Расчет червячного одноступенчатого редуктора с вертикальным расположением червяка




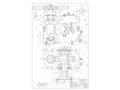
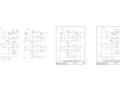
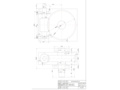
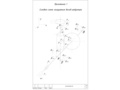
- Добавлен: 24.01.2023
- Размер: 814 KB
- Закачек: 0
Описание
Состав проекта
![]() |
![]() ![]() ![]() ![]() |
![]() ![]() ![]() |
![]() ![]() ![]() ![]() |
![]() ![]() ![]() ![]() |
![]() ![]() ![]() ![]() |
![]() ![]() ![]() |
Дополнительная информация
Сборочный чертеж.dwg

Технические требования q*;1. Необработанные поверхности литых деталей
находящихся в масляной ванне
красить маслостойкой красной эмалью. 2. Наружные поверхности корпуса красить серой эмалью ПФ-115 ГОСТ 6465-76. 3. Плоскость разъема покрыть тонким слоем герметика УТ-34 ГОСТ 24285-80 при окончательной сборке. Редуктор залить маслом: индустриальное И-Т-Д-100 ГОСТ 17479.4-87. 4. Радиальная консольная нагрузка на валу не более: входном 730 Н; выходном 4697 Н.
Редуктор червячный одноступенчатый. Сборочный чертеж
ПЗ.docx
Государственное образовательное учреждение
Высшего профессионального образования
«Владимирский государственный университет
имени Александра Григорьевича и Николая Григорьевича Столетовых»
Кафедра «Теоретическая и прикладная механика»
РАСЧЕТНО-ГРАФИЧЕСКАЯ РАБОТА
«Детали машин и механизмов»
«РАСЧЕТ ОДНОСТУПЕНЧАТОГО РЕДУКТОРА»
Пояснительная записка
на расчетно-графическую работу
Техническое задание 6
Рис. 1. Привод к качающемуся подъемнику
– передача поликлиновым ремнем; 2 – двигатель; 3 – червячный редуктор;
– тяговая цепь; 5 – подъемный монорельс; 6 – подвеска; 7 – груз;
– упругая муфта с торообразной оболочкой
грузоподъемность: F = 20 кН;
скорость подъема: = 075 мс;
шаг тяговой цепи: р = 150 мм;
число зубьев звездочки: z = 7;
допускаемое отклонение скорости подъема: = 7%;
срок службы привода: L = 7 лет.
Кинематический расчет6
1. Выбор электродвигателя6
2. Уточнение передаточных чисел привода7
3. Определение вращающих моментов на валах привода7
РАСЧЕТ ЧЕРВЯЧНЫХ ПЕРЕДАЧ8
1. Выбор твердости термообработки и материала колес8
2. Определение допускаемых контактных напряжений8
3. Определение допускаемых напряжений изгиба9
4. Проектный расчет редукторной пары10
5. Проверочный расчет редукторной пары13
6. Тепловой расчет16
Расчет ременной передачи17
1. Проектный расчет17
2. Проверочный расчет20
Нагрузка валов редуктора22
1. Определение сил в зацеплении червячных передач22
2. Определение консольных сил22
3. Силовая схема нагружения валов23
Проектный расчет валов24
1. Выбор материала валов24
2. Определение геометрических параметров ступеней валов24
3. Выбор соединений26
4. Предварительный выбор подшипников28
Расчетная схема валов редуктора29
1. Определение реакций в опорах подшипников29
2. Построение эпюр изгибающих и крутящих моментов33
Проверочный расчет подшипников35
1. Определение эквивалентной динамической нагрузки35
2. Определение пригодности подшипников37
Конструктивная компоновка привода39
1. Конструирование червячного колеса и червяка39
3. Смазывание смазывающие устройства41
4. Конструирование корпуса редуктора42
Проверочные расчеты44
1. Проверочный расчет валов44
2. Расчет массы редуктора47
Список использованной литературы48
Приложение 1. Силовая схема нагружения валов редуктора49
Целью данной работы является проектирование привода к качающемуся подъемнику на основании комплексного технического задания. Привод включает в себя электродвигатель соединенный при помощи ремённой передачи с червячным одноступенчатым редуктором который в свою очередь при помощи муфты и цепной передачи соединен с валом исполнительного механизма.
В рамках данной расчетно-графической работы проводится расчет и выбор требуемого электродвигателя проектный расчет редуктора и открытой передачи проверочный расчет редуктора валов расчет подшипников.
Червячный одноступенчатый редуктор предназначен для передачи мощности между валами электродвигателя и исполнительного механизма.
Муфта служит для компенсации неточности установки валов и ограничения нагрузок в приводе.
Ремённая передача служит для передачи движения с увеличением крутящего момента от двигателя на редуктор.
КИНЕМАТИЧЕСКИЙ РАСЧЕТ
1. Выбор электродвигателя
1.1. Мощность на выходе:
где F – грузоподъемность Н; – скорость подъема мс;
1.2. Мощность электродвигателя:
где общ – общий КПД;
1.3. Требуемая частота вращения вала электродвигателя:
где – частота на выходном валу
рзв – шаг тяговой цепи мм z – число зубьев звездочки;
uч – передаточное число червячного редуктора (на данном этапе берется ориентировочно);
uц uр – передаточное число цепной и ременной передач;
Таким образом выбираем двигатель 4АМ80В2У3 (ТУ 16-510.776-81) с характеристиками [табл. К9 1]:
– nном = 2850 обмин.
2. Уточнение передаточных чисел привода
3. Определение вращающих моментов на валах привода
где м = 098 – КПД муфты
РАСЧЕТ ЧЕРВЯЧНЫХ ПЕРЕДАЧ
1. Выбор твердости термообработки и материала колес
Червяк изготавливается из легированной стали 40X (ГОСТ 4543-71) с применением термообработки – улучшения с твердостью 269 302НВ.
Материалы для изготовления зубчатых венцов червячных колес условно делят на 3 группы:
– группа I – оловянные бронзы;
– группа II – безоловянные бронзы и латуни;
– группа III- серые чугуны.
Выбор марки материала червячного колеса зависит от скорости скольжения которая определяется по формуле:
где 2 – угловая скорость тихоходного вала 1с.
При vs ≥ 5 мс выбирается материалы группы I при vs =2 5 мс – группы II а при vs 2 мс – группы III.
Значит выбираем материалы группы II.
Таким образом венец червячного колеса изготавливается из безоловянной бронзы БрА9ЖЗЛ (ГОСТ 613-79) полученной способом центробежного литья.
Термообработка для шестерни и колеса – улучшенная [2].
2. Определение допускаемых контактных напряжений
Поскольку червячное колесо обладает меньшей прочностью следовательно допускаемые контактные напряжения будут определяться именно для него.
Допускаемые контактные напряжения для зубчатого венца червячного колеса в зависимости от материалов зубьев (группы II) и твердости витков червяка (269 302НВ ) определяют по формуле [2]:
3. Определение допускаемых напряжений изгиба
Допускаемые напряжения изгиба для зубчатого венца червячного колеса при реверсивной передаче определяют по формуле [2]:
где KFL – коэффициент долговечности при расчете на изгиб
Nk – эквивалентное число циклов нагружения зубьев червячного колеса за весь срок службы передачи
Nk = 5732Lh причем при N 106 принимают N = 106;
Lh = 5 лет – срок службы привода (ресурс);
Nk = 573434536524 = 109107 циклов;
где Т В – предел текучести и предел прочности при растяжении Нмм2;
В табл. 1 приведены характеристики материалов червячной передачи.
Таблица 1. Механические характеристики материалов червячной передачи
Термообработка способ отливки
4. Проектный расчет редукторной пары
1. Предварительное межосевое расстояние:
где Ka = 610 для эвольвентных червяков;
KH = 05(KH0 + 1) – коэффициент концентрации нагрузки (при переменном нагружении);
число витков червяка в зависимости от передаточного числа uред = 172:
KH = 05(115 + 1) = 1075;
Принимаем aw = 140 мм.
2. Число зубьев колеса:
z2 = z1uред = 2172 = 344;
3. Предварительные значения:
– модуля передачи: m = (14 17)aw z2 = (14 17)14034 = 58 7 мм;
принимаем m = 63 мм;
– коэффициента диаметра червяка: q = 2awm – z2 = 214063 – 34 = 104;
4. Коэффициент смещения:
5. Угол подъема линии витка червяка:
– на делительном цилиндре: ;
– на начальном цилиндре: .
6. Фактическое передаточное число и его отклонение от заданного:
7. Основные геометрические размеры червяка (рис. 2):
– делительный диаметр:
– начальный диаметр:
– длина нарезанной части червяка:
Рис. 2. Геометрические параметры червяка
7. Основные геометрические размеры червячного колеса (рис. 3):
– наибольший диаметр:
где k = 2 для эвольвентного червяка
– ширина венца: b2 = a aw где a = 0355 (при z1 = 2)
b2 = 0355140 = 497 мм.
– радиусы закруглений зубьев:
Rf = 05d1 + 12m = 0563 + 1263 = 391 мм;
Ra = 05d1 – m = 0563 – 63 = 252 мм;
– условный угол обхвата червяка венцом колеса [2]:
Рис. 3. Геометрические параметры червячного колеса
5. Проверочный расчет редукторной пары
5.1. Проверка контактных напряжений зубьев колеса
Скорость скольжения в зацеплении:
Уточнение допускаемого контактного напряжения:
Расчетное контактное напряжение:
где z = 5350 – для эвольвентного червяка;
K = KHV KH – коэффициент нагрузки;
KHV – коэффициент динамической нагрузки учитывающий динамические нагрузки в зацеплении;
– окружная скорость колеса;
при V2 ≤ 3 мс KHV = 1;
KН – коэффициент концентрации нагрузки; учитывает неравномерность распределения нагрузки в зоне контакта вызванную деформациями червяка:
где – коэффициент учитывающий влияние режима работы передачи на приработку зубьев червячного колеса и витков червяка;
– коэффициент деформации червяка определяемый в зависимости от z1 и q; при z1=2 и q=10 =86;
Проверка контактных напряжений зубьев колеса [2]:
при этом допускается недогрузка – не более 15% перегрузка – не более 5%.
Получаем что на 145% т.е. условие выполняется.
5.2. Определение КПД передачи
КПД передачи определяется по формуле [2]:
5.3. Проверка напряжений изгиба зубьев колеса
– окружная сила на колесе равная осевой силе на червяке:
– окружная сила на червяке равная осевой силе на колесе:
Расчетное напряжение изгиба:
где YF2 – коэффициент формы зуба колеса определяемый в зависимости от эквивалентного числа зубьев колеса ;
Проверка напряжений изгиба зубьев колеса [2]:
получаем что т.е. условие выполняется.
При проверочном расчете F получаются меньше []F т.к. нагрузочная способность червячных передач ограничивается контактной прочностью зубьев червячного колеса.
5.4. Проверочный расчет на прочность зубьев червячного колеса при действии пиковой нагрузки
– коэффициент перегрузки [2]
Таким образом получаем что – условие выполняется.
6.1. Мощность на червяке:
6.2. Температура нагрева масла (корпуса) при установившемся тепловом режиме без искусственного охлаждения [2]:
= 03 – коэффициент учитывающий отвод теплоты от корпуса редуктора в металлическую плиту или раму;
[t] раб = 95 – 1100С – максимально допустимая температура нагрева масла;
А = 042 м2 (при aw = 140 мм);
KТ – коэффициент теплоотдачи KT = 12 18 Вт(м2);
принимаем KT = 15 Вт(м2);
т.е. условие выполняется.
РАСЧЕТ РЕМЕННОЙ ПЕРЕДАЧИ
Характеристики выбранного электродвигателя:
– Рном = 22 кВт nном = 2850 обмин.
1.1. Выбор сечения ремня
Тип проектируемой ременной передачи предусмотрен техническим заданием – поликлиновый ремень. Выбор сечения ремня производится по номограмме [1] в зависимости от мощности передаваемой ведущим шкивом (номинальная мощность двигателя Рном) и его частоты вращения (номинальная частота вращения двигателя nном).
Выбранный тип сечения ремня – К.
1.2. Определение минимально допустимого диаметра ведущего шкива
Минимально допустимый диаметр ведущего шкива определяется по табл. [1] в зависимости от вращающего момента на валу двигателя и выбранного сечения ремня:
При типе ремня К и Тдв = 74 Нм dmin = 40 мм.
1.2. Расчетный диаметр ведущего шкива
В целях повышения срока службы ремней рекомендуется применять ведущие шкивы с диаметром на 1 2 порядка выше dmin из стандартного ряда [1].
Принимаем d1 = 180 мм.
1.3. Определение диаметра ведомого шкива:
где u = 2 – передаточное число открытой передачи; = 0015 – коэффициент скольжения [1]; полученное значение округляется до ближайшего стандартного;
d2 =1802(1 – 0015) = 355 мм.
1.4. Определение фактического передаточного числа и его отклонения от заданного:
– условие выполняется.
1.5. Определение ориентировочного межосевого расстояния:
a ≥ 055(d1 + d2) + H где Н=4 мм – высота сечения поликлинового ремня [1];
a ≥ 055(180 + 355) + 4 = 298 мм.
1.6. Определение расчетной длины ремня:
округлив до ближайшего стандартного принимаем l = 1600 мм.
1.7. Уточнение значения межосевого расстояния по стандартной длине:
1.8. Определение угла обхвата ремнем ведущего шкива:
– условие выполняется.
1.9. Определение скорости ремня:
где [] = 40 мс – допускаемая скорость (для поликлиновых ремней);
т.е. – условие выполняется.
1.10. Определение частоты пробегов ремня:
где [U] = 30 с-1 – допускаемая частота пробегов;
Данное соотношение условно выражает долговечность ремня и его соблюдение гарантирует срок службы 1000 5000 ч.
1.11. Определение допускаемой мощности передаваемой одним поликлиновым ремнем с десятью клиньями:
где [Ро] = 256 кВт – допускаемая приведенная мощность передаваемая поликлиновым ремнем с десятью клиньями [табл. 5.5 1];
С – поправочные коэффициенты [табл. 5.2 1]:
Ср = 08 – коэффициент динамичности нагрузки и длительности работы;
Сα = 091 – коэффициент угла обхвата α1 на меньшем шкиве;
[Рп] = 25608091098 = 183 кВт.
1.12. Определение числа клиньев поликлинового ремня:
число клиньев поликлинового ремня определяется в зависисмости от типа сечения ремня [табл. К31 1]:
1.13. Определение силы предварительного натяжения:
1.14. Определение окружной силы передаваемой ремнем:
1.15. Определение силы натяжения ведущей и ведомой ветвей:
сила натяжения ведущей ветви: F1 = F0 + 05Ft = 375 + 05328 = 539 H;
сила натяжения ведомой ветви: F2 = F0 – 05Ft = 375 – 05328 = 211 H.
1.16. Определение силы давления на вал:
2. Проверочный расчет
Проверка прочности ремня по максимальным напряжениям в сечении ведущей ветви:
где – напряжение растяжения
А = 05b(2H– h) – площадь сечения Н = 4 мм h = 235 мм
b = (z – 1)t + 2Fоп = (12 – 1)24 + 235 = 334 мм;
А = 05334(24 – 235) = 944 мм2;
Еи = 80 100 Нмм2 – модуль продольной упругости при изгибе для прорезиненных ремней
– напряжения от центробежных сил
ρ – плотность материала ремня (ρ = 1250 1400 кгмм3 для поликлинового ремня)
[]p – допускаемое напряжение растяжения для поликлинового ремня []p = 8 Нмм2 [1];
НАГРУЗКА ВАЛОВ РЕДУКТОРА
1. Определение сил в зацеплении червячных передач
Схема сил в зацеплении червячной передачи изображена на рис. 4.
) окружная сила на червяке:
окружная сила на колесе:
) радиальная сила на колесе и на червяке:
) осевая сила на червяке:
осевая сила на колесе:
угол профиля червяка в осевом сечении; . [1]
Рис. 4. Схема сил в зацеплении червячной передачи
2. Определение консольных сил
В проектируемом приводе конструируется ременная передача определяющая консольную нагрузку на входном валу:
Кроме того консольная нагрузка вызывается муфтой соединяющей редуктор с рабочей машиной [1]:
3. Силовая схема нагружения валов
Силовая схема нагружения валов имеет целью определить направление сил в зацеплении редукторной пары консольных сил со стороны открытой передачи и муфты реакций в подшипниках а также направление вращающих моментов и угловых скоростей валов.
Направление винтовой линии червяка принято правое.
Направление сил в зацеплении редукторной пары в соответствии с выбранным направлением винтовой линии и вращения валов:
– окружные силы Ft1 и Ft2 направлены так чтобы моменты этих сил уравновешивали вращающие моменты T1 и Т2 приложенные к валам редуктора со стороны двигателя и рабочей машины: Ft1 направлена противоположно вращению червяка а Ft2 – по направлению вращения колеса;
– радиальные силы всегда направлены из точки зацепления к центрам колес;
– направление осевых сил принято по схеме представленной на рис. 4.
Направление консольных сил:
– консольная сила от ременной передачи перпендикулярна оси вала и направлена от ведущего шкива к ведомому;
– консольная сила от муфты FM перпендикулярна оси вала но ее направление в отношении окружной силы Ft на соответствующем валу может быть любым (зависит от случайных неточностей монтажа муфты); поэтому рекомендуется принять худший случай нагружения – направить силу FM противоположно силе Ft что увеличит напряжения и деформацию вала.
Ориентировочное направление реакций в подшипниках быстроходного и тихоходного валов принято противоположным направлению окружных (Ft1 и Ft2) и радиальных (Fr1 и Fr2) сил в зацеплении редукторной пары. Точка приложения реакции – середина подшипника [1].
Силовая схема нагружения валов проектируемого червячного редуктора представлена в прил. 1.
ПРОЕКТНЫЙ РАСЧЕТ ВАЛОВ
1. Выбор материала валов
В проектируемом редукторе для изготовления валов применяется термически обработанная легированная сталь 40Х.
2. Определение геометрических параметров ступеней валов
2.1. Выбор допускаемых напряжений на кручение:
– для быстроходного вала []к = 10 Нмм2
– для тихоходного вала []к = 20 Нмм2.
2.2. Определение геометрических параметров ступеней валов:
– вал-червяк – быстроходный вал (рис. 5):
значение d1 округляется до числа кратного пяти в большую сторону т.к. на первой ступени стоит шкив: d1 = 25 мм;
Рис. 5. Конструкция быстроходного вала червячного одноступенчатого редуктора
) d2 = d1 + 2t где t = 22 мм [табл. 7.1 1] – значение высоты буртика
d2 = 25 + 222 = 294 мм
значение d2 необходимо округлить до числа кратного 5 в большую сторону: d2 = 30 мм;
) d3 = d2 + 32r где r = 2 мм [табл. 7.1 1] – координата фаски подшипника
d3 = 30 + 322 = 364 мм;
значение d3 округляется до числа кратного пяти в большую сторону и принимается равным d3 = 40 мм;
df1 > d3 – условие выполняется;
l4 = T где Т – ширина подшипника.
– вал колеса – тихоходный вал (рис. 6):
значение d1 округляется до числа кратного пяти в большую сторону:
Рис. 6. Конструкция тихоходного вала червячного одноступенчатого редуктора
) d2 = d1 + 2t где t = 28 мм [табл. 7.1 1] – значение высоты буртика
d2 = 45 + 228 = 506 мм
значение d2 необходимо округлить до числа кратного пяти в большую сторону: d2 = 55 мм;
) d3 = d2 + 32r где r = 3 мм [табл. 7.1 1] – координата фаски подшипника
d3 = 55 + 323 = 646 мм;
значение d3 округляется до числа кратного пяти в большую сторону и принимается равным d3 = 65 мм;
) d5 = d3 + 3f где f = 2 мм [табл. 7.1 1] – величина фаски ступицы
d5 = 65 + 23 = 71 мм;
значение d5 необходимо округлить до числа кратного пяти в большую сторону: d2 = 75 мм;
значение l5 определится графически из компоновки.
Для соединения валов с деталями передающими вращающий момент (колесо открытая передача муфта) применяются шпоночные соединения (рис. 7).
Рис. 7. Шпоночное соединение
Используются призматические шпонки изготовленные из чистонатянутой стали с В ≥ 600 Нмм2. Длину шпонки выбирают из стандартного ряда так чтобы она была на 5–10 мм меньше длины ступицы насаживаемой детали. Сечение шпонки выбирается по величине соответствующего диаметра ступени по табл. K42 [1].
3.1. Шпоночное соединение под муфту:
по ГОСТ23360–78 выбирается шпонка 140×9×45 основные размеры которой:
d = 45 мм b = 14 мм h = 9 мм t1 = 55 мм t2 = 38 мм принимаем l = 45 мм.
3.2. Шпоночное соединение под червячное колесо:
по ГОСТ23360–78 выбирается шпонка 180×11×56 основные размеры которой:
d = 65 мм b = 18 мм h = 11 мм t1 = 7 мм t2 = 44 мм принимаем l = 56 мм.
3.3. Шпоночное соединение под шкив:
по ГОСТ23360–78 выбирается шпонка 80×7×25 основные размеры которой:
d = 25 мм b = 8 мм h = 7 мм t1 = 4 мм t2 = 33 мм принимаем l = 25 мм.
4. Предварительный выбор подшипников
Выбор наиболее рационального типа подшипника для данных условий работы редуктора весьма сложен и зависит от целого ряда факторов: передаваемой мощности редуктора типа передачи соотношения сил в зацеплении частоты вращения внутреннего кольца подшипника требуемого срока службы приемлемой стоимости схемы установки.
Выбранный тип подшипников – роликовые конические средней серии схема установки – враспор.
Типоразмер подшипников определяется по величине диаметра внутреннего кольца равного диаметру второй и четвертой ступеней вала под подшипники.
Основные размеры подшипников:
– для быстроходного вала:
№ 7306 (d = 30 мм): D = 72 мм Т = 210 мм b = 19 мм с = 17 мм r = 20 мм r1 = 08 мм α = 14° Сr = 400 кН С0r = 299 кН е = 034 Y = 178 Y0 = 098;
– для тихоходного вала:
№ 7311 (d = 55 мм): D = 120 мм Т = 320 мм b = 29 мм с = 25 мм r = 3 мм r1 = 10 мм α = 13° Сr = 1020 кН С0r = 815 кН е = 033 Y = 1 8 Y0 = 099.
Для роликовых конических подшипников точка приложения реакции смещается от средней плоскости и ее положение определяется расстоянием а измеренным от широкого торца наружного кольца [1].
Точка приложения реакции подшипника:
РАСЧЕТНАЯ СХЕМА ВАЛОВ РЕДУКТОРА
В соответствии с силовой схемой нагружения валов редуктора составляются расчетные схемы валов (рис. 8 – 9).
1. Определение реакций в опорах подшипников
1.1. Быстроходный вал (вал-червяк):
) вертикальная плоскость:
) горизонтальная плоскость:
1.2. Тихоходный вал (вал колеса):
2. Построение эпюр изгибающих и крутящих моментов
2.1. Быстроходный вал (вал-червяк):
) Построение эпюр изгибающих моментов:
а) относительно оси х:
б) относительно оси z:
) Построение эпюры крутящих моментов:
2.2. Тихоходный вал (вал колеса):
ПРОВЕРОЧНЫЙ РАСЧЕТ ПОДШИПНИКОВ
1. Определение эквивалентной динамической нагрузки
Эквивалентная динамическая нагрузка RE учитывает характер и направление действующих на подшипник нагрузок условия работы и зависит от типа подшипника.
Суммарные радиальные реакции опор подшипников вала:
Осевые составляющие радиальной нагрузки подшипников:
где е – коэффициент влияния осевого нагружения [табл. К29 1]
Осевая сила в зацеплении: Fа = 3296 Н.
Осевая нагрузка подшипников:
) Ra1 = Rs1 = 1365 H;
) Ra1 = Rs1 + Fa = 1365 + 3296 = 34325 H.
Эквивалентная нагрузка:
) V – коэффициент вращения при вращающемся внутреннем кольце V = 1;
следовательно эквивалентная нагрузка определится по следующей формуле:
где Kб = 11 – коэффициент безопасности [табл. 9.4 1] KT = 1 – температурный коэффициент [табл. 9.5 1];
) следовательно эквивалентная нагрузка определится по следующей формуле:
где Y = 178 – коэффициент осевой нагрузки [табл. К29 1] Х = 04 (для роликовых конических подшипников) – коэффициент радиальной нагрузки
Таким образом наиболее нагруженным является второй подшипник.
1.1. Тихоходный вал (вал колеса):
где е = 033 – коэффициент влияния осевого нагружения [табл. К29 1]
Осевая сила в зацеплении: Fа = 825 Н.
) Ra1 = Rs1 = 23032 H;
) Ra1 = Rs1 + Fa = 23032 + 825 = 31282 H.
На рис. 8 представлены схемы нагружения подшипников.
Рис. 8. Схема нагружения подшипников
2. Определение пригодности подшипников
Проверочный расчет предварительно выбранных подшипников выполняется отдельно для быстроходного и тихоходного валов. Пригодность подшипников определяется сопоставлением расчетной динамической грузоподъемности Crp с базовой Cr или базовой долговечности L10h с требуемой Lh по условиям:
Crp ≤ Cr или L10h ≥ Lh.
Базовая динамическая грузоподъемность подшипника представляет собой постоянную радиальную нагрузку которую подшипник может воспринять при базовой долговечности составляющей 106 оборотов внутреннего кольца.
Требуемая долговечность подшипника Lh предусмотрена ГОСТ 16162-85 и составляет для червячных редукторов Lh ≥ 5000 ч.
угловая скорость вала:
) расчетная динамическая грузоподъемность определяется по формуле:
где – угловая скорость вала; m = 3333 (для роликовых конических подшипников) – показатель степени L10h = 8000 ч [табл. 9.4 1].
) базовая долговечность:
таким образом L10h > Lh – условие выполняется.
расчетная динамическая грузоподъемность:
Требуемые условия выполняются поэтому предварительно выбранные подшипники пригодны для конструирования подшипниковых узлов.
КОНСТРУКТИВНАЯ КОМПОНОВКА ПРИВОДА
1. Конструирование червячного колеса и червяка
Основные параметры червячного колеса и червяка (диаметр ширина модуль число зубьев и пр.) определены при проектировании передач. Конструкция колеса и червяка зависит главным образом от проектных размеров и материала.
Червяк выполняется заодно с валом.
По условиям работы червячные колеса изготавливают составными: центр колеса (ступица с диском) – из стали зубчатый венец (обод) – из антифрикционного материала.
Основные конструктивные элементы колеса – обод ступица и диск. Обод воспринимает нагрузку от зубьев и должен быть достаточно прочным и в то же время податливым чтобы способствовать равномерному распределению нагрузки по длине зуба. Ступица служит для соединения вала. Длина ее должна быть оптимальной чтобы обеспечить с одной стороны устойчивость колеса на валу в плоскости перпендикулярной оси вала а с другой – получение заготовок ковкой и нарезание шпоночных пазов методом протягивания. Диск соединяет обод и ступицу.
На рис. 9 приведена конструкция червячного колеса.
Размеры конструктивных элементов колеса:
внутренний диаметр:
толщина: S0 = 12S = 12107 = 128 мм
h = 015b2 = 01550 = 75 мм t = 08h = 0875 = 6 мм;
внутренний диаметр: d = d3 = 65 мм;
наружный диаметр: dст = 155d = 15565 = 1008 мм;
толщина: ст = 03d = 0365 = 20 мм;
толщина: С ≥ 025b2 С = 025 50 = 13 мм;
радиус закруглений: R = 10 мм;
отверстия: d0 = 25 мм [1].
Рис. 9. Конструкция червячного колеса
Для соединения выходного конца тихоходного вала с редуктора и приводного вала рабочей машины применена муфта с торообразной оболочкой. Эта муфта обладает достаточной податливостью позволяющей компенсировать значительную несоосность валов.
Материал полумуфт – сталь Ст3 (ГОСТ 380 – 71); материал упругой оболочки – резина с пределом прочности при разрыве не менее 10 Нмм2.
Основной характеристикой для выбора муфты является номинальный вращающий момент Т установленный стандартом [табл. К25 1].
Муфта выбирается по большему диаметру концов соединяемых валов и расчетному моменту Тр который должен быть в пределах номинального:
где Кр = 14 – коэффициент режима нагрузки;
Таким образом выбираем муфту 500 – 1 – 45 – 1 – У2 ГОСТ 20884-82 с номинальным вращающим моментом Т = 500 Нм.
3. Смазывание смазывающие устройства
Смазывание червячных зацеплений применяется в целях защиты от коррозии снижения коэффициента трения уменьшения износа отвода тепла и продуктов износа от трущихся поверхностей снижения шума и вибрации.
3.1. Смазывание червячного зацепления
а) способ смазывания – непрерывное смазывание жидким маслом картерным непроточным способом (окунанием);
б) выбор сорта масла – зависит от значения расчетного контактного напряжения в зубьях и фактической окружной скорости колес [табл. 10.29 1]; выбирается смазочное масло И – Т – Д – 100 (ГОСТ 17479.4 – 87);
в) определение количества масла – объем масляной ванны определяется из расчета 04 08 л масла на 1 кВт передаваемой мощности:
г) определение уровня масла:
hм = (01 05)d1 = (01 05)63 = 63 315 мм;
принимается hм = 20 мм;
д) контроль уровня масла – используется жезловый маслоуказатель т.к. он наиболее удобен для осмотра и конструкция их достаточно надежна;
е) слив масла – при работе передач масло постепенно загрязняется продуктами износа деталей передач с течением времени оно стареет свойства его ухудшаются поэтому масло налитое в корпус редуктора периодически меняют; для этой цели в корпусе предусмотрено сливное отверстие закрываемое пробкой с цилиндрической резьбой;
ж) отдушина – при длительной работе в связи с нагревом масла и воздуха повышается давление внутри корпуса что приводит к просачиванию масла через уплотнения и стыки; чтобы избежать этого внутреннюю полость корпуса сообщают с внешней средой путем установки отдушины в его верхней точке.
3.2. Смазывание подшипников
В проектируемом редукторе для смазывания подшипников применяются жидкие смазочные материалы. Подшипники смазываются из картера в результате разбрызгивания масла колесами образования масляного тумана и растекания масла по валам.
Для подшипников которые требуется защитить от излишнего количества масла применяют внутренние уплотнения [1].
4. Конструирование корпуса редуктора
В проектируемом редукторе принята конструкция разъемного корпуса состоящего из крышки и основания.
Корпус редуктора состоит из стенок бобышек фланцев ребер и других элементов соединенных в единое целое. Корпуса современных редукторов должны иметь строгие геометрические формы: все выступающие элементы следует располагать внутри корпуса по осям валов ребра не ставить фундаментные болты располагать в выемках корпуса так чтобы лапы не выступали за его габариты крышку с корпусом соединять винтами ввертываемыми в корпус верх крышки редуктора делать горизонтальным проушины для подъема и транспортировки редуктора отливать заодно с крышкой.
Толщина стенок корпуса принимается равной не менее 6 мм и определяется по формуле:
Для соединения крышки редуктора с корпусом используются винты с цилиндрической головкой и с шестигранным углублением под ключ по ГОСТ 11738-84 класса прочности 6.8.
Для подъема и транспортировки редуктора на крышке отливают проушины в виде сквозных отверстий в корпусе [1].
1. Проверочный расчет валов
Проверочный расчет валов на прочность выполняют на совместное действие изгиба и кручения.
Цель расчета – определение коэффициентов запаса прочности в опасных сечениях вала и сравнение их с допускаемыми:
s ≥ [s] [s] = 13 21.
1.1. Проверочный расчет быстроходного вала (вал-червяк):
) определение опасных сечений:
опасное сечение – сечение N:
) нормальные напряжения в опасном сечении:
где W – осевой момент сопротивления сечения вала
) амплитуда касательных напряжений:
где Wρ – полярный момент инерции сопротивления сечения вала
) коэффициент концентрации нормальных напряжений:
где K = 205 Kd = 068 KF = 1 Ky = 14 [табл. 11.2 – 11.5 1]
) коэффициент концентрации касательных напряжений:
) пределы выносливости в расчетном сечении вала:
где -1 = 410 Нмм2 – предел выносливости гладких образцов при симметричном цикле изгиба и кручения [табл. 3.2 1]
) коэффициенты запаса прочности по нормальным и касательным напряжениям:
) общий коэффициент запаса прочности в опасном сечении:
получаем что следовательно условие выполняется;
1.2. Проверочный расчет тихоходного вала (вал колеса):
опасное сечение – сечение А;
K = 16 Kd = 070 KF = 1 Ky = 145 [табл. 11.2 – 11.5 1]
получаем что следовательно условие выполняется.
2. Расчет массы редуктора
Масса червячного редуктора определяется по формуле:
где ρ = 7300 кгм3 – плотность чугуна;
φ = 72 – коэффициент заполнения [1];
СПИСОК ИСПОЛЬЗОВАННОЙ ЛИТЕРАТУРЫ
Шейнблит А.Е. Курсовое проектирование деталей машин: Учеб. пособие для техникумов. – М.: Высш. шк. 1991. – 432 с.
Дунаев П.Ф. Леликов О.П. Конструирование узлов и деталей машин: Учеб. пособие для техн. спец. вузов. – 5-е изд. перераб. и доп. – М.: Высш. шк. 1998. – 447 с.
Курсовое проектирование деталей машин: Учеб. пособие для учащихся машиностроительных специальностей техникумов С.А. Чернавский К.Н. Боков И.М. Чернин и др. – 2-е изд. перераб. и доп. – М.: Машиностроение 1988. – 416 с.
Атлас конструкций узлов и деталей машин Под. ред. О.А. Ряховского. – М.: Изд. МГТУ им. Баумана 2005. – 380 с.
ПРИЛОЖЕНИЕ 1. СИЛОВАЯ СХЕМА НАГРУЖЕНИЯ ВАЛОВ РЕДУКТОРА
Силовая схема нагружения валов.dwg

Эпюры.dwg

Рис. 9. Расчетная схема тихоходного вала червячного одноступенчатого редуктора. Построение эпюр изгибающих и крутящих моментов
Компоновка.dwg

ДММ_Спецификация.docx
Стакан маслозащитный
Прокладка регулировочная
Редуктор червячный одноступенчатый
с торообразной оболочкой
Манжета ГОСТ 8752-79
Шпонка ГОСТ 23360 - 78
Рекомендуемые чертежи
- 24.01.2023
- 16.03.2019
- 24.01.2023