Строительство автомобильной дороги I категории с приготовлением теплых щебеночно-мастичных смесей при пониженных температурах воздуха (г. Белгород)




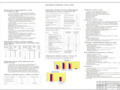
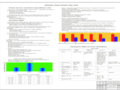
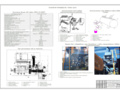
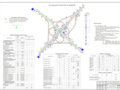
- Добавлен: 24.01.2023
- Размер: 25 MB
- Закачек: 1
Описание
Состав проекта
![]() |
![]() |
![]() ![]() ![]() |
![]() ![]() ![]() ![]() |
![]() |
![]() ![]() ![]() |
![]() |
![]() |
![]() ![]() ![]() ![]() |
![]() |
![]() ![]() ![]() |
![]() |
![]() ![]() ![]() |
![]() |
![]() ![]() ![]() ![]() |
![]() ![]() ![]() ![]() |
![]() ![]() ![]() |
![]() ![]() ![]() |
![]() ![]() ![]() ![]() |
![]() ![]() ![]() ![]() |
![]() ![]() ![]() ![]() |
![]() ![]() ![]() ![]() |
![]() ![]() ![]() ![]() |
![]() ![]() ![]() |
![]() ![]() ![]() |
![]() |
![]() ![]() ![]() |
![]() ![]() ![]() |
![]() ![]() ![]() ![]() |
![]() |
![]() ![]() ![]() |
![]() ![]() ![]() |
![]() ![]() ![]() ![]() |
![]() ![]() ![]() ![]() |
![]() ![]() ![]() ![]() |
![]() ![]() ![]() ![]() |
![]() |
![]() ![]() ![]() |
![]() ![]() ![]() |
![]() |
![]() ![]() ![]() ![]() |
Дополнительная информация
раздел4.РАЗРАБОТКА ТЕХНОЛОГИИ ПРИГОТОВЛЕНИЯ ЩЁБЁНОЧНО-МАСТИЧНОГО АСФАЛЬТОБЕТОНА..docx
В России оптимальные составы щебеночно-мастичных асфальтобетонных смесей впервые были регламентированы техническими условиями ТУ-5718.030.01393697-99[17] разработанными в Союздорнии. В зависимости от крупности применяемого щебня щебеночно-мастичные смеси и щебеночно-мастичный асфальтобетон подразделяются на следующие виды:
При размере зерен до 10 мм - ЩМА-10; до 15 мм - ЩМА-15; до 20 мм - ЩМА-20.
Указанные смеси рекомендуется применять для устройства верхних слоев покрытий толщиной соответственно от 3 до 6 см на автомобильных дорогах любых категорий и городских улицах в I-V дорожно-климатических зонах.
Было установлено что в структурном отношении щебеночно-мастичные асфальтобетонные смеси отличаются от других типов смесей настолько сильно что их можно отнести к самостоятельной группе дорожно-строительных материалов. Принципиальное различие обнаруживается уже на макроструктурном уровне при формировании минерального остова асфальтобетона. Если подбор зернового состава для большинства дорожных смесей основан на получении наибольшей плотности уплотненного материала то в ЩМАС этот принцип не действует.
Зерновые составы ЩМАС характеризуются высоким содержанием фракционированного щебня (порядка 70-80% по массе) который должен обладать улучшенной (кубовидной) формой зерен и предназначен для создания максимально устойчивого каркаса в уплотненном слое покрытия.
Чтобы лучше понять особенности структуры щебеночно-мастичного асфальтобетона проводилось сравнение его с асфальтобетоном типа А и с высоко плотным асфальтобетоном (ВПА).
Асфальтобетонные смеси специально готовили при различном содержании битумного вяжущего которое варьировали с шагом 05% от массы минеральной части чтобы установить оптимальный комплекс показателей физико-механических свойств каждого асфальтобетона. В результате лабораторных испытаний образцов было установлено что щебеночно-мастичный асфальтобетон судя по показателям физико-механических свойств занимает особое место. Пористость минерального остова ЩМА оказалась выше чем у асфальтобетона типа А и значительно больше пористости минерального остова высокоплотного асфальтобетона причем этот показатель увеличивается пропорционально содержанию битума в смеси.
Щебеночно-мастичный асфальтобетон характеризуется ростом пористости минерального остова от 16 до 18% по мере увеличения содержания вяжущего от 5 до 65%.
Повышение содержания битума приводит к снижению остаточной пористости любого асфальтобетона но у ЩМА этот процесс выражен в несколько раз слабее чем у плотного и высокоплотного асфальтобетонов.
При изменении содержания битума в смеси на 1% остаточная пористость изменяется на 5% у высокоплотного асфальтобетона на 3% у плотного асфальтобетона и всего на 1% у щебеночно-мастичного асфальтобетона. Аналогично изменяются и показатели водонасыщения асфальтобетонов Прирост водонасыщения вызванный снижением на 1 % содержания битума в смеси составляет 3% у асфальтобетона типа А и всего 1% у ЩМА.
Результаты испытаний показывают что структура ЩМА целенаправленна на раздвижку минерального остова и на присутствие в уплотненном материале слабоструктурированного и объемного битума. Более толстые пленки асфальтового вяжущего в щебёночно-мастичном асфальтобетоне приближают его к литому асфальтобетону однако по степени структурирования битума минеральным порошком содержанию щебня и по поровой структуре эти составы не сопоставимы. Присутствие объемного битума в ЩМА способствует увеличению его пластической деформативности при растяжении но в то же время приводит к резкому снижению когезионной прочности материала особенно при положительных температурах.
В результате показатели прочности при сжатии у щебеночно-мастичного асфальтобетона оказываются самыми низкими. Причем в зависимости от содержания битума прочность ЩМА не подчиняется правилу створа так как характерные пики прочности на этой зависимости не обнаруживаются. Максимум прочности у высокоплотного асфальтобетона обнаруживается при остаточной пористости 25% у асфальтобетона типа А - при 35% а у ЩМА максимум прочности не обнаруживается во всем регламентируемом диапазоне значений остаточной пористости.
Подобные зависимости были установлены и для показателя когезионного сцепления асфальтобетонов при сдвиге при 50°С. Этот показатель у щебеночно-мастичного асфальтобетона также значительно ниже чем у асфальтобетона типа А. Когезеонное сцепление ЩМА при сдвиге неуклонно снижается по мере повышения содержания вяжущего от 5 до 65% и экстремум этой зависимости также отсутствует.
Аналогичные данные позволяющие выделять щебеночно-мастичные асфальтобетоны по характеру структуры в самостоятельную группу дорожно-строительных материалов были получены и за рубежом. Исходя из высоких требований к сдвигоустойчивости дорожных и аэродромных покрытий низкий показатель когезионного сцепления щебеночно-мастичного асфальтобетона при сдвиге должен компенсироваться высоким и стабильным внутренним трением минерального остова. При правильно подобранном составе щебеночно-мастичный асфальтобетон обладает стабильно устойчивым минеральным остовом который формируется на основе одномерного кубовидного щебня.
Если у асфальтобетона типа А коэффициент внутреннего трения постоянно и существенно снижается по мере увеличения содержания вяжущего то у щебеночно-мастичного асфальтобетона он практически не зависит от содержания вяжущего и значительно выше по абсолютному значению. Поэтому низкий показатель когезионного сцепления щебеночно-мастичного асфальтобетона обусловленный более толстыми и менее структурированными пленками битума компенсируется более высоким и стабильным внутренним трением минерального остова в уплотненном материале. Это условие необходимое для обеспечения сдвигоустойчивости асфальтобетонов было принято за основу при обосновании требований к стандартным показателям физико-механических свойств в том числе к пределу прочности при сжатии при температуре 50°С.
Таким образом структура ЩМА оптимально сочетает максимальную жесткость в условиях трехосного сжатия и сдвигай одновременно максимальную податливость и высокую деформативность материала при растяжении. Исходя из условий напряженно-деформированного состояния дорожных покрытий при эксплуатации эти два противоположных качества асфальтобетона особенно важны.
2 Исследование свойств битума с добавками для теплого асфальтобетона
Показатели свойств битума БНД 6090 Московского НПЗ без добавок а также с добавками для теплого асфальтобетона приведены в таблице 4.2.1. Для жидких добавок расход в битуме составлял 1 и 2% от массы битума а для порошковой добавки Aspha-m для битума с добавкой Aspha-m для битума с добавкой Ворммикс Л при 25°С пенетрация снижается на 20% а при 0°С на 31%; для битума с добавкой Evotherm J1 пенетрация снижается на 24% при 25°С а при 0°С на 45%. Температура размягчения битума с жидкими добавками которая характеризует теплоустойчивость битума снижается для битума с Секабаз РТ 945 на 58% с Ворммикс Л на 87% с Evotherm J1 на 96% а для битума с 10% порошковой добавки Aspha-min увеличивается на 24%. Температура хрупкости битума с жидкими добавками уменьшается т. е. он переходит в хрупкое состояние при более высокой температуре. Для битума с добавкой Секабаз РТ 945 температура хрупкости повышается т. е. ухудшается на 386% с добавкой Ворммикс Л – на 363% а с добавкой Evotherm J1 на 41%. Адгезионные свойства битума характеризуют его сцепление с гранитным материалом фракции 2-5 мм после 30 минут кипячения смеси материала с битумом. Для битума без добавок и с добавками Aspha-min и Ворммикс Л сцепление характеризует образец №3 т. е. сцепление неудовлетворительное менее материала покрыта битумом после кипячения. Для битума с добавкой Секабаз РТ 945 сцепление характеризуется образцом №2 т. е. сцепление хорошее более поверхности материала покрыта битумом после кипячения для битума с 2% добавки Evotherm J1 достигается практически полное покрытие поверхности материала после кипячения т. е. сцепление соответствует образцу №1.
Таблица 4.2.1 Показатели свойств битума с добавками для теплого асфальтобетона
Наименование и количество добавки вводимой в битум
Температура размягчения по КиШ °С
Температура хрупкости °С
Сцепление с гранитным материалом фракции 2-5 мм
Битум БНД 6090 без добавок
Секабаз РТ 945 1% от массы битума
Aspha-min 5% от массы битума
Ворммикс Л 1% от массы битума
Evotherm J1 1% от массы битума
3 Подбор состава щебёночно-мастичного асфальтобетона
Целью проектирования ЩМА является создание оптимальной структуры асфальтобетона с заранее заданными свойствами которые должны обеспечить в конечном итоге требуемые характеристики устраиваемого дорожного покрытия. Сущность проектирования состава смеси состоит в выборе минеральных материалов и битумного вяжущего исходя из их физико-механических свойств а также в определении такого соотношения компонентов которое позволяет обеспечить оптимальную структуру асфальтобетона.
Выбор оптимального типа асфальтобетона и проектирование его состава в соответствии со свойствами исходных материалов характером автомобильного движения и климатическими условиями местности всегда являлись основными задачами строительства долговечных асфальтобетонных покрытий. Традиционно проектирование асфальтобетонной смеси сводится к подбору зернового состава минеральной части и определению оптимального содержания битума. Общие принципы проектирования составов смесей остаются неизменными в то же время подбор состава ЩМА имеет свои особенности.
Прежде чем проектировать состав горячей щебеночно-мастичной асфальтобетонной смеси необходимо назначить ее вид (по крупности применяемого щебня) исходя из проектной толщины устраиваемого слоя покрытия. Смеси ЩМА-10 рекомендуется применять для устройства слоев покрытий толщиной 2-4 см смеси ЩМА-15 - при толщине слоя 3-5 см и смеси ЩМА-20 - при толщине слоя 4-6 см. Для более тонких и более толстых слоев покрытий рекомендуется разрабатывать смеси другой крупности.
Процесс подбора оптимального состава ЩМАС можно разделить на три этапа.
На первом этапе в результате лабораторных испытаний определяют качество исходных минеральных материалов и битумного вяжущего чтобы установить соответствие показателей качества предъявляемым требованиям.
На втором этапе определяют рациональное соотношение содержания щебня песка из отсева дробления минерального порошка битума и стабилизирующей добавки в смеси обеспечивающее показатели свойств асфальтобетона удовлетворяющие требованиям ТУ-5718.030.01393697-99[17].
На заключительном этапе проводят технико-экономическое сравнение вариантов подобранных составов смесей отработку технологии приготовления смеси на асфальтобетонном заводе и при необходимости проводят корректирование состава по результатам пробной укладки и испытания проб смесей из пробных замесов в заводской смесительной установке.
Минеральную часть ЩМАС подбирают на основании предварительно установленных зерновых составов фракционированного щебня песка из отсева дробления и минерального порошка по предельным зерновым составам приведенным в табл. 4.3.1.
Таблица 4.3.1 Требования к зерновым составам ЩМАС
Содержание зерен % мельче данного размера мм
Примечания: 1. При приемосдаточных испытаниях допускается определять зерновые составы смесей по контрольным ситам в соответствии с данными выделенными жирным шрифтом. 2. С целью повышения шероховатости и износостойкости покрытия при воздействии колес с шипованными шинами допускается увеличивать содержание зерен крупнее максимального размера до 15%.
Во фракционном составе применяемого щебня основную часть должна составлять крупная фракция. Минеральную часть смеси подбирают таким образом чтобы кривая зернового состава расположилась в зоне ограниченной предельными кривыми. Подбор состава смеси рекомендуется осуществлять с помощью компьютерной программы или вручную.
Содержание любой фракции в минеральной смеси рассчитывают в зависимости от содержания смешиваемых компонентов и их зерновых составов по формуле
J - номер компонента;
n - количество компонентов в смеси;
аj - содержание j-ro компонента;
хij - содержание i-й фракции у j-ro компонента.
При подборе зернового состава смеси следует учитывать содержание зерен мельче 0071 мм в песке из отсева дробления и условия их частичного удаления из сушильного барабана системой пылеулавливания. При сухой системе пылеулавливания предусматривается дозирование циклонной пыли в смесительную установку вместе с минеральным порошком. При мокрой системе пылеулавливания удаленную из смеси пыль необходимо восполнить дополнительным содержанием минерального порошка.
Содержание битума и стабилизирующей добавки можно предварительно назначить на основании рекомендаций ТУ-5718.030.01393697-99[17] после чего в лаборатории готовят пробный замес асфальтобетонной смеси массой 3 кг. Пробу горячей смеси испытывают на стекание вяжущего.
При показателе стекания больше 02% увеличивают содержание стабилизирующей добавки на 005-01% или снижают содержание битума в смеси. При показателе стекания меньше 02% (рекомендуется от 01 до 015%) из приготовленной смеси формуют два-три образца уплотняя их вибрированием с последующим доуплотнением прессованием в соответствии с ГОСТ 12801-98[18]. Сформованные образцы взвешивают на воздухе и в воде после чего испытывают на водонасыщение. Определив среднюю и истинную плотность асфальтобетона и минеральной части рассчитывают остаточную пористость в образцах и пористость минерального остова. Если остаточная пористость не соответствует нормируемому значению то по полученным характеристикам вычисляют требуемое содержание битума Б (% по массе)
где Vм пор - пористость минеральной части % ;
Vопор - требуемая остаточная пористость асфальтобетона %;
р6 - истинная плотность битума гсм3;
рмm - средняя плотность минеральной части гсм3
С рассчитанным количеством битума вновь готовят смесь определяют показатель стекания вяжущего формуют два или три образца и снова определяют остаточную пористость и водонасыщение асфальтобетона. Если остаточная пористость и показатель водонасыщения будут находиться в заданных пределах то рассчитанное количество битума принимается за основу. В противном случае процедуру подбора содержания вяжущего основанную на приближении к нормируемому объему пор стандартно уплотненного асфальтобетона повторяют.
По последнему рецепту готовят большой замес смеси достаточный для изготовления необходимого количества образцов чтобы определить полный комплекс физико-механических свойств в соответствии с ТУ-5718.030.01393697-99[17] включая показатели сдвигоустойчивости ЩМА.
Если асфальтобетон из смеси подобранного состава не будет соответствовать требованиям этих технических условий пи каким-либо показателям то состав следует изменить. Например при неудовлетворительной прочности при 50°С рекомендуется увеличивать (в допустимых пределах) содержание минерального порошка или применить более вязкий битум; а при неудовлетворительных значениях предела прочности при 0°С - наоборот снизить содержание минерального порошка уменьшить вязкость битума или применить полимерно-битумное вяжущее взамен битума. В случае недостаточной водостойкости асфальтобетона рекомендуется увеличить содержание известнякового минерального порошка либо битума но в пределах обеспечивающих требуемые значения остаточной пористости и пористости минеральной части. Для повышения водостойкости эффективно применять добавки извести поверхностно-активные вещества (ПАВ) катионного типа и активированные минеральные порошки.
Подбор состава смеси можно считать завершенным если все показатели свойств образцов ЩМА будут отвечать предъявляемым требованиям.
4 Технические требования к ЩМА
Смеси асфальтобетонные щебеночно-мастичные и щебеночно-мастичный асфальтобетон должны отвечать предъявляемым требованиям.
Зерновой состав минеральной части ЩМАС приведен в табл. 4.3.1 где обязательные требования по контрольным ситам выделены жирным шрифтом. Показатели физико-механических свойств приведены в табл. 4.4.1.
Смеси должны выдерживать испытание на сцепление вяжущего с поверхностью зерен минеральной части определяемое по ГОСТ 12801-98[18]. Смесь также не должна расслаиваться и сегрегироваться при перевозке выгрузке и распределении асфальтоукладчиком. Показатель стекания вяжущего при расчетной технологической температуре не должен превышать 02%.
Температура ЩМАС при выпуске из смесителя и отгрузке потребителю должна соответствовать требованиям табл. 4.4.2.
Таблица 4.4.1Физико-механические свойства ЩМА
Наименование показателя
Нормы для дорожно-климатических зон
Пористость минерального остова %
Остаточная пористость %
Водонасыщение % по объему:
в лабораторных образцах
в кернах из покрытия не более
Предел прочности при сжатии МПа при температурах не менее:
Коэффициент внутреннего трения tg φ не менее
Сцепление при сдвиге МПа (50°С 50 мммин) не менее
Предел прочности на растяжение при расколе МПа (0°С 50 мммин)
Водостойкость при длительном водонасыщении не менее
Примечание: При использовании полимерно-битумных вяжущих допускается снижать нормы сцепления при сдвиге и предела прочности на растяжение при расколе на 20%.
Таблица 4.4.2 Требования к температуре горячей щебеночно-мастичной асфальтобетонной смеси
Марка вяжущего по глубине проникания иглы при 25°С
Температура смеси °С
Примечание. В случае применения поверхностно-активных веществ или активированных минеральных порошков температуру нагрева минеральных материалов допускается снижать на 10-20°С.
5 Расчёт состава асфальтобетонной смеси
Расчет содержания щебня песка и минерального порошка по данным гранулометрического состава минеральной смеси.
Расчет содержания щебня крупнее 5 мм принимаем количество щебня 67 %. Поскольку зерен крупнее 5 мм в щебне содержится 9054 % то щебня требуется: Щ=679054100 =74 %.
Определяем что частиц мельче 0071 мм во всей минеральной части асфальтобетона должно быть в пределах 10-15 %. Для расчета принимаем 10 %. Если в МП содержится 704 % частиц мельче 0071 мм то минерального порошка должно быть в смеси: МП= 10704100 =14%
П=100-(Щ + МП) =100-(74 + 14) = 12 %.
необходимого количества в смеси каменных материалов :
минерального порошка – 14 % ;
Затем определяют содержание каждой фракции в соответствии с гранулометрическим составом применяемых: щебня песка минерального порошка
и содержания их в запроектированной смеси в таблице на чертеже лист 6.
Расчет содержания битума в асфальтобетоне по битумоемкости минеральных составляющих график зернового состава минеральной части состав смеси физико-механические показатели асфальтобетонной смеси также показаны на чертеже лист 8.
6 Выбор технологического оборудования для введения добавок
Щебеночно-мастичный асфальтобетон приготовляли в смесительных установках периодического действия соответственно путем смешивания в нагретом состоянии щебня песка из отсевов дробления минерального порошка и битума а также добавки в виде пропитанных битумом и спрессованных гранул из волокон целлюлоз хризотил асбеста и др. Добавки вводили в смеситель АБЗ на разогретый каменный материал до или вместе с минеральным порошком производя "сухое" перемешивание в течение 15-20 секунд. При последующем перемешивании смеси с битумом добавка равномерно распределяется в объеме асфальтового вяжущего вещества.
Вводимая в смеситель добавка вначале дозировалась вручную. Однако для уменьшения вероятности ошибки и снижения трудоемкости потребное количество добавки от 02 до 045 % или 20 -45 кг на 1 т смеси необходимо дозировать с допускаемой погрешностью + 5 % используя специальные дозирующие системы объемного или весового типа. Дозирование добавки может осуществляться автоматически из силосной башни или контейнера. При использовании системы объемного дозирования добавка из контейнера или силосной башни объемом 3 - 4 м3 через роторное дозирующее устройство поступает в пневматический конвейер и по трубопроводу подачи диаметром 150 мм подается в циклон с встроенной загрузочной воронкой и датчиком наличия материала. Далее добавка через автоматический клапан выпускного отверстия попадает в трубопровод подачи материала в смеситель.
Система весового дозирования отличается от объемной тем что добавка из контейнера или силосной башни с помощью шнекового конвейера сначала подается в весовой бункер где дозируется а уже затем поступает в трубопровод пневматического конвейера.
Дальнейшая схема прохождения материала аналогична системе объемного дозирования. В обеих системах дозирования в нижней части контейнера или силосной башни монтируется датчик контроля прохождения материала который автоматически включает вибратор установленный на нижней наклонной стенке контейнера или силосной башни при возможном отсутствии материала. Вибратор побуждает добавку перемещаться в контейнере или силосной башне в случае его зависания.
Технологический процесс изготовления теплой ЩМАС предусматривает обязательность применения добавок. Качество получаемой ЩМА смеси во многом зависит от обеспечения равномерной подачи в смеситель требуемого количества подаваемой гранулированной добавки стабильности и равномерности ее подачи.
Указанные требования к подаче добавок реализуются при дооснащении асфальтосмесительных установок дополнительными дозирующими устройствами. Эти установки специально разработаны для дозирования и подачи в мешалку асфальтосмесительной установки добавок при производстве щебеночно-мастичного асфальтобетона.
Конструкция установок обеспечивает возможность монтажа при дооснащении действующих производств и новых асфальтосмесительных установок в течение 1-2 дней
7 Технология приготовления асфальтобетонной смеси
Каменные материалы с помощью фронтальных погрузчиков подаются со склада в агрегат питания бункера которого имеют питатели для непрерывного предварительного грубого дозирования составляющих фракции каменных материалов (щебня и песка). Дозируемые материалы поступают в загрузочное устройство сушильного барабана с помощью ленточного транспортера. В сушильном барабане каменные материалы высушиваются и нагреваются до температуры 100-1200С что выше необходимой заданной температуры смеси (60-800С). Сушильный барабан снабжен топкой с форсункой. Высушенные и нагретые каменные материалы с помощью "горячего" элеватора подают в сортировочный агрегат где с помощью грохота осуществляется их сортировка по фракциям и подача в "горячие" бункера с отсеками а негабаритные материалы диаметр которых больше размеров самой крупной фракции сбрасываются в бункер негабарита. Из отсеков "горячего" бункера каменные материалы поступают в весовой бункер дозировочного отделения. Отдозированные песок и щебень каждого замеса из весового бункера поступают в смеситель. Минеральный порошок из силосной емкости попадает в бункер дозатора минерального порошка и после дозирования соответствующей порции с помощью шнека в смеситель. Силосная емкость загружается пневмотранспортом из цементовозов. Из обогреваемых битумных цистерн (битумохранилища) подогретый до температуры 900С битум подается насосной установкой по обогреваемому битумопроводу в нагревательную установку где обезвоживается и нагревается до за счет нагревателя жидкого теплоносителя а затем в дозирующее устройство из которого отдозированная порция битума подается в смеситель. После этого все компоненты смеси тщательно перемешиваются и готовая смесь выгружается либо непосредственно в кузов автомобиля-самосвала либо в ковш скипового подъемника. Для исключения прилипания смеси к внутренним поверхностям скипового подъемника и кузовов автомобилей-самосвалов предусмотрена система опрыскивания этих поверхностей распыленной струей дизельного топлива. При просушивании и нагреве песка и щебня в сушильном барабане выделяется большое количество мелких и крупных фракций пыли и несгоревших частиц жидкого топлива. Дымовые газы выходящие из сушильного барабана очищаются с помощью различных систем пылеочистки которые как правило имеют две ступени. Дымовые газы поступают в пылеулавливающую систему первая ступень очистки которой состоит из группы циклонов. Уловленная циклонами крупная пыль поступает при помощи винтового конвейера для пыли в элеватор для пыли и минерального порошка или в зависимости от крупности в сушильный барабан. С помощью дымососа предварительно очищенные газы подаются во вторую ступень мокрой очистки а затем в дымовую трубу. Уловленная мелкая пыль из системы мокрой очистки удаляется с помощью очистного устройства.
Теплые щебеночно-мастичные асфальтобетонные смеси приготавливают на обычных асфальтобетонных заводах оборудованных смесителями принудительного перемешивания путем смешения в нагретом состоянии щебня песка из отсевов дробления минерального порошка битума или полимерно-битумного вяжущего а также добавок для теплого асфальтобетона.
В процессе приготовления щебеночно-мастичной асфальтобетонной смеси необходимо как можно более точно выдерживать проектный состав подобранный в лаборатории. Погрешность дозирования компонентов при приготовлении смеси не должна превышать для щебня ±2% минерального порошка и битума±15% добавки волокон ±5% от массы соответствующего компонента.
Добавку вводят как правило в битум. Она призвана исключить отслоение и стенание вяжущего при хранении и транспортировании горячей смеси улучшить однородность и физико-механические свойства ЩМА а также снизить температуру приготовления смеси.
Спецификой теплой щебеночно-мастичной асфальтобетонной смеси является в частности более низкая по сравнению с обычными асфальтобетонными смесями температура приготовления.
Технологический процесс приготовления смеси в смесителях периодического действия включает следующие основные операции:
- подготовку минеральных материалов (подачу и предварительное дозирование высушивание и нагрев до требуемой температуры пофракционное дозирование);
- подачу холодных минерального порошка и стабилизирующей добавки дозирование их перед подачей в смеситель;
- подготовку битума (разогрев и подачу при необходимости из битумохранилища в битумоплавильню выпаривание содержащейся в нем влаги и нагрев до рабочей температуры в необходимых случаях введение поверхностно-активных веществ и других улучшающих добавок дозирование перед подачей в смеситель);
- «сухое» перемешивание горячих минеральных материалов с холодным минеральным порошком и стабилизирующей добавкой;
- перемешивание минеральных материалов с битумом и выгрузку готовой асфальтобетонной смеси в накопительный бункер или автомобили-самосвалы.
Технологический процесс приготовления смеси в смесителях непрерывного действия отличается отсутствием отдельного дозирования горячих минеральных материалов и объединением нагрева и перемешивания минеральных материалов с битумом и стабилизирующей добавкой в одном сушильно-смесительном барабане.
Фракционированный щебень и песок из отсева дробления подают от места складирования к агрегату питания ленточными транспортерами или фронтальными погрузчиками.
Щебень и песок необходимо складировать раздельно на площадке с укрепленным основанием обеспечивающим хороший водоотвод. Площадка складирования материалов должна иметь разделительные стены высотой не менее 3 м для исключения перемешивания щебня различных фракций и песка между собой. Агрегаты питания оборудуют весовыми или объемными дозаторами для предварительного дозирования холодных и влажных минеральных материалов. Из агрегатов питания минеральные материалы поступают в барабан сушильного агрегата где они просушиваются и нагреваются до соответствующей температуры.
Температура нагрева смеси песка и щебня должна быть примерно на 25-30°С выше требуемой температуры готовой асфальтобетонной смеси. Если минеральные материалы перед поступлением в сушильный барабан имеют высокую влажность то добиваться их высушивания и нагрева следует не за счет увеличения подачи топлива в форсунку а в результате уменьшения подачи влажных материалов в сушильный агрегат. В случае применения поверхностно-активных веществ или активированных минеральных порошков температуру нагрева минеральных материалов рекомендуется снижать на 10-20оС.
Нагретые щебень и песок подаются из сушильного барабана по сортировочно-дозирующее устройство где горячий минеральный материал с помощью системы виброгрохотов разделяется по фракциям которые размешаются в отдельных отсеках бункера. Из бункеров в которых накапливаются горячие материалы они поступают в весовой бункер-дозатор. Дозирование фракционированных горячих материалов осуществляется по массе. Минеральный порошок дозируется в холодном состоянии с помощью общего весового дозатора или с помощью отдельных весов с более высокой точностью взвешивания.
Дозируемое содержание фракционированных горячих материалов в смеси назначают исходя из проектного зернового состава смеси подобранного в лаборатории.
Окончательное содержание дозируемых фракций рекомендуется уточнять по результатам испытаний пробного замеса смеси полученного на конкретной смесительной установке при заданной ее производительности. Циклонную пыль из системы пылеулавливания допускается подавать в смесительную камеру в полном объеме взамен части минерального порошка.
Продолжительность перемешивания смеси определяется техническими параметрами смесительной установки степенью изношенности лопастей смесителя и в конечном итоге должна обеспечивать равномерное распределение всех компонентов включая волокна и полное обволакивание дискретных зерен минерального материала битумом.
Приготовленную асфальтобетонную смесь из смесителя выгружают в скиповый подъемник с последующим перемещением ее в накопительный бункер или непосредственно в кузов автомобиля-самосвала для транспортирования к месту укладки. Использование накопительного бункера в качестве временного склада для хранения теплых асфальтобетонных смесей позволяет обеспечивать ритмичность выпуска смесей независимо от наличия транспортных средств изменения режимов укладки и погодных условий а также сократить время загрузки автомобилей-самосвалов и повысить производительность АБЗ. В накопительном бункере рекомендуется ограничивать время хранения щебеночно-мастичной асфальтобетонной смеси не более 1 ч.
Внешне ЩМАС не проявляют признаков сегрегации. Тем не менее их рекомендуется загружать в кузова автомобилей-самосвалов как и обычные смеси в несколько приемов по длине кузова чтобы предотвратить возможность сегрегации. Кузова автомобилей-самосвалов должны быть чистыми. Перед погрузкой их нужно обрабатывать специальными составами предотвращающими прилипание смеси к днищу например мыльным раствором масляной или керосиновой эмульсией кремнийорганической жидкостью и т.п.
Асфальтобетонная смесь загруженная в автомобили-самосвалы должна закрываться на период транспортирования защитными тентами. Дальность транспортирования смеси зависит от ее термоизоляции и условий охлаждения.
Количество автомобилей-самосвалов должно быть достаточным для обеспечения непрерывной укладки смеси заданным темпом который должен быть согласован с производительностью асфальтобетонного завода.
8 Устройство верхнего слоя покрытия толщиной 5 см из теплого щебеночно-мастичного асфальтобетона ЩМА-15
Работы выполняются с помощью асфальтоукладчика «Титан-8820» работающего в автоматическом режиме по натянутой струне катка двухвальцевого САТ СВ-534D гладковальцовых катков DD 138-HFA.
В состав работ рассматриваемых технологической картой входят:
- укладка щебёночно-мастичной асфальтобетонной смеси;
- уплотнение щебёночно-мастичной асфальтобетонной смеси.
Температура асфальтобетонных смесей при выпуске из смесителя должна быть в пределах 135-150 градусов С. Эффективное уплотнение достигается при температуре смеси в начале уплотнения 125-145 градусов.
Район строительства находится в III дорожно-климатической зоне.
Покрытие устраивать только в сухую погоду. Укладку теплой смеси следует производить при температуре окружающего воздуха не ниже -10°С . Перед укладкой смеси за 1-6 часов необходимо произвести обработку поверхности нижнего слоя битумной эмульсией жидким битумом или вязким битумом нагретым до температуры 130°С из расчёта 03 лм2. Обработку нижнего слоя покрытия можно не производить если интервал времени между устройством нижнего и верхнего слоёв составляет не более 2-х суток и отсутствует движение построечного транспорта.
Работы по устройству верхнего слоя асфальтобетонного покрытия выполняются в такой последовательности:
- подготовка основания;
- распределение асфальтобетонной смеси по поверхности нижнего слоя покрытия;
- уплотнение смеси катками.
После установки копирной струны для работы асфальтоукладчика в автоматическом режиме его устанавливают в исходное положение и готовят к укладке смеси.
Поднимают боковые стенки приёмного бункера осматривают шнек и трамбующий брус устанавливают шиберные заслонки на задней стенке бункера в положение обеспечивающее необходимую толщину асфальтобетонной смеси над скребковыми питателями.
С помощью управления автоматическими системами стабилизации угла поперечного уклона и слежения за ровностью покрытия в продольном направлении устанавливают раму с рабочими органами в необходимое для работы положение и контактируют щуп слежения со струной.
Выглаживающую плиту устанавливают в рабочее положение подложив под неё на основание доску или рейку толщина которой на 10-15 % превышает проектную толщину укладываемого слоя и опускают выглаживающую плиту так чтобы между плитой и доской не было просветов и был выдержан необходимый поперечный профиль покрытия. Угол атаки выглаживающей плиты 2-3 %.
Перед загрузкой асфальтобетонной смеси в авто-самосвал кузов должен быть обработан мыльным раствором или известковой суспензией. Жидкость наносится равномерно на стенки и дно кузова
Асфальтобетонную смесь подвозят к асфальтоукладчику автомобилями-самосвалами.
Автомобили-самосвалы подают к приёмному бункеру укладчика задним ходом до касания колёсных упорных валиков укладчика закреплённых на поперечной балке впереди бункера. Смесь выгружают в приёмный бункер укладчика в процессе выгрузки автомобиль-самосвал перемещается вместе с укладчиком.
Кузов автомобиля-самосвала после окончания разгрузки очищают от остатков смеси лопатой с удлинённой ручкой и подают сигнал на отъезд автомобиля самосвала.
Выгруженная в бункер питателя смесь скребковыми питателями подаётся к шнеку и распределяется по всей полосе укладки.
Трамбующим брусом размещённым за шнеком смесь частично уплотняется и обрабатывается выглаживающей плитой.
Скорость передвижения асфальтоукладчика устанавливают в зависимости от особенностей смеси темпа её подвоза и погодных условий.
Хорошее качество укладки смеси (достаточное уплотнение трамбующим брусом ровная поверхность) обеспечивается при малых скоростях передвижения укладчика. При больших скоростях передвижения укладчика в уложенном слое могут появиться разрывы трещины неровности поверхности пустоты по краям.
В процессе работ для получения непрерывной и ровной полосы необходимо следить за равномерным поступлением смеси к шнеку и её распределением.
Смесь к асфальтоукладчику должна подаваться непрерывно. При кратковременных перерывах в доставке смеси асфальтоукладчик останавливают оставляя часть смеси в бункере до подхода следующего автомобиля-самосвала со смесью.
В прохладную погоду (при температуре воздуха ниже 15°С) следят за тем чтобы выглаживающая плита прогревалась обогревателем.
Толщину слоя контролируют мерником. Если толщина слоя смеси имеет отклонения от заданной изменяют положение выглаживающей плиты асфальтоукладчика.
Ровность покрытия проверяют дюралюминиевой рейкой укладываемой вдоль и поперёк полосы. На возвышениях смесь слегка разрыхляют граблями излишки смеси срезают лопатой. Во впадины смесь добавляют рассыпая её тонким слоем. Места значительных просадок слегка разрыхляют граблями а затем заполняют смесью. При укладке необходимо добиваться такой ровности чтобы под рейкой положенной в любом месте в продольном и поперечном направлениях не было просвета.
Внутренний край уложенной полосы выравнивают с помощью режущего диска по прямой линии. Перед проходом укладчика выровненный край смежной полосы прогревают а затем смазывают горячим битумом. В жаркую погоду когда смесь в местах сопряжения остаётся горячей прогревание не обязательно.
Для создания хорошего продольного стыка между асфальтобетонными полосами при работе одного асфальтоукладчика удерживающий щит асфальтоукладчика должен заходить на соседнюю полосу так чтобы на ней образовалась полоса горячей смеси шириной не более 10-20 см. Это обеспечивает укладку достаточного количества асфальтобетонной смеси по линии стыка чтобы можно было произвести правильную укатку без разравнивания избыточного количества смеси. Высота нового слоя асфальтобетонной смеси над уровнем уплотнённой соседней полосы должна быть больше с учётом коэффициента уплотнения.
В конце рабочего дня или при перерывах в работе на длительное время делают рабочий шов. Для этого поперёк полосы закрепляют доску смесь укладывают до доски и затем укатывают её. При возобновлении работы доску убирают торец полосы прогревают прогревателями или горячим битумом. Дальнейшую обработку поперечного шва осуществляют так же как и продольного.
Ровность уложенного полотна в области стыка проверяют с помощью прямоугольной рейки располагаемой поперёк стыка. Прямоугольную рейку кладут на уложенное полотно так чтобы она нависала над ранее уложенным полотном. Высота нависания линейки над уплотнённым полотном должна соответствовать величине на которую уменьшится толщина только что уложенного слоя при его укатке. Проверку с помощью прямоугольной рейки следует провести повторно после укатки полотна.
Укатку начинают продольными проходами катков от края полосы с постепенным смещением проходов к середине покрытия а затем от середины к краям с перекрытием следов на 20-30см. При уплотнении первой полосы необходимо следить за тем чтобы вальцы катка не приближались более чем на 10 см к кромке обращённой к оси дороги. Первые проходы при уплотнении второй полосы необходимо выполнить по продольному сопряжению с ранее уплотнённой полосой. При наезде на свежеуложенную полосу каток должен двигаться ведущими валами вперёд.
Для обеспечения ровности покрытия в процессе уплотнения каток должен трогаться плавно без рывков. Нельзя останавливать каток на недоуплотнённом покрытии. При вынужденной остановке каток следует вывести на укатанную и уже остывшую полосу.
В начале уплотнения рекомендуется соблюдать скорость движения катков в пределах 15-20 кмчас а после пяти-шести проходов по одному следу её необходимо увеличить:
- для моторных катков с гладкими вальцами до 3-5 кмчас;
- для катков на пневмошинах до 5-8 кмчас.
Прилипание смеси к пневмошинам прекращается при их нагреве до рабочей температуры смеси. Время нагрева незначительно. Во избежание остывания шин допускаются только непродолжительные остановки каика вне полосы укатки.
Укатку заканчивают когда после прохода тяжёлого катка на покрытии не остаётся заметного следа. Окончательное заключение о степени уплотнения смеси даёт лаборатория после испытания взятых из укатанного слоя проб.
После окончания уплотнения дефектные места (жирные сухие раковины и т.п.) вырубают тщательно очищают края смазывают жидким горячим битумом заменяют новой доброкачественной асфальтобетонной смесью и укатывают.
Покрытие должно иметь ровную поверхность выровненные по шнуру кромки хорошо заделанные сопряжения полос и не выходить за пределы допускаемых от проектных размеров отклонений.
Работы по устройству асфальтобетонного покрытия выполняет бригада в составе 11 человек:
Машинист асфальтоукладчика 6 разряд - 1
Помощник машиниста 5 разряд - 1
Машинисты катков 6 разряд - 1
Асфальтобетонщики 5 разряд - 1
Разбивочные работы и работы по установке копирной струны выполняет звено которое в состав бригады не включают.
Работу бригады организуют следующим образом.
Машинист асфальтоукладчика управляет машиной регулирует подачу смеси к шнеку с помощью шиберных заслонок следит за тем чтобы трамбующий брус был всегда в работе и выглаживающая плита при необходимости прогревалась.
Помощник машиниста находится у приёмного бункера. Он подаёт сигнал на подход автомобилей-самосвалов и визуально проверяют качество смеси в процессе работы следит за положением выглаживающей плиты проверяет качество натяжения копирной струны. В конце рабочей смены помогает машинисту в очистке машины.
Асфальтобетонщики (5 4 3 и 2 разряд) следуют за асфальтоукладчиком и окончательно обрабатывают поверхность уложенного слоя кромки и швы сопряжения полос а также исправляют дефектные места покрытия.
Асфальтобетонщик 5 разряда является старшим в бригаде и отвечает за общее количество работ. Он принимает участие в работе по отделке поверхности покрытия и проверяет качество асфальтобетонной смеси правильность обработки основания битумом контролирует толщину слоя и регулирует положение выглаживающей плиты асфальтоукладчика даёт указание машинистам катков о режиме укатки. После укатки покрытия осматривает готовый участок и даёт указание об устранении дефектов.
Асфальтобетонщик 4 разряда контролирует ровность покрытия и поперечные уклоны заделывает сопряжение полос.
Асфальтобетонщики 3 и 2 разряда выполняют работы по обрубке кромок в местах сопряжений прогревают их разогревателями или горячей смесью смазывают горячим битумом обрабатывают кромки покрытия и выполняют другие вспомогательные работы.
лист2. конструкция дорожной одежды.dwg

Изоляция битумной эмульсией
Примечания: 1. Поперечные профили земполотна разработаны согласно ТМ 503-0-47.86 "Поперечные профили автомобильных дорог
проходящих по населенным пунктам". 2. Конструкция дорожной одежды разработана согласно ОДН 218.046-01 3. Дорожная одежда запроектирована для III дорожно-климатической зоны. 4. Дренажные прорези устраиваются в шахматном порядке через 20 м шириной 2
м на участках вогнутых кривых и на участках с уклоном до 20. 5. Для сцепления покрытий по типу 1 и по типу 2
после выравнивания укладывается геосетка полимерная ПСД (50х50 - 40х40) шириной 1
Проект производства работ по строительству автомобильной дороги I технической категории
Проектирование автомобильной дороги
Конструкция дорожной одежды
Изм. Кол.уч.Лист Дата
Руководит. Соломенцев
ГОСУНИВЕРСИТЕТ-УНПК" АСИ кафедра "САД
ДП 2012 270205 070755 АД и А
заключение.docx
Экологическая эксплуатационная безопасность дороги обеспечена.
Принятые в рабочем проекте технические решения соответствуют СниП 2.07.01-89* СниП 2.05.02-85 и СниП 2.05.03-84*.
Принятые технология и оборудование строительные решения и организация производства соответствуют новейшим достижениям отечественной и зарубежной науки и техники.
Строительство автодороги обеспечит реализацию перспективных транспортных связей круглогодичное удобное непрерывное и безопасное движение автомобилей с расчётными скоростями и нагрузками позволит сократить затраты на перевозки грузов и пассажиров потери от дорожно-транспортных происшествий. В перспективе строительство дороги позволит улучшить межрайонные и межобластные транспортные связи Белгородской области.
Щебеночно-мастичная асфальтобетонная смесь применяющаяся при строительстве дороги находит все более широкое применение в большинстве стран при устройстве верхних слоев дорожных и аэродромных покрытий обеспечивая устойчивые показатели ровности шероховатости и сцепления в процессе эксплуатации в том числе в условиях интенсивного и большегрузного движения транспортных средств. Покрытия ЩМА характеризуются сдвигоустойчивостью при высоких температурах деформативностью и трещиностойкостью при низких температурах водо- морозостойкостью и устойчивостью к эрозии в условиях повышенной влажности и знакопеременных температур.
Исходя из стоимости материалов производство щебеночно-мастичной асфальтобетонной смеси обходится на 30-40% дороже производства асфальтобетонных смесей типа А вследствие использования большего количества битума щебня высокого качества и применения стабилизирующей добавки из натуральных целлюлозных волокон. Однако использование добавок для теплого асфальтобетона позволяет снизить энергозатраты на приготовление ЩМАС. Также если рассматривать не только процесс приготовления смеси но и возможность ее укладки более тонким слоем эксплуатационные и прочие затраты а также повышение долговечности уложенного слоя то применение ЩМАС становится экономически оправданным. Большая долговечность и меньшая подверженность различным разрушениям по сравнению с альтернативными материалами приводят в долгосрочном рассмотрении к уменьшению вложенных инвестиций даже при большей изначальной стоимости ЩМАС.
Чтобы получить максимальную отдачу от применения ЩМАС очень важно правильно подобрать ее состав и в соответствии с технологическими регламентами изготовить и уложить в покрытие. Соблюдение этих правил является основной гарантией долговечности и качества асфальтобетонных покрытий устраиваемых па достаточно прочных дорожных основаниях.
В нашей стране щебеночно-мастичные асфальтобетонные смеси начали применять для устройства верхних слоев дорожных покрытий начиная с 2000 г. Преимущества эксплуатационного состояния опытных участков покрытий способствовали ускоренному внедрению ЩМАС на дорогах России. Теплые смеси еще не получили широкого распространения не только в России но и в мире. Можно надеяться что рассматриваемый материал найдет достойное место в номенклатуре дорожных смесей и поможет дорожникам России решать государственные задачи связанные с повышением сроков службы и эксплуатационного состояния дорожных покрытий и безопасности дорожного движения.
лист15. мероприятия по охране окружающей среды.dwg

Наименование параметра
Расчетная интенсивность транспортного потока
для прогноза загрязнения атмосферного воздуха
Ежегодный темп роста интенсивности потока
Азимут направления ветра
Принятая экспертом скорость ветра
Приходящая солнечная радиация
Плотность почвенного слоя
Фоновая концентрация загрязнения по СО
Фоновая концентрация загрязнения по NO
Предельно-допустимая концентрация СО
Предельно-допустимая концентрация NOх
Предельно-допустимая концентрация CmHn
Предельно-допустимый уровень шума
Характеристики покрытия
мелкозернистый асфальтобетон
Характеристики поперечного профиля
Ширина разделительной полосы
Экологические характеристики до защиты на Пк 12
Концентрация токсичного вещества
Слева от оси на расстоянии
Справа от оси на расстоянии
Распределение концентрации токсичных веществ
Экологические характеристики до защиты на Пк 13
Экологические характеристики до защиты на Пк 14
Экологические характеристики после защиты на Пк 12
Экологические характеристики после защиты на Пк 13
Экологические характеристики после защиты на Пк 14
Расстояние от дороги до санитарной зоны по шуму
Расстояние от дороги до санитарной нормы по шуму
Параметры защитного экрана
Наименование параметра защитного экрана
Пикет начала защитного экрана
Пикет конца защитного экрана
Расстояние от оси полосы движения до экрана
Горизонтальная проекция откоса экрана
Расст. от оси полосы движения до объекта защиты
Высота объекта защиты над поверхностью дороги
Проект производства работ по строительству автомобильной дороги I технической категории
Безопасность жизнедеятельности
Мероприятия по охране окружающей среды
Изм. Кол.уч.Лист Дата
Руководит. Соломенцев
Консульт. Дмитровская
ГОСУНИВЕРСИТЕТ-УНПК" АСИ кафедра "САД
ДП 2012 270205 070755 АД и А
введение.docx
Интересы дальнейшего развития дорожного строительства нашей страны требуют существенного повышения качества и долговечности асфальтобетонных покрытий. Эта задача помимо дальнейших исследований может быть решена лишь при более полном использовании научных достижений и накопленного опыта а также существенном повышении технического уровня строительства асфальтобетонных покрытий. В дипломном проекте при строительстве автодороги внедряется применение теплой щебёночно-мастичной асфальтобетонной смеси (ЩМАС). Щебеночно-мастичные асфальтобетонные смеси завоевали популярность в Европе в качестве материала дорожных покрытий на дорогах с большой интенсивностью движения в аэропортах и морских портах а также стали распространяться по всему миру. Щебеночно-мастичные асфальтобетонные покрытия характеризуются комфортабельностью и безопасными ездовыми качествами а их текстура отличается шероховатостью и способностью поглощать шум при движении транспортных средств. Жесткая скелетная структура из щебня обуславливает прекрасную сопротивляемость слоя пластическим сдвиговым деформациям а наличие большого количества битумного вяжущего который заполняет пространство между каменным материалом делает щебеночно-мастичный асфальтобетон (ЩМА) более долговечным материалом.
Процесс приготовления и укладки ЩМАС технологичен экономичен и не требует каких-либо специальных дополнительных устройств. Покрытие имеет прекрасные эксплуатационные характеристики долговечно.
В странах где достаточно долго применяли щебеночно-мастичные асфальтобетонные смеси определили что для получения хорошего качества покрытия необходимо чтобы смесь была тщательно подобрана по составу а укладка и уплотнение были произведены в соответствии с технологическим регламентом на высоком техническом уровне.
Горячую асфальтобетонную смесь приготавливают на вязких битумах и традиционно производят при температурах 140 - 160°С. В этом диапазоне температур каменный материал является сухим (его температура может достигать 180°С и вязкость битума понижена до такого уровня при котором он покрывает щебень смесь является достаточно подвижной и удобообрабатываемой для ее равномерного перемешивания и последующего перемещения в накопительный бункер или силос.
За последние 10 лет в Европе а затем в США появились новые технологии позволяющие понизить температуру перемешивания асфальтобетонной смеси приготавливаемой на вязком битуме (с пенетрацией 40 - 130) на 20 - 40°С без ухудшения прочностных характеристик покрытия по сравнению с традиционным горячим асфальтобетоном приготовленным на тех же битумах. Это достигается за счет относительно новых физико-химических эффектов приводящих к снижению сопротивления смеси сдвигу во время ее приготовления и укатки. Обычный диапазон приготовления таких смесей от 105 до 125 С. Их применение позволяет снизить энергозатраты уменьшить выбросы загрязняющих веществ в атмосферу и запах сопровождающий укладку горячей асфальтобетонной смеси снизить интенсивность старения вяжущего увеличить радиус возки и продлить строительный сезон.
В целом новые технологии теплого асфальтобетона показывают следующие преимущества:
- снижение энергозатрат на 15 - 30 % при приготовлении асфальтобетонной смеси на вязком битуме за счет уменьшения температуры;
- замедление остывания смеси при транспортировке (теплые смеси остывают медленнее горячих) и обусловленное этим увеличение дальности возки;
- уменьшение выброса вредных веществ в атмосферу (углекислого газа – на 30% дыма и пылевидных отходов – на 50 - 60 %) уменьшение неприятного запаха при укладке асфальтобетона и температуры в зоне производства работ (что существенно в городских условиях);
- продление строительного сезона за счет улучшения удобообрабатываемости смеси и возможности ее уплотнения при пониженных температурах воздуха;
- уменьшения термоокислительного старения битума вследствие снижения температур приготовления и укладки смеси что повышает сопротивление асфальтобетона усталости и появлению трещин при охлаждении.
Пока доля теплых смесей в Европе не превышает 1 % от производства асфальтобетонных смесей и период наблюдений за их поведением в эксплуатации еще недостаточен для твердого суждения об их перспективах.
доклад.docx
Запроектированная автомобильная дорога располагается в Белгородской области к юго-западу от города Белгород и соединяет поселки Таврово Соломино Разумное. Она является частью системы кольцевых дорог областного центра призванной разгрузить город и вывести на новый уровень внутрирайонные внутриобластные и международные перевозки.
Автодорога «Таврово-Соломино-Разумное» соответствует первой технической категории имеет протяженность 10 км включая мост через Белгородское водохранилище длиной 556 м трасса имеет 20 углов поворота подробная ведомость которых располагается на 1 листе.
Дорога включает две проезжих части по две полосы движения в каждую сторону шириной 35 м между которыми располагается разделительная полоса для улучшения внешнего вида покрытая тротуарной плиткой шириной 23 м. Одна из проезжих частей проходит по существующей дороге на ней устраивается нижний слой покрытия из горячей пористой крупнозернистой асфальтобетонной смеси I марки толщиной 10 см и верхний слой покрытия из щебеночно-мастичной асфальтобетонной смеси толщиной 5 см. Конструкция дорожной одежды проезжей части строящейся с нуля состоит из суглинка укрепленного 7% цемента марки 20 щебеночно-песчаной смеси С4 и трех слоев асфальтобетона а именно: верхнего слоя основания толщиной 8 см из пористого крупнозернистого марки II нижнего слоя покрытия (6 см) из пористого крупнозернистого марки I и верхнего слоя покрытия (5 см) из щебеночно-мастичного асфальтобетона.
Работы по строительству автомобильной дороги проводятся в течение 12 месяцев. Подготовительные работы ведутся в течение первых пяти месяцев параллельно проводятся работы по возведению земляного полотна устройству дорожной одежды и велосипедной дорожки которые продолжаются 11 месяцев. На заключительном этапе строительства в последние 4 месяца дорога обустраивается: устанавливаются дорожные знаки ограждения автопавильоны и наносится разметка проезжей части.
Стоимость всех работ составляет 2576309340 рублей. Стоимость одного километра автодороги при этом исключая мост (994304000 рублей) равна 168012 460 рублям.
Материалы для детально изученного теплого щебеночно-мастичного асфальтобетона поступают по железной дороге до станции Разумное а именно: щебень фракций 10-15 и 5-10 мм со станции Гайворон отсев гранитный фракции 0-5 мм из города Павловск минеральный порошок со станции Гурово битум нефтяной дорожный 6090 из города Москва. Присадка адгезионная дорожная Амдор-10 привозится по автомобильной дороге из Санкт-Петербурга.
Все вышеперечисленные материалы соответствуют требованиям нормативных документов: щебень – ГОСТ 8267-93 отсев – ГОСТ 8736-93 минеральный порошок – ГОСТ Р52129-2003 битум – ГОСТ 22245-90 все добавки – требованиям соответствующих технических условий.
Теплые асфальтобетоны начали использовать для строительства еще во второй половине XXI века. Тогда для их приготовления использовали битумы разжиженные керосином креазотовым маслом и другими веществами. Укладывали такие смеси при температурах от 40 до 80 градусов. Из-за длительного испарения разжижающих веществ формирование уложенных слоев происходило в течение нескольких недель что приводило к нарушению ровности покрытия. Но уже тогда показатели плотности теплых смесей были значительно выше чем горячих.
В настоящее время для приготовления теплых смесей используются добавки. Они снижают вязкость асфальта за счет физико-химических эффектов. Применение таких добавок позволяет снизить энергозатраты уменьшить выбросы загрязняющих веществ в атмосферу и запах сопровождающий укладку смеси снизить интенсивность старения вяжущего уменьшить трещинообразование при охлаждении слоя обеспечить более легкое формирование стыков увеличить радиус возки продлить строительный сезон ускорить открытие движения.
Для исследования были взяты четыре добавки представленные на российском рынке: Ворммикс Л (производство – Италия) – вязкая жидкость темного цвета Секабаз РТ 945 (Франция) – светло-желтая жидкость Evotherm J1 (США) – жидкость янтарного темного цвета и Aspha-min (Германия) – порошок белого цвета фракций 0-09 мм и 0-20 мм. Для оценки влияния добавок на уплотняемость щебеночно-мастичной асфальтобетонной смеси ЩМАС использовалась смесь крупностью до 15 мм соответствующая ГОСТ 31015-2002.
Состав смеси: щебень гранитный фракции 10-15 мм – 43% щебень гранитный фракции 5-10 мм – 30% отсев гранитный фракции 0-5 мм – 14% минеральный порошок – 13% стабилизирующая добавка СД-3 – 03% от массы минеральной части стабилизирующая добавка РТЭП – 03% от массы минеральной части битум БНД 6090 – 60% от массы минеральной части смеси.
Для жидких добавок расход в битуме составлял 1 и 2% от массы битума а для порошковой добавки Aspha-min расход в битуме составлял 03 и 06% от массы смеси или 5 и 10% от массы битума. Глубина проникания иглы (пенетрация) характеризующая вязкость битума с введением добавок снижается т. е. вязкость битума с добавками возрастает. Температура размягчения битума с жидкими добавками которая характеризует теплоустойчивость битума снижается на 5-10% а для битума с 10% порошковой добавки Aspha-min увеличивается на 24%. Температура хрупкости битума с жидкими добавками уменьшается т. е. он переходит в хрупкое состояние при более высокой температуре. Адгезионные свойства битума характеризуют его сцепление с гранитным материалом фракции 2-5 мм после 30 минут кипячения смеси материала с битумом. Для битума без добавок и с добавками Aspha-min и Ворммикс Л сцепление характеризует образец №3 т. е. сцепление неудовлетворительное менее материала покрыта битумом после кипячения. Для битума с добавкой Секабаз РТ 945 сцепление характеризуется образцом №2 т. е. сцепление хорошее более поверхности материала покрыта битумом после кипячения для битума с 2% добавки Evoterm J1 достигается практически полное покрытие поверхности материала после кипячения т. е. сцепление соответствует образцу №1.
Предварительное формование асфальтобетонных образцов ЩМАС-15 без добавок для теплого асфальтобетона диаметром 714 мм проводилось при нагрузке на образец 16 тонн в течение 3 минут. Температура ЩМАС-15 в ходе предварительного формования принималась равной 160°С. Средняя плотность пяти полученных образцов составила 240 гсм3 водонасыщение 245% предел прочности при сжатии водонасыщенных образцов при 20°С составил 365 МПа. Далее определили минимальную нагрузку на образец при формовании при которой достигается плотность полученная в ходе предварительного формования она составила 10 тонн. Для предварительной оценки влияния температуры уплотнения на показатели свойств асфальтобетонных образцов уплотнение провели при 140 120 100 80 и 60°С. Оказалось что средняя плотность образцов при температуре формования ниже 120°С составляет 237гсм3 водонасыщение при этом снизилось незначительно а значения предела прочности при сжатии не изменились при дальнейших испытаниях образцы формовались при температурах 80 и 60°С. Для оценки влияния времени уплотнения образцов на их свойства время уплотнения было уменьшено до 15 минут. Формование образцов проводилось также с усилием Р=10 тонн и при температурах от 140°С до 60°С. Оказалось что за 15 минуты образцы успевают уплотниться так же как и за 3 минуты а показатели водонасыщения и прочности не меняются. Поэтому при дальнейшем изготовлении образцов время уплотнения составляло 15 минуты. При предварительном формовании были выбраны следующие параметры: нагрузка 10 тонн температура 80 и 60°С время 15 минуты. Введение в смесь добавки Амдор-10 не улучшает уплотняемость ЩМАС-15 при температуре 80°С. Введение добавок Ворммикс Л или Evoterm J1 улучшают уплотняемость на 001 гсм3 введение Секабаз РТ 945 позволяет получить среднюю плотность как у образцов при уплотнении при высокой температуре 160°С т. е. 240 гсм3 а введение добавки Aspha-min при 5% в смеси не изменяет среднюю плотность образцов а при 10% в смеси наоборот снижает ее на 003 гсм3. Введение в смесь добавки Амдор-10 не улучшает уплотняемость ЩМАС-15 и при температуре 60°С. Введение добавки Ворммикс Л повышает среднюю плотность образцов на 001 гсм3 введение добавок Секабаз РТ 945 и Evoterm J1 повышают на 002 гсм3 а введение порошка Aspha-min снижает среднюю плотность на 006 гсм3 при расходе 10% от массы битума. Таким образом основываясь на вышеприведенных данных для исследований длительной водостойкости были взяты добавки Ворммикс Л Секабаз РТ 945 и Evotherm J1.
При определении длительной водостойкости образцы испытывались на прочность и водонасыщение на первые пятнадцатые сорок пятые и шестидесятые сутки. Самая высокая прочность наблюдается у образцов с добавкой Унирем-001 – с 304 МПа на первые сутки она уменьшилась до 266 МПа на шестидесятые сутки. На втором месте по показателям прочности образцы с добавками РТЭП СД-3 и Амдор-10 их показатели 272 и 277 МПа соответственно. Далее по убывающей следуют образцы с добавками: 1) РТЭП СД-3 и Evotherm 2) РТЭП СД-3 и Секабаз РТ 945; 3) РТЭП и на последнем месте образцы с добавками РТЭП СД-3 и Ворммикс Л с показателями 212 и 110 МПа.
Показатели водонасыщения варьируются от 216 % у образцов с добавками РТЭП СД-3 и Ворммикс Л до 370 % – у образцов с добавкой Унирем-001 на первые сутки. И от 317 % – у образцов с добавками: 1) РТЭП СД-3 и Секабаз РТ 945 и 2) РТЭП СД-3 и Амдор-10 до 453 % – у образцов с добавкой Унирем-001 на шестидесятые сутки.
При приготовлении теплых смесей на АБЗ предусмотрены следующие линии подачи добавок. Жидкие добавки из приемной емкости объемом 250 л с помощью битумного насоса по трубопроводу закачиваются в битумную цистерну где перемешивается с битумом насосом-смесителем. Гранулированные и порошковые добавки через дозатор могут поставляться как непосредственно в смеситель из бункера накопления добавки так и в бункер с минеральным порошком.
При устройстве покрытий из теплых асфальтобетонов технология сохраняется. Меняется только температура уплотнения смеси. Она снижается на 20-40 градусов т. е. начало укатки производится при температуре 100-140 а окончательное уплотнение – при температуре 80-100 градусов.
Контроль качества при приготовлении теплых ЩМАС и устройстве из них конструктивных слоев дорожной одежды помимо операций выполняемых при использовании горячих смесей включает в себя дозирование добавок для теплых асфальтобетонов и контроль погодных условий: температура воздуха при укладке не ниже -10 градусов.
При обустройстве автомобильной дороги для обеспечения безопасного движения установлено 90 основных дорожных знаков и 50 дополнительных. На проезжей части нанесена размета в количестве 388 м2 – осевая и 1942 м2 – краевая.
При исследовании вредных факторов при строительстве выявлены нарушения допустимого уровня шума. Для его снижения установлен защитный барьер высотой 50 м на расстоянии 60 м от оси трассы. После его установки все показатели транспортного шума не превышают установленных норм. Для снижения уровня шума при эксплуатации дороги предусмотрена посадка лиственных деревьев в четыре ряда на расстоянии 60 м от края дороги.
Мой доклад окончен благодарю за внимание=)))
лист12. технология устройства оснований и покрытий из теплых ЩМАС.dwg

Подготовительные работы
Укладка щебеночно-мастичной
асфальтобетонной смеси
Уплотнение щебеночно-мастичной
укладка щебеночно-мастичной
Автосамосвал КАМАЗ-55111
Асфальтоукладчик ТИТАН 8820
Температура эффективного
уплотнения легким катком
уплотнения основным катком
окончательного уплотнения
Определение температуры эффективного уплотнения теплых асфальтобетонных
Схема укладки асфальтобетона
смесей на различных этапах работы звена дорожных катков
Температура смеси в начале уплотнения
плотного асфальтобетона
высокопористого асфальто-
бетонов с содержанием
плотного асфальтобетона ти-
пористого асфальтобетонов
с содержанием щебня (гравия)
Температура смеси в начале уплотнения для горячих и теплых смесей
(из СНиП 3.06.03-85 Табл. 14)
Проект производства работ по строительству автомобильной дороги I технической категории
Технология и организация строительного производства
Технология устройства оснований и покрытий из теплых ЩМАС
Изм. Кол.уч.Лист Дата
Руководит. Соломенцев
Консульт. Соломенцев
ГОСУНИВЕРСИТЕТ-УНПК" АСИ кафедра "САД
ДП 2012 270205 070755 АД и А
лист7. способы получения теплых смесей.dwg

Изменение технологии приготовления асфальтобетонных смесей
Теплая смесь по методике Шелл-Коло Вейдеке: смешивание в два этапа - обволакивание мягким битумом при
низкой температуре + пена из твердого битума
Изменение технологии процесса - снижение производительности
Использование двух типов битума
Применение для незагруженных дорог
Низкоэнергетический процесс Леако: смешение в 2 этапа
введение влажного песка на горячий крупный
покрытый битумом щебень
в результате чего образуется пар
вспенивающий битум для улучшения
Изменение технологии процесса
Необходимость использования добавок
Использование добавок
в битум снижает его вязкость
способствуя обволакиванию и росту технологичности
Введение парафинов - риск ухудшения низкотемпературных характеристик
Твердение парафинов при 100 С исключает использование процесса при t 100 С
удаление воды при контакте с
переводящим тепло в механическую энергию пара с образованием пены для
Модификация процесса (нужны специальная емкость и подающее оборудование)
Высокая стоимость цеолитов
Сильное воздействие производства цеолитов на окружающую среду
Технология Mead Westvac: на АБЗ производится ввод эмульсии вместо чистого битума при температуре
Необходимость эмульсионной установки
Дополнительные расходы на эмульсию
Использование воды: необходимость эмульгирования
затем необходимость испарения
Проблемы адгезии щебня при контакте с водой
Секабаз РТ 945 от СЕКА:
ввод в битум 2-5 кгт
улучшает обволакивание и технологичность смеси вне зависимости от процесса
так и при непрерывном вводе добавки
Дает эффект без модификации процесса как на циклических
так и на непрерывных заводах
Допускает модификацию процесса
При повышении температуры обеспечивает производственный процесс в плохую погоду и допускает
длительную транспортировку
Увеличивает производительность АБЗ
Свести к минимуму наличие взвешенных частиц в воздухе на рабочем объекте
Избежать неприятного запаха при укладке в городах
Уменьшить производственные затраты
Увеличить транспортный радиус и время транспортирования смесей
Укладывать также зимой
Облегчить укладку с вязкими битумами
Создать дорожную поверхность хорошего качества
в других раствор-лях
в ароматических соеди-
) продукт реакции кон-
продукт реакции кон-
порошок белого цвета
Понижение вязкости асфальта (не битума) при высоких температурах
Измерение скручивающего усилия от веса битумной смеси при постоянной скорости смешивания
Горячая смесь: производство при 150 С
смешивание при 160 С
Теплая смесь: производство при 120 С
смешивание при 100 С
Улучшение уплотняемости при снижении температуры
Совместим со всеми типами вяжущего
Позволяет увеличить время транспортировки и производить укладку при отрицательных температурах
Улучшает работоспособноть смеси и облегчает процесс уплотнения (в т. ч. с применением вторичного асфальта)
Не изменяет температуру размягчения битума
Отсутствие необходимости в предварительном смешивании с вяжущим
Отсутствие серьезных работ по модификации АБЗ
Не требуется увеличения времени смешивания
Evotherm J1 - инновационная комплексная присадка к битумам
Легкость обращения со смесями в процессе их применения
Полученные преимущества и характеристики проверены практическим применением
Высокая эффективность процесса смешения при пониженных температурах для широкого спектра каменных материалов
при использовании крошки фрезерования
Более высокое допускаемое содержание в смеси крошки фрезерования без обратного влияния на требования
применяемому вяжущему
прерывистых составов и составов открытого типа
так и для порционных АБЗ
Снижение выбросов дымовых газов (включая летучие углеводороды
практически наполовину
Снижение загазованности рабочих зон - влияние на рабочий персонал на заводе и при укладке на дороге
Обеспечение лучшей степени уплотнения смесей по сравнению со стандартными смесями при температуре завершения уплотнения
Характеристики добавок для теплого асфальтобетона
Экологические преимущества технологии EVOTHERM: содержание вредных веществ в воздухе рабочей зоны
При производстве горячих смесей
При производстве теплых смесей с Evotherm J1
Проект производства работ по строительству автомобильной дороги I технической категории
Технология и организация строительного производства
Способы получения теплых смесей
Изм. Кол.уч.Лист Дата
Руководит. Соломенцев
Консульт. Соломенцев
ГОСУНИВЕРСИТЕТ-УНПК" АСИ кафедра "САД
ДП 2012 270205 070755 АД и А
раздел1.АНАЛИЗ ИСХОДНЫХ ДАННЫХ И ПРИРОДНЫХ УСЛОВИЙ РАЙОНА.docx
1.1 Природные условия района строительства
Обследуемый участок расположен в юго-западной части Белгородской области на территории Белгородского района и согласно приложения 1 СНиП 2.05.02-85[1] относится к третьей дорожно-климатической зоне. Климат обусловливается сложным комплексом факторов. Важнейшие из них — географическая широта и общая циркуляция атмосферы. Изменение погоды в значительной степени зависит от ветров. Ветры возникают из-за беспрерывного изменения барометрического давления. Воздух притекающий с Атлантического океана зимой вызывает повышение температуры (наступает мягкая пасмурная погода со снегопадами временами оттепелями) а весной — похолодание облачность осадки. Воздух с Арктики вызывает зимой сильные морозы осенью — ранние а весной — поздние заморозки.
В теплое время года когда ось Воейкова (от Харькова через Валуйки Алексеевку и далее в сторону Саратова) ослабевает область попадает под влияние азиатского материка. В это время часто дуют суховеи юго-восточные ветры которые в короткое время иссушают почву.
Среди отдельных элементов климата самое большое значение имеет температура воздуха. Средняя годовая температура воздуха колеблется от +59°С до + 66°С. Максимальные значения ее достигают 41°С а абсолютные минимумы падают до —38°С. Годовая амплитуда температуры воздуха — 79°С.
В самом теплом месяце года (июле) средние температуры составляют 183—212°С а в самом холодном месяце (январе) — от минус 72° до 92С. Почва промерзает и прогревается на 1 метр. В мерзлом состоянии она обычно находится с последних дней декабря до конца марта.
Характерной особенностью температурного режима является сумма среднесуточных температур когда она превышает 10°. Для района строительства она составляет в среднем 2450°С – 2700°С. Продолжительность солнечного сияния равна 1800 часам. Теплая погода весной способствует интенсивному росту растений. Однако в этот период возможны возвраты холодов особенно в начале мая которые вызываются вторжением арктического воздуха и последующим выхолаживанием земли.прекращения заморозков в воздухе на открытом месте приходится на начало мая.
В среднем за год выпадает от 420 до 590 мм осадков. Количество осадков по годам неодинаково. Были года когда их сумма возрастала до 700—750 мм а в другое время выпадало только 260—300 мм.
Неустойчивость выпадения осадков приводит к засухам. Засухи и суховейные явления слабой и средней интенсивности на территории района бывают ежегодно. Интенсивные засухи наблюдаются раз в 40—90 лет а очень интенсивные были отмечены в 1938 1946 1954 1972 годах. Наибольшее число дней с засухой (9—14) падает на июнь.
Устойчивый переход средней суточной температуры воздуха через 0° осенью происходит в середине ноября. Зима устанавливается не сразу. Чаще в начале зимы погода неустойчива со сменой морозных дней оттепелью и попеременным установлением и сходом снежного покрова. С наступлением морозов в начале декабря образуется постоянный снежный покров.
Переход от зимы к весне начинается в марте. Лето продолжительное. Обычно стоит жаркая погода. Пасмурных дней мало. Осень как и весна непродолжительна.
Снежный покров в районе строительства лежит не более ста дней. Безморозный период длится 155—165 дней. Для этого района характерна небольшая влагообеспеченпость.
Район работ представляет собой несколько приподнятую равнину (200 м над уровнем моря) по которой проходят юго-западные отроги так называемого Орловско-Курского плато Среднерусской возвышенности. Современная поверхность района равнинная расчленённая многочисленными речными долинами и густой овражно-балочной сетью носит в целом волнисто-балочный.
1.3 Растительность и почвы
Область отражает черты северной лесостепи для которой характерно чередование лесов с луговой степью. Естественные леса занимают 2463 тыс. гектара - 125 % территории области. Лесные массивы представлены дубами берёзами клёнами ясенем тополем и акацией. Степи большей частью распаханы. Почвенный покров района представлен чернозёмами и тёмно-серыми лесными почвами склонов балок.
1.4 Гидрологические условия
Автомобильная дорога пересекает Белгородское водохранилище объем которого составляет 76 млн. м3. При пересечении его дорогой запроектирован мост длиной 556 м.
Расчетные расходы воды весеннего половодья и ливневого стока вероятностью превышения 1% (дорога I технической категории) определены по формуле предельной интенсивности рекомендованной в качестве основной - для данной части территории с использованием данных наблюдений на изученных реках исследуемого района опубликованных в официальных документах Росгидрометах. Результаты расчётов подтверждают достаточность водопропускной способности существующих сооружений.
Грунтовые воды залегают глубоко и не оказывают влияние на строительство и эксплуатацию автомобильной дороги.
1.5 Геологическое строение
Геологическое строение района представлено фундаментом из кристаллических пород докембрия залегающего на абсолютных отметках 300-500 м ниже уровня моря и толщей осадочных пород. Непосредственно на кристаллическом фундаменте залегает известняк далее между отметками 250-400 м и 140-180 м ниже уровня моря залегают песчано-глинистые отложения. Выше залегает меловая толща верхнемеловых отложений.
2 Технико-экономическая характеристика района.
В технико-экономической части инженерного проекта рассмотрены современное состояние и перспективы развития экономики района тяготения направления характер перевозок и их объемы обоснована перспективная интенсивность движения.
2.2 Характеристика экономики района тяготения
Автомобильная дорога общего пользования «Таврово-Соломино-Разумное» протяжением 10км расположена в юго-западной части Белгородской области. Она относится к территориальным дорогам.
Этот участок является частью системы кольцевых дорог областного центра призванной разгрузить город и вывести на новый уровень внутрирайонные внутриобластные и международные перевозки.
Белгородская область входит в состав Центрального федерального округа (ЦФО) Российской Федерации. Исходя из направленности экономики и тесных хозяйственных связей с областями Черноземья область была включена наряду с другими восьмью областями в ассоциацию экономического взаимодействия «Черноземье». По производству промышленной и сельскохозяйственной продукции Белгородская область занимает в ассоциации одно из первых мест. Денежные расходы и доходы населения области одни из самых высоких.
Площадь территории области – 271 тыс. км2. Численность населения по результатам Всероссийской переписи населения 2010 года составила 1 532670 человек в том числе городского – 1 013 059 (661%). Белгородская область относится к густонаселенным территориям и плотность населения составляет - 565 чел.км2.
Белгородчина — высокоразвитый индустриально-аграрный регион экономика которого опирается на колоссальные богатства недр и уникальные чернозёмы.
Среди промышленных предприятий области:
- Старооскольский завод металлоконструкций "Стройметаллком
- Старооскольский завод пластмасс «Осколпласт»
- Оскольский электрометаллургический комбинат
- Стойленский горно-обогатительный комбинат
- Лебединский горно-обогатительный комбинат
- Оскольский завод металлургического машиностроения
Земельные угодья составляют 27134 тыс. га более 70 % которых — чернозёмы. На душу населения приходится 143 га сельхозугодий в том числе пашни — 11 га Естественные леса и лесопосадки занимают 2483 тыс. га — 125 % территории области. Общие запасы древесины — 343 млн м³.
В 2012 году область вышла в лидеры производства мяса свинины и птицы среди всех регионов России.
Белгородская область традиционно имела и имеет крепкие связи с экономикой и агропромышленным комплексом соседней Украины. Несмотря на небольшие размеры на область приходится пятая часть современного товарооборота РФ и Украины.
2.3 Транспортная сеть района тяготения
Белгородская область обладает мощным производственным потенциалом поэтому назрела необходимость реконструкции и строительства автодорог и мостов. Федеральная целевая программа «Развитие транспортной системы России (2010 – 2015 гг.)» определяет развитие дорожной отрасли основным документом определяющим в настоящее время параметры финансирования дорожной отрасли до 2030 г является «Транспортная стратегия Российской Федерации на период до 2030 года». В рамках распоряжением Правительства РФ от 22 ноября 2008 г. № 1734-р. «Транспортная стратегия РФ на период до 2030 года» осуществляется строительство автодорог в Белгородской области. Существующая сеть автомобильных дорог общего пользования Белгородской области являющаяся составной и неотъемлемой частью развития экономики призвана совместно с транспортными средствами наиболее полно удовлетворять потребности населения в безопасных грузовых и пассажирских перевозках.
По состоянию на 1 января 2011 года общая протяженность автомобильных дорог общего пользования области составляет 7 1240 км из которых имеют твёрдое покрытие 6 5694 км (92%). На сегодняшний день большая часть дорог входящих в опорную сеть дорог Белгородской области и построенных 40-50 лет назад исчерпала свой ресурс и не справляется со своими функциями. Из-за возросшей в разы интенсивности и значительного увеличения нагрузок на ось дорожная одежда разрушается и текущий ремонт не даёт должного эффекта. Белгородская область в рейтинге аварийности оказалась на 63-м месте из 81 субъекта РФ попавшего в исследование. Антилидером страны стала Тува где показатель гибели на дорогах составляет 271 человек на тысячу автомобилей (для сравнения в Белгородской области – 07). Реже всего участники дорожного движения гибнут в Приморском крае (033 человек на тысячу машин). На 74-м месте Белгородская область по количеству пострадавших на тысячу автомобилей (65) в официально зарегистрированные ДТП попадают 458 машин из тысячи (74-е место). В восьмом десятке регион и по такому важнейшему критерию как «число ДТП совершённых пьяными водителями на тысячу автомобилей» (022). Однако смертность в ДТП на десять происшествий (153) в Белгородской области достаточно высока – 26-е место в России. Общее количество погибших в 2010 году – 236 человек (41-е место) пострадавших – 2 195 (47-е место).
Плотность дорог на тысячу квадратных километров территории области составляет 2626 километров. Потребность областного дорожного хозяйства в котором трудятся более шести тысяч работников в асфальтобетонных смесях обеспечивают 62 асфальтобетонных смесителя. На автомобильных дорогах общего пользования сооружено 420 мостов и путепроводов общей протяженностью 170545 погонных метров.
В области уделяется большое внимание обеспечению нормативного транспортно - эксплуатационного состояния автомобильных дорог это достигается путём соблюдения утверждённого комплекса работ по их содержанию и своевременному ремонту. В связи с тем что 70% конструкций дорожных одежд построенных в 60-80 годы рассчитаны на осевую нагрузку в 6 тонн в то время как большинство грузовых автомобилей и автобусов имеет фактическую нагрузку от 8 до 10 тн и выше одним из наиболее важнейших вопросов развития автодорожной инфраструктуры является
реконструкция существующих территориальных автомобильных дорог.
2.4 Объемы перевозок и интенсивность движения
2.4.1 Объемы перевозок
В соответствии с рассмотренными сценариями развития производительных сил района тяготения ожидаются различные темпы роста объемов перевозок по проектируемой автодороге.
При первом оптимистическом варианте предполагается рост объема грузоперевозок к расчетному сроку по 43% в среднем за год при втором – умеренно-оптимистическом – 40% и при третьем – пессимистическом – по 35%.
Транспортные связи осуществляемые по участку дифференцируются на транзит – 115% межобластные – 438% межрайонные – 181% внутрирайонные – 266%.
В грузонапряженности проектируемого участка важную роль имеют межрайонные перевозки (553%) поскольку дорога дает возможность для такого рода транспортного сообщения.
Объемы перевозок пассажиров по проектируемому участку определены по результатам анализа транспортных потоков с использованием следующих транспортно-эксплуатационных показателей автопарка:
Перевозки пассажиров в отчетном году составят 5612 тыс. человек в том числе: легковым автотранспортом 313 тыс. человек автобусами - 2482 тыс. человек. Наиболее вероятный ожидаемый на 20-ти летную перспективу общий объем пассажирских перевозок исходя из роста численности населения увеличения степени его подвижности дальнейшего улучшения транспортного обслуживания пассажиров и других факторов составит 13403 тыс. человек в том числе легковым транспортом 8249 тыс. человек – 553% автобусами 6899 тыс. человек – 447%. Темпы роста пассажиропотоков – 41% в год.
2.4.2 Перспективная интенсивность движения
где Q - объем перевозок грузов по перегону тыс. тонн;
Кн – коэффициент учета необъемных перевозок и дальнего транзита 12;
Кс - коэффициент учета в составе движения спецавтомобилей 115;
Т – число дней работы дороги в течение года – 365;
q – средняя грузоподъемность автомобиля на 2025-2030 года – 74-75тн;
– коэффициент использования грузоподъемности – 093-095;
γ – коэффициент использования пробега – 063-065.
Интенсивность движения пассажирского транспорта на перспективу определена на основе анализа существующего парка прогнозируемого роста автопарка роста численности населения и его подвижности. Принятые в расчетах на перспективу эксплуатационные показатели работы автотранспорта:
Наименование показателей
Средняя вместимость одного автомобиля чел
Коэффициент использования вместимости
Коэффициент использования пробега
Прогноз интенсивности движения проведен по двум вариантам расчетных условий с темпами прироста интенсивности соответствующими оптимистическому и умеренно-оптимистическому (рекомендуемому) сценариям развития экономики.
По оптимистическому прогнозу интенсивность движения на перспективу по проектируемому участку дороги соответствует среднему ежегодному темпу роста 55%. Среднегодовые темпы роста интенсивности по умеренно-оптимистическому прогнозу по видам транспорта прогнозируются в следующих размерах:
грузовые автомобили - 40%;
легковые автомобили - 60%;
Исходя из анализа существующей интенсивности состава и направления движения автотранспорта в учетных местах следует что после завершения строительства объездной автомагистрали перспективная интенсивность движения по ней в 2031 году составит 12 800 автомашинсутки в том числе:
-грузового автотранспорта 3 840 автомашинсутки;
-легкового автотранспорта 8 320 автомашинсутки
-пассажирского автотранспорта 640 автомашинсутки
Интенсивность движения пассажирского автотранспорта на перспективные годы определена на основе анализа существующего движения планируемого роста автопарка роста численности населения в районе тяготения и его подвижности.
В соответствии с перспективной интенсивностью движения требованиями СНиП 2.05.02-85[1] проектируемый участок должен иметь технические нормативы дорог I категории.
3 Технические параметры автодороги
Исходя из нормативной интенсивности движения в транспортных единицах и в приведенных к легковому автомобилю с учетом развития экономики в соответствии с техническим заданием на разработку РП техническими нормами и требованиями СНиП 2.07.01-89*[2] в рабочем проекте минимальные значения элементов плана поперечного и продольного профиля приняты по параметрам дороги I технической категории с регулируемым движением с расчетной скоростью 120 кмчас.
Основные технические параметры приведены ниже:
Параметры элементов дороги
Расчетная скорость кмчас 1200
Число полос движения 4
Ширина проезжей части м 2x75
Ширина укрепительной полосы м 075
Ширина разделительной полосы м 5
Ширина укрепленной полосы на разделительной полосе м 1
Поперечный уклон %о 20
Наибольший продольный уклон %о 40
- кривой в плане м 800
- выпуклой кривой м 15000
- вогнутой кривой м 5000
Наименьшее расстояние видимости:
- для остановки м 250
- встречного автомобиля м 450
На своем протяжении трасса имеет 20 углов поворота. Принятые параметры круговых кривых соответствует нормативным требованиям и подобраны таким образом чтобы обеспечить максимально возможные радиусы кривых в плане зрительную ясность и плавность проектируемой дороги.
Основные технические показатели плана трассы:
протяженность трассы – 997 км
протяженность трассы по воздушной линии – 845 км
коэффициент удлинения – 118
минимальный радиус – 900
количество углов поворота – 20
протяженность кривых – 446658 м
протяженность прямых вставок – 550555 м.
раздел3.ДОРОЖНО-СТРОИТЕЛЬНЫЕ МАТЕРИАЛЫ И ИХ СВОЙСТВА.docx
Минеральный порошок применяемый для приготовления ЩМАС должен отвечать требованиям ГОСТ 16557-78[7]. При использовании активированного минерального порошка следует принимать во внимание что он может оказывать пластифицирующее действие которое проявляется в снижении показателей сцепления при сдвиге и прочности при сжатии.
Стандартный минеральный порошок для асфальтобетонных смесей приготавливается при помоле известняка или доломита в специальных мельницах. Однако при соответствующем технико-экономическом обосновании допускается применять в качестве минерального порошка не только пыль из системы пылеулавливания (зерна из отсевов дробления горных пород мельче 016 мм) но и другие техногенные отходы промышленного производства (золы уноса цементную пыль и т.п.). Пригодность порошкообразных отходов промышленности в качестве минерального порошка должна обосновываться соответствующими лабораторными испытаниями как самого порошка так и образцов ЩМА приготовленных на его основе.
Минеральный порошок является одним из важнейших компонентов асфальтобетона выполняющим две функции: а) заполняет пустоты песчано-щебеночного каркаса и повышает плотность минерального остова; б) превращает нефтяной битум при смешении с ним в прочное асфальтовое вяжущее вещество являющееся тем клеем который объединяет зерна песка и щебня в плотный и прочный монолит.
Суммарная поверхность зерен минерального порошка в смеси минеральных материалов составляет 85 - 90% всей их поверхности и битум в асфальтобетоне взаимодействует главным образом с поверхностью минерального порошка обволакивая его зерна тонкими слоями в которых контактный слой ориентированного битума обладает повышенной вязкостью прочностью и теплоустойчивостью по сравнению со свободным битумом заполняющим 65 - 70% межзерновых пустот в асфальтобетоне.
Для успешного выполнения этих функций минеральный порошок должен обладать комплексом свойств. При смешивании с битумом в асфальтобетонных смесях минеральный порошок не должен комковаться и образовывать агрегаты. Сцепление битума с поверхностью зерен минерального порошка должно быть настолько прочным чтобы вода не отслаивала битум в течение всего нормативного срока службы асфальтобетона в покрытии.
Физико-химическое взаимодействие между поверхностью зерен минерального порошка и битумом должно быть достаточно сильным для ориентации молекул в тонком слое битума однако при этом порошок не должен ускорять процесс старения битума.
Минеральный порошок повышает прочность асфальтобетона но вместе с тем увеличивает его хрупкость поэтому содержание минерального порошка в смеси должно быть предельно минимальным достаточным лишь для придания асфальтобетону нормативной плотности и прочности. Повышение массовой доли минерального порошка сверх необходимого минимума понижает трещиностойкость покрытий и как правило приводит к повышению “жирности” смесей.
При избыточном содержании минерального порошка в смеси даже небольшая ошибка в дозировании битума в сторону его увеличения (что неизбежно в производственных условиях) резко снижает сдвигоустойчивость покрытий.
Для приготовления асфальтобетонных смесей в качестве минерального порошка применяют тонкоизмельчённые известняки и доломиты прочность которых при дробимости должна быть не меньше 200 а также известняковые и доломитовые асфальтовые породы и основные металлургические шлаки.
При приготовлении минерального порошка из известняков и доломитов полученных после второй и третьей стадий дробления требования к ним по прочности не предъявляют. Материалы используемые для приготовления минерального порошка должны быть чистыми не содержащими загрязняющих и глинистых примесей более 5%. В смесях II и III марок смесях для нижнего слоя покрытий и слоя основания можно применять порошки из кислых горных пород и пылевидные отходы промышленности (зола каменного угля сланцевая зола цементная пыль) при соответствии их требованиям ГОСТ 9128 – 97[4].
Минеральный порошок повышенного качества получают путем активации поверхности зерен при дроблении. Активация заключается в том что свежеобразованные поверхности известняка обрабатывают небольшим количеством активирующей смеси состоящей из битума и поверхностно-активного вещества. Соотношение масс битума и поверхностно-активного вещества принимают в пределах 1:111. Общее количество активирующей смеси составляет от 15 до 25% к массе минерального порошка.
Сцепление активирующей смеси со свежеобразованной поверхностью зерен порошка настолько прочно что водостойкость асфальтобетона повышается. Увеличиваются также плотность и прочность асфальтобетона.
Активированный минеральный порошок гидрофобен он не намокает поэтому его транспортирование и хранение облегчаются.
Связи возникающие между битумом и поверхностью минеральных частиц имеют первостепенное значение для свойств асфальтобетона. Поэтому важнейшей характеристикой минерального порошка является его способность к прочному сцеплению с вяжущим.
На прочность сцепления с битумом оказывают влияние химический и минералогический состав минерального порошка а также и свойства битума. Лучшее сцепление с битумом дают карбонатные и основные горные породы. При этом предполагается что в битуме содержится достаточное количество анионактивных поверхностно-активных веществ (в частности асфальтогеновых кислот) способных образовывать в зоне контакта битума с минеральными поверхностями водонерастворимые химические соединения т.е. минеральные порошки должны быть способны к хемосорбционному взаимодействию с битумами. Поэтому в качестве исходных горных пород для приготовления минеральных порошков используют известняки доломиты доломитизированные известняки и другие карбонатные горные породы.
Кислые горные породы (к ним относят породы содержащие более 65% SiO2) при взаимодействии с битумами не образуют хемосорбционных соединений. Вследствие этого адгезия битума к подобным минеральным зернам особенно в присутствии воды пониженная. Минеральный порошок полученный из кислых горных пород не оказывает на битум необходимого структурирующего влияния. В связи с этим асфальтобетон получаемый на основе подобного порошка обычно отличается пониженными показателями прочности водо- и теплостойкости.
Важной характеристикой минеральных порошков отражающей их взаимодействие с водой (а следовательно и особенности взаимодействия с битумом) является степень набухания в воде смеси порошка с битумом. Этот показатель нормируется ГОСТ 52129 - 2003 “Порошок минеральный для асфальтобетонных смесей. Технические условия”[8] а методика его определения - ГОСТ 12784 - 78 “Порошок минеральный для асфальтобетонных смесей. Методы испытаний”[9]. Набухание смеси порошка с битумом (при остаточной пористости образцов 5 - 6%) не должно превышать 25% для неактивированных и 15% для активированных порошков. Этот показатель более четко характеризует свойства порошка в сравнении с ранее применявшейся характеристикой - так называемым коэффициентом гидрофильности.
У обычно применяемых минеральных порошков удельная поверхность составляет от 2500 до 5000 см2г. Чем выше удельная поверхность (в названных пределах) тем в большей степени проявляется структурирующее влияние на битум минерального порошка а следовательно и выше его роль в асфальтобетоне. Следует однако иметь в виду что очень высокая дисперсность порошков (неактивированных) часто не реализуется в асфальтобетоне вследствие агрегирования наиболее мелких частиц. Более того образующиеся агрегаты не только снижают эффективную удельную поверхность порошка но снижают плотность и коррозионную устойчивость асфальтобетона.
Согласно ГОСТ 52129 – 2003[8] тонкость помола минерального порошка должна быть такой чтобы при мокром рассеве проходило через сито с отверстиями: 125мм - 100% 0315мм - не менее 90% 0.071мм - не менее 70%.
Коэффициент гидрофильности частиц мельче 125 мм должен быть не более 10. Массовая доля водорастворимых соединений в цементной пыли допускается не более 08% в промышленных шламах - не более 05%.
Пористость минерального порошка оказывает большое влияние на пористость всей минеральной части асфальтобетона а следовательно и на его битумоемкость. Пористость по объему при уплотнении под нагрузкой 40 МПа должна быть не более 45% у порошков из шламов зол уноса цементной пыли и не более 35% у прочих порошков.
Качество минерального порошка оказывает большое влияние на физико-механические свойства асфальтобетона и на расход вяжущего материала.
Суммарная поверхность частиц минерального порошка очень большая и битум распределяется по ней тонкой пленкой.
При этом улучшаются свойства битума (сцепление температурная устойчивость и др.) и соответственно повышаются свойства асфальтобетона.
Для приготовления ЩМАС следует применять песок из отсевов дробления горных пород отвечающий требованиям ГОСТ 8736-93[10]. Прочность песка должна быть не ниже 1000. Содержание глинистых частиц в песке определяемое методом набухания не должно превышать 05% при этом содержание зерен мельче 016 мм в песке из отсевов дробления не нормируется. Каменная мелочь содержащаяся в песке из отсевов дробления может быть использована в полном объеме при приготовлении ЩМАС взамен части минерального порошка.
Зерна песка занимают большую часть объема асфальтобетона заполняя собой пространства между более крупными частицами щебня или образуя скелетную часть асфальтобетона (в случае песчаного асфальтобетона). Присутствие зерен песка позволяет существенно повысить однородность асфальтобетона что имеет большое значение для условий его работы. Наличие зерен песка значительно повышает удобообрабатываемость смеси и способствует формированию наиболее благоприятной структуры асфальтобетона в процессе его уплотнения.
Песок применяемый для асфальтобетона должен быть чистым состоять из зерен прочных горных пород не иметь загрязняющих примесей. Количество пылевидных глинистых и илистых частиц определяемых отмачиванием не должно превышать 3% в природном и 5% в дробленом песке в том числе глинистых частиц должно быть не более 05%. Требования к дробленым пескам и отсевам продуктов дробления даны в табл. 3.2.1.
Таблица 3.2.1 Требования к дробленым пескам
Нормы для смесей марок
Горячие теплые и холодные типов
Горячие и теплые типов
Предел прочности исходной горной породы при сжатии МПа не менее
Марка исходного гравия по дробимости не более
Массовая доля глинистых примесей % не более
Примечание. Для смесей типа Г марок I и II следует использовать дробленые пески и отсевы продуктов дробления только из изверженных горных пород.
Гранулометрический состав песка должен обеспечивать получение смеси с другими минеральными материалами обладающей оптимальной плотностью.
Согласно ГОСТ 8736 – 93[10] пески разделяются на четыре группы по признакам указанным в таблице:
Полный остаток на сите 063 % по массе
Для приготовления асфальтобетонных смесей применяют крупные и средние пески. В щебёночно-мастичных асфальтобетонных смесях используемых для устройства покрытий обладающих надлежащей шероховатостью поверхности следует применять дробленые пески из изверженных или метаморфических (некарбонатных) пород прочность которых должна быть не ниже прочности горной породы из которой получен щебень. ГОСТ 8736 – 93[10] предусматривает производство и применение дробленых и фракционированных песков. Форма зерен дробленого песка должна быть близкой к кубовидной.
В зависимости от прочности исходной горной породы дробленый песок разделяется на две марки 800 и 400. Для первого из них применяют породы марки по прочности не ниже 800 или гравий с показателем дробимости не выше Др 8 для второго соответственно не ниже 400 и не выше Др 16.
Для постоянства свойств асфальтобетона важно чтобы песок имел один и тот же состав для каждой принимаемой партии. При отсутствии песка с постоянным составом необходимо искусственно подбирать такую смесь из песка разного гранулометрического состава.
Важнейшим элементом структуры ЩМА является щебень. Для приготовления смесей принято использовать щебень с размером зерен 5-10 10-15 15-20 мм из плотных горных пород согласно ГОСТ 8267-93[11]. Рекомендуется щебень из прочных и трудно шлифуемых горных пород обладающий хорошим сцеплением с применяемым битумным вяжущим. Допускается использовать щебень из металлургических шлаков по ГОСТ 3344-83[12] отвечающий соответствующим требованиям. Щебень должен удовлетворять требованиям ГОСТ 9128-97[4] предъявляемым к крупному заполнителю применяемому в асфальтобетонных смесях типа А марки I.
По форме зерен применяемый щебень должен быть кубовидным и относиться к 1-й группе. Содержание зерен пластинчатой и игловатой формы не должно превышать 15%. Для получения качественного щебня с улучшенной формой зерен необходимо как правило применять специальные технологии его изготовления на соответствующем дробильно-сортировочном оборудовании.
Марка щебня по дробимости в цилиндре должна быть не ниже 1200 в случае изверженных и метаморфических горных пород и не ниже 1000 для осадочных горных пород. Марка щебня по истираемости должна соответствовать И-I марка по морозостойкости должна быть не ниже F 50.
Более высокие требования предъявляются к щебню используемому в щебёночно-мастичных асфальтобетонах. Марка щебня из осадочных карбонатных пород изменяется в зависимости от тех же факторов в пределах от 400 до 1000.
Щебень должен состоять из однородных по прочности пород. В нем не должно быть загрязняющих примесей. Гранулометрический состав щебня для асфальтобетонных смесей применяемых в верхнем слое дорожных покрытий должен быть таким чтобы вместе с другими материалами он обеспечивал получение смеси удовлетворяющей требованиям оптимальной плотности.
В щебёночно-мастичном асфальтобетоне условия работы щебня образующего каркас из взаимно соприкасающихся щебенок диктуют повышенные требования к их форме. В этом случае содержание зерен неправильной формы не должно превышать 20%.
Для верхних слоев покрытий следует применять щебень из магматических горных пород так как он обладает высокой плотностью и износостойкостью.
Для нижних слоев целесообразно применять известняковый щебень.
Марка щебня по прочности выбирается в зависимости от марки асфальтобетона и типа гранулометрии равна 1200 (прочность исходной горной породы при сжатии кгссм²) колеблется от 600 до 1200.
Определяется по дробимости Др=10% при сжатии в цилиндре.
Марка щебня по износу назначается исходя из будущих условий работы асфальтобетона (верхний или нижний слой покрытия интенсивность движения по дороге.) Определяется по потере в массе (%) при испытании в полочном барабане. В щебне нормируют содержание зерен пластинчатой (лещадной) и игловатой форм (толщина зерен менее длины в три раза и более) в зависимости от группы щебня по форме:
кубовидная - до 15 % (от общей массы);
улучшенная - от 15 до 25 %;
обычная - от 25 до 35 %.
Зерна кубовидной формы обладают большей прочностью и смесь таких зерен дает наиболее плотную упаковку.
Зерновой (гранулометрический) состав щебня применяемого в качестве крупного заполнителя в асфальтобетоне должен быть оптимальным т.е. соотношение зерен разной крупности должно обеспечивать максимальную плотность и минимальную пустотность щебня при уплотнении.
Содержание глинистых и пылеватых частиц не должно превышать 1 %.
Иначе: - ухудшается сцепление битума с каменным материалом;
- увеличивается расход битума;
Морозостойкость щебня:
для верхних слоев покрытий: не менее 50 циклов (попеременного замораживания и оттаивания);
Битум органический вяжущий материал покрывая поверхность каменных материалов (щебня песка минерального порошка) тонкой пленкой соединяет их в монолит.
Как все органические вяжущие материалы битум обладает рядом особенностей.
Особенности битума он изменяет свое физическое состояние в зависимости от температуры: при нагревании его вязкость снижается и он переходит в жидкое состояние при отрицательных температурах он становится твердым и хрупким. При высоких положительных температурах он обладает такой текучестью что способен хорошо смачивать и обволакивать каменные материалы очень тонкой пленкой а при остывании склеивать их в достаточно прочный монолит.
Условия работы битумов в конструкциях дорожной одежды и условия производства работ разнообразны поэтому в дорожном строительстве применяются вязкие и жидкие битумы а также дорожные эмульсии.
Битумы применяемые в дорожном строительстве должны отвечать требованиям в соответствии с условиями их работы.
Летом пленка битума в слое покрытия или основания должна быть достаточно прочной и обладать невысокой деформативностью.
В слое могут появятся деформации в виде волн сдвигов наплывов.
Зимой пленка битума в слоях дорожной одежды должна обладать достаточной деформативностью что особенно важно при резком перепаде отрицательных температур.
Несоблюдение этого требования может привести к образованию в слоях покрытия и основания трещин.
Весной и осенью пленка битума должна быть достаточно прочной и деформативной. Особенно это важно в весенний период когда несущая способность переувлажненных грунтов под дорожной одеждой снижается.
Невыполнение этого условия может привести к возникновению в дорожной одежде трещин.
Битум должен обладать хорошим сцеплением с поверхностью каменных материалов.
Иначе не будут выполнены требования к прочности и водостойкости асфальтобетона и покрытие быстро разрушится.
Пленка битума должна быть водостойкой и не отслаиваться водой с поверхности каменного материала. Битум должен обладать устойчивостью к старению а его свойства не должны изменяться в слоях дорожной одежды.
Необходимо помнить что в покрытии битум стареет быстрее чем в основании из-за непосредственного воздействия на него солнечной радиации и кислорода воздуха. При перегреве асфальтобетонной смеси происходит интенсивное испарение легких фракций из битума что приводит к его старению.
Для приготовления щебеночно-мастичных асфальтобетонных смесей применяют битумы нефтяные дорожные вязкие отвечающие требованиям ГОСТ 22245-90[13] полимерно-битумные вяжущие по ОСТ 218.010-98[14] и другие битумные вяжущие выпускаемые по технической документации согласованной и утвержденной в установленном порядке.
Нефтяной битум представляет собой сложную дисперсную систему состоящую из смеси разнообразных высокомолекулярных соединений нефти которые по величине молекулярного веса и характеру растворимости в селективных растворителях объединяют в группы углеводородов (масел) смол и асфальтенов. При выборе марки битумного вяжущего для ЩМАС следует руководствоваться следующими рекомендациями.
При выборе структурного типа дорожного битума руководствуются методическими рекомендациями. Например для повышения качества покрытий из ЩМАС в районах с холодным и континентальным климатом рекомендуется применять окисленные битумы марок БНД имеющие коллоидную структуру «золь-гель» и относящиеся к III структурному типу по классификации А.С. Колбановской. В районах с теплым и умеренно-континентальным климатом напротив предпочтительней использовать остаточные битумы в том числе битумы II структурного типа марок БНД которые имеют коллоидную структуру «золь». Классификация предложенная А.С. Колбановской основана на групповом составе нефтяных дорожных битумов характеризующемся относительным содержанием асфальтенов (А) смол (С) и масел (М) в соответствии с этой классификацией построена диаграмма на рис. 10.
Битумы I структурного типа применять не рекомендуется так как они недостаточно устойчивы к старению. Обычно к I структурному типу или типу гель относятся сильно окисленные и состарившиеся битумы присутствующие в старом асфальтобетоне.
Независимо от условий применения ЩМАС нужно ориентироваться на такие образцы вяжущих которые имеют наиболее высокую адгезию с поверхностью применяемого щебня. При плохом сцеплении вяжущего со щебнем рекомендуется применять добавки активаторов или поверхностно-активные вещества преимущественно катионного типа.
В целях повышения устойчивости к действию тяжелых транспортных нагрузок и экстремальных температур рекомендуется применять ЩМАС на основе полимерно-битумных вяжущих (ПБВ) особенно для устройства покрытий на мостах и городских улицах. Наиболее широкое применение в дорожном строительстве получили ПБВ с использованием модифицирующей добавки трехблочного сополимера типа «стирол-бутадиен-стирол» (SBS) в количестве до 6-65% от массы битума. Различная физико-химическая природа структурных блоков сополимера приводит к образованию самоорганизующейся трехмерной полимерной сетки в объеме ПБВ вследствие физической сшивки макромолекул полимера. За счет этого битумное вяжущее приобретает свойства присущие эластомерам что приводит к большей упругой деформативности снижению хрупкости при низких температурах и одновременно к повышению сдвигоустойчивости покрытия при высоких температурах эксплуатации.
Органическим вяжущим является битум марки БНД 6090 Московского нефтеперерабатывающего завода. Свойства битума приведены в таблице чертежа лист 5. Битум соответствует требованиям ГОСТ 22245-90[13].
5 Адгезионная присадка «АМДОР-10»
Адгезионная присадка «АМДОР-10» является усовершенствованным химическим аналогом присадки «АМДОР-9». За счет использования при производстве более квалифицированного сырья улучшены органолептические свойства понижена температура потери текучести уменьшена вязкость по сравнению с присадкой «АМДОР-9». При этом сохранены адгезионные свойства.
Рекомендуемая концентрация присадки «АМДОР-10» при введении в битум – 02-05% от массы битума. Оптимальная концентрация определяется для конкретных щебеночных материалов и битума в дорожной лаборатории при испытании на сцепление по ГОСТ 11508-74[15].
Присадка «АМДОР-10» имеет показатели качества представленные в таблице чертежа лист 3.
Транспортировка производится в 2165 л металлических бочках железнодорожным (вагоны контейнеры) или автомобильным транспортом; возможна отгрузка автомобильными цистернами. Поставляется со складов в г. Нижний Тагил Санкт-Петербург Москва Тольятти Ростов.
6 Добавки для теплого асфальтобетона
Добавки для теплого асфальтобетона представленные на российском рынке: Ворммикс Л (Италия) Секабаз РТ 945 (Франция). Evotherm J1 (США) Aspha-m состав добавки на основе полимеров имидазолина больше 25% щелочность по перхлору 42-52. Американская добавка Evotherm J1 состоит в основном из продукта реакции конденсации полиаминов жирных кислот и талового масла – 75-95% из модифицированного продукта этой реакции – 5-25% а также содержит 22'-иминоэтанол – 2-4%. Добавка представляет собой жидкость янтарного темного цвета pH – 10-12 растворима в воде. Немецкая добавка Aspha-min представляет собой порошок белого цвета фракций 0-09 мм или 0-20 мм который является гидратированным алюмосиликатом с содержанием воды в кристаллической решетке до 25%.
Таблица 3.6.1 Показатели свойств добавок для теплого асфальтобетона
Наименование показателей добавок
Показатели свойств добавок
Секабаз РТ 945 (Франция)
Aspha-min (германия)
Состав на основе полимеров; имидазолина больше 25 %
Продукт реакции конденсации полимеров жирных кислот и таллового масла – 75-95 %
Модифицированный продукт реакции конденсации полиаминов жирных кислот талового масла – 5-25 %
Гидратированный алюмосиликат с содержанием воды в кристаллической решетке до 25 %
Вязкая жидкость темного цвета
При 25°С светло-желтая жидкость
Жидкость янтарного темного цвета
Порошок белого цвета фракций 0-09 мм 0-20 мм
Щелочность по перхлору 42-52
Точка вспышки – больше 150°С
Температура вспышки 143°С
Около 10 кгм3 при 25°С
В ароматических соединениях и спиртах
При 50°С менее 1000 мПа*с
Температура кипения °С
Примечание: сведения о добавках взяты из информационных материалов о добавках представленных фирмами продающими добавки в России.
лист11. технология производства теплых щмас.dwg

- бункер предварительного накопления добавки перед пневмотранспортированием
- пневмопровод подачи добавки к дозатору
- бункер предварительного накопления добавки перед дозированием
- трубопровод подачи добавки в асфальтосмеситель
Внешний вид и оборудование линии дозирования и подачи гранулированных добавок
Технологическая схема введения жидкой добавки
- приемная емкость для жидких добавок V=250л
- загрузочное отверстие
- направление подачи адгезионной добавки
асфальтосмесительной установки
Технологическая схема работы
- транспортер агрегата питания
- загрузочный транспортер
- элеватор минерального порошка
- силос минерального порошка
- дозатор минерального порошка
- дозатор песка и щебня
- нагреватель теплоносителя
План расположения АБЗ на местности
- смесительный агрегат
- емкость дизельного топлива
Наименование показателя
Производительность номинальная
Установленная мощность
Реально потребляемая мощность
Способ загрузки готовой смеси в автотранспорт
Способ утилизации пыли
Способ нагрева битума и оборудования
Тип сушильного агрегата
Компановка сушильного агрегата
Номинальный расход топлива
Компановка оборудования смесительного агрегата
Количество (шт.) х объем (м3) бункеров агрегата питания
Компановка оборудования агрегата питания
Тип питателей агрегата питания
Количество фракций дозируемого каменного материала
Вместимость бункера для горячих каменных материалов
Максимальная масса замеса
Вместимость силоса минерального порошка
Вместимость силоса пыли
Общая вместимость цистерн для битума
Тип пылеулавливающего устройства
Номинальный выброс пыли
мгм3 при 30 гм3 на входе
Уровень шума в кабине управления
Стандартная площадь размещения
Удельные энергозатраты
Значение (номинальное)
Гравитационный: из-под смесителя
Использование в техпроцессе
С приводом от опорных роликов
Инжекторная высокого давления
Периодического действия
наклонный элеватор для
с инвенторным управлением
Циклон и рукавный фильтр
вторичного подъема инертных после весов
Технические данные АБЗ модели СПЕКО АР-2000РТ
Проект производства работ по строительству автомобильной дороги I технической категории
Технология и организация строительного производства
Технология производства теплых ЩМАС
Изм. Кол.уч.Лист Дата
Руководит. Соломенцев
Консульт. Соломенцев
ГОСУНИВЕРСИТЕТ-УНПК" АСИ кафедра "САД
ДП 2012 270205 070755 АД и А
лист5. характеристики применяемых материалов.dwg

Наименование показателей
Глубина проникания иглы
Температура размягчения
Температура хрупкости
Изменение темп-ры размягчения
Битум нефтяной дорожный БНД 6090 Московского НПЗ
Соответствует требованиям ГОСТ 22245-90
Марка исходной горной породы
Содержание Al2O3+Fe2O3
Зерновой состав по массе
Значение удельной эффективной
активности естественных
Порошок минеральный неактивированный
Соответствует требованиям ГОСТ Р52129-2003
Наименование показателя
Требование по ТУ 0257-003-35475596-96
Температура плавления
Сцепление с минеральным материалом битума
не хуже контрольного образца №1
вязкая жидкость от светложелтого до
темнокоричневого цвета
Присадка адгезионная дорожная "АМДОР-10
Соответствует требованиям ГОСТ 8267-93
Соответствует требованиям ГОСТ 8736-93
Максимальная температура нагрева
Теплостойкость при температуре 220
Стабилизирующая добавка СД-3 ГБЦ
Соответствует требованиям СТО 77142802-003-2011
Гранулы цилиндричес-
Массовая доля технологической мелочи
Температура размягченя добавки
Увеличение температуры размягчения
Стабилизирующая добавка "РТЭП
Соответствует требованиям ТУ 5718-001-79259416-2006
Гранулы произвольной
формы размером 2-6мм
ем добавки при температуре 25 С
Соответствует требованиям ТУ 0257-003-35475596-96
Проект производства работ по строительству автомобильной дороги I технической категории
Технология и организация строительного производства
Характеристики применяемых материалов
Изм. Кол.уч.Лист Дата
Руководит. Соломенцев
Консульт. Соломенцев
ГОСУНИВЕРСИТЕТ-УНПК" АСИ кафедра "САД
ДП 2012 270205 070755 АД и А
лист8. подбор состава ЩМАС.dwg

Зерновой состав (остатки на сите с отверстием
Щебень гранит. фр. 10-15 мм
Щебень гранит. фр. 5-10 мм
Отсев гранит. фр. 0-5 мм
Содержание зерен мельче данного размера
Требования ГОСТ 31015-2002
сумма полных проходов
Дозировка на замес 1800 кг
Щебень гранитный фр.10-15 мм
Щебень гранитный фр. 5-10 мм
Отсев гранитный фр. 0-5 мм
Щебеночные фр.10-15 мм
Щебеночные фр. 5-10 мм
ПОДБОР СОСТАВА ЩЕБЕНОЧНО-МАСТИЧНОЙ АСФАЛЬТОБЕТОННОЙ СМЕСИ ЩМА-15
Применяемые материалы
Зерновой состав смеси
Наименование показателей
Фактические показатели
Пористость минерального остова
Остаточная пористость
Прочность при сжатии
Водостойкость при длительном водонасыщении
Сцепление битума с минеральной частью аб смеси
Сдвигоустойчивость по коэффициенту внутреннего трения
Сцепление при сдвиге при температуре 50 С
Трещиностойкость по пределу прочности на растяжение при
расколе при температуре 0 С и скорости деформирования
Показатель стекания вяжущего
Физико-механические показатели асфальтобетонной смеси
Размер зерен минерального материала
Содержание зерен мельче мм
График зернового состава минеральной части
допустимые пределы гранулометрического состава по ГОСТ 31015-2002
Проект производства работ по строительству автомобильной дороги I технической категории
Технология и организация строительного производства
Изм. Кол.уч.Лист Дата
Руководит. Соломенцев
Консульт. Соломенцев
ГОСУНИВЕРСИТЕТ-УНПК" АСИ кафедра "САД
ДП 2012 270205 070755 АД и А
лист10. оценка длительной водостойкости теплого щма.dwg

Прочность при сжатии
Кинетика изменения прочности при 20 С водонасыщенных образцов ЩМА-15
Примечание: образцы № 1
содержат РТЭП и СД-3
Кинетика изменения водонасыщения образцов ЩМА-15
График зависимости прочности при сжатии при 20 С водонасыщенных образцов
ЩМА-15 от времени выдерживания в воде
График зависимости водонасыщения образцов ЩМА-15 от времени выдержвания
ЩМА-15 с добавками РТЭП
СД-3 и Секабаз РТ 945
ЩМА-15 с добавкой Унирем-001
ЩМА-15 с добавкой РТЭП
Проект производства работ по строительству автомобильной дороги I технической категории
Технология и организация строительного производства
Оценка длительной водостойкости теплого ЩМА
Изм. Кол.уч.Лист Дата
Руководит. Соломенцев
Консульт. Соломенцев
ГОСУНИВЕРСИТЕТ-УНПК" АСИ кафедра "САД
ДП 2012 270205 070755 АД и А
лист3. календарный план и график строительства.dwg

Электроснабжение и переустройство кабелей связи
Электромонтажные работы
Переустройство газо- и водопровода
Подпорная стенка (Н-3
Глава 2. Земляное полотно
Рекультивация земель
Глава 3. Дорожная одежда
Устройство водосбросных сооружений
Устройство разделительной полосы
Глава 4. Искусственные сооружения
Глава 5. Пересечения и примыкания
Глава 6. Дорожные устройства и обстановка дороги
Автобусные остановки и посадочные площадки
Разметка проезжей части
Календарный план выполнения работ
График производства работ
Проект производства работ по строительству автомобильной дороги I технической категории
Технология и организация строительного производства
Календарный план и график строительства
Изм. Кол.уч.Лист Дата
Руководит. Соломенцев
Консульт. Соломенцев
ГОСУНИВЕРСИТЕТ-УНПК" АСИ кафедра "САД
ДП 2012 270205 070755 АД и А
раздел6.ТЕХНИКО-ЭКОНОМИЧЕСКИЕ ПОКАЗАТЕЛИ СТРОИТЕЛЬСТВА.docx
Строительство автомобильной дороги «Таврово-Соломино-Разумное» в Белгородском районе Белгородской области.
Таблица 6.1.1 Характеристики объекта
Наименование показателей
Строительная длина участка
Ширина проезжей части
Тип дорожной одежды и вид покрытия
Ширина укрепительной полосы
Ширина разделительной полосы
Ширина укрепленной полосы на разделительной полосе
Стоимость строительства определена на основании объемов работ подсчитанных по чертежам дипломного проекта проектов-аналогов и укрупненных показателей.
При определении сметной стоимости строительства применялись базисно-индексный метод (по аналогам) ресурсный метод при составлении локальных сметных расчетов с применением территориальных единичных расценок по Орловской области в соответствии с «Методикой определения стоимости строительной продукции на территории Российской Федерации МДС 81.35-2004»[23].
Для выделения ресурсных показателей использовались Государственные элементные сметные нормы (ГЭСН-2001[24] ГЭСНм-2001[25]).
Стоимость конструкций и других местных строительных материалов и изделий не вошедших в сборники ТЕР-2001 принята по территориальным и федеральным сборникам сметных цен на материалы изделия и конструкции применяемые в строительстве.
Локальные сметные расчеты на отдельные виды работ составлены с помощью программного комплекса «Смета-ru».
Сметная стоимость строительства автомобильной дороги по состоянию на 1 квартал 2012 года составила 2 576 30934 тыс. руб. (с НДС) в том числе стоимость строительно-монтажных работ – 2 576 25113 тыс. руб. Накладные расходы приняты в процентной форме от фонда оплаты труда согласно нормативам приведенным в «Методических указаниях по определению накладных расходов в строительстве МДС 81.33-2004»[28] по видам строительно-монтажных работ.
Сметная прибыль рассчитана в порядке определенном «Методических указаниях по определению величины сметной прибыли в строительстве МДС 81.25-2004»[27] по видам строительно-монтажных работ.
В сводном сметном расчете учтены следующие затраты.
Затраты на временные здания и сооружения приняты в соответствие с ГСН 81-05-01-2001[26] сборника сметных норм и затрат на строительство временных зданий и сооружений при производстве строительно-монтажных работ.
Дополнительные затраты на производство работ в зимнее время приняты согласно ГСН 81-05-02-2001[26] и МДС 81.35-2004[23].
Непредвиденные работы и затраты определены согласно МДС 81.25-2004[27] п. 4.96 в размере 15%.
За итогом сводного сметного расчета учтены затраты связанные с налогом на добавленную стоимость в размере 18% согласно закона РФ №177-ФЗ от 07.07.2003.
2 Сводный сметный расчет
Сводный сметный расчет стоимости строительства автомобильной дороги «Таврово-Соломино-Разумное» в Белгородской области.
Расчет в сумме: 2 576 30934 тыс.руб.
Составлен в текущих ценах на 1 полугодие 2012г.
Наименование глав объектов работ и затрат
Подготовка территории строительства
Подготовительные работы
Рубка деревьев и кустарника
Укрепительные работы
Рекультивация земель
Устройство водосбросных сооружений
Устройство разделительной полосы
Искусственные сооружения
Мост через водохранилище
Путепровод через железную дорогу
Путепровод на транспортной развязке на Пк 92+72
Овоидальная труба отв. 30 м на Пк 16+70
Труба отв. 12 м с быстротоком на Пк 28+60
Круглая жб косогорная труба отв. 12 м на Пк 40+12
Круглая жб труба отв. 12 м с водоприемным колодцем на Пк 4285
Круглые жб трубы отв 10 м (4 шт.)
Пересечения и примыкания
Устройство примыканий и пересечений
Жб трубы на съездах и подъезде
Кольцевая развязка на Пк 0+00
Кольцевая развязка на Пк 66+85
-х уровневая транспортная развязка на Пк 99+72
Глава 6 Дорожное обустройство
Велосипедная дорожка шир. 15 м
Автобусные остановки
Разметка проезжей части
Глава 9 Временные здания и сооружения
ГСН 81-05-01-2001 п 3.5.2
Временные здания и сооружения при строительстве мостов 105%
Временные здания и сооружения при строительстве автодороги 41%
Прочие работы и затраты
Удорожание связанное с производством работ в зимнее время
МДС 81.-35.2004 п. 9.9 .
Затраты по перевозке работников автомобильным транспортом – 085%
Итого по главам 1-11
Проектные и изыскательские работы авторский надзор
Итого по главам 1-12
Непредвиденные расходы
Итого с непредвиденными
МДС 81-35-2004 п.4.100
Всего по сводно-сметному расчёту (с НДС)
Составил Мусатова И.А.
аннотация.docx
Проведены: оценка эффективности добавок в битуме и ЩМАС оценка длительной водостойкости теплого ЩМА сравнение вариантов добавок.
Данная работа содержит:
Демонстрационных листов
раздел 7.БЕЗОПАСНОСТЬ ЖИЗНЕДЕЯТЕЛЬНОСТИ.docx
Организация и технология работ при строительстве асфальтобетонного покрытия должны обеспечивать безопасность для работающих на всех стадиях производственного процесса и соответствовать требованиям настоящего стандарта ГОСТ 12.3.002-75 СНиП III-4-80.
При выполнении работ по строительству асфальтобетонных покрытий должна быть обеспечена безопасность для работающих при возникновении следующих опасных и вредных производственных факторов: запыленность и загазованность воздуха уровень шума и вибрации недостаточная освещенность отклонения от оптимальных норм температуры относительной влажности и скорости движения воздуха в рабочей зоне; электробезопасность применяемых машин и оборудования.
Содержание вредных веществ в воздухе рабочей зоны не должны превышать ПДК. Допустимые значения уровней шума и вибрации создаваемые машинами на рабочих местах соответственно по ГОСТ12.1.003-83 и ГОСТ12.1.012-90.
Результаты исследований содержания вредных веществ в воздухе рабочей зоны приведены в таблице 7.1.1.
Фактическое значение
Нормативное значение
При выполнении работ по строительству в опасных зонах порядок допуска к производству работ а также границы опасных зон в пределах которых действуют опасные факторы должны соответствовать СНиП III-4-80.
Технологические процессы строительства автомобильных дорог являются источником интенсивного шума и вибрации которые отрицательно воздействуют на здоровье людей как непосредственно принимающих участие в технологических процессах так и проживающих в прилегающих жилой застройке а также на флору и фауну. Особенно сильный внешний шум создается при работе сваебойного оборудования бульдозеров скреперов отбойных молотков и бетоноломов вибраторов вибросит некоторых марок автогрейдеров катков экскаваторов дизельных грузовиков и др.
Результаты измерений уровня шума приведены в таблице 7.1.2.
2 Методы борьбы с шумом
Мероприятия по снижению уровня звука при выполнении технологических процессов сводится главным образом к снижению шума в его источнике т.е. к снижению шума дорожно-строительных машин и применению звукоотражающих или звукопоглощающих экранов на пути распространения звука или шумозащитных мероприятий на самом защищаемом объекте. Для звукоизоляции двигателей дорожных машин можно применять защитные кожуха и капоты с многослойными покрытиями из резины поролона и т.п. Для снижения шума двигателей можно применять усовершенствованные конструкции глушителей значительно снижающие уровень звука при выпуске отработавших газов (лабиринтные реактивные многозвенные и т.п.). В том случае когда не удается снизить уровень шума от строительной площадки до допустимого уровня установленного для данной территории за счет снижения шума дорожно-строительных машин необходимо устанавливать звукоотражающие или звукопоглощающие экраны на пути распространения звука. Эффект снижения шума зелеными насаждениями зависит от характера посадок породы деревьев и кустарников времени года частоты звука и др. Определенного снижения уровня шума от строительной площадки можно добиться путем применения рациональной технологии ведения работ состоящей в сокращении продолжительности работы дорожно-строительных машин прекращении работ в вечерние и ночные часы выборе рационального режима работы дорожно-строительных машин.
3 Обеспечение безопасности движения на автомобильных дорогах в зависимости от категории
В России все автомобильные дороги делятся на пять категорий. Дороги I и II категорий с капитальными типами покрытий полнее отвечают условиям автомобильного движения. К их числу относят например новые автомагистрали с несколькими полосами движения в каждом направлении и двухполосные имеющие по одной полосе движения в одну сторону. Широкие полосы движения (375 м) ограниченные максимальные уклоны (3 4 %) увеличенные радиусы поворота и уширенные обочины обеспечивают на этих дорогах безопасность движения и достаточную пропускную способность.
Дороги III категории рассчитанные на менее интенсивное движение имеют облегченное усовершенствованное покрытие. Ширина каждой полосы движения такой дороги может быть уменьшена до 35 м радиусы кривых в плане до 400 м максимальные уклоны До 5 %.
К IV категории относятся дороги с твердым покрытием но не всегда усовершенствованным (булыжник гравий). Ширина полосы движения на них не более 3 м минимальные радиусы поворотов 250 м максимально продольные уклоны 6 %.
К V категории относятся профилированные дороги не имеющие твердого покрытия (проходящие по естественному грунту). Иногда их поверхность обрабатывают специальными добавками связующими грунт и несколько повышающими стойкость верхнего слоя. В осеннюю и весеннюю распутицу а также в период снежных заносов они обычно становятся непроезжими но в начале зимы с наступлением первых морозов и до сильных снегопадов а также летом в сухое время грунтовые дороги обладают хорошими качествами для эксплуатации.
Проектные решения автомобильных дорог должны обеспечивать: организованное безопасное удобное и комфортабельное движение автотранспортных средств с расчетными скоростями; однородные условия движения; соблюдение принципа зрительного ориентирования водителей; удобное и безопасное расположение примыканий и пересечений; необходимое сцепление шин автомобилей с поверхностью проезжей части; необходимое обустройство автомобильных дорог в том числе защитными дорожными сооружениями; необходимые здания и сооружения дорожной и автотранспортной служб и т.п.
При проектировании элементов плана продольного и поперечного профилей дорог по нормам допускаемым п. 4.21 СНиП 2.05.02-85* следует проводить оценку проектных решений по показателям скорости безопасности движения и пропускной способности в том числе в неблагоприятные периоды года.
При проектировании дорог необходимо разрабатывать схемы расстановки дорожных знаков с обозначением мест и способов их установки и схемы дорожной разметки в том числе горизонтальной - для дорог с капитальными и облегченными дорожными одеждами. Разметку следует сочетать с установкой дорожных знаков (особенно в районах с длительным снеговым покровом). При разработке схем размещения технических средств организации дорожного движения следует пользоваться ГОСТ 23457-86.
Для обеспечения безопасности движения установка рекламы на автомобильных дорогах не допускается.
Осветленные покрытия рекомендуется применять для выделения пешеходных переходов (типа «зебра») остановок автобусов переходно-скоростных полос дополнительных полос на подъемах полос для остановок автомобилей проезжей части в тоннелях и под путепроводами на железнодорожных переездах малых мостах и других участках где препятствия плохо видны на фоне дорожного покрытия.
Стационарное электрическое освещение на автомобильных дорогах следует предусматривать на участках в пределах населенных пунктов а при наличии возможности использования существующих электрических распределительных сетей - также на больших мостах автобусных остановках пересечениях дорог I и II категорий между собой и с железными дорогами на всех соединительных ответвлениях узлов пересечений и на подходах к ним на расстоянии не менее 250 м на кольцевых пересечениях и на подъездных дорогах к промышленным предприятиям или на их участках при соответствующем технико-экономическом обосновании.
Если расстояние между соседними освещаемыми участками составляет менее 250 м рекомендуется устраивать непрерывное освещение дороги исключающее чередование освещенных и неосвещенных участков.
Вне населенных пунктов средняя яркость покрытия участков автомобильных дорог в том числе больших и средних мостов должна быть 08 кдм2 на дорогах I категории 06 кдм2 на дорогах II категории а на соединительных ответвлениях в пределах транспортных развязок - 04 кдм2.
Отношение максимальной яркости покрытия проезжей части к минимальной не должно превышать 3:1 на участках дорог I категории 5:1 на дорогах остальных категорий.
Показатель ослепленности установок наружного освещения не должен превышать 150.
Средняя горизонтальная освещенность проездов длиной до 60 м под путепроводами и мостами в темное время суток должна быть 15 лк а отношение максимальной освещенности к средней - не более 3:1.
Освещение участков автомобильных дорог в пределах населенных пунктов следует выполнять в соответствии с требованиями СНиП 23-05-95* а освещение автодорожных тоннелей - в соответствии с требованиями СНиП 32-04-97.
Осветительные установки пересечений автомобильных и железных дорог в одном уровне должны соответствовать нормам искусственного освещения регламентируемым системой стандартов безопасности труда на железнодорожном транспорте.
Опоры светильников на дорогах следует как правило располагать за бровкой земляного полотна. Допускается располагать опоры на разделительной полосе шириной не менее 5 м с установкой ограждений.
Световые и светосигнальные приборы располагаемые на мостах через судоходные водные пути не должны создавать помех судоводителям в ориентировании и ухудшать видимость судоходных сигнальных огней.
Включение освещения участков автомобильных дорог следует производить при снижении уровня естественной освещенности до 15-20 лк а отключение - при его повышении до 10 лк.
В ночное время следует предусматривать снижение уровня наружного освещения протяженных участков автомобильных дорог (длиной свыше 300 м) и подъездов к мостам тоннелям и пересечениям автомобильных дорог с автомобильными и железнодорожными дорогами путем выключения не более половины светильников. При этом допускается отключение подряд двух светильников а также расположенных вблизи ответвления примыкания вершины кривой в продольном профиле радиусом менее 300 м пешеходного перехода остановки общественного транспорта на кривой в плане радиусом менее 100 м.
Электроснабжение осветительных установок автомобильных дорог надлежит осуществлять от электрических распределительных сетей ближайших населенных пунктов или сетей ближайших производственных предприятий.
Электроснабжение осветительных установок железнодорожных переездов следует как правило осуществлять от электрических сетей железных дорог если эти участки железнодорожного пути оборудованы продольными линиями электроснабжения или линиями электроблокировки.
Управление сетями наружного освещения следует предусматривать централизованным дистанционным или использовать возможности установок управления наружным освещением ближайших населенных пунктов или производственных предприятий.
Проекты автомобильных дорог I-IV категорий в части безопасности движения должны согласовываться с органами ГИБДД МВД Российской Федерации.
Титульник раздел.docx
лист13. контроль качества.dwg

качества и признаки продукции
-заполнение бункеров
впрыскивания битума;
сушильного барабана;
компрессора к работе;
-заполнение емкостей
и топливных баков до
заполнение агрегатов питания
включение автоматов и рубильников
регулировка производительности агрегата питания
установка в кабине оператора задающих стрелок
датчиков на шкале указателей
проверка настройки гидроклапана системы впрыска
проверка настройки регулятора топлива
подготовка компрессора к работе
проверка заполнения: ёмкости нагревания битума
ёмкости минерального порошка
топочных агрегатов розжиговым топливом
проверка системы жидкого теплоносителя
минерального порошка в расходный бункер из бункера
проверка работы датчиков и весов весовой
дозирование минеральных материалов
минеральных материалов
асфальтобетонной смеси
регулировка уровня воды в отсеке
очищенного газа мокрого пылеуловителя
контроль за работой дымососа
очистка смесителя от налипшей массы
освобождение сушильного барабана и дозатора
минерального порошка от материалов
бункеров горячего грохота
весового бункера негаба-
откачка битума из дозатора
и битумных коммуникаций
отключение автоматов и рубильников
очистка от пыли и грязи
равномерность распределения
температура смеси в каждом
через 100 м: высотные отметки
толщину неуплотненного слоя по его оси
ровность под 3-х метровой
качество продольных и поперечных сопряжений
схема движения и скорость катков
температура смеси в начале и конце уплотнения
уплотнение асфальтобетона в покрытии и
показатели асфальтобетона
прочность сцепления между слоями
Нормативный документ
Допустимые отклонения
Высотные отметки по оси
Ровность (просвет под
Погодные условия при
СНиП 3.06.03-85 Приложение 2
проектных значений в пределах до +100 (20) мм
остальные до +50 (10) мм.
проектных значений в пределах от -15 до 20 см
остальные до +10 см.
проектных значений в пределах от -0
проектных значений в пределах до 10 (6) мм
остальные до +5 (3) мм.
СНиП 3.06.03-85 п. 10.16
Температура не ниже -10 С
Контроль качества приготовления щебеночно-мастичной асфальтобетонной смеси
вид и режим контроля рабочих операций
Контроль качества при устройстве покрытий из щебеночно-мастичного асфальтобетона
Контролируемые показатели качества и допустимые отклонения
Примечание: Данные в скобках относятся к комплекту машин с автоматической системой задания вертикальных отметок.
Примечание: Схема движения катков и количество проходов по одному следу назначается по акту пробной укатки.
Проект производства работ по строительству автомобильной дороги I технической категории
Технология и организация строительного производства
Изм. Кол.уч.Лист Дата
Руководит. Соломенцев
Консульт. Соломенцев
ГОСУНИВЕРСИТЕТ-УНПК" АСИ кафедра "САД
ДП 2012 270205 070755 АД и А
раздел2.ПРОЕКТИРОВАНИЕ И РАСЧЁТ КОНСТРУКЦИИ ДОРОЖНОЙ ОДЕЖДЫ.docx
Конструкция дорожной одежды рассчитана по методике ОДН 218.046-01- Проектирование нежёстких дорожных одежд Москва 2002[3] на расчетную перспективную согласно прогноза роста транспортного потока.
Исходные данные для расчета: расчетная нагрузка – 11500 кН срок службы – 15 лет уровень надёжности – 095
Результаты приведения к расчётной нагрузке:
Приведённая суточная интенсивность приложполосу – 414
Минимальный требуемый модуль упругости МПа – 230
Суммарное расчётное число приложений расчётной нагрузки за срок службы ΣNр прилож.полосу – 675271
Требуемый расчетный модуль упругости МПа - 25447
Для выбора оптимальной конструкции дорожной одежды были сконструированы и рассчитаны два варианта дорожной одежды с учетом обеспеченности зоны строительства дорожно-строительными материалами технологическими особенностями строительства объекта:
Асфальтобетон плотный горячий на битуме БНД марки 6090 (Тип Б Марка II) (ГОСТ 9128-97) [4] – 5 см;
Асфальтобетон пористый горячий на битуме БНД марки 6090 (Крупнозернистый Марка II) (ГОСТ 9128-97)[4] – 7 см;
Асфальтобетон пористый горячий на битуме БНД марки 6090 (Крупнозернистый Марка II) (ГОСТ 9128-97)[4] – 12 см;
Щебень фракционированный трудноуплотняемый 40-70 мм с заклинкои мелким щебнем – 28 см.
Подстилающий слой - рабочий слой из местного песка – 30см. удовлетворяющий нормативным требованиям общий для обоих вариантов.
Щебеночно-мастичный асфальтобетон на битуме БНД марки 6090 ЩМА 15 (ГОСТ 31015-2002)[5] – 5 см;
Асфальтобетон пористый горячий на битуме БНД марки 6090 (Крупнозернистый Марка I) (ГОСТ 9128-97)[4] – 6 см
Асфальтобетон пористый горячий на битуме БНД марки 6090 (Крупнозернистый Марка II) (ГОСТ 9128-97)[4] – 8 см
Щебеночно-песчаная смесь С4 0х80 мм(ГОСТ 25607-94)[6] – 39 см;
Суглинок укрепленный 7% цемента М-20 – 15 см;
Все варианты запроектированы с учетом конструктивных требований СНиП 2.05.02-85[1] и ОДН 218.046-01[3].
В результате технико-экономического сравнения рекомендуется вариант № 2 к применению как более экономичный и с оптимальными показателями несущей способности.
Результаты прочностных расчетов по рекомендуемому варианту:
Требуемый коэффициент прочности по упругому прогибу – 130
Требуемый коэффициент прочности по сдвигу и растяжению на изгиб – 100
Расчетный (полученный в результате расчета) коэффициент прочности по упругому прогибу – 168
Общий модуль упругости конструкции 42631 МПа
Величина запаса прочности на растяжение при изгибе в нижнем слое асфальтобетона +2610%
Величина запаса прочности на сдвиг в подстилающем слое +211%
Прогноз ожидаемого колееобразования см при продольном уклоне дороги
Для обеспечения шероховатости покрытия проектом предусматривается одиночная шероховатая поверхностная обработка техникой с синхронным распределением битума и щебня
Дорожная одежда укрепительных полос устраивается по типу основной дороги. Ширина проезжей части в одном направлении 2х35 м; ширина укрепительных полос 05 м.
Поперечный уклон проезжей части принят 20 %о.
В соответствии с п.4.5 СНиП 2.05.02-85*[1].
Требования к материалам для устройства конструктивных слоев дорожной одежды определены соответствующими стандартами которые приведены на конструктивных чертежах лист 3.
Общая площадь покрытия с учетом укрепленных кромок проезжей части по дороге составила 130 660 м2.
2 Расчет первого варианта дорожной одежды
Асфальтобетон плотный горячий на битуме БНД марки 6090 (Тип Б Марка II) - 5 см;
Асфальтобетон пористый горячий на битуме БНД марки 6090 (Крупнозернистый Марка II) - 7 см;
Асфальтобетон пористый горячий на битуме БНД марки 6090 (Крупнозернистый Марка II) - 12 см;
Щебень фракционированный трудноуплотняемый 40-70 мм с заклинкой мелким щебнем - 28 см.
Подстилающий слой - рабочий слой из местного песка 30см
удовлетворяющий нормативным требованиям.
Характеристики материалов конструкции
Материал слоя и грунта
сопротивлению сдвигу
сопротивлению растяжению при изгибе
Асфальтобетон плотный горячий на битуме БНД марки 6090 (Тип Б Марка II)
Асфальтобетон пористый горячий на битуме БНД марки 6090 (Крупнозернистый Марка II)
Rдоп = 16 (1 -17101)0991 = 131 МПа
Щебень фракционированный трудноуплотняемый 40-70 мм с заклинкой мелким щебнем
Подстилающий слой песок средней крупности
Грунт земляного полотна
Wисх = 062 (1 + 17101)
2.1 Определение модуля упругости грунта
Расчетная влажность грунта
= 062Wт – средняя влажность грунта в долях от Wт;
= 01 – коэффициент вариации влажности;
t = 171 – коэффициент нормированного отклонения;
Wр = 062 (1 + 01 171) = 073
Характеристики грунта:
Район строительства дороги расположен в Белгородской области (III дорожно-климатическая зона). Перспективная интенсивность движения составляет 2500 автсут в том числе грузовых автомобилей 1300 автсут автобусов – 100 автсут.
Требуемый модуль упругости дорожной одежды
Етр = 255 МПа > Еminтр = 230 МПа.
2.2 Осушение дорожной одежды
Для отвода воды из основания дорожной одежды предусмотрен дренирующий песчаный слой устраиваемый на всю ширину земляного полотна.
Толщина дренирующего слоя необходимая для временного размещения воды накапливающаяся в основании:
зим – коэффициент заполнения влагой пор в дренирующем слое к началу оттаивания;
n – пористость уплотненного материала;
hзап – дополнительная толщина слоя для обеспечения устойчивости материала дренирующего слоя под действием кратковременных нагрузок;
h’кап –приведенная высота для капиллярной воды над уровнем свободной воды;
Q – количество воды накапливающейся в дренирующем слое за время запаздывания tзап;
q – среднесуточный суммарный приток воды в основание;
Кп – коэффициент пик учитывающий неравномерность поступления воды в процессе оттаивания и атмосферных осадков;
Кг – коэффициент гидрологического запаса;
tзап – время запаздывания начала работы водоотводящих устройств;
Принимаем толщину песчаного слоя 30 см.
2.3 Расчет конструкции на морозоустойчивость
Требуемая общая толщина дорожной одежды:
Zм = Z1ср Кугв Кпл Кнагр Кст Кв где
Z1ср – средняя толщина слоев из стабильных материалов;
Кугв – коэффициент учитывающий глубину залегания УГВ;
Кпл – коэффициент зависящий от степени уплотнения грунта;
Кнагр – коэффициент учитывающий влияние нагрузки от собственного веса вышележащей конструкции на грунт в промерзающем слое и зависящий от глубины промерзания;
Кст – коэффициент учитывающий влияние структуры грунта естественного сложения;
Кв – коэффициент зависящий от расчетной влажности грунта;
Zм = 82 043 11 1 1 1 = 39 см.
Конструкция удовлетворяет требованию морозоустойчивости.
2.4 Расчет толщины дорожной одежды по допустимому упругому прогибу
Расчет заключается в определении такой толщины слоя щебеночного основания которой будет соответствовать общий модуль упругости дорожной одежды равный требуемому модулю Егр = 255 МПа.
Общий модуль упругости на поверхности слоя МПа
Щебень гранитный с заклинкой мелким
2.5 Проверка на устойчивость против сдвига
Рассчитанную по упругому прогибу многослойную одежду приводим к двухслойной системе подстилающее полупространство которой имеет модуль упругости равный модулю упругости грунта Е2 = Егр = 67 МПа угол внутреннего трения = 36 и сцепление С = 0013 МПа. Толщину верхнего слоя системы принимаем равной суммарной толщине дорожной одежды h = 5 + 7 + 12 + 28 + 30 = 82 см а его модуль упругости определяем как средневзвешенное значение модулей упругости всех слоев
условие при котором в конструктивном слое не образуются деформации сдвига выражается неравенством:
а.м – максимальное активное напряжение сдвига от расчетной временной нагрузки;
а.в – активное напряжение сдвига от собственного веса слоев дорожной одежды;
а.доп – допустимое активное напряжение сдвига.
ЕсрЕ2 = 551267 = 823
а.мр = 0015р = 06 МПа
а.м + а.в = 00060 МПа
R1 – коэффициент учитывающий снижение сопротивления сдвигу под действием повторяющихся нагрузок;
R2 – коэффициент запаса;
с – нормированное сцепление в грунте;
Rпр – коэффициент учитывающий эксплуатационные требования к дорожной одежде;
n – коэффициент перегрузки при движении автомобиля;
m – коэффициент учитывающий условия взаимодействия слоев на контакте;
Так как фактическое активное напряжение сдвига меньше допустимого 00060 00073 условие прочности на сдвиг в грунтовом основании удовлетворяется.
2.6 Песчаный подстилающий слой
Средний модуль упругости слоев дорожной одежды расположенных выше песчаного
Эквивалентный модуль упругости на поверхности песчаного слоя Еэкв = 653 МПа
hД = 5233 = 16; Е1Е2 = ЕсрЕобщ = 800653 = 1225
= 40 - угол внутреннего трения песка;
а.м = 00075 06 = 00045 МПа
а.м + а.в = 00045 – 00020 = 00025 МПа
Условие прочности на сдвиг в песчаном основании удовлетворяется.
2.7 Проверка на растягивающие напряжения в связных слоях
В монолитных слоях (из асфальтобетона и щебня обработанного битумом) возникающие при прогибе дорожной одежды растягивающие напряжения т не должны превышать предельно допустимого растягивающего напряжения для материала слоя. Проверку на растягивающие напряжения выполняем для нижнего слоя асфальтобетонного покрытия и монолитного слоя основания из щебня обработанного битумом.
Для асфальтобетонного покрытия находим средний модуль упругости двух его слоев
Модуль упругости на поверхности верхнего слоя основания
Пользуясь монограммой определяем максимальное удельное растягивающее напряжение .
Полное растягивающее напряжение где
Р – расчетное давление на покрытие (Р = 06 МПа).
г = 085 06 265 = 135 МПа
Полученное г = 135 меньше допустимого растягивающего напряжения для асфальтобетона нижнего слоя.
г = 085 06 071 = 036 МПа
6 Rи = 10 МПа – условие выполнено.
3 Расчет второго варианта дорожной одежды
Щебеночно-мастичный асфальтобетон на битуме БНД марки 6090 ЩМА-15 - 5 см;
Асфальтобетон пористый горячий на битуме БНД марки 6090 (Крупнозернистый Марка I) - 6 см
Асфальтобетон пористый горячий на битуме БНД марки 6090 (Крупнозернистый Марка II) – 8 см
Щебеночно-песчаная смесь С4 0х80 мм – 39 см;
Щебеночно-мастичный асфальтобетон на битуме БНД марки 6090 ЩМА- 15
Асфальтобетон пористый горячий на битуме БНД марки 6090 (Крупнозернистый Марка I)
Щебеночно-песчаная смесь С4 0х80 мм
Суглинок укрепленный 7% цемента М-20
= 062Wт Wисх = 062 (1 + + 17101)
Далее расчет по выше приведенным формулам.
3.1 Осушение дорожной одежды
Принимаем толщину песчаного слоя 25 см.
3.2 Расчет конструкции на морозоустойчивость
Zм = 80 055 11 1 1 1 = 484 см
3.3 Расчет толщины дорожной одежды по допустимому упругому прогибу
ЩМА Аб верхнего слоя покрытия
Аб нижнего слоя покрытия
Аб верхнего слоя основания
Щебеночно-песчаная смесь С4
3.4 Проверка на устойчивость против сдвига
h = 5 + 6 + 10 + 15 + 15+30 = 81 см
ЕсрЕ2 = 547567 = 817hД = 8133 = 245 = 36
а.мр = 0008р = 06 МПа
а.м = 0008 06 = 00048
а.м + а.в = 00016 МПа
Так как фактическое активное напряжение сдвига меньше допустимого 00016 00073 условие прочности на сдвиг в грунтовом основании удовлетворяется.
3.5 Песчаный подстилающий слой
hД = 5033 = 152; Е1Е2 = ЕсрЕобщ = 804139 = 578; = 42
а.мр = 0011р = 06 МПа
а.м = 0011 06 = 00066 МПа
а.м + а.в = 00038 МПа
3.6 Проверка на растягивающие напряжения в связных слоях
Проверку на растягивающие напряжения выполняем для нижнего слоя асфальтобетонного покрытия и монолитного слоя основания из щебня обработанного битумом.
Для асфальтобетонного покрытия
г = 085 064 260 = 130 МПа
Полученное г = 130 меньше допустимого растягивающего напряжения для асфальтобетона нижнего слоя.
г = 085 064 032 = 016 МПа
6 Rи доп = 10 МПа – условие выполнено.
Обе конструкции дорожной одежды удовлетворяют всем выдвинутым требованиям выбираем 2 вариант - ввиду лучших физико-эксплуатационных свойств.
содержание.docx
1 Характеристика района строительства
1.1 Природные условия района строительства
1.3 Растительность и почвы
1.4 Гидрологические условия
1.5 Геологическое строение
2 Технико-экономическая характеристика района.
2.2 Характеристика экономики района тяготения
2.3 Транспортная сеть района тяготения
2.4 Объемы перевозок и интенсивность движения
2.4.1 Объемы перевозок
2.4.2 Перспективная интенсивность движения
3 Технические параметры автодороги
Раздел 2 Проектирование и расчет конструкции дорожной одежды
2 Расчет первого варианта дорожной одежды
2.1 Определение модуля упругости грунта
2.2 Осушение дорожной одежды
2.3 Расчет конструкции на морозоустойчивость
2.4 Расчет толщины дорожной одежды по допустимому упругому прогибу
2.5 Проверка на устойчивость против сдвига
2.6 Песчаный подстилающий слой
2.7 Проверка на растягивающие напряжения в связных слоях
3 Расчет второго варианта дорожной одежды
3.1 Осушение дорожной одежды
3.2 Расчет конструкции на морозоустойчивость
3.3 Расчет толщины дорожной одежды по допустимому упругому прогибу
3.4 Проверка на устойчивость против сдвига
3.5 Песчаный подстилающий слой
3.6 Проверка на растягивающие напряжения в связных слоях
Раздел 3 Дорожно-строительные материалы и их свойства
1 Минеральный порошок
5 Адгезионная присадка «АМДОР-10»
6 Добавки для теплого асфальтобетона
Раздел 4 Разработка технологии приготовления теплого щебеночно-мастичного асфальтобетона
1 Состав и структура щебеночно-мастичного асфальтобетона
2 Исследование свойств битума с добавками для теплого асфальтобетона
3 Подбор состава щебёночно-мастичного асфальтобетона
4 Технические требования к ЩМА
5 Расчёт состава асфальтобетонной смеси
6 Выбор технологического оборудования для введения добавок
7 Технология приготовления асфальтобетонной смеси
8 Устройство верхнего слоя покрытия толщиной 5 см из теплого щебеночно-мастичного асфальтобетона ЩМА-15
Раздел 5 Контроль качества работ
1 Контроль качества работ при возведении земляного полотна
2 Контроль качества работ при устройстве дорожной одежды
Раздел 6 Технико-экономические показатели строительства
1 Стоимость строительства
2 Сводный сметный расчет
лист6. обоснование применения теплых смесей.dwg

В СССР теплый асфальтобетон приготавливали на битумах
пониженной вязкости либо жидких битума и укладывли при 40-80 С
(иногда до 100 С). Его формирование
сопровождавшееся испарением
легких фракций с одновременным доуплотнением транспортными
В Германии теплая асфальтобетонная смесь укладывалась в
чем больше ожидалась интенсивность движения
вяжущее применялось;
температура смеси при укладке не ниже 50 С;
оговаривались нормы расхода смеси: при толщине слоя 1 см - не
максимальная толщина слоя - не более 3 см
В и Е мелкозернистого холодного асфальто-
бетона по вязкости и условиям укладки был близок к теплому
асфальтобетону в СССР;
холодный асфальтобетон укладывался в теплом состоянии.
что асфальтобетоны на полувязких битумах
обладают большей трещиностойкостью
применение полувязких битумов облегчает работы при
отрицательных температурах.
Голландии и ряде других стран при транспортировке
битум разжижали керосином
креозотовым маслом и другими
Сравнительная таблица плотности вырубок
асфальтобетона (строительство ад Белгород-Губкин
Результаты испытаний теплого асфальтобетона
Особенности горячих смесей
Работа при высокой температуре вынуждена из-за:
Необходимости полного удаления влаги из щебня;
Необходимости полного обволакивания щебня битумом;
Необходимости вести процесс в сжатых временных рамках;
Обеспечения технологичности;
Обеспечения плотности;
Обеспечения когезии;
Предотвращения колейности.
Особенности теплых смесей
Рабочая температура битума зависит от процесса вакуумной перегонки на НПЗ.
Для снижения выбросов необходимо снизить температуру нагрева щебня.
охлаждение битума до
температуры щебня идет очень быстро
оно происходит в ходе распределения
битума по поверхности щебня.
Для теплых смесей необходимо обеспечивать их хорошую обволакиваемость и
а также решить связанные с ними проблемы.
Ожидаемые преимущества теплых битумных смесей:
Замедление старения битума при смешивании
транспортировке и укладке;
Уменьшение трещинообразования при охлаждении слоя;
Более легкое формирование стыков;
Облегчение очистки оборудования;
Более безопасное проведение работ;
Снижение потребления топлива;
Снижение выбросов CO2
Расширение зоны обслуживания АБЗ: производство в горячем виде - укладка в
Продление строительного сезона;
Ускоренное открытие движения.
С 2002 года поведен большой объем НИР и полевых испытаний теплых смесей
характеризующие теплую аб смесь:
Проверяются в лаборатории: технологичность (подвижность)
прочие характеристики;
Выбросы в атмосферу;
Энергопотребление (топливо
Производительность перемешивания при постоянной скорости подачи;
Конечная пористость;
Результаты испытаний кернов на пористость и когезию;
Однородность поверхности.
Виды проведенных промышленных испытаний:
Пенетрация от 1020 до 70100;
Содержание вяжущего: 4
Способ производства: непрерывный или циклический;
Типы щебня: кислыйщелочной 0 - 14
более высокое содержание
Тип завода: циклического и непрерывного типа;
Температура смешивания: 110 - 135 С;
Температура укатки: 90 - 120 С;
Длительность храненияперевозки: до 4-х часов;
Плохие погодные условия: температура поверхности земли +3 С
пронецаемостью 3550;
Открытие движения: немедленно.
Теплые асфальтобетоны все больше и больше заинтересовывают дорожных
строителей по всему миру;
Теплые асфальтобетонные смеси можно производить:
Изменив технологию производства
С помощью введения добавок;
Добавки можно применять
не внося изменения в процесс и при температуре ниже 100 С;
Дозировка добавки в смесь: 2 - 5 кгт;
Добавки обеспечивают проведение процесса при низкой температуре (длительной
транспортировке плохой погоде);
Характеристики теплых смесей в стандартных тестах аналогичны характеристикам
Современные теплые асфальтобетонные смеси:
Изменение параметров
Лабораторное сравнение горячих и теплых аб
Горячая смесь (ГАБС): нагрев до 160 С. перемешивание при 160 С
Теплая смесь (ТАБС): нагрев до 120 С
перемешивание при 100 С
История теплых асфальтобетонных смесей:
Теплый асфальтобетон - материал
полученный уплотнением
при t=40-90 С рассчитанной и приготовленной при t=90-130 С смеси
минерального порошка и битума марок БНД 130200
происходило в течение нескольких недель.
Новые технологии позволяю понизить температуру перемешивания
асфальтобетонной смеси
приготавливаемой на вязком битуме
(с пенетрацией 40-130) на 20-40 С. Это достигается за счет относительно
новых физико-химических эффектов
приводящих к снижению сопротивления
смеси сдвигу во время ее приготовления и укатки. Диапазон приготовления
таких смесей от 105 С до 125 С. Их применение позволяет снизить
уменьшить выбросы загрязняющих веществ в атмосферу
сопровождающий укладку горячей смеси
снизить интенсивность
. увеличить радиус возки и продлить строительный сезон.
Сравнение параметров горячих и теплых аб смесей
в Волгоградской области в ноябре 2008 года
Условия приготовления укладки и состав асфальтобетона
Условия для приготовления укладки
Температура призводства
Температура укладки смеси
Дозировка добавки Секабаз
Температура воздуха при
Состав асфальтобетона
Песок природный речной
Минпорошок неактивирован-
ный после дезинтегратора
Битум БНД 6090 Лукойл
Стойкость добавки в битуме при 160 С (сутки
Ожидаемая экономия при производстве и укладке 1 тонны смеси - 150-200 руб.тонна
Результаты испытаний вырубок
Пористость минеральной части
Остаточная пористость асфаль-
Предел прочности на сжатие
Водостойкость при длительном
Сцепление битума с минеральной
частью по ГОСТ 12801-98
Проект производства работ по строительству автомобильной дороги I технической категории
Технология и организация строительного производства
Обоснование применения теплых смесей
Изм. Кол.уч.Лист Дата
Руководит. Соломенцев
Консульт. Соломенцев
ГОСУНИВЕРСИТЕТ-УНПК" АСИ кафедра "САД
ДП 2012 270205 070755 АД и А
лист4. стройгенплан.dwg

Бетонные бортовые камни
Пескоцементная смесь
автомобильная дорога 20 км
Сборные жб лотки длиной свыше 3 м
автомобильная дорога 24 км
автомобильная дорога 28 км
Жб звенья труб длиной свыше 3 м
автомобильная дорога 32 км
автомобильная дорога 21 км
Асфальтобетонная смесь
автомобильная дорога 23 км
автомобильная дорога 1567 км
автомобильная дорога 1300 км
Стабилизатор "Viatop-66
автомобильная дорога 685 км
и водопропускных тру
Возрожд. Донбаса" (5)
Гайворонский спецкарьер
Кременьчуг "Кварц" (4)
Щебень фр. 40-70 мм (20-80 мм)
Отсев (ЩПС) фр. 0-10 мм
Транспортная схема поставки материалов и изделий
Ведомость объемов работ
Глава 1. Подготовительные работы
Переустройство кабелей связи
Переустройство газопровода
Переустройство водопровода
Подпорная стенка (Н-3
Глава 2. Земляное полотно
Укрепительные работы
Рекультивация земель
Глава 3. Дорожная одежда
Устройство водосбросных сооружений
Устройство разделительной полосы
Глава 4. Искусственные сооружения
Мост через водохранилище
Путепровод через железную дорогу
Путепровод на транспортной развязке на ПК 92+72
Овоидальная труба отв. 3
м с быстротоком на ПК 28+60
Круглая жб косогорная труба отв. 1
Круглая жб труба отв. 1
м с водоприемным колодцем на ПК 42+85
Круглые жб трубы отв. 1
Глава 5. Пересечения и примыкания
Устройство примыканий и пересечений
Жб трубы на съездах и подъезде
Кольцевая развязка на ПК 0+00
Кольцевая развязка на ПК 66+85
-х уровневая транспортная развязка на ПК 99+72
Глава 6. Дорожные устройства и обстановка дороги
Автобусные остановки
Разметка проезжей части
Глава 9. Временные здания и сооружения
Глава 10. Прочие работы и затраты
связанное с производством работ в зимнее время
Затраты по перевозке работников автомобильным транспортом - 0
Непредвиденные работы и затраты 1
Итого с непредвиденными
трасса автомобильной дороги
Проект производства работ по строительству автомобильной дороги I технической категории
Технология и организация строительного производства
Изм. Кол.уч.Лист Дата
Руководит. Соломенцев
Консульт. Соломенцев
ГОСУНИВЕРСИТЕТ-УНПК" АСИ кафедра "САД
ДП 2012 270205 070755 АД и А
лист1. план автомобильной дороги.dwg

Проектирование автомобильной дороги
План автомобильной дороги
ПЛАН АВТОМОБИЛЬНОЙ ДОРОГИ
Изм. Кол.уч.Лист Дата
Руководит. Соломенцев
Таврово-Соломино-Разумное
Ведомость углов поворота
прямых и круговых кривых
ГОСУНИВЕРСИТЕТ-УНПК" АСИ кафедра "САД
ДП 2012 270205 070755 АД и А
лист14. организация безопасности движения.dwg

Проект производства работ по строительству автомобильной дороги I технической категории
План автомобильной дороги
Должность Фамилия Дата
Руководит. Соломенцев
Примечания: i-1.7708
Схема разработана согласно: i-1.1833
- ГОСТ Р 52289-2004 «Технические средства организации дорожного движения. Правила применения дорожных знаков
дорожных ограждений и направляющих устройств»; - ГОСТ Р 52290-2004 «Технические средства организации дорожного движения. Знаки дорожные. Общие технические требования»; - ГОСТ Р 51256-99 «Разметка дорожная. Типы и основные параметры. Общие технические требования»; - типовых конструкций 3.503.1-89 «Ограждения на автомобильных дорогах». i-1.7708
Опоры знаков и фундаменты приняты согласно типовых конструкций 3.503.9-80 «Опоры дорожных знаков на автомобильных дорогах». 3. Уровень удерживающей способности : i10
У3 - соответствует энергии удара 250 кДж У4 - соответствует энергии удара 300 кДж У5 - соответствует энергии удара 350 кДж в соответствии с ТУ-5216-001-057658220-2007
Таблица подбора стоек дорожных знаков
Разметка 1.24.1 (знак 1.22)
Перильное ограждение 196 м
Перильное ограждение 153.36 м
Перильное ограждение 70.51 м
Перильное ограждение 43.53 м
Перильное ограждение 255.57м
Перильное ограждение 187.41м
-ДО250-0.75:-2.0÷1.08 (У3) 658 м
-ДО250-0.75:-2.0÷1.08 (У3) 66 м
-ДО250-0.75:-2.0÷1.08 (У3) 503 м
-ДО250-0.75:-2.0÷1.08 (У3) 596 м
-ДО250-0.75:-2.0÷1.08 (У3) 80 м
-ДО250-0.75:-2.0÷1.08 (У3) 536 м
-ДО250-0.75:-2.0÷1.08 (У3) 532 м
-ДО250-0.75:-2.0÷1.08 (У3) 580 м
-ДО300-0.75:-1.0÷1.08 (У4) 100 м
-ДО300-0.75:-1.0÷1.08 (У4) 388 м
-ДО350-1.1:-1.5÷1.23 (У5) 76 м
-ДО300-0.75:-1.0÷1.08 (У4) 324 м
-ДО300-0.75:-1.0÷1.08 (У4) 116 м
-ДО250-0.75:-2.0÷1.08 (У3) 14 м
-ДО350-1.1:-1.5÷1.23 (У5) 66 м
-ДО350-1.1:-1.5÷1.23 (У5) 58 м
-ДО350-1.1:-1.5÷1.23 (У5) 60 м
-ДО300-0.75:-1.0÷1.08 (У4) 114 м
-ДО300-0.75:-1.0÷1.08 (У4) 246 м
-ДО300-0.75:-1.0÷1.08 (У4) 258 м
-ДО300-0.75:-1.0÷1.08 (У4) 64 м
-ДО250-0.75:-2.0÷1.08 (У3) 40 м
-ДО250-0.75:-2.0÷1.08 (У3) 544 м
-ДО300-0.75:-1.0÷1.08 (У4) 222 м
-ДО300-0.75:-1.0÷1.08 (У4) 38 м
-ДО300-0.75:-1.0÷1.08 (У4) 214 м
-ДО300-0.75:-1.0÷1.08 (У4) 52 м
Мостовое барьерное ограждение
Мостовое перильное ограждение
-ДО250-0.75:-2.0÷1.08 (У3) 662 м
-ДО300-0.75:-1.0÷1.08 (У4) 272 м
-ДО250-0.75:-2.0÷1.08 (У3) 94 м
-ДО300-0.75:-1.0÷1.08 (У4) 282 м
Условные обозначения:
дорожный знак на стойке с указанием номера
по ГОСТ Р 52290-2004 и пикетного положения
дорожная разметка с указанием номера
по ГОСТ Р 51256-99 и протяженности в м
ОРГАНИЗАЦИЯ БЕЗОПАСНОСТИ ДВИЖЕНИЯ
Технология и организация строительного производства
Организация безопасности движения
Изм. Кол.уч.Лист Дата
Консульт. Соломенцев
ГОСУНИВЕРСИТЕТ-УНПК" АСИ кафедра "САД
ДП 2012 270205 070755 АД и А
Таблица установки ограждений
Барьерное ограждение ТУ 5216-001-05765820-2007
Перильное ограждение
Таблица установки стоек
Таблица устройства разметки
Номер разметки по ГОСТ Р 51256-99
Сплошная двойная линия
Прерывистая линия с соотношением штрихов 1:3
Прерывистая линия с соотношением штрихов 3:1
Прерывистая линия с соотношением штрихов 1:1
Площадная разметка (знак 1.22)
Таблица потребности дорожных знаков
Номер знака по ГОСТ Р 52290-2004
Предупреждающие знаки
Направление поворота
Пересечение с второстепенной дорогой
Предписывающие знаки
Объезд препятствия справа
Объезд препятствия справа или слева
Велосипедная дорожка
Знаки особых предписаний
Направления движения по полосам
Информационные знаки
Предварительный указатель направлений
Указатель направлений
Знаки дополнительной информации (таблички)
Расстояние до объекта
список литературы.docx
СНиП 2.07.01-89* «Градостроительство. Планировка и застройка городских и сельских поселений».
ОДН 218.046-01 «Проектирование нежестких дорожных одежд».
ГОСТ 9128-97 «Смеси асфальтобетонные дорожные аэродромные и асфальтобетон. Технические условия».
ГОСТ 31015-2002 «Смеси асфальтобетонные и асфальтобетон щебеночно-мастичные. Технические условия».
ГОСТ 25607-94 «Смеси щебеночно-гравийно-песчаные для покрытий и оснований автомобильных дорог и аэродромов. Технические условия».
ГОСТ 16557-78 «Порошок минеральный для асфальтобетонных смесей. Технические условия».
ГОСТ 52129 - 2003 «Порошок минеральный для асфальтобетонных смесей. Технические условия».
ГОСТ 12784 - 78 «Порошок минеральный для асфальтобетонных смесей. Методы испытаний».
ГОСТ 8736-93 «Песок для строительных работ. Технические условия».
ГОСТ 8267-93 «Щебень и гравий из плотных горных пород для строительных работ. Технические условия».
ГОСТ 3344-83 «Щебень и песок шлаковые для дорожного строительства. Технические условия».
ГОСТ 22245-90 «Битумы нефтяные дорожные вязкие».
ОСТ 218.010-98 «Вяжущие полимерно-битумные дорожные на основе блоксополимеров типа СБС. Технические условия».
ГОСТ 11508-74 «Битумы нефтяные. Методы определения сцепления битума с мрамором и песком».
ГОСТ 12.1.007-76 «Система стандартов безопасности труда. Вредные вещества. Классификация и общие требования безопасности».
ТУ-5718.030.01393697-99 «Технические условия. Смеси асфальтобетонные щебеночно-мастичные и асфальтобетон».
ГОСТ 12801-98 «Материалы на основе органических вяжущих для дорожного и аэродромного строительства. Методы испытаний».
ГОСТ 5180-84 «Грунты. Методы лабораторного определения физических характеристик».
ИСО 5725-2-94 «Точность (достоверность и сходимость) методов и результатов измерений».
СНиП 3.06.03-85 «Автомобильные дороги».
ГОСТ 30413-96 «Дороги автомобильные. Метод определения коэффициента сцепления колеса автомобиля с дорожным покрытием».
МДС 81.35-2004 «Методика определения стоимости строительной продукции на территории Российской Федерации».
ГЭСН-2001 «Государственные элементные сметные нормы».
ГЭСНм-2001 «Государственные элементные сметные нормы на монтаж оборудования».
ГСН 81-05-01-2001 «Сборник сметных норм затрат на строительство временных зданий и сооружений».
МДС 81.25-2004 «Методические указания по определению величины сметной прибыли в строительстве».
МДС 81.33-2004 «Методические указания по определению величины накладных расходов в строительстве».
«Методические рекомендации по оценке необходимого снижения звука у населенных пунктов и определению требуемой акустической эффективности экранов с учетом звукопоглощения». Росавтодор 2003.
Стебаков А. Кирюхин Г. Гопин О. «Щебеночно-мастичный асфальтобетон - будущее российских дорог». Строит. техника и технологии 2002.
«Строительство дорожных и аэродромных покрытий из щебеночно-мастичных асфальтобетонных смесей». 2003.
Бабков В.Ф. Андреев О.В. «Проектирование автомобильных дорог». Ч. III. 1979.
раздел5.КОНТРОЛЬ КАЧЕСТВА РАБОТ..docx
До начала работ по сооружению земляного полотна должно быть проверено соответствие принятых в проекте и действительных показателей состава (крупность частиц пластичность глинистых грунтов) и состояния (влажность плотность) грунтов в карьерах резервах выемках естественных основаниях. При наличии в зоне работ склонов и откосов круче 1:3 а также слабых грунтов следует проверять нивелированием отсутствие осадок и сдвигов земляного полотна в период строительства.
При операционном контроле качества сооружения земляного полотна следует проверять:
- правильность размещения осевой линии поверхности земляного полотна в плане и высотные отметки;
- толщину снимаемого плодородного слоя грунта;
- плотность грунта в основании земляного полотна;
- влажность используемого грунта;
- толщину отсыпаемых слоев;
- однородность грунта в слоях насыпи;
- ровность поверхности;
- поперечный профиль земляного полотна (расстояние между осью и бровкой поперечный уклон крутизну откосов);
- правильность выполнения водоотводных и дренажных сооружений прослоек укрепление откосов и обочин.
Проверку правильности размещения оси земляного полотна высотных отметок поперечных профилей земляного полотна обочин водоотводных и дренажных сооружений и толщин слоев следует производить не реже чем через 100 м (в трех точках на поперечнике) как правило в местах размещения знаков рабочей разбивки с помощью геодезических инструментов и шаблонов. Плотность грунта следует контролировать в каждом технологическом слое по оси земляного полотна и на расстоянии 15 - 20 м от бровки а по ширине слоя более 20 м - также в промежутках между ними. Контроль плотности следует производить на каждой сменной захватке работы уплотняющих машин но не реже чем через 200 м при высоте насыпи до 3 м и не реже чем через 50 м при высоте насыпи более 3 м.
Контроль плотности верхнего слоя следует производить не реже чем через 50 м. Дополнительный контроль плотности необходимо производить в каждом слое засыпки пазух труб над трубами в местах сопряжения с мостами. Контроль плотности следует производить на глубине равной 13 толщины уплотняемого слоя но не менее 8 см. Отклонение от требуемого коэффициента уплотнения в сторону уменьшения допускается не более чем в 10% определений от их общего числа и не более чем на 004. Глубину промерзания слоя сезонного оттаивания следует проверять по кернам (шурфам) не реже чем через 100 м. Сохранность мохо-растительного слоя проверяется визуально. Контроль влажности используемого грунта следует производить как правило в месте его получения (в резерве карьере) не реже одного раза в смену и обязательно при выпадении осадков. Плотность и влажность грунта следует определять по ГОСТ 5180-84[19]. Для текущего контроля допускается использовать ускоренные и полевые экспресс-методы и приборы.
Ровность поверхности земляного полотна контролируется нивелированием по оси и бровкам в трех точках на поперечнике не реже чем через 50 м. Поверхность основания земляного полотна и промежуточных слоев насыпи в период строительства не должна иметь местных углублений в которых может застаиваться вода.
Карта операционный контроля качества земляного полотна.
Контролируемые параметры
Предельные отклонения
Отметка бровки земляного полотна см
Ширина земляного полотна между осью и бровкой см
Поперечный уклоны %о
Ровность поверхности слоя (просвет под трехметровой рейкой) см
2 Контроль качества работ при устройстве дорожной одежды
При операционном контроле качества работ по устройству дорожной одежды следует контролировать по каждому укладываемому слою не реже чем через каждые 100 м:
- высотные отметки по оси дороги;
- толщину слоя неуплотненного материала по его оси;
- ровность (просвет под трехметровой рейкой на расстоянии 075 - 1 м от каждой кромки покрытия (основания) в пяти контрольных точках расположенных на расстоянии 05 м от концов рейки и друг от друга). При выполнении контролируемых работ разрешается применять новые быстродействующие приборы показатели которых сопоставимы с показателями традиционных приборов. При устройстве морозозащитных и дренирующих слоев необходимо контролировать соответствие качества материалов и песчаных грунтов требованиям проекта плотность материала и отсутствие его загрязнения. При устройстве дренирующего слоя контроль качества грунта следует производить в карьере путем отбора не менее 3 проб из каждых 500 м3 песчаного грунта и проводить его испытание с определением содержания пыли и глины и величины коэффициента фильтрации по действующему ГОСТу. Допускается устанавливать величину коэффициента фильтрации расчетным путем в зависимости от гранулометрического состава песчаного грунта. Плотность материала слоя необходимо контролировать в трех точках на поперечнике (по оси и кромок проезжей части) не реже чем через 100 м.
Карта операционного контроля качества основания.
Высотные отметки по оси мм
При устройстве слоев из аб на месте укладки смеси постоянно проводят контроль: температуры количества укладываемой смеси толщины слоя поперечного уклона ровности плотности прочности однородности аб покрытий по плотности и прочности. Обеспечения требуемых геометрических размеров аб покрытия добиваются настройкой рабочих органов асфальтоукладчиков при этом ширина покрытия не должна отличаться от проектной не более чем на 10 см а толщина слоя - на 10% а поперечный уклон - более чем на 5%. Для контроле плотности аб покрытий широкое применение получили радиационные методы (приборы РПП-1 и РВПП) вакуумные методы основанные на зависимости времени прохождения воздуха через поры аб в зависимости от его плотности. При отсутствии приборов для операционного контроля плотности испытывают керны или вырубки. Коэффициент уплотнения определяют по отношению средней плотности образцов кернов или вырубок взятых из покрытия p к средней плотности переформированных образцов p' из
тех же вырубок или кернов: К=pp'. Коэффициент уплотнения покрытия из горячих смесей должен быть для нижнего слоя не менее 098; а для верхнего слоя из смесей типа А и Б - 099; В Г и Д - 098. Кроме контроля плотности при отборе проб из покрытия измеряют толщину слоев и визуально оценивают прочность сцепления между слоями покрытия и основания.
Контролируют параметры шероховатости и коэффициента сцепления. Такое испытание проводят по методу песчаного пятна в результате которого вычисляют среднюю высоту шероховатой поверхности. Для оперативного контроля сцепных качеств покрытия на месте строительства целью которого является своевременное выявление и устранение дефектов поверхности используют портативный прибор Кузнецова (ППК) который позволяет
определять коэффициент сцепления покрытия без расчетов. Кроме этого постоянно контролируют качество продольных и поперечных сопряжений укладываемых полос.
Карта операционного контроля качества покрытия.
Поперечные уклоны %о
Контроль качества строительства покрытий из ЩМАС должен отвечать действующим правилам при устройстве конструктивных слоев из горячих асфальтобетонных смесей с учетом некоторых особенностей. При приготовлении щебеночно-мастичной асфальтобетонной смеси контролируют: качество всех компонентов температурный режим подготовки битума температуру готовой смеси и се качество. Работу дозаторов минеральных материалов битума и стабилизирующей добавки контролируют в установленном порядке руководствуясь инструкциями по эксплуатации соответствующего оборудования.
При входном контроле определяют качество поступающих на АБЗ материалов в каждой партии по соответствующим паспортам техническим свидетельствам и стандартам. Стабилизирующие добавки применяемые в смесях должны отвечать предъявляемым требованиям и соответствовать техническим спецификациям или свидетельствам поставщиков. Косвенным показателем качества применяемой добавки является стабильность показателя стекания вяжущего в выпускаемой смеси. Контроль осуществляет лаборатория АБЗ в соответствии с утвержденным технологическим регламентом.
При операционном контроле приготовления ЩМАС проверяют 2-3 раза в смену соблюдение установленного температурного режима и качество смешения. Смесь при выходе из смесителя должна быть однородной не содержать непокрытых битумом зерен и сгустков битума. По внешнему виду она должна представлять собой черную блестящую массу и не изменять внешний вид в течение смены.
Для приемочного контроля качества готовой смеси отбирают не менее одной пробы от каждой партии. Партией считают количество смеси одного состава выпускаемое на одной смесительной установке п течение смены но не более 1200 т. При изменении состава ЩМАС и во всех сомнительных и спорных случаях для испытаний отбирают дополнительные пробы. При приемосдаточных испытаниях пробы отбирают в соответствии с ГОСТ 12801-98 и определяют температуру отгружаемой смеси при выпуске из смесителя или накопительного бункера состав смеси водонасыщение предел прочности при сжатии при температуре 50°С и показатель стекания вяжущего.
При периодическом контроле дополнительно определяют пористость минеральной части остаточную пористость водостойкость при длительном водонасыщении коэффициент внутреннего трения предел прочности при сжатии при температуре 0 и 20°С и другие показатели предусмотренные в технологическом регламенте. Периодический контроль осуществляют не реже 1 раза в месяц а также при каждом изменении свойств материалов применяемых для приготовления смеси.
Испытания щебеночно-мастичных асфальтобетонных смесей проводят в соответствии с ГОСТ 12801-98[18] и ТУ-5718.030.01393697-99[17]. Образцы из ЩМАС формуют в цилиндрических формах диаметром 714 мм применяя метод вибрирования с последующим прессованием. В форму между двумя вкладышами и уплотняемой смесью рекомендуется помещать бумажные прокладки. Температура смеси при приготовлении образцов должна соответствовать требованиям.
Основным критерием качества приготовления смеси является точность соблюдения проектного состава. При этом особое внимание следует уделять контролю содержания битума и стабилизирующей добавки. Косвенным показателем содержания битума может служить величина водонасыщения в образцах которые формуются на асфальтобетонном заводе а показатель стекания вяжущего особенно чувствителен к содержанию стабилизирующей добавки в смеси.
Контроль качества щебеночно-мастичного асфальтобетона в покрытии производят по показателю водонасыщения или остаточной пористости образцов-кернов которые отбирают не раньше чем через сутки после укладки и уплотнения слоя. Определять коэффициент уплотнения покрытий из щебеночно-мастичного асфальтобетона не рекомендуется. Этот показатель является менее надежным так как характеризуется низкой повторяемостью и воспроизводимостью по ИСО 5725-2-94[20] вследствие малой толщины контролируемого слоя и высокого содержания щебня в смеси. При переформовке ЩМА наблюдается не только высокий разброс значений плотности в параллельных образцах но и заметно увеличивается дробимость в них щебня.
В процессе укладки смеси должны контролироваться:
- температура смеси в кузове каждого автомобиля-самосвала;
- толщина устраиваемого слоя покрытия;
- ровность и поперечные уклоны;
- качество устройства продольных и поперечных сопряжений полос;
- соблюдение заданных режимов работы асфальтоукладчиков и катков;
- качество ЩМА в покрытии.
Толщина слоя измеряется по отобранным из покрытия образцам-кернам. Результаты замеров не должны отклоняться от проектных значений более чем на 20%. Ровность и поперечный уклоны контролируются с помощью 3-метровой рейки. Шероховатость слоя износа ЩМА следует измерять методом «песчаного пятна» в соответствии со СНиП 3.06.03-85 «Автомобильные дороги»[21]. Коэффициент сцепления колеса автомобиля с увлажненной поверхностью покрытия оценивается по ГОСТ 30413-96[22]. Все результаты замеров заносятся в специальные карты контроля которые входят в перечень приемо-сдаточной документации.
Приёмку смесей проводят партиями.
При приёмке и отгрузке горячих смесей партией считают количество смеси одного состава выпускаемой на одной установке в течение одной смены но не более 600т. Количество поставляемой смеси определяют по массе. Смесь отгружаемую в автомобили взвешивают на автомобильных весах. Для проверки соответствия качества смесей требованиям стандарта проводят приемосдаточные и периодические испытания.
На каждую партию отгружаемой смеси потребителю выдают документ о качестве в котором указывают результаты приемосдаточных и периодических испытаний.
При приемосдаточных испытаниях смесей отбирают по ГОСТ 12801-98[18] одну объединённую пробу от партии и определяют:
температуру отгружаемой смеси при выпуске из смесителя или накопительного бункера;
зерновой состав минеральной части смеси;
предел прочности при сжатии при температуре 50°С и 20°С;
При периодическом контроле качества смесей определяют:
пористость минеральной части;
остаточную пористость;
предел прочности при сжатии при температуре 0°С (для горячих смесей);
сцепление битума с минеральной частью смесей;
сдвигоустойчивость и трещиностойкость при условии наличия этих показателей в проектной документации;
-однородность смесей.
Периодический контроль следует осуществлять не реже одного раза в месяц а также при каждом изменении материалов применяемых при приготовлении смесей Однородность смесей оцениваемую коэффициентом вариации рассчитывают ежемесячно.
При отгрузке смеси потребителю каждый автомобиль сопровождают транспортной документацией.
Потребитель имеет право проводить контрольную проверку соответствия асфальтобетонных смесей требованиям стандарта соблюдая стандартные методы отбора проб приготовления образцов и испытаний указанные в ГОСТ 12801-98[18] применяя при этом следующий порядок отбора проб.
Для контрольных испытаний асфальтобетонных смесей отгружаемых в автомобили отбирают по девять объединённых проб от каждой партии непосредственно из кузовов автомобилей.
Отобранные пробы не смешивают и испытывают сначала три пробы. При получении удовлетворительных результатов испытаний остальные пробы не испытывают. При получении неудовлетворительных результатов хотя бы одной пробы из трёх производят испытания остальных шести проб. В случае неудовлетворительных результатов повторных испытаний хотя бы одной пробы из шести партию бракуют.
При неоднородности горячих смесей оцениваемой визуально наличием зёрен минерального материала непокрытых битумом скоплением битума и минерального порошка а также при несоответствии температуры смеси требованиям смесь бракуют.
До устройства верхнего слоя покрытия из щебёночно-мастичной
асфальтобетонной смеси должны быть выполнены все подготовительные работы с оформлением актов.
Необходимо проверять температуру смеси в каждом автомобиле.
В процессе укладки необходимо контролировать толщину уложенного слоя через 100 м ровность и поперечный уклон не реже чем через 20 м. Особое внимание следует уделять контролю качества устройства
продольных и поперечных сопряжений с использованием трёхметровой рейки. Просвет под серединой рейки в месте сопряжения должен быть не более 6 мм. В процессе уплотнения необходимо контролировать соблюдение заданного режима уплотнения смеси. Уплотнение щебёночно-мастичного асфальтобетона контролируют по показателям остаточной пористости или водонасыщения образцов которые отбирают не ранее чем через сутки после окончания уплотнения в трёх местах на 7000 м2.
лист9. оценка эффективности добавок в битуме и ЩМАС.dwg

Предел прочности при
сжатии в водонасыщенном
Значение показателей при нагрузке
Таблица 2 - Показатели свойств асфальтобетонных образцов при разном
значении нагрузки на образец при формовании при температуре 160 С
Значение показателей при температуре
Таблица 3 - Показатели свойств асфальтобетонных образцов ЩМА-15
при усилии формования Р=10 т при разной температуре формования
Таблица 1 - Показатели свойств битума с добавками для теплого
Таблица 4 - Показатели свойств асфальтобетонных образцов ЩМА-15
при усилии формования образцов 10 т и температуре формования 60 С
Значение показателей свойств асфальтобетонных образцов
с различными добавками для теплого асфальтобетона
Таблица 5 - Показатели свойств асфальтобетонных образцов ЩМА-15
при усилии формования образцов 10 т и температуре формования 80 С
Проект производства работ по строительству автомобильной дороги I технической категории
Технология и организация строительного производства
Оценка эффективности добавок в битуме и ЩМАС
Изм. Кол.уч.Лист Дата
Руководит. Соломенцев
Консульт. Соломенцев
ГОСУНИВЕРСИТЕТ-УНПК" АСИ кафедра "САД
ДП 2012 270205 070755 АД и А
Рекомендуемые чертежи
- 24.04.2014
- 25.01.2023
- 29.07.2014
Свободное скачивание на сегодня
- 23.02.2023