Проект участка механического цеха на изготовление детали Вал-шестерня Л80.22.01.034


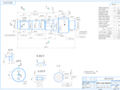
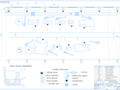
- Добавлен: 24.01.2023
- Размер: 616 KB
- Закачек: 3
Описание
Состав проекта
![]() |
![]() ![]() ![]() |
![]() ![]() ![]() ![]() |
![]() ![]() ![]() |
![]() ![]() |
![]() ![]() ![]() ![]() |
![]() |
![]() ![]() ![]() |
![]() ![]() ![]() |
Дополнительная информация
ТИТУЛЬНЫЙ ЛИСТ ТЕХПРОЦЕССА.doc
Александровский филиал ГОУ СПО Кизеловский горный техникум
ТЕХНОЛОГИЧЕСКИЙ ПРОЦЕСС
Чертеж.cdw

Сталь 40Х ГОСТ 4543-71
Улучшить НВ 241 . . . 285
Межосевое расстояние
операц карты.doc
Наименование операции
МД Профиль и размеры
Фрезерно-центровальная
Сталь 40Х ГОСТ4543-71
Штамповка ø152577х5524
Оборудование устройство ЧПУ
Обозначение программы
Фрезерно-центровальный
Установить и закрепить заготовку
Пневматические тиски с призматическими губками
Фрезеровать торцы выдерживая размеры
Торцовые фрезы Р6М5 ГОСТ 9304-69
Сверлить 2 отверстия одновременно выдерживая размеры
Центровочные сверла Р6М5 ГОСТ 14952-75
ГОСТ 3. 1404-86 Форма 2
Контролировать деталь
Штангенциркуль ШЦ-3 ГОСТ 169-88
Калибр-пробка ГОСТ 14822-69
ГОСТ 3. 1113-82 Форма 7
Штамповка ø152577х524
Код. Наименование операции
Обозначение документа
Код. Наименование оборудования
Горизонтально-ковочная машина
Фрезерно-центровальный станок мод. МР-73М
Токарно-винторезный станок мод. 16Б16Т1
Шпоночно-фрезерный станок мод. 692Р
Круглошлифовальная 1
Круглошлифовальный станок мод. 3М151Ф2
ГОСТ 3. 1113-82 Форма 1б
Наименование детали сб. единицы или материала
Горизонтальный шлицефрезерный станок мод. 5350
Зубофрезерный па мод. 5В312
Сверлильно-фрезерно-расточной станок мод. ИР800ПМФ4
-х кулачковый самоцентрирующий патрон вращающийся центр
Точить поверхности начерно последовательно
Резец проходной упорный Т5К10 ГОСТ 18879-73
Точить начисто последовательно 2 фаски и поверхности
Резец проходной упорный Т15К6 ГОСТ 18879-73
Точить канавку начисто
Резец канавочный Р6М5 ГОСТ 18883-73
Штангенциркуль ШЦ – 3 ГОСТ 169-88
Токарно-винторезный станок
Точить начисто последовательно 5 фасок и поверхности
Точить последовательно тонко поверхности
Резец проходной упорный Т30К4 ГОСТ 18879-73
Шпоночно-фрезерный станок
Фрезеровать шпоночный паз
Шпоночная фреза с цилиндрическим хвостовиком Т15К6 ГОСТ 6396-78
Шаблон для контроля шпоночного паза
Круглошлифовальный станок
Поводковый патрон невращающиеся центра
Шлифовать поверхность
Шлифовальный круг ГОСТ 2425-70
Скоба предельная односторонняя ø80К6 ГОСТ 18362-73
Горизонтальный шлицефрезерный
Поводковый патрон вращающиеся центра
Фрезеровать шлицы начерно выдерживая размеры и ТУ
Червячная фреза Р6М5 ГОСТ 8027-60
Фрезеровать шлицы начисто выдерживая размеры и ТУ
Калибр-кольцо шлицевое ГОСТ 18832-73
Сверлильно-фрезерно-расточной
Сверлить 2 отверстия последовательно
Сверло спиральное с цилиндрическим хвостовиком Р6М5 ГОСТ 10902-77
Сверлить 2 фаски последовательно
Нарезать резьбу в 2 отверстиях последовательно
Метчик Р6М5 ГОСТ 3266-81
Калибр-пробка ø102 ГОСТ 14822-69
Калибр-пробка резьбовая М12-7Н ГОСТ 17757-72
Точить начисто канавку
Скоба предельная односторонняя ø80h11 ГОСТ 18362-73
Скоба предельная односторонняя ø90h6 ГОСТ 18362-73
Круглошлифовальная 2
Шлифовать поверхности последовательно
Шлифовать поверхность последовательно
Скоба предельная односторонняя ø65К6 ГОСТ 18362-73
Скоба предельная односторонняя ø78а11 ГОСТ 18362-73
Вертикальный зубофрезерный
Фрезеровать зубья начерно выдерживая размеры и ТУ
Червячная фреза Р6М5 ГОСТ 9324-80 m=5
Фрезеровать зубья начисто выдерживая размеры и ТУ
Шаблон длины общей нормали
План участка.cdw

График загрузки оборудования
Условные обозначения
- конвеер для стружки
Наименование оборудования
Фрезерно-центровальный
Горизонтальный шлицефрезерный
Сверлильно-фрезерно-расточной
Диплом.doc
1 Выбор и обоснование способа получения заготовки 5
2 Определить припуски на заготовку эскиз заготовки 6
3 Назначить маршрут обработки детали 7
4 Выбрать оборудование режущий мерительный инструмент и приспособления на механические операции 7
5 Назначить режимы резания на механические операции 14
6 Рассчитать нормы времени на механические операции 32
Плано-механическая часть
1 Определить потребное количество станочного оборудования и коэффициент его загрузки 39
2 Определить количество рабочих-станочников вспомогательных рабочих и ИТР на участке 48
3 Определить площадь участка 52
Список литературы 54
Мне было дано задание разработать участок механического цеха на изготовление детали «Вал-шестерня Л80.22.01.034».детали 292кг.
Для этого мне надо выбрать способ получения заготовки и определить припуски на заготовку а также назначить маршрут обработки детали.
Также в моем проекте должен выбрать станки приспособления режущий вспомогательный и измерительный инструмент на каждую операцию. Потом рассчитать на заготовку все режимы резания и нормы времени.
Потом определить количество станочного оборудования и коэффициент его загрузки а также определить количество рабочих-станочников вспомогательных рабочих и ИТР. Затем рассчитать площадь участка.
Технологический раздел
Мне дал дан чертеж детали «Вал-шестерня Л80.22.01.034» который изготовлен из стали 40Х ГОСТ 4543-71 – эта легированная конструкционная качественная улучшаемая сталь где углерода 040% хрома не более 1%.
Масса детали 292 кг. Чертеж выполнен в масштабе 1:2. Габаритные размеры ø142977h11х540±14.
Деталь подвергается улучшению НВ 241 285.
Вал-шестерня имеет зубья m = 5 z = 26 штук шлицы
b-10х72х78а11х12d10 - это шлицы наружные диаметр внутренний – 72мм диаметр наружный – 78а11 шлицы шириной 12d10 мм и 10 шлиц шпоночный паз шириной 25 мм длиной 96 мм и глубиной 9 мм 2 центровочных отверстия ø5 длиной 63 мм а также 2 отверстия с резьбой М12-7Н – резьба внутренняя метрическая правая М12 шаг резьбы – 175 мм класс точности 7Н.
Поверхности ø65h8 длиной 35 мм ø78а11 длиной 82 мм ø80К6 длиной 58 мм ø80К6 длиной 60 мм подвергаются шлифованию до шероховатости Rа125.
Поверхности ø80h11 длиной 65 мм и ø90h6 длиной 80 мм подвергаются тонкому точению до шероховатости Rz20 и Rа25 соответственно.
На торец поверхности ø110 имеется допуск на торцевое биение не более 004 мм относительно базы Д которой является осевая линия.
На поверхности ø65h8 и ø80h8 имеется допуск на радиальное биение не более 004 мм относительно базы Д которой является осевая линия.
Поверхности ø90h6 и ø80К6 имеется допуск на радиальное биение не более 0025 мм относительно базы Д которой является осевая линия.
На поверхность ø142977h11 имеется допуск на радиальное биение не более 005 мм относительно базы Д которой является осевая линия.
На шпоночный паз имеется допуск на параллельность не более 005 мм и допуск на симметричность не более 003 мм относительно базы Д которой является осевая линия.
На зубья имеется допуск на колебание длины общей нормали 0036 мм допуск на радиальное биение зубчатого венца 006 мм и допуск на разность окружных шагов 002 мм.
1 Выбор и обоснование способа получения заготовки
Исходя из конструкции детали и ее массы 292 кг заготовку получаем штамповкой на горизонтально-ковочной машине. Форма заготовки приближена к форме детали что позволяет уменьшить расход материала.
2 Определить припуски на заготовку
Определяем предварительную массу заготовки:
где mд – масса детали кг
На ø65h8 Ra125 : 65+2(43+07)=75+24-12
На ø78а11 Ra125: 78+2(43+07)=88+24-12
На ø80К6 Rа125: 80+2(43+07)=90+24-12
На ø90h6 Rа25: 90+2(43+03)=992+24-12
На ø110 Rz40: 110+2(43+03)=1192+24-12
На ø142977h11 Rz20: 142977+2(44+04)=152577+25-15
На 540 Rz40: 540+2(58+04) =5524+4-2
На 95h12 Rz40: 95+124 = 1074 +24-12
Определяем объемы заготовки:
Vц = (D 24)h см3 (2)
где D – диаметр заготовки см
h – длина заготовки см
Vц 1=(314 7524)25=1104(см3)
Vц2 =(31488 24)82=4985(см3)
Vц3 =(314924)153=9729(см3)
Vц4 =(314992 24)8=618(см3)
Vц5 =(3141192 24)45=502(см3)
Vц6 =(314152577 24)1074=19627(см3)
Vц7 =(3149 24)6=3815(см3)
Общий объем заготовки:
Vц =Vц 1+ Vц 2+Vц 3 +Vц 4 +Vц 5 +Vц 6+Vц 7 см3 (3)
где Vц 1 Vц 2 Vц 3 Vц 4 Vц 5 Vц 6Vц 7– объемы детали см3
Vц =1104+49985+9729+618+502+19627+3815 = 5046 (см3)
где Vц – сумма объемов см3
mд=7.8145046 = 394 (кг)
mз - масса заготовки кг
Вывод: Так как среднесерийное производства Ким должно быть 065 08 в данном случае Ким = 075 он входит в данный диапазон то значит я правильно выбрал способ получения заготовки и допуски что позволит уменьшить расход материала при обработки.
3 Назначить маршрут обработки детали
Фрезерно-центровальная
Круглошлифовальная 1
Круглошлифовальная 2
4 Выбрать оборудование режущий мерительный инструмент и приспособления на механические операции
Фрезерно-центровальная
Станок: Фрезерно-центровальный станок модели МР – 73М
Диаметр обрабатываемой заготовки мм 25-125
Длина обрабатываемой заготовки мм 500-1080
Частота вращения фрезерного шпинделя обмин 125;180;250;355;500;712
Наибольший ход головки фрезы мм 250
Рабочая подача фрезы мммин ( рег. бесступенчатое ) 20-400
Частота вращения сверлильного шпинделя обмин 238;325;450;600;825;1125
Наибольший ход сверлильной головки мм 100
Продолжительность холостых хоров мин 03
Рабочие подачи сверла мммин (рег. бесступенчатое) 20-300
Мощность Эл.двигателя кВт:
- фрезерной головки 75
- сверлильной головки 22
КПД привода станка 07
Габариты станка мм 3790х1630
Категория ремонтной сложности 7
Приспособление – пневматические тиски с призматическими губками
Режущий инструмент – Торцовая фреза Р5М6 ГОСТ 9304-69 Д=100мм В=50мм d=50H7мм zф=14штук
Центровочные сверла ø5 L=70мм l=62мм D=14мм ГОСТ 14952-75 Р6М5
Мерительный инструмент – Штангенциркуль ШЦ – 3 ГОСТ 169-88
Калибр-пробка ГОСТ 14822-69 ø5
Станок: Токарно-винторезный станок с ЧПУ 16Б16Т1
Наибольший ø обрабатываемой заготовки мм
Наибольшая длина заготовки 750 мм
Шаг нарезаемой резьбы 005-4095 мм
Частоты вращения шпинделя 1мин
Наибольшее перемещение суппорта
Подачи суппорта ммоб (мммин)
- продольная (2-1200)
- поперечная (1-1200)
Мощность электродвигателя 71 кВт
Габариты станка в плане 1390х1870
Приспособление – 3-х кулачковый самоцентрирующийся патрон вращающийся центр
Режущие инструменты – Резцы проходные упорный прямые с пластинами из твердого сплава с углом в плане 90º ГОСТ 18879 – 73 Т5К10 h=25мм b=16мм L=120мм e=15мм r=1.0мм
Резцы проходные упорный прямые с пластинами из твердого сплава с углом в плане 90º ГОСТ 18879– 73 Т15К6 h=25мм b=16мм =120мм e=15мм r=1.0мм
Резец канавочный Р6М5 ГОСТ 18883-73 Н=18мм В=4мм L=125мм а=5мм γ=10°
Мерительный инструмент – Штангенциркуль ЩЦ – 3 ГОСТ 169-88
Режущие инструменты – Резцы проходные упорный прямые с пластинами из твердого сплава с углом в плане 90º ГОСТ 18879 – 73 Т5К10 h=25мм b=16мм =120мм e=15мм r=1.0мм
Резцы проходные упорный прямые с пластинами из твердого сплава с углом в плане 90º ГОСТ 18879 – 73 Т15К6 h=25мм b=16мм =120мм e=15мм r=1.0мм
Резцы проходные упорный прямые с пластинами из твердого сплава с углом в плане 90º ГОСТ 18879 – 73 Т30К4 h=25мм b=16мм =120мм e=15мм r=1.0мм
Скоба предельная односторонняя ø80h11 и ø90h6 ГОСТ 18362-73
Станок: Шпоночно-фрезерный станок модели 692Р
Наибольшая ширина фрезерного паза 25мм
Длина фрезерного паза без перестановки 5-300мм
Размеры стола мм 200х800
Расстояние от оси шпинделя мм до вертикальных направляющих 206
Наибольшее расстояние от торца шпинделя мм до рабочей поверхности стола 500
Конус отверстия шпинделя Метрическая№50
Установочное перемещение стола мм
Наибольшее перемещение пиноли мм
Вертикальная подача шпинделя ммход бабки (бесступенчатое) 005-05
Частота вращения шпинделя 1мин 375;460;570;700;870;1070;1320;1620;2000;2500;3100;3750
Продольная подача шпинделя мммин(бесступенчатое) 450-1200
Мощность Эл.двигателя кВт 25
Габарит в плане мм 1620х1450
Категория ремонтной сложности 11
Приспособление - пневматические тиски с призматическими губками
Режущий инструмент – Шпоночная фреза Т15К6 ГОСТ 6396-78 с цилиндрическим хвостовиком ø25е8 L=98мм l=22мм
Мерительный инструмент – Шаблоны для контроля шпоночных пазов
Станок :Круглошлифовальный станок модель 3М151Ф2
Наибольший размер обр. заг. мм
Высота центров мм 125
Наибольший разм. Шлиф. Круга мм
Частота вращения шпинделя шлиф круга обмин 1590
Частота вращения шпинделя заг. 1мин 50-500
Угол поворота стола +3.-10
Подача шпинделя ммоб 01;014;02;028;04;056;08;112;16
Мощность электродвигателя 152кВт
Габариты станка мм 5400х2400
Категория ремонтной сложности 43
Приспособление – поводковый патрон и невращающиеся центра
Режущие инструменты – Круг плоский шлифовальный ГОСТ 2425-70 ПП600х30х305 и ПП600х60х305 24А25АС26К4А
Мерительный инструмент – Скоба односторонняя предельная
Режущие инструменты – Круг плоский шлифовальный ГОСТ 2425-70 ПП600х60х305 24А25АС26К4А
Станок: Горизонтальный шлицефрезерный станок мод. 5350
Число нарезаемых шлиц 4-100
Наибольшие размеры мм:
Обрабатываемой детали:
Частота вращения шпинделя обмин 80-250
Мощность эл.двигателя кВт 75
Габаритные размеры мм 1660х1150
Приспособление – вращающиеся центра поводковый патрон
Режущий инструмент – Червячная фреза для шлицевых валов Р6М5 ГОСТ 8072-60 Dе = 100 мм L = 90 мм d = 40 мм D1 = 60 мм z = 14 штук
Мерительный инструмент – Калибр-кольцо шлицевое ГОСТ 18832-73
Станок: Вертикальный фрезерный па мод. 5В312
Наибольший диаметр обрабатываемой заготовки 312 мм
Наибольший модуль 6 мм
Наибольшая ширина обрабатываемого венца 300 мм
Наибольший угол наклона зуба +45° -45°
Наибольший диаметр фрезы 180мм
Диаметр стола 320 мм
Диаметр отверстия в столе 80 мм
Конус Морзе шпиндельной фрезы 4
Частота вращения шпинделя 1мин: 40;50;63;80;100; 125; 160; 200; 250; 315;400;500
Подачи стола ммоб: 10;165;2;25;35;5;65;95;13;185;26;365;515;716;100
Габаритные размеры в плане мм 1790х1000
Масса станка кг 6400
Категория ремонтной сложности 35
Приспособление – Поводковый патрон вращающиеся центра
Режущий инструмент – Червячная фреза ГОСТ 9324-80 m = 5 Дао= =140мм Д= 50 мм Д1= 85 мм L = 140 мм zо = 14 штук класс точности АА
Мерительный инструмент – Шаблон длины общей нормали
Станок: Сверлильно-фрезерно-расточной станок модели ИР800ПМФ4
Размеры стола мм 800х800
Наибольшая масса обрабатываемой заготовки кг 1500
Наибольшее перемещение (мм) стола:
Расстояние от оси шпинделя до стола мм 80-780
Расстояние от торца шпинделя до центра стола мм 180-980
Конус отверстия шпинделя 50
Емкость инструментального магазина 30
Наибольший диаметр инструмента загружаемый в магазин:
Без пропуска гнезда 110
С пропуском гнезда 125
Частота вращения шпинделя 1мин: 212;225;24;265;28;30;315;33;35;37;40;42;44;46;49;52;55;58;62;65;69;73;78;82;86;92;97;102;108;115;120;128;135;142;150;160;170;180;200;210;225;240;250;265;280;300;315;330;358;370;395;415;440;465;490;520;550;580;620;650;690;730;775;820;865;915;970;1025;1080;1150;1200;1280;1350;1420;1500;1600;1700;1800;1900;2000;2100;2250;2400;2500;2650;2800;3000.
Рабочие подачи мммин 10-2000
Мощность Эл.двигателя кВт 14
Габариты в плане мм 4450х4655
Масса станка кг 12500
Приспособление – Поводковый патрон
Режущий инструмент – Сверло спиральное с цилиндрическим хвостовиком ГОСТ 10902-77 Р6М5 ø102 L=89мм l=43мм
Сверло спиральное с цилиндрическим хвостовиком ГОСТ 10902-77 Р6М5 ø126 L=89мм l=43мм
Метчик с проходным хвостовиком Р6М5 ГОСТ 3266-81 ø12 р=175мм L=89мм l=29мм l1=52мм
Мерительный инструмент – Калибр-пробка резьбовая ГОСТ 17757-72
Калибр-пробка ø102 ГОСТ 14822-69
Штангенциркуль ШЦ – 3 ГОСТ 169-88
5 Назначить режимы резания на механические операции
Фрезеровать торцы до размера 540 мм
где L – длина заготовки мм
t =(5524-540)2=62 4 = 155 (мм)
S0=023-05 ммоб принимаю S0 = 03 ммоб
Sz= Sz=0.3014=0.02(ммзуб)
v = (CvДq)(Тmtxsy Виzр)Kv ммин (7)
где T – среднее значение периода стойкости мин;
t - глубина резания мм;
общий коэффициент представляющий собой произведение из ряда поправочных коэффициентов учитывающих конкретные условия резания.
Cv – Коэффициент при скорости резания
m x y – показатели степеней при скорости резания
Д – диаметр фрезы мм
В – ширина фрезерования мм
Z – число зубьев фрезы штук
где Kmv – коэффициент учитывающий обрабатываемый материал
Kпv – коэффициент учитывающий способ получения заготовки
Kиv - коэффициент учитывающий материал инструмента
Kmv = Kr(750 в) nv (9)
где Kr – коэффициент характеризующий группу стали по обрабатываемости
в – фактические параметры характеризующие обрабатываемый материал для которого рассчитывается скорость резания
nv – показатель степени при обработке
Kmv =085(750 980) 0.9 =058
v = (647100025)(180021550100202 90015140)052 =401(ммин)
Определяем частоту вращения
n = 1000v(D) обмин (10)
где скорость резания ммин
D – наружный диаметр мм
n =(1000401)(3.14100) = 1278(обмин)
Сравниваем с паспортными данными и принимаем
Рассчитываем действительную скорость резания
vдейств = (Dn)1000 ммин (11)
где наружный диаметр мм
частота вращения обмин
vдейств = (314100125)1000 =393(ммин)
Рz = (10Cр txsy Вnz)( Дqnw)Kp Н (12)
где t - глубина резания мм;
Kp общий коэффициент представляющий собой произведение из ряда поправочных коэффициентов учитывающих конкретные условия резания.
Cp – коэффициент при скорости резания
n – частота вращения мммин
Kmp =( в750) n (13)
где в - фактические параметры характеризующие обрабатываемый материал для которого рассчитывается скорость резания
n – показатель степени при обработки резцом
Kmp =( 980750) 03 =108
Pz = (10 8251550950020.89011 14)( 100111250) 108 = 7368 (H)
Определяем мощность резания
Npез=( Pz v)(102060) кВт (14)
где Pz – сила резания Н
v – скорость резания ммин
Npез= (7368393)(102060) = 047 (кВт)
Определяем мощность шпинделя
где N дв. –мощность двигателя кВт
Сравниваю Npез и N и должно быть
Npез ≤ N(047 кВт 525 кВт )
Вывод: Обработка возможна
Сверлить 2 отверстия ø5 глубиной 63 мм
где d – диаметр сверла мм
s = 007-011 ммоб принимаю s = 008 ммоб
v = (CvДq)(Тmsy)Kv ммин (17)
Д – диаметр сверла мм
Kv= КlvKmv Kпv (18)
Klv - коэффициент учитывающий глубину сверления
Kmv определяем по формуле 9
Kmv =085(750 980) 09 = 067
v = (7504)(150200807)067 = 304(ммин)
Частота вращения определяем по формуле 10
n=(1000304)(3145)= 19386 (обмин)
Сравниваем с паспортными данными и принимаем
Рассчитываем действительную скорость резания по формуле 11
vдейств =(31451125)1000 =18(ммин)
Рассчитываем крутящий момент
Мкр = 10 CмДqsyKр Н м (19)
где D - диаметр сверла мм;
Kр - коэффициент учитывающий материал заготовки
Kр определяем по формуле 13
Kp =( 980750) 075 =122
Мкр =10 003455200808 122 = 14 (Hм)
Npез=( Мкр n)(9750) кВт (20)
где Мкр – крутящий момент Нм
n – частота вращения обмин
Npез= (141125)(9750) = 016(кВт)
N определяем по формуле 15
Npез ≤N(016кВт 154кВт )
Точить начерно последовательно поверхности до ø83 на длину 60 мм и ø145857 на длину 102 мм
Определяем глубину резания
tчерн =(Дз-Дчер)2 мм (21)
где Дз – диаметр заготовки мм
Дчер – диаметр черновой мм
t1 =(152577-145857)2=336(мм)
s = 07-12 ммоб принимаю s = 09 ммоб
Определяем скорость резания
V = (CvTmtxsy)Kv ммин (22)
Kv определяем по формуле 8
Kmv определяем по формуле 9
Kmv =095(750 980) 10 = 073
v = (340500233601509045)043 = 588(ммин)
Определяем частоту вращения по формуле 10
n =(1000588)(3.14145857) = 1276 (обмин)
vдейств = (314145857125)1000 = 573(ммин)
Рассчитываем силу резания
Pz = 10 Cptxsyvn Kр Н (23)
V – скорость резания ммин
Рассчитываем коэффициент Kр
Kр = KmpKφρKγρKλρ (24)
где Kmp – коэффициент учитывающий влияние качества материала
Kφρ - коэффициент учитывающий главный угол в плане
Kγρ - коэффициент учитывающий передний угол
Kλρ –коэффициент учитывающий угол наклона главного лезвия
Kmp определяем по формуле 13
Kmp =( 980750) 075 =122
Pz = 10 3003361090.75573-0.15 109 = 55315 (H)
Определяем мощность резания по формуле 14
Npез= (55315573)(102060) = 52 (кВт)
N=определяем по формуле 15
Npез ≤N(52 кВт58кВт )
Точить начисто последовательно 2 фаски 16х45° и 2х45° и поверхности до ø805 на длину 60 мм и ø142977h11 длиной 102 мм
Определяем глубину резания при чистовом точении
tчист =(Дчер-Дчист)2 мм (25)
где Дчист – диаметр чистовой мм
t1 = (83-805) 2 =125(мм)
t2 = (145857-142977) 2 =144(мм)
Определяем скорость резания по формуле 22
Kmv =095(750 980) 10 = 073
v = (3504002144015033035)066 = 1542 (ммин)
n=(10001542)(314145977)= 3363 (обмин)
vдейств =(314315145977)1000 = 1444 (ммин)
Точить канавку начисто до ø79 длиной 5 мм
t =(Ддет-Дкан)2 мм (26)
где Ддет – диаметр детали мм
Дкан – диаметр канавки мм
t = (805-79)2 = 075 (мм)
s = 016 – 023 ммоб принимаю s = 020 ммоб
Определяем скорость резания по формуле 22
Kmv = 085(750980) 175 = 053
v = (42040020750150202)048 = 1389 (ммин)
Частота вращения шпинделя определяем по формуле 10
n=(10001389)(31479)= 5598(обмин) Сравниваем с паспортными данными и принимаем
vдейств =(31479500)1000 = 124 (ммин)
Точить начерно последовательно поверхности до ø68 на длину 25мм
до ø81 на длину 82мм до ø83 на длину 153 мм до ø9276 на длину 80мм до ø11276 на длину 45 мм
Определяем глубину резания по формуле 21
t4 =(996-9276)2=342(мм)
t5 =(1196-11276)2=342(мм)
s = 07-12 ммоб принимаю s = 09 ммоб
v = (340500234201509045)043 = 583(ммин)
n =(1000583)(3.1411276) = 1647 (обмин)
vдейств = (31411276160)1000 = 567 (ммин)
Рассчитываем силу резания по формуле 23
Рассчитываем коэффициент Kр по формуле 24
Kmp =( 980750) 075 =122
Pz = 10 3003421090.75567-0.15 109 = 56392 (H)
Npез= (56392567)(102060) = 522 (кВт)
Npез ≤N(522 кВт 58кВт )
Точить начисто последовательно5 фасок и поверхности до ø655 на длину 25мм до ø785 длиной 82мм до ø80 на длину 30мм до ø805 на длину 65мм до ø805 на длину 58мм до ø9048 на длину 80мм и до ø110 на длину 45мм
Определяем глубину резания при чистовом точении по формуле 25
t1 = (68-655) 2 =125(мм)
t2 = (81-785) 2 =125(мм)
t4 =(83-805)2=125(мм)
t5 =(9276-9048)2=114(мм)
t6 =(11276-110)2=138(мм)
v = (3504002138015051035)066 =1332(ммин)
n=(10001332)(314110)= 3857(обмин) Сравниваем с паспортными данными и принимаем
vдейств =(314110315)1000 = 1088 (ммин)
Точить тонко последовательно поверхность до ø80h11 длиной 65 мм и до ø90h6 длиной 80 мм
t =(Дчист-Ддет)2 мм (37)
Ддет – диаметр детали мм
t1 = (805-80)2 = 025 (мм)
t2 = (9048-90)2 = 024 (мм)
s = 006 – 012 ммоб принимаю s = 01 ммоб
v = 120 – 170 ммин принимаю v = 160 ммин
n=(1000160)(31490)= 5662 (обмин)
vдейств =(31490500)1000 = 1413 (ммин)
Определяем глубину резания при чистовом точении по формуле 26
Фрезеровать шпоночный паз
Скорость резания определяем по формуле 7
v = (122503)(90026180304502525030)066 = 66 (ммин)
n =(100066)(3.1425) = 842(обмин)
vдейств = (31425375)1000 = 294(ммин)
Сила резания определяем по формуле 12
Kp определяем по формуле 13
Kp =( 980750) 03 =1.08
Pz = (10 125180850450.75251 3)( 25073375-013) 108= 18898(H)
Npез= (18898294)(102060) = 091(кВт)
Npез ≤ N(091 кВт 19кВт )
Шлифовать поверхность до ø80К6 длина 60 мм
Припуск h = (805-80)2 = 025 (мм)
Скорость круга Vкр =30мс
Частота вращения круга n = 1590 обмин
Скорость заготовки Vз =30 ммин
Частоту вращения заготовки определяем по формуле 10
n = (100030)(3.1480) =1195(обмин)
vдейств =(31410080)1000 =251 (ммин)
Радиальная подача Sр=0005 ммоб
Определяем мощность резания
Npез=СN Vзr Sрydqbz кВт (28)
где Vз - скорость заготовки ммин
Sр – радиальная подача ммоб
d – диаметр шлифования мм
b- ширина шлифования мм
Nрез=0142510.80.0050.8800.2601=384(кВт)
Определяем мощность резания по формуле 15
Nшг= 152082 = 125 (кВт)
Nрез ≤ Nшп (384 кВт 125 кВт)
Шлифовать поверхности одновременно до ø65h8 длина 25 мм и до ø80К6 длина 58 мм
Припуск h = (655-60)2 = 025 (мм)
h = (855-80)2 = 025 (мм)
Определяем мощность резания по формуле 28
Последовательно поверхность до ø78а11 длина 82мм
Припуск: h = (785-78)2 = 025 (мм)
Скорость круга Vкр = 30 мс
Частота вращения круга nкр = 1590 обмин
Скорость заготовки Vз = 30 ммин
n = (100030)(31478) = 1225(обмин)
vдейств =(31410078)1000 = 245 (ммин)
Продольная подача Sр = 05·82 = 41 (ммоб)
Глубина шлифования t = 005 мм
Npез=CN V3r S y dq tx кВт (29)
S – продольная подача ммоб
t- глубина шлифования мм
Nрез=265 2450.5 0.050.5 410.55 78-02 = 26 (кВт)
Nшг = 152082 = 125 (кВт)
Nрез ≤ Nшп (26 кВт 125 кВт)
Фрезеровать шлицы длиной 85 мм начерно
Припуск на обработку: h = (78-72)2 = 3·07 = 21 (мм)
Скорость резания определяем по формуле
V = (Cv·UqvTmhxvsyv)Kv ммин (30)
гдеT – среднее значение периода стойкости мин;
m x yq – показатели степеней при скорости резания
U – число шлицев шлицевого валика штук
Kv= KmvKwvKnvKuv (31)
где Kmv – коэффициент учитывает качество материала
Kwv - коэффициент учитывает количество перемещений фрезы
Knv- коэффициент учитывает профиль шлицы
Kuv- коэффициент учитывает число шлиц
v = (780· 100.376000402.20531.28)1.4 = 35 (ммин)
Частоту вращения определяем по формуле 10
n = (100035)(31478) = 142.9 (обмин)
vдейств =(31412578)1000 = 30.6 (ммин)
N= 10-5CNSyv duN·VKN кВт (32)
где CN – коэффициент при мощности
KN – поправочный коэффициент учитывающий изменение условий эксплуатации
Nрез. = 10-54222065 7811306 10=259(кВт)
Npез ≤ N(259 кВт 64 кВт )
Фрезеровать шлицы начисто
t = h·0.3 = 0.3·3 = 0.9 (мм)
Скорость резания определяем по формуле 30
Kvопределяем по формуле 31
v = (390· 100.37300040080531.28)1.4 = 383 (ммин)
n = (1000383)(31478) = 1565 (обмин)
vдейств =(31415078)1000 = 367 (ммин)
Фрезеровать зубья начерно
tчерн. =225= 11 (мм)
S=24 – 28 ммоб принимаю s = 25 ммоб
V = (CvTmmxvsyv)Kv ммин (34)
Kv= KmvK3vKwvKΔvKvKiv (35)
K3v - коэффициент учитывает число заходов
KΔv- коэффициент учитывает класс точности
Kv- коэффициент учитывает угол наклона зуба
Kiv - коэффициент учитывает число проходов
Kv=101010100810 = 08
v = (3504800332505501)08 = 197 (ммин)
n = (1000197)(314140) = 445 (обмин)
vдейств =(31440140)1000 = 176 (ммин)
N= 10-3CNsyv DxNmxvzqN VKN кВт (36)
D – диаметр фрезы мм
z – число зубьев колеса штук
Nрез. = 10-31242509 517140-1360 176 10=055(кВт)
Npез ≤ N(055 кВт 49 кВт )
Фрезеровать зубьев начисто
tчерн = 005m мм (37)
tчерн. = 0055= 025 (мм)
S = 08 – 10 ммоб принимаю s = 10 ммоб
Скорость резания определяем по формуле 34
Kv определяем по формуле 35
v = (56024005100855-05)08 = 647 (ммин)
n = (1000647)(314140) = 1471 (обмин)
vдейств =(314125140)1000 = 55 (ммин)
Сверлить 2 отверстия последовательно ø102 длиной 27 мм; сверлить 2 фаски последовательно ø126 под углом 120º
Глубина резания по формуле 16
s = 017-020 ммоб принимаю s = 018 ммоб
Скорость резания по формуле 17
Kv определяем по формуле 18
Kmv =085(750980) 09 = 067
v = (710204)(250201807)067 =207(ммин)
n=(1000207)(314102)= 6489 (обмин)
vдейств =(314102620)1000 = 20 (ммин)
Рассчитываем крутящий момент по формуле 19
Kp =(980750) 075 = 122
Мкр =10 00345102201808 122 = 111(Hм)
Определяем мощность резания по формуле 20
Npез= (111620)(9750) = 071(кВт)
Npез ≤N(071кВт 112кВт )
Нарезать 2 резьбы М12-7Н длиной 22мм
Число рабочих ходов i = 4+1 = 5
Скорость резания определяем по формуле 17
Kv= КТvKmv Kпv (38)
KТv - коэффициент учитывающий точность резьбы
v = (6481212)(9009017505)08 =135 (ммин)
n=(1000135)(31412)= 3575 (обмин)
vдейств =(31412 330 )1000 = 125 (ммин)
Мкр = 10 CмДqрyKр Нм (39)
Мкр =10 00270121417515 085 = 173 (Hм)
Npез= (173330)(9750) =058(кВт)
Npез ≤N(015 кВт 112кВт )
6 Рассчитать нормы времени на механические операции
Штучное время определяем по формуле
Тшт =( T0 +Тв)(1+(К1+К2)100) мин (40)
Основное время на фрезерование
T0 = (Lp.x.(ns))i мин (41)
где Lp.x. – длина рабочего хода мм
Lp.x.=l+l1+l2 мм (42)
где l – ширина фрезерование мм
l1 – длина врезание мм
l2 – длина перебега мм
l1 =05(Д-√Д2-В2) мм (43)
где Д – диаметр фрезы мм
l1 =05(100-√1002-902)= 282 (мм)
Lp.x.= 90+282+2 = 1202(мм)
T0 =(1202(030125))4=1282(мин)
Основное время на сверление определяем по формуле 41
Lp.x. определяем по формуле 42
l1 определяем по формуле :
где Д – диаметр сверла мм
Lp.x.= 63+0+15=78(мм)
T0 =(78(0081125))1=009(мин)
T0 = T0фр + T0св мин (45)
где T0фр – основное время на фрезерование мин
T0св – основное время на сверление мин
T0 =1282+009 = 1291(мин)
Тв = Туст + Тв + Тконтр мин (46)
где Туст – время на установку и снятие заготовки мин
Тв – вспомогательное время связанное с выполнением операции мин
Тконтр – время на контрольные измерения мин
Тконтр=036+0.12=0.56 (мин)
Тв = 050+065+056 = 171 (мин)
Тшт =(1291+171)(1+(35+4)100)= 1572 (мин)
Норма времени на операцию при обработке на станке с ЧПУ определяется по формуле:
Тшт = (Та+ТвKtв)(1+Тоб100) мин (47)
где Та – время автоматической работы по программе мин
Тв – Время ручной вспомогательной работе мин
Тоб – время на техническое и организационное обслуживание рабочего места отдых и личные надобности
Ktв – поправочный коэффициент учитывающий серийность работы
Тоа =Тоа + Тва мин (48)
где Тоа– время основной автоматической работы мин
Тва – время ручной вспомогательной работы мин
Тоа = L is mi мин (49)
где s mi – минутные подачи на участке
L I – длина шага траектории инструмента мм
L I = 60+315+102+60+315+102+16+2+075+075 = 3921(мм)
S mi = s 0 nд мммин (50)
где s 0 – подача ммоб
nд - частота вращения обмин
s mi =09125=1125(мммин)
Тоа = 39211125 = 348 (мин)
Тоа = 348+002 = 35 (мин)
Тв = Тву + Твсп + Тви мин (51)
где Тву – время на установку и снятие заготовки мин
Твсп – вспомогательное время связанное с выполнением операции мин
Тви – время на контрольные измерения мин
Тви =013+016+013+016+021 = 079 (мин)
Тв = 24+010+079 = 329 (мин)
Тшт = (35+32908)(1+5100) = 65 (мин)
Норма времени на операцию при обработке на станке с ЧПУ определяется по формуле 47
Тоа определяем по формуле 48
Тоа определяем по формуле 49
LI=25+65+82+1+153+5+80+10+45+15+25+65+82+1+30+025+65+58+5+80+
+10+45+175+65+80+075+075 = 99425(мм)
S mi определяем по формуле 50
s mi =09160= 144 (мммин)
Тоа = 99425144 = 691 (мин)
Тоа = 691+002 = 692 (мин)
Тв определяем по формуле 51
Твсп =00213=026(мин)
Тви = 013+013+013+016+013+016+013+013+016+016+013+008+008 = =171 (мин)
Тв = 171+24+026 = 437 (мин)
Тшт = (693+43708)(1+5100) = 11 (мин)
Штучное время определяем по формуле 40
Основное время определяем по формуле 41
Lp.x. = 96-25 = 71 (мм)
T0 =(71(375135))5=07(мин)
Тв определяем по формуле 46
Тв =046+057+020 = 123 (мин)
Тшт =(07+123)(1+(3+4)100)= 21 (мин)
Основное время определяем по формуле
T0 = hКв(nt) мин (52)
где h – припуск на обработку мм
n – частота вращения шпинделя обмин
t – глубина фрезерования мм
Кв- коэффициент при основном времени
T0 = (02513)(1000005)=065(мин)
Тв =23+01+008 = 248 (мин)
Тшт =(065+248)(1+(9+4)100)= 354(мин)
T0 = (2·Lp.x.·iК)(n sпр) мин (53)
где Lp.x – длина шлифования мм
К – коэффициент обработки
sпр – продольная подача ммоб
Lp.x определяем по формуле 42
Lp.x.= 82+0.5·60= 112 (мин)
T01 = (2·112.·213)(100 41) = 145 (мин)
Основное время определяем по формуле 52
T02 =(02513)(1000005) = 065 (мин)
T0 = 065+142 = 207 (мин)
Туст = 23+08 = 31 (мин)
Тв = 01+008 = 018 (мин)
Тконтр = 007008+008 = 023 (мин)
Тв = 31+018+023 = 351 (мин)
Тшт = (207+351)(1+(9+4)100) = 54 (мин)
T0 =(Lz)(nsK) мин (54)
где L – длина рабочего хода мм
n- частота вращения обмин
K- число заходов фрезы
Lр.х. определяем по формуле 42
Lчер = 85+5+2 = 92 (мм)
T0чер =(9210)(125221) = 335 (мин)
T0чист =(9210)(150081) = 767 (мин)
T0 = T0чист + T0чер мин (55)
где T0чер – основное время на черновое фрезерование зубьев мин
T0чист – основное время на чистовое фрезерование зубьев мин
T0 = 335+767 = 1102 (мин)
Тпер = 064+064 = 128 (мин)
Тконтр = 033+033 = 066 (мин)
Тв = 23+128+066 = 424 (мин)
Тшт =(1102+424)(1+(4+4)100) = 165 (мин)
T0 определяем по формуле 54
Lр.х. определяем по формуле 42
l1=√(t(D-t)) мм (56)
где t – глубина резания мм
l1=√(11(140-11)) = 377 (мм)
Lчер = 95+377+2 = 1347 (мм)
T0чер =(134726)(40251) = 35 (мин)
L определяем по формуле 42
l1 определяем по формуле 5
l1=√(025(140-025)) = 59 (мм)
Lчист = 95+59+2 = 1029 (мм)
T0чист =(102926)(125101) = 214 (мин)
T0 определяем по формуле 55
T0 = 35+214 = 564 (мин)
Тпер = 094+094 = 188 мин
Тконтр = 0102=020 мин
Тв = 23+188+02 = 438 (мин)
Тшт =(564+438)(1+(4+4)100) = 657 (мин)
Основное время на сверление определяем по формуле 40
Lp.x.= 27+31+0 = 301 (мм)
T01 =(301(018620))1=027(мин)· 2 отв. = 054 (мин)
Lp.x.= 2+0+4 = 6 (мм)
T02 =(6)(018620)=005(мин)· 2 отв. = 01 (мин)
Основное время при нарезание резьбы:
T0 = (18(l+l1)i)(ns) мин (57)
где l – длина нарезания резьбы мм
l1 – величина перебега и врезания мм
T03 = (18(22+4)5)(330175) = 405(мин) · 2 отв. = 81 (мин)
T0 = 054+01+81 = 874 (мин)
Тв =014·2+014·2 +020·2 = 096 (мин)
Тконтр=011·2+010·2+045·2 = 132 (мин)
Тв = 039+096+132 = 267 (мин)
Тшт =(874+267)(1+(43+4)100)=124(мин)
Тшт общее = 1572+65+11+21+354+54+165+657+124 = 13886(мин)
Время изготовления одной детали равно 13886 мин.
1 Определить потребное количество станочного оборудования и коэффициент его загрузки
Определение оптимального размера партии
Характерной особенностью серийного производства является изготовление деталей партиями. Под размером партии деталей понимают число деталей обрабатываемых с одной наладки оборудования.
nопт. - оптимальный размер партии определяется расчётом в определённой последовательности:
Нормы времени по операциям следующие:
Наименование операции
а) рассчитывается минимальный размер (nmin.) партии по формуле:
nmin = Тпз (tшт·a) (58)
где Тпз - подготовительно - заключительное время по ведущей технологической операции т.е. по той где отношение Тпз tшт. величина наибольшая мин.
tшт. - норма штучного времени мин.
α - коэффициент характеризующий величину допустимых потерь времени на переналадку рабочего места α =002 007
nmin =12 (021003) = 191 (шт.)
б) минимальный размер партии nmin. затем корректируется до размера оптимального (nопт..) который должен соответствовать двум условиям:
) Определяем целесообразно-допустимое целое число партий в месяц:
где nопт. – оптимальный размер партии шт.
Nмec- месячный выпуск изделий шт.
где Nгод – годовой выпуск продукции шт.
Nмec =600012 =500(шт.)
) Определяем целесообразно-принятое целое число смен или полусмен:
к2 = nопт.. Ncм. ф. (61)
где Ncм.ф.- фактическая производительность рабочего места в смену шт.
nопт. – оптимальный размер партии шт.
Ncм. ф. = 480Кв tшт. (62)
где кв. - коэффициент выполнения нормы времени
0 мин - продолжительность смены;
Ncм. ф. 1= (480 105)1572 =32(шт.)
к2 1 = 25032 = 8 (смен)
Ncм. ф. 2=(480 105)65 =78(шт.)
к22=25078 = 35(смены)
Ncм. ф. 3=(480105)11 = 46(шт.)
к23 = 25046= 35 (смен)
Ncм. ф. 4= (480105)21 = 240(шт.)
к24 = 250240 = 15 (смены)
Ncм. ф. 5= (480105)354 = 143 (шт.)
к25 = 250143= 2(смен)
Ncм. ф. 6= (480105)54=93(шт.)
к26 = 25093=3(смены)
Ncм. ф. 7= (480105)165=31 (шт.)
к27 = 25031=85(смен)
Ncм. ф. 8= (480105)657=8(шт.)
к28 = 2508=315(смен)
Ncм. ф. 9= (480105)124=41(шт.)
Расчёт сведён в табл. 2
Фактическая сменная производительность станка (с учетом выполнения норм) шт.
Смены (полусмены) на которые станок загружен выбранной партией
Определение трудоёмкости на годовую программу
Трудоемкость Т на каждую операцию определяется по формуле:
Т = (Nг×tшт. к)60 (63)
где Nг. – годовой выпуск программы шт.
tшт.к - штучно-калькуляционное время час
Штучно-калькуляционное время определяется по формуле:
tшт.к = tшт. +(Тпз. nопт.) (64)
где nопт. - оптимальный размер партии шт.
Тпз - подготовительно - заключительное время мин
Расчёт штучно-калькуляционного времени
tшт.к1 =1572+ (10250) =1576(мин);
tшт.к2 =65+(14250) =656(мин);
tшт.к3=11+(14250) =1106(мин);
tшт.к4 =21+(12250) =215 (мин);
tшт.к5 =354+(10250) = 358(мин);
tшт.к6 =54+(10250) = 544(мин);
tшт.к7 =165+(22250) = 1659(мин);
tшт.к8 =657+(24250) = 658(мин);
tшт.к9 =124+(6250) = 1242(мин);
Расчёт трудоёмкости ведётся по формуле
Т1 = (15766000)60=1560(станко-часов);
Т2 = (6566000)60=660(станко-часов);
Т3 = (11066000)60=1140(станко-часов);
Т4 = (2156000)60=240(станко-часов);
Т5 = (3586000)60= 360(станко-часов)
Т6 = (5446000)60= 540(станко-часов)
Т7 = (16596000)60= 1680(станко-часов)
Т8 = (6586000)60= 6600(станко-часов)
Т9 = (12426000)60= 1260(станко-часов)
Остальные расчёты сведены в табл. 3
Штучно-калькуляционное время
Трудоемкость в станко-часах
Расчёт действительного годового фонда времени
Действительный годовой фонд времени работы оборудования определяется по формуле:
Fд= Dp× q × S× (1-0 01× b) (65)
где Dp - число рабочих дней в году дни
q - длительность смены час
S - количество рабочих смен смен
b - процент планируемых потерь рабочего времени на переналадку и ремонт оборудования %;
Dp = Dк - Dв - Dпр (66)
где Dк - число календарных дней в году дни
Dв - число выходных дней дни
Dпр - число праздничных дней дни
Dp =365-104-8=253(дня)
Fд= 25382 (1-0 015) = 3846(часов)
Расчёт количества оборудования и коэффициента его загрузки
Расчёт количества рабочих мест Ср на участке ведётся по формуле:
где Т – трудоёмкость станко-часах;
Кв - коэффициент выполнения норм; Кв = 105
Fд- действительный годовой фонд времени работы оборудования час
Расчёт количества станков и их загрузки по операциям:
СР1 =1560(3846105)=039; Спр =1станок;
СР2 =660(3846105)=016; Спр =1станок;
СР3=1140(3846105)=028; Спр = 1станок;
СР4 =240(3846105)=006; Спр = 1станок;
СР5 =360(3846105)=009; Спр =1станок;
СР6 =540(3846105)=013; Спр =1станок;
СР7 =1680(3846105)=042; Спр =1станок;
СР8 =6600(3846105)=164; Спр =2станок;
СР9 =1260(3846105)=031; Спр =1станок;
Расчётное количество станков округляется до ближайшего целого числа и получаем принятое количество станков (Спр) при этом загрузка оборудования не должна превышать 110%.
Коэффициент загрузки Кз определяется по формуле:
где Cр – количество рабочих мест шт.
Спр – принятое количество станков
Основные расчёты сведены в табл. 4
Действительный фонд времени работы оборудования
Количество расчетных станков Сp
Количество принятых станков Спр
Коэффициент загрузки
Средний коэффициент загрузки по участку (Кср) определяется по формуле:
где Сp - сумма расчётных станков
Спр - сумма принятых станков шт.
Если средний коэффициент загрузки получается чем 80% то производится догрузка оборудования по тем операциям где он меньше 80%. Для этой цели отбирают детали для догрузки в качестве кооперирования или оказания услуг другим участкам или цехам завода.
Расчет среднего коэффициента загрузки:
Так как 69%80% то производим догрузку оборудования
Догрузка оборудования производится следующим образом:
По Фрезерно-центровальной :
Определяются располагаемые станко-часы.
Спр ×Fд ×Кв =13846105=4038 (станко-часов).
Трудоёмкость с догрузкой определяется:
54038=3836(станко-часов).
Определяем количество станко-часов для догрузки:
36-1560=2276(станко-часов).
Определяем расчётное количество станков по трудоемкости с догрузкой:
Ср = Т(Рд × Кв) =3836(3846105)=095
Кз= Ср Спр =0951=095
По Токарной с ЧПУ 1 :
36-660=3176(станко-часов).
По Токарной с ЧПУ 2 :
36-1140=2696(станко-часов).
По Шпоночно-фрезерной:
36-240=3596(станко-часов).
По Круглошлифовальной 1:
36-360=3476 (станко-часов)
По Круглошлифовальной 2:
36-540=3296 (станко-часов)
36-1680=2156(станко-часов).
36-1260=2576(станко-часов).
Расчёт догрузки оборудования по остальным операциям сведён в таблицу 5
Принятое количество станков по заданной программе
Располагаемые станко-часы
Трудоемкость по заданной программе
Трудоемкость программы с догрузкой
Количество станко-часов для догрузки
Расчетное количество станков с догрузкой Ср
Принятое количество станков с догрузкой Спр
Коэффициент загрузки Кз
На основании проведенных расчетов построим график загрузки оборудования где по оси Х располагаются принятые станки по видам а на оси У откладываются % загрузки каждого вида.
2 Определить количество рабочих-станочников вспомогательных рабочих и ИТР на участке
Расчет численности рабочих-сдельщиков
Расчёт этих рабочих производится по формуле:
Рсд = Т (Fдр × Кв × S) (70)
где Т - трудоёмкость программы с догрузкой станко-часы;
S=1 для всех станков кроме операций где нарезаются зубья и шлицы;
Fдр - эффективный годовой фонд времени одного рабочего.
Расчёт эффективного фонда времени (Fдр) рабочего сведён в табл. 6
Число выходных дней в году из них:
Число выходных дней и
Итого число рабочих дней
Невыходы на работу – всего
В т.ч. очередной отпуск
Выполнение гос. Обязанностей
Отпуск в связи с родами
Итого полезный фонд рабочего времени
Расчёт количества основных рабочих:
Рсд1 = 3836(17761051)=206 Рпр1 = 2 (человека)
Рсд2 =3836(17761051)=206 Рпр2 = 2 (человека)
Рсд3 = 3836(17761051)=206 Рпр3 = 2 (человека)
Рсд4 =3836(17761051)=206 Рпр4 = 2(человека)
Рсд5 =3836(17761051)=206 Рпр5 = 2 (человека)
Рсд6 =3836(17761051)=206 Рпр6 = 2 (человека)
Рсд9 =3836(17761051)=206 Рпр9 = 2 (человека)
Определяем коэффициент многостаночного обслуживания S:
S= ((Tмс Kд)Тз) +1 (71)
где Тмс –машиносвободное время мин.
Кд – поправочный коэффициент для специальных станков равный 08.
Тз- время занятости рабочего мин.
Тмс = То –(Твп + Та + Тп) (72)
где То – основное время мин.
Твп – вспомогательное время; время контрольных измерений мин.
Та – время активного наблюдения мин.
Тп – время на переходы от основного станка к другому мин.
Та = 0051102 = 055 (мин)
Тмс = 1102-(23+055+003) = 814 (мин)
Тз = Твн + Твп + Та + Тп (73)
где Твн – вспомогательное время неперекрываемое мин.
Тз= 424+055+23+003 = 712 (мин.)
S= ((8140 8)712) +1= 192
S=1 так как у нас на данную операцию 1 станка
Рсд7 = 3836 (17761051) = 206 Рпр6 = 2 человека
Та = 005564 = 282 (мин)
Тмс = 564-(23+282+003) = 5125 (мин)
Тз= 428+282+23+003 = 953 (мин.)
S= ((51250 8)953) +1= 53
S=2 так как у нас на данную операцию станка
Рсд8 = 6600 (17761052) = 177 Рпр6 = 2 человека
Остальные расчёты сведены в таблицу 7
Трудоемкость с догрузкой
Коэффициент выполнения норм
Полезный фонд времени
Расчетное количество рабочих
Принятое количество рабочих
Определение количества вспомогательных рабочих.
К вспомогательным рабочим относятся: наладчики контролёры электрики подсобные рабочие уборщики помещений.
Количество вспомогательных рабочих определяется:
где Рсд – численность рабочих-сдельщиков чел.
Pвсп = 0218=36 принимаем 4 человека
Принимаем на участке следующих вспомогательных рабочих: одного наладчика одного контролера одного электрика и одного уборщика помещения.
Определение руководителей и специалистов.
К руководителям на участке можно отнести старших мастеров сменных мастеров технологов нормировщиков.
На участке принимаем следующих руководителей и специалистов: двух сменных мастеров и одного технолога.
3 Определить площадь участка
Площадь цеха состоит из производственной и вспомогательных площадей.
Производственная площадь Snp определяется по формуле:
где Sуд – удельная площадь м2
Спр – принятое количество станков шт.
Вспомогательная площадь составляет 40% производственной площади:
где Snp - производственная площадь м2
Общая площадь – это сумма производственной и вспомогательной площадей.
Sобщ = Sпр+Sвсп (77)
Sвcn - вспомогательной площадь м2
Sобщ =200+94=294(м2)
Внутренний объём Vвн определяется по формуле:
Vзд. внутр. = Sобщ×h (78)
где Sобщ- общая площадь м2
Vзд. внутр. =29484=24696(м3)
Внешний объём здания рассчитывается по формуле:
Vзд. внешн. = Vзд. внутр. ×К (79)
где Vзд. внутр.- внутренний объём здания м3
К – коэффициент учитывающий толщину стен.
Vзд. внутр. =24696м3
Vзд. внешн. =2469611=271656(м3)
Для этого я выбрал способ получения заготовки и определил припуски на заготовку а также назначил маршрут обработки детали.
Также в дипломном проекте выбрал станки приспособления режущий вспомогательный и измерительный инструмент на каждую операцию. Потом рассчитал на заготовку все режимы резания и нормы времени.
Потом определил количество станочного оборудования и коэффициент его загрузки а также определил количество рабочих-станочников вспомогательных рабочих и ИТР. Затем рассчитал площадь участка.
Данилевский В.В «Технология машиностроения». Изд. 3-е перераб. и доп. Учебник для техникумов. М. «Высшая школа» 1972. 544с. с илл.
Справочник техника – машиностроителя. В 2-х т. Т2 Под ред. А.Г. Косиловой и Р.К. Мещерякова. – 4-е изд. перераб. и доп. – М. : Машиностроение 1983. 656с илл.
Общемашиностроительные нормативы времени вспомогательного на обслуживание рабочего места и подготовительно-заключительного для технического нормирования станочных работ. Серийное производство. Изд. 2-е. М. «Машиностроение» 1974 421с.
Методичка для расчета массы детали и экономического обоснования заготовки
Методичка для расчета зубофрезерной операции
Методичка для выполнения курсового проекта «Правила записи операций и переходов»
Рекомендуемые чертежи
- 11.03.2024
- 20.02.2016
- 28.02.2024