Проектирование участка по изготовлению конического зубчатого колеса с круговыми (сферическими) зубьями




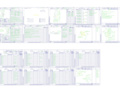
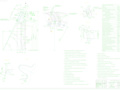
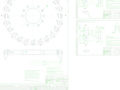
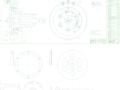
- Добавлен: 25.01.2023
- Размер: 1 MB
- Закачек: 0
Описание
Состав проекта
![]() |
![]() |
![]() ![]() ![]() ![]() |
![]() ![]() ![]() ![]() |
![]() ![]() ![]() ![]() |
![]() ![]() ![]() ![]() |
![]() ![]() ![]() ![]() |
![]() ![]() ![]() ![]() |
![]() ![]() ![]() ![]() |
![]() ![]() ![]() |
![]() ![]() ![]() ![]() |
![]() ![]() ![]() ![]() |
Дополнительная информация
8.Планировка.dwg

4.Эскизный процесс.dwg

9.Карта налодок ЧПУ.dwg

1.Рабочий чертеж.dwg

2.Чертеж заготовки.dwg

3.Технологический процесс.dwg

6.Контрольный шаблон.dwg

7.Приспособление для установки детали.dwg

5.Обрабатывающий инструмент.dwg

Рекомендуемые чертежи
- 04.11.2022