Проект ферментатора для аэробного стерильного глубинного культивирования бактерий-продуцента лизина объёмом 10 м3


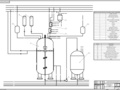
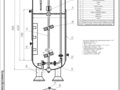
- Добавлен: 19.11.2022
- Размер: 321 KB
- Закачек: 4
Подписаться на ежедневные обновления каталога:
Описание
Проект ферментатора для аэробного стерильного глубинного культивирования бактерий-продуцента лизина объёмом 10 м3
Состав проекта
![]() ![]() ![]() |
Дополнительная информация
Контент чертежей
КР ПИАБ Салеев Р.Б. 19-ТПМ-13 — копия.docx
Федеральное Государственное Бюджетное Образовательное Учреждение
«Московский Государственный Университет Пищевых Производств»
Кафедра «Биотехнология и технология продуктов биоорганического синтеза»
по дисциплине: «Процессы и аппараты биотехнологии»
на тему: «Проект ферментатора для аэробного стерильного глубинного культивирования бактерий-продуцента лизина объёмом 10 »
ст. группы 19-ТПМ-13
Научный руководитель:
проф. Чурмасова Л. А.
ЗАДАНИЕ НА ПРОЕКТИРОВАНИЕ
Рассчитать и спроектировать ферментатор для аэробного стерильного глубинного культивирования бактерий-продуцентов лизина объемом 10 .
Сделать следующие расчеты:
расчет мощности потребляемой мешалкой на перемешивание;
тепловой расчет аппарата;
материальный баланс на 1 загрузку;
расчет установки для пеногашения;
Параметры процесса и физико-химические показатели среды следующие:
динамическая вязкость ;
теплоемкость среды ;
коэффициент заполнения ;
рабочее давление воздуха в аппарате над уровнем жидкости ;
температура культивирования ;
температура воды на входе в рубашку или змеевик на выходе ;
Используется жидкий пеногаситель в количестве 1 кг на 1 среды готовится 1 раз в сутки на 1 аппарат.
Стерилизация масла осуществляется путем нагревания его от до паром () через змеевик из трубок диаметром 2925мм.
лист: обвязка ферментатора;
лист: ферментатор в разрезе.
Технологическая часть5
2. Химическая схема производства6
3. Технологическая схема производства8
4. Характеристика сырья материалов8
4.1 Приготовление стерильных питательных сред8
4.2 Приготовление посевного материала9
4.3 Условия культивирования11
5. Получение препаратов лизина12
5.1Жидкий концентрат лизина12
5.2Сухой концентрат лизина12
5.3Кристаллический лизин15
1. Расчет ферментера17
2. Расчет механической мешалки ферментатора19
3. Тепловой расчет ферментатора23
4. Материальный баланс на одну загрузку.26
5. Расчет установки для пеногашения27
6. Расчет дополнительного оборудования30
Список использованной литературы37
В последние годы в Российской Федерации резко сократилась продукция животноводства и как следствие этого возрос до недопустимых размеров импорт мясопродуктов.
Одной из причин уменьшения производства мясопродуктов является ухудшение качества кормов и повышение их стоимости что вызвано практически полной остановкой предприятий производивших кормовой белок в силу их неконкурентоспособности при изменившейся структуре цен. Сегодня кормовой белок почти полностью импортируется.
Однако есть альтернативное решение проблемы повышения качества кормов. Известно что дефицит белка может быть компенсирован введением в корма незаменимых аминокислот причем в первую очередь устраняется дефицит аминокислоты находящейся в относительном минимуме затем следующей – и так далее т.к. привесы определяются не общим содержанием белка а именно по содержанию наиболее дефицитной незаменимой аминокислоты в нем. Порядок лимитирования определяется применяемыми компонентами кормов и потребностями в аминокислотах у животных и птицы. Аминокислотный состав кормовых ингредиентов и потребности в различных аминокислотах хорошо изучены и давно известны.
Так для зерна злаковых и всех сельскохозяйственных животных и птицы лимитирующими аминокислотами являются метионин лизин триптофан и треонин.
В настоящее время в России в сельском хозяйстве птицеводство является ведущей отраслью. При кормлении птицы первой лимитирующей аминокислотой является лизин второй - метионин который производится как в России так и за рубежом методом химического синтеза и в достаточных количествах поступает на российский рынок.
Эффект применения незаменимых аминокислот в частности L-лизина основывается на том что белок зерновых – основного компонента кормов для сельскохозяйственных животных и птицы – имеет неблагоприятный состав образующих его аминокислот. Одна из них –L-лизин– находится в дефиците и не может быть синтезирована в организме животного.
Обычно дефицит устраняется внесением в рацион т.н. «протеиновых» (белковых) добавок богатых L-лизином – таких как рыбная и мясокостная мука соевый и подсолнечниковый шрот гидролизные и кормовые дрожжи. Однако дефицит как было сказано выше можно устранить и просто введением в корм соответствующего количества кристаллического L-лизина.
В развитых странах в последнее время потребление L-лизина интенсивно растет – 12-15% прироста ежегодно – и приблизилось сегодня к 500 тыс.т.год. До начала экономических реформ СССР являлся крупнейшим производителем L- лизина (до 13 мирового производства в середине 80-х годов).
Технологическая часть
1. Характеристика конечной продукции производства
Лизин – это незаменимая аминокислота входящая в состав практически любых белков необходима для роста восстановления тканей производства антител гормонов ферментов альбуминов.
В настоящее время установлено что лизин в организме является не только структурным элементом белка но и выполняет ряд важных биохимических функций — является предшественником карнитина и оксилизина способствует транспорту кальция и стронция в клетки и др.
Доказано что лизин улучшает аппетит способствует секреции пищеварительных ферментов предотвращает кариес зубов у детей.
В основном L-лизин используется в качестве кормовой добавки что связано с низким количеством этой аминокислоты в растительных кормах.
Лизинсодержащие препараты могут использоваться в растениеводстве. Применение таких препаратов содержащих кроме аминокислот и другие биостимуляторы дает значительное увеличение урожая тепличных и полевых сельскохозяйственных культур.
Кроме того предложено использовать препараты лизина в качестве пищевых атрактантов для дезориентации личинок проволочников.
Пантотенат лизина может быть использован против лейкопении. Противоанемическим и анаболизирующим действием обладают соли фитиновой кислоты и лизина оксилизина. Ацетиласпартат лизина может использоваться для лечения миокарда интоксикаций эндогенного или экзогенного происхождения заболеваний печени и т. д.
Образующиеся после ферментации клетки микроорганизмов наряду с маточными растворами обычно утилизируют в белковый кормовой продукт по технологии производства кормовых дрожжей.
Лизин(26-диаминогексановая кислота) — алифатическая аминокислота с выраженными свойствами основания; незаменимая аминокислота. Лизин известен в виде двух оптически активных D- и L-форм. Бесцветные кристаллы. Природный L-лизин (tпл224—225°С с разложением) хорошо растворим в воде кислотах и основаниях плохо — в спирте. Выделен в 1889 из гидролизата казеина синтезирован в 1902; входит в состав почти всех белков животного и растительного происхождения (в большом количестве лизин содержится в гистонах и протаминах в малом — в белках злаков. Отсутствие лизина в пище замедляет рост у детей у взрослых приводит к отрицательному балансу азота и нарушению нормальной жизнедеятельности организма. Суточная потребность в лизине у взрослых составляет 23мгкгмассы тела у младенцев — 170мгкг.
Химическая формула: C6H14N2O2
2. Химическая схема производства
Химизм образования молекулы лизина показан на рис. 1.
При получении лизина необходимо исключить нежелательные побочные процессы. Так при недостаточной аэрации может идти образование аланина или молочной кислоты вместо синтеза лизина. Очень важным фактором является концентрация дефицитных аминокислот — гомосерина метионина и треонина в среде. Для нормального роста и биосинтеза лизина культурой Brevibacteriumsp. 22 оптимальной считается концентрация треонина в 800 мг метионина — 200 мг на литр питательной среды. Кроме того для развития культуры необходим тиамин в концентрации 200 мкг на 1 л среды. Важным регулятором процесса является биотин. Одна и та же культура Brevibacteriumsp. 22 при концентрации биотина в среде равной 1—4 мкгл продуцирует глутаминовую кислоту а при концентрации 15— 20 мкгл — лизин. Считают чтобиотин изменяет проницаемость клеточной оболочки. При концентрации биотина 25 мгл стимулируется также образование молочной кислоты.
Рис. 1.Химизм биосинтеза лизина
Важную роль играет треонин являясь обязательным фактором роста на начальном этапе ферментации. Однако концентрация его не должна быть большой так как на дальнейших этапах ферментации (при синтезе лизина) он может действовать как ингибитор фермента аспартаткиназы. Присутствие лизинаусиливает ингибирующие свойства треонина.
В производственных условиях если выход лизина составляет 357% от используемых сахаровсуммируемое превращение глюкозы аммиака и кислорода влизин и клеточную биомассу можно описать уравнением:
0C6H12O6+ 219O2+ 86NH335C6H14N2O2+ 16C8H13O4N + 262CO2+ 380H2O + 1669кДж
В правой части данного уравнения первый член показывает количество лизина получаемого из глюкозы. Из 1 молекулы глюкозы образуется 035 молекулы лизина. Второй член характеризует образование биомассы. Из уравнения видно что на переработку каждой молекулы глюкозы требуется 219 молекулы кислорода. Это значит что интенсивность аэрации во время роста культуры должна составлять 2—4 г 02в час на 1 л среды.
3. Технологическая схема производства
В зависимости от назначения из культуральной жидкости можно получить различные микробиологические препараты (рис. 1): жидкий концентрат лизина (ЖКЛ) сухой кормовой концентрат лизина (ККЛ) кристаллический лизин.
Рис. 2.Технологическая схема производства препаратов лизина
Для биосинтеза лизина используют гомосериндефицитные мутанты ауксотрофных бактерий родовBrevibacteriumMicrococcusCorynebacterium.
4. Характеристика сырья материалов
В промышленных условиях в качестве источника углерода применяют фуражное зерно мелассу гидрол гидролизаты целлюлозосодержащего сырья крахмал а также уксусную кислоту.
4.1 Приготовление стерильных питательных сред
Все продуценты лизина являются биотинзависимыми микроорганизмами. Количество биотина в среде должно быть значительно выше (29 мкгл) чем это необходимо для нормального роста и развития микробной клетки (4–5 мкгл). Если снизить количество биотина до 1–2 мкгл биосинтез лизина замедляется но одновременно усиливается образование глутаминовой кислоты.
Источником биотина витаминов и ряда аминокислот являются обычно кукурузный экстракт и свекловичная меласса. Максимальный биосинтез лизина наблюдается на средах с сахарозой (табл. 1).
Влияние источника углерода (концентрация 75 %) на биосинтез
L-лизина продуцентом Brevibacterium flavum
Ассимилляция сахара %
Существенное значение в процессе ассимиляции углеродсодержащих соединений имеет их концентрация в питательной среде. Наибольшее количество лизина получено на средах содержащих 10–12 % сахарозы. При более высоких концентрациях сахарозы удельная скорость роста продуцента снижается и уменьшается коэффициент конверсии сахара (YPS).
4.2 Приготовление посевного материала
Посевной материал готовится в две стадии: сначала в колбах а затем в посевных аппаратах при аэрации (11мин) и интенсивном перемешивании и автоматическом регулировании температуры (300С) и рН=7 в соответствии с регламентом.
Если в качестве источника углерода используют уксусную кислоту (ацетат аммония) то вследствие угнетающего действия ацетат-ионов на рост клеток при концентрации выше 2 % осуществляют дробную подачу субстрата по мере его потребления.
Промышленными продуцентами лизина являются гомосериндефицитные мутанты ауксотрофных бактерий родовBrevibacteriumMicrococcusCorynebacterium.
Клетки Brevibacteriumsp. 22 культуры представляют собой неподвижные грамположительные палочки длиной 12—25 мкм но иногда могут иметь овальную или круглую форму.
Клетки имеют максимальную длину в логарифмической фазе роста. У быстрорастущих клеток хорошо выражен рибосомальный белоксинтезирующий аппарат а у медленно растущих но интенсивно синтезирующих лизин — мембранная система. У клеток интенсивно синтезирующих лизин большую активность проявляют и ферменты цикла Кребса многие из которых связаны с мембранами.
Среди источников азота наиболее часто используют соли аммония и кукурузный экстракт (получают обработкой кукурузных жмыхов серной кислотой при 90–100 °С) кислотные гидролизаты дрожжей или казеина. Последние содержат необходимые ауксотрофному штамму аминокислоты и витамины. Оптимальное соотношение углерода и азота в среде составляет 11 : 1 (при его увеличении выход лизина падает при уменьшении накапливается аланин). В питательной среде также должны содержаться соли калия магния и фосфора (табл. 2).
Состав питательных сред при выращивании продуцента лизина (%)
Промышленный ферментер
Меласса (по содержанию сахара)
Кукурузный экстракт (содержание СВ 50 %)
Однозамещенный фосфат калия
Двухзамещенный фосфат калия
Пеногаситель синтетический
Гидролизат соевой муки
4.3 Условия культивирования
Общая схема производства препаратов лизина представлена на рис. 2
Процесс получения лизина требует строгих асептических условий.
Выращивание производственной культуры продуцента лизина обычно осуществляется периодическим способом в ферментаторах объем которых составляет 50 63 или 100 м3. Посевной материал в количестве 5–10 об. % от объема питательной среды поступает в ферментатор. Сразу после засева в него подается воздух нагретый до 50 °С из расчета 1 объем воздуха на 1 объем питательной среды в минуту при давлении 012–013 МПа.
Продолжительность ферментации составляет 55–72 ч процесс проводят при интенсивном перемешивании среды температуре 28–32 °С рН = 70÷75 (поддерживается добавлением в среду аммиачной воды) и периодической подачей стерильного пеногасителя.
Процесс культивирования состоит из двух стадий. В первые сутки клетки потребляют около 25 % углеводов и азотистых веществ; в это время накапливается почти вся биомасса. На второй стадии скорость накопления биомассы резко снижается но в КЖ происходит накопление лизина. По окончании процесса перестает потребляться титрующий агент (аммиачная вода) и концентрация лизина составляет 60–100 гл биомассы накапливается 10–15 гл (СВ) коэффициент потребления сахара в расчете на лизин составляет 25–35 %.
5. Получение препаратов лизина
В зависимости от назначения из КЖ можно получить различные микробиологические препараты (рис. 2): жидкий концентрат лизина (ЖКЛ) сухой кормовой концентрат лизина (ККЛ) кристаллический лизин.
5.1Жидкий концентрат лизина
Для получения ЖКЛ и ККЛ культуральную жидкость содержащую 10–13 % СВ подкисляют HCl до рН = 50 и добавляют 015% раствор гидросульфита натрия для стабилизации лизина. Стабилизированную культуральную жидкость упаривают под вакуумом до 35–40 % СВ.
5.2Сухой концентрат лизина
Сухой концентрат лизина (ККЛ) получают высушивая ЖКЛ в распылительных сушилках до влажности 5–6 %. Сухой ККЛ очень гигроскопичен поэтому сразу после сушки его упаковывают в полиэтиленовые мешки.
Менее гигроскопичный ККЛ получают высушивая ЖКЛ вместе с наполнителями (костной мукой кормовыми дрожжами пшеничными отрубями и др.).
В состав кормовых препаратов входят помимо лизина и другие аминокислоты а также витамины макро- и микроэлементы (табл. 3).
Химический состав кормовых препаратов лизина
Аминокислотымасс.%от массы СВ
Глутаминовая кислота
Аспарагиновая кислота
Азотистые веществамасс.%от массы СВ
Рибофлавин (витамин В2)
Пантотеновая кислота (витамин В3)
Фолиевая кислота (витамин В4)
Пиридоксин (витамин В6)
Никотиновая кислота (витамин РР)
Другие органические вещества масс. % от массы СВ:
редуцирующие вещества
Минеральные вещества масс.%от массы золы
Зола масс. % от массы СВ
Микроэлементы мг100 г
5.3Кристаллический лизин
Кристаллический лизин выделяют из КЖ после отделения биомассы.
Для получения кормовых продуктов пригодны препараты лизина с содержанием основного вещества (лизинмонохлоргидрата) от 70 % и выше. При этом допускается окраска кристаллов в желтый и светло-коричневый цвета. К препаратам медицинского назначения предъявляются более жесткие требования; для парентерального питания содержание основного вещества должно быть не ниже 99 %.
При нормальном течении процесса доля побочных аминокислот не превышает 3 % от содержания лизина доля микробных клеток — 15 %. Для отделения биомассы от КЖ используют саморазгружающиеся сепараторы а также фильтрование с намывным слоем либо на барабанном вакуум-фильтре либо на рамных фильтр-прессах с последующей промывкой осадка водой.
Растворы содержащие лизин после подкисления соляной кислотой (рН = 50÷52) и введения стабилизатора (NaHSO3) концентрируют выпариванием в вакууме до 45–50 % СВ. Полученный концентрат подвергают кристаллизации которую проводят при 5–12 °С в течение 1–2 сут. Осадок отделяют от маточника в проточных промышленных центрифугах и далее высушивают в распылительной сушилке или в кипящем слое. Готовый продукт как правило окрашен в коричневый цвет и содержит не менее 70 % основного вещества.
Другим способом выделения лизина является ионообменный процесс. Для этого раствор продукта подкисляют H2SO4до рН = 16÷20 в результате чего образуется дикатион аминокислоты. После хемосорбции на катионите (КУ-2х8) используемом в Н+илиNH4+форме отделяются примеси нейтральной и кислотной природы. Аминокислоты элюируют из катионита 05–5 % гидроксида аммония раствор упаривают подкисляют HCl до рН = 49÷50 а концентрат кристаллизуют при 5–12 °С получая кристаллы монохлоргидрата лизина светло-желтого или светло-коричневого цвета которые после высушивания содержат 90–95 % основного вещества и 10–125 % золы. Для получения препарата более высокой степени чистоты в схему очистки включают стадию обработки раствора активным углем перекристаллизацию из 50% этанола и др.
Сделать следующие расчеты:
- расчет мощности потребляемой мешалкой на перемешивание;
- тепловой расчет аппарата;
- материальный баланс на 1 загрузку;
- расчет установки для пеногашения.
Параметры процесса и физико-химические показатели среды следующие:
- плотность среды с = 1100 кгм3 ;
- динамическая вязкость среды с = 000145 Па·с;
- теплоемкость среды С = 4186 Дж(кг·К);
- коэффициент заполнения Кф = 065;
- рабочее давление воздуха в аппарате над уровнем жидкости р = 030·105 Па;
- температура культивирования t = 30 °С;
- температура воды на входе в рубашку или змеевик t1 = 15 °С на выходе t2 = 25 °С;
Используется жидкий пеногаситель в количестве 1 кг на 1 м3 среды готовится 1 раз в сутки на 1 аппарат.
Стерилизация масла осуществляется путем нагревания его от tм' = 20 °С до tм'' = 130 °С паром (р = 4·105 Па) через змеевик из трубок диаметром 2925 мм.
1. Расчет ферментера
Рабочий объем аппарата
Где – общий объем ферментатора;
– коэффициент заполнения.
Внутренний диаметр аппарата принимаем
Эллиптические днища для аппарата такого диаметра имеют следующие показатели (ГОСТ 6533 – 78): внутренний диаметр ; высота эллиптической части ; высота отбортовки; внутренняя поверхность ; емкость днища ; толщина стенки днища .
Согласно ГОСТ 6533 – 78 принимают соответствия:
Полный объем ферментера:
Объем цилиндрической части:
Где – объем эллиптических днищ; ;
Где F – площадь сечения емкостей по внутреннему диаметру;;
Общая высота ферментатора:
Расчет корпуса ферментера на внешнее давление
Для отвода тепла выделяемого культурой при развитии микроорганизмов в рубашку подают воду под давлением p = 1 кГсм2 (00981 МНм2). Под влиянием давления корпус может подвергнуться деформации. Сделаем проверочный расчет корпуса посевного аппарата на устойчивость формы против деформации.
Рабочее давление воды в рубашке p = 1 кГсм2 (00981 МНм2) должно быть меньше критического давления pкр при котором цилиндрическая форма сосуда становится неустойчивой и происходит деформация. Запас на устойчивость формы сосуда для вертикальных цилиндров принимаем 4-хкратный. При рабочем избыточном давлении в рубашке 1 кГсм2 pкр = 1 · 4 = 4 кГсм2 (03924 МНм2).
Толщина стенки ферментера подверженного наружному давлению:
r – средний радиус цилиндра; r = = = 101 м или 101см;
– коэффициент Пуассона; = 03;
E – модуль упругости углеродистой стали; E = 2100000 кГсм2.
S = 101 = 49 см или 0049 м.
Расчет наружной стенки рубашки ферментатора.
Толщина стенки рубашки ферментатора:
Где – внутренний диаметр цилиндра рубашки м;
– рабочее давление в рубашке; Р=000981 МН;
– дополнительное напряжение материала на растяжке =115 МН;
– коэффициент прочности сварных швов =09;
С – прибавка к толщине стенки С=0004 м.
2. Расчет механической мешалки ферментатора
Для интенсивного перемешивания культуральной жидкости используют турбинные мешалки
Диаметр турбинной мешалки согласно нормам:
Для более эффективного перемешивания применяют сдвоенную шестилопастную турбинную мешалку (на одном конце вала – 2 мешалки) диаметром
Для перемешивания среды вязкостью рекомендуется окружная скорость мешалки [6 225c табл.15].
Число оборотов мешалки:
Так как среду растущих бактерий-продуцентов лизина требуется интенсивно
перемешивать то применяем n = 318 обс = 1908 обмин.
По каталогу для мешалки с таким числом оборотов принимаем вертикальный редуктор типа ВО-VI-40180-1500.
Мощность потребляемая одной мешалкой на перемешивание среды без учета влияния вспомогательных устройств:
где – плотность среды = 1100 кгм3;
n и – число оборотов и диаметр мешалки n = 318 обс = 0600 м.
– критерий мощности зависящий от интенсивности перемешивания
характеризующейся центробежным критерием Рейнольдса (Re): = f().
где – плотность среды кг; ;
n – число оборотов; n = 318 обс;
– диаметр мешалки; = 0600 м;
с – динамическая вязкость среды с = 000145 Пас.
По графику нормали [7 226 c рис. 71] находим значение = f() для турбинной мешалки.
Где: m = где а и в – коэффициенты а = 1 в = 40 [7 226 c рис. 71].
Расчетная мощность на валу мешалки:
где – мощность потребляемая одной мешалкой на перемешивание среды без учета влияния вспомогательных устройств (рассчитана ранее);
– коэффициент учитывающий степень заполнения аппарата перемешиваемой средой:
где – высота слоя перемешиваемой жидкости для турбинных мешалок:
( – высота аппарата).
Коэффициент учитывающий увеличение потребляемой мощности в результате повышения сопротивления среды в процессе развития культуры микроорганизмов = 11.
Сумму коэффициентов К учитывающих увеличение потребляемой мощности вызываемое вспомогательными устройствами находящимися внутри аппарата принимаем из [6 226 c табл. 16].
- 4 отражающие перегородки шириной учитывает коэффициент
- дополнительная мешалка: = 035;
- трубка для подвода воздуха: = 02;
- гильза для термометра: = 01.
К = 15 + 035 + 02 + 01 = 215.
Мощность необходимая для преодоления трения в сальнике:
где n и – число оборотов и диаметр вала n = 318 обс; = 0057 м;
– толщина набивки сальника вала= 0012 м;
Р – рабочее давление воздуха в аппарате над уровнем жидкости Р=30000Па;
– высота набивки сальника
Для определения рекомендуется принимать р ≤ Па.
Диаметр приводного вала мешалки определяется по приближенной формуле находя из него прочности на кручение:
где С – прибавка на коррозию эрозию и износ С = 3 мм;
– допускаемое напряжение для материала вала на кручение:
– крутящий момент на валу мешалки;
Для обеспечения жесткости принимаем = 70 мм. Ток вала расположенный выше нижней турбины будет иметь диаметр d’=75ммм; участок вала расположенный выше верхней турбины d”=80мм при проходе через сальник.
Материалом вала принимаем сталь марки Ст.45. Для этого материала предел прочности на растяжение (ГОСТ 1050) = 610 МНм2 (около 62 кгмм2). Принимаем запас прочности = 26.
Допустимое напряжение на растяжение:
= 61026 = 234 МН (около 238 кг);
Допустимое напряжение на кручение:
= 06 · = 06 · 234 = 140 МН (около 1425 кг).
Для валов перемешивающих устройств допустимое напряжение на кручение:
= 05 · = 05 · 140 = 70 МН (около 1713 кг).
Толщина сальниковой набивки:
где – диаметр вала при проходе через сальник принимаем = 008 м.
Окончательная установочная мощность приводного электродвигателя
где – к.п.д. редуктора привода = 095.
По каталогу НИИХиммаша подбираем вертикальный привод ВО-V-40180-1500.
Вал редуктора прсоединяется к валу перемешивающего устройства продольно-разъемной муфтой; выходной вал редуктора вращается со скоростью 180 обмин. Электродвигатель АО2-82-4 Nэл = 55 кВт
3. Тепловой расчет ферментатора
Примерный состав загрузки поступающей в рабочий объем ферментатора при культивировании бактерий-продуцентов лизина приведен в таблице 1.
Кукурузный экстракт 2%
Дигидроортофосфат калия 06%
Гидроортофосфат калия 01%
Рабочий объем ферментатора :
% мелассы (100 кг) в 1 объема.
Значит в 1 объема содержится 50 кг сахара а в 65 – 325 кг сахара соответственно.
Мсах. = 325+39=364 кг
В процессе развития микромицетов происходит диссимиляция сахаров с выделением избыточного тепла:
С6Н12О6 + 6О2 6Н2О + 6СО2 + 674 ккал.
При сгорании 1 моль сахара выделяется 674 ккал тепла или 2820 кДж тепла.
Масса 1 гмоль сахара составляет: 12 · 6 + 1 · 12 + 6 · 16 = 180 г или 018 кг.
Тепловыделение составит: 2820018 = 15670 кДжкг сахара.
На основании экспериментальных данных полагаем что усвоение сахара развивающейся культурой микроорганизмов происходит в течение 48 часов. Для упрощения расчетов принимаем что тепловыделение в этот период происходит равномерно.
Тогда количество биологического тепла выделяемого этой культурой:
Во избежание перегрева среды выделяемое тепло отводят. Тепло отводится охлаждающей водой воздухом подаваемым на аэрирование культуры теплоизлучением .
Тепловой баланс ферментатора:
В расчетах можно не принимать во внимание т.к. величина его незначительна поскольку воздух подают в аппарат с температурой близкой к температуре среды: .
Потери на теплоизлучение в окружающую среду принимаем 2 % от :
Тепло отводимое водой:
Расход воды для отвода тепла (охлаждения ферментатора):
где и – температура воды при входе в рубашку ( = 15 ºС) и при выходе из рубашки ( = 25 ºС).
Потребная поверхность охлаждения ферментатора:
К – коэффициент теплопередачи от охлаждающей воды к охлаждаемой среде:
Для данного случая (32) средняя разность температур теплоносителей:
Принимаем значение К=450 Вт(К) [5 11с табл. 2].
Загрязнение стенок отложениями в процессе эксплуатации приводит к ухудшению коэффициента теплопередачи поэтому для расчета принимаем К=450 Вт(К)
Тогда F = (450909) = 141
При диаметре корпуса ферментатора высота рубашки:
4. Материальный баланс на одну загрузку.
Материальный баланс на 1 загрузку ферментера вычисляется по формуле:
Где – объем пеногасителя; объем пеногасителя на одну загрузку составляет 5% от : ;
– объем посевного материала 10% от ;
– объем среды в ферментаторе;
– объем питательной среды;
- потери на стенках аппарата -2%;
– потери культуральной жидкости уносимые воздухом – 15%:
– расход входящего и выходящего воздуха
– объем культуральной жидкости после культивирования:
5. Расчет установки для пеногашения
При перемешивании среды в ферментаторе в период развития в нем микроорганизмов во многих случаях происходит образование пены и вынос ее из аппарата. Во избежание образования пены в ферментаторы вводят жидкие пеногасители в количестве 05 - 10 кг на 1 среды. Предварительно пеногаситель стерилизуют в отдельном аппарате из которого пеногаситель пропускают в сборник-дозатор.
Часовой расход масла на пеногашение при работе ферментатора:
Суточный расход масла на пеногашение:
Полный объем дозатора для пеногасителя принимаем из расчета вмещения в него суточной потребности при коэффициенте заполнения 08:
Согласно ГОСТ 9931-85 примем корпус стальной со змеевиком объемом 01. Внутренний диаметр дозатора ; высота его Н=825мм. Днище сферическое. Крышка съемная.
Стерилизация масла осуществляется путем его нагревания от до = 130 С паром (р = 4· Па) через змеевик из трубки диаметром 2925мм.
Количество тепла затрачиваемое на стерилизацию суточной потребности пеногасителя (масла):
где ρ – плотность масла ρ = 910 кг;
с – теплоемкость масла с = 2093 Дж(кгград);
3 – коэффициент учитывающий потери тепла стерилизации в окружающую среду.
Расход пара на стерилизацию масла:
где – энтальпия насыщенного пара при Р = 4 ; = 2750 кДжкг;
– энтальпия конденсата пара при Р = 4 ; = 812 кДжкг [7 532 с табл. LVII].
Объемный расход пара на стерилизацию:
Где – удельный объем пара при Р = 4 ; = 064 кг.
Поверхность нагрева змеевика определим по основной формуле теплопередачи:
где Q – количество тепла передаваемого маслу от стенки змеевика при условии что нагрев осуществляется в течение 05 ч.
Средняя логарифмическая разность температур:
Где – температура конденсата пара при Р = 4 : =1436 С
При внешнем диаметре трубок змеевика с заданным диаметром d = 0029 м длина трубок змеевика:
Диаметр одного витка принимаем D = 029 м тогда число витков змеевика:
Принимаем n = 29 витков тогда поверхность нагрева змеевика:
Так как высота цилиндрической части дозатора выбранного диаметра по ГОСТ 9931-85 и должна быть расположена в цилиндрической част стерилизатора то при вычисляемой высоте змеевка равной сумме количества витков умноженных на внешний диаметр и расстояния между ними:
Где 0015 м – расстояние между двумя соседними витками;
– количество шагов змеевика;
– количество витков змеевика;
29 – внешний диаметр трубопровода змеевика;
Значит змеевик умещается в цилиндрическую часть стерилизатора. Простерилизованное масло охлаждают в течение 30 мин в самом стерилизаторе до 35 С путем подачи в змеевики воды. Количество тепла отводимое водой с учетом потерь 3 % на излучение:
Расход воды на охлаждение масла:
где – температура воды на входе в змеевик ; – температура на выходе их змеевика;
Потребная поверхность охлаждения пеногасителя в течение 05 ч:
6. Расчет дополнительного оборудования
Подбор фильтров для обеспыливания и очистки воздуха от микроорганизмов.
Воздух подаваемый в аппарат в качестве сушильного агента подвергается обеспыливанию и очистке от микроорганизмов для стерильности процесса. Воздух подвергают грубой очистке от взвесей и масляных металлических фильтрах.
Рабочий объем ферментатора
Общий расход воздуха воздуха на рабочий объем фильтра.
Сопротивление масляных фильтров определяется по формуле:
Где – толщина фильтра: =1 см; w – скорость воздуха перед входом в фильтр: w=4 мс.
Пусть начальная концентрация пыли в воздухе ун = 42 мг коэффициент очистки воздуха масляными фильтрами достигает 80 – 90 %:
где: – концентрация пыли в воздухе перед фильтром и после фильтра мг.
При концентрация пыли в воздухе после фильтра :
Продолжительность работы масляного фильтра при определяется по таблице 1 [4 18 с табл. 2] и равна 120 ч.
Потребная поверхность индивидуального фильтра для очистки воздуха посевного аппарата:
После грубого обеспыливания в масляных фильтрах воздух для тонкой очистки от отстатков пыли и бактерий пропускают через глубинные фильтры со стекловолокнистым фильтрующим материалом совмещенные со слоями стекловолокна и чесаного хлопка а также фильтры с тканью Петрянова и фторопластовым материалами. Эти фильтры выбираются по таблице [6 284 с табл. 20]. Исходя из полученных данных выбираем фильтр «Лайк» СП 317; СП617; СП1217; F = 17 . Производительность 2448 ; удельная нагрузка 150 на 1 ; скорость движения воздуха 42 смс.
Расчет емкостей для кислот и щелочей
Расход и кислоты и щелочи принимаем равным 2% от рабочего объема ферментатора. тогда рабочий объем емкостей будет равен: . С учетом коэффициента заполнения. С учетом коэффициента заполнения :
Внутренний диаметр емкостей принимаем .
Эллиптические днища для емкостей принятого диаметра имеют следующие показатели (ГОСТ 6533 – 78): внутренний диаметр ; высота эллиптической части ; высота отбортовки; внутренняя поверхность ; емкость днища ; толщина стенки днища
Полный объем емкостей для щелочи и кислот:
Объем цилиндрических частей емкостей для кислот и щелочи:
Высота цилиндрических частей емкостей для кислоты и щелочи:
Расчет емкости для культуральной жидкости
Количество культуральной жидкости с одной ферментации при учете потерь во время ферментации составит 90% от объема питательной среды:
Где – рабочий объем сборника культуральной жидкости.
Для расчета оборудования принимаем коэффициент заполнения для сборника . Тогда:
Согласно ГОСТ 6533-78 принимают соотношения:
Полный объем емкости для культуральной жидкости:
Объем цилиндрической части емкостей для культуральной жидкости:
где – объем эллиптического днища;
Высота цилиндрической части емкости для культуральной жидкости:
Общая высота емкости для культуральной жидкости:
Расчет центробежного насоса
Выбор диаметра трубопровода. Принимаем скорость раствора во всасывающей и нагнетающей системах равной 2 мс. Тогда диаметр трубопровода равен:
где Q – объемный расход суспензии с. () скорость суспензии мс.
Принимаем трубопровод марки Х18Н10Т диаметром 35х35 мм.
Уточняем скорость движения раствора:
Определение потерь на трение и местные сопротивления. Определяем величину критерия Рейнольдса:
где = 1050 кг– плотность суспензии;
= 16 Пас – вязкость суспензии.
Режим турбулентный.
Принимаем абсолютную шероховатость стенок труб е = 02 мм степень шероховатости = 7202 = 360 [7 22 с рис.15] находим значение коэффициента трения =0026.
Определяем сумму коэффициентов местных сопротивлений:
) для всасывающей линии:
- вход в трубу: = 05;
- нормальный вентиль (2): d = 002 м = 80 для d = 004 м = 49 [7 521 с];
Интерполяцией находим для d = 0056 = 378. Учитываем что вентиля два: ;
- колено под углом 90: ;
- дроссельная заслонка: при угле =15;
) для нагнетательной линии:
- выход из трубы = 1;
- нормальный вентиль (2); ;
- колено под углом 90(2): тогда
Определяем потери насоса:
Во всасывающей линии:
Во нагнетательной линии:
Общие потери напора:
Выбор насоса. Определяем полный напор развиваемый насосом:
где – давление в аппарате из которого перекачивается жидкость;
– давление в аппарате в который подается жидкость;
– геометрическая высота подъема жидкости складывается из расстояния от пола до крепления труб под потолком при поступлении среды в сборник за вычетом расстояния от пола до места выхода трубы из ферментера;
– потери напора во всасывающей и нагнетательной линиях.
Полезная мощность насоса определяется:
Принимая = 1 и = 06 для насосов малой производительности найдем
по формуле мощность на валу двигателя:
где – КПД соответственно насоса и передачи от электродвигателя к насосу.
Мощность потребляемая двигателем от сети при
С учетом коэффициента запаса мощности устанавливаем двигатель мощностью:
Устанавливаем центробежный насос марки Х65-50-160 [5 29 с табл. 3.1] со следующей характеристикой: производительность 69 мс напор 32 м КПД насоса 07.
Насос снабжен электродвигателем АВ100L2 номинальная мощность 55 кВт . = 085 частота вращения вала n = 483 .
Предельная высота всасывания рассчитывается при необходимости расположения насоса над резервуаром с раствором. Для центробежных насосов запас напора необходимый для исключения кавитации рассчитывают по формуле:
где – запас напора; n – частота вращения вала ; Q – объемный расход суспензии с.
По таблицам давлений насыщенного водяного пара найдем что при 30°С = 425 Па. Примем атмосферное давление равным = Па а диаметр всасывающего патрубка равным диаметру трубопровода. Тогда:
Таким образом центробежный насос может быть расположен над уровнем раствора в емкости на высоте менее 42 м.
Список использованной литературы
Горбатюк В.И. «Процессы и аппараты пищевых производств». –М: «Колос» 2000. -302 с.
Грачева И.М. Иванова Л.А. Кантере В.М. «Технология микробных препаратов аминокислот и биоэнергия» - М.: «Колос.1992.-388с.
Иванова Л.А. Дорошенко М.И. Иванова И.С. «Методические указания к выполнению курсового проекта по дисциплине «Процессы и аппараты биотехнологии»». Часть 1. М:2000. -35 с.
Иванова Л.А. Иванова И.С. «Методические указания к выполнению курсового проекта по дисциплине «Процессы и аппараты биотехнологии»». Часть 2. М:2002. -39 с.
Иоффе И.Л. «Проектирование процессов и аппаратов химической технологии» - Л.:Химия1991-352 с.
Колосков С.П. «Оборудование предприятий ферментативной промышленности» Л.:Химия1969.-386с.
Павлов К.Ф. Романков П.Г. Носков А.А. «Примеры и задачи процессоы и аппаратов химической технологии: Учебное пособие для вузов» Под ред. чл. корр. АН СССР П.Г. Романкова. -9-е изд. перераб. И доп. –Л.: Химия1981.-560с. ил.
Рекомендуемые чертежи
- 02.11.2023
- 14.06.2022
- 23.10.2023
Свободное скачивание на сегодня
Обновление через: 6 часов 31 минуту