Проектирование привода грузоподъёмной машины





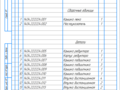
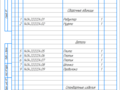
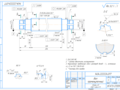
- Добавлен: 24.01.2023
- Размер: 2 MB
- Закачек: 0
Описание
Проектирование привода грузоподъёмной машины. Редуктор 22
Состав проекта
![]() |
![]() |
![]() ![]() ![]() |
![]() ![]() ![]() ![]() |
![]() ![]() ![]() |
![]() ![]() ![]() ![]() |
![]() |
![]() |
![]() |
![]() |
![]() |
![]() |
![]() ![]() ![]() |
![]() ![]() |
![]() ![]() ![]() |
![]() ![]() ![]() |
![]() |
![]() ![]() ![]() |
![]() |
![]() ![]() ![]() ![]() |
![]() |
![]() ![]() ![]() |
![]() |
![]() |
![]() |
![]() ![]() ![]() |
![]() ![]() ![]() |
![]() ![]() ![]() |
![]() ![]() ![]() |
![]() |
![]() ![]() |
![]() ![]() ![]() ![]() |
![]() |
![]() |
![]() ![]() ![]() |
![]() |
![]() |
![]() ![]() ![]() |
![]() |
![]() |
![]() |
![]() ![]() ![]() ![]() |
![]() |
![]() |
![]() ![]() ![]() |
![]() ![]() ![]() |
![]() ![]() ![]() |
![]() |
![]() |
![]() ![]() ![]() ![]() |
![]() ![]() ![]() |
![]() |
![]() |
![]() |
![]() |
![]() |
![]() ![]() ![]() ![]() |
![]() ![]() ![]() |
![]() ![]() ![]() |
![]() |
![]() |
![]() ![]() ![]() ![]() |
![]() ![]() ![]() ![]() |
![]() ![]() ![]() |
![]() |
Дополнительная информация
пробка.frw

Чертеж Приводная станция.cdw

Смещения валов электродвигателя и редуктора не более:
Техническая характеристика
Электродвигатель IM 1081
Мощность электродвигателя - 5
Частота движения вала электродвигателя - 1445 обмин
Общее передаточное отношение редуктора - 20.069
Крутящий момент на выходном валу редуктора - 706 Н
подшипник.frw

Курсовая чертеж быстроходного колеса.cdw

Коэффициент смещения
Радиусы скруглений 1.6 мм max.
Неуказанные пред. откл. размеров: отверстий +t
** размер обеспечить инструментом.
* справочный размер.
маслоуказатель.frw

Курсовая.doc
УФИМСКИЙ ГОСУДАРСТВЕННЫЙ АВИАЦИОННЫЙ ТЕХНИЧЕСКИЙ УНИВЕРСИТЕТ
Кафедра основ конструирования механизмов и машин
РАСЧЕТНО – ГРАФИЧЕСКАЯ РАБОТА
по дисциплине: Детали машин.
ТЕХНИЧЕСКОЕ ЗАДАНИЕ 4
ПРОЕКТИРОВАНИЕ ПРИВОДА ЛЕБЕДКИ.6
ВЫБОР ОПТИМАЛЬНОГО ВАРИАНТА КОМПОНОВКИ РЕДУКТОРА 8
КИНЕМАТИЧЕСКИЙ РАСЧЕТ РЕДУКТОРА 12
СТАТИЧЕСКИЙ РАСЧЕТ РЕДУКТОРА .13
ПРОВЕРКА ЗУБЬЕВ НА ВЫНОСЛИВОСТЬ ПО КОНТАКТНЫМ НАПРЯЖЕНИЯМ..14
ПРОВЕРКА ЗУБЬЕВ НА ВЫНОСЛИВОСТЬ ПО НАПРЯЖЕНИЯМ ИЗГИБА ..18
ГЕОМЕТРИЧЕСКИЙ РАСЧЕТ ПЕРЕДАЧ РЕДУКТОРА 22
КОНСТРУИРОВАНИЕ ВАЛОВ РЕДУКТОРА 23
ПРЕДВАРИТЕЛЬНЫЙ ПОДБОР ПОДШИПНИКОВ .26
ПОДБОР ШПОНОК НА КОНЦАХ ВАЛОВ СОЕДИНЕНИЕ ВАЛ-СТУПИЦА 26
ПРОВЕРОЧНЫЙ РАСЧЕТ ПРОМЕЖУТОЧНОГО ВАЛА ..27
ПРОВЕРОЧНЫЙ РАСЧЕТ ПОДШИПНИКОВ ПРОМЕЖУТОЧНОГО ВАЛА .32
ПРОВЕРОЧНЫЙ РАСЧЕТ СОЕДИНЕНИЙ ..36
КОНЦЕВЫЕ УЧАСТКИ ВАЛОВ 38
КОНСТРУИРОВАНИЕ КРЫШЕК ПОДШИПНИКОВ 39
ЗУБЧАТЫЕ КОЛЕСА ВНЕШНЕГО ЗАЦЕПЛЕНИЯ . ..41
МАНЖЕТНЫЕ УПЛОТНЕНИЯ . .42
СМАЗОЧНЫЕ УСТРОИСТВА . 43
КОНСТРУИРОВАНИЕ КОРПУСНЫХ ДЕТАЛЕЙ . ..44
КРЕПЛЕНИЕ КРЫШКИ К КОРПУСУ ..45
КОНСТРУИРОВАНИЕ ПРОЧИХ ЭЛЕМЕНТОВ ..46
ПОДБОР ВИДА СМАЗКИ 47
ЭСКИЗЫ СТАНДАРТНЫХ ИЗДЕЛИЙ ..49
СПИСОК ИСПОЛЬЗОВАННОЙ ЛИТЕРАТУРЫ. 52
Спроектировать привод грузоподъемного устройства:
Рисунок 1. Схема привода.
Рисунок 2. схема редуктора.
Номинальное натяжение каната: Fk=8300 Н;
Скорость набега каната: Vk=0.63 мс;
Длительность работы под нагрузкой: Lh=7800 часов;
Режим нагружения: II.
Привод грузоподъемной машины состоит из электродвигателя муфты редуктора и лебедки.
При помощи муфты передается вращательный момент от электродвигателя на быстроходную ступень редуктора. Выходной конец вала соединен с лебедкой при помощи муфты. Лебедка состоит из каната навиваемого на барабан. С её помощью мы можем поднимать и перемещать различные грузы.
ПРОЕКТИРОВАНИЕ ПРИВОДА ЛЕБЕДКИ
1Определение диаметра грузового каната.
Диаметр каната определяется из условия прочности с учетом коэффициента безопасности устанавливаемого для каждой категории режима.
2Определение диаметра барабана.
Диаметр грузового барабана назначаем из условия:
Где - коэффициент диаметра барабана выбираемый в соответствии с нормами ГОСГОРТЕХНадзора; принимаем .
Принимаем диаметр барабана равным
3 Определение частоты вращения барабана
4 Выбор электродвигателя
В соответствии с рекомендуемыми для цилиндрических двухступенчатых редукторов передаточным отношением получаем диапазон значений
Частоту вращения двигателя определяется из условия:
Требуемому двигателю соответствуют синхронные частоты вращения электродвигателя: 7501000 1500 обмин.
Теперь определим потребную мощность по формуле:
Значение потерь мощности на трение учитывающие КПД рассчитываем по формуле:
Далее определим мощность электродвигателя связанную с потребной мощностью соотношением:
В итоге расчета был выбран двигатель мощностью с синхронной частотой
Передаточное отношение редуктора:
5 Определение момента на барабане лебедки
6 Момент на зубчатом колесе тихоходной ступени
7 Определение допускаемых контактных напряжений:
Быстроходная ступень:
8 Определение коэффициента относительной ширины колес
Для быстроходной ступени:
Эквивалентное время работы LhE назначают с учетом категории режима работы:
где LhE – заданный срок службы час.
ВЫБОР ОПТИМАЛЬНОГО ВАРИАНТА КОМПОНОВКИ РЕДУКТОРА
Выбор оптимального варианта компоновки редуктора осуществляется по 2 критериям:
по минимальному объёму корпуса;
по минимальной массе зубчатых колес.
Выбор производится из нескольких вариантов компоновки рассчитанных с использованием программы REDUCE.
На рисунке приведены основные размеры зубчатых передач редуктора.
Рисунок 3. Основные размеры зубчатых передач редуктора.
Основные габаритные размеры зубчатых передач редуктора определяем по формулам:
- ширина зубчатого венца;
- межосевое расстояние.
Объем корпуса редуктора можно определить по формуле:
Массу заготовок для зубчатых колес характеризующую затраты на материалы вычисляется по формуле:
где - коэффициент пропорциональности для стальных зубчатых колес можно принять равным 612 кгдм3.
По представленным выше формулам произведем расчет массы и объема для различных вариантов компоновки.
Рисунок 4. Графики объемов и масс редуктора для шести вариантов компоновки.
Вычислим параметр для 2 варианта компоновки:
В результате проведенных расчетов мы получи значения масс и объемов для шести разных вариантов компоновки. Далее выбор заключается на основании условий оговоренных ранее а именно:
Проанализировав графики сделаем вывод что подходящими являются варианты 3 и 4. В этих вариантах компоновки масса зубчатых колес и объем корпуса редуктора меньше чем при других вариантах компоновки. Выбираем вариант 3.
КИНЕМАТИЧЕСКИЙ РАСЧЕТ РЕДУКТОРА.
Найдем частоту вращения быстроходного вала:
Частота вращения промежуточного вала:
Частота вращения тихоходного вала:
СТАТИЧЕСКИЙ РАСЧЕТ РЕДУКТОРА.
1 Определение моментов в зубчатых зацеплениях.
Вращающий момент на шестерне тихоходной ступени:
Вращающий момент на колесе быстроходной передачи:
Момент на шестерне быстроходной ступени:
Момент на входном конце ведущего вала:
Определение составляющих полного усилия в зацеплениях передач.
Усилия действующие на шестерни быстроходной передачи
Усилия действующие на колесо быстроходной передачи:
Усилия действующие на шестерни тихоходно передачи:
Усилия действующие на колесо тихоходной передачи:
ПРОВЕРКА ЗУБЬЕВ НА ВЫНОСЛИВОСТЬ ПО КОНТАКТНЫМ НАПРЯЖЕНИЯМ.
Перед проверкой необходимо определить материал и вид термообработки для шестерен и колес ступеней проектируемого редуктора. Для наилучшей приработки рекомендуется изготовлять шестерни с твердостью на (80 200)НВ больше чем твердость зубчатых колес.
Шестерня будет выполнена из стали 40Х с обработкой ТВЧ до твердости 45HRC
Колесо будет выполнено из стали 40Х и будет подвергнуто термоулучшению до твердости 300НВ.
Шестерня будет выполнена из стали 40Х с обработкой ТВЧ до твердости 50HRC
Колесо будет выполнено из стали 40Х и будет подвергнуто термоулучшению до твердости 350НВ.
Условие прочности по контактным напряжениям:
Быстроходная ступень.
Уточняем допускаемые напряжения.
Допускаемые напряжения для зубьев шестерни и колеса определяем по формуле:
где - предел выносливости контактной поверхности зубьев соответствующий базовому числу циклов переменных напряжений определяемый в зависимости от твердости зубьев колеса и шестерни:
- коэффициент безопасности для зубчатых колес с однородной структурой материала рекомендуется =1.1 для колеса =1.2 для шестерни.
- коэффициент долговечности;
где NHE – эквивалентное число циклов;
NHG = базовое число циклов;
где с-число зацеплений зуба за один оборот; с=1; n-частота вращения вала.
Окончательно за значение допускаемого напряжения принимается меньшее из вычисленных раннее контактных напряжений колеса и шестерни ;
Определение расчетного напряжения:
При расчете косозубой передачи коэффициент определяется о формуле:
где - коэффициент учитывающий распределение нагрузки между зубьями зависящий от степени точности окружной скорости
- коэффициент концентрации нагрузки при расчетах по контактным напряжениям.
Для определения коэффициента необходимо определить коэффициент относительной ширины зубчатого венца относительно диаметра ;
По графику с учетом расположения передачи относительно опор при твердости по величине находим:
- коэффициент динамической нагрузки по контактным напряжениям. по таблице с учетом твердости поверхности () типа передачи степени точности 8 находим .
Вычислим величину напряжения:
Сопоставление расчетного и допускаемого напряжений
Сравниваем расчетное контактное напряжение с допускаемым контактным напряжением:
Вывод: условие прочности выполняется.
где - предел выносливости контактной поверхности зубьев соответствующий базовому числу циклов переменных напряжений определяемый в зависимости от твердости зубьев колеса и шестерни.
где с-число зацеплений зуба за один оборот; с=1;
n-частота вращения вала.
где - коэффициент учитывающий распределение нагрузки между зубьями зависящий от степени точности окружности скорости
По графику рисунка с учетом расположения передачи относительно опор при твердости по величине находим:
- коэффициент динамической нагрузки по контактным напряжениям. по таблице с учетом твердости поверхности () типа передачи (косозубая) степени точности 8 находим .
Условие прочности выполняется.
ПРОВЕРКА ЗУБЬЕВ НА ВЫНОСЛИВОСТЬ ПО НАПРЯЖЕНИЯМ ИЗГИБА.
Условие прочности по напряжениям изгиба: ;
Определяем допускаемые напряжения изгиба:
где - базовый предел выносливости зубьев по напряжению изгиба определяется в зависимости от твердости поверхности зубьев или задается числовым значением:
Для шестерни для колеса .
- коэффициент безопасности для зубчатых колес с однородной структурой материала рекомендуется =175;
коэффициент учитывающий влияние двустороннего приложения (реверсированной) нагрузки.
- коэффициент долговечности (HB>350);
где - базовое число циклов циклов для стальных колес.
- эквивалентное число циклов;
где с – число зацеплений зуба за один оборот; с = 1.
n – частота вращения вала.
Вычисление величин допустимых напряжений:
Определение расчетного напряжения для шестерни:
где - коэффициент формы зуба определяемый по графику в зависимости от коэффициента смещения (x=0 – без смещения) и эквивалентного числа зубьев значение
- коэффициент концентрации нагрузки при расчетах по напряжениям изгиба по графику с учетом расположения передачи относительно опор при твердости поверхности HB>350 по величине коэффициента найдем ;
- коэффициент динамической нагрузки по таблице с учетом твердости поверхности HB>350 типа передачи (косозубая) степени точности 8 находим .
При расчете косозубой передачи коэффициент определяется по формуле:
где - коэффициент учитывающий распределение нагрузки между зубьями зависит от степени точности и окружной скорости.
- коэффициент торцевого перекрытия;
- коэффициент учитывающий повышение изгибной прочности вследствие наклона контактной линии;
Вычисление величины напряжений изгиба шестерни:
Определим расчетное напряжение для колеса:
составляем расчетные уравнения расчетных и допускаемых напряжений изгиба
Сравниваем расчетные напряжения изгиба с допускаемыми напряжениями изгиба
ГЕОМЕТРИЧЕСКИЙ РАСЧЕТ ПЕРЕДАЧ РЕДУКТОРА
Все колеса нарезаются реечным инструментом или долбяком с исходным контуром по ГОСТ 13755-81 с параметрами: коэффициентом головки (ножки) зуба коэффициент радиального зазора
Быстроходная ступень
- делительные диаметры приводятся в распечатке;
- коэффициент осевого перекрытия:
- суммарный коэффициент осевого перекрытия
КОНСТРУИРОВАНИЕ ВАЛОВ РЕДУКТОРА.
Минимально необходимый диаметр вала из условия прочности на кручение:
где Т – крутящий момент на валу
- допускаемое напряжение на кручение рекомендуется принять причем минимальные значения применяются для быстроходных валов а максимальные для тихоходных валов.
- диаметр входного конца ведущего вала
Так как быстроходный вал приводится во вращение электродвигателем через стандартную муфту то необходимо согласовать выходной конец вала с электродвигателем:
Примем диаметр вала
- диаметр под подшипник и уплотнение (dу)
- высота заплечника (буртика) определяется по таблице в зависимости от .
- диаметр буртика под подшипник (равный посадочному диаметру под колесо dK)
где r – координата фаски определяется по таблице в зависимости от величины
- длина посадочного участка
-длина промежуточного участка
- для промежуточного вала диаметр в месте установки зубчатых колес:
Промежуточный вал будет изготовлен со шлицами по ГОСТ 1139-80 обозначение: .
- диаметр вала под подшипник:
В целях унификации для быстроходного и промежуточного валов примем
Примем диаметр входного конца ведущего вала
- длина посадочного участка
ПРЕДВАРИТЕЛЬНЫЙ ПОДБОР ПОДШИПНИКОВ
Быстроходный и промежуточные валы:
по диаметру назначаем – шариковые радиальные подшипники легкой серии №207 (С=255 кН; С0=137 кН) ГОСТ 8338-75.
Проверка выполнения условия;
где - требуемая динамическая грузоподъемность представленная в распечатке.
Тихоходный вал по диаметру назначаем – роликовые радиальные подшипники средней серии №12309 (С=84 кН; С0=628 кН) ГОСТ 8329-75; схема установки – враспор.
Проверим соответствие требованиям представленным в распечатке:
ПОДБОР ШПОНОК НА КОНЦАХ ВАЛОВ СОЕДИНЕНИЕ ВАЛ-СТУПИЦА.
На конце быстроходного вала:
По диаметру подбираем размеры призматической шпонки (ГОСТ 23360-78)
Шпонка устанавливается с торца из стандартного ряда длин выбираем длину
В месте установки колеса быстроходной ступени
Соединения колеса и шестерен с валом при помощи шлицев нарезаемых на валу по ГОСТ 1139-80 обозначение: .
В месте установки колеса тихоходной ступени:
Колеса на тихоходной ступени будут установлены в натяг: .
На конце тихоходного вала:
ПРОВЕРОЧНЫЙ РАСЧЕТ ПРОМЕЖУТОЧНОГО ВАЛА.
Рассмотрим действующие на промежуточный вал нагрузки.
Рис.11.1. Нагрузки действующие на промежуточный вал.
a)Рассмотрим плоскость Y0Z:
Рис.11.1. Плоскость YOZ
Для построения эпюр изгибающих моментов рассмотрим участки вала.
b)Рассмотрим плоскость ZOX:
Рис.11.2. Плоскость ZOX
Крутящий момент на валу создается шестернями тихоходной ступени и колесом быстроходной.
c)Построим эпюры действующих усилий.
Опасными сечениями следует признать те сечения в которых действуют изгибающие моменты величиной 201 и 204 Нм.
Вал соответствует условиям прочности.
Так же необходимо провести проверку на усталостную прочность.
Вал соответствует требованиям по усталостной прочности.
ПРОВЕРОЧНЫЙ РАСЧЕТ ПОДШИПНИКОВ ПРОМЕЖУТОЧНОГО ВАЛА.
Расчет производится для опор промежуточного вала в которых установлены подшипники №207. Требуемый ресурс подшипников - Lhe=1950 часов.
Таблица 1. Параметры подшипников №208
Расчетная схема промежуточного вала рассматривается в двух взаимно перпендикулярных плоскостях – плоскости XY и XZ.
Рисунок 5. Расчетная схема промежуточного вала.
Рассчитаем значения :
При помощи уравнение статики определим опорные нагрузки:
Уравнения равновесия для проекции YX:
Уравнения равновесия для проекции ZX:
Нагрузки на подшипник определяются геометрическим суммированием опорных реакций по формулам:
- опора 3 – плавающая нагруженная радиальной нагрузкой:
- опора 4 – фиксированная нагруженная радиальной и осевой нагрузками
Определение параметра осевого нагружения:
по таблице работ ближайшее подходящее значение e =
Определение коэффициентов радиальной и осевой нагрузок:
Определяем долю осевой нагрузки в зависимости от параметра осевого нагружения с учетом вращения одного из колес подшипника. При вращении внутреннего кольца подшипника - коэффициенте вращения V = 1.
Определение эквивалентной динамической нагрузки.
где - температурный коэффициент принимаем ;
- коэффициент безопасности принимаем;
Определим ресурс подшипника:
где - коэффициент надежности принимаем
- обобщенный коэффициент совместного влияния качества металла и условий эксплуатации принимаем
- для шарикоподшипников
- частота вращения внутреннего кольца
требуемый ресурс подшипника обеспечен.
ПРОВЕРОЧНЫЙ РАСЧЕТ СОЕДИНЕНИЙ.
Условие прочности по напряжениям смятия:
где T – передаваемый вращаемый момент;
- рабочая длина шпонки для шпонки со скругленным торцами
- допускаемое напряжение на смятие рекомендуется
на конце быстроходного вала.
Расчет ведется по ГОСТ 21425-75 учитывает проверку на смятие зубьев и износ.
Проверка по условию смятия завершена.
Условие выполняется.
В месте установки колеса тихоходной ступени.
Колеса на тихоходном валу будут установлены в натяг подберем посадки для заданного типа соединения.
Определим среднее контактное давление:
Определим деформацию деталей:
Выбираем для соединения посадку .
На конце тихоходного вала
КОНЦЕВЫЕ УЧАСТКИ ВАЛОВ
Конические концы валов изготавливают по ГОСТ 12081-72 изготавливают с конусностью 1:10 двух исполнений: с наружной и внутренней резьбой. Коническая форма концевого участка приобрела широкое распространение и обеспечивают точное и надежное соединение возможность легкого монтажа и снятия устанавливаемых деталей.
Для быстроходного вала:
Для тихоходного вала:
Рисунок 6. Концевые участки валов.
КОНСТРУИРОВАНИЕ КРЫШЕК ПОДШИПНИКОВ.
Используем закладные крышки. Эти крышки не требуют специального крепления к корпусу резьбовыми деталями. Они удерживаются кольцевым выступом для которого в корпусе протачивают канавку. Чтобы обеспечить сопряжение торцов выступа крышки и канавки корпуса по плоскости на наружной цилиндрической поверхности крышки перед торцом выступа делают канавку.
Проектируем два вида крышек: глухие и отверстием для выходного и входного вала.
a)На входном валу крышка с отверстием.
Рис 14.1 Крышка подшипника с отверстием.
Определим размеры крышки:
b=4 5 мм принимаем b=5 мм;
S=5 6 мм примем S=5 мм
b1=0.4 0.8 мм принимаем b1=08 мм
D=72 мм по диаметру подшипника.
b)На промежуточном и входном валу установлены крышки без отверстий.
Рис 14.2 Крышка подшипника глухая.
c)На выходном валу так же устанавливается крышка с отверстием.
Рис 14.3 Крышка с отверстием.
D=100 мм по диаметру подшипника.
d)Глухая крышка на тихоходном валу
Рис 14.3 Глухая крышка.
ЗУБЧАТЫЕ КОЛЕСА ВНЕШНЕГО ЗАЦЕПЛЕНИЯ.
a)Быстроходная ступень
Данная форма колеса выбрана из уловий задания по серии. Колеса такого вида изготовляют при мелкосерийном производстве.
S = 2.2m + 005b2 = 2.2*2+0.05*28=6 мм
f = (05 06)m = 16 мм.
b)Тихоходная ступень
lст = (0.8 1.5)d = 41 мм
S = 2.2m + 005b2 = 2.2*25+0.05*322=7 мм
dст=(1.55 1.6)d=75 мм.
МАНЖЕТНЫЕ УПЛОТНЕНИЯ.
Манжета состоит из корпуса изготовленного из маслобензостойкой резины каркаса представляющего собой стальное кольцо Г- образного сечения и браслетной пружины. Каркас придает манжете жесткость и обеспечивает плотную посаду в корпусную деталь без дополнительного крепления.
Эскиз манжетного уплотнения приведен в пункте «Эскизы стандартных изделий»
СМАЗОЧНЫЕ УСТРОИСТВА.
Во время работы редуктора в масло попадают продукты износа следовательно через определенно время нужно производить замену масла. Для этого редуктор снабжается сливным отверстием и соответствующей пробкой для него. Пробка имеет коническую резьбу МК 18 что гарантирует герметичность соединения.
Рис.17.1. Маслосливная пробка.
Для контроля уровня масла в редукторе предусмотрен маслоуказатель.
Рис.17.2. Маслоуказатель
КОНСТРУИРОВАНИЕ КОРПУСНЫХ ДЕТАЛЕЙ.
Толщина стенки корпуса редуктора
Для уменьшения массы крышки боковые стенки выполняют наклонными.
Диаметр приливов в которых располагаются подшипники определяются:
a)Для подшипников быстроходной и промежуточной ступени:
Dп = 125*D + 10 мм = 125*72+10=100 мм
b)Для подшипников тихоходной ступени:
Dп = 125*D + 10 мм = 125*100+10=135 мм
Рис.18.2. Прилив для крышки.
КРЕПЛЕНИЕ КРЫШКИ К КОРПУСУ.
Крепление крышки к корпусу осуществляется при помощи 12 винтов. Отверстия под винты будут просверлены насквозь что существенно облегчит операцию их изготовления.
Рис.19.1. Крепление крышки к корпусу.
Размеры элементов крышки и корпуса принимают:
К = 235*d = 235*12 = 282 мм примем К=30 мм;
С = 11*d = 11*12 = 132 мм примем С =155 мм;
Для точного фиксирования крышки относительно корпуса применяем штифты по ГОСТ 3128-70 которые уложены горизонтально.
Рис.19.2. Фиксирование штифтом крышки относительно корпуса.
КОНСТРУИРОВАНИЕ ПРОЧИХ ЭЛЕМЕНТОВ.
Для транспортировки редуктора предусмотрены проушины которые будут отливаться вместе с крышкой редуктора.
Для заливки масла в редуктор разработан люк имеющий фильтр и отверстия.
Для закрепления редуктора к плите необходимо спроектировать места под болты.
Рис.20.3. Места для крепления редуктора.
Так как в задании не оговорены особые условия смазки и в ходе выполнения расчетов не было выявлено особых условий смазки то можно использоват стандартную смазку – масло И-40А.
Масло И40-А потребляется вкачестве рабочей жидкости вгидравлических системах станочного оборудования автоматических линий прессов для смазывания легко- исредненагруженных зубчатых передач направляющих качения искольжения станков где нетребуется специальные масла идругих механизмов.
Приводная станция состоит из: редуктора двигателя и муфты при помощи которой вал двигателя передает усилия на редуктор.
Муфта упруго втулочно-пальцевая по ГОСТ 21424:
Рис.23.1. Муфта упруго втулочно-пальцевая по ГОСТ 21424.
Плита литая крепление редуктора к плите осуществляется при помощи винтов.
Рис.23.2. Крепление редуктора к плите.
Крепление плиты к поверхности не оговаривается изначально. Но на плите предусмотрены отверстия по болты либо под винты.
Рис.23.3. Отверстия для крепления плиты к поверхности.
ЭСКИЗЫ СТАНДАРТНЫХ ИЗДЕЛИЙ.
Подшипник 207 ГОСТ 8338-75
Мaнжета ГОСТ 8752-79
СПИСОК ИСПОЛЬЗОВАННОЙ ЛИТЕРАТУРЫ
Прокшин С.С. Беляев Б.А. Методические указания к курсовому проектированию по дисциплине «Детали машин и основы конструирования»: Уфимск. гос. авиац. техн. ун-т. – Уфа 2006 - 58 с.
Дунаев П.Ф. Леликов О.П. Конструирование узлов и деталей машин: учебное пособие. – 9-е изд. перераб и доп. – М.: Академия 2006. – 496 с.
Анурьев В.И. Справочник конструктора – машиностроителя: в 3 – х томах. Т.1 – 3 5 – е изд. перераб. и доп. – М.: Машиностроение 1978.
пруж шайба.frw

муфта.frw

Спецификация по новый.spw

Втулка дистанционная
Мaнжета 1-40 х 60-1
Мaнжета 1-35 х 58-1
ред к плите.frw

плита к поверхности.frw

крепление к корпусу.frw

расчет подшипников промежуточного вала.frw

ifq,f vyjuj kfg.frw

размеры редуктора.frw

курсовая - промежуточный вал.frw

люк.frw

Спецификация для привода.spw

крышка.frw

эпюры.frw

манжета ст.frw

Чертеж вид сверху.cdw

щлиц гайка.frw

чертеж главный вид.cdw

Частота вращения тихоходного вала
Число зубьев шестерни
Снаружи редуктор красить серой краской ПФ-115 ГОСТ 6465-76.
Подшипники освободить от консервации.
Монтаж подшипников качения производить с нагревом в
маслянной ванне при температуре не выше 90
Монтаж соединений с натягом охватывающего инструмента до
Проверить плавность вращения валов.
В редуктор залить индустриальное
масло И-40А ГОСТ 20799-75 в количестве 8 литров.
Редуктор обкатать без нагрузки при
частоте вращения быстроходного вала
n=1445 обмин в течении трех часов.
После обкатки масло слить..
Предельные значения осевых зазоров
Техническая характеристика:
Основные параметры зацепления: Табл.1
Передаточное отношение редуктора: 20
Технические требования:
проушины.frw

редуктор к полу.frw

Чертеж шестеренки.cdw

Коэффициент смещения
Радиусы скруглений 1.6 мм max.
Неуказанные пред. откл. размеров: отверстий +t
** размер обеспечить инструментом.
* справочный размер.
Чертеж промежуточного вала.cdw

Неуказанные предельные откл. размеров валов - t
**размеры для справок
штифт.frw
