Проект установки переработки нефти с разработкой ректификационной колонны производительностью 300 тыс. т/год




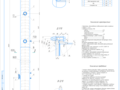
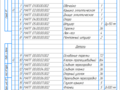
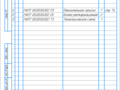
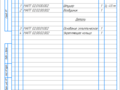
- Добавлен: 25.01.2023
- Размер: 7 MB
- Закачек: 2
Описание
Проект установки переработки нефти с разработкой ректификационной колонны производительностью 300 тыс. т/год
Состав проекта
![]() |
![]() |
![]() |
![]() |
![]() ![]() ![]() ![]() |
![]() ![]() ![]() ![]() |
![]() |
![]() ![]() ![]() ![]() |
![]() |
![]() |
![]() ![]() ![]() ![]() |
![]() ![]() ![]() ![]() |
![]() ![]() ![]() |
![]() |
![]() ![]() ![]() ![]() |
![]() |
![]() ![]() ![]() ![]() |
![]() ![]() ![]() ![]() |
![]() |
![]() |
![]() |
![]() ![]() ![]() |
![]() |
![]() ![]() ![]() ![]() |
![]() |
![]() |
![]() |
![]() ![]() ![]() |
![]() |
![]() |
![]() |
![]() |
![]() ![]() ![]() |
![]() |
![]() |
Дополнительная информация
Спецификация 2.cdw

Крышка эллиптическая
Клапан трапециевидный
Переливная перегородка
Техсхема.cdw

Теплообменник с нагревом мазутом
Теплообменник с водяным охлаждением
Холодильник воздушный
Отбензинивающая колонна
Ректификационная колонна
Конденсатор-холодильник
Условное обозначение
Обезвоженная и обессоленная нефть
Пары легкой бензиновой фракции
Сконденсированные пары
Фракция легкого бензина
Парожидкостная смесь
Пары верха колонны К-2
Охлажденная дизельная фракция
Солесодержащие стоки
Охлажденные солесодержащие стоки
Вода на промывку сырья
Охлажденная подтоварная вода
Технологическая схема
МАПТ 00.00.00.002 Т3
солесодержащие стоки
дизельная фракция на
Спецификация 3.cdw

Шайба 12Л ГОСТ 6202-70
Шайба С12 ГОСТ 10450-78
Шайба 20Л ГОСТ 6202-70
Шайба С20 ГОСТ 10450-78
Klapan_Trapetsievidny.cdw

Неуказанные предельные отклонения размеров +IT142
Спецификация 4.cdw

АС250 исправленная.frw
Экспликация оборудования
Наименование оборудования
Пар водяной насыщенный
Солесодержащие стоки
Дизельная фракция на
Перегретый пар от П1
из 2-ой секции печи П1
Парожидкостная смесь нефти
из 1-ой секции печи П1
(газообразное топливо в С2)
Вода техническая прямая
Конденсат пара водяного
Электродегидратор V=23
Аппарат воздушного охлаждения малопоточный
(АВМ-Г-14.6Ж-1.6-Б1-В6-2-1
Аппарат воздушного охлаждения
(АВМ-Г-14.6Ж-1.6-Б1-В4-4-3 УХЛ1)
(АВМ-Г-9Ж-1.6-Б1-В4-4-3 УХЛ1)
Теплообменник пластинчатый сварной Н0
Электронасос герметичный ГНВЦ-Е-50-150-Х-УХЛ2
Электронасос герметичный 2ЦГ 2580-К-11-6-УХЛ2
Агрегат электронасосный АХ-Е 315-К-55-У2
Электронасос герметичный ГНВЦ-Е-60-80-Х-УХЛ2
Электронасос герметичный ГНВЦ-Е-50-75-Х-УХЛ2
Электронасос герметичный ГНВЦ-Е-12
Насос центробежный полупогружной НВ-Д 5050(3
Насос бочковой F424S-4337Z-1000
Электронасос дозировочный
Электронасос дозировочный
Установка охлаждения технической воды
(калорифер водяной - ВНВ 123-409-01 АТЗ
Холодильник отбора проб
Емкость аварийная V=25 м
Емкость подземная V=16 м
Печь 2-х секционная
Конденсат водяного пара
Пар водяной перегретый
из 2-ой секции печи в К2
Парожидкостная смесь
из 1-ой секции печи в К2
на первоначальный пуск
Мазут (топливо) от Т21
Углеводородные газы (газо-
Агрегат электронасосный шестеренный НМШ 240-1
Вентилятор радиальный высокого давления
Аппарат воздушного охлаждения
вентилятор канальный радиальный
( УНИВЕНТ-2.5-4-1-Д=1.1-0.25-1500-02 ))
ТАБЛИЦА ПРЕДОХРАНИТЕЛЬНЫХ КЛАПАНОВ
ПАЗ - общая система противоаварийной защиты
Перфорированная труба
Конденсат пара водяного
насыщенного в сети предприятия
Паротушение помещения
к ЭД1 на паротушение
к ТД1 на паротушение
из сетей предприятия
К спутникам трубопроводов
К уровнемерной колонке К2
Сырьевые насосы расположены на складе
и экспликация оборудования
расположен на складе
Узел подачи деэмульгатора
Спецификация 1.cdw

с разработкой ректификационной
колонны производительностью
МАПТ 00.00.00.002 ПЗ
МАПТ 00.00.00.002 СБ
Проект ректификационной
Пояснительная записка
Колона ректификационная
Технологическая схема
МАПТ 00.00.00.002 ТЗ
МАПТ.00.00.02.002.cdw

Назначение для разделения отбензиненной нефти на фракции
в горизонтальном положении 1
Рабочая температура среды в колонне
Минимально допустимая отрицательная температура стенки
Расчетная температура стенки
Среда отбензиненная нефть
класс опасности 4 по ГОСТ 12.1007-76
Прибавка для компенсации коррозии
Тип тарелок: трапецевидно-клапанная однопоточная
Группа аппарата по ОСТ 26.291-94 1
Район территории по скоростному напору ветра 01
Аппарат подлежит действию "Правил устройства и безопасной
эксплуатации сосудов работающих под давлением" (ПБ 03-576-03).
испытание и приемка аппарата по
ГОСТ Р 52630-2006 и ОСТ 26-291-94.
*Размеры для справок.
Неуказанные предельные отклонения размеров:
Отклонение от перпендикулярности уголка опорного
тарелок к оси аппарата не должно превышать 3 мм.
Общий прогиб тарелки не должен превышать 3 мм.
Патрубки штуцеров и люков обрезать и обработать заподлицо
с внутренней поверхностью корпуса. После обработки заварить
которые перекрываются деталями тарелок должны
быть зачищены заподлицо с основным металлом.
Отверстия под болты во фланцах распологать симметрично по
отношению к главным осям колонны (но не на главных осях).
Колонну испытать на прочность пробным давлением 1
в горизонтальном положении.
Аппарат на месте монтажа теплоизолировать.
Аппарат должен иметь места маркировки.
Центр масс уточнить после сборки колонны.
Перед приваркой укрепляющих колец сварные швы приварки
штуцеров и люков к обечайке зачистить заподлицо к основному
Для вывода кубового остатка
Для датчика давления
Для указателя уровня
Ввод отбензиненного сырья
Ввод перегретого пара
Колонна ректификационная
Технические требования
Крышка эллиптическая.cdw

Неуказанные предельные отклонения размеров:
Сборочный чертеж последний.cdw

сосудов работающих под давлением" (ПБ 03-576-03).
испытание и приемка аппарата по ГОСТ Р 52630-2006
*Размеры для справок.
Неуказанные предельные отклонения размеров 2
Сварные швы и методы контроля см. таблицу
Корень шва варить в аргоне.
Наплавленный металл типа Э-50А ГОСТ 9467-75.
Нормы оценки качества сварных соединений по ОСТ 26 291-94.
Отклонение от перпендикулярности уголка опорного
аппарата не должно превышать 3 мм.
Общий прогиб тарелки не должен превышать 3 мм.
Патрубки штуцеров и люков обрезать и обработать заподлицо с внутренней
поверхностью корпуса. После обработки заварить корень шва.
которые перекрываются деталями тарелок должны быть зачищены
заподлицо с основным металлом.
Штуцер поз.4 и трубу поз.66 крепить по месту ребрами из листа поз.112.
При попадании втулки поз.67 на сварной шов корпуса аппарата допускается изменять
смещая от края сварного шва на расстояние
стенки. В этом случае расстояние между приварными деталями
расположенными по обе
стороны от смещенной детали должно быть равно сумме двух заданных шагов.
В кармане тарелки поз.33 вырезать отв. по месту.
Отверстия под шпильки во фланцах распологать симметрично по отношению
к главным осям колонны (но не на главных осях).
Колонну испытать на прочность и плотность пробным давлением
кгссм) в горизонтальном положении.
Покрытие наружных поверхностей и внутренней поверхности опоры: люк КО-85
ГОСТ 11066-74 с алюминиевой пудрой ПАП-2 ГОСТ 5494-71 в два слоя.
Уплотнительные поверхности фланцев от покрытия предохранить.
Аппарат на месте монтажа теплоизолировать.
Центр масс уточнить после сборки колонны.
Перед приваркой укрепляющих колец сварные швы приварки штуцеров и люков
к обечайке зачистить заподлицо к основному металлу обечайки.
После проведения пневмоиспытания в отверстия детали поз.51-54 вкрутить
Массу колонны уточнить после получения чертежей на тарелки.
Ввод парожидкостной смеси
Ввод легкой бензиновой фракции
Вывод тяжелой бензиновой фракции
Ввод дизельной фракции (ЦО)
Вывод дизельной фракции
Вывод затемненного продукта
Ввод перегретого пара
Ввод паров тяжелой бензиновой фракции
Ввод паров дизельной фракции
Для датчика давления
Для указателя уровня
Техническая характеристика
Назначение для разделения отбензиненной нефти на фракции
в горизонтальном положении 1
Рабочая температура среды в колонне
Минимально допустимая отрицательная температура стенки
Расчетная температура стенки
Среда отбензиненная нефть
класс опасности 4 по ГОСТ 12.1007-76
Прибавка для компенсации коррозии
трапецевидно-клапанная однопоточная
Группа аппарата по ОСТ 26.291-94 1
Район территории по скоростному напору ветра 01
Габаритные размеры мм 2370х2440х28020
Технические требования
Доклад нормальный Борисов.docx
Здравствуйте уважаемые члены комиссии.
Цель курсового проекта заключается в реконструкции ректификационной колонны и увеличении ее производительности. Для выполнения этой цели мною были произведены следующие действия:
Проведено технико-экономическое обоснование проекта где рассмотрен обзор существующих конструкций а также обоснование выбранной конструкции.
В технологическом расчете дано описание технологической схемы рассчитан материальный и тепловой баланс на основе производительности в результате которого были получены данные выхода компонентов.
Определен диаметр колонны и высота аппарата на основе расчета конструктивных размеров.
В конструкторской части произведен выбор материала определена толщина стенки обечайки с последующей проверкой на прочность и устойчивость. Рассчитано эллиптическое днище фланцевое соединение для люк-лаза. Выбран тип фланца: приварной встык тип уплотнительной поверхности фланцевого соединения — шип-паз. Произведен расчет укрепления отверстия под люк-лаз 500 мм выбрано укрепление отверстия накладным кольцом. Также для цилиндрического аппарата с эллиптическим днищем с учетом расположения и массы колонны – подобрана и рассчитана на прочность цилиндрическая опора аппарата юбочного типа.
В разделе монтажа и ремонта я подобрал кран для установки моей ректификационной колонны это самоходный стреловой кран на гусеничном ходу СКГ-4063 и привел основные его характеристики посчитаны монтажные устройства и приспособления: монтажные штуцера траверсы стропы а также приведен ремонт корпуса аппарата.
Доклад окончен спасибо за внимание.
Курсовой Борисов.docx
ФГБОУ ВПО «СИБИРСКИЙ ГОСУДАРСТВЕННЫЙ ТЕХНОЛОГИЧЕСКИЙ УНИВЕРСИТЕТ»
Факультет Переработки природных соединений
Кафедра машин и аппаратов промышленной технологии
Проект установки переработки нефти с разработкой ректификационной колонны производительностью
Пояснительная записка
(МАПТ 00. 00. 00. 002 ПЗ)
Студент группы 55-11
Н А К У Р С О В О Е П Р О Е К Т И Р О В А Н И Е
студенту ФППС БорисовуА.А. курса 5 спец. 130603.65
ТЕМА: Проект установки переработки нефти с разработкой ректификационной колонны производительностью 300 тыс. тгод
Местонахождение: г. Анжеро - Судженск
Программа: по данным предприятия
Технико-экономическое обоснование
Технологические решения
Конструкторская часть
Монтаж ремонт техническая эксплуатация
Список используемых источников
Содержание конструктивной части:
Объем пояснительной записки: __25-30 страниц
Срок сдачи проекта:__ 20 декабря 2014 г.
Руководитель и консультанты:_Карбышев М.А.
Щербаков В.Н. Конструирование и расчет элементов оборудования. Фланцевые соединения аппаратов В.Н. Щербаков В.Ф. Харин и др. – Красноярск: СибГТУ 2005. – 68 с.
Михалев М.Ф. Расчет и конструирование машин и аппаратов химических производств: Примеры и задачи М.Ф. Михалев Н.П. Третьяков А.И. Мильченко. – Л.: Машиностроение Ленингр. отд-ние 1984. – 301 с.
Поникаров И. И. Расчет машин и аппаратов химических производств и нефтегазопереработки И. И. Поникаров С. И. Поникаров С. В. Рачковский. – М.: Альфа-М 720 с.
Сарандашвили А. Г. Примеры и задачи по технологии переработки нефти и газа А. Г. Сарандашвили А.И.Львова. – М.: Химия 1980. – 256 с.
В данном курсовом проекте необходимо провести технологический и конструктивный расчеты ректификационной колонны с клапанными тарелками непрерывного действия для разделения смеси нефти Полуденного месторождения на 3 основные фракции: 85-180 ºС 180-350 ºС и мазут. Рассчитать расход основных фракций температурный режим составить материальный и тепловой балансы определить основные размеры аппарата исходя из скорости пара. Определить геометрические параметры корпуса колонны такие как: расчетные и исполнительные толщины элементов аппарата размеры фланцевых соединений укрепление отверстий а также был выполнен подбор и расчет опор аппарата. А также проверить на устойчивость и прочность под действием давления испытания.
Пояснительная записка содержит 74 листа текста 6 таблиц 25 рисунков 143 формулы.
Технико-экономическое обоснование ..
1. Обзор существующих конструкций..
2.Обоснование выбранной конструкции
Технологические решения .
1 Описание технологической схемы ..
2 Материальный баланс процесса ..
3 Материальный баланс аппарата ..
4 Тепловой баланс аппарата
5 Определение диаметра колонны .
6 Определение высоты колонны
Конструкторская часть
2 Расчет цилиндрической части ..
3 Расчет эллиптического днища и крышки на прочность
4 Расчет фланцевого соединения
5 Расчет на прочность укрепления отверстий
6 Расчет опор аппарата
Монтаж и ремонт ректификационной колонны ..
2 Расчет монтажных штуцеров ..
3 Расчет траверс работающих на изгиб
Целью конструктивного расчета химического и нефтехимического оборудования является определение размеров отдельных элементов обеспечивающих безопасную эксплуатацию машин и аппаратов за счет достаточной механической прочности плотности разъемных соединений устойчивости к сохранению формы и необходимой долговечности.
Конструкция аппарата должна предусматривать возможность внутреннего осмотра очистки промывки и продувки. Внутренние устройства препятствующие осмотру должны быть съемными. Аппараты должны иметь люки-лазы для внутреннего осмотра расположенные в удобных для обслуживания местах.
Ректификация потребляет огромное количество энергии и во многих случаях потребляет до 50 % всей энергии от потребления всего предприятия. Поэтому значительные усилия тысяч исследователей и разработчиков во всем мире во второй половине 20 века были сосредоточены именно в этой области но не принесли значительных улучшений промышленной технологии.
Надо отметить что в целом промышленная ректификация является крайне консервативным процессом. Огромные ректификационные колонны химических и нефтехимических заводов в некотором смысле даже являются символами современной промышленности. Высота ректификационных колонн часто превышает 30 метров и более. Соответственно стоимость изготовления эксплуатации и ремонта колонн становится огромной. Ректификационные колонны смотрятся как динозавры и совершенно не соответствуют динамическому облику 21 века с колоссальным прогрессом в коммуникациях и компьютерной индустрии.
1 Обзор существующих конструкций
Тарельчатые контактные устройства можно классифицировать по многим признакам; например по способу передачи жидкости с тарелки на тарелку различают тарелки с переточными устройствами и тарелки без переточных устройств (провальные).
Тарелки с переточными устройствами имеют специальные каналы по которым жидкость перетекает с одной тарелки на другую причем по этим каналам не проходит газ. На провальных тарелках нет переливных устройств и жидкость и газ проходят через одни и те же отверстия или прорези в полотне тарелки. Эти прорези работают периодически: в определенный момент времени одни прорези пропускают пар другие — жидкость; затем их роли меняются.
По характеру взаимодействия газового и жидкостного потоков различают тарелки барботажного и струйного типов. Тарелки на которых сплошной фазой является жидкость а дисперсной — газ или пар называют барботажными. На струйных тарелках дисперсной фазой является жидкость сплошной — газ; потоки взаимодействуют в прямоточном режиме на поверхности капель и жидкостных струй взвешенных в газовом потоке.
В зависимости от конструкции устройств ввода пара (газа) в жидкость различают тарелки клапанные колпачковые ситчатые язычковые решетчатые с прямоточно-скоростными контактными элементами и др. Одни из этих тарелок могут работать только в барботажном режиме (колпачковые) другие — только в струйном (язычковые) третьи и в том и в другом режимах (клапанные).
В химической нефтехимической нефтеперерабатывающих отраслях промышленности наиболее распространены барботажные и струйные тарелки с переливами.
Колпачковые тарелки с капсульными колпачками до недавнего времени считали лучшими контактными устройствами для ректификационных и абсорбционных аппаратов благодаря простоте эксплуатации и универсальности.
Основной частью колпачковой тарелки (рисунок 1.1) является стальной диск 1 (или полотно тарелки) с отверстиями для паровых патрубков 6. Патрубки приварены к диску. Над патрубками установлены колпачки 5 диаметром 60 или 80 мм. Колпачки имеют прорези высотой 15; 20 или 30 мм.
В ректификационных аппаратах нефтеперерабатывающих производств используют тарелки с туннельными колпачками (рисунок 1.2). Такие тарелки собирают из штампованных желобов 1 уложенных по ходу жидкости на опорные уголки 2 и накрытых колпачками 3 так что между ними образуются паровые каналы. Для равномерного распределения пара колпачки в нижней части имеют трапецеидальные прорези. Колпачки крепят на полотне тарелки шпильками 4. Для равномерного распределения жидкости на тарелке сливную планку 5 также выполняют с прорезями.
-желобы; 2-упорные уголки; 3-колпачки; 4-шпильки; 5-сливная планка
Рисунок 1.1 - Тарелка с туннельными колпачками
Основное преимущество этих тарелок — небольшое число колпачков и возможность их очистки. Остальные показатели этих тарелок низкие поэтому в настоящее время их заменяют более современными- контактными устройствами.
Тарелки с S-образными элементами
В настоящее время в нефтеперерабатывающих колоннах используют и тарелки с S-образными элементами 1 (рисунок 1.2) установленными перпендикулярно направлению движения жидкости на тарелке. Для того чтобы закрыть каналы с торцов и увеличить жесткость тарелки между S-образными элементами устанавливают пластины 2.
Рисунок 1.2 - Тарелка с S-образными элементами
В зависимости от диаметра аппарата такие тарелки бывают одно- и многосливными. Характерная особенность этих тарелок состоит в том что пар выходит из контактных элементов в направлении движения жидкости. Это способствует уменьшению разностей уровней жидкости на тарелке у сливной и переливной перегородок.
Металлоемкость тарелок с S-образными элементами почти вдвое меньше а производительность на 20—30 % больше по сравнению с тарелками с капсульными колпачками. Эффективность сравниваемых тарелок примерно одинаковая (КПД равен 06 – 08). Оптимальная нагрузка по газу для этой тарелки на 10–25 % меньше чем для колпачковой. Для повышения диапазона устойчивой работы и производительности таких тарелок S-образные элементы 2 (Рисунок 1.3) снабжают прямоточными клапанами 1 прямоугольной формы размещенными на верхней площадке S-образного элемента. Для увеличения жесткости тарелки устанавливают пластины 3. По производительности эти тарелки примерно на 10 % превосходят клапанные прямоточные.
Рисунок 1.3 - Тарелка с S-образными элементами и клапанами
Клапанные тарелки также широко применяют в нефтехимической промышленности. Основные преимущества этих тарелок — способность обеспечить эффективный массообмен в большом интервале рабочих нагрузок несложность конструкции низкая металлоемкость и невысокая стоимость.
Клапанные тарелки изготовляют с дисковыми и прямоугольными клапанами; работают тарелки в режиме прямоточного или перекрестного движения фаз. В отечественной промышленности наиболее распространены клапанные прямоточные тарелки с дисковыми клапанами. На клапанной прямоточной тарелке (рисунок 1.4) в шахматном порядке расположены отверстия в которых установлены саморегулирующиеся дисковые клапаны диаметром 50 мм способные подниматься при движении пара (газа) на высоту до 6—8 мм.
Рисунок 1.4 - Клапанно-прямоточная тарелка
Дисковый клапан снабжен тремя направляющими расположенными в плане под углом 45°; две из этих направляющих имеют большую длину. Кроме того на диске клапана штамповкой выполнены специальные упоры обеспечивающие начальный зазор между диском и тарелкой; это исключает возможность «прилипания» клапана к тарелке (рисунок 1.4 а положение I). При небольшой производительности по пару поднимается легкая часть клапана (рисунок 1.4 положение II) и пар выходит через щель между клапаном и полотном тарелки в направлении противоположном направлению движения жидкости по тарелке. С увеличением скорости пара клапан поднимается и зависает над тарелкой (рисунок 1.4 положениеIII); теперь пар барботирует в жидкость через кольцевую щель под клапаном. При дальнейшем увеличении производительности по пару клапан занимает положение при котором пар выходит в направлении движения жидкости уменьшая разность уровней жидкости на тарелке (рисунок 1.4 положение IV).
При этом короткая направляющая фиксируется в специальном вырезе на кромке отверстия обеспечивая заданное положение клапана при его подъеме.
-переливная перегородка; 2-колпачек; 3-сливная перегородка;
Рисунок 1.5 - Колпачковая тарелка
Для создания необходимого уровня жидкости на тарелке ее снабжают сливной перегородкой 3. Переливная перегородка 1 образует переливной карман а в который погружается сливная планка 4 тарелки расположенной выше.
Применяют два варианта крепления колпачка к тарелке. В исполнении 1 положение колпачка можно регулировать по высоте в исполнении 2 регулирование невозможно и нижние кромки прорезей в этом случае упираются в полотно тарелки.
Тарелка работает следующим образом. Поступающая жидкость заполняет тарелку на высоту определяемую сливной перегородкой 3 при этом прорези колпачков должны быть погружены в жидкость. Пар проходит через паровые патрубки щели колпачков и барботирует сквозь слой жидкости. Газ и жидкость взаимодействуют в перекрестном токе: жидкость движется по тарелке от переливного кармана к сливной перегородке и далее на расположенную ниже тарелку а газ — вверх по оси колонны.
Колпачковые тарелки можно изготовлять из чугуна меди керамики углеграфита пластмасс и др.
Тарелки с капсульными колпачками имеют относительно высокий КПД (075—080) и работают в широком диапазоне производительностей по газу. Их можно использовать при нестабильных нагрузках по жидкости и пару.
Для этих тарелок F 1 (мс) (кгм3)-0.5 а гидравлическое сопротивление зависящее от глубины погружения колпачка не превышает 1 кПа. К недостаткам этих тарелок следует прежде всего отнести значительные металлоемкость и трудоемкость изготовления.
Эффективность клапанных прямоточных тарелок (КПД) 0.70— 085 F 25 (мс) (кгм3)-0.5 диапазон устойчивой работы 35. В области саморегулируемой работы тарелки обладают относительно небольшим гидравлическим сопротивлением.
Для увеличения производительности и диапазона устойчивой работы клапанные тарелки выполняют балластными (рисунок 1.6). Над отверстием тарелки 1 на специальных ножках установлены ограничители подъема 4 а внутри их — на ножках 7 легкий клапан 5 и балласт 2. Для исключения прилипания клапана к балласту имеются упоры 3 и 6. При малой производительности по газу тарелка работает как обычная с дисковыми клапанами меньшей массы; при увеличении нагрузки клапан 5 упирается в балласт и работает совместно с ним как один утяжеленный клапан.
-тарелка; 2-балласт; 3 6-упоры; 4-ограничители подъема; 5-легкий клапан; 7-ножки
Рисунок 1.6 — Клапанная балластная тарелка
Тарелка с групповым балластом
Балластные клапанные тарелки можно выполнять как с индивидуальным так и с групповым балластом. Примером последнего варианта могут служить групповые балластные тарелки ректификационных колонн (рисунок 1.7). Такая тарелка 1 имеет расположенные в несколько рядов прямоугольные вырезы закрытые клапанами 2 прямоугольной формы. Большие размеры клапанов (154 x45 мм) позволяют уменьшить их число по сравнению с дисковыми клапанами в 2-4 раза. Над клапанами расположен общий подвижный балласт 3 выполненный из прутка диаметром 8 мм. При работе таких тарелок вначале поднимается пластина клапана затем она упирается в балласт и поднимается вместе с ним до упора в головку винта 4.
-тарелка; 2-клапана; 3- общий подвижный балласт
Рисунок 1.7 - Тарелка с групповым балластом
Клапанная тарелка со штампованными клапанами цилиндрической формы показана на рисунке 1.8 а. КлапанI лежащий на полотне тарелки 2 представляет собой часть цилиндра с ограничителями подъема 3. Клапан расположен в гнезде имеющем отогнутую полку 4.клапана его конфигурация и положение центра тяжести подобраны так что при достижении определенной скорости пара клапан перекатывается по поверхности отогнутой полки. При этом между плоскостью тарелки и клапаном образуется щель через которую в направлении слива жидкости выходит пар. При значительной производительности по пару клапан поднимается и зависает над тарелкой.
а- тарелка со штампованными клапанами; б- жалюзийно-клапанная тарелка; 1-клапан; 2-тарелка; 3- ограничители подъема; 4- отогнутая полка
Рисунок 1.8 - Тарелки клапанные
В жалюзийно-клапанной тарелке (рисунок 1.8 - а б) щель для входа газа на тарелку 1 образуется при повороте плоских клапанов-жалюзей 3 вокруг их оси укрепленной в рамке 2.
Ситчатые и решетчатые тарелки.
Ситчатые тарелки со сливным устройством применяют в колонных аппаратах диаметром 400—4000 мм при расстоянии между тарелками от 200 мм и более. Основной элемент таких тарелок — металлический диск с отверстиями диаметром 2—6 мм расположенными по вершинам равносторонних треугольников (рисунок 1.9).
Рисунок 1.9 — Элемент сетчатой тарелки
В колоннах диаметром более 800 мм тарелки состоят из отдельных секций. По креплению секций тарелки к корпусу и устройству переливов такие колонны аналогичны аппаратам с колпачковыми и клапанными тарелками. Преимущество ситчатой тарелки — большое свободное (т. е. занятое отверстиями) сечение тарелки а следовательно и высокая производительность по пару простота изготовления малая металлоемкость. По производительности по пару (газу) эти тарелки на 30—40 % превосходят колпачковые. Недостаток — высокая чувствительность к точности установки. Аппараты с ситчатыми тарелками не рекомендуется использовать для работы на загрязненных средах; это может вызвать забивание отверстий.
Для уменьшения гидравлического сопротивления и расширения диапазона устойчивой работы ситчатых тарелок их комбинируют с клапанными устройствами (рисунок 1.10); в результате повышается эффективность работы тарелки при малой и большой производительности по пару. При малых нагрузках тарелка работает как обычная ситчатая с увеличением нагрузки открывается клапан 2 и между клапаном и тарелкой 1 образуется щель откуда под некоторым углом к горизонтали выходит пар обеспечивая перемещение жидкости по тарелке в направлении слива и уменьшая разность уровней жидкости на тарелке. Ситчато-клапанная тарелка обеспечивает большой диапазон устойчивой работы при небольшом гидравлическом сопротивлении что делает ее пригодной для процессов протекающих под вакуумом.
Рисунок 1.10 — Элемент ситчато-клапанной тарелки
Ситчатые тарелки с просечно-вытяжными отверстиями (рисунок 1.11)используют в колонных аппаратах диаметром 1200— 4000 мм. Такие тарелки состоят из отдельных секций 1 изготовляемых из листа толщиной 2—3 мм с просечно-вытяжными отверстиями. Тарелка работает как струйная прямоточная. Для уменьшения брызгоуноса под углом 60° над тарелкой устанавливают отбойные элементы 2.
Рисунок 1.11 — Тарелка с просечно-вытяжными отверстиями
Свободное сечение тарелки выбираемое из условия отсутствия «провала» жидкости должно быть достаточно большим (не менее 30 % сечения колонны) чтобы тарелка обладала невысоким гидравлическим сопротивлением. Благодаря этому такие тарелки используют в вакуумных колоннах. Минимальное расстояние между тарелками в колонне 450 мм.
Ситчатые тарелки наиболее распространены в качестве контактных устройств ректификационных колонн воздухоразделительных установок работающих при низкой температуре. В аппаратах небольшого диаметра применяют S-образные ситчатые тарелки (Рисунок 1.12). Такая тарелка представляет собой перфорированный лист к которому припаяна S-образная перегородка 3 делящая тарелку на две части. Стекающая с верхней тарелки жидкость через прорези в сливном стакане 2 и далее через переливную перегородку 5 поступает на тарелку и движется в направлении указанном стрелками контактируя с паром поднимающимся через отверстия в листе 1. Подойдя к перегородке 3 с другой стороны жидкость стекает на следующую тарелку через сливную перегородку 4 и сливной стакан.
Рисунок 1.12 — Ситчатая тарелка с S-образной перегородкой
Решетчатые провальные-тарелки (рисунок 1.13) используют в установках рабочая производительность которых отклоняется от расчетной не более чем на 25 %.
Рисунок 1.13 — Решетчатая провальная тарелка
К преимуществам этих тарелок следует прежде всего отнести простоту конструкции и малую металлоемкость. Кроме того тарелки имеют большую пропускную способность по жидкости и при достаточной ширине щели могут быть использованы для обработки загрязненных жидкостей оставляющих осадок на тарелке. По эффективности решетчатые провальные тарелки обычно не уступают тарелкам с переливом. К недостаткам относятся узкий диапазон устойчивой работы и сложность обеспечения равномерного распределения орошения по поверхности тарелок в начале процесса.
Конструктивно тарелка представляет собой плоский перекрывающий все сечение колонны диск 1 с выштампованными в нем прямоугольными щелями уложенный на опорную конструкцию 2. Обычно площадь прорезей составляет 10—30 % всей площади тарелки. Прорези (как правило размерами 4x60 мм) располагаются на поверхности тарелки с шагом t = 10 36 мм.
При работе колонны под давлением поступающих паров на полотне тарелки создается слой жидкости через которую барботирует пар. При этом часть жидкости протекает через прорези на расположенную ниже тарелку. Прорези работают периодически: места стока жидкости и прохода пара произвольно перемещаются по полотну тарелки.
Секционированные массообменные устройства.
Одно из направлений технического прогресса в химической нефтехимической и нефтеперерабатывающей промышленности — разработка и применение аппаратов большой единичной мощности. До недавнего времени повышение эффективности и производительности колонн обеспечивали увеличением их высоты и диаметра. Однако с увеличением диаметра колонны возрастает неупорядоченность движения взаимодействующих фаз: на тарелке появляются «байпасные» потоки «мертвые» зоны возникает поперечная неравномерность скорости газового потока и высоты жидкости на тарелке. Все это снижает эффективность массообмена в колонне. В связи с этим производительность аппарата следует повышать не увеличением размеров аппарата а созданием контактных устройств обладающих высокой производительностью по жидкости и пару в частности продольным и поперечным секционированием этих устройств.
Известно что производительность тарелок повышается при контактировании фаз в прямотоке. Однако при прямоточном взаимодействии и большой скорости пара (газа) жидкость смещается в направлении к сливному карману что затрудняет работу сливных устройств.
Для компенсации прямоточного движения фаз и исключения его распространения на всю Тарелку можно устанавливать на тарелке продольные и поперечные перегородки обеспечивающие зигзагообразное движение жидкости на тарелке от перелива к сливу а также создающие условия для движения потоков парожидкостной смеси по тарелке в противоположных или пересекающихся направлениях.
Примером может служить продольно-секционированная тарелка с просечными элементами (рисунок 1.14). На полотне тарелки 2 выштампованы просечки 1 отогнутые под угломa. Тарелка секционирована вдоль потока жидкости вертикальными перегородками 3 причем для создания постоянного гидравлического сопротивления по всей тарелке перегородки перфорированы.
-полотно тарелки; 2-просечки; 3-перегородки
Рисунок 1.14 — Продольно-секционированная тарелка с просечными элементами
При скорости газа до 15 мс тарелки работают аналогично ситчатой и колпачковой: жидкость из переливного кармана а поступает на рабочую часть тарелки газ вводится через просечки барботирует через слой жидкости аэрирует ее и на тарелке образуется газожидкостный слой. При скорости газа более 15 мс газовые струи выходящие из просечек и создаваемые ими потоки жидкости движутся к вертикальным перегородкам или стенкам колонны ударяются о них сепарируются и газ покидает тарелку. При этом жидкость совершает сложное зигзагообразное движение от переливного а к сливному б карману.
Вариантом массообменного устройства с продольным секционированием является клапанная тарелка с продольными перегородками 3 (рисунок 1.15) которая отличается от тарелки с просечными элементами тем что на полотне 1 тарелки вместо просечек смонтированы клапаны 2 с боковыми стенками обеспечивающие направленное движение жидкостного потока.
-полотно тарелки; 2-клапаны; 3-продольные перегородки
Рисунок 1.15 — Комбинированная клапанная тарелка
По производительности такие тарелки превосходят обычные клапанные тарелки без продольного секционирования в 14 раза а по эффективности массообмена в 125—13 раза.
При высокой плотности орошения [более 50 м3(м2-ч)] когда работа тарелок лимитируется производительностью переливных устройств целесообразно применение многосливной продольно-секционированной тарелки или тарелки с двумя зонами контакта фаз (рисунок 1.16). Последняя представляет собой комбинацию барботажной тарелки (ситчатой клапанной) с устройством в котором реализуется зона контакта фаз формирующаяся в пространстве между тарелками при перетекании жидкости. Тарелка состоит из перфорированного основания 1 с установленными на нем сливными карманами 2 (могут быть одно- двух- и трехщелевыми) направляющих планок 3 и отбойных дисков 4.
-перфорированное основание; 2- сливные карманы;
- направляющие планки; 4- отбойные диски
Рисунок 1.16 — Тарелка с двумя зонами контакта
Однощелевой сливной карман установленный на тарелке 1 (рисунок 1.17 а) состоит из патрубка 2 и отбойного диска 3 укрепленного так что между ними образуется кольцевая щель шириной А = 4 12 мм. Через эту щель вытекает кольцевая струя жидкости образуя дополнительную зону контакта. При установке двухщелевого сливного кармана (рисунок 1.17 б) жидкость переливается через сливную перегородку протекает по внутренней стенке наружного патрубка 2 и конусу 4 во внутренний патрубок 5 и вытекает из нижней щели кольцевой струей образуя дополнительную зону контакта.
-тарелка; 2- наружный патрубок; 3-отбойные диски; 4-конус;
-внутренний патрубок
Рисунок 1.17 — Однощелевые (а) и двухщелевые (б) карманы
С увеличением производительности по жидкости уровень ее в патрубке 5 повышается жидкость заполняет пространство в патрубке 2 и начинается истечение из верхней щели. В пространстве между тарелками образуется вторая кольцевая струя. Таким образом многощелевой слив позволяет значительно расширить диапазон нагрузок по жидкости.
Тарелки с двумя зонами контакта фаз позволяют повысить эффективность массообмена примерно на 30 % благодаря образованию дополнительной зоны контакта в пространстве между тарелками.
2 Обоснование выбранной конструкции
В данной колонне в качестве контактных устройств используются ректификационные однопоточные трапециевидно-клапанные тарелки.
Тарелка клапанная трапециевидная «ТРИЭН»
Полезная модель относится к области химического и нефтяного машиностроения и может быть использована в качестве внутреннего устройства ректификационных и абсорбционных аппаратов для осуществления контакта жидкости с газом (паром).
Известна трапециевидно-клапанная тарелка (АТК 26-02-4-89 АООТ «ВНИИНЕФТЕМАШ») работающая в смешанном режиме перекрестно-прямоточном движении контактируемых фаз. Основными контактными элементами тарелки являются подвижные клапаны трапециевидной формы. Клапаны снабжены двумя ножками выполняющими функцию ограничителя высоты его подъема. Передняя ножка расположена на вершине трапеции задняя (широкая) - в основании трапеции. Клапан прикрывает отверстие трапециевидной формы через которое снизу проходит газ (пар).
Недостатком трапециевидно-клапанной тарелки является наличие зазора между широкой кромкой отверстия и задней ножкой через который проваливается жидкость что существенно снижает эффективность контакта фаз при низких нагрузках по газу.
Полезная модель создана с целью устранения провала жидкости и повышения эффективности контакта фаз.
В полезной модели провал жидкости устраняется за счет изменения конструкции задней ножки клапана. Вместо одной широкой задней ножки клапан снабжен двумя задними ножками и козырьком препятствующим поступлению жидкости в отверстие по широкому основанию.
-основание тарелки; 2-клапаны
Рисунок 1.18 Трапециевидно-клапанная тарелка
На рисунке 1.18 показана конструкция трапециевидно-клапанной тарелки состоящая из основания тарелки 1 с трапециевидными отверстиями под клапаны 2.
-основание тарелки; 2-клапан; 3-передняя ножка; 4-задние ножки; 5-козырек; 6-пуклевки
Рисунок 1.19 – Клапан
На рисунке 1.19 показан вид сверху клапана его разрез. Клапан снабжен тремя ножками: одной передней 3 и двумя задними 4 а также козырьком 5 с отогнутой вниз кромкой двумя пуклевками 6.
На рисунке 1.20 показаны положения открытия клапана по мере увеличения нагрузки по газу (пару) на тарелке 2.
Рисунок 1.20 положения открытия клапана
При низких нагрузках по газу (пару) (рисунок 1.20-а) клапан лежит на основании тарелки при этом газ (пар) проходит через зазор между клапаном и основанием тарелки образуемым за счет отогнутой вниз кромки 5 и пуклевок 6. В этом положении клапан и тарелка работают в чисто перекрестном режиме а газ (пар) выходит через зазоры по боковым стенкам клапана.
При средних нагрузках по газу (пару) (рисунок 1.20-б) передняя часть клапана поднимается на максимальную высоту до упора передней ножки 3 в основание тарелки при этом сзади клапан упирается в основание тарелки отогнутой кромкой козырька 5. В этом положении клапан и тарелка работают в смешанном перекрестно-прямоточном режиме.
В первом и втором режимах работы клапан сзади опирается кромкой на основание тарелки не давая набегающей на клапан жидкости провалится под клапан. Тем самым при низких и средних нагрузках по газу (пару) тарелка практически работает без провала жидкости.
При максимальной нагрузке по газу (пару) (рисунок 1.20-в) клапан поднимается в верхнее положение и газ (пар) выходит практически по всему периметру клапана и отверстия при этом высокая скорость газа (пара) препятствует провалу жидкости по всему периметру отверстия под клапан.
К преимуществам трапециевидно-клапанной тарелки оборудованной клапанами с тремя ограничительными ножками и защитным козырьком следует отнести
- отсутствие провала жидкости при низких нагрузках по газу (пару) снижающего эффективность контакта фаз;
- увеличение на 20% периметра контакта фаз при максимальных нагрузках по газу (пару) что приводит к увеличению эффективности контакта фаз снижению гидравлического сопротивления.
-насос; 234-теплообменники; 5-холодильник воздушный; 6-электродегидраторы; 7-отбензинивающая колонна; 8-печь; 9-ректификационная колонна; 10-емкость; 11-конденсатор-холодильник; 12-сепаратор
Рисунок 2.1 – Технологическая схема установки переработки нефти
1Описание технологической схемы
Отбензиненная нефть в виде парожидкостной смеси по трансферным трубопроводам двумя потоками поступает в питательную секцию колонны поз. К2. В неё на фракционирование поступает отбензиненная нефть из печи поз. П1.
Для улучшения отгона легких фракций от мазута в куб колонны К2 подается перегретый водяной пар полученный в пароперегревателе печи поз. П1. Трубопровод перегретого пара на входе в колонну поз. К2 снабжен расходомером и регулирующим клапаном ручной арматурой для возможности отключения и обратным клапаном для предотвращения обратного хода.
Пары верха колонны поз. К2 поступают на конденсацию в воздушный конденсатор-холодильник поз. КХ1 трубопровод на выходе из КХ1 оборудован ручной арматурой для отключения и датчиком температуры для контроля процесса конденсации. Температура сконденсированного продукта регулируется с помощью частотного преобразователя двигателя вентилятора конденсатора-холодильника поз. КХ1 по сигналу датчика температуры. При изменении частоты вращения двигателя конденсатора-холодильника поз. КХ1 изменяется количество воздуха подаваемого на охлаждение. Далее сконденсированные пары доохлаждаются в водяном холодильнике поз. Х2. На трубопроводе оборотной воды после холодильника поз. Х2 установлен регулирующий клапан. Клапан регулирует температуру сконденсированных паров верха колонны поз. К2 расходом оборотной воды. Трубопроводы холодильника поз. Х2 оборудованы ручной арматурой для отключения. Охлажденный продукт направляется в горизонтальный сепаратор поз. С1 где происходит его разделение на фракцию легкого бензина углеводородные газы и воду.
Углеводородные газы из сепаратора поз. С1 по трубопроводу снабженному ручной арматурой и регулирующим клапаном через С2 поступают на сжигание в трубчатую печь поз. П1. Регулирующий клапан регулирует давление верха колонны поз. К2 путем сброса углеводородных газов из сепаратора поз. С1.
Фракция легкого бензина из сепаратора поз. С1 перекачивается насосом по трубопроводу снабженному арматурой с электроприводом и делится на три потока: первый – орошение колонны поз. К2 (подается на верхнюю тарелку) второй – орошение колонны поз. К1 (подается на верхнюю тарелку) третий подается на склад охлаждаясь в концевом водяном холодильнике поз. Х8.
Тяжелый бензин колонны поз. К2 (отбираемый с тарелки 10) через буферную емкость поз. Е3 поступает на охлаждение в воздушный холодильник поз. ХВ2. Пары из буферной емкости тяжелого бензина поз. Е3 возвращаются в колонну поз. К2. Далее тяжелый бензин отстаивается от подтоварной воды в емкости поз. Е5. Подтоварная вода направляется в канализацию. Тяжелый бензин насосом через концевой водяной холодильник поз. Х1 подаётся на склад.
Дизельная фракция из колонны поз. К2 отбираемая с накопительной тарелки между тарелками 18 и 19 через буферную емкость поз. Е4 поступает последовательно в теплообменники нагревая своим теплом поток сырья. Пары из емкости дизельной фракции поз. Е4 возвращаются в колонну поз. К2.
После теплообменника дизельная фракция перекачивается насосом и делится на два потока: первый последовательно проходит через теплообменники нагревает сырье затем охлаждается в холодильнике поз. ХВ1 и после концевого водяного холодильника поз. Х3 поступает на склад; второй в качестве циркуляционного орошения подается в колонну на 16 тарелку и в качестве флегмы на 19 тарелку. Поток дизельной фракции направляемый на склад последовательно проходит через теплообменники после которых трубопровод оборудован датчиками температуры после теплообменника установлен датчик давления. Пройдя теплообменники поток дизельной фракции поступает в воздушный холодильник поз. ХВ1 после которого на трубопроводе установлен датчик температуры. По сигналу температурного датчика регулируется температура дизельной фракции на выходе из воздушного холодильника ХВ1 частотными преобразователями установленными на приводах вентиляторов. Далее фракцию дизельного топлива доохлаждают в концевом водяном холодильнике поз. Х3.
На трубопроводе подачи дизельной фракции в колонну поз. К2 установлена электроприводная арматура для отключения смежных технологических блоков. Перед вводом циркуляционного орошения в колонну поз. К2 на тарелку 16 на трубопроводе дизельной фракции последовательно установлены: расходомер регулирующий клапан регулирующий расход орошения на тарелку 16 ручная арматура для отключения и обратный клапан для предотвращения обратного хода.
Перед вводом флегмы в колонну поз. К2 на тарелку 19 на трубопроводе дизельной фракции последовательно установлены: расходомер регулирующий клапан корректирующий расход орошения на тарелку 19 по сигналу температурного датчика установленного под тарелкой 19 ручная арматура для отключения и обратный клапан для предотвращения обратного хода.
Мазут из куба колонны поз. К2 поступает последовательно в теплообменники нагревая своим теплом поток сырья. Далее мазут насосом проходя последовательно через теплообменники где он нагревает поток сырья подается на склад.
2 Материальный баланс процесса
Материальный баланс установки АТ составляется на основе разгонки нефти на фракции (таблица 2.1) или пользуясь кривыми истинных температур кипения (ИТК) (Приложение А рисунок 1).
Материальный баланс процесса первичной переработки нефти составляется с учетом технологических потерь и на основе закона сохранения массы вещества при равенстве материальных потоков поступающих на установку и выходящих с неё.
При составлении баланса учитываются основные продукты первичной переработки нефти:
Фр. Н.к. - 180 ºС - бензин
Фр. 180 - 350 ºС - Атмосферный газойль
Фр. 350 - 500 ºС – Мазут
) Производительность установки по сырью 300 тыс. тгод;
) Число рабочих дней 365;
) Количество технических потерь 252 тгод =00084%.
Таблица 2.1 - Разгонка ИТК исходной нефти на фракции
Температура выкипания фракции при 1013 кПа °С
Продолжение таблицы 2.1
Определяем суточную производительность установки по сырью тсут.
где: G'с - суточная производительность установки по сырью тсут.
Gс - производительность установки по сырью тыс. тгод;
ч.р.д.- число рабочих дней в году.
Определяем часовую производительность установки по сырью кгч .
где: G"с - часовая производительность установки по сырью кгч;
- количество часов в сутках.
= 82192 = 3424667 кгч.
Определяем выход фракций нефти тыс. тгод.
где: Gc – годовая производительность установки по сырью тыс. тгод;
а – доля фракции нефти на потенциал.
Gфр = 300 0026 = 78 тыс. тгод.
Материальный баланс установки рассчитываем по ИТК
Результаты расчета материального баланса АТ заносятся в таблицу 2.2
Таблица 2.2– Материальный баланс установки АТ
3 Материальный баланс аппарата
Материальный баланс аппарата составляется на основе материального баланса установки при установившемся режиме работы без учета технологических потерь.
Рисунок 2.2 – Материально-потоковый график колонны К-2
Результаты расчета материального баланса атмосферной колонны заносятся в таблицу 2.3
Таблица 2.3 – Материальный баланс атмосферной колонны К-2
4 Тепловой баланс аппарата
Тепловой баланс колонны учитывает все тепло вносимое в колонну и выносимое из неё.
Баланс составляется на основе закона сохранения энергии при равенстве количества тепла поступающего в аппарат и выходящего из него (без учета потерь тепла в окружающую среду).
Для составления эскиза атмосферной колонны определяются температуры выводов потоков однократного испарения:
) Определяется температура вывода фракции 85-180ºС из колонны. Фракция соответствует бензину выводится из верха колонны.
По ИТК определяется значение следующих точек:
Рассчитывается tg угла наклонаИТК;
(·) 100% по ОИ = 57%
Температура вывода фракции 85-180ºС из колонны равна 160С.
) Определяется температура вывода фракции 180-350ºС из колонны. Фракция соответствует бензину выводится из колонны боковым погоном.
Рассчитывается tg угла наклона ИТК;
(·) 100% по ОИ = 65%
Температура вывода фракции 180-350ºС из колонны равна 244С.
Рассчитывается средневзвешенная плотность по формуле:
где – средняя температурная поправка относительной плотности на 1К определяется по эмпирической формуле Кусакова:
Рассчитывается средневзвешенная плотность нефти:
Рассчитывается средневзвешенная плотность
Рассчитывается средневзвешенная плотность:
Рассчитывается средневзвешенная плотность мазута:
Расчетные значения плотностей заносятся в таблицу
Таблица 2.4 - Плотности компонентов
Наименование компонента
Для составления уравнения теплового баланса вычерчивается схема тепловых потоков аппарата:
Рисунок 2.3 – Эскиз тепловых потоков
Уравнение теплового баланса:
где: Qприх. – суммарное количество тепла приходящего в колонну кВт;
Qрасх. – суммарное количество тепла выходящего из колонны кВт.
Температурный режим в колонне регулируется острым орошением и циркуляционными орошениями.
При составлении теплового баланса атмосферной колонны принимается количество острого орошения и определяется количество циркуляционного орошения.
Определяется тепло приходящее в колонну кВт;
Qприх. = Qс + Qостр.орош+(2.8)
Определяется количество тепла поступающего с сырьем кВт;
Qc. = Gc. * + Gc (1- ) (2.9)
где: Gc.- количество нефти отбензиненной берется из материального баланса колонны кгс.
– энтальпия парообразного сырья при температуре 340С и плотности =08434 кДжкг
– энтальпия жидкого сырья при температуре 340С и плотности = 08434 кДжкг
Определяется доля отгона:
Определяется энтальпия пара кДжкг;
= (12958 + 0134 Тср + 000059 ) (4- ) - 30899(2.11)
= (12958 + 0134 * 613 + 000059 6132) (4 – 08434) - 30899 = 105916
Определяется энтальпия жидкости кДжкг:
= * (00017 + 0762 Тср - 33425)(2.12)
= * (00017 6132+ 0762 · 613- 33425) = 84025
Qc. = 894 04242 105916+ 894 (1 – 04242) 84025= 792692
Определяется количество теплоты поступающего с острым орошением кВт;
Qостр.ор.= Gостр.ор. (2.13)
где: Gостр.ор. - количество острого орошения кгс
R – кратность орошения принимается R =2:1
- энтальпия острого орошения при 50С и при плотности ρ=07568 кДжкг.
Определяется количество острого орошения кгс;
Gостр.ор.= 2 Gфр.85-120(2.14)
Определяется энтальпия острого орошения кДжкг;
= (00017 3232+ 0762 · 323- 33425) = 10258
Qостр.ор.= 38 10258= 3898
В расчете примем что расход водяного пара в низ колонны К2 будет подаваться равным 3% на сырье кВт;
Энтальпия в.п. при данной температуре и давлении P=045МПа;
Определяется количество в.п. кгс;
Gв.п.= 003 Gмазут(2.16)
= 01122 3168 = 35544
Qприх. = 792692+3898+ 35544=86722
Определяется тепло выходящее из колонны кВт;
Qрасх.=Qфр.85-180 + Qфр.180-350 + Qмазут + Qв.п.+ Qостр.ор. (2.17)
Определяется тепло уходящее с в.п. кВт:
Qв.п.= Gв.п . (2.18)
– энтальпия в.п. при 150С равна 2773 кДжкг
Qв.п. =01122 2773 =3112
Определяется тепло уходящее с острым орошением кВт;
Qостр.ор.= Gостр.ор. (2.19)
где – энтальпия пара острого орошения при 150С
Определяется энтальпия пара острого орошения кДжкг;
=(12958 + 0134 423 + 000059 423²) (4- 07568) - 30899 = 6376
Qостр.ор.= 38 6374= 24228
Определяется тепло уходящее с фр.85- 180С кВт;
Qфр.85-180 = Gфр.85-180 (2.20)
Qфр.85-180 = 19 · 6374= 1211
Определяется тепло уходящее с фр.180 - 350С кВт;
Qфр.180-350 = Gфр.180-350 (2.21)
Определяется энтальпия фр.180 - 350 кДжкг;
= (00017 5192+ 0762 519- 33425) = 56684
Qфр.180-350 = 33 · 56684= 18706
Определяется тепло уходящее с мазутом кВт;
Qмазут = Gмазут (2.22)
Определяется энтальпия мазута кДжкг;
= (00017 5982+ 0762 598- 33425) = 7638
Qмазут = 374 7638= 28564
Qрасх.= 1211+18706+28564+3112+24228=86722
По разнице тепла приходящего и расходуемого определяется тепло вносимое циркуляционными орошениями кВт ;
ΔQ=Qприх.- Qрасх(2.23)
Результаты теплового баланса атмосферной колонны сводят в таблицу:
Таблица 2.5 – Тепловой баланс атмосферной колонны
Продолжение таблицы 2.5
5 Расчет конструктивных размеров
Определяется диаметр атмосферной колонны.
Диаметр колонны определяется исходя из максимального объема паров и их допустимые скорости в свободном сечении аппарата.
Определяется объемный расход паров м³с;
где: Т – температура верха колонны К;
Р – давление верха колонны МПа;
Mi – средняя молекулярная масса компонентов в паровой фазе.
М фр.85-180 = М остр.ор. гмоль
Определяется допустимая скорость паров в колонне мс;
- плотность жидкости наверху колонны кгм³. = 7568кгм³;
-плотность паров наверху колонны кгм³.
Gпар = Gфр.85-120 + Gостр.ор. + Gв.п (2.29)
Gпар = 18 + 38 + 01122= 58122
Сmax = K1K2C1 – К3( – 35) (2.30)
Коэффициент К1=105 для клапанных тарелок
Коэффициент К2=095 для атмосферных колонн
Значение коэффициента С1 определяется по графику в зависимости от принятого расстояния между тарелками (приложение 4 [1]).
Коэффициент К3 = 40 для всех кроме струйных тарелок
Коэффициент находим из следующего выражения:
где LЖ – нагрузка тарелки по жидкости м3ч;
n – число потоков жидкости на тарелке.
Примем к установке тарелки клапанные прямоточные расстояние между тарелками 600 мм число потоков по жидкости на тарелке равным двум. Тогда К1 = 105 (для клапанных тарелок) C1 = 765 K2 = 095 (для атмосферных колонн при расстоянии между тарелками более 350 мм) К3 = 40 (для любых тарелок кроме струйных).
Определяется диаметр колонны м;
Принимается диаметр согласно ГОСТ равный 18м
Высота атмосферной колонны рассчитывается по уравнению:
НК= Н1+Нк+Ни+Нп+Н2+Нн+Но (2.33)
где: Н1 - высота от верхнего днища до верхней тарелки м; Нк – высота концентрационной тарельчатой части колонны м; Ни – высота отгонной исчерпывающей тарельчатой части колонны м; Нп – высота секции питания м; Н2 – высота от уровня жидкости в кубе колонны до нижней тарелки м; Нн – высота низа колонны от уровня жидкости до нижнего днища м; Н0 – высота опоры м.
Высота Н1 (сепарационное пространство) принимается равной 05 диаметра колонны если днище полукруглое и 025 диаметра если днище эллиптическое. Полушаровые днища применяют для колонн диаметром более 4 метров. Поэтому:
Н1 = 025·18=045м (2.34)
Высота Нк зависит от числа тарелок и расстояния между ними:
Нк = (36 – 1)h = 35·06 = 21м (2.35)
где h=06 м – расстояние между тарелками.
Высота Ни=0 так как подача сырья осуществляется в низ колонны;
Высота секции питания Нп берется из расчета расстояния между тремя-четырьмя тарелками:
Высота Н2 принимается равной от 1 до 2 м чтобы разместить глухую тарелку и иметь равномерное распределение по сечению колонны паров. Примем Н2 = 106 м.
Высота низа (куба) колонны Нн рассчитывается исходя из 5-10 минутного запаса мазута необходимого для нормальной работы насоса в случае прекращения подачи сырья в колонну:
Относительная плотность мазута при температуре низа колонны 330оС:
- площадь поперечного сечения колонны м2
Штуцер отбора нижнего продукта должен находиться на отметке не ниже 4-5м от земли для того чтобы обеспечить нормальную работу горячего насоса. Поэтому высота опоры Но конструируется с учетом обеспечения необходимого подпора жидкости и принимается высотой не менее 4-5м. Примем Но = 40м.
Полная высота колонны:
Нк = 045+21+12+106+031+40=2802м.
Материал для корпуса ректификационной колонны выбирается из условий технических требований из ряда материалов по ГОСТ 5949-75: 09Г2С.
Характеристика материала. Сталь 09Г2С.
Сталь 09Г2С по ГОСТ: сплав содержащий 009% углерода 2% марганца и кремний количество которого не превышает 1%.
Основное предназначение этой стали – использование ее для сварных конструкций. Сварка возможна как при подогреве до 100-120°С с последующей термической обработкой так и без подогрева и обработки. Хорошая свариваемость стали обеспечивается благодаря низкому (меньше 025%) содержанию углерода.
Широкое распространение и популярность стали 09г2с объясняется тем что ее высокие механические свойства позволяют экономить приизготовлении строительных конструкций. Более того такие конструкции имеют меньший вес. Области применения этой марки стали весьма разнообразны. Из нее изготавливаются элементы и детали сварных металлических конструкций которые могут работать при температурах от -70 °С до +450°С. Используется 09г2с лист и для производства листовых конструкций в нефтяной и химической промышленности судостроении и машиностроении. После закалки и отпуска из этого сплава можно изготавливать детали трубопроводной арматуры. Устойчивость к низким температурам позволяет применять трубу 09Г2С в условиях крайнего севера для прокладки нефте – и газопроводов. [3]
Таблица 3.1 – Химический состав в % материала 09Г2С
2 Расчет цилиндрической обечайки на прочность и устойчивость
Цилиндрическая обечайка - цилиндрическое кольцо либо короткая труба которые преимущественно получают вальцовкой при толщине листа до 40 мм гибкой и раскаткой - при большей толщине листа. Для изготовления (чаще всего с использованием сварки) длинномерных труб котлов резервуаров баков и других листовых металлоконструкций. [1]
Рисунок 3.1 – Цилиндрическая обечайка
Нормативное допускаемое напряжение
Допустимое напряжение при гидравлических испытаниях МПа определяем по формуле:
где - предел текучести материала при 20°С таблица II [4].
Расчетную толщину стенки цилиндрической обечайки Sр м определяем по формуле:
где - расчетное давление
- давление испытания;
- коэффициент прочности сварного шва - ручная дуговая электросварка таблица 1.7[4].
Определяется расчетное давление :
Для аппаратов работающих при давлении не выше 02 МПа расчетное давление следует принимать равным 02 МПа. Для аппаратов с большим давлением принимать =+03.
Определяется давление испытания :
Исполнительную толщину стенки S мм определяем по формуле:
где: с – прибавка к материалу с = 38 мм.
По стандартному ряду исполнительную толщину стенки принимаем равной: S=0012 м.
Допускаемое давление в рабочем состоянии и при испытаниях:
По условию прочности:
Давление рабочее и испытания меньше допускаемого давления рабочего и при испытаниях что удовлетворяет условию [4].
Проверка обечайки по условию устойчивости
Допускаемое осевое сжимающее усилие рассчитывается по формуле:
Допускаемое осевое сжимающее усилие из условия устойчивости в пределах упругости:
Допускаемое осевое сжимающее усилие из условия прочности и из условия устойчивости в пределах упругостиМПа рассчитывается [4]:
где: - максимальный вес аппарата с жидкостью в пересчете на Ньютоны;
Масса корпуса без учета массы оборудования
С учетом всего оборудования аппарата необходимо принять общую массу аппарата массу аппарата принимаем:.
Максимальная масса жидкости в аппарате :
где: H-высота жидкости в аппарате так как в колонне жидкость занимает не весь объем принимаем высоту жидкости H=20 м.;
- плотность жидкости в аппарате.
Расчет изгибающего и допускаемого изгибающего момента
где -радиально действующая сила (сила ветра); -высота колонны.
где: -скорость ветра принимается равной 18 мc (штормовой ветер)
где: S- площадь давления ветра
Тогда изгибающий момент равен:
Допускаемый изгибающий момент из условия прочности:
Допускаемый изгибающий момент из условия устойчивости в пределах упругости:
Допускаемый изгибающий момент из условия прочности и из условия устойчивости в пределах упругости рассчитывается [4]:
Для данной цилиндрической обечайки с такими нагрузками условие устойчивости примет вид:
Условие устойчивости выполняется. [4]
3 Расчет эллиптического днища на прочность и устойчивость
Рисунок 3.2 – Эллиптическое днище
Расчетную толщину стенки м рассчитываем по формуле:
Принимаем конструктивно S равным 0012 м [4].
Допускаемое давление при испытаниях:
Давление рабочее и при испытаниях меньше допускаемого давления в рабочем состоянии и при испытаниях что удовлетворяет условию.
4 Расчет фланцевого соединения
Фланцевые соединения – наиболее широко применяемый вид разъемных соединений в химическом машиностроении обеспечивающий герметичность и прочность конструкций а также простоту изготовления разборки и сборки. Соединение состоит из двух фланцев болтов и прокладки которая устанавливается между уплотнительными поверхностями и позволяет обеспечить герметичность при относительно небольшом усилии затяжки болтов.
- фланцы 2- болт 3- прокладка
Рисунок 3.3 – Фланцевое соединение
Конструктивные размеры фланца:
Так как колонна цельносварная считается наибольшее фланцевое соединение то есть для люка-лаза при следующих значениях: D=05 м и Р=1 МПа и максимальной температуре t=350. Выбираем фланец приварной встык тип уплотнительной поверхности фланцевого соединения - шип-паз [4].
Толщина втулки фланца для конструкции приварной встык принимается исходя из условия:
Толщина S1 у основания втулки приварного встык фланца:
где: - коэффициент принимается по рисунку1.39 [4] и равно
Высота втулки фланца:
где: i уклон втулки ( ).
Высота втулки фланца принимаем м.
Диаметр болтовой окружности фланцев:
где: u – нормативный зазор между гайкой и втулкой (u = 4-6 мм) принимаем u = 4мм [4].
- наружный диаметр болта выбираем по таблице 1.40 [4].
Наружный диаметр фланца:
где: - конструктивная добавка для размещения гаек по диаметру фланца принимаем по таблице 1.41 [4].
Наружный диаметр прокладки:
где: е – нормативный параметр зависящий от типа прокладки и принимаемый по таблице 1.41[4].
Средний диаметр прокладки:
где: - ширина прокладки принимаемая по таблице 1.42 [4].
Количество болтов необходимое для обеспечения герметичности соединения:
где: - рекомендуемый шаг расположения болтов выбираемый в зависимости от давления по таблице 1.43 [4].
Количество болтов необходимое для обеспечения герметичности соединения принимаем шт.
Высота (толщина) фланца ориентировочно:
где: =031- принимается согласно рисунку 1.40[4];
- эквивалентная толщина втулки;
Расчетная длина болтов:
где: - расстояние между опорными поверхностями головки болта и гайки (определяется конструктивно);
где: и - толщина фланца и прокладки соответственно [4].
Болтовая нагрузка необходимая для обеспечения герметичности соединения определяется исходя из схемы нагружения рисунок 1.41[4]. Расчет сводится к определению нагрузок для двух различных состояний: при монтаже - и в рабочих условиях - .
Болтовая нагрузка в условиях монтажа:
где - равнодействующая внутреннего давления;
Равнодействующая внутреннего давления:
где - коэффициент зависящий от материала и конструкции прокладки (таблица 1.44.)[4] (таблица 1.44)[4];
- эффективная ширина прокладки.
Коэффициент жесткости фланцевого соединения:
где - линейная податливость болтов;
- угловая податливость фланца;
- линейная податливость прокладки.
Линейная податливость болтов:
где - модуль упругости материала болтов;
- расчетная площадь поперечного сечения болта.
Угловая податливость фланца:
где - безразмерные параметры; и - коэффициенты; Е – модуль упругости материала фланца.
Линейная податливость прокладки:
где - коэффициент обжатия прокладки; - толщина прокладки;
=2000 МПа - модуль упругости материала прокладки таблица 1.44 [4].
Болтовая нагрузка в рабочих условиях
Приведенный изгибающий момент:
Принимаем мах приведенный изгибающий момент
Условие прочности болтов:
Условие прочности болтов при монтаже фланцевого соединения и его рабочем состоянии выполняется [4].
Проверка прокладки на прочность:
где=35 МПа- допускаемое давление на прокладку таблица 1.44 [4].
Условие прочности прокладки выполняется [4].
Максимальное напряжение в сечении ограниченном размером S1:
где: - безразмерный параметр определяемый по формуле:
Максимальное напряжение в кольце фланца:
Условие прочности втулки фланца для сечения ограниченного размером So рисунок 1.37:
где: и - соответственно тангенциальное и меридиональное напряжение во втулке фланца от внутреннего давления;
- допускаемое напряжение для фланца в сечении So
Отсюда условие прочности втулки фланца для сечения ограниченного размером So будет равно:
Условие прочности втулки фланца для сечения ограниченного размером Soвыполняется [4].
Условие герметичности фланцевого соединения определяется углом поворота фланца:
Условие герметичности фланцевого соединения выполняется.
5Расчет на прочность укрепления отверстий
Расчет укрепления отверстия люк-лаза диаметром d=500мм.
Расчетный диаметр отверстия не требующего укрепления при наличии избыточной толщины стенки:
Так как расчетный диаметр одиночного отверстия не удовлетворяет условию а точнее то требуется укрепление отверстия [4].
Расчетный диаметр отверстия в стенке обечайки перехода или днища при наличии штуцера с круглым поперечным сечением ось которого совпадает с нормалью к поверхности в центре отверстия или кругового отверстия без штуцера определяют по формуле:
Расчетные толщины стенок.
Расчетные толщины стенок укрепляемых элементов определяют в соответствии с ГОСТ 14249.
Расчетная толщина стенки штуцера нагруженного наружным давлением
Расчетные длины штуцеров
Расчетные длины внешней и внутренней частей круглого штуцера участвующие в укреплении отверстий и учитываемые при расчете определяют по формуле:
Ширина зоны укрепления в обечайках переходах и днищах
Расчетная ширина накладного кольца
Отношения допускаемых напряжений:
для накладного кольца
Расчетный диаметр отверстия
Условие укрепления одиночных отверстий накладным кольцом
Рекомендуемым вариантом укрепления является укрепление с использованием накладного кольца.
6 Расчет опор аппарата
Установка аппарата на фундамент осуществляется преимущественно с помощью опор. Непосредственно на фундаменты устанавливаются лишь аппараты с плоским днищем предназначенные главным образом для работы под налив.
Так как нам дан вертикальный аппарат с эллиптическим днищем мы рассчитаем для него конкретную опору с наружными стойками под болты [4].
Рисунок 3.5– Опора для цилиндрического аппарата с эллиптическим днищем
Объем аппарата с эллиптическими крышкой и днищем рассчитаем по формуле:
Масса корпуса аппарата для аппарата с эллиптическими крышкой и днищем рассчитаем по формуле:
где - комплекс[6] рассчитываемый по формуле
Проверим обечайку на прочность от напряжения сжатия:
Обечайка прошла проверку напрочность от напряжения сжатия и удовлетворяет условию [4].
Проверим устойчивость формы цилиндрической опоры аппарата по формуле:
Форма цилиндрической опоры аппарата прошла проверку и удовлетворяет условиям устойчивости[4].
Проверяем прочность сварного шва соединяющего опорную обечайку с корпусом аппарата:
Прочность сварного шва обеспечивающего соединение опорной обечайки с корпусом аппарата обеспечивается.
Рассчитаем размеры нижнего опорного кольца:
- внутренний диаметр:
Диаметр болтовой окружности рассчитаем по формуле:
Опорную площадь кольца рассчитаем по формуле:
Момент сопротивления опорной площади кольца равен:
Проверим прочность фундамента под опорным кольцом:
где для бетона марки 200 (таблица 1.8)[6].
Фундамент отвечает условиям прочности[4].
С целью расчета диаметра фундаментальных болтов проверим устойчивость аппарата от опрокидывания для чего найдем минимальное напряжение под опорным кольцом по формуле:
где - вес аппарата без учета оборудования в пересчете на Ньютоны.
где - масса аппарата без учета оборудования.
Так как 1 установка фундаментальных болтов не обязательна но в целях обеспечения большей устойчивости и безопасности исходя из принимаем 16 болтов М36.
Расчетная толщина опорного кольца для опорного узла определяется приближенно по формуле:
где - расстояние от выступающей части кольца до внутреннего диаметра цилиндрической опоры
Расчетную толщину опорного кольца принимаем [4].
Монтаж и ремонт ректификационной колонны
Ректификационные аппараты представляют наибольшую сложность при перевозке и при установке в проектное положение. Они изготавливаются на машиностроительных заводах. Доставляются до места монтажа в горизонтальном положении. Ниже написана последовательность работ по монтажу колонны.
Подготовительные работы:
Освидетельствовать фундамент с анкерами и сдать по акту согласно СН 471-75 «Инструкция по креплению технологического оборудования
фундаментными болтами» под монтаж колонны.
Доставить аппарат и разгрузить на площадке складирования уложив на ложементы. Освидетельствовать колонну на соответствие паспорту и сборочному чертежу.
Для монтажа ректификационной колонны применим самоходный стреловой кран на гусеничном ходу СКГ-4063 с характеристиками:
- Макс. грузоподъемность - 40÷63 тонн
- Макс. высота подъема – 53 м
- Макс. вылет – 276 м.
Порядок монтажа аппарата:
Установить кран СКГ-4063 согласно стройгенплану.
Застропить аппарат на крюки крана согласно схеме строповки в горизонтальном положении.
Работой крана переместить аппарат в вертикальное положение .
Работой крана смонтировать аппарат в проектное положение.
Произвести выверку на вертикальность с исполнительной съемкой и составлением акта на монтаж. Выверку выполнять теодолитами и приспособлениями для выверки (ОСТ 36-18-77).
После выверки на вертикальность закрепить аппарат на фундаменте анкерными болтами расстропить аппарат. Расстроповку выполнять с этажерками М-5.
Выполнить обвязку технологических трубопроводов. Выполнить испытание аппарата с составлением акта.
Монтажной организации совместно с заказчиком представить производственную документацию согласно перечню. [11]
Схема монтажа аппарата представлена на рисунке 4.1.
Требования к качеству монтажа:
Монтаж аппарата проводить согласно «Инструкции по монтажу сосудов и аппаратов колонного и башенного типов ВСН-351-88».
Выверку вертикальности аппарата производить по контрольным
рискам и приспособлениям для выверки по ОСТ 36-18-77 «Приспособления для выверки аппаратов колонного и башенного типов». Допускаемое отклонение от вертикали образующей аппаратом должно быть в пределах 01 % высоты аппарата но не более 15 мм.
Рисунок 4.1 – Схема монтажа ректификационной колонны
Установка реперов на аппарате:
Расположить аппарат на горизонтальной площадке.
Нанести 2 взаимно перпендикулярные оси по аппарату.
По осям расположить репера с привязкой согласно схеме расположения реперов на аппарате. [11]
Монтаж тарелок аппарата осуществляется после окончательной выверки и закрепления аппарата фундаментными болтами установки обслуживающих площадок и лестниц гидравлического испытания. Загрузка секций тарелок в аппарат осуществляется через люки.
2 Расчет монтажных штуцеров
Рассчитать монтажные штуцера для подъема аппарата колонного типа массой кг
Находим усилие действующее на каждый монтажный штуцер при полностью поднятом над землей аппаратомN Н по формуле [11]:
Определяем величину момента М Нм действующего на штуцер по формуле принимая l=02 м
Подсчитываем минимальный момент сопротивления поперечного сечения стального патрубка для штуцера W м3 по формуле:
где: m- масса стального патрубка m=085 кг [11];
- расчетное изгибающее усилие = 210106 МПа [11]
По приложению Г [12] для стальных труб определяем сечение патрубка для штуцера размером 11414 мм с моментом сопротивления W=125510-6 м3.
Проверяем на прочность сварной шов крепления штуцера к корпусу аппарата по формуле
Расчетная длина шва lш м
где D – диаметр штуцера м.
Полученное неравенство свидетельствует о том что сварной шов удовлетворяет условиям прочности.
3 Расчет траверс работающих на изгиб
Подобрать сечение балки траверсы работающей на изгиб для подъема колонны массой кг
Нагрузка действующая на траверсу Р Н согласно формулы
Максимальный изгибающий момент в траверсеМmaxН·м по формуле
Требуемый момент сопротивления поперечного сечения балки траверсыWтрм3 определяется согласно условию формулы
Выбираем конструкцию балки траверсы сквозного сечения состоящую из двух двутавров соединенных стальными пластинами.
Подобрав по приложению З [12] две двутавровые балки № 10 с
Wдx=50710-6м3 определяем момент сопротивления сечения траверсы в целом:
что удовлетворяет условию прочности расчетного сечения траверсы.
Рассчитать стальной канат для стропа применяемого при подъеме вертикальной цилиндрической колонны массой кг.
Количество ветвей стропа n=4 угол наклона ветвей стропа к вертикали α=300.
Напряжение возникающее в одной ветви стропаS Н
Разрывное усилие в ветви стропаR Н по формуле 2.1
По найденному разрывному усилию по ГОСТ 3079-80 (приложение В) [12] выбираем канат со следующими данными:
тип каната ЛК-О 6×36+1о.с.
разрывное усилие 262500 Н
временное сопротивление разрыву 1470 Нмм2
диаметр каната .25 мм
Исходя из расчета выбираем стропы 4 СК-50 8000 ГОСТ 25573-82. [12]
Основным видом износа колонной массообменной аппаратуры является забивка отложениями и коррозия ее элементов. При ремонте аппарат не демонтируется. Демонтируются только его внутренние устройства. После подготовительных операций (пропарка промывка) открываются люки аппарата.
Люки нужно открывать в строгой последовательности начиная с верхнего когда аппарат находится под паром для предотвращения тока воздуха через аппарат при одновременном открытии нижнего и верхнего люков.
После пропаривания аппарат промывается водой и проветривается. Проветривание необходимо для охлаждения аппарата и доведения концентрации продуктов в ней до допустимых санитарных норм. После окончания проветривания необходимо провести анализ проб воздуха взятых из колонны на разных высотных отметках. К работам внутри аппарата разрешается приступать только тогда когда анализ покажет что концентрация вредных газов и паров в ней не превышает предельно допустимых санитарных норм.
Тарелки разбираются внутри колонны выносятся через люки на обслуживающие площадки и транспортируются для чистки и ремонта.
Монтаж и демонтаж секций тарелок расположенных внутри аппарата осуществляется при помощи блоков и полиспастов. При ремонте аппарата основное внимание уделяется очистке внутренних устройств аппарата и его корпуса.
Для безопасного и эффективного технического осмотра и ремонта аппаратов применяется специальная подвесная платформа элементы которой вводятся в аппарат через люк и собираются внутри аппарата. Платформа поднимаемая тросом позволяет выполнять осмотр и чистку внутренней поверхности аппарата осмотр сварных швов ремонт внутренней поверхности аппарата.
Ремонт корпуса аппарата должен осуществляться ремонтными подразделениями завода или другими специализированными ремонтными организациями располагающими специальными техническими средствами и работниками обеспечивающими качественное выполнение работ. К производству сварочных работ включая прихватку и приварку временных креплений допускаются сварщики аттестованные в соответствии с действующими “Правилами аттестации сварщиков” и имеющими удостоверение установленной формы. На каждый ремонт корпуса сосуда или аппарата составляется ремонтная документация которая хранится с паспортом сосуда или аппарата. Ремонтная документация определяет технологию ремонта и лиц ответственных за производство и качество выполняемых работ.
Для ремонта корпуса аппарата применяют материал указанный в паспорте на аппарат. При отсутствии материала указанного в паспорте может быть выбран другой материал в ОСТ 26-291-87. Используемый при ремонте материал должен иметь сертификат подтверждающий его качество. При выборе материалов для ремонта корпуса аппарата должны учитываться: расчётное давление температура стенки корпуса химический состав и характер среды технологические свойства коррозионная стойкость материалов. Материал элементов привариваемых непосредственно к корпусу изнутри и снаружи должны обладать хорошей свариваемостью с материалом корпуса и иметь с ним близкие значения коэффициента линейного расширения. При этом разница в значениях коэффициентов линейного расширения не должна превышать 10 %.
Сварочные материалы применяемые для изготовления и ремонта корпусов аппаратов (деталей сборочных единиц) должны удовлетворять требованиям стандартов или технических условий на них и иметь сертификат. Перед применением каждую партию электродов проверяют на технологичность в соответствии с ГОСТ 9466-75.
Характерными дефектами корпуса аппарата появляющихся в процессе эксплуатации являются:
Трещины всех видов и направлений в сварных швах около шовной зоне и в основном металле.
Коррозионное повреждение сварных швов и основного металла в виде сплошной равномерной или не равномерной коррозии локальной коррозии (язвы питтинги и т.п.).
Гофры вмятины выпучены и другие виды деформации корпуса.
Для определения величины границ дефектов участков применяются следующие методы: визуально-оптический ультразвуковой радиографический цветная дефектоскопия магнитопорошковый и магнитографический.
Выбор способов исправления дефектных участков корпуса аппарата производится с учетом:
конструкции корпуса;
материального исполнения корпуса;
экономической целесообразности выбранного способа исправления.
Ремонт корпуса аппарата производится тремя способами:
заварка дефекта или наплавка дефектного участка;
замена дефектного участка;
Демонтаж корпуса аппарата проводится при необходимости замены
части корпуса. Наиболее часто вследствие коррозии выходит из строя днище. Замена днища – ответственная операция требующая выполнения необходимых расчетов разработки технической документации соблюдения дополнительных мер безопасности.
Ремонт аппарата заканчивается его испытанием. Колонну подвергают гидравлическому испытанию в соответствии с требованиями паспорта аппарата. Гидравлическое испытание допускается проводить водой или другими не коррозионными не ядовитыми не взрывоопасными не вязкими жидкостями. При гидроиспытании перед поднятием давления необходимо убедится в отсутствии воздуха в аппарате. Для этого при наполнении сосуда водой следует держать воздушник открытым. Давление в сосуде должно измеряться контрольным манометром. Увеличение и уменьшение давления должно быть плавным. Гидравлическое испытание аппарата может производиться в горизонтальном положении лишь в том случае когда расчётом на прочность будет установлено что при пробном давлении принятом с учётом гидростатического давления рабочей среды напряжения во всех элементах сосудов не будут превышать 90 % предела текучести для данной марки стали.
Под пробным давлением сосуд должен находиться в течение 5 минут затем давление постепенно снижают до рабочего при котором производится осмотр сосуда обращая особое внимание на сварные швы и вальцовочные соединения. Если есть признаки пропуска воды через наружную изоляцию необходимо полностью или частично удалить воду и провести дополнительный ремонт.
Сосуд считается выдержавшим гидравлическое испытание если не обнаружено признаков разрыва течи следок и потерь в сварных швах и на основном металле видимых остаточных деформации.
В данном курсовом проекте приведен расчет ректификационной колонны. Проведенный расчет включает в себя технологическую часть где был посчитан материальный и тепловой балансы а также определены основные габаритные размеры и конструктивную часть где были определены такие конструктивные данные как: расчетные и исполнительные толщины элементов аппарата размеры фланцевых соединений укрепление отверстий а также был выполнен подбор и расчет опор аппарата. Были проведены необходимые расчеты проверки на устойчивость и прочность.
Курсовой проект состоит из: пояснительной записки и графической части. Записка включает в себя 74 листа машинописного текста формата А4. Графическая часть проекта состоит из: 4 листов формата А1 1 листа формата и 4 листа спецификации формата А4.
Согласно заданию и с учетом методических указаний спроектирован аппарат для ректификации.
Беляев В. М. Миронов В. М. Конструирование и расчет элементов
оборудования отрасли. Ч. I: Тонкостенные сосуды и аппараты
химических производств: Учеб. пособие Том. политех. ун-т. – Томск
Дытнерский Ю.И. Основные процессы и аппараты химической
технологии Дытнерский Ю.И. -Л.: Химия 1981. -512 с.
Касаткин А.Г. Основные процессы и аппараты химической
технологии.М.: Химия 1973.-752 с.
Михалев М.Ф. Расчет и конструирование машин и аппаратов химических производств. Примеры и задачи. Ленинград 1984. -301 с.
Павлов К.Ф. Примеры и задачи по курсу процессов и аппаратов
химической технологии Павлов К.Ф. Романков П.Г. Носков А.Л. -Л.: Химия 1981. -586 с.
Поникаров И.И. Расчеты машин и аппаратов химических производств и нефтегазопереработки (Примеры и задачи). Москва 2008. -717 с.
Щербаков В.Н. Конструирование и расчет элементов оборудования. Часть 2 – Тонкостенные сосуды и аппараты. Красноярск 2005. -164 с.
Щербаков В.Н. Конструирование и расчет элементов оборудования.
Методические указания к выполнению курсовой работы. Красноярск 2006. -32 с.
Ахметов С. А. и др.. Технология и оборудование процессов перера-ботки нефти и газа: Учебное пособие С. А. Ахметов Т. П. Сериков И. Р. Кузеев М. И. Баязитов; Под ред. С. А. Ахметова. – СПб.: Недра 2006. – 868 с.; ил.
Сарданашвили А.А. Львова А. И примеры и задачи по технологии переработки нефти и газа. – 2-е изд. пер. и доп. - М.: Химия 1980. - 256 с. ил.
Технологический регламент установки переработки нефти УПН-250. Анжерская нефтегазовая компания – 2010. – 23 с.
Монтаж оборудования: Методические указания к практическим занятиям для студентов специальности 03050016 «Профессиональное обучение» Сост.Смирнова Н.Ю. – Красноярск: СибГТУ - 2005. – 87с.
Рекомендуемые чертежи
- 16.12.2023
- 25.01.2023