Проект механического цеха по производству деталей типа тел вращения




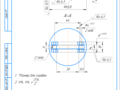
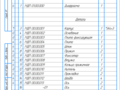
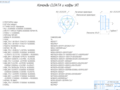
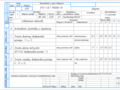
- Добавлен: 24.01.2023
- Размер: 1 MB
- Закачек: 0
Описание
Проект механического цеха по производству деталей типа тел вращения
Состав проекта
![]() |
![]() |
![]() |
![]() ![]() ![]() ![]() |
![]() ![]() ![]() ![]() |
![]() ![]() ![]() ![]() |
![]() ![]() ![]() ![]() |
![]() ![]() ![]() ![]() |
![]() |
![]() ![]() ![]() ![]() |
![]() ![]() ![]() ![]() |
![]() |
![]() ![]() ![]() ![]() |
![]() ![]() ![]() ![]() |
![]() ![]() ![]() ![]() |
![]() ![]() ![]() ![]() |
![]() ![]() ![]() ![]() |
![]() ![]() ![]() ![]() |
![]() ![]() ![]() ![]() |
![]() ![]() ![]() ![]() |
![]() ![]() ![]() ![]() |
![]() ![]() ![]() ![]() |
![]() ![]() ![]() ![]() |
![]() ![]() ![]() ![]() |
![]() ![]() ![]() ![]() |
![]() |
![]() ![]() ![]() ![]() |
![]() ![]() ![]() ![]() |
![]() ![]() ![]() ![]() |
![]() ![]() ![]() ![]() |
![]() ![]() ![]() ![]() |
![]() ![]() ![]() |
![]() ![]() ![]() ![]() |
![]() ![]() ![]() |
![]() |
![]() ![]() ![]() ![]() |
![]() ![]() ![]() ![]() |
![]() ![]() ![]() ![]() |
![]() ![]() ![]() ![]() |
![]() ![]() ![]() ![]() |
![]() ![]() ![]() ![]() |
![]() ![]() ![]() ![]() |
![]() ![]() ![]() ![]() |
![]() ![]() ![]() ![]() |
![]() ![]() ![]() ![]() |
![]() ![]() ![]() ![]() |
![]() ![]() ![]() ![]() |
![]() ![]() ![]() ![]() |
![]() ![]() ![]() ![]() |
![]() ![]() ![]() ![]() |
![]() ![]() ![]() ![]() |
![]() ![]() ![]() ![]() |
![]() ![]() ![]() ![]() |
![]() ![]() ![]() ![]() |
![]() ![]() ![]() ![]() |
![]() ![]() ![]() ![]() |
![]() ![]() ![]() ![]() |
![]() ![]() ![]() ![]() |
![]() ![]() ![]() ![]() |
![]() ![]() ![]() ![]() |
![]() ![]() ![]() ![]() |
![]() ![]() ![]() ![]() |
![]() ![]() ![]() ![]() |
![]() ![]() ![]() ![]() |
![]() ![]() ![]() ![]() |
![]() ![]() ![]() ![]() |
![]() ![]() ![]() ![]() |
![]() ![]() ![]() ![]() |
![]() |
![]() ![]() ![]() |
![]() ![]() ![]() |
![]() ![]() ![]() |
![]() ![]() ![]() |
![]() ![]() ![]() |
![]() ![]() ![]() |
![]() ![]() ![]() |
![]() ![]() ![]() |
![]() ![]() ![]() |
![]() |
![]() ![]() ![]() ![]() |
![]() ![]() ![]() |
Дополнительная информация
5ПОСЛЕД.cdw

внешними устройствами
Выдача УП в машинных
кодах непосредственно
движения инструмента
8ИСХОДНЫЕ ТОЧКИ.cdw

' - нулевые точки РО;
Б' - базовые точки РО;
- система координат детали (программы);
- система координат станка (расчетная);
- система координат инструмента (однокоординатная система);
П - базовая точка станочного приспособления;
Н - точка начала обработки;
- базовая точка инструмента.
Условие совмещения т.Б
с т.Н математически имеет следующий вид:
в расчетной системе координат станка:
Координаты т.Н в расчетной системе координат станка:
РО в исходные точки.
Методы выставления РО в исходные точки.
9ИСХОДНЫЕ ТОЧКИ.cdw

= 25+0+90-(-100)-200=15(мм)
Искомые координаты ссходных точек:
РО в исходные точки.
Методы выставления РО в исходные точки.
4CLDATA.cdw

ИНСТР1 ФРЕЗА РАДИУС=8.000000 КОР.ИН
ИДИ_ТОЧ-38.113549 37.840721 25.000000;
ИДИ_ТОЧ-38.113549 37.840721 16.000000;
ПОДАЧА30.000000 мммин;
ИДИ_ТОЧ-35.083247 41.817814 16.000000;
ИДИ_ОКР-32.810951 25.000065 16.000000
ИДИ_ОКР-38.056080 15.915234 16.000000
ИДИ_ТОЧ-5.245068 -40.915105 16.000000;
ИДИ_ОКР5.245190 -40.915105 16.000000
ИДИ_ТОЧ38.056206 15.915234 16.000000;
ИДИ_ОКР32.811073 25.000065 16.000000
ИДИ_ТОЧ-32.810951 25.000065 16.000000;
ИДИ_ОКР-44.810951 37.000065 16.000000
ИДИ_ТОЧ-39.810951 37.000065 16.000000;
N003G01X-001311Y+001284F4724*
N006X+000303Y+000397L805*
N007G02X+000473Y-000955I+000727J+000955L805*
N008G02X-000245Y-000727I+001200L805*
N009G03X-000525Y-000908I+003281J+002500L005*
N010G01X+003281Y-0005683*
N011G03X+000525Y-000033I+000525J+004092L005*
N012G03X+000525Y+000033J+004125L005*
N013G01X+003280Y+005683*
N014G03X-000525Y+000908I+003806J+001592L005*
N016G02X-001200Y+001200J+001200L805*
N017G50X+000500L005*
N018G01Z+000900F664*
N019X+001481Y-001199F4724*
Расчетная траектория
Фактическая траектория
Команды CLDATA и кадры УП.
3Т.ОБЪЕКТЫ.cdw

Корректор радиусный 5
Размер диаметр 16 мм
[КЭ][ТП] - конструктивный элемент
Технологический переход.
Формирование ТО [СТЕН][ФРЕЗ] для
программирования фрезерного уступа по контуру:
Расчет траектории инструмента [Процессор].
Моделирование обработки на экране [Моделирование]
Просмотр CLDATA [CLDATA]
Просмотр УП [Управляющая программа]
Запись УП на дискету.
Формирование последовательности технологических обьектов (ТО).
6СКОБА.cdw

Цементировать на глубину 0
В и Г оксидофатировать.
7РЕЗЕЦ.cdw

Материал державки - Сталь45
Профиль шлифовать по шаблону с точностью 0
Шероховатость поверхности В -
МДП9.spw

МДП3.cdw

МДП1.spw

МДП6.cdw

МДП7.cdw

МДП4.cdw

обрабатывать в сборе с корпусом МДП 00.00.001.
МДП2.cdw

обрабатывать в сборе с плитой фиксирующей
МДП5.cdw

МДП10.cdw

МДП8.cdw

МДП9.cdw

МДП1.cdw

Техническая характеристика.
Приспособление зажимное служит для закрепления втулки для
выполнения операции 040.
Давление воздуха подаваемое в штуцер В
Давление воздуха подаваемое в штуцер Г
Размеры для справок.
МДП11.cdw

17ЭКОНОМИЧЕСКОЕ.cdw

- условно - постоянные затраты базового и спроектированного технологического процессов.
- условно - переменные затраты базового и спроектированного технологического процессов.
- критическая программа выпуска изделий.
Экономическое обоснование
технологических процессов.
Экономическое обоснование выбора вариантов технологических процессов.
14СОПРОМАТ.cdw

11ЗАЖИМ.cdw

Механизм для автоматического зажима инструментов.
13ЦЕПИ.cdw

16КЛАССИФИКАЦИЯ.cdw

15ПОЛЯ ДОПУСКОВ.cdw

10ПЛАНИРОВКА.cdw

Вспомогательная площадь S
- токарно - винторезный 1К620.
- токарно - винторезный с ЧПУ 1К620Ф3.
- внутри - шлифовальный 3А252.
- вертикально - сверлильный 2А125.
- вертикально - фрезерный с ЧПУ 6А12П.
- кругло - шлифовальный 3180.
Fмех - площадь ремонтных баз механика.
Fэ - площадь ремонтных баз энергетика.
Fпр - площадь мастерской по ремонту приспособлений.
Fсб - площадь служебно-бытовых помещений.
Fз - площадь заточного отделения.
Fирк - площадь инструментально-раздаточных кладовых
Fк - площадь контрольного отделения.
Fпр.с - площадь промежуточного склада.
Fс.з. - площадь склада материала и заготовок.
Fм.с. - площадь межоперационного склада.
12ЭСП.cdw

18.cdw

12.cdw

11.cdw

Режущий и вспомогат.
Контроль-исполнитель с росписью в сопроводительной таре
Инструкция по технике безопасности ИОТ 07-07.011-02
Точить выточку по программе
Установить заготовку и закрепить.
4.cdw

Допускаемое смещение
Доп. на своб. размеры
КГТУ им.А.Н.Туполева
6.cdw

-х кулачковый патрон
Режущий и вспомогат.
Установить заготовку и закрепить.
Притупить острые кромки.
Контроль-исполнитель с росписью в сопроводительной таре
Инструкция по технике безопасности ИОТ 07-07.011-02
13.cdw

Режущий и вспомогат.
Контроль-исполнитель с росписью в сопроводительной таре
Инструкция по технике безопасности ИОТ 07-07.011-02
Точить фаску под углом
Установить заготовку и закрепить.
2.cdw

Наименование и содержание операции
Оборудование код. наименование
Вертикально-сверлильная
Вертикально-фрезерный с ЧПУ
15.cdw

Режущий и вспомогат.
Контроль-исполнитель с росписью в сопроводительной таре
Инструкция по технике безопасности ИОТ 07-07.011-02
Установить заготовку и закрепить.
28.cdw

3.cdw

Наименование и содержание операции
Оборудование код. наименование
10.cdw

5.cdw

9.cdw

Режущий и вспомогат.
Контроль-исполнитель с росписью в сопроводительной таре
Инструкция по технике безопасности ИОТ 07-07.011-02
29.cdw

Режущий и вспомогат.
Контроль-исполнитель с росписью в сопроводительной таре
Инструкция по технике безопасности ИОТ 07-07.011-02
Просушить сухим чистым
Промыть деталь в содохромпиковом
растворе по инструкции 16К05-633.
8.cdw

Режущий и вспомогат.
Контроль-исполнитель с росписью в сопроводительной таре
Инструкция по технике безопасности ИОТ 07-07.011-02
Установить заготовку и закрепить.
1.cdw

ТЕХНОЛОГИЧЕСКИЙ ПРОЦЕСС
механической обработки типовой
24.cdw

22.cdw

17.cdw

Наименование и марка материала
Режущий и вспомогат.
Контроль-исполнитель с росписью в сопроводительной таре
Инструкция по технике безопасности ИОТ 07-07.011-02
Установить заготовку и закрепить.
19.cdw

Режущий и вспомогат.
Контроль-исполнитель с росписью в сопроводительной таре
Инструкция по технике безопасности ИОТ 07-07.011-02
21.cdw

Режущий и вспомогат.
Установить заготовку и закрепить.
Контроль-исполнитель с росписью в сопроводительной таре
Инструкция по технике безопасности ИОТ 07-07.011-02
Фрезеровать заготовку по программе
31.cdw

14.cdw

27.cdw

Режущий и вспомогат.
Контроль-исполнитель с росписью в сопроводительной таре
Инструкция по технике безопасности ИОТ 07-07.011-02
Установить заготовку и закрепить.
Притупить острые кромки.
30.cdw

7.cdw

20.cdw

33.cdw

Наименование изделия. Марка материала.
Наименование оборудования
Втулка. ВТЗ-1 ОСТ190000-70
Контролируемые параметры
Наименование средств ТО
Технический контроль
Индикатор часового типа.
25.cdw

Режущий и вспомогат.
Контроль-исполнитель с росписью в сопроводительной таре
Инструкция по технике безопасности ИОТ 07-07.011-02
Шлифовать поверхность
Установить заготовку и закрепить.
16.cdw

23.cdw

Режущий и вспомогат.
Зачистить заусенцы после
Контроль-исполнитель с росписью в сопроводительной таре
Инструкция по технике безопасности ИОТ 07-07.011-02
32.cdw

Наименование изделия. Марка материала.
Наименование оборудования
Втулка. ВТЗ-1 ОСТ190000-70
Контролируемые параметры
Наименование средств ТО
Проверить внешний вид
Технический контроль
Проверить шероховатость
Эталоны шероховатости.
Скоба измерительная.
Спец приспособление.
26.cdw

1.ТЕХНОЛОГИЧЕСКАЯ ЧАСТЬ.doc
Темой дипломного проекта является проектирование цеха механической обработки по изготовлению деталей типа тел вращения. (Деталей типа «Втулка»).
В данном дипломном проекте при разработке ТП обработки детали «Втулка» внедрено передовое оборудование что улучшает труд рабочих уменьшает время на обработку и существенно снижает себестоимость детали.
При выполнении дипломного проекта будем базироваться и полагать что имеем серийный тип производства. Это производство характеризуется ограниченной номенклатурой и сравнительно большим объемом выпуска изделий изготовляемых периодически повторяющимися партиями.
Выполнение дипломного проекта служит не только комплексной проверкой учащегося к производственной работе в качестве инженера но и вместе с тем важнейшей формой и методом приобретения навыков самостоятельной работы.
Технологическая часть.
1АНАЛИЗ ИСХОДНЫХ ДАННЫХ ДЛЯ
Конструкция детали «Втулка» является технологичной. Т.к.
При переходе от изготовления одной детали к другой не требуется коренной переналадки технологического оборудования .
Используются небольшие припуски на обработку а следовательно высокий коэффициент использования материала.
Используется высокопроизводительное резание.
Используется совмещение обработки нескольких конструктивных элементов детали на одном станке за один установ.
Деталь «Втулка» отлита из титанового сплава ВТЗ-1 ОСТ 1900000-70 предназначенным для изготовления полуфабрикатов. Он имеет следующие физико - механические свойства и химический состав:
Предел прочности кгсмм ²:
при растяжении 45 – 120
пропорциональности 70 -85
Твердость НВ кгсмм ² 260 – 340
Модуль упругости кгсмм ² 11500
Модуль сдвига кгсмм ² 4300
Теплопроводность кал 0019
Химический состав ВТЗ-1%:
Примеси не более 1145
Из анализа чертежа детали видно что к ней предъявляются довольно высокие требования к точности и надежности.
Требования к отдельным поверхностям детали приведены в чертеже детали. Основное внимание здесь уделяется перпендикулярности параллельности и радиальному биению поверхностей.
На основании проведенного анализа можно сформулировать основные задачи которые необходимо решить при разработке технологического процесса для достижения заданных свойств детали:
Разработка технологического процесса с максимальным использованием и внедрением более современного экономически выгодного и автоматизированного оборудования и приспособлений.
В рамках создаваемого технологического процесса обеспечить требуемую точность и чистоту обработки поверхности детали.
Совмещать по мере возможности операции с целью уменьшения цикла обработки заготовки.
2 ВЫБОР ДЕЙСТВУЮЩЕГО ТИПОВОГО ГРУППОВОГО ТП ИЛИ ПОИСК АНАЛОГА ЕДИНИЧНОГОПРОЦЕССА.
В рамках дипломного проекта ТП разрабатывается на основе существующего ТП изготовления аналогичных деталей.
Разработка ТП осуществляется в зависимости от годовой программы выпуска изделий и принятого типа производства.
Для серийного производства необходимо ориентироваться на использование переменно – поточных линий когда последовательно изготовляются партии деталей одних наименований или размеров или групповых поточных линий когда параллельно изготавливаются партии деталей различных наименований.
Разработку этапов ТП будем осуществлять на основании
3 ВЫБОР ИСХОДНОЙ ЗАГОТОВКИ И МЕТОДОВ ЕЁ ИЗГОТОВЛЕНИЯ.
Для изготовления деталей машин применяются заготовки пяти видов: заготовки из проката; поковки и штамповки; отливки; заготовки изготовленные комбинированным способом; заготовки из металлокерамики пластмасс и других неметаллических материалов.
Исходя из технологических свойств материала ВТЗ – 1 ОСТ 1900000 – 70 требуемой точности выполнения заготовки; размеров детали программы выпуска деталей служебного назначения детали выбираем заготовку полученную штамповкой.
Поковки штампованные поставляются в термически обработанном состоянии. Они должны быть очищены от окалины травлением дробеструйным или иным методом. Допускаются местные дефекты в виде шлаковых включений закатов заковов а также трещин глубина которых не должна превышать половины номинального припуска на механическую обработку.
Трещины должны быть удалены зачисткой.
Выбор данного вида заготовки обусловлен тем что заготовка в виде штамповки имеет преймущества перед другими методами. Это выражается в получении в штамповке однородной структуры материала размеров наиболее близких к окончательным. При изготовлении заготовки методом штамповки лучше используется металл и уменьшается степень расхода.
Процесс изготовления штамповки требует малых затрат времени и менее квалифицированных рабочих.
Расчет допусков на размеры штампованных поковок по ГОСТ 7505-89.
Используемое оборудование – горячештамповочный пресс (КГШП).
Технологический процесс – открытая (облойная) штамповка.
Класс точности – Т4.
Степень сложности поковки определяется как отношение массы поковки к массе фигуры в которую вписывается поковка:
Gф = 4×S×ρ = 3144×600 (cм²)×45 = 021 (кг)
Степень сложности – С1
Поверхность разьема штампа – плоская (П).
Ориентировочная величина расчетной массы поковки:
К р = 18 – расчетный коэффициент.
М п.р. = 005 × 18 = 01 (кг)
Исходный индекс – 3.
Выбираем основные припуски на механическую обработку (на сторону).
9 и Ra 32 припуск равен 105 мм.
Размер 330 и Ra 125 припуск равен 10 мм.
Размер 230 и Ra 125 припуск равен 10 мм.
Размер 140 и Ra 125 припуск равен 10 мм.
Выбираем дополнительные припуски:
Смещение по поверхности разьема штампа – 05 мм.
Изогнутость и отклонение от плоскостности и прямолинейности – 08 мм.
Рассчитываем размеры поковки:
9 + (105 + 05) × 2 =410 (мм).
0 + (10 + 05) × 2 = 360 (мм).
0 + (10 + 05) × 2 = 260 (мм).
0 + (10 + 05) × 2 = 170 (мм).
Задаем допускаемые отклонения размеров:
Минимальная величина радиусов закруглений R = 16 мм.
Допускаемая величина остаточного облоя не более 06 мм.
Допускаемая величина заусенца не более 50 мм.
Величина штамповочных уклонов 7°.
4. ВЫБОР ТЕХНОЛОГИЧЕСКИХ БАЗ.
Технологические базы подразделяются на контактные настроечные и проверочные.
Выбор баз и порядок их смены связан с точностью операционных размеров формой детали техническими требованиями на деталь видом станочного оборудования приспособлений режущими и измерительными инструментами маршрутом обработки построением операций.
Разрабатываемый в дипломном проекте технологический процесс строится по
принципу дифференциации операций когда изготовление детали производится с помощью большого числа простых операций состоящих из одного-двух переходов осуществляемых одиночным инструментом.
В этом случае удобнее пользоваться контактными технологическими базами. (На универсальных станках.)
Выбор черновой базы во многом определяет дальнейший ход технологического процесса. Поэтому данный этап достаточно важный и необходимо придерживаться следующих рекомендаций:
Необходимо выбирать поверхности которые позволяли бы при первом установе заготовки провести черновую обработку большинства поверхностей и при этом обработать поверхности которые на следующем установе были бы промежуточными или чистовыми базами.
Важно чтобы черновая база имела достаточные размеры. Это необходимо для надежного крепления детали ибо при черновой обработке производится снятие значительного припуска.
Если с одной из обрабатываемых поверхностей снимается минимальный припуск то эта поверхность должна быть использована в качестве черновой базы.
В нашем случае в качестве черновой базы выбирается наружний диаметр и боковая поверхность .
Закрепление на первой операции обработки детали производится в 3-х кулачковый патрон. Для остальных операций технологического процесса технологические базы указаны в операционных картах.
При выборе промежуточных и чистовых баз придерживаемся принципов совпадения и постоянства баз.
5. СОСТАВЛЕНИЕ ТЕХНОЛОГИЧЕСКОГО МАРШРУТА ОБРАБОТКИ.
При разработке технологического маршрута для достижения заданных свойств детали необходимо учитывать следующие положения:
Учитывать рекомендации изложенные в разделе «Выбор технологических баз».
Выбрать минимальную себестоимость и трудоемкость маршрута обработки детали.
Выбрать методы обработки отдельных поверхностей пользуясь справочными данными экономической точности различных методов обработки.
Выбрать методы обработки сочетания поверхностей на которые заданы требования по точности их взаимного расположения (эксцентричности соосности перпендикулярности параллельности и т.п.).
Разбить процесс изготовления детали на стадии: черновую чистовую отделочную. Что позволяет более точно проявиться остаточным напряжениям в заготовке и уменьшает риск случайного повреждения окончательно обработанных поверхностей.
Каждая последующая операция должна быть точнее предыдущей она должна уменьшать погрешность и улучшать качество поверхности. При этом допуск на промежуточный размер и качество поверхности полученное на предыдущем этапе обработки должны находиться в пределах при которых можно использовать намечаемый последующий метод обработки.
Заканчивается процесс изготовления детали обработкой той поверхности которая должна быть наиболее точной и имеет наибольшее значение для эксплуатации детали.
Если деталь подвергается термической обработке то маршрут обработки разделяется на части: до термической обработки и после нее.
В маршрут технологического процесса включают и такие операции как снятие фасок зачистка заусенцев промывка детали контрольные операции операции термической обработки.
Разработанный технологический маршрут механической обработки записан на маршрутных картах и предоставлен отдельно от пояснительной записки.
6 РАЗРАБОТКА ТЕХНОЛОГИЧЕСКИХ ОПЕРАЦИЙ.
Разработка технологических операций строится на следующих этапах:
Рациональное построение технологических операций. Выбор структуры операции.
Установление рациональной последовательности переходов в операции.
Выбор оборудования обеспечивающего оптимальную производительность при условии обеспечения требуемого качества.
Расчет загрузки технологического оборудования. Выбор конструкции и оснастки. Установление принадлежности конструкции к стандартным системам остнастки.
Установление исходных данных необходимых для расчетов и расчет припусков и операционных размеров.
Установление исходных данных необходимых для расчетов оптимальных режимов обработки и их расчет. Установление исходных данных необходимых расчетов норм времени.
Проектирование технологических процессов обработки заготовок на станках с ЧПУ подчиняется общим правилам разработки технологических процессов однако вследствие больших технологических возможностей этих станков специфики формы образования поверхностей и появления нового технологического элемента – управляющей программы (УП ) – технологическая подготовка производства при использовании станков с ЧПУ имеет свои особенности. При обработке заготовок на станках с ЧПУ операции проектируют по принципу концентрации переходов. При разработке операции выполняются следующие дополнительные пункты: выбор исходной точки; установление траекторий рабочих и вспомогательных ходов инструмента (заготовки) на основе типовых постоянных (автоматических и гибких циклов); разработка расчетно-технологической карты (РТК) с оформлением операционного эскиза при ручном программировании; расчет траектории движения инструмента.
Для серийного производства стремимся применять специализированные и специальные приспособления режущий и измерительный инструмент в виде предельных (стандартных и специальных) калибров и шаблонов обеспечивающих взаимозаменяемость обработанных деталей.
Выбор модели станка определяется возможностью изготовления на нем деталей требуемого качества размеров и форм.
Габариты и основные размеры станков должны соответствовать габаритным размерам детали.
Станки должны обладать необходимой мощностью и жесткостью системы СПИД.
Выбираются станки обеспечивающие наименьшую трудоемкость и себестоимость обработки деталей.
Производительность станков должна соответствовать программе выпуска.
Исходя из выше перечисленных требований для разработанного ТП было выбрано следующее оборудование:
На токарной операции – 1К620 и 1К620Ф3.
На внутришлифовальной операции – 3А252.
На вертикально-сверлильной операции – 2А125
На фрезерной операции – 6А12П.
На круглошлифовальной операции – 3180.
Технические характеристики станков:
ТОКАРНО-ВИНТОРЕЗНЫЙ СТАНОК МОДЕЛИ 1К620.
Станок является универсальным. Он предназначен для выполнения разнообразных токарных работ: для нарезания метрической дюймовой модульной питчевой правой и левой с нормальным и увеличенным шагом одно- и многозаходной резьб. А также для нарезания торцовой резьбы .
Техническая характеристика станка.
Наибольший диаметр обрабатываемой детали в мм:
над нижней частью суппорта 200
Наибольший диаметр обрабатываемого прутка в мм 45
Расстояние между центрами в мм 71010001400
Наибольшая длина обтачивания в мм 655 9451325
Пределы поворота верхней части суппорта в град. ±65
Изменение чисел оборотов шпинделя Бесступенчатое
Пределы чисел оборотов шпинделя в минуту 12-3000
Количество величин подач суппорта 48
Пределы величин продольных подач в ммоб: 0070-416
Пределы величин поперечных подач в ммоб: 0035-208
Шаги нарезания резьб:
метрической в мм 1-192
дюймовой (число ниток на 1) 24-2
модульной модуль в мм 05-48
питчевой в питчах 96-1
Диаметр отверстия в шпинделе в мм 47
Скорость быстрого перемещения суппорта в ммин
Мощность главного электродвигателя в кВт 10
ВНУТРИШЛИФОВАЛЬНЫЙ ПОЛУАВТОМАТ МОДЕЛИ 3А252.
Станок предназначен для высокопроизводительного шлифования цилиндрических и конических сквозных и глухих отверстий а также для торцового шлифования в условиях серийного и массового производства.
После установки и закрепления детали обеспечивается автоматический цикл шлифования включая промеры на ходу и выхаживание.
Диаметр шлифуемого отверстия в мм:
Наибольшая длина шлифования в мм 200
Наибольший диаметр обрабатываемой детали в мм 620
Расстояние от оси шпинделя до стола в мм 315
Пределы чисел оборотов шлифовального
шпинделя в минуту 3550-10000
Наибольший диаметр шлифовального круга в мм 150
Ширина шлифовального круга в мм 60
Пределы чисел оборотов шпинделя изделия в минуту 140-600
Наибольший ход стола в мм 500
Скорость хода стола в ммин:
Наибольший угол поворота бабки изделия в град ±30
Мощность приводного электродвигателя
шлифовального круга в квт 45
ВЕРТИКАЛЬНО-СВЕРЛИЛЬНЫЙ СТАНОК МОДЕЛИ 2А125.
Станок предназначен для сверления зенкерования развертывания а также нарезания резьбы метчиками.
Наибольший диаметр сверления в мм 25
Расстояние от оси шпинделя до вертикальных направляющих
Наименьшее и наибольшее расстояние от торца шпинделя
до фундамента плиты в мм 750-1125
Конус отверстия шпинделя Морзе № 3
Наибольшее ручное и механическое перемещение
Наибольшее установочное перемещение шпиндельной
Размеры рабочей поверхности стола в мм 375×500
Наибольшее вертикальное перемещение стола в мм 325
Число скоростей шпинделя 9
Пределы чисел оборотов шпинделя в минуту 97-1360
Пределы подач в ммоб 01-081
Мощность электродвигателей в кВт:
главного движения 28
насоса охлаждения 0125
Габарит станка в мм:
ВЕРТИКАЛЬНО-ФРЕЗЕРНЫЙ СТАНОК МОДЕЛИ 6А12П.
Станок предназначен для выполнения разнообразных фрезерных работ по заранее заданной программе. Кроме того на станке имеется кнопочное управление или ручное – от рукояток.
Система программного управления позволяет производить автоматическую обработку различных деталей в пределах 24 переходов в трех взаимно перпендикулярных координатах.
Размеры рабочей поверхности стола в мм:
Расстояние от торца шпинделя до поверхности стола в мм 35 – 435
Расстояние от вертикальных направляющих станины
до оси шпинделя в мм 320
Поворот фрезерной головки в град ±45
Наибольшее механическое перемещение стола в мм:
Осевое перемещение шпинделя в мм 50
Число ступеней оборотов шпинделя 18
Число оборотов шпинделя в минуту 40 – 2000
Число ступеней подач стола 18
Подача стола в мммин:
продольная 20 – 1000
поперечная 20 – 1000
вертикальная 8 – 400
Скорость быстрого перемещения стола в мммин:
Скорость замедленного перемещения стола в мммин:
Мощность электродвигателя привода главного
Вес станка в кг 2500
КРУГЛОШЛИФОВАЛЬНЫЙ СТАНОК МОДЕЛИ 3180.
Станок предназначен для наружного шлифования гладких цилиндрических деталей типа валиков поршневых пальцев стержней колец роликов и других подобных деталей методом продольной подачи и кроме того для наружного шлифования тел вращения фасонного профиля и цилиндрических деталей ступенчатой формы методом радиальной подачи. Станок применяется в условиях серийного и массового производства.
Диаметр шлифования в мм:
Наибольшая длина шлифования в мм 180
Расстояние между осями кругов в мм:
Наибольшее перемещение каретки в мм 120
Наибольшее перемещение бабки ведущего круга в мм:
Число оборотов шпиндельного круга в минуту 1200
Пределы чисел оборотов ведущего круга в минуту
при гидравлическом приводе 25 – 225
при механическом приводе 13 – 94
Число оборотов ведущего круга в минуту при правке 300
Наибольший угол поворота ведущего круга в град 6
Мощность электродвигателя шлифовального круга в кВт 14
Расчет припусков и операционных размеров.
В серийном производстве используют статистический (табличный) метод определения промежуточных припусков на обработку заготовок что обеспечивает более быструю подготовку производства по выпуску планируемой продукции. К тому же освобождает ИТР от трудоемкой работы.
Статистический расчет будем вести для операционных размеров и соответствующих припусков. Исходными данными будут служить чертежи детали и заготовки а также технологический процесс изготовления.
Для выявления размерных связей строим эскиз совмещенных переходов.
Затем из него выделяем размерные цепи и рассчитываем их.
При выделении размерных цепей придерживаемся следующих правил:
Размерные цепи строятся от заготовки к детали.
Замыкающими звеньями должны быть припуски и конструкторские размеры которые получаются автоматически.
В размерные цепи где замыкающим звеном является i-припуск не должны входить размеры с номером больше i.
В размерную цепь не должны входить 2 припуска.
Размерная цепь должна быть наикратчайшей. Расчет размерных цепей идет в обратном направлении.
При расчете размерных цепей в качестве нормативных таблиц используем ОСТ 1.41512-86 СТ СЭВ 145-75. В таблицах этого стандарта указаны величины номинальных значений оптимальных припусков для различных методов обработки и различных размеров деталей. Припуски переходов указанные в ОСТе даны вне зависимости от материала деталей и вида заготовок. Это с некоторым допущением возможно так как припуски стандарта относятся лишь к обработке заготовок после первой ступени обработки – обдирки. Влияние материала заготовок на величины припусков следующих после обдирки несомненно имеется но оно не столько существенно как в операциях обдирки.
Первой поддается решению расчетная цепь №6.
Процесс построения технологических размерных цепей значительно отличается при использовании теории графов. В начале нумеруем обрабатываемые поверхности по порядку слева на право. Принимаем поверхности за вершины а размеры за ребра. Строим два дерева. В начале строится производное дерево далее исходное затем два дерева совмещаются.
Решаем размерную цепь № 6
А6 - ТА6 = К1 = 23-014
Записываем основное уравнение размерной цепи.
Данная размерная цепь «простая» ибо она трехзвенная допуски составляющих звеньев заданы в «тело» знаки предельных отклонений составляющих звеньев одинаковые. Для таких цепей табличный припуск не требует коррекции.
Определим его по выражению:
Здесь i = 6 i-1 = 2.
Из таблицы ОСТа определяем
Z6=02 – припуск на шлифование. Из таблицы
ТА2 = 014 – допуск на чистовую обработку.
Решаем размерную цепь № 4.
Записываем основное уравнение размерной цепи. Оно имеет вид:
Размерная цепь сложная поэтому табличный припуск требует коррекции.
Расчетный припуск определяется по выражению:
(мм) - припуск на растачивание.
(мм) - допуск на чистовое обтачивание.
Из основного уравнения следует:
Решаем размерную цепь №7
А7+ТА7 = К3 = 125±04
Z7 = А4 – К2 +А7 - А5
(мм) - припуск на шлифование.
(мм) - допуск на черновое обтачивание.
Решаем размерную цепь № 2.
Z2 = Н1 – Н2 +А1 – А2
(мм) - припуск на чистовое обтачивание.
Решаем размерную цепь № 1.
Предельные отклонения на размер H2 известны:
Размерная цепь сложная так как размер Н2 имеет отклонение не «в тело».Поэтому:
В этом выражении в качестве ТАi-1 необходимо взять такое отклонение размера Н2 (Аi-1) которое делало бы рассматриваемую цепь «простой». Поэтому в качестве ТАi-1 берем ΔIН2.
(мм) - припуск на черновую подрезку.
Определение режимов резания.
Режим резания устанавливаемый для обработки детали является одним из главных факторов технологического процесса.
Режим резания металла включает в себя следующие определяющие его основные элементы:
глубина резания t в мм
скорость резания W в ммин
или число оборотов шпинделя станка n в обмин.
Аналитический расчет режимов резания позволяет определить оптимальное значение на основе учета наибольшего числа факторов оказывающих влияние на выходные параметры процесса резания.
В рамках данного раздела производится аналитический расчет режимов резания по эмпирическим формулам с учетом всех поправочных коэффициентов для 4-х технологических переходов.
Для остальных операций механической обработки элементы режима резания определяются приближенно с помощью нормативных таблиц.
Выявление величины элементов режима резания заносятся в специальные графы бланков ТП.
Аналитический расчет режимов резания проведем для следующих операций:
Точение наружной поверхности D = 384 мм.
Оп.030 - Вертикально - сверлильная
Сверление отверстия D = 35 мм.
Обработка по контуру.
Оп.050 – Круглошлифовальная
Шлифование наружной поверхности D = 38 мм.
Значение подачи скорректировано согласно паспортным данным станка.
Рассчитывается по эмпирической формуле
где Т = 30 (мин) – период стойкости инструмента.
С =110 - коэффициент;
х = 02; у = 045; m = 015
Кv = Кмv × Кnv × Кuv = 06 × 08 × 083 = 039
где Кмv - коэффициент учитывающий влияние материала заготовки
K = 08 - коэффициент учитывающий состояние поверхности
K = 083 - коэффициент учитывающий материал инструмента
где D = 384 (мм) – диаметр обрабатываемой детали.
Корректируем частоту вращения шпинделя по паспортным данным станка и устанавливаем действительное значение частоты вращения.
Определяем действительную скорость главного движения резания.
где Ср = 300 – постоянная
xyn – показатели степени
х = 10; у = 075; n = 0
Кр – поправочный коэффициент
где K- коэффициент учитывающий влияние качества обрабатываемого материала на силовые зависимости.
= 10 - коэффициент учитывающий влияние главного угла.
= 10 - коэффициент учитывающий влияние переднего угла
= 10 - коэффициент учитывающий влияние угла наклона главного лезвия
Мощность резанья кВт
t = 05 × D = 05 × 35 = 175 (мм)
D = 35 (мм) – диаметр сверления
Скорость резания V ммин
где С= 357 - коэффициент
q y m – показатели степени
q = 05; y = 045; m = 012
Т = 6 (мин) – период стойкости.
Общий поправочный коэффициент на скорость резания учитывает фактические условия резания.
где K= 094 - коэффициент на обработку материала.
K= 083 - коэффициент на материал инструмента.
K= 10 - коэффициент учитывающий глубину сверления.
Для сверления инструментом из быстрорежущей стали
Частота вращения ( шпинделя со сверлом)
где D = 35 (мм) – диаметр сверла.
Определяем действительную скорость главного движения.
Крутящий момент М Нм
где С= 0041 – коэффициент.
q y – показатели степени.
K- коэффициент учитывающий фактические условия обработки
где К - коэффициент материала обрабатываемой заготовки.табл. 95
где С= 143 – коэффициент.
Мощность резания N кВт
Глубина фрезерования
Ширина фрезерования
где Т = 60 (мин) – период стойкости инструмента.
С =108 - коэффициент;
q = 0; х = 02; у = 006;u = 03;p = 02; m = 032
Z =6 – число зубьев;
D =16 – диаметр фрезы;
Кv = Кмv × Кnv × Кuv = 06 × 08 × 01 = 048
K = 01 - коэффициент учитывающий материал инструмента
Частота вращения фрезы
Корректируем частоту вращения шпинделя по данным станка и устанавливаем действительную частоту вращения.
Действительная скорость главного движения
где D = 16 (мм) – диаметр фрезы.
Sм = Sz × Z × nD = 006 × 6 × 445 = 1602 (мммин)
Корректируем по паспортным данным станка и устанавливаем действительную минутную подачу.
где Ср = 218 – постоянная
х = 092; у = 078; n = 1; v = 1;w = 0
Кмр – поправочный коэффициент
Оп. 050 Круглошлифовальная
Выбираем шлифовальный круг:
ПП 600×63×305 КЗ 25-6СМ2-С2
Размеры шлифовального круга:
Dк =600 (мм) – диаметр
Вк = 63 (мм) – ширина
Вращение шлифовального круга
Nк = 1112 (обмин) – частота вращения круга по паспортным данным.
Vз = 21 (ммин) – скорость движения заготовки.
Частота вращения заготовки
dз = 38 (мм) – диаметр заготовки.
Эффективная мощность кВт
С =014 - коэффициент;
r =08; х = 08; q = 02; b = 5; z = 1
Расчет норм времени.
Для выполнения каждой операции технологического процесса рассчитывают техническую норму времени. Т.е. время необходимое для выполнения данной операции в нормальных производственных условиях при наиболее целесообразном использовании всех средств производства.
Т – время необходимое для выполнения операции;
Тпз – подготовительно – заключительное время на партию деталей затрачиваемое при одной наладке станка;
n – количество деталей обрабатываемых в партии при одной наладке станка;
Тшт – штучное время затрачиваемое на выполнение операции.
Норма штучного времени определяется по формуле
Тшт = Тосн + Твсп + Тобсл + Тпер
Тосн – основное время в течение которого снимается стружка;
Твсп – вспомогательное время;
Тобсл – время обслуживания рабочего места;
Тпер – время перерывов на отдых и личные потребности рабочего.
Топ = Тосн + Твсп - оперативное время.
Тдоп = Тобсл + Тпер - дополнительное время.
Окончательный вид формулы:
Тшт = Тосн + Твсп + Тдоп = Топ + Тдоп
Величину основного времени подсчитывают по формуле которая несколько видоизменяется от вида обработки:
Тосн = ( l + y + Δ )(n S) = L sм
y – величина врезания инструмента;
Δ – величина перебега инструмента;
n – число оборотов в минуту;
s – подача мм на один оборот;
sм - минутная подача в мммин.
Остальные нормы времени выбираются по специализированным таблицам с учетом вида обработки и других производственных факторов.
4.ЭКОНОМИЧЕСКАЯ ЧАСТЬ.doc
Годовая программа изделий шт.(Nизд)
Применяемость детали в изделиях (ni)
Трудоемкость изготовления детали «Втулка» нч.(ti)
Номенклатура деталей изготовляемых на участке (n)
Удельное значение трудоемкости «Втулка» в трудоемкости всей номенклатуры деталей подлежащих выпуску.(Куд)
Годовая трудоемкость цеха норма-час (Tгод)
Количество участков в цехе.(Куч)
Число календарных дней в году (Dk)
Режим работы смена (S)
Продолжительность смены час (tсм)
Количество технологических операции (m)
Коэффициент загрузки ()
Количество человек занятых на одном рабочем месте (f)
Число рабочих дней (D)
Число предпраздничных дней (d)
Величина сокращения (L)
Коэффициент учитывающий потери времени на капитальный ремонт оборудования ()
Полезный годовой фонд времени одного работающего час (Фд)
Минимальная зарплата руб. (Фmin)
Стоимость 1кВтчас электроэнергии руб. (Цэ)
Стоимость 1м2 производственной площади руб. (Цз)
Масса заготовки кг (Gзаг)
Масса детали кг (Gд)
Цена материала руб. за кг. (Цм)
Цена отхода руб. за кг. (Цотх)
2. РАСЧЕТ ТРУДОЕМКОСТИ ПОЛНОГО ОБЪЕМА
РАБОТ ПОДЛЕЖАЩИХ ВЫПОЛНЕНИЮ УЧАСТКОМ.
Трудоемкость единиц всех деталей условно принимается равной трудоемкости типового представителя по которому ведется проектирование технологического процесса.
2.1. Коэффициент условности.
Куд = 02 – удельное значение трудоемкости втулки.
2.2. Трудоемкость полного объема работ подлежащих выполнению участком.
Ттип – трудоемкость годовой программы типового представителя.
2.3. Годовая программу запуска основной (типовой) детали участка.
– годовая программа выпуска изделий.
– применяемость деталей на один двигатель.
– процент запасных деталей поставляемых в сервисные службы (по заявкам исходя из потребности).
– процент потерь по техническим причинам (при наладке освоении технологического процесса).
2.4. Трудоемкость полного объема работ подлежащих выполнению участком по каждой операции рассчитываются по формуле: где
tшт – трудоемкость операции нч
– полученные по всем операциям результаты приведены в таблице 3.2
Итого по участку: 777939 368 1303
Итого по цеху: 320000 52
Продолжение таблицы 3.2
Установлен. Мощн.; кВт
Стоимость (баланс.) обордв; руб.
Внутрицеховой транспорт (005 стоимости оборудования): 132958
3. ОПРЕДЕЛЕНИЕ ТИПА ПРОИЗВОДСТВА
ВЫБОР МЕТОДОВ И ФОРМ ЕГО ОРГАНИЗАЦИИ.
3.1. Критерием для установления типа производства служит коэффициент закрепления операций.
m – количество технологических операций.
n – номенклатура деталей изготавливаемых на участке.
С – количество рабочих мест на производственном участке.
– трудоемкость годовой программы.
– действительный годовой фонд времени работы единицы оборудования.
– коэффициент выполнения норм.
– количество рабочих занятых одновременно на одном рабочем месте.
– коэффициент загрузки.
– коэффициент учитывающий потери времени на капитальный ремонт оборудования.
– число рабочих дней в году.
– число предпраздничных дней с сокращенным режимом работы.
– величина сокращения рабочего дня.
S – число смен в сутки.
tсм – продолжительность смены.
Полученное значение сравниваем с приведенными в табл.2 [7] значениями: Кзо=104 – соответствует среднесерийному производству.
4. НОРМАТИВНО - КАЛЕНДАРНЫЕ РАСЧЕТЫ В ПРОИЗВОДСТВЕ.
4.1. Минимальный размер партии.
– подготовительно-заключительное время по ведущей операции – штучно-калк. время по ведущей операции.
– коэффициент допустимых потерь на переналадку для среднесерийного производства.
4.2. Периодичность запуска партии деталей.
Nсут – среднесуточный выпуск деталей.
Nтип – годовая программа запуска.
Dк=365 – число календарных дней в году.
Принимаем периодичность запуска R=1день.
4.3. Откорректированный размер партии.
4.4. Длительность производственного цикла.
Кп – коэффициент перевода рабочих дней в календарные.
Ттех – технологический цикл при последовательном виде движения партии деталей по операциям.
Тмо – длительность межоперационных перерывов.
tмо – время межоперационного перерыва.
Значение tмо округляем до значения кратного продолжительности рабочей смены и принимаем tмо=4часа.
Тест=0час – длительность естественных процессов.
4.5. Нормальная величина задела.
Zц – цикловой или производственный задел.
Nсут – суточное потребление изделий последующим цехом.
Zскл – межцеховой складской задел.
Zоб – межцеховой оборотный задел.
d=10дней – число календарных дней с начала месяца до дня поступления очередной партии деталей.
Zстр – межцеховой страховой задел.
5. РАСЧЕТ ПОТРЕБНОГО КОЛИЧЕСТВА ОБОРУДОВАНИЯ И ПЛОЩАДЕЙ.
5.1. Количество оборудования для каждой операции по видам (токарное фрезерное и пр.) определяются исходя из трудоемкости годовой программы i-ой операции по формуле: где
Ттип i – трудоемкость трудовой программы i-ой операции.
Фэф – эффективный фонд времени работы оборудования.
Квн=11 – коэффициент выполнения норм.
f – количество рабочих занятых на одном рабочем месте.
где принятое количество оборудования получаем путем округления расчетного количества оборудования до целого числа в большую сторону.
Полученные по всем операциям результаты приведены в табл.3.2.
5.2. Коэффициенты загрузки оборудования по отдельным его видам в среднем по участку и по цеху определяется по формуле:
Полученные результаты приведены в табл.3.2.
5.3. Производственная площадь приходящаяся на единицу оборудования.
– площадь единицы оборудования по габаритам (длина х ширина).
– коэффициент учитывающий дополнительную площадь для металлорежущего оборудования (рабочая зона вокруг оборудования второстепенные проходы и проезды между станками) принимаемые по табл.5 [7].
5.4. Производственная площадь приходящаяся на принятое количество оборудования.
Полученные результаты по каждой операции приведены в табл.3.2.
5.5. Вспомогательная и площадь проездов рассчитывается в процентах от производственной площади.
– процент всей вспомогательной площади и проездов.
5.6. Общая площадь участка.
5.7. Общая площадь цеха.
6. РАСЧЕТ ЧИСЛЕННОСТИ РАБОТАЮЩИХ.
6.1. Численность рабочих основного производства участка определяется по формуле: где
Тгод – трудоемкость планируемого полного объема работ по операции.
- действительный фонд времени рабочего.
Квн – коэффициент учитывающий выполнение норм:
На универсальном оборудовании и слесарной операции Квн=112.
На станках с ЧПУ Квн=1.
На операциях разметки и контроля Квн=1.
Код – коэффициент учитывающий многостаночное обслуживание станков с ЧПУ (при обслуживании 2-х станков).
6.1.1. Численность рабочих сдельщиков работающих на универсальном оборудовании и на слесарной операции.
6.1.2. Численность рабочих сдельщиков работающих на станках с ЧПУ (при работе одного рабочего на двух станках).
6.1.3. Численность рабочих повременщиков.
6.2. Общая численность рабочих основного производства.
6.3. Расчет численности прочих категорий работающих (рабочих вспомогательного производства ИТР служащих и МОП).
При укрупненном расчете численность каждой категории работающих определяется в процентах от числа производительных рабочих с дифференциацией по цехам по специальным нормативам произведенным в табл.6 [7].
6.3.1. Рабочие вспомогательного производства.
6.3.2. Общее количество рабочих.
6.3.3. Инженерно-технические работники.
6.3.5. Младший обслуживающий персонал
Численность ИТР и служащих производственного участка.
Инженер по инструменту
Численность рабочих вспомогательного производства.
Наладчики оборудования:
слесари по текущему ремонту оборудования
станочники по ремонту оборудования
слесари по ремонту технологической оснастки
станочники по ремонту технологической оснастки
кладовщики материальной и промежуточной кладовой
кладовщики инструментально-раздаточных кладовых
подготовители распределители транспортные рабочие
6.4. ОПРЕДЕЛЕНИЕ СРЕДНЕГО РАЗРЯДА РАБОТ И СООТВЕТСТВУЮЩИХ ИМ ТАРИФНЫХ КОЭФФИЦИЕНТОВ.
6.4.1. Средний разряд работ оплачиваемых по сдельным тарифным ставкам.
-разряд работы j-ой операции.
tшт – штучное время j-ой операции.
m – количество операций.
6.4.2. Средний разряд работ оплачиваемых по повременным тарифным ставкам.
6.4.3. Средний разряд рабочих вспомогательного производства.
– численность рабочих вспомогательного производства по i-ому разряду.
Рi – разряд рабочего.
6.4.4. Средний тарифный коэффициент сдельных работ.
- значения тарифных коэффициентов соответствующих меньшему и большему значению из двух смежных разрядов между которыми находится среднее значение разрядов работ.
6.4.5. Средний тарифный коэффициент повременных работ.
6.4.6. Средний тарифный коэффициент вспомогательного производства.
7. РАСЧЕТ ФОНДОВ ЗАРАБОТНОЙ ПЛАТЫ
7.1. Расчет фонда заработной платы рабочих основного производства.
Фосн – фонд основной заработной платы выплачиваемый рабочим за работу выполненную непосредственно по изготовлению основной продукции.
– коэффициент учитывающий доплаты надбавки и премии.
Фтар – фонд тарифной заработной платы.
Фтарсд – тарифный фонд сдельщиков.
– часовая тарифная ставка.
– тарифный коэффициент.
– часовая тарифная ставка первого разряда.
– месячная тарифная ставка первого разряда.
– месячный плановый фонд времени рабочего.
D – число рабочих дней в году.
t – продолжительность рабочего дня.
d – число предпраздничных дней сокращенных рабочим временем.
t – величина сокращенного рабочего времени.
M – число месяцев в году.
– действительный фонд времени рабочего.
– численность рабочих повременщиков.
Фдоп – фонд дополнительной заработной платы – это выплаты предусмотренные законодательством о труде за неотработанное время: за внутрисменные перерывы (сокращение рабочего дня подросткам кормящим матерям) за целодневные перерывы (очередные и дополнительные отпуска отпуска учащимся выполнение государственных и общественных поручений) устанавливается в пределах 10-12% от основной заработной платы.
Фвысл – фонд вознаграждений за выслугу лет – это поощрение за непрерывный стаж работы на одном предприятии устанавливается в долях месячной тарифной ставки рабочих при стаже непрерывной работы.
Фвозн – фонд вознаграждений за общие результаты работы по итогам за год устанавливается в зависимости от стажа работы в % от среднемесячной основной заработной платы.
7.2. Среднемесячная заработная плата рабочих основного производства.
7.3. Расчет фонда заработной платы рабочих вспомогательного производства.
Фосн – фонд основной заработной платы.
– численность рабочих вспомогательного производства.
Фдоп – фонд дополнительная заработной платы.
Фвысл – фонд вознаграждений за выслугу лет.
Фвозн – фонд вознаграждений за общие результаты работы по итогам года.
7.4. Среднемесячная заработная плата рабочих вспомогательного производства.
таблица с повремен сдельщ вспом.
7.5. Расчет фонда заработной платы ИТР служащих МОП.
Должностные оклады руководителей производственных подразделений специалистов и служащих устанавливаются исходя из установленного минимального уровня оплаты труда и тарифных коэффициентов соответствующих установленному разряду по ЕТС по формуле: где
КТ – тарифный коэффициент принимаемый по табл.12 [7] в зависимости от разряда оплаты труда.
Фонд заработной платы ИТР служащих и МОП рассчитывается исходя из установленных должностных окладов (Dокл) численности этих работников по штатному расписанию (Ч) числа месяцев в планируемом периоде (12) доплат надбавок и премий () вознаграждений за непрерывный стаж работы (Кд) и за общие результаты работы по итогам за год (Квозн).
Среднемесячная заработная плата по каждой категории рабочих определяется делением годового фонда заработной платы на число месяцев и на численность рабочих по формуле: руб.
Фонд заработной платы по цеху определяется по формуле:
(Полученные результаты приведены в табл.3.6).
Всего11Всего по цеху: 863796
8. РАСЧЕТ ОБЩЕПРОИЗВОДСТВЕННЫХ РАСХОДОВ.
8.1. Содержание аппарата управления участка.
– коэффициент учитывающий отчисления на социальные нужды и на социальное страхование от несчастных случаев на производстве и профессиональных заболеваний.
8.2. Содержание прочего персонала.
8.3. Амортизация оборудования и транспортных средств.
– нормы амортизационных отчислений по металлорежущему оборудованию.
К0= 2792118 руб – балансовая стоимость оборудования.
8.4. Расходы на ремонт и содержание оборудования.
К0 = 2792118 руб - балансовая стоимость оборудования.
Н0=0105 – норма затрат на ремонт и содержание (без капитального ремонта).
8.5. Затраты на силовую электроэнергию.
Ny=786 кВт – суммарная установленная мощность электродвигателей оборудования цеха.
KN=0.6 – коэффициент использования электродвигателей по мощности.
Квр=05 – коэффициент использования электродвигателей по времени.
Код=1 – коэффициент учитывающий одновременность работы электродвигателей.
– коэффициент учитывающий потери электроэнергии в сети завода.
– коэффициент полезного действия эл.двигателей.
– коэффициент загрузки оборудования.
Фэф=3783час – действительный годовой фонд времени работы оборудования.
Цэ=09руб – цена киловатт часа электроинергии.
8.6. Затраты на износ малоценного инструмента и приспособлений.
- удельные затраты на технологическое оснащение единицы оборудования.
Спр – принятое количество оборудования.
8.7. Амортизация зданий сооружений.
Sуч – площадь участка.
Sпр=31376м2 – производственная площадь.
Цз - стоимость 1м2 площади.
8.8. Расходы на содержание и текущий ремонт зданий.
Нзд=108% - норма затрат на ремонт и содержание зданий.
8.9. Расходы на охрану труда.
8.10. Затраты на износ малоценного и быстро изнашиваемого инвентаря из расчета 300 руб на одного работающего в год.
8.11. Прочие расходы по ремонту и содержанию оборудования определяется в процентах от суммы затрат по статьям 3 4 5 6: Канцелярские расходы услуги других организаций.
Общепроизводственные расходы по участку.
Содержание аппарата управления участком
Содержание прочего персонала участка
Амортизация оборудования и транспортных средств
Расходы на ремонт и содержание оборудования
Затраты на силовую электроэнергию
Затраты на износ малоценного инструмента и приспособлений
Амортизация зданий и сооружений
Расходы на содержание и текущий ремонт зданий и сооружений
Расходы на охрану труда
Затраты на износ малоценного и быстроизнашиваемого инвентаря
8.12 Процентное соотношение суммы общепроизводственных расходов к сумме основной заработной плате рабочих основного производства.
9. РАСЧЕТ ПЛАНОВОЙ СЕБЕСТОИМОСТИ ПРОДУКЦИИ.
9.1. Сырье и материалы.
Gзаг – вес заготовки.
Gотх=01 – 005 = 005 кг – вес отхода.
Цм – цена материала.
Цотх – цена отходов.
Ктр=105 – коэффициент учитывающий транспортно- заготовительные расходы.
9.2. Основная заработная плата рабочих основного производства на единицу продукции.
– часовая тарифная ставка соответствующая среднему разряду работ сдельщиков и повременщиков.
– штучное время работ оплачиваемых по сдельным повременным тарифным ставкам.
– коэффициент учитывающий надбавки доплаты премии.
9.3. Дополнительная заработная плата рабочих основного производства.
9.4. Отчисления единого социального налога.
9.5. Отчисления на обязательное социальное страхование от несчастных случаев на производстве и профессиональных заболеваниях.
9.6 Итого: прямые затраты.
9.7. Расходы на подготовку и освоение производства.
9.8. Общепроизводственные расходы.
9.9. Цеховая себестоимость.
9.10. Общехозяйственные расходы.
9.11. Налоги включаемые в себестоимость продукции.
На пользование дорогами
В экологический фонд
9.12. Производственная (заводская) себестоимость.
9.13. Внепроизводственные (коммерческие) расходы.
9.14. Полная (коммерческая) себестоимость.
Себестоимость единицы продукции.
Сырье и материалы (за вычетом возвратных отходов).
Основная заработная плата рабочих основного производства.
Дополнительная заработная плата рабочих основного производства.
Отчисления единого социального налога.
Отчисления на обязательное страхование от несчастных случаев на производстве и профессиональных заболеваниях.
Итого прямые затраты
Расходы на подготовку и освоение производства.
Общепроизводственные расходы.
Цеховая себестоимость.
Общехозяйственные расходы.
Производственная себестоимость.
Внепроизводственные (коммерческие) расходы.
Полная (коммерческая) себестоимость.
10. Расчет плановой прибыли.
11. Цена единицы продукции.(производственная)
Технико – экономические показатели участка.
Годовая программа детали Nг (важнейшей номенклатуры)
Трудоемкость годовой программы Ттип
Трудоемкость годовой программы с учетом дозагрузки (при проектировании по условной программе) Тусл
Себестоимость товарной продукции (цеховая)
Численность работающих в т. ч.
-Рабочих основного производства
-Рабочих вспомогательного производства
Средний разряд работы сдельн.повремен.
Фонд оплаты труда рабочих основного производства
Фонд основной заработной платы
Среднемесячная основная заработная плата рабочих основного производства
Выработка на одного рабочего в месяц
Материальные затраты на 1 руб. товарной продукции
Средняя загрузка станочного оборудования
Себестоимость одного нормочаса
ЭКОНОМИЧЕСКОЕ ОБОСНОВАНИЕ ВЫБОРА ВАРИАНТОВ ТЕХНОЛОГИЧЕСКИХ ПРОЦЕССОВ.
Одним из этапов работ технологической подготовки производства является технико-экономическое обоснование выбора варианта технологического процесса. Из возможных вариантов технологии изготовления детали «Втулка» выбирается наиболее экономичный. Критерием экономичности при этом служит минимальная технологическая себестоимость. Это характерно для тех случаев когда анализируются сравниваются варианты технологического процесса в которых различается оборудование оснастка материал и т.п.
Под технологической себестоимостью следует понимать сумму затрат на осуществление технологического процесса без учета покупных изделий. Рассчитываем только те затраты которые изменяются по вариантам технологического процесса. Так как в сравниваемых вариантах используется одна и та же заготовка из одного материала то затраты на материал не рассчитываются.
Входящие в технологическую себестоимость затраты делятся на условно-переменные (Sv) и условно- постоянные (Sc).
Условно-переменные затраты – это расходы на сырье материалы (Sм) и заработную плату производственных рабочих (Sзп) расходы по ремонту и содержанию оборудования (Sрем) расходы на быстроизнашивающийся инструмент (Sин) силовую энергию (Sqэ) амортизационные отчисления от стоимости универсального оборудования (Sам) и другие. Условно-переменные расходы изменяются пропорционально изменению объема выпускаемой продукции.
Условно-постоянные затраты – это расходы на содержание и ремонт специального оборудования оснастки расходы на содержание заводского и цехового персонала на отопление освещение амортизационные отчисления нот стоимости специального оборудования и затраты на наладку спец. оснастки. Эти затраты не зависят от объема производства.
Величина технологической себестоимости определяется по формуле:
S = Sv + - единицы продукции.
S = SvN + Sc – годового объема
Где N – объем выпуска изделий шт.
Выбор того или иного варианта технологического процесса сводится к определению критической программы выпуска изделий т.е. такого объема выпуска при котором технологическая себестоимость рассматриваемых вариантов одинакова.
Сравнение двух вариантов ведут исходя из соотношений:
S1 = Sv1N + Sc1 – для первого варианта;
S2 = Sv2N + Sc2 – для второго варианта.
N критическая будет равна:
Для того чтобы определить S1 и S2 необходимо рассчитывать Sv1 и Sv2 Sc1 и Sc2.
Расчет условно-переменных затрат.
Sv = Sм + Sзп + Sqэ + Sин + Sрем + Sам
Затраты на материалы.
В сравниваемых вариантах технологических процессов используется одна и та же заготовка из одного материала поэтому затраты на материал не рассчитываются.
Sзп = Сч tшт К Кд Котч (руб.).
где Сч = 175 – часовая тарифная ставка (руб)
- часовая тарифная ставка 1 разряда (руб)
Фпл =166 – месячный плановый фонд рабочего времени(час)
tшт – штучное время час.
К - коэффициент учитывающий доплаты и премии (1.4-16);
Кд – коэффициент учитывающий дополнительную заработанную плату (11-112);
Котч – коэффициент учитывающий отчисления единого социального фонда и обязательного страхования от несчастного случая (159);
Sзп1 = 12×220×15×11×159 = 6954 (руб)
Sзп2 = 12×110×15×11×159 = 3477 (руб)
Затраты на силовую энергию.
Nу – установленная мощность электродвигателя кВт
Кn – коэффициент использования электродвигателя по мощности
Квр – коэффициент использования электродвигателя по времени
Код – коэффициент учитывающий одновременность работы двигателей
К - коэффициент учитывающий потери электроэнергии в сети завода.
- коэффициент полезного действия электродвигателя
Квн – коэффициент выполнения норм времени
Цэ – стоимость электроэнергии
Затраты на режущий инструмент.
Sин = [(Ци×Ктр – Црин) + nпер×Спер]× (руб)
Ци – цена инструмента руб
Ктр – коэффициент учитывающий транспортно-заготовительные расходы
Црин – (условно) – выручка от использованного инструмента
nпер – число переточек инструмента
Спер – себестоимость одной переточки
tмаш – машинное время обработки детали час
tст – стойкость инструмента от переточки до переточки час
Куб – коэффициент учитывающий случайную убыль
Sин1 = [(500×102 – 15) + 60×127]××11 = 101(руб)
Sин2 = [(1000×102 – 30) + 120 ×127]×11 = 121 (руб)
Расходы на ремонт и содержание оборудования.
Ср – расходы на ремонт и содержание оборудование за год отнесенные к единице ремонтной сложности руб
Rо – единица ремонтной сложности технологического оборудования
- коэффициент учитывающий ремонт и содержание электрической части оборудования для металлорежущих станков
Фд = 166 – действительный годовой фонд времени работы оборудования час.
Расчет условно-постоянных затрат.
Sc = Sам + Sэсп + Sнал
Расходы на амортизацию спец. оборудования.
Ксп – балансовая стоимость специального оборудования
Тс – срок погашения стоимости оборудования (3-5) лет;
Расходы на содержание и износ спец. приспособления.
Спр – стоимость спец. приспособления руб.
×Спр – затраты на все виды ремонта спец. приспособления в течении срока его службы руб.
Спр.отх – выручка от реализации приспособления после его износа по цене отхода руб;
Тс1 – срок погашения стоимости приспособления
Затраты на наладку оборудования годовые расходы на оплату подготовительно-заключительного времени руб.
Sнал = Cч×Тпз×К×Кд×Котч×nнал. Руб.
Сч = 1584 - часовая тарифная ставка наладчика рубчас;
nнал = - количество наладок в течение года;
Д – количество рабочих дней в году
R – переодичность запуска партии деталей
Sнал1 = 1584×84×15×11×159×250 = 8726818 (руб)
Sнал2 = 1584×42×15×11×159×250 = 4363406 (руб)
Сравнение двух вариантов технологического процесса.
Sv1 = 6954 + 672 +101 + 42625 + 65106 = 7325925 (руб)
Sv2 = 3477 + 457 + 121 + 1316 + 66114 = 703003 (руб)
Sc1 = 65106 + 22833 + 8726818 = 9400711 (руб)
Sc2 = 62114 + 15892 + 4363406 = 5000438 (руб)
S1 = 7325925×8000 + 9400711 = 5870140711 (руб)
S2 = 703003×8000 + 5000438 = 5629024438 (руб)
Рассмотрев два варианта технологического процесса видим что в нашем случае N >Nкр а технологическая себестоимость первого варианта S1 >S2 поэтому для нас более выгоден второй вариант технологического процесса обработки детали «Втулка» так как он более экономичен. Технологическая себестоимость постоянные и переменные расходы этого варианта меньше.
8.СОДЕРЖАНИЕ.doc
1 Анализ исходных данных для разработки ТП 3
2 Выбор действующего типового группового ТП или поиск
аналога единичного процесса 5
3 Выбор исходной заготовки и методов её изготовления 6
4 Выбор технологических баз 9
5 Составление технологического маршрута обработки 10
6 Разработка технологических операций 11
Технические характеристики станков 13
Расчет припусков и операционных размеров 19
Определение режимов резания 28
Расчет норм времени 35
Конструкторская часть 37
1 Проектирование приспособления 37
2 Проектирование режущего инструмента 42
3 Проектирование мерительного инструмента 46
4 Проектирование механизма для автоматического зажима
Специальная часть 53
1 Автоматизированная подготовка УП для станков с ЧПУ 53
2 Методы выставления рабочих органов (РО) в исходные
3 Расчет координат исходных точек 59
Экономическая часть 61
1 Исходные данные 61
2 Расчет трудоемкости полного объема работ подлежащих
выполнению участком 62
3 Определение типа производства выбор методов и
форм его организации 64
4 Нормативно – календарные расчеты в производстве 65
5 Расчет потребного количества оборудования и площадей 68
6 Расчет численности работающих 69
7 Расчет фондов заработной платы по участку 74
8 Расчет общепроизводственных расходов 80
9 Расчет плановой себестоимости продукции 83
Экономическое обоснование выбора вариантов
технологических процессов 87
13 Планировка цеха 94
14 Определение количества оборудования и площадей
вспомогательных отделений 95
Охрана труда и окружающей среды 101
1 Оценка экологической безопасности проекта 102
3 Определение коэффициента безвредности труда 105
3 Расчет коэффициента токсичности и экологичности 107
4 Производственная безопасность 109
5 Система вентиляции 111
6 Производственное освещение 112
7 Электробезопасность 114
8 Расчет заземления 115
9 Пожарная безопасность 117
10 Средства пожаротушения и средства сигнализации о пожаре 119
11 Травмобезопасность 121
Спецификация приспособления зажимного 125
Спецификация диафрагмы 127
6.ЭКОЛОГИЧЕСКАЯ ЧАСТЬ.doc
РАЗРАБОТКА ДЛЯ ПРОЕКТИРУЕМОГО ЦЕХА
МЕРОПРИЯТИЙ ПО ОБЕСПЕЧЕНИЮ ОХРАНЫ ТРУДА
Деятельность человека осуществляется в условиях техносферы или окружающей природной среды т. е. в среде обитания.
Среда обитания - окружающая человека среда обусловленная в данный момент совокупностью факторов (физических химических биологических социальных) способные оказывать прямое или косвенное немедленное или отдаленное воздействие на деятельность человека его здоровье и потомство.
Производственная среда состоит из составляющих ее элементов: предметов труда средства труда продукты труда и т. п.
Деятельность - активное (сознательное) взаимодействие человека со средой обитания результатом которого должна быть ее полезность для существования человека в этой среде. Формы деятельности разнообразны.
Опасность - процессы явления предметы оказавшие негативное влияние на жизнь и здоровье человека.
Опасности связанные с обработкой детали «Втулка»
-неправильная установка детали (приспособления) на станке ведет к влету детали (приспособления) со станка. Это может причинить вред здоровью рабочего и угрожать его жизни.
-неправильная установка режущего инструмента а также не верный выбор режимов резания приводит к поломке инструмента и возникновения отлетающих частиц инструмента
-возникающая при обработке стружка (частицы обрабатываемого материала)
-повышенный уровень шума
1 ОЦЕНКА ЭКОЛОГИЧЕСКОЙ БЕЗОПАСНОСТИ ПРОЕКТА.
В дипломном проекте разрабатывается механический цех по производству деталей типа тел вращения (деталей типа «Втулка»). При изготовлении этого вида деталей используется разнообразное технологическое оборудование. (В частности станки токарной сверлильной фрезерной и шлифовальной групп).
Все системы станков питаются от сети переменного тока. В процессе работы станков имеет место вращение режущего инструмента. При обработке детали на станках используется охлаждающая жидкость. В зоне резания возникает высокая температура что приводит к частичному испарению охлаждающей жидкости. Во время работы станков на больших скоростях от станков начинает лететь стружка.
В данном цехе при обработке металлов как уже было сказано используется смазывающая охлаждающая жидкость. При высоких температурах в зоне резания происходит ее частичное испарение. Аэрозоль нефтяных масел входящая в состав смазывающая охлаждающая жидкость может вызвать раздражение слизистых оболочек верхних дыхательных путей. Поэтому в качестве мероприятий по обезвреживанию газообразных выбросов вредных веществ в проектируемом цехе установлены специальные теплообенники - конденсаторы принцип действия которых заключается в охлаждении паровоздушной смеси ниже точки росы.
Для утилизации отходящих газов а также для их дожигания предусмотрены специальные котлы - пароперегреватели и охладители конвекторных газов.
Очистка вентиляционных выбросов от механических примесей осуществляется аппаратами мокрого пылеулавливания.
Критерий загрязненности воды - ухудшение ее качества вследствие изменения органолептических свойств и появления в ее составе вредных веществ представляющих опасность для человека растительного и животного мира.
На данном предприятии очистка сточных вод осуществляется в отстойниках. Полученный шлам содержащий большое количество металлов утилизируется. Очищенные воды используются в системе оборотного водоснабжения.
Основную долю загрязнения сточными водами водоемов при механической обработке составляет рабочая жидкость (смазывающая охлаждающая жидкость) состоящая из водных растворов различных эмульсий. Кроме того в меньших объемах используется керосин для проведения операций мойки и обезвреживания. В данном проекте предусматривается замкнутый цикл использования рабочих жидкостей с их фильтрацией от загрязнений и регенерацией для восстановления физико-химических свойств что полностью исключает загрязнение водного бассейна.
Характеристика применяемых методов механической очистки
Безвредность изготовления изделия характеризуется параметрами санитарно-гигиенических и психофизических производственных условий труда действующих на рабочего при выполнении операций технологического процесса изготовления детали типа «Втулка». Определение коэффициента безвредности труда приведено в таблице 2. Определение ведется исходя из сравнения величины установленных предельно допустимых концентраций и уровней воздействия на человека и фактических значений этих параметров.
Это является признаком безвредного производства и соответствует допустимым параметрам санитарно-гигиенических и психофизических производственных факторов условий труда. В целях снижения загрязнения почв различными промышленными отходами предусмотрены следующие мероприятия: утилизация обезжиривание методом сжигания и захоронения на специальных полигонах. Отходы металлообрабатывающей промышленности изменяют структуру физико-химические свойства и механический состав почв. Поэтому такие отходы используют при строительстве дорог засыпки котлованов и отработанных карьеров после обезжиривания. Основную долю отходов в проектируемом цехе составляет стружка. Стружку перерабатывают на пакетируещих прессах и отправляют на металлургический завод. Остальные отходы предприятия содержащие кислоты щелочи утилизации не подлежат. Эти отходы собирают в шлаконакопители после чего их засыпают утрамбовывают а место захоронения озеленяют.
2 ОПРЕДЕЛЕНИЕ КОЭФФИЦИЕНТА БЕЗВРЕДНОСТИ ТРУДА
Выводы по определению КБВ:
При значении КБВ ≥ 1 - производство является вредным фактором воздействия на организм человека.
В проектируемом цехе усредненное значение КВБ:
КВБСР = (05+067+067+05+067+067+067+067)8 = 0627
Значения предельно-допустимых концентраций веществ содержащихся в применяемых в цехе СОЖ промывочных жидкостях.
Берилий и его соединения
Кремнесодержащие пыли
Окись углерода аммиак
Примечание к таблице 3.
Буквы обозначающие агрегатное состояние веществ в условиях производства:
П - пары или (и) газы
3 РАСЧЕТ КОЭФФИЦИЕНТА ТОКСИЧНОСТИ И ЭКОЛОГИЧНОСТИ
Коэффициент токсичности выбросов в атмосферу (Кт1) и (Кт2):
КТ1=Σ (L Ci × Mi) Σ Mi
где Ci - отношение ПДК к концентрации выбрасываемого i-ro вещества Mi -объем выбросов того или иного вещества
n -число выбрасываемых веществ (пыль хлор и т. д.)
КТ1= (1(25)×25+1(31)×400)(23+400)= 046
КТ2=Σ (L Ci × Mi) Σ Mi
КТ2=(1(00010001)×2+1(0010002)×1+1(105)×4+1(43)×12+1(2001550)×8(2+1+4+12+8)=06
Коэффициенты токсичности выбросов в атмосферу КТ1 и Кт2 меньше единицы следовательно проектируемый цех имеет малотоксичные отходы.
Индекс экологической опасности
где аij - абсолютные показатели воздействия i-отрасли
Bij - численность промышленно- производственного персонала Ai - показатель землеемкости водопотребления выброса загрязняющих веществ
В - общая численность промышленно- производственного персонала n - количество выбрасываемых веществ n=7
Bij =900чел.=09 тыс. чел. – численность работников цеха
3емлеемкость: цеха - В=4600 чел.
Предприятия - Ai=00604 тыс. га
Водопотребления: цеха - аij=0709 млмгод
Предприятия - Aj=l4 мдн. мгод
Выбросы ЗВ в атмосферу: цеха - аij=540 т.год
Предприятия - Аi=1400т.год
Сброс сточных вод: цеха - aij=7000 т.год
Предприятия - Ai=25000 т.год
Значение ПДК: бензин - с = 0195 мгм
ацетон - с = 0014 мгм
Обьем выбросов: бензин 1000 м
Значение концентраций выбрасываемых веществ:
Иэi =(17)×068×(4609)×(0000700604)+(070914)+(5401400)+
Полученное значение индекса экологической опасности означает что проектируемый цех относится к району с незначительной техногенной нагрузкой.
4 ПРОИЗВОДСТВЕННАЯ БЕЗОПАСНОСТЬ.
МЕТЕРОЛОГИЧЕСКИЕ УСЛОВИЯ И ИХ НОРМИРОВАНИЕ
Метеорологические условия в производственных условиях определяются
следующими параметрами:
Температурой воздуха
Относительной влажностью
Скоростью движения воздуха на рабочем месте.
При высокой температуре воздуха в помещении кровеносные сосуды кожи расширяются при этом происходит повышенный приток крови к поверхности тела и теплоотдача в окружающую среду значительно увеличивается. При температуре окружающего воздуха и поверхностей оборудования и помещений 30-35° отдача теплоты конвекцией и излучением в основном прекращается. При более высокой температуре воздуха большая часть теплоты отдается путем испарения с поверхности кожи. В этих условиях организм теряет определенное количество влаги а вместе с ней и соли играющие важную роль в жизнедеятельности организма.
При пониженной температуре окружающего воздуха реакция человеческого организма иная - кровеносные сосуды кожи сужаются приток крови к поверхности тела замедляется и отдача теплоты конвекцией и излучением уменьшается.
Влажность воздуха оказывает важное влияние на терморегуляцию организма. Повышенная влажность (φ>85%) затрудняет теплорегуляцию из-за снижения
испарения пота а слишком низкая (Р20%) вызывает пересыхание слизистых оболочек дыхательных путей. Оптимальные величины относительной влажности составляют 40-60%.
Движение воздуха в помещениях является важным фактором влияющим на тепловое самочувствие человека.
В жарком помещении движение воздуха способствует увеличению отдачи теплоты организмом и улучшает его состояние но оказывает неблагоприятное воздействие при низкой температуре воздуха в холодный период года.
Для проектируемого механического цеха определим следующие допустимые метеорологические условия которые определяются в зависимости от периода года.
Для поддержания оптимальной температуры на рабочих местах в проектируемом цехе предусмотрены батареи отопления (для зимнего периода) и кондиционер (для летнего периода).
5 СИСТЕМА ВЕНТИЛЯЦИИ
Вредные вещества находящиеся в воздухе производственных помещений через дыхательные пути пищевой тракт могут попасть в организм человека и при определенных условиях вызвать острое или хроническое отравление. В данном проектируемом цехе вредными веществами загрязняющими воздух являются пары и аэрозоли от СОЖ и масел. Предельно допустимая концентрация данных веществ не должна превышать 100 мгм.
Задачей вентиляции является обеспечение чистоты воздуха и заданных метеорологических условий в производственных помещениях.
По способу перемещения воздуха вентиляция бывает:
С естественным побуждением
С механическим побуждением
Смешанная вентиляция
В зависимости от того для чего служит система вентиляции
Приточная вентиляция
Приточно-вытяжная вентиляция.
По месту действия вентиляция бывает:
В качестве мер по очистке воздуха приняты:
-устройство общеобменной приточной вентиляции действие которой основано на разбавление загрязненного нагретого влажного воздуха помещения свежим воздухом до допустимых норм;
-проведение систематических проветриваний помещений и медицинских осмотров.
6 ПРОИЗВОДСТВЕННОЕ ОСВЕЩЕНИЕ
Основная задача освещения на производстве - создание наилучших условий для видения. При освещении производственных помещений используют естественное освещение создаваемое светом неба искусственное осуществляемое электрическими лампами.
В проектируемом механическом цехе будем использовать совмещенное освещение при котором в светлое время суток недостаточное по нормам естественное освещение дополняется искусственным.
Осветительная система должна отвечать следующим требованием:
Освещенность на рабочем месте должна соответствовать характеру зрительной работы.
Необходимо обеспечить достаточно равномерное распределение яркости на рабочей поверхности а также в пределах окружающего пространства. Светлая окраска потолка стен производственного оборудования способствует созданию равномерного распределения яркости в поле зрения.
На рабочей поверхности должны отсутствовать резкие тени. Тени смягчаю применяя светильники со светорассеивающими молочными стеклами.
В поле зрения должна отсутствовать прямая и отраженная блескость. Блескость ослабляют уменьшением яркости источников света правильным выбором защитного угла светильника увеличением высоты подвеса светильников правильным выбором направления светового потока на рабочую поверхность заменой блестящих поверхностей матовыми.
Величина освещенности должна быть постоянной во времени. Требование достигается стабилизацией питающего напряжения применение специальных схем включения газоразрядных ламп.
Следует выбирать оптимальную направленность светового потока что позволяет в одних случаях рассмотреть внутренние поверхности деталей в других - различить рельефность элементов рабочей поверхности.
Следует выбирать необходимый спектральный состав света.
Все элементы осветительных установок должны быть достаточно долговечными электробезопасными а также не должны быть причиной возникновения пожара или взрыва.
Установка должна быть удобной и простой в эксплуатации отвечать требованиям эстетики.
В проектируемом цехе используются следующие виды зрительных работ: Наивысшая точность (2 разряд) - ОТК: минимальный размер 014 мм.
-разряд зрительной работы - 1
-подразряд зрительной работы - в
-контраст объекта различия с фоном - средний
-характеристика фона - светлый
-освещенность - система комбинированная
-освещение - разрядные лампы -3000
Высокой точности (3 разряд) -остальные виды работ
-разряд зрительной работы - 3
- освещение - разрядные лампы -400
Общее освещение должно быть не менее Е= 300 лк
Комбинированное освещение наряду с общим включает местное освещение рабочего места. Для искусственного освещения помещений будем использовать в основном лампы накаливания в том числе галоидные и галогенные лампы. Срок службы этих ламп до 3000 часов световая отдача доходит до 40 ммВт спектр излучения близок к естественному. Электрический светильник представляет собой совокупность источника света и осветительной арматуры. Для ламп накаливания наиболее распространенными являются светильники прямого света. В проектируемом цехе используем светильники УПД УПП-15 ВЗГ.
Система общего искусственного освещения выполнена подвесными лампами размещенными параллельно светоприемникам и равномерно по потолку.
7 ЭЛЕКТРОБЕЗОПАСНОСТЬ
Цех механической обработки относится к категории помещений с повышенной опасностью от поражения электротоком. Все станки оборудование машины используемые в цехе являются потребителями электроэнергии и представляют опасность для человека. При обслуживании и работе на станках могут возникать следующие причины поражения человека электротоком:
-случайное прикосновение к токоведущим частям находящимся под
-появление напряжения на металлических конструктивных частях
электрооборудования в результате повреждения изоляции
-появление напряжения на отключенных токоведущих частях на
которых работают люди вследствие ошибочного включения установки.
В проектируемом цехе предусмотрены следующие основные меры защиты от поражения электротоком:
-недоступность токоведущих частей электроустановок для случайного
прикосновения обеспечена изоляцией токоведущих частей и их
-электрическое разделение частей - разделение электросети на
отдельные электрически не связанные между собой участки с помощью
специальных разделяющих трансформаторов
-при работе с ручным переносным электроинструментом применяется
малое напряжение ( 42В)
-также применяется двойная изоляция - это электрическая изоляция
состоящая из рабочей и дополнительной изоляции
защитное заземление - преднамеренное электрическое соединение с
землей металлических токоведущих частей которые могут оказаться
Цель расчета - определить число и длину вертикальных элементов длину горизонтальных элементов (соединительных шин) и разместить заземлитель на плане электроустановки исходя из регламентированных величин допустимого сопротивления заземления допустимого напряжения прикосновения и шага или максимального потенциала заземления.
Выберем вертикально - фрезерный станок модели 6А12П мощностью 55 кВт который имеет напряжение питания 380В. Исполнение питающей сети - трехфазная четырехпроводная с глухозаземленной нейтралью.
Для контура заземления предполагается использовать трубы ø=40 мм длинной 2м заглубление 1м.
Полоса связи- стальная.
Ширина полосы - 30м.
Величина сопротивления заземления для электроустановок до 1000В при мощности менее 100 кВт не должна превышать 4 0м.
Удельное сопротивление грунта ρ = 1×10² Ом×м.
Число заземлителей – 12.
Расстояние между заземлителями – 35 м.
Расчетное сопротивление одиночного вертикального заземлителя:
l = 2 м – длина заземлителя.
r0 = 002 м – радиус трубчатого заземлителя.
t = 2 м – расстояние от поверхности до середины заземлителя.
Сопротивление соединительной полосы
= 115м - длина полосы;
В = 003 м - ширина полосы;
Сопротивление контура.
Сопротивление расчетного контура меньше установленной величины (40Ом) таким образом условиям безопасности будет удовлетворять контур из 12 труб и соединительной полосы 1=385 м.
9 ПОЖАРНАЯ БЕЗОПАСНОСТЬ
Под пожарной безопасностью понимают неконтролируемое горение наносящее материальный ущерб и (или) приводящий к человеческим жертвам. На предприятиях возникновение пожаров связано с неисправностью оборудования электроустановок контрольно-измерительных и защитных установок или приборов а также с неосторожностью обслуживающего персонала при пользовании огнем и при проведении различного рода огневых работ.
Часто причинами возникновения пожаров являются нарушения герметичности аппаратов и коммуникаций в результате износа отдельных деталей или превышение норм давления и температуры. В таких случаях появляется возможность образования горючей среды что при наличии источника зажигания приводит к возникновению пожара особенно на тех технологических установках приборах и аппаратах в которых применяют легкогорючие жидкости и газы.
Определение категории взрывной и взрывопожарной безопасности. В соответствии со СНиП 11-2-80 все производства делят по пожарной взрывной и взрывопожарной опасности на 6 категорий.
В проектируемом цехе обрабатываются негорючие вещества и материалы в холодном состоянии. Поэтому цех соответствует категории Д. Самые распространенные источники возгораний.
Искры возникающие при коротких замыканиях перегрузках электросетей появлении больших переходных сопротивлений и т. п.
Токи короткого замыкания которые могут достигать нескольких десятков и сотен тысяч ампер что приводит к образованию электрической дуги с температурой до 4000°С и плавлению проводов перегреву токопроводящих частей воспламенения изоляции проводов а также сгораемых предметов веществ и материалов находящихся поблизости. Короткие замыкания сопровождаются резким падением напряжения в электросетях полным расстройством электроснабжения и остановкой машин и оборудования что приводит к порче продукции пожарам и взрывам. Короткие замыкания могут возникать при неправильном прокладывании и монтаже электросетей износе старении и повреждении изоляции электропроводов и оборудования.
Перегрузки электрических сетей машин и аппаратов возникают при токовой нагрузке которая в течение длительного времени превышает величины допускаемые нормали. Перегрузки возникают также в результате нарушения нормативных требований при проектировании электроснабжения несоблюдение правил эксплуатации а также понижения напряжения в питающей сети что приводит к возрастанию тока в обмотках электродвигателей.
Тепло выделяющееся при трении скольжения подшипников дисков ременных передач а также при выходе газов под высоким давлением и с большой скоростью через малые по диаметру отверстия.
Искры образующиеся при ударах некоторых металлических деталей друг о друга о камень и т.п.
Искровые разряды статического электричества.
Также причинами возникновения пожаров могут быть пламя лучистое тепло а также искры образующиеся при эксплуатации огне действующих производственных установок и отопительных приборов электро- и газосварочных аппаратов и т.п.
Возникновение пожара можно предотвратить путем осуществления соответствующих инженерно-технических мероприятий при проектировании с эксплуатации технологического оборудования энергетических транспортных и санитарно- технических установок с помощью строго соблюдения существующих правил и требований пожарной безопасности а также устранения где это осуществимо опасности образования горючей среды или появления тепловых источников способных воспламенить эту среду.
В настоящее время выбрано стандартное определение понятия пожарной безопасности как состояние объекта при котором с установленной вероятностью исключается возможность возникновения и развития пожара воздействия на людей опасных факторов пожара (ОФП) а также обеспечивается защита материальных ценностей (ГОСТ12.083-81 и ГОСТ 12.1004-85)
Пожарная безопасность объекта и его элементов должна предусматриваться как при эксплуатации так и в случае реконструкции и ремонта или аварийной ситуации.
Вся совокупность средств и деятельности для достижения пожарной безопасности объекта разделяется на три составных взаимосвязанных направления:
.Система предотвращения пожара (СПП).
Система противопожарной безопасности (СПЗ).
Организационно-технические мероприятия по обеспечению пожарной безопасности.
10 СРЕДСТВА ПОЖАРОТУШЕНИЯ И СРЕДСТВА
СИГНАЛИЗАЦИИ О ПОЖАРЕ
В практике тушения пожаров наибольшее распространение получили следующие принципы прекращения горения:
.Изоляция очага горения от воздуха или уменьшения концентрации кислорода до значения при котором не может происходить горение. 2.Охлаждение очага горения ниже определенных температур.
Интенсивное торможение скорости химической реакции в пламени. 4.Механический срыв пламени в результате воздействия на него сильной струи газа или воды.
создание условий огнепреграждений.
Основными средствами пожаротушения в механическом цехе являются огнетушители.
Огнетушители по виду огнетушащих средств:
Наиболее эффективными являются углекислотные огнетушители предназначенные для тушения возгораний различных материалов и установок напряжением до 1000В ручные ОУ-2А ОУ-5 ОУ-8. Также в цехе должны быть: гидранты и пожарные рукава ящики с песком.
Пожарная сигнализация является одним из основных условий обеспечения пожарной безопасности в машиностроении так как позволяет оповестить дежурный персонал о пожаре и месте его возникновения.
Проектируемый механический цех оборудован телефоном кнопками оповещения о пожаре а также системой тепловых извещателей принцип действия которых состоит в изменении электропроводности тел контактной разности потенциалов ферромагнитных свойств материалов и т.д.
Необходимо особое внимание уделить мероприятиям режимного характера -запрещение курения в не установленных местах производство сварочных и других работ связанных с огнем в пожаробезопасных помещениях.
Предлагается ввести регулярный осмотр электрооборудования на наличие неисправностей.
Используются также следующие меры пожаробезопасности:
-В цехе предусмотрено достаточное количество аварийных выходов
-Огнестойкость здания по 2 классу
-Наличие пожарной сигнализации
-Строгий контроль за перемещением ЛВЖ и ГЖ на производстве
-Для тушения ЛВЖ предусмотрены пеногенераторы типа ПО-1С ПО-11
-Также в наличии ручные огнетушители ОУ-2А ОУ-5 ОУ-8 гидранты и
пожарные рукава ящики с песком.
11 ТРАВМОБЕЗОПАСНОСТЬ
В данном механическом цехе используются станки с ЧПУ универсальные и специальные станки.
При механической обработке на станках на высоких скоростях резания стружка разлетается на значительное расстояние (до 5м). Металлическая стружка имеет высокую температуру и большую кинематическую энергию представляет серьезную опасность для травм глаз. Также образуется большое количество сливной стружки которая отлетая может быть причиной несчастных случаев. Для улавливания и отвода отлетающей стружки применены специальные стружкоотводчики установленные на суппорте станка и закрывающие зоны резания. Кроме того безопасность обеспечивается дроблением сливной стружки в процессе точения что достигается путем придания передней грани резца криволинейной формы (токарно-расточной и подрезной резцы) и путем напайки уступа (стружколома) на проходной резец.
Опасные зоны технологического оборудования отделены заградительными устройствами что устраняет возможность случайного прикосновения человека.
Конструкция и расположение рычагов управления исключает возможность случайного включения выключения или переключения их во время работы.
3.СПЕЦИАЛЬНАЯ ЧАСТЬ.doc
1 АВТОМАТИЗИРОВАННАЯ ПОДГОТОВКА УП
Производится с применением систем автоматизированного
программирования (САП).
САП – это комплекс технических программных языковых и информацион-ных средств осуществляющих преобразование данных чертежа детали и ее обработки в коды СЧПУ.
Технические средства.
Процессор – это программный модуль предназначенный для решения общих геометрических а иногда и технических задач.
Постпроцессор – это программное изделие предназначенное для преобразования команд СLDATA в кадры УП с адаптацией к конкретному станку с ЧПУ.
Входной язык – это проблемно – ориентированный язык (ПОЯ).
Промежуточный язык – на нем описысаются данные передаваемые от процессора к постпроцессору.
Последовательность автоматизированной подготовки УП.
При формировании исходных данных в диалоговом интерактивном режиме имеют место элементы входного языка САП имея ввиду конструктивный элемент (КЭ) построенный в графическом редакторе САП и используемом при дальнейшем формировании УП. Поэтому говорят что исходные данные о КЭ представляют на геометрическом входном языке.
САП низкого уровня решает в основном геометрические задачи (расчет проектировки инструмента) и реализует подробные указания о составе УП.
САП среднего уровня позволяет дополнительно решать на ЭВМ технические задачи выбора последовательности проходов по заданным обобщенным схемам обработки отдельных конструктивных элементов.
САП высокого уровня дополнительно позволяет решать задачи технических переходов инструментальных наладок и задачи расчета оптимальных режимов резания.
Основные функции процессора и постпроцессора.
Несмотря на многообразие функций разных процессоров можно построить упрощенную схему процессоров которая правильно отражает этапы его работы.
Блок трансляции организует считывание исходных данных (ИД) контроль их корректности и преобразует ИД из символической формы во внутримашинные представления.
Блок СLDATA формирует упорядоченный массив который включает данные о траектории инструмента а также технические параметры обработки.
Обычно постпроцессор имеет инвариантную и специализированную части.
Инвариантная часть является универсальной при формировании УП для разных станков с ЧПУ.
К типовым функциям постпроцессора относятся:
Считывание данных подготовленных процессором.
Проверка по техническим ограничениям станка.
Формирование команд на перемещение с учетом дискретной обработки перемещений.
Формирование команд обеспечивающих коррекцию инструмента.
САП с диалогово – интерактивным входом.
К ним относятся: ADEM COMPAS SIMATRON.
Создание геометрической модели обрабатываемой детали. Фактически информация о конструкции обрабатываемой детали представлена на геометрическом входном языке.
Создание последовательности технических объектов (ТО).
Запуск программного модуля процессора и расчет траектории инструмента.
Моделирование обработки просмотр эквидистанты и CLDATA.
Запуск программного модуля постпроцессора получение УП просмотр УП.
ТО содержит информацию о конструкции и технологии обработки одного конструктивного элемента (КЭ) и этот ТО обозначается в следующем виде:
К ТО также относятся дополнительные технические описания.
ОБЛ область – определяет припуск снимаемый при токарной обработке ограничивается контурами детали и заготовки.
Задаются из панели параметров выбранного конструктивного элемента.
ПЛОСК – координата Z плоскости привязки.
ГЛУБ – определяет положение плоскости дна.
ПХХ – координата Z плоскости X.X.
Эти параметры определяют положение инструмента по отношению к детали по оси Z.
Сверление зенкерование развертывание нарезание резьб врезное фрезерование.
- - - - - перемещение по ускоренной подаче
Обычное фрезерование.
РАЗВ – развертывание
Параметр НЕДОБЕГ отсчитывается от плоскости привязки при врезном фрезеровании и при выполнении сверлильных и прочих ТП.
При обычном фрезеровании параметр ПЕРЕБЕГ отсчитывается от плоскости дна.
При описании ТП и выборке массивов необходимо принять решение о схеме обработки.
Виды участков подхода и отхода инструмента:
При линейном подходе можно обеспечить плавное врезание но в этом моменте возникают проблемы с реализацией радиусной коррекции т.е. блок УЧПУ не может по заложенному в него алгоритму корректно рассчитать поправки при обработке радиусной коррекции.
2 МЕТОДЫ ВЫСТАВЛЕНИЯ РАБОЧИХ ОРГАНОВ (РО)
Перед началом отработки управляющей программы (УП) необходимо инструмент (т.Би) совместить с т.Н заданной технологом – программистом в системе координат детали при этом РО (т.Б и Б) оказывается в некоторых точках координатного пространства ( ) которые назовем исходными (ИТ).
При полном базировании станочного приспособления выставление т.Би в т.Н можно осуществить без помощи специальных установов. Для этого расчетным путем определяются координаты ИТ отсчитываемые от соответствующих нулевых точек 0 и 0 затем в штатном режиме выхода в ноль РО перемещаются в нулевые точки 0 и 0 а затем в штатном режиме ручного ввода данных отрабатываются перемещения РО на величины определенными рассчитанными значениями координат ИТ. (Например если рассчитанная координата ИТ равна 8375 мм то отрабатывается команда X+008375).
X Y Z – координатные оси рабочих органов (РО) станка;
0 - нулевые точки РО;
Б Б - базовые точки РО;
XД YД ZД 0Д – система координат детали (программы);
XC YC ZC 0C – система координат станка (расчетная);
ZИ 0И – система координат инструмента (однокоординатная система);
П – базовая точка станочного приспособления;
Н – точка начала обработки;
БИ – базова точка инструмента.
3 РАСЧЕТ КООРДИНАТ ИСХОДНЫХ ТОЧЕК.
Предварительно координаты точек БИ и Н принадлежащих различным координатным системам переводятся в абсолютную расчетную систему координат XС YC ZС 0С по следующей схеме:
БИ – 0И – Б – 0 – 0С;
H – 0Д – П - Б - 0 - 0С.
Реализуем эту схему получим:
X0СБИ = X0ИБИ + XБ0И + X0Б + X0C0
Y0СБИ = Y0ИБИ + YБ0И + Y0Б + Y0C0 (1)
Z0СБИ = Z0ИБИ + ZБ0И + Z0Б + Z0C0
X0СН = X0ДН + XП0Д + XБП - X0Б + X0C0
Y0СН = Y0ДН + YП0Д + YБП - Y0Б + Y0C0 (2)
Z0СН = Z0ДН + ZП0Д + ZБП - Z0Б + Z0C0
Т.к. базовая точка БИ рассматривается в однокоординатной системе то в (1) слагаемые X0ИБИ XБ0И Y0ИБИ и YБ0И равны нулю. Также равны нулю слагаемые X0Б и Y0Б так как РО – шпиндельная головка координатных перемещений относительно осей X и Y не имеет. (Поэтому на рисунке эти оси не показаны).
Другой РО – стол не имеет координатного перемещения по оси Z.
Следовательно в (2) слагаемое Z0Б равно нулю.(На рисунке ось Zне показана).
Математическое условие совмещения т.БИ с т.Н имеет следующий вид:
Реализуя условие (3) получим:
X0Б = X0ДН + XП0Д + XБП + X0C0 - X0C0
Y0Б = Y0ДН + YП0Д + YБП + Y0C0 - Y0C0 (4)
Z0Б = Z0ДН + ZП0Д + ZБП – Z0ИБИ – Z0C0
Выражения (4) определяют искомые координаты исходных точек.
Поэтому перепишем (4) в следующем виде но при этом учтем что
(Из условия расположения нулевых точек 0 и 0)
XО = X0ДН + XП0Д + XБП
YО = Y0ДН + YП0Д + YБП
ZО = Z0ДН + ZП0Д + ZБП – Z0ИБИ – Z0C0.
Искомые координаты исходных точек.
XО = - 25 + 0 + 0 = - 25 (мм)
YО = 0 + 0 + 0 = 0 (мм)
ZО = 25 + 0 + 90 – (-100) -200 = 15 (мм)
7.ЛИТЕРАТУРА.doc
Семенченко И.И. Нагюшин В.М. Сахаров П.Н. Проектирование металлорежущих инструментов. Машиз.1962г.
Руководство по курсовому проектированию металлорежущих инструментов: Учебное пособие для вузов по специальности «Технология машиностроения металлорежущие станки и инструменты» Под общей редакцией Г.Н. Кирсанова М.: Машиностроение 1988г. 288ст.
Справочник технология машиностроения в 2-х томах. Под редакцией А.Г.Косиловой и Р.К.Мещерякова. – 4-е издание переработанное и дополненное. М.: Машиностроение 1986г.656стил.
Егоров М.Е. и др. Технология машиностроения. Учебник для вузов. Издание 2-е дополненное. М.: «Высшая школа»1976г.
режимы резания труднообрабатываемых материалов: Справочник Я.М.Гуревич М.В. Горохов В.И. Захаров и др. 2-е издание переработанное и дополненное. М.: Машиностроение1986г. 240стил.
Методические указания к дипломному проектированию для студентов 6-го курса специальности 12.01 «Технология машиностроения» Составили Н.А. Ухватов Н.Ф. Пименова Ш.А. Бурчаков П.О. Кувшинов А.С. Ляшев В.М. Белоног КАИ Казань1989г.32ст.
Руководство по эксплуатации Д7690-710-00-000РЭ КМПО. 1996г.
ГОСТ 7293-85. Чугун с шаровидным графитом для отливок.
ГОСТ 26645-85. Отливки из металлов и сплавов. Допуски размеров массы и припуски на механическую обработку.
Егоров Н.Е. и др. Технология машиностроения. Учебник для вузов. Издание 2-е дополненное. М.: «Высшая школа»1976г.
Орлов П.И. Основы конструирования. М: «Машиностроение»1972г.525ст
Нефедов Н.А. Осипов К.А. Сборник задач и примеров по резанию металлов и режущему инструменту. Учебное пособие для техникумов по предмету «Основы резания металлов». 5-е издание переработанное и дополненное. М.: «Машиностроение»1990г.448ст.ил.
2.КОНСТРУКТОРСКАЯ ЧАСТЬ.doc
ПРОЕКТИРОВАНИЕ ПРИСПОСОБЛЕНИЯ.
В данном дипломном проекте разрабатывается автоматизированное приспособление зажимное для операции 040(Фрезерование). Приспособление позволяет во время выполнения фрезерования закрепить деталь с помощью пневмокамеры двухстороннего действия которая состоит из диафрагмы корпуса и основания. Пневмопривод позволяет сократить вспомогательное время обеспечивает необходимое усилие зажима.
Принцип действия приспособления заключается в следующем:
Установить заготовку в плиту фиксирующую(5) и фиксатор(9).
Подать сжатый воздух через ниппель «В» в вневмокамеру. Тем самым достигается перемещение диафрагмы (1) и штока (7) вниз. Что приводит посредством рычажного механизма к зажиму детали прижимами (8).
После выполнения операции 040 подать сжатый воздух через ниппель «Г» в вневмокамеру. Тем самым достигается перемещение диафрагмы (1) и штока (7) вверх. Что приводит к освобождению детали. В это время воздух из верхней полости пневмокамеры полости через ниппель «В» поступает в распределительный кран и уходит в атмосферу.
Вынуть заготовку из приспособления.
Диафрагма входящая в состав пневмокамеры состоит из пластины корпуса и основания. Пластина зажимается между корпусом и основанием с помощью заклепок.
Тарельчатые пластины изготавливают в пресс-формах из четырехслойной ткани бельтинг с нанесенной с обеих сторон маслостойкой резиной.
Расчетный диаметр D=70 мм.
Толщину диафрагмы h выбирают в зависимости от D:
Диаметр корпуса и основания d принимают для резинотканевых диафрагм d=07D:
Расчет пневмопривода.
Основными величинами определяющими работу пневмокамеры является сила Q на штоке и длина рабочего хода штока.
В пневмокамерах усилие на штоке меняется при перемещении штока от исходного положения в конечное. Оптимальная длина хода штока пневмокамеры при котором сила Q изменяется незначительно зависит от расчетного диаметра D диафрагмы ее толщины h материала формы и диаметра d опорного диска диафрагмы.
Если перемещать шток пневмокамеры на всю длину рабочего хода то в конце хода штока вся энергия сжатого воздуха будет расходоваться на упругую деформацию диафрагмы и полезное усилие на штоке снизится до нуля. Поэтому используют не всю длину рабочего хода штока диафрагмы только ее часть чтобы сила на штоке в конце хода составляла 80-85% силы при исходном положении штока.
Приближенно сила Q на штоке диафрагменной пневмокамеры двустороннего действия при подачи сжатого воздуха в бесштоковую полость:
В исходном положении штока:
Где р=4 (мПа) - давление сжатого воздуха.
После перемещения штока на длину 03D (21мм):
Сила Q на штоке при подаче сжатого воздуха в штоковую полость:
В исходном положении:
d1=10(мм) – диаметр штока.
После перемещения на длину 03D (21мм)
Расчет усилия зажима.
Основное уравнение равновесия зажимного приспособления:
Q = 7065(H) – рабочее усилие на штоке пневмопривода.
Р – усилие зажима приспособления.
f = 016 – коэффициент потери на трение в звеньях зажимного устройства.
l1 = 26 (мм) – вертикальный размер (плечо) фиксатора.
l2 = 11 (мм) – горизонтальный размер (плечо) фиксатора.
Р = (Q×l2×f)(l1×2) = (7065×26×016)(11×2) = 1336 (H).
Конструкция проектируемого зажимного приспособления позволяет осуществить базирование заготовки с использованием относительного малого усилия зажима.
Таким образом давления сжатого воздуха
р= 4(мПа) вполне достаточно для обеспечения заготовке надежное закрепление в приспособлении во время выполнения операции 040.
Расчет точности обработки заготовок в приспособлении.
Различают три показателя точности:
Точность выполнения размеров.
Взаимного расположения поверхностей.
При анализе точности обработки заготовок наиболее важным является анализ точности операционных размеров выполняемых в приспособлениях.
В результате выполнения технологической операции суммарная погрешность рассматриваемого размера ΔΣ не должна превышать заданного допуска:
Δо = 0002 (мм) – сумма погрешностей статической и динамической настройки.
- погрешность установки
Δ = 0035(мм) – погрешность базирования.
Δзакр =100(мкм) – погрешность закрепления заготовки при установе в осевом направлении для обработки на станках.
Δизг =0044(мм) – погрешность вызываемая неточностью изготовления приспособления.
Δизн =0(мм) – погрешность обусловленная износом элементов приспособления.
Δуст.пр. =0 05(мм) – погрешность обусловленная установкой приспособления в станке.
Следовательно условие точности выполняется.
2ПРОЕКТИРОВАНИЕ РЕЖУЩЕГО ИНСТРУМЕНТА.
В данном дипломном проекте разрабатывается прорезной (канавочный) резец для операции 020(Токарная). Особенностью этих резцов то что форма режущей кромки должна точно воспроизводить профиль канавки. Прорезные резцы изготовляют прямыми. Так как канавки обычно имеют небольшую ширину то и режущую кромку резца делают узкой что создает опасность его поломки. Для повышения прочности прорезных резцов высоту их головки делают в несколько раз больше ширины режущей кромки. С этой же целью головке придают небольшой передний уклон или делают радиусную (криволинейную) заточку. Прорезные резцы изготовляют обычно с неразьемным креплением: державку делают из углеродистой стали а пластинку привариваемую к державке – из быстрорежущей стали или из твердого сплава. (В нашем случае используется твердый сплав ВК8).После определения размеров резца необходимо проверить выбранное сечение державки на прочность и жесткость. Для этого определяют силы резания и силы действующие на резец.
Определение силы резания.
Значение подачи скорректировано согласно паспортным данным станка.
где Ср = 300 – постоянная
xyn – показатели степени
х = 10; у = 075; n = 0
Кр – поправочный коэффициент
где K- коэффициент учитывающий влияние качества обрабатываемого материала на силовые зависимости.
= 10 - коэффициент учитывающий влияние главного угла.
= 10 - коэффициент учитывающий влияние переднего угла
= 10 - коэффициент учитывающий влияние угла наклона главного лезвия
Определение сил действующих на резец.
Определим реакцию опоры А.
ΣМ(А)= -МА - Р×l = 0
МА = -Р×l = -679×50 = -33950 (Н×мм)
Определим эквивалентный момент.
Определим размер поперечного сечения державки.(h = b)
Принимаем h = b = 6 (мм).
3ПРОЕКТИРОВАНИЕ МЕРИТЕЛЬНОГО ИНСТРУМЕНТА.
В данном дипломном проекте разрабатываем гладний калибр. Калибр это измерительное средство не имеющая шкалы которым проверяют годность действительных размеров детали.
Достоинства: простота и быстрота замеров.
Недостаток: выгодно применять только в массовом и серийном производстве так как для каждого размера с определенным полем допуска нужен свой калибр.
Предельные и нормальные.
Предельными проверяют находится ли действительный размер в номинальном допуске.
У предельных калибров два размера: проходной и непроходной.
Нормальными калибрами проверяют соответствие действительного размера номинальному.
В производстве применяют предельные калибры.
Бывают пространственные калибры ими проверяют взаимное расположение поверхностей.
По назначению бывают рабочие проходные и рабочие непроходные.
Контрольные калибры.
Контрольными калибрами проверяют рабочие калибры.
К – ПР проверяют Р – ПР
К – НЕ проверяют Р – НЕ
К – Н проверяют Р – ПР
По конструкции скобы бывают:
Одно – и двухсторонние
По конструкции пробки бывают:
Для изготовления гладких калибров применяют следующие марки стали:
Ст15 Ст16 Ст20 У10А У15А Х ХГ.
Требования предъявляемые к гладким калибрам:
Высокая точность размеров рабочих поверхностей допуски очень малые;
Высокая износостойкость. Для этого шероховатость рабочих поверхностей выполняют по высокому классу точности рабочие поверхности подвергают цементации хромируют оснащают твердым сплавом.
Для сохранения размеров во времени проводят искусственное старение.
ГОСТ 853-81 устанавливает допуски на не точность изготовления для всех калибров а для Р – ПР допуск на износ.
Допуски калибров составляют 25 – 50 % от допуска размера проверяемой детали.
Исполнительные размеры пробки (задаются на рабочем чертеже с допуском в тело калибра):
Р – ПРисп = Р – ПРмах (-н)
Р – НЕисп = Р – НЕмах (-н)
Исполнительные размеры скобы (задаются на рабочем чертеже с допуском в тело калибра):
Р – ПРисп = Р – ПРмin (+н1)
Р – НЕисп = Р – НЕмin (+н1)
Н Н1 – допуск на пробку и скобу соответственно.
Маркируют калибры указывая:
Номинальный размер проверяемой детали.
Обозначение поля допуска размера проверяемой детали.
Отклонения в мм размера проверяемой детали.
Проведем расчет гладкого калибра – скобы на размер 32h11(-0.17)
Р – ПРисп = Р – ПРмin
Р – НЕисп = Р – НЕмin
Р – ПРн = dмax = 32 (мм)
Р – НЕн = dмin = 3183 (мм)
Определим минимальный рабочий проходной размер:
Р – ПРmin = dмax – Z1 – (Н12)
Н1 = 0011 – допуск на калибр – скобу.
Z1 = 0012 – отклонение середины поля допуска калибра Р – ПР от номинального размера.
dмax = 32 (мм) – максимальный проверяемый размер.
Р – ПРmin = 32 – 0012 – ( 00112 ) = 319825 (мм).
Определим минимальный рабочий непроходной размер:
Р – НЕmin = dmin – (Н12)
dmin = 3183 (мм) – минимальный проверяемый размер.
Р – НЕmin = 3183 – (00112) = 318245 (мм).
Из вышеприведенных расчетов следует:
Р – ПРисп = 319825 (+0011)
Р – НЕисп = 318245 (+0011)
4ПРОЕКТИРОВАНИЕ МЕХАНИЗМА ДЛЯ
АВТОМАТИЧЕСКОГО ЗАЖИМА ИНСТРУМЕНТА.
Способ зажима инструмента на станке с ЧПУ зависит от типа станка конструкции шпиндельного узла базирующих и зажимных элементов инструмента.
Для автоматического зажима фрезерной или расточной оправки с коническим хвостовиком устанавливаемой в шпинделе который расположен непосредственно в корпусе станка служит следующее устройство.
Оправка затягивается в шпиндель с помощью пакета тарельчатых пружин стержня и шарикового захвата а освобождается когда шток гидроцилиндра перемещаясь на право действует на стержень. Для обеспечения надежной работы шарикового захвата корпус гидроцилиндра может передвигаться вправо сжимая пружину до того момента пока гайка не упрется в гайку. Усилие зажима замыкается на шпинделе и не передается на его упорные подшипники. От выпадения шариков при отсутствии в шпинделе оправки предохраняет шток. Шариковое захватное устройство создает небольшое усилие зажима.
При применении автоматических устройств для зажима режущих инструментов необходимо знать усилия запрессовки и выпрессовки а также максимальное давление в соединении. При расчетах исходят из того что имеющие место погрешности углов уклона деталей соединения находясь в полях допусков конических инструментальных поверхностей оказывают существенное влияние на все рабочие характеристики соединения.
Порядок расчета следующий:
В соответствии со степенью точности деталей конического соединения по СТ СЭВ 178 – 75 определяют максимально возможную разность их углов уклона.
Находят максимально возможное осевое усилие Рз действующее на инструмент в процессе резания и представляющее собой фактическое усилие запрессовки.
Учитывают что при запрессовке инструмента в результате деформирования деталей возможны две схемы их взаимного положения:
Расчетная длина контакта
Зная углы αш и αx уклон отверстия в шпинделе и хвостовика инструмента вычисляют угол наклона конического соединения:
α = αх – (αx –αш)×(1 – )×(1- r²R²)
– коэффициент Пуассона.
r – большой радиус соединения.
R – радиус наружной поверхности шпинделя.
Приняв возможный в производственных условиях коэффициент трения при запрессовке fз = 03 (поверхности обезжирены) определяют условное осевое усилие при котором контакт имеется по всей поверхности соединения:
Е – модуль упругости материала шпинделя:
Если сила Р0 меньше максимально возможного усилия на инструменте Рз
В процессе резания то lр > lн и максимальное давление в соединении
При этом нормальная сила действующая на внутреннюю поверхность шпинделя:
Если же сила Ро больше усилия Рз на инструменте в процессе резания то lрlн и максимальное давление в соединении определяют из уравнения
Рв = 2N(fв соsα – sinα).
Коэффициенты трения при выпрессовке fв принимают в зависимости от состояния поверхностей и разности углов уклона деталей соединения.
5.РАСЧЕТ ПЛОЩАДЕЙ ЦЕХА.doc
План расположения оборудования выполняется в масштабе 1;100. Размещение оборудования отвечает разработанному технологическому процессу. Рабочие места расположены в порядке максимально имитирующем последовательность выполнения технологических операций. Станки начальной и конечной обработки примыкают к проездам один из которых питает цех заготовками а с помощью другого детали поставляются в цех сборки.
Ширина межцеховых проездов принята 6 метров для удобства подъезда крупногабаритного транспорта.
Ширина цехового проезда принята 5 метров для возможности разъезда 2-х встречно двигающихся эл. тележек.
Ширина пролета принята 36 метров. Т.к. является наиболее целесообразной величиной.
Длина пролета устанавливается из условия установа всего технологического вспомогательного оборудования и составляет 48 метров.
Принимается сетка колонн 36×12 метров.
Для обеспечения безопасности и удобства работы а также нормального обслуживания оборудования выдержаны монтажные расстояния между габаритами станков:
Между станками по фронту – 09 метра.
Между станками при расположении их в «затылок» - 18 метра.
От стен здания до тыльной стороны станка – 08 метра.
От стен здания до боковой стороны станка – 08 метра.
14ОПРЕДЕЛЕНИЕ КОЛИЧЕСТВА ОБОРУДОВАНИЯ И ПЛОЩАДЕЙ ВСПОМОГАТЕЛЬНЫХ ОТДЕЛЕНИЙ.
14.1Заточное отделение.
Заточка инструментов проводится в специально оборудованных заточных мастерских. Количество необходимых заточных станков определяется по количеству инструмента подлежащего заточке в год по числу переточек каждого инструмента до его полного износа и по времени заточки. Потребное количество заточных станков общего назначения составляет:
Заточные для резцов составляют 2 – 3 % от количества обслуживаемых станков.
×002 = 04 принимаем 1 станок.
Заточные для сверл составляют 1 – 2 % от количества обслуживаемых станков.
Универсально – шлифовальные составляют 05 – 1 % от количества обслуживаемых станков.
Универсально – заточные составляют 4 – 5 % от количества обслуживаемых станков.
Потребная площадь заточного отделения:
Fз = f0 × Sз = (10 - 12) × Sз = 10×4 = 40 (м²)
f0 – норма площади на один станок.
14.2Контрольное отделение.
В механическом цехе предусматривается площадь для пунктов ОТК. Площадь для оперативного контроля выделяется рядом с межоперационной кладовой. Выгораживаемая площадь для контрольных помещений составляет 1 – 3 % от площади занятой оборудованием цеха.
Fконтр. = 15688 ×003 = 47 (м²)
14.3Площадь ремонтных баз механика и энергетика цеха.
Площадь базы механика цеха рассчитываемая по нормам утвержденным ГлавНИИпроектом и Госстроем зависит от количества обслуживаемого оборудования.
Fмех. = 13×6×26 = 195 (м²)
Fэ. = 035× Fмех. == 035×195 = 68 (м²)
14.4Помимо ремонтной мастерской механика необходимо выделить площадь для склада запасных частей распределительной кладовой с заготовительным участком участка слесарей – монтажников участка энергетика.
14.5 Мастерская для ремонта приспособлений инструмента и инвентаря.
В механических цехах серийного производства где станки имеют сложную многоинструментальную оснаску и при обработке деталей применяются специальные приспособления организуется отдельная мастерская по ремонту приспособлений т. к. ремонтный цикл отличается от ремонтного цикла технологического оборудования. Кроме того ремонт приспособлений имеет некоторую специфику заключенную в том что должна быть сохранена взаимосвязь базовых и установочных поверхностей с поверхностями для направления и установки инструмента.
Площадь необходимая для участка определяется по формуле:
Fприсп. = (004 0014)×S×(17 22) = 004×36×17 = 25 (м²)
S = 36 – количество обслуживаемого оборудования.
С учетом площади для ремонта инвентаря площадь принимается:
14.6 Цеховой склад материалов и заготовок.
Для обеспечения бесперебойного снабжения станков необходимо предусмотреть цеховой склад материалов и заготовок.
Норма хранения заготовок – 8 дней.
Площадь цехового склада материалов и заготовок определяется по формуле:
Fсз = Qчерн×Е(260qkи)
Qчерн – масса материала и заготовок годового объема выпуска.
Qчерн = N×m = 8000×01 = 08 (т)
N = 8000 (шт.) – годовая программа выпуска.
m = 01 (кг) – масса одной заготовки.
Е = 6 – среднее количество рабочих дней в течение которых материалы и заготовки хранятся на складе до поступления на обработку.
q = 07 (м²) – средняя допустимая нагрузка на 1 м² полезной площади пола.
kи = 03 – коэффициент использования площади складирования.
Fсз = (08×7)(260×07×03) = 8 (м²)
14.7 Межоперационный склад.
Межоперационный склад полуфабрикатов проектируется для хранения обрабатываемых заготовок прошедших контроль после предыдущей обработки и ожидающих отправку на следующую операцию.
Площадь такого склада:
Fм.с. = Qг×К×t×i(260qkи)
Qг – масса годового объема выпуска деталей.
Qг = N×m = 8000×005 = 04 (т)
m = 005 (кг) – масса одной детали.
К = 115 – коэффициент учитывающий отходы металла на предыдущих операциях.
t = 2 – число рабочих дней межоперационного пролеживания.
i = 11 – среднее число доставок полуфабриката на склад.
q = 15 (кНм²) – средняя грузонапряженность.
kи ≤ 05 – коэффициент использования площади складирования.
Fм.с.= (04×115×3×11)(260×15×05) = 6 (м²)
14.8 Промежуточный склад.
Местом накопления и хранения окончательно обработанных деталей ожидающих поступления на сборку является промежуточный склад. Кроме того туда поступают детали со стороны необходимые для комплектования сборки узла.
Потребную площадь для промежуточного склада рассчитывают по формуле:
Fпр.с. = Q×t(260qkи)
Q – масса деталей и узлов годового объема выпуска подлежащих хранению.
Q = N×m = 8000×005 = 04 (т)
t = 12 – число рабочих дней запаса.
q = 10 40 (кНм²) – средняя грузонапряженность.
kи = 025 030 - коэффициент использования площади складирования.
Fпр.с.= (04×12)(260×10×025) = 8 (м²)
14.9 Инструментально- раздаточные кладовые (ИРК).
ИРК служат для снабжения рабочих и слесарей режущим и мерительным инструментом.
Нормы для расчета площади ИРК и других цеховых кладовых:
Приспособления для установки деталей на станках
(035 09)×36 = 035×36 = 133 (м²)
Приспособления и все виды инструментов
(075 19)×36 = 075×36 = 27 (м²)
Шлифовальные и полировальные круги
(045 07)×36 = 045×36 = 36 (м²)
Обтирочные и хозяйственные материалы
Fирк = 133 + 27 + 36 + 36 = 475 (м²)
14.10 Определение площадей и компоновка служебно – бытовых помещений.
В состав цеховых служебно – бытовых помещений входят объекты культурно – бытового назначения и объекты административно – технического назначения.
Цеховые объекты культурно – бытового обслуживания включают бытовые объекты (гардеробные с умывальниками душевые туалетные комнаты комната для курения устройства для снабжения питьевой водой столовые буфеты и комнаты для приема пищи медпункты) и объекты культурного обслуживания в цехе (помещения для отдыха и т.д.).
Определим площади служебно – бытовых помещений:
Санитарно – гигиенические:
Общественного питания:
Кльтурно - массовые:
Sвсп = 40 + 47 + 195 + 68 + 30 + 8 + 6 + 8 + 475 = 450 (м²)
Sуд.пр. = 3137613 = 25 (м²)
14.11 Выбор цехового транспорта.
Выбор вида транспорта производится исходя из характера изготовляемой продукции ее веса и размеров вида производства и формы организации труда количества перемещаемых грузов назначения транспорта.
В проектируемом цехе применим электрические тележки. Они просты в управлении бесшумны экологически чисты маневренны. Скорость эл. тележки 6 – 15 км в час. Для данного цеха возьмем 4 тележки.
Для транспортировки узлов и приспособлений применим подвесные лебедки.
95CNH.DOC
производственных рабочих по участку.
Рабочие вспомогательного производства
Рабочие вспомогательного производства без рабочих по обслуживанию и ремонту оборудования и технолог. оснастки наладчиков электриков
1ЗАГОТОВКА.cdw

Группа стали-М1 по ГОСТ 7505-89.
Степень сложности-С1.
Неуказанные предельные отклонения размеров:
Неуказанные величины уклонов 7
Допускаются местные дефекты в виде шлаковых включений
заковов и трещин не более 0
припуска на механическую
Величина смещения по поверхности разьема штампа
Величина остаточного облоя не более 0
Величина высоты заусенца на поковке по контуру обрезки
Отклонения по изогнутости от плоскостности и
параллельности не более 0
Местные дефекты должны быть удалены зачисткой.
Место маркировки-МК.
2ДЕТАЛЬ.cdw

Рекомендуемые чертежи
- 15.09.2016
- 07.09.2016
- 24.01.2023