Расчёт военного АТП на 156 авто




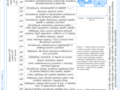
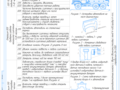
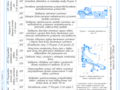
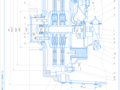
- Добавлен: 25.01.2023
- Размер: 5 MB
- Закачек: 0
Описание
Состав проекта
![]() |
![]() ![]() ![]() ![]() |
![]() ![]() ![]() ![]() |
![]() ![]() ![]() ![]() |
![]() ![]() ![]() ![]() |
![]() ![]() ![]() ![]() |
![]() ![]() ![]() ![]() |
![]() ![]() ![]() ![]() |
![]() ![]() ![]() ![]() |
![]() ![]() ![]() ![]() |
![]() ![]() ![]() ![]() |
![]() ![]() ![]() ![]() |
![]() ![]() ![]() ![]() |
![]() ![]() ![]() |
![]() ![]() ![]() ![]() |
![]() ![]() ![]() ![]() |
Дополнительная информация
3.Участок ТР.cdw

12.Наладки.cdw

8.Карта дефектации.cdw

4.Спецификация к СБ.spw

5.Диагностическая карта.cdw

1.Генеральный план.cdw

6.Технологическая карта.cdw

11.Общий вид подъемника.cdw

7.Технологическая карта.cdw

Спецификация к ОВ.spw

4.Сборочный чертеж.cdw

9.Ремонтный чертеж.cdw

10.Схема сборки.cdw

2.Производственный корпус.cdw

Рекомендуемые чертежи
- 22.08.2014
- 22.08.2014
Свободное скачивание на сегодня
Другие проекты
- 29.08.2014
- 23.08.2014