Разработка технических требований и определение основных параметров роботов (для захвата детали типа вал)




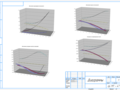

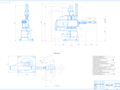
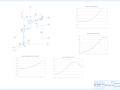
- Добавлен: 24.01.2023
- Размер: 543 KB
- Закачек: 0
Описание
Состав проекта
![]() |
![]() ![]() ![]() |
![]() ![]() ![]() ![]() |
![]() |
![]() |
![]() |
![]() |
![]() |
![]() ![]() ![]() ![]() |
![]() ![]() ![]() ![]() |
![]() ![]() ![]() ![]() |
Дополнительная информация
Разработка технических требований и определение основных параметров роботов.doc
Кинематика манипулятора 5
Список использованной литературы
В современном автоматизированном производстве мехатроника объединят автоматизацию планирования и управления предприятием промышленную автоматику и робототехнику автоматизацию транспортных и диспетчерских служб. Мехатронные системы предназначены для автоматизации сложных технологических процессов и операций в том числе выполняемых в недетерменированых условиях для замены человека при выполнении тяжелых и опасных работ.
Мехатронная функция – интегральная функция всех агрегатов и составляющих компонентов системы машин задействованных в каком-либо производственном процессе комплексе; включает перемещение в пространстве и выполнение работ операций энергообеспечение связь безопасность управление контроль управления эксплутационное обслуживание реновацию утилизацию отходов.
Разработка технических требований и определение
основных параметров роботов (манипуляторов)
Расчет захватного устройства.
Для детали типа вал выбираем захватное устройство с рычажно-стержневым механизмом.
Схема захватного устройства.
Р1- сила требуемая для удержания объекта манипулирования Р2 - сила развиваемая приводом схвата.
Р2 можно рассчитать по формуле [таблица 13.6[1]]:
P2 = 2 P1 b c e (d + c)
Где Р1 рассчитаем по формуле ([1]стр.334):
g-ускорение свободного падения (g=9.8 мс2)
k1-коэфициент запаса (k1=12 2);
k2-коэфициент зависящий от ускорения схвата
k2 = 1+ag (обычно а4мс2)
Кз - коэффициент зависящий от отношения усилия зажима к весу детали определяется по таблице 13.5[1]
Кз = tg ( Q 2) + (a 2 b)
Где Q = 120 a = 45 мм b = 65мм
Кз = tg (120 2) + (45 2 65) = 17
Выбираем коэффициенты равными:
К2 = 1 + 4 9.81 = 14
Массу детали определяем в компасе для стали сталь45 ГОСТ1050-88
M = 153 гр. Округлим m = 160 гр.
Подставим полученные коэффициенты в формулу
Р1=m g k1 k2 k3 = 016 98 2 14 17 = 75 Н
Определим силу Р2 развиваемая приводом схвата.
P2 = 2 P1 b c e (d + c) = 2 75 65 10 15 (20 + 10) = 22 Н
Исходя из полученных данных выбираем линейный электрический
Шаговый привод 5Г28 – 2 типоразмер Г28-23. ( табл.1стр.37)
Кинематика манипулятора.
Кинематическая схема манипулятора имеет вид ВПП:
А - модуль поворота манипулятора
В - модуль подъема – опускания руки
С - модуль вдвижения - выдвижения схвата
Выбираем для манипулятора цилиндрическую систему координат
определим траекторию скорость и ускорение движения захвата при
известных законах движения приводов отдельных степеней свободы.
Вычерчиваем кинематическую схему манипулятора и во всех
кинематических парах показываем системы координат.
Составим уравнение в координатной форме:
x = x3 cos q1 – y3 sin q1 – l2y sin q1
y = x3 sin q1 – y3 cos q1 + l2y cos q1
Для точки D захвата x3 = 0 y3 = q3 z3 = 0. В результате получим
x = - ( q3 + l2y ) sinq1
y = ( q3 + l2y ) cosq1
Для данной схемы механизма выбираем равноускоренный закон движения
звеньев манипулятора.
q = Кз t² где Кз = qn tn²
tn – время позиционирования ( 10 секунд )
qn - время выполнения определенной операции
Значения обобщенных координат:
qп1= П2; qП2=1.1м; qП3=0.2м; q1=П q2=0.011 q3=0.002t2.
Подставляя полученные значения обобщенных координат в уравнения координат точки D в неподвижной системе координат получим:
х=0.011t2*s y=0.011t2*cos(Пt2200); z=-0.002t2+0.4
Уравнение траектории точки D имеет вид:
По данным уравнениям строим диаграммы изменения координат и абсолютного перемещения точки D по времени.
Таблица 1. Значения координат и абсолютного перемещения точки звена D.
Построение производим с помощью компьютера в программном пакете Excel. Дальнейшее построение графиков (диаграмм) изменения координат скорости ускорения и погрешности позиционирования и их абсолютных значений по времени ведем с помощью того же программного пакета.
Дальнейшим шагом является определение скорости точки D захватного устройства. Для этого находим первые производные от координат по времени (x’ y’ z’) или проекции абсолютной скорости:
x'=-0.022t*sin(Пt2200)-0.00011Пt3*cos(Пt2200)
y'=0.022t*cos(Пt2200)-0.00011Пt3*sin(Пt2200)
Абсолютная скорость:
По данным уравнениям строим диаграммы изменения x’ y’ z’ от времени и диаграмму изменения абсолютной скорости V(t) точки D схвата.
Таблица 2. Значение абсолютной скорости точки звена D и её проекций.
Следующий шаг-определение ускорения точки D. Для этого находим вторые производные от координат по времени (x''y''z'') т.е. проекции абсолютного ускорения.
x''=-0.022*sin(Пt2200)-0.00022*Пt2*cos(Пt2200)-0.00033*Пt2*cos(Пt2200)+0.0000011Пt4*sin(Пt2200)
y''=0.022cos(Пt2200)-0.00022Пt2*sin(Пt2200)-
00033Пt2*cos(Пt2200)-0.0000011Пt4*cos(Пt2200)
Абсолютное ускорение:
А=√(x''2+y''2+z''2)
По данным уравнениям строим диаграммы изменения проекций ускорения и абсолютного ускорения по времени.
Таблица 3. Значение абсолютного ускорения точки D и его проекций.
Определяем погрешности позиционирования.
Принимаем что погрешность отработки отдельных приводов манипулятора составляет 01% от полного перемещения соответствующего звена.
Для данной кинематической схемы погрешности позиционирования точки D рабочего органа манипулятора определяются следующими выражениями:
Dx=x+z*y=11*0001+0001*(П2)*y
Dy=y–z*y=11*0001–0001*(П2)*y
Полная погрешность позиционирования точки D рабочего органа манипулятора: ΔD=√ Dx2+Dy2+Dz2
По данным уравнениям строим диаграммы изменения погрешности позиционирования точки D рабочего органа манипулятора.
Таблица 4. Погрешности позиционирования точки D рабочего органа манипулятора.
Моделирование динамики осуществляем с помощью уравнений Лагранжа 2-города:
Полная кинетическая энергия ИУ:
Тогда полная кинетическая энергия Т получится:
T=12[(I+mb*l*q3+mb*q32)*q12+mr*q22+mb*q32]
Частные производные от Т по обобщенной координате и скоростям.
Обобщенные силы Q выразим через силы развиваемые приводами:
Все полученные формулы подставляем в уравнение Лагранжа и находим числовые значения F3
Исходные данные: статическое усилие на исполнительном звене модуля Fn=50H; диапазон перемещения выходного звена 02 м; номинальная скорость 035 мс; номинальная масса 2 кг.
Номинальную массу исполнительного звена принимаем равной
mn=(mнд+1.5mнд)=5кг.
Выбор типа электродвигателя:
Принимаем коэффициент запаса равным 19 и общий КПД модуля 085.
Ориентировочное значение мощности электродвигателя: Р=39.12Вт
В качестве приводного двигателя принимаем высокомоментный электродвигатель постоянного тока ДК135.
Общее передаточное отношение 299.14м-1
Кинематическая цепь модуля состоит из пары зубчатых конических колес и передачи винт-гайка скольжения. Распределим передаточное отношение по узлам модуля:
Примем число зубьев колес равным между собой что обеспечит передаточное отношение равным единице. Тогда передаточное отношение передачи винт-гайка будет равным:
Uвг=Uоб*Uзп=299.141=299.14м-1
Определим шаг винта принимая число заходов винта z=1:
P=2П*Uвг=2П*299.14=0.021м
Принимаем шаг винта равным 20 мм из ряда часто используемых (стр50[5]).
Крутящий момент на валу двигателя:
Проектный расчет модуля
Исходя из того что винт передачи испытывает напряжение растяжения его диаметр можно определить по формуле:
где s-коэффициент запаса прочности.
Ввиду того что винт полый принимаем S=4.
Подставим полученные значения в формулу для определения наименьшего диаметра винта:
Принимаем диаметр винта равным 70 мм. Наружный диаметр гайки исходя из условия обеспечения прочности резьбы принимаем равным 90 мм (ориентировочно).
Средний диаметр конического зубчатого колеса принимаем равным наружному диаметру гайки.
Углы делительных конусов принимаем равными 45º.
Динамический расчет.
Расчет моментов инерции.
Полный момент инерции приведенный к валу электродвигателя:
IД определяем по таблице 3[6стр 30]
Так как кинематическая цепь модуля состоит из двух конических зубчатых колес и передачи винт-гайка угловые перемещения совершают конические колеса и гайка которая выполнена заодно с одним из колес.
При расчете момента инерции колеса-гайки колесо будем рассматривать как полый цилиндр имеющий размеры: внутренний и наружный диаметры гайки и высоту равную 0.25Нг
Нг примем равной 15 Dг
Толщина колеса ориентировочно: В=135*025=34 мм.
Высота полого цилиндра: Н=169 мм.
Второе колесо будем рассматривать как сплошной круглый цилиндр высотой 34 мм и диаметром равным 90 мм.
где d1-диаметр отверстия; d2-наружный диаметр.
V=П(R2-r2)h=П(452-352)*169=425см2
Iкг=338*(007*2+009*2)=54*10-3 кг*м2
Iк=md28=17*009 28=17*10-3 кг*м2
mк=ПR2h=П*452*34*785=17кг
В формуле для определения инерции механических элементов кинематической цепи: mпост=mн+mв;
Принимаем диаметр отверстия в винте равным 40 мм так как в нем располагается тяга для приведения в действие схвата.
mв=П(R2-r2)h=П(352-22)40*785=81 кг
Общий момент инерции механических элементов кинематической цепи модуля:
Iмэ=Ir1+Iкг1+mпостU2общ=7.3*10-3 кг*м2
Общий момент инерциии приведенный к валу двигателя:
I=Iд+Iмэ+mнU2общqобщ=2.45*10-3+7.3*10-3+5.0 299.1420.85=9.82*10-3кг*м2
Определяем общий крутящий момент на валу двигателя:
Тд=Тдст+Тдин=(0.19+0.28)Нм=0.47Нм
Динамический крутящий момент:
Общий крутящий момент на валу электродвигателя необходимый для работы модуля меньше номинального момента двигателя ДК1-3.5.Поэтому оставляем этот двигатель.
Модуль В состоит из двух зубчатых колес и передачи винт-гайка скольжения.
Нагрузка на модуль В определяется массой модуля С максимальным ускорением звеньев модуля В их скоростью и статическим усилием Fн.
mс=mн+mв+mд+mк+mкг=5+81+182+17+33=363 кг.
Исходные данные: статическое усилие на исполнительном звене модуля Fн=300Н диапазон перемещений выходного звена qнmax=11м номинальная скорость q'н=035мс номинальная масса 363 кг.
Выбор типа электродвигателя.
Примем коэффициент запаса равным 1.9 (стр. 39[5]) общий КПД модуля равный 085.
Ориентировочное значение мощности двигателя:
В качестве приводного двигателя примем высокомоментный двигатель постоянного тока ДК1-3.5имеющий
Рд=0.35кВт; nд=1000обмин; mдв=18.2кг.
Пnд30=3.14*100030=104.7радс
Кинематический расчет.
Общее передаточное отношение:
Uобщ=104.7:0.35=299.14м-1
Кинематическая цепь модуля состоит из пары зубчатых колес и передачи винт-гайка скольжения. Распределим передаточное отношение по узлам модуля:
примем числа зубьев колес равными между собой что обеспечивает пере-
даточное отношение равное единице. Тогда передаточное отношение передачи винт-гайка будет равным:
Uвг=UобщUp=299.141=299.14м-1
Определим шаг винта при числе заходов z=1:
Р=2ПU=2*3.14299.14=0.021м.
Принимаем шаг винта из ряда наиболее используемых (стр 50[5]):р=20мм
Рдст=1*0.02*300*104.72*3.14*0.85=117.6Вт
Крутящий момент на валу двигателя:
Тдст=Рдст=117.6104.7=1.12Нм
Ориентировочный расчет узлов модуля:
Исполнительное звено (винт-рука) модуля В испытывает напряжение изгиба. В наиболее опасном сечении винт-рука имеет квадратное сечение со стороной а. Размер а можно определить по формуле:
Примем сторону а=30мм.
Наружный диаметр винта примем равным стороне квадрата а из условия прохождения винта в отверстие люнетной втулки.
Гайка выполняется в виде полого цилиндра с одной стороны глухо закрытого стенкой которая выполняется для закрепления одного зубчатого колеса на гайке.
Длина винтовой части руки манипулятора ориентировочно равна 600мм
Общая длина руки ориентировочно 1700мм.
Динамический расчет модуля В.
где m пост-масса поступательно движущегося звена модуля в которое входит так же модуль С. mc=36.6кг
Масса руки-винта манипулятора.
V1=ПR21 h1=3.14*1.52*60=424.12см3V2=a2l2=32*74=666см3
V3=bhl3=25*3*11=825см3 V4=ПR2 h4=33.14*5.52*17=1615.6см3 Vотв=ПR2отв hотв=3.14*4.5215=954.26см3 V=2576.46см3
m=2576.46*7.85=20.2кг mпост=m+mс=56.5кг
V=2576.46см3 m=2576.46*7.85=20.2кг mпост=m+mс=56.5кг
Расчет моментов инерции кинематической цепи модуля.
Момент инерции гайки как полого цилиндра выполненного в виде гильзы можно представить как сумму момента инерции полого цилиндра и момента инерции стенки.
Наружный диаметр гайки ориентировочно примем равным 50мм исходя из условий прочности. Толщину стенки примем равной 20мм из условий ввертывания в нее крепежных деталей.
Моменты инерции зубчатых колес будут равны между собой так как равны их диаметры и будут определяться по формуле:
Учитывая габаритные размеры электродвигателя и корпуса модуля В ориентировочно примем диаметры колес равными 100мм.Толщину колес так же примем ориентировочно В=15мм.Тогда масса колес будет равна mк=0.93кг.
Момент инерции каждого колеса:
Iк=0.93*0.018=1.2*10-3кг*м2
Iобщ=8.08*10-3кгм2; I=8.56кгм2
Определим общий крутящий момент приведенный к валу двигателя:
Тд=Тст+Тдин=1.12+0.24=1.36Нм
Динамический крутящий момент равен 0.24Нм
К модулю А приложена нагрузка включающая в себя массу двух предыдущих модулей и массу деталей не вошедших в расчет этих модулей. Поэтому массу нагрузки на модуль А рассчитывают ориентировочно
m=mс+mв=(mс+mрв+mпц+mст+2mк)+mдет
где mдет-масса деталей не вошедших в расчет модулей. Примем эту массу как 1.5mмгде mм=mс+mв=28.87+36.3=64.57кг
Тогда получим массу нагрузки на модуль А: mн=mс+mв+15mм=16143кг
Для определения приведенного момента инерции нагрузки Iн построим эквивалентную схему промышленного робота:
-модуль С с захватным устройством
(рассматриваем как поворачиваемый груз)
Момент инерции нагрузки:
I1=mr2=363*112=4392 кг*м2
I2=m3(r12-r1r2+r22)=9.15кг*м2
I3=md28=35*0.228=0.175кг*м2
Предварительный выбор электродвигателя:
Примем коэффициент запаса равным 2.5 (стр. 39 [5]) и общий КПД равный 0.85.
Ориентировочное значение мощности электродвигателя:
По таблице 4 стр29 [6] в качестве приводного двигателя выбираем электродвигатель постоянного тока серии 3SHAT-A тип 112L у которого номинальная мощность–86 кВт номинальный момент-42 Нм; номинальная частота вращения-2000 обмин; момент инерции–3*10-2 кг*м угловая скорость двигателя-20944 радс.
Общее передаточное отношение
Модуль поворота состоит из червячной передачи поэтому передаточное отношение ее равно общему передаточному отношению всего модуля. Принимаем передаточное отношение передачи Uп=134
Расчетный вращающий момент на выходном валу модуля:
Проектный расчет передачи.
Методика расчета изложена в §9[4]
По рекомендациям §9.1[4] принимаем z1=1; z2=z1*U=134
Определяем Т1=Р1 Uп =8.6*103209.44=41.1 Нм
Т2=Т1U =41.1*134*0.85=4405.92 Нм
В первом приближении оцениваем скорость скольжения (стр. 211[4])
V3=45*10-4*n T2=1475 мс
По рекомендации §9.7 и таблицы9.4[4] назначаем материал колеса
БрАЖ9-4 ;червяк-сталь 40Х
По рекомендации (стр. 201[4]) примем q=34
По формуле (9.20)[4] при Епр=1.26*105МПа
По ряду Rа примем аw=300 мм.
По формуле (9.3)[4] определяем модуль m=3.57мм
принимаем модуль равный 4мм по рекомендациям на стр 201[4].
Определим основные размеры червяка и колеса:
dа1=d1+2m=144мм;dа2=d2+2m=544мм
Ширина колеса по рекомендациям на стр 202[4]
Длину червяка ориентировочно принимаем равной диаметру червячного колеса 544мм
Полный момент инерции конструктивного модуля:
Полный момент на валу двигателя:
Расчитаное значение момента на валу двигателя не превышает значение номинального момента на валу двигателя. Это говорит о том что двигатель подобран правильно.
Данные расчеты модулей приведены для тех случаев когда в движении находится один из модулей а другие два находятся в статическом состоянии.
В результате работы получен робот манипулятор для транспортировки деталей призматической формы на металлорежущий станок установки детали в приспособление станка съем готовой детали после обработки и транспортировка ее в приемное устройство. Так как станок полностью автоматизирован применение робота манипулятора позволяет практически исключить человеческий труд на выполняемой операции.
Это в свою очередь позволит повысить эффективность производства его производительность качество. А также это позволит снизить издержки производства а следовательно и себестоимость детали что в свою очередь повлечет за собой снижение себестоимости изделия в целом.
Список используемой литературы.
Кочергин А.И. Конструирование и расчет металлорежущих станков станочных комплексов. Курсовое проектирование: Учебное пособие для ВУЗов.-Минск.:Высшая школа.1991-382с.
Кинематика манипуляторов: Методические указания.
Мясников В.К.:ЯГТУ.-Ярославль.1997-32с.
Мясников В.К.:Расчет электромеханических модулей промышленных роботов: Учебное пособие. - Ярославль ЯПИ. 1984-92с.
Иванов М.Н.: Детали машин: Учебник для студентов высших технических учебных заведений.-5-е издание переработанное. -Москва: высшая школа1991-383с.
Мясников В.К. Основы построения мехатронных систем автоматизации: Учебное пособие.-ЯрославльЯГТУ1997-66с.
Промышленные роботы в машиностроении: Альбом схем чертежей: Учебное пособие для технических ВУЗов.-Москва Машиностроение1986-140с.
Мясников В.К. Тимошкин Л.А. -Проектирование механизмов автоматических манипуляторов: Учебное пособие. Ярославль
А3 Диаграммы.cdw

Кинематическая схема, графики.cdw

Алгоритм работы, погрузка-выгрузка детали А1.cdw

выдерживая указанные размеры.
Шероховатость поверхности Ra = 2
Закрепление заготовки
Промышленный робот М20П.40.01 А1.cdw

Число степеней подвижности 3
Наибольшие линейные перемещения
по вертикальной оси 300
по горизонтальной оси 300
Наибольшее угловое перемещение
руки относительно вертикальной оси 180
Диапазон скорости линейных перемещений
по вертикальной оси 0
по горизонтальной оси 0
Диапазон скорости угловых перемещений
руки относительно вертикальной оси . 60
Наибольшая абсолютная ошибка позиционирования
Усилие зажима схвата
Время зажима - разжима
захватываемых деталей
по наружному диаметру
Масса (без устройства ЧПУ
Рекомендуемые чертежи
- 24.09.2024
- 25.01.2023
- 20.12.2023