Разработка технологического процесса разложения топливного насоса




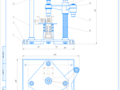
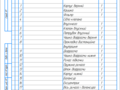
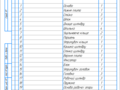
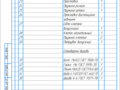
- Добавлен: 24.01.2023
- Размер: 1 MB
- Закачек: 0
Описание
Разработка технологического процесса разложения топливного насоса
Состав проекта
![]() |
![]() ![]() ![]() ![]() |
![]() ![]() ![]() ![]() |
![]() ![]() ![]() ![]() |
![]() ![]() ![]() ![]() |
![]() ![]() ![]() ![]() |
![]() ![]() ![]() ![]() |
![]() ![]() ![]() ![]() |
![]() ![]() ![]() |
![]() ![]() ![]() ![]() |
![]() ![]() ![]() ![]() |
![]() ![]() ![]() ![]() |
![]() ![]() ![]() ![]() |
![]() ![]() ![]() ![]() |
![]() ![]() ![]() ![]() |
![]() ![]() ![]() |
Дополнительная информация
Пристосування ТН.cdw

Спец.1_пристос..cdw

маршрутная_карта_т_п_мех._обр__No.2.frw

Операційна карта розб-П3_No.2.frw

Spets_1.cdw

маршрутная_карта_т_п_мех._обр__No.1.frw

Операційна карта розб-П_2_No.1.frw

Spets_2.cdw

Схема оброб дет.cdw

Операційна карта розб-П_3_No.1.frw

маршрутная_карта_т_п_мех._обр__No.3.frw

Операційна карта розб_005No.1.frw

Спец.2_пристос..cdw

Рекомендуемые чертежи
- 20.06.2022
- 24.01.2023
- 02.04.2024
- 24.01.2023
Свободное скачивание на сегодня
- 22.08.2014
- 29.08.2014