Привод главного движения координатно-расточного станка



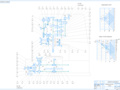
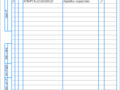
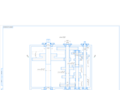
- Добавлен: 25.01.2023
- Размер: 1 MB
- Закачек: 2
Описание
Привод главного движения координатно-расточного станка
Состав проекта
![]() |
![]() |
![]() ![]() ![]() ![]() |
![]() ![]() ![]() ![]() |
![]() ![]() ![]() |
![]() ![]() ![]() ![]() |
![]() ![]() ![]() |
![]() ![]() ![]() |
Дополнительная информация
Ведомость.spw

КПКИМ.14.01.00.000.КЗ
Кинематическая схема
Кинематика 1.cdw

Титул.doc
УО «Полоцкий государственный университет»
кафедра «Технологии и оборудования
машиностроительного производства»
по дисциплине «Конструирование изделий машиностроения»
Тема: «Привод главного движения координатно-расточного станка»
Коробка.cdw

Записка.doc
Разработка и описание компоновки станка.
Проектирование и описание кинематической схемы станка 8
Динамические и прочностные расчеты 15
1. Определение крутящих моментов ..15
2. Расчет клиноременной передачи . ..16
3. Расчет зубчатой передачи . . .19
4. Расчет зубчатой передачи . . .23
5. Расчет зубчатой передачи . . .27
6. Расчет вала I на прочность. .31
7. Расчет вала II на прочность. 35
8. Расчет вала III на прочность. 38
9 Расчет вала IV на прочность .42
9. Подбор и проверочный расчет соединений .. 46
9.1. Соединение шкив-вал 1 .. 46
9.2. Соединение блок зубчатых колес-вал I.. .47
9.3. Соединение зубчатое колесо-вал II . . 48
9.4. Соединение блок зубчатых колес-вал III 49
9.5. Соединение зубчатое колесо -вал III.. . 50
9.6. Соединение блок зубчатых колес-вал IV.. . 51
10. Выбор подшипников .. 52
10.1. Вал 1 коробки скоростей .. ..52
10.2. Вал 2 коробки скоростей .. .. 53
10.3. Вал 3 коробки скоростей .. .. 53
10.4. Вал 4 коробки скоростей .. .. 54
Выбор вида смазывания передач и подшипников уплотняющих
Описание проектируемого узла. 56
В настоящем курсовом проекте решаются задачи связанные с изучением и анализом существующих аналогичных решений обоснованием выполняемых разработок на всех этапах проектирования разработкой оригинальных конструкций. При этом предполагается максимальное использование справочной литературы ГОСТов типовых решений и вычислительной техники.
В этом проекте решаются вопросы выбора и оптимизации технических характеристик станка проектирования кинематической схемы и одного узла координатно-расточного станка исследования новых технических решений модернизации существующих станков обоснования выбранных конструктивных вариантов.
Производятся выбор и описание структурной схемы и компоновки станка динамические и прочностные расчеты проектируемых узлов дается описание конструкции работы и смазки спроектированного узла и в заключении приводится анализ проделанной работы.
Проект состоит из пояснительной записки спецификации и графической части. Объем этих документов этих документов зависит от объема всего проекта установленного учебной программой. Объем графической части составляет три листа формата А1.
Определение технических характеристик станка.
Частота вращения шпинделя nmin
Мощность электродвигателя Nэл.
Наибольший условный диаметр сверления
Расточные станки предназначаются для обработки деталей в условиях единичного и серийного производств. Это широкоуниверсальные станки на которых можно производить черновое и чистовое растачивание отверстий обтачивание наружных цилиндрических поверхностей и торцов отверстий сверление зенкерование и развертывание отверстий фрезерование плоскостей нарезание резьбы и другие операции. Большое разнообразие различных видов обработки производимых на расточных станках позволяет в ряде случаев проводить полную обработку детали без перестановки ее на другие станки что особенно важно для тяжелого машиностроения.
Характерной особенностью расточных станков является наличие горизонтального (или вертикального) шпинделя который совершает движение осевой подачи В шпинделе крепится режущий инструмент—борштанга с резцами сверло зенкер фреза метчик и др.
Параметром определяющим все основные размеры станка является диаметр расточного шпинделя.
Рис. 2.1. Общий вид координатно-расточного станка
Формообразующими движениями в расточных станках являются: вращение шпинделя и движение подачи. Подача сообщается либо инструменту либо заготовке в зависимости от условий обработки. Вспомогательными движениями являются: установочные перемещения шпиндельной бабки в вертикальном направлении установочные перемещения стола в продольном и поперечном направлениях установочное перемещение задней стойки с люнетом перемещение люнета по стойке.
Координатно-расточные станки предназначены для обработки отверстий в кондукторах приспособлениях и деталях для которых требуется высокая точность взаимного расположения отверстий. Наряду с растачиванием на станках могут выполняться сверлильные операции чистовое фрезерование разметка и проверка линейных размеров в частности межцентровых расстояний. Применяя поставляемые со станком поворотные столы и другие принадлежности можно кроме того обрабатывать отверстия заданные в полярной системе координат наклонные и взаимноперпендикулярные отверстия и протачивать торцовые поверхности.
На рис. 2.1 представлен общий вид координатно-расточного станка. Основные узлы станка: 1. Станина 2. Колонна 3. Привод главного движения 4. Стол.
Компоновку заимствуем у станка прототипа.
Проектирование и описание кинематической
Главными приводами со ступенчатым регулированием частоты вращения шпинделя оснащают универсальные станки работающие в единичном и ремонтном производствах. Такие приводы просты компактны имеют высокий КПД долговечны.
Диапазон регулирования Rn частоты вращения исполнительного органа привода определяется по формуле:
Предельные частоты вращения принимаются равными nmax=2500 мин-1 и nmin=10 мин-1 (по заданию на проектирование). С учетом этого диапазон регулирования:
Число ступеней частоты вращения выходного вала определяется по формуле:
Тогда число ступеней:
Число ступеней не может быть дробным поэтому для обеспечения возможности регулирования скорости вращения во всем диапазоне частот принимается z=18. Тогда формула структуры привода z=3(1)3(3)2(9)
Создадим частичное перекрытие ступеней частоты вращения.
Исправим нормальную структуру путем уменьшения на xП=3 характеристики x3=9 последней группы с целью получения перекрытия ступеней частот вращения на последнем валу. Фактическая характеристика последней группы . Фактическое число ступеней частоты вращения на последнем валу .
Тогда формула структуры привода z=3(1)3(3)2(6)
Для составления кинематической схемы привода необходимо дополнить групповые передачи одиночными и соединить коробку с двигателем. Одиночные передачи используются в приводе с целью обеспечения требуемой редукции частоты вращения двигателя и получения стандартных значений частоты вращения шпинделя для передачи движения от коробки к шпинделю.
Для определения передаточных отношений передач привода необходимо в соответствии со структурной формулой построить структурную сетку (см. рис. 3.1).
Рис. 3.1. Структурная сетка
Затем строится график частот вращения (см. рис. 3.2).
Рис. 3.2. График частот вращения
По этому графику определяются передаточные отношения всех передач и проставляем их на графике: .
Произведём расчет чисел зубьев колес для основной группы аналитическим способом.
Формулы для расчета чисел зубьев колес аналитическим способом имеют вид:
где а и b – взаимно простые числа через которые выражается данное
передаточное отношение т. е.
- сумма чисел зубьев в рассматриваемой группе (определяется
наименьшее общее кратное сумм этой группы)
Тогда для основной группы:
Следовательно а наименьшее общее кратное сумм равно 72 которое присвоим Тогда числа зубьев колес передачи составят
Тогда для первой переборной группы:
Следовательно а наименьшее общее кратное сумм равно 60 (примем 120) которое присвоим Тогда числа зубьев колес передачи составят
Тогда для второй переборной группы:
Следовательно а наименьшее общее кратное сумм равно 15 (примем 90) которое присвоим Тогда числа зубьев колес передачи составят
Следует иметь в виду что рассчитанные из кинематических условий числа зубьев колес в дальнейшем при разработке конструкции привода могут быть изменены при сохранении значений передаточных отношений.
Рис. 3.3 Схема коробки скоростей.
Привод подач заимствуем у станка-прототипа. Кинематическая схема представлена на рисунке 3.4.
Рис. 3.4 Кинематическая схема
Описание кинематической схемы станка.
Главное движение шпинделя осуществляется от асинхронного электродвигателя через ременную передачу 125 – 250 на вал I коробки скоростей цилиндрическую зубчатую передачу (z=19) – 2(z=53) либо 3(z=42) – 4(z=30) либо 5(z=24) – 6(z=48)на вал II коробки скоростей далее через цилиндрическую зубчатую передачу 7(z=40) – 8(z=80) либо 9(z=50) – 10(z=70) либо 11(z=24) – 12(z=96) на вал III коробки скоростей далее через цилиндрическую зубчатую передачу 13(z=60) – 14(z=30) либо 15(z=18) – 16(z=72) на шпиндель IV.
Привод подачи осуществляется от выходного вала коробки скоростей через передачу 17(z=43) – 18(z=86) на вариатор 62 на вал 13 далее через червячную передачу 19(к=2) – 20(z=32) на вал 7 и далее на реверсивный механизм с зубчатыми колесами 21 22 23(z=28) на червячную передачу 24(к=1) – 25(z=56) на рейку шпинделя 30.
Механическая подача стола в продольном и поперечном направлениях используемая при тонком фрезеровании осуществляется реверсивным электродвигателем мощностью 04 кет. Движение передается через цепную передачу 41(z=16) – 42(z=50) перебор 44(z=20) – 44(z=84) и 45(z=14) – 46(z=90) (при правом положении муфты М4) вал XI. шестерни 47(z=28)-48(z=50)-49(z=50) червячные и реечные передачи.
Для осуществления продольной подачи включается муфта М5. при этом вращение сообщается валу XX червячной передаче 58(k=1) – 59(z=55) валу XХI и реечной шестерне 60(z=14) находящейся в зацеплении с рейкой 61 прикрепленной к продольным салазкам стола. Поперечная подача стола включается муфтой М6 этом цепь движения аналогична предыдущей.
Для сообщения столу быстрых перемещений муфта М4 включается влево при этом движения передаются столу непосредственно от вала ХХ минуя перебор.
Ручное перемещение шпинделя осуществляется при помощи маховика.
ДИНАМИЧЕСКИЕ И ПРОЧНОСНЫЕ РАСЧЕТЫ
1. Определение крутящих моментов
Следует отметить что при динамическом расчете привода главного движения максимальный крутящий момент на выходе коробки скоростей определяется не по номинальной а по расчетной частоте его вращения которая принимается равной первой ступени второй четверти диапазона регулирования скорости т.е. n4=45 обмин а также исходя из расчета наиболее нагруженных передач за расчетные принимаются частоты на валах: nI=710 мин-1 nII=250 мин-1 nIII=180 мин-1 nIV=45 мин-1.
Крутящий момент на валу электродвигателя (М1)
где: кВт - мощность электродвигателя принимается из задания на проектирование.
Частота вращения на валу двигателя:
Мощность на первом валу коробки скоростей определяется по формуле:
РI=Pэд×hэд×hр.п×hп ; (4.1)
где hэд=097 hп=099 hзп=094 КПД соответственно электродвигателя пары подшипников и ременной передачи 8 табл. 5.4.
Тогда мощность и угловая скорость на первом валу:
РI =72×097×099×094=6499 кВт;
Теперь можно определить наибольший крутящий момент по формуле:
Мощность на втором валу коробки скоростей:
Тогда мощность и угловая скорость на втором валу:
РII =6499×096×099=6177 кВт;
Мощность и угловая скорость на третьем валу:
РIII =6177×096×099=587 кВт;
Мощность на шпинделе:
Тогда мощность и угловая скорость на шпинделе:
РIV =587×096×099=5579 кВт;
Наибольший крутящий момент:
2. Расчет клиноременной передачи
Расчет клиноременной передачи производим с целью получения сил действующих на первый вал которые в дальнейшем понадобятся при расчете вала на прочность.
Р1=72 кВт; Р2=6499 кВт; n1=1440 мин-1; n2=710 мин-1; u=2028;
T1=477 Н·м; T2=8746 Н·м. Межосевое расстояние а=500 мм.
Сечение ремня и размеры сечения:
сечение ремня =f(Т1р) [8 табл. 2.2.1 с.16]
сечение ремня =f(Р1р n1) [8 рис. 2.2.1 с.18]
где Т1р=Т1·ср расчетный передаваемый момент Н·м;
Р1р=Р1·ср расчетная передаваемая мощность кВт;
ср коэффициент учитывающий динамичность нагружения передачи и режим ее работы. ср=15 [8 табл. 2.2.2 с.16]
Минимальный расчетный диаметр ведущего шкива мм d1min=f(сечения ремня) [8 табл. 2.2.1] (d1min=125 мм). Действительный диаметр d1³d1min (первый больший) [8 табл.2.2.4] d1=125 мм.
Диаметр ведомого шкива мм d2=d1·u. Действительный диаметр мм d2d2 [8 табл.2.2.4] (первый меньший).
Действительное передаточное число проектируемой передачи
где =(001÷002) коэффициент упругого скольжения.
Для реализации передачи принимается ремень сечения Б со следующими параметрами Вp=14 В=17 Нp=11 Н=40 (ГОСТ20889-88).
Минимальное межосевое расстояние мм.
Расчетная длина ремня мм
Lp³Lp [8 табл. 2.2.6] и [8 табл. 2.3.1]
Принимаем Lp=1600 мм.
Межцентровое расстояние мм
Коэффициент учитывающий длину ремня
(сечение ремня) [8 табл.2.3.3]
Для сечения Б Lр=1600 мм
Угол обхвата ремнем ведущего шкива град
Значение коэффициента учитывающего влияние угла обхвата на ведущем шкиве [8 табл.2.1.3].с=097
Число ремней передачи шт
где Р0 – мощность передаваемая одним ремнем кВт; Р0=f(сечения ремня ) (табл. 2.2.7); - коэффициент учитывающий число ремней в передаче. =f(z) (табл. 2.2.5). Предварительно можно принять =10 а потом уточнить. z- целое число. Р0=226 кВт
Сила нагружающая валы передачи Н
где предварительное натяжение ремня Н
Сила нагружающая ведомый шкив:
Расчетная долговечность по [ 9 форм. 8.16] :
где - наибольшее напряжение в ведущей ветви в месте набега на малый шкив по [ 9 форм. 8.10].
где s 0 - напряжение от предварительного натяжения; s 0 = 1.2 МПа по [ 9 табл.8.10.]
- полезное напряжение по 9 стр. 166.
МПа – напряжение изгиба на малом шкиве по [ 9 форм. 8.9].
где Е = 60-150 МПа – модуль продольной упругости для ремней кордошнуровых по [ 9 стр.146].
d = 11 мм – толщина ремня
d min = 125 мм – диаметр меньшего шкива.
s V = r × V 2 × 10 –6 = 1400 × 9422 × 10 –6 = 0.12 МПа – напряжение от центробежной силы по 9 стр. 146. Где плотность ремня кгм3 для прорезиненных и клиновых ремней =1200-1500 кгм3
s y = 9 МПа – предел выносливости для клиновых ремней по 9стр.151.
m = 8 – для клиновых ремней по [ 9 стр. 151].
С U = 1.1 – коэффициент учитывающий влияние передаточного числа по [ 9 стр. 151].
С Н = 1.5 – коэффициент учитывающий непостоянство нагрузки по [ 9 стр. 151].
- число пробегов в секунду
В процессе эксплуатации будет необходимо производить замену ремней по истечении 59094 ч.
3. Расчет зубчатой передачи.
Для понижающей зубчатой передачи (1953) принимается прямозубая цилиндрическая передача как наиболее простая в изготовлении. Принимается для изготовления колес передачи для уменьшения номенклатуры сталь 40Х (улучшение) со следующими механическими характеристиками:
для ведущего колеса sв=830 Нмм2 sт=540 Нмм2 НВ=240 290;
для ведомого колеса sв=930 Нмм2 sт=690 Нмм2 НВ=260 300.
Пределы контактной выносливости по [9] табл. 9.11:
для ведомого колеса: s Нlimb=2×HB+70=2×295+70=660 Hмм 2
для ведущего колеса: s Нlimb=2×HB+70=2×285+70=640 Hмм 2
Расчетное число циклов перемены напряжений определяется по формуле [9 с. 193 форм. 9.32]:
где n1 частота вращения ведущего колеса n1=710 обмин;
с число колес находящихся в зацеплении с рассчитываемым принимается с=1.
Lh расчетный срок службы передачи определяется по формуле [9 с. 14]:
Lh=8760×L×Kг×Кс; (4.4)
где L долговечность принимается равной 10 годам.
Кг коэффициент использования в течении года принимается Кг=066.
Кс коэффициент использования в течении суток принимается Кс=025.
Lh=8760×10×066×025=14454 ч ;
NH=60×710×1×14454=61×10 8;
Для ведущего колеса и тем более для ведомого NH >NHO=18×10 7 поэтому принимаем коэффициент долговечности KHL=1 [9 с.191]
Допускаемые контактные напряжения при расчете на выносливость по формуле [9 с. 192 форм. 9.30]
где SH для улучшенных зубьев по [9 с. 192] SH=11.
для ведомого колеса: Hмм 2
для ведущего колеса: Hмм 2
Так как передача прямозубая расчет ведем по s НР наименьшему.
Допускаемые напряжения изгиба по формуле [9 с. 193 форм. 9.35]:
для ведомого колеса: s Flimb=260+HB=260+295=555 Hмм 2
для ведущего колеса: s Flimb=260+HB=260+285=545 Hмм 2
Допускаемые напряжения при SF=2 и KFC=1 односторонняя нагрузка по [9 с. 193] КFL=1 т.к. NFE=60×Lh×n1×с =60×14454×710×1=61×108>NF0=4×106
Ориентировочное значение модуля по формуле [9 с. 184 форм. 9.5]:
где ybd коэффициент ширины шестерни относительно диаметра принимается ybd=04;
YF1 коэффициент учитывающий форму зуба по [9 с. 184 рис. 9.6] принимается YF1=41;
KFb коэффициент учитывающий неравномерность распределения нагрузки по ширине венца по [9 с. 182 рис. 9.5] принимается KFb=105;
Km вспомогательный коэффициент для прямозубых передач принимается Km=14;
Число зубьев колес принимаются по п. 3.3: z1=19 z2=53;
Уточняем диаметры колес по [9 с. 176]:
da1=d1+2×m=57+2×3=63 мм
da2=d2+2×m=159+2×3=165 мм (4.8)
df1=d1–2.5×m=57–2.5×3=495 мм
df2=d2–2.5×m=159–2.5×3=1515 мм
Межосевое расстояние:
Рабочая ширина зацепления:
bw=ybd×d1=04×57=228 мм принимаем bw=25 мм . (4.10)
Проверочный расчет на выносливость по контактным напряжениям. Окружная сила:
По [9 с. 187 табл. 9.10] назначаем девятую степень точности. По [9 с. 186 табл. 9.9] принимаем g 0=73. По [9 с. 186 табл. 9.7] dН=0006.
Удельная расчетная окружная сила в зоне ее наибольшей концентрации рассчитывается по формуле: [9] форм. 9.10:
KНb коэффициент учитывающий неравномерность распределения нагрузки по ширине венца по [9 с. 182 рис. 9.5] принимается KFb=101.
передаточное отношение.
Коэффициент учитывающий динамическую нагрузку возникающую в зацеплении определяем по формуле [9 с. 188 форм.9.15]:
Удельная расчетная окружная сила по формуле [9 с. 185 форм. 9.8]:
Расчетное контактное напряжение по формуле [9 с. 185 форм. 9.7]:
где zH коэффициент учитывающий форму сопряженных поверхностей в полюсе зацепления по [9] стр.185:
zМ – коэффициент учитывающий механические свойства материалов колес по[9 с. 185] zМ=275 Мпа.
ze коэффициент учитывающий суммарную длину контактных линий по [9 с. 185]:
где ea коэффициент торцового перекрытия по [9 с. 174 табл. 9.1]:
Следовательно условие прочности выполнено.
Проверка по напряжениям изгиба. Расчетное напряжение изгиба на переходной поверхности зуба по [9 с. 187 форм. 9.11]:
где YF1=42 коэффициент учитывающий форму зуба по [9 с. 184 рис. 9.6];
YF2=37 коэффициент учитывающий форму зуба по [9 с. 184 рис. 9.6];
Yb=1-b140=1 коэффициент учитывающий наклон зуба по [9 с.187];
Ye=1 коэффициент учитывающий перекрытие зубьев по [9 с.187];
Определяем менее прочное звено:
ведущее колесо менее прочное.
Расчет производим по ведущему колесу.
Из графика [9 с. 182 рис.9.5] коэффициент концентрации нагрузки КFb=105.
По [9с. 185 форм. 9.10]:
где dF=0016 коэффициент учитывающий влияние вида зубчатой передачи и модификации профиля головок зубьев по [9 с 186 табл. 9.8].
По [9 с. 188 форм. 9.16]:
Коэффициент динамической нагрузки по [9 с. 188 форм. 9.15]:
Удельная расчетная окружная сила по [9] форм. 9.12:
где КFa=1 для прямозубых передач по [9 с.188].
sF=42×1×1×17143=240sFP=2775 Нмм 2
Напряжение изгиба действующее в зацеплении меньше допускаемого значит условие прочности выполнено.
4. Расчет зубчатой передачи.
Для зубчатой передачи (5070) принимается прямозубая цилиндрическая передача как наиболее простая в изготовлении. Принимается для изготовления колес передачи для уменьшения номенклатуры сталь 40Х (улучшение) со следующими механическими характеристиками:
где n1 частота вращения ведущего колеса n1=250 обмин;
NH=60×250×1×14454=21×10 8;
для ведомого колеса: s Flimb=260+HB=260+300=560 Hмм 2
Допускаемые напряжения при SF=2 и KFC=1 односторонняя нагрузка по [9 с. 193] КFL=1 т.к. NFE=60×Lh×n1×с =60×14454×250×1=21×108>NF0=4×106
где ybd коэффициент ширины шестерни относительно диаметра принимается ybd=03;
YF1 коэффициент учитывающий форму зуба по [9 с. 184 рис. 9.6] принимается YF1=365;
KFb коэффициент учитывающий неравномерность распределения нагрузки по ширине венца по [9 с. 182 рис. 9.5] принимается KFb=102;
Число зубьев колес принимаются по п. 3.3: z1=50 z2=70;
принимается m=225 мм.
d1=m×z1=225×50=1125 мм
d2=m×z2=225×70=1575 мм
da1=d1+2×m=1125+2×225=108 мм
da2=d2+2×m=1575+2×225=153мм
df1=d1–2.5×m=1125–25×225=106875 мм
df2=d2–2.5×m=1575–25×225=151875 мм
bw=ybd×d1=03×1125=3375 мм принимаем bw=35 мм .
где YF1=365 коэффициент учитывающий форму зуба по [9 с. 184 рис. 9.6];
YF2=36 коэффициент учитывающий форму зуба по [9 с. 184 рис. 9.6];
- ведомое колесо менее прочное.
Расчет производим по ведомому колесу.
Из графика [9 с. 182 рис.9.5] коэффициент концентрации нагрузки КFb=102.
Удельная расчетная окружная сила по [9] форм. 9.12 :
sF=36×1×1×1467225=234sFP=2775 Нмм 2
Для понижающей зубчатой передачи (1872) принимается прямозубая цилиндрическая передача как наиболее простая в изготовлении. Принимается для изготовления колес передачи для уменьшения номенклатуры сталь 40Х (улучшение) со следующими механическими характеристиками:
где n1 частота вращения ведущего колеса n1=180 обмин;
NH=60×180×1×14454=15×10 8;
Допускаемые напряжения при SF=2 и KFC=1 односторонняя нагрузка по [9 с. 193] КFL=1 т.к. NFE=60×Lh×n1×с =60×14454×180×1=15×108>NF0=4×106
YF1 коэффициент учитывающий форму зуба по [9 с. 184 рис. 9.6] принимается YF1=43;
Число зубьев колес принимаются по п. 3.3: z1=18 z2=72;
da1=d1+2×m=90+2×5=100 мм
da2=d2+2×m=360+2×5=370мм
df1=d1–2.5×m=90–25×5=775 мм
df2=d2–2.5×m=360–25×5=3475 мм
bw=ybd×d1=04×90=36 мм принимаем bw=40 мм .
где YF1=43 коэффициент учитывающий форму зуба по [9 с. 184 рис. 9.6];
YF2=365 коэффициент учитывающий форму зуба по [9 с. 184 рис. 9.6];
sF=43×1×1×21165=182sFP=2775 Нмм 2
6. Расчет вала I на прочность.
Составляем расчетную схему где вал рассматриваем как балку лежащую на шарнирных опорах и намечаем расстояние между опорами.
Окружное усилие в зацеплении:
Ft21 = 2 * Т1 d1 = 2 * 18746 0057 = 30687 Н;
Радиальное усилие в том же зацеплении:
Fr21 = Ft21 * tg200 = 30687 · 0364 = 1117 H;
На вал I со стороны ременной передачи действует сила Ft которая определена в п. 4.1 F = 1543 Н;
Строим схему нагружения вала 1 рис. 4.1.
Определяем опорные реакции в вертикальной плоскости (ZOY):
M A = 0: RBy *600 + F * 35 – Fr21 * 110 = 0;
M B = 0: RAy * 600 - F * 635 + Fr21 * 490 = 0;
Определяем опорные реакции в горизонтальной плоскости (ZOX):
Принимаем с учетом рекомендаций по 9 стр. 291 материал вала – сталь 45. По 9 табл. 12.13 для стали 45 : s -1 = 432 Нмм 2 t -1 = 255 Нмм 2 – пределы выносливости материала вала при симметричных циклах изгиба и кручения s B = 883 Нмм 2 – предел прочности. По 9 табл. 12.2 es= 0.91 – коэффициент учитывающий снижение механических свойств материала с увеличением размера заготовок для углеродистых сталей. По 9 табл. 12.5 Кs= 1.7 – эффективный коэффициент концентрации напряжений для шлицевых участков вала. По 9 стр. 275: S = 3 – коэффициент безопасности при симметричном изменении напряжения изгиба и кручения. По 9 табл. 12. 9 b = 2 – коэффициент учитывающий упрочнение поверхности при поверхностной закалке.
Эквивалентное число циклов :
N LE = NH = 60 * 710 * 1 * 14454 = 61 * 10 8 ;
Коэффициент долговечности:
где m = 9 – показатель степени кривой усталости по 9 стр.275.
N 0 = 5 * 10 6 – базовое число циклов перемены напряжений по 9 стр275.
Допускаемый предел выносливости при симметричных циклах изгиба по 9 форм. 12.3:
Суммарный изгибающий момент в опасных сечениях:
Эквивалентный момент в опасных сечениях по 9 стр.185 :
ME I = T = 187460 Н*мм
Диаметр в опасных сечениях по 9 форм. 12.2:
d I = 25 мм – диаметр вала под шкив.
d II = 30 мм – диаметр вала под подшипниками.
d III = 32 мм – диаметр вала под зубчатым колесом.
Рис. 4.1. Схема нагружения вала I
Нормальные напряжения возникающие в поперечном сечении вала от изгиба изменяется по симметричному циклу по 8 форм.14.14 :
где W – момент сопротивления вала со шлицами(6х32х38):
где – для шлицев средней серии наружный диаметр d = 38 мм.
s а = М ЕIII W = 3633175 6488 = 56 Мпа
Так как момент передаваемый валом является переменным то при расчете примем для касательных напряжений наиболее благоприятный знакопостоянный цикл – отнулевой по 8 форм. 14.15:
t а = t m = Т (2*WK) ; (4.29)
t а = t m = 187460 (2*129762) = 72 Мпа
Коэффициент запаса прочности по нормальным напряжениям по 8 форм. 14.9:
где e s = 0.88 - масштабный фактор по 8 табл. 12.2.
По 8 табл. 12.6 для шлицевых валов К s = 1.7 – эффективный коэффициент концентрации напряжений при изгибе. По 8 табл. 14.4 y s = 0.12 – коэффициент учитывающий влияние постоянной составляющей цикла на усталость вала.
где e t = 0.81 - масштабный фактор по 8 табл. 12.1.
По 8 табл. 14.2 К t = 265 – эффективный коэффициент концентрации напряжений при изгибе. По 8 табл. 14.4 y t = 0.7 – коэффициент учитывающий влияние постоянной составляющей цикла на усталость вала.
Условие прочности по 8 форм. 14.8:
где [S] = 1.3 1.5 – требуемый коэффициент запаса для обеспечения прочности.
Прочность вала в опасном сечении обеспечена.
6. Расчет вала II на прочность.
Ft32 = 2 * Т2 d2 = 2 * 23606 01125 = 41966 Н;
Fr32 = Ft32 * tg200 = 41966 · 0364 = 15275 H;
M A = 0: -RBy*520+Ft21*490- Fr32*160=0;
M B = 0: -RAy*520+Fr32*360- Ft21*30=0;
Принимаем с учетом рекомендаций по 9 стр. 291 материал вала – сталь 40ХН. По 9 табл. 12.13 для стали 40ХН : s -1 = 490 Нмм 2 t -1 = 294 Нмм 2 – пределы выносливости материала вала при симметричных циклах изгиба и кручения s B = 981 Нмм 2 – предел прочности. По 9 табл. 12.2 es= 083 – коэффициент учитывающий снижение механических свойств материала с увеличением размера заготовок для легированных сталей. По 9 табл. 12.5 Кs= 1.7 – эффективный коэффициент концентрации напряжений для шлицевых валов. По 9 стр. 275: S = 3 – коэффициент безопасности при симметричном изменении напряжения изгиба и кручения. По 9 табл. 12. 9 b = 2 – коэффициент учитывающий упрочнение поверхности при поверхностной закалке.
Эквивалентное число циклов:
N LE = NH = 60 * 250 * 1 * 14454 = 21 * 10 8 ;
Рис. 4.2. Схема нагружения вала II
d I = 30 мм – диаметр вала под подшипниками.
d II = 35 мм – диаметр вала под зубчатым колесом.
где W – момент сопротивления вала со шлицами(8х36х42):
где – для шлицев средней серии наружный диаметр d = 42 мм.
s а = М ЕIII W = 531205 87602 = 606 Мпа
t а = t m = Т (2*WK) ;
t а = t m = 236060 (2*17520) = 67 Мпа
где e s = 0.77 - масштабный фактор по 8 табл. 12.2.
7. Расчет вала III на прочность.
Ft43 = 2 * Т3 d3 = 2 * 3166 009 = 70355 Н;
Fr43 = Ft43 * tg200 = 70355 · 0364 = 2561 H;
M A = 0: -RBy*600+Fr43*405- Ft32*160=0;
M B = 0: -RAy*600-Fr43*195+ Ft32*440=0;
N LE = NH = 60 * 180 * 1 * 14454 = 156 * 10 8 ;
Рис. 4.3. Схема нагружения вала III
d I = 35 мм – диаметр вала под подшипниками.
d II = 40 мм – диаметр вала под зубчатым колесом.
где W – момент сопротивления вала со шлицами(8х42х48):
где – для шлицев средней серии наружный диаметр d = 48 мм.
s а = М ЕIII W = 911656 13076 = 697 Мпа
t а = t m = 316600 (2*26153) = 605 Мпа
где e s = 0.73 - масштабный фактор по 8 табл. 12.2.
где e t = 0.78 - масштабный фактор по 8 табл. 12.1.
8. Расчет вала IV на прочность.
Окружное усилие в зацеплении 1872:
Ft43 = 2 * Т3 d = 2 * 3166 009 = 70355 Н;
Окружное усилие в зацеплении 4386:
Ft54 = 2 * Т4 d = 2 * 11845 0215 = 110186 Н;
Fr54 = Ft54 * tg200 = 110186 · 0364 = 40107 H;
M A = 0: -RBy*600+Ft54*635-Fr43*195=0;
M B = 0: -RAy*600+Ft54*35+ Fr43*405=0;
N LE = NH = 60 * 45 * 1 * 14454 = 39 * 10 7 ;
ME I = T = 1184500 Н*мм
Рис. 4.4. Схема нагружения вала IV
d I = 55 мм – диаметр вала под подшипниками.
d II = 62 мм – диаметр вала под зубчатым колесом.
где W – момент сопротивления вала со шлицами(8х62х72):
где – для шлицев средней серии наружный диаметр d = 72 мм.
s а = М ЕIII W = 3516556 44133 = 796 Мпа
t а = t m = 1184500 (2*88226) = 67 Мпа
где e s = 0.68 - масштабный фактор по 8 табл. 12.2.
где e t = 0.74 - масштабный фактор по 8 табл. 12.1.
9. Подбор и проверочный расчет соединений.
9.1. Соединение шкив-вал 1.
Выбираем по стандарту призматическую шпонку для соединения зубчатого колеса с валом d = 25 мм. Материал шпонки – Сталь 20 передаваемый момент Т = 8746 Н*м соединение работает при переменной нагрузке. По ГОСТ 23360-78 выбираем шпонку призматическую обыкновенную (исполнение А) со следующими размерами:
B = 7 мм ; h = 7 мм ; t 1 = 4 мм ; t 2 = 33 мм ;
Находим допускаемое напряжение смятия по [8] табл. 5.1:
Определяем рабочую длину шпонки по [8]форм. 5.1:
где k – рабочая высота k = 0.4 * h = 0.4 * 7 = 28 мм.
Находим общую длину шпонки:
L = l P + b = 33 + 3 = 66 мм (4.34)
Принимаем: шпонка 7 7 22 ГОСТ 23360-78
9.2. Соединение блока зубчатых колес – вал 1.
Для соединения блока зубчатых колес с валом 1 принимается шлицевое соединение 6 х 32 х 38 по ГОСТ 1139-58. По [8] табл. 4.5 определяется суммарный статический момент площади рабочих поверхностей соединения относительно оси вала sF = 308 мм2 мм и средний диаметр dm = 0.5 * ( D + d ) = 0.5 * ( 32 + 38 ) = 35 мм.
Среднее давление по [9] форм. 5.8:
Допускаемое давление на смятие по [9] форм. 5.10:
Где sТ — предел текучести материала шлицев по [9] табл.12.13 принимается sТ = 638 Нмм2 .
КСМ — общий коэффициент концентрации нагрузки при расчете на смятие по [9] стр.87:
КСМ = Кз * Кпр * Кп ;
Кз — коэффициент неравномерности распределения нагрузки между шлицами определяется в зависимости от параметра:
по [9] табл.5.7 Кз = 15.
Кпр — коэффициент продольной концентрации нагрузки ( по длине соединения) по [9] стр.83:
Значение коэффициента Ккр определяется по [9] табл.5.8 в зависимости от lD = 9138 = 24 и принимается Ккр = 46.
Значение коэффициента концентрации давления Ке от относительного смещения нагрузки определяется в зависимости от параметра e по [9] стр. 88:
для прямозубых колес b = 0 е = 33 мм — расстояние от середины посадочной поверхности до середины венца зубчатого колеса тогда по [9] рис.5.12 Ке = 14.
Кпр = 46 + 14 – 1 = 5
Кп = 1.1 — для закаленных сталей.
Тогда коэффициент концентрации нагрузки при расчете на смятие:
Ксм = 15 * 5 * 11 = 825
КД = 2 — коэффициент динамичности нагрузки.
Тогда допускаемое давление на смятие:
Соединение удовлетворяет условию прочности на смятие т.к. s = 312 [s] = 276 Нмм2 .
9.3. Соединение зубчатого колеса – вал 2.
Для соединения зубчатого колеса с валом 2 принимается шлицевое соединение 8 х 36 х 42 по ГОСТ 1139-58. По [8] табл. 4.5 определяется суммарный статический момент площади рабочих поверхностей соединения относительно оси вала sF = 343 мм2 мм и средний диаметр dm = 0.5 * ( D + d ) = 0.5 * ( 36 + 42 ) = 39 мм.
по [9] табл.5.7 Кз = 27.
Значение коэффициента Ккр определяется по [9] табл.5.8 в зависимости от lD = 4039 = 1025 и принимается Ккр = 13.
для прямозубых колес b = 0 е = 20 мм — расстояние от середины посадочной поверхности до середины венца зубчатого колеса тогда по [9] рис.5.12 Ке = 24.
Кпр = 13 + 24– 1 = 27
Ксм = 27 * 27 * 11 = 8
Соединение удовлетворяет условию прочности на смятие т.к. s = 756 [s] = 164 Нмм2 .
9.4. Соединение блок зубчатых колес-вал 3.
Для соединения блока зубчатых колес с валом 3 принимается шлицевое соединение 8 х 36 х 42 по ГОСТ 1139-58. По [8] табл. 4.5 определяется суммарный статический момент площади рабочих поверхностей соединения относительно оси вала sF = 343 мм2 мм и средний диаметр dm = 0.5 * ( D + d ) = 0.5 * ( 36 + 42 ) = 39 мм.
по [9] табл.5.7 Кз = 17.
Значение коэффициента Ккр определяется по [9] табл.5.8 в зависимости от lD = 12139 = 31 и принимается Ккр = 45.
для прямозубых колес b = 0 е = 43 мм — расстояние от середины посадочной поверхности до середины венца зубчатого колеса тогда по [9] рис.5.12 Ке = 18.
Кпр = 45 + 18– 1 = 53
Ксм = 17 * 53 * 11 = 10
Соединение удовлетворяет условию прочности на смятие т.к. s = 57 [s] = 227 Нмм2 .
9.5. Соединение зубчатого колеса – вал 3.
Для соединения зубчатого колеса с валом 3 принимается шлицевое соединение 8 х 42 х 48 по ГОСТ 1139-58. По [8] табл. 4.5 определяется суммарный статический момент площади рабочих поверхностей соединения относительно оси вала sF = 396 мм2 мм и средний диаметр dm = 0.5 * ( D + d ) = 0.5 * ( 42 + 48 ) = 45 мм.
по [9] табл.5.7 Кз = 12.
Значение коэффициента Ккр определяется по [9] табл.5.8 в зависимости от lD = 4048 = 08 и принимается Ккр = 16.
Кпр = 16 + 24– 1 = 3
Ксм = 12 * 3 * 11 = 396
Соединение удовлетворяет условию прочности на смятие т.к. s = 1998 [s] = 575 Нмм2 .
9.6. Соединение блок зубчатых колес-вал 4.
Для соединения блока зубчатых колес с валом 4 принимается шлицевое соединение 8 х 62 х 72 по ГОСТ 1139-58. По [8] табл. 4.5 определяется суммарный статический момент площади рабочих поверхностей соединения относительно оси вала sF = 1072 мм2 мм и средний диаметр dm = 0.5 * ( D + d ) = 0.5 * ( 62 + 72 ) = 67 мм.
Значение коэффициента Ккр определяется по [9] табл.5.8 в зависимости от lD = 10072 = 138 и принимается Ккр = 3.
для прямозубых колес b = 0 е = 325 мм — расстояние от середины посадочной поверхности до середины венца зубчатого колеса тогда по [9] рис.5.12 Ке = 14.
Кпр = 15 + 14– 1 = 19
Ксм = 15 * 19 * 11 = 3135
Соединение удовлетворяет условию прочности на смятие т.к. s = 11 [s] = 727 Нмм2 .
10. Выбор подшипников.
10.1. Вал 1 коробки скоростей.
Диаметр шейки вала d = 30 мм частота вращения n = 710 мин –1. По [9] табл. 14.18 Кs = 1.2 – коэффициент безопасности.
Требуемая динамическая грузоподъемность для роликовых подшипников вала по [9] стр.358:
где V – коэффициент учитывающий вращение кольца по [9] стр.348 для вращающегося внутреннего кольца V = 1.
X – коэффициент радиальной нагрузки по [9] табл. 14.14 Х = 1.
К Т – температурный коэффициент если она превышает 398.15 0К то по [9] табл. 14.19 К Т = 1.05.
n – частота вращения вала 1.
L h – долговечность подшипника L h = 14454 ч.
Р – степенной показатель для роликовых по [9] стр. 334 р = 103.
Для данного d = 30 мм подшипника по ГОСТ 27365-87 динамическая грузоподъемность С = 52800 Н что больше требуемой поэтому принимается роликовый радиально-упорный подшипник 7306 который соответствует требуемой долговечности и выдержит прикладываемую опорную реакцию.
10.2. Вал 2 коробки скоростей.
Диаметр шейки d = 30 мм частота вращения n = 250 мин –1. По [9] табл. 14.18 Кs = 1.2 – коэффициент безопасности.
Требуемая динамическая грузоподъемность для роликовых подшипников вала по [9] стр.358 :
10.3. Вал 3 коробки скоростей.
Диаметр шейки d = 35 мм частота вращения n = 180 мин –1. По [9] табл. 14.18 Кs = 1.2 – коэффициент безопасности.
Для данного d = 35 мм подшипника по ГОСТ 27365-87 динамическая грузоподъемность С = 68200 Н что больше требуемой поэтому принимается роликовый радиально-упорный подшипник 7307 который соответствует требуемой долговечности и выдержит прикладываемую опорную реакцию.
10.4. Вал 4 коробки скоростей.
Диаметр шейки d = 55 мм частота вращения n =45 мин –1. По [9] табл. 14.18 Кs = 1.2 – коэффициент безопасности.
Для данного d = 55 мм подшипника по ГОСТ 8338-75 динамическая грузоподъемность С = 134000 Н что больше требуемой поэтому принимается радиальный шариковый подшипник 7311 который соответствует требуемой долговечности и выдержит прикладываемую опорную реакцию.
Выбор вида смазывания передач и
подшипников уплотняющих средств
Смазочной системой называют совокупность устройств для подачи смазочного материала к трущимся поверхностям и возврата его в резервуар. Систему смазывания жидким материалом выбирают исходя из требуемой быстроходности механизмов исходя из их расположения конструкции уплотнений. Для данной коробки скоростей лучше использовать циркуляционное смазывание т.к. оно обладает рядом преимуществ: используется один и тот же объем масла что уменьшает стоимость оборудования осуществляется подвод смазки ко всем трущимся поверхностям одновременно что обеспечит независимую смазку каждого узла. Данная система смазки использует струйную подачу смазочного материала к зубчатым передачам посредством трубок. Опоры валов смазываются маслом которое подается в подшипник по валам.
При выборе сорта масла особое внимание необходимо уделить вязкости. Для этого учитывается частота вращения деталей их конструкция и температура. Согласно вышеизложенному целесообразно применить масло марки И-30А.
Описание проектируемого узла.
При выполнении данного курсового проекта я изучил подробно назначение координатно-расточного станка его структуру область применения освоил расчет привода со ступенчатым регулированием скорости усвоил кинематические расчеты проектируемого узла овладел навыками проектирования шестеренчатых коробок скоростей металлорежущего оборудования.
Список используемых источников
Ачеркан Н.С. Металлорежущие станки. Т1. М.- Машиностроение. 1965г.
Общемашиностроительные нормативы расчета режимов резания.
Тарзиманов Г.А. Проектирование металлорежущих станков. М. “Машиностроение” 1972 312 стр.
Данилов В.А. Методические указания к курсовому проекту. Новополоцк – 1987.
Справочник технолога- машиностроителя. В 2-х т. Под ред. А.Г. Косиловой – 4-е изд. перераб. и доп. - М.: Машиностроение 1986 ил.
Анурьев В.И. “Справочник конструктора-машиностроителя”: В 3-х т.- 5-е изд. перераб. и доп.- М.: Машиностроение 1979 ил.
Кочергин А.И. Конструирование и расчет металлорежущих станков и станочных комплексов. Курсовое проектирование: Учеб. пособие для вузов. - Мн.: Выш. шк. 1991. - 382 с.: ил.
Кузьмин А.В. Расчеты деталей машин: Справ. пособие. - 3-е изд. перераб. и доп. - Мн.: Выш. шк. 1986. - 400 с.: ил.
Детали машин в примерах и задачах Под ред. С.Н. Ничипорчика. - 2-е изд. - Мн.: Выш. школа 1981 – 432 с. ил.
Содержание.doc
Разработка и описание компоновки станка. 7
Проектирование и описание кинематической
Динамические и прочностные расчеты 15
1. Определение крутящих моментов ..15
2. Расчет зубчатой передачи . ..16
3. Расчет зубчатой передачи . . .20
4. Расчет зубчатой передачи . . .23
5. Расчет вала I на прочность. ..27
6. Расчет вала II на прочность. . 31
7. Расчет вала III на прочность. 35
8 Расчет вала IV на прочность .39
9. Подбор и проверочный расчет соединений 43
9.1. Соединение зубчатое колесо-вал 1 . .. 43
9.2. Соединение блок зубчатых колес-вал I.. .44
9.3. Соединение зубчатое колесо-вал II . .45
9.4. Соединение зубчатое колесо-вал III 46
9.5. Соединение блок зубчатых колес-вал IV.. . .47
10. Выбор подшипников .. 48
10.1. Вал 1 коробки скоростей .. ..48
10.2. Вал 2 коробки скоростей .. .. 49
10.3. Вал 3 коробки скоростей .. .. 49
10.4. Вал 4 коробки скоростей .. .. 50
Выбор вида смазывания передач и подшипников уплотняющих
Описание проектируемого узла. 52
Рекомендуемые чертежи
- 22.11.2015
- 21.05.2024