Станок для резки полосовых заготовок (роликовые ножницы)




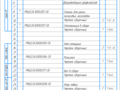
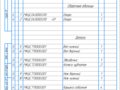
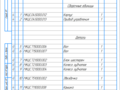
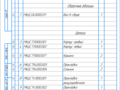
- Добавлен: 25.01.2023
- Размер: 2 MB
- Закачек: 0
Описание
Состав проекта
![]() |
![]() ![]() ![]() ![]() |
![]() ![]() ![]() ![]() |
![]() ![]() ![]() ![]() |
![]() ![]() ![]() ![]() |
![]() ![]() ![]() ![]() |
![]() ![]() ![]() ![]() |
![]() ![]() ![]() ![]() |
![]() ![]() ![]() ![]() |
![]() ![]() ![]() ![]() |
![]() ![]() ![]() ![]() |
![]() ![]() ![]() |
![]() ![]() ![]() ![]() |
![]() ![]() ![]() ![]() |
![]() ![]() ![]() ![]() |
![]() ![]() ![]() ![]() |
![]() ![]() ![]() |
![]() ![]() ![]() ![]() |
![]() ![]() ![]() ![]() |
![]() ![]() ![]() ![]() |
![]() ![]() ![]() ![]() |
![]() ![]() ![]() ![]() |
![]() ![]() ![]() ![]() |
![]() ![]() ![]() ![]() |
Дополнительная информация
Лист 9.cdw

Лист 8_2.cdw

Лист 7_1.cdw

Лист 5...6,5.spw

Лист 8_1.cdw

Лист 9.spw

Листы 3...4.cdw

Опора.spw

Лист 7.cdw

Звездочка.cdw

ВЕДОМОСТЬ.CDW

Лист 5...6,5.cdw

Лист 1...2.cdw

Листы 3...4.spw

Лист 8_1.spw

Экономика.cdw

Опора.cdw

Лист 8_2.spw

Опора-01.spw

Лист 1...2.spw

Лист 7.spw

Лист 7_1.spw
