Разработка техкарты на изготовление зубчатой обоймы муфты типа М3. + чертежи


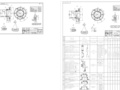
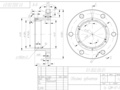
- Добавлен: 24.01.2023
- Размер: 644 KB
- Закачек: 1
Узнать, как скачать этот материал
Подписаться на ежедневные обновления каталога:
Описание
Разработка техкарты на изготовление зубчатой обоймы муфты типа М3. + чертежи
Состав проекта
![]() |
![]() ![]() ![]() |
![]() ![]() ![]() ![]() |
![]() ![]() ![]() ![]() |
Дополнительная информация
Контент чертежей
Моя тех карта3.doc
Разработать маршрутную технологию ремонта деталей
обшивки и капота трактора ДТ-75.
1.Описание конструкции деталей ..3
2.Составление дефектной ведомости .. ..4
3.Разработка маршрутной технологии ремонта . ..4
3.1.Способы восстановления дефектов ..4
3.2.Оборудование необходимое для восстановления дефектов ..5
3.3.Маршрутная карта ремонта деталей . . ..5
Разработать технологическую карту на изготовление зубчатой обоймы муфты типа МЗ.
1.Технологический расчет ..6
1. Выбор заготовки. .6
2.1. Заготовительная операция. (Отрезание заготовки
необходимого размера.) . .7
1.2.Токарная операция. (Обрабатываются наружные поверхности) .7
1.3.Слесарная операция. .. .25
1.4.Зубодолбежная операция ..32
1.5.Термическая обработка. (Закалка и отпуск) ..34
1.6.Зубохонинговальная операция .. . .. ..34
1.7.Контрольная операция.(контролируют все размеры
изготовленной детали). ..34
Расчет и проектирование нестандартного оборудования
1. Расчет механизма подъема 35
Список литературы 40
РАЗРАБОТКА ТЕХНОЛОГИЧЕСКОЙ ЛИНИИ ПО РЕМОНТУ УЗЛОВ И АГРЕГАТОВ.
Задание: необходимо разработать маршрутную технологию ремонта деталей обшивки и капота трактора ДТ-75. (рис. 1).
1.Описание конструкции деталей
Деталь 22 боковина верхнего капота.
Правая и левая боковины верхнего капота шарнирно навешаны на петлях 23 которые могут удерживать боковины в поднятом положении для удобства обслуживания двигателя. На концах боковин верхнего щита имеются защелки 2 плотно притягивающие боковины в опущенном положении к верхнему бачку радиатора и заднему листу капота.
Деталь 4 боковой лист.
Быстросъемный боковой лист установлен между передним листом обшивки и верхним щитом капота.
Деталь 1 облицовка радиатора.
2.Составление дефектной ведомости
Разрыв отверстия крепления
отверстия крепления
Боковина верхнего капота
3.Разработка маршрутной технологии ремонта
3.1.Способы восстановления дефектов
Способ восстановления
-подготовка к покраске;
-зачистка очага коррозии;
-обработка антикоррозийным покрытием.
-засверливание основания трещины;
-вырезание накладки;
-высверливание отверстия.
-метчиком нарезается новая резьба;
-постановка ремонтного болта.
Развальцовка отверстия крепления
- высверливание отверстия.
3.2.Оборудование необходимое для восстановления дефектов
Оборудование необходимое для восстановления дефектов
-вертикально-сверлильный станок;
-обдирочно-шлифовальный станок.
-обдирочно-шлифовальный станок;
-покрасочное оборудование.
-шлифовальный станок;
-вертикально-сверлильный станок.
-токарно-винторезный станок.
- вертикально-сверлильный станок.
3.3.Маршрутная карта ремонта деталей
Боковина верхнего капота:
Правка деформированной боковины;
Подготовка к покраске;
Устранение коррозии;
Обработка антикоррозийным покрытием;
Облицовка радиатора:
Сварка разрыва крепления отверстия;
Приваривание накладки;
Высверливание отверстия;
ТЕХНОЛОГИЧЕСКАЯ ЧАСТЬ
Расчет минимального общего припуска на обработку.
Zmin=Ti-1+Rzi-1+ri-1=150+200+0=350мкм
где: Ti-1-толщина дефектного слоя (перенаклеп трещины прижоги ) оставшиеся с предшетствующего перехода мкм.
Rzi-1-высота микронеровностей оставшихся с предшедствующего перехода мкм.
ri-1-погрешность формы заготовки (коробление изогнутость несоосность) мкм.
Наибольший диаметр детали является 220мм.
Принимая во внимание стандартный ряд круглого проката и учитывая качество отделки поверхности горячего проката применяем в качестве заготовки с учетом припуска на обработку выбираем диаметр 230 мм с допустимым отклонением по диаметру мм.
Определяем длину отрезаемой заготовки с учётом припуска:
Z0 – расчетный минимальный припуск на обработку по длине мм.
Операцию отрезания заготовки проводим на ленточно-отрезном станке 8544.
Минимальный припуск [Косилова 4 – 1]:
где: Rz – высота неровностей профиля [Косилова 1 4 - 3 табл];
h – глубина дефектного поверхностного слоя на предшествующем переходе [Косилова 4 - 3 табл];
DSк – допуск размера длины детали по 14 квалитету [Косилова 1 4 - 3 табл; Анурьев 1 стр. 357 табл. 1];
2Расчёт режимов механической обработки
Маршрутная технология
I. Заготовительная операция.
II. Токарная операция.
III. Слесарная операция.
IV. Зубодолбежная операция.
V. Термическая обработка.
VI. Зубохонинговальная операция.
VII. Контрольная операция.
Метод выполнения заготовок для деталей машин определяется назначением и конструкцией детали материалом техническими требованиями а также экономичностью изготовления. Для изготовления штучных деталей предпочтительно использовать горячекатаную сталь так как она имеет сравнительно низкую стоимость чем другие виды заготовок. К тому же этот вид проката представлен широким диапазоном используемых сталей.
Переход А. Установить снять заготовку.
Отрезать заготовку d=230 мм и длиной l=69 мм.
Отрезать заготовку длиной L = 69 мм.
Глубина резания: t = 235 мм.
Число проходов: i = 1.
Подача: S = 30 мммин.
Скорость резания: V = 15 ммин
Вспомогательное время: Tвсп = 76·2=152 мин.
Для токарной операции выбираем токарно-винторезный станок 16К20.
Подрезать торец на 230 на глубину 1 мм.
Глубина резания t=1 мм. Припуск на данном участке снимаем за 1 проход (i=1).
Обработку ведём подрезным резном; материал резца Т15К6 [Косилова т.2 стр. 116].
Расчет длины рабочего хода суппорта:
где Lр.х – длина рабочего хода;
Lрез – длина резания;
y – величина подвода врезания и перебега инструмента (φ0 = 45 град.) [Гестрин прил. 1].;
Подача: S = 04 ммоб (принимаем по: Косилова т.2 стр.266 ).
Среднее значение периода стойкости Т при одноинструментальной обработке 30-60 мин.
а) Расчёт скорости резания [Гестрин стр. 63].
T – средняя стойкость инструмента;
t – глубина резания;
Kv – произведение коэффициентов:
- коэффициент учитывающий качество обрабатываемого материала (Кг – коэффициент характеризующий группу стали по обрабатвыаемости);
- коэффициент учитывающий качество поверхности;
- коэффициент учитывающий качество материала инструмента.
б) Расчёт рекомендуемого числа оборотов шпинделя станка
в) Уточнение числа оборотов шпинделя (паспорт станка)
Принимаем n=200 обмин.
г) Уточнение скорости резания по принятому числу оборотов.
Расчёт основного машинного времени обработки tм мин (при работе с различными подачами машинное время суммируется по участкам)
Расчёт вспомогательного времени:
Тв= tм к = 152= 3мин где
к - коэффициент зависящий от вида обработки.
Проточить с 230 до 220 h14 на L=20 мм.
Глубина резания t=4505 мм. Припуск на данном участке снимаем за 11 проходов (i=11).
Выбираем проходной резец для обтачивания гладких цилиндрических и конических поверхностей; материал резца Т15К6 [Косилова т.2 стр. 116].
Подача: S = 0401 ммоб (принимаем по: Косилова т.2 стр.266 ).
1 а) Расчёт скорости резания [Гестрин стр. 63] при S = 04:
Принимаем n=160 обмин.
2 а) Расчёт скорости резания [Гестрин стр. 63] при S = 01:
Принимаем n=630 обмин.
Тв= tм к = 082= 16мин где
Снять фаску 2х45º с 220 мм.
Глубина резания t=14 мм. Припуск на данном участке снимаем за 1 проход (i=1).
Подача: S = 08 ммоб (принимаем по: Косилова т.2 стр.266 ).
Тв= tм к = 0042= 008мин где
Переход Б. Переустановить деталь.
Подрезать торец на 230 на глубину 1 мм контролируя размер 67 мм.
Просверлить отверстие 10 на L=67 мм.
Инструмент – сверло 10 мм из твердого сплава ВК8.
Число проходов i =1.
Подача: S = 015 ммоб (принимаем по: Косилова т.2 стр.277 ).
Среднее значение периода стойкости Т при одноинструментальной обработке Т=25 мин. (принимаем по: Косилова т.2 стр.279 ).
а) Расчёт скорости резания
- коэффициент учитывающий качество материала инструмента;
- коэффициент учитывающий глубину сверления.
б) Расчёт рекомендуемого числа оборотов шпиндельного станка
Принимаем n=125 обмин.
Рассверлить отверстие 10 до 60 на L=67 мм.
Инструмент – сверло 60 мм из твердого сплава ВК8.
Подача: S = 02 ммоб (принимаем по: Косилова т.2 стр.277 ).
Среднее значение периода стойкости Т при одноинструментальной обработке Т=110 мин. (принимаем по: Косилова т.2 стр.279 ).
Принимаем n=40 обмин.
Расточить с 60 до 1152 H8 на L=67 мм.
Глубина резания t=43402 мм. Припуск на данном участке снимаем за 611 проходов (i=611).
Выбираем расточной резец для растачивания сквозных отверстий; материал резца Т15К6 [Косилова т.2 стр. 116].
Подача: S = 030301 ммоб (принимаем по: Косилова т.2 стр.266 ).
1 а) Расчёт скорости резания [Гестрин стр. 63] при S = 03 и t=4:
Принимаем n=315 обмин.
2 а) Расчёт скорости резания [Гестрин стр. 63] при S = 03 и t=34:
3 а) Расчёт скорости резания [Гестрин стр. 63] при S = 01 и t=02:
Принимаем n=1000 обмин.
Тв= tм к = 6042= 1208мин где
Расточить с 1152 до 127 H14 на L=2 мм.
Глубина резания t=5405 мм. Припуск на данном участке снимаем за 11 проходов (i=11).
Выбираем расточной упорный резец для растачивания глухих отверстий; материал резца Т15К6 [Косилова т.2 стр. 116].
Подача: S = 0301 ммоб (принимаем по: Косилова т.2 стр.266 ).
1 а) Расчёт скорости резания [Гестрин стр. 63] при S = 03:
Тв= tм к = 012= 02мин где
Проточить с 230 до 145 h14 на L=47 мм.
Глубина резания t=605 мм. Припуск на данном участке снимаем за 71 проходов (i=71).
Тв= tм к = 9792= 1958мин где
Переход В. Переустановить деталь.
Расточить с 1152 до 127 H14 на L=40 мм.
Тв= tм к = 0922= 184 мин где
Выбираем радиально-сверлильный станок 2А135.
Сверлить 6 отверстий 17 на R925 с угла 30º на глубину L=20 мм с шагом 60º.
Инструмент – сверло 17 мм из твердого сплава ВК8.
Среднее значение периода стойкости Т при одноинструментальной обработке Т=45 мин. (принимаем по: Косилова т.2 стр.279 ).
Принимаем n=100 обмин.
Снять фаску 1х45º с 17 с обоих сторон операцию повторить 5 раз.
Инструмент – зенковка сплава ВК8.
Среднее значение периода стойкости Т при одноинструментальной обработке Т=30 мин. (принимаем по: Косилова т.2 стр.279 ).
Принимаем n=400 обмин.
Сверлить 6 отверстий 5 на R675 на глубину L=14 мм с шагом 60º.
Инструмент – сверло 5 мм из твердого сплава ВК8.
Принимаем n=195 обмин.
Нарезать резьбу М6 метчиком №1 операцию повторить 5 раз.
Инструмент – метчик М6 №1.
Подача равна шагу резьбы: S=P=075ммоб.
Рекомендуемое число оборотов n=10 обмин.
Скорость резания по принятому числу оборотов:
Расчёт основного машинного времени обработки tм мин:
Нарезать резьбу М6 метчиком №2 операцию повторить 5 раз.
Инструмент – метчик М6 №2.
Сверлить отверстие 7 в торце 220 на расстоянии L=10 мм от края на глубину 465 мм.
Инструмент – сверло 7 мм из твердого сплава ВК8.
Подача: S = 012 ммоб (принимаем по: Косилова т.2 стр.277 ).
Зенкеровать отверстие 14 на глубину 15 мм.
Инструмент – зенкер 14 сплава ВК8.
Нарезать резьбу М8 метчиком №1.
Инструмент – метчик М8 №1.
Подача равна шагу резьбы: S=P=1ммоб.
Нарезать резьбу М8 метчиком №2.
Инструмент – метчик М8 №2.
Нарезать зубья внутреннего зацепления на 120 m=3 и z=40.
Зубодолбежный полуавтоматический станок 5140.
Зуборезный долбяк: номинальный диаметр 80 мм m=3 и z=40.
) Расчет длины рабочего хода:
- длина резания равная ширине венца.
) Назначение круговой подачи на двойной ход долбяка (ммдв. ход) (карта З-2):
а) определение рекомендуемой подачи. Для стали марки 40ХН подача будет определяться:
б) уточнение подачи по паспорту станка (ммдв. ход):
) Расчет скорости резания V (ммин) и числа двойных ходов долбяка (дв.хмин):
а) определение рекомендуемой скорости резания (карта З-2) V=25 ммин.
б) расчет (дв.хмин):
в) уточнение . По паспорту (дв.хмин).
г) уточнение V (ммин) по принятому значению (дв.хмин):
) Расчет машинного времени мин:
где: - припуск на обработку по межцентровому расстоянию или высота зуба;
- радиальная подача врезания;
- принятое число двойных ходов;
- принятая величина круговой подачи;
V. Термическая операция.
Для достижения высокой поверхностной твёрдости деталь необходимо закалить с нагревом в высокочастотной нагревательной установке ТВЧ с глубиной закалённого слоя 18-22 мм. Для конструкционной стали 40ХН температура закалки составляет 800º что на 30º выше критической точки Ac3.
Переход 1. Производим закалку детали в высокочастотной установке с нагревом до 800о выдержкой при этой температуре 05 часа с последующим охлаждением в масле.
Переход 2. Производим средний отпуск детали в том же индукторе при t=180-250 о выдерживая при этой температуре 1-15 часа и медленно охлаждая на воздухе.
Твердость при этом составит НВ=290-300.
VI. Зубохонинговальная.
Зубохонингование применяют для чистовой отделки закаленных цилиндрических колес внутреннего зацепления. Хонингование осуществляется на хонинговальном станке 5А915. Закаленное обрабатываемое колесо вращается в плотном зацеплении с абразивным зубчатым хоном при угле скрещивания осей 10-15º. Поджим детали к хону осуществляется пружиной с силой 150-450 Н. Зубчатое колесо кроме вращения совершает возвратно-поступательное движение вдоль оси. Направление вращения инструмента меняется при каждом ходе стола. Припуск под хонингование не оставляют. Частота вращения хона 180-200 обмин подача стола 180-210 мммин число ходов стола четыре – шесть. Время хонингования зубчатого колеса 30-60 секунд.
Контрольная операция включает в себя следующее:
- контроль всех размеров согласно чертежу;
- контроль твердости;
- контроль шероховатости;
- контроль радиального биения.
В качестве оборудования для измерения радиального биения используем биениемер Б-10М ГОСТ 5368-81.
Для контроля шероховатости используем профилограф-профилометр А1 ГОСТ 19299-73.
Для измерения размеров используем:
- штангенциркуль ШЦ-2-250-01 ГОСТ 166-80
- нутромер НИ 100-160 ГОСТ 9244-75
- микрометр МК 150-250 ГОСТ 6507-78.
РАСЧЕТ И ПРОЕКТИРОВАНИЕ НЕСТАНДАРТНОГО ОБОРУДОВАНИЯ
Задание: разработать проект электрокара с поворотным краном и подъемной платформой для внутрицеховой перевозки узлов и деталей.
Грузоподъемность – 05 т.
Максимальная скорость перемещения с грузом – 10 кмч.
Эскизное конструктивное решение представлено рис. 1.
Рис. 1. Электрокар с поворотным краном и подъемной платформой: 1- ручка для подъема платформы; 2 – ручка для подъема груза.
1Расчет механизма подъема груза.
В технологическом оборудовании автотранспортных предприятий и станций технического обслуживания при малой грузоподъемности и невысоких скоростях продвижения широко применяется ручной привод. С ручным приводом могут применяться механизмы подъема поворота передвижения опрокидывания а также в приспособлениях для создания технологического усилия (прессы съемники). Ручной привод применяется при редкой и непродолжительной работе и при невозможности использовать другой вид привода. Ручной привод осуществляется рукоятками тяговыми колесами трещотками для которых рекомендуются следующие размеры.
Плечо (радиус) рукоятки R = (01 04) * M предпочтительно 03 * М (плечо рукояток домкратов (02 025) * М). Длина ручки рукоятки (03 035) * М для одного рабочего и (045 050) * М - для двух. Высота вала рукоятки от уровня пола (09 110) * М от середины ручки рукоятки стенной лебедки до стены - не менее 25 М. Радиус R тягового колеса принимается (01 05) * М тяговая цепь изготавливается из круглого стального проката диаметром 5 6 мм. Расстояние от уровня пола до свисающей с колеса цепи должно быть (06 08) * М. При расчете ручного привода необходимо учитывать что в зависимости от продолжительности работы усилие развиваемое рабочим и скорость движения его руки изменяются. Для расчета механизмов передвижения с ручным приводом необходимо использовать нормированное значение усилия рабочего:
- 80 Н при работе до 15 минут;
- 120 Н при работе до 10 минут;
- 200 Н при работе до 5 минут.
Наибольшее усилие при трогании с места не должно превышать 500 Н.
На рис. 1 представлена схема механизма подъема с ручным приводом.
Pис. 1. Схема механизма подъема с ручным приводом.
Момент на рукоятке механизма подъема для одного рабочего можно определить по формуле:
- момент крутящий на рукоятке;
- коэффициент учитывающий неодновременность приложения усилия при совместной работе нескольких операторов (здесь для двух рабочих для трех для четырех рабочих);
Р - нормативное значение усилия одного рабочего на рукоятке;
l - радиус рукоятки или плечо.
Момент сопротивления на валу барабана от груза:
S - натяжение тягового элемента на барабане.
Принимаем кратность простого полиспаста (рис. 5) (см. табл.1).
Таблица 1: Значение кратности полиспаста.
Характер навивки на барабан
Значение кратности при грузоподъемности в
Через направляющий блок
Максимальное усилие в ветви каната навиваемого на барабан
— количество свободных блоков
Канат выбирается по разрывному усилия с учетом коэффициента запаса прочности который принимается по табл. 2
Коэффициент запаса прочности
Тип привода и режим работы
Грузовые и стреловые
Выбираем канат ЛК-Р о.с. диаметром с разрывным усилием (ГОСТ 7679-69).
Диаметр барабана и блоков по центру наматываемого каната
где коэффициент принимаемый по табл.3
Наименьшие допускаемые значения коэффициента
амеханизмы подъема груза и стрелы
Рабочая длина каната наматываемого на барабан
Количество рабочих витков
где — минимальное количество запасных витков (по Правилам Госгортехнадзора );
— количество витков для закрепления каната на барабане.
—запасное расстояние от последних витков каната до концов барабана.
Барабан принимаем гладкий поэтому и
Скорость наматывания каната на барабана
Частота вращения барабана
Частота вращения рукояти лебедки
Расчетное передаточное число зубчатой передачи
Выбираем редуктор 1ЦУ-160 с передаточным числом
Фактическая скорость подъема груза
Номинальный крутящий момент на выходном валу 1250 Н·м что больше момента сопротивления на валу барабана.
Рис.2. Схема механизма подъема.
Гестрин Б.И. Технология машиностроения производство и ремонт ПТМ СДМ: Учебное пособие по выполнению курсового проекта Б.И. Гестрин. – Иркутск: Изд-во ИрГТУ 2008. – с.
Косилова А.Г. Справочник технолога-машиностроителя
Машиностроение 1986-496с
Анурьев В.И. Справочник конструктора-машиностроителя
Машиностроение 1979-789с
Техкарта.dwg

Техкарта 2.dwg

Неуказанные предельные отклонения размеров валов h14
остальных ±IT142 2. Твердость поверхности зубьев HRC 33 38
Коэффициент смещения
Круг В-220 ГОСТ 2590-88 40ХН-1-2-Т ГОСТ 4543-71
Контроль радиального биения
Контроль шереховатости
Контроль всех размеров согласно чертежу
Отрезать заготовку ø230 и L=69
Снять фаску 2x45° с ø220 мм
Расточить с ø60 до ø115
Подрезать торец на ø230 на глубину 1 мм
Рассверлить отверстие ø10 до ø60 L=67 мм
до ø127H14 на L=40мм
Ленточно-отрезной станок 8544
Нарезать резьбу М6 метчиком №1
операцию повторить 5 раз
снять деталь Произвести закалку нагревом до t=800° C с охлаждением в масле Произвести отпуск нагревом до t=180-250° C
Зубохонинговальная Установить
снять деталь Хонинговать зубья.
Проточить с ∅230 до ∅220h14 на L=20 мм
Переустановить деталь
Проточить с ø230 до ø145h14 на L=47 мм
до ø127H14 на L=2 мм
Зенкеровать отверстие ø14 на глубину 15мм
Сверлить 6 отверстий ø17на R92
с угла 30° на глубину L= 20 мм
Сверлить отверстие ø7 в торце ø220 на расстоянии L=10мм от края
Пила ленточная DUOS M42
Самоцентрирующийся трехкулачковый патрон ГОСТ 24351-80
Штангенциркуль ШЦ-2-250-0
ГОСТ 169-89 2. Нутромер НИ100-160 ГОСТ 9244-75 3. Микрометр МК 150-1 125-225 0.01 по ГОСТ 6507-78 4. Микрометр МК 225 200-225 0.01 по ГОСТ 6507-78 5. Профилограф- профилометр А1 по ГОСТ 19299-73
Круг В-230 ГОСТ 2590-88 40ХН-1-2-Т ГОСТ 4543-71
Снять фаску 1х45° с ø17 с обоих сторон
операцию повторить 5 раз.
Сверлить 6 отверстий ø5 на R67
№1 и № 2 по ГОСТ3266-81
Зенкер ø14 мм по ГОСТ12489-71
Зенковка по ГОСТ14953-80
Зубодолбежный полуавтоматический станок 5140
Зуборезный долбяк l0
номинальный диаметр 80мм
Твердомер ИТ-5038 ГОСТ-5570-82
Просверлить отверстие ø10 на L=67 мм
контролируя размер 67 мм
Нарезать резьбу М6 метчиком №2
Нарезать резьбу М8 метчиком №2
Нарезать зубья внутреннего зацепления на ø120
Рекомендуемые чертежи
Свободное скачивание на сегодня
Обновление через: 13 часов 22 минуты