Шток соединительного узла пневмоцилиндра



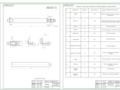
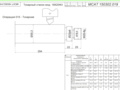
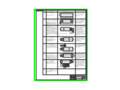
- Добавлен: 24.01.2023
- Размер: 364 KB
- Закачек: 0
Описание
Состав проекта
![]() |
![]() ![]() ![]() ![]() |
![]() ![]() ![]() |
![]() ![]() ![]() ![]() |
![]() ![]() ![]() ![]() |
Дополнительная информация
кп по отм 1 лист.dwg

Таблица - Назначение методов и видов обработки поверхностей
Маршрут обработки поверхности
Точение черновое для торца 1
точение чистовое для торца 2
Фаска1х45° Фаска 2х45° Канавка В=4
q*; Точение черновое
q*; Точение черновое
протачивание канавки
Назначение методов и видов обработки поверхностей
курсовая основ тм.docx
Иллюстративная часть - 2 листа формата А1 1 лист формата А3
ТЕХНОЛОГИЧЕСКИЙ ПРОЦЕСС МАРШРУТНАЯ ТЕХНОЛОГИЯ ТЕХНОЛОГИЧЕСКАЯ ОПЕРАЦИЯ ТЕХНОЛОГИЧЕСКАЯ ОСНАСТКА АВТОМАТИЗАЦИЯ КОНТРОЛЯ.
Объект: шток 00-000.06.22.22.03 пневмоцилиндра 00-000.06.22.22.00.
Цель: повышение эксплуатационных характеристик детали «Шток» соединительного узла пневмоцилиндра.
Темой данной работы является проектирование технологического процесса изготовления и упрочнения детали шток соединительного узла пневмоцилиндра
Исходя из условий эксплуатации и технических условий выбрана марка стали: Сталь 45 ГОСТ 1050-88.
Нормативные ссылки 8
Назначение конструкция детали 9
Анализ технологичности конструкции детали 11
Определение типа производства 13
Выбор технологических баз 19
Выбор вариантов технологических маршрутов обработки поверхностей детали 2
Разработка маршрутной технологии. Построение операций 21
Выбор оборудования и средств технологического оснащения 23
Расчет припусков на обработку и операционных размеров 30
Расчет режимов резания 32
Расчет норм времени операций техпроцесса 37
Список использованных источников 42
Машиностроительный комплекс представляет сложное межотраслевое образование включающее машиностроение и металлообработку. Машиностроение объединяет специализированные отрасли сходные по технологии и используемому сырью. Металлообработка включает промышленность металлических конструкций и изделий а также ремонт машин и оборудования.
Машиностроение является ведущей отраслью тяжелой индустрии страны. Создавая наиболее активную часть основных производственных фондов - орудия труда машиностроение в значительной степени оказывает влияние на темпы и направления научно-технического прогресса в различных отраслях хозяйственного комплекса на рост производительности труда и другие экономические показатели определяющие эффективность развития общественного производства. На долю машиностроения приходится около 15 объема выпускаемой продукции промышленности страны почти 14 основных промышленно-производственных фондов и 13 промышленно-производственного персонала.
Ассортимент выпускаемой продукции машиностроения отличается большим многообразием что обусловливает глубокую дифференциацию его отраслей и влияет на размещение производств выпускающих различные виды продукции. В настоящее время в машиностроении по степени технической оснащенности выделяют пять уровней технологического уклада.
Первый уровеньпредставлен производством оборудования для горнодобывающей промышленности и предприятий перерабатывающих первичное сырье.
Второй уровеньсвязан с производством оборудования для сельского хозяйства.
Третий уровеньпредставлен производством оборудования для черной и цветной металлургии производством строительных материалов.
Четвертый уровеньвключает автомобильную и подшипниковую промышленность электротехническое машиностроение и др.
Пятый уровеньпредставляют предприятия связанные с высокими технологиями: это - производство ЭВМ оптико-волоконная техника роботостроение производство станков и оборудования с числовым программным управлением (ЧПУ) ракетно-космическое производство авиационная промышленность.
Сложность перехода машиностроения на инновационный путь развития состоит в том что при реализации стратегических целей вхождения страны в постиндустриальное общество необходимо в исторически короткое время решать одновременно две задачи: модернизацию самого машиностроения и техническое перевооружение других отраслей экономики. К сожалению приходится констатировать что в нынешнем состоянии предприятия российского машиностроения могут осуществлять производство конкурентоспособной продукции только для сравнительно узких сегментов рынка. Большинство предприятий не может обеспечить комплекс необходимых характеристик конкурентоспособности своей продукции. Но этого часто и не требуется так как в рыночной экономике немалую часть таких характеристик достигают крупные стратегические посредники. Они признаны занять ту нишу которую ранее занимала государственная система материально-технического обеспечения. Следовательно формирование и поддержка таких посредников может считаться одним из основных элементов государственной политики в области повышения конкурентоспособности предприятий машиностроения.
Специалисты констатируют что товарная структура внешней торговли РФ в начале 2011 года не претерпела кардинальных изменений. В экспорте преобладали топливно-энергетические товары на долю которых пришлось более 50% всех поставок а также черные и цветные металлы (17%); вимпорте–продукциямашиностроения(353%) продовольствие и товары широкого потребления.
Для решения поставленных задач следует уделять больше внимания подготовке будущих специалистов. Уровень развития машиностроения - один из самых значимых факторов технического прогресса так как коренные преобразования в любой сфере производства возможны лишь в результате создания более совершенных машин и разработки принципиально новых технологий. Развитие и совершенствование технологий производства сегодня тесно связаны с автоматизацией созданием технических комплексов широким использованием вычислительной техники применением оборудования с числовым программным управлением. Все это составляет базу на которой создаются автоматизированные производства становятся возможными оптимизация технологических процессов создание гибких автоматизированных комплексов.
Комплексная механизация и автоматизация производственных процессов переоснащение машиностроительных предприятий современными металлорежущими станками типизация и стандартизация технологических процессов повсеместное внедрение в практику технологического проектирования электронных вычислительных машин привели к переоценке существующих методов проектирования.
В настоящее время технологическое проектирование - это комплексная система взаимодействия средств и методов обуславливающих создание высококачественной технологической документации на основе широкого применения стандартных технологических решений. Освоение машиностроительными предприятиями новой технологической документации создало предпосылки для разработки и внедрения автоматических систем управления производственными процессами в целом.
В настоящем курсовом проекте использованы ссылки на следующие нормативные документы:
ГОСТ 2789 – 73 ЕСКД. Шероховатость поверхности. Параметры и характеристики.
ГОСТ 1050-88 ЕСКД. Прокат сортовой калиброванный со специальной отделкой поверхности из углеродистой качественной конструкционной стали. Общие технические условия.
ГОСТ 14.004 – 83 ЕСКД. Технологическая подготовка производства. Термины и определения основных понятий.
ГОСТ 2590 – 88 ЕСКД. Прокат стальной горячекатаный круглый.
ГОСТ 25347 – 82 ЕСКД. Основные нормы взаимозаменяемости. Единая система допусков и посадок.
ГОСТ 21495 – 76 ЕСКД. Базирование и базы в машиностроении. Термины и определения.
ГОСТ 28527 – 90 ЕСКД. Фрезы дисковые трехсторонние. Типы и размеры.
ГОСТ 24644 – 81 ЕСКД. Концы шпинделей и хвостики инструментов сверлильных расточных и фрезерных станков. Размеры. Технические требования.
ГОСТ 21167 – 75 ЕСКД. Тиски станочные винтовые самоцентрирующие рычажные для круглых профилей. Конструкция и основные размеры.
ГОСТ 19258 – 73 ЕСКД. Стержни под нарезание метрической резьбы. Диаметры.
ГОСТ 2675 – 80 ЕСКД. Патроны самоцентрирующие трехкулачковые. Основные размеры.
ГОСТ 18259 – 72 ЕСКД. Центры упорные. Конструкция и размеры.
ГОСТ 14034 – 74* ЕСКД. Отверстия центровые. Размеры.
ГОСТ 18868 – 73 ЕСКД. Резцы токарные проходные отогнутые с пластинами из быстрорежущей стали. Конструкция и размеры.
ГОСТ 166 – 89 ЕСКД. Штангенциркули. Технические условия.
Назначение конструкция детали.
Данная деталь относится к классу 71. Детали – тела вращения типа колец дисков шкивов блоков стержней втулок стаканов колонок валов осей штоков шпинделей и др.
При поступлении сжатого воздуха через центральное коническое отверстие крышки задней в полость под диском шток выполняет движение влево совершая работу – преобразование энергии сжатого воздуха. Штоки одностороннего действия применяют в тех случаях когда требуется передача усилия только в одном направлении а возврат происходит беспрепятственно а также тогда когда из соображений безопасности должно обеспечиваться втянутое положение штока при отключении питания (падении давления сжатого воздуха в пневмосети).
Шток служит для передачи крутящего момента и базирования вращающихся деталей. Исходя из служебного назначения исполнительными поверхностями штока будут являться шейки под подшипники и шейки на которых расположены зубчатое колесо и другие вращающиеся с ним детали.
Штоки в основном изготавливают из конструкционных и легированных сталей обладающих высокой прочностью хорошей обрабатываемостью малой чувствительностью к концентрации напряжений а для повышения износостойкости – способностью подвергаться термической обработке. В качестве материал заготовки выбираем сталь 45 по ГОСТ 1050-88. Для уменьшения нагрева и износа уплотнительных колец а также для уменьшения усталостных разрушений (так как шток работает при знакопеременных нагрузках) шероховатость рабочей поверхности должна быть незначительной. Для уменьшения концентраторов напряжений и увеличения срока службы штока все переходы между диаметрами выполняются с округлениями и с небольшой шероховатостью а резьба выполняется не нарезанием а накатыванием.
Сталь 45- сталь конструкционная углеродистая качественная. Сталь 45 марки широко используется в промышленности в частности она идет на изготовление валов (распределительных и коленчатых) шестерней блиндажей шпинделей кулачков цилиндров и т.п. 45-й металл позволяет получать нормализованные улучшаемые поверхности для которых характерна повышенная прочность. При необходимости на порядок улучшить характеристики готовых изделий технологи применяют металл марки 45 легированный хромом – 45х (доля хрома 08-11%) или литейную сталь 45л.
Сталь 45 считается материалом трудносвариваемым однако ему не свойственна отпускная хрупкость. Это достаточно весомый фактор при создании конструкций сложных форм и конфигураций. Сварка данного металла производится 2 способами: КТС и РДС. Определение физико-химических свойств и химического состава стали смотреть в таблице 1 2.
Таблица 1 – Физико – механические свойства стали 45
ударная вязкость ан·105 Джм3
Таблица 2 – Химический состав материала детали в %
Анализ технологичности конструкции детали
Шток должен изготавливаться в соответствии с требованиями настоящего стандарта по технологическому регламенту утвержденному в установленном порядке или по нормативно-технической документации. На поверхности штока не должно быть каких-либо дефектов. Основными конструкционными составляющими штока являются: фаска центровое отверстие канавка шпоночный паз лыска.
Технологический анализ конструкции обеспечивает улучшение технико-экономических показателей разрабатываемого технологического процесса. Основные задачи решаемые при анализе технологичности конструкции детали сводятся к возможному уменьшению трудоемкости и металлоемкости возможности обработки детали высокопроизводительными методами. Таким образом улучшение технологичности конструкции позволяет себестоимость ее изготовления без ущерба для служебного назначения.
Важнейшим показателем технологичности конструкции штока является его жесткость определяющая возможность концентрации операции обработки и применения высоких режимов резания. Жесткость конструкции штока зависит от геометрической формы (L>=10d) следовательно нашу деталь можно считать жесткой.
Обрабатываемые участки штока имеют равные или кратные длины а перепады диаметров штока невелики. Конструкция штока допускает обработку ступеней за проход и обеспечивает удобный подход и выход режущего инструмента.
Деталь имеет глухое отверстие M20-7H что достаточно не технологично.
Шток имеет простую конструкцию экономичный способ получения заготовки несложный технологический процесс изготовления детали. Требуется доступный недорогой материал. Деталь соответствует служебному назначению. Имеется полный комплект основных и вспомогательных баз. Упрощение конструкции детали или замена ее элементов ввиду её служебного назначения и тяжелых условий эксплуатации не представляется возможным. Итак в целом деталь достаточно технологична.
Количественная оценка:
Таблица 3 – Наименование поверхностей детали
Кол-во унифицированных поверхностей
Коэффициент использования материала[1]:
mз – масса заготовки.
Коэффициент унификации:
– число унифицированных элементов детали шт.;
– общее число конструктивных элементов детали шт.;
Коэффициент точности обработки детали:
Тср – средний квалитет точности;
ni- общее кол-во поверхностей.
Ктч== 1-= 0819 (4.6)
Коэффициент шероховатости поверхностей детали:
Шср – средняя шероховатость поверхностей.
Шi – общее кол-во шероховатостей поверхностей.
ni - общее кол-во поверхностей.
Шср = = = 2675 (4.7)
Проведя анализ технологичности конструкции детали можно сделать вывод что в целом деталь является технологичной. Из чертежа детали видно что она содержит достаточное количество точных поверхностей самые точные поверхности имеют 14-ый квалитет. Существующие точность и шероховатость рабочих поверхностей не могут быть изменены так как они являются необходимыми для выполнения деталью своего служебного назначения ГОСТ 2789 – 73.
Определение типа производства
Основой для выбора типа производства и организационной формы сборки является годовая производственная программа включающая номенклатуру и объем выпуска изделий по каждому наименованию ГОСТ 4.004 -83.
Кол-во изг. шт.=1700
Масса детали = 144кг.
Тип производства определяется в зависимости от массы детали и объема производства по таблице 4.[2]
Годовой объем производства деталей одного наименования шт.
тяжелых (крупных) массой свыше30 кг
Таблица 4 – Типы производства
При известных данных мы определили тип производства – среднесерийный. Этот тип предусматривает одновременное изготовление сериями широкой номенклатуры продукции выпуск которой повторяется в течение длительного времени. Серия – это изготовление ряда конструктивно одинаковых изделий запускаемых в производство партиями одновременно или последовательно в течение планового периода. Особенности: одновременное изготовление относительно большой номенклатуры повторяющейся продукции в значительных количествах специализация рабочих мест незначительных объем ручной работы небольшая длительность производственно цикла унификация деталей. Точность данной заготовки является обыкновенной квалификация рабочих может быть средней трудоемкость изготовления и себестоимость продукции средняя.
Годовая программа изготовления деталей в штуках определяется с учетом запасных частей и возможных потерь:
Для условий серийного производства количество деталей в партии для одновременного запуска:
От правильности выбора способа получения заготовки целиком зависит себестоимость получаемой детали. Выбор способа зависит от многих факторов: типа производства массы детали сложности формы требованиями чертежа. При этом необходимо учитывать новейшие тенденции в технологии машиностроения по сокращению расхода материала уменьшению объема мех. обработки ужесточению допусков так как для обработки деталей все чаще применяются станки с ЧПУ станки автоматы и автоматические линии.
Окончательный выбор варианта проводится сравнением себестоимости детали после различных методов получения заготовки. Себестоимость детали определяется суммированием себестоимости заготовки и стоимости последующей мех. обработки. Для определения метода получения заготовки воспользуемся таблицей 5.[1]
Таблица 5 – Методы и способы получения заготовок
Факторы выбора метода и способа получения заготовки
Форма и размеры заготовки
Точность формы размеров
и качество поверхностного слоя заготовок
Технологические свойства материала
Объем выпуска продукции
Сроки освоения производства
по выплавляемым моделям
Сортовой круглый горячекатаный
Анализ матрицы представленной в таблице 5 показал что наибольшее количество баллов набрал метод прокатки (5 балла) являющийся наиболее эффективным и экономичным при изготовлении детали.
Прокат ГОСТ 2590 – 88
Прокат может применяться в качестве заготовке для непосредственного изготовления деталей либо в качестве исходной заготовки при пластическом формообразовании. Прокатке подвергается до 90% всей выплавляемой стали и большую часть цветных металлов. При прокатке металл пластически деформируется вращающимися валками. Взаимное расположение валков и заготовки форма и число валков могут быть различными. Форму поперечного сечения прокатанной полосы называют профилем.
Совокупность форм и размеров профилей получаемых прокаткой называют сортаментом. Сортовой прокат делят на профили простой геометрической формы и фасонные. Процесс проката состоит из чередования в определенной последовательности основных и вспомогательных операций. Каждая операция определяется характером деформирования и применяемым инструментом. [3]
На начальном этапе происходит нагрев отливки подача и прокатывание на блюминге получая заготовки квадратного сечения называемые блюмами. Затем блюмы ступают на заготовочные станы для прокатки заготовок требуемых размеров или сразу на крупносортные станы для прокатки крупных профилей сортовой стали. На заготовочных и сортовых станах заготовка последовательно проходит через ряд калибров постепенно приближающих сечение исходной заготовки к сечению готового профиля. Разработку системы последовательных калибров необходимых для получения того или иного профиля называют калибровкой.
Калибровка является сложным и ответственным процессом. Неправильная калибровка может привести не только к снижению производительности но и к браку изделий. После проката производят резку на пилах и ножницах на части требуемой длины (мерные длины) или сматывания в бунты. [3]
На конечных этапах охлаждают в холодильниках правят на роликовых правильных машинах термически обрабатывают и удаляют поверхностные дефекты.
Из стандартного ряда диаметров по ГОСТ 2590-71 выбираем сталь горячекатаная круглая 30h15 точность обычная способ отрезки – ленточно – отрезной станок.
Рисунок 1 – Эскиз заготовки
Находим массу заготовки из проката:
Mз – масса заготовки;
Vз – объем заготовки;
Согласно точности и шероховатости обрабатываемой поверхности определяем промежуточные припуски. За основу расчета промежуточных припусков принимаем наибольший наружный диаметр 30h15. Назначаем последовательность обработки данной поверхности выбираем табличный припуск ГОСТ 25347 – 82 при квалитете 7.
Определяем расчетный диаметр заготовки при черновом и чистовом точениях и шлифовании:
Стандартный прокат имеет 33 мм. Размер заготовки с отклонениями
Определяем длину заготовки:
z1 z2 – припуск на подрезание торцов;
Lд – длина детали по чертежу;
Lз – длина заготовки.
Определяем объем заготовки:
Определяем массу заготовки:
Производим расчет на себестоимость заготовки:
M – затраты на материал заготовки.
Затраты на материал определяются по массе проката:
Q – масса заготовки кг;
S – цена 1 кг материала заготовки р.;
q – масса готовой детали кг;
Sотх – цена 1 т отходов р.;
kинф – инфляционный коэффициент.
Таблица 6 – Исходные данные для расчета стоимости заготовок
Прокат сортовой круглый ГОСТ 2590 - 88
Масса заготовки Q кг.
Стоимость 1 т материала заготовок р.
Стоимость 1 т стружек р.
Стоимость заготовки получаемой прокатом р.
Вывод: Исходя из проведенных технико-экономических расчетов себестоимости получения заготовки и требований по экономии материалов считаю целесообразным применить для получения заготовки метод прокат сортовой круглый горячекатаный.
Выбор технологических баз
Технологический процесс механической обработки штоков зависит от их конструкции объема выпуска технических требований норм точности и требуемого качества поверхностей обозначения баз производится по ГОСТУ 21495 – 76.[1]
В качестве черновой базы на 005 отрезной 015 и 020 токарных выбираем наружную цилиндрическую поверхности а вспомогательной черновой — торцы заготовки. Данные поверхности имеют достаточную протяженность для надежного закрепления.
Рисунок 2 – Базирование при черновом точении
На чистовой 015 операции обработки наружных цилиндрических поверхностей и на операции для базирования используются центровые отверстия. Данная схема базирования соответствует принципу совмещения баз позволяет обеспечить соосность поверхностей штока после разных стадий обработки.
Рисунок 3 – Базирование при чистовом точении
На операциях 010 030 фрезерования паза для базирования используются наружная цилиндрическая поверхность и торец.
Рисунок 4 – Базирование при шлифовании
Выбор вариантов технологических маршрутов обработки поверхностей детали
На основании типового технологического процесса определяем последовательность методов обработки для каждой поверхности детали по таблице 7.
Таблица 7 – Назначение методов и видов обработки поверхностей
Маршрут обработки поверхности
Точение черновое точение чистовое шлифование.
Точение черновое для торца 1 чистовое для торца 2 фрезерование
Точение черновое точение чистовое.
Точение черновое протачивание канавки.
Точение черновое нарезание резьбы.
Сверление нарезание резьбы.
Вывод: В основном точность получается однократным черновым точением так как в детали преобладает квалитет точности 14 шероховатость 6.3 кроме диаметра 30f9 где используется шлифование.
Разработка маршрутной технологии. Построение операций
На основе разработанных маршрутов обработки поверхностей соблюдая принцип поэтапности составляем матрицу технологического процесса которая представлена в Таблице 8. При этом была поставлена цель минимизировать себестоимость обработки и максимизировать производительность в условиях мелкосерийного производства. Используя матрицу технологического процесса и руководствуясь принципом концентрации производим разбиение технологического процесса на операции: [5]
Таблица 8 – Технологический процесс обработки детали
Наименование и содержание операции
Отрезать заготовку 33 и длиной L=3018мм.
Ленточно – отрезной станок 8А544. Ленточная пила. Металлическая линейка.
Фрезерно–центровальная.
Фрезеровать торцы(1 2 3 4) и выдерживать размер 294. Зацентровка с 2 – х торцов по форме В 315. ГОСТ 14034 – 74*
Фрезерно – центровальный станок МР 71М. Концевая фреза с цилиндрическим хвостиком d=315.
Штангенциркуль ГОСТ 166 – 88
Крепить деталь в 3 – х кулачковом патроне. Точить 33 начерно начисто до 303 до кулачков .Точить 22js6 на длину L= 47 (22+25). Подрезать торец 4 начерно начисто выдерживая размер L=47 (22+25). Точить канавку В=3 мм до 215 мм. Точить канавку В= 44 мм до 164 мм. Снять фаски снять фаски . Точить 185 на L=25. Нарезать резьбу М20-8g.
Токарный станок 16К20Ф3. Проходной резец 2102-0104 с пластиной из твердого сплава Т15К6. ГОСТ18868-73.
Прорезной резец для протачивания канавки 2130-078 ГОСТ 18874-73. Резец токарный фасочный из быстрорежущей стали 2136-0714 ГОСТ 18875-73. Глубиномер штангенциркуля ГОСТ 166-88
Установить деталь в 3 – х кулачковом патроне через мягкие прокладки. Точить поверхность 30f9.
К20Ф3. Проходной резец 2102-0104 с пластиной из твердого сплава Т15К6. ГОСТ18868-73. Калибр-скобы калибр-пробка.
Крепить в поводковом патроне через мягкие прокладки. Шлифовать поверхность 30f9.
Кругло-шлифовальный станок 3М151. Шлифовальный круг прямого профиля ПП600 по ГОСТ 2424-67
Установить в центрах крепить в делительной головкес поворотом делительной головки на Фрезеровать паз В=28 мм выдерживая размер L=15 мм.
Шпоночно-фрезерный станок 6ДФ 92. Фреза шпоночная 100 с коническим хвостиком по ГОСТ 9140-59.Поверочная линейка угольник образцы шероховатости.
Сверлить 19 под М20. Зенковать фаски 1х45°.Нарезать резьбу под М20 – 7Н.
Горизонтально- расточной станок 2М614. Спиральное сверло 19 по ГОСТ 19258 – 73. штангенциркуль ГОСТ 166 – 89 металлическая линейка для измерения центровых отверстий – калибр – пробка.
Зачистить заусенцы притупить острые кромки.
Выбор оборудования и средств технологического оснащения.
Для черновой токарной обработки целесообразно выбрать токарный патронно-центровый станок 16К20ФЗ. Он предназначен для токарной обработки в автоматическом режиме наружных и внутренних поверхностей деталей типа тел вращения со ступенчатым и криволинейным профилем. [2] Обработка происходит в один или несколько проходов в замкнутом автоматическом цикле. Привод главного движения включающий главный двигатель 11 кВт и шпиндельную бабку обеспечивает наибольший крутящий момент до 800 Нм. Высокоточный шпиндель с отверстием 55 мм (по заказу 64 мм) позволяющий обрабатывать детали из пруткового материала.
Таблица 9 – Техническая характеристика станка 16К20ФЗ
Диаметр обработки над станиной мм
Диаметр обработки над суппортом мм
Наибольшая длина обработки 6 – позиционная головка мм
Наибольшая длина обработки 8 – позиционная головка мм
Наибольшая длина обработки 12 – позиционная головка мм
Наибольшая длина обработки в центрах мм
Диаметр цилиндрического отверстия в шпинделе мм
Наибольший поперечный ход суппорта мм
Наибольший продольный ход суппорта мм
Максимальная рекомендуемая скорость продольной рабочей подачи мм
Максимальная рекомендуемая скорость поперечной рабочей подачи мм
Количество управляемых координат шт.
Количество одновременно управляемых координат шт.
Дискретность задания перемещения мм
Пределы частоты вращения шпинделя мин-1
Скорость быстрых перемещений суппорта – поперечного мммин
Скорость быстрых продольных перемещений мммин
Скорость быстрых поперечных перемещений мммин
Количество рабочих скоростей шпинделя
Количество позиций инструментальной головки
Мощность электродвигателя главного движения кВт
Класс точности по ГОСТ 8 - 82
Габаритные размеры станка ( мм
По техническим и экономическим характеристикам видно что станок является среднестатистическим. Эти характеристики позволяет выполнять операции обработки на данной детали.
Для фрезерно-центровальной операции выбираем фрезерно-центровальный станок модели: МР – 71М.
Таблица 10 – Техническая характеристика станка МР – 71М
Диаметр обрабатываемой заготовки мм
Длина обрабатываемой заготовки мм
Число скоростей шпинделя фрезы
Пределы чисел оборотов шпинделя фрезы в минуту.
Наибольший ход головки фрезы (стола) мм.
Пределы рабочих подач фрезы (бесступенчатое регулирование) мммин
Число скоростей сверлильного шпинделя
Пределы чисел оборотов сверлильного шпинделя в минуту
Ход сверлильной головки мм
Пределы рабочих подач сверлильной головки мммин.
Продолжительность холостых ходов мин.
Продольная подача фрезерной головки
Поперечная подача фрезерной головки мммин.
Мощность электродвигателя:
Главного привода кВт
Категория ремонтной сложности
Механическая обработка на многорезцовом полуавтомате позволяет обеспечивать точность в пределах 11 12 квалитетов. Но при правильном выборе режущего инструмента и тщательной наладке фрезерного станка точность может быть увеличена до 8 квалитета. На данном станке разрешено одновременное чистовое и черновое фрезерование если не увеличивается шероховатость и полностью обеспечивается заданная точность обрабатываемой поверхности. Класс точности полуавтомата Н. Параметр шероховатости обработанной поверхности Rа 63 имеет одни зажимные тиски.
Для шлифования выбираем кругло-шлифовальный станок с максимальным диаметром шлифования 200мм максимальной длинной шлифования 700мм мощностью двигателя 10кВт модели 3М151.[2] Станок модели 3М151 предназначен для наружного шлифования гладких и прерывистых цилиндрических и пологих конических поверхностей методами продольного и врезного шлифования.
Таблица 11 – Техническая характеристика станка 3М151
Наибольший размер обрабатываемой заготовки – диаметр мм
Наибольший размер обрабатываемой – длина мм
Рекомендуемый диаметр шлифования мм
Конус Морзе передней бабки
Наибольшие размеры шлифовальной бабки мин-1
Частота вращения шлифованной бабки мин-1
Частота вращения шпинделя изделия мин-1
Скорость перемещения стола ( бесступенчатого регулирования) ммин
Угол поворота шлифовальной бабки рад
Поперечная подача для врезного шлифования на один ход стола мм
Непрерывная подача для врезного шлифования мммин-1
Мощность электродвигателя кВт
Категория ремонтной сложости
Станок модели 3М151 является станком повышенной точности. При обработке на станке детали устанавливают в центрах или закрепляют в патроне. Для обработки деталей на указанном станке обеспечивается вращение шпинделя круга вращение обрабатываемой заготовки продольное перемещение стола непрерывная или периодическая подача на толщину срезаемого слоя. Детали длина которых меньше ширины круга шлифуют без продольного перемещения заготовки методом врезания
На нем можно осуществлять следующие виды шлифования:
продольное и врезное шлифование при ручном управлении
продольное и врезное шлифование до упора при полуавтоматическом цикле работы
Станок 3М151 может быть применен в условиях мелкосерийного среднесерийного и крупносерийного производства.
Для 030 фрезеровочной операции используем шпоночно-фрезерный станок 6Д92.Станок 6Д92 предназначен для обработки шпоночных пазов немерными шпоночными фрезами.
Таблица 12 – Техническая характеристика станка 6Д92
Ширина фрезеруемого паза мм
Наибольшая длина фрезеруемого паза мм
Наибольшая разбивка паза мм
Расстояние от оси шпинделя до стола А мм
Расстояние от торца шпинделя до середины стола Б мм
Размер рабочей поверхности стола мм
Частота вращения шпинделя мин-1
Количество рабочих продольных подач фрезерной головки
Продольная подача фрезерной головки мммин
Количество поперечных подач фрезерной головки
Поперечная подача фрезерной головки мммин
Мощность электродвигателя: главного привода привода подач кВт
Класс точности станка II. Шероховатость обработки боковых сторон шпоночного паза 5 дна паза 4.
Вращение шпинделя станка и перемещение фрезерной головки осуществляется от отдельных электродвигателей. Фрезерная головка имеет механическую подачу и быстрые перемещения и в продольном и поперечном направлениях. Установленная мощность привода главного движения высокие скорости вращения шпинделя и достаточная жесткость станка позволяют производить на нем обработку пазов фрезами оснащенными пластинками из твердого сплава.
Станок может работать в полуавтоматическом цикле. В полуавтоматическом цикле за одну установку на станке может быть обработано до 6 шпоночных пазов одной ширины расположенных на одной прямой вдоль вала.
Для операции расточения используем станок 2М614. Расточные станки предназначаются для обработки деталей в условиях единичного и серийного производств. Это - широкоуниверсальные станки на которых можно производить черновое и чистовое растачивание отверстий обтачивание наружных цилиндрических поверхностей и торцов отверстий сверление зенкерование и развертывание отверстий фрезерование плоскостей нарезание резьбы и другие операции. Большое разнообразие различных видов обработки производимых на расточных станках позволяет в ряде случаев проводить полную обработку детали без перестановки ее на другие станки что особенно важно для тяжелого машиностроения. [2]
Таблица 13 –Техническая характеристика станка 2М614
Диаметр выдвижного шпинделя А мм
Конус Морзе шпинделя
Наибольшее осевое перемещение шпинделя Б мм
Расстояние от оси шпинделя до стола В мм
Размеры рабочей поверхности стола мм
Размер Т- образного паза за стола Г мм
Подача шпинделя мммин
Частота вращения мин-1
Характерной особенностью расточных станков является наличие горизонтального (или вертикального) шпинделя ГОСТ 24644 – 81 который совершает движение осевой подачи. В шпинделе крепится режущий инструмент - борштанга с резцами сверло зенкер фреза метчик и др.
В последнее время широкое применение начинают получать расточные станки с программным управлением что сокращает время на переналадку станка повышает производительность труда и улучшает качество обработки.
На отрезной операции используем ленточно-отрезной станок 8А544. Станок 8А544 применяется для отрезки круглого и профильного материала из стали чугуна и цветных металлов.
Таблица 14 – Технические параметры станка 8А544
Наибольшие размеры сечения разрезаемой заготовки мм:
Максимальная длина устанавливаемой заготовки без дополнительных устройств мм
Размер сечения ленточной пилы мм
Длина ленточной пилы мм
Диапазон скоростей резания регулируемых бесступенчато мсек.
Диапазон рабочих подач ленточной пилы регулируемых бесступенчато ммсек.
Производительность при резке малоуглеродистой стали биметаллическим инструментом кв. смнаим.
общая потребляемая мощность кВт
Габаритные размеры мм
Станочные приспособления применяют для установки заготовок на металлорежущие станки. Различают три вида приспособлений - специальные специализированные и универсальные. Выбор конкретного вида выполняется в зависимости от типа производства стадии обработки сложности заготовки.
Для чернового и получистового точения целесообразно применить трехкулачковый самоцентрирующийся патрон нормальной точности ГОСТ 2675-80.
Для шлифовальной операции с целью повышения точности установки целесообразно применить жесткие центры по ГОСТ 18259 –72.
Для фрезерования паза производят установку в центрах с поворотом делительной головки.
При разработке технологического процесса механической обработки заготовки выбор режущего инструмента его вида конструкции и размеров в значительной мере предопределяется методами обработки свойствами обрабатываемого материала требуемой точностью обработки и качеством обрабатываемой поверхности заготовки.
Приспособления: станочные винтовые самоцентрирующиеся рычажные тески ГОСТ 21167 – 75. Режущий инструмент фреза дисковая 100 по ГОСТ 14952 – 75. Для получения центровочного отверстия М20 применяют спиральное сверло 19 по ГОСТ 19258 – 73.[7] На токарной операции производится использование трехкулачкового патрона по ГОСТУ 2675 – 80 режущий инструмент: для обработки цилиндрических поверхностей – проходные резцы – прямые или отогнутые по ГОСТ 18879 – 73.
Метод контроля должен способствовать повышению производительности труда контролёра и станочника создавать условия для улучшения качества выпускаемой продукции и снижения её себестоимости.
Средства измерения: штангенциркуль ГОСТ 166 – 89 металлическая линейка для измерения центровых отверстий – калибр – пробка калибр – скобы образцы шероховатости. [4]
Расчет припусков на обработку и операционных размеров
В данном разделе расчет припусков производится расчетно-аналитическим методом для размера 30f9 по переходам. [2] Результаты расчета будем заносить в таблицу 15.
Шток получаем из проката сортового круглого горячекатаного.
Масса заготовки 198кг.
Устанавливанием маршрут поверхности обработки 30f9:
Точность заготовки (15-й Квалитет);
Черновое обтачивание (12-й Квалитет);
Чистовое обтачивание (10-й Квалитет);
Шлифование ( 6-й Квалитет).
Таблица 15 – Расчет припусков и межпереходных размеров для 30f 9
Технологический маршрут обработки
Элементы припуска мкм
Размеры по переходам мм
Предельные значения припусков мм
Установим маршрут обработки поверхности детали:
) Расчетные минимальные и максимальные припуски под точение:
Суммарное отклонение:
к –удельная кривизна обрабатываемой поверхности.
На основании записанных в табл. 15 данных производим расчёт минимальных значений межоперационных припусков пользуясь основной формулой (11.1). [2]
) Минимальный припуск:
Графу “Расчётный размер” заполняем начиная с конечного (в данном случае чертёжного) размера последовательным вычитанием расчётного минимального припуска каждого технологического перехода.
) Расчетный размер db:
Определяем наибольшие предельные размеры по переходам по зависимости:
) Наибольший предельный размер:
Расчет фактических максимальных и минимальных припусков по переходам:
)Максимальный припуск:
Расчет общих припусков производим по уравнениям:
) Наибольшего припуска:
) Наименьшего припуска:
Проверку правильности расчетов производим по формуле:
Расчет режимов резания
При назначении и расчета режима резания учитывают тип и размеры инструмента материал его режущей части. материал и состояние заготовки тип оборудования и его состояние. [4]
Рассчитаем режим резания для операции 015 при точении наружных поверхностей штока с 33h15 на 30f9 на токарном станке модификации 16К20Ф3 выдерживая размер L=294.
Станок 16КФ20Ф3 nmax=2000мин-1 nmin = 125 мин-1
Выбираем режущий инструмент: принимаем токарный проходной отогнутый резец с пластиной из твердого сплава Т15К6 ГОСТ18868-73. Материал корпуса резца – сталь 50Сечение державки ВхН = 25х16 мм длина резца 140 мм угол в плане φ=450передний угол =100 угол наклона главного лезвия =00 радиус закругления вершины 10 мм
) При черновом точении глубина резания может быть равной припуску поэтому выбираем значение чуть меньше припуска:
t – глубина резания.
D – диаметр заготовки
) Подача S при черновом точении принимается максимально допустимой по мощности оборудования жесткости системы СПИД прочности режущей пластины и прочности державки. При черновом наружном точении резцами с пластинами из твердого сплава и быстрорежущей стали для стали 45 выбираем подачу S=05ммоб.
) Скорость резания ммин при наружном продольном и поперечном точении рассчитывается по эмпирической формуле:
Cv – постоянная для табличных условий.
T – стойкость режущего инструмента.
xv yv m – показатели степени
Кv– поправочный коэффициент на скорость резания является произведением коэффициентов учитывающих влияние материала заготовки состояния поверхности материала инструмента .
Кv– поправочный коэффициент на скорость резания является произведением коэффициентов учитывающих влияние материала заготовки Кmv состояния поверхности Knv материала инструмента Kuv.
Коэффициент характеризующий группу стали по обрабатываемости KГ=08 показатель степени nv=1.
) Частота вращения шпинделя:
Корректируем частоту вращения по паспорту станка и принимаем
) Фактическая скорость резания:
) Определим главную составляющую силы резания:
где по табл.22 выбираем:
Поправочный коэффициент на силу резания:
KM.P - коэффициент учитывающий влияние качества обрабатываемого материала.
Для режущей части из твердого сплава не учитывается (коэффициенты учитывающие влияние геометрических параметров режущей части инструмента).
) Расчет крутящего момента:
Проверяем достаточность мощности главного привода станка:
У станка 16К20Ф3 мощность следовательно обработка возможна.
где – расчетная длина рабочего хода инструмента мм;
длина обрабатываемой поверхности
врезание резца: (12.20)
перебег резца: мм принимаем =2мм;
- число рабочих ходов в переходе;
Все вычисленные в пункте данные записываем в таблицу 16.Чистовую обработку и операции для других поверхностей записываем в табличном виде.
Таблица 16 – Режимы резания
Наименование операции и технических переходов
Точить начерно с 33 на 303
Токарный проходной отогнутый резец Т15К6
Точить начисто с 303 на 30 под шлифование
Точить начерно с 30 на 22
Подрезать торец 4 начерно.
Подрезать торец 4 начисто.
Точить канавку В=44 мм до 164
Точить канавку В=3мм до 21.5
Точить 185 на L=25мм
Нарезать резьбу М20-7Н на L=25
Расчет норм времени операций техпроцесса
Техническое нормирование — установление норм времени на выполнение отдельной работы или нормы выработки в единицу времени. Определим и запишем все нормы времени для операции 015 в таблицу 17.[9]
Техническая норма времени определяется по формуле:
tшт. – норма штучного времени
tп-з – норма подготовительно –заключительного времени
n – кол-во деталей в партии.
Определим норму штучного времени по формуле:
tо – основное технологическое время
tв – вспомогательное время
tобс – время на обслуживание рабочего места
tотд – время на отдых и естественные надобности.
Основное технологическое время:
L – расчетная длина рабочего хода режущего инструмента мм
i – число рабочих ходов режущего инструмента
nст. –частота вращения шпинделя станка принятая по паспорту обмин-1
Sст. – подача по паспортных данным станка.
Вспомогательное время:
Определяем состав подготовительно – заключительного времени: наладка и установка приспособления – 9 мин; получение инструмента и приспособления до начала работы и сдача их после завершения – 7 мин; установка резца – 2 мин. [2]
Время затраченное на установку и снятие детали закрепления ее и открепления:
Время на приемы управления: включить и выключить станок кнопкой 001 мин; время на поворот резцовой головки на следующую позицию 004; подвести или отвести инструмент к детали 006.
Время затраченное на измерение детали равно 02 мин; при 40% контролируемых деталей получим:
Время на обслуживание рабочего стола и отдыха составляет 6% оперативного времени тогда:
Время на обслуживание в массовом и крупносерийном производстве слагается из времени на организационное обслуживание и времени на техническое обслуживание
Штучно – калькуляционное время:
Таблица 17 – Технические нормы времени
Номер и наименование операции
В процессе выполнения курсового проекта нами был разработан технологический процесс механической обработки штока.
Были проанализированы технические условия к изделию его служебное назначение эксплуатационные показатели показатели надежности технические требования. Выбрали метод достижения требуемой точности.
Был произведен анализ служебного назначения и технических условий на шток. Выбрали методы получения заготовки – прокат горячекатаный круглый произвели размерный анализ технологических процессов в машиностроении при изготовлении штока.
Рассчитали припуски и межпереходные размеры режим резания и техническое нормирование.
Было выбрано и рассчитано специальное станочное приспособление.
Список использованных источников
Основы технологии машиностроения: методические указания по выполнению курсового проекта для студентов всех форм обучения направления 151000.62 Технологические машины и оборудование Сост.: В.В.Иосифов Л.Ф. Мелехин Б.В. Крупнов О.Е. Сухина Е.Е. Сергеева Н.Л.Клокова; Кубан. гос. технол. ун-т. Каф. машиностроения и автомобильного транспорта. – Краснодар: Изд. КубГТУ 2014. – 47 с.
Горбацевич А.Ф. Шкред В.А. Курсовое проектирование по технологии машиностроения: [ Учебное пособие для машоностроит. спец. вузов]. – 4-е изд. перераб. и доп. – Минск.: Выш. школа 1983. – 256 с. ил
А. М. Дальский И. А. Арутюнова Т. М. Барсукова и др. Технология конструкционных материалов; Учебник для машиностроительных специальностей вузов Под общ. ред. А. М. Дальского. – 2-е изд. перераб. и доп. – Машиностроение 1985. – 448 с. ил.
Справочник технолога машиностроителя. В двух томах. Изд. 3 переработанное. Под ред. Заслуженного деятеля науки и техники РСФСР д-ра техн. наук проф. А. Н. Малова М. «Машиностроение» 1972. с 568.
Технология машиностроения (специальная часть): Учебник для машиностроительных специальностей вузов А. А. Гусев Е. Р. Ковальчук. И. М. Колесов и др. – М.: Машиностроение 1986. – 480 с.: ил.
Добрыднев И. С. Курсовое проектирование по предмету « Технология машиностроения» Учебн. пособие для техникумов по специальности «Обработка металлов резанием» - Машиностроение 1985.184 с. ил.
Краткий справочник металлиста Под общ. ред. П. Н. Орлова Е. А. Скороходова. – 3-е изд. перераб. и доп. – М.: Машиностроение 1986. – 960 с.: ил.
Краткий справочник технолога тяжёлого машиностроения И. В. Маракулин А. П. Бунец В. Г. Коринюк. – М.: Маниностроение 1987. – 464 с. ил.
Колесов. И. М. Основы технологии машиностроения: Учебн. для маностроит. спец. вузов. – 2-е изд. испр. – М.: Высш. шк. 1999. – 591 с.: ил.
Справочник нормировщика А. В. Ахумов Б. М. Генкин Н. Ю. Иванов и др.; Под общ. ред А. В. Ахумова. – Л.: Машиностроение Ленингр. отд-ние 1987 – 458 с. ил.
3 лист по отм.dwg

Наименование операции и технических переходов
Токарная Точить начерно
Точит начерно с ø30 на 22 50
Подрезать торец 4 20 28
Точить канавку В=3 до 21
Нарезать резьбу М20-7Н на 20 28
Токарный станок мод. 16К20Ф3
2 лист по отм.dwg

Отрезная Отрезать заготовку ø33 и длиной L=301
Фрезерно - центровальная q*; Фрезеровать торцы(1
) и выдерживать размер 294. Зацентровка с 2 - х торцов по форме В 3
Токарная Крепить деталь в 3 - х кулачковом патроне. Точить 33 начерно
до кулачков.Точить 22js6 на длину L= 47 (22+25. Подрезать торец 4 начерно
выдерживая размер L=47 (22+25). Точить канавку В=3 мм до 21
мм. Точить канавку В= 4
снять фаски .Точить 18
на L=25.Нарезать резьбу М20-8g.
Ленточно - отрезной станок 8А544. Ленточная пила. Металлическая линейка
штангенциркуль ГОСТ 166-88.
Фрезерно - центровальный станок МР71 -М Концевая фреза с цилиндрическим хвостиком d=3
Штангенциркуль ГОСТ 166 - 88.
Токарный станок 16К20Ф3. Проходной резец 2102-0104 с пластиной из твердого сплава Т15К6. ГОСТ18868-73. Прорезной резец для протачивания канавки 2130-078 ГОСТ 18874-73. Резец токарный фасочный из быстрорежущей стали 2136-0714 ГОСТ 18875-73. Глубиномер штангенциркуля ГОСТ 166-88
Токарная Установить деталь в 3 - х кулачковом патроне
через мягкие прокладки. Точить поверхность 30
Токарный станок 16К20Ф3 Проходной резец 2102-0104 с пластиной из твердого сплава Т15К6. ГОСТ18868-73. Калибр-скобы
Шлифовальная Крепить в поводковом патроне через мягкие прокладки. Шлифовать поверхность 30f9.
Кругло-шлифовальный станок 3М151.Шлифовальный круг прямого профиля ПП600 по ГОСТ 2424-67
Фрезерная. Установить в центрах
крепить в делительной головке
с поворотом делительной головки на Фрезеровать паз В=28 мм
выдерживая размер L=15 мм.
Шпоночно-фрезерный станок 6ДФ 92.Фреза шпоночная 100 с коническим хвостиком по ГОСТ 9140-59.Поверочная линейка
образцы шероховатости.
Расточная. Сверлить 19 под М20. Зенковать фаски 1х45° Нарезать резьбу под М20 - 7Н.
Горизонтально- расточной станок 2М614.Спиральное сверло 19 по ГОСТ 19258 - 73. Штангенциркуль ГОСТ 166 - 89
металлическая линейка для измерения центровых отверстий - калибр - пробка.
Слесарная. Зачистить заусенцы
притупить острые кромки.
Разработка маршрутной технологии. Построение операций
Рекомендуемые чертежи
- 04.11.2022