Участок механического цеха по обработке зубчатых колес двигателя Д-260 с разработкой технологического процесса изготовления шестерни промежуточной с втулкой в сборе




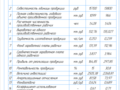
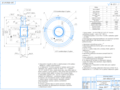
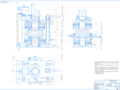

- Добавлен: 25.01.2023
- Размер: 5 MB
- Закачек: 2
Описание
Состав проекта
![]() |
![]() |
![]() ![]() ![]() |
![]() ![]() ![]() ![]() |
![]() ![]() ![]() |
![]() ![]() ![]() ![]() |
![]() ![]() ![]() ![]() |
![]() ![]() ![]() |
![]() ![]() ![]() |
![]() ![]() ![]() |
![]() ![]() ![]() ![]() |
![]() ![]() ![]() |
![]() ![]() ![]() ![]() |
![]() ![]() ![]() ![]() |
![]() |
![]() ![]() ![]() |
![]() ![]() ![]() |
![]() ![]() ![]() |
![]() ![]() ![]() |
![]() ![]() ![]() |
![]() |
![]() ![]() ![]() |
![]() ![]() ![]() |
![]() ![]() ![]() |
![]() ![]() ![]() |
![]() ![]() ![]() |
![]() ![]() ![]() |
![]() ![]() ![]() |
![]() ![]() ![]() |
![]() ![]() ![]() |
![]() ![]() ![]() |
![]() ![]() ![]() |
![]() ![]() ![]() |
![]() ![]() ![]() |
![]() ![]() ![]() |
![]() ![]() ![]() |
![]() ![]() ![]() |
![]() ![]() ![]() |
![]() ![]() ![]() |
![]() ![]() ![]() |
![]() ![]() ![]() |
![]() ![]() ![]() |
![]() ![]() ![]() |
![]() ![]() ![]() |
![]() ![]() ![]() |
![]() ![]() ![]() |
![]() ![]() ![]() |
![]() ![]() ![]() |
![]() ![]() ![]() |
![]() ![]() ![]() |
![]() ![]() ![]() |
![]() ![]() ![]() |
![]() ![]() ![]() |
![]() ![]() ![]() |
![]() ![]() ![]() ![]() |
![]() ![]() ![]() ![]() |
![]() ![]() ![]() ![]() |
![]() ![]() ![]() ![]() |
Дополнительная информация
Ведомость.docx
«шестерня промежуточная со втулкой в сборе 260-1006240СБ»
Сборочный чертеж приспособления для хонингования
Чертеж червячной фрезы
Чертеж подвесного конвейера
Таблица техникоэкономических показателей
(А1)Операционные эскизы(2).cdw

Наименование и модель
Допуск на радиальное биение
Предельные отклонения измерительного
межосевого расстояния
Направление линии зуба
Допуск на погрешность профиля
БНТУ кафедра "технология машиностроения
* Размер обеспечивается инструментом
выдерживая размеры 1
Операция 010 Вертикально-протяжная
Операция 015 токарная-многорезцовая
Операция 035 зубофрезерная
Операция 085 хонинговальная
Операция 104 зубошлифовальная
Хонинговать отверстия
Отзыв.docx
Севбо Артёма Евгеньевича.
Тема проекта: ”Участок механического цеха по обработке зубчатых колес двигателя Д-260 с разработкой технологического процесса изготовления шестерни промежуточной с втулкой в сборе (дет. 260-1006240СБ) и автоматизацией операции зубообработки. Объем выпуска 70 тыс. деталей в год”.
Дипломный проект студента выполнен в полном объёме в соответствии с заданием и методическими указаниями на дипломное проектирование кафедры “Технология машиностроения”. В процессе работы над дипломным проектом студент Севбо Артём Евгеньевич внёс ряд существенных изменений в базовый техпроцесс. В базовом варианте заготовку получают методов штамповки в открытых штампах в проектном же варианте – штамповкой в закрытых штампах что позволяет уменьшить затраты материала. В базовый вариант технологического процесса механической обработки внесены следующие изменения:
) В связи с уменьшением габаритных размеров заготовки уменьшается количество токарных операций что приводит к уменьшению трудоемкости;
) Токарные операции на станках 1А730 и 1Н713 заменяются на токарную операции на одном станке DVH 450 duo
Вышеперечисленные усовершенствования повлекли: сокращение стоимости основных фондов с 13139 до 11296 млн.руб.; повышение рентабельности с 15 до 308% и сокращение срока возврата инвестиций с 756 до 313 лет.
Пояснительная записка содержит полное экономическое обоснование разработанного варианта технологического процесса решение вопросов организации производства охраны труда и техники безопасности а так же охраны окружающей среды.
Спроектированный участок отвечает современному уровню развития машиностроения. На участке механического цеха используется высокопроизводительное оборудование прогрессивная технологическая оснастка.
В процессе работы над дипломным проектом Севбо Артём Евгеньевич показал хорошие знания по общетехническим и специальным дисциплинам способность самостоятельно решать сложные технические задачи. Владеет вопросами проектирования технологического процесса и оснастки умеет пользоваться технической и специальной литературой. В целом дипломный проект выполнен на высоком инженерном уровне и заслуживает оценки “отлично” а студент Севбо Артём Евгеньевич-присвоения квалификации инженера-технолога.
Руководитель проекта: к.т.н.доцент Ярмак Ю.Ю.
(А3)Шестерня промежуточная (поковка) _ 260-1006244-В.cdw

степень сложности С2
индекс 14 ГОСТ 7505-89.
Неуказанные радиусы 3мм.
Неуказанные штамповочные уклоны 3
Смещение штампов до 1.0мм.
Допускается заусенец по контуру обрезки до 1.0мм
Несоостность прошитого отверстия относительно наружного
Внешние деффекты допускаются: на обрабатываемых поверхностях
до 12 фактического одностороннего припуска на механическую
на необрабатываемых - в пределах допусков.
Поковку очистить от окалины.
Коробление поковки до 10мм.
Остальные технические требования по ГОСТ 8479-70.
БНТУ кафедра "технология машиностроения
(А1)Приспособление для хонингования Сборочный чертеж _ 7476-5047 СБ.cdw

поверхности А приты поз. 5 относительно оси шпинделя станка
Опора поз. 3 должна легко без заеданий перемещаться по плите
При отжиме детали плита поз. 5 должна подниматься по стойке
поз. 12 колонкам направляющим поз. 17 без перекосов и заеданий.
Гайку поз. 14 затянуть до упора
Разноразмерность шариков в приспособлении не более 0
Размеры для справок.
Маркировать 7476-5047.
БНТУ кафедра "технология машиностроения
ТИТУЛЬНИК.docx
БЕЛОРУССКИЙ НАЦИОНАЛЬНЫЙ ТЕХНИЧЕСКИЙ УНИВЕРСИТЕТ
Машиностроительный факультет
Кафедра « Технология машиностроения »
ПОЯСНИТЕЛЬНАЯ ЗАПИСКА
«Участок механического цеха по обработке зубчатых колес двигателя Д-260 с разработкой технологического процесса изготовления шестерни промежуточной с втулкой в сборе (дет. 260-1006240СБ) и автоматизацией операции зубообработки. Объем выпуска 70 тыс. деталей в год.»
Специальность 1-36 01 01 «Технология машиностроения»
Специализация 1-36 01 01 01 «Технология механосборочных производств»
Студент-дипломник А.Е.Севбо
Руководитель Ю.Ю. Ярмак
по технологической части Ю.Ю. Ярмак
по САПР И.А.Каштальян
по охране труда Б.М Данилко
по экономической части И.В.Торская
Ответственный за нормоконтроль: Ю.Ю. Ярмак
пояснительная записка – 125 страниц;
графическая часть – 10 листов.
Речь.docx
Окончательной целью проекта было – нахождение оптимального тех. пр-сса изготовления шестерни промежуточной с втулкой в сборе при годовом выпуске 70000в год.
Данная деталь т.е. шестерня промежуточная применяется в двигателе модели Д-260 и является частью распределительного механизма.
Заготовкой для данной детали является поковка в прессах. В проектном варианте был изменен процесс получения заготовки т.е. заготовку получаем не в открытых а в закрытых штампах. Это уменьшает массу получаемой заготовки т.е. снижается коэфф. использования матер. Чертеж детали и заготовки показан на этих листах.
На данных двух листах опер. эскизов показаны операции механической обработки для изготовления новой детали. Отличие проектного варианта от базового в следующем: убраны токарные операции на станках 1А730 1Н713 и заменены на одну токарную операцию на немецком станке DVH 450 duo который представляет собой токарный станок с автоматической загрузкой деталей висячим подвижным шпинделем. В общем виде обработка происходит по следующему маршруту:
На тоокарной операции 005 подготавливаются поверхности под черновую базу.
На операции 010 вертикально-протяжной обрабатывается отв. 44.
Далее на зубофрезерной операции 035 нарезаются зубья.
Далее на зубофасочной операции 040 притупляют фаски по контуру торцев зубьев.
На термической операции 080 нитроцементируют зубья.
Показанное на данном чертеже хонинговальное приспособление применяется на станке 3К82У на операции 085. Зажим детали производится в ручную.
В качестве режущих инструментов применяются резцы сверла зенкеры и протяжки. Резцы изготавливаются из твердого сплава сверла из быстрорежущей стали. Червячная фреза применяемая на зубофрезерном станке 53А30П на операции 035 для нарезания зубьев показана на данном чертеже. Фреза изготовлена из стали Р6М5 ГОСТ 19265-73.
На участке механической обработки шестерни в качестве межоперационного транспорта был принят подвесной грузонесущий конвейер.
В соответствии с заданием разработана планировка участка представленная на данном листе.
Технико-экономические показатели базового и проектного вариантов изготовления шестерни промежуточной при годовом выпуске 70000 штук в год представлены на данном листе. Как видно проектный вариант позволяет уменьшить себестоимость производимой продукции за счёт уменьшения производственных площадей; за счёт уменьшения затрат на изготовление заготовки и собственно на механическую обработку детали. В общем же спроектированный вариант привёл к увеличению рентабельности и уменьшению периода окупаемости инвестиций.
Спасибо за внимание доклад окончен.
Участок механического цеха по обработке зубчатых колес двигателя Д-260 с разработкой технологического процесса изготовления шестерни промежуточной с втулкой в сборе (дет. 260-1006240СБ) и автоматизацией операции зубообработки. Объем выпуска 70 тыс. деталей в год
РЕФЕРАТ.docx
Участок механического цеха по обработке зубчатых колес двигателя Д-260 с разработкой технологического процесса изготовления шестерни промежуточной с втулкой в сборе (дет. 260-1006240СБ) и автоматизацией операции зубообработки. Объем выпуска 70 тыс. деталей в год.
Объектом разработки является техпроцесс изготовления шестерни промежуточной с втулкой в сборе в условиях крупносерийного производства.
Цель проекта: разработать прогрессивный техпроцесс механической обработки шестерни промежуточной с втулкой в сборе с технико-экономическим обоснованием принятых решений.
В проекте было дано описание шестерни промежуточной с втулкой в сборе 260-1006240СБ назначение сборочной единицы. Произведен анализ технологичности конструкции шестерни. Был выбран тип и организационная форма производства. Дан анализ базового варианта технологического процесса и спроектирован новый технологический процесс механической обработки. Был спроектирован конвейер и червячная фреза. Расчитано количество необходимой энергии для осуществления изготовления шестерни промежуточной с втулкой в сборе. Решены вопросы охраны труда и окружающей среды. Дано экономическое обоснование спроектированного тех.процесса.
В процессе проектирования внесены следующие изменения в базовый техпроцесс:
Замена базового способа получения заготовки выполняемом в открытых штампах применением закрытых штампов. Весь техпроцесс получения заготовки автоматизирован припуски на механическую обработку уменьшаются до 15 мм;
Замене токарных операций 015 и 020 выполняемых на станках 1А730 1Н713 на токарные операции выполняемые на станке DVH 450 duo
Разработана конструкция приспособления для хонингования;
Спроектирована фреза червячная для фрезерования зубчатых колес.
Объектами возможного внедрения элементов дипломного проекта могут служить:
Конструкция хонинговального приспособления.
Конструкция червячная фрезы.
Подтверждаю что приведенный в дипломном проекте расчетно-аналитический материал объективно отражает состояние разрабатываемого техпроцесса все заимствованные из литературных источников теоретические и методические положения и концепции сопровождаются ссылками на их авторов.
(А2)Втулка _ 4753430034 240-1006246.cdw

Антифрикционный слой бронза.
Хим. состав в %: Pb 9..11; Sn 9..11;
другиз примесей не более 0
Допускается изготавливать из ленты сталебронзовая.
Основа - лента стальная 08ю-ВГ-Т-I-А ТУ 14-4-1207-82.
не менее-стальной основы
* Размеры для инструмента(матрицы).
Размеры в скобках-после сборки.
покрытие О 1..2. Поверхность В допускается не покрывать.
Размеры и шереховатость поверхностей-после покрытия.
Разностенность не более 0
Допуск овальности поверхности Б не более 0
конусообразности не более 0
6мм(полуразность диаметров).
Диаметр D проверять в контрольном приспособлении под нагрузкой
)кгс]. Эквивалентный диаметр в свободном
состоянии 44.081..44.108мм.
Прилегание поверхности Б к гнезду контрольного приспособления
Маркировать товарный знак предприятия-изготовителя и
обозначение детали шрифтом 2
БНТУ кафедра "технология машиностроения
Рецензия.docx
Представленный дипломный проект выполнен в полном объеме и в соответствии с заданием на проектирование. В проекте развернуто отражены все подлежащие разработке вопросы особенно можно выделить также разделы как «выбор способа получения заготовки» «проектирование станочного приспособления» «Проектирование режущего инструмента».
К недостаткам дипломного проекта следует отнести:
В разделе «назначение детали» неверно указано что промежуточная шестерня передает крутящий момент от шестерни рвала к шестерне привода топливного насоса в то время как она передает крутящий момент на обе эти шестерни от шестерни коленчатого вала.
В разделе «Анализ технологичности конструкции» при определении коэффициента использования материала указаны ошибочные величины массы детали и заготовки(0.1 и 0.3кг).
На эскизе к операции 005 технологического процесса на позициях 357 неверно указано базирование.
В целом дипломный проект выполнен на хорошем уровне и свидетельствует о высокой профессиональной подготовке студента Севбо А.Е. заслуживает оценки «девять».
(А1)ТЭП _ БНТУ-10312810-2013.cdw

Технико-экономические
Кафедра "технология машиностроения
Годовой обьем выпуска продукци
- в натуральном выражении
- в стоимосном выражении
Себестоимость единицы продукции
Полная себестоимость годового
объема произведенной продукции
Расчетная численность
производственных рабочих
Выработка на одного
производственного рабочего
Трудоемкость изготовления продукции
Фонд зароботной платы рабочих
Среднемесячная заработная плата
Прибыль от реализации продукции
Рентабельность продукции
Амортизационные отчисления
Коэффициент использования
остающаяся в распоряжении
Период окупаемости инвестиций
Технико-экономические показатели
БНТУ-ДП-103143С03-2008
(А2)Шестерня промежуточная со втулкой Сборочный чертеж _ 260-1006240 СБ.cdw

' соответствует 20 зубьям
Нормальный исходный
Коэффициент смещения
Степень точности по
Предельные отклонения измерительного
межосевого расстояния
Наименьшее дополнительное
смещение исходного контура
Группа поковки - Гр.II-156..207HB ГОСТ 8479-70. Точность
изготовления поковки - класс II ГОСТ 7505-74
Нитроцементировать h 0.45..0.75мм
.64HRCэ. Сердцевина зубьев
Микроструктура нитроцементированного слоя закаленной шестерни
должна представлять собой безыгольчатый или мелко- и
Неуказанные штамповочные уклоны 3
Допускается уведичение высоты зуба за счет ножки зуба
Углы Ж и З заданы между осями симметрии впадин зубьев на
* Размеры для справок.
Неуказанные предельные отклонения размеров валов h14
Допуск овальности и конусообразности поверхностей
8мм(полуразность диаметров)
На поверхностях шестерни не допускаются трещины
плёны прокатные и другие дефекты
На поверхности Б допускается не более трёх рисок глубиной
Допускается по контуру зубьев фаска величиной не более 1мм на
поверхностях В и Г и не более 0
мм на рабочей поверхности зубьев.
Допускается площадка на одном из зубьев размером Д для проверки
твердости и глубины нитроцементации.
на поверхности Г в местах
указанных на чертеже
глубиной не более 1мм
8-85. Метки и буквы должны быть четко видны. Буквы не
должны заходить за кромку размера E. Метки должны быть расположены на
осях симметрии впадин зубьев и не ближе 2
мм от кромки впадин.
Маркировать шрифтом 2
товарный знак предприятия - изготовителя ударным способом.
Клеймить знак окончательной приемки способом травления.
гарантии изготовителя
Контроль зубчатого венца по нормам точности и боковому
зазору производить при двухпрофильном беззазорном зацеплении
с измерительным колесом.
Шестерня промежуточная
БНТУ кафедра "технология машиностроения
Спец приспособ.docx
Винт ВМ6-6gx10.22H.05
Винт ВМ8-6gх10.22Н.05
Винт ВМ10-6gх35.22Н.05
Винт В1М6-8gх12.88.05
Винт М10-6gх25.88.05
Винт ВМ6-6gх12.22Н.05
Рукав В(II)-6.3-12.5-У
цехСпецификация.docx
Вертикально-токарный
Вертикально-протяжной
Вертикально сверлильный
Пресс гидравлический
БНТУ кафедра «технология машиностроения» группа 103128
Специф шестерня.docx
Шестерня промежуточная со втулкой
Специф конвейер.docx
Устройство поворотное
Конвейер подвесной грузонесущий
охлаждающей жидкости
Крепление поворотного устройства
Записка.docx
Назначение сборочной единицы и обрабатываемой детали9
Анализ технологичности конструкции12
1 Качественная оценка технологичности13
2 Количественная оценка технологичности14
Анализ базового варианта технологического процесса16
Проектирование технологического процесса21
1 Определение типа и организационной формы производства21
2 Выбор метода получения заготовки24
2.1 Анализ методов получения заготовки24
2.2 Экономическое обоснование метода получения заготовки25
3 Выбор варианта технологического маршрута механической обработки по минимуму приведенных затрат26
Проектирование операций механической обработки29
1 Назначение и расчет припусков и предельных размеров29
2 Расчет режимов резания33
2.1 Аналитический расчет режимов резания33
2.2 Опытно-статистический расчет режимов резания36
3 Расчет технической нормы времени41
4 Определение необходимого количества оборудования и построение диаграмм загрузки42
Проектирование станочного приспособления46
1 Выбор вида и типа приспособлений46
2 Силовой и точностной расчет приспособления47
Проектирование режущего и вспомогательного инструментов49
1 Выбор режущих и вспомогательных инструментов49
2 Расчет режущего инструмента49
2.1 Определение конструктивных элементов и геометрических параметров фрезы49
2.2 Определение размеров профиля фрезы в нормальном сечении52
Проектирование средств механизации и автоматизации55
Выбор транспортных средств59
Организация производства цеха61
Энергетическая часть проекта67
1 Производственная санитария техника безопасности и пожарная профилактика69
2 Очистка воздуха от масляного тумана при обработке на металлорежущих станках76
Автоматизация проектирования и расчетов81
1 Проектирование червячных фрез в среде КОМПАС-ГРАФИК81
Экономическая часть проекта90
1 Расчет величины инвестиций90
2 Расчет текущих затрат на объем выпуска продукции (расчет себестоимости продукции)94
3 Расчет основных технико-экономических показателей сравниваемых вариантов114
3Расчет технико-экономических показателей сравниваемых проектов117
Стандартизация в проекте124
Минский завод шестерен одно из крупнейших предприятий по производству шестерен в Республике Беларусь и странах СНГ. Основным направлением деятельности предприятия является производство шестерен для промышленных предприятий РБ(рисунок 1.1)производство запасных частей к тракторам «Беларус» Минского тракторного завода ЮМЗ САЗ К-700 ДТ-75 и др.На предприятии освоен полный технологический циклпроизводства шестерен. На предприятии собственное заготовительное кузнечно-штамповое инструментальное химико-термическое и обрабатывающее производства.
ПРУП «Минский завод шестерен» входит в производственное объединение «Минский тракторный завод» и является одним из крупнейших поставщиков комплектующих запасных частей для тракторов на конвейер МТЗ. В условиях роста спроса на белорусские трактора важно обеспечить качественное техническое обслуживание и ремонт поэтому большинство организаций эксплуатирующих отечественную технику приобретают оригинальные запасные части производства Минского завода шестерен.
Рисунок 1.1 - Один из видов шестерен выпускаемых предприятием
Благодаря огромному инженерно-техническому потенциалу на предприятии освоен выпуск тракторных плугов. Модельный ряд тракторных плугов включает пропашные плуги оборотные навесные и полунавесные плуги для гладкой пахоты плуги с рессорной защитой для каменистых почв.(рисунок 1.2) Вся гамма тракторных плугов производства Минского завода шестерен положительно зарекомендовала себя на полях Республики Беларусь странах СНГ и дальнего зарубежья.
Рисунок 1.2 – Корпус плуга с полувинтовым отвалом ПЛН-01.000 (ПЛД-06.000)
Описание объекта производства
Двигатель Д-260.5Е3 предназначен для установки на седельные и бортовые тягачи с колесной формулой 4х2 6х6 и 6х4 самосвалы с колесной формулой 4х2 6х4 6х6 полноприводные автомобили лесовозы с колесной формулой 4х4 6х6 и шасси под комплектацию с колесной формулой 4х2 6х4 6х6 полной массой до 32т;
Двигатель Д-260.12Е3 – на автомобили грузовые предназначенные для перевозки различных грузов полной массой до 36т.
Рисунок 1.1 – Двигатель Д-260
Таблица 1.1 – Технические характеристики двигателей
Наименование параметров
Четырёхтактный с турбонадувом и охлаждением надувочного воздуха
Способ смесеобразования
Непосредственный впрыск топлива
Степень сжатия (расчетная)
Номинальная мощность кВт
Номинальная частота вращения мин-1
Максимальный крутящий момент Нм
Максимальная частота вращения холостого хода мин не более
Частота вращения при максимальном крутящем моменте мин-1
Удельный расход топлива при номинальной мощности г(кВт.ч):
Масса дизеля по ГОСТ 14846 кг
Назначение сборочной единицы и обрабатываемой детали
Шестерня промежуточная с втулкой в сборе 260-1006240СБ входит в состав распределительного механизма двигателя Д-260.
Рисунок 2.1 - Распределительный механизм.
– Палец промежуточной шестерни; 2 – заглушка; 3 – кольцо уопрное; 4 – планка; 5 – болт; 6 – шайба; 7 – шестерня промежуточная со втулкой; 8 – втулка промежуточной шестерни; 9 – шайба распределительного вала упорная; 10 – болт специальный; 11 – вал распределительный; 12 – шайба; 13 – шестерня распределительного вала; 14 – шпонка; 15 – планка; 16 – болт; 17 – шайба; 18 – шестерня привода топливного насоса; 19 – прокладка (входит в установку топливной аппаратуры).
Шестерня предназначена для передачи крутящего момента от шестерни распределительного вала 13 к шестерне привода топливного насоса 18. Изготавливается «шестерня промежуточная со втулкой в сборе» 260-1006240 СБ из стали 18ХГТ химический состав и механические свойства которой приведены ниже.
Таблица 2.1 - Химический состав стали 18ХГТ
Никель (Ni) не более
Таблица 2.2 – механические свойства стали 18ХГТ при Т=200С
Закалка 8500С масло отпуск 2000С воздух
Твердость 18ХГТ после отжига ГОСТ 4543-71 - HB 10-1 = 217 МПа;
Твердость 18ХГТ нагартованного ГОСТ 4543-71 HB 10-1 = 229 МПа;
Sв - Предел кратковременной прочности [МПа];
ST - Предел пропорциональности (предел текучести для остаточной деформации) [МПа];
d5 - Относительное удлинение при разрыве [ % ];
y - Относительное сужение [ % ] ;
KCU - Ударная вязкость [ кДж м2] ;
HB - Твердость по Бринеллю [МПа];
Технологические свойства стали 18ХГТ:
-Свариваемость: без ограничений т.е. сварка производится без подогрева и без последующей термообработки;
-Флокеночувствительность: не чувствительная;
-Склонность к отпускной хрупкости: малосклонна.
Также допускается изготовление «шестерни промежуточной со втулкой в сборе» 260-1006240 СБ из Стали 25ХГТ в связи с тем что их свойства схожи. Однако у Стали 18ХГТ содержание углерода 0.18% а у Стали 25ХГТ – 0.25%.
Анализ технологичности конструкции
Технологический анализ конструкции обеспечивает улучшение технико-экономических показателей разрабатываемого технологического процесса. Поэтому технологический анализ – один из важнейших этапов технологической обработки. Основные задачи решаемые при анализе технологичности конструкции обрабатываемой детали сводится к возможному улучшению трудоемкости и металлоемкости возможности обработки детали высокопроизводительными методами. Таким образом улучшение технологичности конструкции позволяет снизить себестоимость ее изготовления повысить производительность труда и сократить время на изготовление изделия при обеспечении необходимого его качества.
Оценка технологичности конструкции может быть двух видов:
Качественная оценка характеризует технологичность конструкции обобщенно на основании опыта исполнителя и допускается на всех стадиях проектирования как предварительная.
Количественная оценка технологичности изделия выражается числовыми показателями и оправдана в том случае если они существенно влияют на технологичность рассматриваемой конструкции.
1 Качественная оценка технологичности
Сталь 18ХГТ обладает хорошей обрабатываемостью резанием и имеет не высокую себестоимость.
Деталь имеет поверхности обработку которых можно производить стандартным инструментом присутствуют не обрабатываемые резанием поверхности. Обрабатываемые поверхности простой формы. Но присутствуют поверхности требующие применения сложного и специального инструмента.
Анализируя простановку размеров на чертеже необходимо заметить что предельные отклонения размеров определяющих нерабочие поверхности имеют более широкие поля допусков и большую шероховатость чем размеры рабочих поверхностей что не требует увеличения трудоемкости при изготовлении данной детали.
К положительным моментам можно отнести наличие не обрабатываемых поверхностей не высокие показатели шероховатости не высокую себестоимость материала и простоту формы большинства элементов детали. Это хорошо влияет на процесс получения детали.
2 Количественная оценка технологичности
Она может быть осуществлена только при использовании соответствующих базовых показателей технологичности. Поэтому необходимо определить основные и дополнительные показатели.
При оценке технологичности используются следующие показатели:
Основные показатели:
) Технологическая себестоимость детали: Ст=78747 руб.;
1) Уровень технологичности конструкции по себестоимости:
Ку.с.=СтСт.б.=7874786210=091
) Трудоемкость изготовления детали: Ти=4160=07 ч.
1) Уровень технологичности конструкции по трудоемкости изготовления:
Ку.т.=Ти.Тб.и.=07078=089
Дополнительные показатели:
)Коэффициент унификации конструктивных элементов:
где Q у э и Q э - соответственно число унифицированных конструктивных элементов детали и общее шт;
)Коэффициент применяемости стандартизованных обрабатываемых поверхностей:
где Do.c Dм.о - соответственно число поверхностей детали обрабатываемых стандартным инструментом и всех подвергаемых механической обработке поверхностей шт.
)Коэффициент обработки поверхностей: Кп.о= 1 – Dм.о Dэ ;
где DЭ – общее число поверхностей детали шт.
Кп.о= 1 – 1214 = 0143;
)Коэффициент использования материала:
где q Q – масса детали и заготовки соответственно кг.
1) Уровень технологичности конструкции по использованию материала:
Ку.и.=Кб.и.м.Ки.м.=06068=088;
Кб.и.м.Ки.м. – соответственно базовый и достигнутый коэффициент использования материала.
) Коэффициент применения типовых технологических процессов при изготовлении данной детали : Kт.п.=Qт.п.Qп;
где Qт.п. и Qн – соответственно число типовых техпроцессов для изготовления детали и общее шт.;
) Максимальное значение квалитета обработки IT - 8;
)Максимальное значение параметра шероховатости обрабатываемых поверхностей Rz -50(Ra 125).
Масса детали равна 1465 кг;
Проанализировав количественные показатели технологичности для данной детали следует сказать что к отрицательным показателям характеризующим деталь относятся: коэффициент унификации конструктивных элементов - деталь технологична.
Анализ базового варианта технологического процесса
Анализ техпроцесса проводится с точки обеспечения заданного качества изделия и производительности обработки. Содержание и степень углубленности анализа зависят от различных факторов: конструкции изделия применяемых методов его обработки реальных производственных условий. В общем случае анализ техпроцесса должен включать в себя следующие основные вопросы:
) Рациональность метода получения заготовки для данного масштаба производства метод получения заготовки;
) Метод упрочнения детали и соответствие их ее функциональному назначению и условиям эксплуатации машин;
) Станочное оборудование и рациональность его использования;
) Концентрация и дифференциация обработки как средство повышения производительности;
) Автоматизация техпроцесса;
) Базирование заготовок при обработке и определение погрешностей базирования;
) Брак при обработке и причины его возникновения;
) Степень оснащенности операций и др.
Технологический процесс изготовления «шестерни промежуточной с втулкой в сборе» 260-1006240СБ состоит из следующих операций(таблица 4.1):
Годовая программа выпуска «шестерни промежуточной с втулкой в сборе» 260-1006240СБ 70000в год. Производство – массовое.
Предметом анализа является технологический процесс изготовления «шестерни промежуточной с втулкой в сборе» 260-1006240СБ
Анализ приведенных в таблицах(4.2 4.3) сведений показывает что станки используемые на операциях по габаритным размерам обрабатываемой заготовки достигнутой точности и шероховатости поверхностей соответствует требуемым условиям обработки заданной детали. Цены станков представлены за 2000 год.
Минимальный коэффициент загрузки составляет 044 на станке 2А125максимальный 078 на станке 5Д833. Из-за недогруженности станков на других операциях следует догрузить их обработкой других деталей чтобы коэффициент загрузки был 08-085.
В целях более эффективного производства можно выполнить следующие изменения в получении детали:
5 Токарная на станке 1А730;
0 Токарная на станке 1Н713;
проводим на одном немецком станке DVH 450 duo. Станок DVH 450 представляет собой вертикальный токарный станок с автоматической загрузкой деталей висячим подвижным шпинделем. Немецкий станок стоит 375 млн. руб. В результате появляются свободные площади и сократится количество рабочих обслуживающие ранее установленные станки а значит можно говорить о снижении себестоимости детали. Чтобы узнать выгодно ли нам заменять станки на новый необходимо узнать каков будет годовой экономический эффект. Для этого необходимо знать себестоимость старой и новой деталей.
Таблица 4.1 – Операции технологического процесса изготовления «шестерни промежуточной с втулкой в сборе» 260-1006240СБ
Токарная на станке 1К282;
Свертильная на станке 2А125;
Термическая(Нитроцементация зубьев);
Вертикально-протяжная на станке 7566Н67;
Хонинговальная на станке 3К82У;
Токарная на станке 1А730;
Токарная на станке ТВ-06;
Токарная на станке 1Н713;
Прессовая на станке П6326;
Фасочная на станке 5Б525-2;
Токарная на алмазно-расточном станке ВС-301А;
Контроль (Контрольный стол(КС));
Зубофрезерная на станке 53А30П;
Слесарная на зачистном станке 5Б525-2;
Вертикально сверлильная на станке 2Н125;
Зубошлифовальная на станке 5Д833;
Зубофасочная на станке 5Б525-2;
Зубошлифовальная на станке рейсхауэр
Слесарная (Слесарный стол(СС));
Вертикально-сверлильная на станке 2Н135;
Промывка (Моечная машина(ММ));
Сверлильная на станке 2М112;
Таблица 4.2 - Технологические возможности применяемого оборудования
Предельные или наибольшие размеры обрабатываемой заготовки мм
Технологические возможности метода обработки
Шереховатость обрабатываемой поверхности
Таблица 4.3 – Технологическая характеристика применяемого оборудования
Год изготовления станка
Категория ремонтной сложности
Количество станков на операции
Коэффициент загрузки станка
Проектирование технологического процесса
1 Определение типа и организационной формы производства
Тип производства по ГОСТ 3.1119-89 – характеризуется коэффициентом закрепления операций.[1стр.52]
Р i – явочное число рабочих участка выполняющих различные операции при работе в одну смену.
где н – планируемый нормативный коэффициент загрузки станка всеми закрепленными за ним однотипными операциями; н = 075;
Тшт. – штучное время необходимое для выполнения проектируемой операции мин;(На данном этапе используем Тшт по базовому технологическому процессу)
Nм – месячная программа выпуска заданной детали при работе в одну смену
Рассчитаем П o i на операции 005
Пo 005 = 13182*075 ((174 *70000(24))
Остальные значения сведены в табл.5.1.
Таблица 5.1 – значения П o i
Пo i =58. Р i = 096*075*18=1296.
Кз.о. = 581296 =4475.
Согласно ГОСТ 3.1119-83 для коэффициента закрепления операций Кз.о. = 4475 – производство крупносерийное.
Рассмотрим целесообразность организации поточной линии.
Заданный суточный выпуск изделия: NС = N Г 253
где N Г –годовой объем выпуска изделий
Nc = 70000253 = 2767 шт.
Суточная производительность поточной линии: QС = (FС TСР) З
где FС - суточный фонд времени работы оборудования;
TСР – средняя станкоёмкость основных операций;
где – средний коэффициент выполнения норм времени;
n – количество основных операций.
TСР =3173 (18*13) = 136 станко-мин.
З – коэффициент загрузки оборудования.
Q c = (960 136) * 064 = 451 шт.
Таким образом организация поточной ( однономенклатурной ) линии не целесообразна т.к. заданный суточный выпуск изделий меньше суточной производительности поточной линии при условии ее загрузки на 65..75%. Поэтому для изготовления будем использовать переменно-поточную (многономенклатурную) линию с дозагрузкой её аналогичными деталями.
Такт производства: = 60FЭ NГ где FЭ – эффективный годовой фонд времени работы оборудования.
= 60*397570000 = 341 мин.
2 Выбор метода получения заготовки
2.1 Анализ методов получения заготовки
В настоящее время на заводе в виде заготовки для детали «промежуточная шестерня с втулкой в сборе» 260-1006240СБ используется поковка в прессах в открытых штампах(рисунок 5.1) Материал заготовки сталь 18ХГТ.
Рисунок 5.1 – Эскиз заготовки(в открытых штампах)
С целью экономии материала и уменьшения объема механической обработки можно предложить штамповку в закрытых штампах(рисунок 5.2)
Рисунок 5.2 – Эскиз заготовки(в закрытых штампах)
Сравним два метода получения заготовок:
Штамповка на прессах в 2..3 раза производительнее штамповки на молотах припуски и допуски уменьшаются на 20..35% расход металла на поковки – на 10..15%.
При получении заготовок в закрытых штампах их масса меньше на 14% по сравнению с открытыми.
Таблица 5.2 – сравнительный анализ двух методов получения заготовок
Стоимость 1кг заготовок принятых за базу Si
Стоимость 1кг стружки SОТХ
2.2 Экономическое обоснование метода получения заготовки
Стоимость заготовок получаемых вышеперечисленными методами можно определить по формуле:
Sзаг=(Qkтkckвkмkп)-(Q-q)
Q – масса заготовки кг; Q1=24кг Q2=2064кг;
q – масса детали кг; q=1465 кг;
Sотх – стоимость 1кг отходов руб.; Sотх=300руб.;
kт – коэффициент зависящий от класса точности заготовок (IV); kт=1;
kc – коэффициент зависящий от группы сложности заготовки (2й); kc=084;
kв – коэффициент зависящий от массы заготовки; kв=087;
kм – коэффициент зависящий от марки материала заготовки; kм=1;
kп – коэффициент зависящий от объема производства заготовок; kп=1;
Sзаг1=(1500024108408711)-(24-1465)300 =49813руб;
Sзаг2 =(150002064108508711)-(2064-1465)300=43993руб.;
Экономический эффект от внедрения нового метода получения заготовки:
Эз=(49813 -43993)70000=40740000руб.
Это говорит о том что выбранный метод более эффективен.
В результате применения нового способа получения заготовки детали будут получаться более точные сократится и трудоемкость их последующей обработки резанием а также повысится коэффициент использования материала.
3 Выбор варианта технологического маршрута механической обработки по минимуму приведенных затрат
В целях более эффективного производства выполняем следующие изменения в получении детали:
Для определения себестоимости проведем следующие расчеты:
)Часовые приведенные затраты:
Спз=Сз+Счз+Ен(Кс+Кз)
где Сз – основная и дополнительная заработная плата с начислениями рубчас;
Счз – часовые затраты по эксплуатации рабочего места рубчас;
Ен – нормативный коэффициент экономической эффективности капитальных вложений( Ен=015 );
Кс и Кз – удельные часовые капитальные вложения в станок и здание соответственно руб;
Часовые затраты по эксплуатации рабочего места:
где Сб.м.ч.з – практические часовые затраты на базовом рабочем месте рубчас;
Км – коэффициент показывающий во сколько раз затраты связанные с работой данного станка больше затрат на базовом рабочем месте.
Сч.з.=09*2=1.8=15300 руб.
Капитальные вложения в станок:
Kc=(100*Ц)(Fд*Кз.с.);
где Ц – первоначальная балансовая стоимость станка руб;
FД – действительный фонд времени работы станкач;
Кз.с. – коэффициент загрузки станка.
Кс0 = (100*755313791 )(3950*037)=51680724руб;
Кс1 = (100*375000000 )(3950*08)= 11867088руб;
Капитальные вложения в здание:
Кз=(F*250000*100)(FД*Кз.с.);
где 250000 – средняя стоимость здания приходящаяся на 1 м2 производственной площади руб;
F – площадь производственная занимаемая станком с учетом проходов м2;
Производственная площадь с учетом проходов:
где f – площадь станка в плане м2;
Kf – коэффициент учитывающий дополнительную площадь на проходы;
Кз=(2780000*100)(3950*037)=190215м2;
Кз=(1112000*100)(3950*08)=35189м2;
CПЗ0=2900+15300+015(51680724+190215)=7798840руб;
CПЗ1=2900+15300+015(11867088+35189)=1806542руб;
Основная и дополнительная заработная плата с начислениями на соцстрах и приработок:
где 266 – коэффициент учитывающий дополнительную заработную плату начисления на соцстрах и приработок рабочих;
Стф – часовая тарифная ставка;
К – коэффициент учитывающий зарплату наладчика (К=1);
)Технологическая себестоимость:
С0=(СпзТшт)(60*Квн);
где Тшт – штучное время на выполнение операции мин;
– коэффициент перевода стоимости станко-часа в станко-минуты;
С0=(7798840*548)(60*13)=54791руб;
С1=(1806542*34)(60*13)=7874руб;
Годовой экономический эффект:
Эг=(С0-С1)*N=(547919 -78747)30000=1400 млн.руб;
Исходя из полученных расчетов можно сделать вывод что целесообразнее заменить два станка на один новый. Использование нового станка позволит экономить в год порядка 1400млн.руб на изготовление «шестерни промежуточной с втулкой в сборе» 260-1006240 СБ.
Таблица 5.3 - Сравнение двух вариантов технологического маршрута механической обработки.
Стоимость заготовки руб
Прокат 143 (В открытых штампах)
Прокат 143(В закрытых штампах)
Технологическая себестоимость обработки руб
Токарная на станке 1А730
Токарная на станке 1Н713
Токарная на станке DVH 450
Годовой экономический эффект млн. руб
Проектирование операций механической обработки
1 Назначение и расчет припусков и предельных размеров
Рисунок 6.1 - промежуточная шестерня со втулкой в сборе 260-1006240СБ
Рассчитаем припуск на поверхность расчетно-аналитическим способом а на остальные поверхности назначим согласно ГОСТ 7505-89.
Заготовкой является штамповка. Для получения заданного размера следует пройти следующие этапы технологического процесса: точение черновое точение чистовое шлифование чистовое. Расчет припусков на данную поверхность сводим в таблицу 6.1 в которой последовательно записаны маршрут обработки и все значения элементов припуска.
Суммарное значение пространственных отклонений поверхности заготовки:
где - погрешность смещения штампованных заготовок;
– погрешность штампованных заготовок по эксцентричности;
Погрешность установки заготовки на выполняемой операции
где - погрешность соответственно базирования закрепления положения заготовки.
Таблица 6.1 – расчет припусков и предельных размеров по технологическим переходам на обработку вала в зубчатом колесе
Рассчитываем припуск на обработку :
На последней операции минимальному допустимому размеру на чертеже.
Записываем который округляется до того же значения что и .
Предельные значения припусков:
Общий номинальный припуск:
Проверка правильности выполнения расчетов:
(1800-160)=(4200+700+1350)-(4000+400+210)=1640;
Рисунок 6.2- Схема графического изображения припусков
Аналогичном образом рассчитываем припуски и предельные размеры на обработку вала в зубчатом колесе.
Таблица 6.2 – расчет припусков и предельных размеров по технологическим переходам на обработку вала в зубчатом колесе
Проверка правильности выполнения расчеттов:
(2000-160)=(4200+700+1640)-(4000+400+300)=1840;
Рисунок 6.3- Схема графического изображения припусков
На остальные поверхности припуски назначаем по ГОСТ 7505-89(таблица 6.2)
Таблица 6.2 – Припуски и допуски на обрабатываемые поверхности
2 Расчет режимов резания
2.1 Аналитический расчет режимов резания
Рассчитаем режимы резания на один переход аналитическим методом [2т.2].
Операция 005позиция II и позиция IV: Обработка торцовой поверхности.
При черновом точении и отсутствии ограничений по мощности оборудования жесткости системы СПИД принимается равной припуску на обработку; при чистовом точении припуск срезается за два прохода и более. На каждом последующем проходе следует назначать меньшую глубину резания чем на предшествующем. При параметре шероховатости обработанной поверхности Ra=3.2мкм включительно t=0.5..2.0мм; Ra≥0.8мкм t=0.1..0.4мм.
При черновом точении принимается максимально допустимой по мощности оборудования жесткости системы СПИД прочности режущей пластины и прочности державки. Рекомендуемые подачи при черновом наружном точении приведены в [2т.2табл 11 стр 266] а при черновом растачивании в [2т.2 табл 12 стр 267].
При чистовом точении выбирают в зависимости от требуемых параметров шероховатости обработанной поверхности и радиуса при вершине резца [2т.2 табл 14 стр 268].
При прорезании пазов и отрезании величина поперечной подачи величина поперечной подачи зависит от свойств обрабатываемого материала размеров паза и диаметра обработки p[2т.2табл 15 стр 268].
Скорость резания ммин:
При наружном продольном и поперечном точении и растачивании рассчитывают по эмпирической формуле:
Подача S при размере державки резца мм от 16х25 до 25х40:
S=0.8мм при глубине резания t=1мм.
Среднее значение стойкости Т=30..60 мин при одноинструментной обработке( Принимаем Т=30 мин).
Значение коэффициента показателей степени x y и m приведены в [2т.2 табл 17 стр 269].
Коэффициент = является произведением коэффициентов учитывающих влияние материала заготовки [2т.2 табл 1..4стр.261 ] состояния поверхности [2т.2 табл 5стр. 263] материала инструмента [2т.2 табл 6стр. 263].
в=980МПА; КТ=08; =10;
=340; y=0.45; m=0.20;
Силу резания Н принято раскладывать на составляющие силы направленные по осям координат станка(тангенциальную радиальную осевую ). При наружном продольном и поперечном точении растачивании отрезании прорезании пазов и фасонном точении эти составляющие рассчитывают по формуле:
При отрезании прорезании и фасонном точении t – длина лезвия резца.
Постоянная и показатели степени x y n для конкретных(расчетных) условий обработки для каждой из составляющих силы резания приведены в [2т.2 табл 22 стр 273].
Поправочный коэффициент представляет собой произведение ряда коэффициентов учитывающих фактические условия резания. Численные значения этих коэффициентов приведены в [2т.2 табл 91023 стр 264265275].
При главном угле в плане - ;
При переднем угле - ;
При угле наклона главного лезвия - ;
Мощность резания N кВт:
Рассчитывают по формуле:
2.2 Опытно-статистический расчет режимов резания
Режимы резания для остальных переходов рассчитаем опытно-статистическим методом [3] и сведем все данные в таблицу 6.3.
Операция 005 позиция IV: зенкеровать отверстие .
Последовательность определения режимарезания:
Определение длины рабочих ходов суппортов подачи стойкости скорости резания числа оборотов шпинделя n и машинного времени для каждой позиции производится также как и одношпиндельного многоинструментального станка.[3 этапы I-V стр 14-16].
Для осевого инструмента стойкость рассчитывают как и для резцов [3Т-3 стр 26] при этом
Установление машинного времени работы станка исходя из рассчитанного машинного времени по позициям.
Корректирование(уменьшение) числа оборотов шпинделя и подач на нелимитирующих позициях с учетом установленного машинного времени работы станка. Это корректирование целесообразно осуществлять главным образом за счет снижения числа оборотов.( При обработке стальных деталей твердосплавным инструментом не следует понижать скорости резания меньше чем дом 45..50 ммин).
Проверочные расчеты по мощности резания производят так же как и для одношпиндельных многорезцовых станков; при этом в расчет принимают суммарную мощность резания на всех позициях. Для многоинструментальных одношпиндельных станков [3 этап VI стр 16-17] для осевого инструмента [3 С-6 стр. 126-128].
I Определение длины рабочего хода суппорта [3стр 14]:
Значения y [3приложение 3 стр ]
Эскиз наладки с указанием размеров обработки;
Подвод врезание и перебег инструментов y;
Дополнительная длина хода вызванная в ряде случаев особенностями наладки и конфигурацией детали .
;(для зенкера диаметром D=40мм).
II Назначение подач суппортов на оборот шпинделя в ммоб [3 стр 15]:
Определение подачи каждого суппорта по нормативам[3T-2стр 22-25];
;(уточняем подачу по паспорту станка и принимаем ).
III Определение стойкости мин[3T-3 стр 26-27]:
– стойкость в минутах машинной работы станка;
– коэффициент времени резания.
Стойкость зависит от числа инструментов в наладке и равномерности их загрузки.
В случаях когда >0.7 можно не рассчитывая принимать .
IV Расчет скоростей резания в ммин и числа оборотов шпинделя станка n в минуту:
Скорость резания при зенкеровании [3стр. 306]:
Число оборотов шпинделя n в минуту:
Уточняем число оборотов по паспорту станка и принимаем
V Расчет основного машинного времени в мин:
VI Установление машинного времени работы станка исходя из рассчитанного машинного времени по позициям:
VII Корректирование(уменьшение) числа оборотов шпинделя и подач на нелимитирующих позициях с учетом установленного машинного времени работы станка:
VIII Проверочные расчеты по мощности резания:
а) Определение по нормативам сил резания в кН[3T-5 стр 35-36]:
– коэффициент зависящий от обрабатываемого материала;
– коэффициент зависящий от скорости резания.
б) Расчет мощности резания в кВт:
Режимы резания на остальные поверхности назначаем аналогично по источнику [3] и сводим их в таблицу 6.3
Таблица 6.3 – Режимы резания
Вертикально-протяжная
Вертикально-сверлильная
3 Расчет технической нормы времени
Технические нормы времени в условиях массового и серийного производств устанавливаются расчетно-аналитическим методом.
Тшт – норма штучного времени:
Тшт = То + Тв + Тоб + Тот;
где То – основное время мин;
Тв – вспомогательное время мин.
Вспомогательное время состоит из затрат времени на отдельные приемы: Тв = 185(Тус + Тм.в. + Туп + Тиз);
Тус – время на установку и снятие детали мин;
Тм.в. – машинное вспомогательное время мин;
Туп – время на приемы управления мин;
Тиз – время на измерение детали мин;
Тоб – время на обслуживание рабочего места мин. Складывается из времени на организационное и времени на техническое обслуживание рабочего места; Тот – время перерывов на отдых и личные надобности.
Таблица 6.4 - Сводная таблица технических норм времени по операциям мин
Наименование операции
4 Определение необходимого количества оборудования и построение диаграмм загрузки
Таблица 6.5 - Результаты расчёта коэффициентов использования оборудования
Фо=Фн(1-)=4060(1-003)=3938ч;
Количество единиц оборудования для поточного производства на годовую программу выпуска изделий определяется в соответствии с ГОСТом. Однако в целях унификации расчётов при курсовом проектировании допускается определять количество единиц оборудования по общей зависимости
где – годовой объём выпуска заданной детали ;
– эффективный годовой фонд времени работы единицы оборудования
Т.к. Ки=1то Спр=СРокр; КЗфакт=КЗрасч;
Коэффициент использования оборудования по основному(технологическому) времени:
Коэффициент использования станков по мощности:
где – мощность станка; – мощность привода.
где – коэффициент учитывающий потери мощности за счет трения в узлах станка т.е. КПД ().
До нормативного коэффициента ( станки дозагружаем другими деталями.
Рисунок 6.4 - Диаграмма загрузки оборудования
Рисунок 6.5 – Диаграмма использования оборудования по основному времени
Рисунок 6.6 – Диаграмма использования оборудования по мощности
Рисунок 6.7 – Диаграмма стойкости инструментов мин
Проектирование станочного приспособления
1 Выбор вида и типа приспособлений
На хонинговальной операции на станке 3К82У используется специальное приспособление(рисунок 7.1).
По специальным направляющим в приспособлении выдвигается стол в который загружается зубчатое колесо. Стол задвигается обратно и фиксируется вместе с зубчатым колесом с помощью рукоятки 20. После чего начинается обработка зубчатого колеса. После окончания обработки аналогичным образом зубчатое колесо извлекается из приспособления.
Рисунок 7.1 – Приспособление для хонингования(Вид спереди)
2 Силовой и точностной расчет приспособления
Рисунок 7.2 – Г-образный прихват
Сила резания при хонинговании:
Находим крутящий момент при резании:
– радиус обрабатываемого отверстия(40мм=004м);
Крутящий момент для закрепления детали примерно в 1.5..2 раза больше. Следовательно принимаем:
Зная крутящий момент мы можем посчитать силу необходимую для закрепления детали:
Определяем осевую силу Q:
f – коэффициент трения на направляющей поверхности прихвата;
Для достижения необходимой осевой силы Q необходимый момент составит:
Здесь – средний диаметр резьбы(=11мм); – угол наклона резьбы(tg(=1.73); tg – коэффициент трения в резьбе(017); – коэффициент трения на торце гайки(0.15); q – сопротивление пружины(65731).
Зная крутящий момент М считаем силу Т которую нужно приложить чтобы закрепить деталь:
Проектирование режущего и вспомогательного инструментов
1 Выбор режущих и вспомогательных инструментов
Для нарезания зубьев на операции 035 на зубофрезерном станке 53А30П используем червячную фрезу изготовленную из стали Р6М5 ГОСТ 19265-73.
Червячные фрезы представляют собой одно- или многозаходный червяк. Расположенные вдоль оси профильные стружечные канавки образуют зубья которые имеют передний и задние по вершине и боковым сторонам углы необходимые для обеспечения резания. Зубья фрезы затылованы. Червячные фрезы применяют для нарезания цилиндрических колес с прямыми и косыми зубьями внешнего зацепления червячных колес и шлицевых валов. Фрезы разделяют на черновые чистовые и прецизионные.
2 Расчет режущего инструмента
2.1 Определение конструктивных элементов и геометрических параметров фрезы
Материал режущей части сталь Р6М53;
Фреза цельная. Класс точности В;
Наружный диаметр фрезы ;
– высота зуба фрезы;
где – высота головки зуба фрезы
– высота ножки зуба фрезы
Передний угол принимаем ;
Задний угол принимаем . Принятое значение проверяется расчетом заднего бокового угла :
Минимальное значение должно быть не менее .
Величины затылования на вершине зуба определяются по формулам
Элементы стружечной канавки
б) радиус закругления дна канавки мм;
в) угол профиля канавки
г) толщина зуба у основания C должна соответствовать условию
д) при шлифовании зуба по профилю шлифованная часть зуба должна иметь длину не менее 13 окружного шага или 23 длины зуба по дуге наружного диаметра фрезы. Если длина шлифованной части зуба будет меньше указанной то значительно уменьшается срок службы фрезы. При выборе этой величины необходимо подобрать ориентировочно размеры шлифовального круга и проверить чтобы при затыловании он не врезался в соседний зуб.
Диаметр шлифовального круга определяется по формуле
где – наружный диаметр фрезы;
– угол контакта шлифовального круга с затылуемым зубом фрезы
Длина рабочей части фрезы рассчитывается по формуле
где – высота зуба фрезы;
где – длина буртика мм
Диаметр отверстия под оправку рассчитывается по формуле
Диаметр выточки в отверстии равен
Длина шлифованной части отверстия с каждой стороны
Диаметр начальной окружности для фрезы со шлифованным профилем
Угол подъема витков фрезы по начальной окружности
где – число заходов фрезы
2.2 Определение размеров профиля фрезы в нормальном сечении
Расчетный профильный угол исходной рейки в нормальном сечении
Шаг по нормали (между соседними профилями зубьев фрезы)
Расчетная толщина зуба в нормальном сечении на делительной прямой
где – толщина зуба колеса по дуге делительной окружности с учетом необходимого бокового зазора в передаче
где – величина утоньшения зубьев нарезаемых колес для образования бокового зазора после чистовой обработки мм
Расчетная высота головки зуба чистовой фрезы
Высота ножки зуба фрезы
Радиус закругления на головке и ножке зуба
Шаг по оси между двумя витками
Ход витков по оси фрезы
Направление витков фрезы правое.
Направление винтовых стружечных канавок левое.
Осевой шаг винтовой стружечной канавки
Геометрическое построение фрезы червячной модульной будем производить по данным ГОСТ.
Проектирование средств механизации и автоматизации
Подвесной грузонесущий конвейер(рисунок 9.1) состоит из тягового элемента (цепи каната) 3 замкнутого по контуру трассы с постоянно прикрепленными к нему каретками 2 к которым шарнирно прикреплены подвески 4. На подвески укладывают или подвешивают транспортируемые грузы 5. Каретки при помощи тягового элемента движутся по замкнутому однорельсовому (или двухрельсовому) подвесному пути 1 подвешенному к элементам здания или прикрепленному к конструкциям конвейера.
Тяговый элемент приводится в движение электродвигателем приводного механизма. Гибкость тягового элемента в горизонтальной и вертикальной плоскостях обеспечивает подвесному конвейеру пространственную трассу т.е. его направляющий подвесной путь 1 может иметь повороты как в горизонтальной так и в вертикальной плоскостях в любом направлении. Повороты в горизонтальной плоскости осуществляются при помощи поворотных устройств а в вертикальной – при помощи вертикальных перегибов направляющего пути 1 выполняемых по соответственно выбранным радиусам. Первоначальное натяжение тягового элемента создается при помощи натяжного устройства.
Подвесные грузонесущие конвейеры используются в качестве транспортирующих и транспортно-технологических машин непрерывного действия для внутрицехового и межцехового транспортирования самых различных штучных грузов(или сыпучих грузов в таре) а также перемещения изделий по различным технологическим операциям. Кроме того они могут служить подвесным складом грузов-изделий при поточном методе производства.
Рисунок 9.1 – часть вида грузонесущего конвейера
Имеются две модификации оборудования подвесного грузонесущего конвейера ПР-254-5670 ГОСТ 13568-75:
Оборудование для конвейера с горизонтальной трассой и оборудование для конвейера с пространственной трассой.
Оборудование межоперационного подвесного грузонесущего конвейера состоит из следующих частей: привода натяжного устройства привода натяжки поворотных устройств передачи для двух подвесных конвейеров кареток ходового пути тяговой цепи стыков опор сборника смазочно-охлаждающей жидкости. Схематически это оборудование изображено на рисунках ниже.
Рисунок 9.2 – секция цепи
Рисунок 9.3 – Каретка рабочая нормальная
Рисунок 9.4 – секция трассы прямая
Рисунок 9.5 – пластина стыковая
Рисунок 9.6 – поворот
Рисунок 9.7 – устройство натяжное грузовое
Выбор транспортных средств
Одним из основных резервов повышения производительности труда является совершенствование и дальнейшее снижение трудоёмкости процесса перемещения деталей. Транспорт непрерывно связан с производством он является частью производственного процесса непосредственно влияет на длительность его цикла и способствует точному выполнению каждым рабочим установленных норм времени. Во многих случаях он приобретает роль фактора организующего производство.
При выборе транспортных средств исходят из величины грузопотока. Рассчитывается масса на годовую программу следующих грузопотоков: межцехового – из заготовительного в данный механический цех; межоперационный – от станка к станку при механической обработке; массы стружки образующейся в процессе обработки заготовки.
Межцеховой грузопоток в нашем случае рассчитывают по следующей формуле: Q = N = 24×70000 = 168000 кг
где – черновая масса детали кг;
N – годовая программа.
Межоперационный грузопоток q:
q = N = 1465×70000 =102550 кг
где – чистовая масса детали кг.
Масса грузопотока стружки Qс образующейся в отделении за один час при обработке нескольких деталей:
Qс = ( – )N Fд = (24-1465)×70000 3925 = 167 кгчас.
На основании рекомендаций выбираем межцеховой межоперационный транспорт и определяем способ уборки стружки.
Руководствуясь величиной межцехового грузопотока в нашем случае при расстоянии между механообрабатывающим и заготовительным цехами около 300 метров наиболее целесообразно применение электропогрузчиков грузоподъёмностью 2 тонны обеспечивающие производительность до 45 тонны в час при этом стоимость одного машино-часа составляет около 552 руб. а стоимость транспортировки одной тонны 90 руб.
В качестве межоперационного транспорта применим подвесной конвейер
Для удаления стружки применим одновинтовой стружкоуборочный конвейер.
Организация производства цеха
Под научной организацией труда понимают способ соединения непосредственных производителей со средствами производства с целью создания благоприятных условий для получения высоких экономических результатов.
Основные функции по управлению заводом лежат на генеральном директоре главном энергетике главном инженере главном механике главном экономисте главном бухгалтере а также на ряде начальников цехов и подразделений.
Кроме этого для нормального функционирования предприятия созданы службы благодаря которым осуществляется нормальное протекание производственного процесса.
Службы инструментального обеспечения предназначены для обслуживания всего технологического оборудования заранее подготовленными режущими и вспомогательными инструментами осуществления контроля за его правильной эксплуатацией. Все имеющиеся стандартные инструменты изготавливаются на специализированных заводах что позволяет снизить их стоимость наряду с высоким качеством. Специальные инструменты изготавливают на предприятии в инструментальных цехах либо частично получают по кооперации. Общее же руководство системой инструментального обеспечения осуществляет инструментальное бюро. Так же при проектировании системы инструментального обеспечения учитывается и организация самого процесса замены инструмента.
Методы и сроки проведения периодического контроля технологического оборудования на точность зависят прежде всего от типа оборудования выполняемой операции требуемой точности обработки подверженности оборудования износу. Сам процесс изнашивания протекает достаточно медленно и поэтому периодичность проверки составляет одну-две недели.
Основными задачами системы ремонтного и технического обслуживания являются обеспечение работоспособности всего парка подъёмно-транспортного и технологического оборудования механосборочного производства а также организации процесса удаления и переработки стружки обеспечения рабочих мест СОЖ электроэнергией сжатым воздухом и поддержание необходимого микроклимата рабочей зоны.
Ремонтная служба в цехе осуществляет уход и надзор за действующим оборудованием осуществляет планово-предупредительный ремонт технических средств всех видов а также модернизацию существующего нестандартного оборудования. Необходимые работы осуществляются в ремонтно-механическом цехе а также в корпусных ремонтных базах и отделениях по ремонту электрооборудования и электронных систем.
В механообрабатывающих цехах завода как правило применяют централизованно-циркуляционный и децентрализованный методы подачи СОЖ к станкам.
Централизованно-циркуляционный метод применяется для крупногабаритных станков процесс обработки деталей на которых требует больших расходов смазочно-охлаждающей жидкости. В этом случае система подачи СОЖ включает в себя корпусную станцию для её приготовления регенерации и утилизации несколько циркуляционных установок – одна на 70-80 станков сеть трубопроводов для подачи жидкости непосредственно к станкам и систему фильтрации. Большой объём циркулирующей смазочно-охлаждающей жидкости позволяет увеличить срок её службы в системе и как следствие уменьшить периодичность замены.
Децентрализованный метод применяют для обеспечения СОЖ станков небольших размеров или в случае когда расходы смазочно-охлаждающей жидкости не велики. В этом случае СОЖ доставляется к станкам в специальной таре и так же удаляется отработанная жидкость. При работе станка смазочно-охлаждающая жидкость циркулирует по станочной системе трубопроводов при этом производится её постоянная очистка от стружки и других механических примесей. Периодичность её замены зависит от состава свойств режимов работы станков периодичности долива. Чем больше объём системы тем больше срок службы жидкости. Количество механических примесей в СОЖ при обработке лезвийным инструментом не должно превышать 005-007% от объёма и 0003-0004% при абразивной обработке. Для предварительной очистки используют различные сетчатые фильтры для тонкой очистки магнитные бумажные центрифуги.
Масло необходимое для заполнения гидросистем станков находятся в специальных ёмкостях расположенных в соответствующих местах цеха запас масла периодически пополняется из кладовой масел в кладовой также хранится запас масел и различных смазок необходимых для смазки узлов станка. Смазку оборудования производит смазчик с периодичностью указанной в паспорте станка а также с учётом условий работы конкретного оборудования.
Одной из наиболее ответственных служб завода является система контроля качества изделий. Она предназначена для своевременного определения с требуемой точностью параметров качества выпускаемых изделий. Основной задачей её являются также: контроль за ходом технологического процесса своевременное обнаружение и недопущение брака осуществление приёмочного и операционного контроля качества изделий. Выполнением перечисленных функций занимается отдел технического контроля (ОТК) и цеховые контрольные пункты (КП) расположенные непосредственно в цехе.
В основе организации рабочих мест лежит принцип разделения и кооперации труда на участке что является важным фактором роста производительности труда.
На заводе имеют место следующие формы разделения труда:
) Отделение работ по подготовке от работ по исполнению например отделение работ по наладке станков выполняемых наладчиком от основных технологических работ выполняемых оператором.
) Отделение основной работы от вспомогательной. Это дает возможность полнее использовать рабочее время операторов и загрузить оборудование.
) Отделение квалифицированной работы от неквалифицированной. Рациональное разделение труда и расстановка рабочих по рабочим местам требуют соблюдения следующих правил:
) За каждым рабочим закрепляется рабочее место за состояние которого он несет полную ответственность.
) Круг функций и обязанностей каждого рабочего точно регламентируется технологическими и производственными документами.
) Работы выполняемые каждым рабочим или бригадой а также материалы заготовки детали инструменты и другие материальные ценности выделяемые для выполнения работ и текущего обслуживания рабочих мест должны учитываться.
Разделение труда в общественном производстве обуславливает его кооперацию. Особой формой кооперации труда являются бригады. Для руководства работой бригады один из рабочих выбирается бригадиром распоряжения которого обязательны для всех членов бригады.
Рабочее место - элементарная единица структуры предприятия где размещены исполнители работы обслуживаемое технологическое оборудование часть конвейера на ограниченное время - оснастка и предметы труда.
Системы организационно-технических мероприятий обеспечивающие на рабочем месте необходимые условия для высокопроизводительного труда при наименьшей утомляемости рабочих и полном использовании технических возможностей оборудования называют организацией рабочего места.
Рабочие места на участке оснащены технологической документацией высокопроизводительным оборудованием приспособлениями инструментом. Разработана рациональная планировка рабочих мест. Организовано бесперебойное обеспечение рабочего места материалами заготовками и инструментом. Обеспечены здоровые и безопасные условия труда.
Одной из важнейших задач организации труда является создание благоприятной трудовой обстановки которая включает соблюдение требований физиологии труда и инженерной психологии внедрение производственной эстетики в оформлении цеха и рабочих мест поддержание чистоты и порядка на производстве.
Практика ряда промышленных предприятий показывает что внедрение в производство элементов эстетики и культуры труда способствует повышению производительности труда. В эстетике и культуре труда отражаются все стороны производственной деятельности - стены станки агрегаты и другие средства труда окрашены в специальные цвета на участке поддерживается чистота и порядок четко организован сам производственный процесс. Обеспечение чистоты и порядка на рабочих местах - обязанность всех работающих и всего обслуживающего персонала. Для создания хороших условий труда немаловажную роль играет правильное чередование периодов работы и отдыха. В этих целях устанавливается трудовой режим дни отдыха продолжительность отдыха перерывы в течение рабочего дня оптимальный график выхода на работу.
Дисциплина труда на участке:
Основным методом укрепления трудовой дисциплины является воспитание творческого сознательного отношения каждого трудящегося к своему труду к выполнению своих обязанностей.
Администрация поощряет работников за старательное примерное выполнение ими своих обязанностей по работе объявляя благодарности награждая денежными премиями ценными подарками.
Трудовая дисциплина поддерживается также и рядом административных мер. К лицам нарушающим трудовую дисциплину могут быть приняты следующие административные меры: замечание (постановка на вид) выговор строгий выговор перевод на нижеоплачиваемую работу на срок до трех месяцев или смещение на низшую должность на тот же срок; увольнение с предприятия в случае если все меры административного и общественного воздействия не дали положительного результата. В борьбе за укрепление дисциплины труда за предупреждение нарушения внутреннего трудового распорядка большое значение имеет повышение общеобразовательного профессионального и культурного уровня работников.
Основные положения научной организации труда распространяются на все категории работающих в том числе на инженерно-технических работников и служащих. Для организации труда инженерно-технических работников и служащих первостепенное значение имеет распределение объема работ закрепление обязанностей установление за каждым исполнителем прав ответственности.
Энергетическая часть проекта
В данном разделе производится определение расхода применяемых видов энергии (электроэнергия сжатый воздух вода) а также подсчёт их стоимости на выполнение годовой программы выпуска изделий.
Затраты на электроэнергию определяются по одно-станочному тарифу:
Затраты на электроэнергию определяются по формуле:
где – суммарная установленная мощность оборудования кВт;
– коэффициенты учитывающие соответственно спрос загрузку оборудования по мощности по времени потери электроэнергии в сети:
= 04; =04 ; =016 ; =105;
– действительный фонд времени оборудования: = 3925 час.
– цена 1 кВтчас энергии: = 75 рубкВтчас.
Величина установленной мощности определяем по формуле:
m – количество оборудования.
(1991+21+1375+2125+15+5+225+15+15+375)=133.26 кВт.
В итоге: = (13326×04×04×016×105×3925)× 75 = 1054 млн. руб.
Определяем потребность в электроэнергии на освещение
где H-норматив расхода электроэнергии на освещение кВт·ч H=20кВт·ч;
S-площадь участка S=7869;
h-длительность осветительного периода h = 2000ч.
=20 ·7869· 20001000=31476кВтч.
Затраты на воду для производственных нужд определяются по формуле:
где – стоимость 1 водопроводной воды рубм3;
– годовой расход воды на один станок м3;
– коэффициент загрузки оборудования;
Z – число смен работы оборудования Z = 2;
П - расход воды на промывку деталей в моечной машине;
= 119 руб.м3; = 25 м3; = 04 ; n = 18.
на промывку детали в моечной машине из расчета 1л на 10 деталей:
П =01·70000=7000 л в год;
= 119 · (25 · 04 · 2 · 17+7000) = 873460 руб.
Расчет потребности в паре на отопление участка:
где - расход тепла на 1 здания =30 кКалч;
V-объем здания V=4820;
H-количество часов в отопительном периоде H=4320 ч;
i-теплота испарения i=540 кКал.
Q=30 ·4820· 4320(540 · 100)=11568т.
1 Производственная санитария техника безопасности и пожарная профилактика
Для технологических процессов механической обработки шестерни промежуточной со втулкой в сборе(дет. 260-1006240 СБ) на проектируемых участках характерны опасные и вредные производственные факторы (ОПФ и ВПФ) которые по природе действия подразделяются на физические биологические психофизиологические и химические.
Химические ОПФ и ВПФ характерные для рассматриваемых технологических процессов оказывают на человека преимущественно раздражающее и сенсибилизирующее (воздействуют как аллергены) воздействие.
К психофизиологическим факторам можно отнести физические перегрузки перенапряжение отдельных органов человека монотонность труда.
К физическим факторам относятся:
движущиеся машины и механизмы подвижные части технологического оборудования;
повышенная или пониженная температура воздуха рабочей зоны;
отсутствие или недостаток естественного освещения;
повышенный уровень шума и вибрации;
острые кромки заусенцы шероховатость на поверхности заготовок инструментов и оборудования;
повышенная температура поверхностей оборудования;
повышенное значение напряжений в электрической цепи замыкание которое может произойти через тело человека;
повышенная загазованность воздуха рабочей зоны;
недостаточная освещенность рабочей зоны.
Биологические ОПФ и ВПФ включают в себя бактерии вирусы и продукты их жизнедеятельности. Источником этих факторов является (СОЖ).
К вредным производственным факторам относятся: шум запыленность СОЖ вибрации. В процессе механической обработки полуоси заднего моста 540-2403070 выделяются следующие вредные вещества: металлическая и абразивная пыль пары СОЖ и масляного тумана.
В ходе техпроцесса в связи с применением СОЖ возникает масляной туман. Он состоит из капель размером менее 4 мкм (до 90). Эти капельки характеризуются высокой проникающей способностью в легкие человека. Аэрозоли нефтяных масел входящих в состав СОЖ вызывают раздражение слизистых оболочек верхних дыхательных путей.
Накапливаясь во всем объеме рабочего помещения масляные туманы существенно ухудшают условия труда вызывая профессиональные заболевания.
В результате разбрызгивания и испарения СОЖ при обработке на токарных станках величина концентрации аэрозолей масла в воздухе производственного помещения превышает ПДК в 2 25 раза а в отсасываемом из рабочей зоны станка потоке воздуха концентрация составляет 15 22 мгм3. ПДК аэрозолей масел минеральных нефтяных – 5 мгм3. В соответствии с ГОСТ 12.1007 – 76 по степени воздействия на организм человека масляные туманы относятся к 3–ему классу – вещества умеренно опасные.
При обработке материалов резанием в производственных помещениях механических цехов образуется пыль. Проникая в органы дыхания глаза загрязняя кожный покров пыль способствует возникновению заболеваний дыхательных путей глаз и кожного покрова в зависимости от ее химического состава и степени превышения ПДК запыленности в рабочей зоне. Кроме того пыль загрязняет световые проемы (остекления) а также светильники общего и местного освещения значительно снижая нормативную освещенность рабочих мест. Пыль относится к 3–ему классу опасности – вещества умеренно опасные для которых ПДК составляет 6 мгм3.
На проектируемом участке применяются следующие средства коллективной защиты от ОПФ и ВПФ: оградительные и предохранительные устройства; опознавательная окраска и значки безопасности; специальные средства безопасности (системы освещения и вентиляции производственных помещений). Также применяются средства индивидуальной защиты (СИЗ) от ОПФ и ВПФ средства защиты органов дыхания специальная одежда и обувь средства защиты рук головы глаз органов слуха защитные дерматологические средства.
Для индивидуальной защиты на данном производстве применяются следующие средства:
а) Спецодежда – предохраняет работающих от неблагоприятных факторов воздействия внешней среды: механических физических и химических. Спецодежда надежно защищает тело от вредных производственных факторов и вместе с тем обеспечивает свободу движений нормальную терморегуляцию организма хорошо очищается от загрязнений не изменяя после этого своих свойств.
б) Спецобувь должна быть стойкой к воздействиям внешней среды а подошва должна обеспечивать устойчивость рабочего и иметь изготовленную из маслобензостойких материалов подошву со специальным рифлением.
в) Для защиты кожного покрова от воздействия СОЖ применяется защитный крем для рук: «Силиконовый» и «Средство защитное для рук».
Для обеспечения чистоты воздуха и нормализации параметров микроклимата в производственном помещении помимо местных отсасывающих устройств обеспечивающих удаление вредных веществ из зоны резания (пыли мелкой стружки аэрозолей СОЖ) предусмотрена приточная вентиляция в сочетании с естественной вентиляцией. Общеобменная вентиляция действует постоянно.
Приточная вентиляция обеспечивает подачу в производственные помещения чистого воздуха. Она применяется в производственных помещениях со значительными тепловыделениями и малой концентрацией вредных веществ.
Свежий приточный воздух по воздухопроводам направляют в различные зоны производственного помещения и через распределительные насадки попадают в рабочую зону.
Местная вытяжная вентиляция предназначена для удаления вредных веществ из зоны обработки. Она применяется на шлифовальных станках.
Работа вентиляционных систем в комплексе с выбором технологических процессов по ГОСТ 12.3.002—75 и производственного оборудования отвечающего требованиям ГОСТ 12.2.003—74 должна создавать на постоянных рабочих местах в рабочей и обслуживаемой зонах помещений метеорологические условия и чистоту воздушной среды соответствующие действующим санитарным нормам.
На данном участке применяется как естественная так и местная вентиляция.
Выполняемые на участке работы в зависимости от общих энергозатрат организма относятся к тяжелым физическим работам (категория 3) связанными с ходьбой и переносом тяжестей свыше 10 кг что соответствует энергозатратам более 250 ккалч.
Допустимые микроклиматические условия для проектируемого участка механообработки;
а) для теплого времени года:
– температура 15 26С;
относительная влажность – не более 75 (при температуре 24С и ниже);
скорость движения воздуха – не более 02 06 мс.
б) для холодного времени года:
– температура 13 19С;
относительная влажность – не более 75;
скорость движения воздуха – не более 05 мс.
Оптимальные микроклиматические условия:
а) для теплого времени года:
скорость движения воздуха – не более 04 мс;
относительная влажность – не более 40 60.
– температура 16 18С;
относительная влажность – не более 40 60;
скорость движения воздуха – не более 03 мс.
Интенсивность теплового облучения на рабочих местах не превышает 100Втм2 и облучению подвергаются не более 25 поверхностей тела человека что соответствует нормам ГОСТ 12.1.005 – 88.
На проектируемом участке используется как естественное так и искусственное освещение. Искусственное освещение по своему функциональному значению является рабочим используется в темное время суток и при недостаточном естественном освещении. Естественное освещение используется в дневное время суток осуществляется через окна и световые фонари (комбинированное освещение). Разряд зрительных работ III – работа высокой точности (наименьший размер объекта различения 03 05 мм) подразряд зрительных работ – в контраст объекта различения с фоном – средний фон – средний. Нормативное значение освещенности на рабочем месте – 750 лк.
Для совмещенного освещения КЕО = 3 (по ТКП 45.2004-153-2009). По рекомендациям ТКП 45.2004-153-2009 предлагается использовать следующие источники освещения: для общего искусственного освещения – светильники с люминесцентными лампами белого света (ЛБ); для местного освещения – лампы накаливания типа УНП.
Источниками вибрации на производственном участке являются вращающиеся неуравновешенные массы производственного оборудования. Вибрация является технологической так как возникает из–за работы стационарных машин. Для производственного участка характерно возникновение общей вибрации на рабочих местах. Это технологическая вибрация категории – 3а; ее параметры: виброскорость – до 01510-2 мс логарифмический уровень виброскорости – до 85 дБ что значительно ниже предельно допустимого уровня вибрации по СанПин 2.2.42.1.8.10-33-2002 (виброскорость до 0210-2 мс логарифмический уровень виброскорости – до 92 дБ).
Для борьбы с нежелательными вибрациями предусмотрены следующие мероприятия: фундаменты станков выполняются с акустическими разрывами заполненными пористым материалом и акустическим швом расположенными в нижней части фундамента.
Источниками шума на участке являются рабочее оборудование (приводы электродвигателей) и режущий инструмент (лезвийная обработка).
По ГОСТ 12.1.003 – 83 шум является широкополосным непостоянным и уровень звука за восьмичасовой рабочий день изменяется во времени более чем на 5 дБ и не превышать 80дБА.Снижение шума обеспечивается за счет динамической балансировки роторов электродвигателей применение звукоизоляции. Ожидаемый уровень звука на участке 75 – 80дБА.
По опасности поражения электрическим током проектируемое производственное помещение относится к классу особо опасных так как имеются токопроводящие полы и имеется возможность одновременного прикосновения человека к имеющим контакт с землей металлическим конструкциям здания с одной стороны и металлическим частям с другой.
На участке предусмотрены меры защиты от поражения электрическим током: зануление корпусов оборудования защитное отключение применение пониженного напряжения изоляция токоведущих частей оборудования.
На проектируемом участке существуют следующие опасные зоны: зона резания зона перемещения режущих частей оборудования зона расположения токопроводящих элементов. Все используемое оборудование снабжено средствами защиты работающих: предохранительными оградительными блокирующими сигнализирующими и т.д.
Оборудование на участке располагается группами с соблюдением строительных норм на расположение. Рабочее место организовано таким образом что наклон рабочего вперед не превышает 15 рабочая зона станка располагается на высоте 800 мм при необходимости используется деревянная подставка. Органы управления станком находятся не далее 200 мм от расположения рабочего места во время загрузки станка. Ширина проездов – 45 м ширина проходов – 2 м.
Органы управления станком – кнопочные пульты определенной формы и окраски. Кнопка “Пуск” и кнопки управления утоплены в панель кнопка “Стоп” выступает и имеет красный цвет. Наружные поверхности оборудования окрашены в светло – зеленый цвет внутренние поверхности оградительных устройств – в красный.
По взрывопожарной опасности (ТКП.474-2013) здание относится к категории Д (помещения в которых находятся негорючие вещества и материалы в холодном состоянии).
Производственные здания построены из искусственных и естественных каменных материалов и имеют незащищенные металлические конструкции.
По ТКП 45-2.20-142-211 - Степень огнестойкости здания – Здание построено из естественных и искусственных каменных материалов и имеет незащищенные стельные конструкции. По ТКП 45-2.20-142-211 степень огнестойкости такого здания – 2-ая.
Предел огнестойкости и класс пожарной опасности строительных конструкций
– несущие элементы здания – R120-КО
- перекрытия – REI-60-КО где
R – потеря несущей способности;
I – теплоизолирующая способность
КО – не пожароопасные строительные конструкции;
; 120 – время в минутах.
Возможными причинами пожаров на участке являются: неисправность электрооборудования самовозгорание промасленной ветоши курение в не установленных местах. Мероприятия по пожарной профилактике:
а) организационные – правильная эксплуатация оборудования правильное содержание зданий и сооружений;
б) противопожарный инструктаж работающих;
в) технические – соблюдение противопожарных норм и правил при проектировании зданий и оборудования освещения вентиляции отопления;
г) режимные – запрещение курения в не установленных местах;
д) эксплуатационные – своевременные профилактические осмотры ремонты и испытания технологического оборудования.
Промасленная ветошь собирается в отдельную металлическую тару и организованно вывозится с участка.
В цеху имеется два эвакуационных выхода которые обеспечивают безопасный выход людей наружу кратчайшим путем за минимальное время в случае пожара. Ширина эвакуационных выходов – не менее 1м ширина пожарных проездов – не менее 45 м.
В качестве первичных средств тушения пожаров используются огнетушители ОП–5 и ОУ–5 расположенные по одному на каждые 600 800 м2 ящики с песком лопаты ведра пожарные краны.
2 Очистка воздуха от масляного тумана при обработке на металлорежущих станках
Масляный туман возникает в результате того что интенсификация процессов производимых с целью уменьшения износа режущего инструмента и сохранения структуры обрабатываемых материалов нагревающихся вследствие трения в рабочей зоне до 400 -500°С потребовала эффективного охлаждения их путем обильного смачивания смазочно-охлаждающими жидкостями (СОЖ). В качестве таких жидкостей широко применяются нефтяные минеральные масла и их эмульсии и эмульсолы щелочные мыльно-щелочные и другие охлаждающие и антикоррозийные жидкости – керосин скипидар. Для повышения их смазывающих свойств в состав масел добавляют различные активирующие вещества из которых наибольшее распространение получила сера.
Эмульсии представляют собой 310%-ные водные растворы масел нафтеновых и олеиновых кислот и неорганических щелочей. Для нейтрализации свободных кислот в состав эмульсий вводят кальцинированную соду (до 03–05%).
В процессе использования эмульсии состав её существенно изменяется повышается содержание масел и солей увеличивается загрязнение металлическими примесями. При обработке легированных сталей содержащих хром и никель происходит растворение их в щелочных СОЖ.
Масляный туман конденсационного происхождения в основном состоит из капелек размером менее 4 мкм (до 90%). Средне весовой размер частиц чаще всего находится в пределах от 09 до 14 мкм. Наиболее тонкодисперсные туманы образуются при низких концентрациях паров масел с более высокой температурой кипения. Тонкодисперсные туманы масел характеризуются значительной стойкостью и высокой проникающей способностью в легкие человека.
Величины концентраций аэрозолей масла в производственных помещениях часто превышают ПИК (5 мгм3) иногда в 5–10 раз и более а в отсасываемом из рабочей зоны станка потоке воздуха они составляют 10–150 мгм3 в зависимости от вида технологического процесса обработки типа СОЖ и других условий.
В большинстве случаев твердые нерастворимые частицы содержатся в масляных туманах в свободном виде или в составе капель. Как правило их присутствие обусловлено наличием пыли в производственном воздухе и присадках к маслам а также в продуктах окисления масел иногда в растворах щелочей.
Высокая дисперсность масляных туманов и наличие в них нерастворимых примесей чрезвычайно усложняют разработку туманоуловителей с высокой степенью очистки простых и надежных в эксплуатации.
Накапливаясь во всем объеме рабочих помещений масляные туманы существенно ухудшают условия труда вызывая иногда профессиональные заболевания. Осадки масла на полу станках и инструментах способствуют возникновению травматизма осложняют уборку помещений загрязняют источники света разрушают бетонные строительные конструкции ухудшают функционирование электрических контрольно-измерительных приборов вследствие замасливания контактов. Осаждение и накопление масла на внутренних поверхностях воздуховодов увеличивает пожароопасность кроме того безвозвратно теряются значительные количества масла.
Таким образом решение проблемы устранения масляного тумана в производственных помещениях - одна из актуальных задач промышленной санитарии. Широкое внедрение в области металлообработки последних достижений в теории технике и практике туманоулавливания способствует значительному оздоровлению условий труда снижает травматизм и пожароопасность позволяет экономить масло и способствует лучшему психофизиологическому состоянию рабочих повышая производительность труда.
К настоящему времени накоплен определенный опыт решения этой сложной проблемы который указывает что для эффективного и экономичного снижения концентрации масляного тумана в атмосфере цехов необходимо осуществлять одновременно мероприятия в нескольких направлениях:
снижение генерации тумана масла путем усовершенствования и строгого контроля систем охлаждения СОЖ а также за счет применения специальных составов СОЖ с более высокой температурой кипения и с менее токсичными добавками;
устройство герметичных укрытий источников эмиссии тумана от станков или эффективных локальных отсосов по возможности мобильных и простых;
установка локальных агрегатов а в некоторых случаях централизованных систем для очистки аспирационного воздуха.
Полное удаление загрязненного воздуха из цеха в системах приточно-вытяжной вентиляции с выбросом его в атмосферу без очистки и заменой свежим – весьма невыгодное решение из-за больших энергозатрат на отопление в зимнее время. Кроме того оно не решает проблемы защиты окружающей среды на территории завода и города. Масляные аэрозоли способствуют образованию чрезвычайно устойчивого смога длительное время висящего над заводом и городом а в условиях инверсии - в приземном слое атмосферы.
Beсьмa распространены централизованные системы отсосов от групп станков с очисткой воздуха перед выбросом в атмосферу или в цех. За рубежом в качестве туманоуловителей в таких системах часто используются двухзонные электрофильтры комбинированные двух- и трехступенчатые установки или набивные волокнистые фильтры. Однако такие системы создают трудности в обслуживании плотно расположенного технологического оборудования из-за громоздкости сети воздуховодов и самих установок.
Наиболее перспективными многие авторы считают локальные агрегаты для отсоса и очистки воздуха малогабаритные и мобильные располагаемые вблизи станков или на их укрытиях обеспечивающие такую степень очистки которая позволяет возвращать воздух в цех.
Современные производственные условия предъявляют к очистным установкам определенные жесткие требования главными из которых являются: малые габариты вследствие высокой насыщенности производственных площадей основным технологическим оборудованием;
высокая эффективность очистки (от 80 до 95%) позволяющая возвращать очищенный воздух в цех с соблюдением санитарных требований;
простота обслуживания в сочетании с надежностью и безопасностью работы;
низкие капитальные и эксплуатационные затраты.
Для улавливания масляного тумана отходящего от металлорежущих станков применяют серийно изготовляемый агрегат АЭ2-12 (рис. 15.1). На первой ступени используется-инерционный эффект очистки от крупных частиц и капель масла (кольцевая камера 2) вторая ступень выполнена в виде патронов 1 заполненных многослойной тонкой сеткой а третья ступень (фильтр-шумоглушитель 3) состоит из нескольких слоев дырчатого пенополиуретана которые размещены после вентилятора 4 и служат одновременно глушителем шума. Производительность агрегата 750 м3ч.
Автоматизация проектирования и расчетов
1 Проектирование червячных фрез в среде КОМПАС-ГРАФИК
Одной из наиболее распространенных задач которые возникают в ходе технологической подготовки производства является проектирование режущего и мерного инструмента. Проектирование червячных фрез здесь занимает особенное место поскольку связано с более сложными расчетами. Для решения этой задачи предназначена прикладная библиотека САПР Фрез созданная в "Центре САПР" (г. Львов) в сотрудничестве с Львовским инструментальным заводом который выступил постановщиком задачи и первым пользователем системы.
Червячные фрезы применяют для черновой и чистовой обработки цилиндрических деталей наружного зацепления с прямыми винтовыми и шевронными зубьями. Они могут работать с осевой радиальной диагональной и тангенциальной подачей. В последнем случае конструкция фрезы снабжается режущей частью с длиной равной двум осевым шагам фрезы и с углом конуса 20 30°. По способу крепления фрезы делаются насадными и хвостовыми.
В системе САПР Фрез реализовано проектирование насадных червячных фрез не использующих тангенциальную подачу с передним углом зуба 0° (для нарезания зубчатых колес) прямобочных шлицевых валов звездочек и нестандартных деталей. Основная задача которую решает САПР Фрез — проектирование червячных фрез для:
-зубчатых колес (ГОСТ 1643-81 - фреза ГОСТ 9324-80)
-шлицевых валов (ГОСТ 1139-80 - фреза ГОСТ 8027-86)
-звездочек (ГОСТ 591-69 — фреза ГОСТ 15127-83)
-деталей с нестандартным профилем.
Процесс проектирования состоит из следующих этапов:
задание начальных данных
определение параметров фрезы по стандартам
расчет геометрии зубьев
расчет конструкторских размеров фрезы
заполнение документации
проверка профиля фрезы.
В случае проектирования нестандартных деталей (острошлицевые валы и т.п.) добавляется этап проектирования профиля фрезы по профилю детали графическим методом.
При определении профиля фрез используется метод обкатки — профиль инструмента является огибающей последовательных положений профиля изделия при качении без скольжения начальной окружности изделия по начальной прямой инструмента. С другой стороны профиль шлицевого вала образуется как огибающая последовательных положений зубьев инструмента при качении без скольжения начальной прямой инструмента по начальной окружности изделия что позволяет для проверки получить профиль изделия по имеющемуся профилю фрезы.
Профиль фрезы может быть определен аналитически графически и графоаналитически. Для стандартных профилей шлицевых валов и зубчатых колес рекомендовано использовать аналитический метод. Расчет червячных фрез заключается в определении размеров профиля фрезы в осевом сечении если фреза архимедова или в нормальном сечении если фреза конволютная.
Определение профиля червячных фрез независимо от их типа и назначения ведется в плоскости нормального сечения к виткам фрезы. При этом основные размеры профиля фрезы определяются как размеры прямобочной рейки находящейся в беззазорном зацеплении с зубьями нарезаемого колеса. Такая рейка называется исходной инструментальной рейкой. В соответствии с этим профильный угол фрезы принимается равным номинальному углу зацепления колеса причем обязательным условием является равенство основных шагов рейки фрезы и колеса. САПР Фрез полностью рассчитывает размеры профиля фрезы (рисунок 14.1) как для стандартного ряда начальных данных так и для промежуточных размеров.
Рисунок 14.1. - Расчет профиля зубьев фрезы для нарезания звездочек
Наружный диаметр тип основного червяка число заходов диаметр посадочного отверстия длина режущей части фрезы являются конструктивными элементами и выбираются по стандартам или задаются исходя из паспортных данных станка и опыта эксплуатации фрез.
Начальными данными для расчета червячных фрез для нарезания зубчатых колес являются параметры зубчатого колеса:
модуль угол профиля исходного контура колеса внешний диаметр делительный диаметр диаметр впадины.
В зависимости от параметров зубчатого колеса так же выбираются начальные параметры фрезы. В случае проектирования фрезы под шевингование выбирается модификация профиля. Червячные фрезы под шевингование отличаются от червячных фрез общего назначения модификацией профиля. Целью модификации профиля фрез является улучшение условий шевингования которое получается при определенном распределении припуска под шевер (рисунок 14.2).
Все данные фрезы задаются в зависимости от параметров шлицевого вала. Для стандартных серий вала величины выбираются из ряда а для нестандартного — задаются отдельно. Классы точности А и В используются для чистовых фрез С — для черновых фрез. При проектировании черновых фрез толщина зуба внешний диаметр и внутренний диаметр задаются с учетом величины припуска на последующую обработку.
Следующим этапом является выбор взаимозависимых величин — диаметра начальной окружности и шага профиля. Система дает возможность задать диаметр и рассчитать шаг профиля или задать шаг и рассчитать диаметр. Профиль фрезы представляет собой кривую — огибающую последовательных положений профиля валика при качении начальной окружности валика по начальной прямой фрезы. Практически эта кривая заменяется одной или несколькими дугами окружностей. Отклонения от теоретической кривой рассчитываются по методу Семенченко или более точному методу (рисунок 14.3).
Рисунок 14.2 - Модификация профиля под шевингование
Рисунок 14.3 - Контроль отклонения от теоретического профиля фрезы
Система рассчитывает до восьми контрольных толщин профиля фрезы. На вершине начальной прямой и фланке толщина рассчитывается автоматически. Дополнительно рассчитывается контрольная толщина шлица на высоте усика (типа А шлица) и на высоте точки сопряжения двух дуг. Остальные контрольные точки профиля рассчитываются по желанию пользователя при соответствующем задании высоты от вершины или от начальной линии.
После расчета выводятся размеры профиля с возможностью изменения параметров: ширины усика глубины канавки и угла фланка (рисунок 14.4). При редактировании значений в окнах на всех этапах проектирования зависимые параметры пересчитываются автоматически.
Рисунок 14.4 - Параметры профиля
Система рассчитывает размеры профиля фрезы (рисунок 14.1). В случае задания нестандартных начальных данных (не из ГОСТ 591-69) требуется дополнительная проверка профиля графическим методом.
Графический метод реализован с использованием модуля К3 для САПР Фрез. Его рекомендовано применять при получении профиля для нестандартных деталей (острошлицевые валы зубчатые колеса с модификацией и др.) или нестандартных профилей шлицевых валов (с неравномерным припуском под шлифование) а также для проверки аналитического расчета. Он основан на эмуляции процесса нарезания путем задания законов движения деталей и проведения булевых операций (рисунок 14.5). Полученный в результате профиль рейки (или детали) используется для изготовления инструмента второго порядка и шаблонов.
При расчете конструкции фрезы конструктору дается возможность задать нестандартные размеры внешнего диаметра и посадочного отверстия (иначе они выбираются системой автоматически из стандартных рядов). Внешний диаметр выбирается из ряда или вручную посадочное отверстие вводится только из предложенного ряда. Параметры геометрии зубьев взаимосвязаны. Например при изменении коэффициента затылования одновременно пересчитывается коэффициент дополнительного затылования и глубина канавки (рисунок 14.6).
Рисунок 14.5 - Эмуляция процесса нарезания в К3 для САПР Фрез
Также анализируется пропорция высоты и толщины зуба. Величина пропорции задается в настройках системы. В случае невыполнения условия допустимости толщины тела фрезы в опасном сечении система предложит три варианта решения задачи: стружечные канавки выполнить прямыми и шпоночный паз расположить под зубом уменьшить посадочное отверстие или поменять заданные параметры. Величина соотношения опасного сечения к посадочному диаметру задается в настройках системы.
Полученные результаты расчетов выводятся в текстовый файл который можно просмотреть с помощью встроенного текстового редактора. Чертеж спроектированной фрезы (рисунок 14.7) автоматически формируется в системе КОМПАС-ГРАФИК. В случае необходимости его можно доработать и отредактировать. Вывод графической информации организован в виде шаблонов и может быть изменен по желанию пользователя.
Рисунок 14.6 - Редактирование конструкции фрезы
Рисунок 14.7 Пример чертежа спроектированной фрезы
Экономическая часть проекта
1 Расчет величины инвестиций
В состав инвестиций в долгосрочные активы следует включить капитальные вложения на формирование объектов основных средств предприятия а именно здания (производственные площади) предназначенные для размещения оборудования участка или поточной линии; рабочие машины и оборудование; транспортные средства; инструмент и технологическую оснастку общего назначения; производственный инвентарь и принадлежности.
В общем случае величина инвестиций (капитальных вложений) в основной капитал (Кос) включает следующие составляющие:
где - капиталовложения в технологическое оборудование;- капиталовложения в здания;- капиталовложения в транспортные средства;- капиталовложения в инструмент и технологическую оснастку относимые в состав основных средств;- капиталовложения в производственный инвентарь.
Коэффициент занятости участка можно принять равным отношению среднего фактического коэффициента загрузки оборудования участка (kср.уч) к нормативному коэффициенту загрузки по установленному типу производства (kнз)т.е.
Расчет фактического среднего коэффициента загрузки оборудования производится в технологической части проекта. Среднее значение нормативного коэффициента загрузки оборудования (kнз ) по участку при двухсменной работе принимают: для мелкосерийного производства – 08-09 и выше; для серийного – не ниже 075-085; для массово-поточного и крупносерийного – не ниже 065 – 075.
Определение величины капитальных вложений в технологическое оборудование:
где - количество оборудования на каждой операции; Ц – цена единицы оборудования соответствующего наименования скорректированная по коэффициенту загрузки; - соответственно коэффициенты учитывающие транспортные расходы затраты на монтаж и подготовку фундамента. ( оборудования устанавливается на бетонные полы без сооружения специального фундамента)
Определение величины капитальных вложений в здания:
где - величина удельной площади на единицу соответствующего оборудования ; m - цена одного метра квадратного площади млн. руб.;- коэффициент учитывающий дополнительную площадь в зависимости от площади занимаемой станком.
Определение величины капитальных вложений в инструмент и технологическую оснастку:
где - коэффициент учитывающий затраты на инструмент и оснастку от стоимости оборудования .
Определение величины капитальных вложений в транспортные средства
где - коэффициент учитывающий величину капитальных вложений в механический транспорт от стоимости оборудования
Определение величины капитальных вложений в производственный инвентарь:
где - коэффициент учитывающий величину капитальных вложений в производственный инвентарь от стоимости оборудования .
Определение общей величины капитальных вложений в основной капитал
Полученные данные сводим в таблицу 15.1
Таблица 15.1 – Величина инвестиционных вложений млн. руб.
Категория инвестиций
Капитальные вложения в здание
Капитальные вложения в оборудование
Капитальные вложения в транспортные средства
Капитальные вложения в технологическую оснастку
Капитальные вложения в производственный инвентарь
НДС при приобретении основных средств
Инвестиции в основные средства с учетом НДС
Вложения в нормируемые оборотные средства
Итого полные инвестиционные вложения
2 Расчет текущих затрат на объем выпуска продукции (расчет себестоимости продукции)
Себестоимость всего объема выпущенной продукции представляет собой сумму затрат предприятия на ее производство и реализацию. Все затраты приводятся к единому временному периоду обычно одному году. Одновременно определяется полная себестоимость единицы конкретного наименования продукции.
2.1. Расчет затрат по статьям «Сырье и материалы» «Возвратные отходы»
В статью «Сырье и материалы» включаются затраты на сырье и основные материалы (прокат поковки литые заготовки из чугуна или стали). Затраты на основные материалы рассчитываются на деталь прямым путем исходя из утвержденных норм расхода на единицу продукции и цены этих материалов.
где - масса заготовки т;
- цена одной тонны заготовок с учетом метода их получения ;
- коэффициент учитывающий транспортно-заготовительные расходы при приобретении материалов ;
- цена одной тонны отходов млн. руб.
При приобретении сырья и материалов предприятие учитывает входной НДС по каждому его виду. Величина входного НДС уплачиваемая при покупке материалов (как основных так и вспомогательных отражаемых в косвенных статьях себестоимости) рассчитывается по формуле:
где hндс – ставка налога на добавленную стоимость %
2.2. Расчет затрат по статье «Покупные комплектующие изделия полуфабрикаты и услуги производственного характера»
При выполнении проекта эта статья рассчитывается в том случае если в качестве заготовки применяется отливка или поковка приобретаемые со стороны. В данном случае расчет этой статьи не производится.
2.3 Расчет затрат по статье «Топливо и энергия на технологические цели»
В эту калькуляционную статью себестоимости продукции включаются затраты на топливо и энергию которые непосредственно расходуются в процессе без преобразования в механическую энергию или в другие виды энергии. Расчет производится в энергетической части проекта.
2.4 Расчет затрат по статье «Основная заработная плата производственных рабочих»
В состав основной заработной платы входит оплата по сдельным расценкам а также оплата труда по тарифным ставкам рабочих- повременщиков занятых непосредственно выполнением производственного процесса и отдельных технологических операций. В статью включаются доплаты и выплаты за неблагоприятные условия труда а также премии за производственные результаты.
Основная заработная плата производственных рабочих- сдельщиков определяется на основе расценки по формуле:
Рд – коэффициент учитывающий премии и доплаты;
Рi - расценка на i-ю операцию руб.
Расценка на i-ю операцию определяется на основе трудоемкости и часовой тарифной ставки принятой для тарификации работы на данной операции по формуле:
kмн kсл – коэффициент учитывающий сложность работы ( для станочников принять равным 11).
2.5 Расчет затрат по статье «Дополнительная заработная плата производственных рабочих»
Данная статья учитывает выплаты предусмотренные трудовым законодательством за неотработанное на производстве время; сюда водят выплаты за выполнение государственных обязанностей оплата отпусков доплата подросткам и т. п. Дополнительная заработная плата определяется в процентах от основной заработной платы по формуле:
где НД – норматив дополнительной заработной платы по отношению к основной.
Суммарный фонд заработной платы (ФЗП) производственных рабочих на год:
По результатам расчетов составляем ведомость заработной платы производственных рабочих представленную в таблицах 15.2.1 и 15.2.2
Таблица 15.2.1 Результаты расчета фонда заработной платы основных производственных рабочих (базовый вариант)
Фонд основной заработной платы
Дополнительная заработная плата
Годовой фонд заработной платы тыс. руб.
Премии и доплаты руб.дет.
Годовой фонд основной заработной платы
Таблица 15.2.2 Результаты расчета фонда заработной платы основных производственных рабочих (проектный вариант)
2.6 Расчет численности основных производственных рабочих
Для участков серийного производства число рабочих определяется исходя из трудоемкости работ по изготовлению определенного наименования детали:
где N – программа выпуска деталей шт.;
Kо – количество технологических операций;
Фн – номинальный годовой фонд времени работы одного рабочего (без учета потери рабочего времени в среднем можно принять 2040 часов);
kвн – средний коэффициент выполнения норм выработки (по данным предприятия или принять в диапазоне от 105 до 115).
Полученное количество рабочих соответствует рабочим ставкам. Фактическое явочное количество рабочих основного производства принимается в соответствии с расстановкой их по рабочим местам на планировке участка.
Списочное количество основных рабочих определится как:
где ПП%- планируемые потери рабочего времени (отпуск служебные обязанности и т.п. принять в размере 10%).
Среднемесячная заработная плата основных производственных рабочих рассчитывается по формуле:
где - явочная численность основных производственных рабочих чел.
ФЗП – годовой фонд заработной платы производственных рабочих млн. руб.
2.7 Расчет затрат по статье «Отчисления в бюджет и внебюджетные фонды от средств на оплату труда»
Отчисления от средств на оплату труда в бюджет и внебюджетные фонды определяются по формуле:
где – ставка отчислений на государственное страхование в фонд социальной защиты населения ; - ставка отчислений на обязательное страхование от несчастных случаев .
Сумму расходов связанных с оплатой труда производственных рабочих можно определить по формуле:
РЗПосн = ФЗПосн + Офзп млн.руб.год;
РЗПосн =6576+2242=8818 млн.руб.год;
РЗПосн =6004+2047=8051 млн.руб.год;
2.8 Расчет затрат по статье «Общепроизводственные расходы»
Эта статья затрат (Собщепр) включает: расходы по содержанию и эксплуатации оборудования (РСЭО); расходы по организации обслуживанию и управлению производством.
2.8.1Расходы по содержанию и эксплуатации оборудования
Статья «Расходы по содержанию и эксплуатации оборудования» является комплексной и включает следующие виды расходов: амортизация оборудования транспортных средств и ценного инструмента; эксплуатация оборудования (кроме расходов на ремонт); ремонт оборудования и транспортных средств; внутризаводское перемещение груза; погашение стоимости инструментов и приспособлений общего назначения; прочие расходы.
Амортизация оборудования подъемно-транспортных средств и технологической оснастки. Величина годовых амортизационных отчислений определяется на основе годовых норм амортизации и первоначальной стоимости соответствующих элементов основных средств по формуле:
где Наобтртоинв – годовая норма амортизации соответствующего элемента основных средств;
КМиО Ктр Кто Кинв – капитальные вложения соответственно: машин и оборудования технологической оснастки подъемно-транспортных средств и инвентаря млн. руб.;
В статью «Эксплуатация оборудования» (кроме расходов на ремонт) включаются:
заработная плата (в составе основной дополнительной зарплаты и отчислений в бюджетные и внебюджетные фонды от средств на оплату труда) рабочих занятых обслуживанием машин и оборудования (слесарей наладчиков электромонтеров) и других категорий работающих непосредственно не занятых производством продукции);
Численность вспомогательных рабочих которые обслуживают трудовые процессы выполняемые основными рабочими (наладчики ремонтники складские рабочие и пр.) рассчитывается на основе норм обслуживания или укрупнено в процентах от численности основных рабочих: серийное производство - 40-50%.
где Чосн- численность основных производственных рабочих чел.
Нвсп – численность вспомогательных рабочих % от численности основных рабочих.
Для вспомогательных рабочих годовой фонд заработной платы с учетом дополнительной заработной платы рассчитывается по формуле:
где Чвсп ЧТС Рд – коэффициент учитывающий премии и доплаты к тарифному фонду вспомогательных рабочих (Рд=12-14); Фрабэф – годовой эффективный фонд времени работы одного рабочего(среднее значение принять равным 1860 ч); - коэффициент занятости оборудования учитывается при серийном типе производства; - норматив дополнительной заработной платы по отношению к основной.
Годовые расходы связанные с заработной платой вспомогательных рабочих с отчислениями в бюджетные и внебюджетные фонды:
ФЗПвсп – годовой фонд заработной платы вспомогательных рабочих;
Полученные результаты заносим в таблицу 15.2.3.
Стоимость материалов расходуемых для обеспечения функционирования оборудования принимается по действующим на предприятии нормам расхода на один производственный станок при этом отдельно должна учитываться сумма входного НДС. Укрупнено эти расходы можно принять в размере 3 % от первоначальной стоимости оборудования.
Затраты на электрическую энергию сжатый воздух воду тепловую энергию потребляемую в процессе работы оборудования (принимаются на основании их потребности рассчитанной в энергетической части проекта и стоимости отдельных видов энергии на единицу потребления).
Текущий ремонт оборудования и транспортных средств. Укрупнено расходы на текущий ремонт оборудования и транспортных средств могут быть приняты в размере 3-5 % от стоимости оборудования и транспортных средств.
Внутризаводское перемещение грузов. При укрупненном расчете эту статья затрат может быть принята до 30% от стоимости транспорта.
Погашение стоимости инструментов и приспособления общего назначения. Укрупнено могут быть приняты в размере 02- 05 % от первоначальной стоимости оборудования.
Прочие расходы. Учитывают затраты не вошедшие в вышеперечисленные статьи и составляет 4% от всех предыдущих статей затрат.
Всего затраты на содержание и эксплуатацию оборудования составят:
2.8.2 Расходы по организации обслуживанию и управлению производством (общецеховые расходы)
Включают следующие группы затрат:
содержание аппарата управления - включает оплату труда служащих (руководителей и специалистов) в т.ч. соответствующие отчисления. Служащие цехового уровня и на участках (руководители - мастера и бригадиры; специалисты – инженеры техники распределители работ) рассчитываются на основании штатного расписания или укрупнено в размере 10% от численности основных и вспомогательных рабочих.
Годовой фонд заработной платы служащих можно рассчитать укрупнено исходя из численности среднемесячных окладов среднего числа месяцев работы с учетом дополнительной заработной платы и отчислений от фонда заработной платы по формуле:
где - среднемесячная заработная плата служащих цехового уровня (принимается в среднем для данной категории работников по рассматриваемому предприятию с учетом дополнительной заработной платы) млн. руб.; Ч сл - численность служащих (принимается в процентах от численности основных и вспомогательных рабочих) чел.; Мсл – среднее число месяцев работы служащих принять 114 месяцев; Ндоп.сл. - норматив дополнительной заработной платы служащих (принять равным 10-15%).
Затраты на содержание аппарата управления цеха с учетом отчислений в бюджетные и внебюджетные фонды составит:
Амортизация цеховых (производственных и административных) зданий сооружений инвентаря:
где – норма амортизации здания ;
Кзд – первоначальная стоимость зданий млн. руб.;
Содержание цеховых (производственных и административных) зданий. Содержание цеховых зданий и сооружений определяется на основе норм расхода денежных средств на 1 м2 площади здания учитывающих затраты на освещение отопление и уборку по существующим нормативам. Укрупнено расходы по данной статье можно принять 15% от первоначальной стоимости производственной площади.
Расходы по ремонту цеховых зданий определяются укрупнено в процентах от их стоимости.
Расходы на текущий ремонт цеховых зданий сооружений и инвентаря. Определяются укрупнено в процентном соотношении: 07 - 25 % от стоимости зданий и инвентаря.
Расходы на мероприятия по обеспечению нормальных условий труда техники безопасности (охрана труда) принимаются в соответствии с нормативами установленными на одного работника. Расходы на мероприятия по обеспечению нормальных условий труда техники безопасности укрупнено составляют 015 у.е. на одного работника в год.
Расходы на испытания опыты исследования рационализацию и изобретательство. Укрупнено составляют 60 у.е. на одного рабочего в год.
где – Нрац– норматив расходов на испытания опыты исследования рационализацию и изобретательство (укрупнено принять в размере 018 млн.руб. год на одного работающего).
Прочие расходы. Прочие расходы составляют 3% от суммы предыдущих статей общецеховых расходов.
Всего общецеховые расходы составят:
Результаты расчета величины затрат на оплату труда служащих свести в таблицу 15.2.3.
Таблица 15.2.3 - Расходы на заработную плату работающих с отчислениями в бюджет и внебюджетные фонды
Расходы на оплату труда основных рабочих всего:
1. Основная заработная плата млн. руб.
2. Дополнительная заработная плата млн. руб.
3. Отчисления от ФЗП
Расходы на оплату труда вспомогательных рабочих в том числе:
Расходы на оплату труда служащих в том числе
1. Отчисления от ФЭП
Всего расходов на оплату труда
2.9Расчет затрат по статье «Общехозяйственные расходы»
Эти расходы включают (в данном проекте) следующие группы затрат: оплата труда руководителей и специалистов аппарата управления предприятием; административные расходы (служебные командировки проездные билеты для работников управления с разъездным характером работы и пр.); расходы по содержанию заводского транспорта.
Величина общехозяйственных расходов (Рох) может быть рассчитана укрупнено по следующей формуле:
гдеСз.осн - фонд основной заработной платы производственных рабочих млн. руб.; Нох- норматив общехозяйственных (заводских) расходов к трудовым затратам(Нох=80..180).
По результатам расчета косвенных расходов заполняем табл.15.2.4
Таблица 15.2.4 - Результаты расчетов величины косвенных статей расходов млн. руб.
Величина затрат по вариантам
Общепроизводственные расходы всего:
1. Амортизация оборудования млн. руб.
2. Эксплуатация оборудования млн. руб.
3. Ремонт оборудования млн. руб.
4.Внутризаводское перемещение грузов млн. руб.
5 Погашение стоимости инструмента млн. руб.
6. Оплата труда служащих цехового уровня
включая отчисления млн. руб.
7 Амортизация цеховых зданий и инвентаря млн. руб.
8. Содержание цеховых зданий млн. руб.
9. Ремонт цеховых зданий млн. руб.
10. Охрана труда млн. руб.
11. Расходы на испытания млн. руб.
12. Прочие расходы млн. руб.
Общехозяйственные расходы всего
Расходы на реализацию
Всего накладных расходов
2.10 Расчет затрат по статье «Расходы на реализацию»
Расходы на реализацию включают расходы на рекламу участие в выставках маркетинговые исследования и проч. В условиях проекта можно рассчитать укрупнено как 15 % от общей производственной себестоимости продукции т.е.:
где Спроиз- производственная себестоимость годового выпуска продукции млн. руб.;
Нреал-норматив расходов на реализацию от производственной себестоимости%.
2.11 Платежи отчисления и налоги в себестоимости продукции (кроме отчислений от средств на оплату труда)
Данные расходы включают платежи на землю (земельный налог) отчисления в специальные фонды (инновационный фонд) экологический налог и пр. В силу сложности прямого расчета этих налогов укрупнено эти затраты можно принять в размере 2- 4 % от производственной себестоимости:
где Нпр.отч. - принятый укрупненный норматив отчислений и платежей от производственной себестоимости (2-4%).
Результаты расчета себестоимости продукции годового выпуска приводятся в таблице 15.2.5.
Таблица 15.2.5 - Себестоимость годового выпуска продукции
Значения по вариантам млн. руб.
Сырье и материалы за вычетом возвратных отходов
Основная заработная плата производственных рабочих
Дополнительная заработная плата производственных рабочих
Отчисления в бюджетные и внебюджетные фонды
Общепроизводственные расходы (без амортизации)
Амортизация основных средств
Итого: цеховая себестоимость
Общехозяйственные расходы
Итого: производственная себестоимость
Расходы на реализацию продукции
Платежи отчисления и налоги в себестоимости продукции (кроме отчислений от ФЗП) (Рпр.отч.)
Итого: полная себестоимость (Сп )
Себестоимость единицы продукции определяется :
где Сед.пр.– полная себестоимость единицы реализованной продукции руб.; Сп– полная себестоимость продукции млн. руб.; N - годовой объем выпуска продукции шт.
3 Расчет основных технико-экономических показателей сравниваемых вариантов
3.1 Определение отпускной цены
При выполнении дипломного проекта для расчета рекомендуется использовать метод "издержки плюс прибыль" который означает что цена детали рассчитывается путем прибавления к полной себестоимости единицы продукции рассчитанной величины прибыли.
Если деталь изготавливаемая на участке рассматривается как конечная продукция реализуемая потребителям то к цене прибавляется величина косвенных налогов.
где Сед. пр.– полная себестоимость единицы продукции руб.; Ппл. – планируемая прибыль предприятия на единицу продукции руб.; Нкосв – сумма косвенных налогов и отчислений в цене товара.
Планируемая прибыль на единицу продукции рассчитывается исходя из норматива рентабельности прибыли на вложенный капитал (Rе).
где Rе - норматив рентабельности единицы продукции %.
Ставки налоговых выплат по проекту и исходные данные для дальнейшего расчета целесообразно свести в таблицу 15.3.1.
Таблица 15.3.1 - Ставки налогов и налоговых выплат исходные данные для расчета отпускной цены и прибыли предприятия
Норматив рентабельности единицы продукции
1. в цену (косвенные (оборотные))
- налог на добавленную стоимость (НДС)
Налоги и сборы выплачиваемые из прибыли (прямые) в том числе:
Объем производства в натуральном выражении шт.
Величина полных инвестиций млн. руб. в том числе:
1. в основные средства с учетом НДС млн.руб.
2. в оборотные средства млн.руб.
Себестоимость единицы продукции руб.
Себестоимость произведенной продукции млн.руб.
Расчет отпускной цены продукции проводится по базовому варианту технологического процесса. Порядок расчета цены сводим в таблицу 15.4.2.
Таблица 15.4.2 - Расчет отпускной цены по базовому варианту технологического процесса
Цена предприятия без НДС
Отпускная (свободная) цена предприятия с НДС
Цотп.=ЦпрбезНДС+ НДС
Цена продукции проектного варианта устанавливается на уровне цены базового варианта.
3.2 Определение прибыли предприятия
Порядок расчета прибыли от реализации и чистой прибыли предприятия после уплаты налоговых платежей сводим в таблицу 15.4.3.
Таблица 15.3.3 - Расчет прибыли от реализации и чистой прибыли предприятия
Выручка от реализации в отпускных ценах
Выручка предприятия без косвенных налоговых платежей
Прибыль от реализации
Преал = ВРпред - Сп (б)пр
3Расчет технико-экономических показателей сравниваемых проектов
Расчеты проводятся на основании результатов предыдущих расчетов по соответственно базовому и проектному вариантам.
Выработка продукции - является прямым показателем производительности труда. Выработка на одного рабочего рассчитывается по формуле:
где ВРпред – выручка предприятия от реализации продукции без косвенных налогов млн. руб.
Чосн– численность основных рабочих чел.
Технологическая трудоемкость единицы продукции в чел.-часшт.:
где Фэф- эффективный годовой фонд времени работы одного рабочего 1860 часов.
Фондоотдача основных средств характеризует производство продукции в стоимостном выражении на единицу стоимости основных средств в единицу времени (один год). Она рассчитывается по формуле:
Ф ср.г.осн – среднегодовая стоимость основных средств (принять равной величине инвестиций в основные средства без НДС) млн. руб.
Фондовооруженность труда рассчитывается как отношение среднегодовой стоимости основных средств к численности промышленно-производственного персонала:
Фво= Фср.г.осн.ЧППП млн.рубчел;
где Чппп- численность промышленно-производственного перснала (Чосн+Чвсп+Чсл.цех).
Фво=20246115708=12889 млн.рубчел;
Фво=18337915444=12974 млн.рубчел;
Фондоемкость продукции рассчитывается как:
Материалоемкость продукции рассчитывается как:
где См – затраты на сырье и материалы за вычетом возвратных отходов млн. руб.
Коэффициент использования материала рассчитывается как:
где mд – масса детали кг;
mз – масса заготовки кг.
Рентабельность затрат характеризует долю чистой прибыли предприятия получаемой на единицу затрат на производство продукции и рассчитывается как:
где Пч –чистая прибыль предприятия млн.руб.;
Сп- полная себестоимость годового объема продукции млн.руб.
Рентабельность производства по чистой прибыли характеризует долю чистой прибыли предприятия получаемую на единицу инвестиций при соответственно базовом и проектном варианте инвестирования в производство продукции также в статической системе:
где I – величина инвестиционных вложений в основные средства и нормируемые оборотные средства млн. руб.
Рентабельность продукции определяется по формуле:
гдеПреал– прибыль от реализации продукции млн.руб.;
Сп- полная себестоимость годового выпуска продукции руб.
Период окупаемости инвестиций по чистому доходу представляет временной отрезок использования экономического объекта в течение которого инвестиции в производство возвращаются потоком чистой прибыли и суммой годовых амортизационных отчислений основных средств в статической системе рассчитывается по формуле:
где I – сумма полных инвестиционных вложений с НДС млн. руб.;
Агод – величина годовых амортизационных отчислений по элементам амортизируемых основных средств млн. руб.;
Пч – чистая прибыль млн. руб.;
Годовой экономический эффект по проекту (с учетом чистой прибыли) рассчитывается как:
Эг=240627млн.руб.год
Рассчитанные основные технико-экономические показатели по базовому и проектному вариантам представляют в виде в таблицы 15.4.
Таблица 15.4 - Основные технико-экономические показатели проекта
Годовой объем выпуска продукции:
1. В натуральном выражении
2.В стоимостном выражении
Себестоимость единицы продукции
Полная себестоимость годового объема произведенной продукции
Расчетная численность производственных рабочих
Выработка на одного производственного рабочего
Трудоемкость изготовления продукции
Фонд заработной платы рабочих
Среднемесячная заработная плата одного рабочего
Прибыль от реализации продукции
Рентабельность продукции
Амортизационные отчисления
Коэффициент использования материалов
Прибыль остающаяся в распоряжении предприятия
Период окупаемости инвестиций
На основании таблицы технико-экономических показателей делаем вывод что при проектном технологическом процессе трудоемкость снижается на 79% как следствие производительность возрастает на 79%; на 158% увеличивается рентабельность продукции наряду со снижением себестоимости произведенной продукции на 138% уменьшением периода окупаемости инвестиций и стоимости основных и оборотных средств. Таким образом проектный вариант экономически эффективнее базового.
Стандартизация в проекте
Важную роль в ускорении научно-технического прогресса повышения производительности общественного труда и эффективности использования материальных ценностей играет стандартизация и унификация продукции.
В данном проекте нашли широкое применение стандарты и другие нормативные документы. Они использовались и служили основой на всех этапах проектирования. Наибольшее применение нашли основополагающие стандарты ЕСКД ЕСТД ССБТ которые использовались при разработке графической части проекта и технологической документации применяемые стандарты приведены в табл.16.1.
Таблица 16.1 - Стандарты используемые в дипломном проекте
Общие требования к текстовым документам
Сокращение русских слов
Общие правила нанесения размеров и предельных отклонений
Общие требования к выполнению конструкторской документации.
Технологичность конструкции. Виды и показатели технологичности
Разработка технологических процессов. Основные документы
Поковки стальные штампованные. Допуски припуски и кузнечные напуски.
Зенкеры цельные из быстрорежущей стали
Окончание таблицы 16.1
ССБТ. Шум. Общие требования безопасности.
ССБТ. Вибрация. Общие требования безопасности.
Технологичность конструкции. Виды и показатели технологичности.
Разработка технологических процессов. Основные документы.
Естественное и искусственное освещение.
Нормы расстояний между оборудованием. Ширина проездов проходов при проектировании механосборочных цехов.
В данном дипломном проекте был разработан технологический процесс механической обработки детали «Шестерня промежуточная со втулкой 260-1006240СБ» который обеспечил снижение себестоимости энергопотребления и трудоемкости в сравнении с базовым вариантом. При разработке проектного варианта техпроцесса основное внимание акцентировалось на этих операциях. Себестоимость операций и являлась основным критерием выбора изменений в технологическом процессе.
В качестве изменений техпроцесса было предложено замена оборудования на более совершенное. Таким образом: 1А730 и 1Н713 заменили на DVH 450 duo. В качестве усовершенствования техпроцесса получения заготовок был предложен метод получения заготовок в закрытых штампах что позволяет повысить производительность уменьшить припуски снизить массу заготовки и соответственно поднять КИМ по сравнению с методом получения заготовок в открытых штампах.
Для разработки дипломного проекта использовалось программное обеспечение:
Компас v13 – графическая часть проекта.
Проектирование технологических процессов механической обработки в машиностроении (под ред. В.В. Бабука). Мн.:Выш.шк.1987.
Справочник технолога-машиностроителя под ред. А.Г.Косиловой. М.: Машиностроение 1986. Т. 12.
Режимы резания металлов. Справочник под ред. Ю.В.Барановского. М.: Машиностроение 1972.
Дипломное проектирование по технологии машиностроения (под ред. В.В.Бабука). Мн.: Выш.шк.1979.
М.С.Эдуардов. Штамповка в закрытых штампах. Л.: Машиностроение 1971.
Охрана окружающей среды под ред. С.В.Белова. М.: В.шк.1991.
Г.М. Мельников В.П. Вороненко. Проектирование механосборочных цехов. М.: Машиностроение 1990.
А.Ф. Горбащевич В.А. Шкред. Курсовое проектирование по технологии машиностроения. Мн.: Выш. шк.1983.
065.docx
Шестерня промежуточная со втулкой
Наименование операции
Оборудование устройство ЧПУ
Обозначение программы
Моечная машина 38532015052
Операционная карта механической обработки
060.docx
Шестерня промежуточная со втулкой
Наименование операции
Оборудование устройство ЧПУ
Обозначение программы
Клеймить буквы «Р» «К» «Т»
приспособление для клеймения 7858-5313; клеймо «Р» 7858-5316; клеймо «К» 7858-5314; клеймо «Т» 7858-5315; молоток
Операционная карта механической обработки
ГОСТ 3.1105-84 Форма 7
070.docx
Шестерня промежуточная со втулкой
Наименование операции
Оборудование устройство ЧПУ
Обозначение программы
Проверить визуально детали по шероховатости обработанных поверхностейотсутствию забоинзаусенцев и других дефектов
При необходимости устранить исправимые дефекты. Проверить параметры зубчатого венца-100%(см. эских на оп. 035)
Пневмомашина ИП 2014; круг шлифовальный 150х6х32 14А25 НС1-С2 40мс А 2кл. ГОСТ 2424-87.
Операционная карта механической обработки
107.docx
Шестерня промежуточная со втулкой
Наименование операции
Вертикально-сверлильная
Оборудование устройство ЧПУ
Обозначение программы
%-Виттол-100 ТУ РБ 100005975.006-2004
Установить и закрепить деталь
Приспособление 7342-5005; раскатка 1410-9005; оправка 6104-5021; кожух 431-149-01.
Операционная карта механической обработки
ГОСТ 3.1105-84 Форма 7
120.docx
Шестерня промежуточная со втулкой
Наименование операции
Оборудование устройство ЧПУ
Обозначение программы
Проверить осмотром отсутствие забоинзаусенцев и других дефектов шероховатость обработанных поверхностей
Наличие фасок – 100%.
Образцы шероховатости ГОСТ 9378-87
Проверить размеры – 100%
Нутромер 18-50 ГОСТ 9244-89; концевые меры 3-Н1 ГОСТ 9038-87; концевые меры 3-Н5 ГОСТ 9038-87.
Проверить радиальное биение – 3%
Биениемер Б-10М; оправка контрольная; индикатор 1МИГ ГОСТ 9696-87.
Контрольный прибор МЦ-100Б; центра контрольные ПБ-500; штатив Ш-IIН-8 ГОСТ 10197.
Проверить угол наклона зуба – 3%
Эвольвентомерная и шагомерная машина мод. PFSU-600.
Операционная карта механической обработки
Титульник.docx
Шестерная промежуточная со втулкой
Министерство образования Республики Беларусь
Руководитель Ярмак Ю.Ю.
Консультант Ярмак Ю.Ю.
ТЕХНОЛОГИЧЕСКИЙ ПРОЦЕСС
МЕХАНИЧЕСКОЙ ОБРАБОТКИ
ДЕТАЛИ ВАЛ 822-2308065
010.docx
Шестерня промежуточная со втулкой
Наименование операции
Вертикально-протяжная
Оборудование устройство ЧПУ
Обозначение программы
%-Виттол-100 ТУ РБ 100005975.006-2004
Установить и закрепить деталь
Протянуть отверстие выдерживая размер 1
Патрон вспомогательный 6170-5064; опора 7620-5044; патрон для протяжки 6170-5035; протяжка 2400-5141.
Операционная карта механической обработки
ГОСТ 3.1105-84 Форма 7
045.docx
Шестерня промежуточная со втулкой
Наименование операции
Оборудование устройство ЧПУ
Обозначение программы
Проверить детали на отсутствие забоин заусенцев. При необходимости исправить дефекты зачистить заусенцы.
Пневмомашина ИП 2014;круг шлифовальный150х4х32 14А25Н-40Н СТ1-СТ2 40мс А 2кл.ГОСТ 2424-87;напильник 2820-0023
Операционная карта механической обработки
086.docx
Шестерня промежуточная со втулкой
Наименование операции
Оборудование устройство ЧПУ
Обозначение программы
%-Виттол-100 ТУ РБ 100005975.006-2004
Точить фаску согласно эскизу с двух сторон с переустановкой
±03х450 4 1 1 05 240 50
Операционная карта механической обработки
ГОСТ 3.1105-84 Форма 7
040.docx
Шестерня промежуточная со втулкой
Наименование операции
Оборудование устройство ЧПУ
Обозначение программы
%-Виттол-100 ТУ РБ 100005975.006-2004
Установить и закрепить деталь
Притупить фаски по контуру торцев зубьев с двух сторон
Круг отрезной 100х3.2х20 15А 40-Н 41В 80 мс 2кл. ГОСТ 21963-89
Операционная карта механической обработки
ГОСТ 3.1105-84 Форма 7
020.docx
Шестерня промежуточная со втулкой
Наименование операции
Оборудование устройство ЧПУ
Обозначение программы
%-Виттол-100 ТУ РБ 100005975.006-2004
Установить и закрепить деталь
Планшайба 7067-4012; поводок 7067-4004; Морзе центр 7032-0035 ГОСТ 13214.
Точить деталь выдерживая размеры 1234
Резцедержатель 6720-5121; резцедержатель 6720-5100; резец 2100-4082(2);резец 2102-0187; планшайба 03113-120408.
Операционная карта механической обработки
ГОСТ 3.1105-84 Форма 7
110.docx
Шестерня промежуточная со втулкой
Наименование операции
Оборудование устройство ЧПУ
Обозначение программы
Отобрать детали по шероховатости поверхностей отсутствию забоин заусенцев. При необходимости устранить исправимые
Дефекты притупить острые кромки в отверстии и по наружному диаметру
Пневмомашина ИП 2014; круг шлифовальный 150х6х32 14А25 НС1-С2 40мс А 2кл. ГОСТ 2424-87 напильник 2820-0023
Проверить наличие и исправность сверления и клеймения меток – 100%
Приспособление контрольное 8539-5169
Проверить параметры зубчатого венца – 100%
Контрольный прибор МЦ-400Б
Проверить размеры – 100%
Нутромер 18..50 ГОСТ 9244-87; концевые меры 3-Н5 ГОСТ 9038-89; набор к концевым мерам ГОСТ 4149-89;
Скоба 8150-4489 ; скоба 8102-4128 ; скоба 8119-4214
Операционная карта механической обработки
100.docx
Шестерня промежуточная со втулкой
Наименование операции
Оборудование устройство ЧПУ
Обозначение программы
%-Виттол-100 ТУ РБ 100005975.006-2004
Установить и закрепить деталь
Точить деталь согласно эскизу
Оправка 7112-5225; пневмопривод 7020-5108; центр 7032-0112; ограждение 7056-5039; резец 2112-5010; пластина 2004-5014.
Операционная карта механической обработки
ГОСТ 3.1105-84 Форма 7
005.docx
Шестерня промежуточная со втулкой
Наименование операции
Оборудование устройство ЧПУ
Обозначение программы
%-Виттол-100 ТУ РБ 100005975.006-2004
Установить и закрепить заготовку
Патрон 7112-5083; кулачки 7016-5309
Подрезать торцы выдерживая размеры 12
Стойка для резцов 6727-5039; резец(2) 2100-4082; скоба 8150-5361.
Подрезать торцы выдерживая размеры 12
Стойка для резцов 6727-5040; резец(2) 2100-4082; скоба 8150-5326.
Зенкеровать отверстие выдерживая размер 1
Стойка для крепления зенцера 6675-4001; втулка 6105-5050; зенкер 2320-5105
Операционная карта механической обработки
Расточить отверстие фаску в отверстии выдерживая размеры 12
Оправка для резцов 6702-5066; кронштейн 6675-4002; резец 4142-4052-1П; резец фасочный 2136-4011-1П; пробка 8141-4695.
Раскрепить и снять обработанную деталь. Установить деталь вверх выступающей ступицей.
Оправка кулачковая 7112-5257-01; опора 7030-6524
Подрезать торцы точить фаску на наружном диаметре выдерживая размеры 123
Стойка для резцов 6227-5028 6227-4761; резец(2) 2100-4082 2100-4013; шаблон 8151-4985 97±02
Точить поверхности выдерживая размеры 123456
Стойка для резцов 6727-5027;резец(2) 2100-4013; стойка для резца 6725-5080 6725-5079; резец 2120-4013-1П 2126-4111-1П
Точить поверхности выдерживая размеры 1234
Стойка для резцов 6725-5079; резец 2100-4082 2120-4013-1П 2102-0192; скоба 8113-5306; скоба 8119-4214.
ГОСТ 3.1105-84 Форма 7
105.docx
Шестерня промежуточная со втулкой
Наименование операции
Оборудование устройство ЧПУ
Обозначение программы
%-Виттол-100 ТУ РБ 100005975.006-2004
Установить и закрепить деталь
Шлифовать зубья шестерни
Карандаш 3908-0054 ГОСТ 607-87; круг шлифовальный 350х84х160 25А 12П СМ1..СМ2 8К5 35мс кл.1 ГОСТ 2424-87.
Операционная карта механической обработки
ГОСТ 3.1105-84 Форма 7
015.docx
Шестерня промежуточная со втулкой
Наименование операции
Оборудование устройство ЧПУ
Обозначение программы
%-Виттол-100 ТУ РБ 100005975.006-2004
Установить и закрепить деталь
Планшайба 7067-4012; поводок 7067-4004; Морзе центр 7032-0035 ГОСТ 13214.
Обработать деталь согласно эскизу
Резцедержатель 6723-5337; резцедержатель 6723-5338; резец проходной 2102-0187; планшайба 03113-120408.
Операционная карта механической обработки
ГОСТ 3.1105-84 Форма 7
095.docx
Шестерня промежуточная со втулкой
Наименование операции
Оборудование устройство ЧПУ
Обозначение программы
%-Виттол-100 ТУ РБ 100005975.006-2004
Установить и закрепить деталь
Расточить отверстие согласно эскизу
Головка расточная 6708-5009; резец расточной 2146-5017; пластина ВК 4
Операционная карта механической обработки
ГОСТ 3.1105-84 Форма 7
006.docx
Шестерня промежуточная со втулкой
Наименование операции
Оборудование устройство ЧПУ
Обозначение программы
%-Виттол-100 ТУ РБ 100005975.006-2004
Установить и закрепить деталь
Снять фаску в отверстии согласно эскизу
Патрон 7112-5083; кулачки 7016-5309; зенковка; шаблон 8371-5399
±05 125 2 1 02 500 125
Операционная карта механической обработки
ГОСТ 3.1105-84 Форма 7
104.docx
Шестерня промежуточная со втулкой
Наименование операции
Оборудование устройство ЧПУ
Обозначение программы
%-Виттол-100 ТУ РБ 100005975.006-2004
Установить и закрепить деталь
Шлифовать зубья шестерни предварительно
Алмазный ролик АПРУ 120х22х22 А 800630; карандаш алмазный 3908-0054 2 ГОСТ 607-87
Операционная карта механической обработки
ГОСТ 3.1105-84 Форма 7
035.docx
Шестерня промежуточная со втулкой
Наименование операции
Оборудование устройство ЧПУ
Обозначение программы
%-Виттол-100 ТУ РБ 100005975.006-2004
Установить и закрепить деталь
Фрезеровать зубья согласно эскизу
Приспособление 7533-5288; оправка для фрезы 6224-5031; фреза 5510-5082; оправка контрольная 5031-5109-01.
Операционная карта механической обработки
ГОСТ 3.1105-84 Форма 7
030.docx
Шестерня промежуточная со втулкой
Наименование операции
Оборудование устройство ЧПУ
Обозначение программы
Проверить осмотром отсутствие забоин заусенцев и других дефектов шероховатость поверхностей наличие фасок.
Образцы шероховатости ГОСТ 9378-87
Проверить размеры – 10%
Нутромер 18-50 ГОСТ 9244-85;пробка 8141-4696 ;кольцо 8125-4210-01 ;микрометр МК 25-1 ГОСТ 6507-87.
Штангенглубиномер ШГ- ГОСТ 162-81; плита 2-2-250х250 ГОСТ 10905-81
ПБ-500 центра контррольные; индикатор ич 10кл.1 ГОСТ 577; штатив ш-IIн-8 ГОСТ 10197-81; оправка контрольная 8031-5109
Операционная карта механической обработки
ГОСТ 3.1105-84 Форма 7
025.docx
Шестерня промежуточная со втулкой
Наименование операции
Оборудование устройство ЧПУ
Обозначение программы
%-Виттол-100 ТУ РБ 100005975.006-2004
Установить и закрепить деталь
Притупить острые кромки по ободу венца с двух сторон с переустановкой
Приспособление 7569-5228; круг отрезной 80х2х20 15А25ПСТ 7В 50 мс 1 КЛ А ГОСТ 21963-86
Операционная карта механической обработки
ГОСТ 3.1105-84 Форма 7
050.docx
Шестерня промежуточная со втулкой
Наименование операции
Оборудование устройство ЧПУ
Обозначение программы
Моечная машина 38532015052
Операционная карта механической обработки
037.docx
Шестерня промежуточная со втулкой
Наименование операции
Вертикально-сверлильная
Оборудование устройство ЧПУ
Обозначение программы
%-Виттол-100 ТУ РБ 100005975.006-2004
Установить и закрепить деталь
Зачистить заусенцы после фрезерования зубьев с 2-х сторон
Приспособление 7375-5001; нож 2029-5001; втулка к приспособлению 7030-5379; оправка для ножа 7375-500125.
Операционная карта механической обработки
085.docx
Шестерня промежуточная со втулкой
Наименование операции
Оборудование устройство ЧПУ
Обозначение программы
%-Виттол-100 ТУ РБ 100005975.006-2004
Хонинговать отверстие выдерживая размер 1
Приспособление 7476-5047; подставка 7476-5048; хон 6380-5092; колодка в сборе 2768-5013К; калибр к хону 8139-4203.
Операционная карта механической обработки
ГОСТ 3.1105-84 Форма 7
090.docx
Шестерня промежуточная со втулкой
Наименование операции
Оборудование устройство ЧПУ
Обозначение программы
Запрессовать втулку дет. 240-1006246Б в отверстие ступицы утопив втулку на величину 0.2мм
Подставка 7602-5050; переходник 6153-5012; плита опорная 7081-5059; оправка для запрессовки 7853-5012-03
Операционная карта механической обработки
ГОСТ 3.1105-84 Форма 7
115.docx
Шестерня промежуточная со втулкой
Наименование операции
Оборудование устройство ЧПУ
Обозначение программы
Моечная машина 38532015052
Операционная карта механической обработки
075.docx
Шестерня промежуточная со втулкой
Наименование операции
Оборудование устройство ЧПУ
Обозначение программы
Проверить осмотром отсутствие забоин заусенцев и других дефектов шероховатость обработанных поверхностей
Образцы шероховатости ГОСТ 9378-89
Проверить параметры зубчатого венца-10%
Индикатор ич 10кл.1 ГОСТ 577-81
Проверить угол наклона зуба – 10%
Эвольвентомерная и шагомерная машина мод. PFSU-600. Контрольный прибор МЦ-400Б.
Операционная карта механической обработки
055.docx
Шестерня промежуточная со втулкой
Наименование операции
Оборудование устройство ЧПУ
Обозначение программы
Установить и закрепить деталь
Приспособление 7374-5037; сверло 2300-0148;
Операционная карта механической обработки
ГОСТ 3.1105-84 Форма 7
103.docx
Шестерня промежуточная со втулкой
Наименование операции
Оборудование устройство ЧПУ
Обозначение программы
%-Виттол-100 ТУ РБ 100005975.006-2004
Установить и закрепить деталь
Притупить острые кромки по торцу ступицы с двух сторон
Круг открезной 80х32х202А 25 СТВ 60мс 1клА ГОСТ 21963-82
Операционная карта механической обработки
ГОСТ 3.1105-84 Форма 7
МК.docx
Шестерня промежуточная со втулкой
Код наименование операции
Обозначение документа
Код наименование оборудования
1 Транспортирование КТМ 60140.00001 КТМ 20140.00001 СТИ по ИОТ113
5 Токарная КТМ60140.00002 КТМ60140.00002 СТИ по ИОТ 32
К282 1 15901 3 1 1 1 1 32 1 174
6 Сверлильная КТМ60140.00003 КТМ60140.00003 СТИ по ИОТ 145
А125 1 17474 3 1 1 1 1 32 1 054
0 Вертикально-протяжная КТМ60140.00004 КТМ60140.00004 СТИ по ИОТ 33
66Н67 1 17485 4 1 1 1 1 32 1 056
ГОСТ 3.1404-86 Форма 1а
5 Токарная КТМ60140.00005 КТМ60140.00005 СТИ по ИОТ 32
DVH 450 duo 1 18217 3 1 1 1 1 32 1 223
0 Токарная КТМ60140.00006 КТМ60140.00006 СТИ по ИОТ 32
DVH 450 duo 1 18217 3 1 1 1 1 32 1 183
5 Фасочная КТМ60140.00007 КТМ60140.00007 СТИ по ИОТ 64
Б525-2 1 19479 3 1 1 1 1 32 1 21 089
0 Контрольная КТМ60140.00008 КТМ60140.00008 СТИ по ИОТ 187
Контрольный стол 1 22913 4 1 1 1 1 32 1 016
5 Зубофрезерная КТМ60140.00009 КТМ60140.00009 СТИ по ИОТ 15
А30 1 13902 3 1 1 1 1 32 1 49
7 Вертикально-сверлильная КТМ60140.00010 КТМ60140.00010 СТИ по ИОТ 145
Н125 1 12273 3 1 1 1 1 32 1 095
0 Зубофасочная КТМ60140.00011 КТМ60140.00011 СТИ по ИОТ 35
Б525-2 1 19479 3 1 1 1 1 32 1 2356
5 Слесарная КТМ60140.00012 КТМ60140.00012 СТИ по ИОТ 64
Слесарный стол 1 14723 3 1 1 1 1 32 1 032
0 Промывка КТМ60140.000013 КТМ60140.00013 СТИ по ИОТ 196
Моечная машина 1 14723 3 1 1 1 1 32 1 022
5 Сверлильная КТМ60140.00014 КТМ60140.00014 СТИ по ИОТ 145
М112 1 15922 3 1 1 1 1 32 1 065
0 Маркирование КТМ60140.00015 КТМ60140.00015 СТИ по ИОТ 64
Слесарный стол 1 14723 3 1 1 1 1 32 1 037
5 Промывка КТМ60140.000016 КТМ60140.00016 СТИ по ИОТ 196
5 Контроль КТМ60140.00017 КТМ60140.00017 СТИ по ИОТ 187
Контрольный стол 1 22913 4 1 1 1 1 32 1 058
0 Термическая КТМ60140.00018 КТМ60140.00018 СТИ по ИОТ 64
5 Хонинговальная КТМ60140.00019 КТМ60140.00019 СТИ по ИОТ 35
К82У 1 16801 3 1 1 1 1 32 1 174
6 Токарная КТМ60140.00020 КТМ60140.00020 СТИ по ИОТ 32
ТВ-06 1 18217 3 1 1 1 1 32 1 146
0 Прессовая КТМ60140.00021 КТМ60140.00021 СТИ по ИОТ 136
П6326 1 14723 3 1 1 1 1 32 1 048
5 Токарная КТМ60140.00022 КТМ60140.00022 СТИ по ИОТ 32
ВС-301А 1 15901 3 1 1 1 1 32 1 108
0 Токарная КТМ60140.00023 КТМ60140.00023 СТИ по ИОТ 32
Н713 1 15901 3 1 1 1 1 32 1 0804
3 Слесарная КТМ60140.00024 КТМ60140.00024 СТИ по ИОТ 64
Слесарный стол 1 14723 3 1 1 1 1 32 1 103
4 Зубошлифовальная КТМ60140.00025 КТМ60140.00025 СТИ по ИОТ 166
Д833 1 16811 3 1 1 1 1 32 1 743
5 Зубошлифовальная КТМ60140.00026 КТМ60140.00026 СТИ по ИОТ 166
Рэйсхауэр NZA 1 16811 3 1 1 1 1 32 1 743
7 Вертикально-сверлильная КТМ60140.00027 КТМ60140.00027 СТИ по ИОТ 145
Н135 1 17474 3 1 1 1 1 32 1 106
0 Слесарная КТМ60140.00028 КТМ60140.00028 СТИ по ИОТ 64
Слесарный стол 1 14723 3 1 1 1 1 32 1 163
5 Промывка КТМ60140.00029 КТМ60140.00029 СТИ по ИОТ 196
0 Контроль КТМ60140.00030 КТМ60140.00030 СТИ по ИОТ 187
Контрольный стол 1 14723 3 1 1 1 1 32 1 096
080.docx
Шестерня промежуточная со втулкой
Наименование операции
Оборудование устройство ЧПУ
Обозначение программы
Нитроцементировать зубья h 0.45..0.75 мм.
.64 HRCэ поверхностей; 32..47 для сердцевины зубьев
Операционная карта механической обработки
(А1)Операционные эскизы(1).cdw

Операция 005 токарная
точить фаску на наружном диаметре
выдерживая размеры 1
БНТУ-ДП-10312804-2013
БНТУ кафедра технология машиностроения
* Размер обеспечивается инструментом
выдерживая размер 1.
(А1)Планировка участка.cdw

Производственная площадь участка 508 м
Удельная производственная площадь 12
Количество единиц оборудования 20
Количество рабочих мест 27
КО - комната отдыха;
БНТУ кафедра "технология машиностроения
БНТУ-ДП-10312809-2013
-питьевой фонтанчик;
-отвод охлаждающей воды;
(А2)Фреза червячная _ 2510-5082.cdw

Микротвердость Ho>1800 кгсмм
Допускается изготавливать перезатылованые фрезы 2510-5101
Допуск накопленного отклонения шага на длине любых трех шагов
Допуск профиля зуба не более 0
Остальные технические требования по ГОСТ 9324-80.
Маркировать: товарный знак предприятия-изготовителя:
10-5082; m=2.5; a=20
'; 6242; Р6М5; год выпуска.
Направление нарезки
Сталь Р6М5 ГОСТ 19265-73
БНТУ кафедра "технология машиностроения
Профиль зубьев в нормальном сечении
(А1)Конвейер подвесной грузонесущий _ ПР-254-5670.cdw

Направление движения
Рекомендуемые чертежи
- 26.10.2020
- 11.03.2024
- 24.01.2023