Организация производства


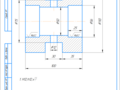
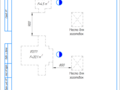
- Добавлен: 24.01.2023
- Размер: 1 MB
- Закачек: 0
Узнать, как скачать этот материал
Подписаться на ежедневные обновления каталога:
Описание
Организация производства
Состав проекта
![]() |
![]() ![]() ![]() ![]() |
![]() ![]() ![]() |
![]() ![]() ![]() ![]() |
Дополнительная информация
Контент чертежей
План цеха Стакан.cdw

Стакан.doc
1 Технологический процесс изготовления детали . .4
2 Выбор варианта технологического маршрута по минимуму
приведённых затрат .. ..16
Расчет эффективного фонда времени работы оборудования .. .21
Расчёт потребного количества оборудования для выполнения
производственной программы 22
Расчёт потребного количества рабочих по профессии разряда
и фонда их заработной платы .23
Расчет потребности и стоимости основных материалов .. 28
Расчет расходов на содержание и эксплуатацию оборудования
1 Амортизация оборудования и транспортных средств . .. 29
2 Эксплуатация оборудования .. 29
3 Текущий ремонт оборудования . 31
4 Внутризаводское перемещение грузов .. ..31
5 Износ малоценных и быстроизнашивающихся инструментов и
Расчет общецеховых расходов .34
Определение цеховой себестоимости изготовления детали 35
Список использованных источников .. . 36
В условиях рыночной экономики выживаемость любого предприятия его устойчивое положение на рынке товаров и услуг определяется уровнем его конкурентоспособности а также его продукции. В свою очередь конкурентоспособность продукции связана с его качествам уровнем цены. Уровень цены зависит от себестоимости изготовления самой продукции. В связи с этим целью данной работы является определение цеховой себестоимости изготовление детали. Кроме того цеховая себестоимость детали определяют с учетом выбранного варианта обеспечивающего минимум приведенных затрат по сравнению с другим вариантом технологического процесса изготовления детали. Второй целью данного курсового проекта является приобретение навыков по расчету цеховой себестоимости изготовления детали.
ХАРАКТЕРИСТИКА ВОЗМОЖНЫХ ВАРИАНТОВ МЕХАНИЧЕСКОЙ ОБРАБОТКИ ДЕТАЛИ
1 Технологический процесс изготовления детали
Технологический процесс изготовления детали составляем в двух вариантах. Первый вариант представлен в табл. 1.
Установить и закрепить прокат в патроне
Подрезка торца чистовая
Трех-кулачковый самоцентрир. патрон.
Чистовое обтачивание
Черновое обтачивание за 6 проходов
Отрезка детали от основного прутка.
Сверление диаметром 20 мм на длину 100 мм
Рассверливание диаметром 50 мм на длину 100 мм
Рассверливание диаметром 56 мм на длину 25 мм
Сверление диаметром 12 мм на длину 75 мм
Второй вариант технологического процесса изготовления детали представлен в табл. 2.
Расчет штучного времени каждой операции
Норма штучного времени определяется следующим образом:
ТШТ = ТОП +ТОБ+ТОТ где
ТОП – оперативное время (ТОП =ТО) мин;
– коэффициент для определения оперативного времени [1 c.35];
ТО – основное время мин; [3 c.146]
ТОБ – время на обслуживание рабочего места мин;
ТОБ – в % от ТОП [2 с.21]
ТОТ – время перерывов на отдых и личные надобности мин;
ТОТ – в % от ТОП [2 с.21]
Операция 005 (чистовое подрезание торца)
d – диаметр обрабатываемого торца;
TО= 00000111102= 01331 мин.
ТОП =18201331 =02422 мин;
Время на обслуживание рабочего места
ТОБ =0057TОП =005702422 =00138 мин;
Время перерывов на отдых и личные надобности
ТОТ=004ТОП=00402422 =00097 мин;
ТШТ =02422+00138+00097=02657 мин.
Операция 010 (чистовое точение)
L – длина обрабатываемой поверхности;
TО = 0000175110100 = 1925 мин.
ТОП =1821925 =35035 мин;
ТОБ =0057TОП =005735035 =01997 мин;
ТОТ=004TОП =00435035 =01401 мин;
ТШТ =35035+01997+01401=38433 мин
Операция 015 (черновое точение за 6 проходов)
k - количество проходов;
TО = 000007575306 = 10125 мин.
ТОП =18210125 =18428 мин;
ТОБ =0057TОП =005718428 =01050 мин;
ТОТ=004TОП =00418428 =00737 мин;
ТШТ =18428+01050+00737=20215 мин
Операция 020 (Отрезка детали от основного прутка)
TО = 00003931102= 47553 мин.
ТОП =18247553 =86547 мин;
ТОБ =0057TОП =005786547 =04933 мин;
ТОТ=004TОП =00486547 =03461 мин;
ТШТ =86547+04933+03461=94941 мин
Операция 025 (Сверление отверстия)
d – диаметр отверстия;
TО = 00005220100 =104 мин.
ТОП =161104 =16744 мин;
ТОБ =005TОП =00516744 =00837 мин;
ТОТ=004TОП =00416744 =0067 мин;
ТШТ =16744+00837+0067=18251 мин
Операция 030 (Рассверливание отверстия)
TО = 000042350100 =2115 мин.
ТОП =1612115 =34052 мин;
ТОБ =005TОП =00534052 =01703 мин;
ТОТ=004TОП =00434052 =01362 мин;
ТШТ = 34052+01703+01362=37117 мин
Операция 035 (Рассверливание отверстия)
TО = 000042356252 =11844 мин.
ТОП =16111844 =19069 мин;
ТОБ =005TОП =00519069 =00953 мин;
ТОТ=004TОП =00419069 =00763 мин;
ТШТ = 19069+00953+00763=20785 мин
Операция 040 (Сверление отверстия)
TО = 0000521275 = 0468 мин.
ТОП =1610156 =07535 мин;
ТОБ =005TОП =00507535 =00377 мин;
ТОТ=004TОП =00407535 =00301 мин;
ТШТ = 07535+00377+00301=08213 мин.
Операции 005 – 020 проводятся на токарно-револьверном станке 1П371 а операции 025 – 040 на вертикально-сверлильном 2Н150 .
Суммарное оперативное время ΣТОП = 219832 мин.
Суммарное штучное время ΣTШТ = 240612 мин.
Операция 020 (Сверление отверстия)
ТОП =182104 =18928 мин;
ТОБ =0057TОП =005718928 =01079 мин;
ТОТ=004TОП =00418928 =00757 мин;
ТШТ = 18928+01079+00757=20764 мин
(Рассверливание отверстия)
ТОП =1822115 =38493 мин;
ТОБ =0057TОП =00538493 =02194 мин;
ТОТ=004TОП =00438493 =0154 мин;
ТШТ = 38493+02194+0154=42227 мин
TО = 00004235625 =05922 мин.
ТОП =18205922=10778 мин;
ТОБ =005TОП =005710778 =00614 мин;
ТОТ=004TОП =00410778 =00431 мин;
ТШТ = 10778+00614+00431=11823 мин
Операция 035 (Отрезка детали от основного прутка)
Операция 045 (Рассверливание отверстия)
ТОП =16105922 =09534 мин;
ТОБ =005TОП =00509534 =00477 мин;
ТОТ=004TОП =00409534 =00381 мин;
ТШТ =09534+00477+00381=10392мин
Операции 005 – 035 проводятся на токарно-револьверном станке 1П371 а операции 040 – 045 на вертикально-сверлильном 2Н150 .
Суммарное оперативное время ΣТОП = 2277 мин.
Суммарное штучное время ΣTШТ = 249665 мин.
2 Выбор варианта технологического маршрута по минимуму приведённых затрат
Чтобы принять решение о методах обработки детали необходимо произвести расчеты экономической эффективности отдельных вариантов и выбрать из них наиболее рациональный для данных условий производства. Критерием оптимальности является минимум приведенных затрат на единицу продукции.
Дано: Общий годовой выпуск деталей N=10000 штук;
Производство: серийное;
ΣТштв1 = 240612 мин. ΣТштв2 = 249665 мин.
Действительный годовой фонд времени работы станка Fд = 38608 ч.
Часовые приведенные затраты [3 с.39]:
СП.З.=СЗ+СЧ.З.+ЕН(КС+КЗ) где
СЗ – основная и дополнительная зарплата с начислениями руб.ч;
СЧ.З. – часовые затраты по эксплуатации рабочего места руб.ч;
ЕН – нормативный коэффициент экономической эффективности капитальных вложений (в машиностроении Ен=015);
КС КЗ – удельные часовые капитальные вложения соответственно в станок и здание руб.ч.
Основная и дополнительная зарплата с начислениями и учетом многостаночного обслуживания:
e - коэффициент учитывающий дополнительную зарплату равную 9% начисления на социальное страхование 76% и приработок к основной зарплате в результате перевыполнения норм на 30%;
СТФ – часовая тарифная ставка станочника-сдельщика соответствующего разряда руб.ч [1 с.40];
k – коэффициент учитывающий зарплату наладчика (т.к. наладка станка выполняется самим рабочим то k=1) [3 с.39]
y – коэффициент учитывающий оплату рабочего при многостаночном обслуживании (т.к. число обслуживаемых станков равно единице то y=1).
СЗ=153×5270×1×1=80631 руб.ч.
Часовые затраты по эксплуатации рабочего места [3 c.40]:
СБ.ПЧ.З – практические часовые затраты на базовом рабочем месте руб.ч;
kМ – коэффициент показывающий во сколько раз затраты связанные с работой данного станка больше чем аналогичные расходы у базового станка [3 с.147].
СБ.ПЧ.З=3630 руб.ч; (для серийного производства)
СБ.ПЧ.З=3630 руб.ч; (для серийного производства);
Для станка: 1П371 kМ1=15 СЧ.З1=363015 = 5445 руб.ч;
Н150 kМ2=12 СЧ.З2=363012 = 4356 руб.ч;
Удельные часовые капитальные вложения в станок руб.ч [3 с.42]:
Ц – балансовая стоимость станка руб.;
FД – действительный годовой фонд времени работы станка ч;
hЗ – коэффициент загрузки станка (в серийном производстве hЗ=08);
Для станка: 1П371 по [3 с.159] Ц1 =69600000 руб.;
Н150 по [3 с. 167] Ц2 = 23600000 руб..
Капитальные вложения в здание руб.ч [3 с.43]:
f – площадь станка в плане м2 [4 с.16];
kf – коэффициент учитывающий дополнительную производственную площадь проходов проездов и др. [3с.43];
Для станка: 1П371 f 1= 42319=8037 м2 поэтому kf=25
F1=8037 25=200925м2;
Н150 f 2= 1290875=11288 м2 поэтому kf=4
F2=11288 4=45152 м2;
F = F1+F2=246077 м2;
СП.З=80631+9801 +015(3017509+624626) = 4704998681 руб.ч.
Технологическая себестоимость операции механической обработки (руб.ч):
ТШТ – штучное время на операцию мин;
kВ – коэффициент выполнения норм обычно принимаемый равным 13;
Так как во втором варианте используются те же станки что и в первом то Сп.з = Сп.з. = 4704998681 руб.ч.
Таблица 3. Сравнение себестоимости двух вариантов техпроцесса
Себестоимость операции руб.
Эг = (Со - Со) × В 100 = -59158823
Штучное время и технологическая себестоимость варианта I меньше чем варианта II поэтому расчет будем проводить по I варианту.
РАСЧЕТ ЭФФЕКТИВНОГО ФОНДА ВРЕМЕНИ РАБОТЫ ОБОРУДОВАНИЯ
Величина эффективного фонда времени работы оборудования зависит от режима работы участника и времени простоя оборудования в ремонте. Число дней на ремонт определяется на основе нормативов содержащихся в «Единой системе планово-предупредительного ремонта оборудования».
На предприятиях с прерывным производством эффективный фонд времени одного станка:
ТЭФ=(ТК-ТВ)×a×c×КИ (час) где
ТК – календарное число дней в году ТК=365;
ТВ – количество выходных и праздничных дней в году ТВ=108;
a – продолжительность работы одной смены а=8 часов;
с – количество смен с=2;
КИ – коэффициент использования оборудования.
Т.к. отсутствуют необходимые данные принимаем коэффициент использования равным Ки = 095.
Тогда эффективный фонд времени одного станка будет равен:
ТЭФ=(365-108)×8×2×095=39064 (час).
РАСЧЕТ ПОТРЕБНОГО КОЛИЧЕСТВА ОБОРУДОВАНИЯ ДЛЯ ВЫПОЛНЕНИЯ ПРОИЗВОДСТВЕННОЙ ПРОГРАММЫ
Расчет потребного количества оборудования производится по каждой операции:
КН – планируемый коэффициент выполнения норм штучного времени Кн=12;
М – общий годовой выпуск деталей (шт) – по индивидуальному заданию М=10000 шт.
Рассчитаем Чр1 для станка 1П371 и Чр2 для станка 2Н150:
(шт.) Принимаем ЧП1=1;
(шт.) Принимаем ЧП2=1;
Таблица 4 - Ведомость потребности в оборудовании
Транс-портировка и монтаж (20% от стоимости станка)
Полная стоимость оборудо-вания тыс. руб.
Токарно-револьверный
Вертикально-сверлильный
Затем определяется коэффициент загрузки на заданную программу:
ЧР – расчетное количество станков;
ЧП – принятое количество станков.
Таким образом коэффициент загрузки на токарно-револьверном станке 1П371 и вертикально-сверлильном 2Н150 соответственно равны 05555 и 02999.
РАСЧЕТ ПОТРЕБНОГО КОЛИЧЕСТВА РАБОЧИХ ПО ПРОФЕССИЯМ РАЗРЯДАМ И ФОНДА ИХ ЗАРАБОТНОЙ ПЛАТЫ
Для расчета потребного количества рабочих занятых на нормируемых работах составляется баланс рабочего времени одного рабочего.
Таблица 5 - Баланс рабочего времени одного среднесписочного рабочего на 2009 год
Состав рабочего времени
Календарный фонд времени дн.
Число нерабочих дней всего
в том числе праздничные дн.
Номинальный фонд времени дн.
Неявки на работу всего дн.
в т.ч. а) очередные и дополнительные отпуска дн.
б) отпуска по беременности и родам
г) выполнение государственных и общественных
д) прочие неявки дн.
Полезный фонд времени дн.
Номинальная продолжительность рабочего дня час.
Потери времени: всего
в т.ч. а) для занятых на вредных работах и в
праздничные дни час.
б) для подростков час.
Средняя продолжительность рабочего дня час.
Эффективный фонд рабочего времени одного рабочего час.
Затем подсчитывается потребное количество основных производственных рабочих численность которых зависит от трудоемкости выполнения отдельных операций.
Для расчета численности основных производственных рабочих используется штучно-калькуляционное время:
ТП.З. – подготовительно-заключительное время которое зависит от характера производственного процесса типа производства характера труда и участия работника в осуществлении производственного процесса организации труда и обслуживании рабочего места.
По [2 с.35] мин где
Оперативное время равно:
n – оптимальный размер партии деталей. [5 c.170]
где Nср.д. – средняя потребность деталей;
где NМ – месячный выпуск изделий шт;
Др – количество рабочих дней в месяц (ДМ=217).
Где nmin – минимальный размер партии деталей. Для нашего случая оно рассчитывается следующим образом:
где tсм – продолжительность смены мин.;
t – норма штучного времени (минимальное из всех выполняемых операций) мин;
Принимаем Rз.-в.=48(мин).
Численность основных производственных рабочих вычисляется по формуле:
Принимаем Rз.-в.=17(мин).
Трудоемкость (Т) годовой программы с учетом выполнения норм выработки составляет:
Таблица 6 - Расчет численности рабочих занятых на нормируемых работах
Трудоемкость годовой программы с учетом выполнения норм выработки (час)
Номинальный фонд времени одного рабочего (час) ТН×ТНОМ
Явочное число рабочих (чел) (3:4)
Полезный фонд времени одного рабочего (час.ТПЛ)
Списочное число рабочих (чел.) (3:6)
Численность вспомогательных рабочих определяется расчетным путем по специальностям исходя из норм обслуживания конкретного предприятия. Ориентировочно она определяется в процентах к численности производственных рабочих: крупносерийное производство - 60-70% серийное производство – 40-50% единичное и мелкосерийное производство – 25-35%. Численность специалистов и служащих устанавливается путем определения необходимых на участке должностей. Для этого используются данные о структуре управленческого аппарата на предприятии с учетом расчетного количества оборудования т.е. пропорционально количеству оборудования потребного для выполнения производственной программы. Поскольку для расчета численности вспомогательных рабочих специалистов и служащих недостаточно данных ограничимся расчетом фонда заработной платы рабочих занятых на нормируемых работах.
Тарифный фонд заработной платы рабочих занятых на нормируемых работах определяется как произведение часовой тарифной ставки и трудоемкости производственной программы.
Часовая тарифная ставка:
МТС – минимальная тарифная ставка 1 разряда МТС=77 000 руб.;
КТАР – тарифный коэффициент;
ТМЕС – месячный фонд времени Тмес. = 1693 (данные Министерства труда и социальной защиты населения ежегодно публикуемые в периодической печати).
Для третьего разряда:
Для четвертого разряда:
Величина доплат по премиальным системам за работу в ночное время оплаты отпусков берется по данным предприятия
Ориентировочно доплаты по премиальным системам составляют 20-25% тарифного фонда заработной платы (принимаем 20%); оплата отпусков и за выполнение государственных и общественных обязанностей 10-15% (принимаем 10%) доплаты в ночные часы равны 40% ЧТС за каждый час работы в ночную смену.
Наименование операции
Час. тариф. ставка руб.
Трудоемкость произ. программы час.
Тарифный фонд зарплаты
Годовой фонд заработной платы руб.
По премиальным сметам руб.
За работу в ночное время руб.
Таблица7– Расчет фонда заработной платы рабочих занятых на нормируемых работах
РАСЧЕТ ПОТРЕБНОСТИ И СТОИМОСТИ ОСНОВНЫХ МАТЕРИАЛОВ
При расчете потребности и стоимости сырья и материалов учитываются все затраты на сырье и материалы необходимые для изготовления данной детали с учетом транспортно-заготовительных расходов.
ЭМ=(ЦМ×НМ×КТ.З.-ЦО×НО)×М где
ЭМ – затраты на сырье и материалы;
ЦМ – оптовая цена материала за 1 кг ЦМ=2600 руб.;
НМ – норма расхода материала на единицу продукции кг;
где размерные величины даны для штучных заготовок с учетом припуска на отрезание.
КТ.З. – коэффициент транспортно-заготовительных расходов;
ЦО – цена возвратных отходов на 1 кг ЦО=900 (руб.);
НО – вес возвратных отходов на единицу продукции кг.
Для удобства заполнения таблицы рассчитаем отдельно слагаемые
ЦМ×НМ×КТ.З×М=2600×74278×11×10000=212435080 руб.
ЦО×НО×М=900×25576×10000=23018400 рублей.
ЭМ=212435080-23018400=189416680 (руб.).
РАСЧЕТ РАСХОДОВ НА СОДЕРЖАНИЕ И ЭКСПЛУАТАЦИЮ ОБОРУДОВАНИЯ
1 Амортизация оборудования и транспортных средств
Затраты на амортизацию оборудования транспортных средств и ценного инструмента определяются исходя из первоначальной их стоимости и действующих годовых норм амортизационных отчислений.
КОБ – полная первоначальная стоимость оборудования и транспортных средств [таблица 4] руб.;
НА – норма амортизационных отчислений %;
НА=141% (для металлорежущего оборудования).
2 Эксплуатация оборудования
2.1. Затраты на вспомогательный материал (смазочные обтирочные материалы эмульсии для охлаждения и прочий вспомогательный материал необходимый для ухода за оборудованием и поддержанием его в исправном состоянии) рассчитываются по формуле:
где: НР – годовая норма расхода материала на единицу оборудования;
ДО – количество единиц оборудования;
ЦМ.В. – цена единицы вспомогательного материала.
При отсутствии необходимых данных затраты на вспомогательные материалы вычисляются из расчета 3% стоимости станка с учетом коэффициента загрузки.
СМ.В.1=003×СОБ×КЗ=003×46946592= 1408398 ( руб.);
СМ.В.2=003×СОБ×КЗ=003×8595120 = 257854 ( руб.);
СМ.В.= 1408398 + 257854 = 1666250 ( руб.).
2.2. Основная и дополнительная заработная плата вспомогательных рабочих обслуживающих оборудование (наладчиков электромонтеров слесарей ремонтных рабочих и др.) зависит от численности рабочих их часовой тарифной ставки и эффективного фонда времени одного рабочего. Ориентировочно принимаем основную и дополнительную заработную плату вспомогательных рабочих равной 40% годового фонда заработной платы основных рабочих т.е.:
ЗПвсп. = 04×3857154 = 1542862 (руб.).
2.3. Годовые затраты на электроэнергию вычисляются по формуле:
где: МУСТ – суммарная мощность электродвигателей установленных на оборудовании кВт;
ТЭФ – эффективный фонд времени работы оборудования час;
ЦЭ – плата за 1 кВт×час электроэнергии ЦЭ=230 руб.кВт×час.
КР – коэффициент одновременной работы двигателя станка
КП – коэффициент учитывающий потери в сети КП=096;
КД – КПД электродвигателей КД=08.
Для токарно-револьверного станка
[3159-160 таблица 4.4] МУСТ=22 кВт:
Для вертикально-сверлильного станка
[3167-168 таблица 411] МУСТ=75 кВт:
В целом затраты на эксплуатацию оборудования составляют
66250+1542862+11851020=15060132 (руб.).
3 Текущий ремонт оборудования
В затратах на текущий ремонт оборудования учитываются в основном расходы связанные с приобретением для текущего ремонта запасных частей и других материалов а также основная и дополнительная заработная плата с отчислениями на социальное страхование рабочих занятых ремонтом оборудования. При отсутствии необходимых данных затраты по этой статье можно ориентировочно принять 10% от стоимости оборудования включая транспортно-заготовительные расходы с учетом коэффициента загрузки.
СТ.Р.1= 01×46946592 = 4694659 (руб.);
СТ.Р.2= 01×8595120 = 859512 (руб.);
СТ.Р.= 4694659+859512=5554171 (руб.);
4 Внутризаводское перемещение грузов
Затраты по данной статье рассчитываются исходя из грузооборота для перевозки деталей и стоимости перемещения 1 тонны груза.
СПЕР – цена перевозки одной килограмма груза (10% от стоимости 1 тонны материала):
КПЕР – коэффициент перемещения грузов равный количеству станков сложенному с единицей
5 Износ малоценных и быстроизнашивающихся инструментов и приспособлений
Сумма износа малоценных и быстроизнашивающихся инструментов и приспособлений приблизительно равна 5% стоимости станка.
СИ1= 005×46946592 = 2347330 (руб.);
СИ2= 005×8595120 = 429756 (руб.);
СИ = 2347330 + 429756=2777086 (руб.).
Итого по статье «Расходы на содержание и эксплуатацию оборудования» определяется как сумма затрат по пунктам 6.1 – 6.5. результаты расчета сведены в таблицу 6.
Таблица 8 - Смета расходов на содержание и эксплуатацию оборудования
Наименование статей расхода
Амортизация оборудования и транспортных средств
Эксплуатация оборудования (кроме расходов на текущий ремонт)
Текущий ремонт оборудования
Внутризаводское перемещение грузов
Износ малоценных и быстроизнашивающихся инструментов и приспособлений
РАСЧЕТ ОБЩЕЦЕХОВЫХ РАСХОДОВ
Общецеховые расходы включают следующие затраты:
Содержание аппарата управления цеха.
Содержание прочего цехового персонала.
Амортизация зданий сооружений и инвентаря.
Содержание зданий сооружений и инвентаря.
Текущий ремонт зданий сооружений и инвентаря.
Испытания опыты и исследования.
Износ малоценного и быстроизнашивающегося инвентаря.
В связи с большой номенклатурой изготовляемых в цехе изделий рассчитать общецеховые расходы приходящиеся на конкретную деталь сложно. Поэтому в курсовой работе при определении этих затрат можно использовать следующую формулу:
где: СЦЕХ.ПР. – годовая сумма общецеховых расходов по проектируемому варианту руб.;
СЦЕХ.СР. – годовая сумма общецеховых расходов по сравниваемому варианту руб.;
ЗОС.СР. – основная заработная плата производственных рабочих по сравниваемому варианту руб.;
ЗОС.ПР. – основная заработная плата производственных рабочих по проектируемому варианту руб.
Отношение находится в диапазоне 175-225. Принимаем .
ОПРЕДЕЛЕНИЕ ЦЕХОВОЙ СЕБЕСТОИМОСТИ ИЗГОТОВЛЕНИЯ ДЕТАЛИ ПО ПРОЕКТИРУЕМОМУ (ПЕРВОМУ) ВАРИАНТУ ТЕХНОЛОГИЧЕСКОГО ПРОЦЕССА
После определения всех расходов связанных с изготовлением детали по первому варианту технологического процесса составляется плановая калькуляция. Плановая калькуляция составляется на годовой объем и на единицу продукции.
Таблица 9 - Плановая калькуляция единицы продукции при изготовлении по первому варианту
Наименование статей затрат
Сырье и основные материалы
Основная заработная плата производственных рабочих
Дополнительная заработная плата производственных рабочих
Отчисления на социальное страхование
Расходы на содержание и эксплуатацию оборудования
Таким образом при применении первого варианта плановая себестоимость единицы продукции составит 290942 руб. а всего выпуска (10000 ед.) – 290941989 руб.
СПИСОК ИСПОЛЬЗОВАННЫХ ИСТОЧНИКОВ
Методические указания. Синтез маршрута обработки типовых компонентов детали. Витебск 2006.
Методические указания. Расчет цеховой себестоимости изготовления детали. Витебск 2001.
Горбацевич А.Ф. Шкред В.А. Курсовое проектирование по технологии машиностроения.- Мн.: Выш. школа 1983. – 256 с. ил.
Справочник технолога-машиностроителя в 2-х томах . – М.: Машиностроение 1986. – 500с.
Новицкий Н.И. Организация и планирование производства. Минск 2004.
Чертеж Стакан.cdw

Рекомендуемые чертежи
- 03.07.2014
- 01.07.2014
Свободное скачивание на сегодня
Обновление через: 6 часов 30 минут