Модернизация привода главного движения токарно-револьверного автомата мод. 1Б125



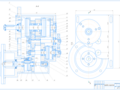
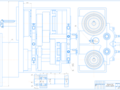
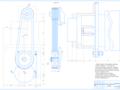
- Добавлен: 25.01.2023
- Размер: 2 MB
- Закачек: 1
Описание
Состав проекта
![]() |
![]() ![]() ![]() |
![]() |
![]() ![]() ![]() ![]() |
![]() ![]() ![]() ![]() |
![]() ![]() ![]() ![]() |
![]() ![]() ![]() |
Дополнительная информация
Титул.doc
ГОСУДАРСТВЕННОЕ ОБРАЗОВАТЕЛЬНОЕ УЧРЕЖДЕНИЕ
ВЫСШЕГО ПРОФЕССИОНАЛЬНОГО ОБРАЗОВАНИЯ
Донской государственный технический университет
ПОЯСНИТЕЛЬНАЯ ЗАПИСКА
к курсовому проекту
«Металлорежущие станки»
« Модернизация привода коробки скоростей токарно-револьверного станка мод. 1Б125»
Руководитель: ст.преп. к.т.н.
развёртка-свёртра.cdw

внешний.cdw

система натяжения.cdw

Усилие для проверки натяжения клинового
ремня коробки скоростей должно составлять
для нового ремня Q=20-30Н. Прогиб по центру
должен составлять 10
Ремни поставляемые со станком
комплектовать по группам. Наибольшая
разность между длинами ремней одной группы
не должна превышать 5мм.
КУРСОВОЙ ПРОЕКТ 1Б125.doc
Полуавтоматом называется автоматический станок в котором часть движений автоматизирована. В большинстве случаев это движения связанные с загрузкой и снятием заготовок.
Токарные станки и полуавтоматы применяют для обработки деталей сложной конфигурации с помощью большого количества инструментов. Они подразделяются: по назначению — на универсальные и специализированные; по виду заготовки — на прутковые и патронные; по количеству шпинделей — на одношпиндельные и многошпиндельные; по расположению шпинделей — на горизонтальные и вертикальные.
Из автоматов и полуавтоматов наибольшее распространение получили станки с кулачковым приводом. Автоматическое управление циклом этих станков осуществляется с помощью распределительного (кулачкового) вала. Обычно за один оборот вала происходит полный цикл обработки детали.
Автоматы можно разделить на три группы. Первая группа — автоматы имеющие один распределительный вал вращающийся с постоянной для данной настройки частотой. Вал управляет как рабочими так и вспомогательными движениями. Для автоматов этой группы характерна большая потеря времени при вспомогательных движениях так как они выполняются при той же (медленной) частоте вращения распределительного вала что и рабочие операции. Однако в автоматах малых размеров с небольшим количеством холостых движений применение такой схемы целесообразно вследствие ее простоты.
Вторая группа — автоматы с одним распределительным валом которому в течение цикла сообщаются две частоты вращения: малая при рабочих и большая при холостых операциях. Такая схема обычно применяется в многошпиндельных токарных автоматах и полуавтоматах.
Третья группа — автоматы имеющие кроме распределительного вала еще и быстроходный вспомогательный вал осуществляющий холостые движения. Команды на выполнение холостых движений подаются распределительным валом с помощью закрепленных на нем специальных барабанов с упорами.
Анализ кинематики станка прототипа.
Основные понятия о приводе.
Совокупность устройств приводящих в действие рабочие органы металлорежущих станков называют приводом. Он состоит из двигателя и механизмов передающих движение рабочим органам. Для приводов металлорежущих станков применяют обычно односкоростные асинхронные электродвигатели переменного тока с короткозамкнутым ротором с синхронной частотой вращения. Обладая жесткой характеристикой эти двигатели обеспечивают постоянство мощности во всём диапазоне скоростей и незначительное изменение частоты вращения вала под нагрузкой.
Как правило вал электродвигателя и ведущий вал привода связаны соединительной муфтой либо одной из передач – ременной или зубчатой. Движение инструмента и заготовок совершается рабочими или исполнительными органами станка. Движение передаётся при помощи кинематических цепей состоящих из отдельных пар. Изображение кинематических пар соединённых в определённой последовательности в кинематические цепи называется кинематической схемой.
Количество кинематических групп из которых слагается кинематическая структура станка соответствует количеству относительных движений между заготовкой и режущим инструментом осуществляющих при обработке процессы врезания формообразования и деления.
1 Фактический ряд станка 1Б125 и его погрешности.
Составление уравнений кинематического баланса и определение погрешности фактического ряда.
2 Построение и анализ структурной сетки
он строится как полулогарифмическая сетка
жирная точка на вертикальной линии означает частоту вращения (положение частоты данного вала на числовой оси);
линия соединяющая точки на вертикальных линиях валов обозначает передачу;
несколько параллельных линий между двумя валами обозначают одну и туже передачу;
если из одной точки на ведущем валу выходят несколько линий то это множительная группа в которой столько передач сколько линий выходит из этой точки.
Представленные на графике группы отличаются числом интервалов между точками на ведомом валу то есть количество интервалов – это характеристика группы.
Характеристика – это показатель степени в которую надо возвести знаменатель ряда j чтобы получить соответствующую величину.
А – количество интервалов на которое поднимается (опускается) линия изображающая соответствующую передачу.
Для данной структурной сетки знаменатель ряда будет равен:
Нормальные ряды чисел в станкостроении для знаменателя ряда j =1.26
Максимально допустимое отклонение чисел оборотов шпинделя
-(j -1)*10%=W=(j -1)*10%
поле рассеивания 52%
Определим отклонение каждого рассчитанного числа оборотов шпинделя от принятого и сравним с допустимым отклонением.
W1=18 % W2=4% W3=05% W4=05% W5=14% W6=3%
W7=25% W8=41% W9=022% W10=375% W11=54% W12=48%
W13=2% W14=19% W15=24% W16=5% W17=095% W18=71%
Анализ погрешности ряда показывает что семь значений превышают допустимое отклонение (W2W6W8W10W11W12W16W18). Поле рассеивания погрешностей также превышает допустимое поле рассеивания (5.4 %>52%).
Анализ фактического ряда обеспечиваемого приводом главного движения токарно-револьверного станка показывает:
Структура не является нормальной следовательно необходимо её улучшение;
предельные отклонения погрешности ряда не укладываются в норматив отраслевого стандарта: положительное отклонение равно 54% вместо допускаемого 26% ;
по полю рассеивания погрешностной норматив также не выполняется (допустимо 52% а имеем 5.4%);
3 Задачи модернизации
Таким образом в задачу модернизации можно включить необходимость улучшения структуры по средствам:
перерасчёт чисел зубьев;
уменьшения числа сменных шестерён;
в системе передач имеется «связанная» шестерня (реверс) оценить ее влияние на структуру и последующий выбор электродвигателя.
1 Выбор режимов резания.
Необходимым условием для установления режима резания является наличие разработанного технологического процесса по операциям и переходам а также паспортных данных станков.
Назначение рационального режима резания заключается главным образом в выборе наиболее выгодного сочетания скорости резания и подачи обеспечивающих в данных условиях с учетом целесообразного использования режущих свойств инструмента и кинематических возможностей оборудования наибольшую производительность общественного труда и наименьшую стоимость операции.
Для уменьшения машинного времени следует применять воз можно большие технологически допустимые подачи и соответствующие им скорости резания. При этом должны быть наиболее полно использованы режущая способность инструмента и его прочность динамические возможности станка при соблюдении технических условий на изготовление детали.
Диаметр из соотношения:
Материал заготовки А12
Резцы с пластинками из твердого сплава Т5К10
Подача S в ммоб до 054
Глубина резания t мм –до 2
Окружная скорость ммин – 188
Мощность резания кВт – до 31
Подача S в ммоб до 05
Окружная скорость ммин – 230
Мощность резания кВт – до 2
Окружная скорость ммин – 167
Мощность резания кВт – 29
Материал заготовки А12
Диаметр сверла мм -20-25
Подача S в ммоб до 049-058
Глубина резания t мм –15-6
Окружная скорость ммин – 30-50
Мощность резания кВт – 03-11
Диаметр зенкера мм - 20-25
Подача S в ммоб до 07-09
Глубина резания t мм –до 03-05
Окружная скорость ммин – 20
Мощность резания кВт – 07-.09
Диаметр развертки мм – 20-25
Подача S в ммоб до 015-15
Глубина резания t мм –до 025-01
Окружная скорость ммин – 10-15
Мощность резания кВт – 025
Нарезание резьбы круглыми плашками
Режущий инструмент из стали 9хс
Диаметр резьбы мм – М12
Шаг резьбы S ммоб 175
Окружная скорость ммин – 285
Мощность резания кВт – 023
Скорость вращения шпинделя n обмин 76
По наибольшей мощности резания – 36 кВт (Карта №25) и КПД коробки скоростей определяем мощность электродвигателя:
2 Подбор электродвигателя
По потребной мощности выбираем трехскоростной асинхронный электродвигатель со следующими характеристиками:
АИР132 М842 по ГОСТу 13859-68
Чистота вращения 75015003000 обмин
Трехфазные короткозамкнутые асинхронные электродвигатели общего назначения серии А2 с основным исполнением на напряжение 380В предназначены для продолжительного номинального режима от сети с частотой 50Гц.
3 Построение и анализ модернизированного графика частот вращения.
Трехскоростной электродвигатель можно условно рассматривать как «электрическую группу» состоящую из трех передач. Характеристика группы может быть найдена исходя из следующих рассуждений. Поскольку скорость вращения шпинделя при переключении электродвигателя с меньшей частотой вращения на большую увеличивается в двое ()то характеристика .
Для получения нормальной структуры привода без перекрытия частот вращения необходимо выбирать такую структуру коробки скоростей при которой=2. Поэтому от выбранного значения знаменателя ряда будет зависеть структурная сетка. При расчете это не всегда удается выполнить и может иметь место совпадение скоростей.
Структурная сетка модернизированного станка 1Б125
4 Определение мощности и крутящих моментов на валах.
Расчет мощностей на валах.
Мощность на II валу:
Мощность на III валу:
Мощность на IV валу:
Определение крутящих моментов передаваемых валами:
Для расчетной ступени.
Крутящий момент на I валу:
Крутящий момент на II валу:
Крутящий момент на III валу:
Крутящий момент на IV валу:
Электромагнитные фрикционные муфты являются важнейшим средством автоматизации позволяющим создавать коробки передач допускающие переключение на ходу переключение на ходу с дистанционным управлением. 0тралевым руководящим материалом предусмотрено три исполнения электромагнитных муфт: бесконтактное (с неподвижной катушкой и вращающимся магнитопроводом) контактное (с токоподводящим кольцом и передачей тока через специальную щетку) тормозные (с неподвижным статором присоединяемым к корпусу).
Бесконтактные электромагнитные муфты избавлены от таких недостатков контактных муфт как искрение в щетках потери энергии на трение износ щеток и контактного кольца. Применяются в тех случаях когда можно обеспечить надежное закрепление и центрование статора в корпусе а также точную регулировку зазора между статором и вращающимся магнитопроводом.
В связи с тем что коэффициент трения в пoкoe значительно больше чем при скольжении муфта при полном сцеплении дисков передает значительно больший момент чем при их пробуксовке. Поэтому если нагрузка превысит момент соответствующий полному сцеплению дисков и начинается их относительное скольжение с обильным выделением тепла муфта самостоятельно (без снятия нагрузки) не сможет вернуться в первоначальное состояние и выйдет из строя из-за перегрева. Поэтому при силовом расчете привода необходимо предусматривать защиту муфт от перегрузки путем введения элемента передающего момент заведомо меньший чем муфта при скольжении между дисками. Лучше если предохранение муфт от перегрузки будет осуществляться не разрушающимися или хорошо защищенным элементом (ременная передача электродвигатель) Основными особенностями коробок передач на электромагнитных муфтах являются:
- повышенный уровень шума обусловленный тем что все зубчатые колеса в зацеплении находятся постоянно;
- увеличенные межосевые расстояния определяемые не силовыми возможностями зубчатых колес а габаритными размерами используемых муфт. Поэтому особое внимание при проектировании должно уделяться:
- правильному расположению электромагнитных муфт на валах (главное чтобы муфты на соседних валах не располагались друг против друга); уменьшению количества зубчатых передач за счет использования многоскоростных электродвигателей сменных элементов замены зубчатых передач ременными; уменьшению шума за счет снижения окружных скоростей зубчатых колес (до значений 3-5 мс) и замены обычных переборов планетарными.
Основное отличие силового расчета коробок передач с электромагнитными муфтами от обычных (с переключаемыми блоками) заключается в том что после определения крутящих моментов на валах по ним выбираются тип и габарит муфт место их установки и с учетом этого - межосевые расстояние. Модули зубчатых колес ориентировочно определяются по известному межосевому расстоянию и сумме чисел зубьев колес принимается по стандарту и проверяются силовым расчетом (на допустимость действующих напряжений).
Конструкция электромагнитных муфт показаны на рисунке а основные параметры и геометрические размеры в таблице.
Выбираем муфты электромагнитные бесконтактные по моменту на валу.
6 Расчет числа зубьев
В связи с тем что ряд не является стандартным и по технологическим показателям (необходимостью иметь больший диапазон скоростей) изменим структурную схему на
Эта замена позволит правильнее подбирать режимы резания для обработки различных материалов. Удорожание конструкции окупится ростом производительности труда за счет оптимизации режимов резания.
Структурная схема имеет следующий вид:
Рассчитаем число зубьев шестерен и зубчатых колес по формуле:
Рассчитаем действительные значения чисел оборотов и отклонения от стандартных значений по формулам:
7 Анализ модернизированного станка. (1Б125)
Структурная схема имеет следующий вид
Определим отклонение каждого рассчитанного числа оборотов шпинделя от принятого и сравним с данным Нормальные ряды чисел в станкостроении для знаменателя ряда j =1.26
Выбираем из стандартного ряда со знаменателем φ=126 следующие значения n:
W1=-09 %; W2=-175%; W3=068%; W4= 056%; W5=-175%; W6=-175%;
W7=-175%; W8=-015%; W9=-175%; W10=-175%; W11=-03%; W12=-176%;
W13=-175%; W14=-156%; W15=-176%; W16=-175%; W17=-175%; W18=-25%;
W19=-175; W20=-175; W21=-25.
Анализ погрешности ряда показывает что все значений попадают в допуски. Поле рассеивания погрешностей также попадет в допустимое поле рассеивания (19 %52%).
Анализ фактического ряда обеспечиваемого приводом главного движения горизонтально-фрезерного станка показывает:
фактический ряд близок к геометрическому в нём отсутствуют наложения и пропуски;
предельные отклонения погрешности ряда укладываются в норматив отраслевого стандарта: положительное отклонение равно 06 отрицательное равно 25% допускаемого 26% ;
по полю рассеивания погрешностной норматив также выполняется (допустимо 52%)
в системе передач имеется «связанная» шестерня.
сокращено количество сменных шестерён.
1Расчет зубчатых колес
Выбор материала и термообработки:
Допускаемые контактные напряжения при расчете
где - предел контактной выносливости соответствующий эквивалентному числу циклов перемен напряжений - коэффициент безопасности (=12) -коэффициент учитывающий шероховатость рабочих поверхностей (=1) -коэффициент учитывающий влияние окружающей среды (=1).
Для колёс закалённых коэффициент долговечности КHL находится в пределах
принимаем КHL равным 1
-предел контактной выносливости соответствующий базовому числу циклов перемен напряжений МПа.
Допускаемое контактное напряжение:
Проверочный расчет зубчатых передач на изгиб
определяются по выражению
где - предел выносливости зубьев при изгибе соответствующий эквивалентному числу циклов перемен напряжений =185 - коэффициент безопасности (поковка) - коэффициент учитывающий шероховатость рабочих поверхностей зубьев - коэффициент учитывающий чувствительность материала к концентрации напряжений.
Предел выносливости зубьев
кFL–коэффициент долговечности примем равным 18 где - предел выносливости зубьев при изгибе соответствующий базовому числу циклов переменного напряжения МПа.
Допускаемые напряжения на изгиб колеса и шестерни:
Конструирование зубчатых передач
Конструирование закрытой цилиндрической передачи .
Основной причиной выхода из строя зубчатых колес является повреждение зубчатых венцов. Целью проводимых расчетов является предотвращение выходов из строя из-за поломок зубьев и выкрашивания их активных поверхностей в результате развития усталостных трещин.
Определение основных коэффициентов для расчета передачи
Вспомогательный коэффициент определяется по вспомогательному параметру который отражает зависимость рабочей ширины зацепления относительно диаметра шестерни тогда
Вспомогательный параметр
Вспомогательный коэффициент определяется в зависимости от вида передачи. Для прямозубой передачи .
Коэффициент распределения нагрузки между зубьями при прямозубой передаче .
Коэффициент неравномерности нагрузки по ширине венца
Коэффициент динамической нагрузки. Для передач 8 степени точности рекомендуется принимать для прямозубой передачи
Определение основных параметров передачи.
Межосевое расстояние первой пары:
Межосевое расстояние второй пары:
Межосевое расстояние третей пары:
Определим контактные напряжения при действии максимальной нагрузки по формуле:
где – максимальный пусковой момент из графика нагрузки .
Допускаемое контактное напряжение при действии максимальной нагрузки
Проверим выполнение условия: – условие выполняется.
Принимаем угол наклона зубьев .
Модуль первой передачи
Принимаем по ГОСТ 9563-60 m=225;
Модуль второй передачи
Модуль третей передачи
Принимаем по ГОСТ 9563-60 m=25;
Рабочая ширина зацепления:
Проверим зубья для предотвращения усталостного излома. Определим коэффициент формы зуба .
Выбираем коэффициенты формы зуба: .
Коэффициент учитывающий угол наклона зубьев
Определяем наиболее слабый элемент передачи по минимальному соотношению:
Наиболее слабым элементом передачи является шестерня № 3.
Для наиболее слабого звена определяем напряжения изгиба действующего в ножке зуба:
Проведем сравнение - условие выполняется.
Проведем проверочный расчет для предотвращения остаточной деформации или хрупкого излома при действии максимальной нагрузки. Определим максимальное допускаемое напряжение по изгибу:
где - предельное напряжение не вызывающее остаточных деформаций и хрупкого излома МПа. = при закалке. - коэффициент безопасности при закалке.
Наиболее слабый элемент передачи:
Наиболее слабым элементом является шестерня № 3 .
Максимальное напряжение по изгибу при действии максимальной нагрузки :
Проведем сравнение: - условие выполняется.
Основные геометрические размеры зубчатой пары:
Ширину шестерён принимаем:
b1= b2=42; b3= b4=14; b5= b6=58; b7= b8=48; b9= b10=43;
b11= b12=79; b13= b14=53.
диаметры делительных окружностей:
диаметры вершин зубьев:
диаметры окружностей впадин:
Силы действующие в зацеплении для расчетной ступени:
где - угол зацепления угол наклона зубьев.
Так как угол наклона зубьев =0 то осевые силы отсутствуют.
Расчеты заносим в таблицу:
A межосевое расстояние
b ширина зацепления; принемаем
Результаты расчета валов на компьютере:
Данные о нагруженности вала
Горизонтальная сост.
Нагрузочные характеристики сечений вала
Х1Л= 10 Х1П= 10 Х2Л= 210 Х2П= 210 ХЗЛ= 308 ХЗП= 308 Х4Л= 352
Горизонтальная сост. Вертикальная сост. Суммарная реакция
Х1Л= 10 Х1П= 10 Х2Л= 172 Х2П= 172 ХЗЛ= 308 ХЗП= 308 Х4Л= 354
Х1Л= 66 Х1П= 66 Х2Л= 128 Х2П= 128 ХЗЛ= 290 ХЗП= 290 Х4Л= 426
3 Расчет подшипников качения.
Исходные данные Вал 1.
Rmax=858H d=20мм F=0
Принимаем подшипник радиальный шарикоподшипник по ГОСТу 8338-57 № 204 с характеристиками:
d=20мм D=47мм B=14мм [C]=15000H [C0]=6000H
Приведенная нагрузка
=1-коэффицент вращения кольца
=1.2- коэффициент безопасности
=1.05-температурный коэффициент
Долговечность подшипника
Где -потребный ресурс в часах
Динамическая грузоподъёмность
Принимаем конструктивно из ГОСТ 8338-57 №204
Исходные данные Вал 23.
Rmax=1441H d=30мм F=0
Принимаем подшипник радиальный шарикоподшипник по ГОСТу 8338-57 № 206 с характеристиками:
d=30мм D=62мм B=16мм [C]=19500H [C0]=10000H
Принимаем конструктивно из ГОСТ 8338-57 подшипник 206
Исходные данные Вал 4.
Rmax=2371H d=40мм F=0
Принимаем подшипник радиальный шарикоподшипник по ГОСТу 8338-57 № 208 с характеристиками:
d=40мм D=80мм B=18мм [C]= 32000H [C0]=17800H
Принимаем конструктивно из ГОСТ 8338-75 №208.
Расчет шпонок производим на смятие:
где Т– наибольший крутящий момент
Шпонка по ГОСТ 23360-78
Проверка 8690 – шпонки подобраны правильно.
По крутящему моменту выбираем клиновый ремень нормального сечения А.
Ориентировочное значение межосевого расстояния
Ориентировочное значение длины ремня
Принимаем L = 1400мм
Точное значение межосевого расстояния:
Число пробегов ремня в секунду
Угол обхвата ремнем малого шкива
Окружная сила на шкивах:
Ориентировочное число клиновых ремней:
γ –частота пробегов ремня;
–ширина ремня по нейтральному слою
–коэффициент влияния передаточного числа;
–коэффициент учитывающий влияние угла обхвата на тяговую способность;
–коэффициент режима работы.
Действительное число ремней с учетом неравномерности распределения нагрузки между ремнями:
Правильный метод смазочных материалов своевременная и качественная смазка узлов оборудования является одним из основных условий позволяющих увеличить долговечность повысить работоспособность и сохранить на длительный период технологическую точность проектируемой коробки подач. Образцовая организация смазочного хозяйства и рациональная смазка уменьшают износ деталей оборудования удешевляют их ремонт сокращают простой и способствуют снижению себестоимости выпускаемой продукции.
Смазка трущихся поверхностей станков устраняет их непосредственный контакт благодаря чему значительно уменьшается сила трения что способствует минимизации износа поверхностей контактирующих друг с другом деталей в следствии трения.
В качестве смазочных материалов в станках применяют жидкие минеральные масла и пластичные консистентные смазки. Преимущественное распространение получили масла наиболее предпочтительны для смазки отечественных быстроходных сопряжений и позволяющих осуществить централизованную смазку.
Выбор смазки для станков неоднозначно очевиден. Сложность в том что станки имеют различные пары трения работающие при различных скоростях и нагрузках. Применение различных смазок предпочтительных в каждом отдельном случае неоправданно усложнило бы конструкцию смазочной системы в целом и затруднило бы эксплуатацию такого станка.
Для обеспечения смазки узлов станка предлагаю использовать централизованную систему смазки общую для всех узлов и механизмов. В случае ее использования система смазки коробки подач непосредственно подключается к общей нагнетательной и сливной системы. Централизованная общая система имеет ряд преимуществ среди которых:
легкость обслуживания и контроля;
дешевизна конструкции отдельных узлов системы смазки;
простота регулирования и наладки;
наличие системы аварийной сигнализации;
общий электропривод насоса.
Рекомендуемые чертежи
- 16.11.2023
- 25.10.2022
- 25.01.2023