Восстановление золотника рулевого управления трактора МТЗ




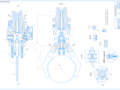
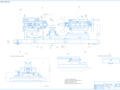
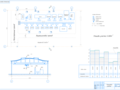
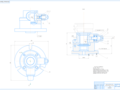
- Добавлен: 24.01.2023
- Размер: 913 KB
- Закачек: 0
Описание
Состав проекта
![]() |
![]() |
![]() ![]() ![]() |
![]() |
![]() ![]() ![]() ![]() |
![]() |
![]() |
![]() ![]() ![]() ![]() |
![]() ![]() ![]() ![]() |
![]() ![]() ![]() ![]() |
![]() |
![]() |
![]() |
![]() |
![]() |
Дополнительная информация
сам диплом.docx
1.Характеристика объектов производства ..
2.Определение типа производства
3. Анализ конструкции детали на технологичность ..
4.Анализ базового технологического процесса .
5. Выбор заготовки .
6. Разработка маршрутного технологического процесса
7.Расчет режимов резания
7.1 Токарные операции
7.2 Зубодолбежные операции .
8 Технологическое нормирование операций
9 Описание инструментальных наладок .
КОНСТРУКТОРСКИЙ РАЗДЕЛ ..
1. Проектирование станочных приспособлений ..
2. Проектирование средств автоматизации.
2.1 Выбор и проектирование средств технологического оснащения РТК
2.2 Выбор основного технологического оборудования
2.3 Выбор промышленного робота
2.4Разработка компоновочных схем РТК
ИССЛЕДОВАТЕЛЬСКИЙ РАЗДЕЛ
1. Методы изготовления заготовок зубчатых колес
2. Основные методы формирования зубьев цилиндрических зубчатых колес
ПРОИЗВОДСТВЕННЫЙ РАСЧЕТ И РАЗРАБОТКА ПЛАНА ЦЕХА ..
2. Форма организации выполнения технологических процессов
3. Производственная структура участка .
4.1. Расчет количества основного оборудования
5 Проектирование подсистем
5.1. Расчет характеристик склада .
5.2. Расчет системы стружкоуборки
6 Строительные решения
7 Технико-экономические показатели участка
ОХРАНА ТРУДА И ЭКОЛОГИЯ
1 Безопасность труда на проектируемом участке ..
2 Методы и средства защиты от механических опасностей .
3 Методы борьбы с шумом
ЭКОНОМИЧЕСКАЯ ЧАСТЬ ..
СПИСОК ИСПОЛЬЗУЕМОЙ ЛИТЕРАТУРЫ 57
Технологический процесс в машиностроении характеризуется не только улучшением конструкции изделия но и непрерывным совершенствованием технологии производства. В настоящее время важно при минимальных затратах и в заданные сроки изготовить изделие применив современное высокопроизводительной оборудование технологическую оснастку средства механизации и автоматизации производственных процессов. От принятой технологии производства во многом зависит долговечность и надежность выпускаемых изделий а также затраты при их эксплуатации.
Одним из важнейших направлений научно-технического прогресса является автоматизация производства. Основной путь автоматизации механической обработки в серийном производстве – применение станков с числовым программным управлением. Известно что такая автоматизация в значительной степени сокращает штучное время улучшает условия труда способствует использованию многостаночного обслуживания. Развитие новых процессов на базе использования станков с ЧПУ роботов гибких производственных систем и вычислительной техники способствует созданию более совершенных машин снижению их себестоимости и уменьшению затрат на изготовление.
В механизмах автомобилей и тракторов для передачи крутящего момента преобразования вращательного движения в возвратно-поступательное а также поддерживания вращающихся деталей широко применяются так называемые круглые стержни т.е. детали которые характеризуются цилиндрической формой при габаритной длине более чем в два раза превышающей ее наружный диаметр. К круглым стержням относятся валы и оси штоки круглые тяги трубы пальцы и т.п. Наибольшее распространение получили валы имеющие различное служебное назначение конструктивную форму и размеры. В настоящее время широко используются как цельные так и пустотелые гладкие и ступенчатые валы; валы с фасонными поверхностями (кулачками шлицами зубчатыми венцами фланцами и т.п.). По форме геометрической оси валы могут быть прямыми коленчатыми и кулачковыми. В автотракторостроении наибольшее применение получили различные ступенчатые валы средних размеров со шлицами глухими и сквозными отверстиями. Шлицевые валы изготовляются в основном с закрытыми шлицами прямобочного и эвольвентного профиля. Достаточно часто используются и валы-шестерни.
Наиболее ответственными у валов являются посадочные цилиндрические и торцевые поверхности под подшипники шестерни муфты рабочие кромки манжет уплотнения а также шлицевые поверхности зубчатые венцы кулачки.
Шероховатость рабочих поверхностей шлицевых валов должна быть не более: для поверхностей под рабочие кромки манжет уплотнения Ra = 063 мкм; для посадочных поверхностей под подшипники диаметром до 80 мм Ra = 125 мкм диаметром более 80 мм Ra = 25 мкм; для цилиндрических центрирующих поверхностей шлицев Ra = 125 мкм; для боковых поверхностей шлицев вала с подвижным соединением Ra = 25 мкм с неподвижным соединением Rz = 20 мкм. Шероховатость боковых поверхностей зубьев валов-шестерён обычно составляет Ra = 25-5 мкм.
Требования по точности обработки рабочих поверхностей зависят от условий работы изделия и от точности сопрягаемых деталей. Как правило наиболее точные наружные цилиндрические поверхности валов изготовляют по 6-8 квалитетам. Радиальное биение посадочных поверхностей под подшипники качения относительно оси детали допускается в пределах 001-005 мм. При центрировании шлицев по наружному или внутреннему диаметрам допуски на эти размеры устанавливают по 6-му квалитету. Отклонение от параллельности боковых поверхностей шлицев относительно оси вала не должно превышать 005 мм на длине 100 мм. Точность зубчатых венцов валов-шестерён как правило соответствует 6-9-ой степеням точности по ГОСТ 1643-81 для цилиндрических зубчатых колёс и ГОСТ 9178-81 для конических зубчатых колёс. Наружную резьбу на валах выполняют по среднему классу точности с полем допуска 6g (ГОСТ 16093-81).
Материал деталей выбирают в зависимости от их назначения. Обычно валы и оси изготовляют из сталей обладающих высокой прочностью малой чувствительностью к концентрации напряжений хорошей обрабатываемостью и способностью подвергаться термической обработке. Этим требованиям наиболее отвечают конструкционные углеродистые стали 35 40 45 50 а также низколегированные стали 35Х 35ХС 40Х 40ХН 40Г 40ХС 50Х 50Г и др. Шлицевые валы и валы-шестерни для повышения долговечности выполняют из высоколегированных сталей так как в этом случае обеспечиваются необходимая твёрдость рабочих поверхностей и сердцевины высокая прочность ударная вязкость и износостойкость минимальное коробление при закалке. Так для изготовления шлицевых валов используют стали 18ХГТ 12ХН3А 20ХН3А с последующей термической обработкой до твёрдости 56-62 HRCЭ. Для повышения обрабатываемости исходные заготовки валов подвергают нормализации (твёрдость после термической обработки HB 187-230) или термическую обработку проводят после черновой обработки (после улучшения твёрдость HB 225-302 28-32 HRCЭ). Для повышения износостойкости и прочности отдельные поверхности подвергают закалке ТВЧ (глубина слоя 15-5 мм твёрдость в пределах 45-62 HRCЭ) цементации цианированию с последующей закалкой и отпуском (глубина слоя 01-11 мм твёрдость 58-62 HRCЭ) . Валы работающие в агрессивных средах выполняют из коррозионностойких сталей и сплавов. Распределительные и коленчатые валы часто изготовляют из специальных высокопрочных чугунов. Структура литого вала способствует лучшему гашению вибрации при работе двигателя. Такие валы менее чувствительны к концентрации напряжений.
Трудоемкость себестоимость и производительность процесса изготовления валов и осей а также качество их поверхностного слоя во многом определяются заготовкой. На выбор метода получения заготовки большое влияние оказывают материал детали ее служебное назначение объем годового выпуска форма поверхностей и размеры детали.
Основным направлением развития заготовительного производства является получение точных заготовок близких по форме и размерам к готовым изделиям что способствует экономии металла уменьшению объема механической обработки сокращению производственного цикла изготовления деталей и снижению себестоимости продукции в целом.
В условиях единичного и мелкосерийного производства валы изготавливают непосредственно из круглого или трубного проката. Горячекатаный и холоднотянутый прокат используется и в других типах производства для изготовления гладких валов и осей ступенчатых валов с небольшим числом ступеней и малыми перепадами диаметров. Заготовки для крупных деталей в единичном и мелкосерийном производствах могут быть получены ковкой на ковочных гидравлических прессах или на паровоздушных пневматических и рессорно-пружинных молотах.
При механической обработке валов в автоматизированном производстве в частности на станках с ЧПУ использование заготовок с низкой точностью недопустимо. В этом случае припуски и допуски заготовок должны быть на 10 - 30% меньше чем при обработке на станках с ручным управлением. Ужесточение требований по точности заготовок обрабатываемых на станках с ЧПУ обусловлено необходимостью уменьшить нагрузку на дорогостоящее оборудование стремлением сократить количество стружки создать благоприятные условия для работы режущего инструмента.
При производстве с достаточно большим масштабом выпуска а также при изготовлении валов более сложной конфигурации со ступенями значительно различающимися по диаметрам заготовки целесообразно получать горячей объемной штамповкой имеющей существенные преимущества перед ковкой. Объемную штамповку выполняют в открытых и закрытых штампах и штампах для выдавливания. Горячим выдавливанием получают заготовки валов со ступенями убывающими по диаметру: на гидравлических и кривошипных горячештамповочных прессах при длине вала до 300 мм на горизонтально-ковочных машинах при длине вала более 150 мм. При получении заготовок этим методом коэффициент использования материала достигает 07. Повышению производительности горячей штамповки и улучшению качества заготовок способствует автоматизация процесса которая облегчает условия труда и уменьшает вероятность травматизма. Перспективным направлением является использование при горячей объемной штамповке квадратного профиля исходного металла взамен круглого т.к. себестоимость квадратного профиля значительно ниже что подтверждается опытом работы кузнечно-штамповочных цехов наиболее развитых в промышленном отношении стран .
Прогрессивным методом получения заготовок является штамповка на радиально-обжимных и ротационно-ковочных машинах. На этих машинах обрабатывают осесимметричные детали с цилиндрическими поверхностями диаметром до 600мм в горячем и холодном состоянии. Метод целесообразно применять при объеме годового выпуска деталей 3000и более. На радиально-обжимных и ротационно-ковочных машинах можно изготавливать ступенчатые и удлиненные поковки из углеродистых и легированных сталей сплавов металлокерамики и металлопорошков; получать отверстия малых диаметров на относительно большой длине.
Используя метод ротационного обжатия можно обеспечить шероховатость поверхности: Ra = 032-008 мкм при холодной и Ra = 5-125 мкм при горячей обработке. В этих случаях обжатие позволяет одновременно заменить точение и шлифование. Точность обработки при холодном обжатии соответствует 6-8-му а при горячем- 11-13-му квалитетам; КИ.М. составляет 080-085 .
В массовом и крупносерийном производстве автомобилей и тракторов для изготовления полуосей осей катков распределительных валов деталей подвески и т.п. внедряются методы профилирования заготовок на станах поперечной поперечно-винтовой и поперечно-клиновой прокатки. Эти методы обеспечивают производство заготовок со значительным перепадом поперечных сечений хорошим качеством поверхностного слоя высокой точностью и производительностью. КИ.М. при этом достигает 090-095 что позволяет снизить себестоимость деталей .
Область использования литья для получения заготовок рассматриваемых деталей весьма незначительна.
ТЕХНОЛОГИЧЕСКИЙ РАЗДЕЛ
1. Характеристика объектов производства
Вал-шестерня содержит в конструкции цилиндрическую зубчатую поверхность внутреннего зацепления – эпицикл. Передача крутящего момента осуществляется от шейки вала посредством сегментной шпонки на зубчатую передачу внутреннего зацепления.
Для данного вала-шестерня была выбрана сталь 20Х ГОСТ 19281-73 . Она обладает высокой прочностью хорошей обрабатываемостью малой чувствительностью к концентрации напряжений а для повышения износостойкой способности должна подвергаться термической обработке.
Заготовку получаем методом горячей штамповки в закрытых штампах на кривошипном горячештамповочном прессе так как она по форме и размерам напоминает готовую деталь что значительно повышает производительность механической обработки и понижает себестоимость за счет малых припусков.
Для получения требуемой шероховатости применяем окончательное шлифование так как эти поверхности сопрягаются в коробке передач точными посадками.
2. Определение типа производства
Тип производства по ГОСТ 3.1121-84 характеризуется коэффициентом закрепления операций:
>=Kзо10 - массовое и крупносерийное производство;
>=Кзо20 - среднесерийное производство;
>=Кзо40 - мелкосерийное производство;
=Кзо – единичное производство.
Величина коэффициента закрепления операций определяется по формуле:
где О - суммарное число различных операций выполняемых на производственном участке в течении месяца;
Р - суммарное число рабочих мест на которых выполняются данные операции.
Тип производства рассчитываем следующим образом:
Определяем расчетное количество станков необходимых для выполнения каждой станочной операции:
где N = 7000- объем годового выпуска деталей оговоренный в задании на проектирование
tш-к – штучно-калькуляционное время i-ой операции мин
Fо - эффективный годовой фонд времени работы станка.
Fo = 3835ч для металлорежущих станков с ЧПУ.
Fo=3915 для металлорежущих станков без ЧПУ.12
Кв- средний коэффициент выполнения норм времени. Кв=1.2
Определяем принятое количество оборудования на каждой станочной операции Si для чего расчетное количество станков Срi округляем до целых значений.
Рассчитываем коэффициент загрузки каждого рабочего места:
Определяем число операций закрепленных за одним рабочим местом:
где hн - нормативный коэффициент загрузки оборудования hн = 075.
Рассчитываем величину коэффициента закрепления операций:
где -общее число рабочих мест на которых выполняются все станочные операции по изготовлению детали.
Тип производства – среднесерийное.
3. Анализ конструкции детали на технологичность
Отработка конструкции на технологичность – это комплекс мероприятий предусматривающих взаимосвязанные решения конструкторских и технологических задач направленных на повышение производительности труда снижение затрат и сокращение времени на изготовление изделия при обеспечении необходимого его качества.
Оценка технологичности проводится качественно и количественно с расчетом показателей технологичности по ГОСТ 14.201-83. При этом качественная характеристика предшествует количественной и характеризует технологичность конструкции обобщенно.
Технологичность детали оценивается сравнением трудоемкости и себестоимости изготовления различных вариантов ее конструкции. Деталь подвергаемая обработке резанием будет технологична в том случае когда ее конструкция позволяет применять рациональную заготовку форма и размеры которой максимально приближены к форме и размерам готовой детали а также использовать высокоэффективные процессы обработки.
Деталь имеет несложную конфигурацию наружного контура. Деталь имеет не симметричное расположение ступиц что может вызвать коробление детали при объемной закалке.
Деталь не требует создания искусственных технологических баз что позволяет провести токарную обработку за 3 установа. Токарная обработка не требует применения специальных приспособлений.
Конструкция детали позволяет применять рациональные формы и размеры заготовок.
Коэффициент использования материала Кми.
Коэффициент точности обработки Ктч.
где: Аср – средний квалитет точности обработки детали по всем поверхностям.
Коэффициент шероховатости поверхности Кш.
где: Бср – среднее числовое значение параметра шероховатости всех поверхностей детали
Анализ рабочего чертежа детали.
Наименование поверхностей
Количество поверхностей
Параметр шероховатостимкм
Внутренняя цилиндрическая поверхность
Наружная цилиндрическая поверхность
Зубчатая поверхность
Определяем Ктч и Кш.
Так как Ктч > 08 а Кш 032 деталь можно считать технологичной.
4. Анализ базового технологического процесса
Базовый технологический процесс содержит все операции необходимые для получения детали заданной точности включая химико-термическую обработку и технический контроль. Операции составлены в необходимой последовательности. Но очень низка степень концентрации операций из-за этого технологический процесс содержит большое число операций.
Метод химико-термической обработки обоснован назначением и условиями эксплуатации детали. Деталь подвергается закалке и отпуском ТВЧ но т.к. требования по твердости поверхностного слоя предъявлены только к некоторым поверхностям следовательно целесообразно подвергнуть цементации только эти поверхности а остальные поверхности защитить специальной мастикой.
Технологические базы выбраны с соблюдением принципов совмещения и постоянства баз.
Однако в базовом технологическом процессе применяется устаревшее оборудование режущий инструмент приспособления с ручным приводом. Применение современных конструкций режущего инструмента и прогрессивных марок инструментальных материалов современного оборудования позволит увеличить скорости обработки уменьшить to и tв. Применение гидро- или пневмоприводов для станочных приспособлений позволит сократить вспомогательное время. Применение современного оборудования также позволит повысить степень концентрации токарных операций.
5 Токарно-Винторезная
0 Токарно-Винторезная
5 Горизонтально- протяжная
0 Круглошлифовальная
Для современных требований предъявляемых к изготовлению заготовок деталей изделий характерны следующие технологические тенденции: максимальное приближение заготовок по формам и размерам к деталям требующимся по чертежу; экономия материала; применение прогрессивных способов получения заготовок.
Для изготовления детали большую роль играет выбор рационального вида исходной заготовки и способа её получения. Способ получения заготовки должен быть обусловлен ее стоимостью и дальнейшей обработкой. Наиболее широко для получения заготовок применяют следующие методы: литьё обработка металлов давлением и сварка а также их комбинации.
При выборе заготовки для заданной детали назначают метод ее получения определяют конфигурацию размеры допуски припуски на обработку и формируют технические условия на изготовление.
Для получения данной заготовки выбираем горячую штамповку в закрытых штампах на кривошипном горячештамповочном прессе. Этот метод обеспечивает изготовление относительно точных поковок без сдвига в плоскости разъема и с малыми припусками. Класс точности Т3 степень сложности С1 группа стали М1 конфигурация поверхности разъема штампа.
6. Разработка маршрута технологического процесса
Технологические процессы разрабатывают при проектировании
Перед разработкой ТП необходимо получить и изучить информацию которая делится на базовую руководящую и справочную.
Базовая - сведения содержащиеся в конструкторской документации на изделие объем выпуска сроки подготовки производства. Рабочий чертеж детали содержит все размеры технические требования к качеству и шероховатости марку и твердость материала.
Руководящая - сведения по развитию отрасли план выпуска материала средств технологического оснащения стандарты на ТП.
Справочная - сведения о прогрессивных методах обработки каталоги номенклатурные справочники оборудования и оснастки. Материалы по выбору технологических нормативов (режимы обработки припуски расход материала и др.) и др. справочные материалы.
Всю механическую обработку разбивают по операциям и таким образом выявляют последовательность выполнения операций их число для каждой операции выбирают оборудование и определяют конструктивную схему приспособлений.
Задачей каждого предыдущего перехода является подготовка поверхности заготовки под последующую обработку и каждый последующий метод
( операция или переход) должен быть точнее предыдущего т. е. обеспечивать более высокое значение показателей качества детали. Поэтому механическая обработка делится на:
черновую обработку когда удаляется большая часть припуска что позволяет обнаружить возможные дефекты заготовки; на первых одной-двух операциях. При базировании по черновым базам обрабатываются основные технологические базы;
чистовую обработку когда в основном обеспечивается требуемая точность:
далее идут операции местной обработки по ранее обработанным поверхностям отделочные операции когда достигается требуемая шероховатость поверхности и окончательно обеспечивается точность детали.
Контроль в ТП предусмотрен с целью технологического обеспечения заданных параметров качества обработанной детали.
Разработанный ТП должен содержать общий план обработки детали и описание содержания операций ТП и выбор типа оборудования. Он должен быть прогрессивным обеспечивать повышение производительности труда и качества детали сокращать материальные и трудовые затраты и быть экологически безопасным.
Построение технологического маршрута обработки во многом определяется конструктивно-технологическими особенностями детали. Выбор маршрутной технологии существенно зависит от типа производства уровня автоматизации и применяемого оборудования.
При серийном производстве применяют универсальные станки с ЧПУ автоматы полуавтоматы агрегатные специализированы и специальные станки. Перспективным в серийном производстве является применение гибких производственных систем ( линий участков цехов) особенно при наличии условий для групповой организации производства.
Выбор станка на операцию определяется возможностью изготовления на нем деталей необходимой конфигурации и размеров обеспечения качества ее поверхности производительности оборудования а также экономическими параметрами.
Проектный техпроцесс
Токарно винторезный 16К20Ф3
Горизонтально фрезерный с ЧПУ 6Р10Ф3
0 Зубодолбежная с ЧПУ
Зубодолбежный 51А08ПФ2
5 Круглошлифовальная с ЧПУ
Круглошлифовальный с ЧПУ 3М151Ф2
7. Расчет режимов резания
Исходными данными для определения режимов резания являются: материал обрабатываемой заготовки и его физико-механические свойства; размеры и геометрическая форма обрабатываемой поверхности; технические условия на изготовление детали; материал типоразмер и геометрические параметры режущей части инструмента; тип и характеристика оборудования.
Режимы резания существенно влияют на точность и качество обрабатываемой поверхности производительность и стоимость обработки.
7.1 Токарные операции
При расчете режимов резания сначала определяют глубину резания. Глубина резания определяется величиной припуска на обработку и возможностью удаления его за один ход. При обработке за несколько рабочих ходов глубину резания устанавливают наибольшей с соответствующим уменьшением числа рабочих ходов. При этом для обеспечения заданной точности и шероховатости поверхности глубину резания на последних рабочих ходах уменьшают.
После определения глубины резания устанавливается подача. Подачу назначают максимально возможную. При черновой обработки ограничивающим фактором является прочность слабого звена технологической системы. При чистовой и отделочной обработке подачу устанавливают в зависимости от точности обработки и шероховатости поверхности.
Скорость главного движения определяют по формуле:
где Кv - произведение ряда коэффициентов.
Кмv – коэффициент учитывающий качество обрабатываемого материала.
где: Кг - коэффициент характеризующий группу стали по обрабатываемости
(для стали 12ХН3А при в=932 Мпа Кr=0.8).
в - предел прочности для заданной стали Мпа.
пv - показатель степени (обработка резцами из твердого сплава) n=1.
Кпv - коэффициент отражающий состояние поверхности заготовки (поковка
Киv - коэффициент учитывающий материал инструмента (Т15К6) Ки=1
Kiv Kv Krv – коэффициенты учитывающие влияние параметров резца.
m х у - показатели степени.
Период стойкости при многоинструментной обработки:
Т - стойкость инструмента. Т=60 мин.
t - глубина резания мм.
Рассчитываем частоту вращения шпинделя по формуле:
где V - рассчитанная скорость резания мсек.
D - обрабатываемый диаметр мм.
Определение потребной мощности двигателя.
Расчет сил резания по формуле:
где Кр - поправочный коэффициент:
где Кмр – коэффициент учитывающий влияние качества обрабатываемого материала на силовые зависимости рассчитывается по формуле:
где п - показатель степени п=0.75.
в - предел прочности материала заготовки 560 МПа.
Кр – коэффициент учитывающий геометрию главного угла Кр=089.
Кр - коэффициент учитывающий геометрию переднего угла Кр=1.25.
Кр – коэффициент учитывающий геометрию угла наклона рeжущей кромки Кр=1.
Кrр-коэффициент учитывающий радиус при вершине Кrр=1.
V - скорость резания ммин.
х у п - показатели степени
Расчет потребной мощности:
Сравниваем полученные данные с паспортными данными станка.
Уточненное значение скорости резания:
операция 005 черновое точение:
t1=2.06 мм S=13 ммоб
t2=1.5 мм S=1.3 ммоб (контурное точение)
Сv=340x=0.15y=0.45m=0.2
принимаем n1=655 обмин.
уточненные значения скоростей резания :
операция 005 чистовое точение:
t1=049 мм S=025 ммоб
t2=020 мм S=025 ммоб (контурное точение)
Сv=340244x=0.150.23y=0.450.3m=0.2
принимаем n1=2000 обмин.
7.2 Зубодолбежные операции
Расчеты проводим по методике 9
При расчете режимов резания сначала определяют число переходов. Затем определяют круговую подачу Sкр в зависимости от модуля колеса. Радиальные подачи принимают равными Sр=(01-03)Sкр. Затем определяют скорость резания V по таблицам
Число двойных ходов долбяка определяют по формуле
где L- длина хода долбяка.
операция 020 зубодолбежная с ЧПУ:
Число двойных ходов долбяка :
8 Технологическое нормирование операций
Техническая норма времени определяющая затраты времени на обработку служит основой для оплаты работы калькуляции себестоимости детали и изделия. На основе технических норм времени рассчитываются длительность производственного цикла необходимое количество станков инструментов и рабочих определяется производственная мощность цехов или участков. Норма времени является одним из основных факторов для оценки совершенства технологического процесса и выбора наиболее прогрессивного варианта обработки заготовки.
Расчет штучно-калькуляционного времени :
Расчет Тп-з по формуле:
Тпз=tчт+tнал+tподс+tуст(1.22)
где tчт - время на чтение чертежа tчт=10 мин.
tнал - время на наладку инструмента станка и приспособления tнал=12 мин.
tподс - время на получение и сдачу после инструмента и приспособления
tуст - время на установку резца на многорезцовой державке на сопряжённый размер.
Тпз=10+12+10+4=36 мин.
Расчет штучного времени :
tШТ=tо+tв+tоб+tт(1.23)
Расчет основного времени по формуле:
где l – расчетная длинна обрабатываемой поверхности.
i число рабочих ходов.
n частота вращения шпинделя.
Расчет tв по формуле:
tв=tмв+tус+tпо+tв+tиз+tпи+tзак(1.25)
где tус - время на установление и снятие заготовки
tпо - время на пуск и останов станка tпо=0.02 мин.
tв - время на включение и выключение подачи
tиз - время на измерения tиз=0.09 мин.
tпо - время на пoдвод инструмента tпо=0.09 мин.
tзак - время на закрепления заготовки.
Расчет tопtт tоб по формулам:
Операция 005 Токарная с ЧПУ
сумма основных времен tо= 174 мин .
сумма машинно-вспомогательных времен tмв=0.44 мин
Вспомогательное время
tв=0.44+0.15+0.02+0.01+0.09+0.09+0.15=0.95 мин
tоп=174+0.95=2.69 мин
Время на обслуживание
tт=0.04*2.69=0.1 мин
tоб=0.08*2.69=0.2 мин
tшт=2.69+0.1+0.2=299 мин
tшт-к=2.99+362400=300 мин
Операция 020 Зубодолбежная с ЧПУ
To расчитывем по формуле :
сумма машинно-вспомогательных времен tмв=0.24 мин
tв=0.24+0.15+0.02+0.01+0.09+0.09+0.15=0.75 мин
tоп=14.74+0.75=15.5 мин
tт=0.04*15.5=0.62 мин
tоб=0.08*15.5=1.24 мин
tшт=15.5+0.62+1.24=17.36 мин
tшт-к=17.36+362400=17.38 мин
9.Технико-экономическое обоснование проектного технологического процесса
Целесообразность разработанной операции механической обработки заготовки определим на основе сравнительной экономической эффективности двух вариантов: базового (с ручным управлением) и проектного (c ЧПУ).
Экономическая эффективность рассчитывается по величине годовой экономии на приведенных затратах .
где Сп'Сп" - сумма годовых приведенных затрат базового и проектного вариантов тнг.
где Cт - годовая технологическая себестоимость операции тнг;
K - сумма годовых капитальных затрат на операции тнг;
Ен - нормативный коэффициент эффективности капитальных вложений Ен=015.
Определение капитальных затрат
Капитальные затраты определяем по формуле:
К=Ср(Ко+Кзд+Кпу)(1.32)
где Ср - расчетное количество станков требуемых для обработки годового выпуска деталей
Ко - вложение средств в оборудование тнг;
Кзд - вложения в производственные помещения тнг;
Кпу - вложения в комплект управляющих программ тнг.
Вложение средств в оборудование определяем по формуле:
Ко=Кто+Кпт+Кк (1.33)
где: Кто - вложения в технологическое оборудование тнг.
Кпт - вложения в подьемно-транспортное оборудование тнг;
Кк - вложения в средства контроля тнг.
где Цто - оптовая цена станка тнг;
Кт - коэффициент учитывающий расходы на транспортировку Кт=11.
Вложения в производственные помещения определяем по формуле:
Kзд=Цпп (S+Sy) γ(1.35)
где Цпп - стоимость 1 кв.м производственной площади механического цеха Цпп = 80000 тнг;
S - площадь занимаемая станком м2;
Sy - площадь занимаемая выносными элементами м2;
γ - коэффициентучитывающий дополнительную производственную площадь приходящуюся на дополнительное оборудование.
Расчет технологической себестоимости:
Основан на использовании нормативов себестоимости одного машино-часа работы оборудования.
Ст=(Счс+Счи+Счэ+Сча+Счр+Счэл+Счп+Счир)+Собсл+Спп (1.36)
где СчсСчнСчэ - нормативы затрат по заработной плате станочников наладчиков и электронщиков приходящихся на 1 час работы оборудования со всеми начислениями кч;
СчаСчрСчэл - нормативы затрат на амортизацию оборудования ремонт и электроэнергию приходящихся на 1 час работы станка кч;
СчпСчир - нормативы затрат на амортизацию и ремонт приспособлений и инструментана 1 час работы кч.
Собсл - годовые затраты на обслуживание и ремонт ЧПУ тнг.
Спу - годовые затраты на подготовку и возобновление управляющих программ тнг.
Спп - годовые затраты на амортизацию и содержание производственных и помещений тнг.
Сравнение вариантов технологических процессов:
Для расчета экономической эффективности используем программу на ЭВМ
Обьем годового выпуска деталей: 2400
Количество операций в базовом варианте : 5
Количество операций в проектном варианте : 2
Коэффициент выполнения норм для станков
- с ручным управлением : 1.2
Коэффициент инфляции в станкостроении : 1
Сведения о маршрутах обработки.
Маршрут обработки в базовом техпроцессе :
Маршрут обработки в проектном техпроцессе :
Базовый вариант Расчетные величины
¦Номер¦Тшт.к¦Fo ¦S+Sy ¦ Цто ¦ Cp ¦ K ¦ Cт ¦ Cп ¦
¦ оп. ¦ мин. ¦час.¦кв. м. ¦тыс.тнг.¦ ¦ тыс.тнг. ¦ тнг. ¦ тыс.тнг. ¦
¦-------+-------+-----+--------+-----------+-----+----------------+---------- -+-----------------¦
¦ 005 ¦ 0.30 ¦4055¦ 3.3¦ 315.0¦ 0.0¦ 3895¦ 294000¦ 29459¦
¦ 010 ¦ 2.12 ¦4055¦ 3.3¦ 315.0¦ 0.0¦ 2752¦ 1356880¦ 136101¦
¦ 040 ¦ 1.71 ¦4055¦ 3.3¦ 315.0¦ 0.0¦ 2220¦ 1117440¦ 112077¦
¦ 050 ¦27.30 ¦4055¦ 7.6¦ 700.0¦ 0.2¦ 74104¦ 12473600¦ 1258476¦
¦ 070 ¦ 0.81 ¦4055¦ 3.3¦ 315.0¦ 0.0¦ 1051¦ 591840¦ 593420¦
L=====¦======¦====¦======¦========¦====¦============¦========¦====Проектный вариант Результаты расчета
¦ оп. ¦ мин. ¦час.¦ кв. м.¦тыс.тнг.¦ ¦ тыс.тнг. ¦ тнг. ¦ тыс.тнг. ¦
¦-------+--------+----+---------+----------+-----+-----------------+-----------+-----------------¦
¦ 005 ¦ 3.00 ¦3935¦ 7.1¦ 15100¦ 0.0¦ 12967¦ 1282240¦ 1286.130¦
¦ 020 ¦17.38 ¦4055¦ 1.8¦ 325¦ 0.1¦ 15837¦ 1404800¦ 1409.551¦
L=====¦======¦====¦======¦========¦====¦============¦========¦============-
где :Тшт.к Штучно-калькуляционное время операции.
S+Sy Суммарная площадь занимаемая станком с выносным оборудованием.
Цто - Оптовая цена станка без учета коэффициента инфляции.
Cp - Расчетное количество станков на данной операции.
K - Сумма годовых капитальных затрат на данной операции.
Cт - Годовая технологическая себестоимость данной операции.
Cп - Годовые приведенные затраты на данной операции.
Величина годовой экономии на приведенных затратах: 2476135 тнг.
10.Описание инструментальных наладок
Обработка производится на зубодолбежном станке с ЧПУ 51А08ПФ2 за один проход .Координаты нулевой точки берутся из соображения минимизации холостых ходов и возможности извлекания детали из приспособления .
За технологические базы используется внешний диаметр ступицы вала и торец. Расчет основных и машинно-вспомогательных времен производится табличным методом по листу наладки.
Используемый станок имеет следующие технические характеристики :
Предприятие изготовитель : Витебский станкостроительный завод им.Коминтерна
Вертикальный зубодолбежный станок с ЧПУ мод.51А08ПФ2
Вертикальный зубодолбежный станок с ЧПУ предназначен для обработки прямозубых циллиндрический зубчатых колес наружного и внутреннего зацепления методом обката. В условиях массового производства зубчатых колес по желанию заказчика станок может быть выполнен как автономным так и встроенным в автоматические линии. Станок имеет компоновку с вертикальной осью изделия и подвижным столом для изменения межцентрового расстояния.
Заготовка закрепляется в приспособлении на столе станка.
Программное обеспечение позволяет использовать работу станка в диалоговом режиме с многопроходным циклом и различными циклами врезания с точной остановкой шпинделя изделия для обеспечения более высокой точности обрабатываемых зубчатых колес Станок имеет ряд преимуществ:
- двухкорректная позиционная система ЧПУ "S
- бесступенчатая частота двойных ходов и круговой подачи; - современные привода и управление;
- пульт управления с визуализацией режимов и параметров обработки; - точность позиционирования межцентрового расстояния +- 3 мкм;
- точность позиционирования оборота заготовки +- 7";
- способы подачи на врезание: радиальная подача с обкатом радиальная подача без отката;
- удобное рабочее пространство; - система контроля за всеми фильтрами градации и смазки.
Технические характеристики:
Наибольший диаметр обрабатывемых зубчатых колес мм
Наибольший модуль обрабатываемых зубчатых колес мм не менее
Наибольшая высота венца обрабатываемых зубчатых колес мм
Наибольший номинальный делительный диаметр долбяка мм
Диаметр циллиндрической шейки оправки для долбяка мм
Диаметр рабочей поверхности стола (фланца шпинделя изделия) мм
Расстояние между осями стола и инструмента мм
Наибольшая длина регулировочного перемещения шпенделя инструмента (салазок суппорта) мм
Частота двойных ходов шпинделя инструмента в минуту (дв.ходмин)
0 1000 бесступенчато
Диапазон круговых подач мммин
Диапазон радиальных подач мммин
Колическтво управляемых координат (ХВ)
Дискретность координаты мкм
Дискретность координаты В угл. сек
Мощность главного привода кВт (двухскоростной двигатель)
Суммарная мощность приводов кВт
Габариты (с отдельно расположенными узлами и электрическим оборудованим) мм
Вес (с отдельно расположенными узлами и электрическим оборудованием)кг
Точность обрабатываемых зубчатых колес по DIN 3962
Возможные исполнения станка:
- с другим напряжением и частотой тока;
- экспортное и тропическое;
- с настройкой на обработку отдельной детали и способностью переналадки;
- с дополнительной стойкой для обработки колес-валов;
- с механизмом для долбления реек.
В комплект поставки станка входят:
- комплект сменных колес для регулировки гитары деления (обкат);
- сменные и запасные части принадлежности и вспомогательный инструмент а также гидроциллиндр для зажима изделия.
ИССЛЕДОВАТЕЛЬСКИЙ РАЗДЕЛ
1. Методы изготовления заготовок зубчатых колес
Зубчатые колеса в зависимости от области применения изготовляют из различных материалов: стали чугуна цветных металлов пластмасс и др. Каждый из этих материалов удовлетворяет определенным требованиям. Самым распространенным материалом из которого изготовляют зубчатые колеса является сталь. Ее применяют для зубчатых передач автомобилей тракторов самолетов станков и других машин которые передают большие нагрузки. Определяющими факторами для этих колес являются: прочность зубьев на изгиб контактная прочность и износ зубьев. При этом следует учитывать стоимость материала возможность обработки резанием степень деформирования в процессе закалки и т. д.
Для снижения уровня шума зубчатые колеса изготовляют из чугуна и пластмассы. Эти материалы по сравнению со сталью имеют меньшую стоимость лучшую обрабатываемость но колеса из этих материалов передают меньший крутящий момент чем стальные колеса. Зубчатые венцы червячных колес чаще всего изготовляют из бронзы которая обладает высокими антифрикционными и антикоррозийными свойствами. Зубчатые колеса насосов экономично изготовлять из металлического порошка.
Выбор метода изготовления заготовки зависит от формы и размеров детали ее материала и назначения объемов производства и т. д. Лучшим методом является тот при котором заготовки получаются более дешевыми включая стоимость последующей механической обработки и имеют требуемое качество. Важнейшим фактором при выборе метода изготовления заготовок является экономия металла. Значительное сокращение расхода металла достигается при использовании технологических процессов малоотходного производства заготовок размеры которых максимально приближаются к размерам деталей. Экономия металла достигается благодаря сокращению припусков под механическую обработку и повышению точности размеров заготовки. Уменьшается трудоемкость механической обработки благодаря более высоким режимам резания исключению черновых операций например точения зубофрезерования и других а также замене их получистовыми и чистовыми операциями.
Особенно высокие требования предъявляют к качеству заготовок которые предназначены для обработки в автоматизированном производстве (автоматы автоматические линии гибкие производственные системы) с применением ЧПУ. К этим заготовкам обычно предъявляют более жесткие требования в отношении припусков точности размеров твердости структуры металла массы и т. д 5 .
Литье является традиционным методом изготовления зубчатых колес без снятия стружки. Точность таких колес в большинстве случаев была недостаточной. Чтобы максимально приблизить форму и размеры заготовки к форме и размерам готовой детали разработаны более совершенные и производительные методы литья заготовок.
Литье в кокиль применяют для изготовления заготовок прямозубых цилиндрических колес зубчатых секторов конических колес с прямыми зубьями и др. Отливки получают путем разливания жидкого металла в кокиль изготовленные из стали или графита. В качестве литейного материала для изготовления зубчатых колес используют преимущественно чугун с шаровидным или пластинчатым графитом а также медь и медные сплавы. Точность заготовок с зубьями зависит от точности кокиля размера и формы детали качества литейного материала. Зубчатые колеса полученные литьем в кокиль без дополнительной обработки зубьев применяют в механизмах и приводах работающих при низких окружных скоростях и с повышенным боковым зазором между зубьями 5 .
Литье под давлением применяют для изготовления зубчатых колес из цветных металлов. В этом случае жидкий металл под высоким давлением и при высокой скорости заливается в закаленные стальные формы. Этим методом можно изготовлять зубчатые колеса с внешним и внутренним зацеплением. Из цинковых сплавов отливают зубчатые колеса с модулем 03 мм и выше из сплавов легких металлов—с модулем 05мм и выше из медных сплавов—с модулем 15 и выше. Наиболее высокая точность (9—10-я степень) достигается при литье под давлением мелких деталей из цинковых сплавов. Для точных зубчатых колес отлитых под давлением из цинкового сплава в большинстве случаев не требуется дополнительная обработка зубьев а для деталей из легких металлов и медных сплавов почти всегда необходима дополнительная обработка зубьев для чего на боковых поверхностях зубьев оставляют припуск 5 .
Литье по выплавляемым моделям применяют для изготовления заготовок и зубчатых колес сложной формы из стали и цветных металлов. Литье выполняют по высокоточным керамическим моделям которые точно соответствуют контуру обрабатываемой заготовки. Этот метод обеспечивает высокую точность: большинство поверхностей не требуют механической обработки а часть поверхностей подвергаются только чистовой или финишной обработке 5 .
Горячая высадка на многопозиционных автоматах применяется для изготовления заготовок дисков подшипниковых колец и др. Технологический процесс высадки полностью автоматизирован. В качестве исходного материала применяют горячекатаный пруток.
Формообразование производится в закрытых штампах поэтому заготовки не имеют заусенцев и штамповочных уклонов. Заготовки имеют чистую поверхность хорошие механические свойства высокую точность и небольшие припуски на механическую обработку 5 .
Холодная объемная штамповка
Холодная объемная штамповка применяется в машиностроении для изготовления крепежных а также более сложных и крупных деталей. Основные преимущества метода: высокая производительность высокий коэффициент использования металла (близок к единице) малая трудоемкость механической обработки. Этим методом получают заготовки зубчатых колес а также конических и цилиндрических колес с прямыми зубьями. Коническое колесо дифференциала автомобиля диаметром 80 мм штампуют с зубьями и отверстием производительность до 2000 штч. После отжига окончательно обрабатывают зубья (припуск на сторону зуба 02 мм) отверстие после термообработки шлифуют или хонингуют. Коэффициент использования около 097 снижен объем механической обработки 5 .
Точная вырубка используется для окончательного изготовления плоских деталей типа шайб рычагов зубчатых колес и т. д. Этот высокопроизводительный метод позволяет за один рабочий цикл изготовить несколько деталей сложной геометрической формы высокого качества без дополнительной механической обработки. При этом достигается значительная экономия металла снижается трудоемкость 5 .
2. Основные методы формообразования зубьев цилиндрических зубчатых колес
Зубофрезерование осуществляется на зубофрезерных вертикальных и горизонтальных станках-полуавтоматах. На зубофрезерных станках производят нарезание цилиндрических зубчатых колес по методу обкатки или копирования.
Нарезание зубьев по методу копирования осуществляют модульной дисковой или модульной концевой фрезой. Нарезание по существу представляет собой разновидность фасонного фрезерования. Режущие кромки зубьев дисковой или концевой фрезы изготовляют по форме впадины между зубьями колеса и при фрезровании они копируют форму впадины создавая таким образом две половины профилей двух соседних зубьев. После нарезания одной впадины заготовка поворачивается на один зуб с помощью делительного механизма и фреза снова проходит по новой впадине между зубьями и т.д.
Нарезание зубьев методом обкатки производится с помощью червячных фрез. Фрезу на станке устанавливают таким образом чтобы ее ось была повернута под углом b подъема винтовой линии витков фрезы. Метод является высокопроизводительным 3 .
Зубодолбление колес с внешними зубьями применяют главным образом для обработки закрытых венцов. Режущим инструментом является долбяк представляющий собой зубчатое колесо с эвольвентным профилем зубьев. В процессе нарезания долбяк и нарезаемое колесо находятся в относительном движении зацепления.
Кроме отмеченных обстоятельств Зубодолбление является единственным методом для нарезания колес с внутренним зацеплением (при средних и малых диаметрах) а также при обработке зубчатых венцов в блочных шестернях 354 .
Этот метод основан на зацеплении колеса и рейки воспроизводимом инструментом — гребенкой. Обработка колес осуществляется на станках двух типов: с вертикальной и горизонтальной осью заготовки. Станки последнего типа применяют также для обработки колес с неразрывным шевронным зубом.
У зубострогания производительность меньше чем у зубофрезерования червячной фрезой и зубодолбления 354 .
Метод основан на воспроизводящем зацеплении пары винтовых колес на скрещенных осях. В качестве многорезцового инструмента применяют цилиндрическое режущее колесо по форме напоминающее долбяк.
Производительность зуботочения в 2—4 раза выше производительности зубофрезерования однозаходной фрезой 35 .
Накатывание зубчатых колес
Накатывание зубчатых поверхностей имеет большие преимущества перед способами обработки резанием: повышает производительность в 5-30 раз; увеличивает износостойкость и прочность зубьев; значительно уменьшает отходы металла и др.
Различают горячее и холодное накатывание. Горячее накатывание применяют для профилей с модулем больше 2 мм; холодное накатывание рекомендуется для мелкомодульных колес с модулем до 15-2 мм 345 .
Шевингование—чистовая обработка зубьев незакаленных цилиндрических зубчатых колес осуществляемая инструментом — шевером.
Шевер имеет форму зубчатого колеса или зубчатой рейки. На поверхности зубьев шевера имеются канавки от головки до ножки.
Шевингование колес заключается в срезании весьма тонких волосовидных стружек толщиной 005—001 мм острыми кромками канавок шевера во время движения обкатки обрабатываемого колеса и инструмента и возникающего при этом относительного скольжения профилей зацепляющихся зубьев.
Обычно в процессе шевингования точность зубчатых колес повышается на одну степень реже — на две.
В настоящее время есть несколько методов шевингования: параллельное диагональное тангенциальное и врезное 345 .
Шлифование зубьев зубчатых колес.
Шлифование зубьев зубчатых колес — наиболее надежный метод отделочной обработки обеспечивающий высокую точность как правило закаленных зубчатых колес. Шлифование зубьев производят на различных зубошлифовальных станках как методом копирования так и методом обкатки.
На станках работающих по методу копирования шлифуют зубчатые колеса профилированными кругами. Ось заготовки в этих станках расположена горизонтально. Они пред назначены главным образом для шлифования прямозубых колес.
Метод обкатки осуществляется на зубошлифовальных станках которые точны и универсальны в наладке но производительность которых сравнительно невелика и зависит от принципа работы и типа применяемых шлифовальных кругов.
Применяют шлифование цилиндрических колес с внутренними прямыми и косыми зубьями также методами копирования и обкатки. Принципы работы станков для внутреннего шлифования 'аналогичны таковым для шлифования наружных зубьев 345.
Хонингование зубчатых колес
Хонингование применяют для чистовой отделки зубьев как правило закаленных цилиндрических колес внешнего и внутреннего зацепления. Процесс осуществляется на зубохонинговальных станках с помощью зубчатого абразивного инструмента — хона.
Зубчатые хоны представляют собой прямозубые или косозубые колеса обычно состоящие из стальной ступицы и абразивного венца того же модуля что и обрабатываемое колесо. Хонингование позволяет уменьшить параметры шероховатости и тем самым повысить долговечность зубчатой передачи 345 .
Производственные расчеты и разработка планировки.
Вал - Шестерня (Осн)
Годовой объем выпуска N = 7000 шт.
Размер партии для одновременного запуска n = 500
Наибольший габаритный размер детали –120 мм.
Масса детали –45 кг.
Масса заготовки – 52 кг.
Материал – 20Х ГОСТ 19281-73
Маршрутный технологический процесс изготовления
Нормы времени на операции
Токарно-винторезный 16К20Ф3
Горизонтально фрезерный 6Р10Ф3
Круглошлифовальная с ЧПУ
Годовой объем выпуска N = 4800 шт.
Размер партии для одновременного запуска n = 600
Наибольший габаритный размер детали –335 мм.
Масса детали –745 кг.
Масса заготовки – 917 кг.
Годовой объем выпуска N = 6400 шт.
Размер партии для одновременного запуска n = 100 .
Наибольший габаритный размер детали –330 мм.
Масса детали – 140 кг.
Масса заготовки – 263 кг.
Материал – Сталь 15ХГН2ТА ГОСТ 4543-71
Размер партии для одновременного запуска n = 550
Наибольший габаритный размер детали – 295 мм.
Масса детали –62 кг.
Масса заготовки – 874 кг.
Материал - Сталь 40Х ГОСТ 4543-71
Станкоемкость (Тшк-к) мин.
2. Форма организации выполнения технологических процессов.
Все технологические процессы обрабатываемых на участке деталей представлены в приложении в комплекте технологической документации.
Участок является участком подетально-групповой специализации. За каждым рабочим местом закреплено несколько технологических операций. Операция содержит несколько технологических переходов. Перемещается деталь в таре от склада к рабочему месту и между станками. Производство непоточное.
3. Производственная структура участка
Участок предназначен для изготовления деталей – конических зубчатых колес. В состав участка входит оборудование для металлообработки а именно токарные сверлильные шлифовальные станки; зубообрабатывающее оборудование контрольно-обкатные станки места контроля системы обеспечения функционирования. Операции заготовительные и термообработки производятся вне участка во вспомогательных производствах завода
4.1. Расчет количества основного оборудования.
Расчет количества основного технологического оборудования производится на основе разработанных технологических процессов изготовления изделий. Для этого определяется время работы станков (станкоемкость) на различных операциях затем с учетом объема выпуска изделий каждого наименования рассчитывается количество станков.
Расчетное количество оборудования:
где Fо- эффективный годовой фонд времени при двухсменном режиме работы;
Fо= 3915 – для станков с ручным управлением и полуавтоматов
Fо= 3835 – для станков с ЧПУ
Полученное значение округляем до ближайшего большего целого Ср
Коэффициент загрузки оборудования
при Кз” меньше нормативного Ки принимаем равным 1 при Кз больше нормативного принимаем Ки согласно данных 6 и уточняем количество технологического оборудования
Полученное значение округляют до ближайшего большего целого Сп
Уточняем коэффициент загрузки оборудования
Результаты расчета приведены в таблице 4.7.
В связи с низкой загрузкой станков дозагружаем деталями с других участков.
4. Проектирование подсистем.
4.1. Расчет характеристик склада.
Определение количества наименований деталеустановок.
где F - месячный фонд времени работы станка ч;
F = Fоб * hз 12 (4.6)
Fоб=3900ч.- эффективный годовой фонд времени при двухсменном режиме работы;
hз=085-нормативный коэффициент загрузки оборудования.
F=3900*08512=27625 ч.
S = 13- число станков на участке;
Тср - средняя станкоемкость изготовления одной деталеустановки мин.
m - число операций технологического процесса изготовления детали-представителя;
Тср = 35485 = 709 мин.
N =500 шт.- месячный объем выпуска деталей-представителей
Округляем до ближайшего большего целого Кнаим = 61 шт.
Определение оптимальной емкости склада.
Округляем до ближайшего большего целого Eс =68 шт.
Изделия транспортируются в таре габаритными размерами L*B*H=800*600*580(400+180)
размеры ячейки склада 950*670*670
количество ячеек по высоте Qh=5 шт.
Высота склада H=5*670+450=3800 мм.
Станки располагаются в две линии склад располагается между ними в 1 ряд. Его обслуживает 1 кран – штабелер.
тогда количество ячеек в 1-м ряду Ql = 34 шт.
длина склада L=32000 мм.
ширина с учетом пространства для работы крана - штабелера B=2610мм.
площадь склада S=8352 м2
производственная площадь участка S = 580 м2
4.2. Расчет системы стружкоуборки.
Для выбора способа удаления и переработки стружки определяют её количество образующееся на 1м2 цеха в год.
Данные для расчёта представлены в таблице 4.3.
Расчет количества стружки
Годовой объем выпуска шт.
Площадь участка 580 м2. На 1м2 приходится 026 т в год. По рекомендациям в 12 необходимо предусмотреть специальные емкости и доставлять к месту сбора или переработки напольным транспортом.
5. Строительные решения.
По длине и ширине спроектированного участка примем ширину пролёта 24 м шаг колонн 12 м и высоту здания 72 м ширину межцехового проезда 26м ширину магистрального проезда 46 м. Планировка участка и график загрузки оборудования представлены на листе 11.
6. Технико-экономические показатели участка.
Количество технологического оборудования- 13 единиц
Занимаемая площадь 580 м2
Средний коэффициент загрузки и использования оборудования 071
Охрана труда и экология
Современное состояние техносферы оказывает всё возрастающее влияние на людей. В этих условиях одной из самых злободневных проблем становится проблема обеспечения жизни и деятельности человека в среде его обитания. Проблема обеспечения безопасности человека охватывает все сферы его жизнедеятельности и является очень сложной. Она включает широкий комплекс организационно-технических медико-биологических социально-экономических и экологических вопросов решение которых возможно лишь с позиции научно обоснованного подхода к данной проблеме. Обеспечение безопасности труда реализуется как при проектировании производственных процессов так и в процессе их реализации. Безопасность труда обеспечивается соблюдением стандартов по безопасности труда правил техники безопасности санитарных норм и правил инструкций по охране труда. Особое внимание обращается на соблюдение этих требований при создании новых видов оборудования разработке и реализации производственных процессов. В государственных стандартах сформулированы требования безопасности к производственным процессам оборудованию промышленной продукции средствам защиты работающих установлены нормы и требования на параметры характеризующие шум вибрацию ультразвук запылённость и загазованность воздуха рабочей зоны электро и взрывобезопасность пожарную безопасность и т.п. Современное машиностроительное производство представляет собой комплекс сложных технологических систем машин и оборудования с высоким уровнем механизации и автоматизации производственных процессов. Факторы безопасности и экологичности обеспечение комфортных условий труда сведение к минимуму риска для обслуживающего персонала выдвигаются в число важнейших критериев характеризующих технический уровень и качество машин оборудования и производственных процессов определяющих их конкурентоспособность на мировом рынке.
Создание безопасных и экологичных производственных процессов машин и оборудования составляет материальную основу обеспечения жизнедеятельности человека и является одной из основных целей системы управления безопасностью труда и экологической безопасностью предприятия.
1 Безопасность труда на проектируемом участке.
Оборудование на проектируемом участке регулярно проходит технический осмотр в ходе которого определяется его безопасность и соответствие требованиям норм экологической безопасности. Оборудование применяемое на участке снабжено специальными защитными и оградительными устройствами уменьшающих риск травмирования рабочего. Выполняемые на участке ТП при соблюдении правил техники безопасности являются достаточно безопасными. Опасным для здоровья человека являются шум пыль вибрации. Все они не должны превышать предельных норм. И для этого на участке созданы специальные предохранительные устройства. Средствами защиты рабочих при выполнении ТП являются спецодежда для защиты от попадания СОЖ и специальные очки для зажиты глаз от попаданий мелких частей стружки.
Одним из наиболее опасных процессов на проектируемом участке является механическая обработка материалов резанием. В связи с этим рассмотрим более подробно вопрос безопасности труда при механической обработке материалов резанием.
2 Методы и средства защиты от механических опасностей
К механическим опасностям следует относить опасности которые могут возникнуть у любого объекта способного причинить травму в результате неспровоцированного контакта объекта или его части с человеком. С опасностями такого рода связано и понятие об опасной зоне машин оборудования.
В ГОСТ 12.0.003-71* приводится классификация ОВПФ которой предусмотрено разделение их по природе действия на организм человека на четыре группы: физические химические биологические и психофизиологические. Эта классификация однако не выделяет факторы непосредственно связанные с механическими опасностями.
К опасностям механически воздействующим на организм человека можно отнести: движущиеся машины и механизмы; подвижные части оборудования; передвигающиеся изделия заготовки материалы; острые кромки заусенцы заготовок инструмента приспособлений оборудования; разрушающиеся конструкции; расположение рабочего места на большой высоте; повышенная запыленность воздуха рабочей зоны; макроорганизмы; физические перегрузки (статические и динамические).
Защита от механических опасностей базируется на общих принципах методах и средствах обеспечении безопасности рассмотренных ранее. В зависимости от имеющихся возможностей защиты человека в условиях его взаимодействия с потенциально опасными объектами применяют два основных метода:
обеспечение недоступности к опасно действующим элементам машин и оборудования;
применение приспособлений непосредственно защищающих человека от опасных производственных факторов.
Первый метод состоит в пространственном или временном разделении гомосферы и ноксосферы. Он реализуется за счет конструктивных особенностей машин и оборудования снижающих опасность травмирования а также благодаря специальным устройствам и соответствующей организации технологических процессов (механизация у. автоматизация дистанционное управление оборудованием использование манипуляторов и роботов различных поколений). Ко второму методу относятся различные технические устройства безопасности а также средства индивидуальной защиты повышающие защитные свойства человека (очки защитные каски спецодежда спецобувь и др.).
В решении задач защиты от механических опасностей особую роль играет правильное определение границ опасной зоны. Под опасной зоной понимается пространство в которой возможно воздействие на работавшего опасного и (или) вредного производственного фактора (ГОСТ 12.0.002-80). Опасная зона может быть: резко ограниченней в пространстве например зона между набегающей ветвью приводного ремня и шкивом зона между двумя валками зона между сходящимися венцами зубчатых колес и др.; переменной в пространстве и непостоянной по размерам как например зона распространения стружки при скоростном точении; переменной в пространстве и постоянной по размерам как например пространство под грузом перемещаемым грузоподъемным механизмом.
При проектировании и эксплуатации производственного оборудования необходимо предусматривать устройства либо исключающие возможность контакта человека с опасной зоной либо снижающие опасность контакта.
Средства коллективной зашиты работающих от воздействия механических факторов подразделяют на следующие устройства: оградительные предохранительные тормозные автоматического контроля и сигнализации дистанционного управления и знаки безопасности (ГОСТ 12.4.125-63).
К оградительным устройствам относятся средства защиты препятствующие попаданию человека в опасную зону. Благодаря простоте надежности и дешевизне эти устройства получили широкое распространение.
По способу установки оградительные устройства подразделяются на стационарные и подвижные (съемные переносные). Стационарное ограждение может быть полным когда локализуется опасная зона вместе с машиной или частичным когда изолируется только опасная зона. Подвижные ограждения представляют собой устройства сблокированные с рабочими органами машины; они закрывают доступ в рабочую зону только при наступлении опасности (рабочем ходе).
Конструктивно оградительные устройства выполняются в виде кожухов дверок щитов козырьков планок барьеров и экранов. Ограждения могут быть сплошными несплошными (перфорированными сетчатыми решетчатыми) и комбинированными.
Предохранительные устройства по характеру действия подразделяют на блокировочные и ограничительные
Блокировочные устройства срабатывают при ошибочных действиях оператора. Они призваны исключить возможность попадания человека в опасную зону или устранить опасный фактор в случае попадания человека в опасную зону.
По принципу действия блокировочные устройства могут быть
механическими электронными электромагнитными пневматическими
гидравлическими оптическими магнитными радиационными и комбинированными.
Ограничительные устройства срабатывают при нарушении параметров технологического процесса или режима работы производственного оборудования В качестве предохранительных устройств в конструкцию машин вводят "слабые звенья" которые при перегрузках разрушаются (не срабатывают) что приводит к остановке машины. К ним относятся срезные штифты к шпонки фрикционное муфты плавкие предохранители разрывные мембраны в установках с повьшением давлением и т.п.
: Тормозные устройства предназначены для замедления или остановки производственного оборудования при возникновении опасной ситуации.
Устройства автоматического контроля и сигнализации даёт информацию о работе технологического оборудования и об изменениях в течении процесса предупреждают об опасностях и сообщают о месте их накопления. Соответственно и системы сигнализации подразделяются на информационные предупреждающие аварийные и ответные. По характеру сигнала они могут быть звуковыми световыми знаковыми и комбинированными.
Дистанционное управление применяется там где по условиям технологии находиться в зоне работы машины и оборудования опасно. Наблюдения проводят либо визуально либо с помощью телеметрии и телевидения. Параметры режимов работы определяют при помощи датчиков контроля сигнал от которых поступают на пульт управления. Значение дистанционного управления особенно возросло в условиях автоматизации электронизации и роботизации производства.
Важную роль в повышении безопасности труда играют знаки безопасности. ГОСТом 2.4.026-76 установлены четыре группы знаков безопасности: запрещающие предупреждающие предписывающие и указательные. Отличительными признаками в знаках безопасности являются цвет и форма (конфигурация) знака.
Специальные средства применяются для защити от воздействия механических факторов связанных с эксплуатацией объектов повышенной опасности; подъемно-транспортного оборудования и герметичных систем находящихся под давлением.
2. Обеспечение экологической безопасности проекта
На окружающую среду и в целом на биосферу крайне отрицательно влияют промышленные загрязнения которые при определенных условиях могут трансформироваться в различные соединения и вызывать нежелательные воздействия на биосферу.
Жесткие выбросы в атмосферу представляют собой аэрозоли образованные мельчайшими капельками распыленных жидкостей (кислот масел СОЖ и т.п.). На участке должны быть предусмотрены средства очистки воздуха.
Производственные сточные воды – воды используемые предприятием и подлежащие обязательной очистке от различных вредных примесей. Т.е. техническую воду должны охлаждать очищать от механических примесей масел разбавлять и затем возвращать в производство.
Промышленные твердые отходы должны собираться и отправляться для переработки.
Тепловое загрязнение биосферы большинством предприятий машиностроения незначительно.
Шум вибрация ультразвук инфразвук должны быть в пределах нормы.
3 Методы борьбы с шумом
Шум на производстве наносит большой ущерб вредно действуя на организм человека и снижая производительность труда. Утомление рабочих и операторов из-за сильного шума увеличивает число ошибок при работе способствует возникновению травм. Нередко и в быту человек подвергается воздействию шума недопустимо высоких уровней. Поэтому борьба с шумом является важной народнохозяйственной задачей.
Часто возникает необходимость защиты не только от шума но и от инфра- и ультразвука.
Для снижения шума можно применить следующие методы: уменьшение шума в источнике; изменение направленности излучения; рациональная планировка предприятий и цехов; акустическая обработка помещений; уменьшение шума на пути его распространения.
Уменьшение шума в источнике. Борьба с шумом посредством уменьшения его в источнике (уменьшение Lp)является наиболее рациональной.
Шум возникает вследствие упругих колебаний как машины в целом так и отдельных ее деталей. Причины возникновения этих колебаний — механические аэродинамические гидродинамические и электрические явления определяемые конструкцией и характером работы машины а также неточностями допущенными при ее изготовлении и наконец условиями эксплуатации. В связи с этим различают шумы механического аэродинамического гидродинамического и электромагнитного происхождения.
Механические шумы. Факторы вызывающие шумы механического происхождения следующие: инерционные возмущающие силы возникающие из-за движения деталей механизма с переменными ускорениями; соударение деталей в сочленениях вследствие неизбежных зазоров; трение в сочленениях деталей механизмов; ударные процессы (ковка штамповка) и т. д.
Основными источниками шума происхождение которого не связано непосредственно с технологическими операциями выполняемыми машиной являются прежде всего подшипники качения и зубчатые передачи а также неуравновешенные вращающиеся части машины.
Частоты колебаний а следовательно и шума создаваемого неуравновешенностью кратны n60 (n - частота вращения обмин).
Спектр шарикоподшипников занимает широкую полосу частот. Звуковая мощность P зависит от скорости вращения машины: Рn73. Увеличение частоты вращения подшипников качения с n1 до n2 (обмин) приводит к возрастанию шума на величину (дБ)
Зубчатые передачи—источники шума в широком диапазоне частот. Основными причинами возникновения шума являются деформации сопрягаемых зубьев под действием передаваемой нагрузки и динамические процессы в зацеплении обусловленные неточностями изготовления колес. Шум имеет дискретный характер.
Шум зубчатых передач возрастает с увеличением частоты вращения колес и нагрузки.
Уменьшение механического шума может быть достигнуто путем совершенствования технологических процессов и оборудования. Например внедрение автоматической сварки вместо ручной устраняет образование брызг на металле что позволяет исключить шумную операцию по зачистке сварного шва. Применение фрезерных тракторов для обработки кромок металла под сварку вместо пневмозубил делает этот процесс значительно менее шумным.
Нередко повышенный уровень шума является следствием неисправности или износа механизмов в этом случае своевременный ремонт позволяет снизить шум.
Необходимо отметить что проведение многих мероприятий по борьбе с вибрациями дает одновременно и снижение шума. Для уменьшения механического шума необходимо:
заменять ударные процессы и механизмы безударными например применять оборудование с гидроприводом вместо оборудования с кривошипными и эксцентриковыми приводами;
штамповку—прессованием клепку—сваркой обрубку—резкой и т. д.;
заменять возвратно-поступательное движение деталей равномерным вращательным движением;
применять вместо прямозубых шестерен косозубые и шевронные а также повышать класс точности обработки и уменьшать шероховатость поверхности шестерен; так ликвидация погрешностей в зацеплении шестерен дает снижение шума на 5—10 дБ; замена прямозубых шестерен шевронными — 5 дБ;
по возможности заменять зубчатые и цепные передачи клиноременными и зубчато-ременными например зубчатую передачу на клиноременную что снижает шум на 10—14 дБ;
заменять когда это возможно подшипники качения на подшипники скольжения; это снижает шум на 10—15 дБ;
по возможности заменять металлические детали деталями из пластмасс и других незвучных материалов либо перемежать со ударяемые и трущиеся металлические детали с деталями из незвучных материалов например применять текстолитовые или капроновые шестерни в паре со стальными; так замена одной из стальных шестерен (в паре) на капроновую снижает шум на10—12 дБ;
использовать пластмассы при изготовлении деталей корпусов что дает хорошие результаты; например замена стальных крышек редуктора пластмассовыми приводит к снижению шума на 2—6 дБ на средних частотах и на 7—15 дБ на высоких особенно неприятных для слухового восприятия;
при выборе металла для изготовления деталей необходимо учитывать что внутреннее трение в различных металлах неодинаково а следовательно различна звучность; например обычная углеродистая сталь легированная сталь являются более звучными чем чугун; большим трением обладают после закалки сплавы из марганца с 15—20% меди и магниевые сплавы; детали из них при ударах звучат глухо и ослаблено; хромирование стальных деталей например турбинных лопаток уменьшает их звучность; при увеличении температуры металлов на 100—150° С они становятся менее звучными;
более широко применять принудительное смазывание трущихся поверхностей в сочленениях;
применять балансировку вращающихся элементов машин;
использовать прокладочные материалы и упругие вставки в соединениях чтобы исключить или уменьшить передачи колебаний от одной детали или части агрегата к другой; так при правке металлических листов наковальню нужно устанавливать на прокладку из демпфирующего материала.
Установка мягких прокладок в местах падения деталей с конвейера или сбрасывания со станков прокатных станов может существенно ослабить шум.
У прутковых автоматов и револьверных станков источником шума являются трубы в которых вращается прутковый материал. Для снижения этого шума применяют различные конструкции малошумных труб; двух стенные трубы между которыми проложена резина трубы с наружной поверхностью обернутой резиной и т. п.
Для уменьшения шума возникающего при работе галтовочных барабанов дробилок шаровых мельниц и других устройств наружные стенки барабана облицовывают листовой резиной асбестовым картоном или другими подобными демпфирующими материалами; устанавливают резиновые прокладки между корпусом и броне футеровкой барабана и звукоизолирующие оболочки на расстоянии от корпуса барабана.
Аэродинамические шумы. Аэродинамические процессы играют большую роль в современной технике. Как правило всякое течение газа или жидкости сопровождается шумом поэтому с повышенным аэродинамическим шумом приходится встречаться часто. Эти шумы являются главной составляющей шума вентиляторов воздуходувок компрессоров газовых турбин выпусков пара и воздуха в атмосферу двигателей внутреннего сгорания и т. п.
Ко всем источникам аэродинамического шума относятся: вихревые процессы в потоке рабочей среды; колебания среды вызываемые вращением лопастных колес; пульсация давления рабочей среды; колебания среды вызываемые неоднородностью потока поступающего на лопатки колес.
В большинстве случаев меры по ослаблению аэродинамических шумов в источнике оказываются недостаточными поэтому дополнительное а часто и основное снижение шума достигается путем звукоизоляции источника и установки глушителей.
Гидродинамические шумы. Эти шумы возникают вследствие стационарных и нестационарных процессов в жидкостях (кавитации турбулентности потока гидравлических ударов). В насосах источником шума является кавитация жидкости возникающая у поверхности лопастей при высоких окружных скоростях и недостаточном давлении на всасывании.
Меры борьбы с кавитационным шумом—это улучшение гидродинамических характеристик насосов и выбор оптимальных режимов их работы. Для борьбы с шумом возникающим при гидравлических ударах необходимо правильно проектировать и эксплуатировать гидросистемы в частности закрытие трубопроводов должно происходить постепенно а не резко.
Рациональная планировка предприятий и цехов. Шум на рабочем месте может быть уменьшен увеличением площади S что достигается увеличением расстояния от источника шума до расчетной точки.
При планировке предприятия наиболее шумные цехи должны быть сконцентрированы в одном-двух местах. Расстояние между шумными цехами и тихими помещениями (заводоуправление конструкторское бюро и т. п.) должно обеспечивать необходимое снижение шума. Если предприятие расположено в черте города то шумные цехи должны находиться в глубине предприятия по возможности дальше от жилых домов.
Внутри здания тихие помещения необходимо располагать вдали от шумных так чтобы их разделяло несколько других помещений или ограждение с хорошей звукоизоляцией.
Пожары на машиностроительных предприятиях представляют большую опасность для работающих и могут причинять огромный материальный ущерб.
Пожарная безопасность может быть обеспечена мерами пожарной профилактики и активной пожарной защиты. Понятие пожарной профилактики включает комплекс мероприятий необходимых для предупреждения возникновения пожара или уменьшения его последствий. Под активной пожарной защитой понимаются меры обеспечивающие успешную борьбу с возникающими пожарами или взрывоопасной ситуацией.
Предприятия машиностроительной промышленности часто отличаются повышенной пожарной опасностью так как их характеризует сложность производственных установок значительное количество легковоспламеняющихся и горючих жидкостей сжиженных горючих газов твердых сгораемых материалов большое количество емкостей и аппаратов в которых находятся пожароопасные продукты под давлением; разветвленная сеть трубопроводов с запорно-пусковой и регулирующей арматурой; большая оснащенность электроустановками.
Данные показывают что основной причиной пожаров на машиностроительных предприятиях является нарушение технологического процесса. В известной мере это связано с большим разнообразием и сложностью технологических процессов. Они как правило помимо операций механической обработки материалов и изделий включают процессы очистки и обезжиривания сушки и окраски связанные с использованием веществ обладающих высокой пожарной опасностью. Сложность противопожарной защиты современных машиностроительных предприятий усугубляется их гигантскими размерами большой плотностью застройки увеличением вместимости товарно-материальных складов применением в строительстве облегченных конструкций из металла и полимерных материалов обладающих низкой огнестойкостью.
Основы противопожарной защиты предприятий определены стандартами: ГОСТ 12.1.004-76 Пожарная безопасность и ГОСТ 12.1.010-76 Взрывобезопасность. Общие требования. Этими стандартами возможная частота пожаров и взрывов допускается такой чтобы вероятность их возникновения в течение года не превышала 10-6 или чтобы вероятность воздействия опасных факторов на людей в течение года не превышала 10-6 на человека.
ЭКОНОМИЧЕСКАЯ ЭФФЕКТИВНОСТЬ ПРОЕКТА
Технико-экономическая оценка проекта.
Расчет накопительных вложений:
где Соб - стоимость приобретенного оборудования Соб=2449120 тнг;
См – затраты на монтаж и перевозку оборудования составляет 15% от первоначальной цены;
Сдм - затраты на демонтаж оборудования составляет 5%;
Подставив значения в формулу получим:
К=2449120+367368+122468=2938936 тнг
Расчет полной себестоимости продукции .
При определении себестоимости продукции учитываются все затраты при изготовлении.
Себестоимость рассчитываем по формуле:
где Смат – затраты на приобретение материалов тнг;
Сзп - основная заработная плата тнг;
Сдп – дополнительная плата тнг;
Ссоц – отчисление на социальное страхование составляет 26% от общей заработной платы тнг;
Ссод – расходы на содержание и ремонт помещений 1м3=48 тнг;
Стр – расходы на текущий ремонт основных оборотных средств 65% балансовой стоимости;
Сам – затраты на амортизационные отчисления 64% от балансовой стоимости;
Синстр – затраты на приобретение и изготовление инструмента и оснастки 5% от товарной стоимости тнг;
Собщ.р – общезаводские расходы;
Свн.р – внепроизводственные расходы составляют 2% от заводской себестоимости.
Таблицица 6.1 Основная заработная плата на участке механической обработки
Фонд заработной платы
Токарь-полуавтоматчик
Дополнительная заработная плата составляет 7-10% от Сзп.
Отчисления на социальное страхование составляет 26% (Сзп+Сдп)
Расходы на ремонт и содержание помещения составляют 1м3
Расходы на текущий ремонт основных оборотных средств составляют 65% от балансовой стоимости:
Затраты на амортизационные отчисления 64% от балансовой стоимости:
Затраты на приобретение и изготовление инструмента и оснастки составляет 5% от товарной стоимости продукции:
Затраты на электроэнергию определим по формуле:
где N – мощность установленных на станках электродвигателей кВт
Кн – средний коэффициент использования мощности (0809); принимаем 09;
Ц – тариф за один киловат установленой мощности;
t – максимальное машинное время на одну деталь;
- средний КПД электродвигателей 092094 принимаем 092.
Подставив данные в формулу получим:
На программу составит 1391478 тн.
Общезаводские расходы определим по формуле:
где Rоп - процент общезаводских расходов 705%
Внепроизводственные расходы составляют 2% от заводской себестоимости:
Полная себестоимость:
Себестоимость одной шестрни составляет:
Себестоимость при существующем технологическом процессе составляет 5184 тнг.
Расчет технико-экономических показателей.
Выпуск товарной продукции.
где Фп и Фб – балансовая стоимость основных фондов базовая и проектируемая.
Съем товарной продукции с 1м2 производственной площади:
где Fпр – производственные площади участка Fпр=1440 м2;
где Р – среднесписочное количество рабочих;
Ф – действительный фонд времени;
Средне годовая заработная плата одного рабочего по проекту:
Расчет годовой экономии от мероприятий по совершенствованию технологического процесса:
гдеСб и Сп – полная себестоимость базового и проектируемого участков по обработке шестерни;
N – годовая программа участка.
Подставив данные получим:
Окупаемость капитальных вложений:
Основные технико-экономические показатели нового технологического процесса в сравнении со старым сводим в таблицу.
Основные технико-экономические показатели участия механической обработки шестерни
Товарная продукция тыс. тнг
Средняя численность рабочих чел
Основные фонды тыс. тнг
Производственные площади м2
Себестоимость шестерни тнг
Годовая экономия приспособления тнг
Срок окупаемости приспособления тнг
Годовая экономия проекта тнг
Срок окупаемости проекта лет
Таким образом разработанный в проекте новый технологический процесс является экономически выгодным и целесообразным для внедрения в производство.
В данном дипломном проекте на основе базового технологического процесса с применением полученных знаний по технологии машиностроения стандартизации автоматизации экономики безопасности жизнедеятельности и проектированию приспособлений; спроектирован технологический процесс обработки шестерни ориентированный на среднесерийное производство.
В ходе разработки дипломного проекта ряд технологических операций были обьединены или переведены на другое подобное оборудования с целью повысить коэффициент загрузки оборудования. В следствии чего часть технологического оборудования высвободилась снизилась трудоёмкость и себестоимость изготовления детали.
В дипломном проекте были проведен анализ действующих технологических процессов получения зубчатых венцов прямозубых колес. В этой работе рассмотрены различные технологические процессы: достигаемые степени точности и шероховатость рабочих поверхностей.
В конструкторском разделе были спроектированы станочные приспособления.
В специальном разделе была рассмотрена тема «Анализ методов формирования зубьев прямозубых колес».
В проекте также были рассмотрены вопросы охраны труда и экологической безопасности.
В экономической части проанализированы необходимые затраты на инвестиции в проект участка и рассчитана возможная прибыль которая по расчётам позволяет окупить проект участка за 174 года.
Методические указания по оформлению технологической документации при выполнении курсовых и дипломных проектов для студентов специальностей 12.01 07.01 21.03 12.02 15.02 15.06.-Курган:КМИ1992-36 с.
Технология машиностроения Методические указания к выполнению курсового проекта для студентов направления 552900.-Курган: КМИ 1995.-42 с.
Мосталыгин Г.П Толмачевский Н.Н. Технология машиностроения - М: Машиностроение 1990.-288 с
Технология производства деталей колесных и гусеничных машин Под ред Н М. Капустина ММашиностроение 1989 г 368 с
Справочник технолога-машиностроителя В 2-х т. Т2 Под ред. А.Г. Косиловой РК Мещерякова - М: Машиностроение 1986.-496 с.
Выбор способа изготовления заготовок. Методические указания .-Курган: КМИ 1995.-42 с.
Мосталыгин Г.П. Орлов В.Н. Проектирование технологических процессов обработки заготовок. –Свердловск: УПИ. 1991.-112 с.
Методические указания к выполнению лабораторных работ по определению припусков для студентов направления Мурзин ВА 552900.-Курган: КМИ 1985.-42 с.
Краткий справочник металлистаПод ред. Орлова П.Н. Скороходова Е.А. – М: Машиностроение1987.-960 с.
Производство зубчатых колес: Справочник С. Н. Калашников А.С.Калашников Г.И.Коган и др. Под общ. ред. Б.А.Тайца. - 3-е изд. перераб. и допол. – М.: Машиностроение 1990. – 464 с.:.
Определение экономической эффективности технологических процессов Методические указания для студентов специальностей 1201 1202 2103 07.01 15.02 15.06 Курган Кми 1994 г
Ансеров М.А. Приспособления для металлорежущих станков 3-е изд. Справочник - М: Машиностроение 1974.-652 с.
Станочные приспособления: Справочник. В 2-х т. Т2Под ред. Б.Н. Вардашкина В.В. Данилевского - М: Машиностроение 1984.-656 с.
Охрана труда в машиностроении Под общ.ред. Е.Я.Юдина С.В.Белова – 2-е изд. – М:Машиностроение 1983
Лист01 Приспособление Зубодолбежное.cdw

Технические требования:
Резьбы выполнять по 7H
Рабочее давление приспособления 2.1 МПа
Давление в пневмосистеме участка 1 МПа
Нерабочие поверхности красить эмаль
кремовая 270 НЦ 132 К ГОСТ 6631-74
Лист04 Планировка.cdw

Коэффициент загрузки
Условные обозначения.
- аптечка медицинская
Магистральный проезд
Внутрицеховой проезд
Лист 02 Шпонкофрезерное приспособление.cdw

Техническая характеристика:
Максимально допустимые размеры заготовок:
приспособления - 30 кг.
Максимальный ход центра задней бабки 60 мм.
Позиция номер 1 условно не показана
Позиция номер 3 условно не показана
Лист 03 Захват.cdw

Диаметр захватываемой заготовки 100 мм
Рекомендуемые чертежи
- 09.06.2021