Проект вакуумного выпарного аппарата для концентрирования сульфата титанила TiOSO4


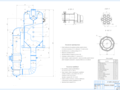
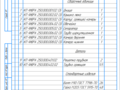
- Добавлен: 25.01.2023
- Размер: 1 MB
- Закачек: 1
Узнать, как скачать этот материал
Подписаться на ежедневные обновления каталога:
Описание
Проект вакуумного выпарного аппарата для концентрирования сульфата титанила TiOSO4
Состав проекта
![]() |
![]() ![]() ![]() |
![]() ![]() ![]() ![]() |
![]() ![]() ![]() ![]() |
![]() ![]() ![]() |
Дополнительная информация
Контент чертежей
Zaschita.cdw

Специф1.cdw

Рекомендуемые чертежи
Свободное скачивание на сегодня
Обновление через: 4 часа 13 минут