Установка подъёмная шахтная с бицилиндроконическим барабаном БЦК-8/5x2




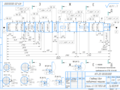
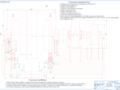
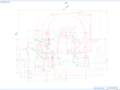
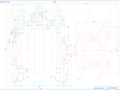
- Добавлен: 24.01.2023
- Размер: 2 MB
- Закачек: 2
Описание
Состав проекта
![]() |
![]() ![]() ![]() |
![]() ![]() ![]() |
![]() |
![]() ![]() ![]() ![]() |
![]() ![]() ![]() ![]() |
![]() |
![]() |
![]() |
![]() ![]() ![]() ![]() |
![]() ![]() ![]() ![]() |
![]() |
![]() ![]() ![]() ![]() |
![]() ![]() ![]() ![]() |
Дополнительная информация
Спецификация БЦК.docx
Механизм перестановки
Крышка под уплотнение
бицилиндроконический
БЦК ПЗ.docx
Разработка конструкции изделия . . ..17
1Описание конструкции изделия . . 17
3Определение часовой производительности скипового подъёма 20
4Расчёт и выбор подъёмного каната .23
5Выбор параметров одноканатной скиповой подъёмной установки .24
5.1.Выбор подъёмной машины для одноканатного подъём . .24
5.2.Определение отношения диаметра барабана ШПМ к диаметру каната . 24
5.3.Проверка подъёмной машины БЦК-85х2 по канату ёмкости органа навивки .24
5.4.Расчёт мощности приводных электродвигателей подъёмной машины БЦК-85х2 ..25
5.5.Расчёт пути пройденного сосудами на каждом участке тахограммы . .25
5.6.Расчёт проведённой массы подъёмной установки 26
5.7.Тяговый расчёт и определение мощности и типа двигателя..27
5.8.Расход электроэнергии и КПД подъёмной установки 32
6.Расчёт углов отклонения (девиации) струны каната машины
6.1.Расчёт угла отклонения (девиации) струны каната машины БЦК-85х2 .33
7.Анализ расчётов при выборе подъёмных машин ..35
8.Выбор расчёт тормозного устройства и коренных подшипников для ПМ БЦК-85х2 ..35
8.1.Выбор и расчёт тормозного устройства 35
8.2.Определение статических нагрузок на подъёмную машину..37
8.3.Выбор тормозных моментов 39
8.4. Расчёт параметров тормозных приводов .39
8.5.Выбор подшипников подъёмной установки 40
8.6.Технические решения по узлам загрузки и разгрузки скипов 42
Список использованной литературы ..53
Строительство и ввод в эксплуатацию в Республике Беларусь калийных рудников позволит удовлетворить растущие потребности внутреннего и внешнего рынка в калийных удобрениях. При стабильной тенденции роста спроса и цены на калийные удобрения ввод в эксплуатацию рудника современного технического уровня позволит обеспечить работу предприятия с высокими технико-экономическими показателями и рентабельностью.
Важнейшим производством горного предприятия влияющим на эффективность инвестиций и технико-экономические показатели его эксплуатации является шахтный подъем обеспечивающий выдачу с подземного горизонта на поверхность полезного ископаемого (калийной руды) спуск в рудник и подъем работников спуск оборудования и материалов аварийный подъем работников на поверхность техническое обслуживание шахтных стволов.
В настоящем курсовом проекте рассматривается выбор типа грузовой скиповой установки для шахтного ствола в соответствии с заданием на разработку.
Целью настоящего проекта является изучение учебной литературы и создание горно-шахтной подъемной установки с бицилинроконическим разрезным барабаном глубиной подъёма до 600 метров и грузоподъёмностью до 40 т. А также изучение опыта мировых производителей в области оборудования шахтного подъема включая шахтные подъёмные машины сосуды узлы загрузки скипов подъёмные канаты и др.
Информационный обзор
Обзор мирового опыта проектирования и эксплуатации скиповых подъемов на калийных рудниках
1 Общий обзор калийных рудников
Основными мировыми производителями калийных удобрений являются Канада (322%) Россия (187%) Беларусь (147%) Германия (114%). На долю этих стран приходится 77% мирового производства калийных удобрений.
В таблице 2.1 приведены данные по добыче руды на калийных рудниках в РФ и РБ в таблице 2.2 – в Канаде и Германии. Анализируя приведенные в таблицах 2.1 и 2.2 данные можно сделать следующие выводы:
На калийных рудниках Беларуси где глубина шахтных стволов колеблется от 500 до 8979 м предельная высота подъема для одноканатных машин (БЦК-85×27) составляет 850 м. При этом повсеместно применяются скипы грузоподъемностью 20-25 т и жесткая многорасстрельная армировка скиповых стволов с шагом 3-4 м.
На руднике 4-го РУ при глубине скиповых стволов 670 и 1000 метров используются многоканатные машины МК 5×4 и ЦШ 5×8 с грузоподъемностью скипов соответственно 22 и 42 т. В стволах применена жесткая многорасстрельная армировка с шагом 6 м.
На всех рудниках Беларуси диаметр шахтных стволов в свету принят равным 7 м.
На калийных рудниках Канады где глубина шахтных стволов достигает 1000-1144 м в большинстве случаев применяется один двухскиповой подъем с многоканатной подъемной машиной со скипами большой грузоподъемности ( 40-50 т). Производительность скипового подъема составляет 600-800 тчас а на руднике Эстергази при глубине скипового ствола 1144 м и одном двухскиповом подъеме c многоканатной подъемной машиной достигает 1229 тчас.
Диаметр шахтных стволов на калийных рудниках Канады принят в пределах 42-55 м.
Наименование показателя
наименование рудника
шахтный комбай-новый
Таблица 2.1. - Добыча калийной руды в РФ и РБ
Продолжение таблицы 2.1
шахтный комбайно-вый +
Таблица 2.2. - Добыча калийной руды в Канаде Германии
Продолжение таблицы 2.2
Циркуляция рассола через затопленные рудники
и выкачивание в бассейны на поверхности
(9 погрузочных насосов по 6800 лмин.)
Koepe winders 8 ropes
Koepe winders 1 rope each
Самый мощный по производительности среди Канадских рудников – Эстергази: годовая производительность 107 млн.т; два шахтных ствола – в каждом по одному двухскиповому подъему с часовой производительностью 792 и 1229 тчас; диаметр шахтных стволов в свету 55 м.
Глубина разработки калийных пластов на рудниках Германии изменяется от 600 до 1000 м годовая производительность рудников 48-106 млн.т.
На рудниках используются многоканатные и одноканатные подъемные машины.
На рудниках Унтербрейзбаш и Хаффорт с годовой производительностью соответственно 40 и 100 млн.т. при диаметре шахтных стволов в свету 60 и 55 м эксплуатируется по два двухскиповых подъема в каждом стволе с использованием одноканатных подъемных машин.
На рудниках калийных предприятий Цилиц и Винтерхал с годовой производительностью соответственно 106 и 80 млн.т руды при шахтных стволах диаметром в свету 75 применен двухскиповой подъем с одной многоканатной (8 канатов) подъемной машиной.
Наземного базирования
Высота приемной воронки м
ТУ24.8.792.73 ТУ24.8.958.75
Производительность млн.т
На руднике 3 РУ (таблица 2.5) на стволе № 4 производительность двух двухскиповых подъемов с одноканатными машинами БЦК-85×27 при глубине загрузки скипов 8204 м грузоподъемности скипов 240 т и скорости 14 мс составляет соответственно 850 тчас и 700 тчас расчетная годовая производительность ствола составляет 44 млн.т.
В последующие годы строительство зданий подъемных машин у шахтных стволов № 4 рудников 1РУ и 3РУ для двух двухскиповых подъемов (рисунок 2.2) выполнено с размещением ПМ в отдельно стоящих зданиях. Площадь застройки одного здания например на руднике 3РУ составляет 24×36 м (864 м2) строительный объем (при максимальной высоте здания – 162 м) – 14000 м3.
Принцип раздельного размещения обоснован работой ПМ для отдельного рабочего горизонта в разных условиях технологического режима работы и улучшения условий обслуживания оборудования.
Работа одноканатной ПМ осуществляется с использованием стационарного металлического копра высотой до 70 м расположенного над устьем ствола и совмещенного с надшахтным зданием. Ось максимально расположенного по высоте отклоняющего шкива размещена на отметке +62 м. Например вес металлоконструкций копра ствола № 4 рудника 3РУ при работе на него двух подъемных установок составляет 590 т.
Одноканатные ПМ оборудованы канатами диаметром 64 мм (Волгоград Россия) изготовленные по ТУ-14-496-76 канаты диаметром 63 мм "Тайгер 6Т" 6х28 (Bridon Англия). Канаты отвечают предъявленным нагрузкам при подъемах скипов с отметок загрузочных станций.
Грузоподъемность скипов достигает для марки CH-195 – 27 т.
Подъем руды осуществляется в автоматическом и ручном режимах.
Применен электропривод подъемных установок на постоянном токе. Общая масса одного двигателя постоянного тока достигает 120 т а вес механической части используемых ПМ – 346 т.
Для обслуживания оборудования ПМ в зданиях используются вспомогательные подъемные устройства в виде мостовых кранов грузоподъемностью (гп) до 60 т с пролетом 225 м и электроталей гп 5-10 т.
Устья всех скиповых стволов оборудованы противопожарными лядами.
Диаметр всех вертикальных стволов в свету – 7 м. Армировка скиповых стволов жесткая расстрелы и проводники – сварные коробчатые основной шаг между ярусами 3-4 м. Сечение ствола № 4 3РУ представлено на рисунке 2.2.
Таким образом опыт эксплуатации скиповых подъемов рудника 3РУ показывает что при высоте подъема 850 м максимальная годовая производительность (при 18 час. работы в сутки 330 рабочих днях в году и коэффициенте неравномерности подъема равным 135) составит не более 374 млн.т. а при наличии двух скиповых подъемов не более 748 млн.т.
На руднике 4РУ глубина шахтного скипового ствола №4 составляет 8979 м – самый глубокий ствол в Солигорском бассейне (таблица 2.4). Шахтный ствол оборудован двумя двухскиповыми подъемами с многоканатными подъемными машинами ЦШ 5×8 (8 канатов) и МК 5×4 (4 каната) производства Новокраматорского машиностроительного завода. Максимальная концевая нагрузка машины МК 5×4 – 49000 кг ЦШ 5×8 – 97500 кг. На подъемных машинах применены подъемные канаты диаметром 435 мм фирмы Bridon (Англия).
Скиповые многоканатные машины расположены в башенном копре с размещением вала ПМ МК 5х4 на отметке 90 и ЦШ 5х8 106 м. Площадь застройки башенного копра 24×21 м (504 м2). Высота башенного копра 1236 м общий вес копра 3300 т.
Диаметр ствола в свету – 7 м. В стволе применена жесткая расстрельная армировка (рисунок 2.3) с коробчатыми сварными расстрелами 210×135×12 и расстрелами из уголка 160×160×12 проводниками 180×180×12 и 200×200×16. Шаг армировки в отличие от других рудников (3-4 м) был принят равным 6 м.
На подъемной машине МК 5×4 эксплуатируются скипы СНМ-19 грузоподъемностью 220 т а на ЦШ 5×8 – СНМ-35 грузоподъемностью 42 т.
В проекте для обеих машин была заложена рабочая скорость скипового подъема для обеих машин – 144 мсек.
- область эффективного применения одноканатных ПМ - работа на глубинах до 800 м с производительностью до 900 тчас при использовании грузовых скипов СН-195 грузоподъемностью 27т;
- работы по техническому обслуживанию многоканатных ПМ по отношению к одноканатным являются более сложными и трудоемкими. При выполнении отдельных видов работ эксплуатация калийного горизонта прекращается;
- на одноканатных ПМ для снижения коррозионного износа каната производят периодическое нанесение смазки Торсиол-35Э;
- на всех подъемных машинах используются тормозные устройства с пневматическим (машины с барабанной навивкой каната) и пружинно-пневматическим (машины со шкивами трения) приводами;
- при работе скиповых подъемов на больших скоростях (свыше 8-10 мс) в шахтных стволах с жесткой расстрельной армировкой требуется усиленный и своевременный контроль состояния проводников ширины колеи роликоопор направляющих башмаков и др.;
- копровые и канатоведущие шкивы установлены на коренных валах с использованием подшипников качения а ПМ с барабанной навивкой каната с использованием подшипников скольжения или качения.
Схема расположения машины в машинном зале и скипов в копре представлена на рисунке 3.8 .
Рисунок 3.8. –Схема расположения машины в машинном зале и искипов в копре.
Разработка конструкции изделия
1 Описание конструкции изделия
Подъемные машины с одним бицилиндроконическим разрезным барабаном применяются для однослойной навивки каната на двухскиповых и двухклетевых подъемах а также для однососудных подъемов с противовесом на глубоких шахтах и рудниках.
Отличительной особенностью машин является бицилиндроконическая форма барабана которая позволяет уравновесить систему подъема (устранить или ослабить влияние массы головных канатов) без применения уравновешивающего каната. Нижний канат закрепленный на заклиненной части барабана может навиваться только до разреза т.е. до переставной части барабана. Верхний канат закрепленный на переставной части барабана переходит через разрез.
Машины могут иметь правое или левое расположение привода при этом конструкция их не отличается (левая часть барабана - заклиненная правая - переставная) но в обеих случаях правый канат должен быть верхним а левый - нижним. Подъемная машина должна быть установлена относительно копровых шкивов таким образом чтобы ось плоскости вращения копрового шкива верхнего каната была смещена на 100 - 150 мм от плоскости разреза барабанов в сторону заклиненной части барабана чем обеспечивается нормальный переход каната через разрез с переставной части барабана на заклиненную.
Заклиненная часть барабана (состоящая из цилиндра малого диаметра конуса и цилиндра большого диаметра) соединена с валом-трубой жестко а другая - переставная (содержащая цилиндр малого диаметра и конус) имеет возможность относительного углового перемещения. Переставная часть барабана установлена на валу-трубе на роликовой опоре (подшипниках качения) и с помощью пружинно-пневматического расцепного устройства зубчатого типа фиксируется в угловом направлении относительно заклиненной части барабана.
Регулируется длина канатов перестановкой барабана – вращением заклиненной части барабана относительно заторможенной переставной части барабана.
При двухсосудном подъеме возможно обслуживание одного или одновременно нескольких смежных горизонтов. В последнем случае расстояние между горизонтами не должно превышать рабочей длины каната на переставной части барабана. Однососудный подъем с противовесом позволяет обслуживать несколько горизонтов без ограничения расстояния между ними. Подъемные машины типа БЦК могут комплектоваться радиально-колодочными или дисковыми тормозами.
Техническая характеристика шахтной скиповой подъемной установки :
(На основании задания по курсовому проектированию)
- длина отвеса головного 622 м
- высота подъема 600 м
- назначение грузовая (подъём руды спуск-подъём
грузов под скипом аварийный вывоз людей
проведение осмотра ствола проведение
ремонтных работ в стволе)
- концевая нагрузка 408 т (25 т – масса груза
- количество комплектов подъемных машин 1
- ориентировка пути вертикальная
- место расположения подъемных машин наземного базирования
- тип подъемных сосудов скипы СН-195
- тип органов навивки каната барабанного типа двухконцевой
- максимальное статическое натяжение каната не менее 630 кН
- число подъемных канатов одноканатная
- тип электропривода переменного или постоянного тока
- схема привода редукторная схема
- количество обслуживаемых горизонтов один
- нагрузки вес поднимаемого полезного груза
за один раз 25000 кг
- срок службы установки не менее 35 лет
- копровые шкивы диаметр 6 м (2 шт.)
На рисунке 1.1 представлена схема скипового ствола с расположением подъемных сосудов в сечении ствола.
Рисунок 1.1 - Схема скипового ствола с расположением
подъемных сосудов в сечении ствола
3 Определение часовой производительности скипового подъема
Исходя из исходных данных (Т=330 t=18 час. Кн=125) рассчитаем часовую производительность скипового подъема с одной подъёмной машиной.
Кн- коэффициент резерва подъёма;
С- годовая проектная произврдительность подъёма;
T- число рабочих дней в году;
t- продолжительность работы машинычсут.
Оценка возможности применения одноканатных подъемных машин
Исходя из приведенных выше требований определим возможность применения на скиповом подъеме одноканатных подъемных машин.
Для анализа выберем самую крупную и значительную по своим характеристикам (максимальному статическому натяжению каната канатоемкости и др.) одноканатную подъемную машину.
Для расчета примем схему 2-х скипового подъема с одной подъемной одноканатной машиной. Грузоподъемность скипов 25 т вес скипа с подвесным устройством 158 т (концевая нагрузка 408 т).
Для расчета используем диаграмму скорости подъемной машины БЦК-85х27 с ускорением-замедлением 10 мс2 (рисунок 2.1). Зависимость годовой производительности 2-х скипового подъема с одной одноканатной подъемной машиной БЦК-85х2 от рабочей скорости представлена на рисунке 2.2.
Как видно из рисунка 2.2 необходимая производительность (45 млн.т руды в год) скипового подъема рудника достигается при скорости подъема скипов 142 мс.
Рисунок 2.1 – Расчетная диаграмма скорости подъемной машины
БЦК-85х27 для обеспечения производительности 45 млн. т
Рисунок 2.2 – Зависимость годовой производительности двухскиповой подъемной установки
с одной одноканатной ПМ от скорости движения скипов
4 Расчет и выбор подъемного каната
Исходные данные для расчета:
грузоподъемность Qгр = 408 т (25 т – масса груза 158 т – масса скипа).
Согласно п.340 [3] отношение суммарного разрывного усилия всех проволок каната к концевому грузу (без учета массы подъемного каната) для одноканатных грузовых подъемных установок должен быть не менее 85-кратного (при длине отвеса более 600 м). Запас прочности с учётом массы каната для грузовых подъёмов должен быть не ниже 45 кратного.
Определим разрывное усилие каната Qразр при нагрузке равной 408 т:
Qразр = Qгр 981 Нкг n (3.2)
где n – коэффициент запаса.
Qразр =40800 кг 981 Нкг 85 = 3402 кН
Исходя из величины концевой нагрузки и требуемого коэффициента запаса должен выбираться канат с минимальным разрывным усилием не менее 3402 кН.
По таблице каталога на канаты Bridon [2] выбираем канат Bridon "Тайгер Дайформ 6R" маркировочной группы 1960 Нмм2 с расчетным суммарным разрывным усилием Qразр =3428 кН. Диаметр каната равен dк =63 мм номинальный вес погонного метра каната γк = 1628 кгм.
Концевая нагрузка на канат при подъеме определяется:
Qконц = Qгр + Qкан (3.3)
Вес груженого скипа
Qгр = 40800 кг 981 Нкг = 400248 кН
Вес каната определяется
Qкан = Нп γ 981 (3.4)
Qкан = 600 м 1628 кгм 981 Нкг =958 кН
Тогда концевая нагрузка на канат с учётом массы каната равна:
Qконц = 400248+ 958 =496048 кН
Проверим запас прочности выбранного каната:
(соответствует требованиям п.340 [3] с учетом массы каната).
5 Выбор параметров одноканатной скиповой подъемной установки
5.1 Выбор подъёмной машины для одноканатного подъёма
В задании по курсовому проекту указано что подъёмная машина должна быть изготовлена на максимальное статическое натяжение ветви каната не менее 630 кН и однослойной навивкой каната.
Максимальное натяжение гружёной ветви каната при применении каната 63 мм составит 5145 кН т.е. максимальные статическое натяжение составит соответственно 817% от 630 кН.
5.2 Определение отношения диаметра барабана ШПМ к диаметру каната
Согласно п. 79 [3] отношение наименьшего диаметра навивки барабана или шкива к диаметру каната должно быть не менее 79-ти:
5.3 Проверка подъемной машины БЦК-85x2 по канатоемкости органа навивки
Проверку подъемной машины по канатоемкости проведем из условия (стр. 23 [4]):
Hmax = ·(Dm·n1+ Dср·n2+Dб·n3)>600 м (5.1)
Dm = 5 м – диаметр малого цилиндра барабана ПМ;
Dб = 8 м – диаметр большого цилиндра барабана ПМ;
Dm = – средний диаметр конической части барабана ПМ;
n1 = - количество витков на цилиндрической части малого барабана ПМ
b = 870 мм – ширина цилиндрической части малого барабана ПМ;
t = 1076·d+26 (стр. 23 [4]) - шаг навивки: (5.2)
t = 1076·63+26 = 70 мм.
n2 = 9 – количество витков на цилиндрической конической части ПМ;
n3 = - количество витков на цилиндрической части большого барабана ПМ (5.3)
k = 150 мм – ширина переходной полосы переставной части барабана на большом цилиндре.
Hmax = 314·(5·7+ 65·9+8·26) = 947>600 м
Таким образом канатоёмкость подъёмной машины БЦК-85х2 достаточна.
5.4 Расчет мощности приводных электродвигателей подъёмной машины БЦК-85x2
Расчёт мощности двигателей проведём для ускорения-замедления подъёмной машины 1 мс2 (для скорости подъёма 142 мс)
Подъемная машина БЦК-85x2
- высота подъема м – 600;
- диаметр малого барабана (Dм) м – 5;
- диаметр большого барабана (Dб) м – 8;
- диаметр шкива (Dш) м – 6;
- ускорение разгона (aр) мс2 – 1;
- ускорение замедления (aз) мс2 – 1;
- скорость подъема сосуда (v) мс – 142;
- масса груза (mгр) кг – 25000;
- масса сосуда (mс) кг – 15800;
- масса погонного метра каната (mк) кгм – 1628;
- маховый момент машины (Iм) Н·м2 – 90000000;
- маховый момент шкива (Iш) Н·м2 – 1390000;
- коэффициент шахтных сопротивлений (k) – 115;
- ускорение свободного падения (g) мс2 – 981.
5.5. Расчет пути пройденного сосудами на каждом участке тахограммы
При расчете пути значения скорости и времени движения сосудов на каждом участке берутся из тахограммы (рисунок 2.1).
Участок 0-1: S0-1 =
Участок 1-2: S1-2= v2·t1-2 = 1·4 = 4м.
Участок 2-3: S2-3 =
Участок 3-4: S3-4= v4·t3-4 = 142·275 = 39052 м.
Участок 4-5: S4-5 =
Участок 5-6: S5-6= v6·t5-6 = 05·8 = 4м.
Участок 6-7: S6-7 =
S=S0-1+S1-2+S2-3+S3-4+S4-5+S5-6+S6-7=05+4+10032+39052+1007+4+013= 600 м
5.6 Расчет приведенной массы подъемной установки.
Приведенная к окружности навивки масса подъемной установки:
m’ = 2· mс+mгр+mк·L+ mш’+mм’ (5.5)
mшк’ – приведенная к окружности навивки приведенная масса шкива кг:
mш’ = (стр. 86 [1]) (5.6)
GD2 – маховый момент кН·м2
mм’– приведенная к окружности навивки приведенная масса машины кг:
m’ = 2· 15800+25000+1628·600+2·3935+187231 = 261469 кг.
5.7 Тяговый расчет и определение мощности и типа двигателя
Движущее усилие приведенное к окружности навивки в начале равноускоренного движения груженого сосуда (т. 0 рисунок 2.1):
F0 = k· mгр·g+ mк·L·g+ m’· aр =
=115·25000·981+1628·600·981+261469·1 = 639331 Н (5.8)
Движущее усилие приведенное к окружности навивки в конце равноускоренного движения груженого сосуда (т. 1 рисунок. 2.3):
F1 = k· mгр·g+ mк·(L+2·S0-1)·g+ m’· aр =
=115·25000·981+1628·(600-2·05)·981+261469·1 = 639171 Н (5.9)
Движущее усилие приведенное к окружности навивки в начале движения с постоянной скоростью груженого сосуда (т. 1’ рисунок 2.3):
F1’ = k· mгр·g+ mк·(L+2·S0-1)·g = (5.10)
5·25000·981+1628·(600-2·05)·981 = 377702 Н.
Движущее усилие приведенное к окружности навивки в конце движения с постоянной скоростью груженого сосуда (т. 2 рисунок 2.3):
F2 = k· mгр·g+ mк·(L+2·(S0-1+ S1-2))·g = (5.11)
5·25000·981+1628·(600-2·(05+4))·981 = 376424 Н.
Движущее усилие приведенное к окружности навивки в начале равноускоренного движения груженого сосуда (т. 2’ рисунок 2.3):
F2’ = k· mгр·g+ mк·(L+2·(S0-1+ S1-2))·g+ m’· aр = (5.12)
5·25000·981+1628·(600-2·(05+4))·981+261469·1 = 637893 Н.
Движущее усилие приведенное к окружности навивки в конце равноускоренного движения груженого сосуда (т. 3 рисунок 2.3):
F3 = k· mгр·g+ mк·(L+2·(S0-1+ S1-2+S2-3))·g+ m’· aр = (5.13)
5·25000·981+1678·(600-2·(05+4+10032))·981+261469·1 = 605850 Н.
Движущее усилие приведенное к окружности навивки в начале движения с постоянной скоростью груженого сосуда (т. 3’ рисунок. 2.3):
F3’ = k· mгр·g+ mк·(L+2·(S0-1+ S1-2+S2-3))·g = (5.14)
5·25000·981+1628·(600-2·(05+4+10032))·981= 344381 Н.
Движущее усилие приведенное к окружности навивки в конце движения с постоянной скоростью груженого сосуда (т. 4 рисунок 2.3):
F4 = k· mгр·g+ mк·(L+2·(S0-1+ S1-2+S2-3+S3-4))·g = (5.15)
5·25000·981+1628·(600-2·(05+4+10032+39052))·981= 219643 Н.
Движущее усилие приведенное к окружности навивки в начале равнозамедленного движения груженого сосуда (т. 4’ рисунок 2.3):
F4’ = k· mгр·g+ mк·(L+2·(S0-1+ S1-2+S2-3+S3-4))·g- m’· aз = (5.16)
5·25000·981+1628·(600-2·(05+4+10032+39052))·98-261469·1=
Движущее усилие приведенное к окружности навивки в конце равнозамедленного движения груженого сосуда (т. 5 рисунок 2.3):
F5 = k· mгр·g+ mк·(L+2·(S0-1+ S1-2+S2-3+S3-4+S4-5))·g- m’· aз = (5.17)
5·25000·981+1628·(600-2·(05+4+10032+39052+1007))·98-261469·1
Движущее усилие приведенное к окружности навивки в начале движения с постоянной скоростью груженого сосуда (т. 5’ рисунок 2.3):
F5’ = k· mгр·g+ mк·(L+2·(S0-1+ S1-2+S2-3+S3-4+S4-5))·g = (5.18)
5·25000·981+1628·(600-2·(05+4+10032+39052+1007))·98=
Движущее усилие приведенное к окружности навивки в конце движения с постоянной скоростью груженого сосуда (т. 6 рисунок 2.3):
F6 = k· mгр·g+ mк·(L+2·(S0-1+ S1-2+S2-3+S3-4+S4-5+S5-6))·g = (5.19)
5·25000·981+1628·(600-2·(05+4+10032+39052+1007+4))·98=
Движущее усилие приведенное к окружности навивки в начале равно-замедленного движения груженого сосуда (т. 6’ рисунок 2.3):
F6’ = k· mгр·g+ mк·(L+2·(S0-1+ S1-2+S2-3+S3-4+S4-5+S5-6))·g- m’· aз = (5.20)
5·25000·981+1628·(600-2·(05+4+10032+39052+1007+4))·98-
Движущее усилие приведенное к окружности навивки в конце равнозамедленного движения груженого сосуда (т.7 рисунок 2.3):
F7 = k· mгр·g+ mк·(L+2·(S0-1+ S1-2+S2-3+S3-4+S4-5+S5-6+S6-7))·g-
5·25000·981+1678·(600-2·(05+4+10032+39052+1007+4+013))·98-
По полученным значениям построим график изменения движущего усилия на каждом участке тахограммы (рисунок 2.3).
Определим среднее значение движущего усилия приведенного к окружности навивки на каждом участке тахограммы умноженное на время в течении которого оно действует по следующим формулам (стр. 31 [4]):
- если разница между Fn и Fn+1 велика:
- если разница между Fn и Fn+1 невелика:
Определим эффективное движущее усилие на окружности навивки (стр. 30 [4]):
T = 874 с – время в течении которого двигатель вращающийся с максимальной скоростью отдал бы в окружающее пространство такое количество тепла которое он фактически отдает за время одного цикла подъема.
Определим эффективную мощность двигателя (стр. 30 [4]):
Для удовлетворения ориентировочной максимальной скорости подъёма необходимая частота вращения барабана
Принимаем редуктор 2ЦО-22 с передаточным отношением i=105 и межосевым расстоянием 2200 мм.
Требуемая частота вращения приводных двигателей :
Выбираем стандартную частоту вращения асинхронного двигателя ()
Действительное значение максимальной скорости подъёма
Выбираем 2 двигателя со следующей технической характеристикой: тип- СДН 2-17-71-6 мощность P=3150 кВт частота вращения статор-напряжение 6000 В КПД =969
Полученные расчетные значения движущего усилия приведенного к окружности навивки на каждом участке тахограммы и эффективную мощность двигателя подъемной машины БЦК 85x2 сведем в таблицу 5.1.
Рисунок 2.3 – Расчетная диаграмма изменения движущего усилия
приведенного к окружности навивки машины БЦК 85х2;
5.8 Расход электроэнергии и КПД подъёмной установки.
Требуемая энергия за один подъём в идеальных условиях
Фактический расход электроэнергии за один подъём
КПД подъёмной установки
Удельное значение фактического расхода электроэнергии на подъём одной тонны массы поднимаемого груза
Годовой расход энергии:
Wгод = Wф 1т*А=182*4500000=8190000 кВтч;
Годовая производительность подъёма:
Коэффициент резерва подъёма :
6 Расчет углов отклонения (девиации) струны каната машины БЦК-85x2
Определим высоту копра (стр. 69 [1]):
hп.п = 394 м - высота приемной площадки (стр. 21 [1]);
hс = 15165 м – высота подъемного сосуда;
hпер = не менее 25 м – высота переподъема (п.300 [3]). Высоту переподъема принимаем 64 м;
Rш = 3 м – радиус копрового шкива.
6.1 Расчет угла отклонения (девиации) струны каната машины БЦК-85x2
Расчет углов отклонения (девиации) струны каната машины БЦК-85x2 определяем графоаналитическим способом так как этим способом углы определяются с большей точностью.
На рисунке 2.4 приведена схема скипового подъема на основании которой проводился графоаналитический расчет углов девиации. Особенностью машин БЦК является то что для нормального перехода каната через разрез с переставной части на заклиненную в месте перехода угол девиации каната должен быть не меньше угла подъема нарезки под канат на большом цилиндре барабана. Практически это сводится к расположению оси копрового шкива (ось перпендикулярная продольной оси машины) не менее чем на 150 мм в сторону заклиненного барабана.
Полученные значения углов девиации сведем в таблицу 2.2.
Как видно из расчета машина БЦК-85x2 согласно п.313 [1] проходит по углам девиации в случаях 5 и 7 витков трения однако не проходит при 9 витках трения. Согласно ПБ необходимое количество витков трения-6.
Рисунок 2.4 – Схема к определению углов отклонений струны
каната подъемной машины БЦК-85x2
7 Анализ расчётов при выборе подъёмных машин
На основании вышеприведенных расчетов машины БЦК-85x2 можно сделать следующий вывод: машина подходит по всем расчетным параметрам и соответствует всем требованиям Заказчика машина БЦК-85x2 имеет ряд преимуществ перед остальными машинами:
- переменный радиус навивки обеспечивает лучшее динамическое уравновешивание системы подъема и облегчает пусковые процессы двигателя;
- переменный радиус навивки лучше обеспечивает статическое уравновешивание системы подъема из-за расположения груженной ветви каната на меньшем радиусе навивки в начале подъема. Натяжение груженной ветви составляет: 532 т (при выборе каната диаметром 63 мм.) а натяжение порожней ветви 158 т.
В связи с этим крутящий момент для машины БЦК-85x2: на меньшем радиусе навивки в начале подъема составляет
Mкр.м=532·25=133т·м;
на большом радиусе навивки
Mкр.б=158·4=632т·м.
Разность этих моментов
(ΔM= Mкр.м- Mкр.б=133-632=698т·м)
определяет загрузку электродвигателя ПМ в начале подъема.
- бицилиндрическая форма барабана позволяет выполнить ширину нарезной части меньше чем для двухбарабанной машины. При этом как показал расчет углы девиации канатов уменьшаются что положительно сказывается на сроке службы канатов;
- в связи с лучшей статической и динамической уравновешенностью системы подъема машины типа БЦК уменьшается нагрев двигателя уменьшаются вибрации и динамика механической части машины и двигателя.
8 Выбор расчёт тормозного устройства и коренных подшипников для ПМ БЦК-85x2
8.1 Выбор и расчёт тормозного устройства
Подъемная машина БЦК-85x2 может иметь как радиальные колодочные так и дисковые тормоза. Комплектация машины радиальными колодочными тормозами с параллельным перемещением тормозных балок позволяет обеспечить срок службы колодок на весь период эксплуатации (применение дисковых тормозов требует постоянной замены тормозных элементов а также тормозных модулей через несколько лет эксплуатации).
Радиальные колодочные тормоза являются экологически чистыми из-за использования воздуха по сравнению с маслом для дисковых тормозов работающих с высоким давлением.
Система гидравлических дисковых тормозов конструктивно сложнее пневматических радиальных колодчатых а поэтому сложнее в эксплуатации.
Качественная работа дисковых тормозов зависит от наклона тормозного поля барабанов подъёмных машин в вертикальной плоскости. Поскольку длина вала подъёмной машины БЦК-58х2 между осями подшипников относительно велика (около 8 м) то возможен некоторый прогиб вала что может сказаться на условиях работы дисковых тормозов.
Использование радиальных колодчатых тормозов не требует применения специальных подшипников качения с уменьшенными радиальными зазорами или подшипников скольжения для переставного барабана как это требуется для дисковых тормозов.
На основании вышеизложенного предлагаем применить на скиповых подъёмных машинах рудника радиальные колодочные тормоза.
8.2 Определение статических нагрузок на подъёмную машину
Если для машин с цилиндрическими органами навивки заранее известно что максимальный статический момент нагрузки имеет место при одном из крайних положений подъёмных сосудов то для машин БЦК неизвестно при каком взаимном расположении точек схода канатов с барабана имеет место максимальный статический момент нагрузки. Поэтому необходимо определить натяжения канатов в так называемых критических точках барабана (см.рис. 2.5).
Рис.2.5 Расположение критических точек на бицилиндроконическом барабане
Дальнейший расчёт будем производить по методике из [7].
Предположим что груз находится в правом сосуде.
Тогда критическими точками будут следующие: 1- начало подъёма 3- переход гружёного каната с конической части на большой цилиндр 5- сход порожнякового каната с конической части на малый цилиндр.
При подъёме груза левым сосудом критическими точками являются соответственно 6 4 и 2.
Статические натяжения канатов при прохождении гружёным канатом критических точек составляют:
R –радиус большого цилиндра м; r-радиус малого цилиндра м.
Статические моменты при прохождении канатами критических точек для двухсосудного подъёма определить по формулам:
При расчёте тормозных моментов выбрать максимальную величину определённую по этим формулам.
Максимальные статические натяжения канатов при перестановке для двухсосудного подъёма определить для критических точек 1 (6) и 3 (4) по формулам:
Статические моменты при перестановки барабанов для критических точек определить по формулам:
Из выше представленных формул выбрать максимальную величину которую и учитывать при расчёте тормоза.
Максимальные статические моменты при обрыве одного из канатов определить для критических точек 1(6) и 3(4) по формулам:
из которых выбрать максимальную величину
8.3 Выбор тормозных моментов
Для обеспечения требований ПБ к коэффициенту статической надёжности тормоза при спуске-подъёме расчётного груза коэффициенту статической надёжности предохранительного и рабочего тормозов при перестановке барабанов и обрыве каната порожнего сосуда а также к величине замедления подъёмной установки в период предохранительного торможения величина тормозного момента должна удовлетворять следующим условиям.
Создание требуемого коэффициента статической надёжности тормоза при спуске-подъёме расчётного груза
Создание требуемого коэффициента статической надёжности тормоза при перестановке барабанов для двухбарабанных подъёмных машин и машин с разрезным барабаном
Момент при 2 приводах тормоза определяется усилиемсоздаваемым одним из приводов.
При наличии 2 приводов тормоза они как правило настраиваются на создание тормозного момента одинаковой величины.
Создание требуемого коэффициента статической надёжности тормоза при обрыве каната порожнего сосуда:
8.4 Расчёт параметров тормозных приводов
По требуемому коэффициенту статической надёжности тормоза (К) найти расчётное усилие в тяге соединяющей каждый привод тормоза с исполнительным органом.
Для машин с грузо-пневматическим
приводом тормоза 3 типа рис.2.6
По требуемому коэффициенту статической надёжности тормоза К=12 при перестановке барабанов найти расчётное усилие одного привода по формуле:
По требуемому коэффициенту статической надёжности тормоза К=12 при обрыве каната порожнего сосуда найти расчётное усилие одного привода по формуле:
8.5 Выбор подшипников подъёмной установки
В конструкции машины могут использоваться как подшипники качения так и подшипники скольжения.
Срок службы высококачественных подшипников качения (типа FAG) составляет около 100000 часов непрерывной работы. При заданных технологических параметрах работы скиповой подъёмной установки непрерывная работа подъёмной машины составит около 5000 часов в год т.е. срок эксплуатации подъёмных машин с подшипниками качения составит примерно 20 лет работы рудника и как минимум один раз придётся менять подшипники за время эксплуатации рудника.
Срок эксплуатации подшипников скольжения также составляет около 20 лет.
Стоимость подшипников качения выше чем подшипников скольжения.
Применение подшипников скольжения несколько увеличит длину вала подъёмной машины. Также применение подшипников скольжения требует специальной маслостанции что приводит к удорожанию технического решения применения подшипников скольжения.
На основании вышеизложенного предлагаем применить на скиповых подъёмных машинах БЦК-85х2 подшипники качения как наиболее приемлимые в эксплуатации.
8.6 Технические решения по узлам загрузки и разгрузки скипов
В соответствии с ОНТП 5-86 [6] для калийных рудников емкость подземного бункера должна обеспечивать непрерывную работу скипового подъема в течение одного часа. При расчетной производительности двухскипового подъема Берёзовского рудника 947 тчас рекомендуется емкость подземного бункера с учетом возможности увеличения суточной производительности подъема принять равной 2000 т.
На рисунке 3.1 приведена схема подземного узла загрузки скипов. Руда с горных участков по панельным и магистральным конвейерам поступает в подземный бункер и далее по пластинчатому (ленточному) питателю – в загрузочные бункера-дозаторы (каждый по 25 т). Загрузочные устройства должны оборудоваться датчиками весовой дозировки и датчиками уровня дублирующими контроль загрузки. Сигнал о заполнении бункера следует выводить на пульт управления машины.
Приемные подземные бункеры должны быть оборудованы устройствами предотвращающими попадание в скипы негабаритов размерами превышающими допустимый максимальный размер куска руды.
Разгрузка скипов в надшахтном здании осуществляется в общий бункер разделенный перегородкой на два отделения. Из приёмного бункера (рисунок 3.2) руда через течки на ленточные конвейера до дробильного отделения обогатительной фабрики.
Скип с секторным затвором обладает одним существенным недостатком – он разгружается с помощью кривых смонтированных на станке копра. Эти разгрузочные кривые зачастую являются причиной аварийности в стволе при разгрузке скипа.
Для скиповых подъёмных установок с секторным затвором на рудниках применяют 7-ми периодные диаграммы скорости (смотри диаграмму на рисунке 2.1). Такой вид диаграммы в частности обусловлен необходимостью снижения скорости скипа при подходе к разгрузочным кривым и при движении в разгрузочных кривых. Постоянная времени при входе-выходе из разгрузочных кривых составит для случая скипового ствола разрабатываемого рудника 135 с (при общем времени цикла спуска-подъёма 874 с).
В настоящее время в мировой практике применяют скипы с шиберным затвором которые в частности позволяют прейти к 3-х периодной диаграмме скорости (смотри рисунок 3.3) тем самым снижая общее время цикла
спуска-подъёма за счёт исключения из цикла постоянной времени движения в разгрузочных кривых (полный цикл спуска-подъёма составит 836 с).
Расчётная диаграмма производительности скипового подъёма при данном времени цикла спуск-подъём представлена на рисунке 3.4. Как видно из диаграммы расчётная годовая производительность скипового подъёма составит 525 млн.т (при применении скипов с секторным затвором 45 млн.т).
Таким образом применение скипов с шиберным затвором позволяет увеличить производительность подъёмной установки за счёт снижения времени цикла спуска-подъёма.
В качестве привода открытия шиберной заслонки применяют различные технические решения в частности:
- открытие шиберного затвора с помощью гидроцилиндра или пневмоцилиндра установленного на площадке разгрузки скипа. Примером подобного технического решения является скип конструкции фирмы "S
Рисунок 3.1 – Схема подземного узла загрузки скипов
Рисунок 3.2 – Схема разгрузки скипов в копре
Рисунок 3.3 – Расчётная трехпериодная диаграмма скорости
Подъёмной машины БЦК 85х25
Рисунок 3.4 – Расчётная диаграмма производительности скипового подъёма
со скипами с шиберным затвором
- открытие шиберного затвора с помощью устройств позволяющих открывать затвор с помощью самой подъёмной машины при подходе скипа к площадке разгрузки. В частности скип такой конструкции разработан для вновь вводимой угольной шахты "Любельская № 1-2" Львовско-Волынского угольного бассейна (Украина). Общий вид скипа представлен на рисунке 3.6. Скип с шиберным затвором и таким образом разгрузки содержит раму 1 кузов 2 со скошенным днищем для разгрузки затвор 3 с роликами 4 движущихся по направляющим 5 гибкий трос 6 огибающий обводной блок 7 смонтированный на стенке кузова с обеих сторон скипа. Одним концом трос соединён с шибером а другим с – кареткой 8 на которой имеется упор 9 с кареткой перемещается по специальным направляющим вниз и вверх открывая шиберный затвор. В станке копра в зоне разгрузки имеются два стопора 10 смонтированные на расстрельных балках с обеих сторон скипа. При движении скипа на участке разгрузки упоры 9 наезжают на стопоры 10 и удерживаются ими в неподвижном положении относительно станка копра. Относительно скипа упоры 9 с кареткой перемещаются вниз по направляющим открывая посредством гибких тросов 6 затвор 3. Скип начинает разгружаться. Открыв полностью течку скипа машина стопорится груз окончательно высыпается в бункер. После загрузки нижнего скипа машина пускается в обратную сторону верхний скип уходит вниз шибер под собственным весом уходит вниз относительно скипа закрывает его течку каретка с упором под тяжестью затвора занимает верхнее исходное положение. Так что упор с кареткой предназначены только для открывания шиберного затвора. В случае непредвиденного переподъёма скипа стопор 10 смонтированный на расстрельной балке 11 срезает предохранительную шпильку 12 проворачивается на оси 13 пропуская скип вверх. Такая конструкция стопора позволяет предотвратить аварии в случае переподъёма скипа. После устранения переподъёма стопор поворачивается в прежнее рабочее положение. Устанавливают новую предохранительную шпильку система готова к работе. Скипы подобной конструкции могут изготавливаться как для многоканатных так и для одноканатных подъёмных машин система готова к работе. Скипы подобной конструкции могут изготавливаться как для многоканатных так и для одноканатных подъёмных машин.
За счёт отсутствия секторного затвора скипы с шиберным затвором имеют более низкий вес (при сохранании требуемой грузоподъёмности). Данное обстоятельство позволит снизить удельной потребленеие электроэнергии подъёмной машиной на тонну выдаваемой руды.
На основании вышеизложенного предлагаем провести углубленное научное исследование по изучению всех аспектов возможности применеия на скиповом стволе Берёзовского рудника скипов с шиберным затвором. В случае положительного исчерывающего решения проблемных вопросов по скипам с шиберным затвором предлагаем их применить на скиповом стволе Берёзовского рудника.
Рисунок 3.5 – Общий вид скипа с шиберным затвором фирмы "Siemag" (Германия)
Рисунок 3.6 – Общий вид скипа с шиберным затвором
со способом открывания шибера при помощи подъемной машины
В соответствии с заданием на курсовое проектирование на основе изучения достижений мировых производителей калия опыта угольной и горнорудной промышленности в области эксплуатации шахтных подъемных скиповых установок и производителей (поставщиков) этих установок выполненных технических расчетов в данной работе обоснованы следующие технические решения и параметры по скиповому подъёму рудника по объекту:
- подъёмная установка 2-х скиповая с ооднойодноканатной подъёмной машиной наземного расположения со скипами с секторным затвором типа СН-195 (грузоподъёмностью 25 т).
- суммарная часовая производительность подъёмной машины – 947 тч ;
- расчётная рабочая скорость подъёмных машин (при заданных требованиях к технологическому режиму) – 145 мс;
- ускорение-замедление подъёмных машин – 1 мс2;
- скиповой подъём с одной одноканатной подъёмной машиной с однослойной навивкой каната с бицилиндроконическим барабаном (типа БЦК-85х2). Подъёмная машина должна быть изготовлена на статическое натяжение гружёной ветви каната не менее 630 кН. Схема компоновки скипового подъёма с указанием основных отметок углов габаритов и расстояний представлена на рисунке 3.7 .
- подъёмный канат диаметром 63 мм. Канат фирмы Bridon тип каната "Тайгер Дайформ 6R" круглопрядный со стальным сердечником маркировочной группы 1960 Нмм2 с расчетным суммарным разрывным усилием Qразр =3428 кН. Номинальный вес погонного метра каната γк = 1628 кгм.
- тормоз барабана подъёмной машины – радиальный колодочного типа пневмогрузовой;
- коренные подшипники барабана подъёмной машины – подшипники скольжения или качения (типа FAG или аналоги);
- электропривод подъёмной машины: 2 двигателя СДН 2-17-71-6 мощность P=3150 кВт частота вращения статор-напряжение 6000 В КПД =969. Электропривод постоянного тока по системе ТП-Д. Электродвигатели двухопорные соединённые с коренным валом редуктора подъёмной машины муфтой. Электропривод должен обеспечивать скорость подъёма в диапазоне 01 – 145 мс;
- редуктор 2ЦО-22 с межосевым расстоянием 2200 мм передаточное число-105;
- подшипники электродвигателя – скольжения или качения (типа FAG или аналоги);
- копровые шкивы диаметром 6 м.
Разработанные технические решения по скиповому подъему могут использоваться при рабочем проектировании рудника.
Рисунок 3.7 – Схема компоновки скипового подъёма
Список использованной литературы
Расчёт шахтных подъёмных установок. А.В. Песвианидзе Москва Недра 1992
Таблице каталога на канаты Bridon2000
Правила технической безопасности при разработке подземны способом соляных месторождений республики Беларусь. - Солигорск 2006.
Шахтные электрические лебедки и подъемные машины. Справочник. Димашко А. Д. Гершиков И. Я. Кревневич А. А. – М.: "Недра" 1973.
Шахтный подъем. Справочник. Под общей редакцией Б.А. Грядущего. Донецк. Юго-Восток 2007.
Общесоюзные нормы технологического проектирования шахтных подъемных установок. ОНТП 5-86. Минуглепром СССР. – М. 1986.
Руководство по техническому обслуживанию и ремонту шахтных подъемных установок. – М.: Донецк "Донеччина" 2009.
А1-сверху+горизонт.cdw

А1-фронтальный.cdw

В процессе обкатки устранить все неполадки
течи масла и т.д. После окончания обкатки подтянуть фундаментные болты и другие крепёжные детали.
В процессе обкатки вести наблюдение за шумовой характеристикой передач и подшипников
за нагревом подшипников и за качеством уплотнений..
Для снижения коррозионного износа каната производят периодическое нанесение смазки Торсиол-35Э.
Подъёмная машина одноканатная бицилиндроконическая БЦК-85х2
Диаметр большого барабана 8 м.
Диаметр малого барабана 5 м.
Тормозная система радиально колодчатая
Навивка каната однослойная.
Привод по редукторной схеме
Скорость при подъёме руды до 16 мс.
Статическое натяжение канатов 630 кН.
машины (без электрооборудования и стволовой сигнализации) не более 350 т.
Рекомендуемый головной канат для эксплуатации диаметром 64 мм поГОСТ 7669-80 или 63 мм фирмы Брайдон
Срок службы до 25 лет.
Техническая характеристика
Технические требования
A3-Крышка под уплотнение _ КП-20 02.00.002.cdw

A3-Главный вал подъёмной машины _Печать.cdw

требования по СТБ 1014-95
Сталь 45 ГОСТ1050-88
А1-сбоку.cdw

А1-разрез.cdw

Рекомендуемые чертежи
- 20.10.2023