Модернизация коксового конвейера в агломерационном цеху ОАОНЗФ




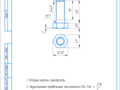
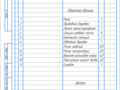
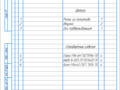
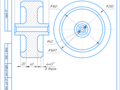
- Добавлен: 24.01.2023
- Размер: 1 MB
- Закачек: 0
Описание
Модернизация коксового конвейера в агломерационном цеху ОАОНЗФ
Состав проекта
![]() |
![]() |
![]() ![]() ![]() ![]() |
![]() ![]() ![]() ![]() |
![]() ![]() ![]() |
![]() ![]() ![]() |
![]() ![]() ![]() ![]() |
![]() ![]() ![]() ![]() |
![]() ![]() ![]() ![]() |
![]() ![]() ![]() ![]() |
![]() ![]() ![]() ![]() |
![]() ![]() ![]() |
Дополнительная информация
Роликоопора модерн..spw

Болт40.cdw

Втулка.cdw

Каток.cdw

Кокс . конвеер.spw

Опора.cdw

Конвейерcdw.cdw

Рекомендуемые чертежи
- 25.01.2023
- 17.05.2023
- 17.05.2023
- 17.05.2023
- 15.04.2024