Проектирование автоматизированной системы для обработки корпусной детали в составе основного и вспомогательного технологического оборудования




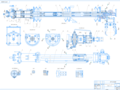
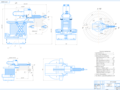
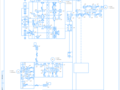
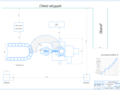
- Добавлен: 24.01.2023
- Размер: 913 KB
- Закачек: 1
Описание
Состав проекта
![]() |
![]() |
![]() ![]() ![]() ![]() |
![]() ![]() ![]() |
![]() ![]() ![]() ![]() |
![]() ![]() ![]() ![]() |
![]() ![]() ![]() ![]() |
![]() ![]() ![]() |
![]() ![]() ![]() ![]() |
Дополнительная информация
3'.cdw

ФЕДЕРАЛЬНОЕ АГЕНСТВО ПО ОБРАЗОВНИЮ.docx
Московский Государственный Технический Университет «МАМИ»
Факультет «Автоматизация и управление»
Кафедра «Автоматизированные станочные системы и инструмент»
ПОЯСНИТЕЛЬНАЯ ЗАПИСКА
к курсовому проекту по курсу «Проектирование автоматизированных систем»
«Проектирование автоматизированной системы для обработки корпусной детали в составе основного и вспомогательного технологического оборудования»
Преподаватель: Иванников С.Н.
Объект производства – деталь типа корпусная.
Материал детали – Сталь 40Х с твердостью HB = 170 217;
Масса детали – m = 25 кг.
Годовая программа выпуска деталей – N = 50000 штгод.
Номенклатура выпуска изделий – Т = 5 шт.
1 Тенденции развития оборудования ..4
2 Описание автоматизированной системы .5
Описание оборудования станка 2Р135Ф2 .6
1 Общие сведения о станке 2Р135Ф2 ..6
2 Описание основных элементов станка .6
3 Основные технические данные и характеристики
вертикально-сверлильного станка 2Р135Ф2 .11
4 Анализ производства 12
5 Расчет припусков и межоперационных размеров на обрабатываемые поверхности детали .12
6 Расчет режимов резания 13
6.1 Фрезерование (одноинструментная обработка) .13
6.2 Сверление (двушпиндельная головка) 14
Описание ПР "Универсал 5.02" .15
1 Общее описание .15
2 Описание захватного устройства робота .18
3 Техническая характеристика ПР "Универсал 5.02" 22
4 Описание делительно-поворотного стола 23
5 Расчет элементов робота 24
Описание транспортной системы 26
Описание системы управления 27
Выводы по курсовому проекту 31
Список литературы 32
1 Тенденции развития оборудования
В настоящее время наметились тенденции к увеличению номенклатуры выпускаемых изделий и сокращению размеров серий. В итоге около 80% производства носит мелкосерийный характер в связи с этим необходимо обеспечить гибкость производства что достигается применением технологического оборудования с ЧПУ.
Технологическое оборудование с ЧПУ объединяют в единые производственные комплексы с помощью транспортных и управляющих систем. Такие производственные комплексы называются гибкими автоматизированными производственными системами (ГПС).
Для сохранения производительности ГПС при отказе отдельного оборудования обычно предусматриваются буферные накопители которые позволяют разбить ГПС на ряд участков обладающих некоторой функциональной независимостью друг от друга.
Такие участки называют технологическими а в случае применения роботов – роботизированными комплексами (РК).
РК охватывают группу оборудования в пределах которой изделия перемещаются только поштучно. Его началом (входом) и окончанием (выходом) являются различного рода накопители.
РК в которых роботы только разгружают и загружают основное технологическое оборудование называются РТК.
В данной курсовой работе построена базовая планировка составлен алгоритм работы циклограмма и другие параметры РТК для обработки детали типа «корпусная деталь».
2 Описание автоматизированной системы
Заданием на курсовой проект является эскиз детали которую необходимо обработать в автоматизированном производстве с применением малолюдной или что является предпочтительным безлюдной технологии. Нашей задачей является разработать и сконструировать автоматизированный участок для проведения над заданной деталью нескольких операций.
Для того чтобы технологический процесс был автоматизирован целесообразно применить станок 2Р135ПФ2 с числовым программным управлением. Это позволит нам не только обрабатывать деталь которая дана заданием но и предусмотреть некоторую гибкость данного участка под обработку других деталей типа тел вращения.
Один станок не позволит нам полностью обеспечить автоматизацию. Для загрузки и разгрузки станка применим промышленный робот Универсал-5.02.
Так как данный робот не может осуществит правильное положении детали то нам придется применить тактовый стол на котором детали будут находится в нужном положении для установки их на станок роботом. Чтобы правильно расположить деталь на столе можно применить систему позиционирования деталей которая будет устанавливать деталь в нужное нам положение.
Описание оборудования станка 2Р135Ф2
1 Общие сведения о станке 2Р135Ф2
Назначение и область применения. Станок вертикально-сверлильные 2Р135Ф2 предназначены для выполнения следующих видов работ: сверления рассверливания зенкерования зенкования развертывания и растачивания отверстий. Растачивание отверстий в том числе расположенных на расстояниях с допусками по II квалитету кроме того станок 2Р135ПФ2 предназначен для легкого фрезерования. Обработка производится быстрорежущим и твердосплавным инструментом в деталях из различных конструкционных материалов. Станки используются для работы в условиях единичного мелкосерийного и серийного производства в ремонтных и сборочных цехах.
Реверсирование электродвигателя главного движения позволяет производить на станках нарезание резьбы машинными метчиками.
Вид климатического исполнения У.ХЛ4 или ТЗ по ГОСТ 15150-69. Класс точности: II по ГОСТ 8-82E.
2 Описание основных элементов станка
) Основание. Колонна станка представляет собой пустотелую чугунную отливку коробчатой формы. Механизированный крестовый стол на станке крепится в Т-образных пазах на неподвижном столе-тумбе. На фундаментной плите внутри колонны установлен электронасос Фундаментная плита является резервуаром для охлаждающей жидкости.
) Коробка скоростей и привод. Коробка скоростей сообщает шпинделю 12 различных частот вращения с помощью передвижных блоков. Опоры валов коробки скоростей размещены в двух плитах: верхней 1 и нижней 4 скрепленных между собой четырьмя стяжками о. Коробка скоростей получает вращение от вертикально расположенного электродвигателя через эластичную муфту 10 и зубчатую передачу 5. Последний вал 2 коробки (гильза) имеет в отверстии шлицы через которые вращение передается шпинделю. Через зубчатую пару 3 вращение передается на коробку подач.
Смазка коробки скоростей как и всех сборочных единиц сверлильной головки производится от плунжерного насоса закрепленного на нижней пучите 4.
Работа насоса контролируется специальным масло-указателем на передней части подмоторной плиты.
) Механизм переключения скоростей и подач. Переключение скоростей производится рукояткой 1 которая в зависимости от конструкции имеет четыре или пять положений по окружности и три вдоль оси.
Переключение подач осуществляется рукояткой 2 имеющей три положения по окружности и три положения вдоль оси. Рукоятки расположены на передней части сверлильной головки. Отсчет включаемых скоростей и подач производится по табличкам.
) Коробка подач. Коробка подач смонтирована в отдельном корпусе и устанавливается в сверлильной головке. Перемещением двух тройных блоков шестерен осуществляется девять различных подач.
Последний вал коробки подач сцентрирован с верхней опорой червяка механизма подачи. На валу коробки подач установлена полумуфта 1 передающая вращение червяку механизма подачи.
) Шпиндель. Шпиндель 1 смонтирован на двух шарикоподшипниках. Осевое усилие подачи воспринимается нижним упорным подшипником а усилие при выбивки инструмента - верхним. Подшипники расположены в пиноли 2 которая с помощью реечной пары перемещается вдоль оси. Для выбивки инструмента из конуса морзе шпинделя служит специальное приспособление на головке шпинделя. Выбивка происходит вращением штурвала от руки при подъеме шпинделя. Обойма 4 приспособления упирается в корпус сверлильной головки и рычаг 3 поворачиваясь вокруг оси выбивает инструмент.
) Сверлильная головка. Сверлильная головка представляет собой чугунную отливку коробчатой формы в которой монтируются все основные сборочные единицы станка: коробка скоростей коробка подач шпиндель механизм подачи противовес шпинделя и механизм переключения скоростей и подач.
Ручная подача шпинделя осуществляется вращением штурвала 6 на себя. При этом храповой механизм должен быть разъединен что достигается перемещением штифта 12 в правое положение при помощи рукоятки 5 которая должна занять верхнее положение. Дня передачи момента от штурвала на вал-шестерню 16 штифт запрессованный в полумуфту II должен быть совмещен с правым пазам на рукоятке 5 установленной на валу-шестерне от которого через реечную передачу происходит поступательное перемещение пиноли со шпинделем.
Для перехода с ручного режима работы на автоматический цикл с правой стороны сверлильной головки на оси штурвала под крышкой расположен механизм переключения о ручной подачи шпинделя на механизированную.
Откинув крышку 10 вниз необходимо повернуть рукоятку 5 на 180° вокруг оси из верхнего положения в нижнее. При этом эксцентрик 13 через палец 14 нажимает на штифт 12 который перемещаясь в крайнее левое положение вместе с диском 9 выводит из зацепления кулачковую полумуфту 17 а зубцы двустороннего диска 8 входят в зацепление с зубцами червячного колеса 7. Произошла подготовка к работе механизма быстрого подвода шпинделя. После нажатия кнопки "Пуск" включается электродвигатель быстрых перемещений расположенный с левой стороны сверлильной головки. При этом электродвигатель главного движения и электромагнитные муфты отключены. Электродвигатель быстрых перемещений шпинделя через ременную передачу пружинную муфту и червячную передачу передает вращение на вал-шестерню 16 а от нее на реечную пару. В результате этого шпиндель через связанную с ним пиноль ползает поступательное движение. Происходит быстрый подвод шпинделя к обрабатываемой детали. При этом от вала-шестерни 16 через двойной блок шестерен 21 вращение передается:
) через мелкомодульную зубчатую пару и эластичную му^ту на датчик контроля перемещения шпинделя работа которого в свою очередь контролируется УЦИ.
) через зубчатую пару внутреннего зацепления и ось 3 на ступицу 2 с установленными на ней кулачками 4 1 которые в необходимый момент включают датчики контроля нулевой точки ограничивающие движение пиноли вверх и вниз. Датчики подают сигнал на отключение электродвигателя быстрых перемещений включение южней тормозной электромагнитной муфты расположенной на валу червяка которая отключается после остановки электродвигателя быстрых ходов включение электродвигателя главного движения и верхней электромагнитной муфты соединяющей коробку подач с валом червяка который через червячное колесо 7 зубчатый диск 8 полумуфту 17 и вал шестерню 16 передает движение пиноли 2 со шпинделем 1. Происходит механическая подача. При этом штифт 15 находится в левом пазу рукоятки 5 позволяющем провернуть штурвал на 20 что дает возможность кулачках полумуфт II и 17 выйти из зацепления.
По окончании механической подачи т.е. окончании обработки детали отключается верхняя электромагнитная муфта 23 включается нижняя тормозная муфта 24 которая после полного прекращения механической подачи должна быть отключена включается электродвигатель быстрых ходов и через описанную выше кинематическую цепь: пружинная муфта - червячная пара - реечная пара - происходит быстрый отвод шпинделя вверх.
В специальном отверстии в нижней части сверлил ной головки с лицевой стороны под крышкой расположен механизм зажима пиноли шпинделя при фрезеровании плоскостей. К пиноли подводят при помощи рукоятки 18 винтом 20 связанную с ним опору 19 и зажимают пиноль которая перед зажимом должна быть установлена вместе со шпинделем в крайнее верхнее положение. При выполнении на станке других видов работ опору выдвигают в крайнее заднее положение поворотом рукоятки. Контроль зажима осуществляется датчиком.
В коробке скоростей установлен датчик контроля вращения шпинделя при перемещении крестового стола в режим фрезерования взаимодействующий с датчиком зажима пиноли.
3 Основные технические данные и характеристики вертикально-сверлильного станка 2Р135Ф2
Технические характеристики основные параметры и размеры согласно ОСТ2 Н62-1-85 ОСТ2 Н62-6-79 ГОСТ 24644-81 и техническому задании.
Наибольший диаметр сверления мм
Наибольший диаметр нарезаемой резьбы мм
Наибольший крутящий момент кгсм
Наибольшее усилие подачи кгс
Число шпинделей револьверной головки
Размер конуса шпинделя
Количество скоростей шпинделя
Пределы скоростей шпинделя ммоб
Пределы рабочих подач мммин
Размеры рабочей поверхности стола мм
Наибольшее расстояние от торца шпинделя до стола мм
Наибольшее рабочее перемещение суппорта мммин
Скорость быстрого перемещения суппорта ммин
Точность позиционирования стола и суппорта мм
Повторяемость позиционирования стола и суппорта мм
Мощность электродвигателя главного привода кВт
Габаритные размеры станка мм
4 Анализ производства
Для изготовления данной детали необходимо обработать три плоских поверхности и четыре отверстия. В соответствии с заданием обработка реализуется фрезерованием и сверление.
Плоские поверхности 1 2 и 3 можно обработать концевой удлиненной фрезой боковой ее поверхностью. Диаметр фрезы D = 32 мм длина рабочей части l = 100 мм по ТУ2-035-710-80.
Поверхность 1 обрабатывается при горизонтальном расположении фрезы с вертикальной ее подачей вниз; поверхность 2 – при вертикальном положении фрезы с горизонтальной подачей поверхность 3 – при горизонтальном положении фрезы с горизонтальной подачей. Размер рабочей части инструмента позволяет обработать каждую из поверхностей за один проход при небольшом припуске на обработку.
Поверхности 4 и 5 – внутренние цилиндрические. Отверстия можно получить сверлением инструментом с диаметром равным диаметру отверстия. Т.е. для 4 и 5 поверхностей используются сверла d = 16 мм и d = 10 мм соответственно. Оба отверстия 4 и 5 сверлятся за один рабочий ход при условии использования многошпиндельных насадок.
5 Расчет припусков и межоперационных размеров на обрабатываемые поверхности детали
В условиях массового производства форма заготовки должна быть максимально приближена к форме детали. Исходя из этого назначаем припуск на обработку t1 = t2 = t4 = 3 мм.
Припуск на сверление равен d2 т.е. t4 = 8 мм t5 = 5 мм.
6 Расчет режимов резания
6.1 Фрезерование (одноинструментная обработка)
Длина рабочего ходаLр.х.= Lрез+y
Lрез (1) = 90 мм; Lрез (2) = 60 мм; Lрез (3) = 60 мм;
Lр.х. (1) = 102 мм; Lр.х. (2) = 72 мм; Lр.х. (3) =72 мм;
Средняя ширина фрезерования bср = FLрез где F – площадь фрезеруемой поверхности
bср (1) = 60 мм; bср (2) = 90 мм; bср (3) = 60 мм;
Подача на зуб фрезы sz в ммзуб
Стойкость фрезы Тр в мин резания Тр = Кф*Тм* где
Кф – коэффициент учитывающий количество инструментов в наладке;
Кф = 1 (один инструмент);
– коэффициент времени резания инструмента = LрезLр.х > 07 можно не учитывать;
Тм - стойкость фрезы в минутах машинной работы Тм = 60 мин;
Скорость резания v = vтаблК1К2К3 ммин где
К1-коэффициент зависящий от обрабатываемого материала;
К2-коэффициент зависящий от стойкости и марки твердого сплава;
К3-коэффициент зависящий от вида обработки;
vтабл (1) = 60 ммин; vтабл (2) = 64 ммин; vтабл (3) = 64 ммин;
К1 = 1; К2 = 065; К3 = 12;
v(1) = 468 ммин; v(2) = 499 ммин; v(3) = 499 ммин;
Число оборотов шпинделя n = 1000v(*D) обмин
n(1) = 4655 обмин; n(2) = 4964 обмин; n(3) = 4964 обмин;
Скорость резания по принятому числу оборотов v = *D*n1000 ммин
Минутная подача sм = sz*z*n мммин
Основное машинное время обработки tм = Lр.хsм мин
tм (1) = 058 мин; tм (2) = 041 мин; tм (3) = 041 мин.
6.2 Сверление (двушпиндельная головка)
y1 = 6 мм; y2 = 5 мм;
Lрез (1) = 10 мм; Lрез (2) = 15 мм;
Lр.х. (1) = 16 мм; Lр.х. (2) = 20 мм;
s0 (1) = 032 ммоб; s0 (2) = 022 ммоб;
Стойкость инструмента Тр в мин резания Тр = Тм* где
– коэффициент времени резания инструмента = LрезLр.х;
(1) = 0625; (2) = 075;
Тм – стойкость сверла в минутах машинной работы Тм = 60 мин;
Тр = Тм (1) = 55 мин; Тм (2) = 35 мин;
Тр (1) = 344 мин; Тр (2) = 263 мин;
К2-коэффициент зависящий от стойкости инструмента;
К3-коэффициент зависящий от отношения длины резания к диаметру;
vтабл (1) = 19 ммин; vтабл (2) = 20 ммин;
К1 = 07; К2 = 13; К3 при горизонтальном сверлении не учитывается;
v(1) = 173 ммин; v(2) = 182 ммин;
Число оборотов шпинделя n = 1000v(*d) обмин
n(1) = 344 обмин; n(2) = 579 обмин;
Минутная подача sм = s0*n мммин
sм (1) = 110 мммин; sм (2) = 127 мммин;
tм (1) = 015 мин; tм (2) = 016 мин;
Описание ПР "Универсал 5.02
Многоцелевые ПР типа «Универсал-5» применяются для автоматизации погрузочно-разгрузочных работ обслуживания различного технологического оборудования межоперационного и меж станочного транспортирования объектов обработки и выполнения других вспомогательных операции.
Исполнительным механизмом ПР является манипулятор который обеспечивает установку в пределах рабочей зоны захватного механизма схвата. Манипулятор имеет четыре степени подвижности руки 1 в сферической системе координат которые реализуются механизмами: поворота 2 относительно оси П—П выдвижения 3 руки 1 вдоль оси — поворота 4 руки относительно вертикальной оси —7 подъема 5 руки вдоль оси —. Две ориентирующие степени подвижности рабочего органа схвата 7 создают механизмы 6 вращения кисти руки относительно ее продольной оси — и поперечной оси IV—IV. Подвижные механизмы манипулятора защищены от попадания пыли грязи и масла ограждением 8.
Установочные перемещения руки осуществляются помощью электромеханических следящих приводов а ориентирующие движения кисти руки и зажим - разжим схвата — пневмоцилиндрами.
Пневмоблок 9 которым комплектуется ПР предназначен для подготовки регулирования подачи сжатого воздуха из заводской сети и блокирования работы манипулятора при падении давления ниже допустимого.
Блок 10 тиристорных электроприводов формирует управляющие напряжения в якорной цепи электродвигателей постоянного тока.
Устройство программного управления 11 позиционного типа имеет возможность записи программы в режиме обучения (по первому циклу) и формирует управляющие сигналы на блок 10 а также технологические команды управления циклом работы манипулятора и обслуживаемого оборудования.
Блоки тиристорного электропривода ЭПТ6-У5.02 обеспечивают управление в следящем режиме электродвигателями постоянного тока типа СЛ-569 и СЛ-661 установленными в механизмах четырех программируемых степеней подвижности манипулятора.
Механизмы электроприводов включают в себя зубчатые или червячные редукторы параметры которых даны в кинематической схеме. Обратная связь исполнительных механизмов манипулятора по положению и скорости осуществляется потенциометрическими датчиками типа ППМЛ приводящимися с помощью зубчатых редукторов и тахогенераторов типа СЛ-121 которые приводятся в движение специальными зубчатыми или ременными механизмами.
Пневмоблок которым комплектуется ПР предназначен для подготовки сжатого воздуха подаваемого из заводской сети к манипулятору а также для циклового управления двумя ориентирующими движениями кисти руки и захватным устройством. Приводы этих движений осуществляются от пневмоцилиндров. Для преобразования поступательного перемещения поршня во вращательное движение кисти руки используются винтовой копир (в приводе поворота кисти руки относительно ее продольной оси) и передача рейка-шестерня (в приводе качания кисти относительно поперечной оси). Привод зажима и разжима губок схвата осуществляется рычажным механизмом присоединенным к штоку пневмоцилиндра. Соединение механизмов манипулятора между собой и устройством аналогового позиционного программного управления типа АПС-1 производится в соответствии с принципиальной электрической схемой.
Базовым узлом манипулятора является механизм поворота конструкция которого показана на листе. В неподвижном корпусе на радиально-упорных подшипниках 2 установлена подвижная планшайба 3 получающая вращение от механизма привода 4 .который установлен в корпусе 1. Механизм привода поворота состоит из электродвигателя 5 постоянного тока червячного редуктора 6 и жестко связанного с валом червяка 7 тахогенератора 8. Крутящий момент на планшайбу 3 передается через цилиндрическую зубчатую передачу колесо 9 которой находится в зацеплении с выходной шестерней 10 редуктора.
На специальном кронштейне 11 закрепленном на корпусе установлен потенциометрический датчик положения 12 валик которого получает вращение через зубчатую передачу. Разрезная шестерня 13 привода находится в зацеплении с зубчатым колесом 9. На крышке 14 предохраняющей от попадания в радиально-упорные подшипники 2 пыли и грязи установлено ограждение 15 внутри которого укладывают два витка электрокабеля. В крышке 14 закреплен угольник 16 в который ввернута труба 17 воздуховода. Через трубу 17 на переднем конце которой установлен обратный клапан - 18 сжатый воздух проходит к угольнику 19 а от него по шлангу подается к пневмоцилиндрам механизма руки.
На неподвижном корпусе установлен дополнительный кронштейн 20 с амортизирующими резиновыми пластинами которые являются ограничителями поворота подвижной планшайбы.
С целью выбора люфта в механизме привода червячное колесо 21 выполнено разрезным: нижняя половина колеса надета на шлицевый вал 22 а верхняя — на ступицу его нижней половины. Выбор люфта производится эксцентриком 23 путем поворота верхней половины червячного колеса относительно нижней. После установления требуемого бокового зазора (002 006 мм) обе половины червячного колеса 22 закрепляются винтами 24.
На планшайбе механизма поворота установлен механизм подъема манипулятора. Механизм подъема манипулятора выполнен в виде пространственного рычажного устройства (типа пантографа) неподвижные нижние шарниры которого закреплены в кронштейне на основании 2. Подвижные нижние шарниры пантографа установлены на каретке 3 которая перемещается на роликах 4 по направляющим 5. При горизонтальном движении каретки 3 пантограф перемещается вертикально вместе с верхней платформой 6. К платформе крепится механизм поворота руки (на рисунке не показан) и скалка 7 являющаяся направляющей для конических роликов 8 каретки 9 в которой установлены верхние подвижные шарниры 10 пантографа.
Механизм привода подъема манипулятора состоит из двух электродвигателей 11 постоянного тока установленных соосно относительно руг друга на основании 2 редуктора 12 и винтовой передачи 13. Консоль перемещения выполняется с помощью потенциометрического датчика 14 соединенного с помощью зубчатой передачи 15 с ходовым винтом. Обратная связь по скорости осуществляется тахогенератором 16 который соединен зубчато-ременной передачей 17 с входным валом редуктора 12.
Винтовая передача 13 конструктивно представляет собой винт 18 с трапецеидальной резьбой установленный в опорах на подшипниках качения. В корпусе 20 каретки 3 установлены две полу гайки 19. Для компенсации погрешности расположения опор винта относительно направляющих 6 корпус 20 имеет осевой люфт (001-003 мм) и радиальный зазор (05 мм) относительно каретки 3.
Для выбора бокового зазора в зацеплении цилиндрических колес редуктора 12 и передачи 15 привода датчика положения (потенциометра) 14 ведомые зубчатые колеса 21 и 22 выполнены разрезными разводящими пружинными кольцами.
2 Описание захватного устройства робота
При выборе типа зажимного устройства для промышленного робота необходимо в качестве исходных данных учитывать:
)тип и конструкцию основного и вспомогательного технологического оборудования (например станков накопительных или экспортных устройств и т. д.) обслуживаемых данным ПР;
)характеристики объекта манипулирования;
)тип и конструкцию самого ПР;
)особенности технологического процесса выполняемого робототехническим комплексом.
В зависимости от формы и габарита объектов манипулирования ЗУ могут быть различных типоразмеров:
для коротких тел вращения типа фланцев диаметром до 160 200 250 и 315 мм (массой от 10 до ) кг);
для длинных тел вращения (типа валов) диаметром до 60 80 100 и 160 мм (с массой от 10 до 160 кг);
для призматических корпусных изделий размером до 160 250 400 мм (с массой от 10 до 40 кг) и т. д.
Конструкция ЗУ определяется двигателем привода исполнительного механизма преобразующего движение привода в необходимое перемещение рабочих элементов схвата. В ЗУ используют различные исполнительные механизмы для преобразования с определенным отношением линейного или углового движения выходного звена привода в поступательное или вращательное перемещение рабочего элемента.
При этом можно выделить две группы исполнительных механизмов:
с постоянным коэффициентом передачи рабочего усилия не зависящим от положения схвата;
с переменным коэффициентом передачи усилия в зависимости от положения схвата.
Преимуществом исполнительных механизмов с переменным передаточным отношением является возможность достижения больших усилий зажима. Однако наибольшие усилия достигаются обычно лишь в узком диапазоне рабочих перемещений.
В связи с этим для обеспечения надежного удержания объектов манипулирования при широком диапазоне их размеров необходимо использовать в ЗУ исполнительные механизмы с постоянным передаточным механизмом (например зубчато-реечные винтовые некоторые рычажные и др.) или предусматривать переналадку исполнительных механизмов с переменным передаточным отношением (например рычажного типа).
Кинематические схемы некоторых ЗУ и значения коэффициента передачи k=PF где Р — тяговая сила на приводе; F — сила зажима в функции основных геометрических параметров исполнительных механизмов и положений схвата (при переменном коэффициенте передачи усилия). У конструктивно места крепления сменных ЗУ на кисти руки манипулятора выполняют в виде фланца с центрирующей расточкой и крепежными резьбовыми отверстиями вокруг нее. Такая конструкция места крепления ЗУ является наиболее простой и универсальной.
С целью унификации конструктивных элементов стандартизованы присоединительные размеры фланцевых мест крепления а также диаметры цилиндрических хвостовиков ЗУ для ПР в машиностроении. Грузоподъемность захватных устройств должна соответствовать одному из значений следующего ряда: 063; 125; 25; 5; 10; 20; 40; 80;160;250; 500 и 1000 кг. Высокая стабильность установки (005 007 мм) достигается за счет профилирования губок схвата.
Две пары рычагов 1 выполненных заодно с зажимными губками свободно установлены на своих осях 2. На рычагах нарезаны зубчатые секторы входящие попарно в зацепление с рейками 3 которые связаны между собой рычагами 4 образующими шарнирный параллелограмм. Шарнирный параллелограмм обеспечивает независимую работу каждой пары зажимных рычагов 1 что необходимо для захватывания и центрирования ступенчатых валов диаметром от 40 до 90 мм и длиной до 250 для схвата первого исполнения а для второго исполнения — диаметром от 40 до 100 мм и длиной 500 мм. Место соединения тяга 5 с гнездом выполненным во втулке 6 привода зажима и разжима схвата а также байонетное соединение хвостовика 7 схвата с головкой шпинделя 8 кисти руки унифицированы.
Предусмотрены два исполнения унифицированного захватного устройства: сменное и быстросменное. В сменном захватном устройстве хвостовик 7 крепится к шпинделю 8 кисти руки при помощи байонетного замка 9 накидного рычага 10 с резьбой и гайки 11. В быстросменном захватном устройстве применяется только байонетное крепление 9 которое может быть использовано и при автоматической смене схвата. При установке хвостовик 7 вводится в гнездо с одновременным отжимом фиксатора 10 который при повороте схвата на 90° входит под действием пружины в отверстие во фланце.
Захватное устройство предназначено для деталей типа валов. С целью автоматического обнаружения очередной детали размещенной в приспособлении схват оснащен специальным датчиком касания рычажного типа. На корпусе захватного устройства установлен кронштейн 2 к которому прикреплена планка 3 с микро выключателем 4. На планке шарнирно установлены рычаг 5 и тяга 6 с упором 7 который воздействует на микровыключатель 4. При касании рычагом 5 детали он поворачивается на небольшой угол и перемещает тягу с упором вверх размыкая при этом микровыключатель. Возврат рычага 5 происходит за счет пружины 8.
3 Техническая характеристика ПР "Универсал 5.02
Число степеней подвижности
Наибольшая величина перемещения:
– вокруг вертикальной оси I-I
– вдоль горизонтальной оси III-III
– вокруг вертикальной оси II-II
– вокруг оси III-III
Наибольшая скорость:
– вокруг оси I-I поворота.
– вертикального хода руки вдоль оси I-I
– выдвижение руки вдоль оси III-III
– поворота руки вокруг оси II-II
Точность позиционирования
4 Описание делительно-поворотного стола
Делительно-поворотные столы предназначены для периодического перемещения установленных на них ( в приспособлениях ) обрабатываемых деталей с одной позиции на другую с точной фиксацией на каждой из позиций что: позволяет производить обработку за несколько технологических переходов. Число позиций планшайбы делительно-поворотных столов составляет 2—12 причем как правило одна из позиций является холостой на которой производят разгрузку обработанных деталей и загрузку заготовок не прерывая работы станка. На 3 листе показана конструкция делительно-поворотного стола (диаметр планшайбы 800-1400 мм) с гидроприводом.
Во время поворота планшайбы опорные направляющие стола гидростатически разгружаются от части массы планшайбы маслом которое подается от станции смазки расположенной рядом с поворотным столом. Масло стекающее с направляющих во внутреннюю полость корпуса и используемое для смазывания зубчатой и червячной передачи попадает в карман откуда самотеком возвращается в станцию смазки.
Планшайба 9 на подшипниках 11 поворачивается гидродвигателем 3 через червячную передачу 6 и цилиндрическую зубчатую передачу 8. В конце поворота упор 12 наезжает на подвижный фиксатор 14 который при ходе вниз включает выключатель 18 и нажимает на плунжер золотника 19 затормаживающий вращение гидродвигателя 3. При дальнейшем вращении планшайбы фиксатор под действием пружины 15 освобождается поднимается вверх и размыкает выключатель 18 который дает команду на реверс гидродвигателя 3. Масло начинает поступать через нижнее отверстие золотника 19 и плунжер золотника поднимаясь вверх освобождает проход масла к гидродвигателю.
Скорость реверса определяется стабилизатором установленным на выходе гидродвигателя В конце реверса упор 12 поворачивает валик 13 расположенный по оси фиксатора 14 преодолевая усилие пружины 20. На нижнем конце валика 13 находится планка с винтом 16 который при повороте валика включает датчик 17 исходного положения. При срабатывании датчик 17 включает реле времени (РВ) выдержка которого достаточна для создания необходимого усилия контакта фиксирующих плоскостей упора 12 и фиксатора 14. При срабатывании РВ отключается гидроразгрузка и включается зажим планшайбы. Цикл деления при этом заканчивается.
На столе имеются ручной привод поворота планшайбы который используется при наладке стола. Привод состоит из подпружиненного вала-шестерни 4 на конце которого выполнено шестигранное отверстие под ключ и зубчатого колеса 2 соединенного обгонной муфтой 1 с червяком 6. При сжатии пружины 5 вал-шестерня 4 вводится в зацепление с зубчатым колесом 2. Далее движение на поворот планшайбы передается тем же путем что и от гидродвигателя 3. При вращении вала-шестерни 4 по часовой стрелке планшайба также вращается по часовой стрелке и наоборот.
Корыто 7 стола предназначено для сбора стружки и СОЖ которые удаляются по лотку в отдельно стоящее приемное устройство. Для удобства демонтажа корыто выполнено разъемным. В оси 10 стола предусмотрено центральное отверстие для подвода труб гидравлики и смазывающего материала к приспособлению.
5 Расчет элементов робота
Анализ динамического звена такого как схват робота можно провести на основе например уравнения моментов сил относительно неподвижной точки А. Т.к. уравнение составляется на определенный момент времени можно использовать закон статики МА = 0.
Мин (А) + Мтр (А) + Мупр (А) = Мвозд (А)
По этому уравнению можно составить математическую модель состояния схвата. Т.к. уравнение имеет допущения например моменты не всех сил действующих на систему учтены модель будет не точной и состояния объекта полученные в результате анализа будут не в полной мере соответствовать действительности. Но даже такую модель можно использовать в логическом эксперименте для изучения свойств и поведения схвата при различных внешних воздействиях обходя стороной эксперимент реальных требующий соблюдение различных условий для получения свойств объекта в той или иной ситуации.
Rn – реакция на губку захвата;
N – усилие контактирования между заготовкой и губкой;
N = Rn = mg = 4*10 = 40 Н
а – плечо силы удержания схвата;
F = Rn*ba = 40*9017 = 212 Н.
Рассчитаем пневмоцилиндр обеспечивающий работу схвата (зажимразжим)
Выбираем из таблицы значения D = 004 м и d = 002 м
Определим площади левой S1 и правой части S2 гидроцилиндра:
Примем давление в левой части гидроцилиндра P1 = 5 Атм а в правой P2 = 1 Атм.
Баланс сил определяется соотношением
где К=09 – эмпирический коэффициент учитывающий потери на трение
поршня о стенки пневмоцилиндра.
F FH цилиндр обеспечивает силу необходимую для удержания заготовки.
Описание транспортной системы
В АТС используется прямолинейный тактовый стол-накопитель. В его функции входит доставка заготовок в рабочую зону промышленного робота и дальнейшее перемещение готовых деталей после их обработки.
Тактовая работа стола заключается в периодическом перемещении заготовок на расстояние между ними. При этом при каждом «шаге» стола в рабочую зону ПР поступает новая заготовка. Время между перемещениями равно времени полного цикла совершаемого всем (основным и вспомогательным) оборудованием.
Рабочая поверхность стола оснащена планками предназначенными для базирования между ними спутников с заготовками ориентированных в пространстве и для удержания их в процессе перемещения.
Описание системы управления
Унифицированные устройства ЧПУ контурного типа серии УКМ модификации УКМ-552 и УКМ-772 которые различаются числом управляемых координат предназначены для управления ПР требующими сложного пространственного перемещения исполнительного органа.
Устройство ЧПУ УКМ-772 (РИС. 7) предназначено для управления ПР и совместно работающим технологическим оборудованием при автоматизации токарных операций. Структура устройства – однопроцессорная: в качестве процессора использована микроЭВМ «Электроника 60» имеющая центральный процессор (ЦП) управляющее устройство (УУ) оперативное заполняющее устройство (ОЗУ) и общую шину которая сопрягается с внутренней шиной устройства ЧПУ через специальный адаптер.
Внутренняя магистраль устройства представляет собой стандартную шину к которой подключены через специальные платы интерфейса функциональные модули.
К числу основных функциональных модулей в данной структуре УЧПУ относятся: 1) пульт управления (ПУ); 2) пульт обучения (ПО); 3) кассетный накопитель на магнитной ленте (КНМЛ) с модулем сопряжения (МС); 4) модули ввода (МВ) и вывода (МВД) дискретной информации; 5) модуль управления приводом (МУП); 6) модуль сопряжения с датчиками положения (МСД).
Благодаря такому модульному построению устройство ЧПУ обладает функциональной гибкостью т. е. может быть скомплексировано из определенного набора данных модулей в зависимости от конкретного назначения.
В частности модуль сопряжения с датчиками положения (МСД) может выполняться в разных вариантах (например для сопряжения с кодовыми фотоэлектрическими датчиками ФЭП-15 или абсолютными потенциометрическими датчиками СП4-8).
Структурная схема устройства УКМ-772
Модуль управления приводом (МУП) в различных модификациях устройства ЧПУ может обеспечивать сопряжение с конкретными следящими электрогидравлическими или электрическими приводами.
Функции долговременного запоминающего устройства для управляющей программы выполняет КНМЛ. Стандартные программы записываются на магнитную ленту с перфоленты через фотосчитывающее устройство (ФСУ). Общая программа управления ПР формируется в ОЗУ в процессе обучения и хранится затем в КНМЛ. В устройстве предусмотрен модуль ППЗУ выполненный на энергонезависимых интегральных микросхемах для записи (например с перфоленты) и хранения системного программно-математического обеспечения УЧПУ.
Техническая характеристика УКМ-772
Контурное (с линейной интерполяцией)
Число программируемых координат
Число двойных разрядов для обработки геометрической информации
Количество степеней точности
Точность позиционирования единиц дискретности
Тип датчика положения
Объем оперативной памяти кадров
Число входных дискретных сигналов
Число выходных технологических команд
Параметры входных сигналов (напряжениеток) ВА
Напряжение питания В
Параметры выходных технологических команд (напряжениеток) В А
Потребляемая мощность кВт
Габаритные размеры (длина ширина высота) мм
Выводы по курсовому проекту
В результате выполнения курсового проекта на тему "Проектирование АС" проекте была спроектирована автоматизированная система для обработки корпусной детали. Для этого был проанализирован объект производства рассчитаны режимы резания на обрабатываемые поверхности. Были выбраны основное и вспомогательное оборудование а именно: вертикально-сверлильный станок промышленный робот транспортная система и система управления. Я ознакомилась с кинематической схемой станка его устройством и принципом работы с принципом работы ПР и системы в целом.
Были разработаны рассчитаны и представлены чертеж ПР и его элементарного звена кинематическая схема станка компоновочная схема циклограмма работы АС и рабочая зона промышленного робота.
Козырев Ю. Г. «Промышленные роботы» справочник «Машиностроение» Москва 1988.
Барановский Ю. В. «Режимы резания металлов» справочник
«Машиностроение» Москва 1972.
Сидоров С. Г. МУ по выполнению курсового проекта по дисциплине
«Проектирование автоматизированных систем» Москва 2006.
Соломенцев Ю. М. «Промышленные роботы» справочник-альбом
«Машиностроение» Москва 1985.
Токарева С. В. под ред. Б. И. Черпакова «Унифицированные узлы
агрегатных станков и автоматических линий» каталог «Машиностроение» Москва 1988.
4.cdw

2.cdw

3.cdw

Пояснялка2.doc
Московский Государственный Технический Университет «МАМИ»
Факультет «Автоматизация и управление»
Кафедра «Автоматизированные станочные системы и инструмент»
ПОЯСНИТЕЛЬНАЯ ЗАПИСКА
к курсовому проекту по курсу «Проектирование автоматизированных систем»
«Проектирование автоматизированной системы для обработки корпусной детали в составе основного и вспомогательного технологического оборудования»
Студент:Кузьмич Т.А.
Преподаватель: Иванников С.Н.
Объект производства – деталь типа корпусная.
Материал детали – ковкий чугун КЧ35-10 с твердостью НВ = 207 229.
Масса детали – m = 2 кг.
Годовая программа выпуска деталей – N = 100000 штгод.
Номенклатура выпуска изделий – Т = 5 шт.
1 Тенденции развития оборудования ..4
2 Описание автоматизированной системы .5
Описание оборудования станка 2Р135Ф2 .6
1 Общие сведения о станке 2Р135Ф2 ..6
2 Описание основных элементов станка .6
3 Основные технические данные и характеристики
вертикально-сверлильного станка 2Р135Ф2 .11
4 Анализ производства 12
5 Расчет припусков и межоперационных размеров на обрабатываемые поверхности детали .12
6 Расчет режимов резания 13
6.1 Фрезерование (одноинструментная обработка) .13
6.2 Сверление (двушпиндельная головка) 14
Описание ПР "Универсал 5.02" .15
1 Общее описание .15
2 Описание захватного устройства робота .18
3 Техническая характеристика ПР "Универсал 5.02" 22
4 Описание делительно-поворотного стола 23
5 Расчет элементов робота 24
Описание транспортной системы 26
Описание системы управления 27
Выводы по курсовому проекту 31
Список литературы 32
1 Тенденции развития оборудования
В настоящее время наметились тенденции к увеличению номенклатуры выпускаемых изделий и сокращению размеров серий. В итоге около 80% производства носит мелкосерийный характер в связи с этим необходимо обеспечить гибкость производства что достигается применением технологического оборудования с ЧПУ.
Технологическое оборудование с ЧПУ объединяют в единые производственные комплексы с помощью транспортных и управляющих систем. Такие производственные комплексы называются гибкими автоматизированными производственными системами (ГПС).
Для сохранения производительности ГПС при отказе отдельного оборудования обычно предусматриваются буферные накопители которые позволяют разбить ГПС на ряд участков обладающих некоторой функциональной независимостью друг от друга.
Такие участки называют технологическими а в случае применения роботов – роботизированными комплексами (РК).
РК охватывают группу оборудования в пределах которой изделия перемещаются только поштучно. Его началом (входом) и окончанием (выходом) являются различного рода накопители.
РК в которых роботы только разгружают и загружают основное технологическое оборудование называются РТК.
В данной курсовой работе построена базовая планировка составлен алгоритм работы циклограмма и другие параметры РТК для обработки детали типа «корпусная деталь».
2 Описание автоматизированной системы
Заданием на курсовой проект является эскиз детали которую необходимо обработать в автоматизированном производстве с применением малолюдной или что является предпочтительным безлюдной технологии. Нашей задачей является разработать и сконструировать автоматизированный участок для проведения над заданной деталью нескольких операций.
Для того чтобы технологический процесс был автоматизирован целесообразно применить станок 2Р135ПФ2 с числовым программным управлением. Это позволит нам не только обрабатывать деталь которая дана заданием но и предусмотреть некоторую гибкость данного участка под обработку других деталей типа тел вращения.
Один станок не позволит нам полностью обеспечить автоматизацию. Для загрузки и разгрузки станка применим промышленный робот Универсал-5.02.
Так как данный робот не может осуществит правильное положении детали то нам придется применить тактовый стол на котором детали будут находится в нужном положении для установки их на станок роботом. Чтобы правильно расположить деталь на столе можно применить систему позиционирования деталей которая будет устанавливать деталь в нужное нам положение.
Описание оборудования станка 2Р135Ф2
1 Общие сведения о станке 2Р135Ф2
Назначение и область применения. Станок вертикально-сверлильные 2Р135Ф2 предназначены для выполнения следующих видов работ: сверления рассверливания зенкерования зенкования развертывания и растачивания отверстий. Растачивание отверстий в том числе расположенных на расстояниях с допусками по II квалитету кроме того станок 2Р135ПФ2 предназначен для легкого фрезерования. Обработка производится быстрорежущим и твердосплавным инструментом в деталях из различных конструкционных материалов. Станки используются для работы в условиях единичного мелкосерийного и серийного производства в ремонтных и сборочных цехах.
Реверсирование электродвигателя главного движения позволяет производить на станках нарезание резьбы машинными метчиками.
Вид климатического исполнения У.ХЛ4 или ТЗ по ГОСТ 15150-69. Класс точности: II по ГОСТ 8-82E.
2 Описание основных элементов станка
) Основание. Колонна станка представляет собой пустотелую чугунную отливку коробчатой формы. Механизированный крестовый стол на станке крепится в Т-образных пазах на неподвижном столе-тумбе. На фундаментной плите внутри колонны установлен электронасос Фундаментная плита является резервуаром для охлаждающей жидкости.
) Коробка скоростей и привод. Коробка скоростей сообщает шпинделю 12 различных частот вращения с помощью передвижных блоков. Опоры валов коробки скоростей размещены в двух плитах: верхней 1 и нижней 4 скрепленных между собой четырьмя стяжками о. Коробка скоростей получает вращение от вертикально расположенного электродвигателя через эластичную муфту 10 и зубчатую передачу 5. Последний вал 2 коробки (гильза) имеет в отверстии шлицы через которые вращение передается шпинделю. Через зубчатую пару 3 вращение передается на коробку подач.
Смазка коробки скоростей как и всех сборочных единиц сверлильной головки производится от плунжерного насоса закрепленного на нижней пучите 4.
Работа насоса контролируется специальным масло-указателем на передней части подмоторной плиты.
) Механизм переключения скоростей и подач. Переключение скоростей производится рукояткой 1 которая в зависимости от конструкции имеет четыре или пять положений по окружности и три вдоль оси.
Переключение подач осуществляется рукояткой 2 имеющей три положения по окружности и три положения вдоль оси. Рукоятки расположены на передней части сверлильной головки. Отсчет включаемых скоростей и подач производится по табличкам.
) Коробка подач. Коробка подач смонтирована в отдельном корпусе и устанавливается в сверлильной головке. Перемещением двух тройных блоков шестерен осуществляется девять различных подач.
Последний вал коробки подач сцентрирован с верхней опорой червяка механизма подачи. На валу коробки подач установлена полумуфта 1 передающая вращение червяку механизма подачи.
) Шпиндель. Шпиндель 1 смонтирован на двух шарикоподшипниках. Осевое усилие подачи воспринимается нижним упорным подшипником а усилие при выбивки инструмента - верхним. Подшипники расположены в пиноли 2 которая с помощью реечной пары перемещается вдоль оси. Для выбивки инструмента из конуса морзе шпинделя служит специальное приспособление на головке шпинделя. Выбивка происходит вращением штурвала от руки при подъеме шпинделя. Обойма 4 приспособления упирается в корпус сверлильной головки и рычаг 3 поворачиваясь вокруг оси выбивает инструмент.
) Сверлильная головка. Сверлильная головка представляет собой чугунную отливку коробчатой формы в которой монтируются все основные сборочные единицы станка: коробка скоростей коробка подач шпиндель механизм подачи противовес шпинделя и механизм переключения скоростей и подач.
Ручная подача шпинделя осуществляется вращением штурвала 6 на себя. При этом храповой механизм должен быть разъединен что достигается перемещением штифта 12 в правое положение при помощи рукоятки 5 которая должна занять верхнее положение. Дня передачи момента от штурвала на вал-шестерню 16 штифт запрессованный в полумуфту II должен быть совмещен с правым пазам на рукоятке 5 установленной на валу-шестерне от которого через реечную передачу происходит поступательное перемещение пиноли со шпинделем.
Для перехода с ручного режима работы на автоматический цикл с правой стороны сверлильной головки на оси штурвала под крышкой расположен механизм переключения о ручной подачи шпинделя на механизированную.
Откинув крышку 10 вниз необходимо повернуть рукоятку 5 на 180° вокруг оси из верхнего положения в нижнее. При этом эксцентрик 13 через палец 14 нажимает на штифт 12 который перемещаясь в крайнее левое положение вместе с диском 9 выводит из зацепления кулачковую полумуфту 17 а зубцы двустороннего диска 8 входят в зацепление с зубцами червячного колеса 7. Произошла подготовка к работе механизма быстрого подвода шпинделя. После нажатия кнопки "Пуск" включается электродвигатель быстрых перемещений расположенный с левой стороны сверлильной головки. При этом электродвигатель главного движения и электромагнитные муфты отключены. Электродвигатель быстрых перемещений шпинделя через ременную передачу пружинную муфту и червячную передачу передает вращение на вал-шестерню 16 а от нее на реечную пару. В результате этого шпиндель через связанную с ним пиноль ползает поступательное движение. Происходит быстрый подвод шпинделя к обрабатываемой детали. При этом от вала-шестерни 16 через двойной блок шестерен 21 вращение передается:
) через мелкомодульную зубчатую пару и эластичную му^ту на датчик контроля перемещения шпинделя работа которого в свою очередь контролируется УЦИ.
) через зубчатую пару внутреннего зацепления и ось 3 на ступицу 2 с установленными на ней кулачками 4 1 которые в необходимый момент включают датчики контроля нулевой точки ограничивающие движение пиноли вверх и вниз. Датчики подают сигнал на отключение электродвигателя быстрых перемещений включение южней тормозной электромагнитной муфты расположенной на валу червяка которая отключается после остановки электродвигателя быстрых ходов включение электродвигателя главного движения и верхней электромагнитной муфты соединяющей коробку подач с валом червяка который через червячное колесо 7 зубчатый диск 8 полумуфту 17 и вал шестерню 16 передает движение пиноли 2 со шпинделем 1. Происходит механическая подача. При этом штифт 15 находится в левом пазу рукоятки 5 позволяющем провернуть штурвал на 20 что дает возможность кулачках полумуфт II и 17 выйти из зацепления.
По окончании механической подачи т.е. окончании обработки детали отключается верхняя электромагнитная муфта 23 включается нижняя тормозная муфта 24 которая после полного прекращения механической подачи должна быть отключена включается электродвигатель быстрых ходов и через описанную выше кинематическую цепь: пружинная муфта - червячная пара - реечная пара - происходит быстрый отвод шпинделя вверх.
В специальном отверстии в нижней части сверлил ной головки с лицевой стороны под крышкой расположен механизм зажима пиноли шпинделя при фрезеровании плоскостей. К пиноли подводят при помощи рукоятки 18 винтом 20 связанную с ним опору 19 и зажимают пиноль которая перед зажимом должна быть установлена вместе со шпинделем в крайнее верхнее положение. При выполнении на станке других видов работ опору выдвигают в крайнее заднее положение поворотом рукоятки. Контроль зажима осуществляется датчиком.
В коробке скоростей установлен датчик контроля вращения шпинделя при перемещении крестового стола в режим фрезерования взаимодействующий с датчиком зажима пиноли.
3 Основные технические данные и характеристики вертикально-сверлильного станка 2Р135Ф2
Технические характеристики основные параметры и размеры согласно ОСТ2 Н62-1-85 ОСТ2 Н62-6-79 ГОСТ 24644-81 и техническому задании.
Наибольший диаметр сверления мм
Наибольший диаметр нарезаемой резьбы мм
Наибольший крутящий момент кгс×м
Наибольшее усилие подачи кгс
Число шпинделей револьверной головки
Размер конуса шпинделя
Количество скоростей шпинделя
Пределы скоростей шпинделя ммоб
Пределы рабочих подач мммин
Размеры рабочей поверхности стола мм
Наибольшее расстояние от торца шпинделя до стола мм
Наибольшее рабочее перемещение суппорта мммин
Скорость быстрого перемещения суппорта ммин
Точность позиционирования стола и суппорта мм
Повторяемость позиционирования стола и суппорта мм
Мощность электродвигателя главного привода кВт
Габаритные размеры станка мм
4 Анализ производства
Для изготовления данной детали необходимо обработать три плоских поверхности и четыре отверстия. В соответствии с заданием обработка реализуется фрезерованием и сверление.
Плоские поверхности 1 2 и 3 можно обработать концевой удлиненной фрезой боковой ее поверхностью. Диаметр фрезы D = 32 мм длина рабочей части l = 100 мм по ТУ2-035-710-80.
Поверхность 1 обрабатывается при горизонтальном расположении фрезы с вертикальной ее подачей вниз; поверхность 2 – при вертикальном положении фрезы с горизонтальной подачей поверхность 3 – при горизонтальном положении фрезы с горизонтальной подачей. Размер рабочей части инструмента позволяет обработать каждую из поверхностей за один проход при небольшом припуске на обработку.
Поверхности 4 и 5 – внутренние цилиндрические. Отверстия можно получить сверлением инструментом с диаметром равным диаметру отверстия. Т.е. для 4 и 5 поверхностей используются сверла d = 16 мм и d = 10 мм соответственно. Оба отверстия 4 и 5 сверлятся за один рабочий ход при условии использования многошпиндельных насадок.
5 Расчет припусков и межоперационных размеров на обрабатываемые поверхности детали
В условиях массового производства форма заготовки должна быть максимально приближена к форме детали. Исходя из этого назначаем припуск на обработку t1 = t2 = t4 = 3 мм.
Припуск на сверление равен d2 т.е. t4 = 8 мм t5 = 5 мм.
6 Расчет режимов резания
6.1 Фрезерование (одноинструментная обработка)
Длина рабочего ходаLр.х.= Lрез+y
Lрез (1) = 90 мм; Lрез (2) = 60 мм; Lрез (3) = 60 мм;
Lр.х. (1) = 102 мм; Lр.х. (2) = 72 мм; Lр.х. (3) =72 мм;
Средняя ширина фрезерования bср = FLрез где F – площадь фрезеруемой поверхности
bср (1) = 60 мм; bср (2) = 90 мм; bср (3) = 60 мм;
Подача на зуб фрезы sz в ммзуб
Стойкость фрезы Тр в мин резания Тр = Кф*Тм*l где
Кф – коэффициент учитывающий количество инструментов в наладке;
Кф = 1 (один инструмент);
Тм - стойкость фрезы в минутах машинной работы Тм = 60 мин;
Скорость резания v = vтаблК1К2К3 ммин где
К1-коэффициент зависящий от обрабатываемого материала;
К2-коэффициент зависящий от стойкости и марки твердого сплава;
К3-коэффициент зависящий от вида обработки;
vтабл (1) = 60 ммин; vтабл (2) = 64 ммин; vтабл (3) = 64 ммин;
К1 = 1; К2 = 065; К3 = 12;
v(1) = 468 ммин; v(2) = 499 ммин; v(3) = 499 ммин;
Число оборотов шпинделя n = 1000v(p*D) обмин
n(1) = 4655 обмин; n(2) = 4964 обмин; n(3) = 4964 обмин;
Скорость резания по принятому числу оборотов v = p*D*n1000 ммин
Минутная подача sм = sz*z*n мммин
Основное машинное время обработки tм = Lр.хsм мин
tм (1) = 058 мин; tм (2) = 041 мин; tм (3) = 041 мин.
6.2 Сверление (двушпиндельная головка)
y1 = 6 мм; y2 = 5 мм;
Lрез (1) = 10 мм; Lрез (2) = 15 мм;
Lр.х. (1) = 16 мм; Lр.х. (2) = 20 мм;
s0 (1) = 032 ммоб; s0 (2) = 022 ммоб;
Стойкость инструмента Тр в мин резания Тр = Тм*l где
Тм – стойкость сверла в минутах машинной работы Тм = 60 мин;
Тр = Тм (1) = 55 мин; Тм (2) = 35 мин;
Тр (1) = 344 мин; Тр (2) = 263 мин;
К2-коэффициент зависящий от стойкости инструмента;
К3-коэффициент зависящий от отношения длины резания к диаметру;
vтабл (1) = 19 ммин; vтабл (2) = 20 ммин;
К1 = 07; К2 = 13; К3 при горизонтальном сверлении не учитывается;
v(1) = 173 ммин; v(2) = 182 ммин;
Число оборотов шпинделя n = 1000v(p*d) обмин
n(1) = 344 обмин; n(2) = 579 обмин;
Минутная подача sм = s0*n мммин
sм (1) = 110 мммин; sм (2) = 127 мммин;
tм (1) = 015 мин; tм (2) = 016 мин;
Описание ПР "Универсал 5.02
Многоцелевые ПР типа «Универсал-5» применяются для автоматизации погрузочно-разгрузочных работ обслуживания различного технологического оборудования межоперационного и меж станочного транспортирования объектов обработки и выполнения других вспомогательных операции.
Исполнительным механизмом ПР является манипулятор который обеспечивает установку в пределах рабочей зоны захватного механизма схвата. Манипулятор имеет четыре степени подвижности руки 1 в сферической системе координат которые реализуются механизмами: поворота 2 относительно оси П—П выдвижения 3 руки 1 вдоль оси — поворота 4 руки относительно вертикальной оси —7 подъема 5 руки вдоль оси —. Две ориентирующие степени подвижности рабочего органа схвата 7 создают механизмы 6 вращения кисти руки относительно ее продольной оси — и поперечной оси IV—IV. Подвижные механизмы манипулятора защищены от попадания пыли грязи и масла ограждением 8.
Установочные перемещения руки осуществляются помощью электромеханических следящих приводов а ориентирующие движения кисти руки и зажим - разжим схвата — пневмоцилиндрами.
Пневмоблок 9 которым комплектуется ПР предназначен для подготовки регулирования подачи сжатого воздуха из заводской сети и блокирования работы манипулятора при падении давления ниже допустимого.
Блок 10 тиристорных электроприводов формирует управляющие напряжения в якорной цепи электродвигателей постоянного тока.
Устройство программного управления 11 позиционного типа имеет возможность записи программы в режиме обучения (по первому циклу) и формирует управляющие сигналы на блок 10 а также технологические команды управления циклом работы манипулятора и обслуживаемого оборудования.
Блоки тиристорного электропривода ЭПТ6-У5.02 обеспечивают управление в следящем режиме электродвигателями постоянного тока типа СЛ-569 и СЛ-661 установленными в механизмах четырех программируемых степеней подвижности манипулятора.
Механизмы электроприводов включают в себя зубчатые или червячные редукторы параметры которых даны в кинематической схеме. Обратная связь исполнительных механизмов манипулятора по положению и скорости осуществляется потенциометрическими датчиками типа ППМЛ приводящимися с помощью зубчатых редукторов и тахогенераторов типа СЛ-121 которые приводятся в движение специальными зубчатыми или ременными механизмами.
Пневмоблок которым комплектуется ПР предназначен для подготовки сжатого воздуха подаваемого из заводской сети к манипулятору а также для циклового управления двумя ориентирующими движениями кисти руки и захватным устройством. Приводы этих движений осуществляются от пневмоцилиндров. Для преобразования поступательного перемещения поршня во вращательное движение кисти руки используются винтовой копир (в приводе поворота кисти руки относительно ее продольной оси) и передача рейка-шестерня (в приводе качания кисти относительно поперечной оси). Привод зажима и разжима губок схвата осуществляется рычажным механизмом присоединенным к штоку пневмоцилиндра. Соединение механизмов манипулятора между собой и устройством аналогового позиционного программного управления типа АПС-1 производится в соответствии с принципиальной электрической схемой.
Базовым узлом манипулятора является механизм поворота конструкция которого показана на листе. В неподвижном корпусе на радиально-упорных подшипниках 2 установлена подвижная планшайба 3 получающая вращение от механизма привода 4 .который установлен в корпусе 1. Механизм привода поворота состоит из электродвигателя 5 постоянного тока червячного редуктора 6 и жестко связанного с валом червяка 7 тахогенератора 8. Крутящий момент на планшайбу 3 передается через цилиндрическую зубчатую передачу колесо 9 которой находится в зацеплении с выходной шестерней 10 редуктора.
На специальном кронштейне 11 закрепленном на корпусе установлен потенциометрический датчик положения 12 валик которого получает вращение через зубчатую передачу. Разрезная шестерня 13 привода находится в зацеплении с зубчатым колесом 9. На крышке 14 предохраняющей от попадания в радиально-упорные подшипники 2 пыли и грязи установлено ограждение 15 внутри которого укладывают два витка электрокабеля. В крышке 14 закреплен угольник 16 в который ввернута труба 17 воздуховода. Через трубу 17 на переднем конце которой установлен обратный клапан - 18 сжатый воздух проходит к угольнику 19 а от него по шлангу подается к пневмоцилиндрам механизма руки.
На неподвижном корпусе установлен дополнительный кронштейн 20 с амортизирующими резиновыми пластинами которые являются ограничителями поворота подвижной планшайбы.
С целью выбора люфта в механизме привода червячное колесо 21 выполнено разрезным: нижняя половина колеса надета на шлицевый вал 22 а верхняя — на ступицу его нижней половины. Выбор люфта производится эксцентриком 23 путем поворота верхней половины червячного колеса относительно нижней. После установления требуемого бокового зазора (002 006 мм) обе половины червячного колеса 22 закрепляются винтами 24.
На планшайбе механизма поворота установлен механизм подъема манипулятора. Механизм подъема манипулятора выполнен в виде пространственного рычажного устройства (типа пантографа) неподвижные нижние шарниры которого закреплены в кронштейне на основании 2. Подвижные нижние шарниры пантографа установлены на каретке 3 которая перемещается на роликах 4 по направляющим 5. При горизонтальном движении каретки 3 пантограф перемещается вертикально вместе с верхней платформой 6. К платформе крепится механизм поворота руки (на рисунке не показан) и скалка 7 являющаяся направляющей для конических роликов 8 каретки 9 в которой установлены верхние подвижные шарниры 10 пантографа.
Механизм привода подъема манипулятора состоит из двух электродвигателей 11 постоянного тока установленных соосно относительно руг друга на основании 2 редуктора 12 и винтовой передачи 13. Консоль перемещения выполняется с помощью потенциометрического датчика 14 соединенного с помощью зубчатой передачи 15 с ходовым винтом. Обратная связь по скорости осуществляется тахогенератором 16 который соединен зубчато-ременной передачей 17 с входным валом редуктора 12.
Винтовая передача 13 конструктивно представляет собой винт 18 с трапецеидальной резьбой установленный в опорах на подшипниках качения. В корпусе 20 каретки 3 установлены две полу гайки 19. Для компенсации погрешности расположения опор винта относительно направляющих 6 корпус 20 имеет осевой люфт (001-003 мм) и радиальный зазор (05 мм) относительно каретки 3.
Для выбора бокового зазора в зацеплении цилиндрических колес редуктора 12 и передачи 15 привода датчика положения (потенциометра) 14 ведомые зубчатые колеса 21 и 22 выполнены разрезными разводящими пружинными кольцами.
2 Описание захватного устройства робота
При выборе типа зажимного устройства для промышленного робота необходимо в качестве исходных данных учитывать:
)тип и конструкцию основного и вспомогательного технологического оборудования (например станков накопительных или экспортных устройств и т. д.) обслуживаемых данным ПР;
)характеристики объекта манипулирования;
)тип и конструкцию самого ПР;
)особенности технологического процесса выполняемого робототехническим комплексом.
В зависимости от формы и габарита объектов манипулирования ЗУ могут быть различных типоразмеров:
для коротких тел вращения типа фланцев диаметром до 160 200 250 и 315 мм (массой от 10 до ) кг);
для длинных тел вращения (типа валов) диаметром до 60 80 100 и 160 мм (с массой от 10 до 160 кг);
для призматических корпусных изделий размером до 160 250 400 мм (с массой от 10 до 40 кг) и т. д.
Конструкция ЗУ определяется двигателем привода исполнительного механизма преобразующего движение привода в необходимое перемещение рабочих элементов схвата. В ЗУ используют различные исполнительные механизмы для преобразования с определенным отношением линейного или углового движения выходного звена привода в поступательное или вращательное перемещение рабочего элемента.
При этом можно выделить две группы исполнительных механизмов:
с постоянным коэффициентом передачи рабочего усилия не зависящим от положения схвата;
с переменным коэффициентом передачи усилия в зависимости от положения схвата.
Преимуществом исполнительных механизмов с переменным передаточным отношением является возможность достижения больших усилий зажима. Однако наибольшие усилия достигаются обычно лишь в узком диапазоне рабочих перемещений.
В связи с этим для обеспечения надежного удержания объектов манипулирования при широком диапазоне их размеров необходимо использовать в ЗУ исполнительные механизмы с постоянным передаточным механизмом (например зубчато-реечные винтовые некоторые рычажные и др.) или предусматривать переналадку исполнительных механизмов с переменным передаточным отношением (например рычажного типа).
Кинематические схемы некоторых ЗУ и значения коэффициента передачи k=PF где Р — тяговая сила на приводе; F — сила зажима в функции основных геометрических параметров исполнительных механизмов и положений схвата (при переменном коэффициенте передачи усилия). У конструктивно места крепления сменных ЗУ на кисти руки манипулятора выполняют в виде фланца с центрирующей расточкой и крепежными резьбовыми отверстиями вокруг нее. Такая конструкция места крепления ЗУ является наиболее простой и универсальной.
С целью унификации конструктивных элементов стандартизованы присоединительные размеры фланцевых мест крепления а также диаметры цилиндрических хвостовиков ЗУ для ПР в машиностроении. Грузоподъемность захватных устройств должна соответствовать одному из значений следующего ряда: 063; 125; 25; 5; 10; 20; 40; 80;160;250; 500 и 1000 кг. Высокая стабильность установки (005 007 мм) достигается за счет профилирования губок схвата.
Две пары рычагов 1 выполненных заодно с зажимными губками свободно установлены на своих осях 2. На рычагах нарезаны зубчатые секторы входящие попарно в зацепление с рейками 3 которые связаны между собой рычагами 4 образующими шарнирный параллелограмм. Шарнирный параллелограмм обеспечивает независимую работу каждой пары зажимных рычагов 1 что необходимо для захватывания и центрирования ступенчатых валов диаметром от 40 до 90 мм и длиной до 250 для схвата первого исполнения а для второго исполнения — диаметром от 40 до 100 мм и длиной 500 мм. Место соединения тяга 5 с гнездом выполненным во втулке 6 привода зажима и разжима схвата а также байонетное соединение хвостовика 7 схвата с головкой шпинделя 8 кисти руки унифицированы.
Предусмотрены два исполнения унифицированного захватного устройства: сменное и быстросменное. В сменном захватном устройстве хвостовик 7 крепится к шпинделю 8 кисти руки при помощи байонетного замка 9 накидного рычага 10 с резьбой и гайки 11. В быстросменном захватном устройстве применяется только байонетное крепление 9 которое может быть использовано и при автоматической смене схвата. При установке хвостовик 7 вводится в гнездо с одновременным отжимом фиксатора 10 который при повороте схвата на 90° входит под действием пружины в отверстие во фланце.
Захватное устройство предназначено для деталей типа валов. С целью автоматического обнаружения очередной детали размещенной в приспособлении схват оснащен специальным датчиком касания рычажного типа. На корпусе захватного устройства установлен кронштейн 2 к которому прикреплена планка 3 с микро выключателем 4. На планке шарнирно установлены рычаг 5 и тяга 6 с упором 7 который воздействует на микровыключатель 4. При касании рычагом 5 детали он поворачивается на небольшой угол и перемещает тягу с упором вверх размыкая при этом микровыключатель. Возврат рычага 5 происходит за счет пружины 8.
3 Техническая характеристика ПР "Универсал 5.02
Число степеней подвижности
Наибольшая величина перемещения:
– вокруг вертикальной оси I-I
– вдоль горизонтальной оси III-III
– вокруг вертикальной оси II-II
– вокруг оси III-III
Наибольшая скорость:
– вокруг оси I-I поворота.
– вертикального хода руки вдоль оси I-I
– выдвижение руки вдоль оси III-III
– поворота руки вокруг оси II-II
Точность позиционирования
4 Описание делительно-поворотного стола
Делительно-поворотные столы предназначены для периодического перемещения установленных на них ( в приспособлениях ) обрабатываемых деталей с одной позиции на другую с точной фиксацией на каждой из позиций что: позволяет производить обработку за несколько технологических переходов. Число позиций планшайбы делительно-поворотных столов составляет 2—12 причем как правило одна из позиций является холостой на которой производят разгрузку обработанных деталей и загрузку заготовок не прерывая работы станка. На 3 листе показана конструкция делительно-поворотного стола (диаметр планшайбы 800-1400 мм) с гидроприводом.
Во время поворота планшайбы опорные направляющие стола гидростатически разгружаются от части массы планшайбы маслом которое подается от станции смазки расположенной рядом с поворотным столом. Масло стекающее с направляющих во внутреннюю полость корпуса и используемое для смазывания зубчатой и червячной передачи попадает в карман откуда самотеком возвращается в станцию смазки.
Планшайба 9 на подшипниках 11 поворачивается гидродвигателем 3 через червячную передачу 6 и цилиндрическую зубчатую передачу 8. В конце поворота упор 12 наезжает на подвижный фиксатор 14 который при ходе вниз включает выключатель 18 и нажимает на плунжер золотника 19 затормаживающий вращение гидродвигателя 3. При дальнейшем вращении планшайбы фиксатор под действием пружины 15 освобождается поднимается вверх и размыкает выключатель 18 который дает команду на реверс гидродвигателя 3. Масло начинает поступать через нижнее отверстие золотника 19 и плунжер золотника поднимаясь вверх освобождает проход масла к гидродвигателю.
Скорость реверса определяется стабилизатором установленным на выходе гидродвигателя В конце реверса упор 12 поворачивает валик 13 расположенный по оси фиксатора 14 преодолевая усилие пружины 20. На нижнем конце валика 13 находится планка с винтом 16 который при повороте валика включает датчик 17 исходного положения. При срабатывании датчик 17 включает реле времени (РВ) выдержка которого достаточна для создания необходимого усилия контакта фиксирующих плоскостей упора 12 и фиксатора 14. При срабатывании РВ отключается гидроразгрузка и включается зажим планшайбы. Цикл деления при этом заканчивается.
На столе имеются ручной привод поворота планшайбы который используется при наладке стола. Привод состоит из подпружиненного вала-шестерни 4 на конце которого выполнено шестигранное отверстие под ключ и зубчатого колеса 2 соединенного обгонной муфтой 1 с червяком 6. При сжатии пружины 5 вал-шестерня 4 вводится в зацепление с зубчатым колесом 2. Далее движение на поворот планшайбы передается тем же путем что и от гидродвигателя 3. При вращении вала-шестерни 4 по часовой стрелке планшайба также вращается по часовой стрелке и наоборот.
Корыто 7 стола предназначено для сбора стружки и СОЖ которые удаляются по лотку в отдельно стоящее приемное устройство. Для удобства демонтажа корыто выполнено разъемным. В оси 10 стола предусмотрено центральное отверстие для подвода труб гидравлики и смазывающего материала к приспособлению.
5 Расчет элементов робота
Анализ динамического звена такого как схват робота можно провести на основе например уравнения моментов сил относительно неподвижной точки А. Т.к. уравнение составляется на определенный момент времени можно использовать закон статики SМА = 0.
Мин (А) + Мтр (А) + Мупр (А) = Мвозд (А)
По этому уравнению можно составить математическую модель состояния схвата. Т.к. уравнение имеет допущения например моменты не всех сил действующих на систему учтены модель будет не точной и состояния объекта полученные в результате анализа будут не в полной мере соответствовать действительности. Но даже такую модель можно использовать в логическом эксперименте для изучения свойств и поведения схвата при различных внешних воздействиях обходя стороной эксперимент реальных требующий соблюдение различных условий для получения свойств объекта в той или иной ситуации.
Rn – реакция на губку захвата;
N – усилие контактирования между заготовкой и губкой;
N = Rn = mg = 4*10 = 40 Н
а – плечо силы удержания схвата;
F = Rn*ba = 40*9017 = 212 Н.
Рассчитаем пневмоцилиндр обеспечивающий работу схвата (зажимразжим)
Выбираем из таблицы значения D = 004 м и d = 002 м
Определим площади левой S1 и правой части S2 гидроцилиндра:
Примем давление в левой части гидроцилиндра P1 = 5 Атм а в правой P2 = 1 Атм.
Баланс сил определяется соотношением
где К=09 – эмпирический коэффициент учитывающий потери на трение
поршня о стенки пневмоцилиндра.
F FH цилиндр обеспечивает силу необходимую для удержания заготовки.
Описание транспортной системы
В АТС используется прямолинейный тактовый стол-накопитель. В его функции входит доставка заготовок в рабочую зону промышленного робота и дальнейшее перемещение готовых деталей после их обработки.
Тактовая работа стола заключается в периодическом перемещении заготовок на расстояние между ними. При этом при каждом «шаге» стола в рабочую зону ПР поступает новая заготовка. Время между перемещениями равно времени полного цикла совершаемого всем (основным и вспомогательным) оборудованием.
Рабочая поверхность стола оснащена планками предназначенными для базирования между ними спутников с заготовками ориентированных в пространстве и для удержания их в процессе перемещения.
Описание системы управления
Унифицированные устройства ЧПУ контурного типа серии УКМ модификации УКМ-552 и УКМ-772 которые различаются числом управляемых координат предназначены для управления ПР требующими сложного пространственного перемещения исполнительного органа.
Устройство ЧПУ УКМ-772 (РИС. 7) предназначено для управления ПР и совместно работающим технологическим оборудованием при автоматизации токарных операций. Структура устройства – однопроцессорная: в качестве процессора использована микроЭВМ «Электроника 60» имеющая центральный процессор (ЦП) управляющее устройство (УУ) оперативное заполняющее устройство (ОЗУ) и общую шину которая сопрягается с внутренней шиной устройства ЧПУ через специальный адаптер.
Внутренняя магистраль устройства представляет собой стандартную шину к которой подключены через специальные платы интерфейса функциональные модули.
К числу основных функциональных модулей в данной структуре УЧПУ относятся: 1) пульт управления (ПУ); 2) пульт обучения (ПО); 3) кассетный накопитель на магнитной ленте (КНМЛ) с модулем сопряжения (МС); 4) модули ввода (МВ) и вывода (МВД) дискретной информации; 5) модуль управления приводом (МУП); 6) модуль сопряжения с датчиками положения (МСД).
Благодаря такому модульному построению устройство ЧПУ обладает функциональной гибкостью т. е. может быть скомплексировано из определенного набора данных модулей в зависимости от конкретного назначения.
В частности модуль сопряжения с датчиками положения (МСД) может выполняться в разных вариантах (например для сопряжения с кодовыми фотоэлектрическими датчиками ФЭП-15 или абсолютными потенциометрическими датчиками СП4-8).
Структурная схема устройства УКМ-772
Модуль управления приводом (МУП) в различных модификациях устройства ЧПУ может обеспечивать сопряжение с конкретными следящими электрогидравлическими или электрическими приводами.
Функции долговременного запоминающего устройства для управляющей программы выполняет КНМЛ. Стандартные программы записываются на магнитную ленту с перфоленты через фотосчитывающее устройство (ФСУ). Общая программа управления ПР формируется в ОЗУ в процессе обучения и хранится затем в КНМЛ. В устройстве предусмотрен модуль ППЗУ выполненный на энергонезависимых интегральных микросхемах для записи (например с перфоленты) и хранения системного программно-математического обеспечения УЧПУ.
Техническая характеристика УКМ-772
Контурное (с линейной интерполяцией)
Число программируемых координат
Число двойных разрядов для обработки геометрической информации
Количество степеней точности
Точность позиционирования единиц дискретности
Тип датчика положения
Объем оперативной памяти кадров
Число входных дискретных сигналов
Число выходных технологических команд
Параметры входных сигналов (напряжениеток) ВА
Напряжение питания В
Параметры выходных технологических команд (напряжениеток) В А
Потребляемая мощность кВт
Габаритные размеры (длина ширина высота) мм
Выводы по курсовому проекту
В результате выполнения курсового проекта на тему "Проектирование АС" проекте была спроектирована автоматизированная система для обработки корпусной детали. Для этого был проанализирован объект производства рассчитаны режимы резания на обрабатываемые поверхности. Были выбраны основное и вспомогательное оборудование а именно: вертикально-сверлильный станок промышленный робот транспортная система и система управления. Я ознакомилась с кинематической схемой станка его устройством и принципом работы с принципом работы ПР и системы в целом.
Были разработаны рассчитаны и представлены чертеж ПР и его элементарного звена кинематическая схема станка компоновочная схема циклограмма работы АС и рабочая зона промышленного робота.
Козырев Ю. Г. «Промышленные роботы» справочник «Машиностроение» Москва 1988.
Барановский Ю. В. «Режимы резания металлов» справочник
«Машиностроение» Москва 1972.
Сидоров С. Г. МУ по выполнению курсового проекта по дисциплине
«Проектирование автоматизированных систем» Москва 2006.
Соломенцев Ю. М. «Промышленные роботы» справочник-альбом
«Машиностроение» Москва 1985.
Токарева С. В. под ред. Б. И. Черпакова «Унифицированные узлы
агрегатных станков и автоматических линий» каталог «Машиностроение» Москва 1988.
1.cdw

Число степеней подвижности 6
Наибольшая величина перемещения:
вокруг вертикальной оси I-I
вдоль горизонтальной оси III-III
вокруг вертикальной оси II-II
Наибольшая скорость:
вокруг оси I-I поворота
вертикального хода руки
выдвижения руки вдоль оси III-III
поворота руки вдоль оси II-II
Точность позиционирования
Масса (вместе с устройством управления)
Рекомендуемые чертежи
- 06.05.2017
- 25.02.2016
- 10.02.2022
- 24.01.2023