Спроектировать токарно-винторезный станок




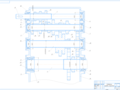


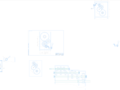
- Добавлен: 25.01.2023
- Размер: 1 MB
- Закачек: 1
Описание
Состав проекта
![]() |
![]() |
![]() ![]() ![]() ![]() |
![]() |
![]() ![]() ![]() ![]() |
![]() ![]() ![]() ![]() |
![]() ![]() ![]() ![]() |
![]() ![]() ![]() |
![]() |
Дополнительная информация
Развёртка коробки скоростей.cdw

Шпиндельный узел.cdw

Свертка коробки скоростей.cdw

Кинематическая схема токарно-винторезного станка.cdw
