Широкоуниверсальный фрезерный станок мод.6720ВФ2


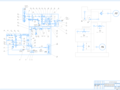
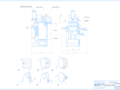
- Добавлен: 25.01.2023
- Размер: 3 MB
- Закачек: 3
Описание
Состав проекта
![]() |
![]() |
![]() ![]() ![]() |
![]() |
![]() ![]() ![]() |
![]() ![]() ![]() |
![]() ![]() ![]() |
![]() |
![]() ![]() ![]() |
![]() ![]() ![]() |
![]() ![]() ![]() |
![]() ![]() ![]() |
![]() ![]() ![]() |
![]() ![]() ![]() |
![]() ![]() ![]() |
![]() ![]() ![]() ![]() |
![]() ![]() ![]() ![]() |
Дополнительная информация
Содержание.docx
1Шпиндельного узла сверлильног станка по патенту 38695 (RU)4
2Шпиндельный узел по патенту 2167744 (RU)5
3Патент шпиндельного узла сверлильного станка по патенту 64965 (RU)6
4Шпиндельная бабка по патенту 2041772(RU)7
Обзор конструкций современных металлорежущих станков8
1Широкоуниверсальный фрезерный станок ВМ133-02 с ЧПУ8
2Широкоуниверсальный фрезерный станок 6ДМ80ШФ2 с ЧПУ10
3Широкоуниверсальный фрезерный станок ОММ67SC с ЧПУ12
Анализ конструкции станка и его технологических возможностей14
1Назначение станка14
2Особенности станка и его устройство14
3Методы образования поверхностей на станке15
4Метод получения производящих линий17
5Схема технологических операций выполняемых на станке19
Оценка технического уровня станка25
1Расчет режимов резания для типовых операций25
1.1 Фрезерование торцувой фрезой25
1.2 Фрезерование концевой фрезой28
2Технические характеристики станка31
Кинематическая структура станка33
1Цепь главного движения34
3Кинематическая настройка станка36
3.1 Цепь главного движения36
3.2 Вертикальтная подача суппорта37
3.3 Продольная подача суппорта37
3.4 Поперечная подача шпиндельной бабки37
4Общие сведения об электродвиг37
5График частот вращения шпинделя график подач.38
Анализ конструкции основных узлов и систем станка39
1Бабка шпиндельная.39
2Головка вертикальня42
4Приспособления оснастка применяемые на станке.45
4.1 Стол горизонтальный45
4.2 Стол угловой универсальный46
4.4 Стол круглый делительный47
4.5 Делительная головка48
4.6 Головка долбежная49
5Система управления станком49
Введение.docx
Специалисты в области технологии машиностроения металлорежущих станков и инструментов находятся на одном из самых ответственных участков всего научно-технического прогресса. Задача заключается в том чтобы в результате коренного совершенствования технологии обработки создания новых металлорежущих станков с микропроцессорным управлением станочных модулей для гибких производственных систем обеспечить техническое и организационное перевооружение всех отраслей машиностроения и на этой основе обеспечить существенное повышение производительности труда. Для успешного творческого труда инженеры-станкостроители должны быть фундаментально подготовлены в области математики физики вычислительной техники иметь фундаментальные знания и навыки по общим инженерным дисциплинам и наконец хорошо знать свою будущую специальность. Необходимо ясно представлять общие важнейшие свойства и качества определяющие технический уровень металлорежущих станков с тем чтобы создавать лучшие образцы и новые модели станков.
В настоящее время и в обозримом будущем потребуется создание новых моделей станков станочных модулей гибких производственных систем поэтому будущие специалисты-станкостроители должны владеть основами конструирования станков и их важнейших узлов. Для успешного применения вычислительной техники при конструировании необходимо хорошо знать содержание процесса проектирования всех видов станочного оборудования владеть методами его моделирования и оптимизации.
Современный станок органически соединил технологическую машину для размерной обработки с управляющей вычислительной машиной на основе микропроцессора. Поэтому специалист-станкостроитель должен хорошо понимать принципы числового программного управления станками владеть навыками подготовки и контроля управляющих программ. Он должен знать устройство микропроцессорных средств управления основные их характеристики и возможности применительно к станочному оборудованию.
1Патентно информационные мсследования.docx
1Шпиндельного узла сверлильного станка по патенту 38695(RU)
Шпиндельный узел в корпусе которого размещена пиноль имеющая верхнюю и нижнюю крышки образующие замкнутую полость заполненную смазочной жидкостью внутри которой размещен шпиндель и его нижняя опора выполненная в виде упорного подшипника а его верхняя опора установлена над пинолью на шпинделе выполнены верхняя и нижняя опорные шейки имеющие нарезку на образующих поверхностях и расположенные с возможностью взаимодействия с поддерживающими втулками со сквозными каналами установленными в пиноли при этом нижний край шпинделя связан с держателем инструмента его верхний край выполнен с возможностью взаимодействия с приводом станка отличающийся тем что на шпинделе в упор к нижней опорной шейки выполнен фланец с двумя гладкими
Рисунок 1.-Шпиндельный узел.
торцевыми поверхностями который помещен с возможностью осевого перемещения в цилиндрическую полость образованную стаканом на донце
которого выполнено центральное отверстие и эксцентричная канавка с несколькими маслоперегонными отверстиями.
Также характерной особенностью данного шпиндельного узла является то что стакан выполнен из антифрикционного материала (например из бронзы) а цилиндрическая полость образованная стаканом должна превышать толщину фланца на 15-20 мм.
2Шпиндельный узел по патенту 2167744(RU)
В данном патенте представлен способ уменьшения влияния температурных деформаций на шпиндельный узел.
Рисунок 2.-Шпиндельный узел.
Шпиндельный узел содержит корпус с установленным в нем с возможностью вращения на подшипниковых опорах шпинделем имеющим равномерно расположенные по окружности наклонные и параллельные оси шпинделя каналы соединенные с цилиндрической полостью в стакане закрепленном на заднем торце шпинделя. Для повышения производительности путем увеличения быстроходности шпинделя за счет устранения застойных зон процесса охлаждения при циркуляции теплоносителя в указанных каналах шпинделя выполнены продольные винтообразные канавки а на поверхности цилиндрической полости стакана - поперечные винтообразные канавки. При этом винтообразные канавки в наклонных и параллельных оси шпинделя каналах совмещены.
3Патент шпиндельного узла сверлильного станка по патенту 64965(RU)
Особенностью данного устройства является то что в корпусе шпиндельного узла дополнительно размещена пиноль заполненная смазочной жидкостью.
Рисунок 3.-Шпиндельный узел.
4Шпиндельная бабка по патенту 2041772(RU)
Особенностью конструкции является то что электродвигатель расположен соосно с гидроцилиндром отжима инструмента и соединен со шпинделем напрямую через промежуточный вал установленный с возможностью перемещения относительно верхнего конца вала являющегося одновременно толкателем механизма отжима инструмента при этом нижний конец вала-толкателя соединен с верхним концом шпинделя.
Рисунок 4.-Шпиндельная бабка.
6 анализ конструкции основных узлов станка.docx
Рисунок 32.- Бабка шпиндельная
Бабка шпиндельная перемещается по горизонтальным направляющим колоны и предназначена для осуществления главного движения станка и навесных принадлежностей вращения режущего и вспомогательного инструмента.
Шпиндельной бабке сообщается поперечная подача. Шпиндель получает вращение от двигателя главного движения установленного на задней стенке корпуса шпиндельной бабки через привод и коробку скоростей смонтированные там же муфта 19 и шестерни 6 и 20. Шпиндель 1 смонтирован на радиальных спорах 3 и 7 воспринимающих радиальные нагрузки осевые нагрузки – упорными подшипниками 4.
Зажим инструмента осуществляется расположенным в шпинделе 1 шомполом 5 который перемещается вдоль оси шпинделя 1 и захватывает с помощью шариков 11 хвостовик 12 инструмента. Осевое перемещение шомпола 5 осуществляется вращением гайки 10 в которую входит резьбовой конец шомпола 5.
Для преобразования вращательного движения гайки 10 в поступательное движение шомпола 5 служит шпонка 13 установленная в шпинделе 1.
Гайка 10 получает вращение от маховика 9. В ободе маховика 9 размещены два рычага 14 имеющие возможность под действием центробежной силы поворачивается на осях 15 и входит в зацепление с зубом втулки 8 которая закреплена на гайке 10 с помощью шпоночного соединения. Вращение маховика 9 производится от электродвигателя 23 при помощи конических зубчатых колес 2829.
Отжим инструмента осуществляется при помощи включения вращения вала электродвигателя 23 в противоположном направлении.
Изменение частоты вращения шпинделя 1 в пределах диапазона производится механизмом переключения следующих образом: рукоятку включения частот вращения 18 нужно поднять при этом диски 30 выходят своими отверстиями из зацепления с пальцами 39; поворотом диска 34 набора частот вращения поворачиваются связанные с ним диски 30. Этим самым произведена подготовка для включения набранной частоты вращения.
Включение частоты вращения происходит в результате поворота рукоятки 18 в исходное положение. При этом диск 30 сводится поворачивая пальцы 39 и связанные с ним рычаги 45. Поворотом рычагов осуществляется перемещение блоков зубчатых колес 46.
При переключении возможны случаи несовпадение торцов зубьев зацепляемых колес в результате чего диск 30 не сводится. В этом случае следует нажать кнопку 27 на вспомогательном пульте 22 в результате чего вал двигателя получает качательное движение и шестерня вводится в зацепление.
Переключение диапазонов частот вращения шпинделя производится рукояткой 17 привода при этом происходит перемещение блока зубчатых колес 42 и 43.
Механическая или ручная подача шпиндельной бабки осуществляется винтом 10 расположенным в станке и гайкой 23. Перемещение шпиндельной бабки контролируется по линейке и лимбу расположенным на станине. Особо точные перемещения контролируются с помощью индикаторного устройства 55. На корпусе 2 шпиндельной бабки предусмотрено отверстие для установки арматуры крепящей трубку подводящую охлаждающую жидкость в зону обработки.
2 Головка вертикальная.
Рисунок 33.- Головка вертикальная
Головка вертикальная крепится к шпиндельной бабке 18 четырьмя винтами 14 и центрируется относительно горизонтального шпинделя двумя штифтами 11.
Вертикальный шпиндель 1 смонтирован в корпусе 2
Шпиндель 1 получает вращение от вала 21 шпиндельной бабки через конические шестерни 9 13.
Благодаря наличию т-образного вала обеспечивается поворот головки в вертикальной плоскости на 90 в обе стороны. Фиксация головки при вертикальном положении шпинделя осуществляется штифтом 12. Штифты 12 обеспечивают перпендикулярность оси вертикального шпинделя к плоскости горизонтального стола в плоскости предельного перемещения его с высокой степенью точности достаточной для выполнения большинства операций производимых с помощью вертикальной головки.
При выполнении особо точных операций рекомендуется производить дополнительную выверку положения оси вращения вертикального шпинделя относительно горизонтального стола. При этом следует добиваться одинаковых показателей индикатора укрепленного на вертикальном шпинделе в диаметрально противоположных точках его траектории. Расстояние от оси вращения шпинделя до измерительного штифта индикатора должно выбираться исходя из конкретных условий обработки детали. Инструмент установленный в конусе шпинделя 1 вытягивается шомполом 10 который и перемещается вдоль оси шпинделя и захватывает с помощью шариков 15 хвостовик 16 инструмента.
Осевое перемещение шомпола 10 осуществляется вращением гайки 8 в которую входит резьбовой конец шомпола 10.
Для преобразования вращательного движения гайки 8 в поступательное движение шомпола 10 служит стопор 17 установленный в шпинделе 1.
Гайка 8 получает вращение от маховика 3. В ободе маховика 3 размещены два рычага 30 имеющие возможность под действием центробежной силы поворачивается на осях 19 и входит в зацепление с зубом втулки 7 которая закреплена на гайке 8 с помощью шпоночного соединения. Маховик 3 получает вращение от электродвигателя 4 через упругую муфту 5.
Отжим инструмента осуществляется при включении вращения вала электродвигателя 4 в противоположном направлении.
Рисунок 34.- Суппорт
Суппорт перемещается на вертикальных направляющих колоны станка и служит для продольного и вертикального перемещения основного вертикального стола механически или вручную. Механическая подача стола осуществляется ходовыми винтами 1 и 2 от приводного вала 3 получаемого вращение от привода подач.
Управление механическим перемещением стола и бабки шпиндельной осуществляется с пульта.
Продольные и вертикальные механические перемещения отключаются проходными и концевыми упорами. Проходные упоры закрепляются в Т-образных пазах и могут быть установлены на требуемый размер хода. Величины продольных и вертикальных перемещений контролируются по линейкам и лимбам. Для особо точных перемещений служат индикаторные устройства.
Включение вертикального перемещения суппорта и продольного перемещения основного вертикального стола осуществляется магнитами. Вертикальное перемещение осуществляется включением магнита 4 который поворачиваясь включает муфту 8 с полумуфтой 9.
Включение горизонтального перемещения осуществляется включением магнита 10 который поворачивает коромысло 5 валик6 рычаг 7 в обратном направлении и включает муфту 8 с полумуфтой 15. Возврат и фиксирование муфты в нейтральное положение происходит при помощи плоской пружины 11 и фиксатора 12.
4 Приспособления оснастка и вспомогательный инструмент применяемые на станке.
4.1 Стол горизонтальный
Рисунок 25.- Стол горизонтальный
Стол горизонтальный I устанавливается на вертикальной плоскости основного вертикального стола» выставляется по его контрольной кромке А и служит для обычных фрезерных работ. С целью увеличения расстояния от торца вертикальной головки до плоскости горизонтального стола и может устанавливаться по нижней кромке верхнего паза основного вертикального стола. Слив охлаждающей жидкости осуществляется через сливное отверстие 3.
4.2 Стол угловой универсальный
Рисунок 35.- Стол угловой
Стол угловой универсальные предназначен для установки обрабатываемых деталей под углом к любой из трех координатных плоскостей и крепится на плоскости основного вертикального стола 6.
Тиски могут устанавливаться как на столе горизонтальном так и на столе угловом универсальном и служат для закрепления мелких обрабатываемых деталей.
Верхняя часть тисков может поворачиваться на 360 и закрепляться в нужном положении.
4.4 Стол круглый делительный
Рисунок 36.- Стол круглый делительный
Стол круглый может устанавливаться как на столе горизонтальном так и на столе угловом универсальном и служить для выполнения различных делений при фрезеровании или растачивании деталей.
4.5 Делительная головка
Рисунок 37.- Делительная головка
Головка делительная предназначена для установки на ней деталей процесс обработки которых требует деление или поворот на определенный угол. Делительная головка имеет шкалу в градусах диск непосредственного деления 2 и делительный диск 7.
На делительной головке возможно:
Деление по шкале (в градусах)
Непосредственное деление при помощи диска 2 и фиксатора 5
Простое деление с применением делительного диска 7
Различные разметочные работы.
4.6 Головка долбежная
Рисунок 38.- Головка долбежная
Головка долбежная устанавливается на корпусе бабки шпиндельной и служит для выполнения долбежных работ в условиях индивидуального производства. Установка долбежной головки происходит на плите 1 головки вертикальной с помощью винтов 11.
5Система управления.
Широкоуниверсальный фрезерный станок данной модели 6720ВФ2 оснащен оперативной системой ЧПУ ОСУ-4.1 предназначенной для автоматизации инструментально фрезерных станков. Устройство применяется для управления инструментально-фрезерными станками с общим приводом подач оснащенных фотоимпульсными датчиками перемещений отвечающими за позиционирование по трем координатам: X и Z- позиционирование стола и суппорта и Z – поперечное перемещение шпиндельной бабки.
Далее приведен принцип позиционирования с использованием отсчетной системы и датчиков обратной связи.
При грубом позиционировании отсчет ведется до 001 мм погрешность не превышает ± 005мм. Датчиком ДС стола (салазок) является блок объединяющий четыре сельсина и связанный с ходовым винтом.
На длине хода стола чтобы вести отсчет до 001 мм необходимо различать 100000 положений. Каждому положению стола соответствует определенное положение сельсинов. Каждый сельсин в блоке соответствует определенному разряду двоичного числа причем сельсин С1 ближайший к ходовому винту отсчитывает десятые и сотые доли миллиметра а сельсин С4 сотни миллиметров.
При обработке координаты сигнал от каждого сельсина в виде изменяющейся фазы напряжения преобразуется в цифровую форму и сравнивается с числом заданным в соответствующем разряде на пульте. При совпадении чисел одновременно во всех размерах стол останавливается.
Фотоэлектрический датчик содержит фоторезистор который под действием света вырабатывает электрический сигнал. Луч от осветителя раздваивается: в одной из линз оптического устройства он попадает на фотодатчик. Когда мимо фотодатчика проходит изображение штриха меры освещенность фоторезистора меняется что сопровождается резким изменением его сигнала.
Система управления улавливает этот момент и останавливает движение стола.
Устройство обеспечивает оперативный ввод программы у станка с помощью пульта программирования и не требует специальных средств подготовки программы.
5 кинематическая структура станка.docx
Рисунок 28.- Структурно кинематическая схема станка
Рисунок 29.- Кинематическая схема станка
1 Цепь главного движения
От электродвигателя 1 привода главного движения вращение передается валу I привода. От вала 1 через зубчатые пары 25 или 34 вращение передается валу IV коробки скоростей.
Далее через коробку скоростей и шестерни 2526 вращение получает горизонтальный шпиндель IX.
Вертикальный шпиндель XIII получает вращение от вала VIII через шестерни 2934.
Изменение направления вращения шпинделей IX и XIII производится реверсированием электродвигателя I привода главного движения.
Насос для смазки 9 получает вращение от электродвигателя 8 через шестерни 67.
Цепь подач осуществляет движение трем рабочим органам :суппорт – по вертикали салазкам – в продольном к шпиндельной бабке – в поперечном направлениях. Все перемещения осуществляются как вручную так и механически.
От электродвигателя 35 цепи подач движение передается через ременную передачу валу XVII.
Ходовой винт 47 шпиндельной бабки связан с валом XVII шестернями 41424445. Ходовой вал XXII суппорта связан с валом XVII шестернями 4142435253.
От ходового вала XVII суппорта вращение передается через шестерни 5657 продольному 58 или через шестерни 5463 вертикальному 63 ходовым винтам.
Изменение величин продольных поперечных и вертикальных подач осуществляется при помощи тиристорного привода 35 обеспечивающего осуществление ускоренных перемещений равных 20ммс (1200 мммин) в рабочих подач в пределах 0167-1667 ммс (10-1000 мммин) Изменение направления этих перемещений осуществляется реверсированием электродвигателя 35.
Ручное продольное перемещение суппорта производится вращением маховика с включением муфты 60 установленной на валу XXIV через винт 58 и гайку 59. Ручное вертикальное перемещение суппорта производится вращением маховика с включенной муфты 66 установлено на валу XXVI через винт 68 и гайку 67.
Ручное поперечное перемещение шпиндельной бабки производится вращением маховика с включением муфты 51 установленной на валу XXчерез конические шестерни 49 и 50винт 47 и гайку 46.
3Кинематическая настройка станка.
3.1 Цепь главного движения
Вращение вертикального шпинделя осуществляется от электродвигателя M1 через коробку скоростей.
Конечные звенья: электродвигатель – шпиндель;
Расчетные перемещения: nдв обмин nшп обмин;
УКБ: nдв×iкор×iconst=nшп
Вращение горизонтального шпинделя осуществляется от электродвигателя M1 через коробку скоростей.
3.2Вертикальная подача суппорта
Подача суппорта осуществляется от электродвигателя постоянного тока М4 через ременную зубчатую и передачу винт гайка.
Конечные звенья: двигатель – суппорт;
Расчетные перемещения: nдв обмин Sвп мм;
УКБ: nдв×iрем×iconst×mz =Sвп
3.3Продольная подача суппорта
Расчетные перемещения: nдв обмин Sпр мм;
УКБ: nдв×iрем×iconst×mz =Sпр
3.4Поперечная подача шпиндельной бабки
Подача шпиндельной бабки осуществляется от электродвигателя постоянного тока М4 через ременную зубчатую и передачу винт гайка.
Конечные звенья: двигатель – шпиндельная бабка;
Расчетные перемещения: nдв обмин Sпп мм;
УКБ: nдв×iрем×iconst×mz =Sпп
4Общие сведения об электродвигателях.
На станке установлены три трехфазных короткозамкнутых электродвигателя и три электродвигателя постоянного тока
М1 – электродвигатель вращения шпинделя станков типа АИР80В4УЗ 22 кВт 380220 в; синхронная скорость 1500 мин-1 ;
М2 – электронасос охлаждения тип Х14-22М; 0.12 кВт производительность 22лмин. 380220В:
М3 – электродвигатель постоянного тока с встроенным тахогенератором привода перемещения стола бабки суппорта типа 2НБ-9СМГ 055 кВт 3000 мин-1 ; 110 В питающийся от привода ЭЦИР-I;
М4 – электродвигатель системы смазки ;АА50В4; 009 кВт 1500 мин-1 380220 В;
М5М6 – электродвигатели зажима инструмента горизонтального и вертикального шпинделей типа СД-26I; 0024 кВт 3600 мин-1.
5График частот вращения шпинделя график подач.
Рисунок 30.- График частот вращения шпинделя
Рисунок 31.- График подач
3 Анализ Конструкции станка и его технологические возможности.docx
Предназначен для горизонтального и вертикального фрезерования цилиндрическими дисковыми фасонными торцевыми концевыми и другими фрезами. Наличие целого ряда приспособлений делает станок удобным для работы в инструментальных и экспериментальных цехах крупносерийного и массового производства а также в основных цехах мелкосерийного и единичного производства.
2 Особенности станка и его устройство
Рисунок 8.- Компоновка станка 6720ВФ2
Фрезерные инструментальные широкоуниверсальные станки состоят из следующих основных частей: основание станина стол суппорт и т.д.
На чугунном основании станины закреплена колона на которой монтируются все основные части станка. На задней стенки колоны устанавливается привод подачи. На верхней части колонны закрепляется съемник на котором устанавливается головка вертикальная.
По горизонтальным направляющим колоны перемещается бабка шпиндельная к которой крепится вертикальная головка и хобот.
По вертикальным направляющим колонны перемещается суппорт а по его горизонтальным направляющим – основной вертикальный стол.
В главном приводе имеется восемнадцати ступенчатая коробка скоростей причем на верхних двенадцати ступенях в передаче участвуют лишь две пары зубчатых колес а на шести нижних ступенях три пары.
Привод подачи - от отдельного электродвигателя постоянного тока с бесступенчатым регулированием.
Пульт управления станком установлен справа на кронштейне крепящемся к колоне. Бак охлаждения с электронасосам размещается в основании станка. Там же размещен насос смазки с приводом.
Шкаф управления расположен справа от станка и соединен со станком при помощи соединительных шлангов.
К вертикальной базовой плоскости основного вертикального стола суппорта крепится горизонтальный стол или универсальный стол служащий для установки на них обрабатываемых деталей.
Для делительных работ станок оснащен круглым столом и делительной головкой которые могут устанавливается как на горизонтальный стол так и на вертикальной плоскости основного вертикального стола. Для долбежных работ предусмотрена долбежная головка которая устанавливается на бабке шпиндельной.
Головка подрезная рискообразователь и борштанга устанавливаются и закрепляются в конусах шпинделей через переходные втулки. Резцедержатель патрон цанговый устанавливается и закрепляется непосредственно в конусах шпинделя.
3 Методы образования поверхностей на станке.
Тело деталей машин ограничено геометрическими поверхностями возникающими в процессе обработки. Это в основном плоскость круговые и некруговые цилиндры круговые и некруговые конусы линейчатые и шаровые поверхности имеющие определенную протяженность и взаимное расположение. Реальные поверхности полученные в результате обработки на станках отличаются от идеальных геометрических поверхностей. След кромки инструмента трение между задней его поверхностью и обработанной поверхностью пластические явления при отрыве отдельных слоев металла упругие деформации поверхностных слоев вибрации и другие явления
возникающие в процессе резания создают на обработанной поверхности микронеровность и волнистость. Их допустимая величина зависит от служебного назначения поверхностей деталей машин и достигается различными методами обработки. Несмотря на это отличие реальные геометрические поверхности могут быть получены теми же методами что и идеальные.
Поверхности обрабатываемых деталей можно рассматривать как непрерывное множество последовательных геометрических положений (следов) движущейся производящей линии называемой образующей по другой производящей линии называемой направляющей. Например для получения плоскости необходимо образующую прямую линию 1 перемещать по направляющей прямой линии 2 (рис. 9 а). Цилиндрическая поверхность может быть получена при перемещении образующей прямой линии 1 по направляющей линии-окружности (рис. 9 б) или образующей окружности 1 вдоль направляющей прямой линии 2 (рис. 9 в). Рабочую поверхность зуба цилиндрического колеса можно получить если образующую линию — эвольвенту 1 передвигать вдоль направляющей 2 (рис. 9 г) или наоборот образующую прямую 1 — по направляющей — эвольвенте 2 (рис. 9 д).
Рисунок 9.- Схемы образования поверхностей у деталей
Рассмотренные поверхности называют обратимыми так как их форма не изменяется если поменять местами образующие линии с направляющими. В противоположность им этого нельзя сделать при образовании необратимых поверхностей. Например если левый конец образующей прямой линии 1 перемещать по направляющей окружности 2 то получим круговую коническую поверхность (рис. 9 e). Но если окружность 2 сделать образующей и переместить вдоль направляющей прямой то конус не получится. В этом случае необходимо чтобы по мере перемещения окружности к точке О ее диаметр изменялся достигая в вершине нуля. Такие поверхности называют также поверхностями с изменяющимися производящими линиями в противоположность поверхностям у которых производящие линии постоянны (рис. 9 а—д).
Большинство поверхностей деталей машин может быть образовано при использовании в качестве производящих линий прямой линии окружности эвольвенты винтовой и ряда других линий. В реальных условиях обработки производящие линии не существуют. Они воспроизводятся комбинацией согласованных между собой вращательных и прямолинейных перемещений инструмента и заготовки. Движения необходимые для образования производящих линий называют рабочими формообразующими движениями. Они могут быть простыми состоящими из одного движения и сложными состоящими из нескольких простых движений. Существует четыре метода образования производящих линий: копирования обката следа и касания.
4 Методы получения производящих линий
Метод копирования основан на том что режущая кромка инструмента по форме совпадает с производящей линией. Например при получении цилиндрической поверхности (рис. 10 а) образующая линия 1 воспроизводится копированием прямолинейной кромки инструмента а направляющая линия 2 — вращением заготовки.
Здесь необходимо одно формообразующее движение — вращение заготовки. Для снятия припуска и получения детали заданного размера необходимо поперечное перемещение резца но это движение (установочное) не является формообразующим. На рис. 10 б показан пример обработки зубьев цилиндрического колеса. Контур режущей кромки фрезы совпадает с профилем впадин и воспроизводит образующую линию.
Направляющая линия получается прямолинейным движением заготовки вдоль своей оси. Здесь необходимы два формообразующих движения: вращение фрезы и прямолинейное перемещение заготовки. Кроме этого для обработки последующих впадин заготовка должна периодически поворачиваться на угол соответствующий шагу зацепления. Такое движение называют делительным.
Метод обката (огибания) основан на том что образующая линия возникает в форме огибающей ряда положений режущей кромки инструмента в результате его движений относительно заготовки. Форма режущей кромки отличается от формы образующей линии и при различных положениях инструмента является касательной к ней. На рис. 10 в показаны схемы обработки зубьев цилиндрического колеса по методу обката. Режущая кромка инструмента имеет форму зуба зубчатой рейки. Если сообщить вращение заготовке и согласованное с ним прямолинейное перемещение рейки вдоль ее оси как в реечной передаче то в своем движении относительно заготовки режущий контур инструмента займет множество положений. Их огибающей явится образующая линия в форме впадины колеса. Направляющая линия по предыдущему образуется прямолинейным перемещением инструмента или заготовки вдоль оси колеса. Для рассматриваемого случая требуется три формообразующих движения: вращение заготовки перемещение инструмента вдоль своей оси перемещение инструмента или заготовки вдоль оси зубчатого колеса.
Рисунок 10.- Методы получения производящих линий
Метод следа состоит в том что образующая линия получается как след движения точки—вершины режущего инструмента. Например при точении образующая 1 (рис. 10 г) возникает как след точки А — вершины резца а при сверлении (рис. 10 д) — сверла. Инструмент и заготовка перемещаются относительно друг друга таким образом что вершина А режущего инструмента все время касается образующей линии 1. Направляющая линия получается вращением заготовки (рис. 10 г) сверла или заготовки (рис. 10 д). В обоих случаях требуется два формообразующих движения.
Метод касания основан на том что образующая линия 1 является касательной к ряду геометрических вспомогательных линий 2 образованных реальной точкой движущейся режущей кромки инструмента (рис. 10 е). Итак образование различных поверхностей сводится к установлению таких формообразующих движений заготовки и инструмента которые воспроизводят образующие и направляющие линии.
5 Схемы технологических операций выполняемые на станке.
Рисунок 11.- Обработка вертикальной плоскости торцевой фрезой
Рисунок 12.- Обработка горизонтальной плоскости цилиндрической фрезой
Рисунок 13.- Обработка горизонтальной плоскости торцевой фрезой
Рисунок 14.- Обработка вертикальной плоскости концевой фрезой
Рисунок 15.- Обработка наклонной плоскости одноугловой фрезой
Рисунок 16.- Обработка наклонной плоскости с поворотом шпиндельной головки
Рисунок 17.- Обработка уступа дисковой трехсторонней фрезой
Рисунок 18.- Обработка уступа концевой фрезой
Рисунок 19.- Обработка прямоугольного паза дисковой трехсторонней фрезой
Рисунок 20.- Обработка прямоугольного паза концевой фрезой
Рисунок 21.- Обработка фасонной поверхности фасонной фрезой.
Рисунок 21.- Обработка паза типа «ласточкин хвост» одноугловой фрезой
Рисунок 22.- Обработка нескольких поверхностей набором фрез.
Рисунок 22.- Обработка шпоночного паза дисковой фрезой
Рисунок 23.- Обработка шпоночного паза шпоночной фрезой
Рисунок 24.- Обработка Т-образного паза фрезой для обработки Т-образных пазов.
Литература.docx
Станочное оборудование автоматизированного производства. В 2-х томах. Под общей ред. В.В. Бушуева – М.: Станки 1994. – 656 с.
Металлорежущие станки. Учеб. пособие для техникумов Н. С. Чернов – М.: Машиностроение 1988. – 416 с. ил.
Чернов Н. Н. Металлорежущие станки: Чернов Н.Н. . - 4-е изд. перераб. и доп. – М.: Машиностроение 1988. - 414с.
Расчет и конструирование узлов и элементов станков Проников А.С. Борисов Е.И. Бушуев В.В. Дмитриев Б.М. Каминская В.В. Михайлов О.П. Нахапетян Е.Г. Проникова Т.А. Пуш А.В. Рожков Е.И. Селезнева В.В. Под общей ред. Проников А.С. . – М.: Издательство МГТУ Москва: Машиностроение 1995. – 369 с.
Металлорежущие станки. Рецензенты канд. техн. Наук А. А. Федотенко и инж. А. И. Ершов. Изд. – Москва 1957 - 659 с.
Чернов Н. Н. Металлорежущие станки: Чернов Н.Н. . - 3-е изд. перераб. и доп. – М.: Машиностроение 1978. - 384с.
Лабораторный практикум по металлорежущим станкам. Под редакцией А. И. Кочергина. Изд. – Минск «Вышэйшая школа» 1986. – 135с.
Станочные приспособления. Болотин Х. Л. Костромин Ф. П. изд. 5-е переработ. и доп. М. «Машиностроение» 1973 344 с.
Металлорежущие станки: Учебник для машиностроительных М54 втузовПод ред. В. Э. Пуша. – М.: Машиностроение 1985. – 256 с.
Современные отечественные и зарубежные координатно-расточные станки Кашепова М.Я и др. – М.: «Москва» 1973 142 с.
2обзор конструкции современных металорежущих станков.docx
1 Широкоуниверсальный фрезерный станок ВМ133-02 с ЧПУ
Рисунок 5.- Широкоуниверсальный фрезерный станок ВМ133-02
Предназначен для разнообразной фрезерной обработки в условиях серийного и мелкосерийного производства деталей и заготовок из черных и цветных металлов и их сплавов а также обработки сверлением и растачиванием.
Станок ВМ133-02 является базовой моделью для широкой гаммы станков отличающихся степенью автоматизации и предназначенных для различных типов производств. Оснащен приводом и УЧПУ фирмы Siemens модели Sinumeric 810D.
Станок оснащен направляющими с полимерным покрытием что обеспечивает плавность перемещения и износостойкость на период эксплуатации.
Перемещение по координатам осуществляется с помощью отдельных приводов с высокомоментными двигателями передающими вращение через зубчатые ремни шариковинтовую передачу к исполнительному органу станка. Работа в автоматическом режиме позволяет производить обработку с использованием линейной и круговой интерполяции по программе набранной с пульта или загруженной с внешнего программоносителя.
Для удобства работы станок оснащен гидроразжимом инструмента в горизонтальном шпинделе и в шпинделе вертикальной головки.
Автоматическая порционная система смазки станка обеспечивает надежную подачу масла к направляющим и в коробку скоростей. Конструкция станка обеспечивает надежную защиту от разлетающейся во время работы станка стружки и СОЖ
Технические характеристики станка ВМ133-02
Размеры рабочей поверхности вертикального стола мм
Размеры рабочей поверхности горизонтального стола мм
Перемещение стола мм
Перемещение горизонтальной головки мм
Перемещение пиноли вертикального шпинделя мм
Величина рабочих программируемых подач мммин
Ускоренные перемещения ммин *Y
Мощность привода главного движения кВт
Класс точности по ГОСТ 8-82
Габаритные размеры мм
2 Широкоуниверсальный фрезерный с крестовым столом с ЧПУ (Heidenhain) 6ДМ80ШФ2
Рисунок 6.- Широкоуниверсальный фрезерный станок 6ДМ80ШФ2
Станок фрезерный инструментальный предназначен для выполнения всех видов фрезерных работ сверления зенкерования и растачивания отверстий на деталях из черных и цветных металлов их сплавов и пластмасс в единичном мелкосерийном и серийном производстве что позволяет существенно расширить технологические возможности инструментального фрезерного станка.
Применение в приводе подач серводвигателя с частотным бесступенчатым регулированием в сочетании с оригинальным конструктивным решением автоматической раздачи движения на управляемые оси дало возможность задания параметров обработки и последовательности перемещений рабочих органов станка непосредственно с пульта оператора.
Конструктивные особенности станка и использование комплектующих изделий ведущих инофирм таких как "Merlin Gerin" "Lenze"Mitsubishi Electric" позволили обеспечить максимальное удобство в работе охватить широкий диапазон режимов обработки повысить надежность и производительность станка и достичь наибольших показателей точности и качества обработки.
Наличие наряду с горизонтальным вертикального поворотного шпинделя имеющего возможность установки под различными углами в двух взаимно перпендикулярных плоскостях механизма зажима инструмента и ряда дополнительных приспособлений и принадлежностей позволяет существенно расширить технологические возможности станков.
Технические характеристики станка 6ДМ80ШФ2
Размеры рабочей поверхности стола мм
Наибольшее перемещение стола мм
Наибольшее перемещение гильзы вертикального шпинделя мм
Пределы подач стола мммин(бесступенчатое регулирование)
Пределы частот вращения шпинделя мин-1
Угол поворота оси вертикального шпинделя град
в продольной плоскости
Габаритные размеры станка мм
3 Широкоуниверсальный фрезерный станок c ЧПУ OMM67SC
Рисунок7.- Широкоуниверсальный фрезерный станок OMM67SC
Широкоуниверсальный фрезерный станок c ЧПУ OMM67SC позволяет изготавливать детали сложной формы в автоматическом и полуавтоматическом режиме проводить наладочные операции в ручном режиме.
Широкие возможности станка обеспечиваются контурной системой управления замкнутой по положению с помощью трёх линейных или круговых фотоимпульсных датчиков. предназначен для горизонтального и вертикального фрезерования изделий из различных материалов цилиндрическими дисковыми торцевыми концевыми шпоночными фасонными и другими фрезами а также для сверления рассверливания зенкерования и расточки отверстий под разными углами в различных плоскостях в широком диапазоне режимов резания в том числе с использованием современного скоростного инструмента.
Особенности OMM67SC:
контроль по двум или трём осям;
-дюймовый цветной жидкокристаллический дисплей
множество функций фрезерования;
простое редактирование объектов с использованием копирования и вставки;
встроенный геометрический калькулятор;
импорт чертежей AutoCAD с дискеты или с подключённого компьютера;
встроенные справочные таблицы;
продолжение работы OMM67SC после аварийного отключения электричества.
Технические характеристики станка OMM67SC
Наибольшее перемещение мм
Пределы частот вращения шпинделей 1мин
Пределы рабочих подач мммин
Максимальная масса обрабатываемой детали кг
Масса OMM67SC станка кг
Анотация.docx
В данной курсовой работе рассматривается изучение конструкций и подсистем фрезерного широкоуниверсального станка с ЧПУ. Также подробно изучены конструкции отдельных узлов станка движения в станке основные технические характеристики а также кинематика станка. На основе обзора технической литературы и документации представлены станки аналоги с подробным описанием технических возможностей.
Заключение.docx
В данном курсовом проекте были рассмотрены и изучены конструкции различных широкоуниверсальных станков с ЧПУ. Так же подробно изучены конструкции отдельных узлов станка 6720ВФ2 движения в станке основные технические характеристики а так же кинематика станка. Представлены основные схемы методов обработки на данном фрезерном станке. Рассчитаны режимы резания на типовые операции выполняемые на широкоуниверсальном станке. Рассмотрены приспособления оснастка и вспомогательный инструмент применяемый на станке.
4 Оценка технического уровня станка.docx
1 Расчет режимов резания для типовых операций.
1.1 Фрезерование торцовой фрезой
Рисунок 25.- Схема фрезерования
Материал заготовки: 12Х18Н9Т = 550 МПа
Инструмент - фреза торцевая диаметром D=100мм и z=10 оснащенная пластинами из твердого сплава Т15К6. Ширина фрезерования -67 мм. Глубина фрезерования t=4мм
Подача. При фрезеровании различают подачу на один зуб SZ подачу на один оборот фрезы S и подачу минутную SМ которые находятся в соотношении:
Где n – частота вращения фрезы
z - число зубьев фрезы.
Определяем SZ по таблице 34 [1 с. 283]
Скорость резания – окружная скорость фрезы:
Значение коэффициента и показателей степени приведены в таблице 39 [1 с. 286] а период стойкости Т – в таблице 40 [1 с. 290]
Коэффициент является произведением коэффициентов учитывающих влияние материала заготовки (определяется по таблицам 1-4 [1 с.261-263]) состояния поверхности (по таблицам 5 [1 с.263]) материала инструмента (по таблицам 6 [1 с.263]).
Сила резания. Главная составляющая силы резания при фрезеровании – окружная сила:
Значение коэффициента и показателей степени приведены в таблице 41 [1 стр. 291] поправочный коэффициент на качество обрабатываемого материала в таблице 9 [1 с. 264].
Величины остальных составляющих сил определяются по таблице 42 [1 с. 292].Расположение сил показано на рисунке 1.
Рисунок 26.- Силы резания при фрезеровании
1.2 Фрезерование концевой фрезой
Рисунок 27.- Схема фрезерования
Материал заготовки: Сталь 40Х =600 МПа
Инструмент – фреза концевая D=10 мм и z=4 Материал фрезы -Т15К6. Ширина фрезерования -7 мм. Глубина фрезерования t=14мм
Значение коэффициента и показателей степени приведены в таблице 41 [1 с. 291] поправочный коэффициент на качество обрабатываемого материала в таблице 9 [1 с. 264].
Величины остальных составляющих сил определяются по таблице 42 [1 с. 292].
2 Технические характеристики станка
Рабочая поверхность вертикального стола
Наибольший ход стола мм
Число Т-образных пазов
Ширина Т-образного паза по ГОСТ 1574-75 мм
Верхнего и центрального
Расстояние между Т-образными пазами по ГОСТ 6569-75мм
Расстояние от оси горизонтального шпинделя до рабочей поверхности углового горизонтального стола мм
( при столе переставленном в верхнее положение)
(при столе переставленном в нижнее положение)
Расстояние от торца вертикального шпинделя до рабочей поверхности углового горизонтального стола мм
Расстояние от зеркала стойки до оси
вертикального шпинделя мм
Наибольшее расстояние от торца горизонтального шпинделя до торца подвески мм
Конец вертикального и горизонтального шпинделя по ГОСТ24644-81
Конус вертикального и горизонтального шпинделей по ГОСТ 15945-70
Количество скоростей шпинделей
Частота вращения шпинделей обмин
Ускоренный ход стола (продольный и вертикальный) мммин
Подача шпиндельной бабки мммин
Ускоренный ход шпиндельной бабки мммин
Наибольший ход шпиндельной бабки мм
Наибольшая масса обрабатываемой детали ( с приспособлением) кг
Наибольшая усилие подачи Н
Наибольшее осевое перемещение вертикального шпинделя мм
Наибольший угол поворота головки в вертикальной плоскости град
кинематика.cdw

Структурно-синематическая схемв станка
График часто вращения шпинделя
компановка.cdw
