Селективная очистка дистиллятной фракции 350 - 400 ºС Усть - балыкской нефти N - метилпирролидоном



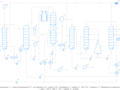
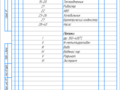
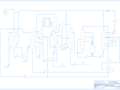
- Добавлен: 25.01.2023
- Размер: 1 MB
- Закачек: 2
Узнать, как скачать этот материал
Подписаться на ежедневные обновления каталога:
Описание
Селективная очистка дистиллятной фракции 350 - 400 ºС Усть - балыкской нефти N - метилпирролидоном
Состав проекта
![]() |
![]() |
![]() ![]() ![]() ![]() |
![]() ![]() ![]() ![]() |
![]() ![]() ![]() ![]() |
![]() ![]() ![]() |
![]() ![]() ![]() |
Дополнительная информация
Контент чертежей
масла.cdw

Спец.cdw

Фрагмент.frw

Рекомендуемые чертежи
- 06.04.2017
Свободное скачивание на сегодня
Обновление через: 9 часов 55 минут