Привод индивидуальный




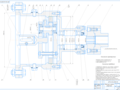
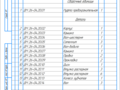
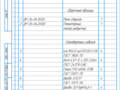
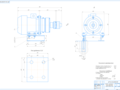
- Добавлен: 24.01.2023
- Размер: 2 MB
- Закачек: 0
Описание
Привод индивидуальный
Состав проекта
![]() |
![]() |
![]() ![]() ![]() ![]() |
![]() ![]() ![]() |
![]() ![]() ![]() |
![]() |
![]() ![]() ![]() ![]() |
![]() |
![]() |
![]() ![]() ![]() ![]() |
![]() ![]() ![]() ![]() |
![]() |
![]() |
![]() ![]() ![]() ![]() |
Дополнительная информация
Сборочный чертеж редуктора.frw

Вращающий момент на выходном валу
Частота вращения выходного вала
Общее передаточное число 9
Технические требования
Необработанные поверхности литых деталей
красить маслостойкой желтой эмалью
Наружные поверхности корпуса красить серой эмалью ПФ-115
Плоскости разъема редуктора покрыть тонким слоем герметика
Редуктор обкатать без нагрузки с залитым маслом И-Г-С-46
литра в течение 60 мин.
после чего масло слить
промыть керосином и залить чистым маслом в количестве 0
Вращение валов должно быть плавным без заеданий
Выступающую часть вала смазать техническим вазелином
ГОСТ 5774-86 и обернуть парафинированной бумагой ГОСТ 9569-89
b-6x21H12h9x25H11h7x6H7d9
РГАТА им. П. А Соловьёва
Задание.doc
технологическая академия им. П.А. Соловьева
Кафедра «Основы конструирования машин»
на курсовой проект по дисциплине
«Детали машин и основы конструирования»
Студент Алексеева А.И. группа ДК2-08 вариант ДМ26-4
Спроектировать индивидуальный привод включающий мотор-редуктор с планетарной ступенью с двухвенцовым сателлитом.
– Муфта предохранительная (Тmax =15Tном)
Режим нагружения: ступенчатая циклограмма (график нагрузки №5);
Термообработка колес: закалка ТВЧ
Выпуск: крупносерийный.
Общий вид привода – 1 лист (ф. А1)
Сборочный чертеж планетарного редуктора – 1 лист (ф. А1)
Рабочие чертежи деталей привода (4 детали) – 1 лист (ф. А1)
Рабочий чертеж корпусной детали – 1 лист (ф. А1)
Мощность на тихоходном валу: Pт =15 кВт
Число оборотов тихоходного вала: nт =95 обмин
Передаточное число привода: Uприв =10
Примечание. Привод установить на сварной раме.
ДМ.26-04.00.00 П3.DOC
РЫБИНСКАЯ ГОСУДАРСТВЕННАЯ АВИАЦИОННАЯ
ТЕХНОЛОГИЧЕСКАЯ АКАДЕМИЯ им. П. А. СОЛОВЬЕВА
Факультет авиадвигателестроения
Кафедра «Основы конструирования машин»
«Детали машин и основы конструирования»
ПРИВОД ИНДИВИДУАЛЬНЫЙ
Пояснительная записка
Студент группы ДК2-08 Алексеева А.И.
Руководитель д.т.н. профессор Надеждин И.В.
Нормоконтроллер д.т.н. профессор Надеждин И.В.
Кинематический расчёт привода . .6
1. Выбор электродвигателя .6
2. Кинематический расчет планетарной ступени мотор-редуктора 7
Расчет на прочность планетарной передачи .. 10
1 Выбор материалов зубчатых колес планетарной передачи .10
2. Расчет допускаемых контактных и изгибных напряжений 10
3. Расчет допускаемых контактных и изгибных напряжений при пиковых перегрузках ..14
4. Проектный расчет планетарной передачи 15
5. Проверочный расчет прочности по контактным и изгибным напряжениям 18
6. Проверка прочности зубьев при пиковых перегрузках ..24
Эскизное проектирование .. .26
Расчет соединений 27
1 Расчет резьбовых соединений 27
2. Расчет шпоночных и шлицевых соединений 27
Расчет тихоходного вала на статическую прочность и сопротивление усталости .29
Подбор подшипников качения с помощью ЭВМ 39
1 Подбор подшипников качения для вала – водила 39
2. Подбор подшипников качения устанавливаемых в сателлиты и опоры выходного вала–водила ..40
Расчет на прочность осей сателлитов 42
Конструирование корпусных деталей . ..44
Выбор смазочных материалов и системы смазывания 44
Порядок сборки редуктора 45
Список использованной литературы 46
Приложение А. Спецификации . .47
Технический уровень всех отраслей народного хозяйства в значительной мере определяется уровнем развития машиностроения. На основе развития машиностроения осуществляется комплексная механизация и автоматизация производственных процессов в промышленности строительстве сельском хозяйстве на транспорте.
Государством перед машиностроением поставлена задача значительного повышения эксплуатационных и качественных показателей при непрерывном росте объема ее выпуска.
Одним из направлений решения этой задачи является совершенствование конструкторской подготовки студентов высших учебных заведений.
При выполнении моей работы активно используется знания из ряда пройденных предметов: механики сопротивления материалов технологий металлов и др.
Объектом курсового проекта является привод с планетарным мотор-редуктором использующий большинство деталей и узлов общего назначения.
Кинематический расчёт привода.
1. Выбор электродвигателя.
1.1. Определяем общий КПД привода:
- КПД планетарной передачи ([1] стр. 76 табл. Б.1).
1.2Находим потребную мощность и частоту вращения электродвигателя:
1.3Выбираем электродвигатель серии АИР ([1] стр.79 табл. Б.6):
Проверяем перегрузку :
Полученная перегрузка попадает в предел 10-12% следовательно электродвигатель не перегружен.
1.4Определяем расчётное значение передаточного числа планетарного редуктора:
2. Кинематический расчет планетарной ступени мотор-редуктора.
2.1. Определяем передаточное отношение пары зубчатых колес a-g ([2] стр. 36 формула 2.22): .
По табл. Б.2 [1] принимаем ближайшее стандартное значение .
2.2. Определяем передаточное отношение пары зубчатых колес f-b ([2] стр. 36 формула 2.23):
2.3. Принимаем число зубьев центрального колеса a: .
2.4. Определяем число зубьев сателлита g:
Округляем до целого: .
2.5. Уточняем передаточное отношение в зацеплении a-g:
2.6. Определяем число зубьев сателлита f:
2.7. Из условия соосности находим число зубьев центрального колеса b:
2.8. Принимаем число сателлитов: .
2.9. Проверяем условие сборки:
Получилось целое число (2475) т.е. условие сборки выполняется.
2.10. Определяем фактическое передаточное отношение планетарной передачи:
и отклонение фактического передаточного числа от заданного:
2.11. Проверяем условие соседства:
или 6495>59 т.е. условие соседства выполняется.
2.11. Находим частоту вращения на выходном валу редуктора:
2.12. Вычисляем отклонение частоты вращения выходного вала от требуемого значения:
2.13. Определяем вращающие моменты на валах планетарного мотор- редуктора:
Расчет на прочность планетарной передачи
1 Выбор материалов зубчатых колес планетарной передачи.
Принимаем для зубчатых колёс планетарной ступени редуктора сталь марки 40ХН с термической обработкой шестерни и колеса - закалка ТВЧ. Средняя твердость поверхности зубьев шестерни колеса предел текучести материала колёс (табл. П.1.1 [2]).
2. Расчет допускаемых контактных и изгибных напряжений.
2.1. По [2] стр. 56 формула 4.3 определяем базовое число циклов перемены напряжений соответствующее длительному пределу выносливости шестерни a и колеса g:
2.2. По [2] стр. 24формула 2.8 и [2] стр. 25 формула 2.9 определяем относительные частоты вращения центральной шестерни a
2.3. Определяем суммарное время работы редуктора в часах (см. пояснения к [2] стр. 56 формула 4.4)
2.4. По [2] стр. 56 формула 4.4 и [2] стр. 56 формула 4.5 находим число циклов перемены напряжений шестерни a и колеса g:
Для заданного режима нагружения (тяжелый; №5 – типовой см. [2] стр.167 рис. П.1.2) определяем эквивалентное число циклов нагружения для шестерни a и колеса g:
где – коэффициент приведения переменного режима нагрузки к постоянному эквивалентному выбираемый по [2] стр. 166 табл. П.1.5 в зависимости от режима нагружения
2.5. Определяем коэффициент долговечности
Условие не выполняется следовательно
2.6. Допускаемое контактное напряжение определяют по [2] стр. 58 формула 4.9:
где – предел контактной выносливости поверхности зубьев соответствующий базовому числу циклов перемены напряжений; выбирают по [2] стр. 165 табл. П.1.2 в зависимости от способа термической обработки зубьев:
– коэффициент безопасности по контактным напряжениям. Для зубчатых колес подвергнутых цементации
Подставляем найденные значения параметров в формулу для определения :
Выбираем в качестве допускаемого контактного напряжения меньшее из двух полученных значений т.е.
2.7. Определяем эквивалентное число циклов напряжений по изгибу
где – коэффициент приведения; выбирают по [2] стр. 166 табл. П.1.5 для заданного режима нагружения и вида термической обработки:
Тогда эквивалентное число циклов напряжений по изгибу для шестерни и колеса будет равно:
2.8. Определяем коэффициент долговечности по изгибу.
2.9. Допускаемые изгибные напряжения определяют по [2] стр. 58 формула 4.10:
где – предел выносливости зубьев при изгибе соответствующий базовому числу циклов перемены напряжений (выбирают по [2] стр.165 табл. П.1.3 в зависимости от вида термической или химико-термической обработки колес);
– коэффициент безопасности; – при вероятности неразрушения зубьев 099; – при вероятности неразрушения более 099. – коэффициент учитывающий влияние двухстороннего приложения нагрузки; при одностороннем приложении (нереверсивные передачи) и соответственно при двухстороннем приложении нагрузки (реверсивные передачи сателлиты и т.д.). Принимаем и .
Подставляем найденные значения параметров в формулу для определения допускаемых изгибных напряжений для шестерни a и колеса g:
3. Расчет допускаемых контактных и изгибных напряжений при пиковых перегрузках.
3. Определяем предельные допускаемые контактные и изгибные напряжения при кратковременной (пиковой) перегрузке ([2] стр. 166 табл. П.1.4):
4. Проектный расчет планетарной передачи
4.1. Предварительное значение межосевого расстояния пары колес a-g планетарной передачи определяют по [2] стр. 58 формула 4.11:
где – предварительное значение межосевого расстояния мм;
– вращающий момент на шестерне a ;
– коэффициент концентрации нагрузки;
– коэффициент межосевого расстояния; для прямозубых передач
– коэффициент неравномерности распределения нагрузки между сателлитами; Принимаем
– коэффициент ширины колеса; принимаем (см. пояснения к [2] стр. 58-59 табл. 4.1);
– передаточное число пары колес a-g;
– число сателлитов;
Для определения коэффициента предварительно найдем коэффициент ширины :
По [2] стр. 167 табл. П.1.6 при и в зависимости от варианта схемы расположения колес относительно опор ([2] стр. 169 рис. П.1.3 схема №6) определяем коэффициент концентрации нагрузки:
Подставляем найденные значения коэффициентов в формулу для определения межосевого расстояния:
По [2] стр. 169 табл. П.1.10 округляем полученное значение до стандартного (из 2-го ряда)
4.2. Определяем ширину сателлитов g и шестерни a:
округляем до целого:
округляем до целого: где
4.3. Определяем предварительное значение диаметра шестерни a:
4.4. Находим предварительно модуль зацепления колес a-g:
Округляем полученное значение модуля ([2] стр. 169 табл. П.1.10) до стандартной величины .
4.5. Вычисляем окончательные размеры колес планетарной ступени редуктора:
делительные диаметры
диаметры окружностей вершин зубьев
диаметры окружностей впадин зубьев
4.6. Определяем окончательное значение межосевого расстояния планетарной ступени привода:
4.7. Проверяем условие соседства по [2] стр. 29 формула 2.16:
или т.е. условие соседства выполняется.
4.8. Проверяем пригодность заготовок колес ([2] стр. 164 рис. П.1.1):
Оба полученных значения значительно меньше предельно допускаемых величин для выбранной марки стали и вида ТО – закалка ТВЧ ([2] стр. 163 табл. П.1.1):
4.9. По [2] стр. 49 формула 3.1 определяем окружную и радиальную силы в зацеплении a-g:
5. Проверочный расчет прочности по контактным и изгибным напряжениям.
5.1. Проверка выполнения условий прочности передачи по контактным напряжениям по [2] стр. 58 формула 4.13
где – контактное напряжение МПа;
– коэффициент учитывающий форму сопряженных поверхностей зубьев. Для прямозубых колес
– коэффициент учитывающий механические свойства материалов сопряженных зубчатых колес. Для стали
– коэффициент учитывающий суммарную длину контактных линий. Для прямозубых передач где – коэффициент торцового перекрытия зубьев;
– начальный диаметр шестерни
– удельная расчетная окружная сила:
где – коэффициент учитывающий распределение нагрузки между зубьями; определяют по [2] стр. 168 табл. П.1.8;
– коэффициент концентрации нагрузки; ранее определили ;
– коэффициент динамической нагрузки;
Для определения коэффициента предварительно найдем окружную скорость шестерни a:
По [2] стр. 168 табл. П.1.8 находим степень точности передачи по нормам плавности (ГОСТ 1643-89) – 8;
Определяем коэффициент (см. [2] стр. 168 табл. П.1.8 – для 8 степени точности):
Коэффициент динамической нагрузки определяем по формуле
где – удельная окружная динамическая сила
При и прямозубых колес без модификации головки ([2] стр. 170 табл. П.1.12). Коэффициент учитывающий влияние разности шагов зацепления зубьев шестерни a и колеса g определяем по [2] стр. 170 табл. П.1.13 в зависимости от модуля () и 8-й степени точности: Предельное значение находим из [2] стр. 171 табл. П.1.14:
Тогда окружная динамическая сила
Подставим полученные значения параметров в формулу для определения
Удельная расчетная окружная сила
Определяем коэффициент торцового перекрытия зубьев:
Определяем расчетное контактное напряжение :
т.к. рассчитаем перегрузку :
перегрузка в пределах нормы.
5.2. Проверка прочности по напряжениям изгиба ([2] стр. 58 формула 4.14):
где – расчетное напряжение изгиба МПа;
– коэффициент учитывающий перекрытие зубьев; для прямозубых колес
– коэффициент учитывающий наклон зубьев; для прямозубых колес
– коэффициент учитывающий форму зубьев;
– допускаемое напряжение при изгибе МПа;
– удельная расчетная сила :
где – окружная сила;
– рабочая ширина зубчатого венца;
– коэффициент учитывающий распределение нагрузки между зубьев; для прямозубых колес ;
– коэффициент учитывающий распределение нагрузки по ширине зубчатого венца;
– коэффициент динамической нагрузки.
Формулу для расчета коэффициент находим в [2] стр. 168 табл. П.1.7 (при схема №6)
где – удельная окружная динамическая сила .
При для прямозубых колес без модификации головки ([2] стр. 170 табл. П.1.12). Коэффициент Предельное значение находим из [1] стр. 171 табл. П.1.14: Тогда
Коэффициенты формы зуба определяем по эмпирической формуле (см. [2] стр. 171 табл. П.1.15) справедливой для внешнего зацепления при
Определяем коэффициенты формы зуба соответственно для шестерни a и колеса g:
Определяем расчетные напряжения изгиба в зубьях шестерни a и колеса g:
Таким образом напряжения изгиба в зубьях колес a и g ниже допускаемых.
6. Проверка прочности зубьев при пиковых перегрузках.
где – расчетные контактные и изгибные напряжения создаваемые наибольшей нагрузкой ; отношение ; – расчетные контактные и наибольшие изгибные напряжения: – предельные допускаемые контактные и изгибные напряжения при пиковых перегрузках .
т.е. условие прочности зубьев при пиковых перегрузках выполняется.
Эскизное проектирование.
1. Разработка компоновочной схемы редуктора и проектный расчет тихоходного вала.
Найдем размеры тихоходного вала мотор-редуктора:
Примем . Длина участка вала: .
Диаметр выходного цилиндрического конца вала: . Длина выходного цилиндрического конца вала: .
Диаметр участка вала с упорным буртиком под подшипник:
2. Выбор типа и схемы установки подшипников качения.
Для опор вала-водила принимаем шариковые радиальные однорядные подшипники №206 ГОСТ 8338-75; для опор сателлитов – радиальные двухрядные сферические подшипники №1200 ГОСТ28428-90.
1 Расчет резьбовых соединений.
Диаметр винтов для крепления крышки корпуса рассчитывают по [1] стр. 74 формула 5.2:
Диаметр болтов для крепления редуктора к раме определяют по [2] стр. 74 формула 5.3:
2. Расчет шпоночных и шлицевых соединений.
Считаем что вращающий момент с выходного цилиндрического конца вала будет передаваться шпоночным соединением. Сечение призматической шпонки для вала ([2] стр. 180 рис. П.1.5): Примем длину шпонки рабочая длина шпонки Определяем расчетное напряжение смятия шпонки (см. [2] стр. 180 п.2 примечаний к табл. П.1.25)
Расчетное напряжение смятия для чугунных деталей превышает допускаемое напряжение. Поэтому заменим шпоночное соединение на шлицевое. Примем прямобочные шлицы средней серии ([2] табл. П.1.26). Размеры шлицев: наружный и внутренний диаметры:
число зубьев фаска . Длина шлицев: .
Расчетные напряжения смятия для шлицевого соединения (см. примечание к табл. П.1.26)
т.е. условие прочности шлицевого соединения выполняется.
Расчет тихоходного вала на статическую прочность и сопротивление усталости.
Чтобы при эксплуатации редуктора не произошло разрушения вала производят расчет на статическую прочность и сопротивление усталости т.е. определяют максимальные нагрузки и изгибающие моменты действующие на вал определяют опасные сечения и проверяют их на коэффициент запаса прочности.
Начинаем с построения схемы вала с приложенными к нему нагрузками.
Рисунок 1. Расчетная схема вала
Из схемы мы видим что на тихоходный вал осевые нагрузки не действуют поэтому будем рассматривать все нагрузки в одной плоскости.
Расчет начинаем с определения радиальных реакций опор и .
Размеры a b c находим из компоновочной схемы:
Найдем сначала радиальную и консольную нагрузки и :
Определяем реакции в опорах А и В:
Построение эпюр изгибающего и крутящего момента:
Рисунок 2. Эпюры изгибающих моментов
Расчет тихоходного вала на статическую прочность.
Условие статической прочности:
где – коэффициент запаса прочности
– допускаемый коэффициент запаса прочности
) Делаем расчет для первого сечения:
Максимально-действующее нормальное напряжение:
где - максимально – действующее нормальное напряжение на вал МПа
- максимально - действующий изгибающий момент на валу Н·м
- момент сопротивления сечения вала при расчете на изгиб мм3
а) Изгибающий момент на валу:
где - коэффициент перегрузки (см. п. 1.1.3.)
б) Момент сопротивления сечения вала при расчете на изгиб:
где d - диаметр участка вала в опасном сечении мм.
Максимально-действующее касательное напряжение
где - максимально-действующее касательное напряжение МПа
- максимально-действующий крутящий момент Нм
- момент сопротивления сечения вала при расчете на кручение мм3
а) Максимально-действующий крутящий момент:
б) Момент сопротивления сечения вала при расчете на кручение:
Определение частных коэффициентов запаса прочности и :
Определяем по [3] стр.183 табл. 10.2 - пределы текучести для высокопрочного чугуна ВЧ60.
Находим общий коэффициент запаса прочности:
) Делаем расчет для второго сечения:
где - максимально – действующее нормальное напряжение на вал МПа;
- максимально - действующий изгибающий момент на валу Н·м;
- момент сопротивления сечения вала при расчете на изгиб мм3.
где - максимально-действующее касательное напряжение МПа;
- максимально-действующий крутящий момент Нм;
- момент сопротивления сечения вала при расчете на кручение мм3.
Таким образом тихоходный вал удовлетворяет условиям статической прочности.
Расчет вала на усталостную прочность.
В качестве материала вала используем высокопрочный чугун ВЧ60 термообработанный до твердости 230 HB имеющий следующие механические характеристики:
Условие усталостной прочности:
) Проверяем первое сечение:
а) Определяем коэффициенты снижения предела выносливости с учетом посадки с натягом под подшипник качения по формулам [3] стр. 189 формула 10.10:
где значения и принимаем по [3] стр.190 табл. 10.13 при :
– коэффициент влияния качества поверхности (для шлифованной поверхности вала под подшипник [3] стр. 189 табл. 10.8);
– коэффициент влияния поверхностного упрочнения (без упрочнения поверхности вала [3] стр. 189 табл. 10.9).
б) Принимаем что нормальные напряжения изменяются по симметричному циклу т.е. а касательные напряжения – по отнулевому т.е.
в) Определяем коэффициенты запаса прочности:
по нормальным напряжениям:
по касательным напряжениям:
Тогда результирующий коэффициент запаса прочности для первого сечения:
) Проверяем второе сечение:
Подбор подшипников качения и выбор посадок с помощью ЭВМ.
1 Подбор подшипников качения для вала – водила.
Исходные данные вносим в виде таблицы:
Тип расчета задаем – проектный расчет
Коэффициент температуры
Коэффициент безопасности
Коэффициент вращения внутреннего кольца
Радиальная реакция левой опоры
Радиальная реакция правой опоры
Внешняя осевая нагрузка
Частота вращения вала
2. Подбор подшипников качения устанавливаемых в сателлиты и опоры выходного вала–водила и выбор посадок.
Подбор подшипников качения устанавливаемых в сателлиты. Предварительно устанавливаем в сателлиты шариковый радиальный сферический двухрядный подшипник ([2] стр. 176 табл. П.1.20). Радиальная нагрузка действующая на подшипник:
По [2] стр. 62 формула 4.25 определяем эквивалентную динамическую нагрузку при
Требуемую динамическую грузоподъемность выбранного подшипника при (см. пояснения к [2] стр. 62 формула 4.25) долговечности относительной частоте вращения и показателе степени (для шарикоподшипников) определяем по формуле:
Динамическая грузоподъемность данного подшипника по каталогу что больше требуемой грузоподъемности поэтому намеченный подшипник №1200 ГОСТ 28428-90 подходит.
Расчет на прочность осей сателлитов.
В качестве материала оси используем сталь 40ХН
Для оси двухвенцового сателлита окружные силы определяются по формулам ([2] стр.65):
где и - вращающиеся моменты внешних сил приложенные к центральным колесам а и b.
Радиальные силы и будут равны:
Результирующий изгибающий момент в опасном сечении оси:
где и - изгибающие моменты соответственно в горизонтальной и вертикальной плоскостях.
Напряжения изгиба оси сателлитов определяют по формуле стр.65 [2] (4.29):
где момент сопротивления где – диаметр оси. .
Расчет показал что т.е. прочность оси сателлита на изгиб обеспечивается.
Конструирование корпусных деталей.
Толщина стенки литого корпуса редуктора:
Примем толщину стенки корпуса равной .
Диаметр болтов для крепления редуктора к раме:
Примем Диаметр отверстия под болты
Выбор смазочных материалов и системы смазывания.
Предварительно рассчитаем окружную скорость вращения шестерни по формуле:
где -делительный диаметр шестерни мм
- относительная частота вращения шестерни.
Смазку колес и подшипников планетарного мотор-редуктора будем осуществлять для контактного напряжения и окружной скорости
По этим характеристикам выбираем масло по табл. П.1.9 [2] И-Г-С-46.
Уровень заливки масла рассчитаем по формуле:
- уровень заливки масла мм
- делительный диаметр сателлита мм.
Порядок сборки редуктора.
Сборку планетарного мотор-редуктора начинают с установки в корпус 2 на клей зубчатого венца 13. В вал-водило 6 и диск 10 устанавливаем подшипники 25 и стопорные кольца 22. Устанавливаем вал 14 со шпонкой 32 и сателлитом 5 в подшипники 22. Стягиваем вал-водило и диск болтами 17 (в соединение также входят гайки 20 шайбы 30 и 31). Проверяем свободность вращения.
В крышку 3 устанавливаем стопорные кольца 23 с подшипниками 25. Крепим крышку к редуктору болтами 15 и шайбами 29.
Ставим манжету 24 на вал-водило закрываем крышкой 7 крепим болтами 15 и шайбами 29.
Корпус мотор-редуктора устанавливаем на электродвигатель с помощью вала-шестерни 4 и шпонки 33.
На вал-водило устанавливаем предохранительную муфту 1.
Список использованной литературы
Детали машин и основы конструирования. Курсовое проектирование: пособиесост. И.В.Надеждин. – РГАТА 2010 - 96с.
Надеждин И.В. Расчет и конструирование планетарных передач авиационных и общемашиностроительных приводов: Учебное пособие. – Рыбинск: РГАТА 2003. – 236 с.
Анурьев В.И. Справочник конструктора - машиностроителя: в 3 т. Т.1.- 8-е изд. перераб. и доп. Под ред. И.Н. Жестоковой.- М.; Машиностроение 2001.- 920 с.; ил.
Дунаев П.Ф. Леликов О.П. Конструирование узлов и деталей машин: Учеб. пособие для техн. спец. вузов. – М.: Высш. шк. 2000. – 447с.
Спецификация.spw

Болт М6-6g x 18.109.35
Болт М14-6g x 40.109.35 (S21)
Винт А. М6-6g x 8.14H
Гайка М14-6H.04 (S21)
Манжета 1.1-30x50-3
Рабочий чертеж корпуса редуктора.cdw

Точность отливки 11-0-0-11 ГОСТ 26645-85
Допускаются дефекты на литых поверхностях глубиной до 2 мм
Допускается исправление литейных дефектов
газо- или электросваркой с последующей зачисткой
или заделкой пастой АСТ 79-69-62 или пайкой
Неуказанные предельные отклонения механически обрабатываемых
Неуказанные литейные радиусы R1max.
Покрытие до механической обработки грунтовка
РГАТА им. П. А Соловьёва
Общий вид привода.cdw

Смещения выходного вала редуктора
Радиальная консольная нагрузка
на выходном валу редуктора
Техническая характеристика
Вращающий момент на выходном валу
Частота вращения выходного вала
Общее передаточное число 9
Привод с планетарным
План фундамента (1:2
Спецификация ВО.spw

РГАТА им.П.А.Соловьева
Пояснительная записка
-6gx50.109.30ХГСА (S18)
Болт 6.3.M 12 x 200 .Ст3кп
Гайка М12-6H.04 (S18)
Рекомендуемые чертежи
- 02.11.2021
- 01.07.2014