Проект теплового насоса для отопления и горячего водоснабжения с использованием тепла масла стенда ожижения природного газа и реконденсации метана ОАО Сумское НПО им.Фрунзе




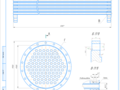
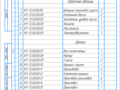
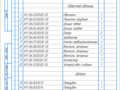
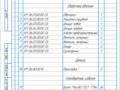
- Добавлен: 24.01.2023
- Размер: 3 MB
- Закачек: 0
Описание
Проект теплового насоса для отопления и горячего водоснабжения с использованием тепла масла стенда ожижения природного газа и реконденсации метана ОАО Сумское НПО им.Фрунзе
Состав проекта
![]() |
![]() ![]() ![]() |
![]() ![]() ![]() ![]() |
![]() ![]() ![]() ![]() |
![]() ![]() ![]() ![]() |
![]() ![]() ![]() ![]() |
![]() ![]() ![]() ![]() |
![]() ![]() ![]() ![]() |
![]() ![]() ![]() ![]() |
![]() ![]() ![]() ![]() |
![]() ![]() ![]() ![]() |
![]() ![]() ![]() |
![]() ![]() ![]() ![]() |
![]() ![]() ![]() ![]() |
![]() ![]() ![]() ![]() |
![]() ![]() ![]() ![]() |
![]() ![]() ![]() ![]() |
![]() ![]() ![]() ![]() |
![]() ![]() ![]() |
![]() ![]() ![]() ![]() |
![]() ![]() ![]() ![]() |
![]() ![]() ![]() ![]() |
![]() ![]() ![]() ![]() |
Дополнительная информация
ПЗ Руся.docx
В период гражданской войны и иностранной интервенции предприятие в основном не работало были разрушены и сожжены все ведущие цехи. К восстановлению при ступили в начале 1922 года на основании решения Харьковского губернского совнархоза. В 1922 году уже были завершены первые восстановительные работы. После завершения восстановительных работ были введены в эксплуатацию заново переоборудованные литейный и механический цехи. В номенклатуре завода появилась более сложная продукция - центробежные насосы лебедки фермы для железнодорожных мостов. Начали выпуск оборудования для электростанций мостовых кранов паровых котлов электрических лебедок для шахт Донбасса.
В 1926 году завод дал продукции на 1655 тыс. рублей в ценах 1913 года что составило 42% всей продукции машиностроения лишь Краматорский завод с показателем 48% опередил наше предприятие.
В 1930 году в стране принята программа развития тяжелой индустрии. На заводе взят курс на техническое совершенствование производства и внедрение новых технологических процессов. В том же году когда на базе ряда старейших заводов страны был заложен фундамент новой отрасли - химического машиностроения предприятие начало специализироваться как завод химического и нефтяного машиностроения. В 1931 году стали в строй новые производственные мощности: насосно-компрессорный цех литейный и инструментальные цехи. Это значительно повысило производственный потенциал завода.
июня 1941 года. Весть о начале войны была страшной но коллектив завода встретил ее с большим мужеством. Сотни трудящихся сразу же добровольцами пошли на фронт А те кто остался изготовляли вооружение боеприпасы. Ежеднев- ные задания выполняли не менее чем на 250 процентов.
В 1948-1950 годах завод внес большой вклад в создание атомной промышленности страны. Учитывая высокое мастерство коллективу поручили ответственное правительственное задание по изготовлению первых аппаратов для ядерной энергетики. Производство опытных изделий возглавил лично главный инженер завода П.Т. Гончаренко.
В 1949 году в г. Сумы было организовано новое предприятие - Сумский насосный завод. Он был создан на базе цеха центрифуг завода имени М.В. Фрунзе. На новое предприятие перешло 330 работников завода имени М.В. Фрунзе – квалифицированных инженеров служащих и рабочих которые и составили основу будущего коллектива насосников. К 1950 году завод уже располагал мощной производственной базой квалифицированным составом ИГР рабочий служащих которым было по плечу решение сложных технических и производственных задач.
50-1965 годы - это период когда неуклонно повышался производственный потенциал завода совершенствовались и перевооружались многие его цехи рождались проекты новых машин и аппаратов. Наряду с развитием химического аппаратостроения на первые рубежи выходит такое сложное и наиболее необходимое в те годы оборудование как тяжелые компрессоры большой производительности и высокого давления. Это требовали создаваемые производства азотных минеральных удобрений пластмасс процессы глубокой переработки нефти и другие. Завод был единственным предприятием в стране способным изготовлять тяжелые компрессорные машины располагая необходимы технологическим оборудованием квалифицированными кадрами и производственным опытом.
65 - 1975 годы в развитии завода можно охарактеризовать как период наиболее интенсивного роста номенклатуры и объемов выпуска химического оборудования и дальнейшего технического оснащения производства.
В эти годы решалась поставленная правительством задача по химизации народного хозяйства страны для чего требовалось резко увеличить темпы развития отрасли химического машиностроения.
В целях более эффективного решения этой задачи концентрации всех конструкторских подразделений для ускорения внедрения достижений науки и техники в производство и на этой основе повышения технического уровня создаваемого нового химического оборудования в 1965 году на заводе на базе его конструкторских служб было создано отдельное специальное конструкторское бюро.
В 1981 году первый насос под руководством начальника управления главного технолога Ю.К-Братушки успешно испытали на стенде Ленинградской АЭС. Подтвердились все технико-экономические и эксплуатационные расчеты. Генеральный конструктор главных циркуляционных насосов Л.А.Аркин по результатам испытаний "благословил" серийный выпуск насосов.
Все последующие ГЦН-195М и насосы II контура проходили приемосдаточные испытания на испытательной станции насосного производства где весь процесс работы насоса был автоматизирован. Они проходили испытания по всем необходимым параметрам вплоть до имитации аварийных ситуаций. Большую работу по организации такой проверки провели квалифицированные специалисты:
начальник испытательной станции С.Г.Обозный. Одновременно с освоением насосов ГЦН-195М организовали производство насосов второго контура АЭС в цехах № 6 и 7 а также некоторых крупных насосов на насосном производстве. В цехе №6 сосредоточили выпуск конденсатных насосов КСВА и сложных центробежных ЦН-50 и ЦН-60.
В период 1986-1990 годов в объединении продолжается рост номенклатуры и объемов выпуска оборудования для топливно-энергетического комплекса страны. Растет число разрабатываемых новых линий установок машин. С первых лет создания объединения был взят курс на увеличение поставок этого важнейшего оборудования что значительно изменило портфель заказов и существенно увеличило номенклатурный перечень изготовляемой продукции. В этих условиях потребовались новые подходы к формированию годовых и перспективных планов производства более оперативной связи с потребителями проведения четкой договорной политики совершенствования механизма межцеховых связей и жесткого контроля сроков исполнения.
Выполнив планы 1991 года объединение вступило в 1992 год. Это был год начала вхождения предприятий Украины в рынок и он был весьма сложным.
В составе управления финансов и сбыта во исполнение директивных документов Президента Украины и Государственного таможенного комитета в декабре 1992 года было создано новое подразделение - отдел декларирования грузов. Основной задачей отдела являлось обеспечение внешнеэкономической деятельности объединения в условиях перехода к рыночным отношениям и в условиях полной независимости Украины. При этом отдел оформлял документацию не только на отгружаемую продукцию но и на импорт. Становление отдела проходило в сложных условиях: отсутствие полноценной законодательной базы в Украине неготовность специалистов к новому типу деятельности большой объем экспортно-импортных операций.
На базе двух управлений: подготовки производства и финансово-сбытового в ноябре 1994 года создали новое подразделение - управление маркетинга и финансов.
В 1991-2007 годах в сложных условиях перехода к рынку благодаря мерам принимаемым по структурной перестройке производства внедрению новых подходов к управлению деятельностью объединения объединение работало относительно стабильно не было случаев остановки производства полностью сохранена социальная сфера которая содержится за счет собственных средств объединения не уменьшилась численность работающих заработная плата выплачивалась ежемесячно нет долгов перед государственным бюджетом. В статусе акционерного общества трудовой коллектив будет стремиться улучшать результаты производственно-хозяйственной деятельности и на этой основе повышать благосостояние работников.
2 Предназначение теплонасосной установки
Тепловой насос осуществляет передачу внутренней энергии от энергоносителя с низкой температурой к энергоносителю с более высокой температурой. Поскольку в соответствии со вторым основным законом термодинамики тепловая энергия без каких-либо внешних воздействий может переходить только с высокого температурного уровня на более низкий для осуществления теплонасосного цикла необходимо использовать приводную энергию. Поэтому процесс передачи энергии в направлении противоположном естественному температурному напору осуществляется в круговом цикле. В качестве примера приведена схема паровой холодильной машины где рабочим веществом служит кипящая при низкой температуре жидкость названная хладагентом так как она уже в течение многих лет применяется в холодильных установках.
Энергоносители поставляющие тепловую энергию с низкой температурой для осуществления теплонасосного цикла называют источниками теплоты. Они отдают тепловую энергию путем теплопередачи конвекции и (или) излучения. Энергоносители воспринимающие в теплонасосном цикле тепловую энергию повышенного потенциала называют приемниками тепла. Они воспринимают тепловую энергию путем теплопередачи конвекции и (или) излучения. Энергоноситель служащий источником теплоты поступает в испаритель где испаряется жидкий хладагент. Теплота испарения необходимая для этого отбирается от источника тепла так как испарение хладагента происходит при низкой температуре.
В круговом цикле пары испарившегося хладагента всасываются компрессором и сжимаются до высокого давления. При сжатии их температура повышается что создает возможность отдачи тепловой энергии теплоприемнику.
Пары хладагента при повышенном давлении поступают в конденсатор через который протекает энергоноситель служащий приемником тепла. Его температура ниже температуры паров хладагента при повышенном давлении. При конденсации пара выделяется тепловая энергия воспринимаемая теплоприемником. Из конденсатора жидкий хладагент через регулирующий вентиль (дроссельный клапан) поступает обратно в испаритель и круговой цикл замыкается. В регулирующем вентиле высокое давление при котором находится хладагент на выходе из конденсатора снижается до давления в испарителе. Одновременно снижается его температура.
Таким образом с помощью теплового насоса возможна передача тепловой энергии от источника теплоты с низкой температурой к приемнику теплоты с высокой температурой при подводе извне механической энергии для привода компрессора (приводной энергии). Схема холодильной машины и теплового насоса отличается только назначением.
К холодильным машинам относится оборудование которое позволяет осуществить отбор тепловой энергии от тел с температурой ниже температуры окружающей среды (т.е. производство холода). Если требуется получить определенное количество теплоты с высокой температурой или одновременно и теплоты и холода такое оборудование относят к тепловым насосам.
Теплопроизводительность (тепловая мощность) теплового насоса складывается из двух составляющих: теплоты полученной испарителем от источника теплоты (так называемой холодопроизводительности Q0) и приводной мощности Р с помощью которой полученная тепловая энергия поднимается на более высокий температурный уровень.
Отсюда можно дать следующее определение тепловым насосам:
«Тепловой насос представляет собой устройство воспринимающее тепловой поток при низкой температуре (на холодной стороне) а также необходимую для привода энергию и использующее оба потока энергии при повышенной (по сравнению с холодной стороной) температуре в виде теплового потока».
Это определение действительно для компрессионных тепловых насосов а также для абсорбционных и термоэлектрических насосов использующих эффект Пельтье.
В абсорбционном тепловом насосе механический компрессор заменен термическим в виде дополнительного циркуляционного контура раствора с генератором (кипятильником) и абсорбером. Вместо электрической приводной энергии подводимой к компрессионным тепловым насосам с электроприводом к генератору подводят тепловую энергию. Однако для обоих процессов используются с помощью испарителя источники энергии в виде отработанной теплоты или энергии окружающей среды.
Обычно в процессе преобразования энергии энергия окружающей среды является конечным этапом процесса. Энергия выделяемая при сжигании твердого топлива или в ядерных реакторах проходит большое число преобразований пока принимает необходимую для потребителя форму полностью используется и наконец практически всегда переходит в энергию окружающей среды.
Тепловые насосы требуют совершенно иного теоретического подхода. Здесь в начале процесса в качестве источника теплоты наряду с приводной энергией используется также и энергия окружающей среды.
В настоящее время отопление и горячее водоснабжение городских объектов осуществляется как правило от централизованных систем теплоснабжения. Источником тепловой энергии в таких системах являются городские ТЭЦ на которых осуществляется комбинированная выработка электроэнергии и тепла или районные котельные. Преимущества централизованного теплоснабжения широко признаны. С термодинамической точки зрения комбинированное производство электроэнергии и тепла на ТЭЦ является гораздо более эффективным чем раздельное производство электроэнергии на конденсационных тепловых электростанциях и тепла котельными.
Вместе с тем применение централизованных систем теплоснабжения имеет свои недостатки и ограничения. Строительство протяженных теплотрасс к удаленным объектам а также к объектам в районах с малой плотностью застройки сопряжено со значительными капитальными вложениями и большими тепловыми потерями на трассе. Их эксплуатация впоследствии также требует больших затрат. Серьезные проблемы возникают и при реконструкции существующих объектов и строительстве новых в обжитых городских районах с плотной застройкой. В этих случаях увеличение тепловых нагрузок создает для застройщика часто непреодолимые трудности в том числе финансовые при получении и реализации технических условий на подключение к районной тепловой сети.
Действующие в настоящее время тарифы на тепловую энергию в сочетании с затратами на подключение к городским тепловым сетям заставляют все чаще задумываться над альтернативными способами теплоснабжения.
Принцип работы ТНУ: в испарителе теплового насоса тепло невысокого температурного потенциала отбирается от некоего источника низкопотенциального тепла и передается низкокипящему рабочему телу теплового насоса. Полученный пар сжимается компрессором. При этом температура пара повышается и тепло на нужном температурном уровне в конденсаторе передается в систему отопления и горячего водоснабжения. Для того чтобы замкнуть цикл совершаемый рабочим телом после конденсатора оно дросселируется до начального давления охлаждаясь до температуры ниже источника низкопотенциального тепла и снова подается в испаритель. Таким образом тепловой насос осуществляет трансформацию тепловой энергии с низкого температурного уровня на более высокий необходимый потребителю. При этом на привод компрессора затрачивается механическая (электрическая) энергия. При наличии источника низкопотенциального тепла с более или менее высокой температурой количество тепла поставляемого
потребителю в несколько раз превышает затраты энергии на привод компрессора. Отношение полезного тепла к работе затрачиваемой на привод компрессора называют коэффициентом преобразования теплового насоса и в наиболее распространенных теплонасосных системах он достигает 3 и более.
В качестве низкопотенциального источника тепла можно использовать грунтовые воды стоки речную и морскую воду низкопотенциальные источники тепла на электростанциях градирнях. Особенно тепловой насос является выгодным при высокой цене на топливо и относительно низкой цене на электроэнергию. Такая ситуация имеет место в многих европейских странах где основная часть электроэнергии вырабатывается на АЭС и ГЭС.
3 Выбор схемы и расчет цикла теплонасосной установки
3.1 Выбор схемы теплонасосной установки
Для теплонасосной установки (ТНУ) целесообразно будет применить цикл холодильной машины с регенеративным теплообменником. В этой схеме пар рабочего вещества выходящий из испарителя (маслоохладителя) в состоянии 7 (рисунок 1.1) направляется в регенеративный теплообменник где он нагревается за счет более теплого рабочего вещества выходящего из конденсатора которое при этом охлаждается. В результате регенерации эффективность установки увеличивается.
Рисунок 1.1 – Схема ТНУ и ее цикл в Ts и pi – диаграммах.
3.2 Исходные данные
Среда потребителя: вода;
Утилизируемая среда : масло И-40;
Параметры среды потребителя :
t1п =550С – температура на входе в ТНУ;
t2п =750С – температура на выходе из ТНУ;
Параметры утилизируемой среды :
t1у = 570C – температура на входе в испаритель (маслоохладитель);
t2у = 500C – температура на выходе из испарителя;
Необходимые значения КПД:
s = 08 – адиабатный КПД.
мех = 097 – механический КПД;
дв = 095 – КПД двигателя;
Определение расчетных температур:
tи = t1у –12 = 57 – 12 = 450C;
tк = t2п + 5 = 75 + 5 = 800С;
t1 = tи + 10 = 45+ 10 = 550С;
t4 = t1п + 10 = 55 + 10 = 650С;
Определение энтальпий:
i2 = (i2s – i1)s + i1 = (478– 454)08 + 454 = 484 кДжкг
Таблица 1.1 – Характеристики в расчетных точках
3.3 Определение удельных параметров цикла
Удельная тепловая нагрузка на конденсатор:
Удельная тепловая нагрузка на переохладитель конденсата:
Удельная тепловая нагрузка на регенеративный теплообменник:
Удельная тепловая нагрузка на испаритель:
Удельная адиабатная работа компрессора:
Удельная работа компрессора:
3.4 Определение режимных параметров ТНУ
Массовый расход хладагента:
Тепловая нагрузка на конденсатор:
Qкд = ma qкд = 036 179 = 64.44 кВт;
Тепловая нагрузка на переохладитель конденсата:
Qпк = ma qпк = 036 21 = 7.56 кВт;
Теплопроизводительность:
QТ = Qкд +Q пк = 64.44+7.56=72 кВт;
Тепловая нагрузка на регенеративный теплообменник:
Qрт = ma qрт = 036 10 = 3.6 кВт;
Адиабатная мощность компрессора:
Мощность компрессора:
Мощность подведенная к компрессору:
Потребляемая мощность:
Nпр = Ne дв =11.13 095 = 1172 кВт.
Коэффициент преобразования ТН:
φ = QтNпр = 721172= 614
Массовый расход потребителя через ТН:
4 Расчет теплопритоков отапливаемого помещения.
4.1 Расчет толщины изоляции
Задаемся следующими размерами помещения 60х24х6 м. Следовательно:
– площадь помещения1440 м2
– объем помещения 8640 м3
Расчет толщины изоляции наружной стены цеха с северной стороны:
Рисунок 1.2 – Конструкция стены
Действительный коэффициент теплоотдачи:
Для каждого материала выбираем соответствующие коэффициенты теплопроводности и толщины:
Для внутренних поверхностей стен отапливаемых помещений
Для наружных поверхностей стен
4.2 Расчет коэффициента теплоотдачи окон цеха
Рисунок 1.3 – Конструкция окна
Для внутренней поверхности окон
Для наружной поверхности окон
Действительный коэффициент теплоотдачи:
4.3 Расчет коэффициента теплоотдачи дверей цеха
Для материала (сталь) соответствующий коэффициент теплопроводности и толщины:
Для внутренней поверхности двери
Для наружной поверхности двери
4.4 Расчет изоляции для покрытия цеха
Рисунок 1.4 – Конструкция покрытия
Для внутренних поверхностей потолка
Для наружных поверхностей бесчердачных покрытий
4.5 Расчет толщины изоляции для пола:
Рисунок 1.5 – Конструкция пола
Для поверхностей пола
4.6 Расчет теплопритоков через ограждение
Теплоприток через ограждения можно найти по формуле:
где Q1T – теплоприток обусловленный разностью температур в помещении и снаружи
Q1С – теплоприток обусловленный наличием солнечной радиации.
Найдем для каждой стены пола и покрытия эти составляющие теплопритока через ограждение:
Теплоприток от разности температур:
Суммарный теплоприток от разности температур:
Теплоприток от солнечной радиации:
где – условная разность температур:
Суммарный теплоприток от солнечной радиации:
Суммарный теплоприток через ограждение:
4.7 Расчет вентиляционного теплопритока
Вентиляционный теплоприток можно найти по формуле
Принимаем число рабочих в помещении 25 человек.
Вентиляционный теплоприток в помещении:
4.8 Расчет эксплуатационных теплопритоков
Теплоприток эксплуатационный можно найти по такой формуле:
Теплоприток от освещения:
где А – количество тепла выделяемого на 1 м2 пола (для производственных помещений 45 Втм2);
F – площадь помещения м2
Теплоприток от работающих людей:
где – тепловыделение от 1 человека (при тяжелой физической работе 350 Вт);
– число людей работающих в данном помещении.
Теплоприток от оборудования принимаем Вт
Теплоприток от открывания дверей:
где – удельный приток тепла от открывания дверей Втм2;
– площадь пола помещения м2.
Суммарный эксплуатационный теплоприток:
4.9 Суммарные теплопритоки
Тепловая нагрузка на оборудование:
Тепловая нагрузка на компрессор:
5 Расчет компрессора теплонасосной установки
5 1. Описание проектируемого компрессора
Проектируемый компрессор – холодильный поршневой одноступенчатый непрямоточный двухцилиндровый вертикальный с блок-картерным исполнением простого действия безкрейцкопфный со встроенным электродвигателем бессальниковый со свободно-принудительной системой смазки (смазка от насоса и разбрызгиванием) стационарный со среднетемпературным режимом работы фреоновый средней холодопроизводительности.
Смазка механизма движения осуществляется как с помощью разбрызгивания так и с помощью шестеренчатого маслонасоса.
Норма расхода смазки для цилиндров составляет . Применяются масла типа ХФ-22-18.
В компрессоре применяются тронковые алюминиевые поршни клапаны на всасывании и нагнетании приняты согласно расчетам – полосовые.
Охлаждение цилиндров – парами холодильного агента (R22). Пар через всасывающий патрубок проходит через электродвигатель охлаждая его гильзу и затем идет на всасывание. Место посадки уплотнено специальными паранитовыми прокладками.
Ротор электродвигателя выполняет роль маховика. Маховик в свою очередь является аккумулятором энергии поршневого компрессора позволяющим преодолеть инерцию механизма движения в мертвых точках.
Маслонасос шестеренчатый встроенного типа. Масло после маслонасоса подается на смазку в пары трения через сверление в валу и шатуне. При этом перед попаданием в маслонасос оно проходит фильтр грубой очистки.
Подшипниковые опоры – шариковые двухрядные.
5.2 Термодинамический расчет холодильного компрессора
Холодильный агентR142
Охлаждение цилиндровпарами холодильного агента
Исполнениебессальниковый
Холодопроизводительность
Для рабочего цикла определяем отношение давлений:
Определяем удельную массовую холодопроизводительность:
Определяем удельную объемную холодопроизводительность:
Определяем коэффициент подачи компрессора на рабочем режиме:
Задаемся величиной тогда
где – компрессия на нагнетании
Коэффициент дросселирования:
где – компрессия на всасывании.
Коэффициент подогрева:
Находим действительную объемную производительность компрессора:
Находим теоретическую объемную производительность компрессора:
Для рабочего цикла определяем мощность электродвигателя в следующем порядке:
Для безкрейцкопфных фреоновых поршневых компрессоров индикаторный КПД принимается в пределах 071 084.
Адиабатную мощность компрессора определяем по формуле:
5.3 Определение геометрических размеров
Принимаем вертикальную двухрядную схему компрессора.
Для непрямоточных машин примем величину . Значение средней скорости поршня для безкрейцкопфных поршневых компрессоров должна лежать в пределах от 25 до 45 мс. Ход поршня принимаем и частоту вращения коленвала тогда
Определяем диаметр поршня ступени:
Принимаем D =110 мм.
Приближенно диаметр шейки коленвала изготовленного из стали 40Х можно определить по формуле:
Крутящий момент можно найти по формуле:
Для стали 40Х вид термообработки улучшение допустимое касательное напряжение составляет
Отсюда можно найти касательное напряжение при кручении:
где k – коэффициент запаса прочности (k = 2 3)
Подставим эти значения в выражение для диаметра коренной шейки :
Диаметр шейки коленвала:
Относительная длина шатуна:
Масса поступательно движущихся частей определяем по найденному значению пользуясь графиком [1] риc. 31.
5.4 Газодинамический расчет компрессора
5.4.1. Расчет полосового клапана
Скорость холодильного агента в клапанах:
где – средняя скорость поршня.
Допустимая скорость хладагента в седле и розетке клапанов: всасывающего принимаем ; нагнетательного принимаем .
Скорость звука в клапанах:
При проектировании клапанов должно выдерживаться условие:
Условие выполняется.
Эквивалентная площадь клапана
где – коэффициент расхода щели;
– коэффициент сопротивления щели полосового клапана.
Площадь проходного сечения щели:
Принимаем ширину щели .
Требуема длина щели:
Принимаем 6 щелей по
5.4.2 Расчет нагнетательного патрубка
Скорость холодильного агента в нагнетательном патрубке:
Принимаем для нагнетательного патрубка ([1] табл. 5.2).
Диаметр нагнетательного патрубка:
3. Расчет всасывающего патрубка
Скорость холодильного агента во всасывающем патрубке:
Принимаем для всасывающего патрубка .
Диаметр всасывающего патрубка:
5.4.4 Выбор электродвигателя
Мощность электродвигателя:
Выбираем электродвигатель асинхронный серии 4А закрытый обдуваемый (ГОСТ 19523-81).
Мощность электродвигателя типоразмер 4А225М4У3
Технические характеристики:
Холодильный коэффициент поршневого компрессора равен:
5.5 Динамический расчет компрессора
Динамический расчет компрессора ведем с помощью программного обеспечения TURBO PASCAL 7.0:
p1 кПа p2 кПа am D м S м nO обмин
lambdaR n m ms кг Nинд кВт ETAмех
(все силы в кH углы в градусах )
модуль Fтр.пс = 0.288 Fтр.вр = 0.192 Pr.2= 5.702
альфа= 0.0 x=0.0000 Pg1= -13.304
J= 1.812 Pсум= -5.502 N= 0.000
дельта= 0.0 Pшат= -5.502 T= 0.000 Z= -5.502
альфа= 21.9 x=0.0035 Pg1= -5.702
J= 1.620 Pсум= 1.908 N= 0.142
дельта=26.1 Pшат= 1.903 T= 0.837 Z= 1.708
альфа= 20.0 x=0.0030 Pg1= -6.303
J= 1.651 Pсум= 1.338 N= 0.091
дельта=23.9 Pшат= 1.335 T= 0.541 Z= 1.220
альфа= 40.0 x=0.0113 Pg1= -5.702
J= 1.209 Pсум= 1.497 N= 0.191
дельта=47.3 Pшат= 1.485 T= 1.091 Z= 1.008
альфа= 60.0 x=0.0236 Pg1= -5.702
J= 0.604 Pсум= 0.892 N= 0.152
дельта=69.7 Pшат= 0.879 T= 0.824 Z= 0.305
альфа= 80.0 x=0.0379 Pg1= -5.702
J= -0.022 Pсум= 0.267 N= 0.052
дельта=90.9 Pшат= 0.261 T= 0.261 Z= -0.004
альфа=100.0 x=0.0521 Pg1= -5.702
J= -0.546 Pсум= -0.258 N= -0.050
дельта=110.9 Pшат= -0.253 T= -0.236 Z= 0.090
альфа=120.0 x=0.0646 Pg1= -5.702
J= -0.906 Pсум= -0.618 N= -0.105
дельта=129.7 Pшат= -0.609 T= -0.469 Z= 0.389
альфа=140.0 x=0.0741 Pg1= -5.702
J= -1.104 Pсум= -0.816 N= -0.104
дельта=147.3 Pшат= -0.810 T= -0.438 Z= 0.681
альфа=160.0 x=0.0800 Pg1= -5.702
J= -1.188 Pсум= -0.900 N= -0.061
дельта=163.9 Pшат= -0.898 T= -0.249 Z= 0.862
альфа=180.0 x=0.0820 Pg1= -5.702
J= -1.208 Pсум= -0.920 N= -0.000
дельта=180.0 Pшат= -0.920 T= -0.000 Z= 0.920
J= -1.208 Pсум= -1.496 N= -0.000
дельта=180.0 Pшат= -1.496 T= -0.000 Z= 1.496
альфа=200.0 x=0.0800 Pg1= -5.872
J= -1.188 Pсум= -1.647 N= 0.112
дельта=196.1 Pшат= -1.643 T= 0.455 Z= 1.578
альфа=277.1 x=0.0400 Pg1= -13.292
J= -0.107 Pсум= -7.985 N= 1.555
дельта=266.0 Pшат= -7.833 T= 7.814 Z= 0.541
альфа=220.0 x=0.0741 Pg1= -6.437
J= -1.105 Pсум= -2.128 N= 0.271
дельта=212.7 Pшат= -2.110 T= 1.141 Z= 1.775
альфа=240.0 x=0.0646 Pg1= -7.583
J= -0.906 Pсум= -3.076 N= 0.525
дельта=230.3 Pшат= -3.031 T= 2.332 Z= 1.936
альфа=260.0 x=0.0521 Pg1= -9.772
J= -0.546 Pсум= -4.905 N= 0.948
дельта=249.1 Pшат= -4.812 T= 4.494 Z= 1.720
альфа=280.0 x=0.0379 Pg1= -13.304
J= -0.022 Pсум= -7.912 N= 1.529
дельта=269.1 Pшат= -7.763 T= 7.762 Z= 0.128
альфа=300.0 x=0.0236 Pg1= -13.304
J= 0.604 Pсум= -7.287 N= 1.244
дельта=290.3 Pшат= -7.180 T= 6.734 Z= -2.492
альфа=320.0 x=0.0113 Pg1= -13.304
J= 1.209 Pсум= -6.681 N= 0.852
дельта=312.7 Pшат= -6.627 T= 4.868 Z= -4.496
альфа=340.0 x=0.0030 Pg1= -13.304
J= 1.650 Pсум= -6.240 N= 0.426
дельта=336.1 Pшат= -6.225 T= 2.524 Z= -5.691
альфа=360.0 x=0.0000 Pg1= -13.304
J= 1.812 Pсум= -6.078 N= 0.000
дельта=360.0 Pшат= -6.078 T= 0.001 Z= -6.078
5.6 Прочностные расчеты
5.6.1. Поверочный расчет днища поршня
Днище поршня рассчитываем как круглую плиту заделанную по периметру.
Расчетное напряжение изгиба:
где – максимальное избыточное давление;
– радиус заделки днища поршня
5.6.2 Проверочный расчет поршневого пальца
Поршневой палец рассчитывается как балка на двух опорах с равномерно распределенной нагрузкой по длине шатунного подшипника.
Напряжение в пальце:
Максимальный изгибающий момент в среднем сечении пальца:
– соответствующие отрезки
Рисунок 1.6 – Поршневой палец
Момент сопротивления изгибу:
где ; – наружный и внутренний диаметр пальца.
Допустимое значение
где – коэффициент запаса;
– толщина пальца удовлетворяет прочностным характеристикам.
5.6.3 Прочностной расчет шатунных болтов
Шатунные болты проверяются на разрыв от максимальной силы инерции поршня и шатуна и усилия затяжки .
Разрывное напряжение равно:
Площадь наименьшего сечения болта:
Усилие от силы инерции шатуна:
Масса вращающейся части шатуна без крышки:
– угловая скорость вращения вала.
– из динамического расчета.
Для болтов стали 40Х:
Запас прочности что вполне допустимо.
5.7 Расчет противовесов
Для уравновешивания сил инерции (их момента) от поступательно движущихся частей первого порядка и момента сил инерции от вращающихся масс применяют противовесы.
Суммарная масса противовесов для двухколенного вертикального поршневого компрессора:
где – радиус кривошипа;
– расстояние между шатунами;
– радиус противовеса;
– расстояние между противовесами.
Масса вращающихся частей:
где – масса шатунной шейки;
т.к. – масса неуравновешенной части щеки;
– масса поступательно движущихся частей.
5.8 Проверочный расчет подшипников
При проектировании компрессора были приняты шарикоподшипники радиальные сферические двухрядные 1310 ГОСТ 28428-90 (средняя серия самоустанавливающиеся).
– динамическая грузоподъемность подшипника;
По динамическому расчету определяем положение при котором силы и достигают одновременно наибольших значений при .
Поскольку расстояние между опорами одинаковые то опоры нагружены одинаково:
Проверим предварительно принятые подшипники:
Эквивалентная нагрузка:
где – коэффициент безопасности [3] с.214;
– температурный коэффициент;
– при вращении наружного кольца.
По таблице 9.24 из [3] с.220 при и – срок службы подшипников: – для шарикоподшипников.
Требуемая динамическая грузоподъемность подшипника:
Получаем что следовательно подшипники подходят для данного компрессора.
6 Расчет горизонтального кожухотрубного конденсатора
6.1 Тепловой расчет конденсатора
Температура воды на входе: tw1 = 55оС
Температура воды на выходе: tw2 = 75оС
Температура фреона (R142b) на входе: tf1 = 103оС
Температура фреона на выходе: tf2 = 65оС
Массовый расход воды через конденсатор:
Температура конденсации холодильного агента в конденсаторе:
Среднелогарифмическая разность температур:
Принимаем основные размеры характеризующие теплопередающую поверхность конденсатора: шахматный пучек из медных труб со стандартным наружным оребрением:
– внутренний диаметр ;
– диаметр окружности выступов ;
– диаметр окружности впадин ;
– площади наружной поверхности 1м длинны трубы ;
– площади внутренней поверхности 1м длинны трубы ;
– коэффициент оребрения .
При средней температуре воды 650С:
– кинематическая вязкость воды ;
– число Прандтля Pr = 2.8;
– теплопроводность воды λ=06 ВтмК.
Предварительно задаем скорость воды в трубах конденсатора.
Число труб в одном ходе:
Принимаем и уточняем скорость воды:
– турбулентный режим течения;
Коэффициенты теплоотдачи со стороны воды:
Принимаем суммарное термическое сопротивление стенки трубы и загрязнений.
Плотность теплового потока:
Ориентировочное значение приняв тогда:
При распределении труб в трубной решетке в вершинах правильных шестиугольников и по сторонам правильных концентрических шестиугольников параметр m определяется следующим образом:
где m – число труб располагаемое по большей диагонали внешнего
S – горизонтальный шаг труб: S=13·dн=13·002=0026 м;
LD – длина трубы к диаметру трубы принимаем равным 5.
Округляем до ближайшего нечётного числа и принимаем nв = m = 11.
Коэффициент теплоотдачи со стороны конденсирующегося фреона отнесённый к внутренней поверхности труб:
где λ=00772 ВтмК - теплопроводность R142b при
=25710-4- динамическая вязкость R142b при tk Пас;
ρ = 923 – плотность R142b при tk кгм3;
r= 15404 – теплота конденсации R142b при tk кДжкг.
Уравнения плотности теплового потока.
Таблица 1.2 – Плотности тепловых потоков
Строим графики зависимостей тепловых потоков и от температуры:
Рисунок 1.7 – Графики зависимостей тепловых потоков и от температуры.
Из графика определяем: .
Более точно qвн находим по интернациональному выражению:
Общее число труб в аппарате:
Число ходов в аппарате по воде:
Внутренняя поверхность теплообмена:
Длина одной трубы в аппарате:
Внутренний диаметр аппарата:
где - число труб в наибольшей диагонали шестиугольника в трубной решетке.
6.2 Гидравлический расчёт
Гидравлическое сопротивление аппарата:
Суммарное гидравлическое сопротивление трения:
где- коэффициент течения в трубном пространстве при турбулентном режиме течения:
Суммарное местное гидравлическое сопротивление:
где - коэффициент местного сопротивления.
где - число входных камер в крышке испарителя
- коэффициент местного сопротивления входной камеры
- число выходных камер
- коэффициент местного сопротивления выходной камеры
- число поворотов потока рассола внутри трубной решетки на
- коэффициент местного сопротивления поворота на .
Тогда гидравлическое сопротивление аппарата:
Обечайка изготавливается из листовой стали сварная продольный стыковой шов выполненный ручной электродуговой сваркой. Коэффициент прочности сварного соединения . Допускаемые напряжения:
– нормативное для стали ВСт3сп ;
– для рабочего состояния ;
Исполнительная толщина стенки обечайки:
где – сумма всех прибавок толщины обечайки.
Ск=1 мм прибавка на коррозию или другой вид химического воздействия рабочей среды на материал.
Сэ=0 прибавка на эрозию учитывается тогда когда скорость движения среды в аппарате больше 20 мс.
Сд=07 дополнительная прибавка по технологическим соображениям.
С0=06 прибавка на округление размера.
6.4 Расчёт патрубков
Расчет проводим исходя из уравнения неразрывности:
Патрубки для холодильного агента:
Скорость на входе w=15 мc; плотность на входе ρ=1057 кгм3; расход фреона G=036кгс.
Скорость на выходе w=2 мc; плотность на входе ρ=848 кгм3 ; расход фреона G=036 кгс.
6.5 Расчет эллиптического днища
Расчётное давление Ртр = 04 МПа температура Т = 338 К.
В днище имеются два отверстия диаметром d=32 мм для входа и выхода охлаждающей воды расположение симметрично относительно центра днища.
Коэффициент ослабления днища отверстиями:
где Dвн = 028 м – внутренний диаметр днища.
Исполнительную толщину эллиптического днища (крышки ) определяем по формуле:
В нашем случае даёт малую величину. По технологическим причинам выбираем толщину днища дн = 5 мм т. е. равной толщине обечайки. Суммарная прибавка к толщине днища: прибавка для компенсации коррозии 2 мм; прибавка для компенсации минусового допуска 06мм; технологическая прибавка 09мм тогда Σс = 00035м.
Допускаемое давление в камере в рабочем состоянии:
Допускаемое давление при гидравлических испытаниях:
7 Расчет горизонтального кожухотрубного испарителя
7.1 Тепловой расчет испарителя
Холодопроизводительность Q0 = 100 кВт
Температура кипения хладагента t0 = 45 0C
Температура масла на входе: ts1 = 57оС
Температура масла на выходе: ts2 = 50оС
Площадь теплопередающей поверхности:
где k - коэффициент теплопередачи Вт(м2 К)
m - средний температурный напор 0С
Среднелогарифмическая разность температур равна:
Свойства масла при средней температуре:
– плотность ρ кгм3 865
– удельная теплоемкость сs кДж(кг·К) 1.992
– теплопроводности λs Вт(м·К) 014
– кинематической вязкости s м2 с 27·10-6
– динамической вязкости s Па·с 29·10-5
– число Прандтля Prж 412629
Теплофизические свойства раствора принимаем из [3] табл. 8 с. 10.
Принимаем основные параметры характеризующие теплопередающую поверхность: трубы медные с накатными ребрами диаметром 20х3 мм. Размеры профиля ребер: внутренний диаметр dвн =133 мм диаметр по окружности ребер dр =206 мм диаметр по окружности впадин dвп = 176 мм шаг ребер sp = 15 мм толщина у вершины ребра = 04 мм угол между ребрами α = 300 ([2] c. 333).
Коэффициент оребрения трубы:
Принимаем скорость масла в трубах равной = 15 мс. Тогда число труб в одном ходе аппарата равна:
Принимаем n1 = 9 тогда скорость масла равна:
Определяем режим движения раствора:
Режим движения раствора ламинарный тогда число Нуссельта равно:
где ldвн - отношение длины трубы на внутренний диаметр.
При интервале 150 ≤ ldвн ≤ 300 принимаем ldвн =150 тогда:
Тогда коэффициент теплоотдачи со стороны масла равен:
Плотность теплового потока со стороны масла:
где i λi - термическое сопротивление загрязнений и медной трубки с накатными ребрами i λi = 02 03 ·10-3 (м2· К )Вт.
Принимаем iλi = 025 ·10-3 (м2· К )Вт. Тогда:
Плотность теплового потока со стороны рабочего вещества отнесенного к внутренней поверхности:
гдеp0 = 06 бар - давление кипения хладагента.
пр - коэффициент учитывающий влияние числа рядов труб по высоте пучка;
Согласно [2] с. 331 пр = 1.
Определим удельный тепловой поток в испарителе графоаналитическим методом. Строим зависимости плотности теплового потока со стороны масла qFs= f(s) и со стороны хладагента qFa= f(a) в интервале температур 0 ≤ a ≤ m и m ≤ s ≤ 0 соответственно (рисунок 1.8).
Из рисунка 1.8 видно что удельный тепловой поток равен qFвн = 3800 Втм2.
Внутренняя поверхность теплообмена в испарителе:
Рисунок 1.8 – Расчет плотности теплового потока
7.2 Конструктивный расчет испарителя
Принимаем размещение труб на плоскости трубной решетки по периметрам правильных шестиугольников.
Принимаем s = 27 мм.
Принимаем отношение длины труб к диаметру аппарата k = lD = 5.
Число труб размещенных по диагонали внешнего шестиугольника:
Внутренний диаметр обечайки:
C учетом неполного заполнения фреона в межтрубном пространстве испарителя принимаем Dвн = 500 мм.
Принимаем l=2500 мм.
Общее количество труб в испарителе:
Принимаем n = 180. Число ходов в аппарате:
Принимаем скорость фреона на входе в испаритель вх = 5 мс на выходе вых = 15 мс.
Диаметр парового патрубка на входе в испаритель:
где вх - удельный объем пара на входе в испаритель.
где x = 0225 - содержание паровой фазы фреона.
ρ' ρ'' - плотности жидкой и паровой фаз фреона ρ' =1.055 кгм3 ρ'' =26.94 кгдм3
Принимаем dвх = 50 мм.
Аналогично определяем диаметр выходного патрубка.
Удельный объем пара на выходе из испарителя вых = 0147 м3кг тогда:
Принимаем dвых = 50 мм.
Диаметр патрубков для хладоносителя:
Принимаем dхн = 30 мм.
7.3 Гидродинамический расчет испарителя
Местные сопротивления определяем по формуле Вейсбаха-Д'Арси:
где - коэффициент сопротивления.
Коэффициент сопротивления:
гдетр - коэффициент сопротивления жидкостного трения.
а - количество входных камер а = 10;
b - количество выходных камер b = 10;
c - количество поворотов потока раствора в крышках испарителя с = 8;
= 1 - коэффициент местного сопротивления внезапного сужения прохода;
= 05 - коэффициент местного сопротивления внезапного расширения прохода;
=2 коэффициент местного сопротивления поворота на 1800 внутри крышки при переходе из одного пучка трубок в другой.
Для ламинарного режима движения формула Пуазейля:
7.4 Прочностной расчет испарителя
7.4.1 Расчет обечайки
Диаметр обечайки Dвн м 05
Длина обечайки l м 25
Площадь теплообменной поверхности Fвн м2 263
Давление в межтрубном пространстве ([2] c. 389 табл. 4.16):
– расчетное рр МПа 078
Рабочее (расчетное) давление в трубном пространстве ртр МПа 04
Принимаем материал обечайки из стали Вст3сп по ГОСТ 380-94. Нормативное допускаемое напряжение стали Вст3сп * = 140 МПа ([2] с.391 табл. 4.17).
Допускаемое напряжение для рабочего состояния материала обечайки корпуса испарителя:
где – коэффициент учитывающий работу аппарата со взрыво- и пожароопасными продуктами =1 для фреонов.
з - коэффициент учитывающий вид заготовки для заготовок из проката з =1.
[]= 1 1 140 = 140 МПа
Допускаемые напряжения при гидравлических испытаниях:
гдет20 - минимальное значение предела текучести стали при 20 0С т20 = 210 МПа ([2] с.391 табл. 4.17).
[]и = 210 11 = 191 МПа.
Расчетная толщина обечайки:
где φ - коэффициент прочности сварочного шва для ручной электродуговой сварки φ = 095 ([6] с. 13 табл. 1.7)
с - прибавка к расчетной толщине стенки на коррозию мм.
Принимаем прибавку на коррозию с = 1 мм.
Расчетная толщина стенки в рабочем состоянии равна:
Давление при гидравлическом испытании равно: pи = 13 · pр = 13 · 078 = 101 МПа.
Расчетная толщина стенки при гидравлическом испытании:
Согласно [6] табл. 25 принимаем исполнительную толщину стенки s = 5 мм.
Допускаемое давление в рабочем состоянии:
Условие прочности: [p] = 132 МПа > рр =078 МПа – выполняется.
Допускаемое давление при гидравлическом испытании:
Условие прочности: [p]и = 18 МПа > ри =101 МПа – выполняется.
Применимость расчетных формул: (s - c)Dвн = (5-1) 500 = 0008 01 - условие применимости выполняется.
7.4.2 Расчет эллиптического днища
Материал днища изготавливаем из стали Вст3сп по ГОСТ 380-94.
Расчетная толщина стенки днища:
где с1 - прибавка к коррозии материала стенки днища.
φ=1 - Так как днище изготовлено из цельного материала.
С учетом прибавки толщины для компенсации коррозии с1 = 15 мм.
Принимаем толщину стенки днища s1 = 5 мм.
Условие прочности: [p]тр =122 МПа > ртр =04 МПа - выполняется.
Давление при гидравлическом испытании равно: pи.тр = 13 · pтр = 13 · 04 = 052 МПа.
Условие прочности: [p]и.тр = 167 МПа > ри =052 МПа - выполняется.
Проверим применимость расчетных формул: (s1 - c1)Dвн = (5-15) 500 = 00044 01 - условие применимости выполняется.
7.4.3 Расчет трубной решетки
Трубную решетку изготавливаем из толстолистовой стали ВСт3сп. В отверстиях решетки закреплены развальцовкой 180 медных труб.
Минимальная конструктивная толщина трубной решетки:
где sтр = 3 мм толщина не оребренной части трубы.
Принимаем hт = 32 мм на участке под фланец hф = 25 мм так как толщины фланцев должны быть одинаковыми или близкими.
Схема развальцовки трубы показана на рисунке 1.9.
Рисунок 1.9 – Схема вальцовки трубы
Примем размеры пазов под вальцовку ([10] c. 640 табл. 25.4):
- расстояние между пазами: а = 15 · sтр = 15 · 3 = 45 мм принимаем а=5 мм;
- величина паза: b = sтр +1 = 3+ 1 = 4 мм;
- диаметр отверстия под трубу: d = (102 1016) · dтр = 102 · 20 = 204 мм;
- диаметр пазов: d1 = d + 02 · sтр + 05 = 204 + 02 · 3 + 05 = 215 мм
Рассмотрим трубную решетку как плоскую пластину на которую действует сила Р=00245 МПа. Тогда условно равномерно распределенная нагрузка действующая на всю поверхность пластины:
При значительной жесткости узла сварки обечайки и трубной решетки можно рассматривать ее как пластину защемленную по контуру.
Тогда максимальное напряжение возникающее на контуре пластины равно:
где r = 05· Dвн = 05 · 05 = 025 м.
φ0 - коэффициент ослабления пластины
Коэффициент ослабления пластины при числе отверстий на радиусе r равным nr = 8:
Напряжение в центре пластины:
где =03 – коэффициент Пуассона.
Максимальный прогиб трубной решетки:
где D0 - цилиндрическая жесткость пластины.
Проверим трубы на продольный изгиб. Гибкость теплообменной трубы:
rи - радиус инерции трубы.
Радиус инерции трубы:
Условие устойчивости трубы при осевом сжатии:
где ny = 15 - коэффициент устойчивости.
Критическое напряжение устойчивости по формуле Эйлера:
Условие устойчивости трубы выполняется. Укрепление труб не требуется.
8 Расчет регенеративного теплообменника
Регенеративный теплообменник (РТ) предназначен для переохлаждения жидкого хладагента выходящего из конденсатора холодными парами этого хладагента выходящими из испарителя. Он позволяет повысить удельную холодопроизводительность холодильной машины по сравнению с циклом без РТ и тем самым повысить её холодильный коэффициент.
8.1 Конструктивный расчёт
Задаёмся конструктивными размерами РТ. Кожух выполнен из цельнотянутой стальной трубы из стали 20 наружным диаметром Dн=0325 м и толщиной стенок к= 0008 м. Змеевик РТ выполнен из стальной трубки (Сталь 10) с наружным диаметром dн=0038 м и толщиной стенок зм=0002 м. Сердечник на который навивается змеевик выполнен из стальной трубы с наружным диаметром Dн=0219 м с толщиной стенок с=0006 м. Толщина дистанционной планки между сердечником и змеевиком принимается равной S=0004 м. Высота крышки кожуха hкр=015 м. Жидкий фреон R142b движется по змеевику а холодный пар противотоком движется по межтрубному пространству РТ.
Находим теплофизические свойства сред обменивающихся теплотой в РТ при их средних температурах:
Средняя температура равна Тж = 05 (Тж1 + Тж2) =05 (328 + 318)=323 К . По [9] табл.13 с.38 находим:
- плотность равна ρж=1041 кгм3;
- удельная теплоемкость сж=9897 кДжкг·К;
- коэффициент теплопроводности равен λж=00686 Втм К;
- коэффициент кинематической вязкости равен ж=0195·10-6м2с.
Средняя температура пара равна Тп=05(Тп1 + Тп2)=05(338 + 331)=3345 К:
- плотность равна ρп=3986 кгм3;
- удельная теплоемкость срп=565 кДжкг К;
- коэффициент теплопроводности равен λп=00078 Втм К;
- коэффициент кинематической вязкости равен п=1245·10-6м2с.
Определяем коэффициент теплоотдачи жидкого хладагента αх
Находим площадь прохождения трубки змеевика Fзм.
Её внутренний диаметр равен dвн=dн-2зм= 0038-2·0002= 0034 м.
Скорость жидкого R142b в трубке равна:
Находим критерии Рейнольдса:
Находим радиус закругления змеевика по осевой линии трубы сердечника:
Rзм = 05Dсн + S + 05 dн = 05·0219+0004+05·0038 = 01325 м.
Критическое число Рейнольдса соответствующее ламинарному режиму течения в трубке змеевика равно:
Критическое число Рейнольдса соответствующее турбулентному режиму течения в трубке змеевика равно:
Вывод: Rеж > Rекр.труб т.е. режим движения в трубке змеевика турбулентный.
Число Прандтля равно:
Число Нуссельта для турбулентного режима течения жидкого фреона R142b в трубке змеевика равно:
Nuж = 0021·Re08ж·Pr043ж·изг
где изг = 1+177= 1+177=1455 - поправка учитывающая влияние центробежного эффекта на процесс теплоотдачи со стороны жидкого R142b:
Nuж = 0021·6625608·293043·1455 = 349
Коэффициент теплоотдачи со стороны жидкого R142b равен:
Определяем коэффициент теплоотдачи со стороны паров R142b.
Внутренний диаметр кожуха РТ равен:
Dвн = Dн – 2к = 0325 – 2·0008 = 0309 м
Площадь межтрубного пространства по поперечному сечению РТ равна:
Скорость пара R142b в межтрубном пространстве РТ равна:
Находим критерий Рейнольдса:
т.е. режим движения пара в межтрубном пространстве – турбулентный.
Находим число Прандтля:
Число Нуссельта для турбулентного режима течения пара в межтрубном пространстве РТ равно [9] с.228:
Nuж = 023·Re065п·Pr033п = 023·48835065·36033 = 392
Коэффициент теплоотдачи со стороны пара R142b равен:
Поскольку в R142b хорошо растворяется масло на стенках змеевика отсутствует масляная пленка поэтому термическое сопротивление трубки змеевика равно термическому сопротивлению стенки стальной трубки.
Для стали 10 коэффициент теплопроводности равен:
Термическое сопротивление стенки трубки змеевика равно:
Коэффициент теплопередачи РТ равен:
Средняя логарифмическая разность температур при движении сред в РТ противотоком равна:
Площадь теплообменной поверхности РТ равна:
С учетом 20% запаса принимаем площадь теплообменной поверхности РТ равной:
Fпр = 12 Fр = 144 м2
Длина трубы змеевика РТ равна:
Число витков змеевика РТ равно:
Задаёмся шагом навивки змеевика на сердечник t = 005 м
Длина змеевика РТ равна:
Lзм = n·t = 15·005 = 075 м
Задаём односторонний припуск по длине трубы змеевика равным l=075 м
Длина теплообменной змеевиковой трубы с учетом припусков на входном и выходном её участки равна:
L1 = L+2l = 121+2·075 = 136 м
Длина кожуха РТ (без патрубков) равна:
Lк = Lзм·11 +2hкр = 075·11+2·015 = 1125 м
8.2Гидравлический расчёт
Определяем гидравлическое сопротивление змеевиковой трубы РТ. Задаёмся величиной шероховатости на внутренней стенке трубы Δ = 01мм = 00001м.
Коэффициент гидравлического трения определяем по формуле А.Д. Альтшуля для турбулентного режима течения жидкого R142b:
Потери давления на трении в змеевике находим по формуле Вейзбаха-Д’Арси:
Коэффициент местного сопротивления витка змеевика при повороте в нём потока на 3600 принимаем равным = 04 [11] с.248.
Местные потери давления в РТ находим по формуле Вейcбаха:
Общее гидравлическое сопротивление РТ по трубному пространству змеевика равно:
Δpзм = Δpтр + Δpм = 851+451 = 4039 Па
Определяем гидравлическое сопротивление РТ по межтрубному пространству. Принимаем что входной и выходной патрубки выполнены из стальной трубы с наружным диаметром dпн = 0089м и толщиной стенки п = 00045 м.
Внутренний диаметр патрубков равен:
dпвн = dпн - 2п = 0089 – 2·00045 = 008 м.
Площадь проходного сечения патрубков рана:
Скорость пара R142b в патрубках равна:
Потери давления на трение в межтрубном пространстве равны:
Δр’тр = 053nRe-0122·ρп2п = 053·15·48835-0122·398593·162=217 Па
Коэффициенты местного сопротивления входного и выходного патрубков в кожухе РТ принимаем равным = 15 [11] с.116 число патрубков n1=2.
Местные потери давления в патрубках кожуха РТ равны:
Общее гидравлическое сопротивление РТ по межтрубному пространству равно:
Δpмтр = Δp’тр – Δp’м = 217+1937 = 4107 Па
8.3 Прочностной расчёт
Трубу змеевика и кожух РТ проверяют на прочность гидравлическими испытаниями с запасом по величине давления 25% по отношению к рабочему значению давления.
Для трубки змеевика РТ давление испытаний равно:
pзм = 125 рк = 175 МПа
Для кожуха РТ давление испытаний равно:
pкож = 125 р0 = 075 МПа
Наибольшее напряжение в стенке кожуха РТ из стали 20 равны:
кoж max [] = 100 МПа для стали 20 даже с учетом 20% запаса по напряжениям из-за вареных в крышке патрубков т.е. условия прочности выполняется.
Наибольшее напряжение в стальной трубке змеевика РТ из стали 20 равны:
зм max [] = 100 МПа т.е. условие прочности выполняется.
9 Подбор вспомогательного оборудования
Выбор насоса для воды:
Массовый расход воды – масла –
По расходу подбираем два центробежных насоса марки 15К-819б(15К-6б) с диаметром рабочего колеса – 105 мм производительностью – 94 м3ч. КПД – 49 % и мощностью на валу насоса – 06 кВт табл.7.7 [Сверлов].
Выбор ресивера: объем линейного ресивера находим по формуле:
Выбираю линейный ресивер марки 075РВ по [сверлов явнель]. Обечайка ресивера выполнена из трубы диаметром 600х8 длиной 3190мм.ресивера – 430 кг.
Для предотвращения движения обратного потока фреона согласно правилам техники безопасности устанавливаем обратный клапан марки КН100 который предназначен для работы с давлением до 1.8 МПа.
Д-ка коленвал.cdw

Поковка ГР IV-КП30 ГОСТ 8479.
*. Размеры для справок.
вмятины не допускаются.
Перед сборкой масляные каналы продуть воздухом
Неуказанные предельные отклонения размеров валов h14
НВ 260 285 кроме места
Неуказанные радиусы 2 мм.
Трубчатка КД.cdw

Неуказанные предельные отклонения
Трубчатку подвергнуть гидравлическим испытаниям р
Неуказанные предельные отклонения размеров Н14
Корпус с трубчаткой
Материал для сварки швов N1 электрод УОНИИ 1355-4.0
* Размеры для справок
Сварные швы контролировать УЗД или рентгенопросвечиванием в объеме:
по трубному пространству-25%
по межтрубному пространству-100%;
контролировать в соответствии с РД 26-11-01-85.
Техническая характеристика
Аппарат предназначен для проведения теплообмена
Расчетная температура конденсации
Наименование рабочей среды
Поверхность теплообмена
Средняя разность температур
Выход к уравнительной линии
Стравливание воздуха
* Размеры для справок.
Детали и сборочные единицы маркировать по РД 3300-1.12.16.
красно-коричневая ГОСТ25-129
люминисцентным индикаторным покрытием решоток
07 МПа после проварки (до развальцовки) труб
М-1(по ТУ 6-02-1132) концентрацией 1-5% допускается замена на
После испытаний аппарат осушить
резьбы смазать смазкой пластинча-
Аппарат красить эмалью светло серой ПФ-115
б) гидравлическим давлением 2.5 МПа в межтрубном пространстве с
а) пневматическим испытанием межтрубного пространства давлением
Качество закрепления труб в трубных решотках проверить:
При гидроиспытании использовать водный раствор ингибитора корозии
межтрубное пространство: 1.8 МПа
трубное пространство: 0.52 МПа
Аппарат испытывать гидравлическим давлением:
контролировать недоступные для УЗД или рентгенопросвечивания швы
и безопасности эксплуатации сосудов работающих под давлением".
Технические требования
Аппарат изготовлен согласно ГОСТ3-17-191 и"Правилам устройства
Клапан предохранительный
в соответствии с РД 26-11-01.
нитрат натрия ГОСТ 19906
Таблица сварных соединений
Спецификация КД.spw

Клапан предохранительный
Фланец 16 Ст 20 ГОСТ12820
Болт М16х80 ГОСТ 7796
Шайба 16.65Г ГОСТ 6402
Припой ПОС-30 ГОСТ 1499
Эмаль ПФ-115 ГОСТ 6465
Грунт ГФ-021 ГОСТ 25129
Керосин технический КТ-1
Дин. лист.cdw

испаритель.frw

Испаритель предназначен для охлаждения 40% раствора этиленгликоля.
Поверхность теплообмена
Рабочее избыточное давление
- в трубном пространстве
- в межтрубном пространстве
Рабочая температура в испарителе
% раствор этиленгликоля
- в межтрубном пространстве
Технические требования
* Размеры для справок.
Аппарат изготовить согласно ГОСТ 26-291-79 и ТУ 26-02-826-78
На аппарат распространяется "Правила устройства безопасной эксплуатации сосудов
работающих под давлением".
Трубы должны поставляться испытанными гидравлически.
Аппарат ипытать в течении 10 минут гидравлически давлением:
- в трубном пространстве р
- в межтрубном пространстве p
Допускается производить люминисцентно-гидравлическое испытание вместо гидравлического и пневматического испытаний с последую
После испытаний аппарат внутри осушить
резьбы смазать смазкой пластинчатой ПВК ГОСТ 19537-74.
Аппарат красить эмалью светло-серой
ГОСТ 6465-76 по грунтовке ГФ - 0
красно-коричневой ГОСТ 25129-82.
Выход предохранительного клапана
СУмГУ ХХ.00.00.00 СБ
Прокладка ГОСТ 15180-86
Фланец ГОСТ 12820-80
Шайба 12 ГОСТ 11371-78
Шайба 16 ГОСТ 11371-78
Вентиль запорный 15кч80п
Клапан предохранительный 11с17ж
Манометр ДМ1001-250 кПа-1
Электроды Э46 ГОСТ 9466-75
Эмаль ПФ-115 ГОСТ6465-76
КД.cdw

Аппарат предназначен для проведения теплообмена
Расчетная температура конденсации
Наименование рабочей среды
Поверхность теплообмена
Средняя разность температур
Выход к уравнительной линии
Стравливание воздуха
* Размеры для справок.
Детали и сборочные единицы маркировать по РД 3300-1.12.16.
красно-коричневая ГОСТ25-129
люминисцентным индикаторным покрытием решоток
07 МПа после проварки (до развальцовки) труб
М-1(по ТУ 6-02-1132) концентрацией 1-5% допускается замена на
После испытаний аппарат осушить
резьбы смазать смазкой пластинча-
Аппарат красить эмалью светло серой ПФ-115
б) гидравлическим давлением 2.5 МПа в межтрубном пространстве с
а) пневматическим испытанием межтрубного пространства давлением
Качество закрепления труб в трубных решотках проверить:
При гидроиспытании использовать водный раствор ингибитора корозии
межтрубное пространство: 1.8 МПа
трубное пространство: 0.52 МПа
Аппарат испытывать гидравлическим давлением:
контролировать недоступные для УЗД или рентгенопросвечивания швы
по трубному пространству-25%
по межтрубному пространству-100%;
Сварные швы контролировать УЗД или рентгенопросвечиванием в объеме:
и безопасности эксплуатации сосудов работающих под давлением".
Технические требования
Аппарат изготовлен согласно ГОСТ3-17-191 и"Правилам устройства
Клапан предохранительный
в соответствии с РД 26-11-01.
нитрат натрия ГОСТ 19906
Таблица сварных соединений
Цикл и схема.cdw

РВ - регулирующий вентиль;
РТ - регенеративный
ПК - переохладитель конденсата;
Схема теплонасосной установки
Испаритель гориз.cdw

* Размеры для справок.
Аппарат изготовить согласно ГОСТ 26-291-79 и
На аппарат распространяется "Правила устройства безопасной
эксплуатации сосудов
работающих под давлением".
Трубы должны поставляться испытанными гидравлически.
Аппарат ипытать в течении 10 минут гидравлически давлением:
- в трубном пространстве р
- в межтрубном пространстве p
После испытаний аппарат внутри осушить
резьбы смазать смазкой
пластичной ПВК ГОСТ 19537-74.
Аппарат красить эмалью светло-серой
красно-коричневой ГОСТ 25129-82.
Давление срабатывания предохранительного клапана 0
Стравливание воздуха
Клапан предохранительный
Таблица сварных соединений
Пробное гидравлическое давление
Среда и ее свойства
Корродирует или нет
Техническая характеристика.
Спецификация решетка трубная.spw

Конденсатор горизонтальный
Припой ПОС-30 ГОСТ 1499
пз руся.doc
В период гражданской войны и иностранной интервенции предприятие в основном не работало были разрушены и сожжены все ведущие цехи. К восстановлению при ступили в начале 1922 года на основании решения Харьковского губернского совнархоза. В 1922 году уже были завершены первые восстановительные работы. После завершения восстановительных работ были введены в эксплуатацию заново переоборудованные литейный и механический цехи. В номенклатуре завода появилась более сложная продукция - центробежные насосы лебедки фермы для железнодорожных мостов. Начали выпуск оборудования для электростанций мостовых кранов паровых котлов электрических лебедок для шахт Донбасса.
В 1926 году завод дал продукции на 1655 тыс. рублей в ценах 1913 года что составило 42% всей продукции машиностроения лишь Краматорский завод с показателем 48% опередил наше предприятие.
В 1930 году в стране принята программа развития тяжелой индустрии. На заводе взят курс на техническое совершенствование производства и внедрение новых технологических процессов. В том же году когда на базе ряда старейших заводов страны был заложен фундамент новой отрасли - химического машиностроения предприятие начало специализироваться как завод химического и нефтяного машиностроения. В 1931 году стали в строй новые производственные мощности: насосно-компрессорный цех литейный и инструментальные цехи. Это значительно повысило производственный потенциал завода.
июня 1941 года. Весть о начале войны была страшной но коллектив завода встретил ее с большим мужеством. Сотни трудящихся сразу же добровольцами пошли на фронт А те кто остался изготовляли вооружение боеприпасы. Ежеднев- ные задания выполняли не менее чем на 250 процентов.
В 1948-1950 годах завод внес большой вклад в создание атомной промышленности страны. Учитывая высокое мастерство коллективу поручили ответственное правительственное задание по изготовлению первых аппаратов для ядерной энергетики. Производство опытных изделий возглавил лично главный инженер завода П.Т. Гончаренко.
В 1949 году в г. Сумы было организовано новое предприятие - Сумский насосный завод. Он был создан на базе цеха центрифуг завода имени М.В. Фрунзе. На новое предприятие перешло 330 работников завода имени М.В. Фрунзе – квалифицированных инженеров служащих и рабочих которые и составили основу будущего коллектива насосников. К 1950 году завод уже располагал мощной производственной базой квалифицированным составом ИГР рабочий служащих которым было по плечу решение сложных технических и производственных задач.
50-1965 годы - это период когда неуклонно повышался производственный потенциал завода совершенствовались и перевооружались многие его цехи рождались проекты новых машин и аппаратов. Наряду с развитием химического аппаратостроения на первые рубежи выходит такое сложное и наиболее необходимое в те годы оборудование как тяжелые компрессоры большой производительности и высокого давления. Это требовали создаваемые производства азотных минеральных удобрений пластмасс процессы глубокой переработки нефти и другие. Завод был единственным предприятием в стране способным изготовлять тяжелые компрессорные машины располагая необходимы технологическим оборудованием квалифицированными кадрами и производственным опытом.
65 - 1975 годы в развитии завода можно охарактеризовать как период наиболее интенсивного роста номенклатуры и объемов выпуска химического оборудования и дальнейшего технического оснащения производства.
В эти годы решалась поставленная правительством задача по химизации народного хозяйства страны для чего требовалось резко увеличить темпы развития отрасли химического машиностроения.
В целях более эффективного решения этой задачи концентрации всех конструкторских подразделений для ускорения внедрения достижений науки и техники в производство и на этой основе повышения технического уровня создаваемого нового химического оборудования в 1965 году на заводе на базе его конструкторских служб было создано отдельное специальное конструкторское бюро.
В 1981 году первый насос под руководством начальника управления главного технолога Ю.К-Братушки успешно испытали на стенде Ленинградской АЭС. Подтвердились все технико-экономические и эксплуатационные расчеты. Генеральный конструктор главных циркуляционных насосов Л.А.Аркин по результатам испытаний "благословил" серийный выпуск насосов.
Все последующие ГЦН-195М и насосы II контура проходили приемосдаточные испытания на испытательной станции насосного производства где весь процесс работы насоса был автоматизирован. Они проходили испытания по всем необходимым параметрам вплоть до имитации аварийных ситуаций. Большую работу по организации такой проверки провели квалифицированные специалисты:
начальник испытательной станции С.Г.Обозный. Одновременно с освоением насосов ГЦН-195М организовали производство насосов второго контура АЭС в цехах № 6 и 7 а также некоторых крупных насосов на насосном производстве. В цехе №6 сосредоточили выпуск конденсатных насосов КСВА и сложных центробежных ЦН-50 и ЦН-60.
В период 1986-1990 годов в объединении продолжается рост номенклатуры и объемов выпуска оборудования для топливно-энергетического комплекса страны. Растет число разрабатываемых новых линий установок машин. С первых лет создания объединения был взят курс на увеличение поставок этого важнейшего оборудования что значительно изменило портфель заказов и существенно увеличило номенклатурный перечень изготовляемой продукции. В этих условиях потребовались новые подходы к формированию годовых и перспективных планов производства более оперативной связи с потребителями проведения четкой договорной политики совершенствования механизма межцеховых связей и жесткого контроля сроков исполнения.
Выполнив планы 1991 года объединение вступило в 1992 год. Это был год начала вхождения предприятий Украины в рынок и он был весьма сложным.
В составе управления финансов и сбыта во исполнение директивных документов Президента Украины и Государственного таможенного комитета в декабре 1992 года было создано новое подразделение - отдел декларирования грузов. Основной задачей отдела являлось обеспечение внешнеэкономической деятельности объединения в условиях перехода к рыночным отношениям и в условиях полной независимости Украины. При этом отдел оформлял документацию не только на отгружаемую продукцию но и на импорт. Становление отдела проходило в сложных условиях: отсутствие полноценной законодательной базы в Украине неготовность специалистов к новому типу деятельности большой объем экспортно-импортных операций.
На базе двух управлений: подготовки производства и финансово-сбытового в ноябре 1994 года создали новое подразделение - управление маркетинга и финансов.
В 1991-2007 годах в сложных условиях перехода к рынку благодаря мерам принимаемым по структурной перестройке производства внедрению новых подходов к управлению деятельностью объединения объединение работало относительно стабильно не было случаев остановки производства полностью сохранена социальная сфера которая содержится за счет собственных средств объединения не уменьшилась численность работающих заработная плата выплачивалась ежемесячно нет долгов перед государственным бюджетом. В статусе акционерного общества трудовой коллектив будет стремиться улучшать результаты производственно-хозяйственной деятельности и на этой основе повышать благосостояние работников.
2 Предназначение теплонасосной установки
Тепловой насос осуществляет передачу внутренней энергии от энергоносителя с низкой температурой к энергоносителю с более высокой температурой. Поскольку в соответствии со вторым основным законом термодинамики тепловая энергия без каких-либо внешних воздействий может переходить только с высокого температурного уровня на более низкий для осуществления теплонасосного цикла необходимо использовать приводную энергию. Поэтому процесс передачи энергии в направлении противоположном естественному температурному напору осуществляется в круговом цикле. В качестве примера приведена схема паровой холодильной машины где рабочим веществом служит кипящая при низкой температуре жидкость названная хладагентом так как она уже в течение многих лет применяется в холодильных установках.
Энергоносители поставляющие тепловую энергию с низкой температурой для осуществления теплонасосного цикла называют источниками теплоты. Они отдают тепловую энергию путем теплопередачи конвекции и (или) излучения. Энергоносители воспринимающие в теплонасосном цикле тепловую энергию повышенного потенциала называют приемниками тепла. Они воспринимают тепловую энергию путем теплопередачи конвекции и (или) излучения. Энергоноситель служащий источником теплоты поступает в испаритель где испаряется жидкий хладагент. Теплота испарения необходимая для этого отбирается от источника тепла так как испарение хладагента происходит при низкой температуре.
В круговом цикле пары испарившегося хладагента всасываются компрессором и сжимаются до высокого давления. При сжатии их температура повышается что создает возможность отдачи тепловой энергии теплоприемнику.
Пары хладагента при повышенном давлении поступают в конденсатор через который протекает энергоноситель служащий приемником тепла. Его температура ниже температуры паров хладагента при повышенном давлении. При конденсации пара выделяется тепловая энергия воспринимаемая теплоприемником. Из конденсатора жидкий хладагент через регулирующий вентиль (дроссельный клапан) поступает обратно в испаритель и круговой цикл замыкается. В регулирующем вентиле высокое давление при котором находится хладагент на выходе из конденсатора снижается до давления в испарителе. Одновременно снижается его температура.
Таким образом с помощью теплового насоса возможна передача тепловой энергии от источника теплоты с низкой температурой к приемнику теплоты с высокой температурой при подводе извне механической энергии для привода компрессора (приводной энергии). Схема холодильной машины и теплового насоса отличается только назначением.
К холодильным машинам относится оборудование которое позволяет осуществить отбор тепловой энергии от тел с температурой ниже температуры окружающей среды (т.е. производство холода). Если требуется получить определенное количество теплоты с высокой температурой или одновременно и теплоты и холода такое оборудование относят к тепловым насосам.
Теплопроизводительность (тепловая мощность) теплового насоса складывается из двух составляющих: теплоты полученной испарителем от источника теплоты (так называемой холодопроизводительности Q0) и приводной мощности Р с помощью которой полученная тепловая энергия поднимается на более высокий температурный уровень.
Отсюда можно дать следующее определение тепловым насосам:
«Тепловой насос представляет собой устройство воспринимающее тепловой поток при низкой температуре (на холодной стороне) а также необходимую для привода энергию и использующее оба потока энергии при повышенной (по сравнению с холодной стороной) температуре в виде теплового потока».
Это определение действительно для компрессионных тепловых насосов а также для абсорбционных и термоэлектрических насосов использующих эффект Пельтье.
В абсорбционном тепловом насосе механический компрессор заменен термическим в виде дополнительного циркуляционного контура раствора с генератором (кипятильником) и абсорбером. Вместо электрической приводной энергии подводимой к компрессионным тепловым насосам с электроприводом к генератору подводят тепловую энергию. Однако для обоих процессов используются с помощью испарителя источники энергии в виде отработанной теплоты или энергии окружающей среды.
Обычно в процессе преобразования энергии энергия окружающей среды является конечным этапом процесса. Энергия выделяемая при сжигании твердого топлива или в ядерных реакторах проходит большое число преобразований пока принимает необходимую для потребителя форму полностью используется и наконец практически всегда переходит в энергию окружающей среды.
Тепловые насосы требуют совершенно иного теоретического подхода. Здесь в начале процесса в качестве источника теплоты наряду с приводной энергией используется также и энергия окружающей среды.
В настоящее время отопление и горячее водоснабжение городских объектов осуществляется как правило от централизованных систем теплоснабжения. Источником тепловой энергии в таких системах являются городские ТЭЦ на которых осуществляется комбинированная выработка электроэнергии и тепла или районные котельные. Преимущества централизованного теплоснабжения широко признаны. С термодинамической точки зрения комбинированное производство электроэнергии и тепла на ТЭЦ является гораздо более эффективным чем раздельное производство электроэнергии на конденсационных тепловых электростанциях и тепла котельными.
Вместе с тем применение централизованных систем теплоснабжения имеет свои недостатки и ограничения. Строительство протяженных теплотрасс к удаленным объектам а также к объектам в районах с малой плотностью застройки сопряжено со значительными капитальными вложениями и большими тепловыми потерями на трассе. Их эксплуатация впоследствии также требует больших затрат. Серьезные проблемы возникают и при реконструкции существующих объектов и строительстве новых в обжитых городских районах с плотной застройкой. В этих случаях увеличение тепловых нагрузок создает для застройщика часто непреодолимые трудности в том числе финансовые при получении и реализации технических условий на подключение к районной тепловой сети.
Действующие в настоящее время тарифы на тепловую энергию в сочетании с затратами на подключение к городским тепловым сетям заставляют все чаще задумываться над альтернативными способами теплоснабжения.
Принцип работы ТНУ: в испарителе теплового насоса тепло невысокого температурного потенциала отбирается от некоего источника низкопотенциального тепла и передается низкокипящему рабочему телу теплового насоса. Полученный пар сжимается компрессором. При этом температура пара повышается и тепло на нужном температурном уровне в конденсаторе передается в систему отопления и горячего водоснабжения. Для того чтобы замкнуть цикл совершаемый рабочим телом после конденсатора оно дросселируется до начального давления охлаждаясь до температуры ниже источника низкопотенциального тепла и снова подается в испаритель. Таким образом тепловой насос осуществляет трансформацию тепловой энергии с низкого температурного уровня на более высокий необходимый потребителю. При этом на привод компрессора затрачивается механическая (электрическая) энергия. При наличии источника низкопотенциального тепла с более или менее высокой температурой количество тепла поставляемого
потребителю в несколько раз превышает затраты энергии на привод компрессора. Отношение полезного тепла к работе затрачиваемой на привод компрессора называют коэффициентом преобразования теплового насоса и в наиболее распространенных теплонасосных системах он достигает 3 и более.
В качестве низкопотенциального источника тепла можно использовать грунтовые воды стоки речную и морскую воду низкопотенциальные источники тепла на электростанциях градирнях. Особенно тепловой насос является выгодным при высокой цене на топливо и относительно низкой цене на электроэнергию. Такая ситуация имеет место в многих европейских странах где основная часть электроэнергии вырабатывается на АЭС и ГЭС.
3 Выбор схемы и расчет цикла теплонасосной установки
3.1 Выбор схемы теплонасосной установки
Для теплонасосной установки (ТНУ) целесообразно будет применить цикл холодильной машины с регенеративным теплообменником. В этой схеме пар рабочего вещества выходящий из испарителя (маслоохладителя) в состоянии 7 (рисунок 1.1) направляется в регенеративный теплообменник где он нагревается за счет более теплого рабочего вещества выходящего из конденсатора которое при этом охлаждается. В результате регенерации эффективность установки увеличивается.
Рисунок 1.1 – Схема ТНУ и ее цикл в Ts и pi – диаграммах.
3.2 Исходные данные
Среда потребителя: вода;
Утилизируемая среда : масло И-40;
Параметры среды потребителя :
t1п =550С – температура на входе в ТНУ;
t2п =750С – температура на выходе из ТНУ;
Параметры утилизируемой среды :
t1у = 570C – температура на входе в испаритель (маслоохладитель);
t2у = 500C – температура на выходе из испарителя;
Необходимые значения КПД:
s = 08 – адиабатный КПД.
мех = 097 – механический КПД;
дв = 095 – КПД двигателя;
Определение расчетных температур:
tи = t1у –12 = 57 – 12 = 450C;
tк = t2п + 5 = 75 + 5 = 800С;
t1 = tи + 10 = 45+ 10 = 550С;
t4 = t1п + 10 = 55 + 10 = 650С;
Определение энтальпий:
i2 = (i2s – i1)s + i1 = (478– 454)08 + 454 = 484 кДжкг
Таблица 1.1 – Характеристики в расчетных точках
3.3 Определение удельных параметров цикла
Удельная тепловая нагрузка на конденсатор:
Удельная тепловая нагрузка на переохладитель конденсата:
Удельная тепловая нагрузка на регенеративный теплообменник:
Удельная тепловая нагрузка на испаритель:
Удельная адиабатная работа компрессора:
Удельная работа компрессора:
3.4 Определение режимных параметров ТНУ
Массовый расход хладагента:
Тепловая нагрузка на конденсатор:
Qкд = ma qкд = 036 179 = 64.44 кВт;
Тепловая нагрузка на переохладитель конденсата:
Qпк = ma qпк = 036 21 = 7.56 кВт;
Теплопроизводительность:
QТ = Qкд +Q пк = 64.44+7.56=72 кВт;
Тепловая нагрузка на регенеративный теплообменник:
Qрт = ma qрт = 036 10 = 3.6 кВт;
Адиабатная мощность компрессора:
Мощность компрессора:
Мощность подведенная к компрессору:
Потребляемая мощность:
Nпр = Ne дв =11.13 095 = 1172 кВт.
Коэффициент преобразования ТН:
φ = QтNпр = 721172= 614
Массовый расход потребителя через ТН:
4 Расчет теплопритоков отапливаемого помещения.
4.1 Расчет толщины изоляции
Задаемся следующими размерами помещения 60х24х6 м. Следовательно:
– площадь помещения1440 м2
– объем помещения 8640 м3
Расчет толщины изоляции наружной стены цеха с северной стороны:
Рисунок 1.2 – Конструкция стены
Действительный коэффициент теплоотдачи:
Для каждого материала выбираем соответствующие коэффициенты теплопроводности и толщины:
Для внутренних поверхностей стен отапливаемых помещений
Для наружных поверхностей стен
4.2 Расчет коэффициента теплоотдачи окон цеха
Рисунок 1.3 – Конструкция окна
Для внутренней поверхности окон
Для наружной поверхности окон
Действительный коэффициент теплоотдачи:
4.3 Расчет коэффициента теплоотдачи дверей цеха
Для материала (сталь) соответствующий коэффициент теплопроводности и толщины:
Для внутренней поверхности двери
Для наружной поверхности двери
4.4 Расчет изоляции для покрытия цеха
Рисунок 1.4 – Конструкция покрытия
Для внутренних поверхностей потолка
Для наружных поверхностей бесчердачных покрытий
4.5 Расчет толщины изоляции для пола:
Рисунок 1.5 – Конструкция пола
Для поверхностей пола
4.6 Расчет теплопритоков через ограждение
Теплоприток через ограждения можно найти по формуле:
где Q1T – теплоприток обусловленный разностью температур в помещении и снаружи
Q1С – теплоприток обусловленный наличием солнечной радиации.
Найдем для каждой стены пола и покрытия эти составляющие теплопритока через ограждение:
Теплоприток от разности температур:
Суммарный теплоприток от разности температур:
Теплоприток от солнечной радиации:
где – условная разность температур:
Суммарный теплоприток от солнечной радиации:
Суммарный теплоприток через ограждение:
4.7 Расчет вентиляционного теплопритока
Вентиляционный теплоприток можно найти по формуле
Принимаем число рабочих в помещении 25 человек.
Вентиляционный теплоприток в помещении:
4.8 Расчет эксплуатационных теплопритоков
Теплоприток эксплуатационный можно найти по такой формуле:
Теплоприток от освещения:
где А – количество тепла выделяемого на 1 м2 пола (для производственных помещений 45 Втм2);
F – площадь помещения м2
Теплоприток от работающих людей:
где – тепловыделение от 1 человека (при тяжелой физической работе 350 Вт);
– число людей работающих в данном помещении.
Теплоприток от оборудования принимаем Вт
Теплоприток от открывания дверей:
где – удельный приток тепла от открывания дверей Втм2;
– площадь пола помещения м2.
Суммарный эксплуатационный теплоприток:
4.9 Суммарные теплопритоки
Тепловая нагрузка на оборудование:
Тепловая нагрузка на компрессор:
5 Расчет компрессора теплонасосной установки
5 1. Описание проектируемого компрессора
Проектируемый компрессор – холодильный поршневой одноступенчатый непрямоточный двухцилиндровый вертикальный с блок-картерным исполнением простого действия безкрейцкопфный со встроенным электродвигателем бессальниковый со свободно-принудительной системой смазки (смазка от насоса и разбрызгиванием) стационарный со среднетемпературным режимом работы фреоновый средней холодопроизводительности.
Смазка механизма движения осуществляется как с помощью разбрызгивания так и с помощью шестеренчатого маслонасоса.
Норма расхода смазки для цилиндров составляет . Применяются масла типа ХФ-22-18.
В компрессоре применяются тронковые алюминиевые поршни клапаны на всасывании и нагнетании приняты согласно расчетам – полосовые.
Охлаждение цилиндров – парами холодильного агента (R22). Пар через всасывающий патрубок проходит через электродвигатель охлаждая его гильзу и затем идет на всасывание. Место посадки уплотнено специальными паранитовыми прокладками.
Ротор электродвигателя выполняет роль маховика. Маховик в свою очередь является аккумулятором энергии поршневого компрессора позволяющим преодолеть инерцию механизма движения в мертвых точках.
Маслонасос шестеренчатый встроенного типа. Масло после маслонасоса подается на смазку в пары трения через сверление в валу и шатуне. При этом перед попаданием в маслонасос оно проходит фильтр грубой очистки.
Подшипниковые опоры – шариковые двухрядные.
5.2 Термодинамический расчет холодильного компрессора
Холодильный агентR142
Охлаждение цилиндровпарами холодильного агента
Исполнениебессальниковый
Холодопроизводительность
Для рабочего цикла определяем отношение давлений:
Определяем удельную массовую холодопроизводительность:
Определяем удельную объемную холодопроизводительность:
Определяем коэффициент подачи компрессора на рабочем режиме:
Задаемся величиной тогда
где – компрессия на нагнетании
Коэффициент дросселирования:
где – компрессия на всасывании.
Коэффициент подогрева:
Находим действительную объемную производительность компрессора:
Находим теоретическую объемную производительность компрессора:
Для рабочего цикла определяем мощность электродвигателя в следующем порядке:
Для безкрейцкопфных фреоновых поршневых компрессоров индикаторный КПД принимается в пределах 071 084.
Адиабатную мощность компрессора определяем по формуле:
5.3 Определение геометрических размеров
Принимаем вертикальную двухрядную схему компрессора.
Для непрямоточных машин примем величину . Значение средней скорости поршня для безкрейцкопфных поршневых компрессоров должна лежать в пределах от 25 до 45 мс. Ход поршня принимаем и частоту вращения коленвала тогда
Определяем диаметр поршня ступени:
Принимаем D =110 мм.
Приближенно диаметр шейки коленвала изготовленного из стали 40Х можно определить по формуле:
Крутящий момент можно найти по формуле:
Для стали 40Х вид термообработки улучшение допустимое касательное напряжение составляет
Отсюда можно найти касательное напряжение при кручении:
где k – коэффициент запаса прочности (k = 2 3)
Подставим эти значения в выражение для диаметра коренной шейки :
Диаметр шейки коленвала:
Относительная длина шатуна:
Масса поступательно движущихся частей определяем по найденному значению пользуясь графиком [1] риc. 31.
5.4 Газодинамический расчет компрессора
5.4.1. Расчет полосового клапана
Скорость холодильного агента в клапанах:
где – средняя скорость поршня.
Допустимая скорость хладагента в седле и розетке клапанов: всасывающего принимаем ; нагнетательного принимаем .
Скорость звука в клапанах:
При проектировании клапанов должно выдерживаться условие:
Условие выполняется.
Эквивалентная площадь клапана
где – коэффициент расхода щели;
– коэффициент сопротивления щели полосового клапана.
Площадь проходного сечения щели:
Принимаем ширину щели .
Требуема длина щели:
Принимаем 6 щелей по
5.4.2 Расчет нагнетательного патрубка
Скорость холодильного агента в нагнетательном патрубке:
Принимаем для нагнетательного патрубка ([1] табл. 5.2).
Диаметр нагнетательного патрубка:
3. Расчет всасывающего патрубка
Скорость холодильного агента во всасывающем патрубке:
Принимаем для всасывающего патрубка .
Диаметр всасывающего патрубка:
5.4.4 Выбор электродвигателя
Мощность электродвигателя:
Выбираем электродвигатель асинхронный серии 4А закрытый обдуваемый (ГОСТ 19523-81).
Мощность электродвигателя типоразмер 4А225М4У3
Технические характеристики:
Холодильный коэффициент поршневого компрессора равен:
5.5 Динамический расчет компрессора
Динамический расчет компрессора ведем с помощью программного обеспечения TURBO PASCAL 7.0:
p1 кПа p2 кПа am D м S м nO обмин
lambdaR n m ms кг Nинд кВт ETAмех
(все силы в кH углы в градусах )
модуль Fтр.пс = 0.288 Fтр.вр = 0.192 Pr.2= 5.702
альфа= 0.0 x=0.0000 Pg1= -13.304
J= 1.812 Pсум= -5.502 N= 0.000
дельта= 0.0 Pшат= -5.502 T= 0.000 Z= -5.502
альфа= 21.9 x=0.0035 Pg1= -5.702
J= 1.620 Pсум= 1.908 N= 0.142
дельта=26.1 Pшат= 1.903 T= 0.837 Z= 1.708
альфа= 20.0 x=0.0030 Pg1= -6.303
J= 1.651 Pсум= 1.338 N= 0.091
дельта=23.9 Pшат= 1.335 T= 0.541 Z= 1.220
альфа= 40.0 x=0.0113 Pg1= -5.702
J= 1.209 Pсум= 1.497 N= 0.191
дельта=47.3 Pшат= 1.485 T= 1.091 Z= 1.008
альфа= 60.0 x=0.0236 Pg1= -5.702
J= 0.604 Pсум= 0.892 N= 0.152
дельта=69.7 Pшат= 0.879 T= 0.824 Z= 0.305
альфа= 80.0 x=0.0379 Pg1= -5.702
J= -0.022 Pсум= 0.267 N= 0.052
дельта=90.9 Pшат= 0.261 T= 0.261 Z= -0.004
альфа=100.0 x=0.0521 Pg1= -5.702
J= -0.546 Pсум= -0.258 N= -0.050
дельта=110.9 Pшат= -0.253 T= -0.236 Z= 0.090
альфа=120.0 x=0.0646 Pg1= -5.702
J= -0.906 Pсум= -0.618 N= -0.105
дельта=129.7 Pшат= -0.609 T= -0.469 Z= 0.389
альфа=140.0 x=0.0741 Pg1= -5.702
J= -1.104 Pсум= -0.816 N= -0.104
дельта=147.3 Pшат= -0.810 T= -0.438 Z= 0.681
альфа=160.0 x=0.0800 Pg1= -5.702
J= -1.188 Pсум= -0.900 N= -0.061
дельта=163.9 Pшат= -0.898 T= -0.249 Z= 0.862
альфа=180.0 x=0.0820 Pg1= -5.702
J= -1.208 Pсум= -0.920 N= -0.000
дельта=180.0 Pшат= -0.920 T= -0.000 Z= 0.920
J= -1.208 Pсум= -1.496 N= -0.000
дельта=180.0 Pшат= -1.496 T= -0.000 Z= 1.496
альфа=200.0 x=0.0800 Pg1= -5.872
J= -1.188 Pсум= -1.647 N= 0.112
дельта=196.1 Pшат= -1.643 T= 0.455 Z= 1.578
альфа=277.1 x=0.0400 Pg1= -13.292
J= -0.107 Pсум= -7.985 N= 1.555
дельта=266.0 Pшат= -7.833 T= 7.814 Z= 0.541
альфа=220.0 x=0.0741 Pg1= -6.437
J= -1.105 Pсум= -2.128 N= 0.271
дельта=212.7 Pшат= -2.110 T= 1.141 Z= 1.775
альфа=240.0 x=0.0646 Pg1= -7.583
J= -0.906 Pсум= -3.076 N= 0.525
дельта=230.3 Pшат= -3.031 T= 2.332 Z= 1.936
альфа=260.0 x=0.0521 Pg1= -9.772
J= -0.546 Pсум= -4.905 N= 0.948
дельта=249.1 Pшат= -4.812 T= 4.494 Z= 1.720
альфа=280.0 x=0.0379 Pg1= -13.304
J= -0.022 Pсум= -7.912 N= 1.529
дельта=269.1 Pшат= -7.763 T= 7.762 Z= 0.128
альфа=300.0 x=0.0236 Pg1= -13.304
J= 0.604 Pсум= -7.287 N= 1.244
дельта=290.3 Pшат= -7.180 T= 6.734 Z= -2.492
альфа=320.0 x=0.0113 Pg1= -13.304
J= 1.209 Pсум= -6.681 N= 0.852
дельта=312.7 Pшат= -6.627 T= 4.868 Z= -4.496
альфа=340.0 x=0.0030 Pg1= -13.304
J= 1.650 Pсум= -6.240 N= 0.426
дельта=336.1 Pшат= -6.225 T= 2.524 Z= -5.691
альфа=360.0 x=0.0000 Pg1= -13.304
J= 1.812 Pсум= -6.078 N= 0.000
дельта=360.0 Pшат= -6.078 T= 0.001 Z= -6.078
5.6 Прочностные расчеты
5.6.1. Поверочный расчет днища поршня
Днище поршня рассчитываем как круглую плиту заделанную по периметру.
Расчетное напряжение изгиба:
где – максимальное избыточное давление;
– радиус заделки днища поршня
5.6.2 Проверочный расчет поршневого пальца
Поршневой палец рассчитывается как балка на двух опорах с равномерно распределенной нагрузкой по длине шатунного подшипника.
Напряжение в пальце:
Максимальный изгибающий момент в среднем сечении пальца:
– соответствующие отрезки
Рисунок 1.6 – Поршневой палец
Момент сопротивления изгибу:
где ; – наружный и внутренний диаметр пальца.
Допустимое значение
где – коэффициент запаса;
– толщина пальца удовлетворяет прочностным характеристикам.
5.6.3 Прочностной расчет шатунных болтов
Шатунные болты проверяются на разрыв от максимальной силы инерции поршня и шатуна и усилия затяжки .
Разрывное напряжение равно:
Площадь наименьшего сечения болта:
Усилие от силы инерции шатуна:
Масса вращающейся части шатуна без крышки:
– угловая скорость вращения вала.
– из динамического расчета.
Для болтов стали 40Х:
Запас прочности что вполне допустимо.
5.7 Расчет противовесов
Для уравновешивания сил инерции (их момента) от поступательно движущихся частей первого порядка и момента сил инерции от вращающихся масс применяют противовесы.
Суммарная масса противовесов для двухколенного вертикального поршневого компрессора:
где – радиус кривошипа;
– расстояние между шатунами;
– радиус противовеса;
– расстояние между противовесами.
Масса вращающихся частей:
где – масса шатунной шейки;
т.к. – масса неуравновешенной части щеки;
– масса поступательно движущихся частей.
5.8 Проверочный расчет подшипников
При проектировании компрессора были приняты шарикоподшипники радиальные сферические двухрядные 1310 ГОСТ 28428-90 (средняя серия самоустанавливающиеся).
– динамическая грузоподъемность подшипника;
По динамическому расчету определяем положение при котором силы и достигают одновременно наибольших значений при .
Поскольку расстояние между опорами одинаковые то опоры нагружены одинаково:
Проверим предварительно принятые подшипники:
Эквивалентная нагрузка:
где – коэффициент безопасности [3] с.214;
– температурный коэффициент;
– при вращении наружного кольца.
По таблице 9.24 из [3] с.220 при и – срок службы подшипников: – для шарикоподшипников.
Требуемая динамическая грузоподъемность подшипника:
Получаем что следовательно подшипники подходят для данного компрессора.
6 Расчет горизонтального кожухотрубного конденсатора
6.1 Тепловой расчет конденсатора
Температура воды на входе: tw1 = 55оС
Температура воды на выходе: tw2 = 75оС
Температура фреона (R142b) на входе: tf1 = 103оС
Температура фреона на выходе: tf2 = 65оС
Массовый расход воды через конденсатор:
Температура конденсации холодильного агента в конденсаторе:
Среднелогарифмическая разность температур:
Принимаем основные размеры характеризующие теплопередающую поверхность конденсатора: шахматный пучек из медных труб со стандартным наружным оребрением:
– внутренний диаметр ;
– диаметр окружности выступов ;
– диаметр окружности впадин ;
– площади наружной поверхности 1м длинны трубы ;
– площади внутренней поверхности 1м длинны трубы ;
– коэффициент оребрения .
При средней температуре воды 650С:
– кинематическая вязкость воды ;
– число Прандтля Pr = 2.8;
– теплопроводность воды λ=06 ВтмК.
Предварительно задаем скорость воды в трубах конденсатора.
Число труб в одном ходе:
Принимаем и уточняем скорость воды:
– турбулентный режим течения;
Коэффициенты теплоотдачи со стороны воды:
Принимаем суммарное термическое сопротивление стенки трубы и загрязнений.
Плотность теплового потока:
Ориентировочное значение приняв тогда:
При распределении труб в трубной решетке в вершинах правильных шестиугольников и по сторонам правильных концентрических шестиугольников параметр m определяется следующим образом:
где m – число труб располагаемое по большей диагонали внешнего
S – горизонтальный шаг труб: S=13·dн=13·002=0026 м;
LD – длина трубы к диаметру трубы принимаем равным 5.
Округляем до ближайшего нечётного числа и принимаем nв = m = 11.
Коэффициент теплоотдачи со стороны конденсирующегося фреона отнесённый к внутренней поверхности труб:
где λ=00772 ВтмК - теплопроводность R142b при
=25710-4- динамическая вязкость R142b при tk Пас;
ρ = 923 – плотность R142b при tk кгм3;
r= 15404 – теплота конденсации R142b при tk кДжкг.
Уравнения плотности теплового потока.
Таблица 1.2 – Плотности тепловых потоков
Строим графики зависимостей тепловых потоков и от температуры:
Рисунок 1.7 – Графики зависимостей тепловых потоков и от температуры.
Из графика определяем: .
Более точно qвн находим по интернациональному выражению:
Общее число труб в аппарате:
Число ходов в аппарате по воде:
Внутренняя поверхность теплообмена:
Длина одной трубы в аппарате:
Внутренний диаметр аппарата:
где - число труб в наибольшей диагонали шестиугольника в трубной решетке.
6.2 Гидравлический расчёт
Гидравлическое сопротивление аппарата:
Суммарное гидравлическое сопротивление трения:
где- коэффициент течения в трубном пространстве при турбулентном режиме течения:
Суммарное местное гидравлическое сопротивление:
где - коэффициент местного сопротивления.
где - число входных камер в крышке испарителя
- коэффициент местного сопротивления входной камеры
- число выходных камер
- коэффициент местного сопротивления выходной камеры
- число поворотов потока рассола внутри трубной решетки на
- коэффициент местного сопротивления поворота на .
Тогда гидравлическое сопротивление аппарата:
Обечайка изготавливается из листовой стали сварная продольный стыковой шов выполненный ручной электродуговой сваркой. Коэффициент прочности сварного соединения . Допускаемые напряжения:
– нормативное для стали ВСт3сп ;
– для рабочего состояния ;
Исполнительная толщина стенки обечайки:
где – сумма всех прибавок толщины обечайки.
Ск=1 мм прибавка на коррозию или другой вид химического воздействия рабочей среды на материал.
Сэ=0 прибавка на эрозию учитывается тогда когда скорость движения среды в аппарате больше 20 мс.
Сд=07 дополнительная прибавка по технологическим соображениям.
С0=06 прибавка на округление размера.
6.4 Расчёт патрубков
Расчет проводим исходя из уравнения неразрывности:
Патрубки для холодильного агента:
Скорость на входе w=15 мc; плотность на входе ρ=1057 кгм3; расход фреона G=036кгс.
Скорость на выходе w=2 мc; плотность на входе ρ=848 кгм3 ; расход фреона G=036 кгс.
6.5 Расчет эллиптического днища
Расчётное давление Ртр = 04 МПа температура Т = 338 К.
В днище имеются два отверстия диаметром d=32 мм для входа и выхода охлаждающей воды расположение симметрично относительно центра днища.
Коэффициент ослабления днища отверстиями:
где Dвн = 028 м – внутренний диаметр днища.
Исполнительную толщину эллиптического днища (крышки ) определяем по формуле:
В нашем случае даёт малую величину. По технологическим причинам выбираем толщину днища дн = 5 мм т. е. равной толщине обечайки. Суммарная прибавка к толщине днища: прибавка для компенсации коррозии 2 мм; прибавка для компенсации минусового допуска 06мм; технологическая прибавка 09мм тогда Σс = 00035м.
Допускаемое давление в камере в рабочем состоянии:
Допускаемое давление при гидравлических испытаниях:
7 Расчет горизонтального кожухотрубного испарителя
7.1 Тепловой расчет испарителя
Холодопроизводительность Q0 = 100 кВт
Температура кипения хладагента t0 = 45 0C
Температура масла на входе: ts1 = 57оС
Температура масла на выходе: ts2 = 50оС
Площадь теплопередающей поверхности:
где k - коэффициент теплопередачи Вт(м2 К)
m - средний температурный напор 0С
Среднелогарифмическая разность температур равна:
Свойства масла при средней температуре:
– плотность ρ кгм3 865
– удельная теплоемкость сs кДж(кг·К) 1.992
– теплопроводности λs Вт(м·К) 014
– кинематической вязкости s м2 с 27·10-6
– динамической вязкости s Па·с 29·10-5
– число Прандтля Prж 412629
Теплофизические свойства раствора принимаем из [3] табл. 8 с. 10.
Принимаем основные параметры характеризующие теплопередающую поверхность: трубы медные с накатными ребрами диаметром 20х3 мм. Размеры профиля ребер: внутренний диаметр dвн =133 мм диаметр по окружности ребер dр =206 мм диаметр по окружности впадин dвп = 176 мм шаг ребер sp = 15 мм толщина у вершины ребра = 04 мм угол между ребрами α = 300 ([2] c. 333).
Коэффициент оребрения трубы:
Принимаем скорость масла в трубах равной = 15 мс. Тогда число труб в одном ходе аппарата равна:
Принимаем n1 = 9 тогда скорость масла равна:
Определяем режим движения раствора:
Режим движения раствора ламинарный тогда число Нуссельта равно:
где ldвн - отношение длины трубы на внутренний диаметр.
При интервале 150 ≤ ldвн ≤ 300 принимаем ldвн =150 тогда:
Тогда коэффициент теплоотдачи со стороны масла равен:
Плотность теплового потока со стороны масла:
где i λi - термическое сопротивление загрязнений и медной трубки с накатными ребрами i λi = 02 03 ·10-3 (м2· К )Вт.
Принимаем iλi = 025 ·10-3 (м2· К )Вт. Тогда:
Плотность теплового потока со стороны рабочего вещества отнесенного к внутренней поверхности:
гдеp0 = 06 бар - давление кипения хладагента.
пр - коэффициент учитывающий влияние числа рядов труб по высоте пучка;
Согласно [2] с. 331 пр = 1.
Определим удельный тепловой поток в испарителе графоаналитическим методом. Строим зависимости плотности теплового потока со стороны масла qFs= f(s) и со стороны хладагента qFa= f(a) в интервале температур 0 ≤ a ≤ m и m ≤ s ≤ 0 соответственно (рисунок 1.8).
Из рисунка 1.8 видно что удельный тепловой поток равен qFвн = 3800 Втм2.
Внутренняя поверхность теплообмена в испарителе:
Рисунок 1.8 – Расчет плотности теплового потока
7.2 Конструктивный расчет испарителя
Принимаем размещение труб на плоскости трубной решетки по периметрам правильных шестиугольников.
Принимаем s = 27 мм.
Принимаем отношение длины труб к диаметру аппарата k = lD = 5.
Число труб размещенных по диагонали внешнего шестиугольника:
Внутренний диаметр обечайки:
C учетом неполного заполнения фреона в межтрубном пространстве испарителя принимаем Dвн = 500 мм.
Принимаем l=2500 мм.
Общее количество труб в испарителе:
Принимаем n = 180. Число ходов в аппарате:
Принимаем скорость фреона на входе в испаритель вх = 5 мс на выходе вых = 15 мс.
Диаметр парового патрубка на входе в испаритель:
где вх - удельный объем пара на входе в испаритель.
где x = 0225 - содержание паровой фазы фреона.
ρ' ρ'' - плотности жидкой и паровой фаз фреона ρ' =1.055 кгм3 ρ'' =26.94 кгдм3
Принимаем dвх = 50 мм.
Аналогично определяем диаметр выходного патрубка.
Удельный объем пара на выходе из испарителя вых = 0147 м3кг тогда:
Принимаем dвых = 50 мм.
Диаметр патрубков для хладоносителя:
Принимаем dхн = 30 мм.
7.3 Гидродинамический расчет испарителя
Местные сопротивления определяем по формуле Вейсбаха-Д'Арси:
где - коэффициент сопротивления.
Коэффициент сопротивления:
гдетр - коэффициент сопротивления жидкостного трения.
а - количество входных камер а = 10;
b - количество выходных камер b = 10;
c - количество поворотов потока раствора в крышках испарителя с = 8;
= 1 - коэффициент местного сопротивления внезапного сужения прохода;
= 05 - коэффициент местного сопротивления внезапного расширения прохода;
=2 коэффициент местного сопротивления поворота на 1800 внутри крышки при переходе из одного пучка трубок в другой.
Для ламинарного режима движения формула Пуазейля:
7.4 Прочностной расчет испарителя
7.4.1 Расчет обечайки
Диаметр обечайки Dвн м 05
Длина обечайки l м 25
Площадь теплообменной поверхности Fвн м2 263
Давление в межтрубном пространстве ([2] c. 389 табл. 4.16):
– расчетное рр МПа 078
Рабочее (расчетное) давление в трубном пространстве ртр МПа 04
Принимаем материал обечайки из стали Вст3сп по ГОСТ 380-94. Нормативное допускаемое напряжение стали Вст3сп * = 140 МПа ([2] с.391 табл. 4.17).
Допускаемое напряжение для рабочего состояния материала обечайки корпуса испарителя:
где – коэффициент учитывающий работу аппарата со взрыво- и пожароопасными продуктами =1 для фреонов.
з - коэффициент учитывающий вид заготовки для заготовок из проката з =1.
[]= 1 1 140 = 140 МПа
Допускаемые напряжения при гидравлических испытаниях:
гдет20 - минимальное значение предела текучести стали при 20 0С т20 = 210 МПа ([2] с.391 табл. 4.17).
[]и = 210 11 = 191 МПа.
Расчетная толщина обечайки:
где φ - коэффициент прочности сварочного шва для ручной электродуговой сварки φ = 095 ([6] с. 13 табл. 1.7)
с - прибавка к расчетной толщине стенки на коррозию мм.
Принимаем прибавку на коррозию с = 1 мм.
Расчетная толщина стенки в рабочем состоянии равна:
Давление при гидравлическом испытании равно: pи = 13 · pр = 13 · 078 = 101 МПа.
Расчетная толщина стенки при гидравлическом испытании:
Согласно [6] табл. 25 принимаем исполнительную толщину стенки s = 5 мм.
Допускаемое давление в рабочем состоянии:
Условие прочности: [p] = 132 МПа > рр =078 МПа – выполняется.
Допускаемое давление при гидравлическом испытании:
Условие прочности: [p]и = 18 МПа > ри =101 МПа – выполняется.
Применимость расчетных формул: (s - c)Dвн = (5-1) 500 = 0008 01 - условие применимости выполняется.
7.4.2 Расчет эллиптического днища
Материал днища изготавливаем из стали Вст3сп по ГОСТ 380-94.
Расчетная толщина стенки днища:
где с1 - прибавка к коррозии материала стенки днища.
φ=1 - Так как днище изготовлено из цельного материала.
С учетом прибавки толщины для компенсации коррозии с1 = 15 мм.
Принимаем толщину стенки днища s1 = 5 мм.
Условие прочности: [p]тр =122 МПа > ртр =04 МПа - выполняется.
Давление при гидравлическом испытании равно: pи.тр = 13 · pтр = 13 · 04 = 052 МПа.
Условие прочности: [p]и.тр = 167 МПа > ри =052 МПа - выполняется.
Проверим применимость расчетных формул: (s1 - c1)Dвн = (5-15) 500 = 00044 01 - условие применимости выполняется.
7.4.3 Расчет трубной решетки
Трубную решетку изготавливаем из толстолистовой стали ВСт3сп. В отверстиях решетки закреплены развальцовкой 180 медных труб.
Минимальная конструктивная толщина трубной решетки:
где sтр = 3 мм толщина не оребренной части трубы.
Принимаем hт = 32 мм на участке под фланец hф = 25 мм так как толщины фланцев должны быть одинаковыми или близкими.
Схема развальцовки трубы показана на рисунке 1.9.
Рисунок 1.9 – Схема вальцовки трубы
Примем размеры пазов под вальцовку ([10] c. 640 табл. 25.4):
- расстояние между пазами: а = 15 · sтр = 15 · 3 = 45 мм принимаем а=5 мм;
- величина паза: b = sтр +1 = 3+ 1 = 4 мм;
- диаметр отверстия под трубу: d = (102 1016) · dтр = 102 · 20 = 204 мм;
- диаметр пазов: d1 = d + 02 · sтр + 05 = 204 + 02 · 3 + 05 = 215 мм
Рассмотрим трубную решетку как плоскую пластину на которую действует сила Р=00245 МПа. Тогда условно равномерно распределенная нагрузка действующая на всю поверхность пластины:
При значительной жесткости узла сварки обечайки и трубной решетки можно рассматривать ее как пластину защемленную по контуру.
Тогда максимальное напряжение возникающее на контуре пластины равно:
где r = 05· Dвн = 05 · 05 = 025 м.
φ0 - коэффициент ослабления пластины
Коэффициент ослабления пластины при числе отверстий на радиусе r равным nr = 8:
Напряжение в центре пластины:
где =03 – коэффициент Пуассона.
Максимальный прогиб трубной решетки:
где D0 - цилиндрическая жесткость пластины.
Проверим трубы на продольный изгиб. Гибкость теплообменной трубы:
rи - радиус инерции трубы.
Радиус инерции трубы:
Условие устойчивости трубы при осевом сжатии:
где ny = 15 - коэффициент устойчивости.
Критическое напряжение устойчивости по формуле Эйлера:
Условие устойчивости трубы выполняется. Укрепление труб не требуется.
8 Расчет регенеративного теплообменника
Регенеративный теплообменник (РТ) предназначен для переохлаждения жидкого хладагента выходящего из конденсатора холодными парами этого хладагента выходящими из испарителя. Он позволяет повысить удельную холодопроизводительность холодильной машины по сравнению с циклом без РТ и тем самым повысить её холодильный коэффициент.
8.1 Конструктивный расчёт
Задаёмся конструктивными размерами РТ. Кожух выполнен из цельнотянутой стальной трубы из стали 20 наружным диаметром Dн=0325 м и толщиной стенок к= 0008 м. Змеевик РТ выполнен из стальной трубки (Сталь 10) с наружным диаметром dн=0038 м и толщиной стенок зм=0002 м. Сердечник на который навивается змеевик выполнен из стальной трубы с наружным диаметром Dн=0219 м с толщиной стенок с=0006 м. Толщина дистанционной планки между сердечником и змеевиком принимается равной S=0004 м. Высота крышки кожуха hкр=015 м. Жидкий фреон R142b движется по змеевику а холодный пар противотоком движется по межтрубному пространству РТ.
Находим теплофизические свойства сред обменивающихся теплотой в РТ при их средних температурах:
Средняя температура равна Тж = 05 (Тж1 + Тж2) =05 (328 + 318)=323 К . По [9] табл.13 с.38 находим:
- плотность равна ρж=1041 кгм3;
- удельная теплоемкость сж=9897 кДжкг·К;
- коэффициент теплопроводности равен λж=00686 Втм К;
- коэффициент кинематической вязкости равен ж=0195·10-6м2с.
Средняя температура пара равна Тп=05(Тп1 + Тп2)=05(338 + 331)=3345 К:
- плотность равна ρп=3986 кгм3;
- удельная теплоемкость срп=565 кДжкг К;
- коэффициент теплопроводности равен λп=00078 Втм К;
- коэффициент кинематической вязкости равен п=1245·10-6м2с.
Определяем коэффициент теплоотдачи жидкого хладагента αх
Находим площадь прохождения трубки змеевика Fзм.
Её внутренний диаметр равен dвн=dн-2зм= 0038-2·0002= 0034 м.
Скорость жидкого R142b в трубке равна:
Находим критерии Рейнольдса:
Находим радиус закругления змеевика по осевой линии трубы сердечника:
Rзм = 05Dсн + S + 05 dн = 05·0219+0004+05·0038 = 01325 м.
Критическое число Рейнольдса соответствующее ламинарному режиму течения в трубке змеевика равно:
Критическое число Рейнольдса соответствующее турбулентному режиму течения в трубке змеевика равно:
Вывод: Rеж > Rекр.труб т.е. режим движения в трубке змеевика турбулентный.
Число Прандтля равно:
Число Нуссельта для турбулентного режима течения жидкого фреона R142b в трубке змеевика равно:
Nuж = 0021·Re08ж·Pr043ж·изг
где изг = 1+177= 1+177=1455 - поправка учитывающая влияние центробежного эффекта на процесс теплоотдачи со стороны жидкого R142b:
Nuж = 0021·6625608·293043·1455 = 349
Коэффициент теплоотдачи со стороны жидкого R142b равен:
Определяем коэффициент теплоотдачи со стороны паров R142b.
Внутренний диаметр кожуха РТ равен:
Dвн = Dн – 2к = 0325 – 2·0008 = 0309 м
Площадь межтрубного пространства по поперечному сечению РТ равна:
Скорость пара R142b в межтрубном пространстве РТ равна:
Находим критерий Рейнольдса:
т.е. режим движения пара в межтрубном пространстве – турбулентный.
Находим число Прандтля:
Число Нуссельта для турбулентного режима течения пара в межтрубном пространстве РТ равно [9] с.228:
Nuж = 023·Re065п·Pr033п = 023·48835065·36033 = 392
Коэффициент теплоотдачи со стороны пара R142b равен:
Поскольку в R142b хорошо растворяется масло на стенках змеевика отсутствует масляная пленка поэтому термическое сопротивление трубки змеевика равно термическому сопротивлению стенки стальной трубки.
Для стали 10 коэффициент теплопроводности равен:
Термическое сопротивление стенки трубки змеевика равно:
Коэффициент теплопередачи РТ равен:
Средняя логарифмическая разность температур при движении сред в РТ противотоком равна:
Площадь теплообменной поверхности РТ равна:
С учетом 20% запаса принимаем площадь теплообменной поверхности РТ равной:
Fпр = 12 Fр = 144 м2
Длина трубы змеевика РТ равна:
Число витков змеевика РТ равно:
Задаёмся шагом навивки змеевика на сердечник t = 005 м
Длина змеевика РТ равна:
Lзм = n·t = 15·005 = 075 м
Задаём односторонний припуск по длине трубы змеевика равным l=075 м
Длина теплообменной змеевиковой трубы с учетом припусков на входном и выходном её участки равна:
L1 = L+2l = 121+2·075 = 136 м
Длина кожуха РТ (без патрубков) равна:
Lк = Lзм·11 +2hкр = 075·11+2·015 = 1125 м
8.2Гидравлический расчёт
Определяем гидравлическое сопротивление змеевиковой трубы РТ. Задаёмся величиной шероховатости на внутренней стенке трубы Δ = 01мм = 00001м.
Коэффициент гидравлического трения определяем по формуле А.Д. Альтшуля для турбулентного режима течения жидкого R142b:
Потери давления на трении в змеевике находим по формуле Вейзбаха-Д’Арси:
Коэффициент местного сопротивления витка змеевика при повороте в нём потока на 3600 принимаем равным = 04 [11] с.248.
Местные потери давления в РТ находим по формуле Вейcбаха:
Общее гидравлическое сопротивление РТ по трубному пространству змеевика равно:
Δpзм = Δpтр + Δpм = 851+451 = 4039 Па
Определяем гидравлическое сопротивление РТ по межтрубному пространству. Принимаем что входной и выходной патрубки выполнены из стальной трубы с наружным диаметром dпн = 0089м и толщиной стенки п = 00045 м.
Внутренний диаметр патрубков равен:
dпвн = dпн - 2п = 0089 – 2·00045 = 008 м.
Площадь проходного сечения патрубков рана:
Скорость пара R142b в патрубках равна:
Потери давления на трение в межтрубном пространстве равны:
Δр’тр = 053nRe-0122·ρп2п = 053·15·48835-0122·398593·162=217 Па
Коэффициенты местного сопротивления входного и выходного патрубков в кожухе РТ принимаем равным = 15 [11] с.116 число патрубков n1=2.
Местные потери давления в патрубках кожуха РТ равны:
Общее гидравлическое сопротивление РТ по межтрубному пространству равно:
Δpмтр = Δp’тр – Δp’м = 217+1937 = 4107 Па
8.3 Прочностной расчёт
Трубу змеевика и кожух РТ проверяют на прочность гидравлическими испытаниями с запасом по величине давления 25% по отношению к рабочему значению давления.
Для трубки змеевика РТ давление испытаний равно:
pзм = 125 рк = 175 МПа
Для кожуха РТ давление испытаний равно:
pкож = 125 р0 = 075 МПа
Наибольшее напряжение в стенке кожуха РТ из стали 20 равны:
кoж max [] = 100 МПа для стали 20 даже с учетом 20% запаса по напряжениям из-за вареных в крышке патрубков т.е. условия прочности выполняется.
Наибольшее напряжение в стальной трубке змеевика РТ из стали 20 равны:
зм max [] = 100 МПа т.е. условие прочности выполняется.
9 Подбор вспомогательного оборудования
Выбор насоса для воды:
Массовый расход воды – масла –
По расходу подбираем два центробежных насоса марки 15К-819б(15К-6б) с диаметром рабочего колеса – 105 мм производительностью – 94 м3ч. КПД – 49 % и мощностью на валу насоса – 06 кВт табл.7.7 [Сверлов].
Выбор ресивера: объем линейного ресивера находим по формуле:
Выбираю линейный ресивер марки 075РВ по [сверлов явнель]. Обечайка ресивера выполнена из трубы диаметром 600х8 длиной 3190мм.ресивера – 430 кг.
Для предотвращения движения обратного потока фреона согласно правилам техники безопасности устанавливаем обратный клапан марки КН100 который предназначен для работы с давлением до 1.8 МПа.
Спецификация РТ.spw

Дистанционная планка
Эмаль ПФ-115 ГОСТ 6465
Грунт ГФ-021 ГОСТ 25129
Керосин технический КТ-1
Решетка трубная.cdw

экономика ТН.cdw

Показатели оборудования по стоимости
Показатели назначения
Теплопроизводительность установки
Годовая выработка теплоты
Температура на входе
Температура на выходе
Экономические показатели
Эксплуатационные затраты
- смазочные материалы
- заработная плата обслуживающего персонала
Годовой экономический эффект
Технико-экономические
теплонасосной установки
Технико-экономические показатели теплонасосной установки
Спецификация Испаритель.spw

Клапан предохранительный
Болт М16х80 ГОСТ 7796
Шайба 16.65Г ГОСТ 6402
Припой ПОС-30 ГОСТ 1499
Эмаль ПФ-115 ГОСТ 6465
Грунт ГФ-021 ГОСТ 25129
Керосин технический КТ-1
Спецификация КМ.spw

Компрессор фреоновый
Шатунно-поршневая группа
Указатель уровня масла
Прокладка регулировочная
Шпилька М8 ГОСТ22034
Бакелитовый лак ЛБС-1
Эмаль ПФ-115 ГОСТ 6465
Грунт ГФ-021 ГОСТ 25129
Керосин технический КТ-1
деталировка кд.frw

Материал для сварки: электрод УОНИИ 1355-4.0
Неуказанные предельные отклонения размеров
Неуказанные предельные отклонения размеров Н14
Шов N1 сварка ручная аргоно-дуговая проволока 1
Материал для сварки швов N2 электрод УОНИИ 1355-4.0
* Размеры для справок
Сварные швы контролировать УЗД или рентгенопросвечиванием в объеме:
по трубному пространству-25%
по межтрубному пространству-100%;
контролировать в соответствии с РД 26-11-01-85.
Корпус с трубчаткой
Материал для сварки швов N1 электрод УОНИИ 1355-4.0
Припой ПОС-30 ГОСТ 1499-70
Электрод УОНИИ 1355-4.0
Список литературы.docx
Е.М. Бамбушек Н.Н. Бухарин и др. Тепловые и конструктивные расчеты холодильных машин. – Л.: Машиностроение 1987 – 424 с.
Н.М. Чернавский. Курсовое проектирование деталей машин. – М.: Машиностроение 1989.
М.И. Френкель. Поршневые компрессоры. – Л.: Машиностроение 1969 – 743 с.
Техника низких температур под редакцией И.П. Усюкина. – М.: Пищевая промышленность 1977 – 244 с.
Холодильные компрессоры. Справочник под ред. А.В. Быкова и др. – М.: Легкая и пищевая промышленность 1981 – 279 с.
Методические указания к курсовому и дипломному проектированию «Расчет и выбор самодействующих клапанов объемных холодильных компрессоров». – Сумы: «Энергетика».
В.М. Арсеньев. Методические указания к курсовому проектированию объемных компрессоров «Термодинамический расчет поршневого холодильного компрессора». – Харьков: ХПИ 1984 – 10 с.
Данилова Г.Н. Богданов С.Н. и др. «Теплообменные аппараты холодильных установок» - Л.: Машиностроение 1986 – 303 с.
Михеев М.А. Михеева И.М. «Основы теплопередачи» - М.: Энергия 1973 – 320 с.
Идельчик И.Е. «Справочник по гидравлическим сопротивлениям» - М.: Машиностроение 1975 – 560 с.
Методичні вказівки до практичних занять на тему «Електробезпка. Розрахунок захисного заземлення та занулення» з курсу «Охорона праці в галузі» для студентів усіх спеціальностей денної та заочної форм навчання Суми СумДУ 2003.
Свечков И.Н. Ярославский А.М. Технология компессоростроения.-М.:Машиностроение1978.-200 с.ил.
Ястребова Н.А. Технология машиностроения: Учебник для студентов обучающихся по специальности «Холодильные и компрессорные машины и установки». – М.: Машиностроение 1987. – 336 с.: ил.
Методичні вказівки до виконання економічної частини дипломних проектів Укладачі: А.Ю. Жулавський О.М.Соляник. – Суми: Вид-во СумДУ 2007. – 48 с.
Робоча програма переддипломної практики студентів професійного напряму 0950 «Енергетика» спеціальностей 090520 «Холодильні машини та установки» та 090508 «Компресори пневмоагрегати та вакуумна техніка» для студентів денної форми навчання. Укладач доцент Ю.М.Вертепов СумДУ 2005 20 с.
Методичні вказівки до виконання дипломних проектів і дипломних робіт із спеціальностей 090520 «Холодильні машини та установки» та 090508 «Компресори пневмоагрегати та вакуумна техніка» для студентів денної форми навчання. Укладач доцент Ю.М.Вертепов СумДУ 2005 10 с.
Хайнрих Т. Найорк . Теплонасосные установки для отопления и горячего водоснабжения. – М.: Стройиздат 1985. – 351с.
ГОСТ 12.2.003-91 Оборудование производственное. Общие требования безопасности.
ГОСТ 12.2.016-81 Оборудование компрессорное. Общие требования безопасности.
ГОСТ 12.2.049-80 (2001) Оборудование производственное. Общие эргономические требования.
ГОСТ 12.1.004-91 ССБТ. Пожарная безопасность. Общие требования.
ГОСТ 12.1.005-88 Система стандартов безопасности труда. Общие санитарно-гигиенические требования к воздуху рабочей зоны.
СНиП II -4-79. Естественное и искусственное освещение + Изменение М.: Стройиздат 1980.-48 с
ГОСТ 14202 Трубопроводы промышленных предприятий.
ГОСТ 12.4.051-87. Система стандартов безопасности труда. Средства индивидуальной защиты органа слуха.
ГОСТ 12.1.019-79 (1996) ССБТ. Электробезопасность. Общие требования и номенклатура видов защиты.
ГОСТ 12.1.030-81. Электробезопасность. Защитное заземление. Зануление. Система стандартов безопасности труда.
ГОСТ 12.1.038-82 (2001) ССБТ. Электробезопасность. Предельно допустимые значения напряжений прикосновения и токов.
Спецификация Обечайка.spw

КМ прод.cdw

Рабочая среда - фреон (R142b).
Действительная объемная производительность V
Коэффициент подачи компрессора
Частота вращения коленвала п=24 с.
Давление всасывания р
давление нагнетания р
Эффективная мощность компрессора Ne=37.8 кВт.
Технические требования.
Регулирование величины линейного мертвого пространства осу-
ществляется с помощью паронитовых прокладок поз.16.
Перед пуском компрессора убедиться в правильности направления
После сборки коленчатый вал компрессора провернуть вручную и
убедится в отсутствии стуков и заеданий.
Перед пуском залить в картер масло до необходимого уровняпо
Уплотняющую поверхность прокладок перед сборкой присыпать
порошком черного графита ГЛ-3 ГОСТ 5279.
Момент затяжки шатунных болтов 147-167 Н
Поверхность клапанной доски перед сборкой уплотнить
Окраска наружных непокрытых поверхностей эмаль ПФ-115
ГОСТ 6465. Класс покрытия - VI
группа условий эксп-
*. Размеры для справок.
Обечайка испарителя.cdw

РТ.cdw

Рабочая среда в змеевике - жидкий R142b.
Рабочая среда в межзмеевиковом пространстве - пар R142b.
Мссовый расход хладагента 0
Давление пара R142b 0.6 МПа.
Давление жидкого R142b 1.4 МПа.
Проверка на прочность маслом в течение 10 минут:
-трубное пространство при давлении Р
-межтрубное пространство при давлении Р
течи и видимые деформации элементов
аппарата не допускаются.
Проверка на герметичность воздухом в течение 5 минут:
Негерметичность не допускается.
обнаруженые в процессе испытаний
с повторными испытаниями.
Перед монтажом продуть корпус сжатым воздухом.
Перед покраской поверхность обезжирить керосином.
Покрытие - Эмаль ПФ115 серая ГОСТ 6465.
Вход газообразного R142b
Выход газообразного R142b
Технологические требования
Таблица сварных швов
Рекомендуемые чертежи
- 01.07.2014
- 04.11.2022
- 20.09.2021
- 20.09.2021
- 20.09.2021
- 01.07.2014
Свободное скачивание на сегодня
- 29.08.2014