Расчет патрона


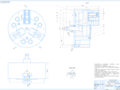
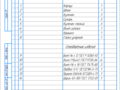
- Добавлен: 25.01.2023
- Размер: 169 KB
- Закачек: 1
Описание
Расчет патрона
Состав проекта
![]() |
![]() ![]() ![]() |
![]() ![]() ![]() ![]() |
![]() ![]() ![]() |
![]() ![]() ![]() ![]() |
Дополнительная информация
титульник.doc
БЕЛАРУССКИЙ НАЦИОНАЛЬНЫЙ ТЕХНИЧЕСКИЙ УНИВЕРСИТЕТ
Кафедра «Металлорежущие станки и инструмент»
Дисциплина «Технологическая оснастка»
Спецификация.spw

Винт М16х45 ГОСТ11738-84
Винт М6 х 18 ГОСТ 17475-80
Пробка 14" ОСТ2С98-3-73
Шарик 65-100 ГОСТ 3722-81
кр вар 11.doc
Обоснование выбранной конструкции и описание принципа действия
В качестве аналога проектируемого патрона для обработки отверстия в детали крышка принимаем универсальный токарный патрон 7102-0072 ГОСТ 24351-80. Данный трехкулачковый клиновой патрон можно использовать в диапазоне регулируемом от d= 20 мм до d = 260 мм. Кроме того погрешность закрепления в трехкулачковом патроне равна нулю [2].
Рисунок 2 – Универсальный токарный патрон 7102-0072 ГОСТ 24351-80
Проектируемый трехкулачковый патрон может устанавливаться как на универсальные токарные станки так и на токарные станки с числовым программным управлением и использоваться с любым видом привода.
Конструктивно проектируемый патрон состоит из следующих основных частей: корпуса 1 штока 2 кулачка основного 3 сухаря 4 кулачка мягкого 5 винта штока 6 крышки 7 гайки упорной 8.
Настройка на заданный диаметр осуществляется при помощи мягких кулачков 5 за счет отжима винтов 10. Кулачки перемещаются по специальной трапециидальной резьбе до получения необходимого зажимного размера. Когда регулировка завершена винты зажимаются.
Трехкулачковый клиновой патрон работает следующим образом. Рабочий устанавливает деталь на кулачки 3 и включает пневмопривод патрона. При подаче сжатого воздуха в штоковую полость пневмоцилиндра шток 2 вместе с винтом штока 6 перемещаются в левую сторону. В результате основной кулачок 3 с установленными в нем сухарями 4 и мягкими кулачками 5 опускается вниз происходит зажатие детали. Разжим осуществляется при подаче сжатого воздуха в заштоковую полость пневмоцилиндра.
Регулировка хода кулачков необходимого для зажима (разжима) осуществляется при помощи упорной гайки 8. В нашем случае ход кулачков равен 15 мм.
Расчет усилия зажима
1 Расчет режимов резания
Рассчитаем режимы резания при растачивании отверстия 30+016 мм. Припуск на обработку 3 мм. Обработку производим расточным резцом со сменными МНП твердого сплава Т15К6.
Определяем глубину резания
Назначаем подачу суппорта на оборот
S = 05 ммоб. [1таб. Т-2]
по паспорту станка принимаем Sпр = 05 ммоб.
Определяем стойкость инструмента по нормативам
Тр = Тпр = 90 мин [1 таб. Т-3] т.к. λ> 07.
Расчет скорости резания
где к1 - коэффициент зависящий от обрабатываемого материала;
к2 - коэффициент зависящий от стойкости и марки твердого сплава;
к3 - коэффициент зависящий от вида обработки.
V = 105·095·08·12 = 949 ммин [1 таб. Т-4].
Частота вращения шпинделя
По паспорту станка принимаем n = 1000 мин-1.
Уточняем скорость резания
Рассчитаем длину рабочего хода суппорта
где Lрез. - длина обработки Lрез. = 20 мм;
у - длина подвода перебега врезания инструмента у = 5 мм [1 стр. 303];
Lр.х. = 20 + 5 + 0 = 25 мм;
Расчет основного времени
Определяем штучное время штучное время
Тшт = Т0 + Тв + Тоб + Тот
где Т0 - основное время мин.;
Тв - вспомогательное время мин.;
Тоб - время на обслуживание рабочего места мин.;
Тот - время перерывов на отдых личные надобности.
Вспомогательное время состоит из затрат времени на отдельные приемы:
Твм = Тус + Тзо + туп + Тиз
где Тус - время на установку и снятие детали мин.;
Тз.о. - время на закрепление и открепление детали мин.;
Туп - время на приемы управления мин.;
Тиз - время на измерение детали мин.
Время на обслуживание рабочего места состоит:
Тоб = Торг + Ттех мин.
где Торг - время на организационное обслуживание рабочего места мин. ;
Ттех - время на техническое обслуживание рабочего места мин.
Время на техническое обслуживание определяется по формуле:
где Поб.от - процент затрат времени на обслуживание и отдых.
Основное время на операцию Т0 = 005 мин.
Тус = 007 мин. [табл. 5.3; 3];
Тз.о. = 0015 мин. [табл. 5.7; 3];
Туп = 0045 мин. [табл. 5.8 5.9; 3];
Тиз = 0031 мин. [табл. 5.12; 3];
Тв = (007 + 0015 + 0045 + 0031) = 0161 мин.
Топ = 005+ 0161 =0211 мин.
Тобсл = 0004 + 0002 = 0006 мин.
Тшт = 005 + 0161 + 0006 + 0013 = 0284 мин.
В состав подготовительно-заключительного времени входит:
- время на наладку станка и установки приспособлений - 42 мин [3 стр. 216];
- время на дополнительные приемы - 24 мин [3 стр. 217].
Тп.3. = 42 + 24 = 66 мин.
Тшт.к. = 666000 + 0284 = 0286 мин.
2 Определяем силу резания
Определяем окружную составляющую силы резания Рz;
где СРz - постоянная характеризующая условия резания СРz = 300Н табл.22 [2]
х у n - показатели степени соответственно равны 10; 075; - 015 табл.22[2].
Поправочный коэффициент Кр представляет собой произведение ряда коэффициентов учитывающих фактические условия резания:
Кр = КМр ·Кφр ·Кγр ·Кλр
где n - показатель степени равный 075 табл.9[2].
Кφр = 089; Кyр = 10; Кλр = 10 табл.23[2].
Кр= 10·089·10·10 = 089;
Р2 = 300·151·050.75 · 942-0.15 · 089 = 1204 Н;
Определяем осевую составляющую силу Рх;
Рх 04·Рz = 04·1204 = 482 Н.
Определяем радиальную составляющую силы Ру;
Ру = 05·Рz = 05 · 1204 = 602 Н.
3 Рассчитываем усилия зажима
Строим расчетную схему
Рисунок 3 – Расчетная схема
Суммарная сила зажима в трехкулачковом патроне:
где К - коэффициент запаса.
Рz - окружная сила резания.
f - коэффициент трения на рабочих поверхностях кулачков.
D1 - диаметр обрабатываемой поверхности; D1=30 мм.
D - диаметр зажимной поверхности; D = 45 мм.
Коэффициент запаса определяется по формуле:
где: К0 - габаритный коэффициент запаса. К0 = 15
К1 - коэффициент учитывающий состояние поверхности заготовок для групповой обработки. К1= 12
К2 - коэффициент учитывающий увеличение силы резания от затупления режущего инструмента. К2=1.
К3 - коэффициент учитывающий условия обработки при прерывистом резании. Для непрерывной поверхности К3 =1.
К4 - коэффициент учитывающий постоянство силы зажима развиваемой силовым приводом приспособления. Для пневмопривода К2 = 2.
К5 - коэффициент учитываемый только при наличии моментов стремящихся повернуть обрабатываемую деталь. К5 = 15.
К = 15·12·1·1·1·15 = 27
Определяем усилие зажима в клиновом механизме.
где W - требуемое усилие зажима;
α - угол скоса клина град;
φ1- угол трения на наклонной плоскости клина град;
φ2 - угол трения на горизонтальной плоскости клина град.
Q = 8669 [tg(5°30' + 7°) +tg90°] = 11922 Н
Рисунок 4 – Схема зажима с клиновым механизмом
Определяем диаметр пневмоцилиндра:
где р - расчетное давление воздуха р = 05 МПа стр. 333[4];
- механический КПД пневмоцилиндра = 08 стр. 333[4];
Так как данное приспособление позволяет обрабатывать детали других типоразмеров то принимаем диаметр пневмоцилиндра Dпр = 150 мм. Основные параметры гидроцилиндра назначаем по [4 стр. 334].
Расчет приспособления на точность
Погрешность допустимая для данного приспособления и вызываемая! неточностью его изготовления:
где Т - допуск выполняемого размера Т = 016;
б 3 ус п и - соответственно погрешности: базирования закрепления установки приспособления на станке положения детали из-за износа установочных элементов и от перекоса (смещения) инструмента;
- экономическая точность обработки;
КТ - коэффициент учитывающий отклонение рассеяния значений составляющих величин от закона нормального распределения Кт = 11 стр 151[4];
кт1 - коэффициент учитывающий уменьшение предельного значения погрешности базирования при работе на настроенных станках кт1 = 08 стр 152[4];
кт2 - коэффициент учитывающий долю погрешности обработки в суммарной погрешности вызываемой факторами не зависящими от приспособления кт2 = 07 стр 152[4].
где ТD - допуск на диаметр ТD = 016 мм
= 005 мм табл. 76 [4];
ус. = 005 мм стр. 169 [4];
и. = U где U - износ установочных элементов.
U = Uо·к1·к2·кз·к4*NNо
где U0 - средний износ установочных элементов Uо = 007 мм [4 табл. 81];
к1 к2 к3 к4 - соответственно коэффициенты учитывающие влияние материала заготовки оборудования условий обработки и числа установок заготовки;
к4= 18 табл. 82 [4];
N0 - базовое число установок N0 = 6000;
N - число установок N = 6000;
U = 007·097·10·094·60006000 = 0063 мм;
Таким образом условие по точности выполняется.
Экономическая целесообразность оснащения станочных операций приспособлением
Применение приспособлений при станочной обработке экономически целесообразно при условии:
где Э - величина ожидаемой экономии цеховой себестоимости обработки детали в результате применения приспособления;
Sобщ. - стоимость изготовления и эксплуатации приспособления.
Э = [Т·Ч·Q)]-[Т'·Ч·Q']
где Т Т' - нормируемая трудоемкость операции до и после оснащения ее приспособлением в ч.; Т = 0312 мин; Т' = 0286 мин.
Ч - тарифная часовая ставка рабочего с учетом поправочного коэффициента Ч = 18537 руб[2стр.219];
Q Q' - цеховые накладные расходы до и после оснащения операции приспособлением Q = 11000 руб Q' = 10780 руб.
n - количество обрабатываемых деталей с применением приспособления n = 6000 шт.
Э = [ 031260 ·18537 ·1100000] - [ 028660·18537·1078000] = 1077988 руб. Стоимость изготовления и эксплуатации приспособления определяем по формуле:
Sобщ. = Sизг. + Sрем.·k
где Sизг. - стоимость изготовления приспособления Sизг = 706440 руб.(по данным производителей).
Sрем - стоимость одного ремонта с учетом поправочного коэффициента Sрем = 86000 руб [5 стр. 219];
k - коэффициент учитывающий категорию сложности ремонта k = 082 [5 стр. 220];
Sобщ. = 706440 + 86000·082 = 776960 руб. 1
Условие выполняется следовательно применение приспособления при станочной обработке экономически целесообразно.
Режимы резания металлов. Справочник. Под ред. Ю.В. Барановского. - М. Машиностроение 1972. - 406 с.
Справочник технолога - машиностроителя. В 2-х томах Под ред. А.Г. Косиловой и Р.К. Мещерякова. М.: Машиностроение 1985. Т1 - 656 с Т2 -496 с.
Горбацевич А.Ф. Шкред В.А. Курсовое проектирование по технологии машиностроения. Мн.: Высшая школа 1989. - 256 с.
Антонюк В.Е. Конструктору станочных приспособлений - Мн.: Беларусь 1991.
Х.Л. Болотин Ф.П. Костромин. Станочные приспособления. - М. Машиностроение 1973. - 339 с.
патрон.cdw

Приспособление соответствует требованиям техники
безопасности по ГОСТ 12.2.029-88.
передаваемая приводом
Ход кулачков не менее 3 мм при максимальном передвижении
Поверхности клиновой опоры
соединения кулачков с корпусом
покрыть пастой ВНИИ НП-232.
Максимальный зазор в соединении штока с корпуса 0
Допускается при балансировке патрона в сборе сверление
балансировочных отверстий выполнять на поверхности В
диаметром и глубиной не более 12 мм.
предельный зажимаемы диаметр заготовки
Рекомендуемые чертежи
Свободное скачивание на сегодня
- 23.02.2023