Проектирование и исследование механизма качающегося конвейера




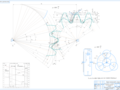
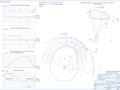
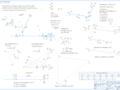
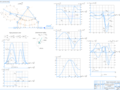
- Добавлен: 24.01.2023
- Размер: 4 MB
- Закачек: 2
Описание
Состав проекта
![]() |
![]() |
![]() |
![]() |
![]() ![]() ![]() ![]() |
![]() ![]() ![]() ![]() |
![]() ![]() ![]() ![]() |
![]() ![]() ![]() |
![]() |
![]() ![]() ![]() ![]() |
Дополнительная информация
Лист 2.cdw

Лист 1.cdw

Лист 3.cdw

Лист 4.cdw

Рекомендуемые чертежи
Свободное скачивание на сегодня
- 22.08.2014
- 29.08.2014