Технология производства вала III оси и сборочной единицы




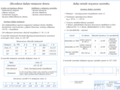
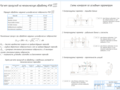
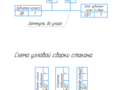
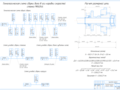
- Добавлен: 24.01.2023
- Размер: 831 KB
- Закачек: 1
Описание
Состав проекта
![]() |
![]() |
![]() |
![]() ![]() ![]() |
![]() ![]() |
![]() ![]() ![]() |
![]() ![]() ![]() |
![]() ![]() ![]() |
![]() ![]() |
![]() ![]() ![]() |
![]() |
![]() ![]() ![]() ![]() |
![]() ![]() ![]() |
![]() ![]() ![]() |
![]() ![]() ![]() ![]() |
![]() ![]() ![]() |
![]() ![]() ![]() |
![]() ![]() ![]() ![]() |
![]() ![]() |
![]() ![]() ![]() |
![]() ![]() ![]() |
![]() |
![]() ![]() ![]() ![]() |
![]() ![]() |
![]() ![]() ![]() |
![]() ![]() ![]() |
![]() |
![]() ![]() ![]() ![]() |
![]() ![]() ![]() ![]() |
![]() ![]() ![]() ![]() |
![]() ![]() ![]() ![]() |
![]() ![]() ![]() ![]() |
![]() ![]() ![]() ![]() |
Дополнительная информация
Список литературы1.doc
Справочник технолога - машиностроителя. В 2-х т. Т. 2 Под редакцией А.М. Дальского А.Г. Суслова А.Г. Косиловой Р.К. Мещерякова - 5-у изд. перераб. и доп. - М.: Машиностроение - 1 2001 944 стр. ил.
Технология машиностроения: В 2 т. Т.1. Основы технологии машиностроения: Учебник для вузов В.М. Бурцев А.С. Васильев А.М. Дальский и др.; Под ред. Г.Н.Мельникова.- 2-е изд. стереотип.- М.: Изд-во МГТУ им. Н.Э. Баумана 2001.- 564 с. ил.
Технология машиностроения: В 2 т. Т.2.Производство машин: Учебник для вузов В.М. Бурцев А.С. Васильев О.М. Деев и др.; Под ред. А.М. Дальского.- 2-е изд. стереотип.- М.: Изд-во МГТУ им. Н.Э. Баумана 2001.- 640 с. ил.
Косилова А.Г. Мещеряков Р.К. Калинин М.А. Точность обработки заготовки и припуски в машиностроении. Справочник технолога. М. «Машиностроение» 1976.- 288 с. ил.
Н.А. Ястребова А.И. Кондаков И.И. Киселев. Методические указания к выполнению курсового проекта по технологии машиностроения.- М.: МВТУ1987.- 42 с. ил.
Разработка технологических эскизов при обработке деталей на металлорежущих станках. Под ред. Е.Ф. Никадимова- М.: МВТУ1963.- 26 с. ил.
Методические указания к курсовому и дипломному проектированию по технологии автоматизированного механосборочного производства Холодкова А.Г. Никадимов Е.Ф. и др.- М.: МГТУ 1990 132 с. ил.
Проектирование технологических процессов сборки В.С. Корсаков Б.Д. Максимович М.А. Калинин И.И. Киселев.- М.: МВТУ 1984.- 50 с.
Кондаков А.И. Островский Ю.А. Разработка маршрутных технологических процессов изготовления деталей: методические указания для курсового и дипломного проектирования.- М.: Изд-во МГТУ им. Н.Э. Баумана 2003.- 50 с.
А.С. Васильев А.И. Кондаков. Выбор заготовок в машиностроении: методические указания для курсового и дипломного проектирования.- М.: Изд-во МГТУ им. Н.Э. Баумана 2001.- 50 с.
Введение1.doc
Первая часть проекта заключается в проектировании технологического процесса сборки который выполняется с учетом анализа технических требований на сборку и отработки сборочного узла на технологичность. В этой части приведен расчет размерных цепей а также разработка технологических схем общей и узловой сборки и разработка технологического процесса с выбором организационной формы сборки.
Во второй части проекта представлено проектирование технологического процесса изготовления вала для чего проводится анализ технических требований чертежа детали и технологичности конструкции обоснование выбора материала и заготовки а также составление маршрутов обработки основных поверхностей выбор баз разработка маршрута и некоторых операций изготовления детали.
Маршрутка.doc
Сталь 45 ГОСТ1050-88
Код наименование операции
Обозначение документа
Код наименование оборудования
Гидравлический пресс
Фрезерно-центровальная
Фрезерно-центровальный полуавтомат мод. МР-71
ГОСТ 3.1118-82 Форма 1б
Токарный станок с ЧПУ мод. 16А20Ф3
Установить и закрепить деталь
Точить 384 -0062 мм на 370 -057 мм
Точить 304 -0062 мм на 232 +021 мм
Подрезать торец 384 -0062 мм выдержав размер 23 мм
Снять фаски 16х450 и 1х450 на 384 -0062 мм и 304 -0062 мм
Обточить канавку 295х3
Ток.станок с ЧПУ мод. 16А20Ф3
Точить 38 -0062 мм на 65 мм
Точить 304 -0062 мм на 388 – 155 мм
Подрезать торец 38 -0062 мм
Снять фаску 1х450 на 304 -0062 мм
Обточить канавку 295х3
Обточить канавку 36 -034 х 19+025 выдержав размер 223+06 мм
Установить деталь в центра и закрепить
Фрезеровать шлицы D-8x32x38g6x6e9 с припуском под шлифование
Червячная модульная фреза D-8х32х38-е9-С ГОСТ 8027-86.
Отпилить острые кромки после фрезерования
Термическая обработка
Произвести закалку ТВЧ поверхности шлицев
Присп. для шлифования центров
Установить деталь в приспособление
Шлифовать с переустановкой центровые отверстия
Токарный станок мод. 16К20
Подрезать левый торец 38 -0062 мм
Круглошлифовальный станок мод. 3М151
Шлифовать 38g6 на длине 356 мм
Шлифовальный круг ПП 400х50х127 15А 50 СМ2 10К ГОСТ 2424-83
Шлифовать с переустановкой 30к6
Шлифовать шлицы D-8x32x38g6x6e9
Вертикально-сверлильная
Вертикально-сверлильный станок мод. 2А125
Установить деталь в приспособление и закрепить
Сверлить отверстие 87 на 40 мм
Сверло спиральное из быстрорежущей стали
Сверлить отверстие 11 на 9+05 мм
Зенковать фаску 156 –10 х600
Нарезать резьбу М10-7Н
Содержание1.doc
1. Назначение узла в машине и краткое описание его конструкции. .
2. Анализ технологичности конструкции: качественные и количественные критерии
оценки технологичности конструкции выводы . .
3. Расчет размерной цепи двумя методами ( вероятностным и maxmin)
4. Разработка и обоснование технологической схемы общей и узловой сборки узла
5. Выбор организационной формы сборки .
Раздел 2. Проектирование технологического маршрута изготовления детали
1. Назначение детали. Анализ технических требований чертежа детали выявление
основных технологических задач разработка схем контроля по основным
параметрам точности .
2. Отработка конструкции на технологичность для заданного типа производства
3. Обоснование выбора материала детали для данного типа производства: критерии
выбора условия эксплуатации . . ..
4. Выбор и обоснование метода получения заготовки: критерии выбора
схематическое изображение (эскиз) заготовки ..
5. Маршруты обработки основных поверхностей детали их обоснование
6. Выбор баз и схем базирования для нескольких операций
7. Разработка маршрута изготовления детали для заданного типа производства
с выбором технологического оборудования инструментов
8. Разработка операционной технологии для нескольких операций с выбором режущих
инструментов обоснованием и расчетом режимов резания и норм времени .. ..
9. Расчет припусков на механическую обработку .
Список литературы .
Заключение1.doc
При проведении анализа технических требований на сборку и отработки сборочного узла на технологичность было установлено что конструкция данной сборочной единицы является технологичной. Была также выполнена разработка технологических схем общей и узловой сборки и разработка технологического процесса сборки.
Во второй части проекта был проведен анализ технических требований чертежа вала и технологичности конструкции на основании чего можно сказать что деталь является технологичной. Также был выбран материал и заготовка (Сталь 45 круглый прокат) составлены маршруты обработки основных поверхностей выбор баз проведена разработка маршрута и некоторых операций изготовления детали.
3.frw

Схема узловой сборки блока зубчатых колес.
соосность.frw

припуски.frw

Карта расчета припусков на обработку и предельных размеров по
технологическим переходам.
контроль.frw

контр.frw

Фрагмент.frw

- глубина дефектного поверхностного слоя на предшествующем переходе;
- суммарные отклонения расположения поверхности и в некоторых
случаях отклонения формы поверхности;
- погрешность установки заготовки на выполняемом переходе.
паралл.frw

Фрагмент56.frw

Фрагмент4.frw

- после получистового точения
- после чистового точения
- после чернового шлифования
- после окончательного шлифования."
Титульный лист1.doc
и ордена Трудового Красного Знамени государственный технический
университет им. Н.Э. Баумана
ФАКУЛЬТЕТ: Машиностроительные технологии.
''Технология машиностроения''
РАСЧЕТНО-ПОЯСНИТЕЛЬНАЯ ЗАПИСКА
К КУРСОВОМУ ПРОЕКТУ НА ТЕМУ:
«Технология производства типовой детали
и сборочной единицы.»
Студент: (Земцов Д.С.) Группа: МТ3-81
Руководитель проекта: (Камсюк М.С.)
проект.doc
1. Назначение узла. Анализ ТУ на сборку выявление основных
технологических задач: разработка схем контроля по основным параметрам
2. Анализ технологичности конструкции: качественные и количественные критерии оценки технологичности конструкции выводы.
3. Расчет размерных цепей двумя методами (вероятностным и maxmin) с выбором методов достижения точности сборки.
4. Разработка и обоснование технологической схемы общей сборки узла и эскизов с пояснениями.
5. Разработка и обоснование технологических схем и эскизов узловой сборки (1 и 2 подсборки из данной конструкции).
6. Разработка технологического процесса сборки с выбором оборудования инструментов техническим нормированием времени и определением суммарной трудоемкости сборки узла.
7. Выбор организационной формы сборки данной конструкции.
Раздел 2. Проектирование технологического маршрута изготовления детали.
1. Назначение детали в узле. Анализ технических требований чертежа детали выявление основных технологических задач разработка схем контроля по основным параметрам точности.
2. Отработка конструкции на технологичность для заданного типа производства.
3. Обоснование выбора материала детали: критерии выбора условия эксплуатации возможные варианты материала.
4. Выбор и обоснование метода получения заготовки: критерии выбора схематическое изображение (эскиз) заготовки с припусками.
5. Маршруты обработки основных поверхностей детали их обоснование.
6. Выбор баз и анализ схем базирования для нескольких операции.
7. Разработка маршрута изготовления детали для заданного типа производства с выбором технологического оборудования инструментов средств контроля.
8. Разработка технологических наладок для 1-3 операций с выбором режущих инструментов обоснованием и расчетом режимов обработки и припусков.
Раздел 1. Разработка технологической схемы сборки узла.
1. Назначение узла в машине и краткое описание его конструкции.
Вал III оси в сборе предназначен для передачи крутящего момента и требуемой частоты вращения от вала I оси к валу VI оси (шпиндель).
На вал посредством шлицевого соединения насаживаются два зубчатых колеса-19(z=45 m=3) и 20(z=15 m=35); два блока зубчатых колес-5(z=30 m=35; z=60 m=3) и 43(z=47 m=225; z=55 m=225; z=38 m=225). Вал установлен на опоры - два цилиндрических радиально-упорных и один шариковый радиальный подшипники.
Технологичность конструкции характеризуется её соответствием современному уровню техники экономичностью и удобствами эксплуатации а также тем в какой мере учтены возможности использования наиболее экономичных и производительных методов её изготовления применительно к заданному выпуску и условиям производства.
Качественная оценка.
- Сборочная единица содержит большое количество деталей.
- Конструкция обеспечивает возможность удобного и свободного подвода сборочного инструмента.
- Конструкция узла обеспечивает возможность его сборки из предварительно собранных составных частей.
- На сопрягаемых деталях имеются фаски.
- Применение специальных приспособлений для сборки деталей не требуется.
- Узел в целом имеет простую компоновку и простое конструктивное решение не вызывающее затруднений при его сборке.
Количественные показатели.
Коэффициент сборности - показывает возможность расчленения на рациональное число составных частей сборку которых можно производить независимо друг от друга.
Е=5 - число сборочных единиц;
Д=3 - число деталей не вошедших в состав сборочных единиц.
В условиях мелкосерийного и серийного производства значение КСБ=062 является приемлемым.
Коэффициент стандартизации - характеризует использование стандартных сборочных единиц и деталей.
КСТ = (ЕСТ+ДСТ)(Е+Д) где
ЕСТ =2 - число стандартных сборочных единиц;
ДСТ =1 - число стандартных деталей не вошедших в сборочные единицы.
КСТ = (2+1)(5+3)=0375
Коэффициент КСТ=0375 показывает что конструкция технологична в условиях серийного производства.
Вывод: На основании проведенного анализа делаем вывод что конструкция технологична в условиях мелкосерийного и серийного производства.
3. Расчет размерных цепей двумя методами (вероятностным и maxmin).
По заданным параметрам составляющих звеньев необходимо найти параметры замыкающего звена.
На рисунке представлена размерная цепь состоящая из семи размеров. Требуется определить гарантированный зазор и двумя методами (вероятностным и методом maxmin) определить допуск на этот размер.
А1=1655 ± 0125 мм А2=62 ± 0095 мм А3=31 ± 008 мм А4=34 ± 008 мм
А5=36 ± 008 мм А6=17 ± 003 мм Х-замыкающий размер.
Расчет номинального размера.
Х = 1655-17-36-34-31-62 = 08 мм.
Расчет допуска вероятностным методом.
DХ = (± 003)+( ± 008)+( ± 008)+( ± 008)+( ± 0095)+( ± 0125) = 049 мм.
Расчет допуска методом maxmin.
DХ = 006 2+ 016 2+ 016 2+ 016 2+ 019 2+ 025 2 = 042 мм.
В результате расчетов назначим допуск на гарантированный зазор полученный методом maxmin.
4. Разработка и обоснование технологической схемы общей и узловой сборки узла.
Технологические схемы сборки в наглядной форме выражают маршрут узловой и общей сборки. Необходимо сначала разработать технологическую схему общей сборки а затем технологическую схему сборки узлов и подузлов.
При составлении технологической схемы сборки необходимо выявить все возможные варианты сравнить их и выбрать оптимальный то есть обеспечивающий заданную точность удобство сборки простоту исполнительных сборочных механизмов надежность и производительность сборочного процесса.
Технологические схемы общей и узловой сборки приведены ниже.
5. Выбор организационной формы сборки данной конструкции.
Производство станков МК6046 и 16К20 в настоящее время имеет характер мелкосерийного и зачастую единичного производства поэтому в данном случае целесообразно применить стационарную сборку без расчленения сборочных работ. Такая организация труда хоть и имеет невысокую производительность и сравнительно высокую стоимость но на лицо такие плюсы по сравнению с поточной сборкой характерной для для массового производства как:
- исключение отрицательных психологических факторов действующих при сильной дифференциации сборочных работ на автоматизированных поточных линиях;
- устранение монотонности и однообразия труда;
- уменьшение усталости и утомляемости рабочего;
- повышение престижа работы (рабочие имеют лучшие условия для своей самореализации).
Деталь МК6046.020000.138 относится к классу валов и входит в состав сборочного узла коробки скоростей станка МК6046. Данная деталь обеспечивает передачу крутящего момента и требуемую частоту вращения от вала I оси к валу VI оси (шпиндель станка) с помощью зубчатых колёс посаженных на вал посредством шлицевого соединения.
Анализ технических требований чертежа детали.
Точность двух посадочных поверхностей под подшипники 30к6 (Ra125). Это требование необходимо соблюсти так как эти поверхности являются посадочными под подшипники. Требование обеспечивается при обработке на круглошлифовальном станке. Контроль точности диаметров обеспечивается с помощью скобы с отчетным устройством;
Точность наружной цилиндрической поверхности шлицов 38g6 (Ra125). Это требование необходимо соблюсти так как при соединении вала с зубчатым колесом центрирование происходит по наружному 38g6. Требование обеспечивается при обработке на круглошлифовальном станке;
Точность боковых граней шлицев 6е9 (Ra25). Это требование необходимо для обеспечения возможности сборки вала с устанавливаемыми на него зубчатыми колёсами. Требование обеспечивается при обработке на шлицешлифовальном станке;
Неуказанные предельные отклонения размеров: отверстий-Н14 валов-h14 остальных ± t22 (Rz40);
Точность канавки под уплотнительное кольцо 36-034х19 +025 (Rz20);
Допуск на биение торца 38-0062 в размер 388 относительно оси детали не более 003 мм. Данный допуск назначают чтобы уменьшить перекос колец подшипников и искажения геометрической формы дорожки качения внутреннего кольца подшипника;
Допуск на биение 38g6 относительно оси детали не более 003 мм. Данная поверхность является посадочной под зубчатые колеса. Невыполнение требования может привести к повышению дисбаланса и возникновению вибраций. Требование обеспечивается при обработке на круглошлифовальном станке при базировании в центрах;
Допуск параллельности боковых граней шлицев относительно оси детали не более 003 мм на длине 300 мм. Необходим для обеспечения возможности сборки вала с устанавливаемыми на него зубчатыми колёсами;
Закалка ТВЧ шлицев детали глубина закаленного слоя - 12..22 мм твердость после закалки - 45..50 HRCэ. Закалка необходима для достижения высокой твердости поверхности и сопротивление износу шлицев так как шлицы работают при постоянных циклических и контактных нагрузках.
Необходимо назначить допуск соосности посадочных поверхностей для подшипников относительно их общей оси чтобы ограничить перекос колец подшипников качения (для роликовых конических подшипников перекос составляет 2 мин.). Назначаем допуск соосности 0005 мм.
Основные технологические задачи.
Обеспечить точность посадочных поверхностей по 6 квалитету и добиться шероховатости этих поверхностей Ra125.
Обеспечить точность боковых граней шлицев по 9 квалитету и добиться шероховатости этих поверхностей Ra25.
Обеспечить точность резьбы по 7 квалитету.
Обеспечит чтобы значение радиального биения 38g6 относительно оси детали не превышало 003мм.
Обеспечит чтобы значение торцевого биения торца относительно оси детали не превышало 003мм.
Обеспечит чтобы значение параллельности боковых граней шлицев относительно оси детали не превышало 003мм.
Обеспечить твердость поверхности шлицев 45..50 HRCэ.
Разработка схем контроля по основным параметрам точности.
Контроль торцевого биения требуемых торцевых поверхностей относительно оси детали.
Деталь закрепляется в центрах которые установлены на специальной основной станине. Щуп индикатора установленного на стойке подводим к контролируемой торцевой поверхности. Индикатор предварительно выставляем на ноль. Далее прокручиваем деталь на 360° (щуп делает один оборот по поверхности детали). Во время прокручивания детали снимаем показания индикатора. При повороте заготовки на 360° показания индикатора не должны превышать 003 мм. Цена деления индикатора составляет 2 мкм.
Контроль радиального биения и соосности требуемых поверхностей относительно оси детали.
Деталь закрепляется в центрах которые установлены на специальной основной станине. Щуп индикатора установленного на стойке опускаем на контролируемые цилиндрические поверхности. Индикатор предварительно выставляем на ноль. Далее прокручиваем деталь на 360° (щуп делает один оборот по поверхности детали). Во время прокручивания детали снимаем показания индикатора.
Допуск на биение 38g6. При повороте заготовки на 360° показания индикатора не должны превышать 003 мм. Цена деления индикатора составляет 2 мкм.
Допуск соосность 30к6. При повороте заготовки на 360° показания индикатора не должны превышать 00025 мм. Цена деления индикатора составляет 05 мкм.
Контроль параллельности боковых граней шлицев относительно оси детали.
Деталь закрепляется в центрах которые установлены на специальной основной станине. Станина имеет шариковые направляющие что позволяет перемещать деталь в горизонтальной плоскости. Щуп индикатора установленного на стойке опускаем на контролируемую поверхность. Индикатор предварительно выставляем на ноль. С обратной стороны шлица подводим упор чтобы исключить вращение детали вокруг своей оси. Далее станину вместе с деталью перемещаем на 300 мм. Во время перемещения снимает показания индикатора. На длине 300 мм. показания индикатора не должны превышать 003 мм. Цена деления индикатора составляет 2 мкм.
Тип производства - серийное.
Конфигурация детали - тело вращения. Она представляет собой сочетание простых геометрических форм. Каких-либо поверхностей затрудняющих обработку деталь не имеет.
Ввиду высокой ответственности деталь является цельной а её замена сварной или сборочной конструкцией недопустима.
Установленные конструктором допуски являются обоснованными. Требования точности обработки и шероховатости поверхности детали соответствуют её служебному назначению. Самая высокая точность поверхности по 6 квалитету.
Для установки и закрепления заготовки предусмотрены надежные технологические базы. Базирование осуществляется легко. Соблюдён принцип постоянства баз.
Простота расположения поверхностей друг относительно друга обеспечивает удобный подвод и свободный выход режущего инструмента.
Система простановки размеров в целом обеспечивает удобство и производительность контроля. Для контроля параметров точности в большинстве случаев можно использовать простые измерительные средства и приспособления.
Значения шероховатости проставленные на различных поверхностях соответствуют размерам поверхностей оговоренных допусками.
Применение токарного станка с ЧПУ позволяет выполнить контур детали без замены инструмента что значительно снижает трудоемкость обработки.
Шлицевое соединение выполнено с центрированием по наружному диаметру вала. Это означает что нарезание шлицев для зубчатых колес можно выполнять протяжкой а протягивание шлицев в свою очередь оптимально для серийного производства так как возможна обработка нескольких зубчатых колес за один установ.
Коэффициент точности обработки детали.
АСР = (5n5 + 6n6 + + 14n14)(n5 + n6 + + n14)
ni -количество поверхностей i-го квалитета.
АСР = (6*3+7*1+9*16+10*1+14*6)(3+1+16+1+6)=71
КТД = 1-(171) = 086 > 03 - соответствует нормальной точности обработки.
Коэффициент шероховатости поверхностей детали.
GСР = (1n1 + 2n2 + ..)(n1 + n2 + ..)
ni - количество поверхностей i-го класса шероховатости.
GСР = (4*8+5*3+6*19+7*3)(3+19+3+8)=55
КШД = 1-(155) = 081 > 26 - соответствует требованиям по шероховатости.
Существует ещё ряд показателей технологичности конструкции детали: например трудоемкость изготовления технологическая себестоимость коэффициент унификации элементов и др. В данном курсовом проекте рассматриваются только два коэффициента.
Вывод: На основании проведенного качественного и количественного анализа считаем конструкцию данной детали технологичной в условиях мелкосерийного и серийного производства.
Выделяют три основные группы свойств: эксплуатационные технологические и стоимостные которые лежат в основе выбора материала определяют техническую и экономическую целесообразность его применения.
Деталь работает при циклических и контактных нагрузках. Таким образом выбираемый материал должен обладать повышенной прочностью. Среднеуглеродистая сталь 45 отличается большей прочностью но меньшей пластичностью чем низкоуглеродистые стали. Сталь 45 имеет следующий химический состав: Si(кремний)=017-037% Mn(марганец)=050-080% Cu(медь)=025% As(мышьяк)=008% Ni(никель)= 025% S(сера)=004% C(углерод)=045% P(фосфор)=0035% Cr(хром)=025%. Эта сталь характеризуется более низким чем у сталей обыкновенного качества содержанием вредных примесей(SP) и неметаллических включений. Ni повышает жаростойкость Cu понижает коэффициент трения Mn и Si повышают(важную для нас) износостойкость карбидообразующий элемент(Cr) повышает прочность.
Механические свойства стали 45: 02= 360МПа В= 610МПа =16% =40% HB=230 KCU= 05МДжм2.
Технологические свойства: плохая свариваемость хорошая обрабатываемость резанием удовлетворительная пластичность низкая теплостойкость. После поверхностной индукционной закалки с нагревом ТВЧ у материала повышается твёрдость поверхности(40-58HRC) и сопротивление износу. Сталь 45 поставляют в виде проката поковок и других полуфабрикатов с гарантированным химическим составом и механическими свойствами.
В качестве заменителя предлагаемого материала можно предложить несколько аналогов. Например стали 40Х 50 50Г2. Стоимость стали 45 -10990 руб. за тонну а стоимость стали 40Х - 11990 руб. за тонну. С экономической и технологической точки зрения выбранная сталь отвечает всем требованиям и нормам.
Для того чтобы выбрать метод получения заготовки прежде всего необходимо определить вид заготовки. Критерии выбора вида заготовки приведены в таблице.
Приоритетный ряд видов
Заготовительные свойства материала:
Обрабатываемость резанием
неудовлетворительная
Ориентированность структуры
Удельная стоимость материала
Ответственность детали
Обозначения. О-отливка; ОД-полученная обработкой давлением; П-прокат; СК-сварная или комбинированная; ПМ-полученная методами порошковой металлургии; ( )-исключая; *-любая (равноприоритетность видов).
Принимаем следующий способ получения заготовки: круглый прокат ГОСТ2590-71.
Заготовку получаем отрезкой круглого проката длиной 435±04 мм.
Размеры заготовки: L= 435±04 мм; D=43-05+01.
Наружные цилиндрические поверхности 30к6 Ra125.
-заготовка IT15 Rz160
-точение черновое IT13 Rz125
-точение получистовое IT12 Rz63
-точение чистовое IT9 Rz20
-шлифование предварительное IT7 Ra25
-шлифование окончательное IT6 Ra125
Наружная цилиндрическая поверхность 38 Rz20.
Наружная цилиндрическая поверхность 38g6 Ra125.
Боковая поверхность шлицев 6е9 Ra25.
-заготовка IT14 Rz80
-фрезерование черновое IT12 Ra125
-фрезерование чистовое IT10 Ra32
-шлифование предварительное IT9 Ra25.
Заготовка детали должна занять и сохранять в течении всего времени обработки определенное положение относительно деталей станка и приспособления. Для этого необходимо исключить возможность трёх прямолинейных движений её в направлении выбранных координатных осей и трёх вращательных движений вокруг параллельных им осей (то есть лишить деталь 6 степеней свободы).
Выбираемые базы должны обеспечить:
- удобство установки (базирования и закрепления) и снятия заготовки;
- возможность беспрепятственного подвода инструмента к намеченным для обработки поверхностям;
- исключение деформаций заготовки при установке и последующей обработке
При выборе баз по возможности должны соблюдаться принципы:
- совмещение установочных и измерительных баз.
Анализируя рабочий чертёж детали делаем вывод что основной конструкторской базой является наружная цилиндрическая поверхность 30к6. Она является явной базой. Мнимой базой в данном случае является ось детали. Технологическими базами являются центровые отверстия (ГОСТ 14.034-81). Обработка в центрах обеспечивает минимальную погрешность установки заготовки. Такая схема позволяет совместить измерительную базу с технологической упрощает наладку режущего инструмента повышает точность выполняемых размеров по длине. Соблюдение принципов совмещения баз позволяет повысить точность обработки за счет ликвидации погрешности базирования заготовки.
Теперь руководствуясь выше сказанным рассмотрим некоторые операции ТП:
- Операция 015. Фрезерно-центровальная. На этом этапе происходит подготовка основной технологической базы (центров). За черновую базу принимаем наружную цилиндрическую поверхность и торец заготовки. Установка заготовки производится в тиски с призматическими губками с базированием в осевом направлении по упору.
- Операция 020. Токарная с ЧПУ. За базу принимают центровые отверстия и торец заготовки. Установка заготовки производится в центрах с упором в торец. Вращение передается посредствам хомутика.
Перед шлифованием применяют дополнительную обработку центровых отверстий с целью обеспечения высокой точности их формы.
- Операция 045. Центрошлифовальная. Базирование заготовки аналогично базированию в операции 015.
- Операция 070. Вертикально-сверлильная. За базу принимают наружную цилиндрическую поверхность 38 и торец заготовки. Установка заготовки производится на плоскость и в тиски с призматическими губками.
7. Разработка маршрута изготовления детали для заданного типа производства с выбором технологического оборудования инструментов.
Маршрут изготовления вала для серийного производства с выбором технологического оборудования и инструментов приведен ниже.
8. Разработка технологических наладок для 1-3 операций с выбором режущих инструментов обоснованием и расчетом режимов обработки и норм времени.
Группу режущего инструмента устанавливают по виду обработки предусмотренному маршрутным технологическим процессом. По конфигурации обрабатываемой заготовки компоновки станка принятой схеме установки заготовки выявляют форму и расположение режущих лезвий определяющий вид режущего инструмента.
Рассмотрим методику выбора режущего инструмента и расчет режимов резания на примере нескольких операций.
Операция 020. Токарная с ЧПУ.
Переход 1. Точить 384-0062 на длине 370 -057 мм.
Режущий инструмент - токарный проходной резец с механическим креплением твердосплавных пластин. Материал пластины - Т15К6. Точение черновое получистовое чистовое.
Оборудование: токарный станок с ЧПУ 16А20Ф3.
t=15 мм - черновое точение;
t=075 мм - получистовое точение;
t=02 мм - чистовое точение;
S=09 ммоб - черновое точение ([2] стр.266 табл.11);
S=06 ммоб - получистовое точение ([2] стр.266 табл.11);
S=042 ммоб - чистовое точение ([2] стр.268 табл.14);
Скорость резания рассчитывается по эмпирической формуле:
Стойкость инструмента: T=60 мин.
KMV = Kr(750sВР)N = 10(750610)1 = 123 ([2] стр.261 табл.1);
КПV = 09 ([2] стр.263 табл.5);
KИV = 115 ([2] стр.263 табл.6);
Kr = 10 ([2] стр.262 табл.2);
N = 10 ([2] стр.262 табл.2);
KV = 123*09*115 = 127;
V=280*12760 02*15 015*09 045 = 155 ммин - для чернового точения;
V=290*12760 02*075 015*06 035 = 200 ммин - для получистового точения;
V=290*12760 02*02 015*042 035 = 280 ммин - для чистового точения;
Частота вращения шпинделя:
d - диаметр заготовки мм;
n = 1000*155p*43 = 1147 обмин - для чернового точения;
n = 1000*200p*40 = 1591 обмин - для получистового точения;
n = 1000*280p*385 = 2053 обмин - для чистового точения;
Уточняем скорость резания:
V = n*p*d1000 = 1200*p*431000 = 162 ммин - для чернового точения;
V = n*p*d1000 = 1600*p*401000 = 201 ммин - для получистового точения;
V = n*p*d1000 = 2000*p*3851000 = 240 ммин - для чистового точения.
Основное время обработки:
Т0 = 3721200*09 = 034 мин - для чернового точения;
Т0 = 3721600*06 = 039 мин - для получистового точения;
Т0 = 3722000*042 = 044 мин - для чистового точения.
Переход 2. Точить 304-0052 на длине 21 -021 мм.
t=25 мм - черновое точение;
t=10 мм - получистовое точение;
t=05 мм - чистовое точение;
S=05 ммоб - черновое точение ([2] стр.266 табл.11);
S=04 ммоб - получистовое точение ([2] стр.266 табл.11);
S=033 ммоб - чистовое точение ([2] стр.268 табл.14);
V=290*12760 02*25 015*05 035 = 178 ммин - для чернового точения;
V=290*12760 02*10 015*04 035 = 222 ммин - для получистового точения;
V=290*12760 02*05 015*033 035 = 269 ммин - для чистового точения;
n = 1000*178p*381 = 1487 обмин - для чернового точения;
n = 1000*222p*331 = 2134 обмин - для получистового точения;
n = 1000*269p*311 = 2753 обмин - для чистового точения;
V = n*p*d1000 = 1500*p*3811000 = 180 ммин - для чернового точения;
V = n*p*d1000 = 2000*p*3311000 = 207 ммин - для получистового;
V = n*p*d1000 = 2700*p*3111000 = 263 ммин - для чистового точения.
Т0 = 251500*05 = 0033 мин - для чернового точения;
Т0 = 252000*04 = 0031 мин - для получистового точения;
Т0 = 252700*033 = 0028 мин - для чистового точения.
Переход 3. Подрезать торец 381 -0062 мм.
Режущий инструмент - токарный проходной резец с механическим креплением твердосплавных пластин. Материал пластины - Т15К6.
Глубина резания: t=2 мм;
Подача: S=06 ммоб ([2] стр.266 табл.11);
V=290*12760 02*2015*06 035 = 176 ммин;
n = 1000*176p*381 = 1470 обмин;
V = n*p*d1000 = 1500*p*3811000 = 180 ммин;
Т0 = 51500*06 = 0005 мин.
Операция 055. Круглошлифовальная.
Шлифовать 38g6 обеспечив Ra125.
Режущий инструмент - шлифовальный круг ПП 400*50*127 15А 50 СМ2 10К ГОСТ 2424-83.
Диаметр круга 400 мм ширина круга 50 мм.
Оборудование: Круглошлифовальный станок 3М151:
пЗ = 50-500 обмин - частота вращения шпинделя заготовки;
пК = 1590 обмин - частота вращения шпинделя шлифовального круга;
Скорость вращения круга:
VК = nК*p*dК1000*60 = 1590*p*4001000*60 = 33 мс;
Скорость вращения заготовки: VЗ = nЗ*p*dЗ1000;
Продольная подача: S0 = (03-07)B - для предварительного шлифования;
S0 = (02-04)B - для окончательного шлифования;
Скорость перемещения заготовки в продольном направлении:
Для предварительного шлифования:
Принимаем : VЗ = 20 ммин ([2] стр.301 табл. 55) тогда
пЗ = 1000*VЗp*dЗ = 1000*20p*38 = 170 обмин;
Для станка 3М151 пЗ = 170 обмин подходит следовательно
VS = S0*nЗ1000 = 05*50*1701000 = 425 ммин.
Т0 = L*t*kn3*S0*SX где L=356 мм t=03 мм к=14 S0 = 25 SX = 001 мм;
Т0 = 356*03*14170*25*001 = 352 мин.
Для окончательного шлифования:
Принимаем : VЗ = 30 ммин ([2] стр.301 табл. 55) тогда
пЗ = 1000*VЗp*dЗ = 1000*30p*38 = 250 обмин;
Для станка 3М151 пЗ = 250 обмин подходит следовательно
VS = S0*nЗ1000 = 03*50*2501000 = 375 ммин.
Т0 = L*t*kn3*S0*SX где L=356 мм t=01 мм к=14 S0 = 15 SX = 0005 мм;
Т0 = 356*01*14250*15*0005 = 265 мин.
Операция 030. Шлицефрезерная.
Шлифовать шлицы D-8*32*38g6*6e9 c припуском под шлифование.
Режущий инструмент - червячная фреза D-8*32*38-е9-С ГОСТ 8027-86.
Оборудование: шлицефрезерный станок модели 5350.
Глубина резания: t=4 мм;
Подача на зуб: SZ = 006 ммоб ([2] стр.284 табл.35);
V=СV*KV*DqTM*tX*SY*BU*zp где
Стойкость инструмента: T=120 мин ([2] стр.286 табл.40);
КПV = 10 ([2] стр.263 табл.5);
KИV = 10 ([2] стр.263 табл.6);
KV = 123*10*10 = 123;
V=44*123*80 045120033*403*006 02*601*1001 = 47 ммин;
Частота вращения фрезы:
D - диаметр фрезы мм;
n = 1000*47p*80 = 190 обмин;
9. Расчет припусков на механическую обработку.
На каждом переходе механической обработки с обрабатываемой поверхности в виде стружки снимается слой материала. Назначенный припуск может быть признан оптимальным если он обеспечивает:
- удаление с установленных в рабочей зоне всех отклонений геометрических параметров обрабатываемой поверхности а также дефектного поверхностного слоя;
- получение заданных геометрических параметров без следов от предшествующей обработки;
- минимально необходимый снимаемый слой материала.
Минимальный припуск при обработке наружных и внутренних поверхностей:
При шлифовании у заготовки после её термической обработки поверхностный слой должен быть сохранен: следовательно слагаемое hi-1 должно быть исключено из расчетной формулы:
Суммарное отклонение расположения при обработке сортового проката круглого сечения в центрах:
Остаточное отклонение расположения заготовки после обработки определяют по приближенной формуле:
Расчет припусков на обработку наружной цилиндрической поверхности 38g6.
Точность и качество поверхности заготовки из проката после механической обработки.
Получистовое точение
Предварительное шлифование
Окончательное шлифование
DS =D2SК + D2ц = 00516 2 + 009 2 = 0103 мм где
Dц=025Т = 025*036 = 009 мм;
Примем e=001 мм - погрешность установки заготовки в центрах
zi min = 2[(Rz+h)i-1 + D2S i-1+ e ] = 2[(016+025)+ 0103 2+ 001 2 = 1025 мм.
Коэффициент уточнения для сортового проката([1] стр.338 табл. 29):
КУ = 006 - после чернового точения;
КУ = 005 - после получистового точения;
КУ = 004 - после чистового точения;
КУ = 003 - после чернового шлифования;
КУ = 002 - после окончательного шлифования;
Остаточное отклонение расположения заготовки:
DОСТ = 006*0103 = 000618 мм - после чернового точения;
DОСТ = 005*0103 = 000515 мм - после получистового точения;
DОСТ = 004*0103 = 000412 мм - после чистового точения;
DОСТ = 003*0103 = 000309 мм - после чернового шлифования;
DОСТ = 002*0103 = 000206 мм - после окончательного шлифования;
Получистовое точение:
DS =DОСТ = 000618 мм;
zi min = 2[(Rz+h)i-1 + D2S i-1+ e ] = 2[(0125+0120)+ 000618 2+ 001 2 = 05 мм.
DS =DОСТ = 000515 мм;
zi min = 2[(Rz+h)i-1 + D2S i-1+ e ] = 2[(0063+0060)+ 000515 2+ 001 2 = 027 мм.
Предварительное шлифование:
При шлифовании у заготовки после её термической обработки поверхностный слой должен быть сохранен: следовательно слагаемое hi-1 должно быть исключено из расчетной формулы.
DS =DОСТ = 000412 мм;
zi min = 2[(Rz+h)i-1 + D2S i-1+ e ] = 2[0020 + 000412 2+ 001 2 = 006 мм.
Окончательное шлифование:
DS =DОСТ = 000309 мм;
zi min = 2[(Rz+h)i-1 + D2S i-1+ e ] = 2[0010 + 000309 2+ 001 2 = 004 мм.
тех процесс1.cdw

Оборудование: токарный станок мод. 16А20Ф3.
Операция 025. Токарная с ЧПУ.
Операция 030. Шлицефрезерная.
Оборудование: станок мод. 5350.
Операция 040. Термообработка.
Операция 015. Фрезерно-центровальная.
Оборудование: фрезерно-центровальный полуавтомат мод. МР-71.
Операция 045. Центрошлифовальная.
Оборудование: центрошлифовальное приспособление.
Операция 050. Токарная.
Оборудование: токарный станок мод. 16К20.
Операция 055. Круглошлифовальная.
Оборудование: станок мод. 3М151.
Операция 060. Круглошлифовальная.
Операция 065. Шлицешлифовальная.
Оборудование: станок мод. 3451.
Операция 070. Вертикально-сверлильная.
Оборудование: вертикально-сверлильный станок мод. 2А125.
Операция 005. Правка.
Оборудование: гидравлический пресс.
Операция 010. Отрезная.
Оборудование: пилоотрезной станок.
Операция 035. Слесарная
(отпилить острые кромки после фрезерования).
Оборудование: верстак слесарный.
Неуказанные предельные отклонения размеров отверстий Н14
МГТУ им. Н.Э.Баумана
Операция 075. Контрольная.
припуски-лист.cdw

При повороте детали на 360
показания индикатора не должны
Маршрут обработки наружной цилиндрической поверхности
Получистовое точение
Предварительное шлифование
Окончательное шлифование
Расчет припусков на механическую обработку
Минимальный припуск при обработке наружных цилиндрических поверхностей:
- высота неровностей профиля на предшествующем переходе
- глубина дефектного поверхностного слоя на предшествующем переходе
- суммарные отклонения расположения поверхности и в некоторых
случаях отклонения формы поверхности
- погрешность установки заготовки на выполняемом переходе.
Полученные предельные
Карта расчета припусков на обработку и предельных размеров по
технологическим переходам.
Цена деления индикатора: 0
На длине 300 мм. показания
индикатора не должны превышать
МГТУ им. Н.Э. Баумана
Схемы контроля по основным параметрам.
Контролируемый параметр - торцевое биение.
Контролируемый параметр - радиальное биение и соосность.
Контролируемый параметр - параллельность шлицев.
Чертеж детали.cdw

выбор заг-ки.cdw

- динамические нагрузки;
- контактные нагрузки;
- высокая ответственность детали.
Требования к материалу заготовки:
- высокая прочность;
- высокая твердость;
- высокая износостойкость.
Критерии выбора материала:
- для предупреждения хрупкого разрушения материал должен обладать
достаточной пластичностью и ударной вязкостью
- для повышения прочностных свойств легирование Cr
В качестве материалов для валов общемашиностроительного назначения
используют стали: сталь 45
Сталь конструкционная легированная
коленчатые и кулачковые валы
втулки и другие улучшаемые детали повышенной прочности.
Критерии выбора заготовки:
Материал - конструкционная легированная сталь 45.
Размерноая характеристика детали:
Точность неответственных размеров.
К детали предъявляются высокие технические требования по всем
поверхностям ( т. е. деталь обрабатывается со всех сторон).
Тип производства - серийный.
Обоснование выбора материала детали.
Механические свойства материалов.
В качестве материала заготовки выбираем сталь 45.
Химический состав в % материала сталь 45.
Выбор метода получения заготовки.
В качестве заготовки выбираем круглый сортовой прокат по ГОСТ 2590.
сборочный узел.cdw

Вероятностный метод:
МГТУ им. Н.Э. Баумана
Технологическая схема общей сборки.
Схема узловой сборки стакана.
Схема узловой сборки корпуса.
Схема узловой сборки блока зубчатых колес.
Расчет размерной цепи.
наладка.cdw

Оборудование: Токарный станок с ЧПУ модели 16А20Ф3
Операция 055: Круглошлифовальная.
Оборудование: Круглошлифовальный станок модели 3М151.
Операция 030. Шлицефрезерная.
Оборудование: Шлицефрезерный станок модели 5350
Неуказанные предельные отклонения размеров отверстий Н14
МГТУ им. Н.Э.Баумана
Схема установки чепвячной фрезы.