Проектирование организации средств контроля в процессе производства детали Вал




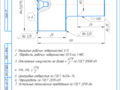
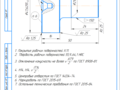
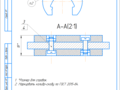
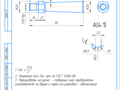
- Добавлен: 24.01.2023
- Размер: 1 MB
- Закачек: 0
Описание
Состав проекта
![]() |
![]() |
![]() |
![]() |
![]() ![]() ![]() ![]() |
![]() |
![]() ![]() ![]() ![]() |
![]() |
![]() ![]() ![]() ![]() |
![]() |
![]() ![]() ![]() ![]() |
![]() |
![]() ![]() ![]() ![]() |
![]() ![]() ![]() ![]() |
![]() ![]() ![]() ![]() |
![]() ![]() ![]() ![]() |
![]() ![]() ![]() ![]() |
![]() |
![]() |
![]() ![]() ![]() ![]() |
![]() ![]() ![]() ![]() |
![]() ![]() ![]() ![]() |
![]() ![]() ![]() ![]() |
![]() |
![]() ![]() ![]() ![]() |
![]() |
![]() ![]() ![]() ![]() |
![]() ![]() ![]() ![]() |
![]() ![]() ![]() ![]() |
![]() ![]() ![]() ![]() |
![]() |
![]() ![]() ![]() ![]() |
![]() |
![]() ![]() ![]() ![]() |
![]() |
![]() ![]() ![]() ![]() |
![]() ![]() ![]() ![]() |
![]() ![]() ![]() |
![]() |
![]() ![]() ![]() |
![]() ![]() ![]() |
![]() ![]() ![]() |
Дополнительная информация
Калибр предельный 2,8Н14.cdw

Калибр 57±0,2 ГОСТ 2534-77.cdw

166h12.cdw

Кольцо 1-90хg6х3,5х9h3 ГОСТ 24969-81.cdw

Калибр-пробка 8133-0960 H14 ГОСТ 14810-69.cdw

Калибр-пробка 8133-0960 Н14 ГОСТ 14810-69.spw

Ручка 8054-0018 ГОСТ 14748-69.cdw

Вставка 8133-0960002 H14 ГОСТ 14810-69.cdw

Вставка 8133-0960001 H14 ГОСТ 14810-69.cdw

Калибр-пробка 5-45х2х9Н3 ГОСТ 24969-81.spw

Калибр-пробка 5-45х2х9Н3 ГОСТ 24969-81.cdw

Ручка 8055-0062 ГОСТ 17767-72.cdw

Пробка 5-45х2х9Н_3 ГОСТ 24969-81.cdw

Калибр 9±0,5 ГОСТ 2534-77.cdw

Калибр-скоба 8113-0149 ГОСТ 18360-93.cdw

Ручка накладка 8056-0015 ГОСТ 18369-73.cdw

190202.001.003.00.spw

ф70k6 калибр-скоба.cdw

Калибр 53±0,2 ГОСТ 2534-77.cdw

Шаблон 92.8166-0174 ОСТ 92-4481-84.cdw

Калибр 110±0,5 ГОСТ 2534-77.cdw

Вал.cdw

Карта контр.форма 2а лист 3.FRW

Карта контроля. Форма 2 лист1.FRW

Карта контр.форма 2а лист 2.FRW

Рекомендуемые чертежи
- 31.01.2023
- 26.04.2016
- 13.05.2023
- 13.05.2023
- 13.05.2023