Разработка узла ТВД SaM-146




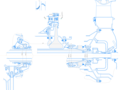
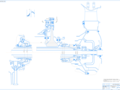
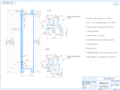
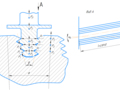
- Добавлен: 25.01.2023
- Размер: 3 MB
- Закачек: 2
Описание
Состав проекта
![]() |
![]() |
![]() ![]() ![]() ![]() |
![]() ![]() ![]() ![]() |
![]() |
![]() ![]() |
![]() ![]() ![]() |
![]() ![]() ![]() ![]() |
![]() ![]() ![]() |
![]() ![]() |
![]() ![]() ![]() |
![]() ![]() ![]() |
![]() ![]() ![]() ![]() |
![]() ![]() ![]() |
![]() ![]() ![]() |
![]() ![]() |
![]() ![]() ![]() |
Дополнительная информация
Пример рабочего чертежа детали.cdw

Штамповка III группы контроля по ОСТ 1 90074-72
мм. Группа контроля 3 ОСТ 1 00021-78
Размеры и допуск биения поверхн. обеспеч. инстр.
Размеры в скобках - после сборки
Диаметральные размеры контролировать на станке
Маркировать шрифтом 3
под Н понимать номер комплекта
Общие требования к изготовлению по ОСТ 1 00450-82
РВД.cdw

Направление вращения ротора - по вращению часовой стрелки -
Допустимый дисбаланс ротора
Вал.frw

Моя.frw

ДефлекторКрит.frw

Хвостовик1.frw

Зуб.frw

Деталь.frw

ДискКрит.frw

диск.frw

Пояснительная записка.docx
ПОЯСНИТЕЛЬНАЯ ЗАПИСКА
(обозначение документа)
В данном курсовом проекте спроектирован узел турбины высокого давления на основе прототипа - двигателя SaM-146.
Курсовой проект включает в себя:
- расчёт на прочность рабочей лопатки турбины;
- расчёт на прочность диска турбины;
- расчёт соединения рабочей лопатки с диском;
- расчет критической частоты вращения ротора;
- патентные исследования охлаждения рабочих лопаток турбины;
- конструкторскую часть.
Расчёту на прочность и конструированию узла турбины предшествовал термогазодинамический расчёт двигателя газодинамический расчёт турбины расчёт по высоте и профилирование рабочей лопатки турбин
Выбор конструктивной схемы двигателя6
Описание конструкции спроектированного узла8
Расчеты на прочность и колебания11
1 Расчет пера рабочей лопатки на статическую прочность14
2 Расчет диска на статическую прочность29
3 Расчет соединения рабочей лопатки с диском37
4 Определение критической частоты вращения ротора47
Патентное исследование58
1 Сравнительный анализ патентов64
Проектируемый узел – турбина высокого давления (ТВД) входит в состав двухконтурного турбореактивного двигателя со смешением потоков (ТРДДсм). В качестве прототипа принят следующий двигатель: SaM146. Двигатель предназначен для региональных самолётов и в настоящее время устанавливается на семейство самолётов Сухой Суперджет-100.
Исходные данные для проектирования узла взяты из курсового проекта по “Теории и расчёту лопаточных машин”.
Газовые турбины относятся к числу самых напряженных узлов конструкций ГТД ограничивающих в большинстве случаев надежность двигателя и его ресурс. Это связано с большими значениями температуры и давления газа перед турбиной и окружной скорости на среднем диаметре рабочих лопаток.
Разработка компоновки узла начато с формирования конструкции элементов образующих проточную часть а затем прорабатывались конструкция деталей ротора опор уплотнений и т.д. последовательно продвигаясь от периферии узла к его оси. Был выполнен чертеж меридионального сечения проточной части с изображением лопаток ротора и статора в масштабе 1:1. Исходя из потребной эффективности охлаждения и расхода охлаждающего воздуха выбраны конструкции рабочей лопатки.
Выбор конструктивной схемы двигателя
Двигатель – двухвальный ТРДДсм. Состоит из широкохордных монолитных стреловидных лопаток вентилятора трех подпорных ступеней КНД разделительного корпуса 6-ступенчатого КВД кольцевой камеры сгорания одноступенчатой турбины высокого давления трехступенчатой турбины низкого давления камеры смешения нерегулируемого реактивного сопла реверсивным устройством.
Примем ротор высокого давления (РВД) – двухопорным установим один подшипник шариковый выполняющий функцию осевой фиксации а второй роликовый - межвальный обеспечивающий смещение ротора относительно статора. Ротор низкого давления (РНД) – трехопорный.
Ротор опирающийся на две опоры представляет собой статически определимую систему при которой лучше обеспечивается соосность подшипников и валов. При этом смещение подшипников приводит лишь к изменениям наклона оси вращения но не вызывают никаких дополнительных статических и динамических нагрузок которые могут появляться в статически неопределимой системе т.е. в трех - или четырехопорном роторе.
При минимальном числе опор упрощается конструкция изделия в целом за счет сокращения количества несущих деталей корпуса уплотнений упрощения маслосистемы системы суфлирования и теплозащиты опор.
При выборе места установки подшипников по длине ротора будем руководствоваться тем что радиально-упорный подшипник воспринимая радиальные нагрузки обеспечивает осевую фиксацию ротора относительно статора и передает результирующую осевую силу ротора на корпус. Конструктивная схема двигателя изображена на рисунке 1.
- шарикоподшипник опоры ротора КНД; 2 - ротор низкого давления; 3 - шарикоподшипник опоры ротора КВД; 4 - ротор высокого давления; 5 - межвальный роликоподшипник задней опоры ротора высокого давления и ТНД; 6 - роликоподшипник задней опоры ротора ТНД; 7 - роликоподшипник средней опоры ротора низкого давления.
Рисунок 1 - Конструктивная схема двигателя
Описание конструкции спроектированного узла
Турбина высокого давления спроектированного двигателя одноступенчатая осевая охлаждаемая привод во вращение 6 ступенчатый компрессор высокого давления. Для охлаждения турбины используется воздух из-за компрессора и из наружного контура. ТВД не имеет бандажной полки антивибрационной полки на рабочей лопатке.
Узел турбины состоит из соплового аппарата ротора и корпуса.
Ступень турбины включает сопловой аппарат и рабочее колесо. Форма проточной части турбины . Ротор ТВД состоит из диска с рабочими лопатками дефлектора носка ТВД с лабиринтами и маслоуплотнительными кольцами. Тип ротора ВД дисковый разъемный центровка и передача осуществляется через соединение призонными болтами расположенными в передней и задней части диска. В передней части диск ТВД через соединение призонными болтами передает крутящий момент валу компрессора высокого давления а центрация осуществляется через носок ТВД (за дисковая область) соединенного фланцем роликового межвального подшипника. Роликовый межвальный подшипник является задней опорой ротора высокого давления.
Рабочая лопатка ТВД имеет конвективно-пленочное охлаждение. Во внутренней полости имеется продольный канал с отверстиями. Хвостовик лопатки «елочного» типа осевая фиксация осуществляется фиксатором с одной стороны и отгибными пластинами. В диске выполнены наклонные отверстия для подвода охлаждающего воздуха к рабочим лопаткам.
Сопловая лопатка – пустотелая охлаждаемая крепление полочного типа. В стенках лопатки выполнена перфорация для создания охлаждающей пленки на поверхности лопатки. В полости расположен дефлектор для подвода охлаждающего воздуха к перфорационным отверстиям.
Радиальные усилия от ротора ТВД на опору через межроторный подшипник вал ТНД и расположенный в опоре подшипник ротора ТНД.
К хвостовику носка ТВД через фланец прикреплено масляное уплотнение и обойма роликового подшипника.
На цилиндрическом пояске в передней части носка ТВД имеется набор уплотнительных колец для уплотнения масляной полости между роторами турбин высокого и низкого давления. Все уплотнения масляных полостей графитовые. В лабиринтных уплотнениях узла используются сотовые вставки и легкосрабатываемые покрытия.
Корпус турбины имеет поперечный разъем.
Активное уплотнение радиальным зазором обеспечивает минимальный зазор между ротором и статором.
Передняя опора ротора ВД воспринимает суммарную осевую и радиальную нагрузки от роторов КВД и ТВД. В переднюю опору входят: корпус подшипника шариковый подшипник радиально-контактное уплотнение. Шариковый подшипник фиксируется в осевом направлении с одной стороны через металлическое кольцо коническим зубчатым колесом а с другой – втулкой. Вращается внутреннее кольцо. Оно же разрезное. Шариковый подшипник с точеным неразъемным сепаратором разделяющим шарики по окружности что исключает трение непосредственно между ними. Смазочное масло подается с помощью форсунки откуда масло попадает в зазор между внутренним кольцом подшипника и сепаратором. Смазочное масло хорошо омывает рабочую поверхность внутреннего кольца подшипника поверхности тел качения под действием инерционных сил попадает на беговую дорожку наружного кольца омывает ее и обеспечивая снятие требуемого количества тепла вытекает через радиальные пазы в маслосборник откуда удаляется отсасывающим маслонасосом.
Задняя опора ВД: наружное кольцо роликового подшипника с одной стороны фиксируется гайкой а с другой через металлическое кольцо буртиком носка ТВД. Подвод масла осуществляется рядом отверстий во внутреннем кольце подшипника. Отвод масла осуществляется через зазор между сепаратором и наружным кольцом наружу через каналы в передней цилиндрической части носка ТНД . Вращаются оба кольца в одну сторону но с разными угловыми скоростями. Опора упруго-демпферная состоящая из упругого кольца.
Допустимые уровни дисбалансов определяют уровень шума и вибрации ресурс изделия в целом. Для жестких роторов весь диапазон точности балансировки разделен на 18 классов точности. Точность балансировки характеризуется произведением удельного дисбаланса на наибольшую частоту вращения ротора в эксплуатации .
Главный вектор дисбалансов перпендикулярен оси ротора и проходит через его центр масс
Допустимый дисбаланс ротора
(при 5 классе точности балансировке)
- угловая скорость вращения ротора при (таблица 3.1)
Материалы основных деталей:
- лопатка – жаропрочный литейный сплав на никелевой основе ЖС-32;
- диск – жаропрочный деформируемый сплав на никелевой основе ЭП962П;
- вал - жаропрочный деформируемый сплав на никелевой основе ЭП742ИД;
- корпус - жаропрочный деформируемый сплав на никелевой основе ХН56ВМТЮ (ЭП199).
Расчеты на прочность и колебания
Исходные данные необходимые для выполнения расчётов приведены в таблице 3.1.
Таблица 3.1- Исходные данные для разработки конструкции узла турбины
Наименование параметра
Расход газа (воздуха)
Средний диаметр проточной части на входе
Высота проточной части на входе
Средний диаметр проточной части на выходе
Высота проточной части на выходе
Температура газа на входе
Осевая составляющая абсолютной скорости на входе из рабочего колеса
Осевая составляющая абсолютной скорости на выходе из рабочего колеса
Окружная составляющая абсолютной скорости на входе в рабочее колесо
Продолжение таблицы 3.1
Окружная составляющая абсолютной скорости на выходе из рабочего колеса
Статическое давление на входе в рабочее колесо
Статическое давление на выходе из рабочего колеса
Температура газа на входе в рабочее колесо
Температура газа на выходе из рабочего колеса
Наружный диаметр лопаточного венца на входе
Наружный диаметр лопаточного венца на выходе
Диаметр втулки на входе
Диаметр втулки на выходе
Хорда профиля рабочей лопатки:
Максимальная толщина профиля:
Угол установки профиля:
Длина проточной части узла
Температура газа на входе в рабочее колесо в относительном движении
1 Расчет пера рабочей лопатки на статическую прочность
Перо лопатки по высоте разбиваем на пять равных участков (рисунок 3.1). Корневое сечение выбирается на расстоянии 2-3 мм от начала переходной галтели от пера к полке хвостовика. Концевое сечение выбирается на 2-3 мм ниже торца пера.
Рисунок 3.1- Расчётная схема
Единичные газовые силы действующие на лопатку
- радиус наружного сечения
- радиус корневого сечения.
Температура лопатки в среднем сечении
где - температура воздуха охлаждающего лопатки
- коэффициент глубины охлаждения (конвективно-пленочное охлаждение).
Типичное распределение температуры по высоте пера лопатки показано на рисунке 3.2. Неравномерность распределения по высоте лопатки может составлять 50-150С.
Принимаем материал рабочей лопатки – жаропрочный литейный сплав на никелевой основе ЖС32 () [8]. В зависимости от температуры для каждого сечения находим значения .
Для этого находим значение параметра Ларсона-Миллера в каждом сечении:
где- температура детали
Время работы на максимальном режиме примем равным 5% от ресурса двигателя. Ресурс двигателя = 20000 ч.
В зависимости от по таблице [8] путём интерполяции определяем точные значения (таблица 3.1)
Геометрические характеристики трех сечений определены в КОМПАС. Геометрические характеристики промежуточных сечений определены методом линейной интерполяции. Лопатка рассматривается как оболочка с толщиной стенок 1-2 мм.
Профиль лопатки в трех рассматриваемых сечениях показаны на рисунках 3.3-3.5. Координаты опасных точек определены в КОМПАС и сведены в таблицу 3.2
Рисунок 3.3 – Профиль лопатки в сечении 0-0
Рисунок 3.4 – Профиль среднего сечения лопатки
Рисунок 3.5 – Профиль лопатки в сечении 5-5
Основные исходные данные сводим в таблицу 3.2.
Таблица 3.2 - Исходные данные для расчёта рабочей лопатки на статическую прочность
Расчёт производим в программе UISAPR. Список используемых обозначений приведен в таблице 3.3. Результаты расчёта приведены в таблице 3.3.1
Таблица 3.3 – Список используемых обозначений
Обозначение в методике
Обозначение в программе и на экране
Угловая скорость вращения ротора
Угол поворота главных центральных осей в i-том сечении лопатки
Плотность материала лопатки
Предел длительной прочности в материале при температуре Т в течение времени
Радиус i-того сечения лопатки
Площадь i-того сечения лопатки
Смещение центра масс i-того сечения лопатки в проекции на ось Х
Смещение центра масс i-того сечения лопатки в проекции на ось Y
Момент инерции i-того сечения лопатки относительно главной центральной оси
Продолжение таблицы 3.3
Координата точки А в i-том сечения лопатки
Координата точки В в i-том сечения лопатки
Координата точки D в i-том сечения лопатки
Единичная газовая сила в направлении оси Х
Единичная газовая сила в направлении оси Y
Изгибающий момент от газовых сил относительно оси Х в i-том сечения лопатки
Изгибающий момент от газовых сил относительно оси Y в i-том сечения лопатки
Изгибающий момент от центробежных сил относительно оси Х в i-том сечения лопатки
Изгибающий момент от центробежных сил относительно оси Y в i-том сечения лопатки
Изгибающий момент относительно главной центральной оси в i-том сечения лопатки
Напряжение растяжения от центробежных сил в i-том сечения лопатки
Напряжение изгиба в точке А в i-том сечения лопатки
Напряжение изгиба в точке B в i-том сечения лопатки
Напряжение изгиба в точке D в i-том сечения лопатки
Результирующиее напряжение в точке А в i-том сечения лопатки
Результирующиее напряжение в точке В в i-том сечения лопатки
Результирующиее напряжение в точке D в i-том сечения лопатки
Коэффициент запаса прочности по напряжениям в i-том сечения лопатки
Объем бандажной полки
Радиус центра масс бандажной полки
Температура напряжениям в i-том сечения лопатки
Максимальное напряжение напряжениям в i-том сечения лопатки
Минимальный коэффициент запаса прочности по напряжениям
Таблица 3.3.1 – Результаты расчета рабочей лопатки на прочность
***********************************************************************
**** РАСЧЕТ РАБОЧИХ ЛОПАТОК ГТД НА ПРОЧНОСТЬ ****
ИСХОДНЫЕ ДАННЫЕ ДЛЯ РАСЧЕТА
материал лопатки gs-32
частота вращения W = 1697.8 1c
единичная газовая сила по оси X Px = 6276.84 Нм
единичная газовая сила по оси Y Py = 8952.96 Нм
плотность материала лопатки Ro = 8760.0 кгм3
объем бандажной полки Yb = 0.0 мм
радиус центра масс бандажной полки Rb = 0.0
!---------------------------------------------------------------------!
! температурыпределы длительной прочности и коэффициенты компенсации !
! номер сечения ! 0 ! 1 ! 2 ! 3 ! 4 ! 5 !
! T (К) ! 1045.0 1056.0 1064.9 1061.8 1047.0 1030.0 !
! SIT (МПа) ! 674.8 645.7 621.4 629.9 670.4 712.8 !
! UKX ( - ) ! 0.000 0.000 0.000 0.000 0.000 0.600 !
! UKY ( - ) ! 0.000 0.000 0.000 0.000 0.000 0.600 !
! геометрические характеристики сечений лопатки !
! R (мм) ! 305.0 296.0 287.0 278.0 269.0 260.0 !
! F (мм2) ! 81.8 98.8 115.5 129.5 140.9 152.0 !
! BET (град) ! 24.2 23.3 22.4 21.9 21.6 21.4 !
! AJ1 (мм4) ! 1412.8 1732.0 2035.0 2232.0 2320.0 2392.4 !
! AJ2 (мм4) ! 7966.6 9530.0 11035.0 12335.0 13080.0 13870.9 !
! AKA (мм) ! -13.3 -13.1 -13.0 -12.8 -12.6 -12.3 !
! AKB (мм) ! 16.2 16.1 16.3 15.9 15.8 15.6 !
! AKD (мм) ! -4.3 -4.4 -4.4 -4.3 -4.1 -4.0 !
! QA (мм) ! -7.8 -7.9 -7.9 -7.9 -7.8 -7.6 !
! QB (мм) ! -7.8 -7.9 -7.9 -7.9 -7.8 -7.6 !
! QD (мм) ! 8.1 8.2 8.2 8.2 8.1 8.0 !
!=====================================================================!
! результаты расчета !
! X (мм) ! 0.2 0.2 0.1 0.1 0.0 0.0 !
! Y (мм) ! 0.3 0.3 0.2 0.1 0.1 0.0 !
! AMPX (Н*м) ! 0.0 -0.36 -1.45 -3.26 -5.80 -9.06 !
! AMJX (Н*м) ! 0.0 0.18 0.75 1.79 3.33 5.44 !
! AMPY (Н*м) ! 0.0 0.25 1.02 2.29 4.07 6.36 !
! AMJY (Н*м) ! 0.0 -0.13 -0.55 -1.28 -2.36 -3.81 !
! AM1 (Н*м) ! 0.0 -0.12 -0.46 -1.00 -1.67 -2.45 !
! AM2 (Н*м) ! 0.0 0.18 0.70 1.48 2.49 3.69 !
! SRS (МПа) ! 0.0 53.3 98.51 140.62 181.55 219.56 !
! SIGA (МПа) ! 0.0 0.80 2.63 5.05 7.98 11.09 !
! SIGB (МПа) ! 0.0 0.23 0.77 1.60 2.58 3.67 !
! SIGD (МПа) ! 0.0 -0.48 -1.60 -3.15 -5.03 -7.09 !
! SSA (МПа) ! 0.0 63.23 117.48 168.22 217.58 263.26 !
! SSB (МПа) ! 0.0 62.66 115.63 164.77 212.18 255.83 !
! SSD (МПа) ! 0.0 61.95 113.26 160.02 204.58 245.07 !
! SMAX (МПа) ! 0.0 63.23 117.48 168.22 217.58 263.26 !
! AN ! 100000000000000000000.0 10.21 5.29 3.74 3.08 2.71 !
***** минимальный коэффициент запаса прочности ANMIN = 2.71
Распределение основных параметров по высоте лопатки показаны на рисунках 3.6 – 3.9.
Рисунок 3.6 - Распределение температуры по высоте лопатки
Рисунок 3.7 - Распределение пределов прочности материала по высоте лопатки
Рисунок 3.8 - Распределение напряжений растяжения и изгиба по длине лопатки
Рисунок 3.9 - Распределение запасов прочности по длине лопатки
Минимальный запас длительной статической прочности получился Допустимое значение запаса длительной прочности примем [1]. Условие выполняется прочностная надёжность обеспечена.
2 Расчет диска на статическую прочность
Исходные данные для расчёта диска берутся из предыдущих расчётов и принимаются по рекомендациям [1] приведены в таблице 3.4.
Таблица 3.4 - Исходные данные для расчёта диска
Для диска выбран высокожаропрочный гранулируемый сплав ЭП962П ().
Диск разбиваем на 20 сечений первое сечение совпадает с образующей центрального отверстия а последнее является касательным к окружности вписанной по нижним точкам впадин (рисунок 3.10). Определяем радиус и толщину каждого кольцевого элемента.
Рабочая температура подшипников ограничивается величиной 500 700 К. С учётом этого температура задаётся в интервале 550 750 К. Принято значение . Величина задаётся на 50 150 К меньше температуры в корневом сечении рабочей лопатки. Принято значение (). Температура в каждом сечении рассчитывается по зависимости:
где m=2 для неохлаждаемых дисков
m=3 для охлаждаемых дисков[2].
В зависимости от температуры используя интерполяцию для каждого сечения находим значение физико-механических характеристик материала . Полученные данные сводим в таблицу 3.5.
Задаём значение напряжений в 1-м сечении для первого и второго расчётов: (для диска с центральным отверстием) [2] - произвольно.
Расчёт производим в программе UISAPR.
Таблица 3.5 - Распределение параметров по сечениям диска
Продолжение таблицы 3.5
Рисунок 3.10 - Исходный контур и расчётная схема диска
Результаты расчёта приведены в таблице 3.5.1
Таблица 3.5.1 – Результаты расчета диска на прочность
* ИСХОДНЫЕ ДАННЫЕ ДЛЯ РАСЧЕТА ДИСКОВ НА ПРОЧНОСТЬ *
* Признак диска(0-компрессора1-турбины) * 1.00000*
* Признак расчета(0-без учета температуры1-с учетом) * 1.00000*
* Число сечений диска * 20.00000*
* Угловая скорость вращения диска [1c] * 1697.82100*
* Плотность материала диска [кгм3] * 8280.00000*
* Напряжение в корневом сечении лопатки [МПа] * 219.56000*
* Площадь корневого сечения лопатки [cм2] * 1.52031*
* Число лопаток * 78.00000*
* Площадь сечения обода диска [cм2] * 3.17002*
* Радиус центра тяжести обода диска [м] * 0.24837*
* Коэффициент Пуассона * 0.30000*
* Радиальн.напряжение в сечении 1 ( расчет 1) [МПа] * 0.00000*
* Радиальн.напряжение в сечении 1 ( расчет 2) [МПа] * 0.00000*
* Тангенциальн.напряжение в сечении 1 (расчет 1) [МПа] * 100.00000*
* Тангенциальн.напряжение в сечении 1 (расчет 2) [МПа] * 200.00000*
* Параметры по сечениям диска *
* Nсеч * R[m] * R[m] * E[Па*E-6]* T[K] * AL[1K*E5] * SD[МПа] *
* 1 * 0.057 * 0.1098 * 191298.0 * 550.0 * 1.2595600 * 1504.65 *
* 2 * 0.071 * 0.1008 * 191291.0 * 550.2 * 1.2596100 * 1504.65 *
* 3 * 0.083 * 0.0890 * 191257.0 * 551.0 * 1.2598300 * 1504.63 *
* 4 * 0.090 * 0.0730 * 191214.0 * 552.0 * 1.2601100 * 1504.61 *
* 5 * 0.099 * 0.0582 * 191127.0 * 554.1 * 1.2606700 * 1504.56 *
* 6 * 0.106 * 0.0444 * 191025.0 * 556.6 * 1.2613400 * 1504.51 *
* 7 * 0.116 * 0.0344 * 190824.0 * 561.4 * 1.2626500 * 1504.41 *
* 8 * 0.132 * 0.0271 * 190332.0 * 573.2 * 1.2658400 * 1504.17 *
* 9 * 0.147 * 0.0240 * 189635.0 * 589.9 * 1.2703700 * 1503.82 *
* 10 * 0.163 * 0.0216 * 188638.0 * 613.8 * 1.2768500 * 1503.32 *
* 11 * 0.177 * 0.0195 * 187360.0 * 644.5 * 1.2851600 * 1502.68 *
* 12 * 0.190 * 0.0171 * 185975.0 * 677.8 * 1.2941600 * 1501.99 *
* 13 * 0.201 * 0.0156 * 184517.0 * 712.7 * 1.3036400 * 1390.45 *
* 14 * 0.209 * 0.0145 * 183424.0 * 739.0 * 1.3107500 * 1351.57 *
* 15 * 0.213 * 0.0152 * 182656.0 * 757.4 * 1.3157300 * 1312.51 *
* 16 * 0.218 * 0.0165 * 181595.0 * 777.6 * 1.3213500 * 1268.21 *
* 17 * 0.223 * 0.0173 * 179730.0 * 798.4 * 1.3275700 * 1191.61 *
* 18 * 0.227 * 0.0313 * 178308.0 * 814.2 * 1.3323100 * 1127.09 *
* 19 * 0.235 * 0.0313 * 174772.0 * 853.5 * 1.3440900 * 966.67 *
* 20 * 0.243 * 0.0313 * 169510.0 * 900.0 * 1.3580600 * 771.46 *
* РЕЗУЛЬТАТЫ РАСЧЕТА ДИСКОВ НА ПРОЧНОСТЬ *
***************************************************
* Nсеч * SIT[МПа] * SIR[МПа] * SIE[МПа] * K *
* 1 * 797.08 * 0.00 * 797.08 * 1.888 *
* 2 * 646.98 * 128.52 * 646.98 * 2.326 *
* 3 * 574.33 * 193.48 * 574.33 * 2.620 *
* 4 * 549.21 * 243.54 * 549.21 * 2.740 *
* 5 * 530.68 * 307.31 * 530.68 * 2.835 *
* 6 * 532.41 * 389.83 * 532.41 * 2.826 *
* 7 * 537.96 * 486.09 * 537.96 * 2.797 *
* 8 * 533.06 * 569.65 * 569.65 * 2.641 *
* 9 * 517.82 * 616.81 * 616.81 * 2.438 *
* 10 * 476.40 * 618.51 * 618.51 * 2.431 *
* 11 * 417.98 * 607.29 * 607.29 * 2.474 *
* 12 * 356.96 * 605.78 * 605.78 * 2.479 *
* 13 * 293.45 * 604.54 * 604.54 * 2.300 *
* 14 * 246.66 * 606.26 * 606.26 * 2.229 *
* 15 * 206.28 * 582.05 * 582.05 * 2.255 *
* 16 * 148.17 * 513.58 * 513.58 * 2.469 *
* 17 * 89.00 * 448.54 * 448.54 * 2.657 *
* 18 * 20.37 * 321.59 * 321.59 * 3.505 *
* 19 * -104.84 * 176.36 * 228.77 * 4.225 *
* 20 * -217.82 * 115.81 * 224.72 * 3.433 *
Графики распределения напряжений по радиусу диска изображены на рисунках 3.11 – 3.14.
Рисунок 3.11 - Распределение тангенциальных напряжений по радиусу диска
Рисунок 3.12 - Распределение радиальных напряжений по радиусу диска
Рисунок 3.13 - Распределение эквивалентных напряжений по радиусу диска
Рисунок 3.14 - Распределение запасов прочности по радиусу диска
Минимальный запас прочности по напряжениям получился Нормативное значение запаса длительной прочности примем [2]
прочностная надёжность обеспечена.
3 Расчет соединения рабочей лопатки с диском
Соединение рабочих лопаток с диском ёлочного типа – весьма напряжённое и ответственное место в конструкции газовых турбин. Конструктивная форма и размеры показаны на рисунках 3.15 - 3.16.
Параметры соединения выбираем в соответствии с рекомендациями [4] и заносим в таблицу 3.6.
Таблица 3.6 - Параметры соединения
После эскизной прорисовки соединения в ПК КОМПАС определяем значения площадей
длин радиусов центров масс соответствующих участков поперечного сечения выступа и хвостовика. Полученные данные заносим в таблицу 3.7.
Рисунок 3.15 - Конструктивная форма характерные размеры соединения ёлочного типа и действующие силы
Рисунок 3.16 - Геометрия и характерные параметры зуба хвостовика лопатки и паза под него в диске
Таблица 3.7 - Исходные данные для расчёта
Продолжение таблицы 3.7
Произведём расчёт используя методику [4].
Инерционная сила пера лопатки:
центробежная сила действующая на 1-й участок хвостовика:
центробежная сила действующая на 2-й участок хвостовика:
центробежная сила действующая на 3-й участок хвостовика:
центробежная сила действующая на 4-й участок хвостовика:
инерционная сила всей лопатки:
(бандажная полка отсутствует);
погонная сила приходящаяся на единицу длины зуба одинаковая для всех зубьев:
сила действующая на каждый зуб:
сила действующая нормально к рабочей поверхности зуба:
Предел длительной прочности по напряжениям смятия примем равным пределу длительной прочности по напряжениям растяжения:
тогда запас по напряжениям смятия определится:
Нормативное значение примем [4]. Условие выполняется следовательно прочностная надёжность обеспечена.
предел длительной прочности по напряжениям среза примем:
Тогда запас по напряжениям среза определится:
Нормативное значение примем [4]. Условие выполняется прочностная надёжность зуба обеспечена.
Изгибающий момент в основании зуба:
момент сопротивления основания зуба:
напряжения растяжения в сечении
Запас статической прочности хвостовика:
Нормативное значение примем [4]. Условие выполняется следовательно прочностная надёжность хвостовика обеспечена.
Центробежная сила действующая на 1-й участок выступа:
центробежная сила действующая на 2-й участок выступа:
центробежная сила действующая на 3-й участок выступа:
Запас статической прочности выступа:
Нормативное значение примем [4]. Условие выполняется следовательно прочностная надёжность выступа обеспечена.
4 Определение критической частоты вращения ротора
Весь ротор по длине разбиваем на участки (рисунок 3.17) которые пронумеровываем слева направо от 1 до N. Количество расчётных сечений будет на единицу больше т.е. N=1. Распределённые массы ротора заменяем сосредоточенными. В этом случае для i-го сечения масса определится как сумма масс половины (i-1)-го участка вала и половины i-го участка вала плюс масса какого-либо элемента ротора расположенного в этом сечении (например диска).
Для каждого участка ротора составляем набор исходных данных в состав которых входят длина участка внешние диаметры на входе и выходе участка соответствующие внутренние диаметры и (см. таблицу 3.8).
Рисунок 3.17- Исходный контур и расчётная схема ротора
Таблица 3.8 - Исходные данные по участкам
Примем материал вала и всех дисков – ЭП742ИД плотностью . Массу участка вала определяем по формуле:
Жёсткость опор определяется:
гдеподатливость опоры.
Податливость опор можно ориентировочно оценить следующими значениями:
Примем жёсткость опор:
Определение полярного и диаметрального моментов инерции диска и его массы
Объем и массу дефлектора и диска определим при помощи ПК КОМПАС. (см. рисунок 3.18-3.19)
Рисунок 3.18 – Определение массы дефлектора
Рисунок 3.18 – Определение массы диска
Массу пера лопатки определим по формуле:
где - плотность материала лопатки;
- средняя площадь поперечного сечения лопатки:
Массу одного выступа вычислим по формуле:
где - плотность материала диска;
- площадь поперечного сечения выступа:
Момент инерции дефлектора и диска были найдены при помощи ПК КОМПАС (см. рисунок 3.18)
Полярный момент инерции лопаточного венца:
где - радиус центра массы профильной части лопатки; приближённо примем что этот центр массы лежит на расстоянии 13 высоты пера лопатки считая от корневого сечения:
Считаем что диски достаточно тонкие. В этом случае диаметральный момент инерции приближённо определим как
Результаты расчётов приведены в таблице 3.9
Таблица 3.9 - Исходные данные по сечениям
Продолжение таблицы 3.9
Расчёт производим в программе UISAPR. Результаты расчёта приведены в таблице 3.9.1
Таблица 3.9.1 – Результаты расчета диска на прочность
* ИСХОДНЫЕ ДАННЫЕ ДЛЯ РАСЧЕТА ВАЛОВ НА КОЛЕБАНИЯ *
* Количество сечений вала * 11.00000*
* Признак наличия конических участков (0 - нет 1 - есть)* 0.00000*
* Модуль упругости [ *10e-5МПа ] * 0.20500*
* * Параметры по сечениям вала *
* *******************************************************************
* N * L * DH1 * DH2 * DB1 * DB2 * M * JP * JD * CB *
* 1*0.03600*0.298*0.298*0.292*0.292* 0.4200*0.000000*0.000000* 0.000*
* 2*0.06600*0.298*0.298*0.292*0.292* 1.1800*0.000000*0.000000* 8.060*
* 3*0.07600*0.298*0.298*0.292*0.292* 1.6400*0.000000*0.000000* 0.000*
* 4*0.05900*0.298*0.298*0.292*0.292* 1.5600*0.000000*0.000000* 0.000*
* 5*0.05000*0.298*0.298*0.292*0.292* 8.7800*0.238000*0.119000* 0.000*
* 6*0.02600*0.298*0.298*0.292*0.292* 0.8800*0.000000*0.000000* 0.000*
* 7*0.02800*0.294*0.294*0.264*0.264*22.3700*1.603000*0.802000* 0.000*
* 8*0.01600*0.272*0.272*0.218*0.218* 2.9200*0.000000*0.000000* 0.000*
* 9*0.02200*0.226*0.226*0.166*0.166* 3.0700*0.000000*0.000000* 0.000*
* 10*0.02600*0.168*0.168*0.152*0.152* 2.1300*0.000000*0.000000* 0.000*
* 11*0.03000*0.168*0.168*0.152*0.152* 0.9400*0.000000*0.000000* 13.330*
* 12* * * * * * 0.5000*0.000000*0.000000* 0.000*
* L - длина участка вала [ м ]; *
* DH1 - наружный диаметр начала участка вала [ м ]; *
* DH2 - наружный диаметр конца участка вала [ м ]; *
* DB1 - внутренний диаметр начала участка вала [ м ]; *
* DB2 - внутренний диаметр конца участка вала [ м ]; *
* M - масса участка вала [ кг ]; *
* JP - полярный момент инерции [ кг*м2 ]; *
* JD - диаметральный момент инерции [ кг*м2 ]; *
* CB - жесткость опоры вала [ МНм ]; *
* РЕЗУЛЬТАТЫ РАСЧЕТА ВАЛА НА КОЛЕБАНИЯ *
* Критическая частота 1 [ радс ] * 0.00000*
* Критическая частота 2 [ радс ] * 0.00000*
* Критическая частота 3 [ радс ] * 0.00000*
Вывод: ротор считаем жестким
Патентное исследование
Тема патентного исследования: охлаждаемые рабочие лопатки турбин.
Целью патентных исследований является ознакомление с существующими методами охлаждения рабочих лопаток турбин выявление достоинств и недостатков существующих схем а также оценка возможности их дальнейшего применения в разрабатываемой конструкции (ТРДДсм).
)Патент №2323343. Охлаждаемая лопатка турбомашины.
Страна публикации: Российская Федерация.
Авторы: Елисеев Ю.С. Беляев В.Е. Косой А.С.
Охлаждаемая лопатка турбомашины содержащая перо лопатки с последовательно соединенными каналом охлаждения входной кромки пера лопатки и промежуточным каналом канал сброса сообщенный с выпускными отверстиями выходной кромки пера лопатки хвостовик с полкой которая снабжена выпускными отверстиями а также канал подвода охлаждающей среды соединенный с каналом охлаждения входной кромки пера лопатки отличающаяся тем что в хвостовике лопатки выполнена полость которая сообщена с выходом промежуточного канала и со входом канала сброса а также с выпускными отверстиями полки хвостовика лопатки.
Охлаждаемая лопатка турбомашины по п.1 отличающаяся тем что канал сброса образован системой каналов охлаждения пера лопатки.
Охлаждаемая лопатка турбомашины по п.1 отличающаяся тем что полость хвостовика лопатки выполнена конической с широкой частью обращенной к выходу промежуточного канала и входу канала сброса.
Охлаждаемая лопатка турбомашины по п.3 отличающаяся тем что входы выпускных отверстий полки хвостовика лопатки расположены на образующей условной конической поверхности вписанной в полость хвостовика лопатки.
Охлаждаемая лопатка турбомашины по п.1 или 2 или 3 или 4 отличающаяся тем что выпускные отверстия полки хвостовика выполнены наклонными к поверхности полки хвостовика обращенной к проточной части турбины.
Охлаждаемая лопатка турбомашины по п.1 или 2 или 3 или 4 отличающаяся тем что полость хвостовика выступает за пределы контура корневого сечения пера лопатки.
)Патент №2283432. Охлаждаемая лопатка турбомашины.
Авторы: Бервинов Б.П. Кинзбурский В.С.
Охлаждаемая лопатка турбомашины содержащая перо с центральной полостью и каналом расположенным в зоне входной кромки и сообщенным входными каналами и выполненными в пере выходными каналами с центральной полостью и внешней поверхностью выпуклой части пера причем выходные и входные каналы выполнены тангенциальными относительно канала расположенного в зоне входной кромки а отношение площадей проходных сечений выходных и входных каналов выбрано в интервале 42>FвыхFвхода>17 отличающаяся тем что ось канала расположенного в зоне входной кромки в меридиональной плоскости турбомашины отклонена от радиального направления на угол от 1 до 8° при этом в пере размещена перегородка на расстоянии h=(008-014)L от входной кромки где L - хорда профиля пера в заданном сечении и входные каналы выполнены в перегородке причем число выходных каналов больше числа входных каналов.
Охлаждаемая лопатка по п.1 отличающаяся тем что число выходных каналов по меньшей мере на два больше числа входных каналов.
) Патент №2387846. Способ охлаждения рабочих лопаток турбины двухконтурного газотурбинного двигателя и устройство для его реализации
Авторы: Некрасова Елена Сергеевна Канахин Юрий Александрович Марчуков Евгений Ювенальевич
Способ охлаждения рабочих лопаток турбины двухконтурного газотурбинного двигателя включающий отбор охлаждающего воздуха из воздушной полости камеры сгорания его транспортировку через воздухо-воздушный теплообменник установленный в воздушном тракте второго контура в аппарат закрутки последующий подвод охлаждающего воздуха во внутренние полости рабочих лопаток через воздушные каналы в рабочем колесе турбины и регулирование его расхода отличающийся тем что внутреннюю полость каждой рабочей лопатки расположенную у входной кромки отделяют от остальной полости перегородкой направленной вдоль входной кромки образованную полость сообщают перфорационными отверстиями в стенке с проточной частью турбины и подают в нее охлаждающий воздух из воздушной полости камеры сгорания через дополнительный аппарат закрутки статора и через дополнительные воздушные каналы в рабочем колесе.
Способ охлаждения рабочих лопаток турбины двухконтурного газотурбинного двигателя по п.1 отличающийся тем что подвод охлаждающего воздуха в воздушные каналы рабочего колеса осуществляют через безлопаточный диффузор рабочего колеса.
Способ охлаждения рабочих лопаток турбины двухконтурного газотурбинного двигателя по п.1 отличающийся тем что подвод охлаждающего воздуха в дополнительные воздушные каналы рабочего колеса осуществляют через дополнительный безлопаточный диффузор рабочего колеса.
Способ охлаждения рабочих лопаток турбины двухконтурного газотурбинного двигателя по п.1 отличающийся тем что полость за дополнительным аппаратом закрутки статора отделяют от полости на входе в безлопаточный диффузор рабочего колеса подвижным уплотнением.
Способ охлаждения рабочих лопаток турбины двухконтурного газотурбинного двигателя по п.1 отличающийся тем что полость за дополнительным аппаратом закрутки статора отделяют от проточной части турбины подвижным уплотнением.
Способ охлаждения рабочих лопаток турбины двухконтурного газотурбинного двигателя по п.1 отличающийся тем что расход охлаждающего воздуха в дополнительные воздушные каналы рабочего колеса изменяют в зависимости от режима работы газотурбинного двигателя.
Устройство для охлаждения рабочей лопатки турбины двухконтурного газотурбинного двигателя содержащее последовательно установленные воздухо-воздушный теплообменник размещенный во втором контуре соединенный своим входом с воздушной полостью камеры сгорания а выходом с воздушным коллектором с управляющими клапанами в нем многоканальный воздуховод проходящий через внутренние полости сопловых лопаток аппарат закрутки статора и воздушные каналы в рабочем колесе соединенные с внутренними полостями рабочих лопаток отличающееся тем что внутренняя полость каждой рабочей лопатки расположенная у входной кромки отделена от остальной полости перегородкой направленной вдоль входной кромки образованная полость сообщена перфорационными отверстиями в стенке с проточной частью турбины и соединена с камерой сгорания через дополнительный аппарат закрутки статора и через дополнительные воздушные каналы в рабочем колесе.
Устройство для охлаждения рабочей лопатки турбины двухконтурного газотурбинного двигателя по п.7 отличающееся тем что на рабочем колесе между его воздушными каналами и аппаратом закрутки статора размещен безлопаточный диффузор.
Устройство для охлаждения рабочей лопатки турбины двухконтурного газотурбинного двигателя по п.7 отличающееся тем что на рабочем колесе между его дополнительными воздушными каналами и дополнительным аппаратом закрутки статора размещен дополнительный безлопаточный диффузор.
Устройство для охлаждения рабочей лопатки турбины двухконтурного газотурбинного двигателя по п.7 отличающееся тем что полость на выходе из дополнительного аппарата закрутки отделена от полости на входе в безлопаточный диффузор рабочего колеса подвижным уплотнением.
Устройство для охлаждения рабочей лопатки турбины двухконтурного газотурбинного двигателя по п.7 отличающееся тем что полость на выходе из дополнительного аппарата закрутки отделена от проточной части турбины подвижным уплотнением.
Устройство для охлаждения рабочей лопатки турбины двухконтурного газотурбинного двигателя по п.7 отличающееся тем что перед дополнительным аппаратом закрутки установлен дополнительный управляющий клапан.
1 Сравнительный анализ патентов
Приведенные выше патенты можно использовать для охлаждения лопаток турбин. Способ охлаждения лопаток представленное в первом описании к авторскому свидетельству позволяет уменьшить потребления хладоресурса охлаждающей среды при одновременном повышении надежности лопатки за счет снижения термонапряженности ее конструкции а также упрощении геометрии каналов охлаждения и повышении технологичности лопатки в целом и снижении требований предъявляемых лопаткой к конструкции системы подвода охлаждающего воздуха и к параметрам охлаждающего.
Изобретение представленное во втором описании позволяет повысить надежность турбомашины повысить эффективность охлаждения входной кромки лопатки и упростить технологию изготовления.
Изобретение представленное во втором описании направлено на повышение экономичности газотурбинных двигателей с высокотемпературными турбинами за счет оптимизации расхода охлаждающего воздуха в разных зонах рабочих лопаток турбин высокого давления при одновременном сохранении надежности и ресурса работы двигателя.
В спроектированном узле можно применить патент №3. То есть использовать вместо дефлектора транспортировку охлаждающего воздуха через воздухо-воздушный теплообменник в аппарат закрутки последующий подвод охлаждающего воздуха во внутренние полости рабочих лопаток но это существенно усложнить конструкцию приведет к увеличению массы и дополнительных затрат.
Расчёт на прочность рабочих лопаток ГТД – Методические указания Сост. Тархов Л.Н. Харитонов В.Ф. – Уфа изд. УГАТУ 2006 38с.
Методические указания “Расчёт на прочность дисков ГТД” Харитонов В.Ф. и др. – Уфа УГАТУ 2005.-25с.
Расчёт критических скоростей вращения роторов ГТД Методические указания Сост. Харитонов В.Ф. и др. – Уфа изд. УГАТУ 2006 17с.
Конструкция и проектирование авиационных и газотурбинных двигателей. Под ред. Д.В. Хронина – М.: Машиностроение 1989 568с.
Конструкция и прочность авиационных двигателей и энергетических установок. Уфимск. гос. авиац. техн. ун-т; Сост.: Б.К. Галимханов В.Ф. Харитонов. – Уфа 2007. – 39с.
Справочник по машиностроительному черчению. Федоренко В.А. Шошин А.И. Л. Машиностроение 1976 336с.
Скубачевский Г.С. Авиационные газотурбинные двигатели. Конструкция и расчет деталей. – М.: Машиностроение 1981 550с.
Материалы деталей авиационных ГТД. Харитонов В.Ф. Методические указания к курсовому и дипломному проектированию. – Уфа 2004. – 38с.
Рекомендуемые чертежи
Свободное скачивание на сегодня
- 29.08.2014
- 24.01.2023
Другие проекты
- 03.08.2014