Разработка технологического процесса получения отливки Диск верхний ХМ 09.22.300А специальным способом литья




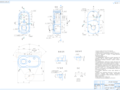
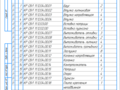
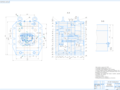
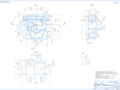
- Добавлен: 25.01.2023
- Размер: 1 MB
- Закачек: 1
Описание
Разработка технологического процесса получения отливки Диск верхний ХМ 09.22.300А специальным способом литья
Состав проекта
![]() |
![]() |
![]() |
![]() ![]() ![]() ![]() |
![]() ![]() ![]() ![]() |
![]() ![]() ![]() ![]() |
![]() ![]() ![]() ![]() |
![]() ![]() ![]() ![]() |
![]() |
![]() ![]() ![]() |
![]() ![]() ![]() |
![]() ![]() ![]() |
![]() ![]() ![]() |
![]() ![]() ![]() |
![]() ![]() ![]() |
![]() ![]() ![]() |
![]() ![]() |
![]() ![]() ![]() |
![]() ![]() ![]() |
![]() ![]() ![]() |
Дополнительная информация
Деталь.cdw

Форма в сборе.cdw

Вставка пуансон.cdw

Спецификация.spw

Вставка матрица.cdw

Рекомендуемые чертежи
- 25.01.2023
Свободное скачивание на сегодня
Другие проекты
- 03.07.2014