Прибор для испытания полимерных материалов на истирание




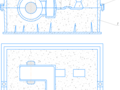
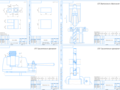
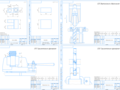
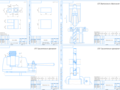
- Добавлен: 24.01.2023
- Размер: 2 MB
- Закачек: 0
Описание
Состав проекта
![]() |
![]() ![]() ![]() |
![]() ![]() ![]() |
![]() ![]() ![]() |
![]() |
![]() ![]() ![]() |
![]() |
![]() ![]() ![]() |
![]() ![]() ![]() |
![]() ![]() ![]() |
![]() |
![]() |
![]() |
![]() |
![]() ![]() ![]() ![]() |
![]() ![]() ![]() |
![]() |
![]() ![]() ![]() |
![]() |
![]() |
![]() ![]() ![]() |
![]() ![]() ![]() |
![]() |
![]() |
![]() |
![]() ![]() |
![]() ![]() ![]() |
![]() |
![]() |
![]() |
![]() ![]() ![]() ![]() |
![]() |
![]() ![]() ![]() ![]() |
![]() ![]() ![]() ![]() |
![]() ![]() ![]() ![]() |
![]() ![]() ![]() ![]() |
![]() ![]() ![]() ![]() |
![]() ![]() ![]() |
![]() ![]() ![]() |
![]() |
![]() ![]() ![]() ![]() |
![]() ![]() ![]() ![]() |
![]() |
![]() ![]() ![]() ![]() |
![]() ![]() ![]() ![]() |
![]() |
![]() ![]() ![]() ![]() |
![]() |
![]() ![]() ![]() |
![]() ![]() ![]() |
Дополнительная информация
Операционные карты.doc
Оборуд. устройство ЧПУ
Обозначение программы
Горизонтально-фрезерный 6Р80Г
)Установить и закрепить деталь в приспособление.
Приспособление - специальное
) Фрезеровать поверхность и торец выдерживая размеры 30.
Фреза цилиндрическая 75 ГОСТ 8904-73
) Фрезеровать поверхность и торец выдерживая размеры 25
ТМ.doc
1 Служебное назначение детали и размерный анализ чертежа детали
Деталь – ходовая гайка - предназначена для передачи движения от ходового винта исполнительному инструменту. Материалом детали является сталь 40 ГОСТ 1050-88. В выбранной системе координат выполняем эскиз детали предварительно пронумеровав все поверхности формы детали и оформив их в цвете: обработанные поверхности – красным цветом необработанные – синим. Поскольку имеются наклонные поверхности то кодируют в виде поверхностей точки пересечения наклонной поверхности с поверхностями проецируемыми на координатные оси. Перенесем размеры на эскиз с чертежа детали. Эскиз приведен на рисунке 4.1. По эскизу строим исходные графы размерных связей поверхностей детали по всем координатам приведенные на рисунках 4.2-4.4.
В графах отсутствуют разорванные поверхности и замкнутые цепи что свидетельствует о правильном задании размеров на чертеже детали.
При выборе размеров рядам с более крупной градации и входящих в них размерам должно отдаваться предпочтение: ряд Ra5 следует предпочитать ряду Ra 10 ряд Ra10 - ряду Ra20 ряд Ra20 – ряду Ra40.Численное значение допусков формы допусков расположения суммарных допусков формы и расположения поверхностей деталей машин должны применяться в соответствии с ГОСТом 24643-81. Допуски по классам точности обозначаются t1 t2 t3 для классов точности соответственно «точный» (11 и 12 квалитет) «средний» (13 и 14 квалитет) и «грубый»(17 квалитет). Предельные отклонения не указанные непосредственно после номинальных размеров оговоренных общей записью в технологических требованиях называются неуказанные предельные отклонения.
Рисунок 4.1 – Эскиз детали
Рисунок 4.2 – Исходный граф по оси М
Рисунок 4.3 – Исходный граф по оси K
Рисунок 4.4 – Исходный граф по оси N
2 Анализ технологичности детали и выбор метода получения заготовки
Технологичность заготовки характеризуется возможностью ее получения наиболее рациональным для данных производственных условий способом с максимально возможным приближением ее формы и размеров к форме и размерам готовой детали при условии обеспечения технологичности дальнейшей механической обработки заготовки. Из чертежа видно что деталь достаточно технологична с точки зрения механической обработки так как у нее нет труднодоступных поверхностей и имеются нормальные технологические базы поэтому конструкцию детали менять не имеет никакого смысла. Теперь можно приступить к выбору метода получения заготовки.
На выбор метода получения заготовки оказывают влияние: материал детали ее назначение и технические требования на изготовление объем и серийность выпуска форма поверхностей и размеры детали.
Поскольку форма детали – призматическая то предпочтительнее использовать заготовку из проката.
Товарные заготовки - болванки квадратные (ГОСТ 4693-77) - служат заготовками под ковку и штамповку крупных валов рычагов и т.д. Сортовые профили общего назначения - круглые и квадратные (ГОСТ 2590-71) шестигранные (ГОСТ 2879-69) и полосовые (ГОСТ 103-76) -используют для изготовления валов как гладких так и с небольшим перепадом диаметров ступеней стаканов диаметром до 50 мм втулок диаметром до 25 мм рычагов. Номенклатура диаметров от 5 до 250 мм и круглой стали от 5 до 200 мм для квадратной от 8 до 100 мм для шестигранной и толщиной от 4 до 60 мм для полосовой. По точности подразделяется на высокую повышенную и обычную. Трубный прокат - стальной бесшовный горячекатаный холоднотянутый и холоднокатаный (ГОСТ 8732-78 ГОСТ 8734-75) - служит для изготовления цилиндров втулок гильз стаканов пустотелых валов и т.д. Периодические профили проката соответствуют изготавливаемым из них деталям.
Механические свойства периодического проката выше чем свойства гладкого проката Отклонения размеров проката от номинального обычно составляют по диаметру профиля ±01% и по длине ±05 %.Точность горячекатаного проката ориентировочно соответствует 12-14 квалитету точности холоднотянутого - 9-12 квалитету.
Исходя из перечисленного обзора принимаем в качестве заготовки полосу горячекатаную ГОСТ 103-76. Предельные отклонения по ширине полосы -09+03; по толщине -09 +03.
Рисунок 4.5 – Эскиз заготовки
3 Дифференциация операций и размерный анализ технологического процесса
После выбора метода получения заготовки приступаем к разработке технологического процесса.
Основной задачей этого этапа является составление общего плана обработки детали формулировка содержания операций технологического процесса и выбор типа оборудования.
В процессе обработки деталь необходимо сориентировать относительно приспособления и закрепить. Такой процесс ориентации называется базированием т.е. это процесс придания требуемого положения относительно выбранной системы координат в процессе конструирования обработки сборки.
Чтобы разработать технологический процесс обработки данной детали необходимо:
Выбрать базы на I-ой операции.
Установить связь между обрабатываемыми и необрабатываемыми поверхностями.
Выбор баз на I-ой операции играет особую роль при разработке технологического процесса так как на этой операции решаются две важнейшие технологические задачи которые влияют на весь ход процесса а именно: устанавливается связь между обрабатываемыми и необрабатываемыми поверхностями и происходит распределение припуска на последующую обработку. Чтобы выполнить обе эти задачи рассмотрим два варианта.
Обработка отверстия всегда более трудоемка чем обработка плоскости поэтому нам нужно равномерное распределение припуска на обработку отверстия и это же отверстие мы примем в качестве технологической базы.
Рисунок 4.6 – Базирование на первых операциях
Составим маршрут обработки детали с базированием на каждой операции. Дифференциацию операций сведем в таблицу 4.2.
Таблица 4.2 – Дифференциация операций
Горизонтально-фрезерная ФРЕП Мр3 Мp4
Горизонтально-фрезерный 6Р81Г
Горизонтально-фрезерная ФРЕП Np10 Np13
Таблица 4.2 - Дифференциация операций
Горизонтально-фрезерная ФРЕП Кр6 Kp9
Горизонтально-фрезерная ФРЕП Мp1
Вертикально-сверлильная СВРО ЗНКЧ отв. 25
Вертикально-сверлильный 2Н150
Горизонтально-фрезерная ФРЕП Np11 12
После разработки укрупненного маршрута обработки детали можно приступить непосредственно к размерному анализу технологического процесса.
Размерный анализ технологического процесса будет проводиться аналогично размерному анализу чертежа.
Принимаем ту же систему координат что и при размерном анализе чертежа. Для того чтобы провести размерный анализ по осям изображаем заготовку с припусками (рисунок 4.7). После этого строим совмещенный граф который получается в результате наложения исходного графа с конструкторскими размерами и размерами припусков на производный граф с технологическими размерами и размерами заготовки (рисунок 4.8). Совмещенный граф дает полную информацию о размерном формообразовании детали.
Расчет и выявление размерных цепей начинается с двухзвенных размерных цепей а затем выявляются цепи где добавляется одно неизвестное звено.
Рисунок 4.7 – Размерная схема технологического процесса по оси N
Рисунок 4.8 – Исходный производный и совмещенный технологические графы по оси N
мм z2 = z3 = z6 = z7 = 07 мм
4 Расчет режимов резания норм времени
Режимы резания определяются глубиной резания t подачей S и скоростью резания V. Значения t V S влияют на точность и качество получаемой поверхности производительность и себестоимость обработки.
Для обработки сначала устанавливают глубину резания а затем подачу и скорость резания. Глубину резания принимаем равной припуску на заданный размер обрабатываемой поверхности.
Скорость резания зависит от выбранной глубины резания подачи качества и марки обрабатываемого материала геометрических параметров режущей части инструмента и ряда других факторов. Скорость резания рассчитывают по установленным для каждого вида обработки эмпирическим формулам которые имеют следующий общий вид:
Значения коэффициента СV характеризующие условия обработки материал заготовки глубину резания и подачу и показателей степени содержащихся в этих формулах так же как и период стойкости Т инструмента применяемого для данного вида обработки выбираются из таблиц.
Норма времени на станочную операцию определяется по формуле
ТО – основное (машинное время);
ТВ – вспомогательное время состоящее из времени на установку и снятие детали времени связанного с переходом времени на измерение смену инструмента и изменение режимов резания.
Основное время рассчитывается по формуле
і – количество рабочих ходов
L = l +l1 + l2 – расчетная длина обработки в направлении подачи здесь
l2 – дополнительная длина на взятие пробных стружек резания.
Sm = s0 n –минутная подача
Вспомогательное время Tв состоит из затрат времени на отдельные приемы:
tус – время на установку и снятие детали
tв.оп. – вспомогательное время связанное с выполнением операции
tконтр – время на контрольное измерение детали
Результаты расчета сведены в таблицу 4.3. На основании расчетов заполняются операционные карты (см. приложение).
Таблица 4.3 - Режимы резания
5 Разработка и расчет установочно-зажимного приспособления
Приспособление предназначено для установки и закрепления детали на фрезерной операции 030. Оно позволяет осуществить процесс базирования и фиксации детали в соответствии со схемой базирования разработанной при проектировании укрупненного маршрута.
В основу данного приспособления заложено самоцентрирующееся зажимное устройство кулачкового типа силовая схема для которого приведена на рисунке 4.9.
Усилие Q необходимое для получения заданной силы зажима определяется по формуле
Р = 10 Н - сила зажима; =09 коэффициент учитывающий потери от трения в шарнирной части прихватов; q = 1 - сопротивление пружины.
Рисунок 4.9 – Силовая схема приспособления
ТМ.docx
1 Служебное назначение детали и размерный анализ чертежа детали
Деталь – ходовая гайка - предназначена для передачи движения от ходового винта исполнительному инструменту. Материалом детали является сталь 40 ГОСТ 1050-88. В выбранной системе координат выполняем эскиз детали предварительно пронумеровав все поверхности формы детали и оформив их в цвете: обработанные поверхности – красным цветом необработанные – синим. Поскольку имеются наклонные поверхности то кодируют в виде поверхностей точки пересечения наклонной поверхности с поверхностями проецируемыми на координатные оси. Перенесем размеры на эскиз с чертежа детали. Эскиз приведен на рисунке 4.1. По эскизу строим исходные графы размерных связей поверхностей детали по всем координатам приведенные на рисунках 4.2-4.4.
В графах отсутствуют разорванные поверхности и замкнутые цепи что свидетельствует о правильном задании размеров на чертеже детали.
При выборе размеров рядам с более крупной градации и входящих в них размерам должно отдаваться предпочтение: ряд Ra5 следует предпочитать ряду Ra 10 ряд Ra10 - ряду Ra20 ряд Ra20 – ряду Ra40.Численное значение допусков формы допусков расположения суммарных допусков формы и расположения поверхностей деталей машин должны применяться в соответствии с ГОСТом 24643-81. Допуски по классам точности обозначаются t1 t2 t3 для классов точности соответственно «точный» (11 и 12 квалитет) «средний» (13 и 14 квалитет) и «грубый»(17 квалитет). Предельные отклонения не указанные непосредственно после номинальных размеров оговоренных общей записью в технологических требованиях называются неуказанные предельные отклонения.
Рисунок 4.1 – Эскиз детали
Рисунок 4.2 – Исходный граф по оси М
Рисунок 4.3 – Исходный граф по оси K
Рисунок 4.4 – Исходный граф по оси N
2 Анализ технологичности детали и выбор метода получения заготовки
Технологичность заготовки характеризуется возможностью ее получения наиболее рациональным для данных производственных условий способом с максимально возможным приближением ее формы и размеров к форме и размерам готовой детали при условии обеспечения технологичности дальнейшей механической обработки заготовки. Из чертежа видно что деталь достаточно технологична с точки зрения механической обработки так как у нее нет труднодоступных поверхностей и имеются нормальные технологические базы поэтому конструкцию детали менять не имеет никакого смысла. Теперь можно приступить к выбору метода получения заготовки.
На выбор метода получения заготовки оказывают влияние: материал детали ее назначение и технические требования на изготовление объем и серийность выпуска форма поверхностей и размеры детали.
Поскольку форма детали – призматическая то предпочтительнее использовать заготовку из проката.
Товарные заготовки - болванки квадратные (ГОСТ 4693-77) - служат заготовками под ковку и штамповку крупных валов рычагов и т.д. Сортовые профили общего назначения - круглые и квадратные (ГОСТ 2590-71) шестигранные (ГОСТ 2879-69) и полосовые (ГОСТ 103-76) -используют для изготовления валов как гладких так и с небольшим перепадом диаметров ступеней стаканов диаметром до 50 мм втулок диаметром до 25 мм рычагов. Номенклатура диаметров от 5 до 250 мм и круглой стали от 5 до 200 мм для квадратной от 8 до 100 мм для шестигранной и толщиной от 4 до 60 мм для полосовой. По точности подразделяется на высокую повышенную и обычную. Трубный прокат - стальной бесшовный горячекатаный холоднотянутый и холоднокатаный (ГОСТ 8732-78 ГОСТ 8734-75) - служит для изготовления цилиндров втулок гильз стаканов пустотелых валов и т.д. Периодические профили проката соответствуют изготавливаемым из них деталям.
Механические свойства периодического проката выше чем свойства гладкого проката Отклонения размеров проката от номинального обычно составляют по диаметру профиля ±01% и по длине ±05 %.Точность горячекатаного проката ориентировочно соответствует 12-14 квалитету точности холоднотянутого - 9-12 квалитету.
Исходя из перечисленного обзора принимаем в качестве заготовки полосу горячекатаную ГОСТ 103-76. Предельные отклонения по ширине полосы -09+03; по толщине -09 +03.
Рисунок 4.5 – Эскиз заготовки
3 Дифференциация операций и размерный анализ технологического процесса
После выбора метода получения заготовки приступаем к разработке технологического процесса.
Основной задачей этого этапа является составление общего плана обработки детали формулировка содержания операций технологического процесса и выбор типа оборудования.
В процессе обработки деталь необходимо сориентировать относительно приспособления и закрепить. Такой процесс ориентации называется базированием т.е. это процесс придания требуемого положения относительно выбранной системы координат в процессе конструирования обработки сборки.
Чтобы разработать технологический процесс обработки данной детали необходимо:
Выбрать базы на I-ой операции.
Установить связь между обрабатываемыми и необрабатываемыми поверхностями.
Выбор баз на I-ой операции играет особую роль при разработке технологического процесса так как на этой операции решаются две важнейшие технологические задачи которые влияют на весь ход процесса а именно: устанавливается связь между обрабатываемыми и необрабатываемыми поверхностями и происходит распределение припуска на последующую обработку. Чтобы выполнить обе эти задачи рассмотрим два варианта.
Обработка отверстия всегда более трудоемка чем обработка плоскости поэтому нам нужно равномерное распределение припуска на обработку отверстия и это же отверстие мы примем в качестве технологической базы.
Рисунок 4.6 – Базирование на первых операциях
Составим маршрут обработки детали с базированием на каждой операции. Дифференциацию операций сведем в таблицу 4.2.
Таблица 4.2 – Дифференциация операций
Горизонтально-фрезерная ФРЕП Мр3 Мp4
Горизонтально-фрезерный 6Р81Г
Горизонтально-фрезерная ФРЕП Np10 Np13
Таблица 4.2 - Дифференциация операций
Горизонтально-фрезерная ФРЕП Кр6 Kp9
Горизонтально-фрезерная ФРЕП Мp1
Вертикально-сверлильная СВРО ЗНКЧ отв. 25
Вертикально-сверлильный 2Н150
Горизонтально-фрезерная ФРЕП Np11 12
После разработки укрупненного маршрута обработки детали можно приступить непосредственно к размерному анализу технологического процесса.
Размерный анализ технологического процесса будет проводиться аналогично размерному анализу чертежа.
Принимаем ту же систему координат что и при размерном анализе чертежа. Для того чтобы провести размерный анализ по осям изображаем заготовку с припусками (рисунок 4.7). После этого строим совмещенный граф который получается в результате наложения исходного графа с конструкторскими размерами и размерами припусков на производный граф с технологическими размерами и размерами заготовки (рисунок 4.8). Совмещенный граф дает полную информацию о размерном формообразовании детали.
Расчет и выявление размерных цепей начинается с двухзвенных размерных цепей а затем выявляются цепи где добавляется одно неизвестное звено.
Рисунок 4.7 – Размерная схема технологического процесса по оси N
Рисунок 4.8 – Исходный производный и совмещенный технологические графы по оси N
мм z2 = z3 = z6 = z7 = 07 мм
4 Расчет режимов резания норм времени
Режимы резания определяются глубиной резания t подачей S и скоростью резания V. Значения t V S влияют на точность и качество получаемой поверхности производительность и себестоимость обработки.
Для обработки сначала устанавливают глубину резания а затем подачу и скорость резания. Глубину резания принимаем равной припуску на заданный размер обрабатываемой поверхности.
Скорость резания зависит от выбранной глубины резания подачи качества и марки обрабатываемого материала геометрических параметров режущей части инструмента и ряда других факторов. Скорость резания рассчитывают по установленным для каждого вида обработки эмпирическим формулам которые имеют следующий общий вид:
Значения коэффициента СV характеризующие условия обработки материал заготовки глубину резания и подачу и показателей степени содержащихся в этих формулах так же как и период стойкости Т инструмента применяемого для данного вида обработки выбираются из таблиц.
Норма времени на станочную операцию определяется по формуле
ТО – основное (машинное время);
ТВ – вспомогательное время состоящее из времени на установку и снятие детали времени связанного с переходом времени на измерение смену инструмента и изменение режимов резания.
Основное время рассчитывается по формуле
і – количество рабочих ходов
L = l +l1 + l2 – расчетная длина обработки в направлении подачи здесь
l2 – дополнительная длина на взятие пробных стружек резания.
Sm = s0 n –минутная подача
Вспомогательное время Tв состоит из затрат времени на отдельные приемы:
tус – время на установку и снятие детали
tв.оп. – вспомогательное время связанное с выполнением операции
tконтр – время на контрольное измерение детали
Результаты расчета сведены в таблицу 4.3. На основании расчетов заполняются операционные карты (см. приложение).
Таблица 4.3 - Режимы резания
5 Разработка и расчет установочно-зажимного приспособления
Приспособление предназначено для установки и закрепления детали на фрезерной операции 030. Оно позволяет осуществить процесс базирования и фиксации детали в соответствии со схемой базирования разработанной при проектировании укрупненного маршрута.
В основу данного приспособления заложено самоцентрирующееся зажимное устройство кулачкового типа силовая схема для которого приведена на рисунке 4.9.
Усилие Q необходимое для получения заданной силы зажима определяется по формуле
Р = 10 Н - сила зажима; =09 коэффициент учитывающий потери от трения в шарнирной части прихватов; q = 1 - сопротивление пружины.
Рисунок 4.9 – Силовая схема приспособления
исходный эскиз.frw

исправленный граф M.frw

исходный граф M.frw

исправленный эскиз.frw

исходник.frw

эскиз отливки.frw

Опоки.frw

исправленный граф N.frw

исходный граф K.frw

исправленный граф K.frw

Ходовая гайка.cdw

Общий вид.cdw

Деталировка1.cdw

Покрытие Хим. Окс. прм.
Коэффициент смещения
Допуск на колебание длины
Допуск на погрешность
Радиус развернутости
эвольвенты в начале
рабочего участка профиля
Сталь 45 ГОСТ 1050-88
Сталь 40 ГОСТ 1050-88
Механизм привода.cdw

Кинематическая схема.cdw

Механизм каретки.cdw

маршрутная карта.doc
Код наименование опер.
Обозначение документа
Код наименование оборудования
5 Горизонтально-фрезерная. Горизонтально-фрезерный станок 6Т804. 0836
Фрезеровать поверхность выдержав размеры 30
5 Горизонтально-фрезерная. Горизонтально-фрезерный станок 6Т804. 0743
Фрезеровать поверхность выдержав размеры 60
5 Горизонтально-фрезерная. Горизонтально-фрезерный станок 6Т804. 0721
Фрезеровать поверхность выдержав размеры 70
5 Горизонтально-фрезерная. Горизонтально-фрезерный станок 6Т804. 0702
Фрезеровать поверхность выдержав размеры 25
0 Вертикально-сверлильная. Вертикально-сверлильный станок 2М112. 082
Сверлить и зенкеровать отверстия выдержав размер 20
5 Горизонтально-фрезерная. Горизонтально-фрезерный станок 6Т804. 0911
Фрезеровать паз выдержав размеры 20
Петля СЧ 20 ГОСТ 1412-85
0 Сверлильная. Вертикально-сверлильный станок 2Н106Н. 0836
Сверлить два отверстия выдержав размеры 20; 40
5 Сверлильная. Вертикально-сверлильный станок 2М112. 0494
Развернуть отверстие отверстие выдержав размер 10
Операционные карты.docx
Оборуд. устройство ЧПУ
Обозначение программы
Горизонтально-фрезерный 6Р80Г
)Установить и закрепить деталь в приспособление.
Приспособление - специальное
) Фрезеровать поверхность и торец выдерживая размеры 30.
Фреза цилиндрическая 75 ГОСТ 8904-73
) Фрезеровать поверхность и торец выдерживая размеры 25
1 лист в 511.frw

Сталь 45 ГОСТ 1050-88
Сталь 40 ГОСТ 1050-88
5 Горизонтально-фрезерная
0 Горизонтально-фрезерная
5 Вертикально-сверлильная
лист 2.в 511frw.frw

Для смазки приспособления в период хранения солидол
синтетический ГОСТ 4366-76
Контроль производим через 2 месяца.
Смену установленных элементов производить раз в 6
Неплоскостность базовой поверхности не более 0
Размеры для справок*
1 лист в 5.11.frw

Сталь 45 ГОСТ 1050-88
Сталь 40 ГОСТ 1050-88
5 Горизонтально-фрезерная
0 Горизонтально-фрезерная
5 Вертикально-сверлильная
лист 2.frw

Для смазки приспособления в период хранения солидол
синтетический ГОСТ 4366-76
Контроль производим через 2 месяца.
Смену установленных элементов производить раз в 6
Неплоскостность базовой поверхности не более 0
Размеры для справок*
1 лист.frw

Сталь 45 ГОСТ 1050-88
Сталь 40 ГОСТ 1050-88
5 Горизонтально-фрезерная
0 Горизонтально-фрезерная
5 Вертикально-сверлильная
Диплом на печать.doc
Обзор существующих конструкций
Технология машиностроения
1Служебное назначение детали и размерный анализ чертежа детали
2 Анализ технологичности детали и выбор метода получения заготовки
3 Дифференциация операций и размерный анализ технологического процесса
4 Расчет режимов резания норм времени
5 Разработка и расчет установочно-зажимного приспособления
Технико-экономический расчёт
Охрана труда и промэкология
2Характеристика объекта
3Санитарно-гигиенические мероприятия. Вентиляция. Отопление
5Противопожарные мероприятия
6Компенсация профессиональных вредностей. Средства индивидуальной защиты. Личная гигиена
7Промышленная экология
Введение и обоснование темы проекта
В современном мире с развитием международных отношений не только в области политики но и в других сферах жизни в том числе и в промышленности появляется необходимость взаимосвязи и сопоставляемости различных характеристик отражающих те или иные свойства объекта исследования.
Благодаря такой унификации появляется возможность качественно сравнить товары различных фирм производителей.
Оборудование для лабораторных испытаний материалов на устойчивость к различным видам воздействия не исключение. Ввиду такой унификации показателей отражающих свойства материалов необходимо применять такие же условия испытания как и производители материалов на мировом рынке.
Для обеспечения заданных условий при испытании материалов необходимо применение оборудования способного обеспечить такие условия. Условия испытания и требования к оборудованию отражены в международном стандарте ИСО4649-85.
Прибор для испытания должен обеспечивать:
надежное крепление образца в держателе и шлифовальной шкурки на вращающемся барабане;
возможность установки высоты части образца выступающей из держателя (20 ±01) мм;
вращение барабана диаметром (1500 ± 02) мм (без учета толщины шлифовальной шкурки) с частотой (40 ± 1) мин-1;
поступательное перемещение образца параллельно оси барабана (4200 ± 40) мм на 100 оборотов барабана;
полную длину пути истирания (400 ± 08) м с учетом подъема образца над барабаном в области крепления к нему абразивного материала;
автоматический контакт образца с абразивным материалом в начале испытания и выход его из
контакта после 84 оборотов при креплении шкурки по п. 3.3.1 или после100;оборотов при креплении
шкурки по п. 3.3.2';
(275 ± 020) оборота образца вокруг своей оси на полном пути истирания при применении прибора с вращающимся держателем;
нормальную силу прижимающую образец к барабану 50 и 100 Н (050 и 100 кгс) с погрешностью не более 02 Н (002 кгс);
возможность уменьшения полного пути истирания в два раза (200 ± 04) м.
(Измененная редакция№ 2).
Поворотное плечо и держатель образца не должны подвергаться вибрациям во время прижима образца к барабану с силой (100 ± 02) Н. Для образцов из мягких материалов обладающих склонностью к вибрации допускается уменьшать силу прижатия до (50 ± 01) Н.
Угол между осью держателя образца и вертикалью в плоскости перпендикулярной оси барабана в сторону вращения барабана должен быть равным (30 ± 03)°.
Допускаемое отклонение центра прижатого к барабану образца от точки пересечения с поверхностью барабана вертикали проведенной от оси барабана ± 1 мм.
Шкурка шлифовальная по ГОСТ 344.
Истираемость контрольной резины на шлифовальной шкурке при нормальной силе прижатия 10 Н (10 кгс) должна быть равна 60—110 мг на полном пути истирания.
Обзор существующих конструкций.
ПРИБОРЫ АЛЯ ИСПЫТАНИЙ НА ИСТИРАНИЕ ПОЛИМЕРНЫХ МАТЕРИАЛОВ
Сложность процессов происходящих при контактных взаимодействиях твердых тел в условиях внешнего трения и приводящих к разрушению поверхностей трения обусловила существование многочисленных методик для оценки свойств материалов при трении. Это привело к созданию обширного класса испытательных машин и стендов. Постоянно создаются все новые типы машин трения обычно в единичных экземплярах которые предназначены чаще всего для решения частных задач [1].
Общепринятой классификации машин трения в настоящее время не имеется и создание ее на-талкивается на ряд трудностей связанных с выделением их общих и главных признаков. Подход к этому вопросу со стороны конструкторов и испытателей различен.
венных материалов так как ассортимент современных подошв быстро растет и необходимо подбирать конструкции приборов позволяющие получать данные сопоставимые с реальными сроками эксплуатации обуви.
Для выявления приборов пригодных для испытания подошвенных материалов на истирание целесообразно определить какие виды изнашивания характерны для данных материалов. Существует большое количество видов изнашивания но наиболее распространенными в легкой промышленности являются абразивные усталостные и окислительные.
При эксплуатации обуви низ подошвы набойки стельки подвергаются трению со стороны стопы и о различные виды грунта обладающего абразивным действием. Следовательно наибольшую роль в износе подошвенных материалов играет абразивный износ. Кроме того при испытаниях материалов на абразивное изнашивание поверхность образцов подвергается интенсивному воздействию истирающего материала которое усугубляется адсорбционно-коррозийным воздействием среды. Эти факторы существенно снижают время испытаний в связи с чем методы испытания на
стойкость к абразивному износу различных видов получили наибольшее распространение. Таким образом следует рассматривать в качестве возможных вариантов для испытания подошвенных материалов именно машины трения имитирующие абразивный износ объекта испытания.
При ходьбе реализуются два вида трения — трение качения и трение скольжения. Следовательно наиболее приближенными к реальным условиям будут испытания проводимые на машинах обеспечивающих эти виды трения.
Конкретные модели данной группы машин характеризуются комплексом устройств обеспечивающих возможность проведения испытаний: для осуществления дополнительных схем испытаний (сменные захваты и т.п.); для создания дополнительных движений образца или контртела (удар вибрация и т.д.); для температурных испытаний (термо- и криокамеры) для испытания в различных средах (вакуум масло абразив); для измерения и регистрации параметров испытаний (сила трения износ температура); для автоматизации процесса испытаний включая обработку результатов. Типоразмер машины зависит от нагрузки на образец и скорости относительного движения образца и контртела в пределах определенного диапазона нагрузок и скоростей.
Испытания на стойкость к абразивному износу также подразделяются на испытания с закрепленным и незакрепленным абразивом. В легкой промышленности в основном используется метод проведения испытаний с закрепленным абразивом (в качестве истирающей поверхности применяют шлифовальную шкурку абразивные шлифовальные круги абразив шаржированный в резину или чугунную плиту).
Кроме того испытания с закрепленным абразивом подразделяются на испытания по возобновляемой и невозобновляемой поверхности [2].
Примером устройства с незакрепленным абразивом является прибор ИКВ конструкции Позняка который применяется для испытаний натуральных подошвенных кож. Влажный образец кожи в данном случае истирают зернами кварцевого песка диаметром 05-085 мм при трении качения. Один конец образца закрепляют на секторе на который действует усилие 250 Н другой конец — зажимом ко дну ванны с влажным песком. Ванна связанная с шатуном совершает возвратно-поступательные движения частотой 104 хода в минуту. Сопротивление истиранию определяется по потере толщины кожи и характеризуется временем необходимым для истирания 1 мм толщины образца [3].
Типичным устройством для испытаний на абразивный износ по невозобновляемой поверхности является прибор типа Грассели в котором создается трение скольжения образца по невозобнов-ляемой поверхности.
На основе данной кинематической схемы построен ряд приборов и методов испытания на износ различных материалов. Наиболее распространенным из них является прибор МИ-2 (рис.1). В данном приборе два образца закрепленные на рычаге прижимаются к шлифовальному полотну прикрепленному к вращающемуся диску. Рычаг имеет ось помещенную в полом валу диска на которой подвешен груз создающий силу 16 20 или 26 Н прижимающую образцы к абразиву. Скорость скольжения образцов составляет 30 мс [3].
Прибор УкрНИИКП является модификацией прибора МИ-2 в котором осуществляется прерывистое истирание материала. Присутствующие в конструкции кулачки позволяют периодически выводить закрепленные на рычаге образцы из соприкосновения с абразивом.
К группе приборов предусматривающих истирание по невозобновляемой поверхности в условиях скольжения относится абразиметр Табера (рис.2). Это универсальный прибор предназначенный для определения устойчивости к истиранию всех типов материалов: пластиков композитных материалов бумаги текстиля резины краски лака металлов т. д. Прибор оснащен цифровым счетчиком циклов блоком всасывания и стандартными дисками для истирания. Два колеса трутся по испытываемой пластине которая с каждым циклом теряет в массе. Прибор поставляется в двух исполнениях: для испытания одного или двух образцов одновременно.
Исследование антифрикционных материалов на трение и изнашивание в условиях качения или скольжения осуществляется с помощью машины трения Амслера типа МИ-1М. При испытании в условиях качения в контакте находятся вращающиеся с постоянной скоростью ролики диаметром 40 мм. В условиях скольжения верхний ролик заменяется вкладышем шириной 10мм. Ролики приводятся во вращение электродвигателем; нагрузка составляющая 26-200 кгс задается пружиной. Скорость вращения составляет 200 обмин. Момент трения регистрируется маятниковым устройством температура определяется термопарой износ образцов - микрометрированием. Нагрузка на образцы может периодически изменяться с помощью эксцентрика [4].
Для определения истираемости (износостойкости) при разработке и освоении новых видов ПВХ-материалов для полов в соответствии с ГОСТ 11529-86 используется машина с возвратно-поступательным движением (рис.3). Сущность метода заключается в определении величины уменьшения толщины материала при истирании в течение заданного количества циклов испытания или в определении количества циклов испытания истирания слоя износа на всю его толщину
Не менее распространена группа оборудования для проведения испытаний с закрепленным абразивом по возобновляемой поверхности.
К этой группе в частности относится прибор для определения сопротивления истиранию при скольжении по возобновляемой поверхности по ГОСТ 23509-79 [6]. Сущность методов описанных в ГОСТ 23509-79 заключается в истирании образца прижатого к абразивной поверхности вращающегося барабана при этом образец перемещается параллельно оси барабана и вращается вокруг своей оси.
Испытания осуществляются на приборе Шоп-пера (рис. 4). В качестве абразивного материала используется абразивная шкурка навернутая на барабан диаметром 150 мм вращающийся со скоростью 40 мин-1. Образец закреплен в образце-держателе который соединен с кареткой через тензочувствительный элемент для измерения сил трения. При вращении ходового винта образец поступательно перемещается вдоль образующей цилиндра со скоростью 420 мм на 100 оборотов барабана. Полная длина пути истирания может составлять 40 м или 20 м. Нормальная нагрузка задается грузом и составляет 5 или ЮН.
Для испытаний по данному стандарту также может применяться прибор ИКР. Данный прибор применяется для испытания на истирание каблучных резин при трении скольжения или при сочетании трения с деформацией удара. Он отличается наличием кулачков заменяя которые можно испытывать образцы с различной ударной нагрузкой или без нее.
Для испытания пластмасс на абразивный износ по ГОСТ 11012-69 [7] и для определения истираемости ПВХ-материалов по ГОСТ 11529-86 [5] применяют аналогичные испытательные машины.
Для проведения испытаний на сопротивление истиранию резин при качении с проскальзыванием по методу ГОСТ 12251-77 используют прибор типа МИР-1 (рис.5) [8].Прибор позволяет проводить испытания в трех режимах: заданного скольжения и заданной силы трения; заданного скольжения и заданной нагрузки; заданной силы трения и заданной нормальной нагрузки.
Сущность метода испытаний заключается в истирании кольцевого резинового образца вращающегося относительно покрытой шлифовальной шкуркой поверхности барабана диаметром 200 мм с частотой 350 мин ' с проскальзыванием и одновременным перемещением образца вдоль образующей барабана на пути длиной 450 см. Скорость перемещения каретки с образцом может быть 50 90 или 440 мммин. Нормальная сила прижимающая образец в статических условиях составляет от 98 до 49 Н.
Пальчиковая машина Арчарда также относится к классу установок обеспечивающих движение образца по возобновляемому пути. В ней могут быть реализованы две схемы испытаний: цилиндрический образец диаметром 6 мм может прижиматься торцом или образующей цилиндра к образующей вращающегося вала диаметром 25-30 мм. Износ определяется взвешиванием образцов или линейным измерением. Кроме того измеряется суммарный износ посредством иглы профилографа устанавливаемой сверху испытуемого образца [4].
Большинство импортных приборов предназначенных для испытания полимерных подошвенных материалов и аналогичных им осуществляют истирание образцов в условиях движения с закрепленным образцом по возобновляемой поверхности. Примером может служить испытательное устройство STM 469 производства фирмы «SATRA» для проверки устойчивости резин и полиуретанов к воздействию истирающих нагрузок которое представляет собой специализированную установку с цилиндрическим истирающим барабаном (рис.6).
Двигатель постоянного тока вращает барабан диаметром 150 мм с частотой 40 обмин. На поверхность барабана посредством двустороннего скотча крепится абразивная бумага. Цилиндрический образец установленного размера вставляется опускается или поднимается с помощью кулачка.
Этой же фирмой разработано испытательное устройство для проверки износоустойчивости обувных подошвенных материалов STM 602 (рис.7).
Барабан диаметром 150 мм вращается с частотой 40 обмин от двигателя асинхронного типа с частотным регулятором скорости.абразивной бумаги Р-60 установлен на барабане при помощи двустороннего скотча. Три цилиндрических образца установленных размеров вставляются в специальный блок держателей и устанавливаются на одном уровне с помощью специального микрометра. Блок держателей совершает перемещение по поверхности бумаги в результате вращения барабана и движения вдоль образующей барабана со скоростью 032 мс при действии постоянной нагрузки в 5 или 10 Н. Распределительный диск позволяет проводить испытания при длине перемещения по винтовой линии в 10 20 30 и 40 м.
Испытательные устройства STM 469 и STM 602 позволяют осуществлять испытания в соответствии со стандартами ISO 4649 DIN 53516 BS 903:А9 по методу A SATRA ТМ 174 и SATRA ТМ 193.
Истирающий тестер фирмы «ELASTOCON» (рис.8) предназначен для проведения испытаний на истирание методом перемещения образца по винтовой поверхности образующейся в результате вращения барабана на котором закрепляется абразивная бумага.
Испытание проводится в соответствии со стандартами DIN 53516 и ISO 4649 регламентирующими дополнительный вес прикладываемые нагрузки в 25 и 50 Н.
Тестер DAT 30801 (рис.9) производимый немецкой фирмой «PFI - PIRMASENS» которая является одной из крупнейших фирм-производителей испытательного оборудования в Западной Европе также предназначен для проведения испытаний на истирание методом перемещения образца по винтовой поверхности образующейся в результате вращения барабана на котором закрепляется абразивная бумага.
Фирмой «SATRA» также выпускается прибор STM 140 для определения износостойкости материалов (рис. 10).
Прибор позволяет быстро и приближенно к условиям эксплуатации протестировать на износостойкость материалы для изготовления подошв и каблуков в соответствии с SATRA ТМ 84. Тестируемые детали протягиваются по прямой под давлением по специальному абразивному материалу закрепленному на горизонтальном основании прибора. Истирание осуществляется на двух образцах попеременно с двух сторон. Материал движется медленно под прямым углом к испытываемой детали так что испытываемая часть всегда в контакте с новой частью абразивного материала который сохраняет свои свойства. Оказываемая нагрузка — 056 кгсм2.
Существуют установки позволяющие проводить испытания как по одному следу так и по свежей поверхности при радиальном перемещении образца. К таким машинам относится установка Хрущева типа Х-4Б. Схема контакта в данной машине: пальчиковый образец-торец диска. Абразивная шкурка прикрепляется на торце диска диаметром 250 мм вращающегося вокруг оси. Пальчиковый образец диаметром 2 мм и длиной 15—20 мм прижимается к поверхности диска грузом. Скорость вращения диска составляет 60 об мин осевая нагрузка - 03 кгс [4].
Большую группу составляет оборудование для проведения комплексных испытаний.
Фирмой «SATRA» разработан биомеханический стенд для комплексного испытания подошвы STM-528 (рис.11). Биомеханический стенд имитирует биомеханические свойства человеческой походки включая воздействие веса взрослого человека и его поворотные движения воспроизводимые в реальной жизни.
Механизм состоит из двух отдельных узлов. Искусственная нога на которую и устанавливается обувь двигается благодаря сервоприводу управляемому компьютером. Механизм перемещения основания на который устанавливаются различные испытательные поверхности позволяет синхрони-зируясь с движением искусственной ноги создавать различные условия эксплуатации. Обычная испытательная программа состоит из 12000 шагов что требует работы стенда в течение шести часов. Такая продолжительность испытания создает изнашиваемость сопоставимую с 30-80-дневной ноской обуви.
Испытательная программа может воспроизводить движения соответствующие не только обычным шагам но и шаговым движениям в которых подворачивается пяточная и носочная части подошвы. Программное обеспечение позволяет использовать как стандартные режимы так и специально разработанные которые могут быть сохранены и в последующем использоваться.
Оборудование также может использоваться для оценки коэффициента трения скольжения истирания прочности крепления подошв. Могут подвергаться проверке все виды материалов: древесина керамика виниловые и ковровые покрытия асфальт песок щебень и др. Кроме того с помощью стенда могут изучаться элементы протекторного рисунка целостность вставок и индивидуальные особенности походок. Также возможно проведение испытания всего узла обуви на многократный изгиб с оценкой стойкости подошв к данному виду деформаций.
Технические характеристики стенда: площадь ходовой площадки 2121 нормальный угол шага ±10°; весовая нагрузка 75 кг; максимальный угол шага от -25° до +30°; максимальная скорость 2000 циклов (шагов) в час.
Прибор ИПД-1 конструкция которого разработана заводом «Ивмашприбор» по технологическому заданию ЦНИИКП [9] обеспечивает возможность сообщения образцу комплекса воздействий в сухих и влажных условиях: трения скольжения повторного сжатия удара - сочетание и интенсивность которых могут регулироваться. Для установления оптимальных условий испытания и увязки получаемых результатов с износостойкостью в эксплуатации в приборе предусмотрена возможность испытания при различных скоростях перемещения ванны с абразивным материалом: 20 30 и 40 смс (или 70 103 и 137 двойных ходов в минуту) и различных скоростях падения штоков: 73 109 и 146 ударов в минуту соответствующих возможным скоростям перемещения стопы при ходьбе и беге. Прибор снабжен комплектом грузов который в сочетании с весом штоков обеспечивает возможность создания нагрузки на образец в 3 4 5 6 кгс. Кроме того величину удельного давления на образец можно менять и путем изменения размеров образцов. (20x20 м 20x30 мм 20x50 мм).
Комплексные испытания готовой обуви в динамических условиях можно проводить с помощью установки инженера Ю. А. Жукова [10].
Установка работает следующим образом: испытуемый образец обуви надевается на специ-
апьную колодку оборудованную датчиками. Ко-лодка с обувью из начального среднего верхнего положения имитируя шаг передвигается вперед и частично опускается. Одновременно с образцом вперед передвигается площадка со съемным устройством. В переднем положении образец опускается на съемное устройство и прижимается к нему с постоянным давлением (равным весу человека) и вместе с подвижной площадкой отводится в крайнее заднее положение.
Для испытания на износ подошв и каблуков в условиях сухого трения на подвижную площадку закрепляется пластина с образцами различных грунтов и покрытий дорог. Износ подошв и каблуков в условиях мокрого трения определяется при закреплении на подвижную площадку ванны с вложенной в нее пластинкой образцов грунта или покрытия дороги.
В. Н. Феоктистовым и Г.А. Валякиным для ис-тирания обувных резин предложен прибор ИПМ позволяющий испытывать материалы в режимах скольжения и качения на поверхности асфальта. При истирании на приборе ИПМ резины деформируются также как и в реальных условиях носки обуви о чем свидетельствует характер разрушения материала. Сопротивление истиранию на приборе ИПМ подсчитывают числом оборотов.
В приборе предусмотрена возможность сооб-щения образцу сжатия сочетания действия трения качения и скольжения а также чередования пе-риодов истирания с периодом «отдыха». Испыта-ние в различных условиях трения т.е. при различ-ном соотношении трения качения и скольжения достигается изменением соотношения окружных скоростей движения устройства с закрепленным образцом и колеса с истирающим материалом. В качестве показателя используют число циклов трения необходимых для истирания 1 мм толщины образца.
Прибор довольно громоздок (устройство с закрепленным образцом совершает возвратно-поступательное движение на пути длиной 3 м) и применяется в основном при выполнении исследо-ваний [9].
Приведенный перечень оборудования далеко не полный однако в нем явно прослеживается преобладание приборов осуществляющих испытания по возобновляемой поверхности закрепленного абразива. Целесообразность их использования для испытания подошвенных полимерных материалов подтверждает широкое распространение такой схемы испытаний в зарубежных приборах.
1Проектирование кинематической схемы
Проектирование кинематической схемы производим исходя из заданных стандартом перемещений образца.
Внешний вид прибора для испытания разрабатываем опираясь на уже существующие приборы.
Одним из важнейших условий разработки является применение готовых деталей и узлов применяемых в конструкции прибора отечественного производства.
Исходя из этого условия для привода прибора в движение примем мотор-редуктор производства Витебского завода «Эвистор».
Двигатель запитывается от сети напряжением 24В мощностью 60Вт.
Частота вращения ротора двигателя составляет 3000 обмин. На выходном валу редуктора частота вращения составляет 80 обмин.
Опираясь на эти данные приступаю к расчёту кинематики прибора без учёта силовых параметров.
Для передачи вращения от редуктора к рабочим органам прибора применим цилиндрическую зубчатую передачу. Учитывая относительно небольшие нагрузки возникающие в приборе в процессе работы и для уменьшения его конечной массы целесообразно применить зубчатые колёса изготовленные из прочной пластмассы.
Для обеспечения требуемой частоты вращения барабана учитывая частоту вращения выходного вала редуктора определяем передаточное отношение пары колёс редуктор-барабан
Привод пары винт-гайка обеспечивается парой зубчатых колёс барабан-винт. Для обеспечения требуемого перемещения образца вдоль оси барабана предварительно примем параметры пары винт-гайка. Принимаем стандартные значения Р=2 и D=20(для обеспечения жёсткости винта на всей длине). Чтобы обеспечить перемещение образца на величину 4.2мм за один оборот барабана при выбранном шаге винта равным 2мм за один оборот барабана винт должен совершить 2.1 оборот.
Исходя из этого условия получаем передаточное отношение пары барабан-винт=047619
Путём подбора целых чисел числа зубьев колёс получаем
для вала редуктора Z=42
для вала барабана Z=84
Определив числа зубьев колёс приступаю к определению геометрических параметров и межосевых расстояний. Используя современные методы систем автоматического проектирования (Компас-SHAFT 2D) задавшись числами зубьев колёс и предварительно приняв модуль m=2 а также приняв ширины зубчатых колёс b1=20 b2=20 b3=20 провожу расчёт геометрии зубчатых колёс (редуктор-барабан приложение 1 барабан-винт приложение 2).
Вращение образца вокруг своей оси осуществляется по средствам пары колесо-рейка. Параметры колеса определяю исходя из длины перемещения образца и требуемого числа оборотов. Образец должен повернуться вокруг своей оси на 2.75 оборота за время продольного движения на расстояние 420мм. Расстояние которое колесо должно преодолеть за один оборот определим так 4202.75=152272727мм. Зная длину окружности колеса определяю его диаметр 152272727314159=4861мм.
1 Служебное назначение детали и размерный анализ чертежа детали
Деталь – ходовая гайка - предназначена для передачи движения от ходового винта исполнительному инструменту. Материалом детали является сталь 40 ГОСТ 1050-88. В выбранной системе координат выполняем эскиз детали предварительно пронумеровав все поверхности формы детали и оформив их в цвете: обработанные поверхности – красным цветом необработанные – синим. Поскольку имеются наклонные поверхности то кодируют в виде поверхностей точки пересечения наклонной поверхности с поверхностями проецируемыми на координатные оси. Перенесем размеры на эскиз с чертежа детали. Эскиз приведен на рисунке 4.1. По эскизу строим исходные графы размерных связей поверхностей детали по всем координатам приведенные на рисунках 4.2-4.4.
В графах отсутствуют разорванные поверхности и замкнутые цепи что свидетельствует о правильном задании размеров на чертеже детали.
При выборе размеров рядам с более крупной градации и входящих в них размерам должно отдаваться предпочтение: ряд Ra5 следует предпочитать ряду Ra 10 ряд Ra10 - ряду Ra20 ряд Ra20 – ряду Ra40.Численное значение допусков формы допусков расположения суммарных допусков формы и расположения поверхностей деталей машин должны применяться в соответствии с ГОСТом 24643-81. Допуски по классам точности обозначаются t1 t2 t3 для классов точности соответственно «точный» (11 и 12 квалитет) «средний» (13 и 14 квалитет) и «грубый»(17 квалитет). Предельные отклонения не указанные непосредственно после номинальных размеров оговоренных общей записью в технологических требованиях называются неуказанные предельные отклонения.
Рисунок 4.1 – Эскиз детали
Рисунок 4.2 – Исходный граф по оси М
Рисунок 4.3 – Исходный граф по оси K
Рисунок 4.4 – Исходный граф по оси N
2 Анализ технологичности детали и выбор метода получения заготовки
Технологичность заготовки характеризуется возможностью ее получения наиболее рациональным для данных производственных условий способом с максимально возможным приближением ее формы и размеров к форме и размерам готовой детали при условии обеспечения технологичности дальнейшей механической обработки заготовки. Из чертежа видно что деталь достаточно технологична с точки зрения механической обработки так как у нее нет труднодоступных поверхностей и имеются нормальные технологические базы поэтому конструкцию детали менять не имеет никакого смысла. Теперь можно приступить к выбору метода получения заготовки.
На выбор метода получения заготовки оказывают влияние: материал детали ее назначение и технические требования на изготовление объем и серийность выпуска форма поверхностей и размеры детали.
Поскольку форма детали – призматическая то предпочтительнее использовать заготовку из проката.
Товарные заготовки - болванки квадратные (ГОСТ 4693-77) - служат заготовками под ковку и штамповку крупных валов рычагов и т.д. Сортовые профили общего назначения - круглые и квадратные (ГОСТ 2590-71) шестигранные (ГОСТ 2879-69) и полосовые (ГОСТ 103-76) -используют для изготовления валов как гладких так и с небольшим перепадом диаметров ступеней стаканов диаметром до 50 мм втулок диаметром до 25 мм рычагов. Номенклатура диаметров от 5 до 250 мм и круглой стали от 5 до 200 мм для квадратной от 8 до 100 мм для шестигранной и толщиной от 4 до 60 мм для полосовой. По точности подразделяется на высокую повышенную и обычную. Трубный прокат - стальной бесшовный горячекатаный холоднотянутый и холоднокатаный (ГОСТ 8732-78 ГОСТ 8734-75) - служит для изготовления цилиндров втулок гильз стаканов пустотелых валов и т.д. Периодические профили проката соответствуют изготавливаемым из них деталям.
Механические свойства периодического проката выше чем свойства гладкого проката Отклонения размеров проката от номинального обычно составляют по диаметру профиля ±01% и по длине ±05 %.Точность горячекатаного проката ориентировочно соответствует 12-14 квалитету точности холоднотянутого - 9-12 квалитету.
Исходя из перечисленного обзора принимаем в качестве заготовки полосу горячекатаную ГОСТ 103-76. Предельные отклонения по ширине полосы -09+03; по толщине -09 +03.
Рисунок 4.5 – Эскиз заготовки
После выбора метода получения заготовки приступаем к разработке технологического процесса.
Основной задачей этого этапа является составление общего плана обработки детали формулировка содержания операций технологического процесса и выбор типа оборудования.
В процессе обработки деталь необходимо сориентировать относительно приспособления и закрепить. Такой процесс ориентации называется базированием т.е. это процесс придания требуемого положения относительно выбранной системы координат в процессе конструирования обработки сборки.
Чтобы разработать технологический процесс обработки данной детали необходимо:
Выбрать базы на I-ой операции.
Установить связь между обрабатываемыми и необрабатываемыми поверхностями.
Выбор баз на I-ой операции играет особую роль при разработке технологического процесса так как на этой операции решаются две важнейшие технологические задачи которые влияют на весь ход процесса а именно: устанавливается связь между обрабатываемыми и необрабатываемыми поверхностями и происходит распределение припуска на последующую обработку. Чтобы выполнить обе эти задачи рассмотрим два варианта.
Обработка отверстия всегда более трудоемка чем обработка плоскости поэтому нам нужно равномерное распределение припуска на обработку отверстия и это же отверстие мы примем в качестве технологической базы.
Рисунок 4.6 – Базирование на первых операциях
Составим маршрут обработки детали с базированием на каждой операции. Дифференциацию операций сведем в таблицу 4.2.
Таблица 4.2 – Дифференциация операций
Горизонтально-фрезерная ФРЕП Мр3 Мp4
Горизонтально-фрезерный 6Р80Г
Горизонтально-фрезерная ФРЕП Np10 Np13
Таблица 4.2 - Дифференциация операций
Горизонтально-фрезерная ФРЕП Кр6 Kp9
Горизонтально-фрезерная ФРЕП Мp1
Вертикально-сверлильная СВРО ЗНКЧ отв. 25
Вертикально-сверлильный 2Н150
Горизонтально-фрезерная ФРЕП Np11 12
После разработки укрупненного маршрута обработки детали можно приступить непосредственно к размерному анализу технологического процесса.
Размерный анализ технологического процесса будет проводиться аналогично размерному анализу чертежа.
Принимаем ту же систему координат что и при размерном анализе чертежа. Для того чтобы провести размерный анализ по осям изображаем заготовку с припусками (рисунок 4.7). После этого строим совмещенный граф который получается в результате наложения исходного графа с конструкторскими размерами и размерами припусков на производный граф с технологическими размерами и размерами заготовки (рисунок 4.8). Совмещенный граф дает полную информацию о размерном формообразовании детали.
Расчет и выявление размерных цепей начинается с двухзвенных размерных цепей а затем выявляются цепи где добавляется одно неизвестное звено.
Рисунок 4.7 – Размерная схема технологического процесса по оси N
Рисунок 4.8 – Исходный производный и совмещенный технологические графы по оси N
мм z2 = z3 = z6 = z7 = 07 мм
Режимы резания определяются глубиной резания t подачей S и скоростью резания V. Значения t V S влияют на точность и качество получаемой поверхности производительность и себестоимость обработки.
Для обработки сначала устанавливают глубину резания а затем подачу и скорость резания. Глубину резания принимаем равной припуску на заданный размер обрабатываемой поверхности.
Скорость резания зависит от выбранной глубины резания подачи качества и марки обрабатываемого материала геометрических параметров режущей части инструмента и ряда других факторов. Скорость резания рассчитывают по установленным для каждого вида обработки эмпирическим формулам которые имеют следующий общий вид:
Значения коэффициента СV характеризующие условия обработки материал заготовки глубину резания и подачу и показателей степени содержащихся в этих формулах так же как и период стойкости Т инструмента применяемого для данного вида обработки выбираются из таблиц.
Норма времени на станочную операцию определяется по формуле
ТО – основное (машинное время);
ТВ – вспомогательное время состоящее из времени на установку и снятие детали времени связанного с переходом времени на измерение смену инструмента и изменение режимов резания.
Основное время рассчитывается по формуле
і – количество рабочих ходов
L = l +l1 + l2 – расчетная длина обработки в направлении подачи здесь
l2 – дополнительная длина на взятие пробных стружек резания.
Sm = s0 n –минутная подача
Вспомогательное время Tв состоит из затрат времени на отдельные приемы:
tус – время на установку и снятие детали
tв.оп. – вспомогательное время связанное с выполнением операции
tконтр – время на контрольное измерение детали
Результаты расчета сведены в таблицу 4.3. На основании расчетов заполняются операционные карты (см. приложение).
Таблица 4.3 - Режимы резания
Приспособление предназначено для установки и закрепления детали на фрезерной операции 030. Оно позволяет осуществить процесс базирования и фиксации детали в соответствии со схемой базирования разработанной при проектировании укрупненного маршрута.
В основу данного приспособления заложено самоцентрирующееся зажимное устройство кулачкового типа силовая схема для которого приведена на рисунке 4.9.
Усилие Q необходимое для получения заданной силы зажима определяется по формуле
Р = 10 Н - сила зажима; =09 коэффициент учитывающий потери от трения в шарнирной части прихватов; q = 1 - сопротивление пружины.
Рисунок 4.9 – Силовая схема приспособления
Расчёт технико-экономического эффекта
Исследование материалов предназначенных для изготовления подошв обуви даёт возможность производителю выбрать наиболее подходящий вариант для производства а так же уверенность в качестве производимой продукции. На обувных предприятиях РБ такие исследования не производятся. Образцы подошв отправляют в РФ. Результаты испытаний приходится ждать определённый период в течении которого запуск материала в производство невозможен. В ходе дипломного проектирования была разработана машина для испытания на истирание резин и эластомеров в соответствии с требованиями стандарта регламентирующего условия испытания.
Источник экономического эффекта заключается в исключении необходимости отправки образцов для испытания в страны ближнего зарубежья замещении испытательных машин импортного производства и создании на предприятии собственной испытательной базы.
Для определения экономического эффекта составим сводную таблицу 5.1 стоимости деталей проектируемого оборудования и сравним их со стоимостью зарубежных аналогов. Машина производства завода «ЛегМаш» г. Санкт-Петербург стоит 24000000 бел.руб. без учёта стоимости пересылки.
Таблица 5.1 – Сводная таблица стоимости деталей требуемых для проектного варианта
Наименование детали
Колесо зубчатое Z=55
Колесо зубчатое Z=20
Шпонка призматическая
Блок управления электрический
Шайба второпластовая
Втулка второпластовая
По данным завода «Эвистор»на котором будет изготавливаться машина к стоимости добавляется сумма накладных расходов которая по действующим на предприятии нормативам составляет 1000%.
Суммарная стоимость изготовления:
Сизг=1653270+(16532701000%)=18185970 бел.руб.
Добавив стоимость транспортировки и монтажа получим а также НДС получим стоимость оборудования для потребителя.
Соб= СизгНДС Сдим =18185970 11811=23605389 бел.руб.
Затраты на получение сертификата для этого прибора составляет 784000 бел.руб.
Исходя из этого с учётом транспортных расходов получаем конечную стоимость импортного оборудования:
Соб.имп.=240000001.1+784000=27184000 бел.руб.
На основе произведенных расчётов можно считать что применение приборов для испытаний отечественного производства экономически целесообразно.
Предприятия лёгкой промышленности оснащены сложным технологическим оборудованием и к лицам обслуживающим это оборудование предъявляются высокие требования с точки зрения обеспечения эффективности надёжности и безопасности работы машин и аппаратов. Причина производственного травматизма или профессионального заболевания как правило определяется комплексом факторов зависящих от надёжности и безопасности машины или технологического процесса поведения человека управляющего ими его быстродействия точности надёжности влияния окружающей среды и других факторов. Причинами травматизма могут быть опасные и вредные производственные факторы которые подразделяются на следующие группы:
-по природе воздействия они могут быть физические химические биологические и психофизические;
-ошибки при изготовлении наладке и ремонте технологического оборудования;
-отказ в работе оборудования и систем обеспечивающих его работу;
-неправильная организация рабочего места и технологического процесса;
-ошибки в действиях человека управляющего технологическим процессом;
-недостатки в подборе обучении персонала.
Все планируемые мероприятия по охране труда должны обеспечить нормальные и безопасные условия труда обслуживающего персонала и должны разрабатываться исходя из конкретных особенностей проектируемого объекта.
Охрана труда в Республике Беларусь обеспечивается системой законодательных актов социально-экономических организационных технических и лечебно-профилактических мероприятий и средств обеспечивающих безопасность сохранение здоровья и работоспособности человека в процессе труда. Основой законодательства о труде является Трудовой Кодекс РБ принятый Палатой представителей и одобренный Советом Республики 30 июня 1999 года. Часть трудового законодательства составляет действующее законодательство об охране труда которое заключено в главе 16 «Охрана труда» (статьи 221–232) раздел II – «Общие правила регулирования индивидуальных трудовых и связанных с ними отношений». Этот раздел регламентирует права работников на охрану труда гарантии этих прав права на компенсацию по условиям труда обязанности нанимателя по обеспечению охраны труда и т.д.
Кроме вышеперечисленного в систему законодательных актов регулирующих вопросы охраны труда в Республике Беларусь входят:
– Конституция РБ гарантирующая право граждан на здоровье и безопасные условия труда;
– Закон РБ «Об основах государственного социального страхования» в котором предусмотрены вопросы страхования граждан от несчастных случаев на производстве и профзаболеваний;
– Закон РБ «О санитарно-эпидемическом благополучии населения» направленный на предупреждение воздействия неблагоприятных факторов среды на здоровье населения и регламентирует действия органов государственной власти и управления предприятий и организаций должностных лиц и граждан по обеспечению санитарно-эпидемического благополучия;
– Закон РБ «О сертификации продукции работ услуг» который обеспечивает безопасность продукции для жизни здоровья и имущества населения а так же охрану окружающей среды;
– Закон РБ «О коллективных договорах и соглашениях» определяющий правовые основы заключения и исполнения коллективных договоров и соглашений для содействия регулированию трудовых отношений и согласованию социально-экономических интересов работников и нанимателей в частности в вопросах создания здоровых и безопасных условий труда улучшения охраны здоровья среды.
2 Характеристика объекта
Все планируемые мероприятия по охране труда обеспечивают безопасные и здоровые условия труда обслуживающего персонала и разрабатываются исходя из проектируемого обувного производства.
Таблица 6.1 – Характеристика опасности поражения персонала электрическим током
Характеристика реализуемого параметра
Класс помещения по опасности поражения электрическим током
I - Помещение без повышенной опасности с нормальной температурой воздуха с теплопроводящим полом
Напряжение электрического тока питания электросистем изделия В
сеть освещения 220 В
сеть эл. привода 220 В
Тип исполнения электрооборудования
Класс электрооборудования по способу защиты человека от поражения электрическим током
-электрооборудование имеющее рабочую изоляцию элемент заземления
Средства коллективной защиты от поражения электрическим током
Защитное заземление; зануление; изоляция .
Способ отключения электрооборудования от сети
ручной (кнопка стоп пуск рубильник); автоматический; общий рубильник
Удельное сопротивление грунта Ом.м
(суглинок) – 04·102
Нормируемое значение сопротивления защитного заземления Ом
Сопротивление защитного заземления Ом
Расчёт системы защитного заземления.
Для системы заземления применяем стальные трубы с наружным диаметром 006 м и стальная соединительная полоса шириной 004 м. Расстояние от поверхности земли до верха трубы равно 070 м. Расчётное напряжение в сети 380 В. Длина трубы 22 м. Удельное электрическое сопротивление грунта (глина) – 04 · 102 Ом·м.
Определяем сопротивление одной трубы:
Число труб в заземлителе:
Сопротивление соединительной полосы:
Общее сопротивление системы заземления:
3 Санитарно-гигиенические мероприятия. Вентиляция. Отопление
При разработке санитарно-гигиенических мероприятий в работе установлены параметры микроклимата рабочей зоны помещения и предусмотрены системы отопления вентиляции или кондиционирования воздуха для их обеспечения в соответствии с требованиями СанПиН 9–80 РБ 98 «Гигиенические требования к микроклимату производственных помещений» СанПиН № 11–09–94 «Санитарные правила организации технологических процессов и гигиенические требования к производственному оборудованию». Данные представлены в таблице 6.2.
Таблица 6.2 – Метрологические условия и средства их обеспечения
Значение реализуемого параметра
Наименование помещения
Характеристика тяжести работы
Средней тяжести IIа –
Температура воздуха рабочей зоны °С
–ниже оптим. 170-189;
–выше оптим. 211-230
Относительная влажность воздуха %
Скорость движения воздуха мс
–ниже оптим. 180-199;
–выше оптим. 221-270.
Предусматриваемые системы вентиляции
Приточная (общеобменная равно-мерная в верхнюю зону) вытяж-ная (общеобменная и местная)
Кратность обмена воздуха в помещении ч-1
Баланс воздуха в помещении
Теплоноситель и его параметры
Мероприятия по искусственному освещению представлены в таблице 6.3
Таблица 6.3 – Искусственное и естественное освещение на участке
Наименование помещения и рабочего места
Площадь помещения м2
Разряд зрительной работы
Освещенность при рабочем освещении лк
Освещенность при аварийном освещении:
на путях эвакуации лк
Источник питания аварийного освещения
Газоразрядный (люминесцентные лампы)
Исполнение светильника
Мощность лампы светильника Вт
Количество светильников шт
Количество светильников определяется по формуле:
где – нормированное освещение = 750 лк;
– площадь цеха = 756 м2;
– коэффициент неравномерности освещения = 12;
– коэффициент запаса = 15;
– световой поток одной лампы = 2850 лм;
– коэффициент использования светового потока = 07;
– количество ламп в светильнике = 2;
– сдвоенные светильники.
Принимаем количество светильников – 112.
5 Противопожарные мероприятия
Противопожарные мероприятия для обувного цеха отражены в таблице 6.4.
Таблица 6.4 – Пожарная безопасность. Молниезащита
Класс помещения по взрывоопасности (пожароопасности)
Категория производства по пожароопасности
Характеристика материалов стен по сгораемости
Характеристика материалов перекрытий по сгораемости
Степень огнестойкости стен здания и их огнестойкость ч
Расстояние от рабочего места до эвакуационного выхода м
Средства пожаротушения
Спринклерные пожарные краны огнетушители
Категория молниезащиты здания (сооружения)
Сопротивление заземляющего устройства
при молниезащите Ом
6 Компенсация профессиональных вредностей. Средства индивидуальной защиты. Личная гигиена
Данные мероприятия отражены в таблице 6.5.
Таблица 6.5 – Компенсация профессиональных вредностей. Средства индивидуальной защиты и личная гигиена работающих
Продолжительность рабочего отпуска после трех лет работы дни
Пенсионный возраст лет женщин мужчин
Обеспечение спецодеждой спецобувью средствами индивидуальной защиты органов зрения и дыхания
Халат хб передник хб косынка хб обувь профилактическая.
Средства обеззараживания кожи
Метод обеззараживания кожи
Мыть с водой и мылом
Периодичность медосмотра
Основными требованиями к помещениям обувного предприятия являются: благоприятный микроклимат нормируемая температура воздуха чистота воздушной среды требуемая относительная влажность воздуха хорошее освещение и пожарная безопасность.
7 Промышленная экология
Наряду с охраной труда большое значение приобретает охрана окружающей среды – одна из важнейших задач современности. Выбросы промышленных предприятий энергетических систем и транспорта в атмосферу водоемы и недра на современном этапе развития достигли таких размеров что в ряде районов земного шара особенно в крупных промышленных центрах уровни загрязнения существенно превышают допустимые санитарные нормы.
Промышленная экология призвана на основе оценки степени вреда приносимого природе индустриализацией разрабатывать и совершенствовать инженерно-технические средства защиты окружающей среды повсеместно развивать основы создания замкнутых безотходных и малоотходных технологических циклов и производств.
Обувная фабрика производит обувные изделия всех ассортиментов. Вредные выбросы производят основные цеха и отделы а также вспомогательные производства (ремонтно-строительный цех транспорт воздушно-компрессионное хозяйство).
Выбросы вредных веществ в атмосферу. Мероприятия по очистке атмосферы. В соответствии с требованиями ГОСТ 17.2.3.0 для каждого проектируемого предприятия устанавливаются предельно-допустимые выбросы (ПДВ) вредных веществ в атмосферу при условии что выбросы вредных веществ от данного источника в совокупности с другими источниками не создают приземную концентрацию ПДК. Основным критерием качества атмосферного воздуха являются ПДК. При определении ПДВ необходимо учитывать концентрацию вещества в приземном слое (С) и фоновую концентрацию вещества (Сф) соблюдая для приземного слоя условия С+Сф≤ ПДК.
Таблица 6.6 – Выбросы в атмосферу
Загрязняющие вещества
Пыль (взвешенные вещества)
Объекты являющиеся источниками выделения в окружающую среду вредных и неприятно пахнущих веществ следует отделять от жилой застройки санитарно-защитными зонами. Размеры этих зон до границы жилой застройки устанавливают в зависимости от мощности предприятия условий осуществления технологического процесса характера и количества выделяемых в окружающую среду вредных и неприятно веществ. Территория санитарно-защитной зоны должна быть благоустроена и озеленена газоустойчивыми породами деревьев и кустарников. Со стороны жилого массива полосы древесно-кустарниковых насаждений должны быть не более 50 м. Основными выбросами предприятия является пыль. Для снижения пылевыделения используют пылеулавливающие устройства циклоны фильтры.
Очистка сточных вод.
Основными мероприятиями по охране поверхностных водных источников являются очистка производственных и коммунально-бытовых стоков обеспечение необходимого разбавления стоков путем регулирования стока рек; внедрение защитных водооборотов на промышленных предприятиях. На обувной фабрике проводится регулярный контроль за состоянием запарной арматуры и трубопроводов технической и хозяйственно-бытовой воды; на рабочих местах и в подсобных помещениях обновили наглядную агитацию призывающую к бережному расходованию вод и охраны их от загрязнения.
Таблица 6.7 – Показатели состава и свойств сточных вод
Наименование показателей
Фактическая концентрация мгл
Водородный показатель рН
Охрану водных ресурсов нельзя решить только созданием очистных сооружений требующих затрат. Снижает водопотребление и уменьшает объем сточных вод внедрение оборотного водоснабжения эффективность которого состоит в сокращении потребления свежей воды и стоков а также в снижении степени очистки сточных вод повторного использования. К системам оборотного водоснабжения относятся системы охлаждения различного технологического оборудования и рециркуляционная вода в системах кондиционирования воздуха [151821].
Утилизация производственных отходов.
Производственные отходы – это неиспользованная по тем или иным причинам часть сырья которая должна рассматриваться как вторичное сырье. Отходы проектируемой фабрики направляются на склад отходов.
Все мероприятия по охране труда должны обеспечить безопасные и здоровые условия труда обслуживающего персонала повысить производительность труда ликвидировать производственный травматизм.
К основным мероприятиям и средствам по оздоровлению труда относятся: разработка и конструирование оборудования исключающего выделения пыли паров и газов в производственных помещениях внедрения и создания автоматизированного оборудования с дистанционным управлением; создания на оборудовании надежной герметизации и укрытий.
Развитие охраны труда и промышленной экологии направлено на повышение производительности труда роста жизненного и культурного уровня трудящихся дальнейшего облегчения и оздоровления условий труда ликвидации производственного травматизма. Для этого необходимо обеспечить рабочих средствами индивидуальной защиты спецодеждой и обувью хорошего качества. Кроме того необходим усиленный надзор за соблюдением норм охраны окружающей среды.
Ахумов А.В. «Справочник нормировщика» 1986.
Барташов Л.И. «Справочник конструктора и технолога по технико-экономическим расчетам» М Машиностроение 1979.
Большаков А.В. Справочник по ремонту наладке и эксплуатации оборудования обувных предприятий - М.: Легкая индустрия 1982. – 312с.
Вредные вещества в промышленности: Справочник для химиков инженеров и врачей. В 3-х т.Под ред. Н.В.Лазарева. Э.Н. Левиной.-7-е изд. перераб. И доп.- Л.: Химия 1976 .
Герц Е.В. Крейнин Г.В. Расчёт пневмоприводов. Справочное пособие. М.: Машиностроение 1975. – 272с.
Герц Е.В. Крейнин Г.В. «Теория и расчет силовых пневматических устройств» М Изд. АН СССР 1960.
Гжиров Р.И. Краткий справочник конструктора: Справочник – Л.: Машиностроение Ленингр. отд-ние 1983. – 464 с.
Горошкин А.К. «Приспособления для металлорежущих станков» справочник М Машиностроение 1979.
Г.Н. 9-106 РБ 98 Предельно допустимые концентрации вредных веществ в воздухе рабочей зоны; введ. 1998-07-01. – Минск: Министерство архитектуры и строительства Республики Беларусь 1998. – 13 с.
Зыбин Ю.П. и др. Технология изделий из кожи. Учебник для студентов вузов лёгкой промышленности. М. Лёгкая индустрия 1975. – 412с.
Иванов М.Н Детали машин: Учеб. для машиностр. спец. вузов. – 4-е изд. перераб. – М.: Высш. Шк. 1984. – 336 с.
Иоффе А.Л. Ремонт и монтаж оборудования обувных фабрик - М.: Легкая и пищевая промышленность 1974. – 321 с.
Кнорринг Г.М. Осветительные установки. – Л.: Энергоиздат Ленингр. отд-ние 1981. – 288с.
Колясин Б.П. и др. Оборудование обувного производства. Учебник для средн. учеб. заведений. М. Лёгкая индустрия 1973. – 488с.
Косилова А.Г. Мещеряков Р.К. Справочник технолога-машиностроителя; том 1. – М.: Машиностроение 1986. – 523 с.
Косилова А.Г. Мещеряков Р.К. Справочник технолога-машиностроителя; том 2. – М.: Машиностроение 1986. – 496 с.
Кузьмин А.В. Расчет деталей машин. Справочное пособие. – М.: Легкая индустрия 1978. – 374 с.
Махаринский Е.И. Горохов В.Л. «Основы технологии машиностроения» учебник Мн. Высшая школа 1997.
Ничипорчик С.Н. Корженцевский М.И. Калачёв В.Ф. и др. Детали машин в примерах и задачах: Учебное пособие. – Мн.: Высшая школа 1981. – 432 с.
Охрана окружающей среды: Учеб. для техн. Спец. ВУЗов под ред. Белова С.В. – 2-е изд. испр. И доп. – М.: Высшая школа 1991. – 319с.
Полтев М.К. Охрана труда в машиностроении: Учеб. для студ. машиностроит. спец. ВУЗов. – М .: Высш. шк. 1980. – 294 с.
Правила устройства электроустановок Минэнерго СССР. – 6-е изд. перераб. и доп. – М.: Энергоатомиздат 1987. – 648с.: ил.
Пульгунов П.П. Сумароков М.В. Утилизация промышленных отходов. – М .: Стройиздат 1990. – 352с.
«Разработка и изготовление пресс форм для формования задников» Отчет НИР ХД-413. рук. В.А.Матвеев Витебск: 1997. – 147 с.
Республика Беларусь. Законы. Трудовой кодекс Республики Беларусь: принят Палатой представителей 8 июня 1999.: одобрен Советом Республики 30 июня 1999г. – Минск: Амалфея 1999. – 240с.
Родионов А.И. Клушин В.Н. Торочешников Н.С. Техника защиты окружающей среды Учеб. для ВУЗов. – 2-е изд. перераб. и доп. – М.: Химия 1989. – 512с.
Санитарные нормы проектирования промышленных предприятий. СН 245 – 71. – М.: Стройиздат 1972. – 96с.
СанПиН 2.2.42.1.8.10-32-2002 Шум на рабочих местах в помещениях жилых общественных общественных зданий и на территории жилой застройки. – Минск: Министерство здравоохранения Республики Беларусь 2003.
СанПиН 9-72 РБ 98 Гигиенические требования к условиям труда женщин; введ. 1998-07-01. – Минск: Министерство архитектуры и строительства Республики Беларусь 1998. -7с.
СанПиН 9-80 РБ 98 Гигиенические требования к микроклимату производственных помещений. – Взамен ГОСТ 12.1.005-88; введ. 1998-07-01. – Минск: Министерство архитектуры и строительства Республики Беларусь 1998. – 10с.
СанПиН 9-89 РБ 98 Вибрация производственная общая. Предельно допустимые нормы; введ. 1998-07-01. – Минск: Министерство архитектуры и строительства Республики Беларусь 1998. – 7с.
СанПиН 9-90 РБ 98 Вибрация производственная локальная. Предельно допустимые нормы; введ. 1998-07-01. – Минск: Министерство архитектуры и строительства Республики Беларусь 1998. – 10с.
СанПиН № 11-16-94 Санитарно-гигиенические нормы допустимой напряженности электростатического поля на рабочих местах; введ. 1994-07-01. – Минск: Министерство архитектуры и строительства Республики Беларусь 1998. – 14с.
ССБТ. ГОСТ 12.1.005-88. Общие санитарно-гигиенические требования к воздуху рабочей зоны. – М.: Издательство стандартов 1988.
СНБ 2.04.05-98 Естественное и искусственное освещение. Нормы проектирования. – Взамен СНиП II-4-79; введ. 1998-07-01. – Минск: Министерство архитектуры и строительства Республики Беларусь 1998. – 58с.
Сункуев Б.С. Расчет пневмо- и гидропривода машин легкой промышленности. – Мн.: БТИ им. С.М. Кирова 1988. – 46 с.
Расчёт цеховой себестоимости изготовления детали. Методические указания. Министерство образования и науки РБ. ВГТУ 1996 г. Составитель: доцент к. э. н. Машков Н.М.
Юдин Е.Я. Белов С.В. Баланцев С.К. и др. Охрана труда в машиностроении: Учеб. для студ. машиностроит. спец. ВУЗов Под ред. Е.Я.Юдина С.В.Белова. – 2-е изд. перераб. и доп. – М.: Машиностроение 1983. – 432 с.
Ю.В. Барановский "Режимы резания металлов" справочник.- М.: Машиностроение 1972. – 463 с.
Филин В.М «Гидравлика пневматика и термодинамика: курс лекций М. ИД «Форум»: ИНФРА-М 2008 – 320 с.
Шкред В.А. Горбацевич А.Ф. "Курсовое проектирование по технологии машиностроения" Учебное пособие для студентов машиностроительных вузов.- Мн.: Высш. школа 1983. – 421 с.
Спецификация на общий вид машины для формования пяточной части
Спецификация на сборочный чертеж
механизма формования
Спецификация на сборочный чертеж механизма колодки
Комплект технологической документации для изготовления детали “рычаг”
Спецификация на сборку.doc
Болт М6-6g20 ГОСТ 7808-78
Штифт 6 ГОСТ 9649-78
Болт М6-6g14 ГОСТ 7808-78
Болт М8-6g22 ГОСТ 7808-78
Шайба 8.65Г ГОСТ 6402-70
Рекомендуемые чертежи
- 24.04.2014
- 24.04.2014
- 24.04.2014
- 18.04.2023
- 24.04.2014