Разработка вагона-цистерны для битума




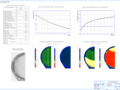
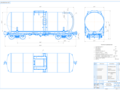
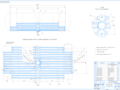
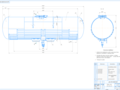
- Добавлен: 25.01.2023
- Размер: 10 MB
- Закачек: 0
Описание
Состав проекта
![]() |
![]() ![]() ![]() ![]() |
![]() ![]() ![]() |
![]() ![]() ![]() ![]() |
![]() ![]() ![]() ![]() |
![]() ![]() ![]() |
![]() ![]() ![]() ![]() |
Дополнительная информация
Л2 - Система разогрева.cdw

Л4 - Битум.cdw

Л1 - общий вид.cdw

Л3 - Котел.cdw
