Модернизация радиальной опоры АКБ-3М




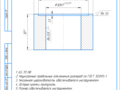
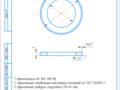
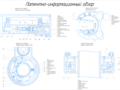

- Добавлен: 24.01.2023
- Размер: 2 MB
- Закачек: 0
Описание
Состав проекта
![]() |
![]() |
![]() |
![]() ![]() ![]() ![]() |
![]() ![]() ![]() ![]() |
![]() ![]() ![]() ![]() |
![]() |
![]() ![]() ![]() ![]() |
![]() ![]() ![]() ![]() |
![]() ![]() ![]() ![]() |
![]() ![]() ![]() ![]() |
![]() ![]() ![]() ![]() |
![]() ![]() ![]() ![]() |
![]() ![]() ![]() ![]() |
![]() |
![]() ![]() ![]() |
![]() ![]() ![]() |
Дополнительная информация
ПИО.cdw

Механический ключ для труб.
Кулачковая полумуфта
Кольцевая направляющая
Кольцевые направляющие
Направляющая кольцевой опоры
Направляющие рычагов
Направляющие кольцевой опоры
Конечный выключатель
Патент РФ № 2223170.
Трубозахватный механизм
Паз наружного кольца
Патент РФ № 2026483.
Трубовращатель бурового ключа
Наружное силовое кольцо
Выдвижной силовой ролик
Патент РФ № 2026484.
Буровой приводной ключ
Патентно-информационный обзор
Блок ключа АКБ-3М2.cdw

Диаметр свинчиваемых и развинчиваемых труб
Привод вращателя поршневой пневмомотор
Частота вращения трубозажимного устройства
максимальный (при двух-трех докреплениях) 30
Длина хода блока ключа
Давление воздуха в сети (у пульта управления)
Объемный расход воздуха
блока ключа с кареткой и колонной 1730х1030х2388
пульта управления 790х430х1320
КП-130602.64-0702253 01.00.000
КП-130602.65-0702253 01.00.000
Трубозажимное устройство
Промежуточная шестерня
КП-130602.65-0702253 02.00.000
Нижний челюстедержатель
Пневмодвигатель П13-16
Подшипник 8211 ГОСТ7872-89
Подшипник 53614 ГОСТ 7872-89
Опора радиальная.cdw

Втулку запрессовать на ось по Н7k6.
Вращение ролика проверить рукой.
Перекос или заедание недопустимы.
Смазка поверхности ролика производится графитной смазкой.
Технические характеристики:
Допустимый крутящий момент
Минимальная температура
КП-130602.65-0702253 02.000.00
Кольцо А54 ГОСТ 13943-86
-32х52-1 ГОСТ 8752-79
Гайка М20 ГОСТ 15521-70
Технические требования:
Ось А3.cdw

Неуказанные радиусы скруглений 1
Размер проточки (вид А) и галтельный переход (вид Б)
обеспечивается инструментом.
Контролировать все размеры. Контроль резьбы - калибр-кольцом.
Сталь 40ХН ГОСТ 4543-71
КП-130602.65-0702253 02.02.000
Ролик А3.cdw

Размер канавки (вид А) обеспечивается инструментом.
Неуказанные радиусы скруглений 0.8 мм max.
Сталь 45 ГОСТ 1050-88
КП-130602.65-0702253 02.01.000
Втулка антифрикционная А4.cdw

Указанная шероховатость обеспечивается инструментом
Острые кромки притупить.
Размер обеспечивается инструментом.
БрОЦС 5-5-5 ГОСТ 613-79
КП-130602.65-0702253-02.03.000
Ось модифицированная А3.cdw

Неуказанные радиусы скруглений 0.8 мм max.
Размер проточки (вид А) обеспечивается инструментом.
Контролировать все размеры. Контроль резьбы - калибр-кольцом.
Улучшение до 269 289 НВ
Сталь 40ХН ГОСТ 4543-71
КП-130602.65-0702253 03.02.000
Упорное кольцо А4.cdw

Неуказанные предельные отклонения размеров по ГОСТ 30.893-1
Неуказанные радиусы скруглений 0.8 мм max.
Острые кромки притупить.
Сталь 45 ГОСТ 1050-88
КП-130602.65-0702253 02.03.000
Втулка А4.cdw

Неуказанные предельные отклонения размеров по ГОСТ 30.893-1
Неуказанные радиусы скруглений 0.8 мм max.
Острые кромки притупить.
КП-130602.65-0702253 02.04.000
Сталь 45 ГОСТ 1050-88
Опора радильная модифицированная.cdw

Вращение ролика проверить рукой.
Перекос или заедание недопустимы.
Смазка поверхности ролика производится графитной смазкой.
Опора заполняется смазкой Циатим-221
Технические характеристики:
Допустимый крутящий момент 30 кНм
Допустимое напряжение сжатия 540 МПа
Минимальная температура -30 С
КП-130602.65-0702253 03.00.000
Кольцо А54 ГОСТ 13943-86
-32х52-1 ГОСТ 8752-79
Гайка М20 ГОСТ 15521-70
Подшипник 205 ГОСТ 8338-75
Подшипник 60205 ГОСТ 7242-81
Технические требования:
01. Титул.docx
образовательное учреждение
высшего профессионального образования
«СИБИРСКИЙ ФЕДЕРАЛЬНЫЙ УНИВЕРСИТЕТ»
«Расчет и автоматическое конструирование машин для бурения нефтяных и газовых скважин»
Модификация бурового ключа АКБ – 3М2
тема проекта (работы)
подпись дата должность ученая степень инициалы фамилия
номер группы номер зачетной книжки подпись дата инициалы фамилия
02. Записка.docx
1 Общие сведения ..4
2 Конструкция и принцип действия .4
Патентно – информационный обзор 10
1 Патент РФ 2243351. Гидроприводной подвесной трубный ключ 10
2. Патент RU 2000010. Механический ключ для труб .11
3. Патент RU 2223170. Механический ключ .14
4. Патент RU 2026483. Трубовращатель бурового ключа ..18
Модернизация АКБ – 3М2 22
1. Техническое предложение ..22
2. Технология модернизации радиального ролика АКБ – 3М2 ..24
3. Прочностной расчет радиального ролика ..28
3.1. Построение расчетной схемы оси ролика 28
3.2. Построение эпюр внутренних силовых факторов ..29
3.3. Проверка выбора материала оси ..31
3.4. Расчет оси на усталостную прочность 33
3.5. Расчет коэффициента запаса усталостной прочности..35
3.6. Расчет коэффициента запаса усталостной прочности. Проверка прочности ..35
3.7. Оценка вероятности безотказной работы 36
3.8. Расчет подшипников качения на заданный ресурс 38
Список использованной литературы .42
Стационарные буровые автоматические ключи - устройства предназначенные для механизации и автоматизации сопутствующих процессов (свинчивание-развинчивание наращивание колонны и др) в ходе спуско-подъемных операций прибурении нефтяных и газовых скважин.Применяются внефтегазовойотрасли.
Выделяютавтоматический буровой ключ(АКБ) и автоматический буровой ключ с гидроприводом (КБГ).
Среди АКБ наиболее распространены АКБ с пневмоприводами3М2и3М2.Э2(модификация 3М2)
Среди стационарных буровых автоматических ключей с гидроприводом чаще всего эксплуатируютсяКБГиКБГ-2.
Они применяются для механизации и автоматизации свинчивания и развинчивания бурильных трубиобсадных труб.
Задачи курсового проекта:
изучить буровой ключ АКБ – 3М2 его устройство и принцип работы;
провести патентно-информационный обзор буровых ключей особое внимание обратить на трубозажимные устройства;
на основе одного из четырех выбранных патентов провести модернизацию бурового ключа АКБ – 3М2;
провести расчет проведенной модернизации;
выполнить необходимые чертежи.
Состав графической части:
Патентно – информационный обзор;
Общий вид рассматриваемого оборудования;
Сборочный чертеж модернизируемого узла оборудования;
Автоматический буровой ключ АКБ – 3М2.
АКБ-3М2 - буровой автоматический стационарный ключ предназначен для механизации процессов свинчивания и развинчивания бурильных и обсадных труб при спуско-подъемных операциях. Буровой ключ АКБ-3М2 применяется при бурении нефтяных и газовых скважин.
Буровой ключ АКБ-3М2 устанавливают на буровой между лебедкой и ротором со стороны приводного вала на вышечно – лебедочном блоке к которому он прикрепляется болтами.
Ключ состоит из блока ключа колонны с кареткой и пульта управления. Механизмы ключа работают при помощи пневмодвигателя и пневмоцилиндров от сети сжатого воздуха.
Блок ключа - основной механизм выполняющий операции свинчивания и развинчивания труб. По направляющим полозьям блок ключа перемещается вдоль каретки под воздействием двух пневматических цилиндров двойного действия и может подводиться к бурильной трубе или отводиться от нее.
Вращение трубозажимного устройства блока ключа - от пневмодвигателя через редуктор. Каретка свободно вращается в верхней части колонны ее положение при работе фиксируется. Каретка с блоком ключа может перемещаться вдоль колонны по высоте.
Дистанционное управление работой ключа обеспечивает пульт.
2.Конструкция и принцип действия.
Автоматический стационарный буровой ключ АКБ –3М2 (рис.1.1 1.2 1.3) состоит из трех основных узлов: блока ключа 1 колонны с кареткой 11 и
пульта управления 111 (рис 1.1 1.2 1.3).
Блок ключа (рис. 1.1) является основным механизмом выполняющим
операции завинчивания или развинчивания бурильных труб.
Рис.1.1. Стационарный автоматический ключ АКБ-3М2
– блок ключа; 2 – каретка с пневмоцилиндром; 3 – стойка; 4 – пульт управления.
Блок ключа представляет собой корпус на котором смонтировано
трубозажимное устройство I понизительный редуктор II пневмомотор III маховик 1Vцилиндр зажима челюстей V блок цилиндров VI.
Блок ключа внизу имеет направляющие полозья на которых он перемещается вдоль каретки под действием двух пневматических цилиндров двойного действия. Благодаря такому устройству блок ключа может подводиться или отводиться от бурильной трубы (центра скважины).
Рис. 1.2 Общий вид ключа.
Рис.1.3. Общий вид ключа.
Трубозажимное устройство в основном состоит из верхнего «плавающего» корпуса 14 с зажимным приспособлением 9 нижнего зажимного приспособления 33 вмонтированного в корпус редуктора разрезной шестерни 2 с втулкой 3 храповика и промежуточного диска 4 с3-мя ведущими пальцами 15.Трубозажимное устройство и корпус ключа в передней части имеют вырезы для прохода бурильной трубы. Каждое верхнее и нижнее трубозажимное приспособление состоит из пары сменных челюстей 8 34 которые вставляются в челюстедержатели 7 и 35 и удерживаются в них дугообразными пружинами 10 31 и болтами 32 вкладышей со спиральной поверхностью устанавливаемых по две пары в каждый корпус. Причем в нижний корпус устанавливаются две пары вкладышей со спиральной поверхностью 11° а в верхний корпус трубозажимного устройства устанавливаются две пары унифицированных вкладышей 52 (утолщенных) спиральные поверхности которых образуют 7° на завинчивание и 9° на развинчивание. Челюстедержатели 7 и 35 из своего первоначального положения могут проворачиваться на некоторый угол относительно своих корпусов при этом челюсти 8 34 скользя по спиральной поверхности вкладышей сближаются и сжимают замок (трубу) (рис. 1.4—III). Для надежного сцепления замком (трубой) челюсти имеют вставные сухари 54 с насечкой(рис. 1.5).При изменении диаметра бурильного инструмента производится замена рабочих элементов ключа — челюстей 8 34 и упоров 11 30 на соответствующие размеры. Проворот нижнего челюстедержателя 35 осуществляется от пневматического цилиндра двойного действия V шток которого шарнирно связан с поводком нижнего челюстедержателя.
Поворот верхнего челюстедержателя осуществляется с помощью храпового устройства представляющего собой пару храповиков 20 и 21установленных во втулке 3 и нижнем челюстедержателе 35.
Рис. 1.4. Блок ключа.
Храповик 21является неподвижным храповик 20 выдвигается штоком 18 блока цилиндров VI в момент зажатия челюстями бурильного замка. Верхний челюстедержатель имеет хвостовик I свободно входящий в паз втулки 3.При вращении разрезной шестерни в момент упора неподвижного храповика 21 в храповик 20 выдвинутый штоком 18 происходит кратковременная остановка втулки 3 и связанного с ней хвостовика I верхнего челюстедержателя 7. В результате дальнейшего вращения верхнего корпуса относительно неподвижного челюстедержателя 7 происходит зажатие замка (рис. 1.4—III).
Рис. 1.5. Блок ключа.
Для установки и фиксации верхнего челюстедержателя в среднем (нейтральном) положении при холостом вращении верхнего корпуса относительно трубы челюстедержатель подпирается двумя бойками 51 и стопорится шариковым фиксатором 13.Быстрая и точная остановка вращающихся частей трубозажимного устройства в нейтральном положении по окончании свинчивания или развинчивания для последующего отвода ключа от трубы осуществляется специальным устройством. Это устройство состоит из штока совмещения 26 который под действием поршня блока цилиндров VI выдвигается вверх и заскакивая в гнездо разрезной шестерни производит остановку. Для смягчения удара и предохранения деталей от поломок верхняя часть штока совмещения с 2-х сторон имеет скосы. Такие же скосы имеются и в гнезде шестерни. Включение штока совмещения может происходить только при вращении шестерни на малых оборотах что предусмотрено конструкцией пульта управления. Для совмещения разрезной шестерни включение пневмодвигателя производится в сторону освобождения челюстей.
Патентно – информационный обзор.
1.Патент РФ 2243351. Гидроприводной подвесной трубный ключ.
Гидроприводной подвесной трубный ключ относится к устройствам для свинчивания и развинчивания обсадных труб нефтяного сортамента в процессе спуско-подъемных операций при бурении нефтяных и газовых скважин. Ключ содержит корпус с двумя откидывающимися створками. В корпусе расположено вращательное зажимное устройство состоящее из ротора рабочей и ценрирующих челюстей. На корпусе установлены гидрораспределитель гидромотор. Тормозное устройство имеет ролик из упругого материала установленный в центральной части рабочей челюсти и взаимодействующий с концевиками при смещении рукоятки гидрораспределителя. Концевики имеют наклонные грани и закреплены на внутренней стенке корпуса по обе стороны относительно ролика. Рабочая челюсть после накатывания ролика на грань концевика притормаживается и начинает перемещаться к трубе. При развинчивании труб ролик накатывается на грань другого концевика и рабочая челюсть притормаживается относительно ротора что позволяет отойти рабочей челюсти от трубы.
Изобретение относится к устройствам для свинчивания и развинчивания обсадных труб нефтяного сортамента в процессе спуско-подъемных операций при бурении нефтяных и газовых скважин.
Ключ содержит корпус 1 с двумя откидывающимися створками 2 которые после наведения ключа на трубу закрываются и фиксируются в месте их соединения замком 3.
На корпусе 1 установлены гидромотор 4 являющийся приводом ключа и гидрораспределитель 5 для управления гидромотором 4.
В ключе имеется зажимное устройство состоящее из ротора 6 двух центрирующих челюстей 7 и рабочей челюсти 8 которая постоянно взаимодействует с ротором 6 через ролик 9.
Тормозное устройство ключа представляет собой ролик 10 из упругого материала (например резины) который установлен в центральной части рабочей челюсти 8 и взаимодействует с концевиками 11которые установлены по обе стороны относительно ролика 10 из упругого материала на внутренней стенке корпуса 1. Крепление концевиков 11 к корпусу 1 осуществляется с помощью болтов 12. На концевиках 11 выполнены наклонные грани для обеспечения захода и схода ролика 10 из упругого материала во время вращения зажимного устройства.
2.Патент RU 2000010. Механический ключ для труб.
Использование: в буровой технике и может быть использовано в буровых установках для свинчивания-развинчивания труб при спуско-подъемных операциях. Сущность изобретения: механический ключ для труб включает корпус размещенный в нем приводе ведомым венцом изогнутые рычаги установленные шарнирно на кольцевой опоре и плашки. Кулачковая полумуфта закреплена на ведущем венце. В направляющей полумуфты установлена другая кулачковая полумуфта связанная с дополнительным приводом размещенным на корпусе и с гидроцилиндрами встроенными в корпус. Рычаги соединены между собой кулисой и установлены на одной плавающей оси вместе с упором подпружиненным относительно кулисы и кольцевой опоры. Плашки сферической поверхностью установлены в рычаги и включают сухари установленные с возможностью взаимодействия с ведомым венцом. Плашки выполнены с двумя рабочими поверхностями которые попарно образуют по крайней мере три самотормозящихся угла.
Механический ключ (фиг.123) состоит из корпуса 1 с размещенным на нем приводом 2 и установленными на нем роликами 3 и 4. На роликах 3 и 4 установлен ведомый венец 5 с закрепленной на нем кулачковой полумуфтой 6 имеющей кольцевую направляющую 7 в которой установлена кулачковая полумуфта 8. Обе кулачковые полумуфты 7 и 8 сцеплены кулачками 9. Ролики 3 фиксируют ведомый венец 5 с закрепленной на нем кулачковой полумуфтой 6 от перемещения по вертикали ролики 4 по горизонтали. В кольцевых направляющих 10 ведомого венца 5 установлена разъемная кольцевая опора 11. В направляющих 12 кольцевой опоры 11 установлены два разъемных рычага 3 и14 которые соединены между собой шарнирно осью 15. В направляющих 16 рычага 14 на оси 15 установлен упор 17. Ось 15 установлена в направляющих 18 кольцевой опоры 11. В направляющих 19 рычагов 13 и 14 установлены плашки со сферическими поверхностями 20. Каждый из рычагов.13 и 14 имеет по пальцу 21 связанных друг с другом кулисой 22 посредством ее лазов 23. Между упором 17 и кулисой 22 установлены пружины 24 а упор 17 подпружинен пружиной 25 относительно кольцевой опоры 11 ведомый венец 5 зафиксирован защелками 26 с шарниром 27 и гидроцилиндрами 28 относительно корпуса 1 На ведомом венце 5 имеется кулачковый профиль 29 для взаимодействия с сухарями 30 закрепленными на плашках со сферическими поверхностями 20 Плашки со сферическими поверхностями 20 имеют рабочие поверхности 31 и 32 (фиг.3) и сферическую поверхность 33 (фиг.2). которой они установлены а направляющих 19 рычагов 13 и 14. В корпус 1 встроены плунжерные гидроцилиндры 34 (фиг. 4) штоки которых упираются в кулачковую полумуфту 8 которая может по ним скользить: которая через сферические подшипники с дополнительным приводам 35. Механический ключ предназначен для работы с трубой 36 которая имеет возможность взаимодействовать с упорам 17 и с рабочими поверхностями 31 и 32 плашек 20. Рабочие поверхности 31 и 32 выполнены (фиг.3) с такими углами наклона относительно оси симметрии 37 плашек со сферическими поверхностями 20 которые при расположении их противоположно друг другу образуют углы меньше двойного угла трения (угла обеспечивающего самоторможение
При условии что материал плашек - сталь и рабочие поверхности выполнены рифлеными коэффициент трения принимается = 03 что соответствует углу трения равному 17 и обеспечивается самоторможение трубы 36 относительно рабочих поверхностей 31 и 32.
Рычаги 39 (фиг. 3) соединены шарнирно с гидроцилиндрами 40 закрепленными на корпусе 1 и имеющими на штоках 41 пружины сжатия 42 Между рычагами 39 установлены два конечных выключателя 43. Рядом с защелками 26 (фиг.1) расположены конечные выключатели 44 соединенные связью 45 с конечными выключателями 43 которые линией связи 46 соединены с электромагнитом 47 золотника управления 48 гидроцилиндрами 40. Рычаги 39 гидроцилиндра 40 с пружинами rr42 на штоках 41 конечные выключатели 43 и 44 связями 45 и 46 соединенные между собой и электромагнитом 47 золотника 48 служат для стопорения кольцевой опоры 11 относительно корпуса 1. Указанное стопорение может быть осуществлено другой любой конструкцией.
3.Патент RU 2223170. Механический ключ.
Изобретение относится к области глубокого бурения скважин и предназначено для свинчивания и развинчивания скважинных труб главным образом при выполнении спускоподъемных операций в процессе бурения крепления и ремонта скважин. Механический ключ содержит корпус роторную шестерню с боковым проемом трубозахватный механизм с челюстедержателем и смонтированными на нем челюстями привод соединенный с роторной шестерней двумя промежуточными зубчатыми колесами опорные ролики взаимодействующие с наружной поверхностью роторной шестерни и ролики для направления челюстедержателя установленные в роторной шестерне или челюстедержателе. Роторная шестерня имеет копиры на внутренней поверхности. Каждая челюсть ключа состоит из шарнирно соединенных между собой корпуса и вкладыша расположенных по одну сторону от оси поворота в челюстедержателе и снабженных на своих концах со стороны обращенной к зажимаемой трубе зубчатыми плашками а со стороны обращенной к копиру роторной шестерни опорными площадками. Челюсть включает самоустанавливающийся ролик выполненный с гребнями для перемещения по копиру роторной шестерни и с одной или более цапфовыми шейками для одновременного контактирования с опорными площадками корпуса и вкладыша челюсти. В результате получена такая конструкция ключа которая обеспечивает при относительной простоте и невысокой стоимости в изготовлении минимальную повреждаемость трубы при ее захвате путем достижения равномерности приложения нагрузок в местах соприкосновения плашек трубозахватных устройств к трубе.
В соответствии с заявляемым техническим решением механический ключ (Фиг. 1) содержит корпус 1 в котором смонтированы опорные ролики 2. На ролики 2 опирается роторная шестерня 3 с боковым проемом 4 и копирами 5 на внутренней поверхности. Ключ содержит также трубозахватный механизм 6 с челюстедержателем 7 и смонтированными на нем челюстями 8. Челюстедержатель центрируется относительно роторной шестерни 3 группой роликов установленных в роторной шестерне или челюстедержателе (не показаны) и имеет возможность ограниченного поворота относительно нее. Относительно корпуса 1 челюстедержатель заторможен с помощью известного тормозного устройства которое не является предметом настоящей заявки и не показано на Фиг.1. Кроме того механический ключ включает привод 9 известного типа соединенный с роторной шестерней 3 посредством двух промежуточных зубчатых колес 10. Каждая челюсть 8 ключа (Фиг. 2) состоит из корпуса 11 челюсти 8 и вкладыша 12 с направляющим отверстием 13 под шарнирный палец 14. Корпус 11 челюсти 8 и вкладыш 12 расположены по одну сторону от оси поворота (шарнирного кольца 14) в челюстедержателе и снабжены на своих концах со стороны обращенной к зажимаемой трубе 15 зубчатыми плашками 16 на корпусе 11 челюсти 8 и 17 на вкладыше 12. Со стороны обращенной к копиру 5 роторной шестерни 3 корпус 11 челюсти 8 и вкладыш 12 имеют опорные площадки соответственно 18 и 19. При этом челюсть 8 включает самоустанавливающийся ролик 20. Последний выполнен с гребнями 21 (фиг 2 3 4) для перемещения по копиру 5 роторной шестерни 3 и с одной (или более) цапфовыми шейками 22 для одновременного контактирования с опорными площадками 18 и 19 корпуса 11 и вкладыша 12 челюсти 8 (фиг.2 3 4). Возможно также выполнение ролика простой цилиндрической формы но это приведет к ухудшению условий его качения повышенному проскальзыванию и износу.
Для исключения рассоединения челюсти 8 на составляющие части при извлечении ее из ключа с целью замены или ремонта ролик 20 с большим радиальным зазором 23 надет на тонкую (не силовую) шпильку 24. укрепленную в проушинах корпуса 11 челюсти 8 (фиг.3 4). Радиальный зазор 23 служит для обеспечения достаточной свободы смещения от номинального положения ролика 20 по копиру 5 (фиг.1 2) роторной шестерни 3 для осуществления перераспределения и выравнивания нагрузки между плашками 16 и 17. Следует отметить что конструктивная схема взаимосвязи ролика 20 с корпусом 11 может быть иной лишь бы соблюдался принцип обеспечения самоустановки ролика под нагрузкой. Корпус 11 челюсти 8 снабжен перемычкой 25 (фиг.2 и 5) между проушинами причем на части окружности отверстие под шарнирный палец 14 расположено в перемычке 25 а направляющее отверстие 13 во вкладыше 12 на соответствующем угле не замкнуто. Такое выполнение обеспечивает усиление отверстия в проушинах и предотвращение изгиба шарнирного пальца 14. Работа заявляемого механического ключа осуществляется следующим образом.
Свинчивание. Вращение роторной шестерне 3 от привода 9 передается по часовой стрелке посредством двух промежуточных зубчатых колес 10.
При этом вначале заторможенный челюстедержатель 7 вместе с шарнирными пальцами 14 челюстей 8 и вкладышей 12 стоит на месте а копиры 5 прямого хода расположенные на внутренней поверхности роторной шестерни контактируя с роликами 20 челюстей придвигают к трубе 15 плечи челюстей 8 и вкладышей 12 с зубчатыми плашками 16 и 17. Это происходит при нарастании крутящего момента на зубчатом венце роторной шестерни. После превышения крутящего момента на зубчатом венце роторной шестерни над тормозным моментом на челюстедержателе 7 дальнейшее вращение роторной шестерни 3 челюстедержателя 7 и зажатой челюстями 8 трубы 15 будет происходить совместно.
Как правило это происходит до достижения заданной величины крутящего момента. После чего вращение прекращается.
Чтобы отвести ключ от трубы производят отделение челюстей от трубы.
Для этого реверсируют направление вращения роторной шестерни. Поскольку при этом соответствующие копиры становятся ниспадающими то под действием упругих деформаций всех элементов участвующих в захвате трубы ролики 20 челюстей 8 скатываются в нижние части копиров 5. Вращение роторной шестерни 3 продолжается до тех пор пока боковые проемы роторной шестерни и челюстедержателя не совместятся (вручную при медленном вращении или автоматически) с боковым проемом корпуса ключа.
Далее ключ отодвигается от трубы причем труба проходя через боковой проем раздвигает челюсти.
Происходит так же как и свинчивание. С разницей только в направлении вращения.
4.Патент RU 2026483. Трубовращатель бурового ключа.
Использование: свинчивание и развинчивание буровых и обсадных труб. Сущность: трубовращатель содержит механизм захвата в виде наружного и внутреннего колец с шарнирными рычагами и переключателем частот его вращения фрикционный тормоз с приводом узел реверсирования поворота внутреннего кольца относительно наружного. Внутреннее кольцо выполнено с подпружиненными фиксаторами наружное кольцо - с внутренними пазами узел реверсирования в виде нескольких стопоров фрикционный тормоз - со средством для создания двух величин тормозного момента стопоры размещены во внутренних пазах наружного кольца с возможностью перемещения по окружности в пределах паза и взаимодействия с подпружиненными фиксаторами при этом усилие срабатывания подпружиненных фиксаторов больше усилия создаваемого стопорами при меньшем тормозном моменте и меньше усилия создаваемого стопорами при большем тормозном моменте. Замкнутый корпус трубовращателя выполнен с фрикционными накладками с приводом а средство для создания двух величин тормозного момента выполнено в виде плоского тормозного диска установленного на внутреннем кольце между фрикционными накладками с возможностью взаимодействия с ними и передачи вращающего момента при этом привод фрикционных накладок выполнен в виде подпружиненных поршней.
На фиг. 1 показан поперечный разрез устройства; на фиг.2 - сечение А-А на фиг.1; на фиг.3 - сечение В-В на фиг.2.
Трубовращатель бурового ключа содержит установленные в корпусе 1 наружное 2 и внутреннее 3 кольца. На внутреннем кольце 3 на осях 4 установлены двуплечие рычаги 5 снабженные отводными 6 и выдвижными 7 опорными роликами. На внутреннем кольце 3 установлены также подпружиненные фиксаторы 8 имеющие возможность взаимодействия со стопорами 9. Стопоры 9 подвижные в угловом направлении их установлены в пазах 10 наружного кольца 2.
На наружном кольце 2 на двух разных уровнях установлены две группы спиральных кулачков 11 и 12 с возможностью взаимодействия с соответствующими роликами 6 и 7 двуплечих рычагов 5. Спиральные кулачки 12 находящиеся в контакте с выдвижными роликами 7 выполнены с карманами 13 для размещения выдвижных роликов 7 при нейтральном положении двуплечих рычагов 5. С внутренним кольцом 3 посредством шлицев 14 связан тормозной диск 15 установленный с возможностью перемещения в осевом направлении.
В корпусе 1 выше и ниже тормозного диска 15 посредством пальцев 16 установлены фрикционные накладки 17 и 18. Верхние накладки 17 связаны с подпружиненными поршнями 19 установленными в крышке 20.
Трубовращатель бурового ключа работает следующим образом.
При свинчивании труб шестерня 21 связанная с приводом (на чертеже не показано) передает вращение наружному кольцу 2 которое начинает вращаться по часовой стрелке (фиг.1 и 2) при этом внутреннее кольцо 3 заторможено так как связанный с ним тормозной диск 15 заторможен усилием пружин поршней 19. За счет этого наружное кольцо 2 начинает поворачиваться относительно внутреннего кольца 3 при этом выдвижные ролики попадают на скосы 22 карманов 13 и при дальнейшем относительном движении ролики 7 с рычагами 5 выводятся в рабочую позицию и двигаясь далее по спиральной поверхности кулачка подводятся к трубе (на фиг. не показано). В процессе выдвижения двуплечих рычагов 5 и подвода их к трубе опорные поверхности 23 прорезей 10 наружного кольца 2 отводят стопоры 9 от фиксаторов 8 на угол зависящий от диаметра свинчиваемой трубы. В этом положении двуплечих рычагов происходит свинчивание труб. Перед их докреплением т.е. кратным увеличением крутящего момента во избежание пробуксовок захватных элементов двуплечих рычагов 5 оператор производит включение второй ступени тормоза. Это производится одновременно (от одной силовой линии) с переключением скоростей редуктора на более медленную скорость. Вторая ступень тормоза включается путем подачи рабочего агента по каналу 24 в полости подпружиненных поршней 19.
По завершении операции свинчивания и докpепления осуществляется реверс привода вращателя (на фиг. не показан) с одновременным переключением на быструю скорость (соответственно и на малый тормозной момент).
При этом рычаги с помощью спиральных кулачков 11 и отводных роликов 6 отводятся от трубы и при дальнейшем движении наружного кольца 2 в обратную сторону выдвижные ролики 7 попадают в карманы 13 что соответствует нейтральному положению двуплечих рычагов 5. Одновременно с этим (посредством упорных поверхностей 26 паза 10) стопоры 9 возвращаются в исходное положение до контакта их симметричных рабочих поверхностей 25 с шариками фиксаторов 8.
При дальнейшем совместном вращении наружного и внутреннего колец 2 и 3 (если оператор по какой-либо причине не успел остановить вращение в нужный момент) выдвижение двуплечих рычагов не происходит так как суммарный момент фиксаторов 8 больше момента первой ступени тормоза и не возникает относительного движения наружного и внутреннего колец. За счет того что шарики фиксаторов 8 подпружинены а рабочие поверхности 25 стопоров 9 скошены не возникает жесткого удара а инерция внутреннего кольца гасится пружинами фиксаторов 8.
При необходимости переключения трубовращателя на режим развинчивания наружное кольцо 2 необходимо вращать против часовой стрелки. При этом поскольку резьба трубы затянута процесс развинчивания начинается с медленной скорости (раскрепление) и при второй ступени тормозного момента. Поэтому величина второй ступени тормозного момента кратно больше момента создаваемого пружинами фиксаторов 8. Рабочие поверхности 25 стопоров 9 утапливают шарики фиксаторов 8 и выступ 27 стопора 9 переходит в зону по другую сторону фиксатора 8. При движении в этом направлении (против часовой стрелки) наружного кольца 2 происходит вывод выдвижных роликов 7 из карманов 13 скосами 28; при дальнейшем движении за счет взаимодействия выдвижных роликов 7 и спиральных кулачков 12 происходит подвод рычагов к трубе зажатие ее и раскрепление. После раскрепления развинчивание осуществляется на высокой скорости. Возврат рычагов в нейтральное положение осуществляется по ранее описанной схеме с той только разницей что выступ 27 стопора 9 подходит к шарику фиксатора 8 с противоположной стороны переместившись на величину свободного хода. Но так как угловой свободный ход стопора равен углу между двумя положениями фиксатора т.е.=(фиг.1) то взаимное положение внутреннего и наружного колец в нейтрали остается неизменным что дает возможность свести к минимуму угловой размер кармана 13 и значительно увеличить рабочую длину спиральных кулачков 12 а следовательно и увеличить диапазон диаметров труб захватываемых без перенастройки ключа. Использование предложенного трубовращателя бурового ключа позволит значительно упростить конструкцию буровых ключей повысить надежность и производительность спускоподъемных операций за счет автоматизации управления реверсированием снизить металлоемкость и повысить диапазон диаметров труб захватываемых без перенастройки ключа.
Модернизация АКБ – 3М2.
1.Техническое предложение.
Проводится модернизация ролика радильной опоры ключа АКБ – 3М2.
Рис 3.1. Ролик радиальной опоры: 1-ролик; 2-ось; 3-антифрикционная втулка; 4-упорное кольцо; 5-втулка; 6-шайба; 7-стопорное кольцо; 8- манжета; 9-гайка.
В процессе работы ролик радиальной опоры испытывает значительные нагрузки загрязнение перепады температур. При сочетании этих факторов разрушается манжета 8 нарушается герметичность ролика и грязь буровой раствор и пр. проникают в полость ролика и при вращении абразивные частицы разрушают мягкую бронзовую втулку 3 что ведет к перекосу и заеданию ролика. Со временем грязь и буровой раствор ведут к закоксовыванию ролика потере его подвижности и выходу из строя. При ремонте ключа возникают трудности при разборке и ремонте роликов. Модернизация ролика заключается в следующем: ось 2 на токарном станке точится до диаметра 25 мм а затем бронзовая втулка 3 заменяется парой роликовых подшипников: 6-205 и 60205.
2.Технология модернизации радиального ролика АКБ – 3М2.
Производится извлечение роликов с помощью проворачивания разрезной шестерни и последующего отворачивания гайки 9 и снятия шайбы 6. Затем с помощью бородка ролик аккуратно выколачивается из паза станины. Бородок следует упирать в торец оси во избежания повреждения резьбы.
Производится проверка и отбраковка роликов. В рабочем состоянии ролик должен проворачиваться от руки перекос оси относительно ролика недопустим. Поверхность ролика не должна содержать вмятин и раковин более 10% от толщины стенки ролика. При несоблюдении этих условий производится разборка и ремонт ролика.
1.Извлечение манжеты 8.
Извлекается длинногубцами.
2.Извлечение стопорного кольца.
Длинногубцами цепляются уши кольца сжимаются и извлекается кольцо 7. В случае нарушения условий эксплуатации или хранения кольцо может сильно закоксоваться в пазу или разрушиться вследствие коррозии. В этом случае паз кольца расчищается и кольцо извлекается по частям.
3.Извлечение оси и втулки.
Извлечение втулки 3 и оси 2 из ролика достаточно трудоемкая задача вследствии закоксовывания ролика сработки внутренней поверхности втулки и как следствие заклинивания. При невозможности извлечь втулку с помощью ручного инструмента применяется следующий метод:
3.1.Ролик устанавливается в вертикальном сверлильном станке. Просверливается сквозное отверстие в торце диаметром 7 мм на глубину толщины стенки( 5 мм.) чтобы не допустить повреждения оси.
3.2.Ролик устанавливается в тисках бородок вставляется в просверленное отверстие и выбивается ось 2.
3.3.В случае сильного срабатывания втулки 3 она при извлечении оси остается в корпусе. В таком случае корпус ролика устанавливается в вертикально – сверлильный станок и с двух сторон просверливаются отверстия с целью прослабления втулки.
3.4.После просверливания втулка ударами плашмя по ровной твердой поверхности легко выбивается из ролика. В случае застревания втулки допускается легкое простукивание молотком по поверхности ролика с целью дальнейшего прослабления.
3.5.В сварочном цеху запаиваются отверстия полученные в результате рассверливания.
4.Ось зажимается в тисках и с нее молотком сбивается упорное кольцо 4 и втулка 5. Не допускается зажатие поверхности оси в тиски без прокладки во избежание появления вмятин и задиров что повлечет за собой затруднение снятия кольца и втулки.
5.Ось устанавливается в токарный станок. Посадочное место под втулку точится до диаметра 25 мм и поля допуска m6(+0008 – +0021 мм).
6.На ось надеваются подшипники: 6-205 с внутренним диаметром 25 внешним диаметром 52 шириной 15 мм.; 60205 с аналогичными размерами и защитным кольцом.
7.На ось напрессовывается упорное кольцо 4 и втулка 5.
8.Ролик заполняется смазкой марки «Циатим – 201» и в него вставляется ось в сборе с подшипниками. Ролик проворачивается несколько раз в обе стороны для равномерного распределения смазки.
9.В ролик вставляется стопорное кольцо и устанавливается манжета шайба и наворачивается гайка.
Данная модернизация позволяет значительно сократить трудоемкость и время на повторную разборку опоры при последующих ремонтах особенно при ремонте ключа в полевых условиях за счет исключения этапов 2.3.1 – 2.3.5. Также увеличивается КПД ролика: КПД подшипника качения КПД подшипника скольжения. Подшипник качения имеет коэффициент трения в то время как коэффициент трения подшипника скольжения варьируется в пределах за счет чего улучшается динамика ролика. Снижается расход дорогостоящего цветного металла: стоимость пары подшипников марки 205 и 60205 равна 65 рублей стоимость втулки 3 рис. 3.1. (втулка бронзовая АКБ-3М2.12-261) – 220 рублей. Экономия времени сборки – разборки одного ролика в условиях ремонтной базы составляет 1-15 часа (основано на практических наблюдениях).
3.Прочностной расчет радиального ролика.
3.1.Построение расчетной схемы оси ролика.
При расчете на статическую прочность представим ось в виде балки на шарнирно – неподвижной опоре.
Рис. 3.2. Расчетная схема оси.
Заменим действие сил действующих на ролик соответствующими нагрузками. Вектор силы F проецируется на оси x и y. Составляющая x представляет собой вектор продольной силы N составляющая y – вектор радиальной силы R. Вектор радиальной силы R переносится в центр тяжести сечения вала по линии их действия. Вектор окружной силы Р – параллельно самой себе. Вычислим значения сил.
Вычислим сосредоточенный изгибающий момент при воздействии силы N:
Вычислим изгибающие моменты:
3.2.Построение эпюр внутренних силовых факторов:
Рис. 3.3. Эпюра продольных сил.
Рис. 3.4. Эпюра сосредоточенного изгибающего момента.
Рис. 3.5. Эпюра Крутящего момента.
Рис. 3.6. Эпюра изгибающего момента в плоскости z.
Рис. 3.7. Эпюра изгибающего момента в плоскости y.
Суммарный изгибающий момент:
Рис. 3.8. Эпюра суммарного изгибающего момента.
3.3.Проверка выбора материала оси.
Ось изготавливается из стали марки 40ХН. Для проверки выбора материала находим величины эквивалентных моментов по третье теории прочности.
Выбор материала делается из условия прочности
Вычислим осевой момент сопротивления:
Допускаемое напряжение Так как сталь 40ХН пластична то за берется предел текучести коэффициент запаса для пластических материалов Примем .
Вычисляем геометрические характеристики сечения:
- площадь поперечного сечения
- осевой момент инерции
- осевой момент сопротивления
- полярный момент инерции
- полярный момент сопротивления
Определим напряжения в опасном сечении:
- нормальное напряжение изгиба:
- нормальное напряжение от сжатия:
- максимальное касательное напряжение:
Построим эпюры этих напряжений:
Рис 3.9. Эпюра касательных напряжений изгиба и растяжения-сжатия.
В точке А имеет место плоское напряженное состояние. В этой точке действуют максимальные эквивалентные напряжения определим их по 3-ей теории прочности:
Условие прочности выполняется т.к.
Определим недогрузку оси:
Рекомендуемое значение недогрузки составляет 15% но так как при докреплении и откручивании крутящие моменты многократно возрастают такая недогрузка оправдана.
3.4.Расчет оси на усталостную прочность.
Выполним расчет оси на усталостную прочность в сечении А-А – месте ступенчатого перехода .
Выберем характеристики стали 40ХН: предел прочности МПа предел текучести МПа предел выносливости на изгиб МПа предел прочности на кручение МПа. В расчетах примем
Конструктивное исполнение опасного сечения.
Рис 3.10. Схема опасного сечения.
Основные размеры оси:
Диаметр оси d=25 мм радиус галтельного перехода r=1мм диаметр переходной канавки
Концентратор напряжений - галтельный переход 1 – 1.
В сечении А-А действуют: нормальная сила N=470 Н изгибающий момент крутящий момент Т=370 Нм.
Определим геометрические характеристики сечения и характеристики циклов перемнных напряжений.
Сечение 1-1 для диаметра d=25 мм.
-осевой момент сопротивления:
-полярный момент сопротивления:
Касательные напряжения:
3.5.Расчет коэффициента запаса усталостной прочности:
3.6.Расчет коэффициента запаса усталостной прочности. Проверка прочности.
Допускаемое значение запаса прочности принимается 15.
Эквивалетный запас прочности соответствующий плоскому напряженному состоянию вычисляется по формуле:
В сечении 1-1 условие прочности выполняется при заданном диаметре обеспечивается статическая и усталостная прочность.
3.7.Оценка вероятности безотказной работы.
Вероятность безотказной работы Р(t) определяют по экспоненциальному закону
где Р(t) - надежность ключа;
λ - интенсивность отказов 1ч;
t – время работы дней.
Задаваясь надежностью ключа = 099 определим интенсивность отказов в течение года.
λ - интенсивность отказов 1ч.;
Определим показатели и построим графики.
Функция распределения F(t).
где F(t) - функция распределения;
P(t) - вероятность безотказности работы.
Плотность распределения f(t)
где f(t) - плотность распределения;
Рис. 3.11. Функция распределения F(t) и вероятность безотказности работы P(t)
Рис. 3.12. Плотность распределения
3.8.Расчет подшипников качения на заданный ресурс.
(Характеристики подшипников качения - Легкая серия диаметров 2 узкая серия ширин 0; 205):
- Номинальный диаметр отверстия внутреннего кольца d = 25 мм;
- Номинальный диаметр наружной цилиндрической поверхности наружного кольца D = 52 мм;
- Номинальная ширина подшипника B = 15 мм;
- Диаметр тел качения Dw = 7938 мм;
- Количество тел качения z = 9 шт.;
- Угол контакта a = 10 град;
-подшипника M = 0129 кг;
- Базовая динамическая грузоподъемность Cr = 14000 Н;
- Базовая статическая грузоподъемность Cor = 6950 Н;
- Предельная частота вращения подшипника nl
- Надежность работы подшипника P1 = 90 %;
- Требуемая долговечность подшипника Lsah = 15000 ч;
Скоростные характеристики:
- Частота вращения n = 200 обмин;
- Максимальная длительно действующая радиальная нагрузка на подшипник Fr ma
- Максимальная длительно действующая осевая нагрузка на подшипник Fa ma
) Определение эквивалентной нагрузки приводя переменный режим нагружения к эквивалентному постоянному.
Режим работы - средний равновероятный.
Коэффициент эквивалентности принимается по табл. ГОСТ 21354-87 KE = 063.
Расчетная радиальная нагрузка на подшипник:
Осевая сила - полностью воспринимается подшипником.
Расчетная осевая нагрузка на подшипник:
Определяем расчетные параметры подшипника:
Режим работы подшипника - умеренные толчки; вибрационная нагрузка; кратковременные перегрузки до 150% номинальной нагрузки.
Вращающееся кольцо - внешнее.
Коэффициент вращения кольца: V =1 .
Диаметр окружности центров тел качения:
Подшипник - шариковый.
Тип подшипника - шариковый радиальный однорядный (ГОСТ 8338-75).
) Расчет динамической нагрузки на шариковый радиальный подшипник.
Коэффициент динамической осевой нагрузки.
Коэффициент динамической радиальной нагрузки.
Определим относительную осевую нагрузку:
Определим отношение осевой и радиальной сил:
Так как в ролике используется пара подшипников то будем рассматривать их как шариковый двухрядный подшипник. По таблице 64 [9] находим значение коэффициента динамической радиальной нагрузки X коэффициента динамической осевой нагрузки Y. Коэффициенты выбираются в зависимости от соотношения
Режим работы подшипника - умеренные толчки; вибрационная нагрузка; кратковременные перегрузки до 150% номинальной нагрузки значит
Условия применения подшипника - обычные (материал обычной плавки) наличие перекосов колец отсутствие надежной гидродинамической пленки масла наличие в нем инородных частиц.
Коэффициент характеризующий совместное влияние на ресурс особых свойств подшипника и условий его эксплуатации принимается по табл. 70 [9] a23 = 08 .
Коэффициент корректирующий ресурс в зависимости от надежности принимается по табл. 68 [9] в зависимости от P1 a1 = 1 .
Долговечность подшипника:
- долговечность подшипника составляет 124% от требуемой условие выполнено.
В курсовом проекте был рассмотрен буровой ключ АКБ – 3М2 его составные части их краткое описание и принцип действия. Был проведен патентно – информационный обзор в ходе которого были рассмотрены 4 варианта исполнения буровых ключей. особый акцент был сделан на трубозажимных устройствах узла подлежащего модернизации; на основе патентного обзора и изучении руководства по эксплуатации АКБ – 3М было сделано техническое предложение по модернизации одного из узлов ключа: ролика радиальной опоры приведена технология ремонта и модернизации ролика. Расчеты показывают что приведенная модернизация имеет достаточный запас статической усталостной прочности ресурс и долговечность.
Данная технология ремонта осевой опоры ключа АКБ - 3М2 с последующей модернизацией позволяет:
улучшить динамические характеристики ключа;
улучшить сохраняемость ключа.
снизить стоимость время и трудоемкость ремонта
Список использованной литературы:
ГОСТ 21354 - 87. Передачи зубчатые цилиндрические эвольвентного внешнего зацепления. Расчет на прочность
ГОСТ 8338 – 75. Подшипники шариковые радиальные однорядные. Основные размеры.
Автоматический буровой ключ для свинчивания-развинчивания бурильных и обсадных труб. А.Е. Анашкина М.Б. Грушевский: Методическое пособие. Тюмень: Издательство “Нефтегазовый университет” 2003. – 33 с.
Бурение нефтяных и газовых скважин: учебник для нач. проф.образования Ю.В. Вадецкий. - М.Издательский центр «Академия» 2003.- 352с.
Буровое оборудование. В.Ф. Абубакиров В.Л. Архангельский Ю.Г. Буримов И.Б. Малкин А.О. Межлумов Е.П. Мороз: Справочник: В 2 – х т. – М.: Недра 2000. – Б 91 Т.1. 000с.: ил.
Диагностика и восстановление нефтепромыслового оборудования. Д.О. Макушкин. Учеб. Пособие Д.О. Макушкин. Красноярск: ИПЦ КГТУ 2002. 142 с.Красноярск: Сиб. Федер. ун-т 2008. – 164 с.
Конструирование узлов и деталей машин: учеб. пособие для техн. спец. вузов. – 5-е изд. перераб. и доп. П.Ф. Дунаев О.П. Леликов – М.: Высш. шк. 1998. – 447 с. ил.
Материаловедение и технология конструкционных материалов С. Н. Колесов И. С. Колесов. М:. Высшая школа. 2004 г.
Расчет валов на статическую усталостную прочность и жесткость: Учебное пособие. В.С. Жернаков В.С. Куликов Т.Н. Мардимасова; Уфимск. Гос. Авиац. Тех. Ун-т. – Уфа: УГАТУ 2003 г. 76с.
Рекомендуемые чертежи
Свободное скачивание на сегодня
- 23.08.2014