Привод механический




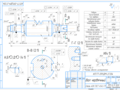

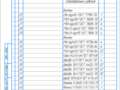
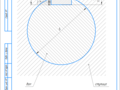
- Добавлен: 24.01.2023
- Размер: 5 MB
- Закачек: 0
Описание
Привод механический
Состав проекта
![]() |
![]() |
![]() |
![]() |
![]() |
![]() |
![]() |
![]() |
![]() |
![]() |
![]() |
![]() ![]() ![]() ![]() |
![]() ![]() ![]() ![]() |
![]() ![]() ![]() ![]() |
![]() ![]() ![]() ![]() |
![]() |
![]() ![]() ![]() ![]() |
![]() ![]() ![]() ![]() |
![]() ![]() ![]() ![]() |
![]() ![]() ![]() ![]() |
![]() ![]() ![]() ![]() |
![]() ![]() ![]() ![]() |
![]() ![]() ![]() ![]() |
![]() ![]() ![]() ![]() |
![]() ![]() ![]() ![]() |
![]() ![]() ![]() ![]() |
![]() ![]() ![]() |
![]() |
![]() ![]() ![]() ![]() |
![]() |
![]() ![]() ![]() ![]() |
![]() ![]() ![]() ![]() |
![]() ![]() ![]() ![]() |
Дополнительная информация
Колесо зубчатое.cdw

Степень точности по
Делительная толщина
Высота до хорды зуба
Обозначение чертежа
КП.ТТ-591.ДМ-3.7.003
Сталь 40Х ГОСТ 4543-71
кафедра "Машиноведение
Стакан.cdw

Червячный вал.cdw

Высота до хорды витка
КП.ТТ-591.ДМ-3.7.007СБ
обеспеч. инструментом
Сталь 40Х ГОСТ 4543-71
кафедра "Машиноведение
Вал.cdw

Сталь 45 ГОСТ 1050-88
кафедра "Машиноведение
Р.С подш.cdw

Тихоход. вал(изменён.).cdw

Стакан.cdw

Тихоход.вал.cdw

Элементы корпуса.cdw

Входной вал.cdw

Кр. подшипников.(стандартн).cdw

Р.С вала.cdw

Р.С. шпоночн. соед..cdw

Промежуточный вал.cdw

Курсовой.docx
Восточноукраинский национальный университет имени В. Даля
Кафедра «Машиноведение»
«ПРИВОД МЕХАНИЧЕСКИЙ»
Анализ технического задания
Поскольку кинематическая схема привода определена техническим заданием наметим лишь некоторые пути проектирования.
Во-первых в целях уменьшения габаритов привода принимаем к расчету клиноременную передачу с ремнями нормального сечения.
Во-вторых учитывая потенциальную возможность мелкосерийного или единичного изготовления данного привода его опорным элементом принимаем сварную раму.
В-третьих выбираем двигатель из трёхфазных асинхронных электродвигателей переменного тока с короткозамкнутых ротором серии 4А.
Выбор двигателя. Кинематический силовой и энергетический расчет двигателя
Мощность на выходном (четвёртом) валу привода:
где = – значения КПД клиноременной цилиндрической и червячной передач соответственно (табл. 2.1).
Потребная мощность на выходном валу двигателя:
По табл. 2.1 из ряда мощностей электродвигателей серии 4А принимаем ближайшее большее значение P = 55 кВт.
Ориентировочное передаточное число привода:
где – ориентировочные передаточные числа ременной цилиндрической и червячеой передач (табл. 2.1).
Ориетировочная частота вращения двигателя:
где - частота вращения выходного вала привода.
По табл. П4.1 для мощности Р=55 кВт ближайшую асинхронную частоту вращения к
имеет двигатель 4А100L2У3 у которого n=2880 мин.
Уточняем общее передаточное число привода (U) и передаточные числа каждой его ступени():
Оставим без изменения значения и .Определим передаточное число цилиндрической зубчатой передачи(U):
Окончательно принимаем:
Определяем кинематические силовые и энергетические параметры валов привода(так как потребная мощность на входе привода Р1=534 кВт меньше номинальной мощности принятого двигателя Р=55 кВт дальнейшие расчеты целесообразно вести именно по потребной мощности Р1).
Частоты вращения валов:
Крутящие моменты на валах:
Расчет передач привода
1 Расчет цилиндрической косозубой передачи
Перед началом проектирования передачи назначим следующие виды упрочнения:
Для зубьев шестерни - цементация для колеса- улучшение. Для этого примем материалы Сталь 18ХТГ и Сталь 40Х соответственно для шестерни и колеса.
1.1 Допускаемое контактное напряжение находим по формуле:
Найдём все входящие в неё неизвестные:
- предел длительной контактной выносливости МПа (табл. 3.1).
и - средние значения твёрдости в единицах Бринелля и Роквелла соответственно (табл. 3.1).
– коэффициент учитывающий шероховатость сопряженных поверхностей.
- коэффициент запаса прочности.
(неоднородная структура - цементация).
(однородная структура - улучшение).
- коэффициент долговечности.
где - базовое число циклов нагружений.
- эквивалентное число циклов нагружений.
- частота вращения шестерни и колеса (индексы 1 и 2).
Подставим найденные значения в формулу (1):
В дальнейшие расчеты берем меньшее из двух значений:
Таким образом искомое значение допускаемого контактного напряжения :
1.2 Допускаемое напряжение изгиба находим по формуле:
- предел длительной выносливости при изгибе МПа.
- коэффициент учитывающий шероховатость переходной поверхности.
- коэффициент запаса прочности при изгибе.
(нормальная вероятность неразрушения).
- базовое число циклов нагружений.
- эквивалентное число циклов напружений при изгибе.
Так как режим работы редуктора реверсивный более тяжелый то полученные значения и слудует уменшить на двадцать процентов:
1.3 Допускаемые максимальные напряжения при кратковременных перегрузках – контактные и изгиба :
1.4 Определение межосевого расстояния.
Из условия контактной выносливости активных поверхностей зубьев вычисляем межосевое расстояние :
Здесь - коэффициент зависящий от типа передачи (для косозубой передачи).
- коэффициент нагрузки (предварительное значение).
– крутящий момент на колесе .
- коэффициент ширины зубчатого венца.
По ряду стандартных межосевых расстояний ГОСТ 2185-66 принимаем
1.5 Определение основных параметров передачи.
1.5.1 Нормальный модуль зацепления:
Из стандартного ряда модулей ГОСТ 9563-80 принимаем
1.5.2 Ширина зубчатого венца колеса:
По ряду нормальных линейных размеров ГОСТ 6636-69 принимаем
1.5.3 Ширина зубчатого венца шестерни:
После округления до ближайшего числа из стандартного ряда
1.5.4 Предварительный угол наклона зубьев:
1.5.5 Число зубьев шестерни:
Ориентировочное значение:
Окончательно принимаем
1.5.6 Окончательное значение угла наклона зубьев:
1.5.7 Число зубьев колеса:
Окончательно принимаем При этом уточним передаточное число:
1.6 Проверочный расчёт на контактную выносливость:
Уточняем коэффициент нагрузки
- коэффициент учитывающий неравномерность распределения нагрузки между зубьями.
- коэффициент концентрации нагрузки вдоль линии контакта зубьев с учётом их приработки.
– коэффициент динамической нагрузки.
Окружная скорость в зацеплении:
где - делительный диаметр шестерни.
По таблице в п. 3.1.4 данной скорости соответствует 9-я степень точности. Однако учитывая что рассчитываемая передача находится в редукторе назначаем 8-ю степень точности. При этом из табл. 3.4 находим значение
По табл. 3.58 для начальный коэффициент нагрузки . При этом:
В результате коэффициент нагрузки составит:
Определяем коэффициенты:
– коэффициент учитывающий механические свойства материалов шестерни и колеса.
- коэффициент учитывающий геометрию поверхности зубьев.
- коэффициент учитывающий многопарность зацепления.
Для цилиндрических передач изготовленных из стали
где - торцовый коэффициент перекрытия.
1.7 Проверочный расчет на изгибную выносливость:
где r = 0828 – по табл. 3.6 для
Для нахождения коэффициента формы зубьев () найдём эквивалентные числа зубьев:
По таблице 3.7 (при коэффициентах смещения ) по найденным значениям эквивалентных чисел зубьев находим коэффициенты формы зубьев:
Коэффициент учитывающий влияние наклона зубьев ():
Выявим менее прочные по изгибу зубья:
Так как на изгибную выносливость проверим менее прочные зубья колеса:
1.8 Проверочный расчет на кратковременные перегрузки.
1.9 Геометрический расчет.
1.9.1 Делительные диаметры:
1.9.2 Диаметры вершин зубьев:
1.9.3 Диаметры впадин зубьев:
1.9.4 Постоянная хорда зуба
1.9.5 Высота до постоянной хорды зуба:
1.10 Расчёт сил в зацеплении.
1.10.1 Окружная сила:
1.10.2 Радиальная сила:
1.10.4 Суммарная сила в зацеплении:
2 Расчёт червячной передачи.
Перед началом проектирования передачи назначим в качестве материала червяка
Сталь 40Х и выберем закалку как способ его упрочнения. Для выбора материала червячного колеса найдём ориентировочное значение скорости скольжения () :
здесь - частота вращения червяка.
- крутящий момент на червячном колесе.
По табл. 3.10 скорости скольжения соответствуют чугуны СЧ18 и СЧ15 но для повышения КПД и значений допускаемых напряжений зададимся латунью ЛЦ23А6Ж3Мц2 с центробежным способом отливки. Для неё:
2.1 Допускаемые напряжения.
Так как материал червячного колеса имеет более низкие механические характеристики чем материал червяка допускаемые напряжения определяем по материалу колеса (табл. 3.11):
2.2 Определение межосевого расстояния.
Из условия контактной выносливости вычисляем межосевое расстояние :
Здесь число зубьев червячного колеса ( число заходов червяка ).
q - коэффициент диаметра червяка.
Предварительное значение:
Из ГОСТ 19672-74 выбираем окончательное значение
- коэффициент нагрузки(предварительное значение).
По ряду стандартных межосевых расстояний ГОСТ 2144-76 принимаем
2.3 Определение основных параметров передачи.
2.3.1 Модуль зацепления:
Из ГОСТ 2144-76 принимаем окончательное значение модуля
2.3.2 Коэффициент смещения червяка:
2.3.3 Начальный угол подъёма витков червяка:
2.3.4 Делительный угол подъёма витков червяка:
2.4 Проверочный расчёт на контактную выносливость:
- коэффициент концентрации нагрузки.
Для этого сначала уточним скорость скольжения червяка:
где начальный диаметр червяка.
Данной скорости скольжения соответствует девятая степень точности.
По табл. 3.4 для данной степени точности и скорости скольжения
здесь – коэффициент деформации червяка. По табл. 3.14
Для уточнения крутящего момента на колесе () уточним сначала КПД:
здесь КПД червячного зацепления.
приведеный угол трения в червячной передаче(табл. 3.15).
Коэффициенты потерь на перемешивание масла () и на трение в уплотнениях () находим с помощью рис.3.8:
Найденное значение следует пересчитать для частоты вращения червяка:
Тогда крутящий момент на колесе:
2.5 Проверочный расчёт на изгибную выносливость:
здесь коэффициент нагрузки при изгибе.
окружная сила на делительной окружности червячного колеса Н.
делительный диаметр червячногоколеса.
Для нахождения коэффициента формы зубьев () найдём сначала эквивалентное число зубьев червячного колеса:
Теперь по табл. 3.7
2.6 Проверка зубьев червячного колеса по кратковременным перегрузкам.
2.7 Проверка вала червяка на жесткость:
2.7.1 По упругому прогибу червяка по середине его нарезанной части:
здесь допустимое значение упругого прогиба.
суммарная сила в поперечной плоскости червяка. В неё входят:
окружная сила на червяке.
L – расстояние между опорами вала. На данном этапе воспользуемся приближенной зависимостью:
осевой момент инерции поперечного сечения червяка.
2.7.2 По углу поворота оси вала в зоне расположения подшипников:
Так как наименьшее допустимое значение угла поворота . для подшипников 2000 и 7000 больше полученого значения то условие
выполняется для всех типов подшипников.
2.8 Проверка червячной передачи по критерию теплостойкости:
Здесь мощность на червяке.
допустимая температура масла.
температура воздуха.
коэффициент теплоотдачи.
коэффициент учитывающий теплоотвод через лапы редуктора.
Площадь свободной поверхности () на данном этапе проектирования неизвестна. Воспользуемся зависимостью справедливой для одноступенчатых червячных редукторов. Если при данном значении площади критерий теплостойкости будет выполняться то он будет выполняться и для двухступенчатого редуктора площадь свободной поверхности которого больше:
2.9 Полный геометрический расчёт червячной передачи.
2.9.1 Геометрические параметры червяка.
2.9.1.1 Делительный диаметр:
2.9.1.2 Начальный диаметр:
2.9.1.3 Диаметр вершин витков:
2.9.1.4 Диаметр впадин витков:
2.9.1.5 Длинна нарезанной части червяка:
Полученное значение округляется до из ряда нормальных линейных размеров ГОСТ 6636-69.
2.9.1.6 Делительная толщина по хорде витка:
2.9.1.7 Высота до хорды витка:
2.9.1.8 Радиус закругления вершин витков (осевая плоскость):
2.9.1.9 Радиус закругления впадин витков (осевая плоскость):
2.9.2 Геометрические параметры червячного колеса:
2.9.2.1 Делительный диаметр:
2.9.2.2 Диаметр вершин зубьев:
2.9.2.3 Наибольший диаметр колеса:
2.9.2.4 Диаметр впадин зубьев:
2.9.2.5 Ширина зубчатого венца:
2.9.2.6 Радиус закругления вершин зубьев в осевой плоскости колеса:
2.9.2.7 Радиус закругления впадин зубьев в осевой плоскости колеса:
2.9.2.8 Радиус закругления вершин зубьев в торцевой плоскости колеса:
2.9.2.9 Радиус закругления впадин зубьев в торцевой плоскости колеса:
2.10 Расчёт сил в зацеплении.
2.10.1 Окружная сила на червяке равная осевой силе на колесе :
2.10.2 Окружная сила на колесе равная осевой силе на червяке :
2.10.3 Радиальная сила:
2.10.4 Суммарная сила в зацеплении:
3 Расчёт клиноременной передачи с ремнями нормальных сечений по ГОСТ 1284.1-80 ГОСТ 1284.3-80.
3.1 Выбор сечения ремня:
По номограмме рис. 3.13 выбираем сечение клинового ремня:
для и подходит ремень сечения А основные параметры которого (табл. 3.21 и рис. 3.14):
3.2 По стандартному ряду выбираем расчётный диаметр меньшего шкива так чтобы Принимаем
3.3 Расчётный диаметр большего шкива:
Расчётное значение округляем до ближайшего стандартного значения
3.4 Уточняем передаточное число c учётом упругого скольжения:
3.5 Предварительное значение межосевого расстояния:
Коэффициент выбираем согласно рекомендаций на странице 65.
3.6 Находим длину ремня:
3.6.1 Предварительное значение:
3.6.2 Предварительное значение округляем до стандартног значения
3.7 Уточняем межосевое расстояние:
3.8 Определяем число ремней в передаче.
мощность на ведущем валу.
где номинальная мощность передачи с одним ремнём (табл. 3.25).
коэффициент учитывающий длину ремня (табл. 3.31).
коэффициент динамичности нагрузки и режима работы (табл. 3.32).
коэффициент учитывающий число ремней. Принимаем
Дабы повысить долговечность ремней и понизить напряжения в них примем сразу
3.9 Проверим прочность ремней по максимальным напряжениям:
Значение коэффициента учитывающего влияния центробежных сил выбираем из табл. 3.33 для сечения А.
Так как проектированная передача без автоматического натяжения значение следует увеличить в полтора раза:
3.10 Определение долговечности ремней.
3.11 Определение давления передачи на валы и опоры.
Разработка эскизного проекта редуктора
В соответствии с рекомендациями выбираем из атласов по деталям машин конструкцию цилиндрическо-червячного редуктора которую будем считать прототипом разрабатываемого редуктора. В качестве такого примем редуктор ЧЦ на рис.76 в . Разумеется что конструктивные решения отдельных его деталей и узлов будут изменены. Эти изменения будут отмечены в соответствующих разделах проекта.
1 Ориентировочный расчёт валов и разработка их предварительной конструкции.
1.1 Быстроходный вал (Рис.1).
1.1.2 За основу принимаем конструкцию вала-шестерни на рис.76 в .Так как в отличии от прототипа разрабатываемый вал будет иметь конический концевой участок расчётный диаметр относится в этом случае к цилиндрическому пояску концевого участка:
Принимаем по ряду нормальных линейных размеров ГОСТ 6636-69
1.1.3 Диаметр под уплотнение из резиновой манжеты выбираем из условия что Согласовав значение с размером манжеты ГОСТ 8752-79 принимаем
Основные размеры манжеты:
1.1.4 Диаметр вала под подшипником принимаем одинаковым в обеих опорах из условия что во-первых а во-вторых значение должно быть кратным пяти. Принимаем ближайшее число удовлетворяющее этим требованиям
По найденному значению и с учётом рекомендаций по выбору подшипников принимаем в обеих опорах подшипник роликовый конический однорядный 7206 ГОСТ 27365-87.
Основные параметры подшипника:
1.1.5 Диаметр буртика правого подшипника принимаем равным диаметру буртика левого подшипника:
1.1.6 Определение осевых размеров вала начнём с его концевого участка который выполнен коническим по ГОСТ 12081-72 исполнение 1 (табл. П11.2).Его основные размеры (мм):
Длина цилиндрического пояска концевого участка определяется графически после вычерчивания шкива с оставлением зазора и составляет =25 мм.
Из табл. П11.2 выпишем параметры шпоночного соединения которое образует концевой участок проектируемого вала со шкивом ременной передачи (мм):
здесь длинна ступицы ведомого шкива клиноременной передачи найденная графически.
При вычерчивании ступицы с коническим отверстием её торец с меньшим диаметром должен проходить по резьбовому участку вала (в данном случае - правый торец) а противоположный – на несколько миллиметров (принято 3 мм) не доходить до максимального диаметра конуса вала. Длина шпонки выбрана так чтобы во-первых она полностью помещалась на коническом участке вала а во-вторых – не выходила за торцы ступицы.
Выполним проверку прочности шпоночного соединения по напряжению смятия на плоских участка боковых граней:
уменьшенное на двадцать пять процентов значение в связи с переменным характером нагрузки.
Поскольку условие прочности шпоночного соединения не выполняется поставим на этом участке вала симметрично вторую шпонку таких же размеров. Значение при этом уменьшится вдвое:
Так как после установки второй шпонки условие прочности выполнилось других изменений в конструкцию вносить не требуется.
1.1.7 Продолжаем определение осевых размеров вала ведя его теперь от зубчатого венца к концевому участку. Длину буртика подшипника (в данном случае - и правого и левого) вычисляем через его высоту:
1.1.8 Длину подшипниковых шеек в данном случае определяет ширина внутреннего кольца подшипника ():
1.1.9 Длину вала под уплотнением определим графически после вычерчивания на нём подшипниковой крышки с добавлением минимального зазора :
здесь зазор образующийся между подшипниковой крышкой и внутренним кольцом подшипника.
Минимальный зазор равен толщине стенки корпуса :
Округлив до ближайшего целого значения получим = 9 мм.
Основные размеры подшипниковой крышки (Рис. 7):
Диаметр отверстия под вал:
Диаметр гнезда под манжету берём равным наружному диаметру манжеты (табл. П10.1):
Остальные размеры бёрем прямо из табл. П.9.2 ГОСТ 18512-73 (мм):
Ширина подшипниковой крышки:
Посадочный диаметр:
Диаметр окружности центров отверстий под винты:
Диаметр винтов – М6 количество – 4.
Для винтов М6 по ГОСТ 11738-84 высота головки Н = 5 мм. Длину стержня винтов L определим как сумму толщины фланца крышки и требуемую глубину завинчивания в чугун :
Окончательно принимаем ГОСТ 7808-70.
1.2 Промежуточный вал (Рис. 2 ).
1.2.1 Приняв за основу конструкцию вала червяка редуктора взятого нами в качестве прототипа начнем разработку его конструкции с участка вала под цилиндрическим колесом так как концевой участок на этом валу отсутствует:
1.2.2 Диаметр обоих подшипниковых шеек примем следующим большим значением кратным пяти:
По найденному значению и с учётом рекомендаций по выбору подшипников учитывая возможное тепловое удлинение принимаем установку вала с одной фиксирующей опорой (левой) и одной плавающей (правой).
Фиксирующей опорой будут служить два шарикових радиально-упорных подшипника 66309 ГОСТ 27365-87.Основные параметры подшипника:
В качестве же плавающей опоры примем подшипник шариковый радиальный однорядный 309 ГОСТ 27365-87.Основные параметры подшипника:
1.2.3 Диаметр буртика правого подшипника принимаем равным диаметру буртика левого подшипника:
1.2.4 Резьбовый участок вала () под круглую шлицевую гайку выбирается так чтобы диаметр вершин резьбы на валу был несколько меньше диаметра подшипниковой шейки (в противном случае напрессовка внутреннего кольца подшипника на вал будет невозможна).Этому условию отвечает резьба М4215 поэтому принимаем
Под эту резьбу подходит гайка М4215-6Н.05.05 ГОСТ 11871-88. Основные параметры:
1.2.5 Определение осевых размеров вала начнём с участка под зубчатым колесом:
здесь ширина венца зубчатого колеса равная длинне его ступицы.
минимальный зазор который обеспечивает дистанционное кольцо установленное между зубчатым колесом и подшипником.
Дадим некоторые объяснения к формуле для нахождения
Так как зубчатое колесо от осевого сдвига на валу будет предохранять концевая шайба закреплённая болтом размер делаем на несколько миллиметров (в нашем случае 2 мм) меньше суммы чтобы обеспечить зазор между шайбой и торцом вала для надёжного крепления колеса. В то же время дистанционное кольцо не должно соприкасаться одновременно с торцом подшипниковой шейки и внутренним кольцом подшипника. Поэтому длину правой подшипниковой шейки делаем на 2 4 мм (в нашем случае 2 мм) меньше размера подшипника 2309 а длину участка под колесом соответственно увеличиваем на такую же величину.
Основные размеры шайбы концевой ГОСТ 14734-69 мм:
Диаметр отверстия под штифт
Расстояние между центрами отверстий под болт и штифт
Из табл. П6.1 выпишем параметры шпоночного соединения которое образует участок проектируемого вала под цилиндрическим колесом с этим колесом (мм):
здесь ширина венца зубчатого колеса.
Длина шпонки выбрана так чтобы она полностью помещалась на участке вала под колесом.
1.2.6 Длина правой подшипниковой шейки:
Объяснения смотреть в пункте 4.1.2.5 данного проекта.
1.2.7 Длина левой подшипниковой шейки:
Здесь В – ширина внутреннего кольца подшипника.
минимальный зазор наличие которого обеспечиваем установкой на валу между подшипниками дистанционного кольца.
1.2.8 Длина резьбового участка бёрётся в зависимости от высоты гайки (Н):
1.2.9 Длину буртиков определяем графически. Начинаем вычерчивать вал червяка начиная с участка под колесом вычерчивая на нём само зубчатое колесо а также вал-шестерню входящую с ним в зацепление со всеми элементами. Далее выверчиваем подшипниковую шейку и сам подшипник правой опоры червячного колеса. Затем параллельно оси червяка на расстоянии 200 мм (межосевое расстояние червячной передачи) вверх откладываем прямую после выбираем точку на этой прямой которая будет центром окружности наибольшего диаметра червячного колеса () и строим эту окружность так чтобы обеспечить минимальный зазор между червячным колесом и опорами входного вала. Далее через центр окружности проводим прямую перпендикулярную оси вала червяка. Точка пересечения этой прямой с осью вала червяка – середина нарезанной части червяка. Вычерчиваем нарезанную часть червяка и соединяем его с уже вычерченной левой подшипниковой шейкой по диаметру и замеряем размер . Затем замеряем расстояние от середины нарезанной части червяка до левой опоры (середины подшипника 309) и откладываем такое же расстояние вправо. Полученная точка – правая опора. Вычерчиваем подшипники и дистанционное кольцо в этой опоре соединяем её с нарезанной частью червяка по диаметру и замеряем размер . После вычерчиваем резьбовый участок с гайкой стакан и подшипниковую крышку.
Полученные длины буртиков:
Так как длина вала вышла значительно большей чем на этапе педварительного расчёта следует проверить вал на жесткость для новой длины:
По упругому прогибу червяка по середине его нарезанной части:
По углу поворота оси вала в зоне расположения подшипников:
Так как при проектировании стакана необходимо знать некоторые параметры подшипниковой крышки- стакан и крышку проектируем одновременно (Рис. 5).
Толщина стенки стакана S выбирается в зависимости от внутреннего диаметра D который равен наружному диаметру подшипников. Для принимаем
Толщина фланца стакана:
Посадочный диаметр стакана:
Так как стакан и крышка будут крепиться одними и теми же болтами диаметры фланцев и диаметры центров отверстий под болты находим по одним и тем же зависимостям. Расчёт ведём по посадочному диаметру стакана который больше посадочного диаметра крышки:
здесь диаметр болтов для крепления. Количество болтов – 6.
Диаметр отверстий под болты назначаем равным
Высота буртика t для упора в торец наружного кольца подшипника :
здесь координата фаски подшипника.
Катет фаски выбираем в зависимости от диаметра поверхности:
Толщину стенки крышки выбираем из таблицы для нестандартних торцевых крышек:
Толщина фланца крышки для болтов с шестигранными головками:
Ширина канавки для выхода шлифовального круга из ГОСТ 8820-69:
Ширина центрирующего пояска:
Размер находим по формуле:
Длину стержней шести болтов определим как сумму толщин фланцев стакана и крышки подшипника и требуемую глубину завинчивания в чугун :
Длина внутренней поверхности стакана определится как сумма:
В отличии от прототипа где на промежуточном валу ввиду недостаточного межосевого расстояния цилиндрической зубчатой передачи применяют нестандартную глухую крышку мы применим стандартную с посадочным диаметром равным диаметру наружного кольца подшипника. Основные параметры крышки (Рис.6):
Диаметр винтов – М10 количество – 6.
Для винтов М10 по ГОСТ 11738-84 высота головки Н = 8 мм. Длину стержня винтов L определим как сумму толщины фланца крышки и требуемую глубину завинчивания в чугун :
1.3 Выходной вал (Рис. 3).
1.3.1 Диаметр концевого участка тихоходного вала:
1.3.2 Диаметр вала под уплотнением :
Согласовав значение с размером манжеты ГОСТ 8752-79 принимаем
1.3.3 Диаметр вала под подшипником принимаем одинаковым в обеих опорах из условия что во-первых а во-вторых значение должно быть кратным пяти. Принимаем ближайшее число удовлетворяющее этим требованиям
По найденному значению и с учётом рекомендаций по выбору подшипников принимаем в обеих опорах подшипник роликовый конический однорядный 7317 ГОСТ 27365-87.
1.3.4 Диаметр вала под червячным колесом примем следующим большим значением из ГОСТ 6636-69:
1.3.5 Диаметр буртика червячного колеса:
1.3.6 Осевые размеры начинаем с определения длины концевого участка. Концевой участок выполняем цилиндрическим. Назначаем длину из ГОСТ 12080-66 (исполнение 2 ):
Из табл. П6.1 выпишем параметры шпоночного соединения на конце вала (мм):
Принимаем окончательно из ГОСТ 23360-78.
1.3.7 Длина вала под червячным колесом:
здесь длина ступицы червячного колеса.
Из табл. П6.1 выпишем также параметры шпоночного соединения которое образует участок проектируемого вала под червячным колесом с этим колесом (мм):
Поскольку условие прочности шпоночного соединения выполняется принятые параметры шпоночного соединения оставляем без изменений.
1.3.8 Длина правой подшипниковой шейки составит:
здесь минимальный зазор обеспечиваемый установкой дистанционного кольца.
1.3.9 Длина вала под уплотнением определится графически после вычерчивания подшипниковой крышки с добавлением минимального зазора :
Основные размеры подшипниковой крышки:
Диаметр винтов – М12 количество – 6.
Для винтов М12 по ГОСТ 11738-84 высота головки Н = 10 мм. Длину стержня винтов L определим как сумму толщины фланца крышки и требуемую глубину завинчивания в чугун :
1.3.10 Длину буртика колеса вычисляем через его высоту:
1.3.11 Длина левой подшипниковой шейки равна ширине внутреннего кольца подшипника:
1.3.12 Параметры глухой подшипниковой крышки на тихоходном валу:
Так как на этапе разработки корпуса редуктора пришлось увеличивать его ширину это вызвало увеличение осевых размеров тихоходного вала а именно длину правой подшипниковой шейки () и буртика колеса () (Рис. 4):
На этом разработка конструкции валов завершена.
2 Разработка корпуса редуктора и определение типоразмеров
крепёжных деталей (Рис.11).
Для корпуса редуктора принимаем серый чугун СЧ20 механические свойства которого приведены в ГОСТ 1412-85.
Толщина стенки корпуса была определена ранее:
Толщина стенки крышки корпуса редуктора:
Принимаем окончательно
Высоты центров редуктора:
Высоту центра вала червяка определяет диаметр вершин зубьев цилиндрического зубчатого колеса установленного на нём так как он больше диаметра вершин витков червяка:
Окончательно примем
Высота центра червячного колеса:
Высота центра вала-шестерни:
Применим винтовые соединения для стягивания фланцев корпуса и крышки. Стяжные болты с уменьшенной шестигранной головкой ГОСТ 7808-70 образуют с отверстием во фланце крышки сопряжения с зазором и завинчиваются в резьбовые отверстия фланца корпуса.
Толщина фланца корпуса:
Толщина фланца крышки:
Диаметр стяжного болта:
Принимаем болт с резьбой М16. Глубина завинчивания в чугун должна быть не менее . Поскольку при найденной толщине фланца это условие не выполняется:
на нижней стороне фланца корпуса предусматриваем бобышки (приливы) в зоне которых толщина фланца будет равна 24 мм.
Бобышки имеют в плане форму полуокружности центр которой совпадает с осью отверстия для стяжного болта. Таким образом длина стержня болта L будет равна сумме толщин и :
По ГОСТ 7808-70 окончательно принимаем длину болтов L = 40 мм.
Условное обозначение выбранных болтов:
Координата расположения оси отверстия для стяжного болта:
По табл. 5.10 из выбираем диаметр отверстия для стяжных болтов и диаметр цековки для создания «чистых» опорных поверхностей под головками болтов:
Для центрирования крышки редуктора относительно его корпуса применяем конические штифты по ГОСТ 3129-70 с диаметром :
Толщина лап корпуса:
Округлив до большего целого примем
Диаметр фундаментных болтов редуктора:
Выбираем метрическую резьбу М20.
Длину стержня фундаментного болта назначаем предварительно:
Принимаем фундаментные болты: ГОСТ 7808-70.
Количество фундаментных болтов согласно рекомендациям при принимаем четыре.
Координата расположения оси отверстия для фундаментного болта:
По табл. 5.10 из выбираем диаметр отверстий в лапах для фундаментных болтов и диаметр цековки для обработки опорных поверхностей под головками болтов:
Для транспортировки редуктора на наружной поверхности крышки предусматриваем две проушины в отличии от прототипа где были использованы рым-болты.
Диаметр отверстий в проушинах:
Литейные радиусы на крышке и корпусе редуктора:
- при сопряжении стенок корпуса (крышки):
-при сопряжении стенки корпуса (крышки) с фланцем:
-при сопряжении стенки корпуса (крышки) с лапами:
На этом разработку основных элементов корпуса закончим.
Разработка технического проекта редуктора
1 Проверочный расчёт валов.
Технический проект редуктора начинаем с проверочных расчётов на прочность валов. В данном проекте ограничимся соответствующими расчётами для промежуточного вала.
Для выбора опасных сечений на промежуточном валу и последующих прочностных расчётов составим его расчётную схему (рис. 8.1 б). В целом рис. 8.1 содержит эскиз вала с деталями и узлами находящимися на нём (рис. 8.1 а) общую расчётную схему вала (рис. 8.1 б) две плоские расчётные схемы вала (рис. 8.1 в д) эпюры изгибающих моментов () в этих плоскостях (рис. 8.1 г е) эпюру крутящего момента () на промежуточном валу (рис. 8.1 ж).
Расчётная схема составлена при следующих допущениях:
вал представлен в виде статически определимой двухопорной балки.
подшипники условно заменены шарнирами 1 и 2 в которых действуют неизвестные пока суммарные радиальные реакции соответственно.
червяк и цилиндрическое колесо заменены силами – соответственно () и () точки которых лежат на делительных окружностях посередине соответственно нарезанной части червяка и зубчатого венца.
Значения сил в зацеплениях (Н) а также делительные диаметры (мм) берём из расчёта передач:
Значения длин звеньев находим замеряя соответствующие участки на схеме (м):
Определяем реакции опор в плоскости X=0.
Уравнение равновесия моментов относительно точки 2:
Так как направление этой реакции меняем на противоположное.
Уравнение равновесия сил в проекции на ось Z:
Определяем реакции опор в плоскости Z=0.
Уравнение равновесия сил в проекции на ось X:
Так как имеют отрицательные значения их направления тоже меняем на противоположные.
Суммарные радиальные реакции в опорах:
Для построения эпюр изгибающих моментов вычислим их значения в сечениях I II и III.
Для проверки правильности вычисления найдём его другим способом:
Оба вычисления дают одинаковый результат следовательно изгибающий момент найден верно.
По полученным величинам строим эпюру изгибающих моментов в плоскости Х=0 рис. 5.1 г.
По найденным величинам и строим эпюру изгибающих моментов в плоскости Z=0 рис. 5.1 е.
Суммарные изгибающие моменты в сечениях I II и III :
Эквивалентные моменты в в сечениях I II и III:
Характер эпюр и показывает что предположительно опасным сечением можно считать сечение I в котором изгибающие моменты имеют максимальное значение.
Однако стоит также проверить вал на сопротивление усталости в сечениях II и III так как в этих сечениях есть такие концентраторы напряжений как посадка с натягом (сечение II ) и шпоночные пазы (сечение III ).
В выбранных сечениях сделаем проверку вала на сопротивление усталости:
Поскольку промежуточный вал в проверяемом сечении выполнении в виде червяка то материал червяка – Сталь 40Х является материалом всего вала.
Пределы пределы текучести и прочности для Стали 40Х:
Пределы выносливости Стали 40Х при симметричном цикле напряжений для изгиба () и кручения () определим по корреляционным зависимостям ГОСТ 25.504-82:
Поскольку напряжения изгиба вала при постоянных нагрузках изменяется по симметричному циклу то:
где амплитудное и среднее напряжения изгиба МПа.
осевой момент сопротивления «чистого» сечения .
Для сечения проходящего по нарезанной части червяка:
Для напряжения кручения принимаем отнулевой цикл у которого амплитудное () и среднее () значения совпадают и равны половине напряжения кручения ():
Коэффициенты влияния асимметрии цикла при изгибе () и кручении () :
Концентратором напряжения здесь являются витки червяка поэтому эффективные коэффициенты концентрации напряжений при изгибе () и кручении () берём для резьбы оказывающей аналогичное влияние (так как в таблице нет значений и для искомые величины определяем линейной интерполяцией коэффициентов и для и ):
Коэффициенты влияния абсолютных размеров поперечного сечения при изгибе () и кручении () выбираем по делительному диаметру червяка (используя линейную интерполяцию):
Коэффициенты влияния шероховатости поверхности при изгибе () и кручении () берём для полирования :
Коэффициенты влияния поверхностного упрочнения выбираем с учётом того что для витков червяка была принята закалка:
Коэффициент анизотропии свойств стали:
Коэффициент снижения предела выносливости с учётом всех факторов:
Коэффициент запаса прочности по усталости при изгибе:
Коэффициент запаса прочности по усталости при кручении:
Расчётный коэффициент запаса прочности по усталости в сечении I:
следовательно сечение I обладает достаточно большим запасом сопротивления усталости.
Делаем проверку вала на статическую прочность при кратковременных перегрузках в выбранном сечении:
Следовательно в сечении I вал имеет большой запас статической прочности.
Для сечения проходящего под внутренним кольцом подшипника:
Расчётный коэффициент запаса прочности по усталости в сечении II:
следовательно сечение II обладает достаточно большим запасом сопротивления усталости.
Следовательно в сечении II вал имеет большой запас статической прочности.
Для сечения с двумя противолежащими шпоночными канавками:
Расчётный коэффициент запаса прочности по усталости в сечении III:
следовательно сечение III обладает достаточно большим запасом сопротивления усталости.
Следовательно в сечении III вал имеет большой запас статической прочности.
2 Проверка подшипников промежуточного вала
Поскольку частота вращения промежуточного вала а вместе с ним и внутренних колец подшипников выбранные подшипники (фиксирующая опора – 66309 плавающая опора – 309 ) проверяем по критерию динамической грузоподъёмности.
Исходные данные к расчету подшипников:
Расчетная схема к рас чету подшипников представлена на Рис. 9.
Вначале выполним расчёт фиксирующей опоры 1.
Выпишем характеристики подшипников фиксирующей опоры:
Суммарная динамическая грузоподъёмность опоры I:
Находим отношение .При этом так как плавающая опора 2 осевую силу не воспринимает ():
Коэффициенты радиальной и осевой нагрузок выбираем по таблице двухрядных шарикоподшипников для :
Эквивалентная динамическая радиальная нагрузка в опоре 1:
Условие применимости метода выполняется:
Расчётная долговечность подшипников фиксирующей опоры:
Следовательно надёжность подшипников фиксирующей опоры выше требуемой.
Выполним расчёт плавающей опоры 2.
Выпишем характеристики подшипников плавающей опоры:
Так как плавающая опора не воспринимает осевую силу () то коэффициенты радиальной и осевой нагрузок для подшипника 309 соответственно равны:
Эквивалентная динамическая радиальная нагрузка в опоре 2:
Расчётная долговечность подшипников плавающей опоры:
Следовательно для плавающей опоры расчётный ресурс значительно превышает требуемый.
3 Выбор сорта смазочного материала для редукторных передач и подшипников
Для редукторных передач принимаем смазку погружением. Объём масляной ванны берём таким чтоб уровень погружения червяка находился в пределах: от высоты витка ( min ) до оси симметрии ( max ).
Требуемую кинематическую вязкость масла определяем в зависимости от параметра для червячной передачи по таблице ( здесь соответственно контактное напряжение МПа и окружная скорость ):
По значению кинематической вязкости выбираем масло цилиндровое 38 ГОСТ 6411-76 у которого .
Так как окружная скорость цилиндрического колеса и скорость скольжения червяка погруженных в масляную ванну меньше подшипники редуктора не могут в достаточной мере смазываться маслом цилиндровым 38 применённым для смазки передач зацеплением за счет образования масляного тумана. Таким образом для смазки подшипников входного и выходного валов применим смазочный материал Литол-24 ГОСТ 21150-87 закладываемый в подшипниковый узел при сборке редуктора. Для предотвращения вытекания смазочного материала из подшипникового гнезда по мере нагрева установим на валах стальные уплотнительные шайбы (). На промежуточном валу подшипниковые узлы которого не нуждаются в дополнительной смазке установим тем не менее штампованные маслозащитные шайбы () предназначенные для ограждения подшипников от избытка масла нагнетаемого витками червяка.
4 Разработка конструкции шкивов
Для окружной скорости в качестве материала шкивов выбираем серый чугун СЧ20 ГОСТ 1412-85. Конструкции шкивов берём из ГОСТ 20889-88: малого – тип 3 болшего – тип 5. Размеры робочих поверхностей шкивов определяем по данным таблицы приведенной в ГОСТ 20889-88 и результатам расчёта ременной передачи. Для клинових ремней сечения А (мм):
Наружный диаметр шкивов:
Толщина обода большего шкива:
Поскольку при окружной скорости требуется балансировка шкивов расчётную толщину обода увеличиваем на окончательно приняв:
Диаметры четырёх технологических отверстий в диске:
Диаметр центров технологических отверстий:
Диаметры ступиц шкивов:
Длины ступиц шкивов:
длину малого принимаем на 2 мм длинней концевого участка вала ротора двигателя 4А100L2У3 для возможности осевого крепления на валу с помощью концевой шайбы:
длина ступицы большего шкива определена при разработке конструкции входного вала редуктора:
Глубина врезания шпонки в ступицу:
Рис. 1. Быстроходный вал
Рис. 2. Промежуточный вал
Рис. 3. Тихоходный вал
Рис. 4. Тихоходный вал изменённый
Рис. 5. Стакан и крышка глухая
Рис. 6. Крышка подшипниковая глухая стандартная
Рис. 7. Крышка подшипниковая с отверстием для манжетного уплотнения стандартная
Рис. 8. Расчётная схема промежуточного валаРис. 9. Расчётная схема подшипников промежуточного вала
Рис. 10. Расчётная схема шпоночного соединения
Рис. 11. Элементы корпуса
Шевченко С.В. Деталі машин. Розрахунки конструювання задачі: Навчальний посібник. - Луганськ: вид-во СУДУ 2000. – 488с.: табл. 150 іл. 234 бібліогр. 14 назв.
Цехнович Л.И. Петриченко И. П. Атлас конструкций редукторов: Учеб. Пособие. – 2-е изд. перераб. и доп. – К: Выща шк. 1990. – 151с.: ил.
Анализ технического задания . 3
Выбор двигателя. Кинематический силовой и энергетический расчет двигателя .. 4
Расчет передач привода:
1.Расчет цилиндрической косозубой передачи . 7
2.Расчёт червячной передачи . 17
3.Расчёт клиноременной передачи с ремнями нормальных сечений по ГОСТ 1284.1-80 ГОСТ 1284.3-80 25
Разработка эскизного проекта редуктора:
1.Ориентировочный расчёт валов и разработка их предварительной конструкции:
1.1.Быстроходный вал .. 29
1.2.Промежуточный вал . 31
2.Разработка корпуса редуктора и определение типоразмеров крепёжных деталей . 40
Разработка технического проекта редуктора:
1.Проверочный расчёт валов 44
2.Проверка подшипников промежуточного вала 52
3.Выбор сорта смазочного материала для редукторных передач и подшипников .. 54
4.Разработка конструкции шкивов .. 54
1.Машинный расчёт . 67
2.Спецификация к сборочному чертежу редуктора .. 76
Список литературы . 79
Чертёж сборочный.cdw

Крутящий момент на тихоходном валу Т = 1465 Н
Частота вращения тихоходного вала
Технические требования
Плоскость разъема покрыть пастой "Герметик".
Необрабоанные поверхности редуктора красить:
внутри редуктора - маслостойкой краской
снаружи - нитроэмалью.
Залить масло цилиндровое 38 ГОСТ 6411-76 до отметки на
Кафедра "Машиноведение
Спецификация 2.cdw

Прокладки регулировочные
Прокладка уплотнительная
М6-6gx16 ГОСТ 7798-70
М10-6gx18 ГОСТ 7808-70
М10-6gx30 ГОСТ 7808-70
М6-6gX20 ГОСТ 11738-84
М10-6gX30 ГОСТ 11738-84
М12-6gX35 ГОСТ 11738-84
Шайба 6Л ГОСТ 6402-70
Шайба 10Л ГОСТ 6402-70
Шайба 12Л ГОСТ 6402-70
Шайба 16Л ГОСТ 6402-70
Шайба 7019-0631 ГОСТ 14734-69
Манжета 1.1-80x105-1 ГОСТ 8752-79
Манжета 1.1-28x50-1 ГОСТ 8752-79
Спецификация 3.cdw

Спецификация.cdw

КП.ТТ-591.ДМ-3.7.000
КП.ТТ-591.ДМ-3.7.01.СБ
КП.ТТ-591.ДМ-3.7.02.СБ
Рекомендуемые чертежи
Свободное скачивание на сегодня
- 29.08.2014
- 25.01.2023