Рама передняя автогрейдера ГС 2504




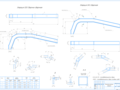
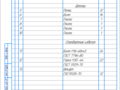
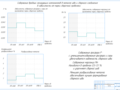

- Добавлен: 24.01.2023
- Размер: 2 MB
- Закачек: 1
Описание
Рама передняя автогрейдера ГС 2504
Состав проекта
![]() |
![]() |
![]() ![]() ![]() ![]() |
![]() ![]() ![]() ![]() |
![]() |
![]() |
![]() ![]() ![]() ![]() |
![]() |
![]() ![]() ![]() ![]() |
![]() ![]() ![]() |
![]() |
Дополнительная информация
исследовательский.cdw

в зависимости от марки сварочной проволоки
Зависимость содержания марганца от
применяемой марки сварочной проволки
Зависимость содержание фосфора и серы от
Меньшее разбрызгивание металла
обеспечивает лучшее формирование
Содержание марганца Мn:
Находится в пределах 0
и упрочняет сварной шов.
Содержание фосфора P :
с уменьшениемсодержания фосфора и серы
увеличивается надежность сварного шва.
Разбрызгивание металла
1 лист.cdw

Операция 045 сварочная
IV - последовательность сварки основных швов
ГОСТ 23518-79-У4-2030
ГОСТ 14771-76-Т1-3080
ГОСТ 14771-76-Т1-30100
- последовательность сборки
Spetsifikatsia3.cdw

дрянь.cdw

моя 211.doc
Курсовой проект предусматривает разработку технологического процесса сборки сварке и контроле качества конструирование средств механизации и автоматизации производства технико-экономический анализ выбранного способа сварки.
Объектом данного курсового проекта является отдельный узел конструкции – передняя рама. Ниже будет рассмотрен базовый вариант технологического процесса с применением полу автоматической сварки который осуществляется непосредственно на производстве. Задачей курсового проекта является анализ базового технологического процесса исследование этого варианта и технико-экономического обоснования.
Итогом этого проекта будет служить альтернативный вариант так называемый проектный вариант технологического процесса который должен устранить недостатки базового варианта.
В настоящее время в промышленности сварка является самым распространенным типом соединения материалов. Сварочное производство развивается бурными темпами в ряде случаев превосходящими темпы роста других процессов металлообработки. Ведущее место в сварочном производстве по-прежнему занимает дуговая сварка которая и в ближайшем будущем останется основным видом сварки плавлением а электродуговая сварка в среде защитных газов или под флюсом является одной из наиболее широко используемых. Такое положение дуговой сварки объясняется высокой концентрацией тепловой энергии универсальностью процесса возможностью сварки в различных условиях и положениях надежностью и относительно низкой стоимостью оборудования стабильностью прочностных характеристик свариваемых соединений сравнительной простотой механизации процесса дуговой сварки.
Техническое описание конструкции рамы автогрейдера
1. Назначение передней рамы и условия её работы
Основная рама выполнена в виде изогнутой выпуклостью вверх хребтовой балки круглого или прямоугольного сечения переходящей в задней части в плоскую конструкцию подмоторной рамы. На подмоторной раме установлены двигатель агрегаты трансмиссии механизмы управления и кабина грейдериста.
Передней частью основная рама опирается при помощи головки на передний мост. Шарнирная связь рамы с мостом позволяет ему наклоняться относительно рамы в вертикальной плоскости.
Задним концом рама опирается на задние оси которые выполняются в виде двух отдельных мостов связанных с основной рамой при помощи балансирной подвески и балансирных тележек поэтому колеса могут менять свое положение в соответствии с неровностями поверхности улучшая проходимость машины.
Силовая передача от двигателя на ходовую часть автогрейдера осуществляется через соединительную муфту коробку передач задний мост и редуктор балансиров. В зависимости от колесной формулы и вида передачи крутящий момент передается от двигателя через механическую или гидромеханическую трансмиссию задним (или всем) колесам.
Ходовая часть автогрейдера состоит из четырех приводных задних пневмоколес и двух приводных или не приводных управляемых передних колес. Задние колеса с каждой стороны машины попарно объединены балансирными балками. Такое соединение позволяет колесам не отрываться от опорной поверхности при наезде одного из колес на препятствия т.е. машина опирается постоянно на все шесть колес независимо от рельефа местности. Для изменения направления движения передние колеса могут поворачиваться в плане с помощью рулевой трапеции. Для повышения устойчивости движения при работе с косо установленным отвалом эти колеса могут отклоняться в боковом направлении.
Рабочий орган – отвал через кронштейны и поворотный круг закрепляют на тяговой раме. Последнюю располагают под хребтовой балкой и соединяют с ней в передней части универсальным шарниром а в задней с помощью гидравлических цилиндров подвешенных к хребтовой балке. Два гидравлических цилиндра работающих независимо один от другого обеспечивают подъем передней части тяговой рамы и ее перекос а гидроцилиндр выноса – ее вынос в сторону от продольной оси автогрейдера. Вращением поворотного круга автогрейдера с жестко закрепленными кронштейнами обеспечивается установка отвала в плане. Благодаря такой подвеске отвал может быть установлен горизонтально или наклонно к вертикальной плоскости под любым углом наклона в плане располагаться в плоскости колеи машины или быть вынесенным за ее пределы быть опущенным ниже уровня поверхности по которой перемещается машина или поднятым над ней.
Конструкция отвала представляет собой жесткую балку коробчатого сечения состоящую из изогнутого по радиусу основного листа усиленного с задней стороны коробкой. Вдоль передней нижней кромки и по торцам к отвалу прикрепляются ножи имеющие обычно двухстороннюю заточку. Это позволяет переворачивать их после износа одной из режущих кромок. По торцам отвала предусматривается возможность установки удлинителей и откосников. Крепление отвала к кронштейнам поворотного круга обеспечивает перестановку его для несимметричного расположения относительно оси поворотного круга и регулировки угла резания
2 Сведения об основном металле
Сталь 09Г2С обеспечивает класс прочности листового широкополосного универсального проката и гнутых профилей при толщине проката от 20 до 160 мм. при толщине от 20 до 32 мм. при толщине от 10 до 20 мм. при толщине до 10 мм. без применения дополнительной упрочняющей обработки.
Прокатка стали. производство стального проката на современном металлургическом заводе осуществляется двумя способами. При первом исходным материалом служат слитки (отлитые в изложницы) которые перерабатываются в готовый прокат обычно в 2 стадии. Сначала слитки нагревают и прокатывают на обжимных станах в заготовку. После осмотра заготовки и удаления поверхностных дефектов (закатов трещин и т.п.) производят повторный нагрев и прокатку готовой продукции на специализированных станах. Размеры и форма сечения заготовки зависят от её назначения: для прокатки листового и полосового металла применяют заготовки прямоугольного сечения шириной 400-2500 мм и толщиной 75-600 мм называемые слябами; для сортового металла - заготовки квадратного сечения размером примерно от 6060 см до 400400 мм а для цельнокатаных труб - круглого сечения диаметром 80-350 мм.
При втором способе применяемом с середины 20 в. прокатка исходной заготовки заменяется непрерывным литьём (разливкой) на специальных машинах. После осмотра и удаления дефектов заготовка как и при первом способе поступает на станы для прокатки готовой продукции. Благодаря применению непрерывно-литой заготовки упраздняются слябинги и блюминги повышается качество проката устраняются потери на обрезку головной части слитка доходящие у слитков спокойной стали до 15-20%.
Верхний пояс балки изготавливается из стали марки 09Г2С.
Сталь09Г2С-низколегированная конструкционнаясталь для сварных работ.09Г2С- сталь свариваемая без ограничений при сварке не требует подогрева и последующей термообработки.
Сталь09Г2С не склонна к отпускной хрупкости.
Сталь09Г2Сиспользуется:
- для производства паровых котлов
- для производства аппаратов и емкостей работающих под давлением при температуре -70 - +450 °С
- для производства сварных листовых конструкций в химическом и нефтяном машиностроении
Заменителями стали09Г2Сявляются марки 09Г209Г2Т09Г2ДТ а так же 10Г2С.
Химический состав и физикотехнические свойства стали 09Г2С приведены в таблице 1 и 2 соответственно.
Химический состав Таблица 1:
Механические свойства стали 09Г2С при Т=20С
Механические свойства стали 09Г2С при Т=20С Таблица 2
Возможность сварки тех или иных металлов можно определить исходя из анализа их свариваемости. Для стали 09Г2С необходимым и достаточным является определение эквивалентного содержания углерода. Чем выше эквивалентное содержание углерода тем свариваемость ниже [3].
Эквивалентное содержание углерода можно определить по следующей зависимости(1):
Так как 0398 СЭкв 045 (для низколегированных сталей) стали марки 09Г2С относятся ко второй группе [3]. К этой группе относят преимущественно стали при сварке которых в нормальных производственных условиях трещины не образуются. В данном случае при использовании стали 09Г2С предварительный подогрев и последующая термообработка не требуется.
3. Анализ конструктивного оформления сварных соединений и сопряжений
В конструкции для сварки верхнего пояса используется тавровое соединение.
При сварке верхнего пояса используются тавровые соединения сваренные по ГОСТ 14771-76 общая протяженность шва L=789+48456мм односторонний без скоса кромок шов сваривается в нижнем положении «в лодочку».
В конструкции для сварки нижнего пояса используется угловое соединение.
При сварке верхнего пояса используются угловые соединения сваренные по ГОСТ 14771-76 общая протяженность шва L=789+48456мм односторонний без скоса кромок шов сваривается в нижнем положении «в лодочку»
Конструктивное оформление шва Таблица 3
Протяженность шва мм
4. Характеристика технологичности сборочной единицы
Под технологичностью понимают выбор таких материалов размеров деталей которые обеспечивают высокие эксплуатационные качества сварных конструкций при экономичном производстве.
Отношение массы наплавленного металла к массе всей конструкции.
где Qн –масса наплавленного металла
Q – масса сварной конструкции
Конструкция считается технологичной если показатель m не превышает 2% [5].
Кроме показателя m используется оценка по непрямым признакам:
анализ конструкции изделия;
оценка свариваемости;
анализ сварных соединений;
анализ площади шва ;
анализ траектории швов;
простота сборочной единицы или возможность разбивки на узлы при сборке.
При изготовлении хребтовой балки используют сталь 09Г2С которая в производственных условиях сваривается без ограничений без дополнительной термообработки и не склонная к образованию трещин.
Сварка верхнего пояса производится непрерывными швами. Следовательно соединение лишено недостатков прерывистого шва таких как снижение механических свойств наплавленного металла в месте возбуждения и обрыва дуги возникновение концентраторов напряжения в начале и в конце каждого участка шва которые снижаю прочность и могут стать причиной возникновения трещин. Сварка может выполняться в автоматическом режиме различными способами что дает высокую производительность процесса повышает качество изделия и снижает трудоемкость.
Обзор литературных данных
При изготовлении сварных балок элементы балки собираются последовательно из отдельных листов и свариваются полуавтоматами или автоматами с использованием специальных или специализированных кондукторов стендов или установок.
Сварка балок в зависимости от программы выпуска материала и конструкции выполняется следующими способами: ручной дуговой сваркой механизированной сваркой в среде защитных газов или смеси защитных газов а также автоматической сваркой под слоем флюса. Сварка может производится как проволокой сплошного сечения так и порошковой проволокой.
Сварка балок в ручную производится электродами Э42 или Э42А в направлении от середины к концам участка обратно-ступенчатым способом. Сварка балочных конструкций коробчатого сечения при толщине соединяемых элементов 3- 8 мм и длине швов 05 – 5 м выполняется полуавтоматов в углекислом газе
Технические условия на изготовление узла
Материалы применяемые для изготовления новых металлоконструкций балки хребтовой на переднюю раму должны соответствовать указаниям УК36.24.12-100-92. Содержание углерода в сталях не должно превышать 022%.
Металл для изготовления Таблица 4
Марка стали категория
Технические требования
2 Обработка основного материала и изготовление заготовок
Перед подачей в производство прокат должен быть просушен очищен от загрязнений и выправлен. Прокат обрабатывают без предварительной правки т.к. отклонение от геометрических правильных форм в нем не превышает: зазор между листом и стальной линейной длиной 1 м для толщины листа 20 мм – (15 20) мм. Правка проката осуществляется на вальцах прессах или других устройствах обеспечивающих плавность приложения нагрузок при правке мелких деталей допускается на плите через гладилку.
Поверхность проката после правки не должна иметь вмятин забоин и других повреждений. Качество поверхности после правки должно отвечать требованиям соответствующих Госстандартов на прокат.
Правка проката наплавкой валиков сваркой не разрешается. Прокат с дефектами поверхности в виде расслоений трещин пузырей и чешуйтости для изготовления металлоконструкций не допускается.
Вырезки заготовок элементов металлоконструкций из проката допускается любым способом резки.
Кромки заготовок деталей должны быть очищены от грата шлака брызг и наплывов металла. Не иметь зарезов в целом занимающих более 20% общей длины кромки. Длина одного зареза допускается не более 150 мм глубина – не более 2 мм. Непрямолинейность реза более 1 мм и наплавы металла должны быть удалены и зачищены механическим способом.
Предельные отклонения размеров при обработки кромок под сварку:
- плоскости кромок от прямого угла стыковых соединений без скоса кромок (-5 +5)0 для тавровых (-5 +5)0 для нахлесточных (-6 +6)0.
- угла разделки величины притупления для РДС – по ГОСТ 5264-80 Аг и Пф – ГОСТ 14771-76 и по ГОСТ 8713-79 соответственно.
При изготовлении деталей металлоконструкции должна учитываться усадка вызываемая наложением сварных швов. Величина припуска при сварке листов встык должна быть равна 01 толщины свариваемых деталей на каждый стык.
Если размеры листового проката не позволяют изготовить детали целиком они могут выполняться составным или из нескольких частей.
Разметку заготовок элементов металлоконструкции проводить с соблюдением следующих требований:
Длина пристыкованного элемента должна быть не менее 15b (b – толщина листа) но не менее 150 мм.
)Стыки поясов должны быть смещены по отношению к стыкам стенок не менее чем на 150 мм.
3 Сборка передней рамы
При сборке под сварку должна быть обеспечена точность сборки деталей в пределах размеров и допусков установленных рабочими чертежами. Для обеспечения требуемой точности сборки следует применять специальные сборочно-сварочные приспособления которые должны исключать возможность деформаций и не затруднять выполнение сварочных работ и переносные сборочные приспособления – обычно универсальные приспособления применяемые для сборки разнообразных изделий.
Приспособления применяемые при сборке под сварку периодически проверяются ОТК предприятия. Принудительная пригонка деталей и элементов нарушающая конструктивные формы предусмотренные чертежом запрещается.
Свариваемые кромки и прилегающие к ним зоны металла шириной не менее 20 мм перед сборкой должны быть очищены от ржавчины грязи масла влаги и др. Зачистку можно производить любыми способами обеспечивающими требуемое качество.
При сборке конструкций под сварку деталь устанавливают таким образом чтобы обеспечить возможность выполнения сварных швов преимущественно в нижнем положении.
Прихватка элементов сварных соединений при сборке должна выполняться сварщиком той же квалификации что и при сварке с использованием тех же сварочных материалов. Прихватки необходимо размещать в местах расположения сварных швов. По окончании сборочных работ швы прихваток и места под сварку должны быть зачищены от шлака окалины брызг. При сборке под сварку в начале и конце стыковых швов должны как правило устанавливаться выводные планки.
Металл при сварке должен быть защищен от сварочных брызг. Дефектные места в швах сварных соединений металлоконструкций должны исправляться заваркой.
Места подготовленные под сварку и заварку должны быть приняты работником технического контроля.
4 Сварка конструкции
Сварку металлоконструкции необходимо производить в соответствии с требованиями технологического процесса. К выполнению сварочных работ должны допускаться сварщики выдержавшие испытания в соответствии с «Правилами аттестации сварщиков» Госгортехнадзора. Способ сварки должен соответствовать указанному в чертеже на конкретное сварное соединение. Для всех способов сварки рекомендуется применять источники питания постоянного тока.
Во избежание создания в металлоконструкциях реактивных напряжений при сварке рекомендуется в первую очередь выполнять в свободном состоянии стыковые соединения и в последнюю очередь – угловые и тавровые.
Сварные соединения несущих элементов металлоконструкции должны иметь клеймо позволяющее установить фамилию сварщика в процессе эксплуатации изделия. Сварочные работы должны выполняться с обеспечением требований по технике безопасности действующих на предприятии.
Перед сваркой необходимо очистить сварочную проволоку от грязи и ржавчины; электроды и флюс просушить и прокалить места под сварку в деталях очистить от случайных загрязнений по 20-30 мм в обе стороны от шва. По окончании сварки швы и прилегающие к ним з оны должны быть зачищены от шлака брызг и натека металла а выводные планки удалены термической резкой.
5 Контроль качества сварных соединений
Сварные конструкции контролируют на всех этапах их изготовления. Кроме того систематически проверяют приспособления и оборудование. Одним из таких видов контроля является магнитная дефектоскопия. Основы метода заключаются в том что в намагниченном изделии магнитный поток встречая препятствия с малой магнитной проницаемостью (трещины неметаллические включения) рассеивается и если упомянутые препятствия (дефекты) расположены неглубоко то на поверхности изделия в месте выхода силовых линий создается магнитная поляризация которая может быть обнаружена специальными магнитными индикаторами (например частицы ферромагнитных веществ и в частности окислы железа). Наиболее интенсивное рассеивание силовых линий происходит при направлении магнитного потока перпендикулярно направлению дефекта что необходимо учитывать при намагничивании изделия. В зависимости от магнитных свойств материала контролируемого изделия применяются два метода контроля. Контроль состоит из трех этапов:
). намагничивание исследуемого объекта;
). нанесение индикаторной среды и регистрация имеющихся на его поверхности дефектов;
). размагничивание объекта.
Чувствительность метода зависит от качества намагничивания и свойств дисперсной среды суспензии -- величины и формы частиц ферромагнитного порошка а также его магнитных свойств.
С помощью магнитного порошкового метода контроля можно выявлять поверхностные дефекты в виде трещин с шириной раскрытия 0001--003 и глубиной 001--004 мм. Контроль качества сварных соединений осуществляется так же визуальным осмотром и замером швов.
Планирование технологического процесса сборки и сварки заданного изделия
1. Выбор способа изготовления заготовок
Резка металла является одной из наиболее трудоемких и сложных операций. Она может быть как заготовительной так и окончательной операцией. В зависимости от типа производства вида и размеров погонки профиля проката и конфигурации линии реза применяют тот или иной метод резки.
Основными видами резки металла являются: плазменная лазерная и газопламенная резка.
Газопламенную резку применять не целесообразно в связи с относительно не большой толщиной металла и низким качества реза.
Лазерная резка металла. Сфокусированное лазерное излучение позволяет разрезать почти любые материалы независимо от их теплофизических свойств. При этом можно получать качественные и узкие резы (шириной 01–1 мм) со сравнительной небольшой зоной термического влияния. При лазерной резке возникают минимальные деформации как временные в процессе обработки заготовки так и остаточные после ее полного остывания. В результате возможна резка с высокой степенью точности в том числе нежестких и легкодеформируемых изделий. Благодаря относительно несложному управлению лазерным пучком можно выполнять автоматическую обработку плоских и объемных деталей по сложному контуру.
Лазерная резка особенно эффективна для стали толщиной до 6 мм обеспечивая высокие качество и точность при сравнительно большой скорости разрезания. Однако для металла толщиной 20–40 мм она применяется значительно реже кислородной или плазменной резки а для металла толщиной свыше 40 мм – практически не используется.
Плазменная резка металла. при правильном использовании она существенно повысит производительность работ уступая в скорости лишь промышленной лазерной сварке но при этом обходясь в разу дешевле. Лучше всего применять плазморезы толщиной до 60 мм. Кроме того плазменная резка универсальна и подходит к самым разным металлам.
Ширина реза при этом обеспечивается минимальная и очень чистая: не образуется ни наплывов ни грата и перекаливания края почти не нужно производить дополнительную обработку. Тепловая деформация деталей очень небольшая даже тогда когда металлический лист совсем тонкий. В сравнении с лазерной резкой он является более дешовым
В связи с тем что годовой выпуск балок не велик то плазма является основным видом резки металла на предприятии
2 Расчёт режима сварки.
Расчет сварочного тока производится по формуле:
Рассчитываем напряжение
Скорость подачи электродной проволоки определяется по формуле:
f- коэффициент потерь металла на угар и разбрызгивание принимается равным 0.02 – 0.03
Скорость сварки рассчитывается по формуле
3 Выбор способа сварки
На заводе-изготовителе прихватка осуществляется ручной дуговой сваркой. Но из за плохого качества и формирования швов прихватку целесообразно применять полуавтоматической сваркой в углекислом газе. При полуавтоматической сварке сварочные швы имеют большую прочность пластичность и ударную вязкость чем при ручной дугой сварке.
При изготовлении балки используется низколегированная сталь марки 09Г2С. Швы верхнего пояса балки производятся полу - автоматической сваркой самозащитной порошковой проволокой диаметр сварочной проволоки 22 мм.
В процессе полуавтоматической сварки в зону сварки одновременно подается электродная проволока и специальный газ например аргон или углекислый газ который защищает свариваемый металл от окружающей среды. Это самый производительный вид сварки который позволяет повысить эффективность работы сварщиков в среднем в три раза за счет облегчения поджига дуги большего удобства и скорости работы отсутствия необходимости менять электроды и зачищать швы. Сварочные аппараты применяемые для этого вида сварки называется полуавтоматами.
Полуавтомат сварочный значительно превосходит по своим характеристикам сварочный аппарат для дуговой сварки. Не стоит забывать что от качества сварки в большой мере зависят технические характеристики и надежность сварной металлоконструкции. Именно поэтому полуавтоматическая сварка получила очень широкое распространение.
Сегодня рынок предлагает огромное количество полуавтоматов от различных производителей. Полуавтоматы могут быть выполнены в виде переносного оборудования и стационарных комплексов. Следует отметить что современные сварочные полуавтоматы отличаются высокой надежностью универсальностью позволяют работать быстро и при этом достаточно мобильны и компактны.
Полуавтоматическая сварка часто оказываются выгоднее автоматической и ручной сварки. Они пригодны для сварки металла толщиной от 2-3 мм до самых больших толщин встречающихся на практике для сварки всех видов стыковых швов - одно- и двусторонних со скосом и без скоса кромок угловых швов в тавровом и нахлесточном соединениях а также и прорезных швов. Шланговыми полуавтоматами можно выполнять не только сплошные но и прерывистые швы; они успешно применяются как в заводских так и в полевых условиях на открытом воздухе например при сварке стыков трубопроводов при сооружении строительных металлоконструкций каркасов высотных зданий и т. д.
Различие между автоматами и шланговыми полуавтоматами довольно условно. Установив неподвижно держатель полуавтомата и перемещая под ним изделие прямолинейно или вращая его получают дуговой автомат. Существуют шланговые автоматы; в них проволока из шланга поступает не в ручной держатель а в компактную самоходную сварочную головку перемещающуюся по линии сварки.
4 Выбор сварочного оборудования
Большое значение при сварке имеет сварочное оборудование которое должно обеспечивать высокое качество сварного соединения. Для выполнения сварки существуют различные виды источников питания: генераторы трансформаторы выпрямители. Традиционным источником переменного тока является сварочный трансформатор. Источником постоянного тока является выпрямитель который сконструирован на базе трансформатора и полупроводникового выпрямителя. Широкое распространение получили также инверторные источники тока которые применяются для сварки как на переменном так и на постоянном токе. Требования к виду внешних характеристик определяется такими показателями сварочного процесса как тип электрода (плавящийся неплавящийся); характер среды в которой происходит сварка (открытая дуга под флюсом в защитных газах); степень механизации (ручная механизированная автоматическая сварка); способ регулирования режима горения дуги (саморегулирование автоматическое регулирование напряжения дуги). При механизированной сварке в среде СО2 и при автоматической сварке под флюсом при постоянной скорости подачи электродной проволоки применяют источники питания с жесткими вольтамперными характеристиками (ЖВХ). В этом случае источник питания работает как регулятор рабочего напряжения которое регулируется в заданных пределах при условии заданной величины силы сварочного тока. Регулирование напряжения при ЖВХ может быть плавным ступенчатым и смешанным. Величина сварочного тока определяется скоростью подачи электродной проволоки а источник питания задает напряжение дуге и обеспечивает саморегулирование длины дуги.
Рассмотрим их характеристики и назначение.
Сварочный полуавтомат ПДГ-525 укомплектован универсальным сварочным выпрямителем ВДУ-506 обеспечивающим получение не только жестких но и падающих внешних характеристик что позволяет путем замены только сварочной горелки приспособить полуавтомат для сварки под флюсом. Полуавтоматическая сварка осуществляется унифицированными сварочными горелками соединенными с механизмом подачи трехметровым шлангом с помощью быстродействующих разъемов. Наконечники сопла разъемы и другие элементы сварочных горелок унифицированы между собой что позволяет в процессе эксплуатации легко выбрать и использовать наиболее удобную в данных условиях сварочную горелку. Полуавтомат обеспечивают повышение производительности труда не только благодаря возможности вести сварку на форсированных режимах (при больших скоростях подачи проволоки) и импульсной дугой но также благодаря сокращению затрат на подготовительно-заключительные и вспомогательные операции и обслуживание оборудования
Технические характеристики ПДГ – 525 Таблица 5
Напряжение питания (50Гц)
Потребляемая мощность не более
Номинальный сварочный ток при ПВ=60%
Номинальный сварочный ток при ПВ=100%
Пределы регулирования сварочного тока
Напряжение холостого хода
Пределы рабочего напряжения
Диаметр сплошной электродной проволоки
Диаметр порошковой электродной проволоки
Пределы регулирования скорости подачи
Количество подающих роликов
- механизм подачи проволоки
0х235х440475х180х330
Выпрямитель сварочный типа ВДУ-506 предназначен для ручной дуговой сварки покрытыми электродами на постоянном токе комплектации полуавтоматов и автоматов для сварки изделий из стали в среде защитных газов на постоянном токе. Является регулируемым тиристорным выпрямителем с жесткой или падающей внешней характеристикой широко известен и имеет одну из самых высоких сварочных характеристик в своем классе.
Технические характеристики ВДУ – 506 Таблица 6
Напряжение питания В
Номинальная потребляемая мощность кВА
Частота питания сети Гц
Номинальный сварочный ток А (ПВ ПН %)
Пределы регулирования сварочного тока А
Рабочее напряжение В:
Напряжение холостого хода не более В
Диаметр штучных электродов мм
Потребляемая мощность кВА не более
Сварочный полуавтомат ПДГ-508 - мощный полуавтомат с широким диапазоном регулирования сварочных параметров. Предназначен для сварки сплошной проволокой малоуглеродистой и низколегированной стали в защитной среде углекислого газа а также легированных и нержавеющих (коррозионностойких) сталей в среде аргона.
Номинальное напряжение питающей сети 50ГцВ
Номинальный сварочный ток: при ПВ=60% и цикле сварки 5 мин А
Расход защитного газа лч
Диаметр электродной проволоки мм
Пределы регулирования скорости подачи электродной проволоки мч
Регулирование скорости подачи электродной проволоки мч
Габаритные размеры подающего устройства мм
Масса подающего устройства кг
Выбираем полуавтомат ПДГ-508 т.к. он занимает меньше производственной площади экономически выгоден подходит по техническим параметрам и режимам сварки и может обеспечить требуемое качество сварного соединения.
5 Выбор сварочных материалов
В соответствии с разработанной технологией сварки (п.4.2 стр.17) произведем выбор порошковой проволоки для сварки стали 09Г2С. Рассмотрим следующие марки проволоки ПП-АН1 и ПП-АН8.
Проволока ПП-АН8. Предназначена для механизированной и автоматической сварки в углекислом газе конструкций из низкоуглеродистых и- низколегированных сталей. Проволокой 25 и 3мм могут выполняться швы в нижнем положении диаметром 2мм - горизонтальные швы на вертикальной плоскости. Проволока предназначена для заводских условий но возможна сварка и на строительных площадках. Однако во всех случаях место сварки должно быть защищено от ветра сквозняков и осадков. Минимальная толщина свариваемого металла - 3мм.
Проволока ПП-АН8 малочувствительна к ржавчине дает весьма плотные швы стойкие против образования горячих трещин. Существенным недостатком порошковой проволоки является обеспечение защиты зоны сварки от взаимодействия с воздухом. Проволока ПП-АН1 более чувствительна к коррозии чем ПП-АН8.
Проволока ПП – АН8 Обладает повышенной стойкостью к порообразованию и трещиностойкостью. Стабильность дуги высокая. Отделимость шлака хорошая.
Химический состав Таблица 6
В следствии вышеперечисленного оставляем проволоку ПП-АН8 т.к. она более производительна имеет меньше вредных вещест по сравнению с ПП-АН8.
Разработка маршрутного технологического процесса.
Маршрутная карта сборки и сварки изделия Таблица 7
Наименование и содержание операции
Сварочное оборудование и сварочные приспособления установки
Норма штучного времени
Кран мостовой П4-00-40 комплект инструмента №2 ТИ 39047250910001.
Кран мостовой П4-00-40
Плита УПТ-287 Комплект инструментов №3 ТИ 39047250910001
0 Сборочно-сварочная
Кран мостовой П4-00-40 Псварочный А-1197 Комплект инструментов№10 ТИ 39047250910001
Сварка основного шва
Павтомат сварочный А-1197 ВДМ-1201 сборочно-сварочный стенд
Кантователь ПС25-136
Проектирование и техническое описание приспособления для сборки
В процессе изготовления сварных конструкций должны быть обеспечены заданные технологическим процессом взаимное положение соединяемых деталей и условия наиболее благоприятные для образования качественного соединения. Это достигается применением технологических приспособлений и оснастки. Сварочные приспособления должны допускать свободное перемещение отдельных элементов конструкции вследствие нагрева и последующего остывания зоны сварки а при необходимости уменьшить или по возможности исключить деформации возникающие в сварном изделии и в самом приспособлении вследствие температурных воздействий. При сварке крупногабаритных конструкций обладающих малой жесткостью (рамные решетчатые листовые) приспособления должны обеспечивать фиксацию отдельных свариваемых кромок а не всего изделия в целом. При проектировании приспособления необходимо предусмотреть доступ к местам сварки и прихватки быстрый отвод теплоты от мест интенсивного нагрева сборку узла с минимального числа установок свободный доступ для проверки размеров изделия и свободный съем собранного или сваренного изделия. Прижимы. Это элементы приспособлений обеспечивающие прижимы деталей к фиксаторам или другим несущим поверхностям приспособлений. Различают прижимы механические пневматические магнитные и гидравлические. Механические прижимы являются наиболее простыми и поэтому наиболее распространенными. Пневматические прижимы по сравнению с механическими имеют ряд существенных преимуществ в том числе быстродействие возможность управления рядом прижимов с одного места возможность подвода сжатого воздуха к прижимам занимающим различное положение в пространстве (через цапфу приспособления или по гибким шлангам) и т. д. Пневматический прижим обладает определенной упругостью что компенсирует деформации свариваемых деталей
Для сборки передней рамы необходимо сварить 4 стальных листа.
Организация контроля качества
Под контролем качества продукции принято понимать проверку соответствия показателей продукции установленным требованиям которые могут быть зафиксированы в стандартах чертежах технических условиях договорах о поставке паспорте изделия и в других нормативных документах. В настоящее время на предприятии применяют различные виды контроля качества отличающиеся по методу исполнения. Входной контроль - контроль потребителем исходных основных и сварочных материалов комплектующих изделий. Такой вид контроля позволяет предупредить образование дефектов из-за ошибок поставщика. Операционный контроль-это контроль технологического процесса сварки выполняемый после завершения определенной операции. Приемочный контроль-это контроль готового сварного соединения после завершения всех технологических операции по его изготовлению. По результатам такого контроля принимается решение о пригодности конструкции к эксплуатации. Существует два метода контроля качества сварного соединения: - неразрушающий; - разрушающий. Рассмотрим неразрушающий вид контроля к нему относят визуально-оптический метод УЗК рентген контроль магнитные методы испытание на герметичность.
Визуально оптический метод. Внешний осмотр - наиболее распространенный и доступный вид контроля не требующий материальных затрат. Данному контролю подвергают все виды сварных соединений несмотря на использования дальнейших методов. При внешнем осмотре выявляют практически все виды наружных дефектов. При этом виде контроля определяют непровары наплывы подрезы и другие дефекты доступные обозрению. Внешний осмотр выполняют невооруженным глазом или используют лупу с 10-ти кратным увеличением. Внешний осмотр предусматривает не только визуальное наблюдение но и обмер сварных соединений и швов а также замер подготовленных кромок. В условиях массового производства существуют специальные шаблоны позволяющие с достаточной степенью точности измерить параметры сварных швов.
Радиационный контроль. Этот метод контроля позволяет обнаружить в полости шва дефекты невидимые при наружном осмотре. Сварной шов просвечивают рентгеновским или гамма-излучением проникающим через металл для этого излучатель (рентгеновскую трубку или гамма - установку) размещают напротив контролируемого шва а с противоположной стороны - рентгеновскую пленку установленную в светонепроницаемой кассете. Лучи проходя через металл облучают пленку оставляя в местах дефектов более темные пятна так как дефектные места обладают меньшим поглощением. Рентгеновский метод более безопасен для работающих однако его установка слишком громоздка поэтому он используется только в стационарных условиях. Гамма - излучатели обладают значительной интенсивностью и позволяют контролировать металл большей толщины. Благодаря портативности аппаратуры и дешевизне метода этот тип контроля широко распространен в монтажных организациях. Но гамма-излучение представляет большую опасность при неосторожном обращении поэтому пользоваться этим методом можно только после соответствующего обучения. К недостаткам радиографического контроля относят тот факт что просвечивание не позволяет выявить трещины расположенные не по направлению основного луча. Этот метод не подходит для контроля качества данной конструкции так как он трудоемкий сложный в исполнении вреден для человека.
Магнитный контроль. При этом методе контроля дефекты швов обнаруживают рассеиванием магнитного поля. Для этого к изделию подключают сердечник электромагнита или помещают его внутрь соленоида. На поверхность намагниченного соединения наносят железные опилки окалину и т.д. реагирующие на магнитное поле. В местах дефектов на поверхности изделия образуются скопления порошка в виде направленного магнитного спектра. Чтобы порошок легко перемещался под воздействием магнитного поля изделие слегка постукивают придавая мельчайшим крупинкам подвижность. Поле магнитного рассеивания можно фиксировать специальным прибором называемым магнитографическим дефектоскопом. Качество соединения определяют методом сравнивания с эталонным образцом. Простота надежность и дешевизна метода а главное его высокая производительность и чувствительность позволяют использовать его в условиях строительных площадок в частности при монтаже ответственных трубопроводов.
Из вышеперечисленных методов контроля наиболее актуально применение визуально оптического так как является оперативным информативным дешевым и обеспечивает получение сварных соединений требуемого качества
Организация рабочего места
Правильное размещение оборудования является основным звеном в организации безопасной работы производственного участка и цеха. При размещении оборудования необходимо соблюдать установленные минимальные разрывы между станками между станками и отдельными элементами здания правильно определять ширину проходов и проездов. Невыполнение правил и норм размещения оборудования приводит к загромождению помещений и травматизму. Расположение оборудования на площади цеха или участка определяется в основном технологическим процессом и местными условиями. Проходы и проезды требуется содержать в чистоте и порядке границы их обычно отмечаются белой краской или металлическими светлыми кнопками. Ширина рабочей зоны принимается не менее 08 м. Расстояние между оборудованием и элементами зданий а также размеры проходов и проездов определяются нормами технологического проектирования механических и сборочных цехов машиностроительных заводов. Рабочее место является первичным звеном производства оно представляет собой определенный участок производственной площади цеха предназначенный для выполнения одним рабочим (или бригадой) порученной работы специально приспособленный и технически оснащенный в соответствии с характером этой работы. От того насколько правильно и рационально будет организовано рабочее место зависит безопасность и производительность труда. Как правило каждое рабочее место оснащено основным и вспомогательным оборудованием и соответствующим инструментом. Отсутствие на рабочем месте удобного вспомогательного оборудования или нерациональное его расположение захламленность создают условия для возникновения травматизма. Мероприятия по улучшению организации рабочих мест заключаются в рационализации трудовых движений и соответствующем оборудовании рабочего места. Технологический процесс не должен допускать непроизводительных и опасных трудовых движений и тем более опасных поз рабочего. 5.2 Организации рабочих мест и НОТ на участке Пространство в котором совершается основная часть трудовых движений сравнительно невелико. Исследования показывают что наиболее благоприятная зона для работ сидя определяется площадкой в 01 м2 когда предплечье поворачивается в локтевом суставе (руки полусогнуты). Другие зоны например работа с помощью полностью вытянутых рук менее благоприятны и вызывают быструю утомляемость. При работе стоя благоприятная зона также невелика. Осуществляя рационализацию трудовых движений необходимо стремиться к обеспечению коротких и наименее утомительных движений. Следует помнить: чем больше сочленений участвуют в выполнении движения тем оно как правило требует большей затраты сил. Поэтому при планировке рабочих мест и в частности при расстановке предметов организационно-технической оснастки необходимо предусматривать применение наиболее простых движений: движения одних пальцев движения пальцев и запястья или движения пальцев запястья и предплечья. Следует по возможности устранять такие движения которые требуют участия не только плеча но и всего корпуса. При размещении на рабочем месте организационно-технической оснастки (стеллажей для заготовок и готовых деталей инструментальной тумбочки планшетов и пр.) или вспомогательного оборудования (поворотные краны транспортеры и пр.) следует тщательно проверить по зонам досягаемости рук насколько рационально установлен тот или иной предмет и какие виды движений будет при этом применять рабочий. Однако решение этой задачи не должно приводить к сближению оборудования так как в противном случае рабочее место будет стеснено и вероятность возникновения травматизма увеличится. На практике используя опыт новаторов производства и соответствующие нормы при расстановке вспомогательного оборудования и оснастки следует придерживаться такого принципа: заготовки и полуфабрикаты располагать на специальных стеллажах с левой стороны от рабочего измерительный инструмент и тару для готовых деталей — с правой. Предметы которыми пользуется рабочий чаще располагают ближе к станку Планировка рабочего места зависит от многих условий — от типа оборудования конфигурации и габаритов деталей применяемой технологии организации обслуживания но для аналогичных работ можно установить типовые рациональные планировки рабочих мест. Следует отметить что основное и вспомогательное оборудование не должно выходить за пределы площадки отведенной для данного рабочего места и устройство рабочего места должно учитывать рост и другие антропометрические данные каждого рабочего.
Пространство в котором совершается основная часть трудовых движений сравнительно невелико. Исследования показывают что наиболее благоприятная зона для работ сидя определяется площадкой в 01 м2 когда предплечье поворачивается в локтевом суставе (руки полусогнуты). Другие зоны например работа с помощью полностью вытянутых рук менее благоприятны и вызывают быструю утомляемость. При работе стоя благоприятная зона также невелика. Осуществляя рационализацию трудовых движений необходимо стремиться к обеспечению коротких и наименее утомительных движений. Следует помнить: чем больше сочленений участвуют в выполнении движения тем оно как правило требует большей затраты сил. Поэтому при планировке рабочих мест и в частности при расстановке предметов организационно-технической оснастки необходимо предусматривать применение наиболее простых движений: движения одних пальцев движения пальцев и запястья или движения пальцев запястья и предплечья. Следует по возможности устранять такие движения которые требуют участия не только плеча но и всего корпуса. При размещении на рабочем месте организационно-технической оснастки (стеллажей для заготовок и готовых деталей инструментальной тумбочки планшетов и пр.) или вспомогательного оборудования (поворотные краны транспортеры и пр.) следует тщательно проверить по зонам досягаемости рук насколько рационально установлен тот или иной предмет и какие виды движений будет при этом применять рабочий. Однако решение этой задачи не должно приводить к сближению оборудования так как в противном случае рабочее место будет стеснено и вероятность возникновения травматизма увеличится. На практике используя опыт новаторов производства и соответствующие нормы при расстановке вспомогательного оборудования и оснастки следует придерживаться такого принципа: заготовки и полуфабрикаты располагать на специальных стеллажах с левой стороны от рабочего измерительный инструмент и тару для готовых деталей — с правой. Предметы которыми пользуется рабочий чаще располагают ближе к станку Планировка рабочего места зависит от многих условий — от типа оборудования конфигурации и габаритов деталей применяемой технологии организации обслуживания но для аналогичных работ можно установить типовые рациональные планировки рабочих мест. Следует отметить что основное и вспомогательное оборудование не должно выходить за пределы площадки отведенной для данного рабочего места и устройство рабочего места должно учитывать рост и другие антропометрические данные каждого рабочего.
Техника безопасности труда
Для изучения факторов влияющих на условия труда рассмотрим взаимосвязи человека с элементами системы труда. В процессе труда человек средствами труда воздействует на предметы труда качественно видоизменяя их или меняя положение его в пространстве. В свою очередь сам предмет труда материалы инструменты и оборудование имеющиеся в распоряжении человека оказывают влияние на характер условий труда. Кроме того безопасность и безвредность труда зависят от параметров производственной среды (микроклимата производственных вредностей) уровня организации труда от взаимоотношения человека с трудовым коллективом. Все элементы процесса труда находятся в диалектической взаимосвязи и образуют единую систему. Для обеспечения безопасности труда на рабочем месте каждого человека должны быть обеспечены: электробезопасность пожаробезопасность безопасность производственного оборудования и технологических процессов безопасность устройства и эксплуатации подъемно-транспортных машин и т. д. Анализ опасных и вредных производственных факторов. При выполнении сварки наплавки резки пайки и напылении металлов на рабочих могут воздействовать опасные и вредные производственные факторы. К вредным производственным факторам относятся: повышенная запыленность и загазованность воздуха рабочей зоны; ультрафиолетовое видимое и инфракрасное излучение сварочной дуги а также инфракрасное излучение сварочной ванны и свариваемых изделий; электромагнитные поля; ионизирующее излучение; шум; ультразвук; статическая нагрузка на руку. При сварке в зону дыхания работающих могут поступать сварочные аэрозоли содержащие в составе твердой фазы окислы различных металлов (марганца хрома никеля меди титана алюминия вольфрама железа и т.д.) их окислы и другие соединения а также токсичные газы (окись углерода озон фтористый водород окислы азота и др.). Количество и состав сварочных аэрозолей их токсичность зависят от химического состава сварочных материалов и свариваемых металлов вида технологического процесса. Воздействие на организм выделяющихся вредных веществ может явиться причиной острых и хронических профессиональных заболеваний и отравлений. Интенсивность излучения сварочной дуги в оптическом диапазоне и его спектр зависят от мощности дуги применяемых материалов защитных и плазмообразующих газов. При отсутствии защиты возможны поражения органов зрения (электроофтальмия катаракта и т.п.) и ожоги кожных покровов. Отрицательное воздействие на здоровье может оказать инфракрасное излучение предварительно подогретых изделий нагревательных устройств (нарушение терморегуляции тепловые удары). При ручных и полуавтоматических методах сварки имеет место статическая нагрузка на руки в результате чего могут возникнуть заболевания нервно-мышечного аппарата плечевого пояса. К опасным производственным факторам относятся воздействие электрического тока искры и брызги выбросы расплавленного металла и шлака; возможность взрыва баллонов и систем находящихся под давлением; движущиеся механизмы и изделия. Требования к безопасности труда. Эти требования включают в себя: устранение непосредственного контакта рабочего с исходными материалами заготовками полуфабрикатами готовой продукции и отходами производства оказывающими вредное действие; замену технологических процессов и операций связанных с возникновением вредных и опасных факторов процессами и операциями при которых данные факторы отсутствуют или обладают меньшей интенсивностью; комплексную механизацию и автоматизацию производства; применение дистанционного управления технологическими процессами и операциями при наличии опасных и вредных производственных факторов и т.д. Рабочее место сварщика должно содержаться в чистоте и порядке не допуская ничего лишнего мешающего работе на рабочем месте а также в проходах и проездах. Детали и заготовки следует держать в устойчивом положении на подкладках и стеллажах; высота штабелей не должна превышать полторы ширины или полтора диаметра основания штабеля и во всех случаях не должна быть более 1 м. Сварочные кабели нельзя располагать рядом с газосварочными шлангами и трубопроводами находящимися под давлением или по участкам с высокой температурой а также вблизи кислородных баллонов и ацетиленовых генераторов. Не должны производиться сварка и резка внутри сосудов с закрытыми люками или невывернутыми пробками у неограждённых или незакрытых люков проёмов колодцев и т.п. Средства индивидуальной защиты. При электродуговой сварке зона сварки (сварочная дуга расплавляемый металл) является источником возможного травмирования электросварщика излучением и теплом сварочной дуги и брызгами расплавленного металла. Для защиты глаз лица кожного покрова головы и шеи сварщика от излучений и брызг металла а также частичной защиты органов дыхания от непосредственного воздействия выделяемых при сварке паров металла шлака и аэрозолей предназначены защитные щитки. Щитки изготавливаются двух основных видов: наголовные и ручные. Наголовный щиток более удобен так как освобождает руку сварщика от необходимости удерживать ручной щиток. Щитки изготавливают углублённой формы для того чтобы они хорошо защищали все открытые части головы и шеи сварщика. При пользовании щитком для обзора конструкции не обязательно открывать щиток назад на голову достаточно поднять крышу рамки со светофильтром и осмотреть конструкцию через прозрачное защитное стекло а также подготовить стык к сварке зачистить кромки удалить шлак и выполнить другие операции требующие хорошей видимости. Для защиты от вредного излучения дуги в щитки вставляют стеклянные светофильтры тёмно - зелёного цвета которые не пропускают вредного излучения но позволяют видеть дугу расплавленный металл и манипулировать электродом для лучшего формирования шва. Применяют 13 классов светофильтров типа C для сварки на токах от 13 до 900 А. Необходимо иметь в виду излучение сварочной дуги может травмировать глаза рабочих находившихся поблизости от работающего сварщика. Поэтому рабочих находящихся в зоне сварки следует снабдить очками и светофильтрами предназначенными для подсобных рабочих. Излучение дуги опасно для зрения на расстоянии до 20м. Сварщики работающие на строительных площадках обязаны носить каски предохраняющие голову рабочего от возможного травмирования падающими предметами и защищающие от ударов поражения электрическим током и атмосферных воздействий. Под каску должен надеть головной убор - подшлемник. Важными средствами индивидуальной защиты сварщика являются спецодежда и спецобувь. Спецодежда (куртки и брюки) изготовляется из материала предохраняющего сварщика от излучений и имеющего противоискровые нашивки. Для работы в стационарных постах сварщик использует фартук предохраняющий от брызг особенно опасных при дуговой резке. Обувь сварщика работающего на монтажной площадке должна быть с нескользящей подмёткой. К средствам индивидуальной защиты относятся также резиновый коврик резиновые перчатки и галоши применяемые при работе в особо опасных местах. Во время работы сварщик должен застёгивать куртку не допуская оголения и поражения лучами дуги открытых мест тела. Клапаны куртки должны быть закрыты брюки носятся на выпуск так чтобы они закрывали ботинки во избежание попадания брызг металла на ноги. При проведении сварочных работ на открытом воздухе в холодное время года спецодежда должна комплектоваться теплозащитными подстёжками в соответствии с климатическими зонами. При использовании материалов выделяющих повышенное количество сварочных аэрозолей (цветных металлов и сталей с цинком и цинковым покрытием и д.р.) применяют усиленную вентиляцию обеспечивающую подачу чистого воздуха к сварщику. Однако общая вентиляция не всегда достигает нужного эффекта поэтому прибегают к средствам индивидуальной защиты. Для этого в основном используют фильтрующие противопылевые респираторы и реже - изолирующие шланговые и автономные дыхательные аппараты. Противопожарная защита. Причинами пожара при сварочных работах могут быть искры и капли расплавленного металла и шлака неосторожное обращение с пламенем горелки при наличии горючих материалов вблизи рабочего места сварщика. Для предупреждения пожаров необходимо соблюдать следующие противопожарные меры: нельзя хранить вблизи от места сварки огнеопасные или легковоспламеняющиеся материалы а также производить сварочные работы в помещениях загрязненных промасленной ветошью бумагой древесными отходами. Запрещается пользоваться одеждой и рукавицами со следами масел жиров бензина керосина и других горючих жидкостей; нельзя выполнять сварку и резку свежевыкрашенных масляными красками конструкций до полного их высыхания. Запрещается выполнять сварку аппаратов находящихся под электрическим напряжением и сосудов находящихся под давлением. Нужно постоянно иметь противопожарные средства – огнетушители ящики с песком лопаты ведра пожарные рукава и следить за их исправным состоянием а также содержать в исправности пожарную сигнализацию; после окончания сварочных работ необходимо выключить сварочный аппарат а также убедиться в отсутствии горящих или тлеющих предметов.
В данном курсовом проекте была разработана технология и оборудование для изготовления хребтовой балки передней рамы автогрейдера.
В курсовом проекте на основании заводской практики литературного и поэтапного поиска было предложено:
) заменить ручную дуговую сварку на полуавтоматическую порошковой проволокой
) Разработать специализированные приспособления с целью уменьшения времени сборки и сварки.
Примененные мероприятия позволили повысить культуру производства повысить производительность труда увеличить точность надёжность и качество изготавливаемой продукции. Также повышен уровень автоматизации и механизации сборочно-сварочного оборудования что позволит предприятию оставаться современным и конкурентоспособным.
Гитлевич А.Д. Этингоф Л.А. Механизация и автоматизация сварочного производства. - М: Машиностроение 1979. - 280 с.
Акулов А.И. Бельчук Г. А. Демянцевич В.П. Технология и оборудование сварки плавлением. - М: Машиностроение 1977. - 432 с.
Баранов М.С. Технология производства сварных конструкций. - М.: Машиностроение 1966. - 332 с.
Красовский А.И. Основы проектирования сварочных цехов: Учебник для вузов по специальности «Оборудование и технология сварочного производства». 4-е изд. перераб. - М: Машиностроение. 1980. - 319 с.
Общемашиностроительные укрупненные нормативы времени на дуговую сварку под флюсом. - М: Экономика 1989 - 182 с.
Кортелев Г.А. Коряжкин В.В. Выбор метода сварки. - Брянск: БИТМ 1989. 76 с.
Проектирование сварных конструкций в машиностроении. Под ред. С.А. Куркина. М: Машиностроение 1975. - 376 с.
Юрьев В.П. Справочное пособие по нормированию материалов и электроэнергии для сварочной техники. - М: Машиностроение 1972. - 52 с.
Контроль качества сварки. Учебник для студентов вузов. Под ред.
В.Н. Волченко. 1975.-328 с.
Кортелев Г. А. Петрушина Г.И. Экономика организация производства управление предприятием. Методические указания к выполнению организационно-экономической части дипломных проектов для студентов всех форм обучения специальности 150202 «Оборудование и технология сварочного производства». - Брянск: БГТУ 2007. - 52с.
Рыморов Е.В. Конструирование и расчет сварочных приспособлений. - Брянск: БИТМ 1987. - 88 с.
Куркин С.А. Технология механизация и автоматизация производства сварных конструкций: Атлас- М.: Машиностроение 1989. - 328 с.
Севбо П.И. Конструирование и расчет механического оборудования. - Киев: Наукова думка 1978. - 400 с.
Сагалевич В.М. Методы устранения сварочных деформаций и напряжений. - М.: Машиностроение 1974. - 248 с.
Журнал «Сварочное производство» - 1977 №8.
Потапьевский А.Г. Сварка в защитных газах. - Киев: Машгиз. Южное отд-ние 1960-98 с. 18. Журнал «Автоматическая сварка» - 1968 №6.
Закс М.И. Сварочные выпрямители. JI: Энергоиздат 1983. - 96 с.
Журнал «Автоматическая сварка» - 1985 №9.
Красовский А.И. Основы проектирования сварочных цехов: Учебник для вузов по специальности «Оборудование и технология сварочного производства». 4-е изд. перераб. - М: Машиностроение. 1980. – 319 с.
Николаев Г.А. Прочность сварных соединений Г.А. Николаев. 1 М.: Просвещение 1982. - 240 с.
ПНАЭ Г-7-009-89 Правила устройства и безопасной эксплуатации оборудования и трубопроводов атомных энергетических установок:введения 01.01.90. - М 2003. - 470 с.
Ерохин А.А. Некоторые закономерности формирования проплава при сварке неповоротных стыков труб А.А. Ерохин Ю.С.Ищенко «Сварочное производство». — №4. — 1967. — с. 16-19
Букаров В.А. Модель управления дуговой сваркой неплавящимся электродом без присадочной проволоки Букаров В.А. «Сварочное производство». - №2. — 1997. — с.28
Технилогические указания по применению мехазинированых способов сварки порошковыми проволоками при изготовлении и монтаже металлоконструкций и нестандартного оборудования на строительстве ТЭС
Рекомендуемые чертежи
Свободное скачивание на сегодня
- 23.02.2023