт оборудования
Износ малоценных и быстроизнашивающихся инструментов
) Определяем процент к основной заработной плате основных производственных рабочих:
7 Cоставление сметы цеховых расходов
)Содержание аппарата управления
Эти затраты равны фонду оплаты ИТР
)Содержание прочего цехового персонала
Эти затраты равны фонду оплаты труда контролеров
Зпроч. = 8396732 руб.
) Амортизация зданий и сооружений
где Ссд– стоимость площади участка (см. п. ) Ссд=215874руб
% - норма амортизации; 1%
)Расходы на рационализацию и изобретательство
Принимаем условно 1000 руб в год на одного основного производственного рабочего.
Зрац=12×1000=12000 (руб)
)Расходы по технике безопасности
Принимаем условно 2 тыс.руб. в год на одного рабочего
Зтб=12×1=12 (тыс.руб.)
) Расходы на содержание зданий сооружений и инвентаря включают:
а) расходы на осветительную электроэнергию
Годовой расход электроэнергии на освещение можно определить по нормам расхода на 1 м2 площади
где Рнорм – нарма расхода на 1 м2 площади
для механических цехов Рнорм=(20 22)Вт; [ стр.378]
S=200 м2 – площадь участка;
Fосв.нагр.- годовая осветительная нагрузка для широты (40 60°) для механических цехов Fосв.нагр.=2100 часов [ стр.379]
Wосв.=21×200×2100=8820 (кВт×ч)
Расходы на освещение
Зосв.=Wосв.×Цэл.=8820 ×125=11025 (руб)
б) расходы на отопление:
[ стр382 ф.289] (4.18)
где qт-расход тепла на 1м3 здания qт=(15 20) ккалчас;
Н – количество часов в отопительном периоде
для средней полосы Н=4320 часов;
Тогда затраты на отопление
Зотоп.=Q×Cотоп.=13824×145=20045 (руб)
в) расходы воды на хозяйственно - бытовые нужды:
Берем укрупненно для обычных чехов 25 литров в смену на каждого работающего:
Qводы=25×Z×254=25×20×254=127000 (литров в год) =127(м3).
Тогда затраты на воду:
Звод=Qводы×Своды (4.19)
Звод= 127× 844=10719 (руб)
где Своды-=8.44 (руб). за м3. : - стоимость воды на хозяйственно-бытовые нужды.
г) Материалы и зарплата на содержание здания
Принимаем условно 25% от стоимости здания
Зсод.=215874 ×0025=5397 (руб).
Принимаем условно 3% от суммы предыдущих затрат
Зпроч.=003×(11025+20045+10719+5397)=5850 (руб).
Смету цеховых расходов представим в таблице 4.8.
Смета цеховых расходов
Содержание аппарата управления
Содержание прочего цехового персонала
Амортизация зданий и сооружений
Расходы на рационализацию и изобретательство
Расходы по технике безопасности
Содержание зданий и сооружений
Прочие расходы (3% от суммы п.1 .6)
)Определяем процент к основной зп основных производственных
8 Составление плановой калькуляции на деталь корпус
Расчет представим в виде таблицы 4.9
Поделив затраты по соответствующей статье на программу запуска получим затраты на одну деталь
Плановая калькуляция цеховой себестоимости детали
Транспортно – заготовительные расходы
Основная зарплата основных
производственных рабочих
Дополнительная зарплата основных
Начисления на социальное страхование
Расходы на содержание и эксплуатацию
Итого цеховая себестоимость:
9 Расчет технико – экономических показателей участка.
Определение годовой экономической эффективности.
Годовой экономический эффект от внедрения нового (проектного) технологического процесса определяем по формуле:
где С1 - себестоимость детали (базовый вариант) С1=815руб;
С2 – себестоимость детали (проектный вариант) С2=687руб;
Е – нормативный коэффициент эффективности капитальных
Ку1 и Ку2 – удельные капитальные вложения проектного
и базового варианта.
где К1 – капитальные затраты базового варианта К1=13386600 руб;
К2 – капитальные затраты проектного варианта К2=12271400 руб;
Nз – программа запуска.
Тогда экономический эффект составит:
Определение срока окупаемости
Снижение себестоимости
Технико-+экономические показатели механического участка по
производству корпуса токосъемника
Технико-экономические
Годовой выпуск деталей
Средний коэффициент.загрузки
Численность всех рабочих
Численность основных производственных рабочих
Средне-месячная зарплата одного
производственного рабочего
Капитальные затраты на единицу
Цеховая себестоимость детали
Снижение цеховой себестоимости
Годовой экономический эффект
Повышение производительности труда:
КОНСТРУКТОРСКАЯ ЧАСТЬ
1. Проектирование станочного приспособления
Для многоцелевой операции 030 выполняемой на многоцелевом станке модели МС 12-250 спроектировано станочное приспособление с пневматическим поршневым приводом двухстороннего действия. В поршневых приводах двустороннего действия сжатый воздух поочередно подается в обе полости А и Б пневмоцилиндра и перемещает поршень 1 со штоком 2 при разжиме и зажиме. Золотник 3 распределительного крана 4 при повороте рукоятки производит последовательную подачу сжатого воздуха в полость А и Б пневмоцилиндра и выпуск воздуха из полостей в атмосферу (см. рис 5.1).
Рис.5.1 Поршневой привод двустороннего действия
При расчете пневмоприводов определяют осевую силу на штоке поршня зависящую от диаметра пнемоцилиндра и давления сжатого воздуха в полостях его.
Расчет осевой силы Q для пневмоцилиндра двустороннего действия при давлении сжатого воздуха на поршень в бесштоковой полости:
где D – диаметр пневмоцилиндра (поршня) см;
d –диаметр штока поршня см;
p –давление сжатого воздуха МПа p = 06;
=085 089 – к.п.д. учитывающий потери в пневмоцилиндре.
2.Расчет и проектирование контрольного приспособления
Контрольное приспособление служит для замера радиального биения 127 и торца Т относительно 80+0030 мм которое должно быть не более 005 мм. Контроль осуществляется с помощью индикатора закрепленного на штанге и находящегося в непосредственном соединении с электроконтактной приставкой со световым табло. Быстродействующее пневматическое приспособление с гидропластом – простое в обслуживании обеспечивает достаточную точность позволяет использовать его на рабочем месте станочника.
Отклонение от номинального диаметра размера фиксируется на индикаторе. Световое табло (красный и зеленые цвета) облегчает визуально контролировать отклонения от заданного размера.
Крепление заготовки осуществляется с помощью гидропласта через тонкостенную втулку. Установка приспособления на заданный размер осуществляется при помощи эталонного образца.
Надежность и правильность работы гидрооправки зависит от правильной конструкции и размеров центрирующей втулки и плунжера. Принцип действия приспособления с гидрорпластмассой основан на равномерной передаче давления гидропластмассы на центрирующие и зажимные элементы приспособления.
Расчет сводится к расчету центрирующей втулки.
Исходные данные для расчета:
Д=80+003 – диаметр базовой поверхности в мм.
t – толщина тонкостенной части втулки в мм.
lp =18 – длина тонкостенной части втулки в мм.
Т=4 – толщина опорных поясков в мм.
tk=6 - толщина втулки в мм.
DS – наибольший зазор между базовой поверхностью втулки и замеряемой деталью.
d - диаметральный натяг между опорными поясками втулки и корпусом оправки.
р - давление гидропластмассы необходимое для деформации тонкостенной части центрирующей втулки.
lэф – длина контактной поверхности втулки в ее рабочем положении.
Величина DS выбирается из обязательного условия DSDД обеспечивающего точное центрирование.
Величина DД зависит от размера Д предела пропорциональности материала [sТ] (Е) для стали
где К - коэффициент запаса прочности равный отношению предела текучести к допускаемому напряжению при lp03Д К=2.
Максимально допустимое приращение диаметра втулки будет равно:
Толщина цилиндрической оболочки втулки:
где Д=80+003 DSDД 01050162.
Давление в полости втулки необходимое для установки и закрепления детали:
Сила действующая на плунжер:
Основные параметры тонкостенной втулки представлены на рис. 5.2.
Рис. 5.2. Параметры тонкостенной втулки.
Для получения внутренних резьб небольших диаметров применяется раскатник (бесканавочный метчик). Конструктивно раскатник имеет много общего с обычными метчиками. Основными отличительными чертами являются форма поперечного сечения и заборной части а также отсутствие стружечных канавок.
Метод получения внутренних резьб раскатником имеет ряд существенных преимуществ перед нарезанием:
стойкость инструмента в несколько раз выше;
отсутствует стружка что важно при получении резьбы в глухих отверстиях;
резьба не разбивается;
инструмент прочней более чем в 2 раза прочность на срез выше в среднем на 20%;
класс чистоты резьбы выше;
обеспечивается стабильное получение резьбы заданного класса чистоты и точности.
Для изготовления раскатников используют следующий материал: наиболее распространен Р18 но сейчас используют Р9К5 Р9Ф5 Р12 а для цветных металлов и сплавов – ХВГ или 9ХС. Изготовляем метчик – раскатник из стали Р18 ГОСТ 5955-85.
Расчет раскатника для резьбы М30.5 в деталях из алюминиевых литейных сплавов АК7ч.
Твердость обрабатываемого материала в среднем НВ 60 62;
Глубина резьбы 19 мм 7 мм и 5 мм;
Отверстия глухие и сквозные;
Скорость обработки V=6 ммин.
Предлагаемый метчик для образования резьбы в вязких материалах отличается тем что его стружечные канавки на заборном конусе имеют переменное сечении от вогнутого к выпуклому так что одна часть заборного конуса вырезает металл из впадин получаемой резьбы а вторая пластически деформирует оставшийся металл по заданным размерам.
Метчик состоит из заборного конуса и калибрующей части. Сечение заборного конуса на участке а (Б-Б) меняется от вогнутого к выпуклому на участке б сечения (А-А).
Калибрующая часть С по форме подобна сечению А-А.
Заборный конус метчика выполняет основную работу по резьбонарезанию:
- участок заборного конуса а сечения Б-Б имеет форму сечения обычного метчика а участок конуса б (2-3 нитки) пластически деформирует оставшийся металл по заданным профилю размерам так как его сечение А-А имеет форму сечения резьбового раскатника. Затылование f по наружному диаметру заборного конуса на участке а выполняется как у обычных метчиков. Рис 5.3.
Основные допуски и размеры регламентированы ГОСТ 9159-59 и 16093-70 и соответствуют:
-средний диаметр d2= 7263-001 мм отклонения среднего диаметра: нижнее –001 мм верхнее мм допуск ;
- внутренний диаметр d1=6699-005 мм отклонения: нижнее –005 мм верхнее 0 мм допуск на изготовление =005 мм
- наружный диаметр d=8 мм верхний предельный размер не регламентируется.
Исполнительные размеры. Средний диаметр рассчитывается по формуле:
где - допуск на средний диаметр резьбы;
- допуск на изготовление среднего диаметра раскатника;
- коэффициенты учитывающие изменения усадки от свойств обрабатываемого материала и шага резьбы. Для принятия условий ;
-выбирают конструктивно ориентируясь по следующей зависимости:
Наружный диаметр подсчитываем по формуле:
где d- номинальный диаметр резьбы;
- допуск на изготовление наружного диаметра принимаем как для метчика М8125 т.е..
При получении резьбы в деталях из алюминиевых сплавов раскатник следует выполнять с ограничением впадины резьбы по dвн. Ширина площади по внутреннему диаметру раскатника подсчитывается по формуле:
где - половина угла профиля резьбы;
- допуск на изготовление площади .
Рассчитанный диаметр отверстия под резьбу вычисляем по формуле:
Так как процесс раскатывания резьбы осуществляется по принципу замкнутого контура то диаметр отверстия будет наибольшим допустимым значением для условий работы т.е. . Наименьший диаметр отверстия:
где - допуск на подготовку отверстия для алюминиевых сплавов
Диаметр сверла можно принять равным 72 мм. Число граней принимаем z=3 в качестве затыловочной кривой – спираль Архимеда. Угол спада кривой на вершинах граней следует назначать в пределах 5-7о принимаем . Полная величина спада кривой k на одной грани должна рассчитываться по формуле:
Величина k необходима для проверки прочности переходного витка.
Заборный конус переходная калибрующая часть.
Принимаем форму заборной части в виде конической резьбы с полным профилем. Исходя из условия прочности переходной нитки и универсальности раскатников угол наклона заборного конуса . Для глухих отверстий длина заборной части должна быть возможно меньше для повышения общей стойкости раскатника. Длина рассчитывается по формуле:
где - диаметр переднего торца который вычисляется как
Длина калибрующей части .
Общая длина рабочей части раскатника
После первых четырех витков калибрующей части целесообразно уменьшить средний и внутренний диаметры резьбы на 003 –005 мм.
Это позволяет уменьшить величину примерно на 30%.
Прочность поперечного сечения раскатника определяется по формуле:
См- коэффициент характеризующий материал обрабатываемой детали См=10;
Кк- коэффициент учитывающий наличие у раскатника смазочных канавок Кк=1;
Ко – коэффициент зависящий от вида применяемой СОЖ Ко=152. Принимаем Ко =2.
При раскатывании замкнутого контура Мкр увеличивается в 3-4 раза. Момент сопротивления раскатника при кручении:
Максимальное касательное напряжение при кручении в сечении раскатника:
Сравнивая с пределом прочности при кручении быстрорежущей стали Р18 получим что раскатник имеет запас прочности:
Основные конструктивные элементы метчика-раскатника показаны на рисунке 5.3
Рис. 5.3. Конструктивные элементы метчика-раскатника
Охрана труда - это система законодательных актов и норм направленных на обеспечение безопасности труда и соответствующих им социально-экономических организационных экологических и санитарно-гигиенических мероприятий.
Главная задача в области охраны труда в настоящий период заключается в максимальном устранении опасных и вредных производственных факторов уменьшения численности работающих в этих условиях создания здоровых безопасных условий труда не рабочих местах и на этой основе добиться снижения профессиональной заболеваемости и производственного травматизма. Обеспечение безопасности труда в дипломном проекте реализуется путем создания прогрессивной технологии. Безопасность труда при выполнении операций техпроцесса обеспечивается соблюдением стандартов по безопасности труда правил по технике безопасности санитарных норм и правил инструкций по охране труда. Улучшение условий труда повышение его безопасности влияет на производительность труда качество и себестоимость выпускаемой продукции.
1. Анализ проектируемого участка и влияние вредных производственных факторов
Проектируемый участок является частью механического цеха по производству корпусных деталей. Производство в данном проекте средне-серийное. На участке производится механическая обработка литых заготовок корпуса из сплава AК7ч. Годовая программа выпуска корпуса – 10000 штук.
Технологический процесс механической обработки ведется на следующих типах металлорежущих станков:
Токарный станок с ЧПУ –модель АТПР 2М-12;
Вертикально-фрезерный станок с ЧПУ- модельФП-4;
Многоцелевой станок с ЧПУ –модель МС 12-250;
Координатно-сверлильный станок с ЧПУ–модельКС 12-500;
Токарный п а модели 1А240П;
Электрохимическая установка.
Станки оснащены специальными быстродействующими зажимными приспособлениями что облегчает труд основных производственных рабочих. Станки и оборудование должны отвечать требованиям ГОСТ 12.2.009-80
ГОСТ 12.2.027-80 ГОСТ 12.2.003-74 а при работе на станках следует руководствоваться ГОСT12.3.025—80 и "Правилами техники безопасности и производственной санитарии при холодной обработке металлов".
Все металлорежущие станки установлены на прочных основаниях тщательно выверены закреплены заземлены и окрашены в соответствии с требованиями ГОСТ 12.4.026-76. Работать на станках разрешается только лицам за которыми они закреплены.
Все механизмы станков ограждаем предохранительными устройствами. Станки снабжены прочным стеклом устанавливаемым между рабочим инструментом и лицом станочника для защиты его глаз. Эти приспособления сблокированы с пусковым устройством станка. При отсутствии предохранительных устройств станочники должны работать в очках.
Станок следует обязательно выключать в случае прекращения подачи тока при смене инструмента закреплении или установке детали при ремонте чистке смазке станка уборке стружки.
Рабочее место станочник должен содержать в чистоте и не загромождать изделиями и материалами. На рабочих местах должны быть вывешены инструкции по технике безопасности. Стружка удаляется со станка крючками и щетками. Убирать стружку руками запрещено. При работе станочники пользуются спецодеждой.
При работе на токарных станках:
) включать сначала вращение шпинделя а затем подачу;
) периодически проверять осевой нажим создаваемый центром задним;
) при обработке детали напильником необходимо отвести резец на безопасное расстояние;
) ручку напильника следует держать левой рукой а его конец правой;
) запрещается измерять обрабатываемую деталь на ходу.
) не допускается торможение патрона рукой.
При работе на сверлильных станках;
)станки оснащены устройствами предупреждающими самопроизвольное торможение траверсы;
)обеспечивается надежный зажим сверла в патроне центрирование;
)запрещается работать в рукавицах;
)запрещено удерживать деталь руками;
) не допускается использование инструментов с изношенными конусами.
При работе на фрезерных станках;
) при установке хвостовика инструмента в шпиндель следует убедиться в том что он сел плотно без люфта;
) чтобы избежать поломки зубьев фрезы направление вращения фрезы и направление подачи должны быть встречными;
) запрещается вводить руки в опасную зону вращения фрезы.
К вредным и опасным производственным факторам можно отнести:
Возможность механического травмирования в процессе складирования и транспортировки так как заготовка является габаритной. Требуется применение специальной тары при транспортировке в процессе механической обработки.
Возможность поражения электрическим током на токоведущих проводах и частях станка при несоблюдении правил и норм электробезопасности и ГОСТ 12.1.030-82 предельно допустимых напряжений ГОСТ 12.1.038-82.
При обработке на станках с ЧПУ возможен сбой станков в работе ввиду разрыва перфоленты и т.д. Необходимо следить за сменой инструмента и работой станка. Смену заготовки необходимо производить с соблюдением правил техники безопасности.
При обработке на станках происходит дробление стружки что может привести к механическим повреждениям глаз. Необходимо пользоваться защитными очками или применять защитный экран.
При использовании в производстве СОЖ возникают вредные воздействия на органы дыхания кожный покров. Для улучшения свойств СОЖ и уменьшения вредных воздействий используются присадки. Чтобы не загнивала СОЖ вводятся бактерицидные добавки - 015 % .
2.Мероприятия по промсанитарии и гигиене труда
Метеорологические условия или микроклимат в производственных помещениях на участке определяется параметрами выбор которых зависит от категории тяжести выполняемых работ. По ГОСТ 12.1.005-88 – работы выполняемые в цехе и на участке относятся к разряду средней тяжести физических работ. Этой категории соответствуют показатели микроклимата которые поддерживаются в помещении средствами отопления и вентиляции:
Температура окружающего воздуха в холодный период +210 +230С в теплый период +220 +240С.
Относительная влажность воздуха допустимая в холодный период года не более 75% в теплый период –62%.
Скорость движения воздуха допустимая в теплый период года 01-03 мс.
Система вентиляции на проектируемом участке является общеобменной по способу перемещения воздуха и механической. Место расположения воздуховодов выбрано с учетом максимального использования их возможностей из расчета того чтобы трубы вентиляции не мешали выполнению техпроцесса и транспортировки деталей.
Коммуникации системы вентиляции расположены на высоте 35 4 м от уровня пола. Применяются вентиляторы низкого давления типа МЦ и ЦЗ-04.
Освещение производственного участка осуществляется с помощью естественного и искусственного освещения. Естественное освещение участка осуществляется как через боковые проемы в стенах так и через верхние проемы. Искусственное освещение выполняется по комбинированной системе когда к общему освещению добавляется местное.
В соответствии с СН и П 4-79 и отраслевыми нормами искусственного освещения предприятий для механических цехов установлена освещенность в пределах зрительного разряда работы IIВ 2000 лк - 500 лк для комбинированного и общего освещения принимаем лампы люминесцентные
Местное освещение для контролеров – лампы типа ЛДЦ-80 для наладчиков операторов и станочников принимаем лампы накаливания типа
Г-215-225-150 светильники НСП-07.
4 Охрана окружающей среды
На данном участке для защиты окружающей среды от вреда выбросов таких как пыль переработанная СОЖ ветошь стружка принять следующие меры:
Пыль - перед тем как воздуху вместе с примесями выйти в атмосферу он проходит через фильтроуловители в которых остается до 80% примесей.
СОЖ - после отработки отправляется на участок по переработке и добавке свежей примеси.
Ветошь - собирается в тару и вывозится на свалку.
Стружка - брикетируется и отправляется на переработку.
5. Защита от шума и вибрации
На проектируемом участке присутствуют механические шумы связанные с технологическими операциями и с работой оборудования. Уменьшение шума достигается своевременным обслуживанием оборудования заменой изношенных механизмов. ПДК - 85 дБ. При спектре частот f = 1000 Гц. ПДК допускается в следующих пределах для видов работ:
сверлильных и фрезерных 85 2 дБ;
Защита от вибраций заключается в том что все оборудование расположено на отдельных фундаментных подушках и на допустимом расстоянии друг от друга.
Нормы вибрации стандартизованы ГОСТ 12.1.012-78. Шум на производстве регламентируется ГОСТ 12.1.003-76.
Уровень вибрации возникающей на проектируемом участке ниже норм установленных ГОСТ 12.1.072-78 благодаря использованию виброгасящих мероприятий при установке станков (фундамент виброподушки). В цехе для производственных рабочих и служащих предусматривается установка фонтанчиков с питьевой водой. В цехе имеются бытовые помещения с раздевалкой и душевой.
6.Мероприятия по технике безопасности
Требования безопасности предъявляемые к оборудованию определены ГОСТ 12.2.009-80. Основными требованиями охраны труда которые предъявляются к металлорежущим станкам являются:
-безопасность для человека;
-надежность и работоспособность;
-удобство в эксплуатации.
Безопасность производственного оборудования на проектируемом участке обеспечивается путем применения защитных экранов. Защитные ограждения имеют место при обработке заготовок от подвижной части оборудования. Все движущие части оборудования окрашены в цвета по ГОСТ 12.4.026-76.
Воздух загрязненный вредными примесями удаляется вентиляцией местного отсоса. При транспортировке тяжелых приспособлений используется ручная тележка. С целью исключения несчастного случая в рабочей зоне имеются защитные щитки с кольцевыми выключателями ГОСТ 12.2.009-80.
Все станки оборудованы системой аварийного отключения (кнопка красного цвета) установленной в легкодоступной части и обеспечивающей отключение электрооборудования независимо от режима его работы. Обеспечение спецодеждой и средствами индивидуальной защиты производится согласно действующему положению. Рабочие не прошедшие инструктаж по технике безопасности к работе не допускаются.
Электробезопасность.
Основными нормами защиты человека от поражения электрическим током на участке являются:
a)средства обеспечивающие недоступность токоведущих частей от случайного соприкосновения. Согласно правил устройства электроустановок (ПУЭ-76) распределительные и осветительные токопроводы оборудованы ограждениями предохраняющими от возможности случайного прикосновения и расположена на высоте 25 метра от уровня пола в производственных помещениях. В местах где токопроводы могут подвергаться механическим повреждениям они имеют специальную защиту.
в) применение малого напряжения для питания светильников местного освещения переносных ламп приборов настройки инструментов используется напряжение 36 В.
с) Защитное заземление. Для всех станков и их комплектов применяют выносное заземление расположенное за пределами здания по ГОСТ 12.1.030-81.
Постоянное обслуживание и ремонт электроустановок предусматривается производить специально обученным электротехническим персоналом.
В данном дипломном проекте использованы достижения современной техники:
Использовано современное автоматизированное оборудование: станки с ЧПУ применяются оптимальные режимы резания что влияет на повышение производительности труда.
Для повышения производительности обработки на операцию 040 было разработано быстродействующее зажимное станочное приспособление.
Для получения более качественной резьбы был разработан режущий инструмент метчик - раскатник. Для накатывания резьбы в сквозных отверстиях на операции 045 используем метчик - раскатник с направляющей частью.
Разработанное контрольное приспособление позволяет уменьшить время на проверку точности изготовления детали.
В целом при разработке технологического процесса быстродействующих зажимных приспособлений инструмента и выбора оборудования учитывались реальные возможности и потребности производства с целью возможного внедрения дипломного проекта на предприятии.
В результате проведенных работ получен годовой экономический эффект 412346 рублей и срок окупаемости 037 года.
Горбацевич А.Ф. Шкред В.А. Курсовое проектирование по технологии машиностроения. Минск «Высшая школа» 1983.
Справочник технолога- машиностроителя. В. 2-х т. Т.12Под ред. А.Г. Косиловой и Р.К. Мещерякова.- 4-е изд. перераб. и доп. – М.: Машиностроение 1986 496с.
Аршинов В.А. Алексеев Г.А. Резание металлов и режущий инструмент. Изд. 3-е перераб. и доп. Учебник для машиностроительных техникумов. М.: «Машиностроение» 1976г.
Нефедов Н.А. Осипов К.А. Сборник задач и примеров по резанию металлов и режущему инструменту: Учеб. пособие для техникумов по предмету «Основы учения о резания металлов и режущий инструмент».5-е изд. перераб. и доп. – М.: «Машиностроение» 1990 448с.
Афонькин А.Р. Проектирование заготовок. М.: «Машиностроение» 1999г
Рязанцев С.И. Методические указания по дипломному проектированию для студентов специальности Ижевск ИМИ.
Общемашиностроительные нормативы времени и режимов резания на работы выполняемые на металлорежущих станках с программным управлением. М.: НИИ 1980.
Общемашиностроительные нормативы режимов резания для технического нормирования работ на металлорежущих станках. Ч.1.Токарные карусельные токарно-револьверные станки алмазно-расточные сверлильные строгальные долбежные и фрезерные станки. – М.: «Машиностроение» 1990 448с.
Безопасность жизнедеятельности. Безопасность технологических процессов и производств (Охрана труда): учебное пособие для вузов п.п. Кукин В.л. Лапин Е.а. Подгорных и др. – М.: Высшая школа 1999. –318с.
Общемашиностроительные нормативы вспомогательного времени и времени на обслуживание рабочего места на работы выполняемые на металлорежущих станках. М.:«Машиностроение» 1971г
КорсаковВ.С.Основы конструирования приспособлений в машиностроении М.:«Машиностроение» 1971г
Горошкин А.Н. Приспособления для металлорежущих станков. Справочник. М.:«Машиностроение» 1986г
Якушев А.И. и другие. Взаимозаменяемость стандартизация и технические измерения. М.:«Машиностроение» 1986г
ЕгоровМ.Е. Основы проектирования машиностроительных предприятий. – – М.: «Машиностроение» 1969г.
Технологичность конструкций. Под редакцией С.Л.Ананьева В.П.Купревича – М.: «Машиностроение» 1990г
Режимы резания металлов. Справочник. Под ред.Ю.В.Барановского
– М.: «Машиностроение» 1972г.
Геваркян А. M. "Экономика и организация производства в дипломных проектах по технологическим специальностям". М. "Высшая школа". 1982 г.
спецификация13.dwg

Винт М8х12 ГОСТ Р 11738-84
Винт М10х40 ГОСТ Р 11738-84
Винт М12х30 ГОСТ Р 11738-84
Гайка М10 ГОСТ 5915-70
Гайка М20 ГОСТ 12460-67
Заклепка В 5х12 ГОСТ 10299-80
Проходник прямой ГОСТ 13959-74
Штифт 6х20 ГОСТ 13128-70
Штифт 10х20 ГОСТ 13128-70
оп055(э)и.dwg

технологической установкой поверхностей за
68-66 ГОСТ 3.1105-84 Форма 8
оп035(э).dwg

оп040(1).dwg

Наименование операции
Обозначения программы
ГОСТ 3.1404-88 Форма 3
Установить и закрепить заготовку
АБВГххх.ххх Приспособление с пневмозажимом
Сверлить и зенкеровать отверстие
выдерживая размеры 1
Укринoл 1м ТУ3810197-82
АБВГххх.ххх Фаскомер
Многоцелевой станок с ЧПУ мод МС12-250
Сверлить отверстия 3 и 4
выдерживая размеры 5
м003....dwg

хххххх.хххЭлектрохимическая
хххххх.хххТокарный па
хххххх.ххх Контрольный стол
хххххх.ххх Координатно-
мод. КС12-500 2 ххххх 3 1 1 1 3
ГОСТ 3.1502-85 Форма2
наименование оборудования СМ Проф Р УТ КР КОИД ЕН ОП Кшт Тп. з. Тшт.
А ххх ххх ххх 050 Многоцелевая
А ххх ххх ххх 055 Токарная
А ххх ххх ххх 060 Токарная
А ххх ххх ххх 065 Слесарная
А ххх ххх ххх 070 Контрольная
Инструкция ОТ № 101-81
оп020(э).dwg

оп025(1).dwg

АБВГххх.ххх Калибр 44
АБВГххх.ххх Калибр 151
станок с ЧПУ мод М С 12-250
Наименование операции
Обозначения программы
ГОСТ 3.1404-88 Форма 3
Установить и закрепить заготовку
АБВГххх.ххх Приспособление
Фрезеровать плошадку
выдерживая размеры 1
Укринол 1м ТУ3810197-82
оп035(э)и.dwg

000....dwg

Наименование технологического процесса
Наименование детали (сборочной единицы)
Обозначение детали (сборочной единицы)
ТЕХНОЛОГИЧЕСКИЙ ПРОЦЕСС
механической обработки
оп025(э).dwg

оп010(1)....dwg

Обозначения программы
ГОСТ 3.1404-88 Форма 3
Токарный па мод. АТПР2М12У
Установить и закрепить заготовку
АБВГххх.ххх Планшайба с гидравл. зажимом
выдерживая размеры 1
АБВГххх.ххх Резец подрезной ВК8 2122-0053 ГОСТ18800-73
АБВГ хххххх.ххх Штангенциркуль ШЦ I-125-0.1 ГОСТ 166-89
Укринол 1м ТУ3810197-82
оп015(э).dwg

оп045(1).dwg

Координатно-сверлильный стано
к с ЧПУ мод МС12-250
АБВГххх.ххх Сверло - зенкер
Наименование операции
Обозначения программы
ГОСТ 3.1404-88 Форма 3
Установить и закрепить заготовку
АБВГххх.ххх Приспособление
Сверлить и зенкеровать отверстие
выдерживая размеры 1
Укринoл 1м ТУ3810197-82
АБВГххх.ххх Фаскомер
Сверлить и зенкеровать отверстия
выдерживая размеры 3
оп060(э)и.dwg

оп005( э ).dwg

оп005(1)....dwg

Обозначения программы
ГОСТ 3.1404-88 Форма 3
Установить и закрепить заготовку
АБВГххх.ххх З-х кулачковый патрон с гидравл. зажимом
Токарный па мод. АТПР2М12У
выдерживая размеры 1
Укринол 1м ТУ3810197-82
АБВГххх.ххх Резец подрезной ВК8 2122-0053 ГОСТ18800-73
выдерживая размеры 4
оп010( э ).dwg

оп020(2).dwg

ГОСТ 3.1404-86 Форма 2а
выдерживая размеры 1
АБВГххх.ххх Резец расточной 2454-4112 ГОСТ18883-79
оп015(2).dwg

АБВГххх.ххх Калибр 7
АБВГххх.ххх Калибр 14
ГОСТ 3.1404-86 Форма 2а
выдерживая размеры 7
АБВГххх.ххх Резец фасонный ВК8
выдерживая размеры 4
оп040(э)и.dwg

м002....dwg

АБВГ хххххх.ххх Многоцелевой
станок с ЧПУ мод МС12-250 2 ххххх 4 1 1 1 6
Б АБВГ хххххх ххх Многоцелевой
станок с ЧПУ мод МС 12-250
АБВГ хххххх ххх Вертикально-
фрезерный станок с ЧПУ мод.ФП-4
фрезерный станок с ЧПУ мод ФП-4
АБВГ хххххх.ххх Координатно-
мод. КС12-500 2 ххххх 3 1 1 1 5
ГОСТ 3.1502-85 Форма2
наименование оборудования СМ Проф Р УТ КР КОИД ЕН ОП Кшт Тп. з. Тшт.
А ххх ххх ххх 025 Фрезерная
А ххх ххх ххх 030 Фрезерная
А ххх ххх ххх 035 Фрезерная
А ххх ххх ххх 040 Многоцелевая
А ххх ххх ххх 045 Сверлильная
Инструкция ОТ № 12-32
Инструкция ОТ № 12-81
Инструкция ОТ № 131-81
оп045(2).dwg

выдерживая размер 4.
АБВГххх.ххх Резец проходной Т15К6 2120-0053 ГОСТ 18700-73
АБВГххх.ххх Фаскомер
оп030( э ).dwg

оп015(1)...исправлен.dwg

АБВГххх.ххх Калибр 279
АБВГххх.ххх Скоба 11
АБВГххх.ххх Калибр 7
Наименование операции
Обозначения программы
ГОСТ 3.1404-88 Форма 3
Укринол 1м ТУ3810197-82
Установить и закрепить заготовку
АБВГххх.ххх Планшайба с гидравл. зажимом
выдерживая размеры 1
АБВГххх.ххх Резец подрезной ВК8 2122-0053 ГОСТ18800-73
выдерживая размеры 2
АБВГххх.ххх Резец подрезной ВК8 2141-0074 ГОСТ2269-89
Токарный па мод.АТПР2М12У
оп055(э).dwg

технологической установкой поверхностей за
68-66 ГОСТ 3.1105-84 Форма 8
оп015( э ).dwg

оп055(1).dwg

Обозначения программы
ГОСТ 3.1404-88 Форма 3
Установить и закрепить заготовку
АБВГххх.ххх З-х кулачковый патрон с гидравл. зажимом
Токарный па мод.АТПР2М12У
выдерживая размеры 2
Укринoл 1м ТУ3810197-82
АБВГххх.ххх Резец подрезной ВК8 2122-0053 ГОСТ18800-73
выдерживая размеры 1
АБВГххх.ххх Резец расточной Т15К6 2102-0053 ГОСТ18800-73
оп040(2).dwg

АБВГххх.ххх Метчик- раскатник М3 Р6М5
выдерживая размеры 3
АБВГххх.ххх Пробка резьбовая М3
выдерживая размеры 4
выдерживая размер 13
АБВГххх.ххх Фаскомер
оп005(2)....dwg

АБВГххх.ххх Скоба 12
ГОСТ 3.1404-86 Форма 2а
выдерживая размеры 2
АБВГххх.ххх Резец расточной ВК8 2102-0071 ГОСТ18817-73
выдерживая размеры 3
АБВГ хххххх.ххх Штангенциркуль ШЦ I-125-0.1 ГОСТ 166-89
оп040(э).dwg

оп030(э).dwg

оп020(1).dwg

Наименование операции
Обозначения программы
ГОСТ 3.1404-88 Форма 3
Установить и закрепить заготовку
АБВГххх.ххх Планшайба с гидравл. зажимом
Токарный па мод.АТПР2М12У
выдерживая размеры 5
Укринол 1м ТУ3810197-82
АБВГххх.ххх Резец подрезной ВК8 2112-0051 ГОСТ18800-73
АБВГххх.ххх Резец подрезной ВК8 2141-0074 ГОСТ2269-89
выдерживая размеры 2
м001...dwg

Код ЕВ МД ЕН Н.расх.
КИМ Код заготовки Профиль и размеры КД МЗ
наименование операции Обозначение документа
А ххх ххх ххх 005 Токарная с ЧПУ АБВГ.60140 ххх;
Инструкция ОТ № 101-81
ГОСТ 3.1502-85 Форма2
наименование оборудования СМ Проф Р УТ КР КОИД ЕН ОП Кшт Тп. з. Тшт.
Токарныйс ЧПУ АТПР2М12 2 18238 3 1 1 1 2.99
Инструкция ОТ № 131-81
АБВГхххххх.хххТокарный с ЧПУ АТПР2М12
АБВГхххххх.ххх Токарный с ЧПУ АТПР2М12
оп060(э).dwg

оп050(1).dwg

Координатно-сверлильный станок
АБВГххх.ххх Метчик - раскатник М6
Наименование операции
Обозначения программы
ГОСТ 3.1404-88 Форма 3
Установить и закрепить заготовку
АБВГххх.ххх Приспособление
Сверлить отверстия под резьбу
выдерживая размеры 1
Укринoл 1м ТУ3810197-82
выдерживая размеры 1
АБВГххх.ххх Пробка резьбовая М6
оп015(2)....dwg

АБВГххх.ххх Калибр 7
АБВГххх.ххх Калибр 14
ГОСТ 3.1404-86 Форма 2а
выдерживая размеры 7
АБВГххх.ххх Резец фасонный ВК8
выдерживая размеры 4
оп030(1).dwg

АБВГххх.ххх Шаблон 60
АБВГххх.ххх Скоба 40
Вертикально-фрезерный станок с ЧПУ мод ФП-4
Наименование операции
Обозначения программы
ГОСТ 3.1404-88 Форма 3
Установить и закрепить заготовку
АБВГххх.ххх Приспособление с гидроприводом
Фрезеровать уступы последовательно на пяти лапах
выдерживая размеры 1
Укринол 1м ТУ3810197-82
оп050(э).dwg

оп010(э).dwg

оп020( э ).dwg

оп050(э)и.dwg

оп005(э).dwg

оп035(1).dwg

АБВГххх.ххх Калибр 4
Вертикально-фрезерный станок с ЧПУ мод ФП-4
Наименование операции
Обозначения программы
ГОСТ 3.1404-88 Форма 3
Установить и закрепить заготовку
АБВГххх.ххх Приспособление
Фрезеровать канавку по контуру
выдерживая размеры 1
Укринoл 1м ТУ3810197-82
оп045(э).dwg

оп060(1).dwg

Обозначения программы
ГОСТ 3.1404-88 Форма 3
Установить и закрепить заготовку
АБВГххх.ххх З-х кулачковый патрон с гидравл. зажимом
Токарный па мод.АТПР2М12У
выдерживая размеры 2
Укринoл 1м ТУ3810197-82
АБВГххх.ххх Резец подрезной Т15К6 2122-0057 ГОСТ18800-73
выдерживая размеры 1
АБВГххх.ххх Резец расточной Т15К6 2102-0053 ГОСТ18800-73
спецификация11.dwg

Болт М8х30 ГОСТ 7808-70
Винт М6х20 ГОСТ Р 11738-84
Винт М16х30 ГОСТ Р 11738-84
Винт М6х40 ГОСТ Р 11738-84
Гайка М12 ГОСТ 5915-70
Гайка М60 ГОСТ 5915-70
Подшипник ГОСТ 8338-75
Ручка 120х100 ГОСТ 8921-69
Мембрана 160х5 ГОСТ 9887-85
Уплотнения О12 ГОСТ 9833-73
Уплотнения 017-016-25
Уплотнения 074-080-46
Цилиндр ГОСТ 15608-70
спецификация2.dwg

Винт М8х12 ГОСТ Р 11738-84
Винт М10х40 ГОСТ Р 11738-84
Винт М12х30 ГОСТ Р 11738-84
Гайка М10 ГОСТ 5915-70
Гайка М20 ГОСТ 12460-67
Заклепка В 5х12 ГОСТ 10299-80
Проходник прямой ГОСТ 13959-74
Штифт 6х20 ГОСТ 13128-70
Штифт 10х20 ГОСТ 13128-70
Планировка1.dwg

участка по производству
корпуса токосъёмника
Наименование оборудования
Вертикально-фрезерный с ЧПУ
Координатно-сверлильный с ЧПУ
Установка электрохимическая
л11-тех-эк показ1.dwg

Проект механического
участка по производству
корпуса токосъемника
Годовой выпуск деталей
нагрузки оборудования
Численность всех рабочих
Численность основных
производственных рабочих
Средне-месячная зарплата
одного производственного
Капитальные затраты на
Технико-экономические
Цеховая себестоимость
себестоимости детали
Годовой экономический
механического участка по производству
Станочное приспособление1.dwg

Рабочее давление воздуха в пневмосети 0
Усилие зажима на штоке 102
клепать заклепками поз. 25.
Сборка1.dwg

л4-технолог наладка1.dwg

ОБОРУДОВАНИЕ ТОКАРНЫЙ ПОЛУАВТОМАТ с ЧПУ модели АТПР-2М-12
ОПЕРАЦИЯ 020 ТОКАРНАЯ с ЧПУ
Наладка1.dwg

ОБОРУДОВАНИЕ МНОГОЦЕЛЕВОЙ СТАНОК с ЧПУ модели МС12-250
л8-раскатники резьбовые1.dwg

тка по производству
корпуса токосьёмника
Сталь Р6М5 ГОСТ 5952-85
Закалить: режущую часть 62 65 HRCэ
хвостовую часть 40 45 HRCэ
направляющую часть 50 55 HRCэ
Допуск на шаг между любыми 2 нитками равен
относительно d не более -0
Центровые отверстия тип В по ГОСТ 14034-74
Маркировать: диаметр метчика
завода изготовителя.
л5-технолог наладка1.dwg

ОБОРУДОВАНИЕ МНОГОЦЕЛЕВОЙ СТАНОК с ЧПУ модели МС12-250
л7-станочное приспособление1.dwg

участка по производтсву
корпуса токосъемника
*Размер для справок.
л3-размерный анализ1.dwg

Предельные отклонения
Контрольное приспособление1.dwg

Рабочее давление воздуха в пневмосети 0
Рабочий ход диафрагмы 10 мм
пневмоцилиндра - 75 мм
клепать заклепками поз. 34.
Смазка трущихся поверхностей осуществляется при сборке
смазкой ЦИАТИМ 221 ГОСТ 9433-80
л2-заготовка1.dwg

участка по производству
корпуса токосъемника
Неуказанные литейные уклоны по ГОСТ 3212-93
пустоты и другие неметаллические включения не
Термообработать по Т-4 ГОСТ 2685-83.
Неуказанные литейные радиусы R 3 мм.
Неуказанные предельные отклонения размеров отливки
по 3 классу точности ГОСТ 1855-85.
л6-технолог наладка1.dwg

тка по производству
корпуса токосьёмника
ОПЕРАЦИЯ №030 ФРЕЗЕРНАЯ с ЧПУ
ОБОРУДОВАНИЕ МНОГОЦЕЛЕВОЙ СТАНОК с ЧПУ модели МС12-250
Л1-деталь А11.dwg

Неуказанные литейные уклоны по ГОСТ 3212-93.
пустоты и другие неметаллические включения не
Деталь грунтовать и красить эмалью ЭП-140
Неуказанные предельные отклонения размеров отверстий по-
Рекомендуемые чертежи
- 24.01.2023
- 24.01.2023