Механизм угла




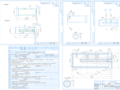
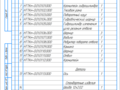
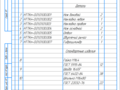
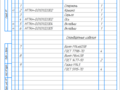
- Добавлен: 24.01.2023
- Размер: 87 MB
- Закачек: 0
Описание
Механизм угла
Состав проекта
![]() |
![]() |
![]() |
![]() |
![]() ![]() ![]() |
![]() |
![]() ![]() ![]() |
![]() |
![]() ![]() ![]() |
![]() ![]() ![]() |
![]() ![]() ![]() |
![]() ![]() ![]() |
![]() ![]() ![]() |
![]() ![]() ![]() |
![]() ![]() ![]() |
![]() |
![]() ![]() ![]() |
![]() |
![]() |
![]() |
![]() |
![]() |
![]() |
![]() |
![]() |
![]() |
![]() |
![]() |
![]() |
![]() |
![]() |
![]() |
![]() |
![]() |
![]() |
![]() |
![]() |
![]() |
![]() |
![]() |
![]() |
![]() |
![]() |
![]() |
![]() |
![]() |
![]() |
![]() |
![]() |
![]() ![]() ![]() |
![]() |
![]() |
![]() ![]() ![]() |
![]() ![]() ![]() |
![]() ![]() ![]() |
![]() ![]() ![]() |
![]() ![]() ![]() |
![]() ![]() ![]() |
![]() ![]() ![]() |
![]() ![]() ![]() |
![]() ![]() ![]() |
![]() ![]() ![]() |
![]() |
![]() |
![]() ![]() ![]() |
![]() ![]() ![]() |
![]() ![]() ![]() |
![]() ![]() ![]() |
![]() ![]() ![]() |
![]() ![]() ![]() |
![]() ![]() ![]() |
![]() ![]() ![]() |
![]() ![]() ![]() |
![]() ![]() ![]() |
![]() ![]() ![]() |
![]() ![]() ![]() |
![]() |
![]() ![]() ![]() |
![]() ![]() ![]() |
![]() |
![]() |
![]() ![]() ![]() |
![]() ![]() ![]() |
![]() ![]() ![]() |
![]() ![]() ![]() |
![]() ![]() ![]() |
![]() ![]() ![]() |
![]() ![]() ![]() |
![]() ![]() ![]() |
![]() |
![]() |
![]() ![]() ![]() |
![]() ![]() ![]() |
![]() ![]() ![]() |
![]() ![]() ![]() |
![]() |
![]() ![]() ![]() |
![]() |
![]() ![]() ![]() |
![]() |
![]() ![]() ![]() |
![]() ![]() ![]() |
![]() |
![]() ![]() ![]() |
![]() ![]() |
![]() |
![]() |
![]() ![]() ![]() ![]() |
![]() ![]() ![]() ![]() |
![]() ![]() ![]() ![]() |
![]() ![]() ![]() ![]() |
![]() ![]() ![]() ![]() |
![]() ![]() ![]() ![]() |
![]() ![]() ![]() ![]() |
![]() ![]() ![]() ![]() |
![]() |
![]() ![]() ![]() ![]() |
![]() |
![]() |
![]() |
![]() |
![]() ![]() ![]() ![]() |
![]() |
![]() |
![]() |
![]() |
![]() |
![]() |
![]() ![]() ![]() ![]() |
![]() ![]() ![]() ![]() |
![]() ![]() ![]() ![]() |
![]() ![]() ![]() ![]() |
![]() ![]() ![]() ![]() |
![]() ![]() ![]() ![]() |
![]() ![]() ![]() ![]() |
![]() ![]() ![]() ![]() |
![]() |
![]() |
![]() ![]() ![]() |
![]() |
![]() |
![]() |
![]() |
![]() |
![]() |
![]() |
![]() |
![]() |
![]() |
![]() |
![]() |
![]() |
![]() |
![]() |
![]() |
![]() |
![]() |
![]() |
![]() |
![]() |
![]() |
![]() |
![]() |
![]() |
![]() |
![]() |
![]() |
![]() |
![]() |
![]() |
![]() |
![]() |
![]() |
![]() |
![]() |
![]() |
![]() |
![]() |
![]() |
![]() |
![]() |
![]() |
![]() |
![]() |
![]() |
![]() |
![]() |
![]() |
![]() |
![]() |
![]() |
![]() |
![]() |
![]() |
![]() |
![]() |
![]() |
![]() |
![]() |
Дополнительная информация
7.Охрана труда.doc
1 Размещение органов управления машиной
Характеризуя условия использования машины устанавливают климатическую зону ее эксплуатации. Данный автогрейдер обычного исполнения предназначенный для районов с умеренным климатом (температура воздуха от -40 до 35 С относительная влажность 60 95%). Одновременно с разработкой узлов и систем машины на начальной стадии проектирования следует обеспечить безвредные и безопасные условия труда обслуживающего персонала.
Обзорность рабочей площадки из кабины оператора определяется конструкцией самой кабины местоположением относительно рабочих органов.
Рисунок 7.1 - Размещение органов управления машиной
- зона очень часто используемых и важных объектов;23- зоны часто и редко используемых объектов.
Хорошая обзорность не вызывает дополнительных движений обеспечивает удобство позы. Это повышает производительность и безопасность труда понижает утомляемость. Проектируя машину на специальном шасси местоположение кабины устанавливают из условия наилучшей обзорности. На основании рекомендаций инженерной психологии эргономике и результатов исследований расположение наиболее часто используемых органов управления назначают в соответствии с данными. Высота кабины автогрейдера должна позволять оператору работать стоя.
Выявляются уровни потенциальных вредностей и опасностей. Рассмотрим такие вредные факторы: шум вибрацию санитарно-гигиенические требования к воздуху рабочей зоны нормы выбросов вредных веществ и дымности отработавших газов.
2 Влияние шума на работу оператора
Шум - это совокупность звуков неблагоприятно воздействующих на человека мешающих его работе и отдыху. ГОСТ 12.1.003-83
Воздействие шума на человека может проявляться не только в виде специфического поражения органа слуха но и неблагоприятно воздействовать на многие другие органы и функции организма.
У лиц подвергающихся действию шума отмечаются изменения секреторной и моторной функций желудочно-кишечного тракта скорости дыхания и пульса возникновение сердечно-сосудистых заболеваний гипертонической болезни сдвиги в обменных процессах (нарушение основного витаминного углеводного белкового жирового солевого обменов). Шум с уровнем звукового давления 30 35 дБ является привычным для человека и не беспокоит его. Повышение уровня звукового давления до 40 70 дБ создает значительную нагрузку на нервную систему вызывая ухудшение самочувствия снижение производительности умственного труда а при длительном действии может явиться причиной невроза язвенной и гипертонической болезни.
Источники шума в автогрейдерах двигатели компрессоры коробки передач раздаточные коробки агрегаты гидропривода. Уровень интенсивности основного источника шума – двигателя равен 105 115 дБ для компрессоров и воздуходувок порядка 100 дБ для вибраторов – 105 110 дБ. В кабину шум проникает через воздушную среду через металлоконструкции при жестком креплении к ним источников шума и кабины. Эти конструкции могут усиливать действие первичных источников за счет резонирования отдельных элементов конструкций и стенок ограждений (капот стенки кабины приборные щитки) ненадежном креплении агрегатов к раме.
Допустимые уровни звукового давления в октановых полосах частот уровни звука и эквивалентные уровни звука на рабочих местах следует принимать: для широкополосного постоянного и непостоянного (кроме импульсного) шума – по таблице 7.1.
Снижение механического шума возникающего вследствие вибрации поверхностей машин и оборудования а также одиночных или периодических ударов сочленении деталей сборочных единиц или конструкций в целом достигается улучшением конструкции оборудования. Заменой по возможности зубчатых и цепных передач клиноременными и зубчато-ременными (снижение шума на 10—14 дБ); заменой подшипников качения на подшипники скольжения (снижение шума на 10—15 дБ); использованием металлов с большим внутренним трением; заменой где это возможно металлических деталей и
Таблица 7.1 Допустимые уровни звукового давления в октановых полосах частот.
Вид трудовой деятельности рабочие места
Уровни звукового давления дБ в октановых полосах со среднегеометрическими частотами Гц
Уровни звука и эквивалентные уровни звука дБ А
Рабочие места водителей и обслуживающего персонала тракторов самоходных шасси строительно-дорожных и др. аналогичных машин
деталями из пластмасс. Эффективно (особенно для высоких тонов) применение демпфирования при котором колеблющаяся поверхность покрывается материалом с большим внутренним трением (резина пробка битум войлок и др.). Основными требованиями предъявляемыми к демпфирующим материалам должны быть высокая эффективность малая масса способность прочно удерживаться на металле и предохранять его от коррозии.
Вибрация – это механические колебания воспринимаемые человеком как сотрясение ГОСТ 12.1.012-2004.
Колебания механических тел с частотой ниже 20 Гц воспринимаются организмом как вибрация а колебания с частотой выше 20 Гц — одновременно и как вибрация и как звук. В настоящее время на многих производствах вибрация является одним из наиболее распространенных вредных факторов воздействующих на работающих.
По способу передачи на человека вибрацию подразделяют:
- общая вибрация передающаяся через опорные поверхности на тело сидящего или стоящего человека;
- локальная вибрация передающаяся через руки человека на ноги сидящего человека и на предплечья контактирующие с вибрирующими поверхностями рабочих столов.
По источнику возникновения общая вибрация бывает:
категории — транспортная вибрация воздействующая на человека на рабочих местах самоходных и прицепных машин транспортных средств при движении по местности и дорогам (в том числе при их строительстве);
категории — транспортно-технологическая вибрация воздействующая на человека на рабочих местах машин перемещающихся по специально подготовленным поверхностям производственных помещений промышленных площадок;
категории — технологическая вибрация воздействующая на человека на рабочих местах стационарных машин или передающаяся на рабочие места не имеющие источников вибрации.
На оператора автогрейдера воздействует общая вибрация 1 категории. Общая вибрация с частотой менее 07 Гц (качка) хотя и неприятна но не приводит к вибрационной болезни. Следствием такой вибрации является морская болезнь которая наблюдается из-за нарушения нормальной деятельности органов равновесия (вестибулярного аппарата). При систематическом воздействии на человека общей вибрации с частотой более 1 Гц могут возникнуть стойкие нарушения опорно-двигательного аппарата центральной и периферической нервной системы системы пищеварения. Особенно опасны общие вибрации с частотами близкими к частотам собственного колебания человека так как в этом случае наблюдается явление резонанса (резкое усиление амплитуды собственных колебаний). Для стоящего наблюдается два пика на частотах 5-12Гц и 17-25 Гц; для сидящего – на частотах 4-6 Гц. Для головы такие частоты лежат в области 20-30 Гц. Начиная с частоты 40 Гц колебания тела под влиянием вибрации становятся во много раз меньше вибрирующей поверхности. Колебания рабочих мест с указанными частотами опасны так как могут вызвать механические повреждения и даже разрыв внутренних органов. Систематическое воздействие общих вибраций в резонансной и околорезонансной зоне может быть причиной вибрационной болезни – стойких нарушения физиологических функций организма обусловленных преимущественно воздействием вибраций на центральную нервную систему. Эти нарушения проявляются в виде головных болей головокружений плохого сна пониженной работоспособности плохого самочувствия нарушений сердечной деятельности.
Ослабление вибрации в источнике - наиболее рациональное средство борьбы с вибрациями на момент проектирования. Выбор кинематических и технологических схем при которых динамические процессы вызванные ударами резкими ускорениями были бы исключены или предельно снижены (например замена: кривошипных механизмов равномерно вращающимися ковки и штамповки — прессованием). Уравновешивание балансировка вращающихся частей для обеспечения плавности работы машины. Устранение дефектов и разболтанности отдельных частей.
Чтобы уменьшить воздействие вибрации на машиниста и на остов машины необходима виброизоляция (введение в систему дополнительной упругой связи с целью ослабления передачи вибраций смежному элементу конструкции или рабочему месту) между рамой машины и такими элементами как двигатель коробка передач кабина приборы рычаги управления. Применяют виброизолирующие опоры типа упругих прокладок или пружин.
4 Общие санитарно-гигиенические требования к воздуху рабочей зоны
Микроклимат – метеорологические условия внутренней среды кабины определяемые температурой воздуха относительной влажностью воздуха скоростью движения воздуха интенсивностью теплового излучения.
В кабинах пультах и постах управления технологическими процессами при выполнении работ связанных с нервно - эмоциональным напряжением должны соблюдаться оптимальные величины температуры 22-24 градуса относительной влажности 60-40% и скорости движения не более 01 мс.
Для обеспечения санитарных норм в холодное время года в кабину автогрейдера устанавливается отопительная система. В целях уменьшения теплопотерь стенки кабины выполняют двухслойными. Наружный слой представляет собой обшивку из стального листа толщиной 06 12 мм внутренний – картон или иной термоизоляционный материал (бумага войлок асбест кожа сталь стекло) толщиной до 4мм. При очень низких температурах атмосферного воздуха проектируют дополнительные термоизоляционные слои. Все соединения кабины герметизированы специальными резиновыми уплотнениями. Пол кабины покрыт войлочно-резиновым ковриком предназначенный как для теплоизоляции так и для уменьшения шума и вибрации на рабочем месте. Большое значение для нормализации воздушной среды в кабине имеет система вентиляция. В летний период теплота передаваемая от внешнего воздуха работающего двигателя и посредством солнечной радиации нагревает кабину. Чтобы снизить утомляемость оператора повысить производительность труда ее оснащают системой кондиционирования воздуха.
Содержание вредных веществ в воздухе рабочей зоны не должно превышать предельно допустимых концентраций (ПДК). Полный список вредных веществ и их ПДК приведен ГОСТ 12.1.005-88.
5 Светотехнические приборы машины и освещение территории
Для обеспечения безопасности движения и выполнения работ в темное время суток автогрейдер оборудуется осветительными приборами. Недостаточная освещенность строительных площадок утомляет операторов приводит к удлинению рабочего цикла машины снижению производительности труда а также резко повышает вероятность возникновения аварийной ситуации. Особую опасность представляют машины не оборудованные требуемыми осветительными приборами при движении ночью в потоке с другими транспортными средствами.
Необходимо общее освещение рабочих площадок сигнальная разметка знаки. ГОСТ Р 12.4.026-2001 распространяется на сигнальные цвета знаки безопасности и сигнальную разметку для производственной общественной и иной хозяйственной деятельности людей строительных площадок и иных объектов где необходимо обеспечение безопасности предотвращения несчастных случаев устранение опасности для жизни вреда для здоровья людей.
6 Пожарная безопасность
Пожарная безопасность (ГОСТ 12.1.004-91) объекта должна обеспечиваться системами предотвращения пожара и противопожарной защиты в том числе организационно-техническими мероприятиями.
Противопожарная защита должно достигаться способами: применение средств пожаротушения применение конструкций и материалов в том числе используемых для облицовок конструкций с нормированными показателями пожарной опасности применение пропитки конструкций объектов антипиренами и нанесение на их поверхность огнезащитных красок и составов применение средств коллективной и индивидуальной защиты людей от опасных факторов пожара. Обязательна организация обучения работников правилам пожарной безопасности.
Необходимо соблюдать следующие правила. Запрещается курить и пользоваться огнеопасными предметами во время работы с горюче- смазочными материалами в холодное время года пользоваться факелами для разогрева масла в агрегатах автогрейдера во время заправки и при работающем дизеле производить монтажные и демонтажные работы. После заправки необходимо удалить подтеки горюче-смазочных материалов. Не допускается попадание горюче-смазочных материалов на агрегаты электрооборудования (генератор стартер и т.д.). Промасленный обтирочный материал хранить в закрытом металлическом ящике. Ремонтные работы связанные с искрообразованием и высокой температурой (сварочные паяльные и др.) производить не на автогрейдере за исключением деталей и узлов которые невозможно снять. Сварочные работы производить на расстоянии не менее 20 метров от машины. Соблюдать правила обращения с электролитом низкозамерзающими жидкостями и этилированным бензином. Для тушения воспламенившегося топлива применять огнетушители засыпать или покрыть его брезентом или войлоком.
Автогрейдер должен отвечать экологическим показателям: выбросы вредных веществ с отработавшими газами ГОСТ 17.2.2.05 – 97 дымность отработавших газов ГОСТ 17.2.2.02 – 98.
Значение удельных выбросов вновь изготовленных и капитально отремонтированных на ремонтных заводах дизелей тракторов и машин не должно быть более норм приведенных в таблице 7.2.
Таблица 7.2 Нормы удельных выбросов.
Наименование вредных веществ
Удельные выбросы г(кВт*ч) при воздухообмене
Нормы выбросов оксидов азота установлены по сумме оксидов азота приведенных к оксиду азота(IV)
Нормы выбросов углеводородов установлены по сумме углеводородов приведенных к условному составу С1Н185
Значение дымности на установившихся режимах вновь изготовленных и капитально отремонтированных на ремонтных заводах дизелей тракторов и машин не должно быть более норм приведенных в таблице:
Таблица 7.3 Нормы дымности.
Условный расход воздуха дм3с
Дымность м-1(%) не более при воздухообмене
8 Указания мер безопасности
К работе на автогрейдере допускаются лица знающие устройство и правила эксплуатации и имеющие удостоверение на право управления автогрейдером.
Работать на неисправной машине строго запрещается. К работе приступить убедившись в исправности всех механизмов и агрегатов обратив особое внимание на исправность рулевого управления колесных тормозов трансмиссии и дизеля.
При работе в комплексе с экскаватором запрещается нахождение автогрейдера в радиусе действия экскаватора плюс 5 м.
Рисунок 7.2 – Работа автогрейдера
Во время работы пол кабины должен быть чистым и свободным от посторонних предметов посторонним лицам запрещается находиться в кабине и в зоне работы.
Во время движения автогрейдера запрещается удалять из-под ножей посторонние предметы.
Нельзя на ходу автогрейдера регулировать исправлять или смазывать его механизмы.
При разравнивании грунта на насыпях высотой более 10 м расстояние от колес автогрейдера (прицепного грейдера) до бровки насыпи должно быть не менее 1 м; отвал не должен выдвигаться за бровку насыпи.
Рисунок 7.3 – Разравнивание грунта
Запрещается сидеть и стоять на раме рабочих органах и крыльях во время движения.
При выполнении работ по ремонту или техническому обслуживанию следует надежно затормозить автогрейдер стояночным тормозом опустить рабочее оборудование на землю или подставки. Производить работы при работающем двигателе не допускается.
Работы по техническому обслуживанию или ремонту должны производиться в специально отведенных местах где обеспечивается удобный доступ и хорошее освещение.
Во время технического обслуживания и ремонта приборов электрооборудования выключить включатель «массы».
Монтаж или демонтаж шин производить на стенде или чистом полу. При накачивании необходимо следить за показаниями манометра не допускается превышение давления воздуха выше нормы.
При необходимости отлучиться от машины надо затормозить стояночным тормозом и заглушить двигатель. Нельзя оставлять автогрейдер на уклонах.
Категорически запрещается при спусках с горы переключать передачи или выключать муфту сцепления. Спуск с горы производить на рабочих передачах.
В случае невозможности транспортирования автогрейдера на специальное место для ремонта его необходимо оградить на месте вынужденной остановки или установить знаки аварийной остановки согласно «Правилам дорожного движения».
После окончания смены машинист обязан предупредить сменщика о всех неисправностях автогрейдера.
При пользовании домкратом необходимо придать ему устойчивое положение предупреждающее завал машины. Места установки домкратов под балкой переднего моста и под корпусами балансиров.
Перед запуском дизеля поставить рычаг переключения передач в нейтральное положение и затормозить автогрейдер стояночным тормозом.
Езда на автогрейдере при открытых незакрепленных дверях кабины запрещается. При движении на транспортных передачах двери должны быть закрыты.
Рычаг распределителя управляющий положением кронштейна подвески гидроцилиндров подъема отвала тяговой рамы должен постоянно находиться в нейтральном положении. При установке отвала для срезания откосов запрещено находиться посторонним лицам в радиусе не менее 3-х метров.
При транспортировании автогрейдера обращать особое внимание на выбор скоростей движения с учетом дорожных условий радиусов поворота видимости и обзорности.
При транспортировании автогрейдера своим ходом на большие расстояния тяговую раму и бульдозерный отвал закрепить проволокой к основной раме. - Поворот (складывание) шарнирно-сочлененной рамы можно производить только на месте или в движении со скоростью не более 6 кмч (первая рабочая передача).
Движение автогрейдера со сложенной рамой на транспортных передачах запрещается.
При выносе отвала и поворота рамы следите за тем чтобы отвал не касался других частей машины.
Не разрешается работа на автогрейдере при наличии течи в баке топливопроводах системах смазки и охлаждения при сильном загрязнении его узлов и агрегатов топливом и смазочными материалами.
Перед движением под уклон еще на ровном участке включают первую или вторую скорость передачи и двигаются на этой передаче до окончания спуска. Запрещается производить переключение передач при спуске на повышенных скоростях выключать главное сцепление и тормозить ручным тормозом. Ручной тормоз предназначен только для затормаживания машины на остановке пользоваться им для торможения в движении запрещается.
Требования после окончания работ
Закончив работу следует поставить автогрейдер (прицепной грейдер) в специально отведенное место выключить двигатель перевести рычаг переключения передач в нейтральное положение прекратить подачу топлива затормозить машину опустить рабочее оборудование на грунт или специальные подставки и принять меры исключающие возможность пуска двигателя автогрейдера посторонними лицами.
В холодное время года необходимо слить воду из радиатора автогрейдера и дать двигателю поработать без воды 2-3 мин. Запрещается оставлять автогрейдер с поднятым навесным оборудованием или с работающим двигателем.
Машину необходимо очистить от пыли и грязи и осмотреть устранив мелкие дефекты.
Механизмы автогрейдера (прицепного грейдера) нужно смазать согласно инструкции после чего следует убрать смазочные материалы на склад а инструменты и обтирочный материал в специальные ящики.
О всех неисправностях обнаруженных при осмотре или работе автогрейдера (прицепного грейдера) машинист обязан сообщить механику или сменщику. Поставить в известность мастера (прораба) об окончании работ и состоянии охраны труда.
9 Расчёт автогрейдера на устойчивость
9.1 Расчёт продольной устойчивости
В процессе работы потеря устойчивости и опрокидывание автогрейдера могут произойти при его движении по наклонной поверхности и при повороте. Автогрейдер – длиннобазовая машина поэтому его продольная устойчивость (рис.7.8) против опрокидывания обеспечена на уклонах являющихся предельными по условию сцепления движителя с дорогой.
Предельный угол подъёма преодолеваемый автогрейдером по условию сцепления движителя с дорогой рассчитывают:
Тогда tgп = 06 – 005 = 055;
Рисунок 7.4 - Схема для определения устойчивости автогрейдера
В итоге предельный угол подъёма п = arctg0.55 = 288°.
Наибольший угол подъёма преодолеваемый по условию реализации 100% мощности двигателя устанавливается по соотношению:
sinп = NGV(1+f2) . (7.2)
Получим sinп = 99 . 076 1088 . 11 (1+0052) = 063.
Тогда наибольший угол подъёма п = arcsin 0.63 = 39° предельный уклон по условию сцепления тормозящих колёс с дорогой находят из равенства:
Тогда предельный уклон п = arctg0.33 = 183°.
9.2 Расчёт поперечной устойчивости
По условию опрокидывания допускаемый угол поперечного уклона
tgп = 05b12hц ; (7.4)
где b = 20м – ширина колеи автогрейдера;
hц = 106м – расстояние от опорной поверхности до центра тяжести автогрейдера;
tgп = 05 . 2012 . 106 = 079.
Тогда допускаемый угол поперечного уклона п = arctg 0.79 = 383°.
Максимальную скорость движения на поворотах по условию опрокидывания находят из формулы:
где Куст = 12 – коэффициент устойчивости;
р – радиус поворота;
е=0 - эксцентриситет центра тяжести относительно продольной оси машины;
По условию сцепления движителя с дорогой допускаемый угол поперечного уклона:
tg = 08φ 12 = 08 . 06 12 = 04;
Тогда допускаемый угол поперечного уклона п = arctg0.4 = 218°.
Максимальная скорость движения на поворотах по условию сцепления движителя с дорогой
2.Особненности изменения угла резания.doc
(Особенности кинематики механизма изменения угла резания
отвала автогрейдера)
У современных автогрейдеров всех типов управление рабочим оборудованием (отвалом) производится из кабины машиниста с помощью гидропривода. Изменение углов резания и захвата непосредственно в процессе разработки грунта позволяет лучше приспособить машину к изменениям грунтовых условий что в конечном счёте повышает её производительность.
Рисунок 2.1 – Конструктивная схема механизма изменения угла резания отвала автогрейдеров моделей ДЗ – 143 и ДЗ – 148
Конструктивная схема механизма изменения угла резания представлена на рис.2.1 подвижными звеньями являются: 1 – отвал; 2 – шток гидроцилиндра с поршнем; 3 – корпус гидроцилиндра. Неподвижное звено – поворотный круг 4 с кронштейнами 5. Данный механизм представляет собой плоский четырёхзвенник с четырьмя низшими кинематическими парами и одной степенью подвижности.
Отличительной конструктивной особенностью механизмов изменения угла резания различных моделей автогрейдеров является место расположения шарнира Б крепления корпуса гидроцилиндра к поворотному кругу (рис.2.1). У автогрейдеров класса 100 (ДЗ – 148) и класса 160 (ДЗ – 143) этот шарнир расположен за отвалом как показано на рис.2.1. у автогрейдеров класса 160 (ДЗ – 122)и класса 250 (ДЗ – 98 ДЗ – 98А) шарнир Б расположен перед отвалом.
Общим для всех современных схем этого механизма является то что при изменении угла резания поворот отвала 1 относительно кронштейна 5 (неподвижное звено) происходит в шарнире 0. У отечественных автогрейдеров классов 100 и 160 диапазон изменения угла резания =30 – 70 0 а у автогрейдеров класса 250 =30 – 80 0.
Рисунок 2.2 –Схема траекторий подвижных точек механизма изменения угла резания угла автогрейдера
Рассмотрим кинематику механизма схема траекторий подвижных точек которого показана на рис.2.2. отвал заглублен в грунт на начальную глубину резания hр0.Точкой D обозначена режущая кромка отвала (ножа). Введём следующие обозначения к схеме на рис.2.2: RD – радиус поворота режущей кромки отвала (ножа); rD – радиус поворота передней грани отвала (ножа); RA – радиус поворота головки штока гидроцилиндра;
Из OE0D0 (рис. 2.2) угол =arcsin rD RD= const.
При угле резания 1 >0 глубина резания hр1 = hр0+C0C1 = hр0+hр1
где hр1 = C0C1 = RD[sin(1-)- sin(0-)].
При 2 >0 hр2 = hр0+C0C2 = hр0+hр2
где hр2 = C0C1 = RD[sin(0-)- sin(2-)].
После преобразования выражений (2) (3) получим
hр1 = 2RD sin 2 cos[(0-)+ 2]
hр2 = 2RD sin 2 cos[(0-)+ 2]
В общем случае при =0± имеем hр = hр0± hр здесь
hр = 2RD sin 2 cos[(0- arcsin rD RD ) ± 2].
Таким образом имея начальную глубину резания hр0 при увеличении или уменьшении начального угла резания 0 на величину будем увеличивать или уменьшать hр0 на величину hр что и является главной особенностью кинематики механизма изменения угла резания отвала современных автогрейдеров.
Анализ функции hр=(0) представленный уравнением (6) показывает что она является монотонной не имеет выраженных экстремумов проходит через начало координат и располагается в первом и третьем квадрантах т. е. в областях положительных и отрицательных значений и hр.
При =0-400 изменение глубины резания составляет у автогрейдеров моделей ДЗ - 143 ДЗ – 148 hр=0 - 205 мм у автогрейдера модели ДЗ – 122 hр=0 - 233 мм.
Из (6) видно что hр=0 при соблюдении одного из следующих трёх условий:
cos[(0- arcsin rD RD ) ± 2]=0.
Условие RD=0 не может быть выполнено конструктивно а
cos[(0 - arcsin rD RD ) ± 2]=0 не выполняется исходя из реальных значений параметров этой функции. Условие же =0 соответствует случаю когда в процессе работы отсутствует корректировка угла резания.
Таким образом существующие кинематические схемы механизмов изменения угла резания отвала автогрейдера не обеспечивают постоянства глубины резания hр=const при изменении в процессе разработки грунта первоначального угла резания 0. Поэтому эти схемы не могут быть использованы в системе автоматического управления процессом разработки грунта по углу резания в оптимальном режиме работы автогрейдера. Между тем как показывают исследования автогрейдер в конкретных условиях работы имеет максимальную производительность и минимальный удельный расход топлива при определённом значении угла резания отвала причём эти зависимости являются экстремальными.
Стоимостные показатели-ЭЧДП-СДМ-2014.doc
на 1 квартал 2014 года
Наименование показателя
Стоимость 1 чел.-ч. рабочего управляющего строительными машинами
Стоимость 1 чел.-ч. ремонтого рабочего
Стоимость 1 чел.-ч. такелажника
Стоимость 1 кг смазочных материалов
Стоимость 1кг гидравлической жидкости
Стоимость 1 кг дизельного топлива
Стоимость 1 Квт-ч электроэнергии
Стоимость 1м3 сжатого воздуха
Стоимость 1 шины (уточнять по прайсу на конкретный вид и размерность шин)
Стоимость пользования 1 часа автомобиля-тягача
Стоимость 1 км пробега
Стоимость машино-часа работы вспомогательного крана
Часовая тарифная ставка водителя тягача 6-го разряда
если у техники есть шины – то количество комплектов оснастки равняется количеству шин. Стоимость 1 комплекта оснастки равняется стоимости 1 шины;
если у техники нет шин – то стоимость всех комплектов оснастки 1% от оптовой стоимости техники;
Срок службы оснастки - 4 года
Ставка рефинансирования Центрального банка Российской Федерации
Процент риска неполучения экономического эффекта в период срока эксплуатации техники
Показатели часовой оплаты труда рабочих-строителей занятых на строительных работах на 1 квартал 2014 г.
Квалификационный разряд рабочих
Показатели часовой оплаты труда руб.
Показатели часовой оплаты труда рабочих управляющих строительными машинами на 1 квартал 2014 г.
экономика.doc
При подготовке производства новых изделий необходимо проанализировать спрос на разрабатываемые изделия размеры финансирования на разработку проекта и освоение производства с целью обоснования целесообразности принятых решений которые определят экономический успех предприятия в случае успешной реализации новой продукции.
В связи с ограничением финансовых ресурсов и конкуренции в условиях рыночных отношений крайне важно на ранних стадиях конструкторской проработки оценить техническую и экономическую целесообразность проектов и своевременно прекратить финансирование неперспективных вариантов.
Вывод о целесообразности проектирования и производства новых видов продукции возможен с помощью предлагаемых методических указаний.
1 Оценка технической целесообразности конструкции изделия
Сравнительный анализ проектируемого изделия на техническом уровне является первым этапом оценки и отбора лучшего варианта.
- оценка технической целесообразности спроектированной конструкции на основании сравнения с аналогом по основным группам функционально-технических показателей;
- обеспечение расчета лимитной цены изделия.
Оценка выполняется в следующей последовательности:
1.1 Выбор перечня показателей оценки технического
Все показатели используемые для оценки технического уровня конструкции можно классифицировать на:
- показатели назначения и тактико-технические данные изделия;
- конструкторские (специальные) показатели влияющие на функционирование изделия;
- общие конструкторские (технические) показатели влияющие на условия производства.
Все электрооборудование размещается на машине согласно его функциональному назначению сообразуясь со схемой расположения механизмов удобством использования и управления электрооборудованием.
Таблица 8.1 Перечень показателей технического уровня и качества изделий.
Проектируемое изделие
Транспортная скорость
Коэф-т исп-ия материала
1.2 Оценка весомости (значимости) показателей
Оценка весомости показателей изделия осуществляется на основе экспертных оценок. Наиболее простым методом индивидуальной экспертизы используемым для оценки весомости показателей является метод попарных сравнений.
Результаты экспертизы представляются в виде матрицы (таблица 6) в которой на пересечении строки и столбца фиксируются индексы тех показателей которые являются более важными в оценке качества изделия при их попарном сравнении.
Далее для каждого показателя определяется количество предпочтений полученных им по отношению ко всем остальным показателям (в первой строке подсчитывается количество 1 во второй – 2 в третьей – 3 и т.д.). Полученное значение увеличивается на единицу.
Количественное представление весомости (значимости) показателей может быть получено по формуле:
где Кi – количество предпочтений i – го показателя.
Таблица 8.2 Матрица попарного сравнения показателей.
1.3 Расчет комплексного показателя технического уровня и качества конструкции
Комплексный показатель позволяет дать обобщенную оценку совокупной технической ценности изделия. В основе оценки лежит сравнение значений выбранного набора показателей базового и проектного варианта с эталонными значениями. В качестве эталонных могут использоваться наилучшие (идеальные) технически достижимые значения рассматриваемых показателей.
Комплексный показатель рассчитывается по формуле:
где q - безразмерный показатель качества по
r Относительный показатель качества по i - му параметру может быть рассчитан с помощью формулы:
где Pjn pjэ - количественные значения i - го показателя соответственно сопоставляемых вариантов и эталонного значения.
Первая формула используется для показателей при увеличении абсолютных значений которых возрастает обобщенный показатель в противном случае вторая формула.
Сопоставление комплексных показателей качества по потенциально воз
можным вариантам конструкций позволяет сделать вывод о технической целесообразности новой разработки определить коэффициент изменения качества при сравнении изделия с аналогом:
и используется в основном с последующей термообработкой . (8.4)
Где Wn Wб - комплексные показатели качества проектного и базового вариантов. Данный коэффициент используется при определении лимитной цены проектируемого изделия.
Таблица 8.3 Оценка технической целесообразности конструкции по вариантам (П - проектный Б - базовый).
Наименование показателей по
Коэффициент значимости
значимости показателя
Оценка вклада показателя
Коэф-т исп-я материала
Коэффициент изменения качества
2 Расчет трудоемкости ОКР
Многообразие существующих методов нормирования ОКР можно свести к трем основным: экспертному опытно-статистическому и расчетно аналитическому. Первый метод базируется на экспертных оценках второй -на сравнении нормируемого объекта с аналогичным нормативы на который известны третий - на корреляционных зависимостях трудоемкости работ от основных технических параметров изделия.
В основу предложенной методики по определению трудоемкости ОКР положен бальный метод.
С помощью бальных оценок по отдельным факторам определяется суммарный показатель объема работ в единицах сложности (баллы) который затем с помощью удельного норматива переводится в трудоемкость. Оценка факторов выполняется дифференцированно по главным узлам и видам работ.
Выделено два вида работ: расчетно-аналитические и чертежно-графические для которых порядок расчета объемных показателей различен.
Расчет выполняют в следующей последовательности:
Осуществляется сбор исходной информации о проектируемом объекте:
-наличие аналога или прототипа оценка общей сложности схемы объекта;
- состав главных узлов объекта;
-характеристики узлов (степень новизны конструкции количество кинематических пар количество оригинальных деталей объем конструкции по внешним контурам количество сложных деталей в узлах).
На основании значений исходных показателей таблицы 8.4 – 8.8 выбираются по каждому узлу нормативы объемов работ в баллах для первой и второй групп QH QH а также корректирующие коэффициенты к0 к1 к2 к3 к4. Результаты сведем в табл.8.9.
Таблица 8.4 Показатель объема работ 1-й группы в единицах сложности (баллах).
Характеристика группы новизны
Имеется близкий аналог (отличия не более 20%).
Имеется аналог с небольшими отличиями (20 – 50%).
Имеется прототип похожий по принципу действия и конструкции отдельных узлов. Отличается по многим параметрам.
Известен прототип из информационных и патентных источников. Нет чертежей.
Прототипа нет или он неизвестен.
Нет прототипа в основе конструкции лежит новая идея.
Таблица 8.5 Показатель объема работ 2-й группы в единицах сложности (баллах).
Группа насыщенности узла деталями
Примерное число оригинальных деталей
Таблица 8.6 Коэффициент К1 К2.
Группа сложности по числу кинематических пар
Таблица 8.7 Коэффициент К3.
Группа объемности конструкции узла
Объем по внешним контурам дм3
Таблица 8.8 Коэффициент К4.
Группа насыщенности узла сложными деталями*
Примерное количество сложных деталей
К сложным относятся детали имеющие сложную форму требующие при конструировании специальных расчетов а также расчеты размерных цепей.
Таблица 8.9 Исходные данные для расчета трудоемкости ОКР.
Характеристика объектов
Сложность схемы изделия
Новизна конструкции
Сложность узла по количеству кинематических пар
Насыщенность оригинальными деталями
Объем конструкции по внешним контурам
Насыщенность сложными деталями
Таблица 8.10 Коэффициент К0 учитывающий сложность и степень автоматизации схемы объекта.
Группа сложности схемы
Простейшая схема с одним энергопотоком без управления процессом.
Простая схема с разветвлением энергопотока с частично автоматическим или ручным управлением
Схема средней сложности с ветвящимся энергопотоком наличием блокировочных регулирующих и других элементов.
Сложная схема с автоматизацией рабочего цикла имеются взаимодействия механических электрически гидравлических и других связей в конструкции
Схема повышенной сложности с полной автоматизацией наличием обратных связей управление от устройства автоматики по заданной программе.
Осуществляется расчет показателей.
Показатель объема работ первой группы по узлу i определяется по формуле:
где QH - нормативное значение объема работ (первой группы в баллах) выбираемое в зависимости от группы новизны узла;
K1 - корректирующий коэффициент учитывающий влияние сложности узла по числу кинематических пар.
Показатель объема работ второй группы по узлу i определяется по формуле:
где QH2 - нормативное значение объема работ второй группы в баллах выбираемое в зависимости от количества оригинальных деталей в узле;
К2 К3 К4 - корректирующие коэффициенты учитывающие влияние группы сложности по числу кинематических пар группы объемности насыщенности узла сложными деталями соответственно.
Суммарная трудоемкость ОКР определяется по формуле:
Где tн - норматив удельной трудоемкости чел.-дн.бал. Норматив устанавливается на основе статистических данных по результатам проектирования аналогичных изделий;
Ко - коэффициент учитывающий сложность и степень автоматизации управления объектов в целом. Расчет трудоемкости ОКР проведем в табл.
Объем работ по группам в баллах
Расчетно-аналитические
Чертежно-графические
Норматив удельной трудоемкости на 1 балл чел - дн
Коэффициент сложности схемы К0
Трудоемкость ОКР чел – дн
3 Расчет временных и стоимостных затрат на проектирование изделия
Важными показателями используемые при технико-экономическом анализе изделия являются стоимостные затраты на разработку и срок реализации проекта.
Укрупненный способ расчета основанный на данных о трудоемкости ОКР известной структуре распределения трудозатрат по стадиям проектирования (таблица 8.12) и норматив длительности стадии (таблица 8.13).
Расчет реализуется в табличной (таблица 8.14) форме в следующей последовательности:
) по типу производства выбирается соотношение трудоемкости
стадий проектирования %; tуд;
) рассчитывается трудоемкость отдельных стадий проектирования
)по суммарной трудоемкости ОКР выбирается нормативная длительность цикла технического и рабочего проектирования Ттпи и Трпи
)определяется длительность цикла технологической подготовки
производства по формуле:
) определяется потребная численность исполнителей по стадиям проектирования:
где Fpн - месячный фонд времени работника (176 часов);
Квн - коэффициент выполнения нормы Квн=11 12.
) Определяется фонд заработной платы на разработку проекта:
где 3jм - средняя месячная заработная плата исполнителей
Нсн - коэффициент отчисления на социальные нужды (Нсн=26%);
) определяются полные затраты на разработку проекта:
где Кзп - удельный вес заработной платы в общей структуре себестоимости выбирается по статистическим данным (КЗП = 035 – 04);
) осуществляется оценка срока реализации проекта:
где Кпар - коэффициент параллельности учитывающий величину совмещения стадий (Кпар=07).
Таблица 8.12 Соотношение трудоемкости стадий проектирования %.
Стадии и этапы работ
Разработка ТЗ и эскизное проектирование
Техническое проектирование (ТП)
Рабочее проектирование (РП)
Технологическая подготовка
Проектирование технологических процессов
Проектирование спецоснастки
Таблица 8.13 Нормативы длительности стадий конструкторской подготовки производства.
Общая трудоемкость проектирования н–ч.
Длительность цикла мес.
Таблица 8.14 Расчет временных и стоимостных затрат на проектирование изделия.
Соотношение трудоемкости стадий проектирования %
Трудоемкость нормо-час
Длительность производственного цикла мес.
Потребное количество исполнителей чел
Средняя заработная плата исполнителей руб.
Фонд заработной платы по стадиям руб.
Общий фонд заработной платы на проектирование руб.
Оценка затрат на разработку проекта руб.
Оценка срока реализации проекта мес.
4 Прогнозирование себестоимости изделия
На стадии конструкторской подготовки проекта когда отсутствуют необходимые технологические документы и нормативы для расчета себестоимости приходится применять различные методы прогнозирования: удельных весов и коэффициентов приведения известной структуры себестоимости аналогов.
Прямыми стадиями определяющими себестоимость конструкции являются:
- затраты на основные материалы;
- затраты на комплектующие основные изделия;
- заработная плата производственных рабочих.
4.1 Расчет затрат на основные материалы
Расчет затрат на основные материалы при небольшом количестве деталей и узлов можно выполнять в целом по изделию.
Стоимость основных материалов определяется на основе норм расхода каждого вида материала и цен за вычетом стоимости отходов.
Расчет затрат на основные материалы производим в табличной форме.
Затраты на основные материалы по базовому узлу можно рассчитать по формуле:
Цм - цена материала руб;
Ц° - цена отходов руб;
Котх - средний процент реализации отходов (табл.8.15 );
Ктз - коэффициент транспортно-заготовительных расходов (Ктз=103 -107).
Таблица 8.15 Нормы планируемых отходов %.
Таблица 8.16 Расчет затрат на основные материалы.
Итого по базовому узлу руб.
С учетом транспортно-заготовительных расходов
4.2 Затраты на комплектующие покупные изделия
Затраты на покупные комплектующие изделия осуществляются на основе спецификаций применяемости Рij и цен Цкi по формуле:
Расчет затрат на комплектующие покупные изделия см. табл.8.17
Расчет затрат на комплектующие покупные изделия и полуфабрикаты по базовому узлу.
Двигатель ЯМЗ 236 Г-2
Редуктор поворота отвала
С учетом транспортно-заготовительных расходов руб.
Таблица 8.18 Расчет затрат на основные материалы в целом по изделию.
Комплектующие изделия
4.3 Расчет затрат на заработную плату производственных рабочих
На стадии конструкторской подготовки производства расчет заработной платы базируется на показателе удельной трудоемкости на 1 кг массы конструкции изделия аналога. При отсутствии таких данных для приближенных расчетов можно использовать усредненные отраслевые значения. Расчет заработной платы (основной и дополнительной) производственных рабочих.
Трудоемкость изделия
tуд - удельная трудоемкость 1 кг массы конструкции; G - масса конструкции.
Трудоемкость годового выпуска
Nг-прогнозируемый объм выпуска
Потребное количество основных производственных рабочих
Fpr - годовой действительный фонд времени одного рабочего
Годовой фонд ЗП основной и дополнительный
Зср-средняя заработная плата ОПР
ЗП с учетом отчислений на соц. нужды.
Нсн - коэффициент расходов на социальные нужды Нсн=26%
4.4 Расчет полной себестоимости изделия
Расчет полной себестоимости изделия осуществляется по формуле:
Нвн - норматив внепроизводственных расходов %; (для данного типа производства 7%);
З0и - заработная плата производственных рабочих на единицу изделия.
5 Определение прогнозируемой цены изделия
Лимитная цена выражает предельно допустимый уровень цены проектируемого изделия с учетом улучшения потребительских свойств изделия при котором обеспечивается относительное удешевление его для потребителя.
При отсутствии аналогов для сопоставления и невозможности определить полезный эффект от принципиально нового изделия лимитная цена определяется на основе укрупнённых нормативов материальных и трудовых затрат и повышенной по сравнению с нормативным уровнем рентабельности до 15 раз
где - плановая себестоимость изделия;
- плановый уровень рентабельности к себестоимости изделия.
6 Расчет уровня капитальных вложений в НИОКР и освоение производства
В условиях ограничения финансовых ресурсов технический и коммерческий успех проекта во многом определяется величиной новых капитальных вложений при его разработке и реализации. Капитальные затраты на всех этапах жизненного цикла изделия являются важной оценкой экономической эффективности новых проектов.
Единовременные затраты в сфере производства включают предпроизводственные затраты Кппз и капитальные вложения в производственные фонды завода изготовителя Кпф
Укрупненный расчет капитальных вложений в производственные фонды завода может производиться по формуле.
где Коб - капитальные вложения в оборудование и оснастку руб.;
Кос - капитальные вложения в оборотные средства руб.
где Цп - прогнозируемая цена изделия руб.;
Nе- прогнозируемый объем выпуска шт.;
- отраслевой норматив удельных капитальных вложений в оборудование на один рубль объема реализации новых изделий
- коэффициенты учитывающие соответственно годовой объем
производства для данного типа производства соответственно 125 и 115.
Расчет прибыли на единицу изделия:
7 Оценка эффекта от производства и использования
Расчет экономической эффективности новых изделий основан на сопоставлении результатов и затрат в сфере производства и в сфере использования.
Формула расчета экономического эффекта:
где П – прибыль на одно изделие руб.; ЕН – нормативный коэффициент экономической эффективности ЕН=015; КУ – удельные капитальные вложения в производство рубшт; N – прогнозируемый годовой объем выпуска
Расчет экономической эффективности
8 Сводные показатели оценки экономической целесообразности
Заключительным этапом технико-экономического обоснования проектируемого изделия является составление таблицы показателей оценки экономической целесообразности конструкции (таблица 8.20).
Наименование показателя
Прогнозируемый объем выпуска
Единовременные капитальные вложения
Производственные затраты
Вложения в производство
Текущие издержки на производство
Полная себестоимость
Прибыль на единицу изделия
Прогнозируемая цена изделия
Экономический эффект
Срок реализации проекта
Вывод. Проведенные технико-экономическое обоснование производства автогрейдера выявило перспективность осуществления этого проекта. Проектируемое изделие по ряду технических показателей будет превосходить существующие аналоги. Проведенные экономические расчеты себестоимости и цены изделия позволяют определить планируемую прибыль и рентабельность а также годовой экономический эффект при производстве проектируемого изделия - автогрейдера.
6. Расчет технико-экономических показателей проекта.doc
При подготовке производства новых изделий необходимо проанализировать спрос на разрабатываемые изделия размеры финансирования на разработку проекта и освоение производства с целью обоснования целесообразности принятых решений которые определят экономический успех предприятия в случае успешной реализации новой продукции.
В связи с ограничением финансовых ресурсов и конкуренции в условиях рыночных отношений крайне важно на ранних стадиях конструкторской проработки оценить техническую и экономическую целесообразность проектов и своевременно прекратить финансирование неперспективных вариантов.
Вывод о целесообразности проектирования и производства новых видов продукции возможен с помощью предлагаемых методических указаний.
1 Оценка технической целесообразности конструкции изделия
Сравнительный анализ проектируемого изделия на техническом уровне является первым этапом оценки и отбора лучшего варианта.
- оценка технической целесообразности спроектированной конструкции на основании сравнения с аналогом по основным группам функционально-технических показателей;
- обеспечение расчета лимитной цены изделия.
Выбор перечня показателей оценки технического
Все показатели используемые для оценки технического уровня конструкции можно классифицировать на:
- показатели назначения и тактико-технические данные изделия;
- конструкторские (специальные) показатели влияющие на функционирование изделия;
- общие конструкторские (технические) показатели влияющие на условия производства.
Все электрооборудование размещается на машине согласно его функциональному назначению сообразуясь со схемой расположения механизмов удобством использования и управления электрооборудованием.
Расчет годовой экономической эффективности от внедрения в производство автогрейдера с модернизированным рабочим оборудованием. За базовую технику «БТ» принят серийно выпускаемый автогрейдер среднего типа ДЗ-143.
По сравнению с «БТ» новый автогрейдер «НТ» имеет следующие положительные отличия:
а)Работы машины в режиме близком к оптимальному за счет подстройки угла подходящего для данного грунта;
б)Уменьшение времени на перестройку оборудования для изменения глубины резания.
Таблица 6.1 – Исходные данные
Масса конструктивная
Техническая часовая
Количество обслуживающего персонала
Периодичность смены масла в гидросистеме
Рекомендации по ТО и Р
2 Определение капитальных вложений по базовой и новой технике
Капитальные затраты по базовой и новой технике включают в себя оптовую цену машины и затраты на ее доставку и монтаж
где Ц - оптовая цена машин руб.;
кб - коэффициент учитывающий затраты на первоначальную доставку техники и монтаж
3 Определение годовой эксплуатационной производительности
где ВЭЧ - эксплуатационная среднечасовая производительность м3ч;
КПР - коэффициент учитывающий внутрисменные простои
КПР = 075 (табл. 3 [3]);
ТГ – количество часов работы техники в году ч.
где ВТЧ - техническая часовая производительность принятая из расчета м3ч;
кТ - коэффициент перехода от технической производительности к эксплуатационной
кТ = 04 (табл. 3 [3]).
где ТФ - годовой фонд рабочего времени
ТФ = 200 дн. (табл. 124 [1]);
tсм - средняя продолжительность смены ч
tсм = 68 (для шестидневной недели)
tсм = 82 (для пятидневной недели);
ксм - коэффициент сменности
ксм = 1 (табл. 12.3 [1]);
- продолжительность одной перебазировки дн;
Т об - продолжительность работы техники на одном объекте ч;
Др - простои при всех видах технического обслуживания и ремонта днч.
где m - число разновидностей ремонтов или технических обслуживаний за межремонтный цикл;
- продолжительность ожидания ремонта доставка в ремонт и обратно дн (для текущего ремонта для капитального ремонта);
– число i-х ремонтов или техобслуживаний за межремонтный цикл.
где – периодичность выполнения ремонтов и технического обслуживания;
Тц - межремонтный цикл ч;
Продолжительность работы техники на одном объекте для базовой техники ч. (табл. 12.3 [1])
4 Расчет годовых текущих затрат
Показатель амортизационных отчислений на полное восстановление
где Цб - расчетная стоимость машины данной марки включающая затраты на ее доставку на базу механизации руб.;
На - норма амортизационных отчислений на полное восстановление
Заработная плата машинистов управляющих машинами принимается с учетом численности звена и квалификационного состава машинистов
где кр - средний районный коэффициент
λ - коэффициент учитывающий премии
n - число рабочих занятых управлением машины в одну смену;
руб.ч. – часовая тарифная ставка рабочего шестого разряда.
Расчет затрат на топливо для техники с ДВС
где ЦТi - цена топлива i-го вида р.л
- часовой расход топлива
- количество часов работы техники на топливе
m - число видов топлива.
где - номинальная мощность двигателя л.с.;
- удельный расход топлива при номинальной мощности гл.с.ч.;
- коэффициент использования двигателя по мощности за рабочий цикл;
- коэффициент использования двигателя по времени за час рабочей смены;
- коэффициент учитывающий изменение расхода топлива в зависимости от степени использования двигателя по мощности;
- коэффициент учитывающий снижение расхода топлива при холостой работе двигателя.
Определение затрат на все виды ремонта
Затраты на все виды ремонта Ср включают в себя:
- затраты на техническое обслуживание текущий ремонт и капитальный ремонт.
Затраты на техническое обслуживание (ТО) текущий ремонт (ТР) и капитальный ремонт (КР) определяется по формуле
где СЗП – заработная плата ремонтных рабочих руб.;
СРМ – стоимость ремонтных материалов и запасных частей руб.
Заработная плата ремонтных рабочих
где Тц - продолжительность межремонтного цикла ч.;
- коэффициент премиальных доплат ремонтным рабочим ;
Ср - часовая тарифная ставка ремонтных рабочих
ri - трудоемкость i-х видов технических обслуживаний и ремонтов чел.ч. [2].
Стоимость ремонтных материалов и запасных частей
где к - коэффициент перехода от заработной платы к затратам на запасные части и материалы
Затраты на гидравлическую жидкость
где - объем масла заливаемого в гидросистему дм3;
- объемная масса жидкости
- коэффициент доливок гидравлической жидкости
ЦМ - фактически складывающаяся цена гидравлической жидкости с учетом затрат на ее доставку к обслуживаемой машине рубл
tмг - периодичность замены гидравлической жидкости в гидросистеме машины машч.
Затраты на смазочные материалы
где Скг – стоимость одного килограмма смазочных материалов
W – часовой расход топлива
Затраты на сменную оснастку.
К сменной оснастке относятся материалы и комплектующие изделия которые в процессе работы периодически заменяют и ремонтируют. В данном случае к сменной оснастке относятся шины
где ЦСО - цена сменной оснастки
- число сменной оснастки в комплекте шт.;
- срок службы сменной оснастки ч.;
- число видов сменной оснастки.
Затраты на перебазировку осуществляемую своим ходом.
Рассчитываем исходя из стоимости одного машино-часа и продолжительности переездов в течение года
где - затраты на одну перебазировку руб.;
- заработная плата машиниста руб.;
- текущие затраты при переезде своим ходом руб.;
- продолжительность работы техники в году чгод;
- продолжительность работы техники на одном объекте ч;
где - часовая тарифная ставка машиниста руб.ч;
- продолжительность переезда своим ходом ч;
где - расстояние перебазировки км;
- транспортная скорость кмч;
СЭ = СТР + СТ + ССМ + СМГ + ССО
СТР – затраты на техническое обслуживание текущий ремонт и капитальный ремонт машины руб.;
СТ – затраты на топливо для машины с двигателем внутреннего сгорания руб.;
ССМ – затраты на смазочные материалы;
СМГ – затраты на жидкость для гидросистемы руб.;
ССО – затраты на сменную оснастку руб.
Расчет годовых текущих затрат представлен в табл. 6.2.
Таблица 6.2 – Расчет годовых текущих затрат
Амортизационные отчисления
Заработная плата машинистам
Затраты на ТО ТР и КР
Затраты на сменную оснастку
Затраты на перебазировку
5 Экономическая эффективность новой техники
Удельные приведенные затраты
где С – годовые текущие затраты (себестоимость продукции) связанные с выполнением технологического процесса руб.год;
ЕН – нормативный коэффициент эффективности (минимально допустимая отдача с каждого рубля вложенный в новую технику)
к – капитальные вложения (затраты) связанные с приобретением и эксплуатацией техники руб.;
В – годовая эксплуатационная производительность машины м3год.
Экономический эффект
где и - удельные приведенные затраты рубм3;
- годовая эксплуатационная производительность новой техники м3год;
F - коэффициент суммирования годовых эффектов за срок службы новой техники с учетом факторов времени [3];
А - количество единиц техники.
Определение сравнительной металлоемкости продукции
Металлоемкость (материалоемкость) продукции по базовой и новой технике определяется с учетом затрат материалов запасных частей и комплектующих изделий за весь срок службы техники.
Удельная металлоемкость
где F - масса техники кг;
км - коэффициент использования материала
Экономия материала за год кггод
Определение удельного расхода топлива
где WT - часовой расход топлива кгч.
Годовая экономия топлива
6 Определение основных удельных показателей
Удельные текущие затраты (себестоимость) на измеритель работ определяются по формуле
Удельные капитальные вложения на измеритель работ определяются по формуле
7 Определение дисконтированного экономического
эффекта за период срока службы объекта
Приведем общую сумму экономического эффекта от модернизации базовой техники к текущему периоду с учетом изменения стоимости денег с течением времени.
Дисконтирование является универсальной методикой приведения будущих денежных потоков (в нашем случае будущих экономических эффектов) к настоящему моменту основанной на понятиях сложных процентов. Формула суммарного дисконтированного экономического эффекта выглядит следующим образом [1.8]
где n – число периодов
r – ставка дисконтирования.
Ставка дисконтирования определялась как ставка рефинансирования Центрального банка Российской Федерации увеличенная на процент риска неполучения экономического эффекта в период срока эксплуатации техники.
8 Определение срока окупаемости использования новой техники
Срок окупаемости затрат на приобретение и эксплуатацию новой техники определяется следующим методом
где Змод – затраты на модернизацию базовой техники
Так как сумма дисконтированного экономического эффекта за два года больше затрат на модернизацию следовательно за этот период затраты на модернизацию базовой техники окупятся.
Рентабельность модернизации показывает во сколько раз суммарный дисконтированный экономический эффект от модернизации базовой техники за весь срок эксплуатации превышает затраты на модернизацию.
Рентабельность модернизации рассчитывается по следующей формуле
Содержание 2@.doc
6 Определение основных удельных показателей92
7 Определение дисконтированного экономического
эффекта за период срока службы объекта93
8 Определение срока окупаемости использования
Охрана труда и техника безопасности95
1 Размещение органов управления машиной95
2 Влияние шума на работу оператора96
4 Общие санитарно – гигиенические требования к воздуху
5 Светотехнические приборы машины и освещение
6 Пожарная безопасность100
8 Указание мер безопасности101
9 Расчет автогрейдера на устойчивость104
9.1 Расчет автогрейдера на устойчивость104
9.2 Расчет автогрейдера на устойчивость105
Список использованных источников108
Титульный@.doc
Федеральное государственное бюджетное образовательное учреждение
Высшего профессионального образования
«Воронежский государственный архитектурно – строительный университет»
ПОШВИН АРТЁМ ИВАНОВИЧ
Исследование и модернизация механизма изменения
угла резания отвала автогрейдера
Направление 190100:«Наземные транспортно – технологические комплексы»
Программа 190108 «Машины и оборудование для разработки грунтов»
Диссертация на соискание степени
магистр техники и технологии
Научный руководитель: д.т.н. профессор
кафедры строительной техники и
Жулай Владимир Алексеевич
Заключение.doc
Наибольший эффект данное оборудование дает от применения его у в условиях работы где есть возможность изменения типа грунта.
Большую роль в модернизированном оборудовании играет стабилизация положения ножа отвала в процессе резания. Это значительно облегчает работу оператора и повышает производительность.
Наглядным примером расчета модернизированного узла является САПР APM FEM. Крайне полезно применение современного оборудования для расчета и анализа разрабатываемых машин.
Проведенные экономические расчеты себестоимости и цены изделия позволяют определить годовой экономический эффект в размере 394820 р. при производстве изделия.
Аннотация.doc
Темой данной диссертации предложена модернизация рабочего оборудования с целью повышения эффективности путём стабилизации глубины резания при изменении угла резания отвала в процессе работы.
В пояснительной записке представлены исследования и расчёты: по общим параметрам автогрейдера производительности тяговый на прочность конструкции и механизмов технологического процесса изготовления детали и технико-экономических показателей а так же сведениями об охране труда и технике безопасности. Расчеты на прочность частично произведены в САПР.
На чертежах показана наиболее интересная часть рассмотренных патентов а так же общий вид машины модернизированное рабочее оборудование узлы и подузлы в сборке деталировки 3D модели механизма стабилизации при расчете на прочность технологический процесс изготовления детали технологический процесс производства работ модернизированной машиной и результаты экономического расчета.
5.Технологический процесс изготовления детали.doc
Проектирование технологических процессов изготовления деталей машин имеет цель установить наиболее рациональный и экономичный способ обработки обеспечивающий заданную точность и частоту обрабатываемых поверхностей.
При проектировании технологических процессов необходимо учитывать основные направления в современной технологии машиностроения которые в основном сводятся к следующему:
Возможно большее сокращение обработки металлов резанием путем изготовления заготовок деталей приближающихся по форме размерам и качеству поверхности к готовым деталям.
Применение для механической обработки высокопроизводительного оборудования твердосплавного металлокерамического и алмазного инструмента быстродействующих приспособлений оптимальных режимов резания и более производительных методов обработки.
Применение упрочняющей технологии механическими или термомеханическими способами.
Концентрация операций для одновременной обработки нескольких поверхностей большим количеством инструментов с высокими режимами резания и автоматизацией различных вспомогательных действий.
Автоматизация технологических процессов холодной и горячей обработки деталей.
На характер технологического процесса обработки деталей влияют следующие факторы:
а)объем выпуска деталей;
б)конструктивная форма размер и технологичность детали;
в)вид материала детали и его свойства;
г)форма размер и точность изготовления заготовки;
д)требование к точности и качеству обрабатываемых поверхностей и другие требования по техническим требованиям (балансированность отклонение веса и др.);
е)характер используемого оборудования и технологической оснастки;
ж)требования наибольшей экономичности и производительности.
На основе анализа чертежей была выбрана деталь для разработки технологического процесса её изготовления. Этой деталью является палец блока крюковой обоймы. Эта деталь имеет цилиндрическую форму изготовленную из стали 45 ГОСТ 1050-88.
2 Определение размера партии деталей и типа производства
Годовой объем с учетом поставок запасных частей ремонтных и эксплуатационным хозяйствамрассчитывается по формуле [19]
где m - количество одноименных деталей на одном автомобиле;
- количество изготавливаемых машин за год;
- количество деталей изготавливаемых в качестве запасных частей в процентах;
- процент возможного брака при обработке заготовок;
Размер партии деталей одновременно запускаемых в производство
где - количество рабочих дней на которое надо иметь запас деталей для бесперебойной работы сборочного цеха;
Ф - число рабочих дней в году;
Тип производства приближенно можно определить по программе и количеству деталей в партии. По таблице 2.1. устанавливаем что тип производства - мелкосерийное.
3 Выбор способа получения заготовки
Заготовка получается резкой из проката так как конфигурация детали приближается к круглому сортовому прокату и кроме того нет значительной разницы в поперечных сечениях детали. Следовательно для получения окончательной формы можно избежать снятия большого количества металла.
4 Разработка технологического маршрута обработки детали
в САПР Вертикаль 2013
Технологический маршрут обработки детали в САПР Вертикаль 2013 представлен на рисунке 5.1
Рисунок 5.1 - Технологический маршрут обработки детали
Всякая заготовка предназначенная для дальнейшей механической обработки изготавливается с припуском против размеров готовой детали. Припуск представляет собой слой материала удаляемый при обработке необходим для получения детали заданных размеров и требуемой чистоты её поверхностей. поверхности не подлежащие обработке припусков не имеют.
Определение величины минимального припуска на обработку симметричный припуск на диаметр при обработке наружных и внутренних поверхностей вращения производится по формуле:
- при черновой обработке
где- высота микронеровностей поверхности на предшествующем переходе
- глубина дефектного поверхностного слоя полученного при изготовлении заготовки
- суммарное значение пространственных отклонений взаимосвязанных поверхностей оставшихся после выполнения предшествующего перехода (отклонение от параллельности перпендикулярности соосности симметричности)
где - погрешность установки при выполняемом переходе
при чистовой обработке
Общий припуск на обработку равен сумме промежуточных припусков по всем технологическим переходам процесса обработки - от заготовки до готовой детали.
Действительные припуски на обработку в партии заготовок колеблются в пределах от до .
где - максимальный припуск;
- допуск по размеру на предшествующем переходе мм; (стр. 7-12 13);
- допуск по размеру на выполняемом переходе мм; (стр. 7-12 13).
Чистовая обработка:.
Общий припуск на обработку
Правильность расчётов проверяют по формуле
где - допуск на заготовку
=11 - условие выполняется.
Минимальный диаметр заготовки
Принимаем диаметр заготовки dз = 50мм.
Номинальный припуск [19]
Минимальный припуск на обработку торца заготовки рассчитываем по формуле
где - высота микронеровностей поверхности на предшествующем переходе
- погрешность установки при выполняемом переходе
Максимальный припуск
где - допуск по размеру на предшествующем переходе
- допуск по размеру на выполняемом переходе
Исходя из расчёта припусков в качестве заготовки будем использовать прокат диаметром 50 мм длиной 134 мм.
Для дальнейших расчетов в САПР Вертикаль 2013 воспользуемся следующими исходными данными представленными на рисунке 5.2
Рисунок 5.2 – Исходные данные
6 Расчет режимов резания
Расчет режимов резания в САПР Вертикаль производятся в следующем окне для подрезки торца представленном на рисунке 5.3
Рисунок 5.3 - Расчет режимов резания для подрезки торца в САПР Вертикаль
- при черновой обработке
где dпр - размер заготовки до обработки
dчерн - диаметр детали после черновой обработки
tр=(500-4122)2=44мм;
- при чистовой обработке
Подача при черновой обработке выбирается с учетом ограничивающих се факторов: жесткость и прочность системы СПИД мощность привода станка.
При диаметре заготовки 50 мм и глубине резания tр=44мм подачу для черновой обработке выбираем из интервала S=04-08 ммоб размер державки резца от 16х25 до 25х40 диаметр детали от 40 до 60мм. [13]
Составим ряд подач для станка 1М63:
Так как в справочниках не указаны все значения подач то пользуясь тем что эти величины в станкостроении нормализованы их определяют по коэффициенту геометрической прогрессии согласно зависимости [19]
где j - коэффициент геометрической прогрессии определяемый по формуле [19]
где - соответственно максимальное и минимальное значение подачи
Z - число ступеней подач [13]
Расчетное значение коэффициента корректируется по ближайшему стандартному φ=106.
Принимается S=055 ммоб.
Скорость резания рассчитывается по формуле [14]
где Т - стойкость резца
t - глубина резания
Значение коэффициентов - Сv Kv и показателей степеней m x yv приведены в соответствующих таблицах.
Сv =350; Kv =1; yv =035; m=02;
По расчётной скорости определяем частоту вращения шпинделя
где d - диаметр обрабатываемой поверхности
Полученное значение частоты вращения для станков со ступенчатым его изменением необходимо скорректировать по станку выбирая ближайшее меньшее.
Ряд чисел оборотов определяется так же как и ряд подач.
где nmax nmin - соответственно максимальная и минимальная частота вращения шпинделя
к - число передач вращения шпинделя
n1=10;12.6;15.876;20;25.2;31.8;40.1;50.5;63.6;79.5;100.2;126.3;159.1;200.5;252.6;318.3;401.1;505.4;636.7;789.2;992;1250.
Принимается n= 789 обмин;
Для проверки возможности осуществления выбранных режимов обработки проводится проверка их по ограничивающим факторам. С этой целью прежде всего определяется сила резания.
Значение ее определяется по эмпирическим формулам значение показателей степени в которых для различных видов обработки приведены в таблицах.
Значение коэффициентов - Ср Kр и показателей степеней np x р y р приведены в соответствующих таблицах [14].
Ср =300; Kр =1; yр =075; np =-015;
При обработке резцами прочность проверяется расчетом на изгиб от действия
где В Н - соответственно ширина и высота державки резца
[s] - допустимое напряжение для державки резца
2540000 условие выполняется.
Мощность резания Nрез кВт рассчитывается по формуле :
Расчетная мощность резания Nрез сравнивается с мощностью электродвигателя станка Nэ
условие выполняется.
Режим резания для чистовой обработки
При чистовой обработке резцом максимально допустимая подача исходя из требуемой чистоты обработки определяется по формуле [19]
где - максимальная высота микронеровностей на обрабатываемую поверхность
r - радиус закругления при вершине резца в плане
j j1 - соответственно главный и вспомогательный угол в плане резца в градусах;
Cn y = 14; u = 07; z= 035. [19];
принимаем S=029мм об.
Скорость резания рассчитывается по формуле:
Сv =300; Kv =1; yv =02; m=02;
где d - диаметр обрабатываемой поверхности
Принимается n=1250 обмин;
Тогда действительная скорость
Сила резания по формуле (4.22)
Значение коэффициентов - Ср Kр и показателей степеней np x р y р приведены в соответствующих таблицах.
Ср =300; Kр =1; yр =075; np =-015.
При обработке резцами прочность проверяется расчетом на изгиб от действия ;
740000 условие выполняется.
Мощность резания по формуле (5.25)
Расчетная мощность резания Nрез сравнивается с мощностью электродвигателя станка Nэ [14]
Режим резания для сверлильной операции
Глубина резания определяется по формуле
где D- диаметр инструмента
Максимально допустимая подача по табл.27 14- S=018-028ммоб.
Станок вертикально сверлильный 2Н118 сверло диаметром 8мм материал быстрорежущая сталь Р18.
Составим ряд подач для станка.
Так как в справочниках не указаны все значения подач то пользуясь тем что эти величины в станкостроении нормализованы их определяют по коэффициенту геометрической прогрессии согласно зависимости
где j - коэффициент геометрической прогрессии определяемый по формуле (4.19)
z - число ступеней подач
S1=0.1;0.14;0.2;0.28;0.4;0.56.
Принимаем S=020ммоб.
Значение коэффициентов - Сv Kv и показателей степеней qv m x yv приведены в соответствующих таблицах.
Сv =7;; yv =07; m=02 qv=0.4 ; ;
По расчётной скорости определяем число оборотов сверла
где d – диаметр сверла
где nmax nmin- соответственно максимальная и минимальная частота вращения шпинделя
n1=180;254;358;504;710;1000;1410;1987;2800
принимается n=254 обмин;
Крутящий момент и усилие при сверлении определяется по формуле
Значение коэффициентов - Сm Kp Ср и показателей степеней qm ym qp yр приведены в соответствующих таблицах [14].
Сm =0.0345; Ср =68; ym =08; m=02; qv=0.4; qp=10; yр=07;
Мощность резания Nрез кВт рассчитывается по формуле
Расчетная мощность резания Nрез сравнивается с мощностью электродвигателя станка Nэ ;
7 Расчет нормы времени
Определение нормы времени и квалификации рабочего на сверлильную операцию
Норма штучного времени на операцию подсчитывается по формуле [8]
где to - основное (технологическое) время;
tв - вспомогательное время;
tТО - соответственно время технического и организационного обслуживания рабочего места;
tср- время перерывов на отдых и физические потребности.
Основное время сверления определяется по формуле для глухих отверстий
где l- длина отверстия
l1- величина врезания
n- число оборотов инструмента в минуту
s- подача инструмента на оборот
Вспомогательное время затрачивается на выполнение вспомогательных переходов: установку переустановку и снятие заготовки пуск и остановку станка изменение режимов обработки в процессе выполнения операций измерения и контроль качества заготовки готовой детали и т.д.
Вспомогательное время определяется по нормативам.
tв=005+004+002+002+003+004+004+014+003=041мин
Сумма основного и вспомогательного времени составляет оперативное время
Время организационного и технического обслуживания рабочего места и перерывов определяется по нормативам
где %- доля от основного времени
Время перерывов на отдых и физические потребности
Нормирование по штучному времени производится в массовом производстве. В серийном производстве определяется штучно-калькуляционное время
где tпз- подготовительно-заключительное время
n - количество деталей в партии
Подготовительно-заключительное время затрачиваемое на получение задания знакомство с работой наладку оборудования и приспособлений сдачу выполненной работы и т.д. определяется по нормативам
Разряд сверловщика - 3 по тарифно-квалификационному справочнику.
Определение нормы времени и квалификации рабочего на токарную операцию
Норма штучного времени на операцию подсчитывается по формуле (5.33):
Основное время при черновом точении определяется по формуле
где l- длина обрабатываемой поверхности в направлении подачи
l1 - величина врезания инструмента
l2 - величина вывода инструмента
l3 – длина проходов при взятии пробных стружек
S- подача резца на один оборот
- число оборотов детали в минуту
Основное время при чистовом точении определяется по формуле
Основное время сверления определяется по формуле для глухих отверстий
S- подача инструмента на оборот
Основное время рассверливания определяется по формуле для сквозных отверстий
Основное время на подрезание торца определяется по рекомендациям
Тогда основное время на всю операцию
Вспомогательное время определяется по нормативам
где α- доля от основного времени
В серийном производстве определяется штучно-калькуляционное время
Разряд токаря - 4 по тарифно-квалификационному справочнику.
Библиограф. список@.doc
Номенклатурный каталог. Строительные дорожные мелиоративные лесо - и торфозаготовительные коммунальные ручные отделочные машины оборудование для производства стройматериалов лифты пожарная техника кондиционеры и вентиляторы. М.: Минстроймаш 1990.
Никулин П.И. Гильмутдинов В.И. Литвинов В.С. Расчет и построение тяговой характеристики землерейно-транспортной машины с гидромеханической трансмиссией. Методические указания к курсовому и дипломному проектированию. Воронеж: ВГАСА 1993. – 30 с.
Ульянов Н.А. Теория самоходных колесных землерейно-транспортных машин. М.: Машиностроение 1969. - 520 с.
Алексеева Т.В. Артемьев К.А. Бромберг А.А. Дорожные машины машины для земляных работ (теория и расчет). М.: Машиностроение 1969. - 520 с.
Бородачев И.П. Справочник конструктора дорожных машин. М.: Машиностроение 1964. - 591 с.
Решетов Д.Н. Детали машин. М.: Машиностроение 1975. – 650 с.
Артобалевский И.И. Теория механизмов и машин. М.: Науки 1988. - 640 с.
Биджиев Р.Х. Расчет центрально сжатых стержней на устойчивость. Методичексие указания. Воронеж: ВГАСА 1999. - 24 с.
Шамаев И.А. Проектирование технологических процессов изготовление детали. И.А. Шамаев : Методический указания по дипломному проекту. - Ворорнеж : ВИСИ 1974.
Справочник технолога-машиностроителя. Под ред. Косиловой О.К. Мещерикова. -М.: Машиностроение Т.2 1986. – 496с.
Трухин Н.И Овсенников И.С. Чугунов А.В. Выполнение экономических расчетов в дипломном проекте: Метод. указания Воронежский ГАСУ- Воронеж 2011.-43с.
Жулай В.А. Бузин Ю.М. Геращенко В.Н. Щиенко А.Н. Дипломное проектирование по специальности 19205: Требования к сосвтаву и оформлению: учебно-методическое пособие 2-е издание; Воронежский ГАСУ- Воронеж 2010-66с.
5...2.Общий расчет.doc
1 Тяговый расчет автогрейдера ДЗ-143
Движение машины возможно если максимальное тяговое усилие Тmах (Н) будет не меньше суммарного сопротивления движению W(Н):
Установлено что при = 01 колесный движитель работает с максимальным КПД при = 02 достигается максимальная тяговая мощность при = 03 развивается наибольшая устойчивая сила тяги.
Усилие Тmах ограничено двумя факторами - мощностью привода ходового устройства и условиями сцепления движителя с опорным основанием с которыми оно связано зависимостями:
Тmах(Рх) = 1000 Рх х v; (2.1)
Тmах(φ) = G φ (2.2)
где Рх - суммарная мощность двигателей механизма передвижения
х - общий КПД механизма передвижения (табл. 2.3);
φ - коэффициент сцепления движителя с основанием (табл. 2.1);
v - скорость передвижения (мс).
Шинноколесный движитель
рыхлый свежеотсыпанный
слежавшийся уплотненный
Значения коэффициентов k (при ) и kn
Величины необходимые для расчета
Основные параметры и характеристики двигателя Д-260.2
Наименование параметров
Четырехтактный дизель с турбонаддувом
Способ смесеобразования
Непосредственный впрыск топлива
Расположение цилиндров
Рабочий объем цилиндров
Порядок работы цилиндров
Направление вращения коленчатого вала (со стороны вентилятора)
Степень сжатия (расчетная)
Допустимые углы наклона при работе: продольный поперечный
Мощность номинальная
Мощность эксплуатационная
Номинальная частота вращения
Мин. устойчивая частота вр-я хол. хода
Максимальная частота вращения холостого хода ограничиваемая регулятором
Частота вращения при максимальном значении крутящего момента
Максимальный крутящий момент
Удельный расход топлива при номинальной мощности
Удельный расход топлива при эксплуатационной мощности
Давление масла в главной магистрали при:номинальной частоте вращения минимальной частоте вращения
не заправленного горючесмазочными материалами и охлаждающей жидкостью
Для шинноколесных движителей v - теоретическая скорость (мс):
где rc - силовой радиус м;
пд - номинальная частота вращения вала двигателя ходового механизма (обмин);
и - передаточное число трансмиссии.
Силовой радиус определяется как радиус недеформированного колеса rо за вычетом наибольшей радиальной деформации шины (в центральной зоне контактной поверхности) λ (м):
Приближенно при движении по плотному грунту λ = (012 015) В; по рыхлому грунту - λ = (008 01) В (В - ширина профиля шины).
Фактическую скорость передвижения шинноколесной машины определяют с учетом буксования по формуле (мс):
vф = v (1 - ) (2.4)
где - коэффициент буксования.
Совместив необходимые формулы рассчитываем vф:
Полученное значение соответствует I передаче автогрейдера (табл. 2.4).
Имея необходимые показатели рассчитываем усилие (Тmах(Рх)) мощности привода ходового устройства и усилие (Тmах(φ)) сцепления движителя с опорным основанием:
Для дальнейших расчетов берем меньшее из полученных значений.
Сопротивление передвижению W (Н) складывается из сопротивлений на рабочем органе машины Wp (Н) передвижению (перекатыванию) движителей Wпep (H) по горизонтальному пути повороту машины Wnoв (H) движению на уклоне местности Wу (Н) инерции при разгоне и торможении Wи (H) и ветрового давления WB (H):
W = Wp + Wпep + Wnoв ± Wу ± Wи + WB . (2.5)
Из этого набора сопротивлений удерживаются только те сопротивления которые имеют место в конкретном транспортном режиме работы машины.
Сопротивление повороту колесных машин (рыхлый грунт);
Wnoв = (025 . . . 05) Wпep . (2.6)
Сопротивление движению от уклона местности ;
Wу = ± тg sinα (2.7)
где т - масса машины кг;
g - ускорение свободного падения g = 981 мс2;
α - угол подъема пути машины (+) на подъем (-) под уклон.
Сопротивление сил инерции при разгоне и торможении:
Wи = ± m v tр(т) (2.8)
где v - скорость в конце разгона или начале торможения (мс):
tр(т) - продолжительность разгона (торможения) (с).
Сопротивление ветрового давления:
где S - площадь воспринимающая давление ветра (м2);
qB =125 – 500 - распределенная ветровая нагрузка на 1 м2 (Па).
Сопротивления Wnoв Wу WB и Wи в данном тяговом расчете не учитываются так как по условию участок горизонтальный автогрейдер движется с равномерной скоростью а разворот совершается после выполнения операций (резание транспортировании укладке) а сопротивление ветрового давления незначительно при данной скорости.
Сопротивление резанью:
где k – коэффициент сопротивления резанью (табл. 2.2);
В – ширина отвала (м);
h1 – глубина резания во время перемещения призмы грунта (м2).
где kn – коэффициент потерь грунта при перемещении (табл. 2.2)
Vпр – объем призмы волочения(м3).
Вычисляем объем призмы волочения:
Вычисляем глубину резания во время перемещения призмы грунта:
Вычислив необходимые величины находим сопротивление резанью:
Сопротивление перекатыванию:
где f- коэффициент сопротивления передвижению движителей (табл. 2.1);
G - вертикальная составляющая внешней нагрузки на движители (Н)
Подставив значения необходимых усилий находим сопротивление перемещению W (H):
Проверяем соответствие условию Тmах ≥ W:
Условие соблюдено тяговые характеристики автогрейдера подходят для работы в заданных условиях. Неудовлетворение указанному выше условию по тяговому усилию Тmах(Рх) означает недостаток мощности для движения машины с заданной скоростью v. Если то же условие не удовлетворяется по усилию Тmах(φ) то это означает что машина не может двигаться из-за буксования движителей.
1.Титульный.doc
Федеральное государственное бюджетное образовательное учреждение высшего профессионального образования
«ВОРОНЕСКИЙ ГОСУДАРСТВЕННЫЙ АРХИТЕКТУРНО-СТРОИТЕЛЬНЫЙ УНИВЕРСИТЕТ»
КАФЕДРА СТРОИТЕЛЬНОЙ ТЕХНИКИ И ИНЖЕНЕРНОЙ МЕХАНИКИ
Курсовой проект по дисциплине
«Конструирование и расчёт НТТМ (машин для разработки грунта)»
Модернизация рабочего оборудования автогрейдера ДЗ - 143
Магистрант группы М1986
2.Содержание.doc
автогрейдеров с патентным исследованием 5
1 Назначение автогрейдера ДЗ-143 .. 5
2 Основное рабочее оборудование автогрейдера 6
3 Проведение патентного поиска 8
Расчёты на прочность отвала и механизма стабилизации .17
Расчёты технических показателей автогрейдера . ..20
Библиографический список .. ..24
4...1.Анализ конструкций.doc
1 Назначение автогрейдера ДЗ-143
Основным назначением автогрейдера ДЗ-143 является профилирование земляного полотна строительство грунтовых дорог на нулевых отметках или на насыпях воздвигаемых из грунта кюветов планировка грунтовых поверхностей.
Рисунок 1.1 – Автогрейдер
Выполнение всех функций грейдера происходит с помощью специального рабочего органа— отвала с ножом который смонтирован на раме машины. Его можно поднимать опускать поворачивать в горизонтальной и вертикальной плоскости.
2 Основное рабочее оборудование автогрейдера
Автогрейдеры имеют три вида рабочего оборудования: отвал рыхлитель-кирковщик бульдозер. Помимо перечисленных видов рабочего оборудования автогрейдеры могут оснащаться откосником кюветоочистителем снегоочистителем.
Грейдерный отвал – основной рабочий орган машины и его главное достоинство – способность занимать в пространстве практически любое положение. Он может вращаться в горизонтальной плоскости на 360° в любом направлении становиться вертикально справа или слева от автогрейдера выдвигаться вправо или влево более чем на треть своей длины поворачиваться вокруг собственной режущей кромки. А получил он такую замечательную возможность благодаря системе крепления отвала к раме машины.
Главная особенность системы крепления заключена в том что собственно отвал является частью узла основу которого составляет тяговая рама автогрейдера представляющая собой А- или Т-образную в плане металлоконструкцию сваренную из балок коробчатого сечения и шарнирно прикрепленную к передней части основной рамы (хребтовой балки) машины в одной точке над осью передних колес. Для крепления тяговой рамы используется универсальный шарнир позволяющий ей поворачиваться во все стороны и вращаться вокруг собственной продольной оси. Прочность шарнира вполне соответствует усилиям возникающим на отвале.
Широкая сторона тяговой рамы поддерживается двумя гидроцилиндрами подъемаопускания отвала (левым и правым). Вместе эти устройства образуют своеобразный рычажный механизм жесткость которому в поперечном направлении придает еще один гидроцилиндр служащий для выноса тяговой рамы в сторону и образующий диагональ «четырехугольника». Такая система обеспечивает раме большие возможности перемещения диапазон которых резко увеличивается если гидроцилиндры подъемаопускания отвала и гидроцилиндр выноса тяговой рамы крепятся к скобе вращающейся вокруг хребтовой балки машины.
К тяговой раме крепятся скользящие опоры (пять и более) поддерживающие большое зубчатое колесо с внешним или внутренним зацеплением – поворотный круг к которому прикреплен отвал вращающийся относительно тяговой рамы благодаря гидромотору или гидроцилиндрам. Особенности крепления отвала к поворотному кругу позволяют поворачивать его относительно режущей кромки и сдвигать относительно круга влево или вправо.
Рисунок 1.2 - Рабочее оборудование
-тяговая рама; 2-поворотный круг; 3-гидроцилиндр выноса отвала; 4-гидравлический шарнир; 5-шарнир; 6-водило; 7-редуктор поворота отвала; 8-палец; 9-крышка; 10-шарнир; 11-отвал; 12-кронштейн; 13-гидроцилиндр изменения угла резания отвала; 14-кронштейн; 15-регулировочный болт; 16-накладка; 17-болт; 18-регулировачная прокладка; 19-зубчатый венец
Основным рабочим органом автогрейдера является отвал (рис.129) который состоит из трех сборочных единиц: тяговой рамы поворотного круга непосредственно отвала. Тяговая рама имеет треугольную форму. В ее передней части имеется шарнир с крышкой для соединения с головкой основной рамы. Снизу к раме приварены плиты для крепления поворотного круга. На передней плите крепится редуктор поворота отвала. Поворотный круг состоит из кольца с приваренными лапами зубчатого венца прикрепленного к кольцу болтами. Такое устройство поворотного круга позволяет изменять положение венца относительно круга при неравномерном износе зубьев. К тяговой раме поворотный круг крепится накладками с регулировочными болтами. Отвал крепится к поворотному кругу двумя кронштейнами установленными на штанге поворотного круга. Отвал снащен основными и боковыми ножами реверсивного типа. При износе режущей кромки основных ножей перестановка их производится переворачиванием. Боковые ножи при износе их режущей кромки переставляют выдвижением смещая на одно отверстие вниз или переворачиванием. Изменение угла резания отвала производится гидроцилиндрами этим же гидроцилиндром отвал выносится относительно тяговой рамы в обе стороны. Съемный кронштейн для крепления головки штока гидроцилиндра на отвале может быть передвинут. Поворот отвала в плане осуществляется редуктором цилиндрическая шестерня которого входит в зацепление с зубчатым венцом поворотного круга. Гидравлический шарнир закрепленный на поперечной балке тяговой рамы обеспечивает пропуск рабочей жидкости к гидроцилиндрам изменения угла резания отвала и его выноса.
Редуктор поворота отвала закреплен на тяговой раме болтами и шпильками. Основными его деталями являются корпус червячное колесо червяк крышки подшипники валы шестерня. Посредством втулки и муфты червяк соединяется с валом гидромотора.
3 Проведение патентного поиска
В ходе проведённого поиска патентной информации был принят к сведению материал следующего авторского свидетельства.
Авторское свидетельство № 1315569
Цель изобретения – повышение эффективности путём стабилизации глубины резания при изменении угла резания отвала в процессе работы.
Рисунок 1.3 – Рабочий орган. Авторское свидетельство № 1315569
Изобретение относится к землеройно – транспортным машинам и повышает эффективность путём стабилизации глубины резания при изменении угла резания отвала в процессе работы. Оборудование автогрейдера включает поворотный круг 1 с кронштейном 2 отвал 3 и гидроцилиндр (ГЦ) 5 изменения угла резания. Отвал 3 нижней частью посредством двуплечего рычага 9 шарнирно соединён со свободным концом кронштейна 2. С корпусом ГЦ 5 шарнирами 12 и 13 соединена тяга 11 управления. Шток ГЦ 5 шарнирно соединён с тягой 11. Отвал 3 поворачивается в шарнире 8 по часовой стрелке увеличивая угол резания и глубину. Корпус ГЦ 5 поворачивается в шарнире 6 по часовой стрелке перемещая через шарнир 13 тягу 11 вниз. Рычаг 9 поворачивается в шарнире 10 против часовой стрелки а отвал 3 перемещается вверх уменьшая глубину резания. 2 з.п ф – лы 2 ил.
Изобретение относится к землеройно – транспортным машинам в частности к управлению рабочими органами автогрейдеров предназначенных для использования главным образом в дорожном строительстве.
Механизм изменения угла резания отвала автогрейдера содержит поворотный круг 1 с кронштейном 2 отвал 3 соединённый в верхней части шарниром 4 со штоком гидроцилиндра 5 корпус которого в шарнире 6 соединён с неподвижным кронштейном 7 поворотного круга 1. Гидроцилиндр 5 может быть установлен в середине отвала 3 или в количестве двух штук по его краям. В нижней части отвал 3 соединён в шарнире 8 с двуплечим рычагом 9 который в шарнире 10 соединён со свободным концом кронштейна 2 поворотного круга 1. Привод двуплечего рычага 9 осуществляется от корпуса гидроцилиндра 5 тягой 11 управления соединённой с ними в шарнирах 12 и 13.
Предлагаемый механизм является шестизвенным с одной степенью свободы (ведущее звено – шток с поршнем гидроцилиндра 5 ведомое звено – отвал 3 неподвижное звено – поворотный круг 1 с кронштейнами 2 и 7).
8.Библ список.doc
Номенклатурный каталог. Строительные дорожные мелиоративные лесо - и торфозаготовительные коммунальные ручные отделочные машины оборудование для производства стройматериалов лифты пожарная техника кондиционеры и вентиляторы. М.: Минстроймаш 1990.
Никулин П.И. Гильмутдинов В.И. Литвинов В.С. Расчет и построение тяговой характеристики землерейно-транспортной машины с гидромеханической трансмиссией. Методические указания к курсовому и дипломному проектированию. Воронеж: ВГАСА 1993. – 30 с.
Ульянов Н.А. Теория самоходных колесных землерейно-транспортных машин. М.: Машиностроение 1969. - 520 с.
Алексеева Т.В. Артемьев К.А. Бромберг А.А. Дорожные машины машины для земляных работ (теория и расчет). М.: Машиностроение 1969. - 520 с.
Бородачев И.П. Справочник конструктора дорожных машин. М.: Машиностроение 1964. - 591 с.
Решетов Д.Н. Детали машин. М.: Машиностроение 1975. – 650 с.
Артобалевский И.И. Теория механизмов и машин. М.: Науки 1988. - 640 с.
Биджиев Р.Х. Расчет центрально сжатых стержней на устойчивость. Методичексие указания. Воронеж: ВГАСА 1999. - 24 с.
Трухин Н.И Овсенников И.С. Чугунов А.В. Выполнение экономических расчетов в дипломном проекте: Метод. указания Воронежский ГАСУ- Воронеж 2011.-43с.
Жулай В.А. Бузин Ю.М. Геращенко В.Н. Щиенко А.Н. Дипломное проектирование по специальности 19205: Требования к сосвтаву и оформлению: учебно-методическое пособие 2-е издание; Воронежский ГАСУ- Воронеж 2010-66с.
Шамаев И.А. Проектирование технологических процессов изготовление детали. И.А. Шамаев : Методический указания по дипломному проекту. - Ворорнеж : ВИСИ 1974.
Справочник технолога-машиностроителя. Под ред. Косиловой О.К. Мещерикова. -М.: Машиностроение Т.2 1986. – 496с.
7...4.Техн. показ..doc
Расчёт производительности и продолжительности цикла
Производительность является важнейшей выходной характеристикой машины. Ее определяют количеством продукции произведенной машиной в единицу времени.
Различают расчетную (теоретическая или конструктивная) техническую и эксплуатационную производительность. Под расчетной (теоретической конструктивной) производительностью понимают производительность за 1 ч непрерывной работы при расчетных скоростях рабочих движений расчетных нагрузках на рабочем органе и расчетных условиях работы. Теоретическую производительность рассчитывают на стадии разработки конструкторской документации на машину используя для этого нормативные значения расчетных параметров и расчетных условий. Под технической производительностью понимают максимально возможную в данных производственных условиях производительность при непрерывной работе машины. Под эксплуатационной производительностью понимают фактическую производительность машины в данных производственных условиях с учетом ее простоев и неполного использования ее технологических возможностей.
Производительность определяем по формуле (м3ч):
П = 3600Vпp × ky × kи (tцkp) (4.1)
где Vпp – объем грунта в разрыхленном состоянии (объем призмы волочения) находящийся перед отвалом в конце транспортирования м3;
tц – продолжительность цикла с;
ky – коэффициент уклона (kу=1 так как участок горизонтальный);
kи – коэффициент использования автогрейдера во времени(kи =085);
kp – коэффициент разрыхления грунта т.е. отношение объема разрыхленного грунта к объему грунта такой же массы в естественно плотном состоянии ( kp =1085 табл. 4.1).
Средние значения коэффициента разрыхления kp
Категория породы по трудности разработки
Разновидность горной породы
Песок супесок растительный грунт торф
Легкий и лессовидный суглинок влажный рыхлый лёсс мягкий солончак гравий мелкий и средний песок супесок и растительный грунт смешанные со щебнем и галькой насыпной слежавшийся грунт с примесью щебня или гальки
Жирная мягкая глина тяжелый суглинок гравий крупный галька мелкая щебень крупностью 15 40 мм суглинок со щебнем пли галькой
Объем призмы волочения (м3):
V'пр = BH2(2kпр) (4.2)
где В и Н – ширина и высота отвала м (табл.4.2);
kпр – коэффициент призмы установленный экспериментально и зависящий от свойств грунта и соотношения размеров отвала (табл.4.2 ).
kпр =HB=062 374=0165 (115)
V'пр = 3740622(2115)=062 м3.
Коэффициент призмы kпр
Значение kпр при отношении HB
Продолжительность цикла (с):
tц = l1u1 + l2u2 + l3u3 + l4u4 + nпtп + nоtо + nповtпов (4.3)
l4= l1+ l2+ l3=10+40+15=65 м
u1=19 u2=u3=35 u4=uмах=117 – скорости движения на соответствующих участках пути мс (табл. 4.3);
tп – время на переключение передач (tп 25с);
tо – время опускания и подъема отвала (tо 45с);
tпов – время разворота автогрейдера на 180° (tпов 125с);
nп=3 nо=5 nпов=2 – соответственно количество переключений передач подъемов и опусканий отвала и разворотов на 180°.
В итоге время цикла tц и производительность П будут равны
tц= 1019 + 4035 + 1564 + 65117 + 325 + 545 + 2125796 с
П = 3600Vпp × ky × kи (tцkp)= 3600062 1085 (796115)=346 м3ч
Параметры автогрейдера ДЗ-143
Скорости движения мс
6...3.Прочность.doc
1 Расчёт отвала и механизма стабилизации
Расчёт отвала следует проводить с учётом нагружения его максимальной реакцией грунта Рх приложенной к концу отвала находящегося в положении наибольшего выноса в сторону относительно кронштейнов (рис.3.1). При этом считают что сила Рх действует по оси симметрии отвала изгибая его в горизонтальной плоскости и пренебрегают возникающими в нём напряжениями от кручения. Таким образом расчёт отвала сводится к расчёту его на изгиб как консоли.
Изгибающий момент в опасном сечении I-I
Рх принимают равной 926кН так как она максимальна при первом расчётном положении.
здесь Lотв = 372м – длина отвала;
l1 = 15м – расстояние между опорами отвала.
Рис.3.1 Схема сил для расчёта отвала
Под действием силы Рх в волокнах части сечения расположенной справа от нейтральной линии ОО возникнут напряжения растяжения а в части расположенной слева от сечения - напряжения сжатия.
Момент инерции в сечении I-I:
где = 001м – толщина отвала;
R0 = 058м – средний радиус кривизны сечения отвала.
Тогда моменты сопротивления зон растяжения и сжатия сечения определяют по выражениям:
где 0 = расстояние от х до
нейтральной линии ОО; (3.5)
Нормальные напряжения:
в растянутых волокнах
Полученные напряжении необходимо сравнить с допускаемыми и убедиться что они не превышают последних.
Определяем приведенное напряжение по формуле [11]:
Определяем коэффициент запаса прочности по формуле:
гдет – предел текучести стали 09Г2С по ГОСТ 380-71 т =325 МПа
Отвал из выбранного материала и выбранной толщины отвала удовлетворяет условиям прочности расчёта.
Коэффициент запаса прочности большой значит можно уменьшить толщину стенки или выбрать другой менее прочный материал что приведёт к уменьшению металлоёмкости и капиталовложений в производимый отвал.
Так как характеристики дополнительного отвала такие же как у основного то дополнительный отвал принимаю такой же.
3.Введение.doc
Так как парк машин для земляных работ очень велик и разнообразен как по функциям так и по устройству конструкции машин в данной курсовой работе рассмотрим одну из машин данного класса а именно автогрейдер марки ДЗ-143. Так как автогрейдеры оснащают различным сменным дополнительным оборудованием (до 20 видов) область применения их очень широка.
В данном курсовом проекте рассматривается изобретение для рабочего оборудования автогрейдера повышающее эффективность путём стабилизации глубины резания при изменении угла резания отвала в процессе работы. Автогрейдер является одной из распространённых и востребованных машин что доказывает актуальность данной курсовой работы.
Курсовой автогрейдер.doc
АВТОГРЕЙДЕРА ДЗ-143 . 3
1 Назначение автогрейдера ДЗ-143 . 3
2 Состав автогрейдера ДЗ-143 . 4
3 Установка силовая автогрейдера ДЗ-143 . 8
4 Кинематическая схема автогрейдера ДЗ-143 11
5 Рабочий цикл автогрейдера ДЗ-143 . 12
ТЕХНИКО-ЭКСПЛУАТАЦИОННЫЕ ПОКАЗАТЕЛИ
АВТОГРЕЙДЕРА ДЗ-143 .. 13
1 Тяговый расчет . 14
2 Расчет производительности автогрейдера . 18
ТЕХНИКА БЕЗОПАСНОСТИ ПРИ ЭКСПЛУАТАЦИИ АВТОГРЕЙДЕРА ДЗ-143 .. 21
СПИСОК ИСПОЛЬЗУЕМОЙ ЛИТЕРАТУРЫ 23
В настоящее время ни одно строительство не обходится без земляных работ и машин выполняющих эти работы (кусторезы бульдозеры рыхлители экскаваторы скреперы и т. д.). Рост темпов объёмов строительства усложнения конструкции возводимых сооружений только увеличил интерес и потребность в машинах для земляных работ.
На сегодняшний день их производством занимается немало компаний с мировыми именами. Некоторые из них используют свои собственные оригинальные разработки и создают конструктивные особенности этих машин но в целом принципы их устройства и сферы применения являются одинаковыми.
Так как парк машин для земляных работ очень велик и разнообразен как по функциям так и по устройству конструкции машин в данном курсовом проекте рассмотрим одну из машин данного класса а именно автогрейдер марки ДЗ-143. Так как автогрейдеры оснащают различным сменным дополнительным оборудованием (до 20 видов) область применения их очень широка. Автогрейдер является одной из распространённых и востребованных машин что доказывает актуальность данного курсового проекта.
КОНСТРУКТИВНЫЕ ОСОБЕННОСТИ И РАБОТА АВТОГРЕЙДЕРА ДЗ-143
1 Назначение автогрейдера ДЗ-143 [3]
Основным назначением автогрейдера ДЗ-143 является профилирование земляного полотна строительство грунтовых дорог на нулевых отметках или на насыпях воздвигаемых из грунта кюветов планировка грунтовых поверхностей. Автогрейдер может быть использован для киркования (рис.1.1 а) грунта и изношенного полотна дорог а также для перемешивания грунтов с добавками и вяжущими материалами на полотне дороги. Все рабочие операции автогрейдеры осуществляют при продольных проходах машин с помощью основного рабочего оборудования – отвала с различными приспособлениями (уширителем удлинителем откосником кювето-очистителем) и навесного оборудования (бульдозерного отвала рыхлителя (рис.1.1 б) снегоочистителя смесителя и пр.)
Рисунок 1.1- навесное оборудование автогрейдера
а) рыхлитель; б) кирковщик
2 Состав автогрейдера ДЗ-143 [123]
Автогрейдер ДЗ-143 представляет собой самоходную колесную землеройно-транспортную машину с отвальным рабочим органом.
Рисунок 1.2 – автогрейдер ДЗ-143 вид сбоку
Автогрейдер ДЗ-143 состоит из следующих основных частей:
Длинной и выгнутой в средней части основной рамы 1 служащей для установки на ней всех механизмов автогрейдера и опирающейся сзади на заднюю тележку 10 снабжённую балансирами с ведущими колёсами 8 а спереди на переднюю ось 4 с управляемыми колёсами; двигателя 14 закреплённого сверху рамы над задней тележкой; трансмиссии передающей вращение от двигателя к ведущим колёсам гидронасосам и пр.; грейдерного отвала 7 расположенного в пространстве под выгнутой узкой в плане частью рамы называемой хребтовой балкой на специальной тяговой раме 6 закреплённого с помощью сферического шарнира на концевой части хребтовой балки над передней осью и двух гидроцилиндров подъёма отвала 2 установленных на кронштейнах с двух сторон хребтовой балки в её самой приподнятой части; кабины 11 с органами и пультом управления и сиденьем машиниста; отвала бульдозера 5 гидроцилиндра 12 для их привода; капота 9 с откидными стенками закрывающего двигатель; электросистемы сигнализации и освещения13.
При такой компоновке создаётся полезная нагрузка на ведущие колёса и кроме того из кабины машиниста открывается достаточно хороший обзор по ходу машины и на всю зону расположения отвала что позволяет машинисту автогрейдера непосредственно наблюдать за самим процессом обработки грунта на дороге при любых положениях отвала в пространстве.
Таблица 1.1 – техническая характеристика автогрейдера ДЗ-143
Эксплуатационная масса кг
Мощность кВт (л. с.)
Число передач: впередназад
Максимальная скорость кмч
«Брянский завод дорожных машин»
К конструктивным особенностям автогрейдера можно отнести изогнутую форму основной рамы в изгибе которой расположен отвал (рис.1.3.а) устанавливающийся с различными углами в горизонтальной и вертикальной плоскостях а так же балансирную заднюю подвеску для лучшего вписывания в неровности и увеличения сцепления колес с поверхностью (рис.1.3.б). С целью повышения поперечной устойчивости на наклонных поверхностях на автогрейдере предусмотрен наклон передних колёс осуществляемый с помощью специального механизма (рис.1.3.в). Благодаря наклону передние колёса всегда занимают вертикальное положение на уклонах поэтому машина более устойчива к поперечному опрокидыванию.
Рисунок 1.3 – конструктивные особенности автогрейдера
а) - схема основной рамы; б) - схема балансирной подвески; в) - схема работы механизма наклона передних колес
Благодаря размещению рабочего органа—отвала приблизительно посередине колесной базы и балансирной подвеске задних колес вертикальные перемещения режущей кромки при преодолении колесами неровностей существенно меньше высоты неровностей что обеспечивает после каждого прохода автогрейдера выравнивание поверхности грунта (рис.1.4).
Рисунок 1.4 - схема работы автогрейдера
3 Установка силовая [4]
В качестве силовой установки на автогрейдер ДЗ-143 установлен дизельный двигатель Д-260.2. Двигатель рассчитан на эксплуатацию при температуре окружающего воздуха от -45 до +40 °С. Конструкция двигателя рассчитана на длительную работу без капитального ремонта при условии соблюдения правил эксплуатации хранения и своевременного технического обслуживания.
- форсунка; 2 - головка цилиндров; 3 - стартер; 4 - маховик; 5 - картер масляный; 6 - пробка; 7 - блок цилиндров; 8 - фильтр топливный тонкой очистки; 9 - топливный насос высокого давления; 10 -топливный насос; 11 - турбокомпрессор;12 - вентилятор; 13 - генератор; 14 - фильтр масляный центробежный; 15-фильтр очистки масла; 16-фильтр грубой очистки топлива; 17-масломерный щуп; 18-заливная горловина
Рисунок 1.5 - общий вид двигателя Д-260. 2
Таблица 1.2 - основные параметры и характеристики двигателя Д-260.2
Наименование параметров
Четырехтактный дизель с турбонаддувом
Способ смесеобразования
Непосредственный впрыск топлива
Расположение цилиндров
Рабочий объем цилиндров
Порядок работы цилиндров
Направление вращения коленчатого вала (со стороны вентилятора)
Степень сжатия (расчетная)
Допустимые углы наклона при работе: продольный поперечный
Мощность номинальная
Мощность эксплуатационная
Номинальная частота вращения
Минимальная устойчивая частота вращения холостого хода
Максимальная частота вращения холостого хода ограничиваемая регулятором
Частота вращения при максимальном значении крутящего момента
Максимальный крутящий момент
Удельный расход топлива при номинальной мощности
Удельный расход топлива при эксплуатационной мощности
Давление масла в главной магистрали при:номинальной частоте вращения минимальной частоте вращения
не заправленного горючесмазочными материалами и охлаждающей жидкостью
Рисунок 1.6 - продольный разрез двигателя Д-260.2
- масляный картер; 2 - масляный насос; 3 - демпфер; 4 - шкив коленчатого вала; 5 - ремень вентилятора; 6 - крышка распределения; 7 - шкив натяжной; 8 - форсунка для охлаждения поршня; 9 - вентилятор; 10 - водяной насос; 11 - корпус термостатов; 12 - шатун; 13 - поршень; 14 - гильза цилиндров; 15 -колпак; 16 крышка головки цилиндров; 17 - головка цилиндров; 18 - блок цилиндров; 19 - задний лист; 20 - маховик; 21 - коленчатый вал; 22 - маслоприемник; 23 - распределительный вал
4 Кинематическая схема автогрейдера ДЗ-143
Рисунок 1.7 – кинематическая схема автогрейдера ДЗ-143
I – двигатель Д-260.2; II – шкив привода вентилятора; III – стартер двигателя; IV – привод маховика; V – насос; VI – вал карданный верхний; VII – гидротрансформатор; VIII – коробка гидромеханическая; IXXI – муфта фрикционная дисковая; X – муфта зубчатая; XII – вал карданный нижний; XIII – колесо с шиной; XIV – тормоз стояночный; XV- тормоз колесный; XVI – балансир; XVII – передача главная; XVIII – муфта сцепления.
5 Рабочий цикл автогрейдера ДЗ-143 [2]
Процесс работы автогрейдера состоит из последовательных проходов при которых осуществляется резание грунта его перемещение разравнивание и планировка поверхности сооружения.
При разработке грунта отвал устанавливают режущей кромкой как параллельно его поверхности так и наклонно под углом 10 15o с заглублением отвала или только его части по ширине. Угол резания составляет от 35o до 45o соответственно при разработке тяжелых и легких грунтов. При зарезании отвала в грунт одним концом угол между режущей кромкой отвала и продольной осью машины (угол захвата) принимают равным 35 50° при отделочных планировочных работах - 45 90° при копании с отводом грунта в сторону по отвалу - 60°.
В зависимости от размеров обрабатываемого участка рельефа местности наличия искусственных сооружений земляные работы с использованием автогрейдера ДЗ-143 выполняют движением по круговым и челночным технологическим схемам. Так при длине обрабатываемого участка (захватки) 400 1500 м автогрейдер движутся по круговым технологическим схемам а при меньших длинах - челночным способом - движением в одном направлении вперед в обратном - задним ходом. При этом в случае очень коротких захваток (около 150 м) грунт разрабатывают только движением вперед после чего возвращают машину на исходную позицию следующей проходки вхолостую задним ходом на повышенной скорости. При больших длинах захваток грунт разрабатывают как передним так и задним ходом с разворотом отвала на 180° в плане на концах захватки.
ТЕХНИКО-ЭКСПЛУАТАЦИОННЫЕ ПОКАЗАТЕЛИ АВТОГРЕЙДЕРА ДЗ-143
Основными технико-эксплуатационными показателями автогрейдера являются тяговомощностные показатели и показатели производительности расчет которых мы и произведем в рамках данного курсового проекта.
Для разработки несвязной горной породы типа легкого суглинка перемещения ее на расстояние l2=40 м и послойной укладки на участке l3=15 м для горизонтального участка если набор горной породы происходит на длине пути резания l1=10 м когда пути резания перемещения и укладки горной породы лежат на одной прямой а условия работы позволяют применить скорости соответствующие I передаче при резании II – при транспортировании и укладке и наибольшую скорость при возвращении.
Рисунок 2.1 - расчетная схема
1 Тяговый расчет [256]
Таблица 2.1 – коэффициенты f и φ
Шинноколесный движитель
рыхлый свежеотсыпанный
слежавшийся уплотненный
Талица 2.2- значения коэффициентов k (при α = 45 60°) и kn
Таблица 2.3 – величины необходимые для расчета
Установлено что при = 01 колесный движитель работает с максимальным КПД при = 02 достигается максимальная тяговая мощность при = 03 развивается наибольшая устойчивая сила тяги.
Движение машины возможно если максимальное тяговое усилие Тmах (Н) будет не меньше суммарного сопротивления движению W(Н):
Усилие Тmах ограничено двумя факторами - мощностью привода ходового устройства и условиями сцепления движителя с опорным основанием с которыми оно связано зависимостями:
Тmах(Рх) = 1000 Рх х v; Тmах(φ) = G φ
где Рх - суммарная мощность двигателей механизма передвижения
х - общий КПД механизма передвижения (табл. 2.3);
φ - коэффициент сцепления движителя с основанием (табл. 2.1).
v - скорость передвижения (мс);
Для шинноколесных движителей v - теоретическая скорость (мс):
где rc - силовой радиус м;
пд - номинальная частота вращения вала двигателя ходового механизма (обмин);
и - передаточное число трансмиссии.
Силовой радиус определяется как радиус недеформированного колеса rо за вычетом наибольшей радиальной деформации шины (в центральной зоне контактной поверхности) λ (м):
Приближенно при движении по плотному грунту λ = (012 015) В; по рыхлому грунту - λ = (008 01) В (В - ширина профиля шины).
Фактическую скорость передвижения шинноколесной машины определяют с учетом буксования по формуле (мс):
где - коэффициент буксования.
Совместив необходимые формулы рассчитываем vф:
Полученное чначение соответствует I передаче автогрейдера (табл. 2.6).
Имея необходимые показатели рассчитываем усилие (Тmах(Рх)) мощности привода ходового устройства и усилие (Тmах(φ)) сцепления движителя с опорным основанием;
Для дальнейших расчетов берем меньшее из полученных значений.
Сопротивление передвижению W (Н) складывается из сопротивлений на рабочем органе машины Wp (Н) передвижению (перекатыванию) движителей Wпep (H) по горизонтальному пути повороту машины Wnoв (H) движению на уклоне местности Wу (Н) инерции при разгоне и торможении Wи (H) и ветрового давления WB (H):
W = Wp + Wпep + Wnoв ± Wу ± Wи + WB
Из этого набора сопротивлений удерживаются только те сопротивления которые имеют место в конкретном транспортном режиме работы машины.
Сопротивление повороту колесных машин (рыхлый грунт);
Wnoв = (025 . . . 05) Wпep
Сопротивление движению от уклона местности ;
где т - масса машины кг;
g - ускорение свободного падения g = 981 мс2;
α - угол подъема пути машины (+) на подъем (-) под уклон.
Сопротивление сил инерции при разгоне и торможении:
где v - скорость в конце разгона или начале торможения (мс):
tр(т) - продолжительность разгона (торможения) (с).
Сопротивление ветрового давления:
где S - площадь воспринимающая давление ветра (м2);
qB =125 – 500 - распределенная ветровая нагрузка на 1 м2 (Па).
Сопротивления Wnoв Wу WB и Wи в данном тяговом расчете не учитываются так как по условию участок горизонтальный автогрейдер движется с равномерной скоростью а разворот совершается после выполнения операций (резание транспортировании укладке) а сопротивление ветрового давления незначительно при данной скорости.
Сопротивление резанью:
где k – коэффициент сопротивления резанью (табл. 2.2);
В – ширина отвала (м);
h1 – глубина резания во время перемещения призмы грунта (м2).
где kn – коэффициент потерь грунта при перемещении (табл. 2.2)
Vпр – объем призмы волочения(м3).
Вычисляем объем призмы волочения;
Вычисляем глубину резания во время перемещения призмы грунта;
Вычислив необходимые величины находим сопротивление резанью;
Сопротивление перекатыванию:
где f- коэффициент сопротивления передвижению движителей (табл. 2.1);
G - вертикальная составляющая внешней нагрузки на движители (Н) (табл. 2.2).
Подставив значения необходимых усилий находим сопротивление перемещению W (H);
Проверяем соответствие условию Тmах ≥ W:
Условие соблюдено тяговые характеристики автогрейдера подходят для работы в заданных условиях. Неудовлетворение указанному выше условию по тяговому усилию Тmах(Рх) означает недостаток мощности для движения машины с заданной скоростью v. Если то же условие не удовлетворяется по усилию Тmах(φ) то это означает что машина не может двигаться из-за буксования движителей.
2 Расчет производительности автогрейдера [6]
Производительность является важнейшей выходной характеристикой машины. Ее определяют количеством продукции произведенной машиной в единицу времени. Различают расчетную (теоретическая или конструктивная) техническую и эксплуатационную производительность. Под расчетной (теоретической конструктивной) производительностью понимают производительность за 1 ч непрерывной работы при расчетных скоростях рабочих движений расчетных нагрузках на рабочем органе и расчетных условиях работы. Теоретическую производительность рассчитывают на стадии разработки конструкторской документации на машину используя для этого нормативные значения расчетных параметров и расчетных условий. Под технической производительностью понимают максимально возможную в данных производственных условиях производительность при непрерывной работе машины. Под эксплуатационной производительностью понимают фактическую производительность машины в данных производственных условиях с учетом ее простоев и неполного использования ее технологических возможностей.
Таблица 2.4 - средние значения коэффициента разрыхления kp
Категория породы по трудности разработки
Разновидность горной породы
Песок супесок растительный грунт торф
Легкий и лессовидный суглинок влажный рыхлый лёсс мягкий солончак гравий мелкий и средний песок супесок и растительный грунт смешанные со щебнем и галькой насыпной слежавшийся грунт с примесью щебня или гальки
Жирная мягкая глина тяжелый суглинок гравий крупный галька мелкая щебень крупностью 15 40 мм суглинок со щебнем пли галькой
Таблица 2.5 - коэффициент призмы kпр
Значение kпр при отношении HB
Таблица 2.6 – параметры автогрейдера ДЗ-143
Скорости движения мс
Производительность определяем по формуле (м3ч):
П = 3600Vпp × ky × kи (tцkp)
где Vпp – объем грунта в разрыхленном состоянии (объем призмы волочения) находящийся перед отвалом в конце транспортирования м3;
tц – продолжительность цикла с;
ky – коэффициент уклона (kу=1 так как участок горизонтальный);
kи – коэффициент использования автогрейдера во времени(kи =085);
kp – коэффициент разрыхления грунта т.е. отношение объема разрыхленного грунта к объему грунта такой же массы в естественно плотном состоянии ( kp =1085 табл. 2.4).
Объем призмы волочения (м3):
где В и Н – ширина и высота отвала м (табл.);
kпр – коэффициент призмы установленный экспериментально и зависящий от свойств грунта и соотношения размеров отвала (табл.2.5 ).
Продолжительность цикла (с):
tц = l1u1 + l2u2 + l3u3 + l4u4 + nпtп + nоtо + nповtпов
l4= l1+ l2+ l3=10+40+15=65 м
u1=19 u2=u3=35 u4=uмах=117 – скорости движения на соответствующих участках пути мс (табл. 2.6);
tп – время на переключение передач (tп 25с);
tо – время опускания и подъема отвала (tо 45с);
tпов – время разворота автогрейдера на 180° (tпов 125с);
nп=3 nо=5 nпов=2 – соответственно количество переключений передач подъемов и опусканий отвала и разворотов на 180°.
П = 3600Vпp × ky × kи (tцkp)=346 м3ч
ТЕХНИКА БЕЗОПАСНОСТИ ПРИ ЭКСПЛУАТАЦИИ АВТОГРЕЙДЕРА
К работе на автогрейдере допускается машинист имеющий соответствующее удостоверение.
Работать на неисправном автогрейдере запрещается. Перед выездом на работу машинист обязан осмотреть автогрейдер и устранить все обнаруженные неисправности. При осмотре автогрейдера двигатель должен быть заглушён.
При движении автогрейдера машинист обязан соблюдать все правила дорожного движения установленные для автотранспорта.
Снятие или установку сменного дополнительного оборудования а также другие тяжёлые работы должны выполнять двое рабочих.
Электроосвещение установленное на автогрейдере должно обеспечивать хорошую видимость движения и каждого рабочего органа во время работы.
оставлять без присмотра автогрейдер при работающем двигателе;
регулировать исправлять и смазывать автогрейдер на ходу или при работающем двигателе;
останавливать автогрейдер на уклонах;
находиться под рамой автогрейдера при поднятом отвале;
во время работы автогрейдера удалять из-под ножа случайно попавшие предметы.
Техническое обслуживание и ремонт автогрейдера следует проводить только после полной остановки двигателя.
Техническое обслуживание проводится по истечении установленного срока эксплуатации.
В данном курсовом проекте рассмотрен автогрейдер марки ДЗ-143 его конструктивные особенности особенности работы основные составные части конструкции. Так же представлены основные характеристики и общее устройство силовой установки кинематическая схема машины описание рабочего цикла автогрейдера.
Произведен расчет наиболее важных технико – эксплуатационных показателей автогрейдера в условиях разработки несвязной горной породы II категории с последующим ее перемещением и послойной укладкой на горизонтальном участке. Расчитанны - мощность привода ходового устройства равная 79667 кН усилие сцепления движетеля с опорным основанием равное 675 кН произведен расчет производительности автогрейдера равной 346 м3ч дающий представление о возможностях машины.
Представлена техника безопасности при эксплуатации автогрейдера.
СПИСОК ИСПОЛЬЗУЕМОЙ ЛИТЕРАТУРЫ
Абрамов Н. Н. «Курсовое и дипломное проектирование по дорожно-строительным машинам» «Высшая школа» – 1972 г. - 119 с.[1]
Алексеева Т. В. Артемьев К. А. Бромберт Л. А. «Дорожные машины. Часть I. Машины для земляных работ» «Машиностроение» – 1972 г. - 499 с.[2]
Белецкий Б. Ф. Булгакова И. Г. «Строительные машины и оборудование» «Феникс» - 2005 - 606 с.[3]
Ляшенко Ю.М. «Методические указания к курсовому проекту
по дисциплине: Машины для земляных работ» ШИ (ф) ЮРГТУ (НПИ) – ЮРГТУ 2010. – 19 с.[5]
Ляшенко Ю.М. «Методические указания к выполнению
практических занятий и домашнего задания» ШИ (ф) ЮРГТУ (НПИ) – ЮРГТУ 2010. – 72 с.[6]
7.Прочность.doc
Расчёт отвала и механизма стабилизации
Расчёт отвала следует проводить с учётом нагружения его максимальной реакцией грунта Рх приложенной к концу отвала находящегося в положении наибольшего выноса в сторону относительно кронштейнов (рис.4.1). При этом считают что сила Рх действует по оси симметрии отвала изгибая его в горизонтальной плоскости и пренебрегают возникающими в нём напряжениями от кручения. Таким образом расчёт отвала сводится к расчёту его на изгиб как консоли.
Изгибающий момент в опасном сечении I-I
Рх принимают равной 926кН так как она максимальна при первом расчётном положении.
здесь Lотв = 372м – длина отвала;
Рис.4.1 Схема сил для расчёта отвала
Под действием силы Рх в волокнах части сечения расположенной справа от нейтральной линии ОО возникнут напряжения растяжения а в части расположенной слева от сечения - напряжения сжатия.
Момент инерции в сечении I-I
где = 001м – толщина отвала
R0 = 058м – средний радиус кривизны сечения отвала
Тогда моменты сопротивления зон растяжения и сжатия сечения определяют по выражениям:
где 0 = расстояние от х до
нейтральной линии ОО; (4.5)
Нормальные напряжения:
в растянутых волокнах
Полученные напряжении необходимо сравнить с допускаемыми и убедиться что они не превышают последних.
Определяем приведенное напряжение по формуле [11]:
Определяем коэффициент запаса прочности по формуле:
гдет – предел текучести стали 09Г2С по ГОСТ 380-71 т =325 МПа
Отвал из выбранного материала и выбранной толщины отвала удовлетворяет условиям прочности расчёта.
Коэффициент запаса прочности большой значит можно уменьшить толщину стенки или выбрать другой менее прочный материал что приведёт к уменьшению металлоёмкости и капиталовложений в производимый отвал.
Так как характеристики дополнительного отвала такие же как у основного то дополнительный отвал принимаю такой же.
1.Титульный.doc
Федеральное государственное бюджетное образовательное учреждение высшего профессионального образования
«ВОРОНЕСКИЙ ГОСУДАРСТВЕННЫЙ АРХИТЕКТУРНО-СТРОИТЕЛЬНЫЙ УНИВЕРСИТЕТ»
КАФЕДРА СТРОИТЕЛЬНОЙ ТЕХНИКИ И ИНЖЕНЕРНОЙ МЕХАНИКИ
По дисциплине «Рабочие органы машин для разработки грунтов»
Модернизация системы управления угла резания отвала автогрейдера ДЗ - 143
Магистрант группы М1985
4.Анализ конструкций.doc
1 Назначение автогрейдера ДЗ-143
Основным назначением автогрейдера ДЗ-143 является профилирование земляного полотна строительство грунтовых дорог на нулевых отметках или на насыпях воздвигаемых из грунта кюветов планировка грунтовых поверхностей.
Рисунок 1.1 – Автогрейдер
Выполнение всех функций грейдера происходит с помощью специального рабочего органа— отвала с ножом который смонтирован на раме машины. Его можно поднимать опускать поворачивать в горизонтальной и вертикальной плоскости.
2 Основное рабочее оборудование автогрейдера
Автогрейдеры имеют три вида рабочего оборудования: отвал рыхлитель-кирковщик бульдозер. Помимо перечисленных видов рабочего оборудования автогрейдеры могут оснащаться откосником кюветоочистителем снегоочистителем.
Грейдерный отвал – основной рабочий орган машины и его главное достоинство – способность занимать в пространстве практически любое положение. Он может вращаться в горизонтальной плоскости на 360° в любом направлении становиться вертикально справа или слева от автогрейдера выдвигаться вправо или влево более чем на треть своей длины поворачиваться вокруг собственной режущей кромки. А получил он такую замечательную возможность благодаря системе крепления отвала к раме машины.
Главная особенность системы крепления заключена в том что собственно отвал является частью узла основу которого составляет тяговая рама автогрейдера представляющая собой А- или Т-образную в плане металлоконструкцию сваренную из балок коробчатого сечения и шарнирно прикрепленную к передней части основной рамы (хребтовой балки) машины в одной точке над осью передних колес. Для крепления тяговой рамы используется универсальный шарнир позволяющий ей поворачиваться во все стороны и вращаться вокруг собственной продольной оси. Прочность шарнира вполне соответствует усилиям возникающим на отвале.
Широкая сторона тяговой рамы поддерживается двумя гидроцилиндрами подъемаопускания отвала (левым и правым). Вместе эти устройства образуют своеобразный рычажный механизм жесткость которому в поперечном направлении придает еще один гидроцилиндр служащий для выноса тяговой рамы в сторону и образующий диагональ «четырехугольника». Такая система обеспечивает раме большие возможности перемещения диапазон которых резко увеличивается если гидроцилиндры подъемаопускания отвала и гидроцилиндр выноса тяговой рамы крепятся к скобе вращающейся вокруг хребтовой балки машины.
К тяговой раме крепятся скользящие опоры (пять и более) поддерживающие большое зубчатое колесо с внешним или внутренним зацеплением – поворотный круг к которому прикреплен отвал вращающийся относительно тяговой рамы благодаря гидромотору или гидроцилиндрам. Особенности крепления отвала к поворотному кругу позволяют поворачивать его относительно режущей кромки и сдвигать относительно круга влево или вправо.
Рисунок 1.2 - Рабочее оборудование
-тяговая рама; 2-поворотный круг; 3-гидроцилиндр выноса отвала; 4-гидравлический шарнир; 5-шарнир; 6-водило; 7-редуктор поворота отвала; 8-палец; 9-крышка; 10-шарнир; 11-отвал; 12-кронштейн; 13-гидроцилиндр изменения угла резания отвала; 14-кронштейн; 15-регулировочный болт; 16-накладка; 17-болт; 18-регулировачная прокладка; 19-зубчатый венец
Основным рабочим органом автогрейдера является отвал (рис.129) который состоит из трех сборочных единиц: тяговой рамы поворотного круга непосредственно отвала. Тяговая рама имеет треугольную форму. В ее передней части имеется шарнир с крышкой для соединения с головкой основной рамы. Снизу к раме приварены плиты для крепления поворотного круга. На передней плите крепится редуктор поворота отвала. Поворотный круг состоит из кольца с приваренными лапами зубчатого венца прикрепленного к кольцу болтами. Такое устройство поворотного круга позволяет изменять положение венца относительно круга при неравномерном износе зубьев. К тяговой раме поворотный круг крепится накладками с регулировочными болтами. Отвал крепится к поворотному кругу двумя кронштейнами установленными на штанге поворотного круга. Отвал снащен основными и боковыми ножами реверсивного типа. При износе режущей кромки основных ножей перестановка их производится переворачиванием. Боковые ножи при износе их режущей кромки переставляют выдвижением смещая на одно отверстие вниз или переворачиванием. Изменение угла резания отвала производится гидроцилиндрами этим же гидроцилиндром отвал выносится относительно тяговой рамы в обе стороны. Съемный кронштейн для крепления головки штока гидроцилиндра на отвале может быть передвинут. Поворот отвала в плане осуществляется редуктором цилиндрическая шестерня которого входит в зацепление с зубчатым венцом поворотного круга. Гидравлический шарнир закрепленный на поперечной балке тяговой рамы обеспечивает пропуск рабочей жидкости к гидроцилиндрам изменения угла резания отвала и его выноса.
Редуктор поворота отвала закреплен на тяговой раме болтами и шпильками. Основными его деталями являются корпус червячное колесо червяк крышки подшипники валы шестерня. Посредством втулки и муфты червяк соединяется с валом гидромотора.
3 Проведение патентного поиска
В ходе проведённого поиска патентной информации был принят к сведению материал следующего авторского свидетельства.
Авторское свидетельство № 1315569
Цель изобретения – повышение эффективности путём стабилизации глубины резания при изменении угла резания отвала в процессе работы.
Рисунок 1.3 – Рабочий орган. Авторское свидетельство № 1315569
Изобретение относится к землеройно – транспортным машинам и повышает эффективность путём стабилизации глубины резания при изменении угла резания отвала в процессе работы. Оборудование автогрейдера включает поворотный круг 1 с кронштейном 2 отвал 3 и гидроцилиндр (ГЦ) 5 изменения угла резания. Отвал 3 нижней частью посредством двуплечего рычага 9 шарнирно соединён со свободным концом кронштейна 2. С корпусом ГЦ 5 шарнирами 12 и 13 соединена тяга 11 управления. Шток ГЦ 5 шарнирно соединён с тягой 11. Отвал 3 поворачивается в шарнире 8 по часовой стрелке увеличивая угол резания и глубину. Корпус ГЦ 5 поворачивается в шарнире 6 по часовой стрелке перемещая через шарнир 13 тягу 11 вниз. Рычаг 9 поворачивается в шарнире 10 против часовой стрелки а отвал 3 перемещается вверх уменьшая глубину резания. 2 з.п ф – лы 2 ил.
Изобретение относится к землеройно – транспортным машинам в частности к управлению рабочими органами автогрейдеров предназначенных для использования главным образом в дорожном строительстве.
Механизм изменения угла резания отвала автогрейдера содержит поворотный круг 1 с кронштейном 2 отвал 3 соединённый в верхней части шарниром 4 со штоком гидроцилиндра 5 корпус которого в шарнире 6 соединён с неподвижным кронштейном 7 поворотного круга 1. Гидроцилиндр 5 может быть установлен в середине отвала 3 или в количестве двух штук по его краям. В нижней части отвал 3 соединён в шарнире 8 с двуплечим рычагом 9 который в шарнире 10 соединён со свободным концом кронштейна 2 поворотного круга 1. Привод двуплечего рычага 9 осуществляется от корпуса гидроцилиндра 5 тягой 11 управления соединённой с ними в шарнирах 12 и 13.
Предлагаемый механизм является шестизвенным с одной степенью свободы (ведущее звено – шток с поршнем гидроцилиндра 5 ведомое звено – отвал 3 неподвижное звено – поворотный круг 1 с кронштейнами 2 и 7).
2.Содержание.doc
автогрейдеров с патентным исследованием 5
1 Назначение автогрейдера ДЗ-143 .. 5
2 Основное рабочее оборудование автогрейдера 6
3 Проведение патентного поиска 8
Особенности кинематики механизма изменения угла резания отвала
Кинематический расчёт механизма стабилизации 15
Расчёты на прочность отвала и механизма стабилизации ..18
Библиографический список .. ..21
6.Кинемат.Расчёт.doc
Для того чтобы обеспечить бесперебойную работу машины необходимо иметь достаточные скорости управления различными рабочими органами автогрейдера. Так например при перегрузке двигателя когда есть опасность его остановки нужно быстро разгрузить отвал путем подъема его из грунта. Быстрое управление отвалом бывает также необходимым при планировочных работах когда требуется менять его установку в соответствии с рельефом местности.
Механизм подъема отвала рассчитывается исходя из таких предпосылок. Рабочий ход механизма подъема должен обеспечивать заданную глубину копания возможность полного выглубления отвала и удовлетворять условиям проходимости автогрейдера в транспортном положении. При расчете механизма подъема в соответствии с рисунком 3 определяют подъемное усилие необходимое для выполнения этой операции мощность.
Подъемное усилие рассчитывается при выглублении отвала опущенного в грунт одним концом. Предполагается что угол захвата равен и на отвал действуют силы и .
Рисунок 3 - Расчетная схема для определения усилия подъема рамы автогрейдера
Тогда согласно схеме этого рисунка
где сила тяжести тяговой рамы с отвалом; здесь можно принять
Считается что в этом случае автогрейдер реализует полное усилие тяги по сцеплению. Тогда
коэффициент для колесной формулы .
коэффициент сцепления для растительного покрова
Мощность привода механизма находится по формуле:
- скорость подъема отвала принимается равной 009 018 мс;
Поворот отвала в горизонтальной плоскости осуществляется зубчатым редуктором или гидравлическим приводом. Последний может быть выполнен в виде гидродвигателя. В связи с тем что поворот отвала производится лишь при полном его выглублении из грунта затрачиваемая на это мощность незначительна поэтому может не рассчитываться.
8.Библ список.doc
Номенклатурный каталог. Строительные дорожные мелиоративные лесо и торфозаготовительные коммунальные ручные отделочные машины оборудование для производства стройматериалов лифты пожарная техника кондиционеры и вентиляторы. М.: Минстроймаш 1990.
Никулин П.И. Гильмутдинов В.И. Литвинов В.С. Расчет и построение тяговой характеристики землерейно-транспортной машины с гидромеханической трансмиссией. Методические указания к курсовому и дипломному проектированию. Воронеж: ВГАСА 1993. – 30 с.
Ульянов Н.А. Теория самоходных колесных землерейно-транспортных машин. М.: Машиностроение 1969. - 520 с.
Алексеева Т.В. Артемьев К.А. Бромберг А.А. Дорожные машины машины для земляных работ (теория и расчет). М.: Машиностроение 1969. - 520 с.
Барадачев И.П. Справочник конструктора дорожных машин. М.: Машиностроение 1964. - 591 с.
Решетов Д.Н. Детали машин. М.: Машиностроение 1975. – 650 с.
Артобалевский И.И. Теория механизмов и машин. М.: Науки 1988. - 640 с.
Биджиев Р.Х. Расчет центрально сжатых стержней на устойчивость. Методичексие указания. Воронеж: ВГАСА 1999. - 24 с.
3.Введение.doc
Так как парк машин для земляных работ очень велик и разнообразен как по функциям так и по устройству конструкции машин в данной курсовой работе рассмотрим одну из машин данного класса а именно автогрейдер марки ДЗ-143. Так как автогрейдеры оснащают различным сменным дополнительным оборудованием (до 20 видов) область применения их очень широка.
В данной курсовой работе рассматривается изобретение для рабочего оборудования автогрейдера повышающее эффективность путём стабилизации глубины резания при изменении угла резания отвала в процессе работы. Автогрейдер является одной из распространённых и востребованных машин что доказывает актуальность данной курсовой работы.
5.Особненности изменения угла резания.doc
У современных автогрейдеров всех типов управление рабочим оборудованием (отвалом) производится из кабины машиниста с помощью гидропривода. Изменение углов резания и захвата непосредственно в процессе разработки грунта позволяет лучше приспособить машину к изменениям грунтовых условий что в конечном счёте повышает её производительность.
Конструктивная схема механизма изменения угла резания представлена на рис.2.1 подвижными звеньями являются: 1 – отвал; 2 – шток гидроцилиндра с поршнем; 3 – корпус гидроцилиндра. Неподвижное звено – поворотный круг 4 с кронштейнами 5. Данный механизм представляет собой плоский четырёхзвенник с четырьмя низшими кинематическими парами и одной степенью подвижности.
Отличительной конструктивной особенностью механизмов изменения угла резания различных моделей автогрейдеров является место расположения шарнира Б крепления корпуса гидроцилиндра к поворотному кругу (рис.2.1). У автогрейдеров класса 100 (ДЗ – 148) и класса 160 (ДЗ – 143) этот шарнир расположен за отвалом как показано на рис.2.1. у автогрейдеров класса 160 (ДЗ – 122)и класса 250 (ДЗ – 98 ДЗ – 98А) шарнир Б расположен перед отвалом.
Общим для всех современных схем этого механизма является то что при изменении угла резания поворот отвала 1 относительно кронштейна 5 (неподвижное звено) происходит в шарнире 0. У отечественных автогрейдеров классов 100 и 160 диапазон изменения угла резания =30 – 70 0 а у автогрейдеров класса 250 =30 – 80 0.
Рассмотрим кинематику механизма схема траекторий подвижных точек которого показана на рис.2.2. отвал заглублен в грунт на начальную глубину резания hр0.Точкой D обозначена режущая кромка отвала (ножа). Введём следующие обозначения к схеме на рис.2.2: RD – радиус поворота режущей кромки отвала (ножа); rD – радиус поворота передней грани отвала (ножа); RA – радиус поворота головки штока гидроцилиндра;
Из OE0D0 (рис. 2.2) угол =arcsin rD RD= const.
При угле резания 1 >0 глубина резания hр1 = hр0+C0C1 = hр0+hр1
где hр1 = C0C1 = RD[sin(1-)- sin(0-)].
При 2 >0 hр2 = hр0+C0C2 = hр0+hр2
где hр2 = C0C1 = RD[sin(0-)- sin(2-)].
После преобразования выражений (2) (3) получим
hр1 = 2RD sin 2 cos[(0-)+ 2]
hр2 = 2RD sin 2 cos[(0-)+ 2]
В общем случае при =0± имеем hр = hр0± hр здесь
hр = 2RD sin 2 cos[(0- arcsin rD RD ) ± 2].
Таким образом имея начальную глубину резания hр0 при увеличении или уменьшении начального угла резания 0 на величину будем увеличивать или уменьшать hр0 на величину hр что и является главной особенностью кинематики механизма изменения угла резания отвала современных автогрейдеров.
Анализ функции hр=(0) представленный уравнением (6) показывает что она является монотонной не имеет выраженных экстремумов проходит через начало координат и располагается в первом и третьем квадрантах т. е. в областях положительных и отрицательных значений и hр.
При =0-400 изменение глубины резания составляет у автогрейдеров моделей ДЗ - 143 ДЗ – 148 hр=0 - 205 мм у автогрейдера модели ДЗ – 122 hр=0 - 233 мм.
Из (6) видно что hр=0 при соблюдении одного из следующих трёх условий:
cos[(0- arcsin rD RD ) ± 2]=0.
Условие RD=0 не может быть выполнено конструктивно а
cos[(0 - arcsin rD RD ) ± 2]=0 не выполняется исходя из реальных значений параметров этой функции. Условие же =0 соответствует случаю когда в процессе работы отсутствует корректировка угла резания.
Таким образом существующие кинематические схемы механизмов изменения угла резания отвала автогрейдера не обеспечивают постоянства глубины резания hр=const при изменении в процессе разработки грунта первоначального угла резания 0. Поэтому эти схемы не могут быть использованы в системе автоматического управления процессом
разработки грунта по углу резания в оптимальном режиме работы автогрейдера. Между тем как показывают исследования [1] автогрейдер в конкретных условиях работы имеет максимальную производительность и минимальный удельный расход топлива при определённом значении угла резания отвала причём эти зависимости являются экстремальными.
моя ПЗ.doc
Анализ вариантов проектирования конструкции автогрейдера и выбор окончательного варианта проектирования для дипломного проекта 9
Описание устройства выбранного варианта конструкции машины 11
Патентный поиск с целью проверки изделия на патентную чистоту 19
Расчет и проектирование автогрейдера 24
1 Мощность двигателя 24
3 Расчет производительности автогрейдера 33
4 Определение сил действующих на автогрейдер 34
5 Расчет механизмов управления 39
6 Расчет ходового оборудования 42
7 Определение нагрузок действующих на раму автогрейдера 45
7.1 Расчетный случай I 45
7.2 Расчетный случай II 50
8 Расчет основной рамы в САПР АПМ WinMachine 53
Гидравлическая система 69
Электрооборудование машины 73
Экономико-организационная часть 83
1 Оценка технической целесообразности конструкции изделия 83
2 Расчет трудоемкости ОКР 87
3 Расчет временных и стоимостных затрат на проектирование изделии 93
4 Прогнозирование себестоимости изделия 96
5 Определение прогнозируемой цены изделия 100
6 Расчет капитальных вложений в НИОКР и освоение производства 101
7 Оценка эффекта от производства и использования изделия 102
8 Сводные показатели оценки экономической целесообразности проекта 102
3 Общие санитарно- гигиенические требования к воздуху рабочей зоны 114
4 Светотехнические приборы машины и освещение территории 115
5 Пожарная безопасность 116
6 Охрана природы 117
7 Указание мер безопасности 118
Список литературы 123
Приложение: спецификации 125
Первые опыты строительства грунтовых дорог с использованием грейдера были проведены в России еще в 1910-х годах и впоследствии эти машины получили у нас широкое распространение. Из-за огромных масштабов дорожного строительства в нашей стране в послевоенное время возникла и развилась новая отрасль машиностроения. В настоящее время дорожно-строительное производство немыслимо без применения этих специализированных машин современной конструкции. Строительные организации РФ располагают значительным парком дорожно-строительных машин; из года в год расширяется их номенклатура растет выпуск улучшается качество машин.
Число производителей автогрейдеров в мире велико хотя эти машины менее многочисленны чем скажем бульдозеры или одноковшовые погрузчики. Несмотря на обилие марок лежащие в основе конструкций автогрейдеров технические идеи практически одинаковы. Именно они придают этим машинам столь оригинальный вид. Современный автогрейдер – это как правило длиннобазовые трехосные машины у которых две пары задних колес расположены очень близко друг к другу а между средней и передней осями размещается грейдерный отвал длина которого больше высоты в 5 7 раз.
Выпуск автогрейдеров в России в настоящее время осуществляют три завода строительно-дорожных машин – Брянский Орловский и Челябинский причем серийный выпуск тяжелых грейдеров освоил лишь Челябинский завод. Эти машины наиболее эффективны при выполнении землеройно-планировочных работ на строительстве при ремонте и содержании дорог. По необходимости применяют их и в других сферах деятельности. Российские машиностроители могут с уверенностью сказать что наши автогрейдеры по своим характеристикам мало уступают зарубежным аналогам и экспортируются более чем в 50 стран мира. Отечественным производителям автогрейдеров противостоит мощная конкуренция компаний передовых стран которая вынуждает российские фирмы следовать тенденциям мирового технического прогресса.
Тем не менее по данным Госстроя России парк автогрейдеров в стране в силу различных причин в последнее время становится меньше. Так в 1995 году их насчитывалось 14 тысяч в 2000 – уже не более 10 тысяч причем 20% выработали срок амортизации. Начиная с 1997 года производство автогрейдеров начало увеличиваться но в 2001-м произошел резкий его спад. Если в 1990 году было изготовлено 4732 автогрейдера то в 2002 – лишь 992.
Снижение динамики продаж дорожно-строительной техники отмечается и в Западной Европе. Так объем продаж грейдеров в 2003 году по отношению к 2002 году составил лишь 84%. Причины спада за рубежом очень похожи на российские – значительные производственные и финансовые ресурсы необходимые для выпуска подобной техники ее дороговизна и многое другое.Однако просторы нашей страны состояние дорог и универсальность автогрейдеров всегда обеспечат высокий спрос на эти машины.
Такое положение вещей обостряет конкуренцию и производители вынуждены постоянно улучшать свою продукцию используя самые современные технические решения. Основное внимание уделяется выпуску высокопроизводительных энергонасыщенных и автоматизированных машин обеспечивающих выполнение работ в дорожном строительстве прогрессивными методами и позволяющих решать задачи комплексной механизации трудоемких строительных процессов. Это предъявляет определенные требования к уровню эксплуатации строительных дорожных машин а так же квалификации обслуживающего персонала.
Словом сейчас многие сервисные и машиностроительные предприятия России оперативно реагируют на нужды рынка. В последнее время в развитии конструкций автогрейдеров определились такие тенденции: повышение мощности двигателей без значительного увеличения массы машины; улучшение способности работать при большом крене а также в условиях низких и высоких температур сильной запыленности воздуха; повышение транспортной и рабочей скоростей автоматизация управления профилированием по заданным параметрам; повышение эргономичности и комфортности кабины; соответствие возрастающим требованиям по экологии.
Цели и задачи проектирования
Целью проекта является разработка конструкции автогрейдера класса 140 с гидравлической системой управления рабочими органами. Для достижения этой цели необходимо решить следующие задачи:
на основании сравнительного анализа различных вариантов исполнения автогрейдера выбрать конструкцию автогрейдера для проектирования;
выполнить описание устройства и работы выбранной конструкции;
выполнить патентный поиск с целью проверки изделия на патентную чистоту;
определить основные параметры автогрейдера выполнить тяговый расчет расчет производительности;
выполнить расчет механизмов управления и ходового оборудования;
определить силы действующие на рамы автогрейдера и на его рабочее оборудование;
рассчитать раму автогрейдера в системе автоматического проектирования с применением программы АПМ W
в экономическом разделе дать экономическое обоснование принятым в проекте техническим решениям;
в разделе «охрана труда» разработать мероприятия по ликвидации возникающих вредных и опасных факторов влияющие на рабочего и окружающую среду;
по результатам проделанной работы сделать заключение.
Анализ вариантов проектирования конструкции автогрейдера и выбор окончательного варианта проектирования для дипломного проекта
Для сравнительного анализа необходимо рассмотреть предназначение достоинства и недостатки классифицируемых автогрейдеров.является одним из главных параметров автогрейдеров так как от нее зависят нагрузки на колеса а следовательно тяговое усилие на ведущие колеса являющиеся тем показателем по которому судят о рабочих возможностях автогрейдеров. Легкие автогрейдеры не обладают достаточными мощностями для выполнения всех необходимых видов работ. Поэтому их применение ограничивается лишь работами по содержанию и ремонту дорог.
Краткой но выразительной характеристикой ходовой части автогрейдеров является их «колесная формула». Это общепринятое сочетание трех символов составляемое по схеме «A х B х C». A - показывает количество осей с управляемыми колесами B – число ведущих осей и C – общее количество осей. Легкие и средние автогрейдеры имеют одинаковую колесную формулу 1 х 2 х 3. В тяжелых грунтовых условиях или ситуациях когда скорость работы важней всего предпочтительна формула 1 х 3 х 3. Как правило это тяжелые машины массой 19 тонн и более широкое использование которых сдерживалось их непропорционально большой ценой. Следует отметить что серийный выпуск тяжелых грейдеров освоил лишь Челябинский завод. Возможно когда бурное развитие гидрообъемных трансмиссий коснется и этой отрасли дорожного машиностроения стоимость полноприводных автогрейдеров не будет столь разительно отличать их от заднеприводных. У полноприводных автогрейдеров выше сила тяги и значительно лучше курсовая устойчивость (потеря курсовой устойчивости при больших сопротивлениях на отвале – слабое место всех автогрейдеров). Их целесообразно применять при сооружении строительстве и содержании дорог в сложных грунтовых условиях в северных регионах страны.
У строителей наиболее популярны машины с формулой 1 х 2 х 3. Так автогрейдеры среднего типа предназначены для работ при сооружении дорог средних грунтовых условиях при ремонте и восстановлении грунтовых дорог. Средние автогрейдеры по сравнению с тяжелыми имеют меньшие габаритные размеры что повышает их маневренность. На территории центрального Черноземья целесообразно использовать модели средних автогрейдеров так как они превосходят своих легких собратьев по большинству показателей.
Специфика машины такова что без специального переоборудования ее можно использовать только для планирования и профилирования доля которых в общем объеме работ относительно невелика. Отдельного упоминания заслуживают усилия машиностроителей направленные на сокращение простоев автогрейдеров. Их конструкция позволяет использовать почти все виды дополнительного рабочего оборудования навешиваемые на раму. Это повышает его производительность. Все модели автогрейдеров унифицированы. В российских условиях машины выходят из строя после 7 9 лет жесткой эксплуатации. Они не просто ломаются а изнашиваются. У этой проблемы есть решения – капитальный полнокомплектный ремонт при котором возможна замена до 90% изношенных деталей. Этот вариант решения обойдется значительно дешевле чем покупка новой машины это немаловажно.
Проанализировав сказанное ранее я выбираю автогрейдер класса 140 с колесной формулой 1 х 2 х 3. Этот автогрейдер наиболее подходит для нашего региона и обладает хорошими технико - экономическими показателями в том числе и наиболее разумной ценой. В случае необходимости можно будет провести полнокомплектный ремонт с установкой самых последних новшеств и рационализаторских предложений.
Описание выбранной конструкции
Автогрейдер класса 140 предназначен для землеройно-профилировочных работ строительства и содержания дорог и может использоваться на работах по перемещению и распределению грунта и дорожно-строительных материалов планировке откосов выемок насыпей устройству корыта и боковых канав очистке дорог от снега смещения грунтов с добавками и вяжущими материалами на полотне дороги а также для рыхления асфальтовых покрытий булыжных мостовых и тяжелых грунтов с помощью дополнительного рабочего органа-рыхлителя заднего расположения. Он может работать в грунтах I-III категорий при температуре от 313К (40о) до 233К (-40 о) в условиях умеренного климата.
Общий вид автогрейдера приведен ниже на рисунке 3.1. Главными составными частями являются: основная рама тяговая рама с поворотным кругом и отвалом бульдозер силовая установка трансмиссия ходовая часть механизмы управления кабина оператора рыхлитель - кирковщик.
На автогрейдере в качестве силовой установки используется дизельный двигатель. В силовую передачу входят: муфта сцепления коробка передач задний мост и карданные валы.
Муфта сцепления двухдисковая постоянно замкнутого типа установлено на дизеле. На автогрейдерах устанавливается механическая коробка передач с шестью передачами вперед и двумя назад. Задний мост представляет собой балансирную двухосную тележку со всеми ведущими колесами. Передний мост шарнирно соединен с основной рамой автогрейдера. Такое соединение обеспечивает поперечное качение моста в обе стороны. Основным рабочим органом автогрейдера является отвал который имеет универсальную установку в пространстве для производства работ специфичных для автогрейдера. Дополнительные рабочие органы – бульдозер и рыхлитель. Рулевое управление состоит из гидроруля и привода к нему. Передние колеса поворачиваются цилиндрами. Колеса заднего моста оборудованы колодочными тормозами. В системе управления тормозами имеется гидроусилитель. Стояночный тормоз колодочного типа установлен на входном валу заднего моста. Управление муфтой сцепления механическое с гидроусилителем. Гидравлическая система управления рабочими органами раздельно-агрегатная. Гидронасос установлен на двигателе. Гидрораспределители закреплены снаружи на передней стенке кабины. Кабина оборудована сиденьем рычагами и педалями управления щитком приборов. На автогрейдере имеются звуковой сигнал указатели поворотов габаритов и торможения рабочие и транспортные фары проблесковый маяк. Конструкция автогрейдеров предусматривает возможность агрегатирования с плужным снегоочистителем удлинителем отвала толкающей плитой щеткой погрузчиком а также другим навесным оборудованием.
Рисунок 3.1 - Общий вид автогрейдера.
- рыхлитель-кирковщик; 2-рама подмоторная; 316-корпус фары; 4-бак гидросистемы; 5-крыло; 7-ящик аккумуляторный; 8-мост задний; 9-бак топливный; 10-кабина; 11-гидроцилиндр выноса тяговой рамы; 12-механизм фиксации; 13-гидроцилиндр подъема отвала; 14-рама тяговая; 15-балка хребтовая; 17-бульдозер; 18-мост передний; 19-круг поворотный; 20-отвал; 21-гидроцилиндр изменения угла резания отвала; 22-подножка; 23-коробка передач; 24-вал карданный
Рама автогрейдера сварной конструкции. Она состоит из подмоторной рамы и хребтовой балки. На подмоторной раме установлены кабина коробка передач двигатель капот баки. В задней части подмоторной рамы крепится рыхлитель – кирковщик снизу присоединяется задний мост. К хребтовой балке к передней части присоединены передний мост бульдозер и тяговая рама рабочего органа. В средней части к раме крепиться механизм подвески гидроцилиндров подъема отвала и выноса тяговой рамы.
Рисунок 3.2 - Основная рама.
-кронштейн крепления рыхлителя; 2-подмоторная рама; 3-хомут; 4-опора кабины; 5-подножка; 6-хребтовая балка; 7-механизм подвески гидроцилиндров; 8-отливка головная; 9-рама крепления бульдозера; 10-поворотный хомут; 11-цапфа; 12-сектор; 13-фиксатор; 14-винт; 1517-штуцер; 16-гидроцилиндр
Механизм подвески гидроцилиндров имеет поворотный хомут 10 с тремя кронштейнами на которых установлены вилки гидроцилиндров подъема отвала и выноса тяговой рамы. Хомут может поварачиваться вокруг цапфы 11 приваренной к хребтовой балке. Замыкания поворотного хомута в определенном положении производиться фиксатором 13 который закреплен на штоке гидроцилиндра16. Сектор 12 приваренный к хребтовой балке имеет 5 пазов. Крайние пазы служат для фиксации механизма подвески при установке отвала под углом до 90 градусов средний паз служит для установки механизма в исходное положение промежуточные пазы – для промежуточных положений.
Управление гидроцилиндром фиксатора производится рычагом из кабины. При замыкании механизма фиксатор входит в паз сектора при размыкании – выходит из паза.
Грейдерный отвал – основной рабочий орган машины и его главное достоинство – способность занимать в пространстве практически любое положение. Он может вращаться в горизонтальной плоскости на 360° в любом направлении становиться вертикально справа или слева от автогрейдера выдвигаться вправо или влево более чем на треть своей длины поворачиваться вокруг собственной режущей кромки. А получил он такую замечательную возможность благодаря системе крепления отвала к раме машины.
Главная особенность системы крепления заключена в том что собственно отвал является частью узла основу которого составляет тяговая рама автогрейдера представляющая собой А- или Т-образную в плане металлоконструкцию сваренную из балок коробчатого сечения и шарнирно прикрепленную к передней части основной рамы (хребтовой балки) машины в одной точке над осью передних колес. Для крепления тяговой рамы используется универсальный шарнир позволяющий ей поворачиваться во все стороны и вращаться вокруг собственной продольной оси. Прочность шарнира вполне соответствует усилиям возникающим на отвале.
Широкая сторона тяговой рамы поддерживается двумя гидроцилиндрами подъемаопускания отвала (левым и правым). Вместе эти устройства образуют своеобразный рычажный механизм жесткость которому в поперечном направлении придает еще один гидроцилиндр служащий для выноса тяговой рамы в сторону и образующий диагональ «четырехугольника». Такая система обеспечивает раме большие возможности перемещения диапазон которых резко увеличивается если гидроцилиндры подъемаопускания отвала и гидроцилиндр выноса тяговой рамы крепятся к скобе вращающейся вокруг хребтовой балки машины.
К тяговой раме крепятся скользящие опоры (пять и более) поддерживающие большое зубчатое колесо с внешним или внутренним зацеплением – поворотный круг к которому прикреплен отвал вращающийся относительно тяговой рамы благодаря гидромотору или гидроцилиндрам. Особенности крепления отвала к поворотному кругу позволяют поворачивать его относительно режущей кромки и сдвигать относительно круга влево или вправо.
Рисунок 3.3 - Рабочее оборудование.
-тяговая рама; 2-поворотный круг; 3-гидроцилиндр выноса отвала; 4-гидравлический шарнир; 5-шарнир; 6-водило; 7-редуктор поворота отвала; 8-палец; 9-крышка; 10-шарнир; 11-отвал; 12-кронштейн; 13-гидроцилиндр изменения угла резания отвала; 14-кронштейн; 15-регулировочный болт; 16-накладка; 17-болт; 18-регулировачная прокладка; 19-зубчатый венец
Рабочее оборудование состоит из трех крупных узлов: тяговой рамы 1 поворотного круга 2 отвала 11 и закрепленных на них агрегатов.
Тяговая рама 1 сварной конструкции V- образной формы. В передней части рамы имеется шарнир с крышкой для соединения с головной отливкой основной рамы. Снизу к раме приварены плиты для крепления поворотного круга 2 на передней плите крепиться также редуктор поворота отвала 7. На поперечной балке имеется три шарнира для крепления штоков цилиндров подъема отвала и выноса тяговой рамы.
Поворотный круг состоит из кольца с приваренными лапами и зубчатого венца 19 прикрепленного к кольцу болтами. Это дает возможность изменять положение венца относительно поворотного круга при неравномерном износе зубьев. К тяговой раме поворотный круг крепится с накладками 16 с регулировочными прокладками 18.
Отвал 11 крепиться к поворотному кругу двумя кронштейнами 12 установленными на штанге поворотного круга. На отвале установлены основные и боковые ножи реверсивного типа. При износе режущей кромки основных ножей перестановка их производится переворачиванием. При износе режущей кромки боковых ножей перестановка их производится выдвижением ( смешением на одно отверстие вниз) или переворачиванием.
Изменение угла резания отвала производиться гидроцилиндрами 13. Вынос отвала относительно тяговой рамы в обе стороны производится гидроцилиндром 3. Съемный кронштейн для крепления головки штока гидроцилиндра на отвале может быть передвинуть.
Поворот отвала в плане осуществляется редуктором 7 цилиндрическая шестерня которого входит в зацепление с зубчатым венцом поворотного круга.
Гидравлический шарнир 4 закрепленный на поперечной балке тяговой рамы служит для подвода рабочей жидкости к гидроцилиндрам изменения угла резания отвала и выноса отвала.
Описание кинематической схемы
Первичный вал 18 коробки передач вращается на подшипниках посаженных в корпусе. На первичном валу на шлицах закреплена ведущая шестерня 17 которая находится в постоянном зацеплении с шестерней 14 вторичного вала 15. Кроме того на первичном валу на подшипниках посажены шестерня16 находящаяся в постоянном зацеплении с шестернями 13 и 19 и шестерня 7 которая находиться в постоянном зацеплении с шестерней 6 промежуточного вала. На первичном валу на шлицах закреплена шестерня 8 по которой скользит зубчатая муфта 9.
На вторичном валу на подшипниках посажены шестерни 10 и 13 и на шлицах шестерни 14 и 11. По шестерни 11 скользит зубчатая муфта 12. Зубчатые муфты 9 и 12 управляются рычагом из кабины водителя. На промежуточном валу 21 на шлицах неподвижно закреплены шестерни 561920. Шестерни 5 и 20 находятся в постоянном зацеплении соответственно с шестернями 27 и 22 ведомого вала посаженными на подшипниках. По шестерне 26 закрепленной неподвижно на шлицах на ведомом валу 23 скользит зубчатая муфта 24 управляемая рычагом из кабины водителя.
Коробка передач соединена с муфтой сцепления двигателя карданным валом 2 для остановки которого установлен тормозок 1.
Задний мост служит для увеличения крутящего момента подводимого к нему от коробки передач и передачи его на колеса. Задний мост состоит из редуктора моста и двух бортовых редукторов (балансира). Редуктор моста соединяется с коробкой передач карданным валом 4 и состоит из смонтированных в одном блоке главной передачи с дифференциалом и двух планетарных передач.
Главная передача – коническая одинарная. Ведущая коническая шестерня 27 вращается на двухрядном коническом роликовом подшипнике. Ведомая коническая шестерня 28 закреплена на ступице дифференциала представляющим собой двухстороннюю зубчатую муфту свободного хода бесшумного типа. Корпус дифференциала вращается на шариковом подшипнике и двухрядном коническом роликовом подшипнике. Передача крутящего момента от главной передачи на колеса осуществляется валами 29 планетарными передачами через шестерни 32 редуктора моста и шестерни 33 34 правого и левого балансиров на колесные валы 35 на которых закреплены ступицы с установленными на них колесами и колесными тормозами 36.
На редукторе заднего моста установлен стояночный тормоз 3 дискового типа диск которого закреплен на фланце входного вала этого редуктора. Стояночный тормоз через систему рычагов и тяг управляется из кабины водителя.
Патентный поиск с целью проверки изделия на патентную чистоту
1 Характеристика объекта разработки
Объектом разработки является самоходная машина- автогрейдер основным рабочим органом которой является отвал с ножом.
Ретро-спектив-ность (за какой период)
Источники информации
Страны (68) и классификационные индексы предмета поиска (МКИ) (79)
Рефе-ратив-ный журнал
О патентном поиске при исследовании автогрейдера
Наименование источника
Классификационные индексы предмета поиска
№ авторских свидетельств патенты или периодические издания
5 Библиографический перечень
Отобранной в процессе поиска информации (указываются изобретения непосредственно относящиеся к исследуемому объекту).
№ авторского свидетельства
Название изобретения
Рабочий орган автогрейдера
Трехосный автогрейдер
Система автоматического управления рабочим органом автогрейдера
Отобранная в процессе поиска информация.
№2134328 Изобретение относится к строительно-дорожным машинам а именно к гидроприводам автогрейдеров. С целью создания более надежной и с большим быстродействием системы защиты отвала автогрейдера в автогрейдере включающем основную и тяговую рамы соединенные между собой гидроцилиндром перемещения и двумя гидроцилиндрами подъема тяговой рамы поршневые полости гидроцилиндров подъема соединены с поршневой полостью гидроцилиндра перемещения тяговой рамы через два обратных клапана а штоковая полость этого гидроцилиндра соединена с напорным клапаном который в свою очередь соединен через два обратных клапана со штоковыми полостями гидроцилиндров подъема отвала при этом отношение площадей штоковых и поршневых полостей гидроцилиндров должны удовлетворять условию Sn1Sш1 Sn2Sш2 где Sn1 - площадь поршневой полости гидроцилиндра подъема тяговой рамы; Sш1 - площадь штоковой полости гидроцилиндра подъема тяговой рамы; Sn2 - площадь поршневой полости гидроцилиндра перемещения тяговой рамы Sш2 - площадь штоковой полости гидроцилиндра перемещения тяговой рамы.
№2184813 Изобретение относится к землеройно-транспортным машинам типа автогрейдеров. Рабочий орган автогрейдера состоит из центральной двух боковых секций и гидроцилиндров их выдвижения. Каждый гидроцилиндр связан с соответствующей боковой секцией с помощью шарнира представляющего корпус образованный стаканом и втулкой который своим стаканом закреплен на конце штока гидроцилиндра а втулкой охватывает верхний конец пальца который своим нижним концом шарнирно соединен с верхней частью наружного конца соответствующей боковой секции. Центральная секция снабжена с тыльной стороны винтовыми направляющими "шевронного" типа с подъемом в направлении от торцов к середине центральной секции в которых посредством ползунов установлены боковые секции. Каждая боковая секция имеет длину l=(L2)-025 м где L - длина центральной секции. Увеличивается производительность планировочных работ упрощается конструкция рабочего органа.
№2200799 Трехосный автогрейдер относится к землеройно-транспортным машинам и предназначен для планировки грунта при строительстве и ремонте дорог а также для скоростной очистки дорог площадей и аэродромов от снега. Трехосный автогрейдер содержит тягач имеющий две задние ведущие оси с установленными на них колесами и связанную с ним хребтовую балку с передней поддерживающей осью на которой установлены колеса. Колеса на задних ведущих осях выполнены управляемыми. Хребтовая балка балансирно соединена с тягачом а колеса на передней поддерживающей оси выполнены свободно поворачивающимися. Одна из задних ведущих осей тягача и передняя поддерживающая ось установлены на поперечно качающихся осях. Повышаются планирующая способность и производительность автогрейдера.
№2006123158 Система автоматического управления рабочим органом автогрейдера содержащая датчик действительной скорости движения машины датчик объема грунта задатчик опорных сигналов управляющий блок включающий в себя устройство ввода постоянное запоминающее устройство к выходам которых подключен однокристальный микроконтроллер присоединенный своим выходом к устройству вывода и исполнительный механизм состоящий из электрозолотников подключенных своим входом к устройству вывода и гидроцилиндров присоединенных входом к выходу электрозолотников и управляющих заглублением или выглублением рабочего органа отличающаяся тем что с целью достижения максимально возможной текущей производительности автогрейдера при высоком качестве получаемой поверхности в процессе планирования грунта управляющим воздействием служит изменение угла захвата косопоставленного отвала для чего она снабжена одним дополнительным гидроцилиндром обеспечивающим стабильную возможность непрерывного управления поворотом отвала во время разработки грунта причем в исполнительном механизме системы автоматического управления используются не гидроцилиндры применяемые для заглубления и выглубления рабочего органа а стандартное устройство поворота отвала и один дополнительный гидроцилиндр для поворота отвала относительно продольной оси машины присоединенный своим входом к выходу электрозолотников к другому выходу которых присоединено своим входом стандартное устройство поворота отвала которые в результате совместной работы увеличивают или уменьшают угол захвата рабочего органа что приводит к отсутствию управляющих воздействий в виде вертикальных перемещений отвала в процессе планирования грунта.
Указанные изобретения в разработанном проекте автогрейдера не применяются. Следовательно разработанный проект автогрейдера обладает патентной чистотой по отношению к зарегистрированным на территории России указанным выше патентам.
Расчет и проектирование автогрейдера
1 Мощность двигателя
Сила тяжести G – главный параметр автогрейдера
где коэффициент учитывающий неравномерность в сечении стружки
при отдельных проходах автогрейдера ;
- площадь поперечного сечения кювета глубина кювета (03 08 м)
удельное сопротивление грунта копанию; если учесть не только
резание но и перемещение грунта как перед отвалом так и вдоль
него то можно полагать что кН м;
коэффициент для колесной формулы ;
коэффициент сцепления для растительного покрова
число проходов обычно составляет .
Максимальная свободная сила тяги автогрейдера
где коэффициент для колесной формулы ;
G – сила тяжести автогрейдера.
Развивающая на ведущих колесах общая мощность
мощность расходуемая на вырезание грунта (полезная мощность);
мощность расходуемая на передвижение автогрейдера как тележки;
мощность расходуемая на буксование.
где коэффициент сцепления ;
сила тяжести автогрейдера кН;
фактическая рабочая скорость автогрейдера кмч;
Мощность расходуемая на передвижение автогрейдера как тележки
где коэффициент сопротивления движению автогрейдера
Мощность расходуемая на буксование
коэффициент сопротивления движению автогрейдера
коэффициент буксования =018 022;
фактическая рабочая скорость автогрейдера кмч
Мощность двигателя для транспортного режима
где коэффициент буксования =004 0045;
к.п.д. трансмиссии - для механической;
заданная максимальная скорость автогрейдера кмч; =35 50 кмч
Необходимая мощность двигателя
где развивающая на ведущих колесах общая мощность;
коэффициент снижения мощности двигателя ввиду неустановившейся нагрузки =09;
к.п.д. трансмиссии - для механической.
На автогрейдер устанавливается двигатель ЯМЗ 236 Г-2 мощностью 110 кВт.
При работе автогрейдера по вырезанию и одновременному перемещению грунта необходимая сила тяги находится по формуле:
где сопротивление перемещению автогрейдера как тележки;
сопротивление сил инерции при трогании с места;
сопротивление грунта резанию;
сопротивление перемещению призмы волочения;
сопротивление от перемещения грунта вверх по отвалу;
сопротивление от перемещения грунта вдоль отвала (в сторону).
где G- общая сила тяжести машины;
- коэффициент сопротивления движению автогрейдера f=007-010;
где скорость машины принимаем для расчета скорость первой передачи
коэффициент учитывающий инерцию вращающихся масс
трансмиссии и двигателя
масса машины М=13120 кг.
где удельное сопротивление грунта резанию кН м;
h – толщина стружки h=(008 012)Н=012*620=744м; где H – высота отвала.
где сила тяжести грунта в призме волочения;
коэффициент трения грунта о грунт ;
где объем призмы волочения;
объемная масса грунта кг м;
ускорение силы тяжести.
где длина призмы L=3680мм=368м;
высота призмы Н=550мм=055м;
поправочный коэффициент .
коэффициент трения грунта о сталь ;
Условие движения автогрейдера без пробуксовки. Необходимо чтобы сила тяги на ведущих колесах превышала общее сопротивление. Для реализации этого тягового усилия должно соблюдаться неравенство
Условие выполняется.
3Расчет производительности автогрейдера
Часовая производительность по объему (мч) вырезанного грунта может быть выражена зависимостью
где V- объем призмы грунта вырезанной и перемещенной отвалом за один
коэффициент использования времени;
t- время рабочего цикла ч.
Время рабочего цикла определяется по формуле
где время прохода по участку которое определяется по его длине и скорости движения машины C;
время подъема и опускания отвала мин; ;
продолжительность поворота автогрейдера в конце участка включая
время затрачиваемое на переключение скоростей .
4Определение сил действующих на автогрейдер
На рисунке 5.4.1 представлена схема сил действующих в процессе резания грунта. Автогрейдер устроен с применением самой распространенной колесной формулы: . Действующие на автогрейдер силы можно разделить на активные и реактивные.
Рисунок 5.4.1 – Силы действующие на автогрейдер
К активным силам относятся сила тяжести и окружная сила на ведущих колесах ; к реактивным - вертикальные реакции на колесах и силы сопротивления грунта перекатыванию колес и реакция грунта действующая на отвал которая может быть разложена на горизонтальную и вертикальную составляющие а также боковые реакции направленные вдоль осей автогрейдера и . Последние образуются за счет сил сцепления развивающихся на поверхностях контактов колес с грунтом.
Здесь допускается что реакция грунта направлена перпендикулярно отвалу а реакции и на правых и левых колесах равны и направлены по их вертикальным осям. Кроме того допускается что реакции на всех ведущих колесах одинаковы. Известными являются силы и а неизвестными - ; ; ; ; ; ; и . Определить эти неизвестные силы можно по уравнениям равновесия:
при этом должны быть учтены следующие соотношения между силами:
Выражаем из 4-го уравнения :
Выразим из 1-го уравнения :
Подставив найденные значения и в 3-е уравнение найдем :
Подставим и найдем и :
Сила будет находится из 5-го уравнения:
Сила будет находится из 2-го уравнения:
Сила стремиться повернуть машину вокруг центра тяжести. Такому повороту препятствуют силы сцепления и поэтому должна быть проверена устойчивость машины в горизонтальной плоскости во время работы. При таком расчете следует принять максимальное значение которое может быть определено из следующего уравнения:
Устойчивость машины определится неравенством
Здесь горизонтальные силы и должны быть определены по условиям сцепления:
5Расчет механизмов управления
Для того чтобы обеспечить бесперебойную работу машины необходимо иметь достаточные скорости управления различными рабочими органами автогрейдера. Так например при перегрузке двигателя когда есть опасность его остановки нужно быстро разгрузить отвал путем подъема его из грунта. Быстрое управление отвалом бывает также необходимым при планировочных работах когда требуется менять его установку в соответствии с рельефом местности.
Механизм подъема отвала рассчитывается исходя из таких предпосылок. Рабочий ход механизма подъема должен обеспечивать заданную глубину копания возможность полного выглубления отвала и удовлетворять условиям проходимости автогрейдера в транспортном положении. При расчете механизма подъема в соответствии с рисунком 5.5.1 определяют подъемное усилие необходимое для выполнения этой операции мощность.
Подъемное усилие рассчитывается при выглублении отвала опущенного в грунт одним концом. Предполагается что угол захвата равен и на отвал действуют силы и .
Рисунок 5.5.1 - Расчетная схема для определения усилия подъема рамы автогрейдера
Тогда согласно схеме этого рисунка
где сила тяжести тяговой рамы с отвалом; здесь можно принять
Считается что в этом случае автогрейдер реализует полное усилие тяги по сцеплению. Тогда
коэффициент для колесной формулы .
Мощность привода механизма находится по формуле:
- скорость подъема отвала принимается равной 009 018 мс;
Поворот отвала в горизонтальной плоскости осуществляется зубчатым редуктором или гидравлическим приводом. Последний может быть выполнен в виде гидродвигателя. В связи с тем что поворот отвала производится лишь при полном его выглублении из грунта затрачиваемая на это мощность незначительна поэтому может не рассчитываться.
6Расчет ходового оборудования
На ходовое устройство автогрейдера действуют усилия являющиеся следствием как силы тяжести машины так и сил действующих со стороны грунта на отвал.
Тележка заднего моста в обычных условиях находится под воздействием реакции и боковых сил . Кроме того оси находятся под воздействием крутящих моментов и . Ранее для упрощения было принято что реакция со стороны грунта для передних и задних колес тележки одинаковы. Однако в действительности ввиду действия подводимого от двигателя крутящего момента реакции неодинаковы.
В соответствии с рисунком 5.6.1 балансир представляет собой систему зубчатых передач где вращение ходовым колесом передается от центральной шестерни через промежуточные зубчатые колеса.
Рисунок 5.6.1 - Схема балансира
Реакции и находятся из уравнения равновесия системы относительно оси подвески балансира с учетом того что
где часть действующей на тележку силы тяжести машины.
где передаточное число от ведущего вала балансира к осям ведущих
к.п.д. балансирной передачи
Здесь расстояние от оси подвески балансира до горизонтальной оси колес.
7Определение нагрузок действующих на раму автогрейдера
7.1 Расчетный случай I.
На раму автогрейдера действует максимальные нагрузки возникающие в условиях нормальной эксплуатации в соответствии с рисунком 5.7.1. Такие условия имеют место в конце зарезания когда передний мост вывешен и упирается в край кювета; задние колеса буксуют на месте отвал установлен под углом 45о и режет одним краем а автогрейдер наклонен под некоторым углом к горизонту
Рисунок 5.7.1 - Схема сил действующих в I случае
Силы и реакции действующие на автогрейдер сосредоточены в следующих точках.
Точка О – конец режущей кромки ножа отвала. Действуют горизонтальное усилие RX боковое RY и вертикальное RZ.
Точки О1 О2 – проекции середин балансиров на опорную поверхность. Действующие реакции и силы: вертикальные реакции Z1 и Z2 силы тяги X1 и X2 боковые реакции Y1 и Y2.
Точка О3 – касание переднего колеса края кювета соответствующее нижнему концу вертикального диаметра передних колес. Действует боковая реакция Y3 .
Вес сосредоточен в центре тяжести автогрейдера определяемом координатами Н и l2 .
Высота расположения центра тяжести
где rc – статический радиус колес.
где В– база автогрейдера.
Силы инерции действуют на машину в процессе торможения. Равнодействующая этих сил Рj приложена в центр тяжести и состовляет
где – коэффициент динамичности ;
– коэффициент использования сцепного веса;
– вес автогрейдера приходящийся на задний мост
Силы и реакции находятся из соотношений:
Определяем усилия в переднем шаровом шарнире приложенные в точке О4:
Рисунок 5.7.2 - Схема сил действующих на передний шаровой шарнир
7.2 Расчетный случай II.
Этот случай соответствует действию нагрузок возникающих при встрече автогрейдера с труднопреодолимым препятствиями. На величину нагрузок основное влияние оказывает масса машины и препятствия и скорость в момент столкновения. Наибольшее значение динамические нагрузки достигают в режиме планировки или перемещения грунта в связи с высокой скоростью выполнения указанных работ составляющей 5 7 кмч при малом буксовании ведущих колес. Ось поворотного круга лежит в плоскости продольной симметрии автогрейдера отвал выдвинут в сторону. Этот случай соответствует рисунку 5.7.3.
Рисунок 5.7.3 - Схема сил действующих во II случая
В точке О (точка контакта с препятствием) действуют силы и . В центре тяжести машины действуют вес и дополнительное динамическое усилие .
Дополнительная динамическая нагрузка
где m – масса автогрейдера;
v – скорость автогрейдера в момент встречи с препятствием;
c – суммарная жесткость 6 20 кНсм.
Силы и реакции находятся из следующих соотношений:
Определяем усилия в переднем шаровом шарнире для II случая:
8 Расчет рамы автогрейдера в САПР АПМ WinMachine
Рама автогрейдера является основным несущим элементом автогрейдера на котором монтируют все силовые агрегаты рабочее и ходовое оборудование. Она изготавливают из профильного проката или отдельных листов свариваемых между собой.
Рама автогрейдера изготовляется из низколегированной стали 09Г2С. Эта сталь имеет по сравнению со сталью Ст3 более высокие механические свойства (временное сопротивление и предел текучести) повышенную стойкость против атмосферной коррозии и меньшую хладноломкость лучшую износостойкость. Применение низколегированных сталей приводит к уменьшению массы металлоконструкции примерно на 15%. Маркируется двумя цифрами показывающими содержание углерода в сотых долях процента. Также содержит 2 % марганца и 1 % кремния.
Название вида: Произвольный Вид
Количество стержней 24
Хрептовая балка (0)
Подмоторная балка (1)
Полка 50 * 200 мм (2)
) Загружение 0 Множитель собст. веса 0
Таблица: Нагрузки на узлы Загружение: Загружение 0
Коэф. температурного расширения [°C]
Коэф. теплопроводности [Вт(°C*мм)]
модели 1045.586843 [кг]
Центр тяжести модели ( 3704.258155 750.000000 148.794750 ) [мм]
Моменты инерции модели ( 21160002000.111843 922052289.126651 62073063.192016 ) [кг*мм*мм]
Список поперечных сечений
Поперечное сечение 0
Площадь 11122.18 кв.мм
Центр масс: X= -0.007 Y= 41.775мм
относит. оси X 169872894.89мм4
относит. оси Y 150520506.10мм4
полярный 320393400.99мм4
Угол наклона главных центральных осей 0.01градус
Поперечное сечение 1
Площадь 5381.25 кв.мм
Центр масс: X= -0.000 Y= 0.001мм
относит. оси X 38500291.81мм4
относит. оси Y 6559724.88мм4
полярный 45060016.69мм4
Поперечное сечение 2
Площадь 9999.85 кв.мм
Центр масс: X= -0.001 Y= 0.000мм
относит. оси X 2079774.01мм4
относит. оси Y 33328392.62мм4
полярный 35408166.63мм4
Угол наклона главных центральных осей 0.00градус
Таблица: Перемещения узлов (Загружение 0)
Линейное перемещение [мм]
Угловое перемещение [градус]
Усилия в узлах стержней (Загружение 0)
Индекс стержня 0 (Rod 10)
Индекс стержня 1 (Rod 11)
Индекс стержня 2 (Rod 12)
Индекс стержня 3 (Rod 13)
Индекс стержня 4 (Rod 14)
Индекс стержня 5 (Rod 15)
Индекс стержня 6 (Rod 16)
Индекс стержня 7 (Rod 17)
Индекс стержня 8 (Rod 19)
Индекс стержня 9 (Rod 20)
Индекс стержня 10 (Rod 21)
Индекс стержня 11 (Rod 22)
Индекс стержня 12 (Rod 23)
Индекс стержня 13 (Rod 25)
Индекс стержня 14 (Rod 26)
Индекс стержня 15 (Rod 27)
Индекс стержня 16 (Rod 28)
Индекс стержня 17 (Rod 29)
Индекс стержня 18 (Rod 30)
Индекс стержня 19 (Rod 36)
Индекс стержня 20 (Rod 37)
Индекс стержня 21 (Rod 38)
Индекс стержня 22 (Rod 39)
Индекс стержня 23 (Rod 40)
Общая масса конструкции 1045.59 кг
Напряжение в стержне (макс.) [Нм^2] (Загружение 0)
Карта результатов - Загружение 0
Гидравлическая система
Гидравлическая система автогрейдера состоит из бака двух гидронасосов распределителя гидроцилиндров гидромотора гидроруля гидроусилителей и трубопроводов.
Рисунок 6.1 - Схема гидравлическая
Н1Н2 - гидронасосы; МН1 МН3 - манометры; УС1УС2 - гидроусилители; КР1 КР5 - клапаны предохранительные; В1В2 - гидробаки; ЗМ1 ЗМ7 - гидрозамки; КЗ1 КЗ3 - клапаны замедлительные; М1 - гидромотор; Т - фильтр; Н3 - насос-дозатор (гидроруль); С1 С14 - гидроцилиндры; Р1 - гидрораспределитель; КРТ1 - клапан потока
Гидронасос расположенный с левой стороны дизеля служит для привода гидроруля. Правый гидронасос предназначен для привода всех остальных агрегатов.
Работа гидросистемы происходит следующим образом: рабочая жидкость из бака всасывается насосами и подается к распределителю и гидрорулю. При нейтральном положении рычагов распределителя полости всех гидроцилиндров и гидромотора заперты и рабочая жидкость от правого насоса пройдя через гидроусилители сцепления тормоза и распределитель сливается через фильтр в бак. Включая соответствующие рукоятки распределителя машинист направляет поток жидкости в соответствующую полость гидроцилиндра (другая полость соединяется при этом со сливом).
Рабочая жидкость от левого насоса проходит через гидроруль и сливается через тот же фильтр в бак. При повороте рулевого колеса жидкость через гидроруль подается в один из цилиндров поворота передних колес.
Бак гидросистемы состоит из двух баков соединенных между собой рукавом низкого давления. Они установлены в задней части подмоторной рамы и служат элементами капота.
К правому баку подсоединены всасывающие трубопроводы насоса НШ-50 дизеля.
К левому баку подключены всасывающий трубопровод насоса НШ-10 слив распределителей и дренаж. Для нормальной работы гидросистемы крышка левого бака должна быть плотно закрыта (для создания избыточного давления).
Маслоуказатели расположены на правом баке. Уровень масла следует проверять при неработающем дизеле. Уровень должен быть не ниже нижнего маслоуказателя и не выше.
Распределитель. Служит для управления потоком рабочей жидкости приводящим в движение исполнительные механизмы в гидроприводе. Под управлением потоком рабочей жидкости подразумевается изменение его направления регулирование его величины и запирание рабочей жидкости в полостях гидроцилиндров и гидромоторов. Применен гидроцилиндр секционного типа. Состоит из 10 секций собранных в один блок с помощью промежуточной плиты и шпилек. В первой секции имеется предохранительный клапан. Рычаги управления золотниками выведены в кабину. Рабочая жидкость подводится к распределительному устройству от насоса НШ-50.
При нейтральном положении золотников рабочая жидкость проходит через распределительное устройство на слив.
При включении золотника любой секции линия слива перекрывается и рабочая жидкость поступает по трубопроводу в полость гидроцилиндра другая полость гидроцилиндра в это время соединяется со сливом.
При повышении давления в напорной линии выше давления настройки открывается предохранительный клапан и рабочая жидкость проходит на слив.
Гидроцилиндры. С их помощью производится перемещение рабочего и другого оборудования автогрейдера. Гидроцилиндры автогрейдера однотипны по устройству. Гидроцилиндры подъема отвала наклдона колес выноса отвала выноса тяговой рамы и поворота колес имеют одинаковые диаметры гильзы поршня штока и уплотнения.
Гидроцилиндры поворота колес плунжерного типа одностороннего действия. Роль поршня в цилиндре выполняет шток.
Гидроцилиндры рыхлителя и бульдозера отличаются большим диаметром гильзы поршня штока и уплотнений.
На гидроцилиндрах наклона колес подъема отвала бульдозера и рыхлителя установлены гидрозамки. Они предназначены для запирания гидроцилиндров при неработающем двигателе или при повреждении трубопроводов от замка к распределителю.
Фильтры. Предназначены для очистки масла от механических примесей размером до 25 мкм. Они устанавливаются в сливных линиях и разделяются на магистральные и встроенные (в гидробаки) фильтры с бумажными фильтрующими элементами и сетчатыми фильтрующими дисками.
Гидробак. Емкость для рабочей жидкости служит для ее охлаждения и создания запаса на случай возможных утечек. Вместимость бака превышает вместимость всей системы в 15 раза и более. Его сваривают из штампованного листа и снабжают заливной горловиной с фильтром грубой очистки сапуном для связи полости бака с атмосферой сливным отверстием с пробкой и указателем уровня масла.
Трубопроводы. Разделяются на жесткие и эластичные. Жесткие трубопроводы изготавливаются из стальных труб (цельно-натянутые для проводов высокого давления и сварные – для низкого давления). Эластичные трубопроводы предназначены для подсоединения подвижных гидроагрегатов (гидроцилиндров). Их подсоединение осуществляется с помощью типовых быстроразъемных резьбовых соединений.
Электрооборудование машины
Рисунок 7.1 - Схема размещения электрооборудования на автогрейдере
34-блокфара; 56-аккумуляторная батарея; 78-стеклоочиститель; 9-фонарь; 10-плафон; 11-отопитель; 12 – стеклоомыватель электрический; 13 – преобразователь напряжения; 14 – датчик указателя уровня топлива; 15 – лампа подкапотная; 16 21 – сигнал звуковой; 17 - датчики; 18 – индикатор загрязненности фильтра; 19 – стартер; 20 – генератор; 22 – фара.
Система электрооборудования автогрейдера выполнена по однопроводной схеме с присоединением минуса на массу автогрейдера. Напряжение в сети 12 В.
Электрооборудование автогрейдера включает следующие основные группы:
- источники электроэнергии питающие электрическую схему;
- потребители электроэнергии обеспечивающих работу систем и механизмов автогрейдера;
- коммутационную аппаратуру и провода с помощью которой осуществляется включение потребителей электроэнергии защита электрической схемы ее монтаж;
- электрические провода.
Все электрооборудование размещается на машине согласно его функциональному назначению сообразуясь со схемой расположения механизмов удобством использования и управления электрооборудованием.
Источниками электроэнергии являются аккумуляторные батареи и генератор переменного тока.
На автогрейдере установлены две аккумуляторные батареи соединенные параллельно что обеспечивает получение общего напряжения 12 В. При пуске дизеля в цепи питания электростартера напряжение равно 24 В. Это обеспечивается переключателем соединяющим батареи последовательно. Питание остальных потребителей в этот момент осуществляется от одной батареи. Схема электрическая принципиальная приведена на чертеже.
Электрооборудование работоспособно только при наличии аккумуляторных батарей. При остановках автогрейдера в целях предупреждения разряда батарей необходимо отключить батарею выключателем «массы».
Основными потребителями электроэнергии на автогрейдерах являются стартер электродвигатели отопительной системы кабины вентилятора и стеклоочистителя контрольно-измерительные приборы фонари система освещения и сигнализации а так же автоматическая система управления отвалом в случае ее наличия.
Система освещения. Предназначена для освещения пути движения и зоны работы автогрейдера в темное время суток обозначения габаритов автогрейдера предупреждения о его поворотах остановках освещения рабочего места машиниста и пульта управления. К ней относятся дорожные (транспортные) фары рабочие фары лампы освещения щитков приборов фонари контрольных ламп указатели поворотов передние и задние фонари плафон. На автогрейдерах предусмотрена и переносная лампа со штепселем включаемая в электрическую цепь предназначенная для освещения мест подлежащих обслуживанию и ремонту.
Фара состоит из корпуса рефлектора с патроном стекла – рассеивателя лампы ободка с прокладкой и проводов. Корпус изготавливается из тонкого стального листа. Рефлектор служит для отражения световых лучей узким параллельным пучком на расстояние до 150 м. Его внутренняя поверхность серебрится хромируется и полируется.
Стекло – рассеиватель выполнен рифленым и служит для преломления световых лучей с целью получения нужного распределения освещенности на полотне дороги.
Лампы используемые в фарах подфарниках имеют крепление фланцевое и на шпильках. При фланцевом креплении ламп подпружиненные штифты патрона входят в прорези фланцев удерживая его на патроне. При креплении на шпильках радиально расположенные на цоколе ламп шпильки входят в Г-образные прорези патрона при нажатии подпружиненный контакт и повороте ламп в нем. Переключателем 13
Звуковая сигнализация. Применяется специальный электрический вибрационный звуковой сигнал питаемый от аккумуляторной батареи 6. Он состоит из корпуса 1 расположенной на его торце мембраны 7 с резонатором 5 электромагнита 3 с якорем 4 по оси которого проходит стержень 10 одной стороной связанный с мембраной и резонатором а другой действующий на контакты 1112 прерывателя цепи 9 электромагнита. Электропитание поступает на клеммы сигнала от аккумуляторной батареи 6 через массу и кнопку 2 сигнала находящуюся на щитке приборов в кабине. При нажатии этой кнопки возбуждается цепь; электромагнита якорь притягивается перемещая стержень 10 с мембраной и размыкая контакты 1112 прерывателя. Мембрана 7 возвращает якорь 4 и стержень 10 в исходное состояние и цикл повторяется. Для исключения искрения контактов в цепь сигнала введен конденсатор 13. Колебания мембраны и создают звук.
Рисунок 7.2 - Сигнал
-корпус; 2-кнопка; 3-электромагнит; 4-якорь; 5-резонатор; 6-аккумуляторная батарея; 7 – мембрана; 8 – перегородка; 9 - обмотка; 10–стержень; 11 12 – контакты прерывателя 13 – конденсатор
Аккумуляторные батареи. Устанавливают на автогрейдерах для питания электрическим током стартера при пусках двигателя а также другого электрооборудования при неработающем двигателе. На автогрейдерах применяют 12-вольтные свинцово-кислотные аккумуляторные батареи различной емкости (в ампер-часах). При необходимости увеличить емкость аккумуляторные батареи соединяют в группу параллельно. На тяжелых автогрейдерах используется электропитание напряжением 24 В. В этом случае две аккумуляторные батареи по 12 вольт соединяют последовательно. Для увеличения емкости к ним параллельно подсоединяется еще такая же групп аккумуляторов.
Рисунок 7.3 - Аккумуляторная батарея
– бак 2 – защитный щиток 3. 7 – отрицательный и положительный штыри 4 – пробка 5 – перемычка 6- крышка 8 – элемент
Каждая аккумуляторная батарея состоит из эбонитового или пластмассового бака 1 разделенного перегородками на шесть отсеков и вставленных в отсеки шести последовательно соединенных элементов 8. В отсеки бака запрессованы тонкостенные кислотостойкие вставки из пластмассы предохраняющие бак от разъедания кислотой. Каждый из шести элементов включает несколько положительно и отрицательно заряженных пластин специальной конструкции. Каждая пластина представляет собой отлитую из свинца с сурьмой (для прочности) решетку в которую впрессована так называемая активная масса т. е. смесь порошкообразного свинца или его окислов (свинцового сурика или свинцового глёта) с серной кислотой. После изготовления такие пластины подвергают многократным процессам зарядки и разрядки. Все пластины с одним зарядом соединяются в полублок общей свинцовой перемычкой с выводным штырем. Таким образом в каждом отсеке бака располагаются два полублока из положительных и отрицательных пластин с таким расчетом чтобы положительные пластины были закрыты с двух сторон отрицательными (поэтому отрицательных на одну больше). Это препятствует короблению положительных пластин при большом разрядном токе. В отсеки заливается электролит которым является раствор серной кислоты плотностью 124 131 гсм3. В эксплутационых условиях аккумуляторная батарея заливается в зависимости от климатического пояса различными по плотности растворами серной кислоты. Плотность электролита зависит от степени заряженности аккумуляторной батареи и с достаточной точностью для практических подсчетов можно принять что уменьшение плотности электролита на 001 гсм3 соответствует разряду батареи на 6 %.
От соприкосновения соседних пластин или замыкания их выпадающей активной массы предохраняют пористые прокладки (сепараторы) через которые легко проходит электролит. Их изготавливают из эбонита пластмассы и др. Элементы в сборе снизу в отсеках бака устанавливаются не на дно а на выступы дна что предохраняет их от замыкания при выпадании на дно активной массы. Сверху каждый элемент перекрыт пластмассовым
щитком 2 с многочисленными отверстиями дли пропуска электролита при
его заливе. Щиток предохраняет пластины от механических повреждений. Каждый отсек сверху закрыт крышкой 6 снабженной отверстием с пробкой 4. Для герметичности места соединения крышки с баком замазаны кислотоупорной мастикой. Через крышки зыведены штыри блока пластин. У соседних элементов штыря соединены междусобой перемычками 5. Крайние выступающие штыри 3 7 аккумуляторной батареи служат для подсоединения проводов от внешней электрической сети. Через отверстия в крышках производится заливка электролита и проверка его уровня а через отверстия в пробках выходят газы из отсеков батареи. Новые аккумуляторные батареи поставляются в сухом (без электролита) виде. Для приведения батареи в работоспособное состояние необходимо залить электролит и зарядить. Напряжение в одном заряженном элементе независимо от количества пластин всегда равно примерно 2 В (при полной разрядке допустимо напряжение 17 В). При последовательном соединении элементов пропорционально растет только напряжение батареи но не ее емкость. Все данные по аккумуляторной батарее заложены в ее маркировке. На автогрейдере установлены батареи марки 6СТ-182ЭМ обозначает последовательно: 6 – число элементов СТ – стартерного типа 182 – емкость в ампер-часах Э – эбонитовый бак М – мипластовый сепаратор.
Генератор. Предназначены для питания электрооборудования и зарядки аккумуляторной батареи во время работы двигателя. Хотя они могут быть переменного и постоянного тока чаще всего применяются генераторы переменного тока отличающиеся простотой и надежностью.
Рисунок 7.4 - Генератор
– обмотка возбуждения ротора 2 – ротор 3 – обмотка статора 4- статор 5 11 – крышки 6 8 – кремнивые вентили. 7 – корпус выпрямителя 9 – крыльчатка 10 – шкив
Такие генераторы состоят из статора 4 собранного из электротехнической стали с надетыми на выступы статора девятью катушками 3 трехфазной обмотки стального ротора 2 имеющего форму шестилучевой звезды с обмотками возбуждения 1 двух крышек 511 с опорными подшипниками качения для вала ротора полупроводникового выпрямителя на кремниевых диодах установленного на передней крышке генератора и предназначенного для преобразования переменного трехфазного тока и приводного шкива 10 служащего для привода генератора от двигателя автогрейдера с помощью клиноременной передачи. На шкиве закреплена крыльчатка 9 вентилятора для создания потока воздуха с целью охлаждения выпрямителя и генератора. Выпрямитель в свою очередь состоит из алюминиевого корпуса 7 с тремя запрессованными в него кремниевыми диодами 8 с отрицательным потенциалом и изолированного теплоотвода с запрессованными диодами 6 с положительным потенциалом.
Генераторы должны работать с реле-регуляторами обеспечивающими автоматическое поддержание напряжения в заданных пределах а также нормальных режимов зарядки аккумуляторной батареи. Для этого реле-регуляторы содержат: регулятор напряжения поддерживающий величину напряжения при изменении оборотов двигателя и генератора; ограничитель силы тока предупреждающий перегрузку генератора при одновременном питании аккумуляторной батареи и электрооборудования; реле обратного тока автоматически включающее аккумуляторную батарею когда ЭДС генератора выше ЭДС батареи и наоборот выключающего аккумуляторную батарею когда ЭДС батареи выше ЭДС генератора чтобы исключить прохождение через генератор разрядного тока и тем самым защитить генератор от повреждений а аккумуляторную батарею от бесполезной разрядки.
Стартеры. Предназначены для проворачивания коленчатого вала двигателя при его пуске. В зависимости от напряжения в электрической системе автогрейдера применяют стартеры с напряжением в цепи 12 и 24 В. Стартер представляет собой электродвигатель постоянного тока питаемый непосредственно от аккумуляторной батареи снабженной выключателем и механизмом включения ведущей шестерни.
Рисунок 7.5 - Схема стартера с механическим включением и дистанционным управлением
– пусковая кнопка 2 – добавочное реле 3 – контакты добавочного реле 4 5 – обмотки сцепного реле 6 – якорь 7 – рычаг 8 – обгонная муфта 9 – ведущая шестерня 10 –пластина 11 – зубчатый венец маховика 12 – стартер 13 – аккумуляторная батарея
Так как этот электродвигатель имеет последовательное или смешанное возбуждение он обладает способностью развивать возрастающий крутящий момент при увеличении сопротивления на якоре что и требуется для пуска холодного двигателя автогрейдера. Крутящий момент достигает наибольшей величины при полном торможении якоря и при питании от полностью заряженной аккумуляторной батареи когда сила тока в цепи стартера достигает максимальной величины (до 800 А). Наиболее употребительны стартеры с механическим включением шестерни и дистанционным управлением. Стартер оснащен сцепным реле имеющим две обмотки 45 с расположенным внутри якорем 6 воздействующим через двуплечий рычаг 7 на обгонную муфту 8 с ведущей шестерней 9 для ввода ее в зацепление с зубчатым венцом 11 маховика. При включении пусковой кнопки 1 срабатывает добавочное реле 2 которое замыкает контакты 3 в цепи сцепного реле и вводит его в действие. В его обе обмотки 45 попадает ток создавая магнитное поле втягивающее якорь 6 а с ним вместе рычаг 7 который перемещает обгонную муфту 8 и шестерню 9 в направлении маховика. При этом толкатель якоря своей торцовой пластиной 10 замкнет цепь стартера 12 приводя его в действие и отключит цепь одной из обмоток якоря (что позволит увеличить силу тока в электродвигателе и соответственно крутящий момент на его валу).После пуска двигателя автогрейдера ведущая шестерня 9 стартера становится ведомой и срабатывает обгонная роликовая муфта 8 предотвращая ее воздействие на вал. Из зацепления с зубчатым венцом 11 маховика шестерню выводит после остановки стартера возвратная пружина.
Экономико-организационный раздел
При подготовке производства новых изделий необходимо проанализировать спрос на разрабатываемые изделия размеры финансирования на разработку проекта и освоение производства с целью обоснования целесообразности принятых решений которые определят экономический успех предприятия в случае успешной реализации новой продукции.
В связи с ограничением финансовых ресурсов и конкуренции в условиях рыночных отношений крайне важно на ранних стадиях конструкторской проработки оценить техническую и экономическую целесообразность проектов и своевременно прекратить финансирование неперспективных вариантов.
Вывод о целесообразности проектирования и производства новых видов продукции возможен с помощью предлагаемых методических указаний.
1 Оценка технической целесообразности конструкции изделия
Сравнительный анализ проектируемого изделия на техническом уровне является первым этапом оценки и отбора лучшего варианта.
- оценка технической целесообразности спроектированной конструкции на основании сравнения с аналогом по основным группам функционально-технических показателей;
- обеспечение расчета лимитной цены изделия.
Оценка выполняется в следующей последовательности:
1.1 Выбор перечня показателей оценки технического уровня конструкций
Все показатели используемые для оценки технического уровня конструкции можно классифицировать на:
- показатели назначения и тактико-технические данные изделия;
- конструкторские (специальные) показатели влияющие на функционирование изделия;
- общие конструкторские (технические) показатели влияющие на условия производства.
Таблица 8.1 Перечень показателей технического уровня и качества изделий.
Проектируемое изделие
Транспортная скорость
Коэф-т исп-ия материала
1.2 Оценка весомости (значимости) показателей
Оценка весомости показателей изделия осуществляется на основе экспертных оценок. Наиболее простым методом индивидуальной экспертизы используемым для оценки весомости показателей является метод попарных сравнений.
Результаты экспертизы представляются в виде матрицы (таблица 6) в которой на пересечении строки и столбца фиксируются индексы тех показателей которые являются более важными в оценке качества изделия при их попарном сравнении.
Далее для каждого показателя определяется количество предпочтений полученных им по отношению ко всем остальным показателям (в первой строке подсчитывается количество 1 во второй – 2 в третьей – 3 и т.д.). Полученное значение увеличивается на единицу.
Количественное представление весомости (значимости) показателей может быть получено по формуле:
где Кi – количество предпочтений i – го показателя.
Таблица 8.2 Матрица попарного сравнения показателей.
1.3 Расчет комплексного показателя технического уровня и качества конструкции
Комплексный показатель позволяет дать обобщенную оценку совокупной технической ценности изделия. В основе оценки лежит сравнение значений выбранного набора показателей базового и проектного варианта с эталонными значениями. В качестве эталонных могут использоваться наилучшие (идеальные) технически достижимые значения рассматриваемых показателей.
Комплексный показатель рассчитывается по формуле:
где q - безразмерный показатель качества по
r Относительный показатель качества по i - му параметру может быть рассчитан с помощью формулы:
где Pjn pjэ - количественные значения i - го показателя соответственно сопоставляемых вариантов и эталонного значения.
Первая формула используется для показателей при увеличении абсолютных значений которых возрастает обобщенный показатель в противном случае вторая формула.
Сопоставление комплексных показателей качества по потенциально воз
можным вариантам конструкций позволяет сделать вывод о технической целесообразности новой разработки определить коэффициент изменения качества при сравнении изделия с аналогом:
Где Wn Wб - комплексные показатели качества проектного и базового вариантов. Данный коэффициент используется при определении лимитной цены проектируемого изделия.
Таблица 8.3 Оценка технической целесообразности конструкции по вариантам (П - проектный Б - базовый).
Наименование показателей по
Коэффициент значимости
значимости показателя
Оценка вклада показателя
Коэф-т исп-я материала
Коэффициент изменения качества
2 Расчет трудоемкости ОКР
Многообразие существующих методов нормирования ОКР можно свести к трем основным: экспертному опытно-статистическому и расчетно аналитическому. Первый метод базируется на экспертных оценках второй -на сравнении нормируемого объекта с аналогичным нормативы на который известны третий - на корреляционных зависимостях трудоемкости работ от основных технических параметров изделия.
В основу предложенной методики по определению трудоемкости ОКР положен бальный метод.
С помощью бальных оценок по отдельным факторам определяется суммарный показатель объема работ в единицах сложности (баллы) который затем с помощью удельного норматива переводится в трудоемкость. Оценка факторов выполняется дифференцированно по главным узлам и видам работ.
Выделено два вида работ: расчетно-аналитические и чертежно-графические для которых порядок расчета объемных показателей различен.
Расчет выполняют в следующей последовательности:
Осуществляется сбор исходной информации о проектируемом объекте:
-наличие аналога или прототипа оценка общей сложности схемы объекта;
- состав главных узлов объекта;
-характеристики узлов (степень новизны конструкции количество кинематических пар количество оригинальных деталей объем конструкции по внешним контурам количество сложных деталей в узлах).
На основании значений исходных показателей таблицы 8.4 – 8.8 выбираются по каждому узлу нормативы объемов работ в баллах для первой и второй групп QH QH а также корректирующие коэффициенты к0 к1 к2 к3 к4. Результаты сведем в табл.8.9.
Таблица 8.4 Показатель объема работ 1-й группы в единицах сложности (баллах).
Характеристика группы новизны
Имеется близкий аналог (отличия не более 20%).
Имеется аналог с небольшими отличиями (20 – 50%).
Имеется прототип похожий по принципу действия и конструкции отдельных узлов. Отличается по многим параметрам.
Известен прототип из информационных и патентных источников. Нет чертежей.
Прототипа нет или он неизвестен.
Нет прототипа в основе конструкции лежит новая идея.
Таблица 8.5 Показатель объема работ 2-й группы в единицах сложности (баллах).
Группа насыщенности узла деталями
Примерное число оригинальных деталей
Таблица 8.6 Коэффициент К1 К2.
Группа сложности по числу кинематических пар
Таблица 8.7 Коэффициент К3.
Группа объемности конструкции узла
Объем по внешним контурам дм3
Таблица 8.8 Коэффициент К4.
Группа насыщенности узла сложными деталями*
Примерное количество сложных деталей
К сложным относятся детали имеющие сложную форму требующие при конструировании специальных расчетов а также расчеты размерных цепей.
Таблица 8.9 Исходные данные для расчета трудоемкости ОКР.
Характеристика объектов
Сложность схемы изделия
Новизна конструкции
Сложность узла по количеству кинематических пар
Насыщенность оригинальными деталями
Объем конструкции по внешним контурам
Насыщенность сложными деталями
Таблица 8.10 Коэффициент К0 учитывающий сложность и степень автоматизации схемы объекта.
Группа сложности схемы
Простейшая схема с одним энергопотоком без управления процессом.
Простая схема с разветвлением энергопотока с частично автоматическим или ручным управлением
Схема средней сложности с ветвящимся энергопотоком наличием блокировочных регулирующих и других элементов.
Сложная схема с автоматизацией рабочего цикла имеются взаимодействия механических электрически гидравлических и других связей в конструкции
Схема повышенной сложности с полной автоматизацией наличием обратных связей управление от устройства автоматики по заданной программе.
Осуществляется расчет показателей.
Показатель объема работ первой группы по узлу i определяется по формуле:
где QH - нормативное значение объема работ (первой группы в баллах) выбираемое в зависимости от группы новизны узла;
K1 - корректирующий коэффициент учитывающий влияние сложности узла по числу кинематических пар.
Показатель объема работ второй группы по узлу i определяется по формуле:
где QH2 - нормативное значение объема работ второй группы в баллах выбираемое в зависимости от количества оригинальных деталей в узле;
К2 К3 К4 - корректирующие коэффициенты учитывающие влияние группы сложности по числу кинематических пар группы объемности насыщенности узла сложными деталями соответственно.
Суммарная трудоемкость ОКР определяется по формуле:
Где tн - норматив удельной трудоемкости чел.-дн.бал. Норматив устанавливается на основе статистических данных по результатам проектирования аналогичных изделий;
Ко - коэффициент учитывающий сложность и степень автоматизации управления объектов в целом. Расчет трудоемкости ОКР проведем в табл.
Объем работ по группам в баллах
Расчетно-аналитические
Чертежно-графические
Норматив удельной трудоемкости на 1 балл чел - дн
Коэффициент сложности схемы К0
Трудоемкость ОКР чел – дн
3 Расчет временных и стоимостных затрат на проектирование изделия
Важными показателями используемые при технико-экономическом анализе изделия являются стоимостные затраты на разработку и срок реализации проекта.
Укрупненный способ расчета основанный на данных о трудоемкости ОКР известной структуре распределения трудозатрат по стадиям проектирования (таблица 8.12) и норматив длительности стадии (таблица 8.13).
Расчет реализуется в табличной (таблица 8.14) форме в следующей последовательности:
) по типу производства выбирается соотношение трудоемкости
стадий проектирования %; tуд;
) рассчитывается трудоемкость отдельных стадий проектирования
)по суммарной трудоемкости ОКР выбирается нормативная длительность цикла технического и рабочего проектирования Ттпи и Трпи
)определяется длительность цикла технологической подготовки
производства по формуле:
) определяется потребная численность исполнителей по стадиям проектирования:
где Fpн - месячный фонд времени работника (176 часов);
Квн - коэффициент выполнения нормы Квн=11 12.
) Определяется фонд заработной платы на разработку проекта:
где 3jм - средняя месячная заработная плата исполнителей
Нсн - коэффициент отчисления на социальные нужды (Нсн=26%);
) определяются полные затраты на разработку проекта:
где Кзп - удельный вес заработной платы в общей структуре себестоимости выбирается по статистическим данным (КЗП = 035 – 04);
) осуществляется оценка срока реализации проекта:
где Кпар - коэффициент параллельности учитывающий величину совмещения стадий (Кпар=07).
Таблица 8.12 Соотношение трудоемкости стадий проектирования %.
Стадии и этапы работ
Разработка ТЗ и эскизное проектирование
Техническое проектирование (ТП)
Рабочее проектирование (РП)
Технологическая подготовка
Проектирование технологических процессов
Проектирование спецоснастки
Таблица 8.13 Нормативы длительности стадий конструкторской подготовки производства.
Общая трудоемкость проектирования н–ч.
Длительность цикла мес.
Таблица 8.14 Расчет временных и стоимостных затрат на проектирование изделия.
Соотношение трудоемкости стадий проектирования %
Трудоемкость нормо-час
Длительность производственного цикла мес.
Потребное количество исполнителей чел
Средняя заработная плата исполнителей руб.
Фонд заработной платы по стадиям руб.
Общий фонд заработной платы на проектирование руб.
Оценка затрат на разработку проекта руб.
Оценка срока реализации проекта мес.
4 Прогнозирование себестоимости изделия
На стадии конструкторской подготовки проекта когда отсутствуют необходимые технологические документы и нормативы для расчета себестоимости приходится применять различные методы прогнозирования: удельных весов и коэффициентов приведения известной структуры себестоимости аналогов.
Прямыми стадиями определяющими себестоимость конструкции являются:
- затраты на основные материалы;
- затраты на комплектующие основные изделия;
- заработная плата производственных рабочих.
4.1 Расчет затрат на основные материалы
Расчет затрат на основные материалы при небольшом количестве деталей и узлов можно выполнять в целом по изделию.
Стоимость основных материалов определяется на основе норм расхода каждого вида материала и цен за вычетом стоимости отходов.
Расчет затрат на основные материалы производим в табличной форме.
Затраты на основные материалы по базовому узлу можно рассчитать по формуле:
Цм - цена материала руб;
Ц° - цена отходов руб;
Котх - средний процент реализации отходов (табл.8.15 );
Ктз - коэффициент транспортно-заготовительных расходов (Ктз=103 -107).
Таблица 8.15 Нормы планируемых отходов %.
Таблица 8.16 Расчет затрат на основные материалы.
Итого по базовому узлу руб.
С учетом транспортно-заготовительных расходов
4.2 Затраты на комплектующие покупные изделия
Затраты на покупные комплектующие изделия осуществляются на основе спецификаций применяемости Рij и цен Цкi по формуле:
Расчет затрат на комплектующие покупные изделия см. табл.8.17
Расчет затрат на комплектующие покупные изделия и полуфабрикаты по базовому узлу.
Двигатель ЯМЗ 236 Г-2
Редуктор поворота отвала
С учетом транспортно-заготовительных расходов руб.
Таблица 8.18 Расчет затрат на основные материалы в целом по изделию.
Комплектующие изделия
4.3 Расчет затрат на заработную плату производственных рабочих
На стадии конструкторской подготовки производства расчет заработной платы базируется на показателе удельной трудоемкости на 1 кг массы конструкции изделия аналога. При отсутствии таких данных для приближенных расчетов можно использовать усредненные отраслевые значения. Расчет заработной платы (основной и дополнительной) производственных рабочих.
Трудоемкость изделия
tуд - удельная трудоемкость 1 кг массы конструкции; G - масса конструкции.
Трудоемкость годового выпуска
Nг-прогнозируемый объм выпуска
Потребное количество основных производственных рабочих
Fpr - годовой действительный фонд времени одного рабочего
Годовой фонд ЗП основной и дополнительный
Зср-средняя заработная плата ОПР
ЗП с учетом отчислений на соц. нужды.
Нсн - коэффициент расходов на социальные нужды Нсн=26%
4.4 Расчет полной себестоимости изделия
Расчет полной себестоимости изделия осуществляется по формуле:
Нвн - норматив внепроизводственных расходов %; (для данного типа производства 7%);
З0и - заработная плата производственных рабочих на единицу изделия.
5 Определение прогнозируемой цены изделия
Лимитная цена выражает предельно допустимый уровень цены проектируемого изделия с учетом улучшения потребительских свойств изделия при котором обеспечивается относительное удешевление его для потребителя.
При отсутствии аналогов для сопоставления и невозможности определить полезный эффект от принципиально нового изделия лимитная цена определяется на основе укрупнённых нормативов материальных и трудовых затрат и повышенной по сравнению с нормативным уровнем рентабельности до 15 раз
где - плановая себестоимость изделия;
- плановый уровень рентабельности к себестоимости изделия.
6 Расчет уровня капитальных вложений в НИОКР и освоение производства
В условиях ограничения финансовых ресурсов технический и коммерческий успех проекта во многом определяется величиной новых капитальных вложений при его разработке и реализации. Капитальные затраты на всех этапах жизненного цикла изделия являются важной оценкой экономической эффективности новых проектов.
Единовременные затраты в сфере производства включают предпроизводственные затраты Кппз и капитальные вложения в производственные фонды завода изготовителя Кпф
Укрупненный расчет капитальных вложений в производственные фонды завода может производиться по формуле.
где Коб - капитальные вложения в оборудование и оснастку руб.;
Кос - капитальные вложения в оборотные средства руб.
где Цп - прогнозируемая цена изделия руб.;
Nе- прогнозируемый объем выпуска шт.;
- отраслевой норматив удельных капитальных вложений в оборудование на один рубль объема реализации новых изделий
- коэффициенты учитывающие соответственно годовой объем
производства для данного типа производства соответственно 125 и 115.
Расчет прибыли на единицу изделия:
7 Оценка эффекта от производства и использования
Расчет экономической эффективности новых изделий основан на сопоставлении результатов и затрат в сфере производства и в сфере использования.
Формула расчета экономического эффекта:
где П – прибыль на одно изделие руб.; ЕН – нормативный коэффициент экономической эффективности ЕН=015; КУ – удельные капитальные вложения в производство рубшт; N – прогнозируемый годовой объем выпуска
Расчет экономической эффективности
8 Сводные показатели оценки экономической целесообразности
Заключительным этапом технико-экономического обоснования проектируемого изделия является составление таблицы показателей оценки экономической целесообразности конструкции (таблица 8.20).
Наименование показателя
Прогнозируемый объем выпуска
Единовременные капитальные вложения
Производственные затраты
Вложения в производство
Текущие издержки на производство
Полная себестоимость
Прибыль на единицу изделия
Прогнозируемая цена изделия
Экономический эффект
Срок реализации проекта
Вывод. Проведенные технико-экономическое обоснование производства автогрейдера выявило перспективность осуществления этого проекта. Проектируемое изделие по ряду технических показателей будет превосходить существующие аналоги. Проведенные экономические расчеты себестоимости и цены изделия позволяют определить планируемую прибыль и рентабельность а также годовой экономический эффект при производстве проектируемого изделия - автогрейдера.
Охрана труда и окружающей природы
Характеризуя условия использования машины устанавливают климатическую зону ее эксплуатации. Данный автогрейдер обычного исполнения предназначенный для районов с умеренным климатом (температура воздуха от -40 до 35 С относительная влажность 60 95%). Одновременно с разработкой узлов и систем машины на начальной стадии проектирования следует обеспечить безвредные и безопасные условия труда обслуживающего персонала.
Обзорность рабочей площадки из кабины оператора определяется конструкцией самой кабины местоположением относительно рабочих органов.
Рисунок 9.1 - Размещение органов управления машиной
- зона очень часто используемых и важных объектов;23- зоны часто и редко используемых объектов.
Хорошая обзорность не вызывает дополнительных движений обеспечивает удобство позы. Это повышает производительность и безопасность труда понижает утомляемость. Проектируя машину на специальном шасси местоположение кабины устанавливают из условия наилучшей обзорности. На основании рекомендаций инженерной психологии эргономике и результатов исследований расположение наиболее часто используемых органов управления назначают в соответствии с данными. Высота кабины автогрейдера должна позволять оператору работать стоя.
Выявляются уровни потенциальных вредностей и опасностей. Рассмотрим такие вредные факторы: шум вибрацию санитарно-гигиенические требования к воздуху рабочей зоны нормы выбросов вредных веществ и дымности отработавших газов.
Шум - это совокупность звуков неблагоприятно воздействующих на человека мешающих его работе и отдыху. ГОСТ 12.1.003-83
По характеру спектра шум следует подразделять: широкополосный с непрерывным спектром шириной более 1 октавы; тональный в спектре которого имеются выраженные дискретные тона. Тональный характер шума для практических целей устанавливают измерением в третьоктавных полосах частот по превышению уровня звукового давления в одной полосе над соседними не менее чем на 10 дБ.
Воздействие шума на человека может проявляться не только в виде специфического поражения органа слуха но и неблагоприятно воздействовать на многие другие органы и функции организма.
Кратковременное воздействие интенсивного шума приводит к временному понижению остроты слуха с быстрым восстановлением функций после прекращения действия фактора (адаптационная защитно-приспособительная реакция слухового органа). Длительное воздействие интенсивного шума может приводить к перераздражению клеток звукового анализатора и его утомлению а затем к стойкому снижению остроты слуха. Наиболее неблагоприятными с этой точки зрения являются высокочастотные (около 4000 Гц) импульсные шумы. Длительное воздействие шума свыше 75 дБ может привести к резкой потере слуха - профессиональной глухоте.
Помимо действия шума на органы слуха установлено его влияние и на центральную нервную систем которое проявляется в виде комплекса симптомов: раздражительность ослабление памяти апатия подавленность изменение кожаной чувствительности замедление скорости психических реакций расстройство сна и другое. При работе на фоне шума повышается расход энергии при одинаковой физической нагрузке значительно ослабляет внимание рабочего увеличивает число ошибок в работе в результате чего снижается производительность труда и ухудшается качество работы. Шум затрудняет своевременную реакцию рабочего что способствует возникнoвению несчастных случаев.
У лиц подвергающихся действию шума отмечаются изменения секреторной и моторной функций желудочно-кишечного тракта скорости дыхания и пульса возникновение сердечно-сосудистых заболеваний гипертонической болезни сдвиги в обменных процессах (нарушение основного витаминного углеводного белкового жирового солевого обменов). Шум с уровнем звукового давления 30 35 дБ является привычным для человека и не беспокоит его. Повышение уровня звукового давления до 40 70 дБ создает значительную нагрузку на нервную систему вызывая ухудшение самочувствия снижение производительности умственного труда а при длительном действии может явиться причиной невроза язвенной и гипертонической болезни.
Допустимые уровни звукового давления в октановых полосах частот уровни звука и эквивалентные уровни звука на рабочих местах следует принимать: для широкополосного постоянного и непостоянного (кроме импульсного) шума – по таблице 9.1.
Таблица 9.1 Допустимые уровни звукового давления в октановых полосах частот.
Вид трудовой деятельности рабочие места
Уровни звукового давления дБ в октановых полосах со среднегеометрическими частотами Гц
Уровни звука и эквивалентные уровни звука дБ А
Рабочие места водителей и обслуживающего персонала тракторов самоходных шасси прицепных и навесных сельскохозяйственных машин строительно-дорожных и др. аналогичных машин
Для тонального и импульсного шума – на 5 дБ меньше значений указанных в таблице.
Источники шума в автогрейдерах двигатели компрессоры коробки передач раздаточные коробки агрегаты гидропривода. Уровень интенсивности основного источника шума – двигателя равен 105 115 дБ для компрессоров и воздуходувок порядка 100 дБ для вибраторов – 105 110 дБ. В кабину шум проникает через воздушную среду через металлоконструкции при жестком креплении к ним источников шума и кабины. Эти конструкции могут усиливать действие первичных источников за счет резонирования отдельных элементов конструкций и стенок ограждений (капот стенки кабины приборные щитки) ненадежном креплении агрегатов к раме.
Для снижения шума могут быть применены следующие методы:
Уменьшение шума в источнике – наиболее рациональное средство борьбы с шумом. Шум механизмов возникает вследствие упругих колебаний машины в целом и ее отдельных частей. Причины этих колебаний – механические аэро- гидродинамические и электрические явления.
Снижение механического шума возникающего вследствие вибрации поверхностей машин и оборудования а также одиночных или периодических ударов сочленении деталей сборочных единиц или конструкций в целом достигается улучшением конструкции оборудования. Заменой по возможности зубчатых и цепных передач клиноременными и зубчато-ременными (снижение шума на 10—14 дБ); заменой подшипников качения на подшипники скольжения (снижение шума на 10—15 дБ); использованием металлов с большим внутренним трением; заменой где это возможно металлических деталей деталями из пластмасс. Эффективно (особенно для высоких тонов) применение демпфирования при котором колеблющаяся поверхность покрывается материалом с большим внутренним трением (резина пробка битум войлок и др.). Основными требованиями предъявляемыми к демпфирующим материалам должны быть высокая эффективность малая масса способность прочно удерживаться на металле и предохранять его от коррозии.
Причиной аэро- и гидродинамических шумов являются соответственно стационарные или нестационарные процессы в газах или жидкостях. Их снижение достигается прежде всего уменьшением скорости обтекания и улучшением аэро- и гидродинамики тел что приводит к уменьшению вихреоб-разования в струях а также путем звукоизоляции источника и установки глушителей.
Электромагнитные шумы возникают вследствие колебаний элементов электромеханических устройств под влиянием переменных магнитных сил — колебания статора и ротора электрических машин сердечника трансформатора и др. Снижение электромагнитного шума осуществляется путем конструктивных изменений в электрических машинах.
Уменьшение шума на пути его распространения путем установки звукоизолирующих преград в виде стен перегородок кожухов причем их эффективность возрастает с увеличением частоты шума.
Сущность звукоизоляции состоит в том что падающая на ограждение энергия отражается в гораздо большей степени чем проникает за ограждение.
Такие преграды имеют гладкую поверхность. При одной и той же толщине звукоизолирующей преграды эффект возрастает с увеличением числа слоев материала но при условии отсутствия жесткой связи между слоями.
Средствами индивидуальной защиты от шума являются вкладыши наушники и шлемофоны.
Вкладыши вставляют в наружный слуховой проход они бывают мягкие (эластичные и волокнистые) и твердые. Мягкие изготавливают из губки ваты марли ультратонкой стекловаты (иногда их пропитывают маслами воском смолами парафином); твердые – из пластмасс эбонита резины.
Вкладыши являются самыми дешевыми и компактными средствами защиты от шума однако недостаточно эффективными (снижение шума на 5-20 дБ) и в ряде случаев неудобными так как раздражают слуховой проход.
Наушники плотно облегают ушную раковину и удерживаются дугообразной пружиной (могут встраиваться в головной убор). Степень ослабления шума зависит от конструкции наушников и частоты шума причем наибольший эффект наблюдается на высоких частотах что необходимо учитывать при их использовании.
Шлемы применяют при воздействии шумов с уровнями более 120 дБ так как в этом случае шум действует непосредственно на мозг человека (через черепную коробку) и вкладыши и наушники не обеспечивают необходимой защиты.
Вибрация – это механические колебания воспринимаемые человеком как сотрясение. ГОСТ 12.1.012-2004. Колебания механических тел с частотой ниже 20 Гц воспринимаются организмом как вибрация а колебания с частотой выше 20 Гц — одновременно и как вибрация и как звук. В настоящее время на многих производствах вибрация является одним из наиболее распространенных вредных факторов воздействующих на работающих.
По способу передачи на человека вибрацию подразделяют:
- общая вибрация передающаяся через опорные поверхности на тело сидящего или стоящего человека;
- локальная вибрация передающаяся через руки человека на ноги сидящего человека и на предплечья контактирующие с вибрирующими поверхностями рабочих столов.
По источнику возникновения общая вибрация бывает:
категории — транспортная вибрация воздействующая на человека на рабочих местах самоходных и прицепных машин транспортных средств при движении по местности и дорогам (в том числе при их строительстве);
категории — транспортно-технологическая вибрация воздействующая на человека на рабочих местах машин перемещающихся по специально подготовленным поверхностям производственных помещений промышленных площадок;
категории — технологическая вибрация воздействующая на человека на рабочих местах стационарных машин или передающаяся на рабочие места не имеющие источников вибрации.
На оператора автогрейдера воздействует общая вибрация 1 категории. Общая вибрация с частотой менее 07 Гц (качка) хотя и неприятна но не приводит к вибрационной болезни. Следствием такой вибрации является морская болезнь которая наблюдается из-за нарушения нормальной деятельности органов равновесия (вестибулярного аппарата). При систематическом воздействии на человека общей вибрации с частотой более 1 Гц могут возникнуть стойкие нарушения опорно-двигательного аппарата центральной и периферической нервной системы системы пищеварения. Особенно опасны общие вибрации с частотами близкими к частотам собственного колебания человека так как в этом случае наблюдается явление резонанса (резкое усиление амплитуды собственных колебаний). Для стоящего наблюдается два пика на частотах 5-12Гц и 17-25 Гц; для сидящего – на частотах 4-6 Гц. Для головы такие частоты лежат в области 20-30 Гц. Начиная с частоты 40 Гц колебания тела под влиянием вибрации становятся во много раз меньше вибрирующей поверхности. Колебания рабочих мест с указанными частотами опасны так как могут вызвать механические повреждения и даже разрыв внутренних органов. Систематическое воздействие общих вибраций в резонансной и околорезонансной зоне может быть причиной вибрационной болезни – стойких нарушения физиологических функций организма обусловленных преимущественно воздействием вибраций на центральную нервную систему. Эти нарушения проявляются в виде головных болей головокружений плохого сна пониженной работоспособности плохого самочувствия нарушений сердечной деятельности.
При работе на автогрейдере появляются колебания незатухающего характера. Высокочастотные с частотой 20 Гц возникают из-за недостаточной уравновешенности двигателя карданных передач. Низкочастотные до 10 Гц появляются вследствие движения машины по неровностям опорной поверхности и в связи с непостоянством нагрузок на рабочем органе. Санитарными нормами ограничивается допустимый уровень вибрации 20 Гц на рабочих местах.
Ослабление вибрации в источнике - наиболее рациональное средство борьбы с вибрациями на момент проектирования. Выбор кинематических и технологических схем при которых динамические процессы вызванные ударами резкими ускорениями были бы исключены или предельно снижены (например замена: кривошипных механизмов равномерно вращающимися ковки и штамповки — прессованием). Уравновешивание балансировка вращающихся частей для обеспечения плавности работы машины. Устранение дефектов и разболтанности отдельных частей.
Чтобы уменьшить воздействие вибрации на машиниста и на остов машины необходима виброизоляция (введение в систему дополнительной упругой связи с целью ослабления передачи вибраций смежному элементу конструкции или рабочему месту) между рамой машины и такими элементами как двигатель коробка передач кабина приборы рычаги управления. Применяют виброизолирующие опоры типа упругих прокладок или пружин.
Пружинные виброизоляторы по сравнению с прокладками имеют ряд преимуществ. Они могут применяться для изоляции как низких так и высоких частот дольше сохраняют постоянство упругих свойств во времени хорошо противостоят действию масел и температуры относительно малогабаритны. Однако они могут пропускать высокочастотные колебания поэтому пружинные виброизоляторы рекомендуется в этом случае устанавливать на прокладки из упругих материалов типа резины (комбинированный виброизолятор) В кабине кресло оператора необходимо подрессоривать. Система должна обеспечивать только вертикальные перемещения кресла. На автогрейдерах следует устанавливать кресла с эластичной подвеской так как жесткое подрессоривание выполняют при частоте колебаний остова менее 2 Гц. Исходными данными для расчета виброизоляции рабочего места являются виброскорость = мс на частоте колебаний=5 Гц масса опорной поверхности =10 кг масса человека =80 кг. Расчет виброизоляции с использованием пружин:
По ГОСТ 12.1.012-90 ССБТ «Вибрационная безопасность. Общие требования» (табл. 1) для заданной частоты вынужденных колебаний =5 Гц допустимую виброскорость рабочего места =045 мс.
Необходимый для данной системы виброизоляции коэффициент передачи
Частоту собственных колебаний виброизолированного рабочего места Гц
Статическая деформация пружинных виброизоляторов м
где Гц – частота собственных колебаний рабочего места; мс2 – ускорение свободного падения.
Требуемая суммарная жесткость пружинных виброизоляторов Нм
Выбираем количество устанавливаемых пружин –
Жесткость одного виброизолятора Нм
Расчетная нагрузка на одну пружину Н
Диаметр проволоки для изготовления пружины м
где =12 – эмпирический коэффициент; =7 – отношение диаметра пружины к диаметру проволоки; – допускаемое напряжение материала пружины на кручение (для пружинной стали марки при Нм2).
Число рабочих витков пружины
где – модуль упругости на сдвиг (для стали Нм2).
Число нерабочих витков пружины
при (на оба торца пружины).
Полное число витков пружины
Также применяют вибродемпфирование уменьшение вибраций за счет увеличения силы трения демпфирующего устройства т. е. перевод энергии колебаний в теплоту и виброгашение (динамическое гашение колебаний) введение в колебательную систему дополнительных масс или увеличение жесткости системы.
В качестве средств индивидуальной защиты от вибрации применяют специальные рукавицы и специальную обувь изготавливаемые с использованием упругодемпфирующих материалов в соответствии с требованиями стандартов ГОСТ 12.4.002—97 «ССБТ. Средства защиты рук от вибрации» ГОСТ 12.4.010—75 «ССБТ. Средства индивидуальной защиты. Рукавицы специальные» ГОСТ 12.4.024—76 «ССБТ. Обувь специальная виброзащитная.»
3 Общие санитарно-гигиенические требования к воздуху рабочей зоны
Микроклимат – метеорологические условия внутренней среды кабины определяемые температурой воздуха относительной влажностью воздуха скоростью движения воздуха интенсивностью теплового излучения.
В кабинах пультах и постах управления технологическими процессами при выполнении работ связанных с нервно - эмоциональным напряжением должны соблюдаться оптимальные величины температуры 22-24 градуса относительной влажности 60-40% и скорости движения не более 01 мс.
Для обеспечения санитарных норм в холодное время года в кабину автогрейдера устанавливается отопительная система. В целях уменьшения теплопотерь стенки кабины выполняют двухслойными. Наружный слой представляет собой обшивку из стального листа толщиной 06 12 мм внутренний – картон или иной термоизоляционный материал (бумага войлок асбест кожа сталь стекло) толщиной до 4мм. При очень низких температурах атмосферного воздуха проектируют дополнительные термоизоляционные слои. Все соединения кабины герметизированы специальными резиновыми уплотнениями. Пол кабины покрыт войлочно-резиновым ковриком предназначенный как для теплоизоляции так и для уменьшения шума и вибрации на рабочем месте. Большое значение для нормализации воздушной среды в кабине имеет система вентиляция. В летний период теплота передаваемая от внешнего воздуха работающего двигателя и посредством солнечной радиации нагревает кабину. Чтобы снизить утомляемость оператора повысить производительность труда ее оснащают системой кондиционирования воздуха.
Содержание вредных веществ в воздухе рабочей зоны не должно превышать предельно допустимых концентраций (ПДК). Полный список вредных веществ и их ПДК приведен ГОСТ 12.1.005-88.
4 Светотехнические приборы машины и освещение территории
Для обеспечения безопасности движения и выполнения работ в темное время суток автогрейдер оборудуется осветительными приборами. Недостаточная освещенность строительных площадок утомляет операторов приводит к удлинению рабочего цикла машины снижению производительности труда а также резко повышает вероятность возникновения аварийной ситуации. Особую опасность представляют машины не оборудованные требуемыми осветительными приборами при движении ночью в потоке с другими транспортными средствами.
В соответствии с требованиями безопасности движения самоходные машины оборудуются: двухсветными фарами переднего света передними и задними габаритными огнями световыми указателями поворотов «стоп-сигналами» фонарями номерного знака. Цвет передних габаритных огней должен быть белый а задних – красный. При необходимости на автогрейдер устанавливаются дополнительные фары для освещения рабочих органов. Кабина оператора оборудуется осветительным плафоном в ней предусматривается подсветка приборного щитка.
Необходимо общее освещение рабочих площадок сигнальная разметка знаки. ГОСТ Р 12.4.026-2001 распространяется на сигнальные цвета знаки безопасности и сигнальную разметку для производственной общественной и иной хозяйственной деятельности людей строительных площадок и иных объектов где необходимо обеспечение безопасности предотвращения несчастных случаев устранение опасности для жизни вреда для здоровья людей.
5 Пожарная безопасность
Пожарная безопасность (ГОСТ 12.1.004-91) объекта должна обеспечиваться системами предотвращения пожара и противопожарной защиты в том числе организационно-техническими мероприятиями.
Противопожарная защита должно достигаться способами: применение средств пожаротушения применение конструкций и материалов в том числе используемых для облицовок конструкций с нормированными показателями пожарной опасности применение пропитки конструкций объектов антипиренами и нанесение на их поверхность огнезащитных красок и составов применение средств коллективной и индивидуальной защиты людей от опасных факторов пожара. Обязательна организация обучения работников правилам пожарной безопасности.
Необходимо соблюдать следующие правила. Запрещается курить и пользоваться огнеопасными предметами во время работы с горюче- смазочными материалами в холодное время года пользоваться факелами для разогрева масла в агрегатах автогрейдера во время заправки и при работающем дизеле производить монтажные и демонтажные работы. После заправки необходимо удалить подтеки горюче-смазочных материалов. Не допускается попадание горюче-смазочных материалов на агрегаты электрооборудования (генератор стартер и т.д.). Промасленный обтирочный материал хранить в закрытом металлическом ящике. Ремонтные работы связанные с искрообразованием и высокой температурой (сварочные паяльные и др.) производить не на автогрейдере за исключением деталей и узлов которые невозможно снять. Сварочные работы производить на расстоянии не менее 20 метров от машины. Соблюдать правила обращения с электролитом низкозамерзающими жидкостями и этилированным бензином. Для тушения воспламенившегося топлива применять огнетушители засыпать или покрыть его брезентом или войлоком.
Автогрейдер должен отвечать экологическим показателям: выбросы вредных веществ с отработавшими газами ГОСТ 17.2.2.05 – 97 дымность отработавших газов ГОСТ 17.2.2.02 – 98.
Значение удельных выбросов вновь изготовленных и капитально отремонтированных на ремонтных заводах дизелей тракторов и машин не должно быть более норм приведенных в таблице 9.2.
Таблица 9.2 Нормы удельных выбросов.
Наименование вредных веществ
Удельные выбросы г(кВт*ч) при воздухообмене
Нормы выбросов оксидов азота установлены по сумме оксидов азота приведенных к оксиду азота(IV)
Нормы выбросов углеводородов установлены по сумме углеводородов приведенных к условному составу С1Н185
Значение дымности на установившихся режимах вновь изготовленных и капитально отремонтированных на ремонтных заводах дизелей тракторов и машин не должно быть более норм приведенных в таблице:
Таблица 9.3 Нормы дымности.
Условный расход воздуха дм3с
Дымность м-1(%) не более при воздухообмене
7 Указания мер безопасности
- К работе на автогрейдере допускаются лица знающие устройство и правила эксплуатации и имеющие удостоверение на право управления автогрейдером.
- Работать на неисправной машине строго запрещается. К работе приступить убедившись в исправности всех механизмов и агрегатов обратив особое внимание на исправность рулевого управления колесных тормозов трансмиссии и дизеля.
- Во время работы пол кабины должен быть чистым и свободным от посторонних предметов посторонним лицам запрещается находиться в кабине и в зоне работы.
- Во время движения автогрейдера запрещается удалять из-под ножей посторонние предметы.
- Нельзя на ходу автогрейдера регулировать исправлять или смазывать его механизмы.
- Запрещается сидеть и стоять на раме рабочих органах и крыльях во время движения.
- При выполнении работ по ремонту или техническому обслуживанию следует надежно затормозить автогрейдер стояночным тормозом опустить рабочее оборудование на землю или подставки. Производить работы при работающем двигателе не допускается.
- Работы по техническому обслуживанию или ремонту должны производиться в специально отведенных местах где обеспечивается удобный доступ и хорошее освещение.
- Во время технического обслуживания и ремонта приборов электрооборудования выключить включатель «массы».
- Монтаж или демонтаж шин производить на стенде или чистом полу. При накачивании необходимо следить за показаниями манометра не допускается превышение давления воздуха выше нормы.
- При необходимости отлучиться от машины надо затормозить стояночным тормозом и заглушить двигатель. Нельзя оставлять автогрейдер на уклонах.
- Категорически запрещается при спусках с горы переключать передачи или выключать муфту сцепления. Спуск с горы производить на рабочих передачах.
- В случае невозможности транспортирования автогрейдера на специальное место для ремонта его необходимо оградить на месте вынужденной остановки или установить знаки аварийной остановки согласно «Правилам дорожного движения».
- После окончания смены машинист обязан предупредить сменщика о всех неисправностях автогрейдера.
- При пользовании домкратом необходимо придать ему устойчивое положение предупреждающее завал машины. Места установки домкратов под балкой переднего моста и под корпусами балансиров.
- Перед запуском дизеля поставить рычаг переключения передач в нейтральное положение и затормозить автогрейдер стояночным тормозом.
- Езда на автогрейдере при открытых незакрепленных дверях кабины запрещается. При движении на транспортных передачах двери должны быть закрыты.
- Рычаг распределителя управляющий положением кронштейна подвески гидроцилиндров подъема отвала тяговой рамы должен постоянно находиться в нейтральном положении. При установке отвала для срезания откосов запрещено находиться посторонним лицам в радиусе не менее 3-х метров.
- При транспортировании автогрейдера обращать особое внимание на выбор скоростей движения с учетом дорожных условий радиусов поворота видимости и обзорности.
- При транспортировании автогрейдера своим ходом на большие расстояния тяговую раму и бульдозерный отвал закрепить проволокой к основной раме. - Поворот (складывание) шарнирно-сочлененной рамы можно производить только на месте или в движении со скоростью не более 6 кмч (первая рабочая передача).
- Движение автогрейдера со сложенной рамой на транспортных передачах запрещается.
- При выносе отвала и поворота рамы следите за тем чтобы отвал не касался других частей машины.
В данном дипломном проекте был проведен сравнительный анализ различных вариантов исполнения автогрейдера выполнен патентный поиск с целью проверки изделия на патентную чистоту. Приведено описание устройства и работы выбранного варианта автогрейдера.
Определены основные параметры машины такие как масса и требуемая мощность двигателя. Был выбран двигатель соответствующий полученным значениям. Была определена часовая производительность по объему вырезанного грунта. На основе полученных параметров сделан тяговый расчет и в результате которого были найдены:
сопротивление перемещению автогрейдера как тележки;
Определены силы действующие на рабочее оборудование и раму: активные и реактивные. Был произведен расчет механизма управления для обеспечения бесперебойной работы машины. Рассчитано ходовое оборудование.
Определены силы возникающие во время работы и действующие на раму автогрейдера по данным которых проведен расчет основной рамы с использованием системы автоматизированного проектирования САПР АПМ WinMachine.
Приведены схемы гидравлической и электрической системы автогрейдера. Имеется описание работы и составных частей приведенных схем.
В экономическом разделе дипломного проекта проведено технико-экономическое обоснование производства автогрейдера. Проведенные экономические расчеты себестоимости и цены изделия позволяют определить прибыль годовой экономический эффект при производстве изделия.
В разделе охрана труда были выявлены вредные факторы влияющие на рабочего в результате эксплуатации автогрейдера. Предложены средства защиты от них.
Хархута Н. Я. Дорожные машины : теория конструкция и расчет Н. Я. Хархута М.И. Капустин В.П. Семенов И.М. Эвентов. - 2-е изд. перераб. и доп. – Л. : Машиностроение 1976. – 472 с.
Бородачев И. П. Справочник конструктора дорожных машин : cправочник Б. Ф. Бондаков С.А.Варганов М.Р. Гарбер и др.. - 2-е изд. перераб. И доп.– М. : Машиностроение 1973. – 504 с.
Холодов А. М. Проектирование машин для земляных работ : учеб. пособиеА.М. Холодов. – Х. : Вища. шк. Изд-во при Харьк. ун-те 1986. – 272 с.
Машины для землеройно-транспортных работ: отраслевой каталог ЦНИИТЭстроймаш. – М.:1989.-202 с.
Бандаков Б.Ф. Автогрейдеры: учеб. для подг. и повыш. квал-ции кадров и мастеров на пр-ве. Б. Ф. Бандаков. – М. : Транспорт 1988. – 301 с.
Абрамов Н. Н. Курсовое и дипломное проектирование. Учеб. пособие для студентов дорожно-строительных вузов. М. «Высш. школа» 1972. -120с.
Добронравов С. С. Строительные машины и оборудование: справочник С. С. Добронравов М.С. Добронравов. – 2-е изд. перераб. и доп.– М. : Высш. шк. 2006. – 445 с.
Плешков Д. И. Бульдозеры скреперы грейдеры. Учебник для средн. проф.-техн. учеб. заведений. Плешков Д. И. Хейфец М. И. Яркин А. А. Изд. 2е перераб. и доп. – М: Высш. шк. 1976. 320 с.
Папаев С. Т. Охрана труда. С.Т. Папаев - М.: ИПК Издательство стандартов 2003. - 400 с.
О дальнейшем стимулировании творческой активности молодых ученых : Пост. Совета Министров СССР от 26 янв. 1991 года № 231 Собр. законодательства РФ. - 1991. - № 6. – Ст. 117.
ГОСТ Р 51771 –2001. Аппаратура радиоэлектронная бытовая. Входные и выходные параметры и типы соединений. Технические требования. – Введ. 2002-01-01. – М. : Госстандарт России : Изд-во стандартов 2001. – IV 27 с. : ил.
ГОСТ 7.53-2001. Издания. Международная стандартная нумерация книг. - Взамен ГОСТ 7.53-86 ; введ. 2002-07-01. - Минск : Межгос. совет по стандартизации метрологии и сертификации ; М. : Изд-во стандартов сор. 2002. – 3 с. - (Система стандартов по информации библиотечному и издательскому делу).
А. с. 107970 СССР МКИ В25 J 1500. Устройство для захвата неориентированных деталей типа валов
В. С. Ваулин В. Г. Кемайкин (СССР). – № 336058525 -08 ;
заявл. 23.11.81 ; опубл. 30.03.83 Бюл. № 12. - 2 с. : ил.
Пат. 2187888 Российская Федерация МПК H 04 B 138 H 04 J 1300. Приемопередающее устройство Чуева В. И. ; заявитель и патентообладатель Воронеж. науч.-исслед. ин-т связи. - № 200013173609 ; заявл. 18.12.00 ; опубл. 20.08.02 Бюл. № 23 (II ч.). - 3 с. : ил.
Винтовой холодильный компрессор ВХ 1400-7-3 : каталог Центр. ин-т НТИ и техн.-экон. исслед. по хим. и нефт. машиностроению. – М. 1993. – 2 с.
Оптовые цены на инструменты с алмазной насечкой : прейскурант № 19-08 : утв. Госкомцен СССР 12.08.90 : ввод. в действие 01.01.91. – М. : Прейскурантиздат 1990. – 60 с.
Спиридонова В. И. Понятие свободы у М. Крозье и его критика В. И. Спиридонова МГУ им. М. В. Ломоносова. - М. 1984. – 24 с. – Библиогр.: с. 23-24. - Деп. в ИНИОН АН СССР 27.09.92 № 319097.
Белова С.В. Безопасность жизнедеятельности: Учебник для вузовС.В. Белов А.В. Ильницкая А.Ф. Козьяков и др. 4-е изд. испр. и доп. – М.: Высш. шк. 2004. – 606 с.
Гохберг М.М. Справочник по кранам: в 2 т. Т. 1. Характеристики материалов и нагрузок В.И. Брауде М.М. Гохберг И.Е. Звягин и др.-Л.:Машиностроение. Лен-ое отд-ие 1988.-536 с.
Техническое описание и инструкция по экспл-ции
автогрейдера ДЗ-180А ТО 1993. – 157 с.
Каталог деталей и сборочных единиц ДЗ-180А Каталог
Каталог на рус.англ.фр.и исп. яз. – Внешторгиздат
ГРМТИ 1993. – 127 с.
Крикун В.Я. Строительные машины: учебное Книга
пособие для вузовВ.Я. Крикун. –М.: АСВ2005.-232с. с 1 автором
пояснительная записка.doc
1 Описание автогрейдера
При отделке земляного полотна дороги требуется произвести вырезание кюветов и профилирование поверхности и боковых откосов насыпи и выемок для придания этим элементам дорожного полотна необходимых поперечных и продольных уклонов. Эти работы выполняют автогрейдеры.
Автогрейдер - самоходная землеройно-транспортная колесная дорожно-строительная машина. Мощные автогрейдеры могут быть использованы и для возведения земляного полотна в нулевых отметках. Автогрейдеры применяют также на планировочных и вспомогательных работах и в других отраслях строительства - при сооружении площадок профильных выемок и насыпей. В зимнее время автогрейдером очищают дороги от уплотненного снега.
Автогрейдер обладает большой маневренностью и возможностью изменения углов установки отвала в горизонтальной и вертикальной плоскостях а также может осуществлять вынос отвала в сторону.
Рисунок 1.1 Общий вид автогрейдера
-двигатель;2-рычаги управления;3-коробка управления;4-редуктор подъема отвала;5-редуктор выноса отвала;6-редуктор подъема кировщика;7-редуктор рулевого механизма;8-кировщик;9-тяговая рама;10-поворотный круг;11-отвал;12-балансир
Прицепные грейдеры обладая теми же функциями как и автогрейдёры не имеют собственного двигателя и трансмиссии и работают на прицепе за гусеничными тракторами. Прицепные грейдеры значительно уступают
автогрейдерам в маневренности и производительности.
Кроме основного рабочего органа - отвала и имеющегося на многих автогрейдерах кирковщика эта машина может работать также с различными видами сменного навесного рабочего оборудования: грейдер-элеваторного снегоочистительного и другого будучи дешевле специализированных машин. В силу этих причин выпуск прицепных грейдеров продолжается главным образом с целью сезонного использования тракторов но этот тип машин не является перспективным и не развивается.
2 Классификация автогрейдеров
Автогрейдеры можно классифицировать по следующим основным признакам:
а) повесу машины: легкие весом до 9 т средние весом 10-12 т тяжелые весом 13-15 т и особотяжелые весом 17-23 т;
б) по устройству ходового оборудования: двухосные - с одной или двумя ведущими осями и трехосные - с двумя или тремя ведущими осями;
в) по системе управления рабочими органами:
с механическим (редукторным) или гидравлическим управлением.
Легкие автогрейдеры используют для содержания и мелкого ремонта дорог и для постройки грунтовых дорог в нулевых отметках.
Средние автогрейдеры используют для возведения земляного полотна при небольших отметках насыпи и выемки в грунтах оптимальной влажности и для среднего ремонта дорог.
Автогрейдеры тяжелые и особотяжелые целесообразно использовать
при наличии больших объемов работ и в тяжелых грунтовые условиях.
Обычно у автогрейдеров управляемыми (поворотными) являются колеса передней оси; некоторые типы автогрейдеров имеют управляемыми колеса передней и задней оси что обеспечивает им возможность поворота со значительно меньшим радиусом и позволяет осуществлять поступательное движение при котором колеса задней оси не движутся по окончательно отделанной поверхности дороги.
Для удобства обозначения количества ведущих осей и осей имеющих управляемые колеса в технической литературе часто приводятся условные обозначения:
А - число осей с управляемыми колесами;
Б - число ведущих осей;
В - общее число осей машины.
Пользуясь таким способом обозначения для двухосного автогрейдера с двумя ведущими осями и всеми управляемыми колесами колесная схема будет обозначаться 2х2х2; для автогрейдера трехосного с двумя ведущими и одной управляемой осью колесная схема будет иметь вид.
Машины трехосные с двумя ведущими и одной управляемой осью (1 х 2 х 3) обладают по сравнению с другими автогрейдерами лучшей планирующей способностью достаточно хорошими тяговыми качествами и способностью сохранять устойчивость заданного прямолинейного движения при наличии боковой нагрузки например когда отвал работает будучи вынесенным в сторону. Такую схему ходового оборудования имеет подавляющее большинство мирового парка автогрейдеров.
Автогрейдеры со всеми ведущими колесами значительно дороже и сложнее в эксплуатации поэтому их применяют лишь в тех случаях когда от машины требуются высокие тяговые качества в трудных грунтовых условиях.
Поперечная устойчивость автогрейдеров при боковых нагрузках достигается за счет наклона ведомых колес при помощи специального механизма.
Основным рабочим органом автогрейдера является отвал с ножом; отвал имеет постоянный радиус кривизны. Практикой установлены следующие пределы изменения углов установки отвала автогрейдера: угол резании б = 30-г----80° с интервалами перестановки в 3-5°; угол захвата (р = 0-180°). Применение полноповоротного механизма установки отвала в плане дает возможность работать при любом угле захвата.
Рабочее оборудование автогрейдера состоит из отвала укрепленного на тяговой раме и кирковщика. Все механизмы управления рабочим оборудованием приводятся карданными валами от коробки управления установленной на колонке независимого отбора мощности. Все четыре колеса этого автогрейдера являются ведущими и управляемыми.
Система управления колесами позволяет например повернуть передние и задние колеса в противоположные стороны; при этом машина будет перемещаться по дуге круга; если же передние и задние колеса повернуть в одну сторону то машина будет двигаться поступательно под некоторые углом к своей продольной оси.
3 Технологические схемы производства работ
Технологический процесс выполнения работы состоит из ряда последовательных операций: зарезания грунта поперечного его перемещения послойного разравнивания. Для этого необходима бригада автогрейдеров. Бригада автогрейдеров состоит из четырех однотипных машин(рисунок 1.2) работающих в одном комплекте. Первый автогрейдер работает на зарезании грунта из резерва. Зарезание грунта производится левым или правым концами отвала в зависимости от направления движения автогрейдера. Отвал устанавливают на максимальное зарезание с углом захвата 40-45 угол наклона до 13 и угол резания 40-45°. Зарезание ведут послойно от внутренней бровки резерва стружкой возможно большего сечения.
Рисунок 1.2 Схема работы бригады автогрейдеров
Вырезанный грунт перемещается к оси насыпи тремя автогрейдерами работающими по ступенчатой схеме одним фронтом. Для большей производительности валы автогрейдеров работающих на перемещении оборудуются удлинителями и имеют соответствующую установку: угол захвата 40-45° угол наклона 3-5 и угол резания 45-50°. Следует стремиться за один проход грейдеров переместить грунт на возможно большее расстояние. Технологически возведение насыпи грейдерами производят послойно: после отсыпки первого слоя грунта таким же порядком отсыпают второй и последующие слои постепенно наращивая высоту насыпи. Валики грунта в насыпи можно укладывать по-разному в зависимости от заданной степени уплотнения грунта насыпи. Если насыпь не требует наслойного уплотнения после каждого слоя отсыпанного грунта а расчет ведется на ее естественную осадку и уплотнение то валики в насыпи можно укладывать вприжим.
Если на насыпи будет устроено капитальное покрытие то насыпь необходимо возводить с послойным уплотнении. Для повышения производительности грейдеров необходимо: увеличить площадь поперечного сечения стружки применять высокие скорости передвижения грейдера уменьшать холостые пробеги а также рыхление грунта одновременную работу двух автогрейдеров (рисунок 1.3).
Рисунок 1.3 Схема одновременной работы двух автогрейдеров
Механизация строительства
Проектирование механизации строительства дорог связано с определением типов машин и их количества которые впоследствии объединяются в комплекты и комплексы. Оптимальным будет тот парк машин использование которого обеспечит выполнение заданных объёмов работ в заданные сроки с минимальными денежными энергетическими трудовыми и другими видами затрат.
Общепринятым методом определения оптимального состава специализированного комплекта машин (СКМ) в настоящее время является сравнение технико-экономических показателей различных комплектов машин для принятого темпа строительства.Целью данного раздела дипломного проекта является определение количественных составов СКМ и сопоставление их технико-экономических показателей.
1 Описание объекта строительства
Вид работ: возведение земляного полотна.
Объём работ: 700000 м3.
Категория грунта – I.
Параметры объекта: высота насыпи Н = 08 м ширина дороги L = 15 м уклон m = 1:115.
Ведущая машина: скрепер самоходный объём ковша ДЗ - 11 q = 9 м3.
Дальность транспортирования: 05; 10; 15; 20 км.
2 Технология механизация и организация строительства
2.1 Технология производства работ
Технологическая схема строительства земляного полотна и задействованный при этом комплект машин приведён в таблице 2.1
Таблица 2.1-Схема строительства земляного полотна
Срезка растительного слоя
Автогрейдер ДЗ-143 ДЗ-143М
Разработка и премещение грунта в I-й слой насыпи
Разработка и премещение грунта в II-й слой насыпи
Планировка верха земляного полотна
Прикатка верха земляного полотна
Планирование откосов насыпи
2.2 Механизация строительства
Для устройства земляного полотна формируется специализированный комплект машин (СКМ) ведущей машиной в котором является скрепер ДЗ - 11 и модернизированный автогрейдер ДЗ-143М.
Для срезки растительного слоя применяем модернизированный автогрейдер ДЗ – 143М.
Для разработки грунта в резерве и доставке его тело земляного полотна используется прицепной скрепер ДЗ-11.
В разделе механизация строительства будут рассчитаны два варианта СКМ которые мы условно назовём “старый” или СКМ-1 и “новый” – CКМ-2. Соответственно СКМ-1 работает по схеме с базовым автогрейдером ДЗ – 143 а СКМ-2 с модернизированным автогрейдером ДЗ-143М. Это даст нам возможность сравнить эффективность изменения конструкции автогрейдера.
В таблице 2.2 приведены марки машин используемых в двух вариантах СКМ с указанием их цены мощности силовой установки и технологических операций на которых они используются.
Таблица 2.2 – Марки машин используемых в СКМ.
Разработка и перемещение грунта
Планировка верха земляного
Прикатка верха земляного
3 Организация производства работ
Под организацией работ понимается установление сроков выполнения
работ режима сменности работы обеспечение строящегося объекта материалами машинами транспортными средствами трудовыми ресурсами электроэнергией связью и другими ресурсами.
В дорожном строительстве наибольшее распространение получил поточный метод организации работ. Основным показателем потока является его темп то есть объём готовой продукции выпускаемый в единицу времени.
Определение темпа работ
Темп работ t м3смену определяется по формуле:
гдеVобщ – общий объём работ м3 Vобщ = 700000 м3;
Nрд – число рабочих смен в строительном сезоне. Строительный сезон длится с 25.05 по 8.10 число нерабочих дне по метеоусловиям – 5. По календарю определяем число рабочих дней Nрд = 85. Число рабочих смен определяется по формуле:
гдеКсм – коэффициент сменности Ксм = 14 2; примем Ксм = 14.
3.1 Определение длины сменной захватки
Рисунок 2.1- Поперечное сечение полотна
По рисунку 2.1 определяем расстояния l1 l2 и площади поперечного сечения насыпи.
Общая площадь поперечного сечения насыпи м2 определяется по формуле:
гдеН – высота насыпи Н = 08 м;
расстояние l2 м определяется по формуле:
Поперечные сечения слоёв определятся соответственно по формулам:
гдеh – высота насыпи h = 04 м;
расстояние l1 м определяется по формуле:
Длина сменной захватки мсмену определится по формуле:
гдеt – темп работ м3смену t = 5882 м3смену.
3.2 Определение эксплуатационных производительностей машин
Эксплуатационные производительности машин м2см входящих в составы СКМ-1 и СКМ-2 кроме автогрейдера ДЗ – 143 и ДЗ-143М определим по формуле 12
Квi – коэффициент использования i-й машины по времени в течении смены учитывающий непроизводительные затраты времени ма шины по техническим технологическим причинам.
Значения эксплуатационных производительностей машин определённых по формуле (2.6) значения сменных производительностей средств механизации определённые по Е и Р и принятые значения коэффициентов использования по времени в течение смены для машин входящих в составы СКМ-1 и СКМ-2 кроме скрепера приведены в таблице 2.3.
Работа по срезке растительного слоя производится автогрейдером ДЗ-143. Объём работы в смену м2смену определяется по формуле:
гдеLп – длина полосы (см. рисунок 1) Lп = 194 м.
Сменная эксплуатационная производительность автогрейдера при срезке растительного слоя м2смену определяется по формуле:
Производительность автогрейдера при планировании откосов производим по формуле
где L – длина технологической захватки м; bз – ширина захватки м; n – число проходов; tср – среднее время операций за один проход.
t1 – время на перемещение отвалом грунта с; t2 – время подъёма отвала t2=5c; t3 – время на переключение передач и повороты t3=40 с; t4 – время на опускание отвала в рабочее положение t4=3с.
Определим сменную производительность для базовой машины ДЗ - 143
Определим сменную производительность для модернизированной
Необходимое число машиносмен определяется по формуле:
гдеVсм – сменный объём работ;
П – производительность.
Расчёт необходимого числа машиносмен сведён в таблице 2.4
Разработка и перемещение грунта в первый слой насыпи
Разработка грунта производится скрепером самоходным . Производительность скрепера м3смену определяется по формуле:
гдеНВ – норма времени выполнения операции копания час определяется по формуле:
гдеНВо – основная норма времени час НВо = 25 часа (табл.1 стр. 82 1);
Д – добавочное время час Д = 017 часа;
lтр – дальность транспортирования.
Результаты расчёта по формуле (1.13) сведены в таблице 2.3.
Таблица 2.3- Расчёт производительности скрепера
Дальность транспортирования м.
Производительность скрепера ДЗ-11
Число машиносмен необходимых для выполнения общего объёма работ Vобщ определяется по формуле:
гдеt – темп работ м3смену t = 5882 м3смену;
Результаты расчёта по формуле (2.15) сведены в таблице 2.4.
Таблица 2.4- Число машиносмен скреперов
В качестве расчётного значения принимаем число скреперов Nскр = 21 расчётная производительность
Объём работы в смену м3смену определяется по формуле:
гдеLсм – длина захватки Lсм = 4539 м;
S1 – площадь поперечного сечения первого слоя м2 S1 = 672 м2.
Необходимое число скреперов:
= 1056 примем Nскр = 11.
Уплотнение первого слоя насыпи
Уплотнение насыпи проводим только тяжёлым катком ДУ-29 т.к. при отсыпке скрепер достаточно уплотняет насыпь и проходов среднего катка не требуется. Уплотнение проводим при четырёх проходах по одному следу. Объём работы в смену м3смену определяется по формуле (2.16). 3050 м3смену. Сменная производительность катков при уплотнении насыпи м3смену определяется по формуле:
гдеТсм – продолжительность смены Тсм = 82 часа;
НВ – норма времени выполнения операции часов для ДУ-29: НВ = 022 часа.
Производительность ДУ-29:
Необходимое число машиносмен катков определяется по формуле (2.15) расчёт сведен в таблице 2.4.
Разработка и перемещение грунта во второй слой насыпи
S2 – площадь поперечного сечения второго слоя м2 S2 = 624 м2.
Необходимое число машиносмен скреперов определяется по формуле (2.12) расчёт сведен в таблице 2.4.
Уплотнение второго слоя насыпи
Объём работы в смену м3смену определяется по формуле (2.18). 2832 м3смену. Сменная производительность катков при уплотнении насыпи м3смену определяется по формуле (1.17).
Необходимое число машиносмен определяется по формуле (2.12) расчёт сведен в таблице 2.4.
Планировка верха полотна производится автогрейдером ДЗ-143 илиДЗ-143М. Объём работы в смену м2смену определяется по формуле:
гдеВ – ширина дороги м В = 15 м.
Сменная производительность автогрейдера при при планировке земляного полотна м2смену определяется по формуле (2.11).
Прикатку полотна осуществляем средним катком ДУ-31А. Объём работы в смену м2смену определяется по формуле (2.17). 6808 м2смену. Сменная производительность катка при уплотнении поверхности м2смену определяется по формуле:
гдеНВ – норма времени выполнения операции часов для ДУ-31А при уплотнении поверхности НВ = 079 часа часа (табл.3 стр.104 1).
Планировка откосов насыпи
Планирование откосов насыпи производим автогрейдером ДЗ-143. Способ
планировки – рабочий ход в двух направлениях. Ширина откоса м определяется по формуле:
гдеН – высота насыпи м Н = 08 м;
m – уклон насыпи m = 1115.
Объём работы в смену м2смену определяется по формуле:
необходимое число машиносмен определяется по формуле (2.12) расчёт сведен в таблице 2.4.
Таблица 2.4-Технологический расчёт строительства земляного полотна
Технологическая операция
Сменная производительность
Необходимое число машиносмен
Рассматривая весь технологический процесс можно отметить что при использовании модернизированного автогрейдера ДЗ-143М количество машиносмен существенно снижается.
Для ДЗ -143 – 134 машиносмена
Для ДЗ -143М – 043 машиносмена
В таблице 2.5 сведен расчёт необходимого количества машиносмен скрепера при всех дальностях транспортирования.
Таблица 2.5- Количество машиносмен скреперов
Разработка и перемещение грунта в I-й слой насыпи
Разработка и перемещение грунта в II-й слой насыпи
3.3 Выбор количества машин в комплекте
Основываясь на данных таблицы 2.4 окончательно принимаем следующий комплект машин:
Таблица 2. 6 -Комплекты машин
Делая вывод можно отметить что использование модернизированного автогрейдера ДЗ – 143М позволяет уменьшить количество автогрейдеров во втором комплекте СКМ 2 что выгодно его отличает от базового комплекта т.к. при одинаковом объёме работы требуется меньшее количество машин и положительно скажется на эффективности строительства земляного полотна.
Проведение патентного исследования и анализ его результатов
1 Разработка задания на проведение патентных исследований
На проведение патентного исследования
Этап (стадия): техническое задание
Задачи патентных исследований: Разработка технического предложения на модернизацию автогрейдера ДЗ-143М
Подразделения - исполнители (исполнители)
Краткое содержание работ
Ответственные исполнители
Проведение патентных исследований
2 Разработка регламента поиска информации
Регламента поиска представляет собой программу определяющую область проведения поиска по фондам патентной и другой научно – технической (в том числе конструкторской - экономической) информации. Для определения области поиска требуется сформировать предмет поиска и классификационные рубрики (МКИ НКИ УДК).
Предмет поиска определяют исходя из конкретных задач патентных исследований категории объекта (устройство способ вещество) а так же из того какие элементы параметры свойства и другие его характеристики предполагается исследовать.
Наименование темы: Автогрейдер ДЗ-143М
Таблица 3.2 – анализ результата поиска
Предмет поиска(тема объект его составные части)
цель поиска информации
Классификационные индексы
Ретроспективность поиска
Наименование источников информации
Повышение надежности автогрейдера
Снижение металлоемкости
Дополнительное оборудование
Энергетическая эффективность
3 Поиск и отбор патентной информации
Для правильного поиска информации необходимо определить классификационные рубрики по каждому предмету поиска: для поиска научно – технической и конструкторно – экономической информации используют универсальную десятичную классификацию (УДК) для поиска описаний изобретений к авторским свидетельствам и патентам используют международную и национальные классификации изобретений (МКНМКИ).
В нашем случае будем использовать международную патентную классификацию (МПК).
4 Оформление результатов поиска
Результаты поиска оформляются в виде справки о поиске.
Шифр темы: КР ДМ - 2009067 00 00 00
Поиск проведен по следующим материалам:
По фонду какой организации проведен поиск
Источники информации
Научно технич документация
Патентная документация
5 Рассмотрение сущности найденных патентов
Цель изобретения: повышение надежности автогрейдера путем разгрузки шарнира поворота хребтовой балки относительно подмоторной рамы гидроцилиндрами поворота хребтовой балки относительно подмоторной рамы.
Цель изобретения в автогрейдере включающем колесный движитель содержащий балансиры со своей осью качания установленные на колесном движителе хребтовую балку со своей задней наклонной частью подмоторную раму соединенные друг с другом посредством шарнира и двух гидроцилиндров поворота хребтовой балки относительно подмоторной рамы шарнирно прикрепленную к переднему концу хребтовой балки тяговую раму прикрепленный к тяговой раме отвал гидроцилиндры выноса тяговой рамы и подъема и опускания отвала которые шарнирно присоединены к хребтовой балке и тяговой раме достигается тем что угол между плоскостью проходящей через продольные оси гидроцилиндров поворота хребтовой балки и опорной плоскостью автогрейдера лежит в пределах от 2 до 45о. Плоскость проходящая через продольные оси гидроцилиндров поворота хребтовой балки проходит через ось качания балансиров.
На рисунке 1 изображен автогрейдер с углом наклона плоскости
проходящей через продольные оси гидроцилиндров поворота хребтовой балки относительно подмоторной рамы к опорной плоскости автогрейдера лежащим в пределах от 2 до 45о; на рисунке 2 автогрейдер где плоскость проходящая через продольные оси гидроцилиндров поворота хребтовой балки параллельна задней части хребтовой балки; рисунке 3 автогрейдер где плоскость проходящая через продольные оси гидроцилиндров поворота хребтовой балки проходит через ось качания балансиров.
Автогрейдер включает колесный движитель 1 содержащий балансир 2 со своей осью 3 качания установленные на колесном движителе хребтовую балку 4 со своей задней наклонной частью 5 подмоторную раму 6. Хребтовая балка 4 соединена с подмоторной рамой 6 посредством шарнира 7 и двух гидроцилиндров 8 поворота хребтовой балки 4 относительно подмоторной рамы 6. Тяговая рама 9 шарнирно прикреплена к переднему концу хребтовой балки 4. Отвал 10 прикреплен к тяговой раме 9 посредством поворотного круга 11 механизма изменения угла резания отвала 10 в виде гидроцилиндров 12 направляющих 13 выдвижения отвала 10 относительно тяговой рамы 9. Гидроцилиндры 14 выноса тяговой рамы 9 и подъема и опускания отвала 10 шарнирно присоединены к тяговой раме 9 и хребтовой балке 4. К хребтовой балке 4 гидроцилиндры 14 могут быть присоединены посредством хомута 15 установленного с возможностью поворота относительно хребтовой балки 4. Угол α между плоскостью 16 проходящей через продольные оси гидроцилиндров 8 поворота хребтовой балки 4 и опорной плоскостью 17 автогрейдера лежит в пределах от 2 до 45о. С целью удобства чтения чертежа плоскость 17 перенесена параллельно вверх.
Указанный предел от 2 до 45о выбран вследствие того что усилие Р от колесного движителя действует от оси 3 качания балансиров 2 на подмоторную раму при действии рабочих динамических максимальных усилий на отвал под углом который лежит в пределах от 2 до 45о. На указанную ось качания действует горизонтальная составляющая усилия Р в которую входит динамическая составляющая от удара отвалом 10 в непреодолимое препятствие и статическая составляющая сцепление движителя 1 с грунтом. Вертикальная составляющая усилия Р возникает от силы тяжести автогрейдера которую можно считать постоянной. Горизонтальная составляющая может быть различной в зависимости от грунтоопорной поверхности скорости движения автогрейдера при ударе отвалом 10 в препятствие. Поэтому угол при действии максимальных нагрузок на отвале будет в указанных пределах. Для того чтобы разгрузить шарнир 7 и повысить надежность автогрейдера необходимо чтобы плоскость 16 была параллельна усилию P и следовательно чтобы угол α лежал в равных пределах с углом (рисунок 1). С целью улучшения технологичности конструкции автогрейдера и разгрузки задней наклонной части 5 плоскость 16 проходящая через продольные оси гидроцилиндров 8 параллельна задней наклонной части 5. Для того чтобы максимально уменьшить сосредоточенный момент от усилия Р необходимо направить действие усилия Р в одну плоскость с плоскостью 16 то есть чтобы плоскость 16 проходящая через продольные оси гидроцилиндров 8 проходила через ось 3.
Автогрейдер работает следующим образом.
Отвал 10 известным образом занимает необходимое положение с помощью поворотного круга 11 механизма изменения угла резания отвала 10 в виде гидроцилиндров 12 и механизма выдвижения отвала 10 относительно тяговой рамы 9 с направляющими 13. Движителем 1 содержащим балансиры 2 со своей осью 3 качания создается напорное усилие на отвале 10. При этом от оси 3 качания реакция Р действует на подмоторную раму 6 и имеет угол в пределах от 2 до 45о с опорной плоскостью 17 автогрейдера. Для того чтобы разгрузить шарнир 7 необходимо нагрузить гидроцилиндры 8 от усилия-реакции Р. Для этого угол α должен лежать в пределах 2-45о. При этом гидроцилиндры 8 снимают часть нагрузки с шарнира 7.
Цель изобретения снижение металлоемкости автогрейдера путем достижения оптимального профиля хребтовой балки.
Для этого в автогрейдере включающем колесный движитель и установленные на движителе подмоторную раму и хребтовую балку состоящую из задней наклонной промежуточной и передней частей к переднему концу которой шарнирно присоединена тяговая рама с поворотным кругом к которому присоединен отвал посредством механизма изменения угла резания и механизма выдвижения отвала гидроцилиндры подъема и опускания отвала выноса тяговой рамы шарнирно соединенные с хребтовой балкой и тяговой рамой передняя часть хребтовой балки выполнена параллельно тяговой раме при ее установке в крайнее верхнее положение.
На чертеже показан автогрейдер вид сбоку.
Автогрейдер включает колесный движитель 1 и установленные на нем подмоторную раму 2 и хребтовую балку 3 состоящую из задней 4 промежуточной 5 и передней 6 частей. К переднему концу хребтовой балки 3 шарнирно присоединена тяговая рама 7 с поворотным кругом 8. К поворотному кругу 8 присоединен отвал 9 посредством механизма изменения угла резания отвала 9 в виде гидроцилиндров 10 и механизм 11 выдвижения отвала 9 обычной конструкции. Гидроцилиндры 12 подъема и опускания отвала 9 и гидроцилиндр 13 выноса тяговой рамы 7 шарнирно присоединены к хребтовой балке 3 и тяговой раме 7 посредством хомута 14 установленного с возможностью поворота вокруг хребтовой балки 3. Хребтовая балка 3 выполнена параллельно тяговой раме 7 при ее установке в крайнее верхнее положение т.е. участок АБ на хребтовой балке (передняя часть 6 хребтовой балки 3) параллелен участку СД (тяговой раме 7) при максимально поднятом отвале 9 что соответствует установке тяговой рамы 7 в крайнее верхнее положение. Это позволяет получить максимальную компактность автогрейдера и минимальную длину хребтовой балки 3 что ведет к минимальной металлоемкости автогрейдера.
Колесный движитель 1 придает движение всему автогрейдеру. Гидроцилиндрами 12 подъема и опускания отвала 9 гидроцилиндром 13 выноса тяговой рамы 7 поворотным кругом 8 гидроцилиндрами 10 изменения угла резания отвала 9 механизмом 11 выдвижения отвала 9 последнему придается необходимое рабочее положение. В крайнем верхнем положении тяговой рамы 7 при максимальном подъеме отвала 9 передняя часть 6 хребтовой балки 3 параллельна тяговой раме 7.
Цель достигается тем что в автогрейдере включающем шарнирно-сочлененную раму состоящую из моторной и хребтовой рам опирающихся соответственно на задний ходовой механизм выполненный в виде балансирных тележек и передний ходовой механизм выполненный в виде одноосного моста с поперечной балкой основной отвал связанный поворотным кругом с тяговой рамой имеющей шаровой шарнир закрепленный на хребтовой раме дополнительный рабочий орган навешенный впереди автогрейдера гидроцилиндры управления введены следующие конструктивные изменения поперечная балка переднего ходового механизма связана продольным цилиндрическим шарниром с поворотной рамой которая соединена вертикальным цилиндрическим шарниром с хребтовой рамой при этом на поворотной раме установлен портал с закрепленным на нем дополнительным рабочим органом например погрузчика бульдозера.
Новыми существенными признаками изобретения является то что
поперечная балка переднего ходового механизма связана продольным цилиндрическим шарниром с поворотной рамой которая соединена вертикальным цилиндрическим шарниром с хребтовой рамой при этом на поворотной раме установлен портал для крепления дополнительных рабочих органов например погрузчика бульдозера.
Указанные конструктивные признаки являются новыми так как не известны в технической и патентной литературе и позволяют получить новый положительный эффект заключающийся в более высокой компактности переднего дополнительного рабочего оборудования и более высокой его маневренности вследствие приобретения поворотной рамой дополнительной степени свободы относительно хребтовой рамы.
На рисунке 1 автогрейдер вид сбоку; на рисунке 2 автогрейдер в режиме работы при котором хребтовая рама расположена соосно с моторной рамой вид сверху; на рисунке 3 автогрейдер в режиме работы при котором хребтовая рама отклонена относительно продольной оси моторной рамы вид сверху.
Автогрейдер включает шарнирно-сочлененную раму состоящую из моторной рамы 1 и хребтовой рамы 2 соединенных вертикальным шарниром 3 на хребтовой раме 2 задний ходовой механизм состоящий из балансирных колесных тележек 4 и 5 связанных с моторной рамой 1 передний ходовой механизм состоящий из поперечной балки 6 соединенной продольным цилиндрическим шарниром 7 с поворотной рамой 8 которая вертикальным цилиндрическим шарниром 9 соединена с хребтовой рамой 2.
На поворотной раме 8 закреплен портал 10 на котором установлена дополнительное погрузочное оборудование включающее стрелу 11 ковш 12 гидроцилиндры 13 управления стрелой и гидроцилиндр 14 поворота ковша. Гидроцилиндры 15 и 16 рулевого управления автогрейдера шарнирно закреплены на хребтовой раме 2 и связаны с поворотной рамой 8. Основной отвал 17 поворотным кругом 18 связан с тяговой рамой 19 имеющей шаровой шарнир 20 закрепленный на хребтовой раме 2.
Гидроцилиндры 21 и 22 вертикального перемещения отвала 17 и гидроцилиндр 23 бокового выноса тяговой рамы 19 одним концом закреплены на хребтовой раме 2 другим связаны с тяговой рамой 19. Гидроцилиндры 24 и 25 поворота хребтовой рамы 2 одним концом соединены с моторной рамой 1 другим с хребтовой рамой 2.
Работу автогрейдера рассмотрим в трех основных режимах: 1 процесс копания грунта основным отвалом при соосном положении хребтовой рамы относительно продольной оси моторной рамы; 2 процесс копания грунта основным отвалом при отклонении хребтовой рамы на угол относительно продольной оси моторной рамы; 3 процесс копания грунта дополнительным передним рабочим органом.
Работа автогрейдера в режиме копания грунта основным отвалом не отличается от работы автогрейдеров известных конструкций. Процесс копания грунта при соосном положении хребтовой рамы 2 относительно продольной оси моторной рамы (рисунок 2) происходит после установки отвала 17 гидроцилиндрами 21-23 в положение копания. Копание грунта происходит основным отвалом 17 при поступательном движении автогрейдера. При этом направление заданного курса движения обеспечивается рулевым механизмом путем поворота колес переднего ходового механизма гидроцилиндрами 15 и 16.
Второй режим копания грунта осуществляется после установки хребтовой рамы 2 под углом к продольной оси моторной рамы при помощи гидроцилиндров 24 и 25 и установки колес переднего ходового механизма под углом α к продольной оси хребтовой рамы гидроцилиндрами 15 и 16 (рисунок 3).
Для обеспечения установившегося поступательного движения автогрейдера с отклоненной на угол хребтовой рамой оператор устанавливает угол α при помощи гидроцилиндров 15 и 16 рулевого управления. Управление основным отвалом 17 при копании грунта не отличается от управления отвалом в известных автогрейдерах.
Третий режим работы автогрейдера копание грунта дополнительным передним рабочим органом происходит при поднятом в транспортное положение основном отвале 17. Ковш 12 навесного фронтального погрузочного оборудования приводится в исходное положение черпания материала путем опускания стрелы 11 гидроцилиндрами 13 в нижнее положение и поворота ковша 12 зубьями вперед гидроцилиндром 14. Процесс наполнения ковша происходит при поступательном движении автогрейдера на штабель и одновременном повороте ковша 12 или подъеме стрелы 11 гидроцилиндрами 13 и 14. После транспортирования материала к месту доставки или к самосвалу стрела 11 гидроцилиндрами 13 поднимается в верхнее положение и после подъезда к транспорту ковш 12 разгружается путем включения гидроцилиндра 14. При подъезде к самосвалу ковш 12 может быть точно установлен параллельно боковым стенкам кузова автомобиля благодаря повороту передней рамы 8 гидроцилиндрами 15 и 16.
Таким образом благодаря поворачиваемости передней рамы облегчается установка ковша над разгружаемым транспортом.
Предлагаемая конструкция в отличие от прототипа расширяет функциональные возможности автогрейдера за счет более компактного расположения переднего дополнительного рабочего органа в колесе передних колес ходового механизма. При этом повышается маневренность механизма при работе передним дополнительным рабочим органом улучшается планирующая способность и боковая устойчивость при работе основным отвалом за счет оптимизации нагрузки на передний мост.
В результате указанных свойств производительность автогрейдера возрастает на 35-40%
Цель изобретения "Автогрейдер с переменной массой" повышение энергетической эффективности расширение технологических возможностей автогрейдера повышение надежности.
Сущность изобретения заключается в том что: самоходное шасси с грейдерным отвалом (базовая машина) выполнено с минимальной массой и ее распределением обеспечивающими реализацию операций перемещения грунта на повышенных рабочих скоростях допускаемых технологией;
рыхлитель и бульдозер выполнены массой и ее распределением обеспечивающими реализацию операций резания грунта всем используемым на автогрейдере для этих целей рабочим и дополнительным оборудованием;
рыхлитель и бульдозер выполнены с массой сосредоточенной на минимальном конструктивно возможном расстоянии от режущих частей оборудования.
Самоходное шасси с грейдерным отвалом выполненное с минимальной массой определяемой необходимой силой тяги по сцеплению для перемещения грунта с возможным ограничением уровнем развития техники имеет минимальное сопротивление движению при выполнении операций планирования в сравнении с прототипом и аналогами.
Дозагрузка самоходного шасси с грейдерным отвалом съемным балластом и применение в качестве балласта съемного дополнительного оборудования установленного на оконечностях шасси обеспечивает реализацию по сцеплению максимальной тяги двигателя при наиболее экономичном режиме номинальной мощности при резании рыхлении перемещении грунта рабочим и дополнительным оборудованием. Относительно прототипа автогрейдер обладает большей производительностью и экономичностью.
Применение в качестве балласта съемного дополнительного
оборудования упрощает конструкцию расширяя функции дополнительного оборудования. Размещение дополнительной массы на оконечностях автогрейдера значительно увеличивает момент инерции масс относительно вертикальной оси что уменьшает влияние переменных составляющих внешних сил на устойчивость хода. Низкое положение дополнительного оборудования большой массы снижает высоту центра масс всего автогрейдера повышая его устойчивость при работе на косогоре расширяет технологические возможности его использования.
Выполнение рыхлителя и бульдозера с массой сосредоточенной возможно близко к режущим частям оборудования сглаживает действие переменных составляющих сил сопротивления грунта при работе рыхлителем и бульдозером на несущие конструкции трансмиссию и двигатель самоходного шасси что повышает долговечность автогрейдера и экономичность работы двигателя.
В целом предлагаемый "Автогрейдер с переменной массой" обладает существенными новыми свойствами. Он обладает более высокой производительностью энергетической эффективностью (экономичностью) долговечностью расширенными технологическими возможностями в сравнении с известными аналогами и прототипом.
На рисунке 1 показан автогрейдер с рыхлителем и бульдозером; на рисунке 2 показан рыхлитель; на рисунке 3 показан бульдозер; на рисунке 4 показан автогрейдер без дополнительного оборудования.
Автогрейдер (рисунок 1) состоит из самоходного шасси 1 с грейдерным отвалом 2 и шарнирно соединенных с шасси 1 рыхлителя 3 и бульдозера 4. Рыхлитель 3 (рисунок 1) состоит из двух продольных балок 5 (рисунок 2) соединенных поперечной балкой 6 к которой через проушину 7 осью 8 присоединен шток гидроцилиндра 9. На концы балок 5 одет поперечный брус 10 с зубьями 11. Брус 10 на продольной балке 5 фиксируется буртом 12 и пальцем 13. Брус 10 выполнен массивным и выполняет функции балласта.
Бульдозер 4 (рисунок 1) состоит из бульдозерного отвала 14 (рисунок 3) соединенного через оси 15 стержнем 16 параллелограмной подвески и гидроцилиндром 17 с шасси 1. Бульдозерный отвал 14 выполнен массивным с максимальным приближением центра масс к режущей кромке 18 и выполняет функции балласта.
Гидроцилиндры 9 (рисунок 2) и 17 (рисунок 3) оборудованы гидрозамками.
Для выполнения операций планирования с автогрейдера снимается бульдозер 4 (рисунок 1) и поперечный брус 10 (рисунок 2) рыхлителя. Для снятия бульдозера вынимаются оси 15 (рисунок 3) соединяющие стержни 16 с шасси 1 и гидроцилиндр 17 с бульдозерным отвалом 14. Для снятия поперечного бруса 10 (рисунок 2) извлекаются пальцы 13 из балок 5. Автогрейдер для выполнения операций планирования показан на рисунке 4.
Безопасность жизнедеятельности
1 Анализ вредных факторов возникающих при работе автогрейдера
В процессе труда человек-оператор взаимодействует с производственной обстановкой и окружающей средой. В этом случае организм человека подвергается неблагоприятному воздействию ряда факторов :
- отклонение от норм микроклимата;
- производственный шум;
- систематическое воздействие вибрации;
- производственная пыль;
- воздействие токсичных веществ и газов;
- постоянное напряжение зрения при недостаточном освещении;
- ограниченный обзор;
- устойчивость машины.
Влияние всех этих факторов может вызвать профессиональное заболевание либо отклонение здоровья человека-оператора.
Для обеспечения безопасности человека для нормальной его работоспособности и в конечном итоге повышения производительности планировочных работ необходимо решить задачу по устранению перечисленных вредных факторов или уменьшению их воздействия до предельно допустимых норм установленных ГОСТами ССБТ и СН и П.
Производственный шум имеющий высокий уровень вызывает притупление слуха отрицательно сказывается на нервной системе человека при этом повышается кровеносное давление происходит ослабление внимания. Основным источником шума при работе автогрейдера является двигатель внутреннего сгорания. Другие источники шума – трансмиссия ходовое оборудование и прочие элементы машины их уровень шума сравнительно ниже уровня шума двигателя. ГОСТ 12.1.003-83 устанавливает допускаемые значения шумовых характеристик машин и оборудования. По ГОСТу уровень шума должен находиться в пределах 89 95 дБ. Для предотвращения или уменьшения уровня шума от двигателя необходимо проводить своевременный качественный ремонт и техническое обслуживание всех систем и механизмов двигателя. Уменьшает уровень шума звукоизоляция шумных узлов машины в частности на автогрейдере для понижения уровня шума от работы двигателя установлен звукоизолирующий капот. Кабина человека-оператора одновременно служит тепло - и звукоизоляционным устройством рабочего места. Звукоизолирующая кабина позволяет снизить шум от 20 до 30 дБ в средних и высокочастотных диапазонах.
Длительное воздействие вредных факторов микроклимата может вызвать тепловой (солнечный) удар (в летнее время года); при высокой влажности происходит нарушение терморегуляции тела человека. Оптимальные и допустимые нормы температуры относительной влажности и скорости движения воздуха в рабочей зоне машины установлены ГОСТ 12.2.023-76 7 ГОСТ 12.2.019-76 6 . В них сказано что в кабине принудительная вентиляция должна обеспечить подачу свежего воздуха в количестве не менее 30 м3ч на одного человека. Температура воздуха в кабине должна быть на 2-3 С выше температуры наружного воздуха но не ниже +14 С и не выше +28 С при относительной влажности 40-60 %. Естественная вентиляция обеспечивается люками открывающимися окнами которыми снабжена кабина автогрейдера ДЗ-143-2. Для очистки обзорных стекол кабины от атмосферных осадков предусмотрены стеклоочистители.
Оператор автогрейдера подвергается общей вибрации которая вызывает сотрясение всего организма человека а также локальной вибрации. Систематическое воздействие вибрации может вызвать виброболезнь с необратимыми патологическими изменениями. Причинами возникновения вибрации на автогрейдере являются неуравновешенность вращающихся масс и возвратно-поступательно движущихся. Дисбаланс приводит к возникновению центробежных сил которые вызывают вибрацию.
Действующие гигиенические оценки вибрации изложены в ГОСТ 12.1.012-90. Методы и средства вибрационной защиты изложены в ГОСТ 12.4.064-78. На автогрейдере ДЗ-143 установлена виброизоляция сидения человека-оператора по ГОСТ 12.2.023-76 которая представляет собой гидроамортизатор. Для снижения колебаний (вибрации) передаваемых от двигателя к раме или остову на автогрейдере предусмотрены амортизаторы резинометаллические устанавливаемые между двигателем и рамой.
Воздействие пыли и газов может привести к поражению органов дыхания человека-оператора. Особую опасность для здоровья человека представляют соединения окиси углерода окиси азота и альдегиды содержащиеся в отработавших газах двигателя. Источниками выделения токсичных компонентов являются системы выпуска питания смазки и вентиляции картерной полости двигателя. Для обеспечения защиты оператора от пыли газов а также атмосферных осадков люки и окна кабины автогрейдера герметизированы. Для предотвращения попадания пыли и газов через неплотности пола в области рычагов управления ручек руля педалей предусмотрены специальные кожухи прикрывающие эти неплотности. Интенсивный выход токсичных веществ при работе двигателя может являться результатом неправильной регулировки двигателя поэтому необходимо своевременно и тщательно проводить все плановые мероприятия по ремонту и техническому обслуживанию двигателя и автогрейдера в целом.
При неудовлетворительном освещении зрительная способность глаз снижается. СН и П II-4-79 предусматривает нормированные значения освещенности на рабочих местах при естественном и искусственном освещении. Для обеспечения нормальных условий эксплуатации механизмов и приборов внутри кабины автогрейдера освещенность должна быть не менее 50 лк. Величина освещенности приборов и указателей должна быть в пределах 03 11 лк. Днем естественное освещение в кабине автогрейдера реализуется через оконные проемы расположенные на боковых передней и задней стенках кабины. Для работы в темное время суток на автогрейдере предусмотрены фонари которые обеспечивают освещение рабочих органов и планируемой поверхности.
Для обеспечения хорошей обзорности по ГОСТ 12.2.023-76 7 кабина оборудована с четырех сторон окнами а также с боков кабины установлены зеркала заднего вида.
Опрокидывающий момент в результате которого автогрейдер может потерять устойчивость складывается из действия различных сил: реакции грунта на режущие грани рабочих органов воздействия сил инерций сил возникающих от уклона или подъема пути и других. Автогрейдер ДЗ-143 снабжен механизмом наклона передних колес тем самым увеличивается устойчивость автогрейдера обеспечиваются лучшие условия нагружения подшипников колес облегчается работа рулевого управления что непосредственно уменьшает утомляемость оператора автогрейдера.
C целью обеспечения пожарной безопасности кабина автогрейдера оснащается кронштейном для крепления огнетушителя а также крепления специального молотка для разбивания окон в случае когда использовать огнетушитель не удаётся и затруднено открывание дверей кабины.
В данном дипломном проекте рассматривается модернизированная конструкция автогрейдера ДЗ-143 добавляются дополнительные выдвижные секции отвала. При их полном выдвижении длина отвала составляет 4570 мм. Для обозначения кромок выдвинутых секций последние снабжаются габаритными указателями в виде красно-белых полос. Оператор при выдвижении секций подает звуковой сигнал для оповещения о возможной опасности.
2 Общие требования безопасности
2.1. Мужчины не моложе 18 лет прошедшие соответствующую подготовку имеющие профессиональные навыки удостоверение на право управления автогрейдером перед допуском к самостоятельной работе должны пройти:
обязательные предварительные (при поступлении на работу) и периодические (в течении трудовой деятельности) медицинские осмотры (обследования) для признания годными к выполнению работ в порядке установленном Минздравом России;
обучение безопасным методам и приемам выполнения работ инструктаж по охране труда стажировку на рабочем месте и проверку знаний требований охраны труда.
2.2. Машинисты обязаны соблюдать требования безопасности труда для обеспечения защиты от воздействия опасных и вредных производственных факторов связанных с характером работы:
повышенное содержание в воздухе рабочей зоны пыли и вредных веществ;
движущиеся машины механизмы и их части;
обрушающиеся горные породы.
2.3. Для защиты от общих производственных загрязнений и механических воздействий машинисты обязаны использовать предоставляемыми работодателями бесплатно комбинезон хлопчатобумажный сапоги резиновые рукавицы комбинированные костюмы на утепляющей прокладке и валенки для зимнего периода.
При нахождении на территории стройплощадки машинисты должны носить защитные каски.
2.4. Находясь на территории строительной (производственной) площадки в производственных и бытовых помещениях участках работ и рабочих местах машинисты обязаны выполнять правила внутреннего распорядка принятые в данной организации.
Допуск посторонних лиц а также работников в нетрезвом состоянии на указанные места запрещается.
2.5. В процессе повседневной деятельности машинисты должны:
применять в процессе работы машины по назначению в соответствии с инструкциями заводов-изготовителей;
поддерживать машину в технически исправном состоянии. Не допуская работу с неисправностями при которых эксплуатации запрещена;
быть внимательным во время работы и не допускать нарушений требований безопасности труда.
2.6. Машинисты обязаны немедленно извещать своего непосредственного или вышестоящего руководителя о любой ситуации угрожающей жизни и здоровью людей о каждом несчастном случае происшедшем на производстве или об ухудшении состояния своего здоровья в том числе о появлении острого профессионального заболевания (отравления)
Требования безопасности перед началом работы
2.7. Перед началом работы машинист обязан:
а) предъявить руководителю работ удостоверение о проверке знаний безопасных методов работ получить задание заполнить вахтенный журнал и пройти инструктаж на рабочем месте по специфике выполняемых работ;
б) надеть спецодежду и спецобувь установленного образца.
2.8. После получения задания машинист обязан:
а) осмотреть с руководителем работ место расположения подъемных сооружений и коммуникаций которые должны быть обозначены флажками или вешками проверить наличие ограждений и обозначений опасных зон знаками безопасности а также убедиться в отсутствии помех от других машин и механизмов;
б) уточнить последовательность выполнения работы и меры по обеспечению безопасности;
в) произвести ежесменное техническое обслуживание согласно инструкции по эксплуатации автогрейдера;
г) осмотреть двигатель и узлы машины проверить их исправность и состояние смазки трущихся частей. Проверить наличие и достаточность горючего в топливном баке воды - в системе охлаждения масла - в картере двигателя. Проверить исправность гидросистемы систем сигнализации и электроосвещения наличие и исправность инструментов и средств пожаротушения;
д) предупредить о запуске двигателя работников обслуживающих машину или находящихся в зоне ее работы и убедиться что рычаг переключения передач находится в нейтральном положении;
е) произвести запуск двигателя проверить на холостом ходу работу всех механизмов и на малом ходу - работу тормозов.
2.9. Машинист не должен приступать к работе при следующих нарушениях требований безопасности:
а) неисправностях или дефектах указанных в инструкции завода - изготовителя автогрейдера при которых не допускается его эксплуатация;
б) обнаружении подземных коммуникаций не указанных руководителем работ;
в) уклоне местности превышающем указанный в паспорте завода-изготовителя;
г) наличие деревьев пней или крупных камней.
Обнаруженные нарушения требований безопасности следует устранить собственными силами а при невозможности сделать это машинист обязан сообщить о них руководителю работ и лицу.
Требования безопасности во время работы
2.10. Перед началом маневрирования во время работы автогрейдера
машинист обязан убедиться в отсутствии людей в зоне действия автогрейдера и подать звуковой сигнал. На крутых поворотах скорость перемещения автогрейдера должна быть минимальной
2.11. Во время подъема плужной балки автогрейдера машинист обязан контролировать процесс подъема и выключить механизм подъема при достижении плужной балкой предельного положения.
2.12. При рыхлении грунта взрывным способом на время выполнения взрывных работ машинист обязан отогнать автогрейдер от места взрывных работ на расстояние указанное руководителем взрывных работ но не менее чем на 50 м.
2.13. При выполнении работ автогрейдером с гидравлической системой управления машинист обязан следить за исправностью предохранительного клапана и соединениями гибких шлангов. Шланги имеющие вздутие или течь масла в соединениях следует заменить. Ремонт шлангов высокого давления не допускается. При эксплуатации шлангов не допускаются их скручивание зажатие перегибы.
2.14. Машинист обязан контролировать исправность манометров в системе гидропривода. Манометры должны быть исправны и опломбированы.
2.15. Во время работы машинисту запрещается:
а) открывать кран слива воды из радиатора при работающем двигателе а также сразу после его выключения;
б) заливать жидкость в радиатор если двигатель перегрет;
в) заправлять автогрейдер горючим при работающем двигателе;
г) оставлять автогрейдер с работающим двигателем а также передавать управление автогрейдером лицу не имеющему удостоверения на право
д) перевозить на площадках или в кабине автогрейдера посторонних лиц а также легковоспламеняющиеся материалы.
2.16. Устранять неисправности осматривать отдельные узлы автогрейдера а также осуществлять их смазку или регулирование следует только при остановленном двигателе включенном тормозе и установленном в нейтральное положение рычаге переключения передач.
2.17. При перегреве двигателя машинист обязан с осторожностью открывать крышку заливной горловины радиатора не наклоняясь над ней находясь с подветренной стороны и следя за тем чтобы горячий пар не обжег лицо и руки.
2.18. При перемещении автогрейдера своим ходом по дорогам общего пользования машинист обязан выполнять правила дорожного движения.
2.19. При движении автогрейдера на уклоне во избежание сползания или опрокидывания не следует допускать резких поворотов автогрейдера. При движении автогрейдера под уклон не следует выключать первую передачу а при движении на подъем - переключать передачи.
2.20. При планировке или отсыпке грунта расстояние от крайнего колеса до бровки насыпи должно быть не менее 1 м.
2.21. Техническое обслуживание автогрейдера следует осуществлять только после остановки двигателя и снятия давления в гидравлической и пневматической системах кроме тех случаев которые предусмотрены инструкцией завода-изготовителя.
Сборочные единицы автогрейдера которые могут перемещаться под действием собственной массы при техническом обслуживании следует заблокировать или опустить на опору в целях исключения произвольного их перемещения.
2.22. В процессе эксплуатации автогрейдера машинист обязан:
а) содержать механизмы и оборудование автогрейдера в чистоте и исправном состоянии;
б) своевременно смазывать трущиеся детали автогрейдера в соответствии с указаниями инструкции завода-изготовителя;
в) хранить смазочные и обтирочные материалы в закрытой металлической таре; удалять с автогрейдера использованный обтирочный материал;
г) следить чтобы на автогрейдере не было каких-либо незакрепленных предметов;
д) знать сроки и результаты проведения слесарями и электромонтерами профилактических осмотров автогрейдера и его отдельных механизмов и узлов по записи в журнале периодических осмотров.
Требования безопасности в аварийных ситуациях
2.23. При возникновении неисправностей (поломок) отдельных узлов автогрейдера машинист обязан остановить работу автогрейдера до устранения этих неисправностей. Если устранить неисправности собственными силами не представляется возможным то машинист обязан поставить об этом в известность руководителя работ и ответственного за техническое состояние автогрейдера.
2.24. При сползании автогрейдера под откос или потере устойчивости вследствие попадания колеса в выемку в грунте машинисту следует опустить нож до упора в грунт покинуть машину и вытащить ее на ровное место на буксире.
2.25. При возгорании горючесмазочных или других материалов машинист обязан немедленно затушить очаги пожара огнетушителем или другими подручными средствами: песком землей или брезентом.
Запрещается заливать водой горящее топливо. При невозможности затушить очаги пожара собственными силами машинист обязан вызвать пожарную охрану и поставить в известность руководителя работ
Требования безопасности по окончании работы
2.26. По окончании работы машинист обязан:
а) поставить автогрейдер на место отведенное для его стоянки;
б) выключить двигатель и перекрыть подачу топлива. В зимнее время слить воду из системы охлаждения двигателя;
в) затормозить автогрейдер и поставить рычаги управления в нейтральное положение;
г) снять спецодежду и убрать ее для хранения в отведенное для этого место;
д) сообщить руководителю работ и лицу осуществляющему надзор за техническим состоянием автогрейдера о всех неполадках возникших во время работы и сделать запись в вахтенном журнале.
Бируля А. К. Эксплуатация автомобильных дорогА. К. Бируля. – М.: НТИ Автотрансп. Лит 1956. 340 с.
Борадочёв И. П. Справочник конструктора дорожных машин И. П. Борадочёв- Изд. 2-е перераб. и доп. М.: Машиностроение 1973. – 503 с.
Борадочёв И. П. Дорожные машины И. П. Борадочёв В. А Васильев.- М.: Машгиз 1953. – 506 с.: ил.
Горелышев Н. В. Технология и организация строительства автомобильных дорог Н. В. Горелышев. - М. 1992. – 551с.
Дорожные машины. Ч. 1. Машины для земляных работ Т. В. Алексеева К. А. Артемьев А. А. Бромберг и др.- Изд. 3-е перераб. и доп. –М.: Машиностроение 1972. –504 с.
Строительные нормы и правила. Автомобильные дороги: СниП 3.06.03-85: Срок введ. в действие 1.01.86 Госстрой СССР . – М.: ЦНТП Госстроя СССР 1986.- 112 с
Содержание 1@.doc
магистерской диссертации8
1 Обоснование темы диссертации8
2 Проведение патентного поиска9
3 Анализ вариантов технических решений13
Теоретический раздел
(Особенности кинематики механизма изменения угла резания
отвала автогрейдера) 21
1 Мощностной расчет25
2 Расчет производительности27
4 Расчет механизма стабилизации36
5 Определение сил действующих на автогрейдер38
Расчеты на прочность42
2 Расчет устройства стабилизации в САПР APM FEM 44
2.1 Общие сведения о САПР APM FEM .44
2.2 Выбор рассчитываемого узла ..45
2.3 Расчет механизма стабилизации .46
2.4 Задание закреплений и приложение нагрузки 49
2.5 Генерация КЭ – сетки .. 49
2.6 Выполнение расчета .51
Технология изготовления детали ..63
1 Анализ чертежей 63
2 Определение размера партии деталей и типа
3 Выбор способа получения заготовки64
4 Разработка технологического маршрута обработки
детали в САПР Вертикаль 2013 ..64
5 Расчет припусков65
6 Расчет режимов резания68
7 Расчет нормы времени 77
Расчет технико-экономических показателей диссертации82
1 Оценка технической целесообразности конструкции
2 Определение капитальных вложений по базовой и новой
3 Определение годовой эксплуатационной
производительности 84
4 Расчет годовых текущих затрат86
0.Введение.doc
Так как парк машин для земляных работ очень велик и разнообразен как по функциям так и по устройству конструкции машин в данной магистерской диссертации рассмотрим одну из машин данного класса а именно автогрейдер марки ДЗ-143 с модернизированным рабочим оборудованием. Так как автогрейдеры оснащают различным сменным дополнительным оборудованием (до 20 видов) область применения их очень широка.
Рассматривается изобретение для рабочего оборудования автогрейдера повышающее эффективность путём стабилизации глубины резания при изменении угла резания отвала в процессе работы. Автогрейдер является одной из распространённых и востребованных машин что доказывает актуальность данной магистерской диссертации.
т-э обоснование д.п.исправл.doc
1 Анализ существующих отечественных и зарубежных конструкций
Одноковшовые гидравлические экскаваторы предназначены для разработки погрузки и укладки грунта. Они относятся к машинам циклического действия которые производят все операции последовательно в определенном порядке многократно повторяя цикл работ.
Особенность одноковшовых экскаваторов заключается в стационарности рабочего процесса: разработка грунта ведется им со стоянки до тех пор пока из зоны действия ковша будет удален весь грунт. Для продолжения разработки грунта экскаватор перемещается на новую стоянку. Главным отличительным признаком одноковшовых экскаваторов является рабочее оборудование. Основные виды его для гидравлического экскаватора-обратная лопата прямая лопата грейфер и погрузчик.
Рабочее оборудование может быть как шарнирно-сочлененным так и телескопическим. Большинство гидравлических экскаваторов имеет шарнирно-сочлененное рабочее оборудование позволяющее при незначительном переоборудовании или замене рабочего органа производить разнообразные экскавационные и погрузочные работы. Однако выполнение таким оборудованием планировочных работ при прямолинейном движении рабочего органа затруднительно.
Стремление к эффективному использованию гидравлических экскаваторов со сменными рабочими органами на экскавационных погрузочных планировочных и других работах привело к созданию рабочего оборудования позволяющего изменить рабочие параметры экскаватора -глубину радиус копания и высоты выгрузки. Изменение геометрических параметров такого рабочего оборудования основные элементы которого (стрела и рукоять) выполняется составными или сменными может осуществляться непрерывно в процессе выполнения рабочих операций либо ступенчато.
Для выполнения работ в близи фундаментов зданий и других сооружений некоторые экскаваторы имеют устройства позволяющее поворачивать рукоять относительно плоскости стрелы.
Так у французского экскаватора «Oleomat» H11P рукоять вместе с гидроцилиндром может быть повернута в плане на 150 в лево или вправо. Ось траншеи при этом смещается на 135 м от продольной оси машины а максимальная глубина копания составляет 37 м. У экскаватора ТС-45 фирмы «Poclain» вставка стрелы вместе с рукоятью и гидроцилиндром может быть повернута на угол 270 и закреплена в новом положении специальной пятой. Ось траншеи при этом смещается на 15 м.
Недостатком первой и второй конструкции является то что при опускании стрелы вертикальная плоскость поворота рукояти становится непараллельной продольной оси отрываемой траншеи. В следствии этого нарушается прямолинейность в стенках траншеи. Лишены этого недостатка экскаваторы BEN-145BS фирмы «Benati». Это достигнуто благодаря повороту головной части стрелы относительно двух вертикальных шарниров при этом плоскость поворота рукояти с ковшом остается параллельной плоскости подъема-опускания стрелы.
Еще дальше по пути универсализации рабочего оборудования гидравлического одноковшового экскаватора пошла японская фирма «Комацу» выпустившая экскаватор PF-55. Эта машина относится к новому типу экскаваторов повышенной универсальности для работы в стесненных условиях строительства. Отличительной особенностью экскаватора модели PF-55 является кинематика приближенная к действию человеческой руки. Данный гидравлический экскаватор имеет двух секционную стрелу и механизм вращения рукояти повышающий его технологические возможности при сохранении функции обычного гидравлического экскаватора.
Применение двухсекционной стрелы расширило зону действия рабочего оборудования.
Рукоять с ковшом имеют возможность неограниченного вращения вокруг своей оси в обоих направлениях а применение микропроцессора обеспечило возможность автоматического применения вращения рукояти что повышает удобство управления экскаватором.
Двухсекционная стрела состоит из двух шарнирно-сочлененных секций связанных посредством гидроцилиндра. С помощью педального управления можно произвольно менять угол складывания секций.
Рукоять состоит из двух частей соединенных между собой с помощью поворотного круга. На коренной части рукояти установлен гидромотор вращения рукояти со встроенным редуктором приводящим во вращение шестерню с внутренним зацеплением закрепленной на второй внешней части рукояти. В средней части имеется поворотное соединение с помощью которого рабочая жидкость подается в гидроцилиндр ковша. Такая конструкция рукояти позволяет: копать в боковом направление осуществлять переворот ковша с обратной лопаты на прямую и наоборот смещать ось копания планировать откосы.
В нашей стране так же ведутся разработки систем ускоренной замены рабочих органов. Так например Кабардино-Балкарский государственный университет разработал устройство для переоборудования ковша без ручного вмешательства при минимальных затратах времени с надежной его фиксацией в рабочем оборудований одноковшового экскаватора.
2 Патентное исследование
Проведенные патентные исследования показали что многие конструкторы как у нас в стране так и зарубежом часто обращают свое внимание на создание универсального рабочего оборудования.
Так Б.Д. Оренбойм В.И.Лиферов и другие предлагают с целью быстрого переоборудования ковша с прямой лопатой на обратную и наоборот включить между рукоятью и ковшом шарнир вращения. В нужном положении ковш фиксируется болтами. При необходимости можно отвернув болты повернуть ковш на 180 0 или заменить его на ковш другой емкости.
Регламент поиска патентной информации.
Перечень вопросов или элементов по которым необходим поиск информации
Рабочее оборудование
Описание изобретений в СССР.
Бюллетень «Открытие изобретения промышлен-
ные образцы товарные знаки».
ния в СССР и зарубежном.
Руководитель Бузин Ю.М.
Патентовед Бузин Ю.М.
Перечень патентных документов отобранных при поиске.
Номер авторского свиде-тельст-ва или патента
Действи-тельные авторы
Название изоб-ретения
Б.Д Оренбойм В.И Лиферов И.А Фоменко
Рабочее оборудо-вание одноковшового экскава-тора
В.И. Баловнев Л.А. Хмара Л.И. Деревянчук А.И. Голубченко
Рабочее оборудо-вание одноковшового гидравли-ческого экскаватора
В.И. Баловнев Г.Д. Моисеев А.Г. Савельев
Устройство для выполне-ния земляных работ
В.П. Павлов Г.Г. Назаров В.В. Минин
Рабочее оборудо-вание одноков-шового экскава-тора
Продолжение таблицы 1.2.
Б.Н. Лоханов А.С. Ненашев Б.Н. Рыбаков А.П. Глазков В.А. Ермолаев
Рабочее оборудо-вание одноковшового гидравл. Экскава-тора
А.И. Голубченко Б.Р. Заславский
Днепропетровский инжинерно-строительный и Московский автомо-бильно-дорожный институ-ты
Рабочее оборудо-вание одноковшового гидравли-ческого экскава-тора
Фирма «Катерпил-лер»
Установочное устройство для ковша экскава-тора
Рабочее оборудо-вание одноков-шового гидравли-ческого экскава-тора
Заявитель патенто- обладатель
Устройство для автосцепки рабочих органов с рабочим оборудованием
Быстросьемное соединение рабочих органов универсальной машины
Тюменск-ий государственный нефтегазовый универси-
Одноковшового экскаватора
3 Пути модернизации рабочего оборудования
Основной тенденцией развития универсальных строительных одноковшовых экскаваторах в настоящее время является производство машин с гидравлическим приводом выпуск которых составляет 90% от общего объема .
Одним из направлений повышения эффективности работы гидравлических экскаваторов является совершенствование его рабочего оборудования.
Продолжительность операций копания составляет до 30% продолжительности рабочего цикла экскаватора . И эта операция является наиболее энергоемкой.
Анализ отечественных и зарубежных конструкций а также результаты патентных исследований позволяют сформулировать пути совершенствования рабочего оборудования одноковшовых гидравлических экскаваторов .
Расширение номенклатуры сменных видов рабочего оборудования и сменных рабочих органов а также применение сдвоенного рабочего оборудования (ковш-рыхлитель ковш – гидромолот и другие ).
Совершенствование кинематической схемы рабочего оборудования позволяет адаптировать его к изменяющимся условиям работы (параметров копания – Нк и Rк и выгрузки Нв и Rв ). Изменяя линейные размеры рабочего оборудования тем самым изменяем рабочие зоны экскаватора .
Улучшение конструкции отдельных элементов рабочего оборудования:
в) ковш – раскрывающегося с откидным днищем оптимальной формы.
г) шарниров рабочего оборудования за счет более качественных уплотнителей и механизированной централизованной смазки.
Как видно из приведенных выше примеров в развитии землеройной техники ведущими тенденциями является универсализация машин то - есть расширение функциональных возможностей при ограниченном числе видов и конструкций базовых машин .
Возможность выполнения ряда функций в пределах одной базовой машины достигается комплексом конструкторских приемов направленных на оптимальное сочетание рабочего органа с конструкцией и кинематикой рабочего оборудования.
В ряде случаев задача повышения универсализации решаются увеличением степени подвижности рабочего оборудования что наряду с расширением сменных рабочих органов придает машине свойства строительного манипулятора.
Строительные одноковшовые экскаваторы являются полноповоротными универсальными машинами имеющими комплект сменного рабочего оборудования. Недостаток этого комплекта состоит в том что оборудование входящее в него является сменным т. е. адаптация его к изменяющимся технологическим условиям работы экскаватора происходит дискретно с затратой времени на его смену. Кроме того элементы сменного рабочего оборудования а именно стрелы и рукояти повторяются но с другими размерами и конфигурацией. Т.е. комплект является многочисленным по номенклатуре а следовательно в целом металлоемким и достаточно дорогим.
Цель проводимых исследований состояла в том чтобы универсальность машины обеспечивалась не комплектом сменного рабочего оборудования а единым адаптивным рабочим оборудованием с сменными рабочими органами (ковшами рыхлителем захватными устройствами ножницами и др.) имеющим возможность машинисту непосредственно с рабочего места непрерывно изменять главные рабочие параметры разработки грунта режимы этой разработки (прямое обратное и боковое) и заменять рабочие органы в соответствии с технологией производства работ. Такое рабочее оборудование существенно повышает эффективность работы единого энергетического модуля – базовой машины с учетом изменяющихся условий работы.
Используя возможности жесткой подвески рабочего оборудования одноковшового гидравлического экскаватора как основы для создания строительного манипулятора представляется существенно расширить его адаптивные возможности.
Эти машины работают в различных технологических условиях когда изменяются параметры копания и выгрузки грунта режимы копания – прямое обратное и боковое и возникает необходимость оперативно использовать различные рабочие органы. Часто эти условия чередуются особенно в специфических ситуациях что требует оперативной адаптации экскаватора.
Анализ отечественной и зарубежной научно – технической литературы по одноковшовым гидравлическим экскаваторам и промышленных образцов позволяет констатировать следующие три основных направления адаптации отдельных элементов рабочего оборудования.
При работе в условиях изменяющихся параметров копания и выгрузки грунта необходимо оперативно изменять линейные размеры рабочего оборудования а именно длину стрелы и рукояти. Это достигается за счет их телескопических конструкций и шарнирно – сочлененной стрелы с управляемым углом складывания ее секций.
Совмещение прямого обратного и бокового режимов разработки грунта достигается поворотом рукояти.
Для оперативного использования нужного вида сменного рабочего органа между ним и рукоятью устанавливается быстросъемное устройство.
Таким образом по нашему мнению специальное полностью адаптированное рабочее оборудование одноковшового гидравлического экскаватора для работы в специфических условиях эксплуатации (стесненные условия застройки чрезвычайные ситуации и др.) должно включать:
а) шарнирно – сочлененную стрелу с индивидуальным гидромеханизмом управления углом складывания ее секцией;
б) полноповоротную рукоять управляемую от индивидуального гидромотора с планетарным или волновым редуктором;
в) быстросъемное устройство с индивидуальным гидроуправлением для оперативной установки соответствующего рабочего органа.
Данное рабочее оборудование позволяет существенно расширить технологические возможности базовой машины тем самым повысить эффективность ее работы. Одновременно позволяет заменить комплект сменного рабочего оборудования комплектом сменных рабочих органов что уменьшает общую металлоемкость и стоимость рабочего оборудования. Таким образом одноковшовый экскаватор с данной структурой рабочего оборудования становится строительным манипулятором.
4 Предварительная оценка технико-экономической эффективности проводимой модернизации
В качестве базовой машины принят серийно выпускавшийся экскаватор 5-й размерной группы ЭО-5221 массой 422 т. с увеличенной опорной поверхностью гусеничного хода что повышает его устойчивость.
Основные виды съемного рабочего оборудования: обратная лопата с ковшом вместимостью q=125 м3 для разработки грунта I-IV категории ковшом q=16м3 для грунтов I-III категории и двумя сменными рукоятями длиной 25 и 35 м ; прямая лопата с ковшом q=16 м3 для разработки грунтов I-IV категории и q=2 м3 –для грунтов I-III категории; погрузочное оборудование с ковшом q=3 м3.Эти виды оборудований имеют свои стрелы и рукояти.
Так как для работы в специфических условиях необходимо иметь полный комплект сменного рабочего оборудованиято он должен включать в себя:3 стрелы для прямой обратной лопат и погрузочного оборудования; 4 рукояти для этих стрел (2 из них для обратной лопаты) и набор сменных рабочих органов.
В нашем проекте используется регулируемая по длине стрела вращающаяся рукоять быстросъемное устройство и комплект сменных рабочих органов. То есть мы перешли от комплекта сменного рабочего оборудования к комплекту сменных рабочих органов при одной стреле и рукояти.
В результате получена экономия металла (примерно 5000 кг) сокращено время на переход с одного режима разработки грунта на другой за счет адаптации рабочего оборудования тем самым повышен технический коэффициент использования машины по времени на 20-25% доведя его практически с 075 до 10 . То есть по существу одноковшовый экскаватор стал манипулятором для производства земляных работ.
Авт. свид. № 817157.doc
Авторское свидетельство № 817157
Изобретение относится к строительно-дорожным машинам а именно к землеройным машинам типа бульдозеров.
Известно рабочее оборудование землеройной машины включающее отвал в виде подпружиненной гибкой ленты опирающийся на решетчато-балочную конструкцию режущий нож и гидроцилиндры управления.
Наиболее близким по технической сущности и достигаемому результату к предлагаемому является рабочее оборудование землеройной машины включающее отвал с изменяемым профилем толкающие брусья гидроцилиндры управления и подкосы.
Недостатком устройства является малая эффективность работы в связи с отсутствием регулировки угла наклона отвала.
Цель изобретения - повышение эффективности разработки грунта путем обеспечения регулирования угла наклона отвала.
Указанная цель достигается тем что толкающие брусья снабжены серьгами с гидроцилиндрами поворота а гидроцилиндры изменения профиля отвала соединены с серьгами.
Причем отвал выполнен из упругого листа.
На фиг. 1 изображено рабочее оборудование вид сбоку; на фиг. 2 - то же вид в плане.
Рабочее оборудование землеройной машины включает отвал 1 выполненный из гибкого упругого листа например из полиуретана на тыльной стороне которого жестко закреплены горизонтальные секции 2 одна из которых шарнирно установлена на толкающих брусьях 3.
В нижней части отвала 1 закреплен режущий нож 4. На толкающих
брусьях шарнирно установлены серьги 5 с возможностью поворота посредством гидроцилиндров 6 шарнирно установленных на толкающих брусьях 3. Регулируемый поворот секций 2 обеспечивается гидроцилиндрами 7 установленными на серьгах 5.
Рабочее оборудование землеройной машины работает следующим образом.
Отвал 1 опускается на грунт. Режущий нож 4 устанавливается под необходимым углом резания. Стружка грунта отделяемая режущим ножом от массива поднимается по отвальной поверхности. При этом секции 2 поворачиваются гидроцилиндрами 7 изменяя
кривизну отвальной поверхности в поперечном сечении.
Одновременно с этим серьги 5 поворачиваются посредством гидроцилиндров 6. При повороте серег 5 изменяется и угол наклона отвала 1 поскольку последний связан с серьгами. 5 посредством гидроцилиндров 7.
Введение в конструкцию регулирования угла наклона отвала позволяет уменьшить сопротивление продвижению
грунта по отвалу и уменьшить энергоемкость копания грунта что приводит к повышению эффективности разработки
1_Tekhniko-ekonomicheskoe_obosnovanie_temy_proekt.doc
с проведением патентного поиска
1 Обоснование темы проекта
Темой данной работы является проект рабочего оборудования гидравлического экскаватора V размерной группы. Следовательно необходимо сделать так чтобы эта машина стала ещё более универсальной а это может быть достигнуто путём модернизации отдельных узлов и деталей или выпуском совершенно новой техники. Последнее в сложившейся экономической ситуации в нашей стране сделать практически невозможно из-за недостатка финансовых средств в отрасли машиностроения. Поэтому пути внедрения на уже существующую машину новых узлов и деталей с последующим проведением экономических анализов даётся полное экономическое заключение использования того или другого новшества внедряемого на базовую технику.
Непосредственно в нашем случае происходит снижение удельных приведённых затрат при использовании унифицированного рабочего оборудования которое даёт возможность выполнять два вида работ при одном виде навесного оборудования. Ковш ёмкостью 16 м3 в предлагаемом рабочем оборудовании является поворотным что достигается за счёт применения зубчатого венца который обеспечивает поворот рабочего оборудования на необходимый угол с помощью зубчатой шестерни приводимой в действие при помощи гидродвигателя и червячного редуктора. Это даёт возможность производить работы по разработке грунта как выше уровня стояния машины так и ниже а именно использовать как прямую так и обратную лопаты при одном виде сменного рабочего оборудования экскаватора.
За счёт использования дополнительного устройства очевидно техническое усовершенствование за которым непосредственно следует положительный экономический эффект. При эксплуатации экскаватора с предлагаемым рабочим оборудованием снижаются годовые текущие затраты. На мой взгляд это является основным критерием по которому можно судить о целесообразности использования экскаватора с проведёнными на нём усовершенствованиями.
2 Проведение патентного поиска
В ходе проведённого поиска патентной информации по классам МПК
Е02F338 Е02 3413 были приняты к сведению материалы следующих авторских свидетельств.
Материалы патентного поиска сведены в табл. 1.1 табл. 1.2.
Регламент поиска патентной информации
Наименование источников информации по которым проводился поиск
Рабочее оборудование одноковшового экскаватора
Описание изобретений к авторским свидетельствам и патентам.
Изобретения в СССР и зарубежом.
Справка о поиске патентных документов
Дата приоритета.публикации.
Название изобретения
Авторское свидетельство
Московское научно-производственное объединение по строительному и дорожному машиностроению
Устройство для соединения сменного рабочего органа с рукоятью манипулятора
Продолжение таблицы 1.2
Рабочее оборудование одноковшового гидравлического экскаватора
Воронежская государственная архитектурно - строительная академия
Тюменский государственный нефтегазовый университет
Вращающаяся рукоять одноковшового экскаватора
Исполнитель: Крестников А.В.
Руководитель: Геращенко В.Н.
Авторское свидетельство № 1247470
Изобретение относится к манипуляторам а именно к одноковшовым экскаваторам со сменными рабочими органами.
Цель изобретения – расширение эксплуатационных возможностей и повышение надёжности.
Рис.1.1 Схема экскаватора с манипулятором
На рис.1.1 изображён экскаватор-манипулятор вид сбоку; на рис.1.2 – устройство для соединения рабочего органа с рукоятью манипулятора и схема системы управления.
Экскаватор-манипулятор содержит базовую машину 1 стрелу 2 рукоять вилочного типа 3 внутри которой на цапфах установлена телескопическая рукоять 4 с механизмом вращения вокруг продольной оси 5 стыковочным устройством 6 для неподвижного соединения со сменными рабочими органами например грейдером 7 ковшом 8 или другими органами.
На ходовой раме машины 1 расположены кассеты 9 для хранения сменных рабочих органов которыми могут быть схваты для круглых или плоских изделий ножницы для резки арматуры трамбовки и т.д.
Рис.1.2 Схема устройства для стыковки сменного рабочего органа
Устройство 6 для стыковки (соединения) сменного рабочего органа является частью телескопической рукояти 4 неподвижная труба 10 которая крепится в рукояти 3 а подвижная труба 11 (например квадратного сечения) имеет возможность выдвигаться на ползунах 12 с помощью силового гидроцилиндра закреплённого корпусом 13 на неподвижной трубе 10 шток 14 которого соединён с пружиной 15 подвижной трубы 11. Поршень 16 силового гидроцилиндра снабжён подпружинным клапаном 17 который во втянутом положении штока 14 перекрывает сливную ветвь и установленный на ней предохранительный клапан 18. На торце рабочих органов 7 8 и других имеется посадочный хвостовик 19 с конической заходной частью для соединения с подвижной трубой 11. Частность и надёжность фиксации обеспечивается фиксирующими защёлками 20 которые установлены у наружного торца подвижной трубы 11 и вводится пружинами 21 в прорезы 22 выполненные на поверхности посадочного хвостовика 19 и подвижной трубы 11. Профиль защёлок 20 и координаты осей их крепления обеспечивают при действии растягивающих усилий самозавинчивание защёлок в прорезях 22. Для размыкания защёлок служат упоры 23 (буртики) по торцевой поверхности неподвижной трубы 10.
Для поступательного перемещения рабочего органа силовой гидроцилиндр 13 телескопической рукояти 4 подключён к насосу 24 через трёхпозиционный гидрораспределитель 25 например с дистанционным гидравлическим управлением. Для ограничения величины усилия действующего на шток 14 во время работы в магистрали питания выношены предохранительные клапаны 26 и 27 причём клапан 27 выполнен с управляемой (от редуцирующего клапана 28) настройкой. При этом машинист включает клапан 28 педальным рычагом управления.
С помощью клапана 29 осуществляется подключение распределителя 25 к блоку управления или к редуцирующему клапану 28.
Клапан с управляемой настройкой имеет первоначальную настройку меньшую или равную настройке клапана 18 а максимальную – при включении редуцирующего клапана управления 28 – (11 – 12) KFP1 где KF - отношение площадей поршневой к штоковой полостей силового гидроцилиндра; P1 – давление настройки клапана 18.
Устройство работает следующим образом. Перемещение элементов рабочего оборудования (стрелы 2 рукояти 3 телескопической рукояти 4) машинист располагает подвижную трубу 11 телескопического механизма над хвостовиком 19 сменного рабочего органа расположенного в кассете 9 или на грунте. С помощью гидроцилиндра 13 подачей жидкости в поршневую полость осуществляется выдвижение штока 14 и вместе с ним подвижной трубы 11 которая центрирует посредством скосов хвостовика 19 продольную ось стыкуемого рабочего органа. По мере выдвижения трубы 11 фиксирующие защёлки расходятся и в момент совпадения прорезей 22 хвостовика и подвижной трубы с выступами защёлок 20 пружины 21 перемещают защёлки вовнутрь прорезей. Происходит фиксация рабочего органа на рукояти 4 манипулятора. Положение поршня может быть произвольным.
Авторское свидетельство № 819269
Изобретение относится к рабочему оборудованию экскаваторов в частности имеющему средства для замены сменных рабочих органов.
Целью настоящего изобретения является снижение трудоёмкости замены сменных рабочих органов. Эта цель достигается тем что в известном рабочем оборудовании шпоночное соединение выполнено из имеющих конические хвостовики шпонок при этом каждая шпонка имеет форму правильной усечённой пирамиды.
На рис 1.3 показано рабочее оборудование; на рис. 1.4 – рабочее оборудование с повёрнутым вокруг оси шарниры ковшом.
Рис 1.3 Схема рабочего оборудования гидравлического экскаватора
Рабочее оборудование одноковшового экскаватора включает: рукоять цилиндр управления тяги ковш и соединённые с рукоятью посредством пальцев проушины. Рукоять соединена с ковшом посредством шарнира вращения верхней частью которого служат проушины 7 а нижняя часть 8 соединена с ковшом посредством пальцевого шпоночного соединения 9 с фиксирующим приспособлением 10.
Шпоночное соединение выполнено из имеющих конические хвостовики 11 шпонок каждая из которых имеет форму правильной усечённой пирамиды 12.
На рис. 1.4 показана ось 13 поворота ковша.
Рис 1.4 Схема приспособления для поворота ковша
Для того чтобы заменить один ковш на другой фиксирующее приспособление которое выполнено в виде полых винтов вывинчивают из своих гнёзд на некоторое расстояние. В результате шпонки отходят от своих посадочных мест в виде углублений в нижней части 8. Далее нижнюю часть 8 вместе с ковшом поворачивают вокруг оси 13 а затем полые винты завинчивают в обратном направлении в результате головки шпонок входят в углубления нижней части 8
шарниры вращения и ковш фиксируются относительно рукояти.
При этом введение шпонок в кольцевой паз облегчается благодаря тому что они выполнены в виде правильных усечённых пирамид а конические хвостовики шпонок способствуют увеличению их хода что позволяет установить ковш с различными размерами нижней части 8 шарнирного соединения.
Авторское свидетельство № 759658
Изобретение относится к экскаваторной технике а более конкретно к рабочему оборудованию гидравлических экскаваторов.
На рис 1.5 показано рабочее оборудование; на рис 1.6 – механизм выдвижения рукояти.
Рис. 1.5 Схема рабочего оборудования
Рис 1.6 Схема механизма выдвижения рукояти
Рабочее оборудование экскаватора содержит стрелу 1 рукоять с внутренней 2 и наружной 3 секциями и ковшом 4 и механизм выдвижения внутренней секции 2 рукояти который имеет гидроцилиндр 5. Внутренняя секция 2 рукояти выполнена цилиндрической с винтовыми канавками 6 на её наружной поверхности 7. Наружная секция 3 рукояти снабжена жёстко прикреплённым к ней фланцем 8 имеющим сферические гнёзда 9 и расположенные в них шарики 10 с выступающими над гнёздами частями которые расположены в винтовых канавках 6 внутренней секции рукояти. При выдвижении штока гидроцилиндра 5 внутренней секции рукояти передаётся посредством винтовой канавки 6 и шариков 10 вращательно-поступательное движение. При этом длина рукояти изменяется а ковш поворачивается вокруг оси рукояти.
При работе обратной лопатой длина рукояти и глубина копания могут быть максимальными при повороте ковша на заданный угол происходит уменьшение длины рукояти чем достигается снижение изгибающих и крутящих моментов в местах соединения звеньев конструкции. При повороте рукояти на 180о рабочее оборудование будет представлять собой прямую лопату а уменьшение её длины снижает опрокидывающий момент что способствует устойчивости экскаватора.
Таким образом механизм выдвижения рукояти совмещён с механизмом поворота ковша что упрощает конструкцию рабочего оборудования в целом.
Авторское свидетельство № 647411
Изобретение относится к землеройной технике.
Цель изобретения – ускорение и повышение удобства замены одной лопаты на другую а также основного ковша на другой рабочий орган.
Это достигается тем что рукоять соединена с ковшом посредством шарнира вращения верхней частью которого служат проушины а нижняя часть соединена с ковшом посредством кольцевого шпоночного соединения с фиксирующим приспособлением.
На рис 1.7 представлено рабочее оборудование обратной лопаты; также – рабочее оборудование обратной лопаты.
Рис. 1.7 Схема конструкции соединения рукояти с ковшом
Рабочее оборудование одноковшового экскаватора содержит рукоять 1 цилиндр 2 тяги 3 ковш 4 проушины 5 и шарнир 6 вращения для соединения рукояти с ковшом. Проушины соединены с рукоятью посредством пальцев 7 и 8 и вместе приваренной к ним трубой 9 является верхней частью шарнира вращения. Нижней частью шарнира является труба 10 приваренная к ковшу 4.
На трубе 10 расположено шпоночное соединение с фиксирующим приспособлением состоящее из ряда призматических шпонок 11 с хвостовиками 12 и коническими головками 13 и полых винтов 14. Полые винты завинчены в трубу 10 и удерживают от выпадения шпонки 11 хвостовики которых расположены в отверстиях винтов.
Призматические поверхности шпонок входят в кольцевой паз выполненный в трубе 9 для фиксации обеих труб от осевого перемещения при возможности их поворота. Шпонки 11 своими коническими головками 13 входят в соответствующие углубления выполненные в кольцевом пазу трубы 9 и фиксируют ковш 4 от поворота в требуемом положении.
Для того чтобы заменить одну лопату на другую необходимо отвернуть на несколько оборотов полые винты 14 и провернуть на 180о трубу 10 относительно трубы 9. Благодаря тому что головки 13 имеют коническую поверхность они свободно выходят из углубления в пазу трубы 9. После поворота ковша 4 на определённый угол винты 14 завинчиваются до упора в квадраты шпонок которые своими коническими головками входят в другие углубления выполненные кольцевом пазу трубы 9. Затем винты 14 стопорятся контргайками 15.
Для замены основного ковша на другой рабочий орган ковш укладывается на грунт винты 14 вывинчивают на столько чтобы шпонки 11 вышли из кольцевого паза трубы 9 рукоять 1 с проушинами 5 и трубой 9 с помощью гидропривода экскаватора вынимают из трубы 10 ковша 4 после чего рукоять вставляют в другой рабочий орган и крепят его вновь шпонками 11.
Авторское свидетельство № 1265253
Рабочее оборудование одноковшового гидравлического экскаватора включает корпус 1 механизма осевого вращения и продольного перемещения штангу 2 рукояти соединённой с подвижной зубчатой рейкой 3. Штанга рукояти имеет например прямоугольное сечение и размещена с возможностью осевого перемещения в соответствующих отверстиях втулок 4 наружной цилиндрической частью посаженных во внутренних обоймах подшипников 5 наружные обоймы которых закреплены в корпусе 1. Винтовая гайка входит в винтовое зацепление с винтовой втулкой 7 имеющей соответствующую нарезку по наружной цилиндрической поверхности и посредством цилиндрической головки размещённой с возможностью осевого перемещения в цилиндрической выточке 8 выполненной в корпусе 1. Во внутреннем прямоугольном отверстии винтовой втулки 7 размещена штанга 2 рукояти имеющая возможность осевого перемещения относительно неё.
Рис. 1.8 Схема механизма поворота ковша
Винтовая втулка 7 шарнирно связана со штоком гидроцилиндра 9 поворота посредством хомута 10. Рис 1.8. Во внутренней полости корпуса 1 тесно закреплена неподвижная зубчатая рейка 11 имеющая направляющие вытачки 12. Такие же зубья и вытачки имеет подвижная зубчатая рейка 3. Между подвижной и неподвижной зубчатыми рейками установлена кинематически связывающая их двухребордная приводная шестерня 13 которая своими рейками выполненными по её наружной поверхности входит в зацепление с обеими рейками а боковыми ребордами – в направляющие выточки 12 обеих реек. На выходных концах оси 14 приводной шестерни выполнены лыски 15 размещённые в продольных направляющих 16 корпуса 1. Подвижная зубчатая рейка 3 связана со штангой рукояти посредством двух подшипниковых узлов 20 обеспечивающих поворот штанги вокруг собственной оси на фиксирующих его от осевого смещения относительно рейки 3. К оголовку 21 штанги рукояти эксцентрично подвешен ковш 22 который посредством рычага 23 и двупленного рычага 24 связан с гидроцилиндром привода ковша 25 навешенного на кронштейн 26 жёстко закреплённым на оголовке штанги. Шток 27 гидроцилиндра поворота рукояти вокруг оси подвеса на стреле шарнирно сочленён с промежуточным плечом трёхлинейного рычага 28 нижнее плечо которого шарнирно сочленено с боковиной стрелы 29 а верхнее посредством прямого рычага 30 – с кронштейном 31 закреплённым в проушинах 32 корпуса 1.
Для перехода с прямой лопаты на обратную и наоборот вынимают гидроцилиндр 9 шток которого посредством хомута 10 перемещает винтовую втулку 7 вдоль направляющей выточки 8. В процессе продольного перемещения винтовая втулка 7 посредством винтового зацепления с неподвижной гайкой 6 совершает осевое вращение поворачивая при этом штангу 2 вместе с ковшом.
Изобретение относится к землеройной технике. Рабочее оборудование одноковшового экскаватора выполняет рукоять цилиндр управления соединённый одним концом через систему тяг посредством проушин и шарниров с ковшом поворотное устройство с элементами стопорения. Поворотное устройство выполнено в виде установленных на рукояти поворотных кронштейнов один из которых шарнирно соединён с ковшом и системой тяг связывающих цилиндр управления с ковшом а другой также шарнирно соединён со вторым концом цилиндра управления.
На рис. 1.9 представлено рабочее оборудование обратной лопаты; и рабочее оборудование прямой лопаты; на рис 1.10 – конструкция поворотного кронштейна и мест соединения.
Рис. 1.9 Схема поворотного рабочего оборудования
Рис. 1.10 Схема конструкции поворотного кронштейна
Рабочее оборудование одноковшового экскаватора содержит рукоять 1 на которую устанавливаются поворотные кронштейны 5 и 6 с элементами стопорения 7. Цилиндр 2 управления ковшом одним своим концом непосредственно крепится к кронштейну 6 а другим – к системе тяг 4 которая соединена с кронштейном 5 гидроцилиндром 2 проушиной 9 при помощи шарниров 8. В свою очередь ковш 3 крепится к поворотному кронштейну 5 также с помощью шарнира.
Для того чтобы заменить одну лопату на другую необходимо отвернуть на несколько оборотов элементы стопорения 7 расположенные на поворотных кронштейнах 5 и 6 и повернуть последние на 1800 вокруг своей оси рукояти 1 при этом вместе с кронштейнами 5 и 6 поворачивается цилиндр 2 с системой тяг 4 шарнирно соединённой с ковшом 3. После поворота всех элементов на указанный угол стопорные элементы 7 завинчиваются до упора.
В связи с тем что стопорение кронштейнов 5 и 6 осуществляется стопорным элементом 7 происходит ускорение замены основного вида лопаты на другую что делает процесс более удобным.
Авторское свидетельство № 1313957
Изобретение относится к строительно-дорожным машинам и позволяет повысить производительность за счёт повышения надёжности работы при переоборудовании с прямой лопаты на обратную и наоборот. Оборудование содержит рукоять 1 шарнирно связанный с ней ковш 5 и механизм поворота ковша 5 с гидродвигателем (ГД) 14 в виде моментного гидроцилиндра и со стопорным механизмом 13 в виде гидроцилиндра с подпружиненным поршнем. Механизм поворота ковша 5 выполнен в виде роликового опорно-поворотного круга (ОПК) имеющего систему гидроуправления. Причём ГД 14 установлен соосно ОПК посредством пазового соединения с ним. Между подвижной 11 и неподвижной 8 частями ОПК размещены упоры 17 и 18. Система гидроуправления содержит трёхпозиционный золотниковый распределитель имеющий нейтральное положение два подпружиненных нормально закрытых гидроэлемента установленные на упоре 17 два обратных клапана и систему напорных и сливных магистралей. При переоборудовании с прямой лопаты на обратную и наоборот оператор воздействует на золотниковый распределитель и рабочая жидкость подаётся в рабочую полость ГД 14.
Рис.1.11 Схема конструкции поворотного приспособления
Рабочие полости ГД сообщены обратными клапанами со штоковой рабочей полостью СМ 13 и через нормально закрытые гидроэлементы сообщены со сливной магистралью. Поршневая полость СМ 13 сообщена со сливной гидромагистралью. В начальный момент времени происходит отрывание СМ 13. Затем ковш 5 начинает поворачиваться и происходит отжатие гидросегмента. При повороте ковша 5 на 1800 толкателями гидроэлементов упираются в упоры 18 происходит их плавное перемещение и штоковая полость СМ 13 соединяется со сливной магистралью. Происходит фиксация ковша 5 посредством штока СМ 13.
На рис 1.11 представлен разрез конструкции поворотного приспособления; на рис 1.12 – вариант рабочего оборудования.
Рис. 1.12 Схема рабочего оборудования
Рабочее оборудование одноковшового экскаватора содержит рукоять 1 гидроцилиндр 2 управления ковшом тяги 3 опорно-поворотный круг 4 и ковш 5. Рукоять соединена с ковшом посредством пальцев 6 и проушин 7 приваренных к неподвижной части ОПК 4 являющегося механизмом поворота ковша. ОПК 4 содержит неподвижную часть состоящего из верхнего 8 и нижнего 9 фланцев соединённых между собой болтами 10 подвижную часть 11 роликовый сепаратор 12 стопорный механизм 13 и гидродвигатель 14. Вал 15 ГД соединён с подвижной частью 11 посредством пазового соединения 16. На верхнем фланце 8 подвижной части опорно-поворотного круга расположены предохранительные упоры 17 а на подвижной части 11 - предохранительный упор 18 и два отверстия для фиксации ковша.
Изобретение относится к землеройной технике в частности к рабочему оборудованию одноковшовых экскаваторов. Сущность изобретения – вращающаяся рукоять одноковшового экскаватора состоит из неповоротной и поворотной частей винтовой пары гидроцилиндра включающего корпус поршень и шток. Неповоротная и поворотная часть соединены ОПУ винт и гайка имеют не самотормозящую резьбу винт и шток гидроцилиндра соединены между собой а гайка соединена с основанием ОПУ. На рис. 1.13 изображён общий вид вращающейся рукояти.
Рис. 1.13 Схема вращающейся рукояти
Вращающаяся рукоять одноковшового экскаватора содержит неповоротную1 и поворотную 2 части. На неповоротной 1 части расположен гидроцилиндр 3. Шток 4 гидроцилиндра 3 соединён с винтом 5 который входит в соединение с гайкой 6 закреплённой на основании ОПУ 7. Основание 7 соединено с поворотной частью рукояти. Для предотвращения поворачивания винта служит скользящая шпонка 8.
При подаче рабочей жидкости в полость гидроцилиндра 3 шток 4 совместно с винтом 5 угол подъёма винтовой линии которого больше угла трения пары винт-гайка совершают возвратно-поступательные движения заставляя вращаться гайку 6 и закреплённое с гайкой основание ОПУ 7 которое приводит во вращение поворотную часть 2 вследствие чего происходит вращение рукояти.
3 Анализ вариантов технических решений
Патентные исследования по теме «Модернизация рабочего оборудования одноковшового экскаватора» проводились в Центральной Библиотеке имени И.С. Никитина. После проведения патентных исследований и анализа отобранных мной патентов и авторских свидетельств из огромного количества находящихся в библиотеке я выбрал наиболее интересные варианты.
Из отобранных вариантов как источник базовой информации для внедрения новшества разрабатываемого в моей квалификационной работе бакалавра выбрал патент МПК Е02F338 340 № 2149951.
техэконом.doc
1 Обоснование темы диссертации
В настоящее время ни одно строительство не обходится без земляных работ и машин выполняющих эти работы. Рост темпов объёмов строительства усложнения конструкции возводимых сооружений непрерывный рост интенсивности движения автомобильного транспорта а так же возрастающая необходимость в возведении новых промышленных и транспортных объектов только увеличил интерес и потребность в машинах для земляных работ.
На сегодняшний день их производством занимается немало компаний с мировыми именами. Некоторые из них используют свои собственные оригинальные разработки и создают конструктивные особенности этих машин но в целом несмотря на обилие марок принципы их устройства и сферы применения являются одинаковыми. Именно они придают этим машинам столь оригинальный вид.
Рисунок 1.1 – Автогрейдер
Выпуск автогрейдеров в России в настоящее время осуществляют три завода строительно-дорожных машин – Брянский
Орловский и Челябинский причем серийный выпуск тяжелых грейдеров
освоил лишь Челябинский завод. Эти машины наиболее эффективны при выполнении землеройно-планировочных работ на строительстве при ремонте и содержании дорог. По необходимости применяют их и в других сферах деятельности.
Так как парк машин для земляных работ очень велик и разнообразен как по функциям так и по устройству конструкции машин темой данной диссертации станет проект модернизации системы управления рабочего оборудования автогрейдера ДЗ – 143. Следовательно необходимо сделать так чтобы эта машина стала ещё более универсальной а это может быть достигнуто путём модернизации отдельных узлов и деталей или выпуском совершенно новой техники.
Основным назначением автогрейдера ДЗ-143 является профилирование земляного полотна строительство грунтовых дорог на нулевых отметках или на насыпях воздвигаемых из грунта кюветов планировка грунтовых поверхностей.
Выполнение всех функций грейдера происходит с помощью специального рабочего органа – отвала с ножом который смонтирован на раме машины. Его можно поднимать опускать поворачивать в горизонтальной и вертикальной плоскости.
Так как автогрейдеры оснащают различным сменным дополнительным оборудованием область применения их очень широка. Автогрейдер является одной из распространённых и востребованных машин что доказывает актуальность данной диссертации.
2 Проведение патентного поиска
Регламента поиска представляет собой программу определяющую область проведения поиска по фондам патентной и другой научно – технической (в том числе конструкторской - экономической) информации. Для определения области поиска требуется сформировать предмет поиска и классификационные рубрики (МКИ НКИ УДК).
Предмет поиска определяют исходя из конкретных задач патентных исследований категории объекта (устройство способ вещество) а так же из того какие элементы параметры свойства и другие его характеристики предполагается исследовать.
Для правильного поиска информации необходимо определить классификационные рубрики по каждому предмету поиска: для поиска научно – технической и конструкторно – экономической информации используют универсальную десятичную классификацию (УДК) для поиска описаний изобретений к авторским свидетельствам и патентам используют международную и национальные классификации изобретений (МКНМКИ).
Регламент поиска патентной информации.
Перечень вопросов или элементов по которым необходим поиск информации
Рабочее оборудование автогрейдера
Описание изобретений к авторским свидетельствам и патентам.
Изобретения в СССР и за рубежом.
Руководитель Жулай В.А.
Патентовед Жулай В.А.
В нашем случае будем использовать международную патентную классификацию (МПК).
Перечень патентных документов отобранных при поиске.
Номер авторского свиде-тельст-ва или патента
Действи-тельные авторы
Название изоб-ретения
ВС. Щербаков. В.В. Беляев и В.Е Калугин
Т. Хидиров Х. Муратов
Грейдерное навесное оборудование
Амельченко В.Ф. Денисов В.П. Мещеряков В.А. Славский А.А.
Caterpillar Tractor Co
Motor grader blade adjusting mechanism
Raising and lowering mechanism for bulldozers
В.А. Кацин В.П. Попов А.М. Завьялов A.. Ефремов Г.H. Мусонов МБ. Баянников Н.В. Сакулин И.А. Матвеенко В.М. Куринский и A.A. Литвиненко
Рабочее оборудование землеройной машины
Ю.М.Бузин Л.ХШарипов В.А.Жулай.
Воронежский инженерно-строительный институ
Stanwell Parkes Frederick
Road-grading machine
Raymond A Gurries Burnett J Christensen
Road building machine with two adjustable work implements
Vergil Philip HendricksonCarroll Richard Cole
Caterpillar Tractor Co.
Motor grader blade mounting and tilt mechanism
3 Анализ вариантов технических решений
Патент США № 3444936
Лезвие автогрейдера соединено с кругом через параллелограмм и предусмотренным средством управления. В результате чего высота лезвие может быть изменена без нарушения параметров. И наоборот наконечник может регулироваться без изменения высоты. Обе настройки быстро осуществляются с драйверами станции и без операции первичных управлений положением лезвия.
Настоящее изобретение относится к оборудованию для земляных работ а более конкретно легко контролируемым быстродействующим действиям и более точным механизмам регулировки земляных работ лезвием грейдера.
Цель настоящего изобретения – обеспечение более точного и полного управления положением лезвия автогрейдера.
Задачами настоящего изобретения являются:
- упрощение работы грейдера;
- обеспечение изменения наклона механизма для подъема и опускания лезвия грейдера;
- обеспечение быстрого контроля по глубине среза лезвия автогрейдера с помощью одного средства управления;
- обеспечение сохранения лезвия в фиксированном положении для подъема или опускания лезвия грейдера;
- обеспечение увеличения клиренса лезвия грейдера не нарушая других его параметров.
Изобретение вместе с дополнительными задачами и преимуществами будут лучше понятны со ссылкой на последующие описания в совокупности с прилагаемыми чертежами из которых:
Фиг.1 представляет собой вид сбоку грейдер согласно изобретению;
Фиг.2 представляет собой вид в перспективе передней части грейдера по фиг.1 показывающий его лезвие в наклонном положении и части структуры лезвие монтажной нарушенной вне.
Обратимся теперь к рисунку - на нём автогрейдер 11 как правило имеет двигатель 12 и операторов станции 13 езды на задних колесах 14 и арочные основы элементов рамы 16 проходящую вперед к поддержанию 17 с передними колесами 18 такие действия. Лезвие отвала для земляных работ 19 рисуется для тяговой структуры 21 имеющей передний конец прикрепленный к валику 17 посредством шарнира 22 который обеспечивает его поворот и поворот дышла и присоединенных элементов на теле грейдера 11.
Лезвие 19 прикреплено к лопасти круга 26 поддержки и управления узлом 32 который будет подробно описан ниже. Он в свою очередь прикреплен к лопасти окружности отключаемых средств таких как болты 33. Поворот лопасти 19 по отношению к направлению движения грейдера 11 имеет тенденцию быть в пределах ограниченного диапазона настройки для большинства операций.
Рисунок 1.2 – Схема механизма стабилизации
Смысл в том чтобы сконцентрировать износ лезвий окружности зубьев 28 в ограниченном сегменте с лезвиями круга. Тем не менее в настоящем строительстве лезвие круга 26 может быть периодически замкнуто от опорного узла лезвий 32 и поворачивается относительно него. Посредством этого расположение зубов 28 может быть равномерно распределено по кругу 26 и это значительно продлевает срок службы механизма обеспечивающего большую жесткость и упрощает техническое обслуживание.
Грейдер 11 использует настоящее изобретение как правило с обычным набором регулировки лезвия и управляет дополнением к более быстрому и точному управлению представленного изобретения. Обратимся снова к фиг.1: типичные стандартные элементы управления включают в себя пару подъемников 34 простирающихся вдоль каждой стороны основного элемента рамы 16 и имеющих связь 36 подключения к соответствующей стороне поперечины тяги 24 через шаровой шарнир 37. По работе на подъем 34 дышла 21 и таким образом лезвие 19 может быть выглублено или заглублено. При дифференциальной эксплуатации лифтов 34 наклон лопатки 19 со ссылкой на поперечную горизонтальную ось проходящую через грейдер может быть избирательно изменено. Как выше уже отмечалось изменение в любой из этих регулировок может мешать другим требующим дальнейших перенастроек в восстановлении лезвия 19 на предпочтительную установку. Кроме того в не зависимости от проблем управления передаточные числа обычно используемые в лифтах 34 исключает очень быстрые изменения в установки лопасти.
Для поворота дышла 21 и таким образом лезвия 19 в боковом направлении стандартный механизм бокового смещения 35 смонтирован на раме 16 и соединен через связи 40 чтобы пересечь элемент 24 дышла на шаровой шарнир 38. Связь 39 проходит от станции оператора 13 к описанным выше механизмом для вращения лезвия 26 относительно дышла.
Авторское свидетельство № 817157
Изобретение относится к строительно-дорожным машинам а именно к землеройным машинам типа бульдозеров.
Известно рабочее оборудование землеройной машины включающее отвал в виде подпружиненной гибкой ленты опирающийся на решетчато-балочную конструкцию режущий нож и гидроцилиндры управления.
Наиболее близким по технической сущности и достигаемому результату к предлагаемому является рабочее оборудование землеройной машины включающее отвал с изменяемым профилем толкающие брусья гидроцилиндры управления и подкосы.
Недостатком устройства является малая эффективность работы в связи с отсутствием регулировки угла наклона отвала.
Цель изобретения - повышение эффективности разработки грунта путем обеспечения регулирования угла наклона отвала.
Указанная цель достигается тем что толкающие брусья снабжены серьгами с гидроцилиндрами поворота а гидроцилиндры изменения профиля отвала соединены с серьгами.
Причем отвал выполнен из упругого листа.
На фиг. 1 изображено рабочее оборудование вид сбоку; на фиг. 2 - то же вид в плане.
Рабочее оборудование землеройной машины включает отвал 1 выполненный из гибкого упругого листа например из полиуретана на тыльной стороне которого жестко закреплены горизонтальные секции 2 одна из которых шарнирно установлена на толкающих брусьях 3.
В нижней части отвала 1 закреплен режущий нож 4. На толкающих
брусьях шарнирно установлены серьги 5 с возможностью поворота посредством гидроцилиндров 6 шарнирно установленных на толкающих брусьях 3. Регулируемый поворот секций 2 обеспечивается гидроцилиндрами 7 установленными на серьгах 5.
Рабочее оборудование землеройной машины работает следующим образом.
Отвал 1 опускается на грунт. Режущий нож 4 устанавливается под необходимым углом резания. Стружка грунта отделяемая
Рисунок 1.3 – Схема отвала с изменяемым профилем
режущим ножом от массива поднимается по отвальной поверхности. При этом секции 2 поворачиваются гидроцилиндрами 7 изменяя
кривизну отвальной поверхности в поперечном сечении.
Одновременно с этим серьги 5 поворачиваются посредством гидроцилиндров 6. При повороте серег 5 изменяется и угол наклона отвала 1 поскольку последний связан с серьгами. 5 посредством гидроцилиндров 7.
Введение в конструкцию регулирования угла наклона отвала позволяет уменьшить сопротивление продвижению
грунта по отвалу и уменьшить энергоемкость копания грунта что приводит к повышению эффективности разработки
Патент США № 2604708
Настоящее изобретение делает возможным контроль над передним углом лезвия перед процессом копания и т.п. без ограничения вызванного неподвижными центрами для управления связью. В настоящем изобретении связанные четырехугольники предназначены для поддержки лезвия от источника носителем таким как трактор таким же образом как описано в исходной заявке. Эти кулачковые дорожки могут иметь любую желаемую конфигурацию для того чтобы сместить изменение угла лезвия автогрейдера при перемещении лезвия.
В этой конструкции следовательно любое желаемое передний угол лезвия могут поддерживаться или разнообразны как лезвие поднимается и опускается. В показанном варианте изобретения лезвие проходит по вертикали всего ее нормального диапазона отмеченного выше и ниже уровня земли а затем наклоняется вперед выше диапазона очищающего.
Задачей настоящего изобретения является:
- улучшение сцепления для сборки исходной заявки с серийным номером 523464. При этом передний угол реализовывается при поддержке сборки сцепления;
- создание рабочего оборудования которое поддерживает его передний угол который может быть выбран при любом положении лопасти в процессе его диапазона перемещения;
- создание связи которая управляет передним углом бульдозера лопасти по желанию и без каких-либо ограничений;
- обеспечение бульдозера скребковым узлом в котором передний угол от бульдозерного лезвия или лезвия скребка контролируется кулачком;
Другие и дополнительные цели изобретения будут очевидны специалистам в данной области техники из следующего подробного описания прилагаемых чертежей которые в качестве предпочтительного примера иллюстрируют один вариант изобретения.
Корпус заднего моста I4 поддерживает трак I5 и средство передачи (не показан) внутри корпуса моста приводится в движение двигателем для привода звездочки на вал I6. Направляющие ролики 2l на гусеничных рамах взаимодействуют с нижними прогонами треков 20.
Рисунок 1.4 – Схема конструкции контроля переднего угла
Пластины 24 и 25 могут быть закреплены на наружных поверхностях балки с помощью заклепок сварки и тому подобное.
Поперечные трубы 26 и 27 охватывают верхние концы пластин 24 и 25 расположенных параллельно. Эти поперечные трубки закреплены на пластинах. Пара консольных плит 23 приварены передней поверхностью трубок 26 и 27 в центральных частях.
Гидравлический домкрат (узел 29) для подъема и опускания отвала включает в себя гидроцилиндр 30 расположенный между кронштейнами 28 и имеющих цапфы 3I выступающих вбок от нее промежуточной оси их концов и шарниров 32 на кронштейнах 28.
Авторское свидетельство № 1315569
Цель изобретения – повышение эффективности путём стабилизации глубины резания при изменении угла резания отвала в процессе работы.
Изобретение относится к землеройно – транспортным машинам и повышает эффективность путём стабилизации глубины резания при изменении угла резания отвала в процессе работы. Оборудование
Рисунок 1.5 – Рабочий орган. Авторское свидетельство № 1315569
автогрейдера включает поворотный круг 1 с кронштейном 2 отвал 3 и гидроцилиндр (ГЦ) 5 изменения угла резания. Отвал 3 нижней частью посредством двуплечего рычага 9 шарнирно соединён со свободным концом кронштейна 2. С корпусом ГЦ 5 шарнирами 12 и 13 соединена тяга 11 управления. Шток ГЦ 5 шарнирно соединён с тягой 11. Отвал 3 поворачивается в шарнире 8 по часовой стрелке увеличивая угол резания и глубину. Корпус ГЦ 5 поворачивается в шарнире 6 по часовой стрелке перемещая через шарнир 13 тягу 11 вниз. Рычаг 9 поворачивается в шарнире 10 против часовой стрелки а отвал 3 перемещается вверх уменьшая глубину резания. 2 з.п ф – лы 2 ил.
Изобретение относится к землеройно – транспортным машинам в частности к управлению рабочими органами автогрейдеров предназначенных для использования главным образом в дорожном строительстве.
Механизм изменения угла резания отвала автогрейдера содержит поворотный круг 1 с кронштейном 2 отвал 3 соединённый в верхней части шарниром 4 со штоком гидроцилиндра 5 корпус которого в шарнире 6 соединён с неподвижным кронштейном 7 поворотного круга 1. Гидроцилиндр 5 может быть установлен в середине отвала 3 или в количестве двух штук по его краям. В нижней части отвал 3 соединён в шарнире 8 с двуплечим рычагом 9 который в шарнире 10 соединён со свободным концом кронштейна 2 поворотного круга 1. Привод двуплечего рычага 9 осуществляется от корпуса гидроцилиндра 5 тягой 11 управления соединённой с ними в шарнирах 12 и 13.
Предлагаемый механизм является шестизвенным с одной степенью свободы (ведущее звено – шток с поршнем гидроцилиндра 5 ведомое звено – отвал 3 неподвижное звено – поворотный круг 1 с кронштейнами 2 и 7).
Патент США 2604708.doc
Настоящее изобретение делает возможным контроль над передним углом лезвия перед процессом копания и т.п. без ограничения вызванного неподвижными центрами для управления связью. В настоящем изобретении связанные четырехугольники предназначены для поддержки лезвия от источника носителем таким как трактор таким же образом как описано в исходной заявке. Эти кулачковые дорожки могут иметь любую желаемую конфигурацию для того чтобы сместить изменение угла лезвия автогрейдера при перемещении лезвия.
В этой конструкции следовательно любое желаемое передний угол лезвия могут поддерживаться или разнообразны как лезвие поднимается и опускается. В показанном варианте изобретения лезвие проходит по вертикали всего ее нормального диапазона отмеченного выше и ниже уровня земли а затем наклоняется вперед выше диапазона очищающего.
Задачей настоящего изобретения является:
- улучшение сцепления для сборки исходной заявки с серийным номером 523464. При этом передний угол реализовывается при поддержке сборки сцепления;
- создание рабочего оборудования которое поддерживает его передний угол который может быть выбран при любом положении лопасти в процессе его диапазона перемещения;
- создание связи которая управляет передним углом бульдозера лопасти по желанию и без каких-либо ограничений;
- обеспечение бульдозера скребковым узлом в котором передний угол от бульдозерного лезвия или лезвия скребка контролируется кулачком;
Другие и дополнительные цели изобретения будут очевидны специалистам в данной области техники из следующего подробного описания прилагаемых чертежей которые в качестве предпочтительного примера иллюстрируют один вариант изобретения.
Корпус заднего моста I4 поддерживает трак I5 и средство передачи (не показан) внутри корпуса моста приводится в движение двигателем для привода звездочки на вал I6. Направляющие ролики 2l на гусеничных рамах взаимодействуют с нижними прогонами треков 20.
Пластины 24 и 25 могут быть закреплены на наружных поверхностях балки с помощью заклепок сварки и тому подобное.
Поперечные трубы 26 и 27 охватывают верхние концы пластин 24 и 25 расположенных параллельно. Эти поперечные трубки закреплены на пластинах. Пара консольных плит 23 приварены передней поверхностью трубок 26 и 27 в центральных частях.
Гидравлический домкрат (узел 29) для подъема и опускания отвала включает в себя гидроцилиндр 30 расположенный между кронштейнами 28 и имеющих цапфы 3I выступающих вбок от нее промежуточной оси их концов и шарниров 32 на кронштейнах 28.
Авт. свид. № 1315569.doc
3 Проведение патентного поиска
В ходе проведённого поиска патентной информации был принят к сведению материал следующего авторского свидетельства.
Авторское свидетельство № 1315569
Цель изобретения – повышение эффективности путём стабилизации глубины резания при изменении угла резания отвала в процессе работы.
Рисунок 1.3 – Рабочий орган. Авторское свидетельство № 1315569
Изобретение относится к землеройно – транспортным машинам и повышает эффективность путём стабилизации глубины резания при изменении угла резания отвала в процессе работы. Оборудование автогрейдера включает поворотный круг 1 с кронштейном 2 отвал 3 и гидроцилиндр (ГЦ) 5 изменения угла резания. Отвал 3 нижней частью посредством двуплечего рычага 9 шарнирно соединён со свободным концом кронштейна 2. С корпусом ГЦ 5 шарнирами 12 и 13 соединена тяга 11 управления. Шток ГЦ 5 шарнирно соединён с тягой 11. Отвал 3 поворачивается в шарнире 8 по часовой стрелке увеличивая угол резания и глубину. Корпус ГЦ 5 поворачивается в шарнире 6 по часовой стрелке перемещая через шарнир 13 тягу 11 вниз. Рычаг 9 поворачивается в шарнире 10 против часовой стрелки а отвал 3 перемещается вверх уменьшая глубину резания. 2 з.п ф – лы 2 ил.
Изобретение относится к землеройно – транспортным машинам в частности к управлению рабочими органами автогрейдеров предназначенных для использования главным образом в дорожном строительстве.
Механизм изменения угла резания отвала автогрейдера содержит поворотный круг 1 с кронштейном 2 отвал 3 соединённый в верхней части шарниром 4 со штоком гидроцилиндра 5 корпус которого в шарнире 6 соединён с неподвижным кронштейном 7 поворотного круга 1. Гидроцилиндр 5 может быть установлен в середине отвала 3 или в количестве двух штук по его краям. В нижней части отвал 3 соединён в шарнире 8 с двуплечим рычагом 9 который в шарнире 10 соединён со свободным концом кронштейна 2 поворотного круга 1. Привод двуплечего рычага 9 осуществляется от корпуса гидроцилиндра 5 тягой 11 управления соединённой с ними в шарнирах 12 и 13.
Предлагаемый механизм является шестизвенным с одной степенью свободы (ведущее звено – шток с поршнем гидроцилиндра 5 ведомое звено – отвал 3 неподвижное звено – поворотный круг 1 с кронштейнами 2 и 7).
Патент США 3444936.doc
Лезвие автогрейдера соединено с кругом через параллелограмм и предусмотренным средством управления. В результате чего высота лезвие может быть изменена без нарушения параметров. И наоборот наконечник может регулироваться без изменения высоты. Обе настройки быстро осуществляются с драйверами станции и без операции первичных управлений положением лезвия.
Настоящее изобретение относится к оборудованию для земляных работ а более конкретно легко контролируемым быстродействующим действиям и более точным механизмам регулировки земляных работ лезвием грейдера.
Цель настоящего изобретения – обеспечение более точного и полного управления положением лезвия автогрейдера.
Задачами настоящего изобретения являются:
- упрощение работы грейдера;
- обеспечение изменения наклона механизма для подъема и опускания лезвия грейдера;
- обеспечение быстрого контроля по глубине среза лезвия автогрейдера с помощью одного средства управления;
- обеспечение сохранения лезвия в фиксированном положении для подъема или опускания лезвия грейдера;
- обеспечение увеличения клиренса лезвия грейдера не нарушая других его параметров.
Изобретение вместе с дополнительными задачами и преимуществами будут лучше понятны со ссылкой на последующие описания в совокупности с прилагаемыми чертежами из которых:
Фиг.1 представляет собой вид сбоку грейдер согласно изобретению;
Фиг.2 представляет собой вид в перспективе передней части грейдера по фиг.1 показывающий его лезвие в наклонном положении и части структуры лезвие монтажной нарушенной вне.
Обратимся теперь к рисунку - на нём автогрейдер 11 как правило имеет двигатель 12 и операторов станции 13 езды на задних колесах 14 и арочные основы элементов рамы 16 проходящую вперед к поддержанию
с передними колесами 18 такие действия. Лезвие отвала для земляных работ 19 рисуется для тяговой структуры 21 имеющей передний конец прикрепленный к валику 17 посредством шарнира 22 который обеспечивает его поворот и поворот дышла и присоединенных элементов на теле грейдера 11.
Лезвие 19 прикреплено к лопасти круга 26 поддержки и управления узлом 32 который будет подробно описан ниже. Он в свою очередь прикреплен к лопасти окружности отключаемых средств таких как болты 33. Поворот лопасти 19 по отношению к направлению движения грейдера 11 имеет тенденцию быть в пределах ограниченного диапазона настройки для большинства операций. Смысл в том чтобы сконцентрировать износ лезвий окружности зубьев 28 в ограниченном сегменте с лезвиями круга. Тем не менее в настоящем строительстве лезвие круга 26 может быть периодически замкнуто от опорного узла лезвий 32 и поворачивается относительно него. Посредством этого расположение зубов 28 может быть равномерно распределено по кругу 26 и это значительно продлевает срок службы механизма обеспечивающего большую жесткость и упрощает техническое обслуживание.
Грейдер 11 использует настоящее изобретение как правило с обычным набором регулировки лезвия и управляет дополнением к более быстрому и точному управлению представленного изобретения. Обратимся снова к фиг.1: типичные стандартные элементы управления включают в себя пару подъемников 34 простирающихся вдоль каждой стороны основного элемента рамы 16 и имеющих связь 36 подключения к соответствующей стороне поперечины тяги 24 через шаровой шарнир 37. По работе на подъем 34 дышла 21 и таким образом лезвие 19 может быть выглублено или заглублено. При дифференциальной эксплуатации лифтов 34 наклон лопатки 19 со ссылкой на поперечную горизонтальную ось проходящую через грейдер может быть избирательно изменено. Как выше уже отмечалось изменение в любой из этих регулировок может мешать другим требующим дальнейших перенастроек в восстановлении лезвия 19 на предпочтительную установку. Кроме того в не зависимости от проблем управления передаточные числа обычно используемые в лифтах 34 исключает очень быстрые изменения в установки лопасти.
Для поворота дышла 21 и таким образом лезвия 19 в боковом направлении стандартный механизм бокового смещения 35 смонтирован на раме 16 и соединен через связи 40 чтобы пересечь элемент 24 дышла на шаровой шарнир 38. Связь 39 проходит от станции оператора 13 к описанным выше механизмом для вращения лезвия 26 относительно дышла.
1.Технико-экономичесское обоснование .doc
1 Обоснование темы диссертации
В настоящее время ни одно строительство не обходится без земляных работ и машин выполняющих эти работы. Рост темпов объёмов строительства усложнения конструкции возводимых сооружений непрерывный рост интенсивности движения автомобильного транспорта а так же возрастающая необходимость в возведении новых промышленных и транспортных объектов только увеличил интерес и потребность в машинах для земляных работ.
На сегодняшний день их производством занимается немало компаний с мировыми именами. Некоторые из них используют свои собственные оригинальные разработки и создают конструктивные особенности этих машин но в целом несмотря на обилие марок принципы их устройства и сферы применения являются одинаковыми. Именно они придают этим машинам столь оригинальный вид.
Рисунок 1.1 – Автогрейдер
Выпуск автогрейдеров в России в настоящее время осуществляют три завода строительно-дорожных машин – Брянский Орловский и Челябинский причем серийный выпуск тяжелых грейдеров
освоил лишь Челябинский завод. Эти машины наиболее эффективны при выполнении землеройно-планировочных работ на строительстве при ремонте и содержании дорог. По необходимости применяют их и в других сферах деятельности.
Так как парк машин для земляных работ очень велик и разнообразен как по функциям так и по устройству конструкции машин темой данной диссертации станет проект модернизации системы управления рабочего оборудования автогрейдера ДЗ – 143. Следовательно необходимо сделать так чтобы эта машина стала ещё более универсальной а это может быть достигнуто путём модернизации отдельных узлов и деталей или выпуском совершенно новой техники.
Основным назначением автогрейдера ДЗ-143 является профилирование земляного полотна строительство грунтовых дорог на нулевых отметках или на насыпях воздвигаемых из грунта кюветов планировка грунтовых поверхностей.
Выполнение всех функций грейдера происходит с помощью специального рабочего органа – отвала с ножом который смонтирован на раме машины. Его можно поднимать опускать поворачивать в горизонтальной и вертикальной плоскости.
Так как автогрейдеры оснащают различным сменным дополнительным оборудованием область применения их очень широка. Автогрейдер является одной из распространённых и востребованных машин что доказывает актуальность данной диссертации.
2 Проведение патентного поиска
Регламента поиска представляет собой программу определяющую область проведения поиска по фондам патентной и другой научно – технической (в том числе конструкторской - экономической) информации. Для определения области поиска требуется сформировать предмет поиска и классификационные рубрики (МКИ НКИ УДК).
Предмет поиска определяют исходя из конкретных задач патентных исследований категории объекта (устройство способ вещество) а так же из того какие элементы параметры свойства и другие его характеристики предполагается исследовать.
Для правильного поиска информации необходимо определить классификационные рубрики по каждому предмету поиска: для поиска научно – технической и конструкторно – экономической информации используют универсальную десятичную классификацию (УДК) для поиска описаний изобретений к авторским свидетельствам и патентам используют международную и национальные классификации изобретений (МКНМКИ).
Таблица 1.1 - Регламент поиска патентной информации.
Перечень вопросов или элементов по которым необходим поиск информации
Рабочее оборудование автогрейдера
Описание изобретений к авторским свидетельствам и патентам.
Изобретения в СССР и за рубежом.
Руководитель Жулай В.А.
Патентовед Жулай В.А.
В нашем случае будем использовать международную патентную классификацию (МПК).
Таблица 1.2 - Перечень патентных документов отобранных при поиске.
Номер авторского свиде-тельст-ва или патента
Действи-тельные авторы
Название изоб-ретения
ВС. Щербаков. В.В. Беляев В.Е Калугин
Т. Хидиров Х. Муратов
Грейдерное навесное оборудование
Амельченко В.Ф. Денисов В.П. Мещеряков В.А. Славский А.А.
Caterpillar Tractor Co
Motor grader blade adjusting mechanism
Raising and lowering mechanism for bulldozers
В.А. Кацин В.П. Попов А.М. Завьялов A.. Ефремов Г.H. Мусонов МБ. Баянников Н.В. Сакулин И.А. Матвеенко В.М. Куринский и A.A. Литвиненко
Рабочее оборудование землеройной машины
Ю.М.Бузин Л.ХШарипов В.А.Жулай.
Воронежский инженерно-строительный институ
Stanwell Parkes Frederick
Road-grading machine
Raymond A Gurries Burnett J Christensen
Road building machine with two adjustable work implements
Vergil Philip HendricksonCarroll Richard Cole
Caterpillar Tractor Co.
Motor grader blade mounting and tilt mechanism
3 Анализ вариантов технических решений
Патент США № 3444936
Лезвие автогрейдера соединено с кругом через параллелограмм и предусмотренным средством управления. В результате чего высота лезвие может быть изменена без нарушения параметров. И наоборот наконечник может регулироваться без изменения высоты. Обе настройки быстро осуществляются с драйверами станции и без операции первичных управлений положением лезвия.
Настоящее изобретение относится к оборудованию для земляных работ а более конкретно легко контролируемым быстродействующим действиям и более точным механизмам регулировки земляных работ лезвием грейдера.
Цель настоящего изобретения – обеспечение более точного и полного управления положением лезвия автогрейдера.
Задачами настоящего изобретения являются:
- упрощение работы грейдера;
- обеспечение изменения наклона механизма для подъема и опускания лезвия грейдера;
- обеспечение быстрого контроля по глубине среза лезвия автогрейдера с помощью одного средства управления;
- обеспечение сохранения лезвия в фиксированном положении для подъема или опускания лезвия грейдера;
- обеспечение увеличения клиренса лезвия грейдера не нарушая других его параметров.
Изобретение вместе с дополнительными задачами и преимуществами будут лучше понятны со ссылкой на последующие описания в совокупности с прилагаемыми чертежами из которых:
Фиг.1 представляет собой вид сбоку грейдер согласно изобретению;
Фиг.2 представляет собой вид в перспективе передней части грейдера по фиг.1 показывающий его лезвие в наклонном положении и части структуры лезвие монтажной нарушенной вне.
Обратимся теперь к рисунку - на нём автогрейдер 11 как правило имеет двигатель 12 и операторов станции 13 езды на задних колесах 14 и арочные основы элементов рамы 16 проходящую вперед к поддержанию 17 с передними колесами 18 такие действия. Лезвие отвала для земляных работ 19 рисуется для тяговой структуры 21 имеющей передний конец прикрепленный к валику 17 посредством шарнира 22 который обеспечивает его поворот и поворот дышла и присоединенных элементов на теле грейдера 11.
Лезвие 19 прикреплено к лопасти круга 26 поддержки и управления узлом 32 который будет подробно описан ниже. Он в свою очередь прикреплен к лопасти окружности отключаемых средств таких как болты 33. Поворот лопасти 19 по отношению к направлению движения грейдера 11 имеет тенденцию быть в пределах ограниченного диапазона настройки для большинства операций.
Рисунок 1.2 – Схема механизма стабилизации
Смысл в том чтобы сконцентрировать износ лезвий окружности зубьев 28 в ограниченном сегменте с лезвиями круга. Тем не менее в настоящем строительстве лезвие круга 26 может быть периодически замкнуто от опорного узла лезвий 32 и поворачивается относительно него. Посредством этого расположение зубов 28 может быть равномерно распределено по кругу 26 и это значительно продлевает срок службы механизма обеспечивающего большую жесткость и упрощает техническое обслуживание.
Грейдер 11 использует настоящее изобретение как правило с обычным набором регулировки лезвия и управляет дополнением к более быстрому и точному управлению представленного изобретения. Обратимся снова к фиг.1: типичные стандартные элементы управления включают в себя пару подъемников 34 простирающихся вдоль каждой стороны основного элемента рамы 16 и имеющих связь 36 подключения к соответствующей стороне поперечины тяги 24 через шаровой шарнир 37. По работе на подъем 34 дышла 21 и таким образом лезвие 19 может быть выглублено или заглублено. При дифференциальной эксплуатации лифтов 34 наклон лопатки 19 со ссылкой на поперечную горизонтальную ось проходящую через грейдер может быть избирательно изменено. Как выше уже отмечалось изменение в любой из этих регулировок может мешать другим требующим дальнейших перенастроек в восстановлении лезвия 19 на предпочтительную установку. Кроме того в не зависимости от проблем управления передаточные числа обычно используемые в лифтах 34 исключает очень быстрые изменения в установки лопасти.
Для поворота дышла 21 и таким образом лезвия 19 в боковом направлении стандартный механизм бокового смещения 35 смонтирован на раме 16 и соединен через связи 40 чтобы пересечь элемент 24 дышла на шаровой шарнир 38. Связь 39 проходит от станции оператора 13 к описанным выше механизмом для вращения лезвия 26 относительно дышла.
Авторское свидетельство № 817157
Изобретение относится к строительно-дорожным машинам а именно к землеройным машинам типа бульдозеров.
Известно рабочее оборудование землеройной машины включающее отвал в виде подпружиненной гибкой ленты опирающийся на решетчато-балочную конструкцию режущий нож и гидроцилиндры управления.
Наиболее близким по технической сущности и достигаемому результату к предлагаемому является рабочее оборудование землеройной машины включающее отвал с изменяемым профилем толкающие брусья гидроцилиндры управления и подкосы.
Недостатком устройства является малая эффективность работы в связи с отсутствием регулировки угла наклона отвала.
Цель изобретения - повышение эффективности разработки грунта путем обеспечения регулирования угла наклона отвала.
Указанная цель достигается тем что толкающие брусья снабжены серьгами с гидроцилиндрами поворота а гидроцилиндры изменения профиля отвала соединены с серьгами.
Причем отвал выполнен из упругого листа.
На фиг. 1 изображено рабочее оборудование вид сбоку; на фиг. 2 - то же вид в плане.
Рабочее оборудование землеройной машины включает отвал 1 выполненный из гибкого упругого листа например из полиуретана на тыльной стороне которого жестко закреплены горизонтальные секции 2 одна из которых шарнирно установлена на толкающих брусьях 3.
В нижней части отвала 1 закреплен режущий нож 4. На толкающих
брусьях шарнирно установлены серьги 5 с возможностью поворота посредством гидроцилиндров 6 шарнирно установленных на толкающих брусьях 3. Регулируемый поворот секций 2 обеспечивается гидроцилиндрами 7 установленными на серьгах 5.
Рисунок 1.3 – Схема отвала с изменяемым профилем
Рабочее оборудование землеройной машины работает следующим образом.
Отвал 1 опускается на грунт. Режущий нож 4 устанавливается под необходимым углом резания. Стружка грунта отделяемая режущим ножом от массива поднимается по отвальной поверхности. При этом секции 2 поворачиваются гидроцилиндрами 7 изменяя кривизну отвальной поверхности в поперечном сечении. Одновременно с этим серьги 5 поворачиваются посредством гидроцилиндров 6. При повороте серег 5 изменяется и угол наклона отвала 1 поскольку последний связан с серьгами. 5 посредством гидроцилиндров 7.
Введение в конструкцию регулирования угла наклона отвала позволяет уменьшить сопротивление продвижению грунта по отвалу и уменьшить энергоемкость копания грунта что приводит к повышению эффективности разработки грунта.
Патент США № 2604708
Настоящее изобретение делает возможным контроль над передним углом лезвия перед процессом копания и т.п. без ограничения вызванного неподвижными центрами для управления связью. В настоящем изобретении связанные четырехугольники предназначены для поддержки лезвия от источника носителем таким как трактор таким же образом как описано в исходной заявке. Эти кулачковые дорожки могут иметь любую желаемую конфигурацию для того чтобы сместить изменение угла лезвия автогрейдера при перемещении лезвия.
В этой конструкции следовательно любое желаемое передний угол лезвия могут поддерживаться или разнообразны как лезвие поднимается и опускается. В показанном варианте изобретения лезвие проходит по вертикали всего ее нормального диапазона отмеченного выше и ниже уровня земли а затем наклоняется вперед выше диапазона очищающего.
Задачей настоящего изобретения является:
- улучшение сцепления для сборки исходной заявки с серийным номером 523464. При этом передний угол реализовывается при поддержке сборки сцепления;
- создание рабочего оборудования которое поддерживает его передний угол который может быть выбран при любом положении лопасти в процессе его диапазона перемещения;
- создание связи которая управляет передним углом бульдозера лопасти по желанию и без каких-либо ограничений;
- обеспечение бульдозера скребковым узлом в котором передний угол от бульдозерного лезвия или лезвия скребка контролируется кулачком;
Другие и дополнительные цели изобретения будут очевидны специалистам в данной области техники из следующего подробного описания прилагаемых чертежей которые в качестве предпочтительного примера иллюстрируют один вариант изобретения.
Корпус заднего моста I4 поддерживает трак I5 и средство передачи (не показан) внутри корпуса моста приводится в движение двигателем для привода звездочки на вал I6. Направляющие ролики 2l на гусеничных рамах взаимодействуют с нижними прогонами треков 20.
Рисунок 1.4 – Схема конструкции контроля переднего угла
Пластины 24 и 25 могут быть закреплены на наружных поверхностях балки с помощью заклепок сварки и тому подобное.
Поперечные трубы 26 и 27 охватывают верхние концы пластин 24 и 25 расположенных параллельно. Эти поперечные трубки закреплены на пластинах. Пара консольных плит 23 приварены передней поверхностью трубок 26 и 27 в центральных частях.
Гидравлический домкрат (узел 29) для подъема и опускания отвала включает в себя гидроцилиндр 30 расположенный между кронштейнами 28 и имеющих цапфы 3I выступающих вбок от нее промежуточной оси их концов и шарниров 32 на кронштейнах 28.
Авторское свидетельство № 1315569
Цель изобретения – повышение эффективности путём стабилизации глубины резания при изменении угла резания отвала в процессе работы.
Изобретение относится к землеройно – транспортным машинам и повышает эффективность путём стабилизации глубины резания при изменении угла резания отвала в процессе работы. Оборудование
Рисунок 1.5 – Рабочий орган. Авторское свидетельство № 1315569
автогрейдера включает поворотный круг 1 с кронштейном 2 отвал 3 и гидроцилиндр (ГЦ) 5 изменения угла резания. Отвал 3 нижней частью посредством двуплечего рычага 9 шарнирно соединён со свободным концом кронштейна 2. С корпусом ГЦ 5 шарнирами 12 и 13 соединена тяга 11 управления. Шток ГЦ 5 шарнирно соединён с тягой 11. Отвал 3 поворачивается в шарнире 8 по часовой стрелке увеличивая угол резания и глубину. Корпус ГЦ 5 поворачивается в шарнире 6 по часовой стрелке перемещая через шарнир 13 тягу 11 вниз. Рычаг 9 поворачивается в шарнире 10 против часовой стрелки а отвал 3 перемещается вверх уменьшая глубину резания. 2 з.п ф – лы 2 ил.
Изобретение относится к землеройно – транспортным машинам в частности к управлению рабочими органами автогрейдеров предназначенных для использования главным образом в дорожном строительстве.
Механизм изменения угла резания отвала автогрейдера содержит поворотный круг 1 с кронштейном 2 отвал 3 соединённый в верхней части шарниром 4 со штоком гидроцилиндра 5 корпус которого в шарнире 6 соединён с неподвижным кронштейном 7 поворотного круга 1. Гидроцилиндр 5 может быть установлен в середине отвала 3 или в количестве двух штук по его краям. В нижней части отвал 3 соединён в шарнире 8 с двуплечим рычагом 9 который в шарнире 10 соединён со свободным концом кронштейна 2 поворотного круга 1. Привод двуплечего рычага 9 осуществляется от корпуса гидроцилиндра 5 тягой 11 управления соединённой с ними в шарнирах 12 и 13.
Предлагаемый механизм является шестизвенным с одной степенью свободы (ведущее звено – шток с поршнем гидроцилиндра 5 ведомое звено – отвал 3 неподвижное звено – поворотный круг 1 с кронштейнами 2 и 7).
3.Кинемат.Расчёт.doc
Для того чтобы обеспечить бесперебойную работу машины необходимо иметь достаточные скорости управления различными рабочими органами автогрейдера. Так например при перегрузке двигателя когда есть опасность его остановки нужно быстро разгрузить отвал путем подъема его из грунта. Быстрое управление отвалом бывает также необходимым при планировочных работах когда требуется менять его установку в соответствии с рельефом местности.
Механизм подъема отвала рассчитывается исходя из таких предпосылок. Рабочий ход механизма подъема должен обеспечивать заданную глубину копания возможность полного выглубления отвала и удовлетворять условиям проходимости автогрейдера в транспортном положении. При расчете механизма подъема в соответствии с рисунком 3 определяют подъемное усилие необходимое для выполнения этой операции мощность.
Подъемное усилие рассчитывается при выглублении отвала опущенного в грунт одним концом. Предполагается что угол захвата равен и на отвал действуют силы и .
Рисунок 3 - Расчетная схема для определения усилия подъема рамы автогрейдера
Тогда согласно схеме этого рисунка
где сила тяжести тяговой рамы с отвалом; здесь можно принять
Считается что в этом случае автогрейдер реализует полное усилие тяги по сцеплению. Тогда
коэффициент для колесной формулы .
коэффициент сцепления для растительного покрова
Мощность привода механизма находится по формуле:
- скорость подъема отвала принимается равной 009 018 мс;
Поворот отвала в горизонтальной плоскости осуществляется зубчатым редуктором или гидравлическим приводом. Последний может быть выполнен в виде гидродвигателя. В связи с тем что поворот отвала производится лишь при полном его выглублении из грунта затрачиваемая на это мощность незначительна поэтому может не рассчитываться.
Определение сил действующих на автогрейдер.doc
На рисунке 5.4.1 представлена схема сил действующих в процессе резания грунта. Автогрейдер устроен с применением самой распространенной колесной формулы: . Действующие на автогрейдер силы можно разделить на активные и реактивные.
Рисунок 5.4.1 – Силы действующие на автогрейдер
К активным силам относятся сила тяжести и окружная сила на ведущих колесах ; к реактивным - вертикальные реакции на колесах и силы сопротивления грунта перекатыванию колес и реакция грунта действующая на отвал которая может быть разложена на горизонтальную и вертикальную составляющие а также боковые реакции направленные вдоль осей автогрейдера и . Последние образуются за счет сил сцепления развивающихся на поверхностях контактов колес с грунтом.
Здесь допускается что реакция грунта направлена перпендикулярно отвалу а реакции и на правых и левых колесах равны и направлены по их вертикальным осям. Кроме того допускается что реакции на всех ведущих колесах одинаковы. Известными являются силы и а неизвестными - ; ; ; ; ; ; и . Определить эти неизвестные силы можно по уравнениям равновесия:
при этом должны быть учтены следующие соотношения между силами:
Выражаем из 4-го уравнения :
Выразим из 1-го уравнения :
Подставив найденные значения и в 3-е уравнение найдем :
Подставим и найдем и :
Сила будет находится из 5-го уравнения:
Сила будет находится из 2-го уравнения:
Сила стремиться повернуть машину вокруг центра тяжести. Такому повороту препятствуют силы сцепления и поэтому должна быть проверена устойчивость машины в горизонтальной плоскости во время работы. При таком расчете следует принять максимальное значение которое может быть определено из следующего уравнения:
Устойчивость машины определится неравенством
Здесь горизонтальные силы и должны быть определены по условиям сцепления:
Условие выполняется.
Определение нагрузок.doc
7.1 Расчетный случай I.
На раму автогрейдера действует максимальные нагрузки возникающие в условиях нормальной эксплуатации в соответствии с рисунком 5.7.1. Такие условия имеют место в конце зарезания когда передний мост вывешен и упирается в край кювета; задние колеса буксуют на месте отвал установлен под углом 45о и режет одним краем а автогрейдер наклонен под некоторым углом к горизонту
Рисунок 5.7.1 - Схема сил действующих в I случае
Силы и реакции действующие на автогрейдер сосредоточены в следующих точках.
Точка О – конец режущей кромки ножа отвала. Действуют горизонтальное усилие RX боковое RY и вертикальное RZ.
Точки О1 О2 – проекции середин балансиров на опорную поверхность. Действующие реакции и силы: вертикальные реакции Z1 и Z2 силы тяги X1 и X2 боковые реакции Y1 и Y2.
Точка О3 – касание переднего колеса края кювета соответствующее нижнему концу вертикального диаметра передних колес. Действует боковая реакция Y3 .
Вес сосредоточен в центре тяжести автогрейдера определяемом координатами Н и l2 .
Высота расположения центра тяжести
где rc – статический радиус колес.
где В– база автогрейдера.
Силы инерции действуют на машину в процессе торможения. Равнодействующая этих сил Рj приложена в центр тяжести и состовляет
где – коэффициент динамичности ;
– коэффициент использования сцепного веса;
– вес автогрейдера приходящийся на задний мост
Силы и реакции находятся из соотношений:
Определяем усилия в переднем шаровом шарнире приложенные в точке О4:
Рисунок 5.7.2 - Схема сил действующих на передний шаровой шарнир
7.2 Расчетный случай II.
Этот случай соответствует действию нагрузок возникающих при встрече автогрейдера с труднопреодолимым препятствиями. На величину нагрузок основное влияние оказывает масса машины и препятствия и скорость в момент столкновения. Наибольшее значение динамические нагрузки достигают в режиме планировки или перемещения грунта в связи с высокой скоростью выполнения указанных работ составляющей 5 7 кмч при малом буксовании ведущих колес. Ось поворотного круга лежит в плоскости продольной симметрии автогрейдера отвал выдвинут в сторону. Этот случай соответствует рисунку 5.7.3.
Рисунок 5.7.3 - Схема сил действующих во II случая
В точке О (точка контакта с препятствием) действуют силы и . В центре тяжести машины действуют вес и дополнительное динамическое усилие .
Дополнительная динамическая нагрузка
где m – масса автогрейдера;
v – скорость автогрейдера в момент встречи с препятствием;
c – суммарная жесткость 6 20 кНсм.
Силы и реакции находятся из следующих соотношений:
Определяем усилия в переднем шаровом шарнире для II случая:
Определение основных параметров автогрейдера.doc
К основным параметрам и размерам автогрейдера относятся: масса длина и высота отвала боковой вынос отвала дорожный просвет и заглубление отвала угол резания ножа углы захвата наклона отвала калёсная база колея передних и задних колёс колёсная формула.
Определим оптимальную силу тяжести автогрейдера по заданным площади поперечного сечения кювета автодороги и необходимому для создания земляного полотна числу проходов:
где m – коэффициент учитывающий неравномерность сечений стружки при последовательных проходах m = 135
S –площадь сечения треугольного кювета S = 225hk2 = 2.25 . 0.62 = 0.81м2
k – удельное сопротивление грунта резанию k = 130 кПа
– коэффициент учитывающий колёсную формулу автогрейдера
= 075 при формуле 1х2х3
φсц – коэффициент сцепления при буксовании колёс φсц = 075
n – число проходов при устройстве земляного полотна в нулевых
отметках для грунтов II категории n = 4
Сила тяжести автогрейдера приходящаяся на его задний мост:
где G = 1053кН – вес автогрейдера
Сила тяжести автогрейдера приходящаяся на его передний мост:
Сцепной вес автогрейдера (вес приходящийся на ведущие колёса):
где 1 – коэффициент определяемый колёсной схемой автогрейдера дл схемы 1х2х3 1 = 07 075
Необходимая при рабочем режиме мощность двигателя:
где Nпол – полезная мощность кВт:
где Vф =4 кмч – фактическая скорость перемещения машины
Nдв – мощность затрачиваемая на перекатывание:
Nбукс – мощность затрачиваемая на пробуксовку:
k1 = 1 - коэффициент учитывающий уменьшение мощности двигателя в
условиях неустановившейся нагрузки.
= 076 – КПД трансмиссии для гидромеханической трансмиссии
Мощность двигателя определяемая для транспортного режима:
где f = 004 – коэффициент сопротивления качению
Vmax – максимальная скорость движения автогрейдера
Из найденных двух значений мощности выбираем максимальную и используем её в расчётах. Найденная максимальная мощность совпадает с номинальной рассчитываемого автогрейдера.
где mа – масса автогрейдера mа = Gg = 1053981 = 107 т
Радиус кривой отвала:
В поперечном сечении профиль отвала обычно очерчивается по дуге окружности (рис.1). При таком профиле стружка вырезаемого грунта перемещаясь по отвалу вверх поворачивается на нём в направлении его движения и дойдя до верхней кромки отвала рассыпается или опрокидывается перед ним образуя призму грунта.
Рис.1 Поперечный профиль отвала
Чтобы исключить пересыпание грунта за отвал угол опрокидывания принимают равным 65 70°. При установки углов должно быть обеспечено равенство
т.е. = – – = 180° - 50° - 65° = 65°
База автогрейдера выбирается из условия возможности разворота отвала (рис.2).
рис.2 Ходовое устройство автогрейдера
где L – база трёхосного автогрейдера
L1 – база двухосного автогрейдера:
Lотв = 372м – длина отвала
b= 20м – колея автогрейдера
Δ = 0055м – минимальный зазор между отвалом и колесом
D = 12м – внешний диаметр шины
Δ’ = 06м – минимальный зазор между задними колёсами
Размеры b и Lотв и связанного с ними радиуса поворота R автогрейдера (рис.2) выбираю такими чтобы машина имела наименьшие размеры. Однако наличие наименьших величин обуславливается следующим. Устойчивость движения автогрейдера при вырезании стружки с наибольшей шириной захвата обеспечивается если колёса автогрейдера идут по краям забоя.
3. Производительность.doc
Расчёт производительности и продолжительности цикла
Производительность является важнейшей выходной характеристикой машины. Ее определяют количеством продукции произведенной машиной в единицу времени.
Производительность автогрейдеров зависит от объема одновременно перемещаемого грунта скорости перемещения расстояния на которое перемещают грунт длины захватки надежности работы машины и квалификации машиниста.
Таблица 4.1 Расстояние перемещения грунта в поперечном направлении при разных углах захвата м
Длина рабочего органа м
Отвал с одним стандартным удлинителем
То же с двумя удлинителями
Различают расчетную (теоретическая или конструктивная) техническую и эксплуатационную производительность. Под расчетной (теоретической конструктивной) производительностью понимают производительность за 1 ч непрерывной работы при расчетных скоростях рабочих движений расчетных нагрузках на рабочем органе и расчетных условиях работы. Теоретическую производительность рассчитывают на стадии разработки конструкторской документации на машину используя для этого нормативные значения расчетных параметров и расчетных условий. Под технической производительностью понимают максимально возможную в данных производственных условиях производительность при непрерывной работе машины. Под эксплуатационной производительностью понимают фактическую производительность машины в данных производственных условиях с учетом ее простоев и неполного использования ее технологических возможностей.
Производительность определяем по формуле (м3ч):
где B- длина отвала м (принимается по паспорту);
h - высота отвала м (принимается по паспорту);
- угол естественного откоса (принимается с коэффициентом 084 по табл. 4.5);
kp – коэффициент разрыхления грунта т.е. отношение объема разрыхленного грунта к объему грунта такой же массы в естественно плотном состоянии ( kp =112 табл. 4.2).
tц – продолжительность цикла мин.
Таблица 4.2 Средние значения коэффициента разрыхления kp
Категория породы по трудности разработки
Разновидность горной породы
Песок супесок растительный грунт торф
Легкий и лессовидный суглинок влажный рыхлый лёсс мягкий солончак гравий мелкий и средний песок супесок и растительный грунт смешанные со щебнем и галькой насыпной слежавшийся грунт с примесью щебня или гальки
Жирная мягкая глина тяжелый суглинок гравий крупный галька мелкая щебень крупностью 15 40 мм суглинок со щебнем пли галькой
Продолжительность цикла (мин):
tц = t1 + t2 + t3+ t4 + t5 + t6 (4.3)
где t1 - время на разработку грунта отвалом мин;
- скорость автогрейдера при разработке грунта (на первой передаче - принимается по табл. 4.4);
t2 - время холостого ходамин;
- скорость холостого хода автогрейдера (на второй передаче - принимается по по табл. 4.4);
t3 и t4 - время на подъем отвала в транспортное положение и на опускание отвала; t3 = t4 = 0033 мин;
t 5 - время на переключение передач; t 5 = 0033 мин;
t 6 - время на поворот в конце рабочего хода и в конце обратного хода; t 6 = 0165 мин.
tц = + + 0033 + 0033 + 0033 + 0166 =04 мин.
Производительность будет равна:
Таблица 4.3 Коэффициент призмы kпр
Значение kпр при отношении HB
Таблица 4.4 Параметры автогрейдера ДЗ-143
Скорости движения мс
Таблица 4.5 Значения углов естественного откоса и их тангенсов
Наименование грунтов
Чтобы автогрейдер в процессе работы не опрокидывался рекомендуется работать с углом захвата не менее 35 °. Если угол захвата превышает 50° то перед отвалом увеличивается призма волочения которая снижает скорость передвижения грейдера.
Производительность автогрейдера зависит также от угла срезки слоя грунта. С увеличением угла возрастает удельное сопротивление грунта срезке для преодоления которого требуются дополнительные тяговые усилия поэтому рекомендуется по возможности работать с минимальными углами срезки.
3. Мощность силовой установки.doc
Сила тяжести G – главный параметр автогрейдера
где m - коэффициент учитывающий неравномерность в сечении стружки при отдельных проходах автогрейдера m = 125 135;
S - площадь поперечного сечения кювета h - глубина кювета
- удельное сопротивление грунта копанию; если учесть не только резание но и перемещение грунта как перед отвалом так и вдоль него то можно полагать что:
- коэффициент для колесной формулы
- коэффициент сцепления для растительного покрова;
n - число проходов обычно составляет n = 4 6;
G – сила тяжести автогрейдера кН;
Максимальная свободная сила тяги автогрейдера:
Развивающая на ведущих колесах общая мощность:
- мощность расходуемая на вырезание грунта (полезная мощность);
- мощность расходуемая на передвижение автогрейдера как тележки;
- мощность расходуемая на буксование.
где - фактическая рабочая скорость автогрейдера кмч;
Мощность расходуемая на передвижение автогрейдера как тележки:
где - коэффициент сопротивления движению автогрейдера = 007 01;
Мощность расходуемая на буксование:
Мощность двигателя для транспортного режима:
где - коэффициент буксования = 004 0045;
- к.п.д. трансмиссии = 083 086 - для механической;
- заданная максимальная скорость автогрейдера кмч;
Необходимая мощность двигателя:
где N - развивающая на ведущих колесах общая мощность;
- коэффициент снижения мощности двигателя ввиду неустановившейся нагрузки =09;
На автогрейдер устанавливается двигатель Д-260.2 мощностью 956 кВт.
3.Тяговый расчет.doc
В случае землеройно-транспортных машин следует различать два режима работы — тяговый или рабочий и транспортный. Тяговый режим соответствует процессу копания грунта а транспортный — его перевозке. В каждый момент времени внешние сопротивления должны уравновешиваться той окружной силой которая развивается на ходовом устройстве. Уравнение которым обусловливается это равновесие называется тяговым балансом.
Движение машины возможно если максимальное тяговое усилие Тmах (Н) будет не меньше суммарного сопротивления движению W(Н):
Установлено что при = 01 колесный движитель работает с максимальным КПД при = 02 достигается максимальная тяговая мощность при = 03 развивается наибольшая устойчивая сила тяги.
Усилие Тmах ограничено двумя факторами - мощностью привода ходового устройства и условиями сцепления движителя с опорным основанием с которыми оно связано зависимостями:
Тmах(Рх) = 1000 Рх х v; (2.1)
где Рх - суммарная мощность двигателей механизма передвижения
х - общий КПД механизма передвижения (табл. 2.3);
φ - коэффициент сцепления движителя с основанием (табл. 2.1);
v - скорость передвижения (мс).
Таблица 2.1 Коэффициенты f и φ
Шинноколесный движитель
рыхлый свежеотсыпанный
слежавшийся уплотненный
Таблица 2.2 Категории грунта
Таблица 2.3 Величины необходимые для расчета
Таблица 2.4 Основные параметры и характеристики двигателя Д-260.2
Наименование параметров
Четырехтактный дизель с турбонаддувом
Способ смесеобразования
Непосредственный впрыск топлива
Расположение цилиндров
Рабочий объем цилиндров
Порядок работы цилиндров
Направление вращения коленчатого вала (со стороны вентилятора)
Степень сжатия (расчетная)
Допустимые углы наклона при работе: продольный поперечный
Мощность номинальная
Мощность эксплуатационная
Номинальная частота вращения
Мин. устойчивая частота вр-я хол. хода
Максимальная частота вращения холостого хода ограничиваемая регулятором
Частота вращения при максимальном значении крутящего момента
Максимальный крутящий момент
Удельный расход топлива при номинальной мощности
Удельный расход топлива при эксплуатационной мощности
Давление масла в главной магистрали при:номинальной частоте вращения минимальной частоте вращения
не заправленного горючесмазочными материалами и охлаждающей жидкостью
Для шинноколесных движителей - теоретическая скорость (мс):
где rc - силовой радиус м;
пд - номинальная частота вращения вала двигателя ходового механизма (обмин);
и - передаточное число трансмиссии.
Силовой радиус определяется как радиус недеформированного колеса rо за вычетом наибольшей радиальной деформации шины (в центральной зоне контактной поверхности) λ (м):
Приближенно при движении по плотному грунту λ = (012 015) В; по рыхлому грунту - λ = (008 01) В (В - ширина профиля шины).
Фактическую скорость передвижения шинноколесной машины определяют с учетом буксования по формуле (мс):
где - коэффициент буксования.
Совместив необходимые формулы рассчитываем vф:
Полученное значение соответствует I передаче автогрейдера (табл. 2.4).
Имея необходимые показатели рассчитываем усилие (Тmах(Рх)) мощности привода ходового устройства и усилие (Тmах(φ)) сцепления движителя с опорным основанием:
Для дальнейших расчетов берем меньшее из полученных значений.
Сопротивление передвижению W (Н) складывается из сопротивлений на рабочем органе машины Wp (Н) передвижению (перекатыванию) движителей Wпep (H) по горизонтальному пути повороту машины Wnoв (H) движению на уклоне местности Wу (Н) инерции при разгоне и торможении Wи (H) и ветрового давления WB (H):
W = Wp + Wпep + Wnoв ± Wу ± Wи + WB . (2.5)
Из этого набора сопротивлений удерживаются только те сопротивления которые имеют место в конкретном транспортном режиме работы машины.
Сопротивление повороту колесных машин (рыхлый грунт):
Wnoв = (025 . . . 05) Wпep . (2.6)
Сопротивление движению от уклона местности :
Wу = ± тg sinα (2.7)
где т - масса машины кг;
g - ускорение свободного падения g = 981 мс2;
α - угол подъема пути машины (+) на подъем (-) под уклон.
Сопротивление сил инерции при разгоне и торможении:
Wи = ± m v tр(т) (2.8)
где v - скорость в конце разгона или начале торможения (мс):
tр(т) - продолжительность разгона (торможения) (с).
Сопротивление ветрового давления:
где S - площадь воспринимающая давление ветра (м2);
qB =125 – 500 - распределенная ветровая нагрузка на 1 м2 (Па).
Сопротивления Wnoв Wу WB и Wи в данном тяговом расчете не учитываются так как по условию участок горизонтальный автогрейдер движется с равномерной скоростью а разворот совершается после выполнения операций (резание транспортировании укладке) а сопротивление ветрового давления незначительно при данной скорости.
Сопротивление резанью:
где k – коэффициент сопротивления резанью (табл. 2.2);
В – ширина отвала (м);
h1 – глубина резания во время перемещения призмы грунта (м2).
где kn – коэффициент потерь грунта при перемещении (табл. 2.2)
Vпр – объем призмы волочения(м3).
Вычисляем объем призмы волочения:
Вычисляем глубину резания во время перемещения призмы грунта:
Вычислив необходимые величины находим сопротивление резанью:
Сопротивление перекатыванию:
где f- коэффициент сопротивления передвижению движителей
G - вертикальная составляющая внешней нагрузки на движители (Н)
Подставив значения необходимых усилий находим сопротивление перемещению W (H):
W = Wp + Wпep = 366+20300 = 207 кН. .
Проверяем соответствие условию Тmах ≥ W:
Тmах =675 ≥ W = 207 = 207 кН.
Условие соблюдено тяговые характеристики автогрейдера подходят для работы в заданных условиях. Неудовлетворение указанному выше условию по тяговому усилию Тmах(Рх) означает недостаток мощности для движения машины с заданной скоростью v. Если то же условие не удовлетворяется по усилию Тmах(φ) то это означает что машина не может двигаться из-за буксования движителей.
3. Общие расчеты.doc
Сила тяжести G – главный параметр автогрейдера
где m - коэффициент учитывающий неравномерность в сечении стружки при отдельных проходах автогрейдера m = 125 135;
S - площадь поперечного сечения кювета h - глубина кювета
- удельное сопротивление грунта копанию; если учесть не только резание но и перемещение грунта как перед отвалом так и вдоль него то можно полагать что:
- коэффициент для колесной формулы
- коэффициент сцепления для растительного покрова;
n - число проходов обычно составляет n = 4 6;
G – сила тяжести автогрейдера кН;
Максимальная свободная сила тяги автогрейдера:
Развивающая на ведущих колесах общая мощность:
- мощность расходуемая на вырезание грунта (полезная мощность);
- мощность расходуемая на передвижение автогрейдера как тележки;
- мощность расходуемая на буксование.
где - фактическая рабочая скорость автогрейдера кмч;
Мощность расходуемая на передвижение автогрейдера как тележки:
где - коэффициент сопротивления движению автогрейдера = 007 01;
Мощность расходуемая на буксование:
Мощность двигателя для транспортного режима:
где - коэффициент буксования = 004 0045;
- к.п.д. трансмиссии = 083 086 - для механической;
- заданная максимальная скорость автогрейдера кмч;
Необходимая мощность двигателя:
где N - развивающая на ведущих колесах общая мощность;
- коэффициент снижения мощности двигателя ввиду неустановившейся нагрузки =09;
На автогрейдер устанавливается двигатель Д-260.2 мощностью 956 кВт.
2 Расчет производительности
Расчёт производительности и продолжительности цикла
Производительность является важнейшей выходной характеристикой машины. Ее определяют количеством продукции произведенной машиной в единицу времени.
Производительность автогрейдеров зависит от объема одновременно перемещаемого грунта скорости перемещения расстояния на которое перемещают грунт длины захватки надежности работы машины и квалификации машиниста.
Таблица 3.1 Расстояние перемещения грунта в поперечном направлении при разных углах захвата м
Длина рабочего органа м
Отвал с одним стандартным удлинителем
То же с двумя удлинителями
Различают расчетную (теоретическая или конструктивная) техническую и эксплуатационную производительность. Под расчетной (теоретической конструктивной) производительностью понимают производительность за 1 ч непрерывной работы при расчетных скоростях рабочих движений расчетных нагрузках на рабочем органе и расчетных условиях работы. Теоретическую производительность рассчитывают на стадии разработки конструкторской документации на машину используя для этого нормативные значения расчетных параметров и расчетных условий. Под технической производительностью понимают максимально возможную в данных производственных условиях производительность при непрерывной работе машины. Под эксплуатационной производительностью понимают фактическую производительность машины в данных производственных условиях с учетом ее простоев и неполного использования ее технологических возможностей.
Производительность определяем по формуле (м3ч):
где B- длина отвала м (принимается по паспорту);
h - высота отвала м (принимается по паспорту);
- угол естественного откоса (принимается с коэффициентом 084 по табл. 4.5);
kp – коэффициент разрыхления грунта т.е. отношение объема разрыхленного грунта к объему грунта такой же массы в естественно плотном состоянии ( kp =112 табл. 4.2).
tц – продолжительность цикла мин.
Таблица 3.2 Средние значения коэффициента разрыхления kp
Категория породы по трудности разработки
Разновидность горной породы
Песок супесок растительный грунт торф
Легкий и лессовидный суглинок влажный рыхлый лёсс мягкий солончак гравий мелкий и средний песок супесок и растительный грунт смешанные со щебнем и галькой насыпной слежавшийся грунт с примесью щебня или гальки
Жирная мягкая глина тяжелый суглинок гравий крупный галька мелкая щебень крупностью 15 40 мм суглинок со щебнем пли галькой
Продолжительность цикла (мин):
tц = t1 + t2 + t3+ t4 + t5 + t6 (3.11)
где t1 - время на разработку грунта отвалом мин;
- скорость автогрейдера при разработке грунта (на первой передаче - принимается по табл. 4.4);
t2 - время холостого ходамин;
- скорость холостого хода автогрейдера (на второй передаче - принимается по по табл. 4.4);
t3 и t4 - время на подъем отвала в транспортное положение и на опускание отвала; t3 = t4 = 0033 мин;
t 5 - время на переключение передач; t 5 = 0033 мин;
t 6 - время на поворот в конце рабочего хода и в конце обратного хода; t 6 = 0165 мин.
tц = + + 0033 + 0033 + 0033 + 0166 =04 мин.
Таблица 3.3 Средние значения коэффициента разрыхления kp
Производительность будет равна:
Таблица 3.4 Коэффициент призмы kпр
Значение kпр при отношении HB
Таблица 3.5 Параметры автогрейдера ДЗ-143
Скорости движения мс
Таблица 3.6 Значения углов естественного откоса и их тангенсов
Наименование грунтов
Чтобы автогрейдер в процессе работы не опрокидывался рекомендуется работать с углом захвата не менее 35 °. Если угол захвата превышает 50° то перед отвалом увеличивается призма волочения которая снижает скорость передвижения грейдера.
Производительность автогрейдера зависит также от угла срезки слоя грунта. С увеличением угла возрастает удельное сопротивление грунта срезке для преодоления которого требуются дополнительные тяговые усилия поэтому рекомендуется по возможности работать с минимальными углами срезки.
В случае землеройно-транспортных машин следует различать два режима работы — тяговый или рабочий и транспортный. Тяговый режим соответствует процессу копания грунта а транспортный — его перевозке. В каждый момент времени внешние сопротивления должны уравновешиваться той окружной силой которая развивается на ходовом устройстве. Уравнение которым обусловливается это равновесие называется тяговым балансом.
Движение машины возможно если максимальное тяговое усилие Тmах (Н) будет не меньше суммарного сопротивления движению W(Н):
Установлено что при = 01 колесный движитель работает с максимальным КПД при = 02 достигается максимальная тяговая мощность при = 03 развивается наибольшая устойчивая сила тяги.
Усилие Тmах ограничено двумя факторами - мощностью привода ходового устройства и условиями сцепления движителя с опорным основанием с которыми оно связано зависимостями:
Тmах(Рх) = 1000 Рх х v; (3.14)
Тmах(φ) = G φ (3.15)
где Рх - суммарная мощность двигателей механизма передвижения
х - общий КПД механизма передвижения (табл. 2.3);
φ - коэффициент сцепления движителя с основанием (табл. 2.1);
v - скорость передвижения (мс).
Таблица 3.7 Коэффициенты f и φ
Шинноколесный движитель
рыхлый свежеотсыпанный
слежавшийся уплотненный
Таблица 3.8 Категории грунта
Таблица 3.9 Величины необходимые для расчета
Таблица 3.10 Основные параметры и характеристики двигателя Д-260.2
Наименование параметров
Четырехтактный дизель с турбонаддувом
Способ смесеобразования
Непосредственный впрыск топлива
Расположение цилиндров
Рабочий объем цилиндров
Порядок работы цилиндров
Направление вращения коленчатого вала (со стороны вентилятора)
Степень сжатия (расчетная)
Допустимые углы наклона при работе: продольный поперечный
Мощность номинальная
Мощность эксплуатационная
Номинальная частота вращения
Мин. устойчивая частота вр-я хол. хода
Максимальная частота вращения холостого хода ограничиваемая регулятором
Частота вращения при максимальном значении крутящего момента
Максимальный крутящий момент
Удельный расход топлива при номинальной мощности
Удельный расход топлива при эксплуатационной мощности
Давление масла в главной магистрали при:номинальной частоте вращения минимальной частоте вращения
не заправленного горючесмазочными материалами и охлаждающей жидкостью
Для шинноколесных движителей - теоретическая скорость (мс):
где rc - силовой радиус м;
пд - номинальная частота вращения вала двигателя ходового механизма (обмин);
и - передаточное число трансмиссии.
Силовой радиус определяется как радиус недеформированного колеса rо за вычетом наибольшей радиальной деформации шины (в центральной зоне контактной поверхности) λ (м):
rc = rо – λВ. (3.17)
Приближенно при движении по плотному грунту λ = (012 015) В; по рыхлому грунту - λ = (008 01) В (В - ширина профиля шины).
Фактическую скорость передвижения шинноколесной машины определяют с учетом буксования по формуле (мс):
где - коэффициент буксования.
Совместив необходимые формулы рассчитываем vф:
Полученное значение соответствует I передаче автогрейдера (табл. 2.4).
Имея необходимые показатели рассчитываем усилие (Тmах(Рх)) мощности привода ходового устройства и усилие (Тmах(φ)) сцепления движителя с опорным основанием:
Для дальнейших расчетов берем меньшее из полученных значений.
Сопротивление передвижению W (Н) складывается из сопротивлений на рабочем органе машины Wp (Н) передвижению (перекатыванию) движителей Wпep (H) по горизонтальному пути повороту машины Wnoв (H) движению на уклоне местности Wу (Н) инерции при разгоне и торможении Wи (H) и ветрового давления WB (H):
W = Wp + Wпep + Wnoв ± Wу ± Wи + WB . (3.22)
Из этого набора сопротивлений удерживаются только те сопротивления которые имеют место в конкретном транспортном режиме работы машины.
Сопротивление повороту колесных машин (рыхлый грунт):
Wnoв = (025 . . . 05) Wпep . (3.23)
Сопротивление движению от уклона местности :
Wу = ± тg sinα (3.24)
где т - масса машины кг;
g - ускорение свободного падения g = 981 мс2;
α - угол подъема пути машины (+) на подъем (-) под уклон.
Сопротивление сил инерции при разгоне и торможении:
Wи = ± m v tр(т) (3.25)
где v - скорость в конце разгона или начале торможения (мс):
tр(т) - продолжительность разгона (торможения) (с).
Сопротивление ветрового давления:
где S - площадь воспринимающая давление ветра (м2);
qB =125 – 500 - распределенная ветровая нагрузка на 1 м2 (Па).
Сопротивления Wnoв Wу WB и Wи в данном тяговом расчете не учитываются так как по условию участок горизонтальный автогрейдер движется с равномерной скоростью а разворот совершается после выполнения операций (резание транспортировании укладке) а сопротивление ветрового давления незначительно при данной скорости.
Сопротивление резанью:
где k – коэффициент сопротивления резанью (табл. 2.2);
В – ширина отвала (м);
h1 – глубина резания во время перемещения призмы грунта (м2).
где kn – коэффициент потерь грунта при перемещении (табл. 2.2)
Vпр – объем призмы волочения(м3).
Вычисляем объем призмы волочения:
Вычисляем глубину резания во время перемещения призмы грунта:
Вычислив необходимые величины находим сопротивление резанью:
Сопротивление перекатыванию:
где f- коэффициент сопротивления передвижению движителей
G - вертикальная составляющая внешней нагрузки на движители (Н)
Подставив значения необходимых усилий находим сопротивление перемещению W (H):
W = Wp + Wпep = 366+20300 = 207 кН. .
Проверяем соответствие условию Тmах ≥ W:
Тmах =675 ≥ W = 207 = 207 кН.
Условие соблюдено тяговые характеристики автогрейдера подходят для работы в заданных условиях. Неудовлетворение указанному выше условию по тяговому усилию Тmах(Рх) означает недостаток мощности для движения машины с заданной скоростью v. Если то же условие не удовлетворяется по усилию Тmах(φ) то это означает что машина не может двигаться из-за буксования движителей.
4 Расчёт механизма стабилизации
Для того чтобы обеспечить бесперебойную работу машины необходимо иметь достаточные скорости управления различными рабочими органами автогрейдера. Так например при перегрузке двигателя когда есть опасность его остановки нужно быстро разгрузить отвал путем подъема его из грунта. Быстрое управление отвалом бывает также необходимым при планировочных работах когда требуется менять его установку в соответствии с рельефом местности.
Механизм подъема отвала рассчитывается исходя из таких предпосылок. Рабочий ход механизма подъема должен обеспечивать заданную глубину копания возможность полного выглубления отвала и удовлетворять условиям проходимости автогрейдера в транспортном положении. При расчете механизма подъема в соответствии с рисунком 3 определяют подъемное усилие необходимое для выполнения этой операции мощность.
Подъемное усилие рассчитывается при выглублении отвала опущенного в грунт одним концом. Предполагается что угол захвата равен и на отвал действуют силы и .
Рисунок 3.1 - Расчетная схема для определения усилия подъема
Тогда согласно схеме этого рисунка:
где сила тяжести тяговой рамы с отвалом; здесь можно принять
Считается что в этом случае автогрейдер реализует полное усилие тяги по сцеплению. Тогда:
коэффициент для колесной формулы ;
коэффициент сцепления для растительного покрова;
Мощность привода механизма находится по формуле:
- скорость подъема отвала принимается равной 009 018 мс;
Поворот отвала в горизонтальной плоскости осуществляется зубчатым редуктором или гидравлическим приводом. Последний может быть выполнен в виде гидродвигателя. В связи с тем что поворот отвала производится лишь при полном его выглублении из грунта затрачиваемая на это мощность незначительна поэтому может не рассчитываться.
5 Определение сил действующих на автогрейдер
На рисунке 3.2 представлена схема сил действующих в процессе резания грунта. Автогрейдер устроен с применением самой распространенной колесной формулы: . Действующие на автогрейдер силы можно разделить на активные и реактивные.
Рисунок 3.2 – Силы действующие на автогрейдер
К активным силам относятся сила тяжести G и окружная сила на ведущих колесах ; к реактивным - вертикальные реакции на колесах и силы сопротивления грунта перекатыванию колес и реакция грунта действующая на отвал N которая может быть разложена на горизонтальную и вертикальную составляющие а также боковые реакции направленные вдоль осей автогрейдера и . Последние образуются за счет сил сцепления развивающихся на поверхностях контактов колес с грунтом.
Здесь допускается что реакция грунта N направлена перпендикулярно отвалу а реакции и на правых и левых колесах равны и направлены по их вертикальным осям. Кроме того допускается что реакции на всех ведущих колесах одинаковы. Известными являются силы и G а неизвестными - ;;;;; ; и . Определить эти неизвестные силы можно по уравнениям равновесия:
При этом должны быть учтены следующие соотношения между силами:
Выражаем из 4-го уравнения :
Выразим из 1-го уравнения :
Подставив найденные значения и в 3-е уравнение найдем :
Подставим и найдем и :
Сила будет находится из 5-го уравнения:
Сила будет находится из 2-го уравнения:
Сила стремиться повернуть машину вокруг центра тяжести. Такому повороту препятствуют силы сцепления и поэтому должна быть проверена устойчивость машины в горизонтальной плоскости во время работы. При таком расчете следует принять максимальное значение которое может быть определено из следующего уравнения:
Устойчивость машины определится неравенством
Здесь горизонтальные силы и должны быть определены по условиям сцепления:
Условие выполняется.
на прочность.doc
Создание современного оборудования на этапе проектирования не ограничивается его геометрическим моделированием. Без всестороннего инженерного анализа проектируемого объекта невозможно выпускать конкурентоспособную продукцию. Разработчики во всем мире трудятся над тем чтобы их конструктивные решения обеспечивали статическую прочность и жесткость достаточную долговечность устойчивость и подходящие динамические характеристики имея при этом минимальный вес минимальную стоимость минимальное энергопотребление.
Оптимизация создаваемых конструкций является залогом их конкурентоспособности. Использование инструментов CAE-анализа позволит современным предприятиям создавать продукцию не уступающую лучшим мировым образцам и даже их превосходящую.
Данную проблему может помочь решить система прочностного анализа APM FEM для КОМПАС-3D.
Система APMFEM предназначена для выполнения экспресс-расчетов твердотельных объектов в системе КОМПАС-3D и визуализации результатов этих расчетов.
В состав APMFEM входят инструменты подготовки деталей и сборок к расчёту задания граничных условий и нагрузок а также встроенные генераторы конечно-элементной сетки (как с постоянным так и с переменным шагом) и постпроцессор. Этот функциональный набор позволяет смоделировать твердотельный объект и комплексно проанализировать поведение расчётной модели при различных воздействиях с точки зрения статики собственных частот устойчивости и теплового нагружения.
Процедуры расчета построены на базе метода конечных элементов. Поэтому в расчетных моделях могут быть учтены практически все особенности конструкций и условий их эксплуатации.
2.2 Выбор рассчитываемого узла порядок подготовки модели и выполнения расчета
В качестве рассчитываемого объекта берется механизм стабилизации рабочего оборудования а конкретнее сборка состоящая из трёх деталей: тяга палец двуплечий рычаг.
d визуализация данного механизма представлена на рис.4.1.
Рисунок 4.2 – Механизм стабилизации
Прочностной анализ модуля APMFEM позволяет решать линейные задачи:
-напряженно-деформированного состояния (статический расчет);
-статической прочности сборок;
-стационарной теплопроводности.
Динамический анализ позволяет:
-определять частоты и формы собственных колебаний в том числе для моделей с предварительным нагружением.
Результатами расчетов являются:
-распределение эквивалентных напряжений и их составляющих а также главных напряжений;
-распределение линейных угловых и суммарных перемещений;
-распределение деформаций по элементам модели;
-карты и эпюры распределения внутренних усилий;
-значение коэффициента запаса устойчивости и формы потери устойчивости;
-распределение коэффициентов запаса и числа циклов по критерию усталостной прочности;
-распределение коэффициентов запаса по критериям текучести и прочности;
-распределение температурных полей и термонапряжений;
-координаты центра тяжести вес объем длина площадь поверхности моменты инерции модели а также моменты инерции статические моменты и площади поперечных сечений;
-реакции в опорах конструкции а также суммарные реакции приведенные к центру тяжести модели.
Порядок подготовки модели и выполнения расчета:
Описание рассчитываемых элементов;
Подготовка модели к расчету – задание закреплений и приложение нагрузки;
Задание совпадающих граней (для КЭ-анализа сборки);
Просмотр результатов в виде карт напряжений перемещений.
2.3 Расчет механизма стабилизации
2.3.1. Описание рассчитываемых элементов
Рассмотрим детали из которых состоит наш механизм более подробно:
Для создания конечно-элементного представления объекта в APMFEM предусмотрена функция генерации КЭ-сетки при вызове которой происходит соответствующее разбиение объекта с заданным шагом. Если созданная расчетная модель имеет сложные неравномерные геометрические переходы то может быть проведено так называемое адаптивное разбиение. Для того чтобы результат процесса был более качественным генератор КЭ-сетки автоматически (с учетом заданного пользователем максимального коэффициента сгущения) варьирует величину шага разбиения.
Генерация КЭ-сетки в APM FEM осуществляется в автоматическом режиме с использованием таких параметров как максимальная длина стороны элемента максимальный коэффициент сгущения на поверхности и коэффициент разрежения в объеме.
-стационарной теплопроводности.
-определять частоты и формы собственных колебаний в том числе для моделей с предварительным нагружением.
6. Рабочий орган@.cdw

4.Общий вид@.cdw

рабочим оборудованием
НТТКм 0.01.00.00.000 ВО
Рабочее оборудование
НТТКм 0.01.01.00.000 СБ
5.2 Рабочее оборудование@.cdw

5.1 Рабочее оборудование@.cdw

Рабочее оборудование
НТТКм-0.01.01.00.000 ВО
НТТКм-0.01.01.02.000
НТТКм-0.01.01.03.000
НТТКм-0.01.01.04.000
НТТКм-0.01.01.05.000
НТТКм-0.01.01.06.000
НТТКм-0.01.01.07.000
НТТКм-0.01.01.08.000
НТТКм-0.01.01.09.000
НТТКм-0.01.01.10.000
Гидравлический шарнир
Гидроцилиндр изменения
Редуктор поворота отвала
НТТКм-0.01.01.01.000
НТТКм-0.01.01.12.000
Кронштейн гидроцилиндра
НТТКм-0.01.01.11.000
НТТКм-0.01.01.13.000
7.Тяга.cdw

8. Деталировка.cdw

Неуказанные радиусы 1 мм.
Изм № документа Дата
Отливка 15Л-III ГОСТ 977-75
НТТКм-О.01.01.01.004 СБ
НТТКм-О.01.01.01.027 СБ
НТТКм-О.01.01.01.158 СБ
НТТКм-О.01.01.02.002 СБ
НТТКм-О.01.01.02.004 СБ
НТТКм-О.01.01.02.005 СБ
НТТКм-О.01.01.01.083 СБ
СЧ15-32 ГОСТ 1412-70
Сталь 45 ГОСТ 2050-74
2.Теоретичесские исследования@.frw

изменения угла резания
Схема траекторий подвижных точек
механизма изменения угла резания
отвала автогрейдера.
Конструктивная схема механизма изменения
угла резания отвала автогрейдеров моделей
ДЗ - 143 и ДЗ - 148.
НТТКм-0.01.00.00.000 ТЧ
График зависимости глубины копания от угла резания отвала
7.Сбор чертеж тяга.cdw

*Размер для справок.
НТТКм-0.01.01.02.000 СБ
6.Сбор чертеж отвала ! .frw

НТТКм-0.01.01.01.000 СБ
Допускается удаление прплавов сварных швов механическим путём
заподлицо с основным материалом
врезание в материал при этом
* Размеры для справок.
Обозначение и изображение шва
5. Деталировка.cdw

Неуказанные предельные отклонения размеров
Ст.5 nс 3-I ГОСТ 535-88
Изм № документа Дата
Отливка 15Л-III ГОСТ 977-75
Сталь 45 ГОСТ 1050-88
НСТб - О.05.04.02.002
НСТб - О.05.04.02.013
НСТб - О.05.04.02.015
НСТб - О.05.04.02.006
НСТб - О.05.04.02.008
НСТб - О.05.04.02.004
НСТб - О.05.04.02.003
10.Технология.cdw

(Совмещенный чертёж
детали с заготовкой)
Сталь 45 ГОСТ 1050-88
наименование операции
наименование оборудования
Обозначение документа
Токарно-винторезный станок 1М63
резец проходной Т15К6 ГОСТ 18878-73
резец подрезной Т15К6 ГОСТ 18878-73
Патрон трёхкулачковый ГОСТ 2675-80
Горизонтально-фрезерный станок 6Н804Г
Фрезеровать поверхность
Вертикально-сверлильный станок 2Н118
Контроль детали согласно чертежу
точить поверхность начерно
точить поверхность начисто
рассверлить отверстие
Слесарные тиски с призматическими губками ГОСТ 4045-57
метчик ручной М12 ГОСТ 9522-60
Патрон сверлильный ГОСТ 8522-70
слесарные тиски с призматическими губками ГОСТ 4045-57
Машинные тиски ГОСТ 4045-57
фреза дисковая пазовая
мм ширина 5мм ГОСТ 3964-69
Нарезать резьбу М12 со стороны шляпки на длине 10
12.Экономика.cdw

Технико-экономические
* БТ-базовая техника;
Удельные капитальные
годовой эксплуатационной
Удельные текущие затраты
Экономическая эффективность
Годовой экономический эффект
от применения техники
Суммарный дисконтированный
экономический эффект от
за весь срок эксплуатации
Срок окупаемости затрат на
модернизацию базовой техники
Рентабельность модернизации
Численные показатели:
Капитальные вложения
Годовые текущие затраты
Сравнительная характеристика
Годовая эксплуатационная
Динамика дисконтированного экономического эффекта
за срок службы объекта
Основные удельные показатели
Удельные капитальные вложения
1.Анализ техничесских решений ! .frw

стабилизации глубинырезания при
изменении угла резания отвала
- обеспечивают постоянства глубины
резания при изменении в процессе
разработки грунта первоначального
- простота конструкции;
- дешевизна производства.
- обеспечение регулировки механизма подъёма и опускания ножа отвала через одну манипуляцию
без ущерба для эффективного угла резания.
- утяжеление конструкции;
- усложнение конструкции.
- простота конструкции.
- большие габариты и кинематика движения механизма при установки на автогрейдер.
- уменьшение сопротивления продвижения грунта
по отвалу и уменьшение энергоёмкости копания грунта.
- недостаточная эффективность работы.
техничесских решений
Исследование и проектирование механизма
стабилизации глубины резания отвала автогрейдера
Авторское свидетельство № 1315569 Рабочее оборудование автогрейдера
Патент США № 3444936 Механизм регулировки ножа автогрейдера
Патент США № 2604708 Механизм подъёма и опускания отвала бульдозера
Авторское свидетельство № 817157 Рабочее оборудование землеройной машины
4.Общий вид автогрейдера ! .frw

рабочим оборудованием
НТТКм-0.01.00.00.000 ВО
Техническая характеристика
Боковой вынос грейдерного отвала
в обе стороны относительно тяговой рамы
Кабина одноместная закрытого типа
* Размеры для справок
5.Сбор.чертеж тяговой рамы@ .frw

11.Профилирование.frw

Технологичесская схема профилирования слоёв земляного полотна автогрейдером ДЗ-143
НТТКм-0.01.00.00.000 ТС
Схема изменения глубины копания в зависимости от свойств грунта
9.САПР ! .frw

НТТКм-0.01.00.00.000
Расчет механизма стабилизации в САПР APM FEM
Линейное перемещение
Коэффициент запаса по текучести
Коэффициент запаса по прочности
3.Теоретичесские исследования@.frw

угла резания отвала автогрейдера.
Кинематика механизма
изменения угла резания
Углы резания автогрейдера до модернизации (а) и после модернизации (б)
График зависимости глубины копания от угла резания отвала
НТТКм-0.01.00.00.000 ТЧ
3д.cdw
