Расчет привода с червячным редуктором




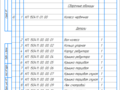
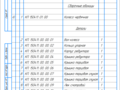
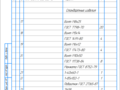
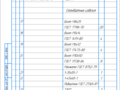
- Добавлен: 24.01.2023
- Размер: 1 MB
- Закачек: 0
Описание
Состав проекта
![]() |
![]() |
![]() ![]() ![]() |
![]() |
![]() ![]() ![]() |
![]() ![]() |
![]() ![]() ![]() |
![]() ![]() ![]() ![]() |
![]() |
![]() ![]() ![]() ![]() |
![]() ![]() ![]() ![]() |
![]() ![]() ![]() ![]() |
![]() ![]() ![]() ![]() |
![]() ![]() ![]() |
![]() ![]() ![]() ![]() |
![]() ![]() ![]() |
![]() ![]() ![]() |
![]() ![]() ![]() |
![]() |
![]() ![]() ![]() ![]() |
![]() ![]() ![]() ![]() |
![]() ![]() ![]() ![]() |
![]() ![]() ![]() ![]() |
![]() ![]() ![]() |
![]() ![]() ![]() ![]() |
![]() |
![]() ![]() |
![]() |
![]() ![]() ![]() ![]() |
![]() ![]() ![]() |
![]() ![]() ![]() ![]() |
![]() ![]() ![]() |
Дополнительная информация
М Заключение.doc
Для расчета валов мы определили диаметры ступеней их длины и предварительно выбрали подшипники для них. После чего мы произвели проверочный расчет валов на прочность по напряжениям изгиба и кручения. После проверочного расчета валов мы подобрали и проверили шпоночные соединения под полумуфту колесо. Далее мы описали принятую систему смазки редуктора и подшипников описали процесс сборки нашего редуктора.
Достоинства: высокая нагрузочная способность надежность работы малые габариты постоянство передаточного числа высокий КПД в одной ступени простота в эксплуатации.
Недостатки: шум при больших скоростях повышенные требования к точности изготовления возможность перегрузок невозможность компенсации динамических нагрузок.
Рассчитав редуктор мы познакомились с его внутренним устройством усвоили принцип работы научились рассчитывать и конструировать отдельные элементы.
Редукторы получили широкое распространение и поэтому их нужно уметь рассчитывать.
Б Содержание.doc
Пояснительная записка
Кинематический и силовой расчет привода 7
1 Подбор электродвигателя .. ..7
2 Определение передаточных чисел привода .7
3 Определение силовых и кинематических параметров . ..8
Расчет зубчатой передачи .. .11
1 Выбор материалов .. . 11
2 Расчет допускаемых контактных напряжений . . 11
3 Расчет допускаемых изгибающих .. .12
4 Расчет зубчатой передачи .. ..13
Расчет гибкой связи .. .. .18
Определение размеров элементов корпуса редуктора 22
1 Определение толщины стенок редуктора . 22
2 Определение размеров крепежных болтов и винтов 22
3 Детали и элементы корпуса редуктора 22
Расчет валов редуктора .24
1 Предварительный расчет валов редуктора ..24
2 Эскизная компоновка . ..25
3 Определение сил в зацеплении передачи ..25
4 Определение реакций в опорах .26
5 Проверочный расчет подшипников 31
6 Проверочный расчет валов на выносливость .. .33
Подбор и проверочный расчет шпоночных соединений . . ..37
1 Шпонка под полумуфту .. ..37
2 Шпонка под зубчатое колесо . 38
3 Расчет применение посадок в редукторе .39
Описание принятой системы смазки . ..45
1 Смазывание редуктора ..45
2 Смазывание подшипников 45
Описание процесса сборки редуктора 46
К Описание системы смазки.doc
1 Смазывание редуктора
Смазывание конических зацеплений и подшипников принимают в целях защиты от коррозии снижения коэффициента трения уменьшение износа отводов продуктов износа от трущихся поверхностей снижения шума и вибраций. Для смазывания конического зацепления применяем непрерывное смазывание жидким маслом картерным непроточным способом (окунанием).
Выбор сорта масла зависит от значений расчетного контактного напряжения в зубьях и фактической окружной скорости колес. Принимаем индустриальное масло по таблице [1] марки И-Г-А-68 (масло индустриальное для гидравлических систем без присадок).
Определение количества масла л по формуле [1с.255]
Объем масляной ванны литр определяют из расчета от 04 до 08 литров на 1 кВт передаваемой мощности
Определение уровня масла мм по формуле [1с.255]
где - высота масла мм определяется по формуле [1c.321]
Для контроля уровня масла находящегося в корпусе редуктора применяем трубчатый маслоуказатель.
При работе передач масло постепенно загрязняется продуктами износа деталей передач. С течением времени оно стареет свойства его ухудшаются. Поэтому масло налитое в корпус редуктора периодически меняют. Для этой цели в корпусе предусматривают сливное отверстие закрываемое пробкой с цилиндрической или конической резьбой.
При длительной работе в связи с нагревом масла и воздуха повышается давление внутри корпуса. Это приводит к просачиванию масла через уплотнения и стыки. Чтобы избежать этого внутреннюю полость корпуса сообщают с внешней средой путем установки отдушины в его верхних точках.
2 Смазывание подшипников
Подшипники смазывают пластичной смазкой. Смазочный материал набивают в подшипник вручную при снятой крышке подшипникового узла на несколько лет. Смену смазочного материала производят при ремонте. Для смазки применяют солидол.
Сборочный чертеж.cdw

Число редуктора u = 20.
Вращающий момент на тихоходном валу Т
Частота вращения быстроходного вала n
Технические требования
Необработанные поверхности литых деталей
находящихся в масляной ванне
красить маслостойкой красной эмалью.
Наружные поверхности корпуса красить серой эмалью ПФ-115 ГОСТ 6465-76.
Редуктор залить маслом: индустриальное И-Т-Д-68 ГОСТ 17479.4-87
Допускается эксплуатировать редуктор с отклонением от горизонтального
положения на угол до 5
. При этом должен быть обеспечен уровень масла
для смазки зацепления и подшипниковых узлов червяка .
Колесо червячное.cdw

Коэффициент смещения червяка
Исходный производящий червяк
Межосевое расстояние
Вид сопряженного червяка
Число витков сопряженного червяка
Размеры для справок.
Неуказанные радиусы 3 мм.
Формовочные уклоны 3
Редуктор спецификация 2 лист.cdw

КП. 150411. 00. 00. 13
КП. 150411. 00. 00. 14
КП. 150411. 00. 00. 15
Мaнжета ГОСТ 8752-79
Подшипник ГОСТ 27365-87
Сборочный чертеж.cdw

Число редуктора u = 20.
Вращающий момент на тихоходном валу Т
Частота вращения быстроходного вала n
Технические требования
Необработанные поверхности литых деталей
находящихся в масляной ванне
красить маслостойкой красной эмалью.
Наружные поверхности корпуса красить серой эмалью ПФ-115 ГОСТ 6465-76.
Редуктор залить маслом: индустриальное И-Т-Д-68 ГОСТ 17479.4-87
Допускается эксплуатировать редуктор с отклонением от горизонтального
положения на угол до 5
. При этом должен быть обеспечен уровень масла
для смазки зацепления и подшипниковых узлов червяка .
Редуктор спецификация 3 лист.cdw

Редуктор спецификация 1 лист.cdw

КП. 150411. 00. 00. 01
КП. 150411. 00. 00. 02
КП. 150411. 00. 00. 03
КП. 150411. 00. 00. 04
КП. 150411. 00. 00. 05
КП. 150411. 00. 00. 06
КП. 150411. 00. 00. 07
КП. 150411. 00. 00. 08
КП. 150411. 00. 00. 09
КП. 150411. 00. 00. 10
КП. 150411. 00. 00. 11
Крышка торцовая глухая
Червяк.cdw

Неуказанные предельные отклонения размеров:
Делительный угол подъема
Направление линии витка
Делительный диаметр червяка
КП. 150411. 00. 00. 15
Сталь 45 ГОСТ 1050-88
8 ОПИСАНИЕ ПРОЦЕССА СБОРКИ РЕДУКТОРА.doc
Перед сборкой внутренней полости корпуса тщательно очищают и покрывают маслостойкой краской. Сборку редуктора производят в соответствии с чертежом общего вида. Начинают сборку редуктора с быстроходного вала: надевают шариковые радиально-упорные однорядные подшипники предварительно нагрев их в масле до 80-100. Собранный быстроходный вал устанавливают в корпусе редуктора. Сборку тихоходного вала начинают с установки зубчатого колеса. Для этого сначала закладывают в паз на валу шпонку и затем напрессовывают колесо на вал. Затем напрессовывают шариковые подшипники нагретые в масле. Собранный вал с колесом и насаженными подшипниками устанавливают в корпусе редуктора затем устанавливают врезные крышки. Редуктор закрывают крышкой и затягивают болты. Место разъема корпуса редуктора и крышки покрывают лаком.
Регулировку роликовых конических однорядных подшипников производят с помощью регулировочных винтов и шайб установленные в подшипниковые крышки. В конце сборки редуктора маслоспускное отверстие закрывают пробкой и устанавливают маслоуказатели. В редуктор заливают масло и закрывают смотровое отверстие крышкой. Собранный редуктор подвергают испытаниям на холостом ходу.
Червячный редуктор Мой Расчет Исправ..doc
1 Подбор электродвигателя
Определяем общий КПД привода по формуле [1c.41]
где РЕМ- КПД плоскоременной передачи;
ПОДШ- КПД одной пары подшипников качения;
ЧП- КПД червячной передачи;
Определяем требуемую мощность электродвигателя NДВ кВт по формуле [1c.42]
где N - требуемая выходная мощность на валу рабочей машины кВт.
По таблице по требуемой мощности электродвигателя Nдв=797 КВт выбираем тип двигателя 4АМ132S4УЗ. Значение символов в обозначении: цифра 4 указывает порядковый номер двигателя; буква А- род двигателя в данном случае асинхронный; М – модернизированный; цифра 132 указывает высоту оси вращения ротора; S- установочный размер по длине станины;
- число полюсов; буквы УЗ показывают что двигатель предназначен для эксплуатации в зоне умеренного климата.
Исходные данные электродвигателя:
Nдв – номинальная мощность электродвигателя; 75 кВт
nсинх – синхронная частота вращения; 1500 обмин
nном – номинальная частота вращения вала электродвигателя 1455 обмин.
2 Определение передаточных чисел привода
Определяем общее передаточное число привода U по формуле [1c.43]
где nДВ- номинальная частота вращения вала электродвигателя обмин;
nвых - требуемая частота вращения вала рабочей машины обмин;
Определяем передаточное число ременной передачи UГС обмин по формуле[2c.43]
где UР- передаточное число редуктора;
U- общее передаточное число.
3 Определение силовых и кинематических параметров на валах привода
Определяем частоту вращения вала электродвигателя nДВ обмин.
Определяем частоту вращения быстроходного вала n1 обмин по формуле [1c.47]
где Uг.с-общее передаточное число гибкой связи.
Определяем частоту вращения тихоходного вала n2 обмин по формуле [1c.47]
Определяем угловую скорость вала электродвигателя радс по формуле [1c.48]
где nдв- частота вращения двигателя обмин;
Определяем угловую скорость быстроходного вала радс по формуле [1c.48]
где Uг.с- передаточное число ременной передачи;
- угловая скорость вала электродвигателя радс.
Определяем угловую скорость тихоходного вала редуктора радс по формуле [1c.48]
где UР.- передаточное число редуктора..
Определяем вращающий момент вала электродвигателя ТДВ Нм по формуле [1c.48]
где - угловая скорость вала электродвигателя радс;
NДВ- мощность электродвигателя кВт.
Определяем вращающий момент на быстроходном валу Т1 Нм по формуле [1c.48]
где UГ.С.- передаточное число ременной передачи;
Т1- вращающий момент вала электродвигателя Нм.
Определяем вращающий момент на тихоходном валу Т2 Нм по формуле [1c.48]
где UР- Передаточное число редуктора;
Т1-вращающий момент на быстроходном валу Нм.
Расчет сводим в таблице 1.1
Таблица 1.1- Определение силовых и кинематических параметров привода.
Последовательность соединения элементов схемы
P1 = Pдв п м = 75 099 098 = 727 кВт
P2 = P1 зп п = 727 085 099 = 611 кВт
Pрм = P2 оп п = 611 097 099 = 586 кВт
Частота вращения n обмин
Продолжение таблицы 1.1
Вращающий момент Т Нм
РАСЧЕТ ЗУБЧАТОЙ ПЕРЕДАЧИ
Принимаем марки стали для червяка и колеса .
Для червяка выбираем сталь 45 улучшенную имеющую следующие характеристики в = 890 МПа; = 650 МПа; -1 = 380 МПа.
Выбираем марку материала червячного колеса. Она зависит от скорости скольжения.
Определяем скорость скольжения по формуле [1 с. 57]
где uзп – передаточное отношение редуктора; 20
w2– угловая скорость тихоходного вала; 475 1с
Т2– вращающий момент на тихоходном валу. 13234 Нм.
При данной скорости скольжения выбираем для венца червячного колеса бронзу БрО10Н1Ф1 полученную с помощью центробежного литья со следующими характеристиками:
в = 285 МПа; = 165 МПа.
2 Расчет допускаемых контактных напряжений
Определяем коэффициенты долговечности для червяка КНL1 и колеса КНL2 по формулам [1с.55]:
где N - число циклов переменных напряжению за весь срок службы определяется по формулам [1c.55]:
где 2- угловая скорость быстроходного вала редуктора радс
Lh - срок службы рассчитывается по формуле [1c.55]
где tс - продолжительная смена в часах (принимаем 8ч);
Lc - количество смен (принимаем 2 смену)
Определяем допускаемые контактные напряжения по формуле [1 с. 58].
где KHL2 =102 – коэффициент долговечности;
СV = 085 – коэффициент учитывающий износ материала.
3 Расчет допускаемых изгибающих напряжений
Определяем коэффициенты долговечности КFL1 и КFL2 для зубьев по формуле [1c.55]:
где N- число циклов переменных напряжению за весь срок службы.
Определяем допускаемые изгибные напряжения по формуле [1 с. 58]
гдеKFL2 = – коэффициент долговечности при расчете на изгиб.
Таблица 2.1 - Механические характеристики материалов червячной передачи
4 Расчет зубчатой передачи
Определяем межосевое расстояние по формуле [1c.74]
где Т2- вращающий момент на тихоходном валу редуктора Нм .
По стандартному ряду принимаем межосевое расстояние равным 180 мм.
Выбираем число витков червяка Z1 оно зависит от передаточного числа редуктора
Uр =20 принимаем Z1 =2;
Определяем число зубьев червячного колеса Z2 по формуле[1c.74]
По стандартному ряду принимаем Z2=40.
Определяем модуль зацепления mмм по формуле [1c.74]
По стандартному ряду принимаем m=7.
Из условия жесткости определяем коэффициент диаметра червяка q по формуле [1c.75]
По стандартному ряду принимаем q = 10.
Определяем коэффициент смещения инструмента Х по формуле [1c.75]
Должно выдерживаться соотношение .
Определяем фактическое передаточное число по формуле [1c.76]
Проверяем отклонение от заданного:
Фактическое передаточное число UФ= UР заданному
Определяем фактическое межосевое расстояние мм по формуле [1c.76]
Определяем основные геометрические размеры передачи по формулам [1c.76]
- делительный диаметр червяка мм
- начальный диаметр мм
- диаметр вершин витков червяка мм
- диаметр впадин витков червяка мм
- делительный угол подъема линии витков
- длина нарезаемой части червяка
Принимаем b1 = 130 мм.
- делительный диаметр червячного колеса мм
- диаметр вершин зубьев мм
- наибольший диаметр колеса:
- диаметр впадин зубьев мм
Принимаем b2 = 63 мм.
Определяем радиусы закругления зубьев и мм по формулам [1c.76]
Определяем угол обхвата червяка венцом колеса по формуле [1c.76]
Принимаем угол обхвата 48035.
5 Проверочный расчет
Определяем коэффициент полезного действия червячной передачи по формуле [1c.77]
где - делительный угол подъема линии витков червяка 0;
- угол трения. Определяется в зависимости от фактической скорости скольжения VS
Значение угла трения принимаем по таблице [1]
Проверяем контактные напряжения зубьев колеса по формуле [1 с. 77]
где – окружная сила на колесе;
d1 – делительный диаметр червяка 70 мм;
d2 – делительный диаметр колеса. 280 мм;
К – коэффициент нагрузки. Выбирается в зависимости от окружной скорости колеса.
При окружных скоростях менее 3 мс К = 1.
Передача работает с перегрузкой так как расчетные контактные напряжения больше допускаемых. Допускается перегрузка до 10 %.
Величина перегрузки составляет .
Проверяем напряжения изгиба зубьев колеса по формуле [1 с. 78]
гдеYF2– коэффициент формы зуба колеса. Определяется в зависимости от эквивалентного числа зубьев: 155
Условие прочности по изгибным напряжениям выполняется.
Если при проверочном расчете расчетные напряжения значительно меньше допускаемых то это допустимо так как нагрузочная способность большинства зубчатых передач ограничивается контактной прочностью. Если напряжения изгиба зубьев свыше 5% то надо увеличить модуль соответственно пересчитать число зубьев шестерни и колеса и повторить проверочный расчет на изгиб. При этом внешний делительный диаметр колеса не изменится а следовательно не нарушается контактная прочность передачи.
Таблица 2.2 – Параметры червячной передачи
Межосевое расстояние
Ширина зубчатого венца колеса
Длина нарезаемой части червяка
Коэффициент диаметра червяка
Делительный угол витков
Угол обхвата червяка венцом колеса
Число витков червяка Z1
Число зубьев колеса Z2
Допускаемые значения
Коэффициент полезного действия
Контактные напряжения
РАСЧЕТ ГИБКОЙ СВЯЗИ. (ППЛОСКОРЕМЕННАЯ)
Расчет гибкой связи выполняем в соответствии с рисунком 3.1
а – сечение плоского ремня
б – сечение клинового ремня
в – сечение поликлинового ремня
Рисунок 3.1 – Геометрические и силовые параметры ременной передачи
Определяем диаметр ведущего шкива мм по формуле [1c.80]
где -толщина ремня. Принимаем по данным таблицы [1]
Диаметр ведущего шкива округляем до ближайшего стандартного по таблице [1] =200 мм.
Определяем диаметр ведомого шкива по формуле [1c.81]
где - коэффициент скольжения .
Диаметр ведомого шкива принимаем по таблице [1] =355 мм.
Определяем фактическое передаточное отношение Uф по формуле [2c.81]
Проверяем его отклонение от заданного U по формуле [2c.81]
Определяем ориентировочное межосевое расстояние по формуле [3c.81]
Определяем расчетную длину ремня lмм по формуле [1c.81]
Расчетную длину ремня принимаем по стандарту l =3000 мм.
Уточняем значение межосевого расстояния по стандартной длине l по формуле [4c.81]
При монтаже передачи необходимо обеспечить возможность уменьшения
на для того чтобы облегчить надевание ремня на шкив; для увеличения натяжения ремней необходимо предусмотреть возможность увеличения на
Определяем угол обхвата ремнем ведущего шкива по формуле [6c.81]
Определение скорости ремня мс по формуле [7c.81]
Условие выполняется.
где и соответственно диаметр ведущего шкива мм и его частота вращения обмин;
- допускаемая скорость мс; мс – для плоских ремней
Определяем частоту пробега ремня U c-1 по формуле [8c.81]
Условие выполняется.
где - допускаемая частота пробегов ; ;
Соотношение условно выражает долговечность ремня и его соблюдение гарантирует срок службы 1000 5000 ч.
Определяем окружную силу передаваемой ремнем H по формуле [1c.83]
Определяем допускаемую удельную окружную силу по формуле [2c.83]
где -коэффициент угла обхвата на меньшем шкиве; 097
- коэффициент влияния диаметра меньшего шкива; 12
- коэффициент угла наклона линии центров шкивов к горизонту; 1
- коэффициент влияния натяжения от центробежной силы; 1
- допускаемая приведенная удельная окружная сила 232 Определяется по таблице [5]
С – поправочные коэффициенты принимаем по таблице [5]
Определяем ширину ремня b мм по формуле [3c.83]
Ширину ремня b округляем до стандартного значения. Принимаем b =100 мм
В=112 – стандартное значение ширины шкива
Определяем площадь поперечного сечения ремня А мм 2
Определяем силы предварительного натяжения Н по формуле [1c.84]
где - предварительное напряжение изгиба ;2 принимаем по таблице [5]
Определяем силы натяжения ведущей и ведомой ветвей Н по формулам [34c.84]
Определяем силы давления на вал Н по формуле [5c.84]
Проверяем прочность ремня по максимальным напряжениям в сечении ведущей ветви по формуле [6с.84]
где - напряжение растяжения в плоском ремне ;
- напряжения изгиба в плоском ремне ;
где - модуль продольной упругости при изгибе для прорезиненных ремней принимаем 80;
- напряжения от центробежных сил ;
где - плотность материала ремня ; - для плоских ремней. Принимаем
- допускаемое напряжение растяжения ;
- для плоских ремней.
Условие прочности выполняется.
Таблица 3.1 – Параметры плоскоременной передачи
Частота пробегов ремня U 1с
Межосевое расстояние а
Диаметр ведущего шкива
Диаметр ведомого шкива
Максимальное напряжение
Предварительное натяжение ремня Н
Угол обхвата ведущего шкива град
Сила давления ремня на вал Н
ОПРЕДЕЛЕНИЕ РАЗМЕРОВ ЭЛЕМЕНТОВ КОРПУСА РЕДУКТОРА
1 Определение толщины стенок корпуса редуктора
Определяем толщину стенок редуктора мм по формуле [1с.231]
Толщину стенки принимаем мм.
2 Определение размеров крепежных болтов и винтов
Крепежные болты (винты) выбираем в зависимости от главного параметра редуктора – межосевого расстояния по таблице [1].
-для крепления редуктора к раме принимаем болты М16.
-для соединения основания и крышки корпуса – винты с цилиндрической головкой и шестигранным углублением под ключ размером М10.
-для крепления торцовых подшипниковых крышек принимаем болты М8.
-для крепления крышки смотрового люка выбираем винты М6.
3 Детали и элементы корпуса редуктора
Они служат для осмотра редуктора при эксплуатации. Для удобства осмотра располагаем его на верхней крышке корпуса редуктора что позволяет использовать люк для заливки масла. Люк закрываем крышкой из стального листа толщиной 2 мм. Под крышку устанавливают уплотняющую прокладку из резины толщиной 2 мм.
Для подъема и транспортировки редуктора применяют проушины их отливают за одно с крышкой редуктора. Они выполнены в виде ребер с отверстиями.
В корпусе редуктора также предусматривают отверстие под масло указатель и сливную пробку.
3.3 Отверстия под маслоуказатель и сливную пробку
Оба отверстия желательно располагать рядом на одной стороне основания корпуса в доступных местах. Нижняя кромка сливного отверстия должна быть на уровне днища или несколько ниже него. Дно желательно делать с уклоном 1 2 градуса в сторону отверстия. У самого отверстия в отливке основания корпуса выполняют местное углубление для стока масла и отстоявшейся грязи. Отверстие под маслоуказатель должно располагаться на высоте достаточной для точного замера верхнего и нижнего уровней масла. Форма и размеры отверстий зависят от типа выбранных маслоуказателя и сливной пробки. Наружные стороны отверстий оформляют опорными платиками. При установке маслоуказателя и сливной пробки с цилиндрической резьбой обязательно применяют уплотнительные прокладки из паронита или резиновое кольцо. Пробка с конической резьбой не требует уплотнения.
а – ребра с отверстиями;
б – сквозные отверстия в корпусе.
Рисунок 4.1- Проушины для подъема редуктора
РАСЧЕТ ВАЛОВ РЕДУКТОРА
1 Предварительный расчет валов редуктора
Целью данного расчета является определение геометрических размеров каждой ступени вала редуктора диаметра и длины.
Таблица 5 - Расчет геометрических размеров ступеней валов редуктора
Ступень вала и ее размеры
-я ступень под элемент открытой передачи
-я ступень под уплотнение и подшипник
-я ступень под шестерню колесо
-я ступень под подшипник
Продолжение таблицы 5
-я ступень под резьбу или упорная
L5 определяют графически
Предварительно выбираем подшипники:
- быстроходный вал – роликовые конические однорядные подшипники7608 ;
- тихоходный вал – роликовые конические однорядные подшипники 27317.
2 Эскизная компоновка
Эскизная компоновка редуктора выполнена на миллиметровой бумаге формата А2 в масштабе 1:1 и содержит: упрощенное изображение редуктора в двух проекциях и таблицу размеров.
Определяем зазор между корпусом редуктора и поверхностью колеса мм по формуле [1c.117]
гдеL– максимальная высота редукторной пары 37815 мм
Зазор между корпусом и поверхностью колеса принимаем 12 мм.
Определяем расстояние между дном корпуса и поверхностью колеса.
3 Определение сил в зацеплении передачи и консольных сил
Определение консольных сил.
В червячной передаче в зацеплении действуют силы: окружная осевая и радиальная.
На выходных концах валов действуют консольные силы:
на быстроходном – сила Fоп вызванная открытой передачей;
на тихоходном – сила Fм вызванная муфтой.
Консольная сила Fм определяется по формуле [1c.117]
гдеТ1– вращающий момент на быстроходном валу. 6617 Нм
Консольная сила от действия ременной передачи Fоп = 11177 Н.
Определение сил в зацеплении передачи и консольных сил сводим в таблицу 5.2
Таблица 5.2- Силы в зацеплении червячной передачи
4 Определение реакций в опорах
4.1 Определение реакций в подшипниках быстроходного вала
На вал действуют следующие силы:
– окружная сила на червяке;
– осевая сила на червяке;
– радиальная сила на червяке;
Действие осевой силы Fа заменяем действием крутящего момента Ма величину которого определяем по формуле [1c.157]
Определяем реакции опор в вертикальной плоскости
Строим эпюру изгибающих моментов Мx в вертикальной плоскости
Определяем реакции в опорах в горизонтальной плоскости
Строим эпюру изгибающих моментов Мy в горизонтальной плоскости
Строим эпюру крутящих моментов
Определяем суммарные радиальные реакции
Определяем суммарные изгибающие моменты
4.2 Реакции опор на валу колеса;
Действие осевой силы заменяем действием крутящего момента
Строим эпюру изгибающих моментов в вертикальной плоскости
Строим эпюру изгибающих моментов в горизонтальной плоскости
Определяем суммарные реакции опор и изгибающих моментов
Расчетная схема тихоходного вала представлена на рисунке 5.2
5 Проверочный расчет подшипников
Расчет подшипников на тихоходном валу. Предварительно выбраны роликовые конические однорядные подшипники 27317. Осевая сила =18905Н.
Рисунок 3-схема установки подшипников на тихоходном валу
Определяем осевые составляющие Н по формуле [1c.135]
где е- коэффициент влияющий на осевые нагрузки
- суммарная реакция подшипников Н
- суммарная реакция подшипника Н.
Определяем осевые нагрузки подшипников по формулам [1c.148]
Определяем эквивалентные нагрузки подшипника D Н по формуле [1c.141]
Если соотношение то эквивалентную нагрузку подшипника находим по формуле [1c.141]
где Х- коэффициент радиальной нагрузки
Y- коэффициент осевой нагрузки.
Определяем эквивалентные нагрузки подшипника С Н по формуле [1c.141]
где V- коэффициент вращения;
где -коэффициент безопасности;
- температурный коэффициент;
Дальнейший расчет ведется по подшипнику D т.к. он оказался более нагруженным.
Рассчитываем долговечность подшипника по формуле [1c.140]
где - коэффициент надежности при безопасной работе подшипника
- коэффициент учитывающий влияние коэффициента
- динамическая грузоподъемность подшипника
m - показатель степени для роликовых подшипников
n- частота вращения тихоходного вала обмин.
Расчет подшипника на валу червячного колеса. Предварительно выбраны роликовые конические однорядные подшипники7608 ; Осевая сила в зацеплении .
Рисунок 4-схема установки подшипника на валу червячного колеса
Определяем осевые составляющие Н по формуле [1c.141]
Определяем осевые нагрузки подшипников Н по формулам [1c.148]
Определяем эквивалентную нагрузку подшипника В Н по формуле [1c.141]
Определяем эквивалентные нагрузки подшипника А Н по формуле [1c.141]
Дальнейший расчет ведется по подшипнику В т.к. он оказался более нагруженным
6 Проверяем расчет валов на выносливость
Проверочный расчет валов прочность выполняют на совместное действие изгиба и кручения. При этом расчет отражает разновидность цикла напряжений изгиба и кручения усталостные характеристики материала размеры формулу и состояния поверхности валов.
Цель расчета – определить коэффициент запаса прочности и сравнить их с допускаемыми.
Расчетные коэффициенты запаса прочности определяем отдельно для быстроходного и тихоходного вала редуктора.
6.1 Проверочный расчет быстроходного вала.
Материал вала сталь 45 улучшенную. .
Опасным сечением является место куда садится подшипник.
Определяем номинальные напряжения в опасном сечении МПа по формуле [1c.269]
где - максимальный изгибающий момент Н*м;
- осевой момент сопротивления мм3 определяется по формуле [1c.270]
где d- диаметр впадин червяка мм.
Определяем касательные напряжения в опасном сечении МПа по формуле [1c.269]
где МКР- крутящий момент на быстроходном валу Н*м;
WРНЕТТО- полярный момент сопротивления мм3 определяем по формуле [1c.270]
Определяем коэффициент концентрации нормальных напряжений по формуле [1c.270]
где - эффективный коэффициент концентрации нормальных напряжений
- коэффициент внешних абсолютных размеров поперечного сечения
- коэффициент влияния шероховатости.
Определяем коэффициент концентрации касательных напряжений по формуле [1c.271]
где - эффективный коэффициент касательных напряжений.
Определяем предел выносливости по формулам [1c.273]
-для нормальных напряжений
-для касательных напряжений
Определяем коэффициенты запаса прочности по формулам [1c.273]
-по нормальным напряжениям
-по касательным напряжениям
Определяем общий коэффициент запаса прочности S по формуле [1c.273]
Полученное значение коэффициента запаса прочности должно быть больше допустимого
6.2 Проверочный расчет тихоходного вала.
Материал вала сталь 45 улучшенная. .
где d- диаметр вала под колесо мм.
где - эффективный коэффициент концентрации нормальных напряжений;
- коэффициент внешних абсолютных размеров поперечного сечения;
Определяем коэффициент концентрации консольных напряжений по формуле [1c.271]
ПОДБОР И ПРОВЕРОЧНЫЙ РАСЧЕТ ШПОНОЧНЫХ СОЕДИНЕНИЙ
1 Шпонка под полумуфту
Диаметр вала под шпонку равен 70 мм. Длина ступени 85 мм. В зависимости от диаметра вала выбираем шпонку 20*12. Длину шпонки принимаем на 5 10 мм меньше длины ступени вала и округляем до стандартного значения 80 мм.
Проверочный расчет на смятие производим по формуле [1c.265]
где - окружная сила на шестерне Н;
- допускаемое напряжение при смятии МПа;
- площадь смятия мм определяется по формуле [1c.265].
где h- высота шпонки мм;
- глубина паза на валу мм;
- расчетная длина шпонки мм определяется по формуле [1c.265]
Условие прочности на смятие выполняется.
Проверочный расчет на срез производится по формуле [1c.265]
где - диаметр вала мм;
b- ширина шпонки мм;
- допускаемое напряжение на срез МПа;
Т- крутящий момент на тихоходном валу МПа;
Условие прочности на срез выполняется.
1.2 Быстроходный вал
Диаметр вала под шпонку равен 34 мм. Длина ступени 41 мм. В зависимости от диаметра вала выбираем шпонку 10*8. Длину шпонки принимаем на 5 10 мм меньше длины ступени вала и округляем до стандартного значения 28 мм.
где- - площадь смятия мм определяется по формуле [1c.265]
Диаметр вала под шпонку равен 98 мм. Длина ступени 108 мм. В зависимости от диаметра вала выбираем шпонку 25*14. Длину шпонки принимаем на от 5 до10 мм меньше длины ступени вала и округляем до стандартного значения 100 мм.
где -окружная сила на шестерне Н;
- площадь смятия мм определяется по формуле [1c.265]
Т- крутящий момент на тихоходном валу МПа.
3 Расчет применение посадок в редукторе
Допуски и посадки шпоночных соединений
3.1 Исходные данные (быстроходный вал):
- диаметр вала d=34 мм;
- характер соединения – нормальное;
- нагрузки постоянные без частых реверсов;
- соединение неподвижное;
- шпонка 10х8х28 ГОСТ 23360-78;
- глубина паза на валу 5 мм;
- глубина паза на шкиве 33 мм.
Определяем допуски на размеры шпонки паза вала и паза втулки по ширине шпонки b мм по таблице [3]
-ширина паза при нормальном соединении
Таким образом сопряжение шпонка – паз вала выполнено по посадке а сопряжение шпонка – паз втулки по посадке .
Определяем предельные зазоры и натяги мкм по формулам [3с.160]
- в соединении шпонки с пазом вала (N9h9)
где ES – верхнее отклонение мкм;
ei – нижнее отклонение вала мкм.
где es – верхнее отклонение вала мкм;
EI – нижнее отклонение мкм.
- в соединении шпонки с пазом втулки (Js9h9)
Определяем допуски на сопрягаемые размеры мм по таблице [3]
- глубина паза вала или ;
- глубина паза втулки или .
3.2 Исходные данные (тихоходный вал):
- диаметр вала d=70 мм;
- шпонка 20х12х80 ГОСТ 23360-78;
- глубина паза на валу 75 мм;
- глубина паза на валу 49 мм.
- ширина паза при нормальном соединении
- длина паза вала ;
- глубина паза вала или;
На сборочных чертежах указывают условные обозначения полей допусков посадок а на чертежах валов и втулок – только поля допусков соответствующий размеров детали. Допуски не центрирующих диаметров в условных обозначениях можно не указывать.
Допуски и посадки подшипников
3.3 Исходные данные (быстроходный вал):
- подшипники роликовые конические однорядные легкой серии 7608
- вид нагружения кольца: наружного – местное
внутреннего – циркуляционное;
- радиальная реакция на подшипник R=90000 Н;
- внутренний диаметр d=40 мм;
- наружный диаметр D=90 мм;
- ширина подшипника В=355 мм;
- ширина фаски r=25 мм;
- рабочая ширина посадочного места b=33 мм.
Подбираем посадку для внутреннего кольца подшипника испытывающего циркуляционное нагружение.
Определяем интенсивность нагрузки Нмм по формуле [3c.95]
где - динамический коэффициент посадки зависящий от характера нагрузки;
- коэффициент учитывающий степень ослабления посадочного натяга;
- коэффициент неравномерности распределения нагрузки между рядами роликов в двухрядных конических роликоподшипниках или между сдвоенным радиально-упорным шарикоподшипниками при наличии осевой нагрузки на опору.
По таблице [3] принимаем основное отклонение h при d=40 мм и =32167 Нмм. Допуск намечаем по шестому квалитету для подшипников класса точности нуль.
Подбираем поля допусков для обработки посадочных поверхностей корпуса: наружное кольцо испытывает местное нагружение нагрузка с умеренными толчками корпус разъемный. По таблице [3]. Для этих условий рекомендуется основное отклонение Н допуск намечаем по седьмому квалитету.
Таким образом посадка внутреннего кольца подшипника на вал осуществляется по h6 а наружного в корпус по Н7.
Находим предельные отклонения посадочных поверхностей колец подшипника вала и корпуса.. предельные отклонения посадочных поверхностей колец подшипника находим по таблице [3] для средних диаметров: внутреннего наружного кольца подшипника:
- наружный диаметр подшипника
- внутренний диаметр подшипника
- предельные отклонения отверстий для посадки наружного кольца
- предельное отклонение вала для посадки внутреннего кольца
Определяем предельные зазоры и натяги в сопряжении мм по формулам [3c.95]
- отверстие корпуса – наружное кольцо подшипника (зазор)
- вал – внутреннее кольцо подшипника (натяг)
Для ограничения отклонений формы допуск цилиндричности посадочных мет валов и отверстий корпусов не должен превышать четверти допуска на диаметр посадочной поверхности.
Определяем допуск цилиндричности для вала мкм по формуле [3c.96]
Округляем до стандартного и принимаем 4 мкм.
Определяем допуск цилиндричности для отверстия корпуса мкм по формуле [3c.96]
Округляем до стандартного и принимаем 8 мкм.
3.4 Исходные данные (тихоходный вал):
- подшипники роликовые конические однорядные легкой серии 27317
- радиальная реакция на подшипник R=145000 Н;
- внутренний диаметр d=85 мм;
- наружный диаметр D=180 мм;
- ширина подшипника В=45 мм;
- рабочая ширина посадочного места b=41 мм.
По таблице [3] принимаем основное отклонение k при d=85 мм и =34381 Нмм. Допуск намечаем по шестому квалитету для подшипников класса точности нуль.
Таким образом посадка внутреннего кольца подшипника на вал осуществляется по k6 а наружного в корпус по Н7.
Находим предельные отклонения посадочных поверхностей колец подшипника вала и корпуса.. предельные отклонения посадочных поверхностей колец подшипника находим по таблице [3] для средних диаметров: внутреннего наружного кольца подшипника
- наружный диаметр подшипника
Точность подшипников [ГОСТ 520-71 (СТ СЭВ 774-77)] определяется отклонениями установленными в пяти классах точности на геометрические и кинематические параметры.
Класс точности (кроме класса нуль) указывают впереди условного обозначения подшипника.
Для соединения подшипников с валами и корпусами ГОСт 3325-55 (СТ СЭВ 773-77) установлены поля допусков отобранные из ЕСДП. Поля допусков для соединения подшипников валами и корпусом подбирают с учетом условий работы типа размера класса точности подшипника а также вида нагружения его колец. При местном и колебательном нагружении колец поля допусков для соединения подшипников с валом и корпусом можно выбирать по таблицам. При циркуляционном нагружении поля допусков следует выбирать по интенсивности радиальной нагрузки на посадочной поверхности кольца которая характеризуется величиной условной радиальной нагрузки приходящейся на единицу ширины внутреннего кольца.
На чертежах общих видов и деталей помещают условные обозначения полей допусков только обрабатываемых деталей. Отклонения формы от шероховатости отверстий и валов в местах сопряжения с подшипниками назначают по таблицами обозначают на чертежах деталей в соответствии со стандартами.
ОПИСАНИЕ ПРИНЯТОЙ СИСТЕМЫ СМАЗКИ
1 Смазывание редуктора
Смазывание червячных зацеплений и подшипников принимают в
целях защиты от коррозии снижения коэффициента трения уменьшение износа отводов тепла и продуктов износа от трущихся поверхностей снижения шума и вибраций.
Для червячного зацепления принимаем непрерывное смазывание
жидким маслом картерным способом (окунанием).
1.1 Выбор сорта масла
Смазочное масло для передачи принимаем в зависимости от
значения расчетных контактных напряжений и фактической
окружной скорости колеса. Принимаем индустриальное масло марки И-Т-Д-220(индустриальное тяжело нагруженных узлов масло с антиокислителем; антикоррозионное с присадками).
1.2 Определение количества масла
В червячном редукторах уровень масла определяется из
где - высота масла мм определяется по формуле [1c.321]
1.3 Контроль уровня масла
Для контроля уровня масла находящегося в корпусе редуктора
применяем круглый маслоуказатель.
При работе редуктора масло постепенно загрязняется
продуктами износа деталей передач. С течением времени оно стареет свойства его ухудшаются. Поэтому масло в редукторе периодически меняют. Для этой цели в корпусе предусматривают сливное отверстие
закрываемое пробкой с цилиндрической резьбой.
При длительной работе в связи с нагревом масла и воздуха
повышается давление в нутрии корпуса. Это приводит к просачиванию масла через уплотнение и стыки. Чтобы избегать этого внутреннюю полость редуктора сообщают с внешней средой путем установки отдушины в смотровом люке редуктора.
2 Смазывание подшипников
При окружной скорости выше 2 мс возможно надежное
смазывание подшипников разбрызгиванием. Для сборочного проникновения масла в полость подшипника должна быть открыта внутрь корпуса.
ОПИСАНИЕ ПРОЦЕССА СБОРКИ РЕДУКТОРА
Перед сборкой внутренней полости корпуса тщательно очищают
и покрывают маслостойкой краской. Сборку редуктора производят в соответствии с чертежом общего вида. Начинают сборку редуктора с быстроходного вала: надевают шариковые радиально-упорные однорядные подшипники предварительно нагрев их в масле до 80-100. Собранный быстроходный вал устанавливают в корпусе редуктора. Сборку тихоходного вала начинают с установки червячного колеса. Для этого сначала закладывают в паз на валу шпонку и затеем напрессовывают колесо на вал. Затем напрессовывают шариковые подшипники нагретые в масле. Собранный вал с колесом и насаженными подшипниками устанавливают в корпусе редуктора затем устанавливают врезные крышки. Редуктор закрывают крышкой и затягивают болты. Место разъема корпуса редуктора и крышки покрывают лаком.
Регулировку шариковых радиально-упорных подшипников
производят с помощью регулировочных винтов и шайб установленные в подшипниковые крышки. В конце сборки редуктора маслоспускное отверстие закрывают пробкой и устанавливают маслоуказатели.
В редуктор заливают масло и закрывают смотровое отверстие
крышкой. Собранный редуктор подвергают испытаниям на холостом ходу.
Титульник.doc
Березниковский политехнический техникум
РАСЧЕТ ПРИВОДА С ЧЕРВЯЧНЫМ РЕДУКТОРОМ
Пояснительная записка
КП. 150411. 00. 00. ПЗ
Редуктор спецификация 2 лист.cdw

КП. 150411. 00. 00. 13
КП. 150411. 00. 00. 14
КП. 150411. 00. 00. 15
Мaнжета ГОСТ 8752-79
Подшипник ГОСТ 27365-87
Сборочный чертеж.cdw

Число редуктора u = 20.
Вращающий момент на тихоходном валу Т
Частота вращения быстроходного вала n
Технические требования
Необработанные поверхности литых деталей
находящихся в масляной ванне
красить маслостойкой красной эмалью.
Наружные поверхности корпуса красить серой эмалью ПФ-115 ГОСТ 6465-76.
Редуктор залить маслом: индустриальное И-Т-Д-68 ГОСТ 17479.4-87
Допускается эксплуатировать редуктор с отклонением от горизонтального
положения на угол до 5
. При этом должен быть обеспечен уровень масла
для смазки зацепления и подшипниковых узлов червяка .
Червячное колесо.cdw

Коэффициент смещения червяка
Исходный производящий червяк
Межосевое расстояние
Вид сопряженного червяка
Число витков сопряженного червяка
Размеры для справок.
Неуказанные радиусы 3 мм.
Формовочные уклоны 3
Редуктор спецификация 3 лист.cdw

Редуктор спецификация 1 лист.cdw

КП. 150411. 00. 00. 01
КП. 150411. 00. 00. 02
КП. 150411. 00. 00. 03
КП. 150411. 00. 00. 04
КП. 150411. 00. 00. 05
КП. 150411. 00. 00. 06
КП. 150411. 00. 00. 07
КП. 150411. 00. 00. 08
КП. 150411. 00. 00. 09
КП. 150411. 00. 00. 10
КП. 150411. 00. 00. 11
Крышка торцовая глухая
Червяк.cdw

Неуказанные предельные отклонения размеров:
Делительный угол подъема
Направление линии витка
Делительный диаметр червяка
КП. 150411. 00. 00. 15
Сталь 45 ГОСТ 1050-88
Червяк.cdw

Неуказанные предельные отклонения размеров:
Делительный угол подъема
Направление линии витка
Делительный диаметр червяка
КП. 150411. 00. 00.
Сталь 45 ГОСТ 1050-88
Литература.doc
Эрдеди А. А. Техническая механика. Детали машин А. А. Эрдеди Н. А. Эрдеди.- М. :
Высшая школа 1992. -272 с. - ISBN 5-06-000699-9
Березовский Ю.Н. и др. Детали машин: Учебник для машиностроительных техникумов Ю.Н. Березовский Д.В. Чернилевский М.С. Петров; Под ред. Н.А. Бородина. – М.: Машиностроение 1983. – 384 с ил..
Козловский Н.С Брюховец Д.Ф. Рабин В. М. Ключников В.М. Сборник примеров и задач по курсу «Основы стандартизации допуски посадки и технические измерения». Учебное пособие для учащихся техникумов. – М.: Машиностроение 1983. – 304 с. –ISBN 5 -76951569-4
Федоренко В.А Шошин А.И. Справочник по машиностроительному черчению. Под ред. Г.Н. Поповой. - Л.: Машиностроение Ленинград. отд-ние 1981.-416 с. ил.
Методические рекомендации по технической механике. Москва: Высшая школа 1985.
Эскизная компоновка Я Испр.cdw

Введение.doc
Редукторы широко применяются в различных отраслях машиностроения и поэтому они весьма разнообразны по своим кинематическим схемам а также конструктивному исполнению. Редукторы бывают с цилиндрическими и коническими зубчатыми колёсами а также с червячными парами. Вид и конструкцию редуктора определяют типом расположением и количеством отдельных передач (ступеней).
Различают следующие виды редукторов:
а) цилиндрические зубчатые;
б) конические зубчатые;
г) коническо - цилиндрические зубчатые;
д) червячно - цилиндрические и др.
г) многоступенчатые.
-по расположению вала и зубчатых колёс
Рекомендуемые чертежи
- 25.10.2022
- 20.04.2023
- 10.03.2024