Проектирование печи подогрева отбензининной нефти



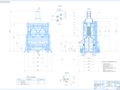
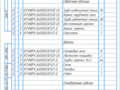
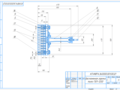
- Добавлен: 25.01.2023
- Размер: 4 MB
- Закачек: 3
Описание
Проектирование печи подогрева отбензининной нефти
Состав проекта
![]() |
![]() |
![]() |
![]() ![]() ![]() ![]() |
![]() |
![]() |
![]() ![]() ![]() ![]() |
![]() |
![]() ![]() ![]() ![]() |
![]() ![]() ![]() |
![]() |
![]() ![]() ![]() |
Дополнительная информация
горелка.cdw

Спецификация печь трубчатая.spw

КП.ФЮРА.360000.001.00 СБ
КП.ФЮРА.360000.001.00 ПЗ
Пояснительная записка
Труба конвекционной секции
Каркас трубчатой печи
Труба радиантной секции
Беспламенная горелка
КП.ФЮРА.360000.001.01 Д
Обтюрация ГОСТ 1235-67
Асбестовая прокладка
Чертеж печи.cdw

Количество средних секций - 0
Полная тепловая нагрузка 4
металла (без змеевика) 43 т
футеровки (подвесной кладки) 68 т
КП.ФЮРА.360000.001.00.СБ
Техническая характеристика
курсовой трубчатая печь.docx
1 Основные характеристики трубчатых печей6
2 Конструкции трубчатых печей7
1 Расчет процесса горения топлива15
2 К.П.Д. печи ее тепловая нагрузка и расход топлива21
3 Поверхность нагрева радиальных труб и размеры камеры радиации23
4 Проверка скорости сырья на входе в змеевик печи26
5 Расчет лучистого теплообмена в топке26
6 Расчет конвективной поверхности нагрева печи28
7 Гидравлический расчет змеевика печи35
8 Расчет потерь напора в газовом тракте печи41
Автоматизации трубчатой печи48
Список использованной литературы55
Трубчатая печь является аппаратом предназначенным для передачи нагреваемому продукту тепла выделяющегося при сжигании топлива непосредственно в этом же аппарате.
Трубчатые печи широко распространены в нефтеперерабатывающей и нефтехимической промышленностях они являются составной частью многих установок и применяются в различных технологических процессах таких как перегонка нефти мазута каталитический крекинг и риформинг гидроочистка очистка масел и др.
В начальный период развития нефтеперерабатывающей промышленности для нагрева сырья использовались кубы; однако они имели много существенных недостатков и поэтому теперь не применяются.
Трубчатые печи получили широкое распространение благодаря следующим своим особенностям. Их работа основывается на принципе однократного испарения что обеспечивает либо более глубокий отгон при данной конечной температуре нагрева сырья либо заданный отгон при более низкой температуре нагрева. Они обладают высокой тепловой эффективностью так как в дополнение к основной части тепла которая передается излучением существенная часть передается конвекцией вследствие сравнительно высокой скорости движения дымовых газов. Помимо этого трубчатые печи являются компактными аппаратами их коэффициент полезного действия высок они могут обеспечивать высокую тепловую мощность. Продолжительность пребывания нагреваемого сырья в зоне высоких температур не превышает нескольких минут что уменьшает возможность его разложения и коксоотложения в трубах вследствие чего при необходимости сырье можно нагревать до более высокой температуры. Печи удобны в эксплуатации позволяют осуществлять автоматизацию.
В зоне нагрева трубчатых печей единовременно находится относительно небольшое количество нефтепродукта что снижает пожарную опасность. В случае прогара труб пожар легче устранять.
Технологии и конструкции аппаратов
Трубчатые печи нашли самое широкое применение в нефтеперерабатывающей нефтехимической химической газовой и других отраслях промышленности. Так в нефтепереработке трубчатые печи используются для огневого нагрева и частичного испарения нефти и продуктов её переработки на установках АВТ каталитического крекинга риформинга и многих других. Трубчатые печи широко используются и в качестве реакционных аппаратов (установки термического крекинга пиролиза) причем реакционные процессы могут протекать как в жидкой так и в паровой фазах.
По способу передачи тепла потоку перерабатываемого сырья трубчатые печи можно разделить на три группы: конвективные радиантно-конвективные и радиантные.
В конвективных печах тепло передается продукту при соприкосновении продуктов сгорания топлива с трубами по которым прокачивается сырье. Топочная камера в печах вынесена отдельно а трубные экраны отсутствуют. За счет конвекции передается до 80% от общего количества тепла (остальное количество тепла передается радиацией). В печах данного типа обеспечиваются более мягкие условия теплообмена (меньшая разность температур между стенкой трубы и перерабатываемым продуктом).
В печах радиантно-конвективного типа 40 - 60% всего тепла передается радиацией а остальное - конвекцией.
В радиантных печах основная доля тепла передается радиацией. В печах этого типа стены топочной камеры покрыты экранами из радиантных труб. Тепло от факела горения передается экранам излучением. Камера конвекции имеет вспомогательное значение. Печи данного типа наиболее компактны. Основным их недостатком является высокая температура отходящих газов что ухудшает экономические показатели печного агрегата. В зависимости от места расположения трубные экраны радиантных печей (секций) разделяются на потолочные (подвесные) боковые (фронтальные) и подовые (напольные) а в зависимости от направления подвода тепла излучением - одно- и двухстороннего облучения.
1 Основные характеристики трубчатых печей
В промышленности применяются трубчатые печи с поверхностью нагрева радиантных труб от 15 до 2000 м2. Тепло- производительность печей меняется в широком диапазоне и составляет от 07 до 60 МВт на крупных установках она может достигать 100 МВт. Температура и давление нагреваемой среды на входе и на выходе из печи в зависимости от типа технологического процесса также могут меняться в самых широких пределах (температура – от 70 до 900 °С давление – 01 до 30 МПа).
Допускаемая теплонапряженность поверхности нагрева зависит от вида нагреваемого продукта и скорости его движения по трубам. Чем тяжелее нагреваемый продукт тем меньше величина допускаемой теплонапряженности (см. табл. 1). Для труб конвективных камер величина теплонапряженности составляет от 8 до 175 кВтм2. Теплонапряженность топочного пространства в современных трубчатых печах установок нефтепереработки составляет от 40 до 80 кВтм3.
Таблица 1 – Допустимые тепловые напряжения
поверхности нагрева радиантных труб
Процесс протекающий в печи
Теплонапряженность кВтм2
Нагрев без испарения
Нагрев и испарение нефти (до 613 К)
Вакуумная перегонка мазута
Замедленное коксование
Каталитический крекинг
Каталитическое дегидрирование бутана
Отгонка растворителей от масел
КПД трубчатой печи зависит от величины коэффициента избытка воздуха подаваемого в горелки печи температуры отходящих продуктов сгорания топлива качества тепловой изоляции печи и ряда других параметров. КПД современных трубчатых печей находится на уровне 065-093.
2 Конструкции трубчатых печей
Для увеличения единичной тепловой мощности трубчатых печей их выполняют многокамерными или секционными. В многокамерных печах кроме настенных радиантных змеевиков одностороннего облучения имеются межкамерные одно- или двухрядные радиантные экраны подверженные двухстороннему облучению высокотемпературным пламенем факельных горелок что обеспечивают более равномерный обогрев труб увеличивая КПД печи особенно в радиантной камере.
На рис. 1 представлена принципиальная схема двухскатной (шатровой) двухкамерной печи с двумя камерами радиации и одной конвекционной камерой. Трубы радиантных змеевиков 2 здесь имеют три экрана одностороннего облучения: фронтальный - расположен напротив горелок у перевальной стены 4 подовый (напольный) - установлен в поду печи и потолочный - подвешен на металлоконструкции 6 наклонного свода печи. Факельные горелки 1 с относительно коротким пламенем расположены в амбразурах обмуровки 5 вдоль боковых стенок печи. Это позволяет более эффективно использовать теплоту излучения горизонтального факела в радиационной камере печи. Отработанные газы после омывания труб конвективного змеевика 3 выбрасываются в дымовую трубу 8 через нижний боров 7.
Благодаря простоте конструкции легкости обслуживания и удобства проведения ремонтных работ двухкамерные печи шатрового типа с факельными горелками находят широкое применение на установках АВТ каталитического и термокрекинга в производстве масел и других производствах. Однако основным недостатком таких печей является значительные габаритные размеры и относительно низкие теплотехнические показатели. Так размеры печи тепловой мощностью 18 МВт составляют 20×15×8 м теплонапряженность топки 60-95 кВтм3. Одностороннее облучение длинными факелами создает неравномерность нагрева труб по окружности и по длине трубчатого змеевика. При форсировании режима горения возможны прогары труб. Из-за высоких удельных затрат металла и огнеупоров а также низкого КПД (60 - 70%) их постепенно заменяют на трубчатые печи с горелками беспламенного горения.
Рисунок – 1. Двухскатная двухкамерная печь с горизонтальными трубами радиантной и конвекционной камер: 1 - факельные горелки; 2 - трубы радиантных экранов одностороннего облучения; 3 - трубы конвективных змеевиков; 4 - перевальная стена; 5 - обмуровка; 6 - металлоконструкция (каркас) печи; 7 - нижний боров (дымоход); 8 - дымовая труба.
Схема типовой двухкамерная печи с беспламенными панельными горелками в разрезе представлена на рис. 2. В отличие от печей с факельными горелками данная конструкция печей имеет значительно меньшую ширину. Расположенные на боковых стенах печи газовые беспламенные горелки 4 типа ГБПш создают равномерное облучение труб фронтальных 5 и подвесных потолочных 13 экранов радиантных змеевиков эффективно используя не только прямое тепловое излучение от раскаленных панелей но и отраженное излучение от стен обмуровки. Хороший теплосъем и высокий КПД печи обеспечивает конвективный змеевик 11 размещенный на выходе топочных газов с радиантной камеры откуда использованные дымовые газы через нижний боров 15 выбрасываются в дымовую трубу.
Рисунок 2 – Двухкамерная трубчатая печь с горелками беспламенного горения:
– металлический каркас; 2 - огнеупорная футеровка; 3 - кладка из керамических призм беспламенных горелок; 4 - панельные горелки; 5 13 - трубы фронтового и потолочного экранов; 6 - обслуживающие площадки; 7 - гляделка; 8 - взрывное окно-лаз; 9 - навес; 10 12 - ре- турбендные камеры; 11 - трубы конвекционной камеры; 14 - кровля.
Для наблюдения за состоянием горелок и труб радиант- ного змеевика на торцевой стенке печи на уровне обслуживающей площадки 6 установлены взрывные окна-лазы 8 снабженные поворотными смотровыми окнами (гляделками) 7. Соединение печных труб в радиантном и конвективном змеевиках выполнено методом развальцовки их концов в специальных двойниках - ретурбендах. Для удобства обслуживания и защиты развальцовочного соединения от воздействия высоких температур ретурбенды вынесены за пределы топки и размещены в ретурбендных камерах 10 и 12. При выходе из строя печных труб разъемное соединение с помощью ретурбендов позволяет производить замену труб без значительных капитальных затрат через соответствующие окна в ретурбендных камерах. Металлический каркас 1 повторяющий очертания наружной формы печи устанавливается на бетонном фундаменте и несет практически всю нагрузку от основных элементов печи: трубных змеевиков гарнитуры кровли обслуживающих площадок а также кладки обмуровки 2 и подвесного свода.
На рис. 3 представлены конструкции трубчатых печей с двухрядными центральными радиантными экранами. Благодаря двухстороннему облучению центрального экрана трубы получают равномерное излучение от горелок поэтому коэффициент облученности радиантных труб в этих печах близок к единице.
Рисунок 3 – Печи с центральными двухрядными экранами
двухстороннего облучения:
а) двухкамерная с нижним отводом дымовых газов: 1 - факельные горелки; 2 - центральный радиантный экран; 3 - конвекционный змеевик; 4 - обмуровка; 5 - воздуховод; 6 - нижний боров (дымоход);
б) вертикальная печь с верхним отводом дымовых газов: 1 - инжекционные беспламенные горелки со сферической излучающей чашей; 2 - центральный радиантный экран; 3 - конвективный змеевик; 4 - обмуровка; 5 - металлоконструкция; 6 - газоход;
На рис. 3а двухстороннее облучение труб двухрядного центрального экрана производится расположенными сверху газовыми горелками 1 со свободным нисходящим факелом. Кроме основного излучения от пламени горелок здесь происходит дополнительный обогрев труб центрального экрана за счет отраженного излучения нагретых пламенем боковых стенок обмуровки печи. Горячие топочные газы после радиантной камеры проходят через нижнюю конвекционную камеру 3 и отводятся через нижний боров 6 в дымовую трубу.
На рис. 3б для двухстороннего облучения центрального двухрядного радиантного экрана 2 использованы беспламенные инжекционные газовые горелки со сферической излучающей чашей 1 расположенные по всей высоте боковых стенок топки. Достоинством такой компоновки печи является возможность поддержания оптимального температурного режима по высоте радиантного экрана за счет регулирования расхода газа подводимого к горелкам. После обогрева труб верхнего конвективного змеевика 3 отработанные топочные газы отводятся в газосборник 6 для выброса в дымовую трубу.
Устройство многокамерной трубчатой печи типа Р в разрезе показана на рис. 4. Печи данной конструкции применяют для нагрева газосырьевой смеси в высокотемпературных процессах каталитического риформинга и гидроочистки. Печь состоит из трех камер радиации 6 с вертикальными трубчатыми змеевиками печные трубы которых соединены друг с другом сварными калачами. Между смежными камерами радиации расположены двухрядные боковые радиантные экраны двухстороннего облучения. В некоторых случаях между трубами соседних экранов могут быть установлены огнеупорные разделительные стены. Во фронтальных стенах печи смонтированы комбинированные горелки 1 типа ФГМ факелы от которых направлены горизонтально к противоположным стенам где имеется канал 5 для отвода продуктов сгорания топлива в камеру конвекции. Змеевики камеры конвекции выполнены трехходовыми для интенсификации теплоотдачи от отходящих дымовых газов за счет высоких скоростей их омывания а также имеют наружное ореб- рение (или ошиповку) труб 3 для дополнительной турбулизации потока. Металлический каркас печи 8 состоит из отдельных рам футеровка - из огнеупорного кирпича или сборных панелей из легкого огнеупорного перлитобетона.
Рисунок 4 – . Многокамерная трубчатая печь типа Р в разрезе: 1 - горелка; 2 - камера конвекции; 3 - конвективный змеевик; 4 - канал топочных газов; 5 - окно для отвода продуктов сгорания топлива; 6 - радиантная камера; 7 - смотровое окно; 8 - металлический каркас.
За счет реализации указанных мер в многокамерных печах типа Р обеспечиваются следующие теплотехнические характеристики:
Тепловая мощность - 46 МВт;
Среднедопускаемая теплонапряженность радиантных труб - 40 кВтм2.
Для высокопроизводительных установок АВТ ВНИИНефтемашем разработаны узкокамерные печи с верхним отводом дымовых газов типа Г. Указанный тип печей отличается большой единичной мощностью имеет два исполнения - ГС (рис. 5) и ГН (рис.6).
В печах марки ГС (исполнение I) со свободным вертикальным факелом (рис. 5) радиантные и конвекционные змеевики расположены горизонтально газомазутные вертикально-факельные горелки 6 типов ГИК и ФГМ смонтированы в шахматном порядке в поде радиантной камеры. При горении топлива образуется стена вертикальных факелов излучающих тепло сырьевым змеевикам радиантной камеры 3 расположенным на кронштейнах у стен топки. Огнеупорная панельная и блочная футеровка 2 выполняется из легковесного огнеупорного керамзитобетона на глиноземистом цементе либо выкладывается из шамотного кирпича и собирается на металлическом каркасе 4. Дымовые газы отводятся вверх проходят через змеевик 9 конвекционной камеры и через газосборник 8 ход выбрасываются в отдельно стоящую дымовую трубу.
Рисунок 5 – Узкокамерная горизонтальная печь со свободным факелом горения типа ГС: 1 - смотровое окно; 2 - футеровка; 3 - радиантный и конвекционные змеевики; 4 - металлический каркас; 5 - люк-лаз; 6 - вертикальные горелки; 7 - выхлопные предохранительные окна.
Теплопроизводительность печей ГС составляет 147 - 576 МВт средняя теплонапряженность радиантных труб выполненных из труб размером 152×8 мм - 406 кВтм2.
В узкокамерных печах типа ГН (исполнение II) с настильным пламенем (рис. 6) комбинированные горелки 6 типа ФП-2 для объемно-настильного сжигания топлива расположены в боковых стенах печи с двух сторон под углом 45. Факел образованный при горении топлива настилается с двух сторон на огнеупорную настильную стену 3 расположенную в центре печи от которой тепло излучается к настенным радиантным экранам 2 одностороннего облучения. Настильная стена делит камеру радиации на две камеры с независимым температурным режимом. Топочные газы отводятся вверх через камеру конвекции 7 в металлический сборник футерованный изнутри легким огнеупорным бетоном откуда сбрасываются в дымовую трубу смонтированную на каркасе печи. Футеровка 4 печи выполнена аналогично печи ГС и собирается на металлическом каркасе 5. Подовые блоки изготовляются из жаростойкого бетона с шамотным заполнителем на портландцементе.
Рисунок 6 – Узкокамерная горизонтальная печь с настильным факелом горения типа ГН: 1 - дымоход; 2 - радиантный и конвективный змеевики; 3 - центральная настильная стена; 4 - обмуровка; 5 - металлический каркас; 6 - амбразура горелки.
Каркасы печей ГС и ГН изготовлены из металлических рам соединенных сваркой или на болтах. Тепопроизводительность печей ГН составляет 74 - 237 МВт средняя тепловая напряженность радиантных труб - 35 кВтм2.
1 Расчет процесса горения топлива
Цель данного этапа: расчет низшей теплотворной способности топлива количества и состава продуктов сгорания теплосодержания продуктов сгорания.
Для начала определим плотность исходной нефти и долю отгона при температуре выходе нефти из печи равной 355 °С. Для этого воспользуемся программой «HYSYS».
Рисунок 7 – Доля отгона нефти при температуре 355°С
Как видно из рис.7 доля отгона при температуре 355 °С равна 06933 (в мольных долях). Пересчитаем долю отгона в массовые доли. Для этого найдем массовые расходы компонентов в исходной нефти и в паровой фазе при температуре 355 °С.
Таблица 2 – Данные о расходах исходной нефти и паровой фазы
при температуре 355 °С
Из табл. 2 определяем долю отгона в массовых долях:
Далее необходимо рассчитать плотность нефти при температуре 25 °С. Для этого из данных «HYSYS» находим плотности каждого компонента нефти при температуре 25 °С (табл. 3).
Таблица 3 – Плотности компонентов нефти и их массовые доли
Плотность компонента кгм3
Состав массовые доли
По формуле определим плотность отбензининой нефти паров в печи и жидкости в печи [1]:
где – массовая доля компонента нефти;
– плотность компонента смеси кгм3.
Для определения низшей теплоты сгорания мазута марки М-100 определим его элементный состав. В таблице 4 приведен элементный состав мазута согласно ГОСТ 10585-99 [2]:
Таблица 4 – Элементный состав мазута
Состав мазута % масс.
Далее определим низшую теплотворную способность топлива по уравнению Менделеева:
где C H S O W – соответственно содержание в топливе углерода водорода серы кислорода влаги % масс.
Определим теоретическое количество воздуха необходимого для сжигания 1 кг мазута по формуле [3]:
где Н О S – элементный состав топлива в массовых процентах.
Для печей с излучающими стенками коэффициент избытка воздуха =103 – 107. Принимаем =106. Тогда действительное количество воздуха:
где = 1293 кгм3 – плотность воздуха при нормальных условиях (273К и 01·10 6 Па).
Определим количество продуктов сгорания образующихся при сжигании 1 кг топлива [3]:
Суммарное количество продуктов сгорания найдем по формуле [3]:
Содержание влаги в воздухе пренебрегаем.
Далее найдем объёмное количество продуктов сгорания (в м 3)на 1 кг топлива (при нормальных условиях) [3]:
Суммарный объем продуктов сгорания:
Плотность продуктов сгорания при 273 К и 01·106 Па:
Определим энтальпию продуктов сгорания на 1 кг топлива при различных температурах по уравнению:
где Т – температура продуктов сгорания К;
– средние массовые теплоемкости продуктов сгорания определяемые из таблицы 5 кДж(кг·К) [3].
Таблица 5 – Средняя массовая теплоемкость газов
при постоянном давлении [(кДж(кг·К)]
Теплоемкость кДж(кг*К)
Найдем для примера величину :
Результаты расчетов сведены в табл.6.
Таблица 6 – Зависимость энтальпии продуктов сгорания от температуры
По данным этой таблицы строим график q ÷ Т – энтальпия продуктов сгорания ÷ температура (рис.8).
Рисунок 8 – Зависимость энтальпия продуктов сгорания от температуры
2 К.П.Д. печи ее тепловая нагрузка и расход топлива
К.п.д печи найдем по формуле [3]:
где – потери тепла в окружающую среду в долях от низшей теплоты сгорания топлива;
– потери тепла с уходящими дымовыми газами в долях от низшей теплоты сгорания топлива.
Примем что = 006 и температура дымовых газов покидающих конвекционную камеру печи на 120 К выше температуры Т1 сырья поступающего в печь:
При Тух =593 К найдем по графику q – Т (рис.8) потерю тепла с уходящими дымовыми газами:
или в долях от низшей теплоты сгорания топлива:
Подставив численные значения величин получим что к.п.д. печи
Полная тепловая нагрузка печи Q T будет равна:
где Qполезн – полезное тепло печи кДжч.
Полезное тепло печи ( в кДжч) рассчитываем по формуле:
где G – производительность печи по сырью кгч;
е = 05533 – массовая доля отгона сырья на выходе из печи при Тк= 628 К;
– энтальпия соответственно паровой и жидкой фаз сырья на выходе из печи при Т2 = 628 К кДжкг;
– энтальпия сырья на входе в печь при Тн = 473 К кДжкг.
По таблицам энтальпий жидких нефтепродуктов и нефтяных паров [3] зная плотности отбензиненной нефти отгона и остатка однократного испарения найдем:
Подставляем в формулу соответствующие величины получим
Часовой расход топлива:
3 Поверхность нагрева радиальных труб и размеры камеры радиации
Поверхность нагрева радиантных труб (в м2) определяется по формуле [3]:
где Qр – количество тепла переданного сырью в камере радиации кВт;
еплонапряжение радиантных труб кВтм2.
Количество тепла переданного сырью в камере радиации (прямая отдача топки) найдем из уравнения теплового баланса топки [3]:
где – коэффициент эффективности (к.п.д) топки;
– энтальпия дымовых газов на выходе из камеры радиации при температуре Тп кДжкг топлива.
Примем Тп = 1093 К и определим по графику q – Т (рис. 8)
Ранее было принято что потери тепла в окружающую среду равны 6%. Пусть 4 % в том числе составляют потери тепла в топке.
Примем теплонапряжение радиантных труб = 35 кВтм2.
Таким образом поверхность нагрева радиантных труб будет равна:
Определим температуру Тк сырья на входе в радиальные трубы.
Полагая на основе опытных и расчетных данных что нефть в конвекционных трубах не испаряется найдем ее энтальпию на входе в радиальные трубы из уравнения:
По таблице энтальпий нефтепродуктов [3] искомая температура Тк=529 К.
Выбираем трубы диаметром 1148 мм с полезной длиной lтр = 6 м (полная длина трубы с учетом заделки концов в трубные двойники равна 65 м) [4].
Число радиальных труб:
Учитывая опыт промышленности принимаем узко-камерную печь беспламенного горения типа с двухрядным экраном двухстороннего облучения с горизонтальным шахматным распоряжением труб и двумя верхними конвекционными секциями.
По существующим нормам принимаем шаг размещения экранных труб S = 025 м. Тогда расстояние между вертикальными рядами радиантных труб:
По данным ВНИИНефтемаша расстояние от излучающих стен до трубного экрана должно быть от 05 до 15 м. Принимаем это расстояние ат =125 м. В каждом вертикальном ряду экрана разместим по 19 труб. Тогда высота радиантной камеры (топки) составит:
где – число труб в одном вертикальном ряду;
= 025 м – расстояние от нижней и верхней труб вертикального ряда соответственно до пода и потолка печи.
Подставив числовые значения величин получим:
Ширина радиантной и конвекционной камер печи:
Объем камеры радиации:
Теплонапряжение топочного объема печи:
В современных трубчатых печах теплонапряжение топочного объема печи лежит в пределах от 40 до 80 кВтм3.
Для обеспечения равномерного обогрева каждой трубы экрана по окружности и по длине принимаем для проектируемой печи газовые горелки ВНИИНефтемаша типа ГБП-1200 теплопроизводительностью qг = 12МВт [4 5].
Принимаем для каждой из двух излучающих стен топки по 2 горелки по высоте.
4 Проверка скорости сырья на входе в змеевик печи
Оптимальное значение скорости сырья на входе в змеевик печи с учетом эффективного теплообмена и минимальных энергетических затрат на прокачивание сырья составляет 05 – 25 мс.
Проверим соответствует ли скорость подачи сырья для проектируемой печи установленным пределам.
При двухпоточном движении сырья в змеевике печи его линейная скорость (в мс) определится по формуле:
где dв =0064 м – внутренний диметр конвекционных труб;
m = 2 – число потоков сырья;
ρ473 =700 кгм3 – плотность сырья (нефти) при 473 К.
Как видно начальная скорость сырья в змеевике печи находится в допустимых пределах.
5 Расчет лучистого теплообмена в топке
Целью данного расчета является определение температуры газов выходящих из топки (Тп). Температуру газов выходящих из топки (Тп) определим по уравнению [4]:
где – определяется из следующего соотношения (для узкокамерных печей):
–отношение длины факела к длине топки по ходу движения дымовых газов. Для беспламенных горелок отношение длины факела к длине топки по ходу движения дымовых газов принимается 01;
– коэффициент лучеиспускания абсолютно черного тела равный 575 Вт(м*К4);
– отношение поверхности радиантных труб к эквивалентной абсолютно черной поверхности (для стенки топки из беспламенных горелок принимается равным 3);
– теплонапряженность поверхности радиантных труб Втм2;
– конвективный тепловой поток через 1 м2 тепловоспринимающей поверхности экрана Вт м2;
– температура наружной стенки экрана К.
Определим коэффициент :
Далее определим конвективный тепловой поток через 1 м2 тепловоспринимающей поверхности экрана:
коэффициент теплоотдачи конвекцией от дымовых газов к экрану () определяется по уравнению:
коэффициент учитывающий разность температур газов на выходе из топки и около змеевика (при расчетах может быть принят равным 09).
Определим температуру наружной стенки экрана:
где – средняя температура сырья в радиантных трубах К;
– коэффициент теплоотдачи от стенки труб к нефти (принимается равным 940 Вт(м2*К));
– толщина стенки трубы м;
– коэффициент теплопроводности материала стенки трубы Вт(м*К) (принимается равным 454).
Средняя температура сырья в радиантных трубах равна:
Конвективный тепловой поток через 1 м2 тепловоспринимающей поверхности экрана:
Получаем что температуру газов выходящих из топки (Тп) равна:
Как видно из расчетов расхождение с ранее принятой температурой (1093 К) находится в допустимых пределах –погрешность составляет менее 5%.
6 Расчет конвективной поверхности нагрева печи
Поверхность нагрева конвекционных труб определяется по формуле:
где – количество тепла предаваемого сырью в конвекционных трубах Вт;
– коэффициент теплопередачи в конвекционной камере печи Вт(м2·К);
– средний температурный напор К.
Количество тепла передаваемого сырью в конвекционных трубах:
Коэффициент теплопередачи в конвекционной камере вычисляется по формуле [3 6]:
– коэффициент теплоотдачи конвекцией от дымовых газов к трубам Вт(м2·К);
– коэффициент теплоотдачи излучением от трехатомных газов к трубам Вт(м2·К);
Коэффициент определим по формуле из которой :
где С – постоянная для шахматного пучка труб равна 033;
– коэффициент зависящий от числа рядов труб в пучке (полагая что число рядов будет более 10 примем = 1 );
– коэффициент теплопроводности дымовых газов Вт(м·К).
Критерии Re и Pr в формуле вычисляются при средней температуре дымовых газов в камере конвекции. Скорость газов рассчитывается для самого узкого сечения пучка.
В камере конвекции устанавливаются трубы с полезной длиной lтр= 6 м наружным диаметром dн = 76 мм и толщиной стенки 6 мм. В каждой камере размещается змеевик для двух потоков сырья. В одном горизонтальном ряду устанавливаем в шахматном порядке по две трубы с шагом S =172 мм.
Найдем наименьшую площадь свободного сечения для прохода дымовых газов. Согласно приведенной схеме она будет равна:
где – число труб в одном горизонтальном ряду равное 2
Определим линейную скорость дымовых газов в самом узком сечении пучка по формуле:
– средняя температура дымовых газов в камере;
m = 2 – число параллельно работающих камер или в нашем случае число потоков сырья.
Для определения критериев Re и Pr нужно вычислить для дымовых газов при Тср=843 К кинематическую вязкость плотность теплоемкость и коэффициент теплопроводности.
Коэффициент динамической вязкости найдем по формуле:
где Мг – молекулярная масса и динамическая вязкость дымовых газов;
– динамические вязкости компонентов дымовых газов – определяются по номограмме [1];
– объемные доли компонентов дымовых газов в смеси.
Теплоемкость и коэффициент теплопроводности находим из таблиц [7]. Все необходимые данные приведены в табл 7.
Таблица 7 – Физико-химические свойства компонентов
дымовых газов при температуре 843 К
Теплопроводность Вт(м*К)
Далее рассчитаем массовые и объемные доли компонентов дымовых газов. Массовые доли:
Далее определим молярную массу дымовых газов:
Далее рассчитываем вязкость смеси [1]:
Плотность дымовых газов:
Кинематическая вязкость газов:
Коэффициент теплопроводности дымовых газов найдем по формуле:
где – коэффициент теплопроводности компонентов дымовых газов определяемый по таблице 6.
Теплоемкость дымовых газов:
где – теплоемкости компонентов дымовых газов;
– массовые доли компонентов в дымовых газах.
Находим значения критериев:
После подстановки всех величин в формулу для вычисления получим:
Коэффициент теплоотдачи излучением от трехатомных газов [6]:
где – коэффициенты теплоотдачи излучением от СО2 и Н2О определяемые по номограммам в зависимости от средней температуры дымовых газов в конвективной камере силы поглощения трехатомных газов и температуры стенки.
Также данные коэффициенты можно рассчитать используя формулу Нельсона [6]:
Среднелогарифмическая температура дымовых газов в конвекционной камере:
Суммарный коэффициент теплоотдачи будет равен:
В конвекционной камере проектируемой печи теплопередачи от дымовых газов к сырью в трубах осуществляется при смешано – перекрестном токе с индексом противоточности равным единице. Поэтому средний температурный напор рассчитывается по уравнению Грасгофа.
Из исходных данных и предыдущих расчетов необходимые температуры известны поэтому
Таким образом поверхность нагрева конвекционных труб
Определим число труб в конвекционной камере
Тогда число труб по вертикали в одной камере:
Высота занимаемая трубами в конвекционной камере при шаге труб по глубине конвекционного пучка S1=0148 м:
Рассчитаем теплонапряженность конвекционных труб:
Как видно из расчетов теплонапряженность конвекционных труб равна 89 кВтм2 что является допустимым так как среднее теплонапряжение конвекционной поверхности лежит в пределах 8 – 17.5 кВтм2.
7 Гидравлический расчет змеевика печи
Целью гидравлического расчета является определение гидравлического сопротивления змеевика печи. Давление на выходе из змеевика печи в нашем случае известно: Па. В проектируемой печи происходит частично испарение сырья поэтому гидравлический расчет змеевика ведем по методу Бакланова [3].
Давление сырья на входе в змеевик печи рассчитываем по формуле:
где – потери напора на участке испарения Па;
– потери напора на участке нагрева радиантных труб Па;
– потери напора в конвекционном змеевике печи Па;
– статистический напор необходимый для подъема нефти в змеевике от уровня ее ввода в конвекционный змеевик до уровня вывода из радиантных труб Па.
Расчет необходимо начинать с определения потерь напора на участке испарения:
где – давление в начале участка испарения Па.
Началу участка испарения соответствует сечения змеевика в котором сырье нагревается до температуры начала однократного испарения (ОИ). При этой температуре давления насыщенных паров сырья становится равным давлению вначале участка испарения которое определяется методом постепенного приближения.
Для облегчения расчетов предварительно строим вспомогательную кривую зависимости температуры начала однократного испарения сырья Тн.о.и от давления (или что то же самое кривую зависимости давления насыщенных паров сырья от температуры начала однократного испарения). Фракционный состав отбензиненной нефти (сырья) определим используя данные из «HYSYS». Фракционный состав нефти приведен таблице 8.
Таблица 8 – Фракционный состав нефти
Пределы кипения фракций К
Выход фракции мол.доля
Порядок построения кривой следующий: для каждой узкой фракции находим при нескольких температурах (в нашем случае при 483 533 583 633 683 К) давление ее насыщенных паров Pi по уравнению Ашворта [8]:
где Р — давление насыщенных паров Па;
Т — средняя температура кипения фракции К;
Т0 — температура кипения фракции при атмосферном давлении (в нашем случае следующие температуры – 483 533 583 633 683 ) К;
f (Т) f (T0) — функции соответствующих температур выражаемые уравнением:
Далее по уравнению изотермы жидкой фазы
находим для каждой из выбранных температур давление паров сырья.
В итоге все расчеты сведены в табл.9.
Таблица 9 – Давление насыщенных паров отбензинниной нефти
при различных температурах
По данным таблицы 9 построена кривая давления паров сырья (рис. 9).
Рисунок 9 – График для определения паров
Предварительно задаемся давлением в начале участка испарения Па и по кривой кипения отбензиненной нефти находим соответствующую этому давлению Тн =623 К. Если эта температура выше той с которой сырье входит в радиантные трубы то значит испарение сырья начинается в радиантной секции. В нашем случае Тн >Тк..
Найдем эквивалентную (расчетную) длину радиантных труб для одного потока сырья:
где = 65 м – полная длина трубы;
= 19 – число радиантных труб в одном потоке;
= 50 – коэффициент зависящий от вида соединения труб;
– внутренний диаметр радиантных труб м.
Рассчитаем эквивалентную длину участка испарения:
где = 863 кДжкг – энтальпия сырья в начале участка испарения при Тн = 623 К;
= 5834 кДжкг – энтальпия сырья на входе в радиантные трубы;
– энтальпия сырья на входе из печи равная:
Определим давление в начале участка испарения по формуле Бакланова:
где =200·103 Па – давление сырья на выходе в змеевик печи или что то же самое в конце участка испарения;
А и В – расчетные коэффициенты.
Коэффициент А находим по формуле:
где – коэффициент гидравлического сопротивления равный для атмосферных печей 0020 – 0024 (принимаем );
L1 – секундный расход сырья по одному потоку кгс;
= 660 кгм3 – плотность сырья при средней температуре на участке испарения Тср =05 (623 + 628) = 6255 К.
Коэффициент В находим по формуле
где е = 05533 массовая доля сырья на выходе из печи;
средняя плотность паров сырья при давлении 981 Па (принимается).
Давление в начале участка испарения:
Полученное значение совпадает с ранее приятым значением поэтому пересчет не требуется.
Вычисляем потерю напора на участке испарения:
Потери напора на участке нагрева радиантных труб:
где = 0031 – коэффициент гидравлического сопротивления;
– эквивалентная длина участка нагрева радиантных труб по одному потоку равная ;
– внутренний диаметр радиантных труб;
u – массовая скорость сырья в трубах кг(м2с);
– плотность отбензиненной нефти при средней температуре на участке нагрев радиантных труб () равная 680 кгм3
Массовая скорость сырья в трубах (одного потока):
Подставляя в формулу для числовые значния веичин получим:
Потери напора в конвекционном змеевике (для одного потока) найдем по формуле:
– эквивалентная (расчетная) длина конвекционного змеевика по одному потоку м;
– внутренний диаметр конвекционных труб;
uк – массовая скорость сырья в конвекционных трубах кг(м2с);
– плотность сырья при средней температуре в конвекционных трубах () равная 700 кгм3
Эквивалентная длина конвекционного змеевика для одного потока:
где – число труб в одном потоке;
= 65 м – полная длина трубы;
Подставляя в формулу для числовые значения величин получим:
Определим статистический напор в змеевике печи:
где – плотность сырья при Тср = 501 К.
Таким образом давление сырья на входе в змеевик печи будет:
8 Расчет потерь напора в газовом тракте печи
Общие потери напора по газовому тракту печи или величина тяги дымовой трубы рассчитывается по формуле:
где – величина разряжения в камере радиации (принимается =1962 Па);
– потери напора в камере конвекции Па;
– потери напора в борове Па;
– потери напора в дымовой трубе Па.
Потери напора в камере конвекции :
где – потери напора в конвекционном пучке труб Па;
– статический напор в камере конвекции при нисходящем потоке газов Па.
Потери напора в конвекционном пучке труб:
где – критерий Эйлера;
– плотность дымовых газов при средней температуре газов в конвекционной камере;
– линейная скорость дымовых газов в наиболее узком сечении пучка (найдена ранее);
b – коэффициент зависящий от угла атаки (угол между осью трубы и направлением потока газов) - принимается по таблице равным единице.
m = 19 – число рядов труб в пучке в направлении потока газов;
Re – критерий Рейнольдса (найден ранее).
Из приведенной выше формулы получим:
Статический напор в камере при нисходящем потоке газов:
где – высота столба газа в конвекционной камере;
– плотность воздуха при температуре окружающей среды.
Потери напора в борове :
где – потери напора на преодоление местных сопротивлений Па;
– потери напора на прямолинейном участке борова Па;
Предварительно проведем расчет газохода.
Площадь поперечного сечения борова:
где – секундное количество продуктов сгорания кгс;
u – массовая скорость газов в борове кг(м2).
Секундное количество продуктов сгорания:
Массовая скорость газов в борове:
где – линейная скорость газов в борове мс;
– плотность продуктов сгорания при температуре Тух = 593 К.
Примем линейную скорость газов в борове = 6 мс. Тогда
Принимаем высоту борова hб = 05 м ширину b = 1 м длину lб = 7 м.
Потери напора от местных сопротивлений рассчитываем по формуле:
где – сумма коэффициентов местных сопротивлений.
Дымовые газы делают в борове два поворота по 90о проходят шибер открытый наполовину а затем три входных канала в общий коллектор.
Коэффициент местного сопротивления при повороте на 90о [9].
Коэффициент местного сопротивления при входе газа в коллектор для наполовину открытого шибера .
По написанной выше формуле получим:
Потери на прямолинейном участке борова:
– коэффициент гидравлического сопротивления;
– эквивалентный диаметр борова м.
Коэффициент гидравлического сопротивления зависящий от величины критерия Рейнольдса находим по формуле:
где – кинематическая вязкость дымовых газов при температуре в борове Тб = Тух=593 К.
Кинематическую вязкость дымовых газов можно рассчитать как было показано выше. Из [7] по таблицам находим динамическую вязкость газов. Значения динамической вязкости дымовых газов приведены в табл.10:
Таблица 10 – Значение динамической вязкости дымовых газов при температуре 593 К
Динамическая вязкость мПа*с
Рассчитываем вязкость смеси [1]:
Потери напора в дымовой трубе:
где напора при входе газов в трубу и выходе из нее Па;
– потери напора на трение при движении газов в трубе Па.
Предварительно рассчитаем диаметр дымовой трубы:
– массовая скорость газов на входе в дымовую трубу кг(м2с).
Величину найдем по формуле:
где – линейная скорость газов на входе в дымовую трубу;
– плотность газов при их температуре входа в дымовую трубу кгм3;
Примем температуру Тогда
Подставив в формулу найденные выше числовые значения получим:
Потери напора при входе газов в трубу и выхде из нее определим по формуле:
где – коэффициенты местных сопротивлений;
uср – массовая скорость газов при их средней температуре в трубе кг(м2с).
– плотность газов при их средней температуре в трубе кгм3.
Из таблицы [1] найдем: .
Примем температуру газов на выходе из дымовой трубы Твых = 558 К имея в виду потери тепла поверхностью трубы в окружающую среду.
Тогда средняя температура газов в трубе будет равна:
Плотность газов при этой температуре:
Массовая скорость газов при их средней температуре в трубе:
Потери напора на трение при движении газов в дымовой трубе:
где – коэффициент гидравлического сопротивления;
Н – высота дымовой трубы м.
Определим по формуле Якимова:
где а – коэффициент равный 0025.
Предварительно приняв высоту трубы Н = 27 м получим:
Общая потеря напора по газовому тракту печи или величина тяги дымовой трубы:
Проверим высоту дымовой трубы:
где – температура окружающего воздуха К;
– средняя температура дымовых газов в трубе К.
Полученное значение Н мало отличается от ранее принятого поэтому пересчета делать не следует.
Автоматизации трубчатой печи
Целью данного раздела является автоматизация трубчатой печи и подбор соответствующих датчиков КИП. В трубчатой печи необходимо контролировать следующие параметры:
температура – до входа в печь мазут должен быть иметь определенную температуру;
давление – снижение давления мазута ниже 8 атм приводит к значительному ухудшению качества распиливания и уменьшению производительности форсунок;
расход – определяет выходную температуру отбензининной нефти.
расход – в данном случае расход воздуха будет зависеть от подаваемого в печь мазута;.
Для входного потока отбензинниной нефти:
температура – должна быть в определенных пределах так как сильно низкая температура повлияет на нагрузку печи;
расход – оказывает влияние на нагрузку печи и обеспечивает необходимое давление на выходе из печи.
Для выходного потока нефти:
температура – на выходе из печи нефть должна быть нагрета до заданной температура так как затем поступает на разделение;
давление – на выходе из печи нефть должна иметь определенной давление так как затем поступает на разделение.
концентрация кислорода – по концентрации остаточного кислорода судят о полноте (эффективности) сгорания топлива а также имеется возможность определения потери тепла с дымовыми газами;
давление – достаточно низкое давление в дымоходе необходимо для отвода отработавших газов;
температура – резкий рост температуры дымовых газов на перевалах печи при сохранении других показателей работы установки прежними свидетельствует об образовании кокса на внешних стенках змеевиков.
Для печи – контроль пламени.
В табл. 11 приведены нормы технологического режима для вышеуказанных параметров датчики КИП диапазоны их измерений и количество приборов.
Таблица 11 – Контролируемые параметры и средства автоматизации
Наименование прибора
Краткая техническая характеристика
Расход топочного мазута
Ультразвуковой расходомер счетчик вязких жидкостей
Измеряемая среда – вязкие жидкости;
±075% от текущего значения
Частотный 0-1000Гц импульсный выход (кг на импульс);
Сигнал (токовый) выход 4-20 мА;
Интерфейс RS485 (часы реального времени и архив);
Источник бесперебойного питания.
Питание 12-24-36 В постоянного тока.
Температура топочного мазута
Интеллектуальный датчик температуры
Диапазон температур от -50 д0 +150°С
Температура окружающей среды: -40 80°С
-20 мА с HART-протоколом; 0-5 мА
Основная приведенная погрешность
до ±0075%; опции до ±02%; ±05%
Взрывозащищенное исполнение
Давление топочного мазута
Интеллектуальный датчик давления
Измеряемые среды: жидкости в т.ч. нефтепродукты; пар газ газовые смеси
Диапазоны измеряемых давлений:
минимальный 0-0025 кПа;
максимальный 0-68 МПа
-20 мА с HART-протоколом
до ±0075%; опция до ±02%
Перенастройка диапазонов измерений
Высокая стабильность характеристик
Взрывозащищенное исполнение вида
Измеритель расхода воздуха
Температура воздуха от 0 до 50 °С;
Расход воздуха – до 99999 м3ч;
Защищенность от электромагнитных помех (EMI) защищенность от радиопомех (RFI) электромагнитная совместимость (EMC);
Относительная влажность –до 90 ;
Датчик пламени Siemens
Датчики контроля пламени Siemens QRA2 разработаны для совместного использования вместе с автоматами горения Сименс для контроля пламени горения газа желтого или синего пламени горения жидкого топлива и для проверки искры зажигания они поддерживает прерывистую работу. Металлизированный пластмассовый корпус предотвращает образование статических зарядов создаваемых потоками воздушных масс от работающего вентилятора и устанавливается непосредственно на горелочном устройстве
Концентрация кислорода в дымовых газах
Анализатор кислорода в дымовых газах
Пределы измерения концентрации кислорода об.% - 01-23;
Погрешность измерения – +- 20 %;
Время реагирования 30с;
Аналоговый выход –4-20 мА;
Интерфейс связи с ЭВМ – RS-485;
Температура окружающей среды у блока газоанализатора – -30 - +50 °С;
Характеристика анализируемого газа:
- температура до +600 °С .
Давление дымовых газов
Дифференциальный датчик-реле для контроля давления дымовых газов
Регулировочная шкала с цифровыми обозначениями уставок в Па позволяет легко настроить датчик
Пластмассовый корпус
Высокая чувствительность мембраны;
Небольшие габаритные размеры
Диапазон измерений –20-5000 Па;
Температура дымовых газов
Диапазон температур от -200 д0 +800°С
Температура входного потока нефти
Диапазон температур от -50 д0 +300°С
Расход входного потока нефти
Массовый расходомер со сдвоенной прямой измерительной трубой
OPTIMASS 1000 производства Krohne
Максимальный расход до 50000 кгч;
Простота и удобство дренирования и очистки измерительной трубы
Устойчив к воздействию внешних негативных факторов
Оптимизированный разделитель потока для минимизации потери давления
Высокий уровень точности и превосходное соотношение цены и производительности
Модульная концепция электронного блока: простота замены электроники.
Давление выходного потока нефти
Температура выходного потока нефти
В данном курсовом проекте был произведен технологический расчет трубчатой печи для подогрева отбензиненной нефти.
Расчет состоял из восьми этапов на каждом из которых были получены данные необходимые для того чтобы спроектировать трубчатую печь. Так результатом расчетов первых двух этапов (расчет процесса горения топлива и расчет к.п.д. печи и расхода топлива) стала полная тепловая нагрузка значение которой Qт = 4709 кВт. В следующем этапе была рассчитана поверхность радиантных труб которая позволила подобрать типоразмер печи. Была выбрана печь типа АБ2 высотой 234 м и длиной 89 м с поверхностью нагрева радиантных труб 816 м2 длиной труб 6 м допустимым теплонапряжением 35 кВтм2. В печах данного типа могут быть использованы только беспламенные горелки типа – ГБП. Мы выбрали горелки типа ГБП мощность 1200 кВт. Далее в этапе расчета рассчитали высоту радиантной секции равной 5125 м и ширину радиантной секции равной 27 м при этом размеры радиантных труб равны 114×8 мм. Подтвердили расчетом температуру газов выходящих из топки. Расчет камеры конвекции дал нам информации о высоте hк = 2664 м при этом размеры труб камеры конвекции составили 76×6 мм. Был проведен расчет определения давления отбензиненной нефти на входе в змеевик печи – давление составило 44 атм. В следующем разделе был проведен аэродинамический расчет дымовой трубы получены ее размеры: диаметр равный D = 08 м и высота h = 27 м. В последнем разделе приведена автоматизация трубчатой печи с указанием датчиков КИП и диапазонами измерений.
Список использованной литературы
ГОСТ 10585-99 «Топливо нефтяное. Мазут. Технические условия»
Кузнецов А.А. Кагерманов С.М. Судаков Е.Н. Расчеты процессов и аппаратов нефтеперерабатывающей промышленности Л.: Химия. 1974 г. - 344 с.
Трубчатые печи: Каталог Составители А.А. Казенов Г.В.Филатов Ц.А. Бахшиян М.Н. Вергасова. М:ЦИНТИхимнефтемаш 1990 г. - 32 с.
Горелки для трубчатых печей: Каталог Составители А.А. Казенов Г.В.Филатов Ц.А. Бахшиян М.Н. Вергасова. М:ЦИНТИхимнефтемаш 1990 г. – 25 с.
Скобло А.И. Молоканов Ю.К. А.И. Владимиров. Процессы и аппараты нефтегазопереработки и нефтехимии. – М.: Недра 2000 г. – 677 с.
О.Флореа О. Смигельский. Расчеты по процессам и аппаратам химической промышленности. – М: Химия 1971 г. – 448 с.
Кирсанов Ю.Г. Расчетные и графические методы определения свойств нефти и нефтепродуктов. – Екатеринбург: Изд-во Урал. ун-та 2014. — 136 с.
Юренев В.Н. Лебедев П.Д. Теплотехнический справочник. Изд. 2-е перераб. – М.: «Энергия» 1976. – 896 с. с ил.
титульник.docx
федеральное государственное автономное образовательное учреждение
«НАЦИОНАЛЬНЫЙ ИССЛЕДОВАТЕЛЬСКИЙ
ТОМСКИЙ ПОЛИТЕХНИЧЕСКИЙ УНИВЕРСИТЕТ»
Направление подготовки (специальность)Химическая технология
КафедраХимической технологии топлива и химической кибернетики
ПОЯСНИТЕЛЬНАЯ ЗАПИСКА
к курсовому проектуработе
по дисциплине «Технологическое проектирование и типовое оборудование процессов переработки природных энергоносителей»
(Название дисциплины)
на тему «Проектирование печи подогрева отбензининной нефти»
(Номер группы) (Подпись) (Ф.И.О.)
Руководительк.т.н. доцентМ.А. Самборская
(Ученая степень ученое звание должность) (Ф.И.О.)
(Оценка руководителя) (Подпись)
Рекомендуемые чертежи
- 24.01.2023