Механический цех по производству приводного вала для планетарного редуктора




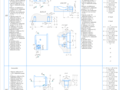
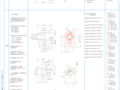
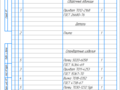
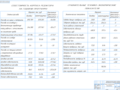
- Добавлен: 24.01.2023
- Размер: 5 MB
- Закачек: 2
Описание
Состав проекта
![]() |
![]() |
![]() ![]() ![]() ![]() |
![]() ![]() ![]() ![]() |
![]() |
![]() ![]() ![]() ![]() |
![]() ![]() ![]() ![]() |
![]() |
![]() |
![]() |
![]() |
![]() |
![]() |
![]() |
![]() ![]() ![]() ![]() |
![]() ![]() ![]() ![]() |
![]() ![]() ![]() ![]() |
![]() ![]() ![]() ![]() |
![]() ![]() ![]() ![]() |
![]() |
![]() ![]() ![]() ![]() |
![]() |
![]() ![]() ![]() ![]() |
![]() ![]() ![]() ![]() |
![]() ![]() ![]() ![]() |
![]() |
![]() ![]() ![]() |
![]() ![]() ![]() |
![]() ![]() ![]() |
![]() ![]() ![]() |
![]() ![]() ![]() |
![]() ![]() ![]() |
![]() ![]() ![]() |
![]() ![]() ![]() |
![]() ![]() ![]() |
![]() ![]() ![]() |
![]() ![]() ![]() |
![]() ![]() ![]() |
![]() ![]() ![]() |
Дополнительная информация
ЦЕХ.cdw

Годовая станкоемкость - 235000
Количество станков -152
Количество работающих - 306
Общая площадь цеха - 4459
Режим работы цеха - 2-хсменный
План цеха мех. обработки
корпуса редуктора очистной
Разработка технологического процесса изготовления
корпуса редуктора очистной установки сиспользованием
САПР технологической и конструкторской документации
Сверлильно-фрезерно-расточный
ЭКСПЛИКАЦИЯ ПОМЕЩЕНИЙ
Наименование помещения
Участок для ремонта приспособлений
Мастерская по ремонту инвентаря
Участок сбора и регенерации СОМЖ
Отделение для переработки стружки
Вентиляционная камера
Инструментально-раздаточные кладовые
Трансформаторная подстанция
Склад материалов и заготовок
Заготовительное отделение
Ремонтная база механика
Ремонтная база энергетика
Секция наладки и освоения оборудования
Помещение для компрессорной установки
Межоперационный склад
Помещения общественных организаций
Контрольное отделение
Помещения культурного обслуживания
Помещения общественного питания
Производственные участки цеха
04-Стан.приспособление!! beta.cdw

БГТУ им. В. Г. Шухова
Разработка технологического процесса изготовления
корпуса редуктора очистной установкис использованием
САПР технологическорй и конструкторской документации
Сила затяжки гайки 7 не менее 1600 Н.
техмаршрут02Last.cdw

Зенкеровать отверстия
Развернуть окончательно
выдерживая размеры 4
Сверлить сквозное отверстие
выдерживая размеры 2
Сверлить последовательно
Повернуть стол на 180
Фрезеровать углубление
Сверлить 2 отверстия
Повторить переход 5.
Повторить переход 6.
Развернуть отверстие
выдерживая размеры 3
Повернуть стол на 30
выдерживая размер 11.
Повернуть стол на 60
Разработка технологического процесса изготовления
корпуса редуктора очистной установки с использованием
САПР технологическорй и конструкторской документации
Технологические эскизы
01-чертеж корпуса редуктора!!.cdw

Разработка технологического процесса изготовления
корпуса редуктора очистной установки с использованием
САПР технологическорй и конструкторской документации
* Размер для справок.
группа 1Г по ОСТ 23.4.50-73
точность отливки 8-3-8-6 по ГОСТ 26645-85.
На необрабатываемых поверхностях отливок допускаются
одиночные газовые раковины
количестве 5на поверхность.
На обрабатываемых поверхностях допускаются любые дефекты
выводимые припуском на мех. обработку.
Спец часть автопроект.cdw

Проектирование технологического процесса на основе
дублирующей технологии
Проектирование технологического процесса с
использованием базы данных
Проектирование технологического процесса с
использованием библиотеки типовых операций
Проектирование сквозного технологического процесса
БГТУ им. В.Г. Шухова
Разработка технологического процесса изготовления
корпуса редуктора очистной установки сиспользованием
САПР технологической и конструкторской документации
Разработка технологического процесса с использованием Компас-АВТОПРОЕКТ 9.3
Типы технологической документации
Выбор режущего инструмента
Структура технологического процесса
-05-КОНТРОЛЬНОЕ.cdw

Разработка технологического процесса изготовления
корпуса редуктора пневмодвигателя "Крот-12" с использованием
САПР конструкторской и технологической документации
На виде Б индикатор не показан
должен перемещаться без заеданий
Спецификация чтаночного.spw

изготовления корпуса редуктора очистной установки
с использованием САПР технологической и конструкторской докумнтации
БГТУ им. В. Г. Шухова
Гайка М16 ГОСТ 5915-70
Болт B.М16-6g х 160
Гайка М12 ГОСТ 5915-70
Ось 7-14 х 45 ГОСТ 9650-80
35-4145 ГОСТ 14364-69
03-4022 ГОСТ 14364-69
Кольцо запорное 12МН470-61
Кольцо запорное 14МН470-61
Шайба 28.01.05 ГОСТ 10450-68
Болт 7002-2561 ГОСТ 13152-67
техмаршрут01.cdw

Сверло 2300-0843 ГОСТ 19543-74
Развертка 2363-0721
Втулка 50-5 ОСТ2 П12-7-84
Патрон 2-50-5-90 ГОСТ 26539-85
Штангенциркуль ШЦ-I 200 0
Фрезеровать поверхность
Сверлить 2 отверстия
выдерживая размеры 2
Развернуть 2 отверстия
Фрезеровать торец в размер 1
выдерживая размеры 5
Расточить начерно отверстия:
Расточить начисто отверстия
Сверлить 5 сквозных
выдерживая размеры 4
а. Повернуть стол на 180
Фрезеровать канавки
выдерживая размеры 15
Фреза 2223-5281 ГОСТ 23247-78
Резец 2142-0102 МН 622-84
Зенковка 2353-0139 ГОСТ 14953-80
Сверло 2300-0868 ГОСТ 19543-74
Фреза 2234-0162 ГОСТ 6648-79
Фреза 2220-0521 ГОСТ 16225-81
Метчик 2640-0623 ГОСТ 17929-72
Втулка 50-4 ОСТ2 П12-7-84
Борштанга 6300-0332 МН 2645-81
Втулка 50-2 ОСТ2 П12-7-84
Патрон 2-50-7-90 ГОСТ 26539-85
Патрон 2-50-10-90 ГОСТ 26539-85
Технологический маршрут
изготовления корпуса
редуктора пневмодвигателя
Сплав АЛ7 ГОСТ 1583-93
БГТУ им. В. Г. Шухова
Разработка технологического процесса изготовления
корпуса редуктора очистной установки с использованием
САПР технологическорй и конструкторской документации
Технологические эскизы
Экономика_корпус.cdw

НА ГОДОВУЮ ПРОГРАММУ
СРАВНИТЕЛЬНЫЕ ТЕХНИКО-ЭКОНОМИЧЕСКИЕ
БГТУ им. В. Г. Шухова
Технико-экономические
Разработка технологического процесса изготовления
корпуса редуктора очистной установки с использованием
САПР технологической и конструкторской документации
Расходы на сырье и материалы
Амортизационные отчисления
Цеховая себестоимость
Общезаводские расходы
Внепроизводственные расходы
Полная себестоимость
Расходы на основную и
дополнительную заработную
плату рабочих с отчислениями
Расходы на текущий ремонт
и межремонтное обслуживание
Годовой выпуск продукции
Производительность труда
Рентабельность продукции
Годовой экономический
Срок окупаемости затрат
Число рабочих-станочников
Себестоимость единицы
одного рабочего-станочника
Себестоимость годового
Материалоемкость продукции
Затраты на 1 руб. товарной
Экономические показатели
---06-РТКа.cdw

Втулка 50-5 ОСТ2 П12-7-84
Дискретность отсчета
Втулка 50-4 ОСТ2 П12-7-84
Расчетно-технологическая
БГТУ им. В.Г. Шухова
Разработка технологического процесса изготовления
корпуса редуктора очистной установки сиспользованием
САПР технологической и конструкторской документации
Величина перемещения
Конец цикла обработки 2
РТК-2.cdw

Патрон 2-50-5-90 ГОСТ 26539-85
Разработка технологического процесса изготовления
корпуса редуктора очистной установки сиспользованием
САПР технологической и конструкторской документации
Величина перемещения
Конец цикла обработки 3
09-Спец часть- 3D байда.cdw

корпуса редуктора очистной установки
с использованием среды Компас 3D
Разработка технологического процесса изготовления
корпуса редуктора очистной установкис использованием
САПР технологическорй и конструкторской документации
02-чертеж заготовки корпуса редуктора!!.cdw

БГТУ им. В. Г. Шухова
Разработка технологического процесса изготовления
корпуса редуктора очистной установкис использованием
САПР технологическорй и конструкторской документации
1 Введение.doc
Целью дипломной работы является создание усовершенствованного технологического процесса механической обработки корпуса редуктора пневмодвигателя «Крот-12» с целью получения экономического эффекта за счет внедрения нового оборудования и разработки станочных и контрольных приспособлений.
Рис.1. Корпус редуктора пневмодвигателя «Крот-12»
Маршрутные и операционные карты.doc
Код наименование операции
Обозначение документа
Код наименование оборудования
мех 005 Фрезерно-центровальная
МР76М фрезер 2 1 1 1 60 15 0412
А. Установить заготовку на призмы до упора и закрепить
Поз. 1 Фрезеровать торцы выдержав размер
Фреза 2214-0082 ГОСТ 9373-80
Поз. 2 Сверлить центровые отверстия 4 на глубину 8+05
Сверло 2317-0109 ГОСТ 14952-75
Б. Открепить заготовку и снять; контроль исполнителем
Штангенциркуль ЩЦ-I ГОСТ 166-89
Линейка 0400 ГОСТ 427-75
8+05 32 1 012 250 94
РТК АСВР-05 токар 2 1 1 1 60 17 1978
А. Установить деталь в центрах и закрепить
Центр вращающийся I-5 ГОСТ 8742-75
Центр рифленый ГОСТ 13214-77
Подрезать торец выдерживая размеры 26.4
Резец 2112-0065 Т15К6 ГОСТ 18880-73
Резцедержатель 1-50 ОСТ-2П-15-5-84
Точить поверхность выдерживая размеры 2.17
6±04 53±02 15 1 025 315 79
Точить поверхность выдерживая размеры 19.20
7±02 97±035 115 1 025 315 79
Подрезать торец выдерживая размер 24
Резец 2100-0059 Т15К6 ГОСТ 18879-73
7±02 126±035 115 1 025 315 79
Точить фаску выдерживая размеры 21.23
Резцедержатель 1-50 ОСТ-2П-15-5-8
-04 2+025 15 1 04 400 108
Точить поверхность выдерживая размеры 22.25
Точить канавку выдерживая размеры 11.12.13
Точить фаску выдерживая размеры 6.7
Точить поверхность выдерживая разм. 5.10 и 45
Резец 2102-0059 Т15К6 ГОСТ 18877-73
Точить поверхность выдерживая размеры 8.10
Точить поверхность выдерживая размеры 9.18
Точить поверхность выдерживая размеры 1.14.16
Точить фаску выдерживая размеры 15.19
Резец 2100-0059 Т15К6 ГОСТ 18878-73
Точить поверхность выдерживая размер 19
М63Б шлиф 2 1 1 1 60 21 04
А. Установить заготовку в люнет
Люнет 1М63Б.66.000.СБ
Подрезать торец выдерживая размер 10
Точить поверхность выдерживая размер 8
точить фаску выдерживая размеры 7.9
Точить поверхность выдерживая размеры 2.7
Точить фаску выдерживая размер 5
Резец 2141-0079 Т15К6 ГОСТ 18883-73
х45о 2 3 1 012 630 277
Расточить отверстие выдерживая размеры 3.6
+085 2 3 1 012 630 1492
Расточить фаску выдерживая размер 4
х45о 2 3 1 012 630 1492
А. Установить заготовку в патрон
Патрон ГОСТ 14734-83
Сверлить отверстие D24 выдерживая размер 4
Сверло 2301-0069 ГОСТ 10903-77
Патрон ГОСТ 14586-76
Рассверлить отверстие D35 выдерживая разм. 4
Сверло 2301-0092 ГОСТ 10903-77
Расточить отверстие выдерживая разм. 4.5 15
Резец 2141-0082 Т15К6 ГОСТ 18883-73
5+2 2 3 1 026 500 1272
Расточить отверстие выдерживая разм. 2.3 15
2+04 2 075 1 026 500 1272
Расточить отверстие выдерживая разм. 7 и 30
+03 2 3 1 012 500 1272
Расточить отверстие выдерживая размер 1
5+02 2 075 1 012 500 1138
мех 045 Токарная с ЧПУ
АСВР-041 шлиф 2 1 1 1 60 21 04
А. Установить заготовку в патрон
Точить поверхность выдерживая размеры 1.2.3
6±04 2 1 1 026 630 217
Точить поверхность выдерживая размеры 4.6
+026 2 1 1 026 630 189
Нарезать резьбу выдерживая размер 5
Резец 2660-0007 Т15К6 ГОСТ 18885-73
М110х2g 2 0.4 1 2 400 138
М55 шлиф 2 1 1 1 60 21 04
Патрон 6251-0192 ГОСТ 14077-83
Сверлить 3 отв. последовательно D12.43 выд.разм 4
Сверло 2301-0040 ГОСТ 10903-77
Патрон 2-5-55 ГОСТ 14077-83
Зенковать последовательно 3 фаски выд. разм. 2
Зенковка 2353-0134 ГОСТ 1453-80
х45о 2 16 1 09 250 251
Нарезать последовательно резьбу в 3-х отв.выдерживая разм. 1.3
Метчик 2620-3489Н4 ГОСТ 17933-72
М14х15-6Н 2 0785 1 15 250 11
мех 065 Зубодолбежная
КС3-52М1 шлиф 2 1 1 1 60 21 04
Долбить зубья выдерживая размер по роликам М=64.911
Приспособление специальное
М=64.911 2 02 1 026 80 185
мех 075 Зубофрезерная
К324А шлиф 2 1 1 1 60 21 04
Фрезеровать зубья выдерживая размер W=48.65-0.2
Фреза 2510-4201 ГОСТ 9324-80
W=48.65-0.2 2 135 1 2 50 251
мех 085 Фрезерная с ЧПУ
Р324А шлиф 2 1 1 1 60 21 04
Фрезеровать паз выдерживая разм. 1.2.3
Фреза 223-0083 ГОСТ 17026-71
Втулка 6163-004 ГОСТ 13790-78
±018 2 65 1 128 400 201
А. Установить заготовку в о фрезерное приспособление
Калибровать резьбу выдерживая разм. 1
Резец 2650-007 ГОСТ 18885-73
М14х15-6Н 8 2 65 1 2 400 138
мех 120 Круглошлифовальная
М841 шлиф 2 1 1 1 60 21 04
А. Установить заготовку в центра
Центра ГОСТ 15435-86
Шлифовать одновременно поверхность и торец выдерживая разм. 1.3
Круг шлифовальный 2П350х25х127 24АП40-25-ПСМ 7К8-935мc ГОСТ 2424-83
М14х15-6Н 8 2 035 1 0005 1115 35
Шлифовать поверхность. выдерживая разм. 2.4
ø95-014 2 035 1 0005 1115 35
мех 130 Зубошлифовальная
А. Установить заготовку на опору
Шлифовать зубья выдерживая размерW=48.162
Круг шлифовальный 2П350х25х127 24АП40-25-ПСМ 7К8-935мc 1кл.А ГОСТ 2424-83
W=48.162 2 035 1 0005 1115 35
ø95-014 2 008 01 0005 1115 204
5 Цеха.doc
1. Исходные данные для проектирования
Спроектировать механический цех по изготовлению запасных частей редукторов большегрузных автомобилей.
Исходными данными для проектирования являются:
Nгод = 1500 штгод – годовая программа выпуска.
Тс = 520000 станкочасов – годовая станкоемность.
Режим работы цеха 2 сменный.
mдет. = 36 кг – вес детали.
mзаг. = 536 кг – вес заготовки.
Удельная станкоемкость Туд. = 105 ст.ч.т. ( табл.1.)
Технические нормы времени на выполнение операций
технологического процесса
Наименование операции
Штучно-калькуля-ционное время
Фрезерно-центровальная
2. Определение типа производства и формы организации производства
Пользуясь условиями классификации [2] отнесем деталь к средним по массе (м=36 кг). Далее с учетом годовой программы N = 1500 шт.год по табл. 1[2] примем тип производства серийным. Рассчитаем для условий серийного производства размер партии одновременно обрабатываемых заготовок предварительно допустив что для бесперебойной работы цеха должен быть запас готовых деталей на 11 дней тогда
Примем к исполнению и для расчетов n = 65 шт.
Соразмерив величину n с данными табл. 3 [1] будем считать производство среднесерийным. Следовательно форма организации производства данной детали является непоточной.
3. Расчёт количества и определение состава основного
технологического оборудования цеха
Определение количества требуемого основного оборудования:
Где Тс = 520000 с-ч – станкоемкость годового объема выпуска изделий с запасными частями;
Фо = 4015 ч – средний действительный годовой фонд времени работы оборудования для металлорежущих станков массой до 10 тонн при двухсменном режиме работы ([15] табл. 2.1);
kз– средний коэффициент загрузки оборудования ([14] табл. 1);
kи – средний коэффициент использования оборудования ([14] табл. 1).
По данным табл. 1[2] определим среднее значение коэффициентов Кз и Ки:
Таким образом потребное количество станков составит:
4. Определение состава вспомогательных служб
и участков цеха и выбор оборудования
Состав механического цеха зависит от объема выпуска типа и формы производства. Для серийного производства запасных деталей редукторов а в частности «вала приводного» требуются следующие вспомогательные службы:
- служба энергетика
- мастерская для ремонта приспособлений и инструмента
- площади для сбора и регенерации СОЖ
- отделение для сбора и переработки стружки
- инструментально-раздаточные кладовые
- термическое отделение
- цеховой склад материалов и заготовок
- промежуточные склады.
Определение общего количество станков заточного отделения. Количество станков выбирается в зависимости от количества основного производства оснащенных режущим инструментом специального и специализированного назначения.
Определим количество станков заточного отделения:
Sон – количество станков основного производства оснащенных режущим инструментом общего назначения;
Sон = Sпр – Sсп – Sшт = 167-117= 50 шт.
- коэффициент условной производительности = 15215
= 18 (т.к. данный коэффициент должен закладываться на перспективу.)
- коэффициент учитывающий долю станков оснащенных режущим инструментом с не перетачиваемыми пластинами ( = 021) Принимаем = 08.
Определим количество оборудования для ремонтной базы механика.
Согласно табл.2 [1] для количества основных станков менее 300 количество основных станков ремонтной базы составляет 2% и не менее 6 шт.
следовательно принимаем Sм = 6 шт.
Мастерская энергетика режущим оборудованием не комплектуется.
Определение числа станков в мастерской по ремонту оснастки:
Определение количества транспортных средств.
Так как цех не имеет тяжёлых для транспортировки деталей (станин и др.) нет необходимости в оснащении цеха кранами так как установка мостовых и подвесных кранов любой грузоподъёмности только для монтажа и ремонта оборудования запрещается. Учитывая это выбираем напольное транспортное средство – электропогрузчик грузоподъёмностью 01 2 тонн.
Количество транспортных средств:
Время одного цикла перевозок.
Кок – количество транспортных операций с одним и тем же грузом.
Qц = 05 т – масса материала заготовок перевозимых за один цикл.
Т. е. для нормальной работы цеха необходимо 5 электропогрузчиков грузоподъемностью 01 2 т.
Также для установки детали на станок (на всех операциях) будет применяться промышленный робот (что связанно с относительно большой для человека массой изготавливаемой детали).
Общее число станков: Sоб = 167 + 9 + 6 + 12 = 194 шт.
5. Определение численности и состава работающих
В состав работающих цеха входят:
- производственные рабочие;
- вспомогательные рабочие;
- инженерно-технические работники (ИТР);
- младший обслуживающий персонал (МОП).
К категории производственных рабочих относятся все рабочие непосредственно участвующие в технологическом процессе производства товарной продукции (станочники слесари разметчики мойщики слесари сборщики).
Определение численности производственных рабочих производится по станкоёмкости:
Тс = 520000 – станкоемкость
Фр =1760 часов - годовой фонд времени рабочего.
Км - коэффициент многостаночного обслуживания; (13 – 15) – для среднесерийного производства. Принимаем Км = 135.
Определение общего числа производственных рабочих с учетом слесарей-сборщиков:
Все работы необходимые для функционирования основного производства выполняются вспомогательными рабочими. В современных условиях их количество выбирают в пределах 3570% от количества основных производственных рабочих.
Работа по организации производственного процесса и его функционированию выполняют ИТР. Их количество выбирают в пределах от 115 до 14% от общего количества основных и вспомогательных рабочих.
Служащие составляют 152% от числа основных и вспомогательных рабочих.
К служащим цеха относятся: табельщики; бухгалтера; кассиры; заведующие складов:
Младший обслуживающий персонал составляет 23% от общего числа основных и вспомогательных рабочих.
К младшему обслуживающему персоналу относятся: уборщики; гардеробщики; курьеры:
Суммарное количество работников составляет:
Nобщ = Nпр. +Nвс +Nитр +Nсл +NМОП
Nобщ = 219+110+39+5+8=381 чел.
6. Расчет площадей и компоновка оборудования
Укрупненный расчет потребных производственных площадей произведем в зависимости от количества и типов применяемого оборудования размеров и массы обрабатываемых деталей применяемых транспортных средств и т.п.
Площадь производственных участков равна:
Sпр. – принятое количество производственного оборудования;
Fст. - удельная площадь на единицу оборудования (табл. 7 [1]).
Площадь заточного отделения:
Sзат – число станков заточного отделения (Sзат=9 шт)
Площадь контрольного отделения:
Площадь ремонтной базы механика цеха:
- удельная площадь на станок ремонтной базы.
Sмех. – количество станков ремонтной базы механика.
Площадь склада запасных частей:
Площадь ремонтной мастерской:
Площадь распределительной кладовой:
Площадь участка слесарей монтажников и слесарей по техническому обслуживанию транспортных устройств:
Площадь ремонтной базы энергетика:
Площадь для ремонта электрооборудования:
Площадь участка слесарей:
Площадь участка для ремонта приспособлений.
Sпр. – количество обслуживаемого производственного оборудования.
Площадь участка сбора и регенерации СОЖ:
Площадь отделения для переработки стружки:
Площадь под кладовые масла:
Fкл. масла = 01 Sобсл
Sобсл – количество всех обслуживаемых станков.
Sобсл = Sпр + Sзат. +Sр.ан+Sм = 167+9+12+6 = 194 ст.
Цеховой склад материалов и заготовок:
- масса материалов и заготовки годовые объема выпуска; - среднее количество дней в течение которых металл и заготовки хранятся на складе;
- средняя допускаемая нагрузка на 1м2 площади (для средних заготовок 2 2);
к – коэффициент использования площади к=03;
( выбираем ориентируясь на технологическую часть данного диплома табл.3)
Площадь межоперационного и промежуточного складов:
Межоперационный склад:
Qг – масса годового выпуска деталей: Qг = 4952 3 т.
– коэффициент учитывающий отходы металла на предыдущих операциях:
j – среднее число доставок полуфабрикатов на склад (в соответствии с количеством операций технологического процесса принимаем j 5)
t’=2 3 – число дней межоперационного хранения t’=2.
- средняя нагрузка (допускаемая) на единицу площади.
=05 – коэффициент использования площади.
Промежуточный склад:
число рабочих дней запаса =8
= 03 – коэффициент использования площадей.
Инструментально – раздаточные кладовые:
Fуд. – удельная площадь на один станок производства.
Fуд = 025 (табл.8 прилож.[1]).
Мастерская по ремонту инвентаря:
Помещение для компрессорных установок:
Помещение секции наладки и освоения оборудования:
Трансформаторные подстанции:
Fтрансф. = 001 Fпр.= .
Вентиляционные камеры:
Общая площадь цеха без учета площадей служебно - бытовых помещений:
7. Разработка компоновочного плана цеха
Наиболее распространенной конструкцией зданий для размещения механических цехов согласно [1] являются одноэтажные многопролетные здания прямоугольной формы с полом на бетонном основании и перекрытием поддерживаемым системой колонн образующих пролеты цеха. Выбор основных параметров здания производится с учетом особенностей технологического процесса и определяется рациональным размещением производства и экономичностью строительства достигаемой при применении унифицированных строительных элементов и типовых конструкций.
Для полученной площади здания наиболее рациональной формой здания будет прямоугольник с соотношением строк 1:2. Принимаем шаг внутренних колонн равным 12 м шаг колонн по периметру здания – 6 м ширину пролета – 24 мм; высоту пролета – 72 м.
С учетом произведенных расчетов основываясь на принципе минимума грузопотоков (стр. 15[1]) спроектируем компоновочный план цеха.
Определение площадей и компоновка служебно-бытовых помещений.
Служебно-бытовые помещения где находятся административно-технические службы размещают в пристройках в отдельно стоящих зданиях с утеплённым переходом или во вставках больших корпусов. Применение многоэтажных отдельно расположенных служебно-бытовых корпусов позволяет освободить производственную площадь от вспомогательных энергетических устройств расположить склады заготовок комплектующих изделий и готовой продукции в зонах соответствующих цехов приблизить бытовые помещения к рабочим местам.
В состав служебно-бытовых помещений цеха входят объекты культурно-бытового назначения и объекты административно-технического назначения.
Цеховые объекты культурно-бытового назначения включают гардеробные с умывальниками душевые туалетные комнаты помещения для личной гигиены комнаты для курения устройства для снабжения питьевой водой столовые буфеты комнаты для приёма пищи - столовые медпункты красные уголки закрытые помещения для отдыха.
К цеховым объектам административно-технического назначения относятся помещения начальников смен мастеров и бригадиров цеховые конторы помещения общественных организаций лаборатории а также помещения для учебных занятий работающих и практики студентов.
Площади служебно-бытовых помещений определяются по формуле:
где Fуд – удельная площадь (на одного работающего) рекомендуемая для расчета площадей служебно-бытовых помещений цеха [14 табл. 5 стр. 20].
Nобщ – общая численность работающих в цехе: Nобщ = 381 чел.
Гардеробные механосборочных цехов занимают наибольшую площадь и проектируются для хранения учебной и рабочей одежды в закрытых шкафах. Типы шкафов и их размеры выбираются в зависимости от группы санитарно-технических условий технологических процессов:
а) для хранения рабочей одежды применяют одинарные закрытые вентилируемые шкафы – глубина 50 см ширина 25 – 50 см;
б) для чистой (уличной домашней) используют двойные закрытые шкафы – глубина 50 см ширина 35 – 40 см.
Высота всех шкафов 165 – 180 см. Шкафы собирают в секции шириной 800 или 1000 мм. Нормы проходов между рядами шкафов:
) 2 м в проходах со скамьями;
) 1 15 м без скамеек;
) 13 м между рядами со скамьями и стеной;
) 1 м между стеной и ряжами без скамеек.
Принимаем для гардеробных шкафчиков размеры см. ширину прохода между шкафами со скамьями 2 м. между шкафами и стеной – 13 м площадь комнаты для инвентаря – 3 м2. Общее кол-во шкафчиков составит 381 шт.
Умывальники разместим в комнате рядом с гардеробной. Примем количество умывальников в расчете 15 чел. на 1 умывальник тогда получим общее количество умывальников:
Примем размер одного умывальника ширину прохода – 15 м.
Fумыв.ж. = Fумыв.м. 36 м2.
Душевые с преддушевым помещением для переодевания располагают в смежных с гардеробом помещениях. Они имеют приточно-вытяжную вентиляцию. Количество душевых сеток – одна на 15 человек. Общее количество душевых сеток определяют по числу рабочих в наибольшую (обычно – первую) смену.
Т.о. общее количество сеток ставит:
Размеры душевых кабинок примем равными
Fдуш. ж.= Fдуш.м.=37 м2.
Санузлы с умывальниками располагают по цеху равномерно с шагом более 75 м. Обязательно наличие вытяжной вентиляции и шлюзового отсека с умывальниками. Общая площадь санузла составляет 36 м2.
Также необходимо предусмотреть наличие комнат для курения. Они располагаются рядом с туалетом. Расстояние от наиболее удалённого рабочего места не более 100 м. Эти помещения должны быть оборудованы скамейками урнами и вентиляцией.
Площадь санитарно-гигиенических помещений (гардеробные душевые туалеты и др.):
Fсг = 316 · Nобщ = 316 · 381 = 120396 м2
- В состав столовой входят следующие помещения:
- для посетителей – гардеробная туалет и умывальная обеденный зал с раздаточной и буфетом;
- производственные – кухня цех по переработки продуктов охлаждаемые камеры;
- административно-бытовые – контора комната персонала;
- технические – машинное отделение подъёмников холодильник и др.
Учитывая малые габариты цеха и немногочисленный состав работающих в одну смену (381 чел.) столовую в состав цеха включать не будем предполагая что цех входит в состав завода на территории которого располагается общая столовая в отдельном здании.
При работе по принципу самообслуживания число посадочных мест принимают из расчёта одно место на 3 – 4 человека работающих в наибольшей смене. Площадь занимаемую одним столиком на 4 человека принимают равной 4 м2. С учётом проходов площадь одного посадочного места составляет 18 м2. Площадь помещения буфетов колеблется в пределах 30 110 м2. Площадь комнат для приёма пищи определяется из расчёта 1 м2 на человека но не менее 12 м2.
Площадь помещений общественного питания включая подсобные помещения кухни:
Fоп = 061 · Nобщ = 061 · 381 = 23241 м2
Медицинский пункт цеха следует размещать вблизи наиболее многолюдных и опасных в отношении травматизма цехов как правило около входа на первом этаже административно-технических помещений. В состав здравпункта входят:
- вестибюль с регистратурой;
- комната ожидания больных;
- комната приёма больных;
- процедурный кабинет;
- комната для дежурного персонала;
Площадь медицинского помещения:
Fмед = 023 · Nобщ = 023 · 381 = 8921 м2
Цеховые помещения для культурного обслуживания предназначены для проведения культурных мероприятий и отдыха в обеденный перерыв. Они включают красные уголки цеховые читальни и библиотеки. Площадь красного уголка рассчитывают с учётом обеспечения местами 30 % работающих в наибольшую смену при норме 1 м2 на одно место. Красные уголки следует размещать в зонах близких к столовым.
Площадь помещений для культурного обслуживания (библиотеки учебные комнаты и др.) разместим на втором этаже:
Fк обс = 03 · Nобщ = 03 · 381 =1886 м2
Цеховые конторские помещения предназначены для цехового персонала занимающегося производственно-техническим планированием техническим руководством и бухгалтерским учётом. К ним также относятся цеховые общественные организации.
Служебные помещения необходимо размещать с учётом их разделения на помещения для служб общего назначения (начальник цеха бухгалтерия и т. п.) и оперативного характера (диспетчерские начальники участков и т. п.). Помещения общего назначения располагаются на втором этаже фасадных пролётов а помещения служб оперативного характера должны находится ближе к производственным участкам цеха.
Общая площадь служебных помещений (цеховые конторы лаборатории) исходя из удельных площадях 07 м2 на 1 чел. ([1] табл.5) составит:
Fсп = 07 · Nобщ = 07 · 381 = 2896 м2
Площадь помещений общественных организаций:
Fоо = 004 · Nобщ = 004 · 381 = 1524 м2
Общая площадь служебно-бытовых помещений составляет:
Fсл = 1204 + 232 + 90 + 189 + 300 + 15 = 1930 м2.
На основании компоновки служебно-бытовых помещений скорректируем компоновочный план цеха.
2 Назначение и конструкция детали.doc
Корпус является базовой деталью пневмодвигателя установки «Крот-12» предназначенной для гидромеханического разрушения карбонатных отложений на внутренней поверхности различных труб. Установка состоит из двух основных элементов: пневмодвигателя и редуктора.
Корпус редуктора предназначен для размещения в нем передаточного устройства и водяной насадки а также для присоединения гибкого вала.
Внизу корпус имеет коробчатую форму с размерами верхняя половина имеет форму цилиндрической поверхности длиной 105 мм и радиусом 46 мм.
Боковая поверхность является базовой и предназначена для крепления корпуса редуктора к установке. Она выполнена в виде фланца толщиной 10 мм с пятью сквозными отверстиями 7 мм три из которых располагаются на окружности 104 мм (два на горизонтальной оси а одно на вертикальной оси сверху) а два оставшихся располагаются симметрично относительно вертикальной оси корпуса на удалении 6 мм от его боков и 10 мм от его основания.
В корпусе на глубину 46 мм выполнен паз в виде двух пересекающихся цилиндров диаметром 78 мм. Паз предназначен для размещения в нем пары зубчатых колес редуктора. Для данного паза задан допуск биения 16 мкм относительно ступенчатого сквозного отверстия 524745мм выполненного на расстоянии 100 мм от основания и предназначенного для установки подшипникового узла. Ступени отверстия выполняются с шероховатостью 16 мкм по параметру Ra с биением относительно друг друга 16 мкм. Допуск перпендикулярности данных отверстий относительно базовой плоскости 16 мкм. В ступенчатом отверстии выполнены канавки для уплотнительных колец. В нижнем цилиндре паза выполнено глухое отверстие 40 мм глубиной 12 мм для установки подшипника под вал.
С правой стороны корпус имеет форму усеченного конуса на котором имеется 4 отверстия М6 расположенных под углом 45° к осевым линиям на окружности 60 мм для крепления крышки
В отверстии 45мм под углом на расстоянии 10 мм от правого торца корпуса выполнен канал 13мм который сообщается с другим каналом выполненным в виде ступенчатого отверстия 3718222830 и предназначенного для расположения в нем элементов гидроклапана. Данная система каналов предназначена для подвода воды в рубашку гибкого вала.
На заднем торце корпуса расположены 4 отверстия М6-6Н для установки крышки предназначенной для соединения с трубопроводом; на переднем торце так же расположены 4 отверстия М5 для установки крышки под пружину и для соединения с трубопроводом.
Также имеются два отверстия для подвода смазки: первое выполнено в верхней стенке корпуса диаметром М10 куда ввинчивается заглушка; второе 4мм выполнено сквозным через стенку корпуса до ступенчатого отверстия 524745мм. С задней стороны данного ступенчатого отверстия выполнен паз 3516 мм для размещения стопорного элемента.
Нижняя плоскость предназначена для установки корпуса редуктора «Крот-12» на какую-либо поверхность во время его эксплуатации. Для этого на основании корпуса имеется 2 отверстия М6 на расстоянии 64 мм друг от друга и 14 мм от правого торца предназначенные для крепления лап к корпусу.
Корпус пневмодвигателя выполняется из сплава алюминия АЛ7 ГОСТ 1453-93 - сплав предназначенный для изготовления фасонных отливок. АЛ7 - сплав на основе системы алюминий - медь (табл. 1).
Химический состав литейного сплава АЛ-7 ГОСТ 2685-75
Механические свойства сплава.
сопротивление кгсмм2
В - литье в песчаные оболочковые и по выплавляемым моделям. К - литье в кокиль. Т4 - закалка. Т5 - закалка и кратковременное (неполное) искусственное старение;
Для АЛ7 дается характеристика и примерное назначение как сплаву с хорошей обрабатываемостью пониженными свариваемостью и коррозийной стойкостью уровень рабочей температуры 225 0С. Данный сплав применяется для получения отливок несложной формы средненагруженных деталей.
Для уменьшения и перераспределения остаточных напряжений а также для достижения необходимой величины твердости указанной в технических требованиях на чертеже детали отливку подвергают закалке и искусственному старению.
Диплом.docx
ТЕХНОЛОГИЧЕСКАЯ ЧАСТЬ10
1.Исходные данные для проектирования.10
2.Определение типа производства.11
3.Отработка изделия на технологичность и технологический контроль чертежа12
4.Анализ существующего технологического процесса. Выявление его достоинств и недостатков.14
5.Выбор и обоснование способов изготовления заготовок.17
6.Назначение технологических баз.20
7.Выбор способов обработки отдельных поверхностей.21
8.Разработка маршрута механической обработки детали.24
9.Выбор оборудования.29
10.Выбор режущего и вспомогательного инструмента.31
11.Выбор приспособлений и измерительного инструмента36
12.Расчет припусков промежуточных размеров и допусков окончательная корректировка чертежа заготовки.37
13.Проектирование механических операций.42
14.Расчет режимов резания сил резания проверка соответствия выбранного оборудования.43
15.Аналитическое прогнозирование точности и качества обработки поверхностей.47
16.Техническое нормирование.50
17.Проектирование схем технологических наладок оборудования.53
КОНСТРУКТОРСКАЯ ЧАСТЬ54
1.Исходные данные для проектирования станочного приспособления.54
2.Выбор типа приспособления54
3.Выбор схемы станочного приспособления и конструкции установочных деталей.55
4.Расчет сил закрепления заготовки.57
5.Выбор конструкции и размеров зажимных устройств58
6.Расчет погрешности закрепления60
7.Описание конструкции и принципа работы станочного приспособления60
8.Эффективность использования и стоимость технологической оснастки.61
ПРОЕКТИРОВАНИЕ ЦЕХА63
1.Исходные данные для проектирования.63
2.Расчёт количества основного технологического оборудования64
3.Определение состава вспомогательных служб и участков цеха выбор оборудования.65
Расчёт численности и состава работающих.67
4.Расчёт площадей и компоновка оборудования.69
5.Компоновка цеха.73
6.Определение площадей и компоновка служебно-бытовых помещений.74
ЭКОНОМИЧЕСКАЯ ЧАСТЬ76
1.Технико-экономический анализ.76
2.Определение дополнительных капитальных вложений (инвестиций).76
3.Расчет себестоимости продукции77
БЕЗОПАСНОСТЬ ЖИЗНЕДЕЯТЕЛЬНОСТИ85
2.Требования охраны труда к производственным и санитарно-бытовым помещениям86
3.Требования охраны труда к оборудованию и оснастке.88
4.Оздоровление воздушной среды в производственных помещениях.90
5.Меры по снижению уровня шума и вибраций в производственных помещениях.91
6.Производственное освещение. Расчет освещенности цеха.94
7.Электробезопасность. Расчет защитного заземления.96
8.Обеспечение пожарной безопасности.99
СПЕЦИАЛЬНАЯ ЧАСТЬ102
1.Использование трехмерного моделирования для подготовки рабочего чертежа детали.102
2.Выбор системы проектирования.102
3.Трехмерное проектирование корпуса редуктора.103
4.Проектирование плана цеха с использованием библиотеки отрисовки планов зданий и сооружений.104
СПИСОК ЛИТЕРАТУРЫ108
Технический прогресс современного производства во всех отраслях народного хозяйства определяется развитием машиностроения его технический уровнем выпуском продукции с высокими качественными показателями при максимальной эффективности производства. Одним из основных факторов повышения технического уровня машиностроения является внедрение высокоэффективных технологических процессов и конструкторских разработок.
Целью дипломной работы является создание усовершенствованного технологического процесса механической обработки корпуса редуктора пневмодвигателя «Крот-12» с целью получения экономического эффекта за счет внедрения нового оборудования и разработки станочных и контрольных приспособлений.
Рис.1 Корпус редуктора пневмодвигателя «Крот-12»
Назначение и конструкция детали
Корпус является базовой деталью пневмодвигателя установки «Крот-12» предназначенной для гидромеханического разрушения карбонатных отложений на внутренней поверхности различных труб. Установка состоит из двух основных элементов: пневмодвигателя и редуктора.
Корпус редуктора предназначен для размещения в нем передаточного устройства и водяной насадки а также для присоединения гибкого вала.
Внизу корпус имеет коробчатую форму с размерами верхняя половина имеет форму цилиндрической поверхности длиной 105 мм и радиусом 46 мм.
Боковая поверхность является базовой и предназначена для крепления корпуса редуктора к установке. Она выполнена в виде фланца толщиной 10 мм с пятью сквозными отверстиями 7 мм три из которых располагаются на окружности 104 мм (два на горизонтальной оси а одно на вертикальной оси сверху) а два оставшихся располагаются симметрично относительно вертикальной оси корпуса на удалении 6 мм от его боков и 10 мм от его основания.
В корпусе на глубину 46 мм выполнен паз в виде двух пересекающихся цилиндров диаметром 78 мм. Паз предназначен для размещения в нем пары зубчатых колес редуктора. Для данного паза задан допуск биения 16 мкм относительно ступенчатого сквозного отверстия 524745мм выполненного на расстоянии 100 мм от основания и предназначенного для установки подшипникового узла. Ступени отверстия выполняются с шероховатостью 16 мкм по параметру Ra с биением относительно друг друга 16 мкм. Допуск перпендикулярности данных отверстий относительно базовой плоскости 16 мкм. В ступенчатом отверстии выполнены канавки для уплотнительных колец. В нижнем цилиндре паза выполнено глухое отверстие 40 мм глубиной 12 мм для установки подшипника под вал.
С правой стороны корпус имеет форму усеченного конуса на котором имеется 4 отверстия М6 расположенных под углом 45 к осевым линиям на окружности 60 мм для крепления крышки
В отверстии 45мм под углом на расстоянии 10 мм от правого торца корпуса выполнен канал 13мм который сообщается с другим каналом выполненным в виде ступенчатого отверстия 3718222830 и предназначенного для расположения в нем элементов гидроклапана. Данная система каналов предназначена для подвода воды в рубашку гибкого вала.
На заднем торце корпуса расположены 4 отверстия М6-6Н для установки крышки предназначенной для соединения с трубопроводом; на переднем торце так же расположены 4 отверстия М5 для установки крышки под пружину и для соединения с трубопроводом.
Также имеются два отверстия для подвода смазки: первое выполнено в верхней стенке корпуса диаметром М10 куда ввинчивается заглушка; второе 4мм выполнено сквозным через стенку корпуса до ступенчатого отверстия 524745мм. С задней стороны данного ступенчатого отверстия выполнен паз 3516 мм для размещения стопорного элемента.
Нижняя плоскость предназначена для установки корпуса редуктора «Крот-12» на какую-либо поверхность во время его эксплуатации. Для этого на основании корпуса имеется 2 отверстия М6 на расстоянии 64 мм друг от друга и 14 мм от правого торца предназначенные для крепления лап к корпусу.
Корпус пневмодвигателя выполняется из сплава алюминия АЛ7 ГОСТ 1453-93 - сплав предназначенный для изготовления фасонных отливок. АЛ7 - сплав на основе системы алюминий - медь (табл. 1).
Химический состав литейного сплава АЛ-7 ГОСТ 2685-75
Механические свойства сплава.
сопротивление кгсмм2
В - литье в песчаные оболочковые и по выплавляемым моделям. К - литье в кокиль. Т4 - закалка. Т5 - закалка и кратковременное (неполное) искусственное старение;
Для АЛ7 дается характеристика и примерное назначение как сплаву с хорошей обрабатываемостью пониженными свариваемостью и коррозийной стойкостью уровень рабочей температуры 225 0С. Данный сплав применяется для получения отливок несложной формы средненагруженных деталей.
Для уменьшения и перераспределения остаточных напряжений а также для достижения необходимой величины твердости указанной в технических требованиях на чертеже детали отливку подвергают закалке и искусственному старению.
Технологическая часть
1.Исходные данные для проектирования.
Исходными данными для проектирования являются:
–чертеж детали корпус редуктора пневмодвигателя Крот-12;
–годовая программа выпуска - 2500 штгод;
–базовый технологический процесс изготовления корпуса редуктора;
–материал преддипломной практики;
–Техническая научная справочная учебно-методическая литература по технологии машиностроения.
При проектировании данного технологического процесса необходимо учитывать технические требования предъявляемые к детали конструктором которые изложены на чертеже детали.
Твердость получаемой детали должна составлять НВ 70 90. Заготовка - отливка в кокиль группа 1Г по ОСТ 23.4.50 - 73 5 группа сложности точность получаемой отливки 8-3-8-6 по ГОСТ 26645 - 85.
2.Определение типа производства.
Тип производства и соответствующие ему формы организации труда определяют характер технологического процесса и его построение. Ориентируясь по номенклатуре годовой программе и другим характерным признакам (массы изделия габаритных размеров и т. д.) определяется тип производства.
Произведем выбор типа производства по рекомендациям приведенным в [1] позволяющим устанавливать его в зависимости от габаритных размеров массы и годового объема выпуска деталей. По программе выпуска 2500(1 таблица 1) для среднего по массе типа деталей (т=34 кг) данное производство характеризуется как серийное.
Рассчитаем размер партии для условий серийного производства.
гдеа=6-10 - периодичность запуска (необходимость запаса деталей на складах) дни;
N - годовая программа выпуска 2500 шт.год.
Выбор серийности произведем по таблице 3 [1]. По расчетному количеству деталей в серии (99 штук) и отношению данной детали к средним по массе данное производство относится к среднесерийному типу.
3.Отработка изделия на технологичность и технологический контроль чертежа
Чертеж детали «Корпус редуктора» содержит достаточное количество видов разрезов сечений. Размеры на чертеже проставлены правильно и в достаточном количестве. Корпус имеет несколько поверхностей по которым он базируется относительно других деталей важно точное выполнение требований к базовым и основным функциональным поверхностям.
В технических требованиях указаны величины литейных уклонов и радиусов которые на стадии получения заготовки выполняются с целью свободного удаления модели из кокиля. Однако незначительная их величина (литейные уклоны до 2 радиусы до 2 мм) оставшаяся после механической обработки не влияет на эксплуатационные свойства изделия и могут оставаться в указанных пределах.
Технические условия на изготовление корпуса редуктора содержат также требования включающие информацию о наличии дефектов поверхностного слоя и допускаемых их значениях как к обрабатываемым поверхностям (допускаются любые дефекты выводимые припуском на мех. обработку) так и к необрабатываемым (допускаются одиночные газовые раковины 3 мм глубиной до 2 мм в количестве 5на поверхность).
Неуказанные предельные отклонения предельных размеров отверстий и валов 7-ой степени точности соответствуют 14 квалитету точности по ЕСДП СЭВ с полями допусков: для отверстий по Н14 для валов по h14 остальные по .
Размеры обозначенные относятся к справочным то есть к размерам неподлежащим выполнению по данному чертежу и указанных для большего удобства пользования.
Анализ чертежа детали показывает что общее количество размеров на чертеже минимально но достаточно для изготовления и контроля изделия.
Отверстия 40 мм 47 мм 52 мм должны быть обработаны по 7 квалитету точности с шероховатостью 16 Ra. Данные поверхности служат для установки подшипников качения. Согласно рекомендациям справочной литературы 5 (т.1 с. 278) опоры быстровращающихся валов средней точности должны быть обработаны по 7-8 квалитету точности.
Радиальное биение 45 относительно 47 составляет 0016 мм что соответствует 5 степени точности. По 5 (т.1 с. 424) для торцов корпусов высокого давления торцов рам и корпусов гидро- и пневмоприборов радиальное биение отверстий под вал должно соответствовать 4 - 5 степени точности. Аналогично проверим правильность назначения всех остальных допусков на погрешность формы. Шероховатость функциональных поверхностей Ra 16 крепежных отверстий Ra 63 необрабатываемых поверхностей Ra 10.
Корпус имеет форму близкую к параллелепипеду одна сторона которого имеет закругление.
Нетехнологичным элементом представляющим большую сложность обработки является отверстие под углом 60 к основанию. Точная его обработка представляется возможным либо при установке обрабатываемой детали в специальное приспособление либо при базировании корпуса редуктора таким образом чтобы данное отверстие было расположено в горизонтальной плоскости что возможно на станке горизонтальной компоновки с поворотным столом.
Малотехнологичными элементами является множество мелких точных резьбовых отверстий расположенных на торцах и боковых поверхностях корпуса.
Тем не менее в целом все обрабатываемые поверхности с точки зрения обеспечения заданной точности и шероховатости легкости подвода инструмента не представляют технологических трудностей.
4.Анализ существующего технологического процесса. Выявление его достоинств и недостатков.
Производя анализ существующего технологического процесса необходимо выяснить обеспечиваются ли все требования чертежа правильно ли выбраны базы соответствует ли последовательность выполнения операций достижению заданной точности и т. д.
Проанализируем технологический процесс по следующим пунктам:
а)соответствие метода получения заготовки данному масштабу производства её соответствие чертежу по размерам припусков на обработку и технических условий.
Согласно базовому технологическому процессу заготовку корпуса редуктора получают литьем в кокиль. Применяемый метод литья соответствует среднесерийному производству. Заготовка пневмодвигателя имеет несложную фасонную форму средних размеров. Отливка относится к 8 классу размерной точности степень точности поверхностей – 8 класс точности массы – 6.
Точность получаемой отливки 8-3-8-6 по ГОСТ 26645 - 85.
Для улучшения свойств отливки а также для достижения необходимой величины твердости указанной в технических требованиях чертежа изделия (НВ 70-90) в технологическом процессе применяется кратковременное (неполное) искусственное старение которое заключается в нагреве заготовки до с последующим остыванием. В существующем технологическом процессе термообработка выполняется на стадии получения заготовки.
Проверим правильность назначения припусков и допусков на заготовку. Заготовка является обобщенной для различных типов корпусов поэтому имеет завышенные припуски особенно по длине корпуса. Допуски на все размеры назначаются по 14 квалитету что не соответствует рекомендуемым для отливок данного класса точности. Значения литейных уклонов и литейных радиусов - соответствуют действительности.
Коэффициент использования материала имеет среднее значение К=07 что соответствует единичному и мелкосерийному производству. Для средне- и крупносерийного необходимо достигнуть увеличения использования материала. Для более удобного извлечения заготовки из кокиля на заготовке предусмотрены уклоны в сторону плоскости разъема.
В дальнейшем необходимо рассмотреть возможность применения другого способа получения заготовки либо оптимизировать данный вариант путем приближения формы заготовки к форме детали.
б)правильность выбора баз на всех операциях и соблюдение принципа единства баз.
В существующем технологическом процессе обработка корпуса редуктора пневмодвигателя производится при схеме базирования по плоскости и перпендикулярным ей двум отверстиям. Данная схема базирования соблюдается на протяжении практически всего технологического процесса при обработке всех основных функциональных поверхностей.
в)соответствие последовательности операции достижению заданной точности детали.
На первой операции производится обработка основания и двух технологических отверстий. Далее базируясь по основанию и двум отверстиям осуществляем последовательную обработку торцов корпуса редуктора отверстий. После чего базируясь по торцам и основанию получаем отверстие под масленку отверстие под углом к основанию нарезаем резьбу в технологических отверстиях.
Последовательность операций соответствует достижению заданной точности.
г)соответствие оборудования требованиям данной операции по точности габаритным размерам производительности (прогрессивным режимам резания).
На всех операциях механической обработки базового технологического процесса используется многоцелевой сверлильно-фрезерно-расточной станок мод. ГДВ400ПМ1Ф4.
Обработку корпуса редуктора будем производить на горизонтальном сверлильно-фрезерно-расточном станке с автоматической загрузкой инструмента и заготовок мод. 2204ВМ1Ф4. Данный станок предназначен для обработки корпусных деталей с 4-х сторон без переустановки по программе. На станке данной модели можно производить получистовое и чистовое фрезерование различных видов поверхностей фрезами всех типов сверление зенкерование развертывание растачивание нарезание резьбы метчиками.
При этом один рабочий может обслуживать несколько станков что в конечном счете приведет к уменьшению себестоимости детали.
д)оснащенность операции высокопроизводительным режущим и измерительным инструментом и приспособлением.
В качестве режущего инструмента используется универсальный режущий инструмент. В базовом технологическом процессе используются токарные резцы из материала группы ВК8 свёрла фрезы метчики из материала Р6М5. Все выбранные режущие инструменты соответствуют операциям и характеристикам получаемых поверхностей.
В качестве станочного приспособления выбраны тиски что увеличивает время закрепления детали. Для его уменьшения можно применить гидравлический или пневматический привод в тисках или другое приспособление.
Контроль производится только на конечной стадии не производится контроль погрешностей формы. Контроль размеров производится при помощи штангенциркуля точность штангенциркуля составляет 01 мм. Исходя из анализа чертежа очевидно что необходимо для контроля размеров применять более точный измерительный прибор
Таким образом в базовом технологическом процессе следует заменить указанный в базовом тех. процессе станок на многоцелевой станок с ЧПУ 2204ВМ1Ф4 а также дополнить технологический процесс необходимыми данными (выдерживаемые размеры тип и марка режущего инструмента) правильно выбрать контрольное приспособление.
5.Выбор и обоснование способов изготовления заготовок.
Материалом корпуса редуктора пневмодвигателя Крот-12 является алюминиевый сплав АЛ7 ГОСТ 1583-93. Согласно базовому технологическому процессу заготовку корпуса редуктора получают литьем в кокиль.
Отливки в кокиль имеют высокую точность размеров (12 14 квалитеты) и шероховатость поверхности отливки Ra = 5 10 мкм что позволяет уменьшить припуски на обработку резанием в 2-3 раза по сравнению с другими способами получения заготовки. Для отливок в кокиль характерна более плотная мелкозернистая структура металла что повышает их механические свойства на 15%. С учетом выбранного типа материала и массы получаемой отливки многократность использования металлической формы кокиля обеспечивает полное выполнение годовой программы выпуска.
Внутренняя конфигурация отливки должна обеспечиваться с помощью песчаных стержней. Таким образом величина припусков на внутренние поверхности образуемые на этапе получения заготовки будет увеличена по сравнению с припусками на внешние поверхности. Для полной подготовки заготовки после литья выполняется термическая обработка - кратковременное (неполное) искусственное старение так как требования по твердости изготовленной отливки не удовлетворяют условиям указанным на чертеже корпуса редуктора.
В целом данный вид литья соответствует необходимым требованиям к заготовке. Спроектируем заготовку наиболее приближенную к конфигурации детали и сравним ее с базовым вариантом.
К заготовке отливаемой в кокиль предъявляются ряд определенных требований:
–для легкости разъема и извлечения из формы отливка должна иметь минимум выступающих элементов и уклоны в сторону плоскости разъема;
–для создания условий нормального заполнения формы толщина стенок должна быть не менее 3 4 мм.
Определим основные параметры проектируемой заготовки:
класс размерной точности отливки – 8;
степень коробления – 3;
степень точности поверхностей – 8;
шероховатость поверхности Ra 10;
класс точности массы – 6;
литейные уклоны - 2 радиусы - 2 мм;
вес готового изделия – 2615 кг.
С учетом всех предложений к проектированию формы отливки спланируем чертеж заготовки.
Предлагается сравнить имеющийся способ получения заготовки (см. рис. 2б) с базовым (см. рис.2а).
Рис.2 Эскизы заготовок.
Расчет стоимости заготовки при литье в кокиль по базовому и проектируемому вариантам произведем по формуле [4]:
- коэффициенты зависящие от класса точности группы сложности массы материала и объема производства заготовок;
q - масса готовой детали = 2615 кг;
Sотх - цена за одну тонну отходов = 56740 руб;
Все перечисленные значения принимаем из таблиц 2.6 2.11 Шкред для отливки из алюминиевого сплава 4-го класса точности 3-ей группы серийности при массе отливки 3 10 кг.
Имеем: Сi=112000 руб .
Таким образом учитывая что масса заготовки равна кг стоимость заготовки при литье в кокиль по проектируемому варианту равна:
При оценке получения отливки в кокиль по базовому варианту необходимо учесть что масса заготовки тогда будет равна кг. Тогда стоимость заготовки по базовому варианту равна:
Экономические расчеты по выбору варианта получения заготовки корпуса редуктора приведем в табл. 3.
Результаты сравнения способов получения заготовки.
Проектируемый вариант
Масса готовой детали кг
Коэффициент использования материала
Стоимость заготовки руб.
*- Экономия (+) или перерасход (-) по второму варианту по сравнению с первым.
Таким образом литье в кокиль по проектируемому варианту целесообразней.
6.Назначение технологических баз.
С целью получения заданной точности и экономичности обработки необходимо соблюдать принцип совмещения технологических баз с конструкторскими и измерительными что позволит исключить погрешность базирования и выполнить размеры с использованием полного поля допуска установленного конструктором. С целью уменьшения погрешностей в расположении поверхностей следует в качестве баз на всех операциях использовать одни и те же поверхности.
Составим эскиз детали корпус редуктора на котором все основные поверхности пронумеруем цифрами (см. прил.)
На первой операции производится обработка основания (пов. 1) и двух отверстий (пов. 9). Базирование осуществляется по поверхности 2 (установочная база) 32 (направляющая база) 4 (опорная и измерительная база).
На второй операции и последующих операциях деталь базируется по поверхности 1 (установочная база) и поверхности двух технологических отверстий 9 (направляющая и центрирующая базы опорная база).
На последующих операциях когда невозможна обработка детали по указанным схемам деталь базируется по поверхностям 2 или 3 (установочная база) 1 или 4 (направляющая база) и 32 (опорная база).
Выбрав такие базы сведем погрешность базирования к минимуму обеспечим снятие равномерного припуска и сведем к минимуму количество операций.
7.Выбор способов обработки отдельных поверхностей.
Некоторые виды поверхностей могут быть обработаны различными способами. Выбор того или иного вида обработки на производстве зависит преимущественно от наличия оборудования оснастки типа и формы организации производства и др. Выбранный метод обработки должен учитывать требования чертежа точность шероховатость массу конфигурацию и жесткость детали метод получения заготовки и т.д.
Согласно чертежу и техническим требованиям к детали обработке подвергаются все поверхности корпуса за исключением наружных боковых (4 32 33).
На первой операции производится обработка технологических баз корпуса: основание пов. 1 два технологических отверстия пов. 9. Точность основания не задана в явном виде поэтому о ней можно судить лишь косвенно по размерам от основания наименьшая точность таких размеров соответствует 8-9 квалитетам. Шероховатость основания Ra 10. Точность технологических отверстий также должна соответствовать 8 квалитету. Согласно нормативной литературе (Карта 724 поз. 1 инд. б. 12) таких требований по точности можно добиться путем фрезерования основания сверления и развертывания отверстия.
Аналогично произведем анализ всех поверхностей данные сводим в таблицу 4
Способы обработки поверхностей и технологической базы.
Номера и наименование обрабатываемой поверхности
Вид механической обработки
Номер базовой поверхности
- Два технологических отверстия
Сверление и развёртывание
– левый торец корпуса
– правый торец корпуса
– отверстие для установки уплотнения
Растачивание (получистовое и чистовое)
– отверстие под подшипник
(получистовое и чистовое)
– паз под размещение шестерен редуктора
– глухое отверстие под подшипник
– маслоотводящее отверстие
24 – крепежные отверстия
– отверстие для установки втулки
Сверление развертывание
– отверстие для установки
– крепежные отверстия
Сверление и нарезание резьбы
– маслоподводящее отверстие
– крепежное отверстие под масленку
Зенкование нарезание резьбы
– 5 крепежных отверстий
– 4 крепежных отверстия
8.Разработка маршрута механической обработки детали.
Цель разработки технологического маршрута обеспечение наиболее рационального процесса обработки детали заданной точности и качества. При этом указывается содержание и последовательность выполнения технологических операций.
Анализ типовых технологических процессов корпусных деталей показывает что после выполнения заготовительных операций механическую обработку выполняют как правило в следующей последовательности: первоначально осуществляют подготовку баз для последующего использования при основном базировании. При этом возможны две схемы базирования детали на последующих операциях: по трем координатным плоскостям и по двум отверстиям и перпендикулярной им плоскости.
В данном процессе механической обработки основными операциями являются операции фрезерования сверления зенкерования расточка и т.д. Окончательными будут выполняться слесарные операции.
Маршрут механической обработки корпуса редуктора пневмодвигателя разработаем руководствуясь следующими данными:
–метод получения заготовки;
–требования к точности и шероховатости;
–принципа единства и совмещения технологических баз.
С учетом принятых способов обработки поверхностей и рекомендаций литературы [17] составим эскизный вариант маршрута обработки детали (табл.2.3).
Укрупненный технологический маршрут изготовления корпуса пневмодвигателя.
№ операции и пози-ции
Название и содержание операции
Эскиз базирование примечание
Фрезеровать основание пов. 1
Сверлить 2 технологических отверстия отв. пов. 9
Развернуть 2 технологических отверстия отв. пов. 9
Фрезеровать торец корпуса полость углубление 35*14
Расточить начерно отверстия 45 47 52 40согласно эскизу.
Расточить начисто отверстия 45 47 52 40согласно эскизу.
Подрезать фаски согласно эскизу
Сверлить 5 сквозных отверстий в торце корпуса по программе.
Фрезеровать торец корпуса пов. 3
Фрезеровать 2 кольцевые канавки по программе
Фрезеровать паз под стопорный элемент
Сверлить 4 крепежных отверстия.
Нарезать резьбу в 4-х крепежных отверстиях.
Сверлить отверстия 17 27 согласно эскизу
Зенкеровать отверстия 22 30 согласно эскизу
Развернуть отверстия 18 28 окончательно согласно эскизу.
Сверлить маслоотводящее отверстие 9 пов. 21
Сверлить сквозное отверстие 11
Сверлить отверстие 4 на длину 46 согласно эскизу
Сверлить последовательно 4 отверстия 41 под резьбу М5 согласно эскизу
Зенковать фаски согласно эскизу
Нарезать резьбу М10 в маслоотводящем отверстии
Нарезать резьбу М12 согласно эскизу
Нарезать резьбу М5 согласно эскизу.
Фрезеровать углубление 37*8 по программе.
Сверлить 2 отверстия под крепежный элемент
Сверлить сквозное отверстие 11
Сверлить отверстие 4 на длину 46
Зенковать фаски по программе
Нарезать резьбу М4 согласно эскизу
Сверлить сквозное отверстие 7
Сверлить отверстие ступенчатое
Нарезать резьбу под масленку
Сверлить отверстие сквозное 13
Сверлить отверстие сквозное
9.Выбор оборудования.
При выборе оборудования необходимо чтобы металлорежущие станки отвечали ряду требований:
–возможность достижения заданной точности обработки поверхностей
–соответствие рабочей зоны станка габаритам обрабатываемой детали;
–соответствие мощности жесткости и кинематических возможностей станка режимам резания;
–соответствие производительности станка заданной годовой программе выпуска.
Исходя из того что для большинства современных производств выгодно использовать широкопрофильное легко перестраиваемое и точное оборудование необходимым является использование многооперационных станков с ЧПУ.
С учетом вышеприведенных требований к оборудованию окончательно выбираем многоцелевой сверлильно-фрезерно-расточной станок с ЧПУ 2204ВМ1Ф4 т.к. позволяет получить максимальную концентрацию операций. Опишем характеристику выбранного станка.
Техническая характеристика станка 2204ВМ1Ф4:
Размеры рабочей поверхности стола и спутника мм:
Диаметр поворотной части стола мм:
Наибольшие координатные перемещения мм:
Наибольшая масса обрабатываемой детали кг
Конус шпинделя по ГОСТ 15945-70
Частота вращения шпинделя
Рабочая подача шпиндельной головки и стола
Скорость быстрого перемещения
Наибольший допускаемый крутящий момент на шпинделе
Наибольшее усилие подачи Н
Емкость инструментального магазина
Мощность электродвигателя привода вращения шпинделя кВт
Количество управляемых координат:
с одновременным перемещением
Дискретность задания геометрических размеров мм:
по линейным координатам
по круговым координатам
Габаритные размеры мм:
Многоцелевой станок мод. 2204ВМ1Ф4 предназначен для обработки корпусных деталей средних размеров с 4-х сторон без переустановок по программе. На станке данной модели можно производить получистовое и чистовое фрезерование различных видов поверхностей фрезами всех типов сверление зенкерование развертывание растачивание нарезание резьбы метчиками в деталях из стали чугуна цветных металлов и пластмасс.
Класс точности станка В по ГОСТ 8-77.
Категория качества станка – высшая.
Станок оснащен устройством автоматической загрузки и выгрузки изделий предназначенным для установки заготовки на сменные столы (паллеты) и последующей автоматической загрузкой столов на станок а также их выгрузки со станка после окончания обработки. Использование сменных столов позволяет совместить загрузку или выгрузку обработанных изделий с работой станка что существенно сокращает холостые простои повышает эффективность его использования и производительность.
Управление станком – от универсальной комплексной системы ЧПУ “Размер 2М-1300”. Тип системы числового программного управления – комбинированная.
Обработка ведется последовательно различными инструментами в автоматическом цикле поэтому используем его на всех дальнейших операциях.
10.Выбор режущего и вспомогательного инструмента.
Режущий инструмент должен позволять реализовать принятый метод обработки детали на данном оборудовании обеспечивая при этом требуемую точность и шероховатость поверхностей детали при наиболее рациональных и производительных режимах обработки. Для выбора режущего и вспомогательного инструмента исходными данными являются :
а)обрабатываемый материал;
б)величина шероховатости поверхности;
г)присоединительные размеры шпинделя станка.
Произведем выбор режущего и вспомогательного инструмента согласно сборникам.
Рассмотрим операцию 010 – комплексную на ОЦ с ЧПУ. На данной операции производится фрезерование основания корпуса редуктора и отверстий 9: сверление и развертывание. Конец шпинделя станка имеет метрический конус 50 ГОСТ15945-70. Таким образом вспомогательный инструмент должен иметь соответствующий наружный конус.
Согласно рекомендациям прил. 1-4 [12] для цветных сплавов из быстрорежущих сталей следует отдавать предпочтение инструменту из Р6М5 или Р18 для инструмента с твердосплавными пластинами использовать пластины из ВК 4 ВК 6 ВК 8. Исходя из этого выбираем по [3] фрезы сверла и др. инструмент - из Р6М5 или Р18.
Для первой позиции (фрезерование торца пов. 1) по [3] выбираем фрезу концевую 63 коническим хвостовиком конус Морзе 4. Обозначение фрезы: Фреза 2223-0071 ГОСТ17026-71. Вспомогательный инструмент – Втулка 50-5 ОСТ2 П12-7-84.
Для второй позиции (сверление 2 отверстий пов. 9) выбираем сверло Р6М5 42 Сверло 2300-0843 ГОСТ19543-74. Вспомогательный инструмент - Патрон 2-50-4.2-90 ГОСТ 26539-85
Для третьей позиции (развертывание 2-х отверстий пов. 9) принимаем развертку Р6М5 5 Развертка 2363-0721 ГОСТ11172-70. Вспомогательный инструмент - Патрон 2-50-5-90 ГОСТ 26539-85.
Аналогично выбираем инструмент на остальные операции и позиции и сводим в таблицу согласно тех. процесса.
№ операции и позиции
Приспособления и инструмент
Фрезеровать основание пов. 1
Фреза 2223-0071 ГОСТ17026-71
Втулка 50-5 ОСТ2 П12-7-84
Сверло 2300-0843 ГОСТ19543-74
Развернуть 2 технологических отверстия отв. пов. 9.
Развертка 2363-0721 ГОСТ11172-70
Патрон 2-50-5-90 ГОСТ 26539-85
Фрезеровать торец корпуса углубление
Фреза 2223-0015 ГОСТ 17026-71
Втулка 50-4 ОСТ 2 П12-7-84
Расточить отверстия 45 47 52 40 начерно
Резец 2142-0102 ВК8 МН 622-84
Борштанга 6300-0332 МН 2645-81
Втулка 50-4 ОСТ2 П12-7-84
Расточить отверстия 45 47 52 40 начисто.
Резец 2145-0104 ВК8 МН 623-84
Сверлить 5 отверстий в торце корпуса по программе
Сверло 2300-0858 ГОСТ 19543-74
Патрон 2-50-6-90 ГОСТ 26539-85
Фрезеровать кольцевые канавки по программе (пов. )
Фреза 2234-0160 ГОСТ 6648-79
Патрон 2-50-7-90 ГОСТ 26539-85
Фреза 2220-0521 ГОСТ 16225-81
Сверлить 4 отверстия
Сверло 2300-0848 ГОСТ 19543-74
Метчик 2629-2285 ГОСТ 17928-72
Втулка 6143-0103 ГОСТ 15936-70
Сверло 2310-0392 ОСТ 2И20-6-80
Втулка 50-3 ОСТ2 П12-7-84
Развернуть отверстие окончательно
Развертка 2363-0843
Втулка 50-2 ОСТ2 П12-7-84
Фрезеровать отверстия (диаметры 27 30)
Фреза 2223-1311 ГОСТ 23247-78
Развернуть отверстие
Развертка 2363-0865 ГОСТ19268-73
Сверлить маслоотводящее отверстие
Сверло 2300-0888 ГОСТ 19543-74
Патрон 2-50-9-120 ГОСТ 26539-85
Нарезать резьбу в маслоотводящем отверстии
Метчик 2629-2057 ГОСТ 17928-72
Патрон 2-50-10-120 ГОСТ 26539-85
Сверлить 4-е отверстия по программе
Сверло 2300-0842 ГОСТ 19543-74
Патрон 2-50-4-90 ГОСТ 26539-85
Нарезать резьбу по программе
Метчик 2629-2021 ГОСТ 17928-72
Фрезеровать паз по программе
Сверло 2300-0833 ГОСТ 19543-74
Зенковка 2353-0108 ГОСТ 14953-80
Сверлить 4 отверстия по программе
Сверлить сквозное отверстие
Сверло 2300-0868 ГОСТ 19543-74
Патрон 2-50-7-120 ГОСТ 26539-85
Сверло 2310-0390 ОСТ 2И20-6-80
Патрон 2-50-10-150 ГОСТ 26539-85
Сверло 2301-2866 ГОСТ 19546-74
Сверло 2300-0816 ГОСТ 19543-74
Патрон 2-50-2-90 ГОСТ 26539-85
Фреза 2234-0355 ГОСТ 9140-78
Патрон 2-50-6-120 ГОСТ 26539-85
Метчик 2629-2027 ГОСТ 17928-72
11.Выбор приспособлений
и измерительного инструмента
Каждая технологическая операция механической обработки выполняется с использованием станочных приспособлений. Использование приспособлений способствует повышению производительности и точности обработки расширению технологических возможностей оборудования повышению безопасности работы.
На операции 010 (многоцелевая) при обработке основания и двух технологических отверстий деталь базируется по необрабатываемым поверхностям. Корпус устанавливается на боковую поверхность и фиксируется при помощи упоров и прижима.
Для упрощения технологического процесса принятая схема базирования с операции 020 по 030 включительно выполняется при использовании одного приспособления - спутника с базированием на 2-х пальцах (один срезанный) и прижимом с поверхности 4. При переустановке корпуса из-за мягкости материала необходимо заново обрабатывать базы поэтому выгодно использовать приспособление - спутник когда деталь проходит все этапы обработки при данной схеме базирования без переустановки. Такая схема позволяет использовать многопозиционную обработку с применением вращающегося стола. В дальнейшем необходимо точно спроектировать конструкцию приспособления и рассчитать его точность.
При изготовлении корпуса редуктора пневмодвигателя согласно проектируемому технологическому процессу необходимо производить контроль следующих параметров:
Все линейные размеры проставленные на чертеже выполняются с точностью до десятых долей миллиметра. Контроль данных размеров можно производить стандартными измерительными инструментами: Линейка 0-300 ГОСТ 427-75; Штангенциркуль ШЦ-III ГОСТ 166-89 Глубиномер ГИ-100 ГОСТ 7661-67.
Диаметральные размеры выполняются с точностью до десятых долей миллиметра. Контроль этих размеров также можно производить стандартными измерительными инструментами: Нутромер ГОСТ 9244-75;
Контролировать чистоту шероховатости после обработки
Контроль производится при помощи образцов шероховатости поверхности ГОСТ 9378 - 75 или черт. 199 - 0214.
Для контроля резьб М6 - 7Н М10 - 7Н применяется пробка резьбовая 8221 - 3036 - 7Н; ГОСТ 17758 - 72.
12.Расчет припусков промежуточных размеров и допусков окончательная корректировка чертежа заготовки.
Требуется рассчитать припуски на обработку и промежуточные предельные размеры на поверхность корпуса редуктора пневмодвигателя расчетно-аналитическим методом.
Величина промежуточного припуска по этому методу должна быть такой чтобы при его снятии устранялись дефекты поверхностного слоя которые возникли на предшествующих переходах а также погрешности установки обрабатываемой заготовки возникающие на выполняемом переходе.
Заготовка представляет собой отливку массой 3271 кг. Технологический маршрут обработки отверстия 45Н7 состоит из двух стадий обработки: получистового чистового растачивания выполняемых при одной установке обрабатываемой детали.
Корпус редуктора пневмодвигателя базируется на столе станка по предварительно обработанным плоскости основания отливки пов. 1 и двум технологическим отверстиям пов. 9 . Прижим заготовки осуществляется призмой по внешней части корпуса.
Согласно ГОСТ 26645-85 после первого технологического перехода для цветных металлов и сплавов при расчете величину h необходимо исключить. Поэтому для получистового и чистового растачивания указываем только величину Rz (50 и 20 мкм соответственно).
Рассчитаем величину и припусков. Суммарное значение пространственных отклонений для заготовки данного типа определим по формуле .
Коробление отверстия следует учитывать как в диаметральном так и в осевом его сечении. Тогда имеем где
- удельная кривизна заготовок на 1 мм длины;
- диаметр и длина обрабатываемого отверстия соответственно.
Учитывая что суммарное смещение отверстия в отливке относительно наружной ее поверхности представляет геометрическую сумму в двух взаимно перпендикулярных плоскостях получаем
где - допуски на размеры 1036 и 29 по классу точности соответствующий данной отливке [4 табл.2.4]
Тогда суммарное значение пространственного отклонения заготовки
Остаточное пространственное отклонение после чернового растачивания
Известные нам данные вносим в таблицу
Элементы припуска мкм
Расчетный припуск 2Zmin мкм
Предельный размер мм
Предельные значения припусков мкм
Погрешность установки при черновом растачивании
Так как для получения 45 деталь устанавливается в приспособление после обработки основания и при этом деталь не переустанавливается то погрешность базирования детали отсутствует. Таким образом погрешность базирования состоит только из погрешности закрепления.
Погрешность закрепления при установке в зажимное приспособление при базировании по предварительно обработанной плоскости и технологическим отверстиям согласно табл. 4.13 [4] принимаем равной 120 мкм.
Остаточная погрешность установки при чистовом точении . Так как получистовое и чистовое точение производится в одной установке то . Тогда мкм.
Расчет минимальных значений припусков произведем по формуле
Минимальный припуск под растачивание:
Для чистового растачивания
Для получистового растачивания
Значение допуска определяем по таблице согласно допуску на размер. Таким образом для чистового фрезерования для получистового фрезерования для заготовки .
Наименьший предельный размер для
чистового растачивания мм
получистового растачивания мм
Рассчитаем максимальные и минимальные предельные значения припусков:
Для чистового растачивания
Для получистового растачивания
Рис.3 Схема расположения припусков.
Припуски на поверхности корпуса
Наименование операции поверхности и их обозначение (см. прил.)
Величина припуска мм
13.Проектирование механических операций.
Разработав маршрут подобрав оборудование и оснастку приступаем к детальной проработке технологических операций. В общем случае содержание операций устанавливают наличием переходов которые могут быть выполнены на выбранном типе станка.
Рассмотрим подробно проектирование операции 020 – многоцелевая.
Согласно технологическому маршруту эта операция осуществляется с одного установа - выполняется обработка 2-х торцов и расположенных вдоль корпуса редуктора отверстий. После окончания обработки с одного торца поворотный стол осуществляет поворот на 180.
Операция включает в себя позиций:
Данная операция выполняется на горизонтальном сверлильно-фрезерно-расточном станке мод. 2204ВМ1Ф4. Базирование осуществляется по предварительно обработанным основанию корпуса редуктора пов. 1 и двум технологическим отверстиям пов. 9 прижим производится с пов. 4.
При данной схеме выполнения операции и на принятом станке можно будет достигнуть заданную точность и шероховатость обрабатываемых поверхностей.
14.Расчет режимов резания сил резания
проверка соответствия выбранного оборудования.
Расчет режимов резания для проектируемых операций начинают с изложения исходных данных:
–форма и размеры обрабатываемой поверхности;
–марка и технические свойства материала;
–требования к точности и шероховатости обрабатываемой поверхности;
–способы базирования и закрепления заготовки.
При определении режимов резания используют нормативные данные и рекомендации изложенные в литературе [12]. Результаты режимов резания сводим в таблицу 2.7.
Рассмотрим подробно определение режимов резания на фрезерование основания (переход 1 операция 010).
Произведем расчеты согласно нормативной литературе 12.
Обрабатываемый материал – Сплав АЛ7 ГОСТ 1583-93
Режущий инструмент: фреза концевая 63 Р6М5
Характер заготовки: отливка в кокиль
Припуск на фрезерование основания – 16 мм.
Расчет режимов резания для фрезерования основания:
Определение количества стадий обработки.
По карте 72 выбираем составляющие показатели количества стадий обработки для фрезерования концевой фрезой основания корпуса в зависимости от:
твердости обрабатываемого материала
отношения вылета фрезы к диаметру
отношении ширины фрезерования к диаметру фрезы
Таким образом показатель количества стадий обработки для фрезерования равен
Согласно карте 72 лист 4 поз. 1 инд. б требуемая точность может быть достигнута за одну стадию обработки.
Выбор глубины резания.
Выбор величины глубины резания определяем по карте 75 поз. 8 инд. ж:
Из чего следует что достаточно обработки основания корпуса за один рабочий ход.
Табличное значение подачи на зуб равно (карта 79 поз. 33 инд. ф). Так как условия работы отличаются от нормативных произведем корректировку величины подачи на зуб с учетом поправочных коэффициентов (карта 82) в зависимости от:
материала режущей части фрезы
отношения фактического числа зубьев к нормативному
С учетом поправочных коэффициентов подача принимает значение
Значение подачи допустимой по шероховатости обработанной поверхности (карта 83 поз. 21 инд. в) .
Окончательно принимаем минимальное значение .
Выбор скорости и мощности резания.
Согласно карте 86 поз. 37 инд. д. карте 86 поз. 37 инд. е. .
Поправочные коэффициенты для корректировки табличных значений скорости и мощности резания для измененных условий работы находим согласно карте 86 в зависимости от:
группы обрабатываемого материала
материала режущей части фрезы
периода стойкости режущей части фрезы
отношения фактической ширины фрезерования к нормативной
состояния поверхности заготовки
Окончательно получаем:
Частота вращения шпинделя .
По паспорту станка принимаем ближайшее значение .
С учетом этого фактическая скорость резания равна
Фактическая мощность резания равна
Определение величины силы резани.
По карте 88 поз. 9 инд. ж радиальная составляющая силы резания равна .
Согласно карте 88 поз. 9 инд. з касательная составляющая силы резания .
Поправочные коэффициенты для измененных условий работы в зависимости от:
твердости обрабатываемого материала
Таким образом фактические величины составляющих сил резания равны:
Проверка соответствия выбранного оборудования:
Проведем проверку мощности резания по мощности станка:
NСТ=63кВт – мощность электродвигателя привода вращения шпинделя по паспорту станка;
Аналогичным путем определяем режимы резания для сверления и развертывания двух отверстий результат вычислений заносим в табл. 2.7.
Фрезерование основания
Развертывание отверстий
Аналогично рассчитываются режимы резания и для остальных операций технологического процесса изготовления корпуса редуктора пневмодвигателя. Результаты расчетов заносятся в карты технологических переходов представленные в Приложении.
15.Аналитическое прогнозирование точности и качества обработки поверхностей.
На точность обработки в общем случае оказывает влияние комплекс взаимонезависимых факторов:
–невыполнение принципов совмещения и постоянства баз
–погрешности связанные с неточностью изготовления инструмента ;
–погрешности настройки станка ;
–погрешности установки заготовки в приспособлении ;
–погрешности связанные с температурными деформациями технологической системы СПИД-.;
–погрешности формы связанные с геометрическими неточностями оборудования ;
–рассеивание размеров связанное с методом обработки .;
–недостаточность припусков на обработку.
Проверим обеспечивается ли точность размера при фрезеровании пов.3 на операции 030.
Условие обработки без брака Тd где
Допуск на выполняемый размер Td = 10 мм.
- суммарная погрешность механической обработки
где - погрешность связанная с деформациями системы СПИД мкм. Для принятых режимов обработки g очень мала так как обрабатываемый материал имеет твердость НВ 70..90.
- погрешность установки для принятой системы обработки = 0 так как технологическая база совпадает с измерительной что свидетельствует о удачно выбранном виде базирования заготовки
- погрешность связанная с неточностью изготовления и износом режущего инструмента u=6 мкм [11] (стр.74 табл.29).
- погрешность связанная с температурными деформациями технологической системы СПИД мкм. Принимаем Т = 0 т.к. за время операционного цикла и хорошей податливости заготовки инструмент не успевает разогреться до величин при которых может значительно изменить свои размеры.
- погрешность связанная с геометрическими неточностями оборудования. Ф = 10 мкм [11] (стр.23).
Таким образом суммарная погрешность (мкм) или 0028 что 01 мм.
Вывод: на основании проведенного расчета очевидно что выполняется условие обработки без брака.
Важнейшим показателем определяющим надежность и долговечность изделия является качество поверхностей деталей и машин которое определяется параметрами шероховатости волнистости твердости и др. Основным показателем является параметр шероховатости.
Проведем аналитическое прогнозирование соответствия величины шероховатости полученной согласно проектируемому технологическому процессу изготовления корпуса редуктора при фрезеровании основания изделия пов. 1 на операции 010 – многоцелевой шероховатости поверхности на чертеже Ra = 10 мкм.
По формуле [6 табл. 5 стр. 104]:
где - подача на зуб
- глубина фрезерования
Таким образом при фрезеровании основания корпуса редуктора пневмодвигателя (пов.1) требуемая шероховатость обеспечивается так как 02 мкм 10 мкм.
16.Техническое нормирование.
Техническое нормирование служит инструментом с помощью которого определяют все затраты связанные с изготовлением изделия то есть его себестоимость. Оно служит основой для расчета зарплаты основных и вспомогательных рабочих а также при проектировании нового производства.
Штучное время для операции 010 – многоцелевая будет складываться из штучного времени на фрезерование основания сверление и развертывание двух технологических отверстий. Для нахождения нормы штучного времени воспользуемся справочной литературой [12].
Норма штучного времени определяется по следующей формуле:
- время цикла автоматической работы станка по программе;
- вспомогательное время;
- время на организационное и техническое обслуживание рабочего места отдых и личные потребности.
Время цикла автоматической работы станка по программе складывается из основного времени автоматической работы станка по программе и машинно-вспомогательного времени на автоматическую смену инструмента .
Основное время автоматической работы станка по программе равно
- длина обрабатываемой поверхности (согласно чертежу);
- длина врезания и перебега.
Используя данные табл. произведем расчеты и внесем их в табл. .
Определим машинно-вспомогательного времени на выполнение автоматических вспомогательных ходов.
Исходя из условий минимизации холостых перемещений и соблюдения техники безопасности расстояние от точки «0» до точки «1» выбрано равным или . При фрезеровании второй половины основания корпуса фреза перемещается на величину с подачей холостого хода . Время холостых ходов при сверлении и при развертывании отверстий будет равно. Расстояние от точки «0» до точки «1» равно (). После обработки первого отверстия инструмент перемещается на величину . По окончании обработки второго отверстия для возвращения в точку «0» инструмент должен переместиться на расстояние или .
Таким образом машинно-вспомогательное время на выполнение автоматических вспомогательных ходов и технологические паузы равно:
Определим машинно-вспомогательное время на автоматическую смену инструмента. Для данного станка время при повороте револьверной головки на одну позицию составляет . Для цикла обработки детали необходимо произвести трижды смену инструмента с поворотом револьверной головки на одну позицию. Суммарное время на автоматическую смену инструмента составит .
Вспомогательное время складывается из составляющих:
- вспомогательное время на установку закрепление открепление и снятие детали. (ч.1 карта 13 поз. 44 инд. д. карта 13 поз. 5 инд. е.)
- вспомогательное время связанное с операцией определим по ч. 1 карте 14 поз. 1 4 6 инд. б.: .
- вспомогательное время на произведение контроля
Итого получаем что .
Время на организационное и техническое обслуживание рабочего места отдых и личные потребности приведено в процентах от оперативного времени (ч.1 карта 16 поз. 20) .
Учитывая полученные данные окончательно имеем
Аналогично нормируем все операции технологического процесса. Данные о нормах основного и штучного времени сведены в таблицу 2.9.
17.Проектирование схем технологических наладок оборудования.
Приведем схему технологической наладки для операции 020 – фрезерование торца и полости корпуса растачивание системы отверстий подрезание фасок сверление отверстий в торце корпуса под крепежный элемент.
Исходными данными при проектировании наладки являются:
Название операции – многоцелевая.
Станок на котором выполняется операция – многоцелевой 2204ВМ1Ф4.
Используемое приспособление – фрезерное.
Режущий инструмент: см. п. 2.10
Конструкторская часть
1.Исходные данные для проектирования станочного приспособления.
Исходными данными для проектирования приспособления являются:
–чертежи детали и заготовки с указанием требований к ним;
–технологический процесс выполнения операции разработанный применительно к условиям среднесерийного производства;
–операционные эскизы с указанием промежуточных и окончательных размеров требований к качеству поверхностей;
–годовая программа выпуска изделий: N=2500шт.
Обработку предполагается производить на станке – 2204ВМ1Ф4.
Заготовка детали - отливка из алюминиевого сплава АЛ7 ГОСТ 1583 - 93. Исходя из анализа чертежа поверхности 17 18 41 не обрабатываются и могут служить черновыми базами каковыми и являются на операции 010. На операции 010 подготавливается чистовая технологическая база пов.1 и два отверстия базирования. На операциях 020 и 030 при получении основных элементов детали схема базирования одинакова поэтому предлагается разработать приспособление для этих операций.
2.Выбор типа приспособления
Пользуясь рекомендациями ЕСТПП выбираем подходящий тип станочного приспособления в зависимости от периода производства изделий Тп и коэффициента загрузки:
Кз= Nоп t ш-кFп где:
Nоп - число повторений операций в месяц;
t ш-к – штучно-калькуляционное время;
Fп -100 - месячный фонд времени работы приспособления.
Число повторений операций в месяц определяем по формуле:
N=2500 штгод –годовая программа выпуска.
По графику [8 рис.3] подходящим типом станочного приспособления является УСП.
3.Выбор схемы станочного приспособления и конструкции установочных деталей.
Схема приспособления во многом определяется построением технологической операции и требованиям к ее производительности.
Согласно технологическому процессу ведется многоинструментальная обработка на многоцелевом станке с ЧПУ. Приспособление должно устанавливаться на плиту поворотного приспособления и фиксироваться в определенном положении. При базировании заготовку следует лишать шести степеней свободы. Заготовка корпуса пневмодвигателя после операции 010 имеет уже обработанную поверхность 1 которая и будет служить установочной базой. В качестве направляющих и опорных баз целесообразно использовать обработанные отверстия под монтаж корпуса пневмодвигателя где в технологическом процессе намерено была проведена дополнительная обработка отверстий развертыванием и тем самым повышена точность до Н7. Повышение точности изготовления отверстий служит для уменьшения погрешности установки что тем самым сильно влияет на общую точность изделия в целом.
Рис.4 Схема базирования заготовки в приспособление.
В качестве установочного элемента выбираем плиту УСП. Направляющими элементами являются установочный и срезанный пальцы. Прижим осуществляется с поверхности 4.
Деталь устанавливается в приспособление после обработки основания на операциях 020 и 030 деталь не переустанавливается. Поэтому погрешность базирования детали отсутствует погрешность базирования состоит из погрешности закрепления.
4.Расчет сил закрепления заготовки.
При обработке корпуса пневмодвигателя на фрезерных позициях операции 020 наиболее подходящий тип схемы закрепления заготовки от смещения предложен в [15 стр.69 рис.40]. Эта расчетная схема применима для случая установки на два пальца и перпендикулярную к ним плоскость.
Рис.5 Схема расчета сил закрепления заготовок от смещения
При достаточной жесткости опор и при наличии зажиного устройства второго типа закрепления Q определим как: где
- коэффициент запаса;
- коэффициенты трения заготовки с установочными и зажимными элементами;
Из условий обработки и предохранения базового отверстия от вмятин ромбического пальца сила резания должна восприниматься силой трения на базовой плоскости заготовки т.е. пальцы должны быть полностью загружены. В данном случае f1= f2=016 - коэффициент трения.
Коэффициент запаса k найдем по рекомендациям [15 стр.83].
k=k0 k1 k2 k3 k4 k5 k6
k0-гарантированный коэффициент запаса при зажиме k0=18.
k1-12 - коэффициент учитывающий неравномерность снимаемого припуска.
k2-17 [15 стр.84 табл.12] - коэффициент учитывающий изменение сил резания.
k3-12 - коэффициент учитывающий динамический характер нагрузки при прерывистом резании.
k4-1 - коэффициент характеризующий зажимное устройство с точки зрения непостоянства сил закрепления.
k5-1 - коэффициент характеризующий удобство расположения рукояток в ручных зажимных устройствах.
k6 - 15 - коэффициент учитывающий только при наличии моментов стремящихся повернуть заготовку.
Итого: k=181217121115=66
Из операции 020 выбираем позицию с наибольшей силой резания - позиция 1.
Рx - определяем как: Рx =05 Рz [7 стр.292]
Рx =051550 (Н) откуда
5.Выбор конструкции и размеров зажимных устройств
Основное назначение зажимных устройств станочного приспособления - обеспечение надежного контакта заготовки с установочными опорами и предупреждение смещений и вибраций заготовки.
Зажимные устройства приспособления должны:
–быть простыми по конструкции удобными и надежными;
–не препятствовать подводу и отводу инструмента;
–не деформировать заготовки;
–не сдвигать заготовки при закреплении;
–обеспечивать закрепление с минимальными затратами времени;
–обеспечивать равномерный зажим.
В качестве зажимного устройства из узлов УСП выбран прихват 7012-2178 ГОСТ 26680-76. Преимущество данного вида прихвата в применении центрирующей призмы для прижима по цилиндрической поверхности. Это устройство осуществляет как прижим так и повышает устойчивость заготовки.
Рассчитаем достаточна ли сила зажима выбранного устройства. Из теории «деталей машин» найдем минимальный допустимый диаметр шарнирных болтов стягивающих заготовку. Сила стяжки болтов - Q.
Сила передаваемая одному болту: где i- число болтов т.е. i=2.
Расчетная нагрузка на болт:
где коэффициент зависящий от упругих свойств входящих в соединение частей; -усилие затяжки одного болта Н.
Практически можно считать тогда ориентировочно для прокладки из меди - 035. Тогда общее уравнение: i
где F-площадь сечения болтов по внутреннему диаметру резьбы м2.
[p] - допускаемое напряжение при растяжении МПа.
При выборе болта М16 - его сечение F=141 см2=141*10-4 м2 отсюда
что вполне допустимо.
6.Расчет погрешности закрепления
При закреплении из-за контактных деформаций в стыке базовой поверхности с опорной поверхностью заготовка опускается. Изменяется расстояние между измерительной базой и осью инструмента. Появляется погрешность закрепления величину которой определим из выражения [7 с.52 табл.26]:
з = (КRz Rz + KHBHB + C) (Q10)m 1Fm
где Rz- показатель шероховатости по ГОСТ 2789-73 Rz = 3.6 * 4 = 14.4 мкм;
НB - твёрдость материала заготовки НВ 80;
F - расчётная площадь контакта заготовки с опорами F = 116 см2 ;
КRz KHB C - коэффициенты которые при обработке заготовок из алюминия соответственно равны: 0016; -00045 и (0776 + 0053*F).
Подставим значения в расчётную формулу:
з = (0016144 - 0004580 + 0776 + 0053116) (1598410)06 111606
7.Описание конструкции и принципа работы
станочного приспособления
Схема проектируемого приспособления довольно проста не вызывает затруднений при его эксплуатации. Станочное приспособление предназначено для крепления и правильного базирования детали типа "Корпус редуктора" на многоцелевом сверлильно-фрезерно-расточном станке 2204ВМ1Ф4.
На предварительной операции 010 в корпусе редуктора пневмодвигателя обрабатываются основания и два отверстия по которым в последствии будет производиться базирование корпуса в приспособлении.
Заготовка устанавливается на два цилиндрических отверстия с параллельными осями и перпендикулярную к ним плоскость. Преимущества данной схемы базирования заключаются в простоте конструкции приспособления возможности соблюдения постоянства баз на большинстве операций технологического процесса и относительно простая передача и фиксация заготовок на поточных и автоматических линиях.
По сравнению с установкой на шесть точек эта схема обеспечивает большую доступность режущего инструмента к обрабатываемой заготовке. Станочное приспособление устанавливается на стол станка 2204ВМ1Ф4.
Базирование приспособления на столе станка производится по пальцу 2 и шпонке 18. Прижим приспособления осуществляется прижимом 15. Заготовка корпуса пневмодвигателя устанавливается на 2 пальца приспособления и накрывается вилкой 3 на которую в свою очередь накидывают шарнирный болт 8 с гайкой 7. Затем производится затяжка болта 7. Для правильного закрепления следует добавить что прижимная призма 12 должна соблюдать симметричность к своей оси.
8.Эффективность использования и стоимость технологической оснастки.
Рассчитаем стоимость приспособления S руб.по методике [9]:
где К - количество деталей в приспособлении шт.;
Ус - удельная себестоимость руб.
По спецификации к чертежу общее количество деталей в приспособлении равно 21 в том числе оригинальных - 2. Габаритные размеры приспособления не велики а его изготовление не вызовет затруднений. На основании изложенного отнесём приспособление к 1 группе сложности и будем считать что к = 2 т.е. количеству оригинальных деталей. Примем по табл. 2 [20] Ус = 12600. Тогда стоимость приспособления
S = 2 12600 = 25200 руб.
Годовая станкоемкость изготовления продукции цеха: 235000 станко-часа.
Программа выпуска: 2500 штгод.
Размер партии: 99 шт.
Тип производства – среднесерийный.
Производимое изделие: корпус редуктора пневмодвигателя “Крот-12”
Масса детали (корпус редуктора): 2615 кг.
Масса заготовки: 3271 кг.
График работы - 2-х сменный.
Исходя из массы детали и годовой программы пользуясь таблицей 3 [19] принимаем тип производства - среднесерийное.
2.Расчёт количества основного технологического оборудования
Определим количество требуемого основного оборудования [19]:
где Тс - станкоёмкость годового объёма выпуска изделий с запасными частями станкочасов;
Фз - средний действительный годовой фонд времени работы оборудования ч (принимаем равным 2030 ч.);
средний коэффициент загрузки оборудования (09) [19];
средний коэффициент использования оборудования (085) [19].
принимается 152 станка в цехе.
В том числе по участку изготовления корпуса редуктора пневмодвигателя:
Станкоёмкость операции - tс равна штучному времени на операцию.
Станкоёмкость годового выпуска корпуса редуктора пневмодвигателя с запасными частями равна:
где N - заданный объём выпуска изделий;
Кзап - коэффициент учитывающий выпуск запасных частей.
tс - станкоёмкость операции (равна штучному времени на операцию).
Учитывая что корпус редуктора пневмодвигателя «Крот-12» согласно проектируемому технологическому процессу обрабатывается на одном и том же станке получаем
принимается 2 многоцелевых станка с ЧПУ 2204ВМ1Ф4.
3.Определение состава вспомогательных служб
и участков цеха выбор оборудования.
Состав механического цеха зависит от объёма выпуска типа и формы производства.
Для среднесерийного производства требуются следующие вспомогательные службы:
-заточное отделение;
-контрольное отделение;
-мастерская для ремонта приспособлений и инструмента;
-площади для сбора и регенерации СОМЖ;
-отделение по переработке стружки;
-инструментально-раздаточная кладовая;
-термическое отделение;
-заготовительное отделение;
-цеховой склад материалов и заготовок;
-промежуточные склады.
Определим общее количество станков заточного отделения [19]:
где Sоп - количество станков основного производства оснащённых режущим инструментом общего назначения; Sон=152 шт.
- коэффициент условной производительности [19] (примем 1=15);
- коэффициент характеризующий долю МНП с механическим креплением [19]; =05.
Sсп - количество станков основного производства оснащённых специальным РИ. Sсп=0 шт.
Примем количество станков для заточного отделения равным 8 шт.
Определим количество оборудования для ремонтной базы механика. Согласно таблице 2 [19] для количества основных станков менее 300 количество основных станков ремонтной базы составляет 2% и не менее 6
Sм=0.02·152=304 следовательно принимаем Sм=6 шт.
В мастерской энергетика цеха производят чистку периодический осмотр и ремонт электродвигателей включая пропитку сушку и испытание обмотки смену подшипников перемотку и восстановление катушек восстановление контактов пусковой аппаратуры и прочие работы для поддержания в исправном состоянии оборудования освещения электродвигателей транспортных и подъемных устройств а также санитарной техники цеха. Режущим оборудованием мастерская не комплектуется.
Мастерская для ремонта приспособлений и инструмента
Определим число станков в мастерской по ремонту приспособлений [19]:
где Sмпр - расчётное число станков определяемое в процентах от обслуживаемого оборудования. Для количества станков 152 согласно [19] стр. 8 примем Sмпр=4% от Sпр
- коэффициент условий производительности 1 = 15. тогда имеем:
Sмп=004·Sпр*15=004·152·15=912следовательно принимаем Sмп =10 шт.
Отделение переработки стружки
Может комплектоваться конвейерами для переработки стружки дробилками сепараторами установками для обезжиривания и брикетировочными прессами.
Расчёт численности и состава работающих.
Состав рабочих в цехе включает следующие категории:
- производственные рабочие;
- вспомогательные рабочие;
- инженерно-технические работники (ИТР);
- младший обслуживающий персонал (МОП).
Производственные рабочие
Их количество определяется по формуле для укрупненных расчетов:
гдеОП – количество принятого производственного оборудования
ФЭ - эффективный годовой фонд времени работы оборудования в часах ФЭ = 2030 ч;
ФР - эффективный годовой фонд времени рабочего в часах ФР=1860ч;
– средний коэффициент использования оборудования =085 [19];
кМ – коэффициент многостаночного обслуживания кМ = 105.
принимается 156 производственных рабочих.
Вспомогательные рабочие
Их число определяют по формуле:
NВСП = (035 07)·NПР = 05·156 = 78 чел
принимается 78 вспомогательных рабочих.
Младший обслуживающий персонал (МОП)
NМОП = (002 003)(NПР + NВСП) = 002·(156 + 78) = 568 чел
принимается 6 человек младшего обслуживающего персонала (гардеробщики уборщики бытовых и служебных помещений курьеры и др.)
Их количество принимают равным 13 – 16 % от общего числа рабочих и составляет:
NЦЕХ СЛ = 013(NПР + NВСП) = 013·(156+ 78) = 304 чел
принимается 31 человек цеховых служащих.
Инженерно-технические работники (ИТР)
Их количество принимают равным 115 – 14 % от общего числа рабочих и составляет:
NИТР = 013(NПР + NВСП) = 013·(156 + 78) = 304 чел
принимается 31 человек инженерно-технических работников.
Счетно-конторский персонал
Их количество принимают равным 15 – 2 % от общего числа рабочих и составляет:
NСЧ-КОН = 0015(NПР + NВСП) = 0015·(156 + 78) = 351 чел
принимается 4 человека счетно-конторского персонала.
Общая численность работающих в цехе NОБЩ. = 306 человек.
4.Расчёт площадей и компоновка оборудования.
Укрупнённый расчёт потребных производственных площадей произведём в зависимости от количества и типов применяемого оборудования размеров и массы обрабатываемых деталей применяемых транспортных средств.
Площадь производственных участков равна [19]:
где Sпр - принятое количество производственного оборудования
F - удельная площадь на единицу оборудования (табл. 7 [19]).
Площадь заготовительного отделения [19]:
гдеSЗО – число станков заготовительного отделения SЗО = 5 ст.
FЗО = 30·5 = 150 м2.
Площадь заточного отделения [19]:
где Sз - количество станков заточного отделения. В соответствии с п.3 имеем:
Площадь контрольного отделения [19]:
Fк=002·Fпр=002·2736=5472 м2.
Площадь ремонтной базы механика [19]:
где Sм - количество соответствующего оборудования
Здесь площадь склада запасных частей принимается в размере 28% от площади ремонтной базы [19]: F1=028·Fм=028·195=546 м2
площадь ремонтной мастерской - 40%:F2=04·Fм=04·195=78 м2
площадь распределительной кладовой - 20 %:F3=02·Fм=02·195=39 м2
площадь участка слесарей-монтажников и слесарей по техническому обслуживанию транспортных устройств - 12%: F4=012·Fм=012·195=234 м2.
Определим площадь ремонтной базы энергетика [19]:
Fэ=035·Fм=035195=6825 м2
в том числе площадь для ремонта оборудования [19]:F1э=02·Fм=02·195=39 м2
площадь участка слесарей [19]: F2э=015·Fм=015·195=2925 м2.
Площадь участка по ремонту приспособлений [19]:
Fрп=Sпр·22=10·22=220 м2.
Площадь участка сбора и регенерации СОЖ [19]:
Fж=005·Fпр=005·2736=1368 м2.
Площадь отделения по переработке стружки [19]:
Fстр=0035·Fпр=0035·2736=9576 м2.
Цеховой склад материалов [19]:
где среднее количество дней хранения материалов на складе
Qг - масса материала годового объёма выпуска
k - коэффициент использования площади
средняя допускаемая нагрузка на единицу площади
.материала годового объёма выпуска Qг:
Примем по рекомендациям ([19] стр. 13) k=03 и тогда с учётом массы крышки передней и годовой программы выпуска получим следующее значение площади склада:
Определим площадь межоперационного и промежуточного складов:
где Qг - масса годового объёма выпуска деталей
- коэффициент учитывающий отходы металла на предыдущих операциях (согласно стр.13 [19] принимается равным 115)
t - число дней межоперационного хранения (принимается равным 2 дня стр. 13 [19])
i - среднее число доставок полуфабрикатов на склад (в соответствии с количеством операций технологического процесса принимаем i=3)
и - средняя допускаемая нагрузка на единицу площади (в обоих случаях принимаем равными 15 кНм2 стр. 13 [19])
и - коэффициенты использования площади принимаемые согласно [19] соответственно 05 и 03
число рабочих дней запаса (принимаем по таблице 3 [19] равным 12).
Таким образом получаем:
Определим площадь инструментально-раздаточных кладовых [19]:
где Fуд - норма площади на один станок основного производства Sпр - количество станков основного производства. По таблице 8 приложения [19] принимаем Fуд=06 тогда:
Площадь кладовой масел [19]:
где S - количество обслуживаемого оборудования. Суммарное количество единиц обслуживаемого оборудования составит:
S=Sпр+Sвсп=152+8+6+10=176 шт.
тогда площадь кладовой составит:
Площадь мастерской по ремонту инвентаря секции по наладке и освоению оборудования согласно рекомендациям [19] стр.14 соответственно равны:
Fри=30 м2 и Fно=50 м2.
Площадь помещения под компрессорные установки [19]:
Fку=0008·Fпр=0008·2736=219 м2.
Площадь под трансформаторные подстанции [19]:
Fтр=001·Fпр=001·2736=2736 м2
но с учётом требования: Fтр50=К (целое число) [19] стр.14 принимаем при К=1 Fтр=50 м2.
Площадь вентиляционных камер [19]:
Fвк=007·Fпр=007·2736=19152 м2.
Таким образом общая площадь цеха без учёта площадей служебно-бытовых помещений равна:
Наиболее распространённой конструкцией зданий для размещения механосборочных цехов согласно [19] являются одноэтажные многопролётные здания прямоугольной формы с полом на бетонном основании и перекрытием поддерживаемым системой колонн образующих пролёты цеха. Выбор основных параметров здания производится с учётом особенностей технологического процесса и определяется рациональным размещением производства и экономичностью строительства достигаемой при применении унифицированных строительных элементов и типовых конструкций.
Для полученной площади здания (см. п. 4.5) наиболее рациональной формой является прямоугольник с соотношением сторон 1:2. принимаем шаг внутренних колонн равным 24 м шаг колонн по периметру здания - 12 м ширину пролёта - 24 м высоту пролёта – 72 м.
С учётом произведённых расчётов основываясь на принципе минимума грузопотоков (стр. 15 [19]) спроектируем компоновочный план цеха. Такому принципу отвечает расположение на плане цеха заточного отделения рядом с инструментально-раздаточной кладовой отделения оперативного контроля – рядом с межоперационной кладовой цеховые склады материалов и заготовок – рядом с заготовительным участком.
Производственная часть механического цеха представляет собой общий зал без перегородок разделенный на отдельные участки магистральными и поперечными проездами (таблица 4 [19]).
К планировке оборудования производственных участков наряду с требованиями эстетики предъявляется ряд производственных и эксплуатационных требований основными из которых являются удобство и безопасность работы. Кроме того должен быть обеспечен удобный подвоз тяжелого инструмента крупных приспособлений и запасных узлов оборудования безопасный подход к станку для смазки и разборки его на месте установки возможность уборки стружки.
При расстановке оборудования должны выдерживаться расстояния между крайними положениями рабочих органов станков между станками и проездами стенами и колоннами.
6.Определение площадей и компоновка служебно-бытовых помещений.
В состав служебно-бытовых помещений цеха входят объекты культурно-бытового назначения и объекты административно-технического назначения. К первым относятся гардеробные с умывальниками душевые туалетные комнаты помещения для личной гигиены комнаты для курения устройства для снабжения питьевой водой столовые медпункты помещения для отдыха. Ко вторым относятся помещения начальников смен мастеров и бригадиров цеховые конторы лаборатории помещения для учебных занятий и пр.
Наибольшую площадь занимают гардеробные. Согласно рекомендациям [19] стр. 18 принимаем для гардеробных шкафчиков размеры 50x50x165 см ширину прохода между шкафами со скамьями 2м между шкафами и стеной - 13 м площадь комнаты для инвентаря - 3м2. Общее количество шкафчиков составит 306
Умывальные разместим в помещении гардеробной. Примем количество умывальников в расчёте 15 чел на 1 умывальник тогда получим общее количество умывальников:
Примем размер одного умывальника 60x40 см ширину прохода - 15 м.
Санузлы располагают равномерно на расстоянии не более 75 м. Площадь комнаты с учётом шлюзов составляет 36 м2.
Медицинский пункт цеха расположим вблизи выхода на первом этаже служебно-бытовых помещений. Принимаем согласно [19] стр. 19 площадь медпункта - 90 м2.
Площадь помещений общественного питания включая подсобные помещения кухни:FОП = 061·NОБЩ. = 061·306 = 186.6 м2.
Площадь помещений для культурного обслуживания (библиотеки учебные комнаты и др.): FК ОБС = 03·NОБЩ. = 03·306 = 91.8 м2.
Площадь служебных помещений (цеховые конторы лаборатории):
FСП = 07·NОБЩ. = 07·306 = 214.2 м2
Конторские помещения для цехового персонала занимающегося технологическим планированием руководством и бухгалтерским учётом расположим на втором этаже служебно-бытовых помещений. При удельных площадях 07 м2 на 1 человека ([19] табл.5) их общая площадь составит:
Площади санитарно-гигиенических помещений примем приблизительно по данным табл. 5 [19]:306316=966.96 м2.
Более точно данные площади определим после их предварительной компоновки с учётом данных приведённых выше.
1.Технико-экономический анализ.
Согласно п.2.5 в проектируемом технологическом процессе изготовления корпуса редуктора пневмодвигателя «Крот-12» используется заготовка измененной конфигурации: масса заготовки уменьшилась на 0401 кг.
За счет изменения структуры технологического процесса и использования современного оборудования время обработки сократилось следовательно трудоемкость изготовления в проектируемом варианте ниже.
2.Определение дополнительных капитальных вложений (инвестиций).
Общие капитальные вложения определяются по формуле [23 стр. 8]:
К = КОБ + КОСН + КЗДН + КПР
гдеКОБ КОСН - затраты на приобретение доставку монтаж наладку оборудования и оснастку руб.;
КЗДН - стоимость необходимых производственных площадей зданий сооружений;
КПР - прочие капитальные вложения например затраты на научно-исследовательские и проектно-конструкторские работы.
гдеаТЗ - процент учитывающий транспортно-заготовительные расходы [23 табл. 2.1 стр. 26];
аМ - процент учитывающий затраты на монтажные работы [23 табл. 2.1 стр. 26];
Ц - договорная цена единицы оборудования руб.;
n - количество технологического оборудования необходимого для выполнения заданного годового объема работ:
N - годовая программа выпуска;
КВН - коэффициент выполнения норм.
Учитывая что согласно проектируемому технологическому процессу обработка корпуса редуктора пневмодвигателя «Крот-12» производится на многоцелевом станке мод. 2204ВМ1Ф4 произведем расчет затрат на приобретение доставку монтаж наладку оборудования следующим образом:
t = 092 ч; N = 2500 шт.; ФД = 2030 ч; КОДН = 1; КВН = 105;
Ц = 274000 руб.; аТЗ = 5%; аМ = 4%;
Таким образом общие затраты на приобретение доставку монтаж наладку оборудования составляют КОБ = 598416 руб.
Затраты на изготовление приспособления используемого на операциях 020 и 030 укрупненно определяются по [17 табл. 17 стр. 426].
Стоимость приспособления:
КОСН = 39·1618 = 63102 руб.
где1618 - коэффициент перевода стоимости на текущий период.
Затраты на проектирование технологических процессов и приспособлений рассчитываются по трудоемкости считая что 1 человеко-час работы разработчика составляет примерно 2912 руб.
Нормы времени на технологические и конструкторские работы приведены в [16 табл. 29 30 стр. 433 435]. Для технологических процессов механической обработки деталей группы сложности нормы времени составляют 1245 ч. Для конструирования технологической оснастки группы сложности нормы времени составляют 785 ч. Тогда затраты на проектирование 59114 руб.
В данных расчетах капитальные вложения на здания и сооружения не учитываются так как внедрение новой техники не связано с изменением необходимой площади зданий и сооружений.
Окончательно дополнительные капитальные вложения:
К = 598416 + 63102 + 59114 = 59963816 руб.
3.Расчет себестоимости продукции
Для сопоставления текущих затрат на изготовление корпуса долота в условиях базового и проектируемого вариантов необходимо определить технологическую себестоимость. При этом расчет следует производить по изменяющимся элементам затрат к которым могут относиться следующие расходы [23 стр. 11]:
С = ЗМ + ЗСТ + АОБ + АЗД + ЗЭЛ + ЗРИ + ЗР + ЗПОМ
гдеЗМ - затраты на материалы руб.;
ЗСТ - затраты на основную и дополнительную заработную плату с отчислениями на социальные нужды руб.;
АОБ - амортизационные отчисления от стоимости оборудования руб.;
АЗД - амортизационные отчисления от стоимости здания руб.;
ЗЭЛ - затраты на силовую электроэнергию руб.;
ЗРИ - затраты на режущий инструмент руб.;
ЗР - затраты на текущий ремонт и межремонтное обслуживание оборудования руб.;
ЗПОМ - затраты на эксплуатацию производственных и бытовых помещений руб.
Затраты на материалы включают в себя затраты на основные материалы и затраты на вспомогательные.
К основным материалам относятся отливки поковки прутковый и листовой прокат метизы трубы полуфабрикаты.
Стоимость сырья и материалов определяется на основании норм расхода каждого вида материалов и цен за вычетом стоимости отходов.
Расход на основные материалы для изделий на годовую программу:
где НР - норма расхода материала на одно изделие кг;
ЦМ - планово-заготовительная цена 1 кг. руб.;
РО - возвратные отходы кг.;
ЦО - цена 1 кг. отходов руб.;
N - годовая программа выпуска продукции шт.
К вспомогательным расходам относятся смазочные масла керосин бензин резина обтирочные материалы материалы для текущего ремонта оборудования. Затраты на вспомогательные материалы определяют исходя из установленных норм расхода на рабочее место и цен.
При укрупненных расчетах затраты на вспомогательные материалы составляет 152% от стоимости основных материалов
По базовому варианту
По проектируемому варианту:
Затраты на основную и дополнительную заработную плату с отчислениями на социальные нужды на годовую программу выпуска определяются по [23 стр. 12]:
гдеtШТ - норма штучного времени на операцию для базового технологического процесса tШТ = 654 мин для проектируемого технологического процесса tШТ = 552 мин
ТСТ - часовая тарифная ставка соответствующего разряда по сдельной оплате труда на
КСП - коэффициент учитывающий премиальные доплаты КСП = 12;
КДЗ - коэффициент учитывающий дополнительную зарплату КДЗ = 13;
КСН - коэффициент учитывающий отчисления на социальные нужды КСН = 126;
n - число операций для базового варианта n = 7 для проектируемого варианта n = 4;
N - годовая программа выпуска N = 2500 шт.
Итого получаем что затраты на основную и дополнительную заработную плату с отчислениями на социальные нужды составляют:
по базовому варианту:
по проектируемому варианту:
Годовые амортизационные отчисления от стоимости оборудования рассчитываются по [23 стр. 13]:
гдеЦ - первоначальная стоимость оборудования руб.;
НА - норма амортизационных отчислений %.
Годовые амортизационные отчисления от стоимости оборудования:
Ц = 924000 руб.; НА = 116% [23 табл. 2.2 стр. 28]
Ц = 598416 руб.; НА = 116% [23 табл. 2.2 стр. 28]
Годовые амортизационные отчисления от стоимости зданий можно не учитывать так как размеры площадей значительно не изменяются от варианта к варианту.
Затраты на силовую электроэнергию на годовую программу выпуска [22 стр. 426]:
гдеNЭ - установленная мощность всех электродвигателей оборудования кВт;
- коэффициенты загрузки станков по времени и по мощности [22 табл. 18 стр. 427] =04;
ЦЭ – цена 1 кВт·ч электроэнергии ЦЭ = 12 руб;
N – годовая программа выпуска N = 2500 шт.
Затраты на силовую электроэнергию на годовую программу выпуска:
по проектному варианту
Затраты на текущий ремонт и межремонтное обслуживание оборудования составляют 3% от стоимости оборудования [16 стр. 424]:
гдеЦ - общая стоимость оборудования ЦБ = руб. по базовому варианту ЦПР = 598416 руб. по проектируемому варианту
ЗР = 003· = 27720 руб.;
ЗР = 003·598416 = 1795248 руб.
Затраты на режущий инструмент принимаются в сумме 1800 руб. на 1 станок [26 стр. 14].
ЗРИ = 1800·3 = 5400 руб.;
ЗРИ = 1800·2 = 3600 руб
Затраты на эксплуатацию производственных и бытовых помещений можно не учитывать так как размеры площадей значительно не изменяются от варианта к варианту.
Таким образом себестоимость изделия корпус долота на годовую программу составит:
С = ++++5400+27720 = 1300793 руб.
По проектируемому варианту
С = ++++3600+1795248= 115366815 руб.
Цеховые расходы принимаются в размере 80% от основной заработной платы производственных рабочих и составляют:
по базовому варианту - 19711039 руб.
по проектируемому варианту - 16636838 руб.
Общезаводские расходы принимаются в размере 67% от основной заработной платы производственных рабочих и составляют: по базовому варианту – 16507994 руб. по проектируемому варианту – 13933352 руб.
Величина внепроизводственных расходов принимается в размере 3% от производственной себестоимости и составляет:
по базовому варианту – 3902379 руб.
по проектируемому варианту – 3413395 руб.
Полная себестоимость продукции (на весь объем продукции):
по базовому варианту 170200712 руб.;
на единицу 6808 руб.;
по проектируемому варианту 1493504руб.;
на единицу 5974 руб.
Данные по себестоимости изготовления корпуса долота на годовую программу выпуска приведены в таблице 5.1.
Себестоимость продукции на годовую программу
Расходы на сырье и материалы
Расходы на основную и
дополнительную заработную
плату рабочих с отчислениями на
Амортизационные отчисления
Расходы на силовую электроэнергию
Расходы на режущий инструмент
Расходы на текущий ремонт
и межремонтное обслуживание
Цеховая себестоимость
Общезаводские расходы
Производственная себестоимость
Внепроизводственные расходы
Полная себестоимость
Прибыль в проектируемом варианте определяется по формуле:
ППР = ПБАЗ + СБАЗ – СПР.
Прибыль в базовом варианте заложена с учетом рентабельности выпуска 20% и составляет:
ПБАЗ = 02·СБАЗ = 02·1702000 = 340400 руб.
ППР = 340400+ 1702000 – 1494000 = 548400 руб.
Оптовая цена продукции в базовом и проектируемом вариантах остается неизменной:
Производительность труда одного рабочего-станочника
гдеn – число рабочих-станочников изготавливающих данную деталь nБ = 3 чел. nПР = 2 чел.;
N – годовой выпуск продукции N = 2500 шт.
Пt Б = 81696·25003 = 680800 руб.
Пt ПР = 81696·25002 = 1021200 руб.
Рентабельность выпуска корпуса редуктора определяется по формуле:
Основные технико-экономические показатели
Годовой экономический эффект определяется по формуле [23 стр. 17]:
ЭГОД = (СБ – СПР) – ЕН·ΔК
гдеЕН – нормативный коэффициент дополнительных капитальных вложений ЕН = 015 [23 стр. 17];
ΔК – дополнительные капитальные вложения ΔК = 59963816 руб.
ЭГОД = (1702000 – 1494000) – 015·59963816 = 118554276руб.
Срок окупаемости дополнительных капитальных вложений [23 стр. 17]:
Сравнительные технико-экономические показатели вариантов технологических процессов изготовления корпуса редуктора приведены в таблице 5.2.
Сравнительные технико-экономические показатели
Годовой выпуск продукции шт.
Товарная продукция тыс. руб.
Число рабочих-станочников
Себестоимость единицы продукции руб.
Производительность труда 1
рабочего-станочника тыс. руб.чел.
Себестоимость годового выпуска
Материалоемкость продукции
Затраты на 1 руб. товарной продукции
Рентабельность продукции %
Балансовая прибыль тыс. руб.
Годовой экономический эффект
Срок окупаемости затрат лет
БЕЗОПАСНОСТЬ ЖИЗНЕДЕЯТЕЛЬНОСТИ
Охрана труда – это система законодательных актов социально-экономических технических и лечебно-профилактических мероприятий обеспечивающих безопасность сохранение здоровья и работоспособности человека в процессе труда.
Задача охраны труда – свести к минимуму вероятность поражения или заболевания работающего с одновременным обеспечением комфортности и максимальной производительности труда.
Охране труда на предприятиях всегда оказывалась большое внимание и являлась общегосударственной задачей. Однако с развитием научно-технического прогресса появляется ряд новых проблем. Повышение технической оснащённости машиностроительных предприятий применение новых материалов конструкций увеличение скоростей и мощности машин оказывает влияние на характер и частоту несчастных случаев и заболеваний па предприятиях. Улучшение условий труда приводит к экономическим и социальным результатам – улучшению здоровья трудящихся повышению степени удовлетворённости трудом укреплению дисциплины повышению производительности труда и т.д.
Современным требованиям научно-технического прогресса может отвечать только всесторонне обоснованная система комплексных задач охраны труда.
2.Требования охраны труда к производственным
и санитарно-бытовым помещениям
На каждого работающего должно приходиться не менее 15 м3 объема и не менее 15 м2 площади помещений. Рабочие места проходы и проезды не должны загромождаться сырьем полуфабрикатами и готовыми изделиями. Граница проходов и рабочих площадок надлежит обозначать видимыми белыми линиями шириной не менее 50 мм.
Использование производственных помещений для принятия пищи запрещается. Все производственные помещения рабочие места и оборудование должны содержаться в чистоте и порядке. Отбросы и мусор должны регулярно собираться и удаляться в специально отведенные для этой цели места. Для отбросов и мусора в производственных помещениях должны быть установлены в доступных и удобных местах мусорные ящики и урны которые должны быть убраны не реже одного раза в день и систематически дезинфицироваться.
Пол стены и потолки рабочих помещений должны содержаться в исправности своевременно ремонтироваться.
Раздевалки гардеробные душевые и другие санитарно-бытовые помещения необходимо периодически подвергать дезинфекции.
Душевые необходимо обеспечивать горячей водой в количестве достаточном для всех рабочих Смесительные приборы должны быть безопасными легко открываться и не подтекать. Температура воды 28 37 °С.
Структура системы охраны труда работающих состоит из трех подсистем (рис.6). Подсистема обеспечения безопасной работы персонала предназначена для эксплуатации и обслуживания металлорежущего оборудования а также профилактики и ликвидации пожаров.
Большое значение в этой системе имеет защита от воздействия механических устройств. Все ременные передачи закрыты кожухами зона обработки на токарных сверлильных зубообрабатывающих станках закрывается в процессе обработки защитными экранами со смотровым окном. Время торможения шпинделя ограничено 5 секундами. Рукоятки и другие органы управления станками должны быть снабжены надежными фиксаторами не допускающими самопроизвольных перемещений органов управления. Двери электрошкафов станков должны закрываться специальными замками.
Защита от стружки о СОЖ должна быть как индивидуальной (очки специальная обувь) а также осуществляться с помощью оградительных устройств.
Рис.6 Структура системы охраны труда.
Должны быть приняты все меры обеспечивающие надежную защиту работающих от любого вида поражения электрическим током.
Пожарная безопасность должна обеспечиваться мерами противопожарной профилактики и активной пожарной защиты включающей систему пожарных гидрантов стационарных пожарных установок автоматических ручных с дистанционным пуском огнетушителями противопожарными щитами с ящиками для песка.
Подсистема обеспечения санитарных условий труда должна включать в себя меры по соблюдению санитарных норм воздушной среды освещенности чистоты рабочих мест защиты рабочих мест от шума вибраций. А также проведение мероприятий по производственной эстетике.
Подсистема обслуживания работающих предназначена для создания нормальных условий работающим путем организации бытового и медицинского обслуживания а также службы общественного питания.
По видам обслуживание должно включать в себя:
Местное – в радиусе 50-90 м от рабочих мест необходимо предусмотреть курительные санитарные узлы питьевые устройства.
Цеховые – в радиусе 200-400 м должен быть предусмотрен комплекс гардеробов умывальников и душевых помещений.
Общезаводские - в радиусе 500-800 м должны быть предусмотрены прачечные химчистки и другие объекты бытового использования.
3.Требования охраны труда к оборудованию
В спроектированном механическом цехе 152 единиц металлорежущего оборудования основного производства. Транспортировка контейнеров с заготовками осуществляется электрокарами.
Отличительной особенностью этих станков является кинематика их рабочих движений. На этих станках инструмент совершает вращение иили выполняет движение подачи.
Основными опасными производственными факторами при эксплуатации станков является образующаяся в процессе резания стружка.
При работе с высокими скоростями резания особое внимание должно быть уделено правильному и надежному закреплению заготовок.
Движущие части представляющие опасность должны быть ограждены. Конструкции ограждающих устройств должны быть прочными надежно крепиться не мешать производственной работе уборке и наладке станка.
Станки следует снабжать экранами защищающими рабочих и окружающих от травмирования или от брызг СОЖ. Конструкция экранов должна быть легкоподвижной и предусматривать возможность чистки смотровых окон от загрязнения. Конструкция станков и их элементов должны способствовать отводу стружки из зоны резания быть удобной для очистки от стружки пыли масла.
Станки на которых вспомогательные перемещения производятся при включении органов главного движения станка необходимо снабжать быстродействующими тормозными устройствами. Рычаги и рукоятки управления должны быть расположены в местах удобных для обслуживания и не требовать значительных перемещений рук рабочего. Местоположение этих органов и рукояток должно исключать возможность случайного включения.
Пусковые педали оборудования должны иметь надежное ограждение или предохранительные устройства исключающие возможность непреднамеренного включения оборудования по какой-либо случайной причине.
Все органы управления эксплуатируемого оборудования должны иметь четкие и ясные надписи и символы указывающие их назначение.
4.Оздоровление воздушной среды в производственных помещениях.
Самочувствие и работоспособность человека зависят от состояния метеорологических характеристик окружающей среды которая определяется основными параметрами:
-относительной влажностью;
-подвижностью воздуха.
Оптимальная температура воздуха в машинном зале составляет 20-22С влажность 60-65% и скорость движения воздуха в пределах 02т – 04 мс.
Вентиляцией называется комплекс взаимосвязанных устройств и процессов предназначенных для создания организованного воздухообмена с целью обеспечения нормальных метеорологических условий в рабочей зоне помещений.
Вентилирование помещений осуществляется с помощью вентиляционных систем которые по своему назначению подразделяются на три типа:
)Общеобменные – системы которые осуществляют смену воздуха во всем помещении.
)Местные – системы которые обеспечивают улавливание производственных вредностей в местах их выделений и последующее удаление из помещений.
)Смешанные – системы которые выполняют одновременно обе функции.
Устройство в помещении только местной вентиляции недопустимо. Общеобменная вентиляция необходима во всех случаях.
Системы вентиляции по способу побуждения движения воздуха делятся:
-системы с естественным побуждением движения воздуха (аэрация);
-системы с искусственным побуждением движения воздуха (механическая или принудительная вентиляция).
В первом случае причиной перемещения воздуха служат естественные факторы (тепловой напор или движение ветра) во втором – для перемещения воздуха применяют специальные побудители тяги: вентиляторы воздуходувы эжекторы и др.
Вентиляционные установки могут быть приточными и вытяжными. Приточные установки подают свежий воздух в помещении а вытяжные удаляют из помещения отработанные загрязненный воздух. Обычно эти установки действуют совместно образуя приточно-вытяжную систему.
При продолжительной работе с ЭВМ и другими электроустановками воздух в помещении нагревается поэтому для сохранения нормальной температуры необходимо применять принудительную вентиляцию.
В проектируемом цехе нет процессов выделяющих в окружающую среду вредных веществ и следовательно для воздухообмена достаточно свежего воздуха из естественной среды.
5.Меры по снижению уровня шума и вибраций в производственных помещениях.
Шум – это совокупность апериодических звуков различной интенсивности и частоты. С физиологической точки зрения шум – это всякий неблагоприятно воспринимаемый шум. Шум является одним из распространенных и неблагоприятных факторов на производстве.
Интенсивный шум на производстве способствует снижению внимания и увеличению ошибок при выполнении работы. Из-за шума снижается производительность труда и ухудшается качество работы. Шум затрудняет своевременную реакцию работающих на предупредительные сигналы внутрицехового транспорта (автопогрузчики мостовые краны и т. п.) что способствует возникновению несчастных случаев на производстве.
Источником шума в цехе являются машины механизмы агрегаты и другое оборудование цеха. Степень влияния шума зависит от его интенсивности и продолжительности воздействия состояния центральной нервной системы и что очень важно от индивидуальной чувствительности организма к акустическому раздражителю. Вредное воздействие шума отражается на органах слуха оказывает отрицательное влияние на центральную нервную систему и весь организм в целом.
Гигиенические нормативы шума определены ГОСТ 12.1.003–83 и СН 2.2.42.1.8.562–96. Допустимый уровень звука и эквивалентный уровень звука на постоянных рабочих местах и в рабочих зонах в производственных помещениях и на территории предприятий составляет 75-85 дБ.
Понизить уровень шума для обеспечения максимального комфорта и других условий труда позволяет использование мероприятий по борьбе с шумом:
)снижение звуковой мощности источника шума;
)изменение направленности излучения шума;
)акустическая обработка помещений;
)уменьшение шума на пути его распространения;
)применение глушителей шума;
)применение средств индивидуальной защиты (вкладышей наушников шлемов).
Вибрация – это малые механические колебания возникающие в упругих телах. Вибрация относится к факторам обладающим высокой биологической активностью. Действие вибрации зависит от частоты и амплитуды колебаний продолжительности воздействия демпфирующих свойств тканей организма человека явлений резонанса и других условий.
Гигиеническое нормирование вибраций осуществляется по ГОСТ 12.1.012–90 и СН 2.2.42.1.8.566–96.
Вибрация высокой интенсивности при продолжительном воздействии вызывает изменения в нервной и сердечно-сосудистой системах опорно-двигательном аппарате желудочно-кишечном тракте органах равновесия.
Основными методами борьбы с вибрациями машин и оборудования являются:
)снижение виброактивности машин;
)отстройка от резонансных частот;
)вибродемпфирование;
)повышение жесткости системы;
)применение индивидуальных средств защиты (для рук - виброизолирующие рукавицы перчатки вкладыши и прокладки; для ног - виброизолирующая обувь стельки подметки).
Для уменьшения вибраций используются виброизоляция (виброопоры из резины пружины рессоры). При невозможности проведения указанных технических мероприятий обязательно использование индивидуальных средств защиты (виброботинки виброрукавицы и т. д.).
Уровни вибрации на рабочих местах определяются на установке для испытания на нормы точности. Проверка уровня вибрации производится при испытании каждого нового образца оборудования.
Для профилактики профессиональных заболеваний и снижения вредного воздействия шума и вибраций необходимо применять предупредительные меры. Прежде всего они должны учитываться при проектировании строительстве и организации технологического процесса. Шумное с интенсивной вибрацией процессы и оборудование размещается в изолированных помещениях. Для снижения фона отраженного шума стены потолки нужно облицовывать звукопоглощающими материалами. Вращающиеся движущиеся части технологического оборудования являются источниками шума и вибраций поэтому они должны тщательно пригоняться балансироваться смазываться.
6.Производственное освещение. Расчет освещенности цеха.
Освещение рабочего места – важнейший фактор создания нормальных условий труда. Освещение должно отвечать условиям оптимальной работы органов зрения человека. Повышение освещенности как правило ведет к росту производительности труда однако есть предел при котором дальнейшее повышение освещенности такого эффекта уже не дает.
Освещение должно быть равномерным так как перевод взгляда с более освещенной поверхности на менее освещенную вызывает повышенную утомляемость глаза. Светлая отделка потолков стен способствует созданию равномерного распределения световых потоков.
На рабочих поверхностях должны отсутствовать резкие тени прямой и отраженный блеск. Ограничение прямой блесткости достигается уменьшением яркости источников света правильным выбором защитного угла светильника увеличением высоты подвески светильников. Отраженная блесткость устраняется путем использования матовых поверхностей изменением угла наклона рабочей поверхности. Освещение не должно искажать светопередачу. Равномерность цветопередачи обеспечивается использованием комбинированного освещения которое представляет совокупность местного и общего освещения. Осветительная установка должна быть удобной надежной экономной не создавать шума и не быть источником дополнительной опасности.
Освещенность на рабочих местах и поверхностях станков класса П и В должна быть не ниже 400 лк при освещении газоразрядными лампами. Общее искусственное освещение цеха с металлорежущими станками должно быть равным 400 лк при освещении газоразрядными лампами.
В данном разделе производится расчет освещения производственных участков механического цеха. Для расчета рабочего искусственного освещения цеха в качестве исходных данных принимается:
тип источника света: для освещения производственного помещения – лампа дуговая ртутная люминесцентная ДРЛ–400 имеющая величину светового потока ФП = 19000 лм ;
тип системы освещения – комбинированная;
характеристики цеха: длина –96 м ширина – 48 м высота расположения светильников – 96 м;
коэффициент минимальной освещенности равный отношению средней освещенности и минимальной ЕСРЕMIN для ламп ДРЛ z = 115.
Расчет общего равномерного искусственного освещения горизонтальной рабочей поверхности выполняется методом коэффициента использования светового потока.
Световой поток (лм) одной лампы
гдеЕН – нормированная минимальная освещенность по СНиП 23–05–95 ЕН = 200 лк;
S – площадь освещаемого помещения S = 4608 м2;
z – коэффициент неравномерности освещения z = 115;
kЗ – коэффициент запаса kЗ = 15;
И – коэффициент использования светового потока;
N – число светильников в помещении.
Коэффициент использования светового потока И давший название методу расчета определяют по СНиП 23–05–95 в зависимости от типа светильника коэффициентов отражения потолка ρП стены ρC пола ρР размеров помещения определяемых индексом помещения
гдеА – длина помещения в плане А = 96 м;
В – ширина помещения в плане В = 48 м;
НР – высота подвеса светильников над рабочей поверхностью НР = 88 м.
Согласно справочной литературе для коэффициентов отражения потолка ρП = 30% стены ρC = 10% пола ρР = 10% и индекса помещения i = 229 коэффициент использования светового потока И = 06.
Таким образом определяется число светильников в помещении:
Таким образом для освещения проектируемого механического цеха принимается 140 светильника типа УПДДРЛ с лампами ДРЛ–400.
Определяется световой поток
Отклонение потока выбранной лампы ДРЛ–400 (ФП = 19000 лм) от расчетного
что лежит в пределах –10% +20%.
7. Электробезопасность. Расчет защитного заземления.
Цеха промышленного производства как правило оснащены значительным количеством электроустановок. Проектируемый цех не является исключением поэтому достаточное внимание должно уделяться вопросам безопасности при эксплуатации электрооборудования.
Электробезопасность – это система организационных и технических мероприятий и средств обеспечивающих защиту от вредного и опасного воздействия электрического тока электромагнитного поля и статического электричества.
Основными мерами защиты от поражения током является обеспечение недоступности токоведущих частей; электрическое разделение сети; устранение опасности поражения при появлении на корпусах кожухах и других частях электрооборудования; выравнивание потенциала заземления; организация безопасности эксплуатации электроустановок.
Согласно «Правилам устройства электрических установок» сопротивление защитного заземления для установок с напряжением до 1000 В не должно превышать 4 Ом.
Защитным заземлением называется преднамеренное электрическое соединение с землей металлических нетоковедущих частей установок которые могут оказаться под напряжением. Схема заземления приведена на рис.7.
Рис.7 Схема защитного заземления
– внутренний контур заземления; 2 – наружный контур заземления;
– переходное соединение в наружной стене механического цеха;
– заземлитель; 5 – оборудование; 6 – наружная стена цеха.
Для снятия напряжений до безопасной величины относительно земли на металлических частях оборудования необходимо произвести расчет защитного заземления. Защитное заземление состоит из группы заземлителей расположенных непосредственно в земле и соединительной полосы. С их помощью осуществляется надёжное заземление станка.
В качестве заземления используем стальную трубку ø50 мм и длиной 3 м.
Сопротивление трубки:
ρ – удельное сопротивление; ρ=025·104 Ом для 10% влажности;
t – глубина заземления; t=1600 мм;
d – диаметр трубки; d=50 мм;
Количество заземлений в системе:
r1=12 и r2=06 – коэффициенты экранизации;
Соединение заземлений ведем стальной полосой шириной B=5 см и толщиной h=05 см.
a=3 м – шаг заземления;
r=105 – коэффициент удлинения полосы.
Сопротивление полосы:
t0=08 – глубина залегания полосы.
Сопротивление всей системы заземления:
8.Обеспечение пожарной безопасности.
Пожары на предприятиях представляют большую опасность для работающих и могут причинять громадный материальный и моральный ущерб. Вопросы обеспечения пожарной безопасности зданий и сооружений имеют большое значение и утверждены специальными государственными постановлениями и решениями.
Пожарная безопасность может быть обеспечена мерами пожарной профилактики и активной пожарной защиты. Пожарная профилактика включает в себя комплекс мероприятий необходимых для предупреждения возникновения пожара или уменьшения его последствий..
Механический цех относится к категории D т.к. в цехе обрабатываются негорючие материалы в холодном состоянии и все основные конструкции выполнены из несгораемых материалов – железобетона кирпича металлоконструкций.
Основные опасные факторы пожара: открытый огонь искра повышенная температура воздуха и окружающих предметов токсичные продукты горения дым нахождение технологического оборудования под напряжением и т. д.
Мероприятия предупреждающие возникновение пожара на предприятии:
Запрещено разведение открытого огня на всей территории завода и на территории прилегающей к ней ближе чем на 50 м.
На каждом участке установить специальные контейнеры для использованного обдирочного материала отходов ветоши которые регулярно вывозятся.
Регулярно проверять состояние электрической проводки.
Сварочные работы проводить в местах удаленных от легковоспламеняющихся материалов.
Все работники предприятия ознакомляются с приемами тушения пожаров в каждом цехе есть ответственный за противопожарную безопасность.
Курение разрешено только в специально отведенных местах.
Для эвакуации людей и материальных ценностей разрабатывается план эвакуации. Руководителю предприятия предоставлено право налагать дисциплинарные взыскания за нарушения правил и требований пожарной безопасности.
В каждом здании должно быть достаточное количество выходов для обслуживающего персонала.
Для тушения пожаров в начальной стадии внутри зданий предусматриваются внутренние пожарные водопроводы. Внутренний водопровод состоит из вводов водомерных узлов стояков разводящей сети водоразборной и регулирующей аппаратуры.
Внутренние пожарные краны устанавливаются в нишах или шкафчиках у входов на площадках отапливаемых лестничных клеток в коридорах и других доступных местах на высоте 135 м от уровня пола. К пожарным кранам присоединяются рукава со стволами.
Систему внутреннего пожарного водопровода проектируют таким образом чтобы обеспечить бесперебойную и удобную подачу воды из пожарных стволов до прибытия более мощных средств пожарной защиты или тушения пожаров.
Пожарные краны оборудуют пожарными стволами с диаметром насадки 16 мм. Пожарные краны размещают так чтобы компактные струи подаваемые из стволов подключенных к двум соседним кранам соприкасались в наиболее высокой и удаленной точке на границе их взаимодействия.
Рассчитаем необходимое количество огнетушителей для проектируемого цеха:
S – площадь цеха S=4608 м2;
0 м2 – норма площади на один огнетушитель.
Таким образом в проектируемом цехе необходимо установить 46 огнетушителей.
1.Использование трехмерного моделирования для подготовки рабочего чертежа детали.
В дипломном проекте проведено моделирование корпуса редуктора пневмодвигателя с целью получения информации о геометрических и массо-центровочных параметрах а также для анализа возможности получения точной отливки заготовки выбранным способом.
Кроме того в процессе моделирования были проведен анализ исходной конструкторской документации.
Полученные модели деталей можно использовать в дальнейшем для создания и анализа сборочной модели пневмодвигателя «Крот-12М».
2.Выбор системы проектирования.
Общепринятым порядком моделирования твердого тела является последовательное выполнение булевых операций (сложения и вычитания) над объемными примитивами (сферами призмами цилиндрами конусами пирамидами и т.д.). Большинство таких операций были использованы при создании трехмерной модели корпуса радиатора.
В КОМПАС-3D объемные примитивы образуются путем выполнения такого перемещения плоской фигуры в пространстве след от которого определяет форму примитива. При этом получение формы детали во многом может соответствовать известным формообразующим методам используемым в механической обработке путем снятия материала.
Проектирование детали начинается с создания базового тела путем выполнения операции над эскизом (или несколькими эскизами).
При этом доступны следующие типы операций:
вращение эскиза вокруг оси лежащей в плоскости эскиза;
выдавливание эскиза в направлении перпендикулярном плоскости эскиза;
кинематическая операция - перемещение эскиза вдоль указанной направляющей;
построение тела по нескольким сечениям-эскизам.
Каждая операция имеет дополнительные опции позволяющие варьировать правила построения тела.
3.Трехмерное проектирование корпуса редуктора.
На рис.8 показано дерево построения отображающее последовательность операций используемых при создании трехмерной модели детали «Корпус редуктора».
Рис. 8 Последовательность создания модели «Корпус редуктора».
Полученная модель может использоваться для получения моделей сборок и рабочих чертежей а также передаваться в расчетные пакеты для математического анализа и расчетов. Для этого имеется возможность сохранения файлов моделей в форматах IGS SAT X_T X_B STP STEP.
Система КОМПАС-3D позволяет производить расчеты геометрических и массо-центровочных характеристик трехмерных объектов а также сохранение результатов в виде текстовых документы и специальных форматов для дальнейшего использования и анализа.
4.Проектирование плана цеха с использованием библиотеки отрисовки планов зданий и сооружений.
Проектирование механических цехов является одной из трудоемких задач технологической подготовки производства. Это обусловлено и наличием довольно объемных расчетов зависящих от количества различных типов оборудования в цехе количества рабочего персонала вспомогательных служб. Не менее сложной является задача выполнения планировки помещений и производственных участков с последующей подготовкой конструкторской и технологической документации. С целью сокращения сроков данного этапа проектирования рационально применение систем автоматизированного проектирования (САПР). В дипломном проекте в соответствии с заданием предложено использование таких типов систем российской фирмы АСКОН а именно программные средства САПР семейства КОМПАС. Система позволяет провести проектирование с использованием соответствующих модулей и библиотек.
Данная библиотека функционирует в среде КОМПАС-ГРАФИК. Она предназначена для выпуска проектной документации при работе с планировками а также для выпуска поэтажных планов используемых в качестве подосновы при проектировании внутренних инженерных сетей (в частности возможна ее совместная работа с Библиотекой проектирования систем вентиляции или Библиотекой элементов электрических схем).
Пользователь Библиотеки оперирует типичными для специализированных архитектурно-строительных САПР инструментами - такими как колонна стена окно дверь лестница и т.д. Имеется возможность создавать одно- и многослойные стены и перекрытия при их сопряжении Библиотека осуществляет пересчет и корректно представляет узлы примыкания.
Созданные пользователем стили элементов ограждающих конструкций (стен перекрытий и т.п.) а также колонн и прямых лестничных маршей могут быть сохранены как в файле проекта так и в библиотеке стилей что позволяет использовать их в других проектах.
Проектировщику будет полезен и бесплатный продукт поставляемый вместе с Библиотекой отрисовки планов зданий и сооружений: Библиотека типовых узлов строительных конструкций реализованная в виде библиотеки фрагментов КОМПАС. Данная библиотека содержит 70 узлов относящихся к различным конструктивным элементам здания.
Типовые узлы в Библиотеке разбиты на следующие категории:
Состав и утепление фундаментов и стен подвала
Сооружение и утепление пола
Сооружение и утепление стены с кирпичной кладкой
Утепление и оборудование деревянных каркасных стен
Сооружение и утепление скатной крыши
Сооружение и утепление совмещенной крыши
Противопожарная защита
Новые технологии утепления
В дипломном проекте библиотека используется для построения сетки колонн в соответствии с расчетами стеновых панелей планировки участков и вспомогательных помещений расположения дверей и окон.
В итоге получается чертеж плана цеха выполненный в соответствии с требованиями ЕСКД.
Так замена станка мод. ГДВ400ПМ1Ф4 применяемый в базовом технологическом процессе многоцелевым горизонтальным сверлильно-фрезерно-расточным станком мод. 2204ВМ1Ф4 позволила сократить затраты на электроэнергию (за счет меньшей мощности двигателя) улучшить условия труда (за счет меньших габаритов) что в конечном итоге привело к снижению затрат.
Для операций 020 и 030 спроектировано производительное и обеспечивающее необходимую точность станочное приспособление внедрение которого сократило штучное время обработки;
В ходе проектирования была предложена конструкция заготовки наиболее приближенной формы к изделию что позволило сократить расход материала.
Таким образом проведенные в данной работе технологические конструкторские операционно-экономические мероприятия позволили поднять производительность и улучшить условия труда повысить уровень автоматизации механизации и общей культуры производства т.е. поставленные цели были достигнуты.
Методические указания к выполнению курсового проекта по технологии машиностроения для студентов специальности 12.01.00. - Белгород: Изд. БелГТАСМ 2002.
Анурьев В.И. Справочник конструктора-машиностроителя в 3-х томах. - М.: Машиностроение 1980
Справочник технолога-машиностроителя «Обработка металлов резанием»под ред. А.А. Панов и др. - М: Машиностроение 1988 г.
Горбацевич А. Ф. Шкред В. А. Курсовое проектирование по технологии машиностроения. Учебник для вузов. - Минск: Вышэйшая школа 1983 г.
Допуски и посадки: Справочник под ред. В.А. Мягков М.А. Полей и др. - М: Машиностроение 1982 г.
Справочник технолога-машиностроителя т.1 Под ред. А. Г. Косиловой и Р. К. Мещерякова. - М.: Машиностроение 1985
Справочник технолога-машиностроителя т.2 Под ред. А. Г. Косиловой и Р. К. Мещерякова. - М.: Машиностроение 1985
Лебедев Л.В. Начало технологического проектирования: Учебное пособие. - Белгород БТИСМ 1992 г.
Лебедев Л.В. Проектирование технологической оснастки. Метод. указан. - Белгород. БТИСМ 1989 г.
Косилова А. Г. Мещеряков Р. К. Калинин М. А. Точность обработки заготовки и припуски в машиностроении: Справочник технолога. - М.: Машиностроение 1976 г.
Общемашиностроительные нормативы режимов резания для технического нормирования работ на металлорежущих станках. - М.: Машиностроение 1975. - Ч.1 2.
Технология машиностроения (специальная часть): Гусев А.А. и др.- M.: Машиностроение 1986г.
Общемашиностроительные нормативы времени и режимов резания для нормирования работ выполняемых на универсальных и многоцелевых станках с числовым программным управлением. – М.: Экономика 1990. – Ч.1 2.
Безопасность жизнедеятельности Под ред. С. В. Белова. - М.: Высш. шк. 2000 г.
Корсаков В. С. Основы конструирования приспособления: Учебник для вузов. - М.: Машиностроение 1983 г.
Ансеров М.А. Приспособления для металлорежущих станков. Л.: Машиностроение 1973 г.
Охрана труда в машиностроении: Учебник для машиностроительных вузов. Под ред. Е. Я. Юдина С. В. Белова. - М.: Машиностроение 1983
Рязанов В. И. Дуганов В. Я. Методические указания по проектированию механосборочных цехов. - Белгород БелГТАСМ
Справочник контролера машиностроительного завода. Допуски посадки линейные измерения Под ред. А. И. Якушева. - М.: Машиностроение 1980 г.
Белкин И. М. Допуски и посадки (Основные нормы взаимозаменяемости): Учебное пособие для студентов машиностроительных специальностей высших технических заведений. - М.: Машиностроение 1992
Егоров М.Е. Основы проектирования машиностроительных заводов: Учебник для машиностроительных ВУЗов – М.: Высшая школа 1969 г.
Дьяков В. И. Типовые расчеты по электрооборудованию: Метод. пособие. - М.: Высш. шк. 1985
Рудычев А. А. Березняков В. А. Кузнецова И. А. Методические указания к выполнению курсовой работы по дисциплине "Организация производства и менеджмента в машиностроении" для студентов специальности 120100 - Технология машиностроения. - Белгород 1999.
6 БЖД.doc
Безопасность жизнедеятельности - наука о комфортном и безопасном взаимодействии человека с техносферой (производственной зоной) и окружающей природной средой.
Охрана труда - система обеспечения безопасности жизни и здоровья работников в процессе трудовой деятельности включающая в себя правовые социально - экономические организационно - технические санитарно - гигиенические лечебно - профилактические реабилитационные и иные мероприятия [20].
В сфере обеспечения безопасности человека в производственных условиях в стране действует законодательство в области охраны труда.
Основными законодательными актами в области охраны труда на территории Российской Федерации являются: Конституция РФ Федеральный закон «Об основах охраны труда в РФ» (закон № 181-ФЗ от 17.7.1999 г) закон Белгородской области «Об основах охраны труда» трудовой кодекс РФ указы президента постановление правительства РФ и государственные нормативные акты РФ.
Основные положения Федерального закона «Об основах охраны труда в РФ» (в дальнейшем Основы) заключаются в следующем:
–определена сфера действий Основ и основные принципы государственной политики в области охраны труда;
–определено управление охраной труда как на государственном уровне так и на уровне предприятий и их объединений;
–установлены обязанности работодателя по обеспечению безопасных условий труда работников а также обязанности работника по обеспечению охраны труда на предприятии;
–проведение обучения и инструктажа работников по охране труда проведению медицинских осмотров;
–определена ответственность работодателя за вред причиненный здоровью работника трудовым увечьем ответственности предприятия за невыполнение требований по созданию здоровых и безопасных условий труда ответственность работодателей должностных лиц и работников за нарушение законодательных и иных нормативных актов об охране труда;
–предусмотрено предоставление работникам дополнительных льгот и компенсаций за тяжелые работы и работы с вредными и опасными условиями труда;
–определены основные функции и ответственность органов государственного надзора и контроля за соблюдением законодательства об охране труда; определены органы организации и лица которые должны осуществлять общественный контроль за охраной труда;
–предусмотрена приостановка производственной деятельности предприятий или их закрытие за нарушение нормативных требований по охране труда.
Управление охраной труда осуществляется: на предприятии – генеральным директором (техническим директором); в цехах и производственных участках – руководителями соответствующих служб и подразделений. Организационно методическую работу по управлению безопасностью труда подготовку управленческих решений и контроль за их реализацией осуществляет служба техники безопасности подчиненная генеральному директору. Общее руководство системой управления охраны труда на предприятии осуществляет генеральный директор. Координация работ связанных с функционированием системы возлагается на отдел техники безопасности. Начальник цеха осуществляет непосредственное руководство по системе в производственном подразделении; начальник участка (мастер) обеспечивает безопасную организацию работ в смене. Бригадир и члены бригады осуществляют самоконтроль за исполнением инструкций по охране труда.
1. Требования охраны труда к производственным и санитарно-бытовым помещениям
Согласно ГОСТ 12.1.005-88 ССБТ и СНиП 2.09.04-87 (СТРОИТЕЛЬНЫЕ НОРМЫ И ПРАВИЛА АДМИНИСТРАТИВНЫЕ И БЫТОВЫЕ ЗДАНИЯ) на каждого работающего должно приходиться не менее 15 м3 объема и не менее 15 м2 площади помещений. Рабочие места проходы и проезды не должны загромождаться сырьем полуфабрикатами и готовыми изделиями. Границу проходов и рабочих площадок надлежит обозначать видимыми белыми линиями шириной не менее 50 мм.
Использование производственных помещений для принятия пищи запрещается. Все производственные помещения рабочие места и оборудование должны содержаться в чистоте и порядке. Отбросы и мусор должны регулярно собираться и удаляться в специально отведенные для этой цели места. Для отбросов и мусора в производственных помещениях должны быть установлены в доступных и удобных местах мусорные ящики и урны которые должны быть убраны не реже одного раза в день и систематически дезинфицироваться.
Пол стены и потолки рабочих помещений должны содержаться в исправности своевременно ремонтироваться. Раздевалки гардеробные душевые и другие санитарно-бытовые помещения необходимо периодически подвергать дезинфекции. Душевые необходимо обеспечивать горячей водой в количестве достаточном для всех рабочих Смесительные приборы должны быть безопасными легко открываться и не подтекать. Температура воды 28 37 ºС.
2.Требования охраны труда к оборудованию и оснастке
Металлорежущие станки являются наиболее распространенными среди металлообрабатывающего оборудования. В их группу входят токарные фрезерные шлифовальные расточные и другие. Отличительной особенностью этих станков является кинематика их рабочих движений.
На этих станках заготовки получают вращательное движение или вращение совершает инструмент или режущий инструмент выполняет движение подачи.
Основными опасными производственными факторами при эксплуатации станков являются: вращающиеся станочные приспособления и заготовки образующаяся в процессе резания стружка.
При работе с высокими скоростями резания особое внимание должно быть уделено правильному и надежному закреплению заготовок.
Движущие части представляющие опасность должны быть ограждены. Конструкции ограждающих устройств должны быть прочными надежно крепиться не мешать производственной работе уборке и наладке станка.
Станки следует снабжать экранами защищающими рабочих и окружающих от травмирования или от брызг СОЖ. Конструкция экранов должна быть легкоподвижной и предусматривать возможность чистки смотровых окон от загрязнения. Конструкция станков и их элементов должны способствовать отводу стружки из зоны резания быть удобной для очистки от стружки пыли масла.
Станки на которых вспомогательные перемещения производятся при включении органов главного движения станка необходимо снабжать быстродействующими тормозными устройствами. Рычаги и рукоятки управления должны быть расположены в местах удобных для обслуживания и не требовать значительных перемещений рук рабочего. Местоположение этих органов и рукояток должно исключать возможность случайного включения.
Пусковые педали оборудования должны иметь надежное ограждение или предохранительные устройства исключающие возможность непреднамеренного включения оборудования по какой-либо случайной причине.
Все органы управления эксплуатируемого оборудования должны иметь четкие и ясные надписи и символы указывающие их назначение.
3. Характеристика и анализ производственных условий
Метеорологические условия или микроклимат в производственных условиях определяются следующими параметрами которые получили название показателей микроклимата: температурой скоростью относительной влажностью и атмосферным давлением окружающего воздуха.
Нормативные показатели производственного микроклимата установлены ГОСТ 12.1.005-88 (Общие санитарно-гигиенические требования к воздуху рабочей зоны) а также СанПиН 2.2.4.584-96 (Гигиенические требования к микроклимату производственных помещений).
Этими нормами регламентировали показатели микроклимата в рабочей зоне производственного помещения: температуру относительную влажность скорость движения воздуха в зависимости от способности организма человека к акклиматизации в разное время года характера одежды интенсивности производимой работы и характера тепловыделений в рабочем помещении.
В проектируемом механическом цехе выполняются работы средней тяжести (категория 2) в частности работы связанные с ходьбой и переноской небольших тяжестей (категория 2 б).
Для проектируемого механического цеха показатели микроклимата составляют [20]:
-температура воздуха 17 19 ºС в холодный период года и 19 21 ºС в теплый период года;
-относительная влажность воздуха 40 75 % в холодный и теплый периоды года;
-скорость движения воздуха = 02 05 мс в холодный период года и .= 05 1 мс в теплый период года.
Для поддержания требуемых параметров метеорологических условий помещений цеха в указанных пределах выполняются определённые мероприятия: применение технологических процессов и оборудования исключающих образование вредных веществ или попадания их в рабочую зону; защита от источников тепловых излучений устройство вентиляции и отопления; применение средств индивидуальной защиты.
Отопление проектируемого цеха предусмотрено смешанного типа: воздушное отопление а вдоль стен здания устанавливаются нагревательные приборы (радиаторы ребристые трубы) предохраняющие рабочие места от притоков холодного воздуха.
Эффективным средством обеспечения допустимых показателей микроклимата воздуха рабочей зоны является промышленная вентиляция. Вентиляцией называется организованный и регулируемый воздухообмен обеспечивающий удаление из помещения воздуха и подачу на его место свежего.
В проектируемом механическом цехе выполняется приточно-вентиляционная общеобменная вентиляция.
Для эффективной работы системы вентиляции важно чтобы были выполнены следующие технические и санитарно-гигиенические требования:
объем воздуха подаваемого в цех должен быть равен объему воздуха удаляемого из цеха; разница между ними не должна превышать 10 15 %;
свежий воздух необходимо подавать в те части цеха где количество вредных выделений минимально (или их нет вообще) загрязнённый или нагретый воздух удаляется из тех частей цеха где выделение вредных веществ максимально;
система вентиляции не должна вызывать переохлаждения или перегрева работающих;
система вентиляции не должна создавать шум на рабочих местах превышающий предельно допустимые уровни;
система вентиляции должна быть электро- пожаро- и взрывобезопасной проста по устройству надёжна в эксплуатации и эффективна.
При нормальном микроклимате и отсутствии вредных выделений количество воздуха при общеобменной вентиляции принимают в зависимости от объема помещения приходящегося на одного работающего.
Шум - это совокупность апериодических звуков различной интенсивности и частоты. С физиологической точки зрения шум - это всякий неблагоприятно воспринимаемый звук. Шум является одним из распространенных и неблагоприятных факторов на производстве.
Интенсивный шум на производстве способствует снижению внимания и увеличению ошибок при выполнении работы. Из-за шума снижается производительность труда и ухудшается качество работы. Шум затрудняет своевременную реакцию работающих на предупредительные сигналы внутрицехового транспорта (автопогрузчики мостовые краны и т. п.) что способствует возникновению несчастных случаев на производстве.
Источником шума в цехе являются машины механизмы агрегаты и другое оборудование цеха. Степень влияния шума зависит от его интенсивности и продолжительности воздействия состояния центральной нервной системы и что очень важно от индивидуальной чувствительности организма к акустическому раздражителю. Вредное воздействие шума отражается на органах слуха оказывает отрицательное влияние на центральную нервную систему и весь организм в целом.
Гигиенические нормативы шума определены ГОСТ 12.1.003-83 (Шум. Общие требования безопасности) и СН2.2.42.1.8.562-96 (Шум на рабочих местах в помещениях жилых общественных зданий и на территории жилой застройки. Постановление Госкомнадзора России от 31 декабря 1996 г. № 36.). Допустимый уровень звука и эквивалентный уровень звука на постоянных рабочих местах и в рабочих зонах в производственных помещениях и на территории предприятий составляет 75 80 дБА.
Понизить уровень шума для обеспечения максимального комфорта и других условий труда позволяет использование мероприятий по борьбе с шумом:
–снижение звуковой мощности источника шума;
–изменение направленности излучения шума;
–акустическая обработка помещений;
–уменьшение шума на пути его распространения;
–применение глушителей шума;
–применение средств индивидуальной защиты (вкладышей наушников шлемов).
Вибрация - это малые механические колебания возникающие в упругих телах. Вибрация относится к факторам обладающим высокой биологической активностью. Действие вибрации зависит от частоты и амплитуды колебаний продолжительности воздействия демпфирующих свойств тканей организма человека явлений резонанса и других условий.
Гигиеническое нормирование вибраций осуществляется по ГОСТ 12.1.012-90 (Вибрационная безопасность) и СН 2.2.42.1.8.566-96.
Допустимые параметры вибраций передаваемых на руки от 99 до 120 дБА при средних геометрических частотах активных полос от 8 до 2000 Гц.
Вибрация высокой интенсивности при продолжительном воздействии вызывает изменения в нервной и сердечно-сосудистой системах опорно-двигательном аппарате желудочно-кишечном тракте органах равновесия.
Основными методами борьбы с вибрациями машин и оборудования являются:
–снижение виброактивности машин;
–отстройка от резонансных частот;
–вибродемпфирование;
–повышение жесткости системы;
–применение индивидуальных средств защиты (для рук - виброизолирующие рукавицы перчатки вкладыши и прокладки; для ног виброизолирующая обувь стельки подметки).
Для уменьшения вибраций используются виброизоляция (виброопоры из резины пружины рессоры). При невозможности проведения указанных технических мероприятий обязательно использование индивидуальных средств защиты (виброботинки виброрукавицы и т. д.).
Уровни вибрации на рабочих местах определяются на установке для испытания на нормы точности. Проверка уровня вибрации производится при испытании каждого нового образца оборудования.
Для профилактики профессиональных заболеваний и снижения вредного воздействия шума и вибраций необходимо применять предупредительные меры. Прежде всего они должны учитываться при проектировании строительстве и организации технологического процесса. Шумное с интенсивной вибрацией процессы и оборудование размещается в изолированных помещениях. Для снижения фона отраженного шума стены потолки нужно облицовывать звукопоглощающими материалами. Вращающиеся движущиеся части технологического оборудования являются источниками шума и вибраций поэтому они должны тщательно пригоняться балансироваться смазываться.
4. Расчет освещенности цеха
Правильно спроектированное и выполненное освещение на предприятиях обеспечивает возможность нормальной производственной деятельности. Сохранность зрения человека состояние его центральной нервной системы и безопасность на производстве в значительной мере зависят от условий освещения. От освещения зависят также производительность труда и качество выпускаемой продукции.
Основной задачей производственного освещения является поддержание на рабочем месте освещенности соответствующей характеру зрительной работы.
При освещении проектируемого механического цеха используется совмещенное освещение при котором недостаточное по нормам естественное освещение дополняется искусственным. При этом естественное освещение является комбинированным то есть сочетающим верхнее (осуществляемое через световые фонари) и боковое (осуществляемое через световые проемы) освещения. Искусственное освещение проектируемого цеха также является комбинированным то есть представляющим совокупность местного и общего освещение.
Освещенность на рабочих местах и поверхностях станков класса Н и П должна быть не ниже 2000 лк при освещении газоразрядными лампами [20]. Общее искусственное освещение цеха с металлорежущими станками должно быть равным 400 лк при освещении газоразрядными лампами [23].
Для расчета рабочего искусственного освещения цеха в качестве исходных данных принимается:
-тип источника света: для освещения производственного помещения - лампа дуговая ртутная люминесцентная ДРЛ-1000 имеющая величину светового потока ФП = 57000 лм
-тип системы освещения - комбинированная;
-характеристики цеха: длина - 81 м ширина - 50 м высота расположения светильников – 72 м;
-коэффициент минимальной освещенности равный отношению средней освещенности и минимальной для ламп ДРЛ z = 115.
Расчет общего равномерного искусственного освещения горизонтальной рабочей поверхности выполняется методом коэффициента использования светового потока.
Световой поток (лм) одной лампы [23]:
где Ен - нормированная минимальная освещенность по СНиП 23-05-95(Искусственное и естественное освещение).
S - площадь освещаемого помещения S = 4050 м2;
z - коэффициент неравномерности освещения z = 115 [23];
Кз - коэффициент запаса Кз = 15 [23];
н - коэффициент использования светового потока;
N - число светильников в помещении.
Коэффициент использования светового потока н давший название методу расчета определяют по СНиП 23-05-95(Искусственное и естественное освещение) в зависимости от типа светильника коэффициентов отражения потолка ρп стены ρс пола ρр размеров помещения определяемых индексом помещения:
где А - длина помещения в плане А = 81 м;
В - ширина помещения в плане В = 50 м;
Н - высота подвеса светильников над рабочей поверхностью Н = 72 м.
По [20] для коэффициентов отражения потолка ρп = 30% стены ρс =10% пола ρр = 10% и индекса помещения i = 4 коэффициент использования светового потока н =063.
Таким образом определяется число светильников в помещении:
Таким образом для освещения проектируемого механического цеха принимается 176 светильников типа УПДДРЛ с лампами ДРЛ-1000.
Определяется световой поток:
Отклонение потока выбранной лампы ДРЛ-1000 (ФП = 57000 лм) от расчетного:
что лежит в пределах -10% +20%.
Немаловажное значение имеет правильная цветовая отделка помещений. Покрытие стен должно быть матовым без бликов; верхние участки стен и потолок следует окрашивать в белый цвет так как этот цвет обладает наибольшей отражающей способностью и тем самым увеличивает освещенность помещения.
5. Электробезопасность. Расчет заземляющего устройства
Электроэнергия в механическом цехе является основным видом энергии поэтому электробезопасности уделяется большое внимание.
Защитным заземлением называется преднамеренное электрическое соединение с землей металлических нетоковедущих частей установок которые могут оказаться под напряжением.
Для снятия напряжений до безопасной величины относительно земли на металлических частях оборудования необходимо произвести расчет защитного заземления. Защитное заземление состоит из группы заземлителей расположенных непосредственно в земле и соединительной полосы. С их помощью осуществляется надёжное заземление станка.
Согласно "Правилам устройства электроустановок" в электрических сетях напряжением до 1000 В сопротивление заземляющих устройств не должно превышать 4 Ом.
6. Мероприятия по обеспечению пожарной безопасности
Пожары и взрывы на производстве являются причинами больших материальных ущербов а в ряде случаев уносит жизни обслуживающего и другого персонала. Поэтому все механические цеха и другие помещения завода должны быть защищены от таких случаев. Пожарная безопасность обеспечивается мерами пожарной профилактики активной пожарной дисциплиной применением противопожарной сигнализации а также разными средствами пожаротушения.
Механический цех по изготовлению запасных частей солнечной шестерни в соответствии с НПБ 105-03 по пожарной безопасности относится к категории Г (производства связанные с обработкой несгораемых веществ и материалов в холодном состоянии) так как все основные конструкции выполнены из несгораемых материалов - железобетона кирпича металлоконструкций.
В целях предупреждения пожаров и взрывов в цехе должны проводиться ежегодные организационные и инженерно-технические мероприятия в соответствии с правилами и нормами охраны труда.
Гидросистема смазки и система подачи СОЖ не должны иметь посторонних утечек масла керосина и других жидкостей. При возгорании электропроводки применяют огнетушители с составом окиси углерода (ОУ-5 ОУ-8). При возгорании других веществ применяют порошковые огнетушители (ОПС-10).
В цехе на рабочих местах в пожароопасных зонах должны находиться средства пожаротушения: огнетушители пожарные комплекты рукава краны установки стационарного и передвижного пожаротушения.
По рекомендации СНиП 21-01-97 (Пожарная безопасность зданий и сооружений) стены цеха и других помещений завода должны быть несгораемыми с пределом огнестойкости не менее 075ч. Плиты технологических полов должны быть трудносгораемыми с пределом огнестойкости не менее 05ч или несгораемыми. Перекрытия плит допускается из сгораемых материалов: линолеума паркета и т. д. Подпольное пространство под технологическим полом должно разделяться несгораемыми диафрагмами на отдельные отсеки площадью не более 250 м2.
Необходимо обеспечить пожарную безопасность вентиляционных систем путем проведения мероприятий исключающих возможность образования источников загорания. Принять меры к недопущению распространения огня по воздуховодам для этого в воздуховоде устраивают противопожарные заслонки в местах прохода воздуховодов через противопожарные стены (они автоматически срабатывают при возникновении пожара).
В цехе должна быть предусмотрена автоматическая сигнализация. В машинных залах под технологическим полом за подвесным потолком рекомендуется устанавливать извещатели реагирующие на появление дыма. Данная система сигнализации должна обеспечивать автоматический пуск в действие средств пожаротушения
внутренними пожарными водопроводами ручными и передвижными огнетушителями сухим песком асбестовыми одеялами. Пожарные краны должны быть установлены в коридорах на площадках лестничных клеток у входов. Щиты противопожарной защиты должны быть оснащены ручными углекислотными огнетушителями так как для данного класса помещений рекомендуется использовать химические средства тушения пожара. Для тушения пожаров в замкнутых объемах каким и является помещение техотдела применяют углекислый газ для прекращения подачи кислорода воздуха к очагу возгорания. Первичными средствами пожаротушения могут послужить ручные огнетушители типа: ОУ-6 и ОУ-8. В помещении в качестве первичных средств пожаротушения предусмотрены порошковые огнетушители типа ОПС-6 однако их применение может произвести значительный ущерб в следствии порчи дорогостоящей электронной аппаратуры поэтому рекомендуется применять пенный огнетушитель типа ОХП-10.
Проектируемый цех снабжен индивидуальными средствами пожаротушения огнетушителями ОХП-10. Количество огнетушителей принято из расчета 1 огнетушитель на 600 м2 т.к. общая площадь производственного участка равна: 3006 м2 то общее количество огнетушителей равно:
принимаем 6 огнетушителей.
7. Защита окружающей среды
Создание безотходных производств требует решения сложных организационных технических технологических и экономических задач. Для разработки и внедрения безотходных производств можно выделить ряд взаимосвязанных принципов.
Например принцип системности лежащий в основе создания безотходных производств позволяет учесть усиливающуюся взаимосвязь и взаимозависимость производственных социальных и природных процессов. Это подтверждается тем что каждый отдельно взятый процесс или производство необходимо рассматривать как элемент динамично развивающейся эколого-экономической системы включающей кроме материального производства и другой хозяйственно-экономической деятельности человека природную среду (популяции живых организмов; атмосферу гидросферу литосферу биогеоценозы ландшафты) а также человека.
Другим важнейшим принципом создания безотходного производства является комплексность использования ресурсов основанным на максимальном использовании сырьевых компонентов и энергетического потенциала. Все сырье практически является комплексным; и в среднем более трети его количества составляют сопутствующие элементы которые могут быть извлечены только при комплексной его переработке.
Не менее важным принципом создания безотходного производства является цикличность материальных потоков. К цикличным материальным потокам можно отнести замкнутые водо- и газооборотные циклы. Последовательное применение этого принципа должно привести к формированию сознательно организованного и регулируемого техногенного круговорота вещества и связанных с ним превращений энергии. При разработке технологических процессов обеспечивающих малоотходность или безотходность производства необходимо выполнить требования по ограничению воздействия производства на окружающую природную и социальную среды с учетом планомерного и целенаправленного роста его объемов и экологического совершенства. Это в первую очередь связано с сохранением таких природных и социальных ресурсов как атмосферный воздух вода поверхность земли рекреационные ресурсы здоровье населения. Реализация такого подхода осуществима лишь в сочетании с эффективным мониторингом развитым экологическим нормированием и многозвенным управлением природопользованием.
Еще одним определяющим принципом создания безотходного производства является рациональность организации производства. Определяющими здесь выступают требования: разумного использования всех компонентов сырья; максимального уменьшения энерго- и трудоемкости производства; поиск новых экологически обоснованных сырьевых и энергетических технологий.
Это позволит снизить отрицательное воздействие на окружающую среду и уменьшить нанесенный ей ущерб. Конечной целью в данном случае следует считать оптимизацию производства одновременно по энерготехнологическим экономическим и экологическим параметрам. Основным путем достижения этой цели является разработка новых и усовершенствование существующих технологических процессов и производств.
Совокупность работ связанных с охраной окружающей среды и рациональным освоением природных ресурсов позволяет сформулировать главные направления создания мало- и безотходных производств. К ним относятся: комплексное использование сырьевых и энергетических ресурсов; усовершенствование существующих и разработка принципиально новых технологических процессов и производств и соответствующего оборудования; внедрение водо- и газоотборных циклов на базе эффективных газо- и водоочистных методов; кооперация производств с использованием отходов одних производств в качестве сырья для других и создание безотходных территориально-производственных комплексов.
При совершенствовании существующих а также при разработке принципиально новых технологических процессов необходимо соблюдение ряда общих требований: осуществление производственных процессов с использованием минимально возможного числа технологических стадий (аппаратов) так как на каждой из них образуются отходы и теряется сырье; применение непрерывных процессов позволяющих наиболее эффективно использовать сырье и энергию; увеличение единичной мощности агрегатов до оптимальных значений; интенсификация производственных процессов их оптимизация и автоматизация; создание энерготехнологических процессов позволяющих полнее использовать энергию химических превращений экономить энергоресурсы сырье и материалы и увеличивать производительность агрегатов.
При организации безотходных производств большое значение имеет кооперирование предприятий различных отраслей промышленности.
Образование отходов является одним из основных факторов определяющих масштабы вредного воздействия производства на окружающую среду. Следовательно в качестве показателя экологичности технологического процесса может использоваться такой критерий как количество отходов. Кроме количественной оценки отходов возникает необходимость учета их качества позволяющего определить токсичность компонентов отходов и их опасность для окружающей среды.
Для оценки токсичности твердых отходов предполагается использование ПДКж так как при хранении твердых отходов возможно их растворение в атмосферных осадках сточных и грунтовых водах.
Критерий экологичности учитывает жидкие газообразные и твердые отходы. При этом количество i-го компонента в жидких отходах определяется по формуле:
где Q – количество жидких отходов м3ч; п – число рабочих дней в году; Р – количество выпускаемой продукции тгод.
При расчете первых двух слагаемых учитываются все источники жидких и газообразных отходов. Так для газообразных выбросов для каждого компонента рассчитывается по формуле:
где С Vj – объем выбросов в j-м источнике м3ч.
Количество i-го токсичного компонента выбрасываемого с газообразными отходами j-м источником mjг определяется суммированием miгj по i-му компоненту с учетом рабочего времени:
Средняя концентрация i-го компонента в газообразных отходах рассчитывается по уравнению
где ΣVj – общий объем вредных выбросов м3ч.
Количество i-го токсичного компонента в твердых отходах
где Тm – количество твердых отходов тгод; ri – содержание i-го токсичного компонента (элемента) в твердых отходах %.
При безотходной технологии коэффициент Кэк равен нулю.
Рассмотренный критерий имеет четкую экологическую значимость так как его значение зависит от количества отходов и от их токсичности определяющих воздействие технологического процесса на окружающую среду. Следовательно он может быть использован для сравнения традиционных технологических процессов получения товарной продукции с перспективными безотходными и малоотходными технологиями что существенно облегчает оценку безотходности.
4 Конструкторская часть.doc
1. Проектирование станочного приспособления
для выполнения операции 055-сверлильной
Исходными данными для проектирования станочного приспособления являются:
)Технологический процесс выполнения операции разработанный применительно к условиям серийного производства.
Обработка отверстий производится на радиально-сверлильном станке модели 2М55 в следующей последовательности:
-сверление отверстий 1243 мм и глубиной
-зенкование фасок 16х45°;
-нарезание резьбы М14х15-7Н.
Заготовка детали – поковка из конструкционной легированной стали марки 20ХНЗА ГОСТ 4543-71 твёрдостью 255НВ. Поверхность углубления обработана окончательно и имеет шероховатость Ra63. На торце углубления имеется центровое отверстие выполненное по ГОСТ 14034-74. На выполняемые отверстия установлен позиционный допуск 05 мм.
При конструировании приспособления необходимо предусмотреть возможность его автоматизации для перехода к безлюдной технологии обработки детали. Предполагаемая продолжительность выпуска изделий – не менее 3 лет.
Тип технологической оснастки и рекомендации по оснащению производства.
Пользуясь рекомендациями ЕСТПП выберем подходящий тип приспособления в зависимости от коэффициента загрузки Кз и продолжительности выпуска изделий Тн.
Примем месячный фонд времени работы приспособления Fn100 час. Штучно-калькуляционное время по техпроцессу операции tшк=521 мин= =0087 час; число повторений операций в месяц Non=N12=150012=125. К расчёту примем Non=130. Коэффициент загрузки:
Согласно исходной информации величина Тн3 года=36 месяца. Для расчётных значений Кз и Тн по графику [21] с.8 рис. 3 наиболее подходящим типом является специализированное наладочное приспособление. В дальнейшем будем проектировать СНП к радиально-сверлильному станку мод. 2М55.
1.1. Выбор схемы приспособления и конструкции
установочных деталей. Расчёт погрешности базирования
Согласно техпроцессу операции и исходным данным обработка отверстий в детали производится на радиально-сверлильном станке последовательно сверлением зенкованием фасок нарезанием резьбы. Инструменты последовательно вставляются в шпиндель станка совершающий вращательное и поступательное движения. Таким образом предусмотрена одноместная однопозиционная схема обработки отверстий последовательно несколькими инструментами. Приспособление должно устанавливаться в определённом положении. При базировании заготовку следует лишать шести степеней свободы.
Заготовка детали устанавливается в приспособлении на предварительно обработанную на токарном станке цилиндрическую поверхность которая служит установочной базой. Цилиндрическая поверхность после токарной обработки имеет диаметр шероховатость Ra63. Таким образом приходим к стандартной схеме установки на наружную цилиндрическую поверхность с упором в торец цилиндрической поверхности 1439 мм. Для реализации этой схемы деталь базируется в призмы упираясь в призмы торцом цилиндрической поверхности 1439. Заготовка закрепляется сходящимися само центрирующими призмами. Кондукторная плита в которой установлены сменные кондукторные втулки базируется посредством конуса на поверхность центрового отверстия и прижимается с помощью пневмоцилиндра. Для снятия заготовки из приспособления необходимо поднять кондукторную плиту повернуть её в любую сторону и после этого разжать само центрирующие призмы. Использование такой конструкции приспособления обеспечивает совпадение измерительной конструкторской и технологической баз что позволяет полностью исключить погрешность базирования. Существенно сокращается время на открепление и снятие заготовки т.е. уменьшается вспомогательное время и увеличивается производительность. Схема установки заготовки в приспособление показана на рис.3.1.
1.2. Расчёт сил закрепления заготовки
При обработке отверстий в детали наибольших значений достигает осевая сила при сверлении и момент резания М когда глубина резания и подача максимальны. Осевая сила Ро полностью воспринимается зажимными элементами приспособления (призмами) кроме того она направлена вдоль выполняемого размера и обеспечивает дополнительное усилие зажима. Действие момента резания М который создаёт силу Рвр стремящуюся повернуть заготовку в приспособлении (рис. 6) уравновешивается и нейтрализуется кондукторными втулками ([22] с. 76). Однако в случае обработки без кондуктора (досверливание отверстий и т.п.) сила Рвр уравновешивается силами закрепления Q создаваемыми с помощью зажимных устройств. Определим значения М и Рвр. Из технологического процесса операции схемы установки и исходных данных к проекту следует что: материал заготовки – сталь 20ХНЗА твёрдостью 255НВ; обработка ведётся стандартным спиральным сверлом диаметром D=1243 мм из быстрорежущей стали со скоростью резания V=312 ммин и подачей S=016 ммоб; максимальная глубина резания:
Для этих условий согласно [12] с. 209 момент резания:
Мкр=См·Dqm·Syн·Км=33836 Н·м
(расчёт режимов резания проводится в пункте 2.10 технологической части).
Проворачивающая сила:
где К=006м – радиус окружности на которой расположены отверстия:
Направления сил Мкр и Рвр показаны на расчётной схеме (рис. 3.2). Условия равновесия заготовки описываются уравнением:
где Q - сила противодействующая вращательному моменту;
=952=475 мм – плечо силы.
Сила зажима согласно [22] с.74:
где P = 1965 кН – вращающая сила; М = 33836 Нм
f = 016 – коэффициент трения заготовки о призмы ([22])
k= коэффициент запаса; R = 006 м
По методике [22] с. 84: k = k0*k1*k2*k3*k4*k5*k6
k0 = =12*11*12=16 – коэффициент учитывающий неточность расчётов;
k1 =10 – коэффициент учитывающий наличие случайных неровностей на поверхности заготовки и увеличение сил резания;
k2 = 13 – коэффициент учитывающий затупление инструмента;
k3 = 10 – коэффициент учитывающий непрерывность процесса резания;
k4 = 10 – коэффициент учитывающий непостоянство сил зажима;
Рис. 3.1. Схема базирования заготовки в приспособлении.
Рис. 3.2. Схема расчета сил резания.
K5 = 10 – коэффициент учитывающий удобство расположения рукоятки;
k6 = 12 – коэффициент учитывающий поверхность контакта заготовки с зажимными элементами.
K = 16*10*13*10*10*10*12 = 25
Т.к. усилие зажима создается с двух сторон то сила зажима одной призмой:
Выбор конструкции и размеров зажимных устройств. Расчёт погрешности закрепления. Согласно схеме (рис. 3.3) деталь устанавливается в призмы. Каждая призма прижимается к детали с силой Q1=5428 Н.
Для закрепления заготовки можно воспользоваться двумя самоцентрирующимися призмами приводящимися в действие поршневым вращающим двигателем через кривошипно-шатунный механизм. Время закрепления в 45 с. Столько же времени требуется и на открепление. Общее время на закрепление и открепление детали:
Для уменьшения размеров приспособления принимаю плечо кривошипа hк = 003 м. Тогда поршневой двигатель должен развивать момент Мкр.дв. = Q* hк = 5428*003 = 16284 Нм. Приняв размеры зубчатого колеса двигателя дел = 60 ммопределим размеры поршневого двигателя:
где р = 08 Мпа – давление воздуха в сети;
d – диаметр цилиндра;
dдел = 006 м – делительная окружность колеса.
Принимаем диаметр цилиндра d = 009 м.
Наиболее слабым звеном зажимного устройства следует считать оси шатунов кривошипа которые подвергаются усилию среза. Оси шатунов выполняются из стали 40Х ГОСТ 4541-71 имеющей [т] = 294 Мпа. Проверим их на прочность. Усилие среза:
где - напряжения среза в штифте;
т=03*294=882 Мпа 90 Мпа – допустимые напряжения среза ([23] c. 40).
Таким образом конструкция и основные параметры зажимного устройства установлены. Т.к. усилие зажима заготовки прилагается в направлении перпендикулярном выполняемому размеру то погрешность закрепления Eз=0.
1.3. Вспомогательные устройства направляющие и корпусные
детали технологической оснастки
Схема проектируемого приспособления проста. Не вызывает затруднений и его эксплуатация. Заготовку массой М=43 кг с помощью крана устанавливают в призмы. Далее поворотом рукоятки крана включают пневмодвигатель. Заготовка закрепляется. Далее поворачивается кондукторная плита и с помощью пневмоцилиндра опускается до соприкосновения центра с поверхностью центрового отверстия. Открепление и съем детали после обработки осуществляется в обратной последовательности.
Для повышения жесткости сверла предусмотрено переднее направление инструмента с помощью кондукторных втулок 7051-2121 ГОСТ 18431-73. Базирование заготовки осуществляется в призмах 7033-0039 ГОСТ 12195-66 ([24] c. 363).
Корпус приспособления сварен из пластин вырезанных из листового проката. Материалом служит сталь 3 ГОСТ 380-71. Конфигурация и размеры корпуса диктуются его функциональным назначением. Он имеет продольную вертикальную плоскость симметрии. Базовая деталь – прямоугольная пластина с «ласточкиным хвостом» (направляющие кулачков) и выборкой внутри располагается горизонтально. К ней крепятся две вертикальные пластины – стойки. Базовая деталь вместе со стойками образуют П-образный корпус который приваривается к опорной пластине.
Сварная конструкция технологична имеет небольшую массу позволяет изготавливать корпус с минимальными затратами в максимально сжатые сроки.
Расчёт точности выполнения технологической операции.
Погрешность положения заготовки в приспособлении:
где Еn = 001 мм [22] – погрешность изготовления приспособления;
- погрешность возникающая из-за износа приспособления;
=05 ([21] с. 32) – эмпирический коэффициент;
N=1500 – количество контактов заготовки с опорами за год;
- погрешность установки приспособления на станок (свободная установка):
Т.к. погрешность закрепления заготовки то погрешность установки мм что меньше допуска на расстояние между осями отверстий Th=005 мм ([19] c. 34).
Следовательно приспособление позволяет обработать деталь с заданной точностью.
1.4. Эффективность использования и стоимость
технологической оснастки
Рассчитаем ориентировочную стоимость проектируемого приспособления и стоимость обработки отверстий в детали.
По методике [19] с. 190 ориентировочно стоимость приспособления определяется по формуле:
где К – количество деталей в приспособлении;
Уc – удельная стоимость.
По спецификации к сборочному чертежу общее количество деталей в приспособлении равно в т.ч. оригинальных – 25.
Все элементы приспособления крепятся к корпусу; его конструкция проста. Зажимные устройства – стандартные цилиндры. Габаритные размеры приспособления (890 х 370 х 310) не велики а его изготовление в инструментальном цехе не вызовет затруднений. На основании изложенного отнесём приспособление к 3-ей группе сложности (средняя стоимость) и будем считать что К=25 примем по табл. 2 с. 39 [21] Уc=232 т.руб.
Тогда стоимость приспособления:
S = 25·232=580 т.руб.
За выполнение технологической операции сверловщик получит зарплату:
L= tшк·l=521*1886560=1638 руб
где tшк – штучно калькуляционное время операции.
L = 18865 рубч ([21] c. 38) – тарифная ставка станочника III разряда.
Примем для серийного производства накладные расходы цеха: Z=200%; срок приспособления
Коэффициенты связанные с проектированием и эксплуатацией приспособления дп=05 и дэ=02 ([22] c.189) рассчитаем стоимость операции:
С=L(1+)+(1++дэ)=1638(1+)+(1+=10037 руб
2. Проектирование приспособления для выполнения
операции 085-фрезерная с ЧПУ
Тип технологической оснастки.
По техпроцессу tшк=312мин=0052час.
Коэффициент загрузки:
По графику [21] с.8 рис. 2.3 наиболее подходящим типом является специализированное наладочное приспособление (СНП).
2.1. Выбор схемы приспособления и конструкции установочных
деталей. Расчёт погрешности базирования
Согласно техпроцессу операции обработка паза производится на вертикально-фрезерном станке с ЧПУ модели 6Р13Ф3 концевой фрезой из быстрорежущей стали установленной в оправке. Предусмотрена одноместная однопозиционная обработка паза одним инструментом. Приспособление устанавливается на стол станка и фиксируется в определенном положении. При базировании заготовка лишается шести степени свободы. Схема установки заготовки (рис. 3.3) – на наружную цилиндрическую поверхность с упором в торец. Загрузка и выгрузка заготовки производится промышленным роботом. Закрепление заготовки производится само центрирующими призмами. При такой схеме базирования происходит несовпадение измерительных и технологических баз. При этом погрешность базирования составляет половину допуска на размер поверхности т.е.
Рис. 3.3. Схема базирования заготовки.
2.2. Расчет сил закрепления заготовки
При обработке паза наибольших значений достигает сила Pz. Действие Pz уравновешивают и нейтрализуют силами закрепления Q создаваемыми с помощью зажимных устройств. Сила резания Pz определена в пункте 3.10. технологической части проекта и составляет:
где Cp=682; yp=072; Up=10; qp=086 ([8])
t=65 мм; S=004 ммзуб; B=16 мм; z=4 шт; D=16 мм; n=400 обмин:
Направление действия Pz показано на рис. 3.4.
Рис. 3.4. Схема расчета сил резания.
Сила зажима согласно [22] с. 44:
Так как усилие зажима создается с двух сторон то сила зажима одной призмой: .
2.3. Выбор конструкции и размеров зажимных устройств.
Расчет погрешности закрепления
Согласно схеме деталь устанавливается в самоцентрирующие призмы. Каждая призма прижимается к детали с силой Q=4925 кН
Для закрепления заготовки можно воспользоваться двумя самоцентрирующими призмами приводящимися в действие пневмоцилиндром посредством реечной зубчатой передачи и винт-гайки.
Для создания зажимной силы Q=4925 кН рассчитаем размеры передачи винт-гайка и реечной зубчатой передачи.
Средний диаметр резьбы:
где - отношение высоты гайки к среднему диаметру резьбы;
[q]=10 Мпа – допускаемое давления для резьбы (незакаленная сталь по бронзе)
Высота профиля резьбы:.
Наружный диаметр резьбы: .
Внутренний диаметр резьбы: .
Ход резьбы (число заходов резьбы n=1):
Следовательно угол подъма резьбы .
Коэффициент трения стали по бронзе при слабой смазке примем f=01 ([23] с. 268). Значит и угол трения . Условие самоторможения винта обеспечено так как .
Крутящий момент в опасных сечениях винта по [23] с .268:
Для создания такого момента при диаметре делительной окружности dдел зубчатого колеса равной 63 мм (m=3; z=21 шт) необходима сила тянущая рейку такая сила может быть создана при помощи стандартного пневмоцилиндра диаметром Dц=80 мм ГОСТ 15608-81 ([20]с.426 табл.1).
Проверим зубья передачи на изгибную прочность.
где YF=408 ([23] с. 192 рис. 21.23) – коэффициент формы зуба;
- для прямозубых передач
- коэффициент динамической нагрузки
- коэффициент ширины венца
Допустимые напряжения изгиба:
где - предел выносливости зубьев при изгибе (с.195 табл. 12.6);
SF=17 – коэффициент безопасности;
KLF=1 – коэффициент долговечности;
KFC=075 – при двухсторонней нагрузке передачи;
Так как то в передаче не возникают опасных напряжений изгиба. Принятые значения z=21 и m=3 мм удовлетворяют условию изгибной прочности зубьев.
Таким образом конструкция и основные параметры зажимного устройства установлены. Так как усилие зажима заготовки прилагается в направлении перпендикулярном выполняемому размеру то погрешность закрепления .
2.4. Расчет точности выполнения механической операции
Погрешность положения заготовки в приспособлении:
где - погрешность изготовления приспособления.
- погрешность установки приспособления на станок.
Погрешность установки заготовки:
Так как погрешность установки заготовки в приспособление меньше допуска на размер то условие выполняется. По рекомендации [25] с.171 назначим допуск на расстояние от оси заготовки до нижней плоскости основания равный TL=±005 мм.
2.5. Эффективность использования и стоимость технологической оснастки
Стоимость приспособления:
где - удельная стоимость.
Приняв k*=33in – количество оригинальных деталей. Тогда по [22] с. 39 т.2 yc=23.2 т.руб.
Так как загрузка и выгрузка детали производится промышленным роботом а станок функционирует в полностью автоматическом цикле то рабочий на данной операции отсутствует.
Примем для серийного производства накладные расходы цеха z=200%; срок службы приспособления коэффициент q=05 и qэ=02 рассчитаем стоимость операции:
3. Проектирование контрольного приспособления для контроля
биений цилиндрических поверхностей и зубчатых венцов
Согласно заданию необходимо спроектировать быстродействующее бесшумное контрольное приспособление для контроля радиального биения цилиндрических поверхностей и зубчатых венцов (рис. 3.5)
Рис. 3.5. Схема контролируемых размеров.
Необходимо предусмотреть возможность полной механизации и автоматизации приспособления и возможности контроля без участия человека.
Выбор схемы приспособления и конструкций установочных деталей. Расчет погрешности базирования.
Согласно чертежу детали в качестве измерительной базы служит ось детали. Для обеспечения наибольшей точности измерений необходимо стремиться к тому чтобы конструкторская технологическая и измерительная базы совпадали (принцип единства баз). Поэтому в качестве базовых поверхностей детали при измерении биений следует использовать поверхность центрового отверстия и фаску.
Такую схему базирования можно реализовать установкой заготовки в центрах (рис. 3.6).
Рис. 3.6. Схема контрольного приспособления.
При базировании заготовки в центрах обеспечивается совпадение измерительной и технологической баз следовательно погрешность базирования заготовки в приспособлении .
3.1. Выбор конструкции и размеров установочных измерительных и вспомогательных элементов. Расчет погрешности закрепления
Согласно схеме (рис. 3.6) деталь устанавливается в центрах. Базовые поверхности центровых отверстий имеют шероховатость Ra 32. Для закрепления детали можно воспользоваться выдвижным шпинделем в котором установлен центр приводимым в движение вручную с помощью винт-гайки или в перспективе – пневмоцилиндром. Так как деталь имеет сравнительно большую массу то при закреплении необходимо прикладывать большие усилия. Для уменьшения сил трения и устранения рывков при вращении центра устанавливается в шариковые радиально-упорные подшипники.
При измерении радиального биения зубчатых венцов за базовые поверхности принимаются эвольвентные поверхности зубьев. В качестве установочных элементов применяются пальцы имеющие сферический конец. Диаметр сферической поверхности определяется по формуле ([18] с. 55):
где r0 – радиус основной окружности мм;
r2 – расстояние точки контакта сферы от оси детали:
где ha – высота головки зуба;
rв – радиус окружности выступов;
z – число зубьев венца;
S – толщина зуба по дуге делительной окружности;
rд – радиус делительной окружности;
Для наружного зубчатого венца:
Полученное значение диаметра сферы округляем до 16 мм.
Для наружного зубчатого венца диаметр установочного пальца равен
Для внутреннего зубчатого венца диаметр сферы Dпв=75 мм (из тех. условий к чертежу).
В качестве измерительных устройств применяются индикаторы часового типа ИЧ-5 ГОСТ 577-68 имеющие точность измерения 001 мм что составляет 18-110 контролируемых параметров (допуска на радиальное биение).
Так как усилие зажима в приспособлении прикладывается в направлении параллельном оси изделия и следовательно перпендикулярном контролируемым параметрам (радиальное биение) то погрешность закрепления равна нулю .
3.2. Вспомогательные устройства направляющие и корпусные
К вспомогательным устройствам в данном приспособлении относятся фиксатор предназначенный для предотвращения поломки установочного пальца для контроля внутреннего венца; защелка для стопорения установочного пальца для контроля наружного зубчатого венца.
Схема проектируемого приспособления проста. Не вызывает затруднений и его эксплуатация. Изделие с помощью подъемника устанавливается в центрах. Далее удерживая деталь от проворота поворотом штурвала производится зажим детали. Деталь закрепляется. Затем на стойке приспособления устанавливается планка с индикаторами производится их выверка (установка на ноль). После этого проворачивая заготовку за штурвал производится контроль цилиндрических поверхностей. Затем расфиксировав защелки производится пошаговый контроль зубчатых венцов (последовательный или параллельный).
Корпус приспособления состоит из двух стоек сваренных из листовой стали и отрезков круглого проката и механически обработанных устанавливаемых на опорной плите. Сборно-сварная конструкция корпуса технологична имеет небольшую массу позволяет изготавливать корпус с минимальными затратами в максимально сжатые сроки.
3.3. Расчет требуемой точности оснастки
Погрешность установки детали в приспособление:
По рекомендации [8] примем погрешность изготовления приспособления погрешность связанная с износом установочных деталей:
Величина погрешности установки:
Из технических условий к детали видно что минимальное радиальное биение поверхностей детали составляет Fr=008 мм что больше чем погрешность установки детали в приспособлении. Следовательно контролируемые параметры могут быть измерены в приспособлении с требуемой точностью.
3.4. Эффективность использования и стоимость
Необходимо рассчитать ориентировочную стоимость контрольного приспособления.
По методике [19] с .40 стоимость приспособления S при проектировании определяют по формуле:
где k – количество деталей в приспособлении шт.;
yc – удельная себестоимость.
По спецификации к чертежу общее количество деталей в приспособлении равно 82 штук в том числе оригинальных (включая детали корпуса) – 24. Корпус собирается из двух стоек и опорной плиты на винтах и двух штифтах; его конструкция проста.
Габаритные размеры приспособления 1440 х 300 х 470 мм сравнительно невелики а его изготовление в инструментальном цехе не должно вызвать затруднений. На основании изложенного отнесем приспособление к 3-ей группе сложности (средняя сложность) и будем считать что k=24 то есть количеству только оригинальных деталей. Примем по [21] с. 39 табл.2 yc=17400 р. Тогда стоимость контрольного приспособления составляет:
4. Проектный расчет хвостового долбяка
Для нарезания внутреннего зубчатого венца в детали используется зуборезный долбяк. Так как обработка ведется в труднодоступном месте (малый диаметр отверстия и небольшая его глубина) то подобрать стандартный инструмент затруднительно. Поэтому необходимо спроектировать специальный инструмент.
Исходные данные нарезаемого зубчатого венца:
угол профиля рейки .
Число зубьев долбяка:
По [10] с. 435 табл. 9.3 исходя из условий обработки для хвостовых долбяков рекомендуется диаметр делительной окружности d0=50 мм. Тогда
Принимаю z0=14. При этом диаметр делительной окружности .
Размеры долбяка в исходном сечении:
(исходное расстояние A=0):
-высота головки и ножки по [10] с. 420 ф.9.4:
где=10 – коэффициент высоты зуба;
- коэффициент радиального зазора для зубчатых колес обрабатываемых долбяками.
- диаметры окружностей выступов и впадин:
- толщина зуба по дуге делительной окружности:
- угол давления эвольвенты на головке зуба:
- толщина зуба на окружности выступов:
- минимально допустимая по условию стойкости ширина головки зуба нового долбяка:
Величина смещения исходного сечения:
где - задний угол при вершине зуба
Размеры долбяка в плоскости его переднего торца (A=4751 мм):
высота головки и ножки:
-толщина зуба по дуге делительной окружности:
- высота головки зуба по передней поверхности:
где - для чистовых долбяков
Для уменьшения искажений профиля режущих кромок долбяка от наличия углов и скорректируем профильный угол долбяка по [10] с. 437 ф. 9.38:
Фактический диаметр основного цилиндра долбяка:
Коэффициент смещения:
Коэффициент толщины зуба нового долбяка по наружному диаметру:
Конструктивные элементы проектируемого долбяка изображены на рис. 3.7.
По [5] с. 406 табл. 5 для долбяков с m=25 40 мм рекомендуется максимально возможная величина стачивания долбяка вдоль его оси H=65 мм и длина зубьев L=20мм. Тогда расстояние торцового сечения предельно сточенного долбяка от исходного сечения составляет:
Для обеспечения нормального входа и выхода долбяка в зону резания принимаю длину шейки соединяющей хвостовик и режущую часть равной 114 мм. Для установки и закрепления долбяка в шпиндель станка используется укороченный конус Морзе В24 СИ СЭВ 148-75.
Рис. 3.7. Конструктивные элементы долбяка.
3 Технологическая часть.doc
1. Исходные данные для проектирования
Исходными данными для проектирования являются:
–чертеж детали корпус редуктора пневмодвигателя Крот-12;
–годовая программа выпуска - 2500 штгод;
–базовый технологический процесс изготовления корпуса редуктора;
–материал преддипломной практики;
–Техническая научная справочная учебно-методическая литература по технологии машиностроения.
При проектировании данного технологического процесса необходимо учитывать технические требования предъявляемые к детали конструктором которые изложены на чертеже детали.
Твердость получаемой детали должна составлять НВ 70 90. Заготовка - отливка в кокиль группа 1Г по ОСТ 23.4.50 - 73 5 группа сложности точность получаемой отливки 8-3-8-6 по ГОСТ 26645 - 85.
2.Определение типа производства.
Тип производства и соответствующие ему формы организации труда определяют характер технологического процесса и его построение. Ориентируясь по номенклатуре годовой программе и другим характерным признакам (массы изделия габаритных размеров и т. д.) определяется тип производства.
Произведем выбор типа производства по рекомендациям приведенным в [1] позволяющим устанавливать его в зависимости от габаритных размеров массы и годового объема выпуска деталей. По программе выпуска 2500(1 таблица 1) для среднего по массе типа деталей (т=34 кг) данное производство характеризуется как серийное.
Рассчитаем размер партии для условий серийного производства.
гдеа=6-10 - периодичность запуска (необходимость запаса деталей на складах) дни;
N - годовая программа выпуска 2500 шт.год.
Выбор серийности произведем по таблице 3 [1]. По расчетному количеству деталей в серии (99 штук) и отношению данной детали к средним по массе данное производство относится к среднесерийному типу.
3.Отработка изделия на технологичность и технологический контроль чертежа
Чертеж детали «Корпус редуктора» содержит достаточное количество видов разрезов сечений. Размеры на чертеже проставлены правильно и в достаточном количестве. Корпус имеет несколько поверхностей по которым он базируется относительно других деталей важно точное выполнение требований к базовым и основным функциональным поверхностям.
В технических требованиях указаны величины литейных уклонов и радиусов которые на стадии получения заготовки выполняются с целью свободного удаления модели из кокиля. Однако незначительная их величина (литейные уклоны до 2 радиусы до 2 мм) оставшаяся после механической обработки не влияет на эксплуатационные свойства изделия и могут оставаться в указанных пределах.
Технические условия на изготовление корпуса редуктора содержат также требования включающие информацию о наличии дефектов поверхностного слоя и допускаемых их значениях как к обрабатываемым поверхностям (допускаются любые дефекты выводимые припуском на мех. обработку) так и к необрабатываемым (допускаются одиночные газовые раковины 3 мм глубиной до 2 мм в количестве 5на поверхность).
Неуказанные предельные отклонения предельных размеров отверстий и валов 7-ой степени точности соответствуют 14 квалитету точности по ЕСДП СЭВ с полями допусков: для отверстий по Н14 для валов по h14 остальные по .
Размеры обозначенные относятся к справочным то есть к размерам неподлежащим выполнению по данному чертежу и указанных для большего удобства пользования.
Анализ чертежа детали показывает что общее количество размеров на чертеже минимально но достаточно для изготовления и контроля изделия.
Отверстия 40 мм 47 мм 52 мм должны быть обработаны по 7 квалитету точности с шероховатостью 16 Ra. Данные поверхности служат для установки подшипников качения. Согласно рекомендациям справочной литературы [5] (т.1 с. 278) опоры быстровращающихся валов средней точности должны быть обработаны по 7-8 квалитету точности.
Радиальное биение 45 относительно 47 составляет 0016 мм что соответствует 5 степени точности. По [5] (т.1 с. 424) для торцов корпусов высокого давления торцов рам и корпусов гидро- и пневмоприборов радиальное биение отверстий под вал должно соответствовать 4 - 5 степени точности. Аналогично проверим правильность назначения всех остальных допусков на погрешность формы. Шероховатость функциональных поверхностей Ra 16 крепежных отверстий Ra 63 необрабатываемых поверхностей Ra 10.
Корпус имеет форму близкую к параллелепипеду одна сторона которого имеет закругление.
Нетехнологичным элементом представляющим большую сложность обработки является отверстие под углом 60° к основанию. Точная его обработка представляется возможным либо при установке обрабатываемой детали в специальное приспособление либо при базировании корпуса редуктора таким образом чтобы данное отверстие было расположено в горизонтальной плоскости что возможно на станке горизонтальной компоновки с поворотным столом.
Малотехнологичными элементами является множество мелких точных резьбовых отверстий расположенных на торцах и боковых поверхностях корпуса.
Тем не менее в целом все обрабатываемые поверхности с точки зрения обеспечения заданной точности и шероховатости легкости подвода инструмента не представляют технологических трудностей.
4.Анализ существующего технологического процесса. Выявление его достоинств и недостатков.
Производя анализ существующего технологического процесса необходимо выяснить обеспечиваются ли все требования чертежа правильно ли выбраны базы соответствует ли последовательность выполнения операций достижению заданной точности и т. д.
Проанализируем технологический процесс по следующим пунктам:
а)соответствие метода получения заготовки данному масштабу производства её соответствие чертежу по размерам припусков на обработку и технических условий.
Согласно базовому технологическому процессу заготовку корпуса редуктора получают литьем в кокиль. Применяемый метод литья соответствует среднесерийному производству. Заготовка пневмодвигателя имеет несложную фасонную форму средних размеров. Отливка относится к 8 классу размерной точности степень точности поверхностей – 8 класс точности массы – 6.
Точность получаемой отливки 8-3-8-6 по ГОСТ 26645 - 85.
Для улучшения свойств отливки а также для достижения необходимой величины твердости указанной в технических требованиях чертежа изделия (НВ 70-90) в технологическом процессе применяется кратковременное (неполное) искусственное старение которое заключается в нагреве заготовки до с последующим остыванием. В существующем технологическом процессе термообработка выполняется на стадии получения заготовки.
Проверим правильность назначения припусков и допусков на заготовку. Заготовка является обобщенной для различных типов корпусов поэтому имеет завышенные припуски особенно по длине корпуса. Допуски на все размеры назначаются по 14 квалитету что не соответствует рекомендуемым для отливок данного класса точности. Значения литейных уклонов и литейных радиусов - соответствуют действительности.
Коэффициент использования материала имеет среднее значение К=07 что соответствует единичному и мелкосерийному производству. Для средне- и крупносерийного необходимо достигнуть увеличения использования материала. Для более удобного извлечения заготовки из кокиля на заготовке предусмотрены уклоны в сторону плоскости разъема.
В дальнейшем необходимо рассмотреть возможность применения другого способа получения заготовки либо оптимизировать данный вариант путем приближения формы заготовки к форме детали.
б)правильность выбора баз на всех операциях и соблюдение принципа единства баз.
В существующем технологическом процессе обработка корпуса редуктора пневмодвигателя производится при схеме базирования по плоскости и перпендикулярным ей двум отверстиям. Данная схема базирования соблюдается на протяжении практически всего технологического процесса при обработке всех основных функциональных поверхностей.
в)соответствие последовательности операции достижению заданной точности детали.
На первой операции производится обработка основания и двух технологических отверстий. Далее базируясь по основанию и двум отверстиям осуществляем последовательную обработку торцов корпуса редуктора отверстий. После чего базируясь по торцам и основанию получаем отверстие под масленку отверстие под углом к основанию нарезаем резьбу в технологических отверстиях.
Последовательность операций соответствует достижению заданной точности.
г)соответствие оборудования требованиям данной операции по точности габаритным размерам производительности (прогрессивным режимам резания).
На всех операциях механической обработки базового технологического процесса используется многоцелевой сверлильно-фрезерно-расточной станок мод. ГДВ400ПМ1Ф4.
Обработку корпуса редуктора будем производить на горизонтальном сверлильно-фрезерно-расточном станке с автоматической загрузкой инструмента и заготовок мод. 2204ВМ1Ф4. Данный станок предназначен для обработки корпусных деталей с 4-х сторон без переустановки по программе. На станке данной модели можно производить получистовое и чистовое фрезерование различных видов поверхностей фрезами всех типов сверление зенкерование развертывание растачивание нарезание резьбы метчиками.
При этом один рабочий может обслуживать несколько станков что в конечном счете приведет к уменьшению себестоимости детали.
д)оснащенность операции высокопроизводительным режущим и измерительным инструментом и приспособлением.
В качестве режущего инструмента используется универсальный режущий инструмент. В базовом технологическом процессе используются токарные резцы из материала группы ВК8 свёрла фрезы метчики из материала Р6М5. Все выбранные режущие инструменты соответствуют операциям и характеристикам получаемых поверхностей.
В качестве станочного приспособления выбраны тиски что увеличивает время закрепления детали. Для его уменьшения можно применить гидравлический или пневматический привод в тисках или другое приспособление.
Контроль производится только на конечной стадии не производится контроль погрешностей формы. Контроль размеров производится при помощи штангенциркуля точность штангенциркуля составляет 01 мм. Исходя из анализа чертежа очевидно что необходимо для контроля размеров применять более точный измерительный прибор
Таким образом в базовом технологическом процессе следует заменить указанный в базовом тех. процессе станок на многоцелевой станок с ЧПУ 2204ВМ1Ф4 а также дополнить технологический процесс необходимыми данными (выдерживаемые размеры тип и марка режущего инструмента) правильно выбрать контрольное приспособление.
5.Выбор и обоснование способов изготовления заготовок.
Материалом корпуса редуктора пневмодвигателя Крот-12 является алюминиевый сплав АЛ7 ГОСТ 1583-93. Согласно базовому технологическому процессу заготовку корпуса редуктора получают литьем в кокиль.
Отливки в кокиль имеют высокую точность размеров (12 14 квалитеты) и шероховатость поверхности отливки Ra = 5 10 мкм что позволяет уменьшить припуски на обработку резанием в 2-3 раза по сравнению с другими способами получения заготовки. Для отливок в кокиль характерна более плотная мелкозернистая структура металла что повышает их механические свойства на 15%. С учетом выбранного типа материала и массы получаемой отливки многократность использования металлической формы кокиля обеспечивает полное выполнение годовой программы выпуска.
Внутренняя конфигурация отливки должна обеспечиваться с помощью песчаных стержней. Таким образом величина припусков на внутренние поверхности образуемые на этапе получения заготовки будет увеличена по сравнению с припусками на внешние поверхности. Для полной подготовки заготовки после литья выполняется термическая обработка - кратковременное (неполное) искусственное старение так как требования по твердости изготовленной отливки не удовлетворяют условиям указанным на чертеже корпуса редуктора.
В целом данный вид литья соответствует необходимым требованиям к заготовке. Спроектируем заготовку наиболее приближенную к конфигурации детали и сравним ее с базовым вариантом.
К заготовке отливаемой в кокиль предъявляются ряд определенных требований:
–для легкости разъема и извлечения из формы отливка должна иметь минимум выступающих элементов и уклоны в сторону плоскости разъема;
–для создания условий нормального заполнения формы толщина стенок должна быть не менее 3 4 мм.
Определим основные параметры проектируемой заготовки:
класс размерной точности отливки – 8;
степень коробления – 3;
степень точности поверхностей – 8;
шероховатость поверхности Ra 10;
класс точности массы – 6;
литейные уклоны - 2° радиусы - 2 мм;
вес готового изделия – 2615 кг.
С учетом всех предложений к проектированию формы отливки спланируем чертеж заготовки.
Предлагается сравнить имеющийся способ получения заготовки (см. рис. 2б) с базовым (см. рис.2а).
Рис.2. Эскизы заготовок.
Расчет стоимости заготовки при литье в кокиль по базовому и проектируемому вариантам произведем по формуле [4]:
- коэффициенты зависящие от класса точности группы сложности массы материала и объема производства заготовок;
q - масса готовой детали = 2615 кг;
Sотх - цена за одну тонну отходов = 56740 руб;
Все перечисленные значения принимаем из таблиц 2.6 2.11 [Шкред] для отливки из алюминиевого сплава 4-го класса точности 3-ей группы серийности при массе отливки 3 10 кг.
Имеем: Сi=112000 руб .
Таким образом учитывая что масса заготовки равна кг стоимость заготовки при литье в кокиль по проектируемому варианту равна:
При оценке получения отливки в кокиль по базовому варианту необходимо учесть что масса заготовки тогда будет равна кг. Тогда стоимость заготовки по базовому варианту равна:
Экономические расчеты по выбору варианта получения заготовки корпуса редуктора приведем в табл. 3.
Результаты сравнения способов получения заготовки.
Проектируемый вариант
Масса готовой детали кг
Коэффициент использования материала
Стоимость заготовки руб.
*- Экономия (+) или перерасход (-) по второму варианту по сравнению с первым.
Таким образом литье в кокиль по проектируемому варианту целесообразней.
6.Назначение технологических баз.
С целью получения заданной точности и экономичности обработки необходимо соблюдать принцип совмещения технологических баз с конструкторскими и измерительными что позволит исключить погрешность базирования и выполнить размеры с использованием полного поля допуска установленного конструктором. С целью уменьшения погрешностей в расположении поверхностей следует в качестве баз на всех операциях использовать одни и те же поверхности.
Составим эскиз детали корпус редуктора на котором все основные поверхности пронумеруем цифрами (см. прил.)
На первой операции производится обработка основания (пов. 1) и двух отверстий (пов. 9). Базирование осуществляется по поверхности 2 (установочная база) 32 (направляющая база) 4 (опорная и измерительная база).
На второй операции и последующих операциях деталь базируется по поверхности 1 (установочная база) и поверхности двух технологических отверстий 9 (направляющая и центрирующая базы опорная база).
На последующих операциях когда невозможна обработка детали по указанным схемам деталь базируется по поверхностям 2 или 3 (установочная база) 1 или 4 (направляющая база) и 32 (опорная база).
Выбрав такие базы сведем погрешность базирования к минимуму обеспечим снятие равномерного припуска и сведем к минимуму количество операций.
7.Выбор способов обработки отдельных поверхностей.
Некоторые виды поверхностей могут быть обработаны различными способами. Выбор того или иного вида обработки на производстве зависит преимущественно от наличия оборудования оснастки типа и формы организации производства и др. Выбранный метод обработки должен учитывать требования чертежа точность шероховатость массу конфигурацию и жесткость детали метод получения заготовки и т.д.
Согласно чертежу и техническим требованиям к детали обработке подвергаются все поверхности корпуса за исключением наружных боковых (4 32 33).
На первой операции производится обработка технологических баз корпуса: основание пов. 1 два технологических отверстия пов. 9. Точность основания не задана в явном виде поэтому о ней можно судить лишь косвенно по размерам от основания наименьшая точность таких размеров соответствует 8-9 квалитетам. Шероховатость основания Ra 10. Точность технологических отверстий также должна соответствовать 8 квалитету. Согласно нормативной литературе (Карта 724 поз. 1 инд. б. [12]) таких требований по точности можно добиться путем фрезерования основания сверления и развертывания отверстия.
Аналогично произведем анализ всех поверхностей данные сводим в таблицу 4
Способы обработки поверхностей и технологической базы.
Номера и наименование обрабатываемой поверхности
Вид механической обработки
Номер базовой поверхности
- Два технологических отверстия
Сверление и развёртывание
– левый торец корпуса
– правый торец корпуса
– отверстие для установки уплотнения
Растачивание (получистовое и чистовое)
– отверстие под подшипник
(получистовое и чистовое)
– паз под размещение шестерен редуктора
– глухое отверстие под подшипник
– маслоотводящее отверстие
24 – крепежные отверстия
– отверстие для установки втулки
Сверление развертывание
– отверстие для установки
– крепежные отверстия
Сверление и нарезание резьбы
– маслоподводящее отверстие
– крепежное отверстие под масленку
Зенкование нарезание резьбы
– 5 крепежных отверстий
– 4 крепежных отверстия
8.Разработка маршрута механической обработки детали.
Цель разработки технологического маршрута обеспечение наиболее рационального процесса обработки детали заданной точности и качества. При этом указывается содержание и последовательность выполнения технологических операций.
Анализ типовых технологических процессов корпусных деталей показывает что после выполнения заготовительных операций механическую обработку выполняют как правило в следующей последовательности: первоначально осуществляют подготовку баз для последующего использования при основном базировании. При этом возможны две схемы базирования детали на последующих операциях: по трем координатным плоскостям и по двум отверстиям и перпендикулярной им плоскости.
В данном процессе механической обработки основными операциями являются операции фрезерования сверления зенкерования расточка и т.д. Окончательными будут выполняться слесарные операции.
Маршрут механической обработки корпуса редуктора пневмодвигателя разработаем руководствуясь следующими данными:
–метод получения заготовки;
–требования к точности и шероховатости;
–принципа единства и совмещения технологических баз.
С учетом принятых способов обработки поверхностей и рекомендаций литературы [17] составим эскизный вариант маршрута обработки детали (табл.2.3).
Укрупненный технологический маршрут изготовления корпуса пневмодвигателя.
№ операции и пози-ции
Название и содержание операции
Эскиз базирование примечание
Фрезеровать основание пов. 1
Сверлить 2 технологических отверстия отв. пов. 9
Развернуть 2 технологических отверстия отв. пов. 9
Фрезеровать торец корпуса полость углубление 35*14
Расточить начерно отверстия 45 47 52 40согласно эскизу.
Расточить начисто отверстия 45 47 52 40согласно эскизу.
Подрезать фаски согласно эскизу
Сверлить 5 сквозных отверстий в торце корпуса по программе.
Фрезеровать торец корпуса пов. 3
Фрезеровать 2 кольцевые канавки по программе
Фрезеровать паз под стопорный элемент
Сверлить 4 крепежных отверстия.
Нарезать резьбу в 4-х крепежных отверстиях.
Сверлить отверстия 17 27 согласно эскизу
Зенкеровать отверстия 22 30 согласно эскизу
Развернуть отверстия 18 28 окончательно согласно эскизу.
Сверлить маслоотводящее отверстие 9 пов. 21
Сверлить сквозное отверстие 11
Сверлить отверстие 4 на длину 46 согласно эскизу
Сверлить последовательно 4 отверстия 41 под резьбу М5 согласно эскизу
Зенковать фаски согласно эскизу
Нарезать резьбу М10 в маслоотводящем отверстии
Нарезать резьбу М12 согласно эскизу
Нарезать резьбу М5 согласно эскизу.
Фрезеровать углубление 37*8 по программе.
Сверлить 2 отверстия под крепежный элемент
Сверлить сквозное отверстие 11
Сверлить отверстие 4 на длину 46
Зенковать фаски по программе
Нарезать резьбу М4 согласно эскизу
Сверлить сквозное отверстие 7
Сверлить отверстие ступенчатое
Нарезать резьбу под масленку
Сверлить отверстие сквозное 13
Сверлить отверстие сквозное
9.Выбор оборудования.
При выборе оборудования необходимо чтобы металлорежущие станки отвечали ряду требований:
–возможность достижения заданной точности обработки поверхностей
–соответствие рабочей зоны станка габаритам обрабатываемой детали;
–соответствие мощности жесткости и кинематических возможностей станка режимам резания;
–соответствие производительности станка заданной годовой программе выпуска.
Исходя из того что для большинства современных производств выгодно использовать широкопрофильное легко перестраиваемое и точное оборудование необходимым является использование многооперационных станков с ЧПУ.
С учетом вышеприведенных требований к оборудованию окончательно выбираем многоцелевой сверлильно-фрезерно-расточной станок с ЧПУ 2204ВМ1Ф4 т.к. позволяет получить максимальную концентрацию операций. Опишем характеристику выбранного станка.
Техническая характеристика станка 2204ВМ1Ф4:
Размеры рабочей поверхности стола и спутника мм:
Диаметр поворотной части стола мм:
Наибольшие координатные перемещения мм:
Наибольшая масса обрабатываемой детали кг
Конус шпинделя по ГОСТ 15945-70
Частота вращения шпинделя
Рабочая подача шпиндельной головки и стола
Скорость быстрого перемещения
Наибольший допускаемый крутящий момент на шпинделе
Наибольшее усилие подачи Н
Емкость инструментального магазина
Мощность электродвигателя привода вращения шпинделя кВт
Количество управляемых координат:
с одновременным перемещением
Дискретность задания геометрических размеров мм:
по линейным координатам
по круговым координатам
Габаритные размеры мм:
Многоцелевой станок мод. 2204ВМ1Ф4 предназначен для обработки корпусных деталей средних размеров с 4-х сторон без переустановок по программе. На станке данной модели можно производить получистовое и чистовое фрезерование различных видов поверхностей фрезами всех типов сверление зенкерование развертывание растачивание нарезание резьбы метчиками в деталях из стали чугуна цветных металлов и пластмасс.
Класс точности станка В по ГОСТ 8-77.
Категория качества станка – высшая.
Станок оснащен устройством автоматической загрузки и выгрузки изделий предназначенным для установки заготовки на сменные столы (паллеты) и последующей автоматической загрузкой столов на станок а также их выгрузки со станка после окончания обработки. Использование сменных столов позволяет совместить загрузку или выгрузку обработанных изделий с работой станка что существенно сокращает холостые простои повышает эффективность его использования и производительность.
Управление станком – от универсальной комплексной системы ЧПУ “Размер 2М-1300”. Тип системы числового программного управления – комбинированная.
Обработка ведется последовательно различными инструментами в автоматическом цикле поэтому используем его на всех дальнейших операциях.
10.Выбор режущего и вспомогательного инструмента.
Режущий инструмент должен позволять реализовать принятый метод обработки детали на данном оборудовании обеспечивая при этом требуемую точность и шероховатость поверхностей детали при наиболее рациональных и производительных режимах обработки. Для выбора режущего и вспомогательного инструмента исходными данными являются :
а)обрабатываемый материал;
б)величина шероховатости поверхности;
г)присоединительные размеры шпинделя станка.
Произведем выбор режущего и вспомогательного инструмента согласно сборникам.
Рассмотрим операцию 010 – комплексную на ОЦ с ЧПУ. На данной операции производится фрезерование основания корпуса редуктора и отверстий 9: сверление и развертывание. Конец шпинделя станка имеет метрический конус 50 ГОСТ15945-70. Таким образом вспомогательный инструмент должен иметь соответствующий наружный конус.
Согласно рекомендациям прил. 1-4 [12] для цветных сплавов из быстрорежущих сталей следует отдавать предпочтение инструменту из Р6М5 или Р18 для инструмента с твердосплавными пластинами использовать пластины из ВК 4 ВК 6 ВК 8. Исходя из этого выбираем по [3] фрезы сверла и др. инструмент - из Р6М5 или Р18.
Для первой позиции (фрезерование торца пов. 1) по [3] выбираем фрезу концевую 63 коническим хвостовиком конус Морзе 4. Обозначение фрезы: Фреза 2223-0071 ГОСТ17026-71. Вспомогательный инструмент – Втулка 50-5 ОСТ2 П12-7-84.
Для второй позиции (сверление 2 отверстий пов. 9) выбираем сверло Р6М5 42 Сверло 2300-0843 ГОСТ19543-74. Вспомогательный инструмент - Патрон 2-50-4.2-90 ГОСТ 26539-85
Для третьей позиции (развертывание 2-х отверстий пов. 9) принимаем развертку Р6М5 5 Развертка 2363-0721 ГОСТ11172-70. Вспомогательный инструмент - Патрон 2-50-5-90 ГОСТ 26539-85.
Аналогично выбираем инструмент на остальные операции и позиции и сводим в таблицу согласно тех. процесса.
№ операции и позиции
Приспособления и инструмент
Фрезеровать основание пов. 1
Фреза 2223-0071 ГОСТ17026-71
Втулка 50-5 ОСТ2 П12-7-84
Сверло 2300-0843 ГОСТ19543-74
Развернуть 2 технологических отверстия отв. пов. 9.
Развертка 2363-0721 ГОСТ11172-70
Патрон 2-50-5-90 ГОСТ 26539-85
Фрезеровать торец корпуса углубление
Фреза 2223-0015 ГОСТ 17026-71
Втулка 50-4 ОСТ 2 П12-7-84
Расточить отверстия 45 47 52 40 начерно
Резец 2142-0102 ВК8 МН 622-84
Борштанга 6300-0332 МН 2645-81
Втулка 50-4 ОСТ2 П12-7-84
Расточить отверстия 45 47 52 40 начисто.
Резец 2145-0104 ВК8 МН 623-84
Сверлить 5 отверстий в торце корпуса по программе
Сверло 2300-0858 ГОСТ 19543-74
Патрон 2-50-6-90 ГОСТ 26539-85
Фрезеровать кольцевые канавки по программе (пов. )
Фреза 2234-0160 ГОСТ 6648-79
Патрон 2-50-7-90 ГОСТ 26539-85
Фреза 2220-0521 ГОСТ 16225-81
Сверлить 4 отверстия
Сверло 2300-0848 ГОСТ 19543-74
Метчик 2629-2285 ГОСТ 17928-72
Втулка 6143-0103 ГОСТ 15936-70
Сверло 2310-0392 ОСТ 2И20-6-80
Втулка 50-3 ОСТ2 П12-7-84
Развернуть отверстие окончательно
Развертка 2363-0843
Втулка 50-2 ОСТ2 П12-7-84
Фрезеровать отверстия (диаметры 27 30)
Фреза 2223-1311 ГОСТ 23247-78
Развернуть отверстие
Развертка 2363-0865 ГОСТ19268-73
Сверлить маслоотводящее отверстие
Сверло 2300-0888 ГОСТ 19543-74
Патрон 2-50-9-120 ГОСТ 26539-85
Нарезать резьбу в маслоотводящем отверстии
Метчик 2629-2057 ГОСТ 17928-72
Патрон 2-50-10-120 ГОСТ 26539-85
Сверлить 4-е отверстия по программе
Сверло 2300-0842 ГОСТ 19543-74
Патрон 2-50-4-90 ГОСТ 26539-85
Нарезать резьбу по программе
Метчик 2629-2021 ГОСТ 17928-72
Фрезеровать паз по программе
Сверло 2300-0833 ГОСТ 19543-74
Зенковка 2353-0108 ГОСТ 14953-80
Сверлить 4 отверстия по программе
Сверлить сквозное отверстие
Сверло 2300-0868 ГОСТ 19543-74
Патрон 2-50-7-120 ГОСТ 26539-85
Сверло 2310-0390 ОСТ 2И20-6-80
Патрон 2-50-10-150 ГОСТ 26539-85
Сверло 2301-2866 ГОСТ 19546-74
Сверло 2300-0816 ГОСТ 19543-74
Патрон 2-50-2-90 ГОСТ 26539-85
Фреза 2234-0355 ГОСТ 9140-78
Патрон 2-50-6-120 ГОСТ 26539-85
Метчик 2629-2027 ГОСТ 17928-72
11.Выбор приспособлений и измерительного инструмента
Каждая технологическая операция механической обработки выполняется с использованием станочных приспособлений. Использование приспособлений способствует повышению производительности и точности обработки расширению технологических возможностей оборудования повышению безопасности работы.
На операции 010 (многоцелевая) при обработке основания и двух технологических отверстий деталь базируется по необрабатываемым поверхностям. Корпус устанавливается на боковую поверхность и фиксируется при помощи упоров и прижима.
Для упрощения технологического процесса принятая схема базирования с операции 020 по 030 включительно выполняется при использовании одного приспособления - спутника с базированием на 2-х пальцах (один срезанный) и прижимом с поверхности 4. При переустановке корпуса из-за мягкости материала необходимо заново обрабатывать базы поэтому выгодно использовать приспособление - спутник когда деталь проходит все этапы обработки при данной схеме базирования без переустановки. Такая схема позволяет использовать многопозиционную обработку с применением вращающегося стола. В дальнейшем необходимо точно спроектировать конструкцию приспособления и рассчитать его точность.
При изготовлении корпуса редуктора пневмодвигателя согласно проектируемому технологическому процессу необходимо производить контроль следующих параметров:
Все линейные размеры проставленные на чертеже выполняются с точностью до десятых долей миллиметра. Контроль данных размеров можно производить стандартными измерительными инструментами: Линейка 0-300 ГОСТ 427-75; Штангенциркуль ШЦ-III ГОСТ 166-89 Глубиномер ГИ-100 ГОСТ 7661-67.
Диаметральные размеры выполняются с точностью до десятых долей миллиметра. Контроль этих размеров также можно производить стандартными измерительными инструментами: Нутромер ГОСТ 9244-75;
Контролировать чистоту шероховатости после обработки
Контроль производится при помощи образцов шероховатости поверхности ГОСТ 9378 - 75 или черт. 199 - 0214.
Для контроля резьб М6 - 7Н М10 - 7Н применяется пробка резьбовая 8221 - 3036 - 7Н; ГОСТ 17758 - 72.
12.Расчет припусков промежуточных размеров и допусков окончательная корректировка чертежа заготовки.
Требуется рассчитать припуски на обработку и промежуточные предельные размеры на поверхность корпуса редуктора пневмодвигателя расчетно-аналитическим методом.
Величина промежуточного припуска по этому методу должна быть такой чтобы при его снятии устранялись дефекты поверхностного слоя которые возникли на предшествующих переходах а также погрешности установки обрабатываемой заготовки возникающие на выполняемом переходе.
Заготовка представляет собой отливку массой 3271 кг. Технологический маршрут обработки отверстия 45Н7 состоит из двух стадий обработки: получистового чистового растачивания выполняемых при одной установке обрабатываемой детали.
Корпус редуктора пневмодвигателя базируется на столе станка по предварительно обработанным плоскости основания отливки пов. 1 и двум технологическим отверстиям пов. 9 . Прижим заготовки осуществляется призмой по внешней части корпуса.
Согласно ГОСТ 26645-85 после первого технологического перехода для цветных металлов и сплавов при расчете величину h необходимо исключить. Поэтому для получистового и чистового растачивания указываем только величину Rz (50 и 20 мкм соответственно).
Рассчитаем величину и припусков. Суммарное значение пространственных отклонений для заготовки данного типа определим по формуле .
Коробление отверстия следует учитывать как в диаметральном так и в осевом его сечении. Тогда имеем где
- удельная кривизна заготовок на 1 мм длины;
- диаметр и длина обрабатываемого отверстия соответственно.
Учитывая что суммарное смещение отверстия в отливке относительно наружной ее поверхности представляет геометрическую сумму в двух взаимно перпендикулярных плоскостях получаем
где - допуски на размеры 1036 и 29 по классу точности соответствующий данной отливке [4 табл.2.4]
Тогда суммарное значение пространственного отклонения заготовки
Остаточное пространственное отклонение после чернового растачивания
Известные нам данные вносим в таблицу:
Элементы припуска мкм
Расчетный припуск 2Zmin мкм
Предельный размер мм
Предельные значения припусков мкм
Погрешность установки при черновом растачивании
Так как для получения 45 деталь устанавливается в приспособление после обработки основания и при этом деталь не переустанавливается то погрешность базирования детали отсутствует. Таким образом погрешность базирования состоит только из погрешности закрепления.
Погрешность закрепления при установке в зажимное приспособление при базировании по предварительно обработанной плоскости и технологическим отверстиям согласно табл. 4.13 [4] принимаем равной 120 мкм.
Остаточная погрешность установки при чистовом точении . Так как получистовое и чистовое точение производится в одной установке то . Тогда мкм.
Расчет минимальных значений припусков произведем по формуле
Минимальный припуск под растачивание:
Для чистового растачивания
Для получистового растачивания
Значение допуска определяем по таблице согласно допуску на размер. Таким образом для чистового фрезерования для получистового фрезерования для заготовки .
Наименьший предельный размер для
чистового растачивания мм
получистового растачивания мм
Рассчитаем максимальные и минимальные предельные значения припусков:
Для чистового растачивания
Для получистового растачивания
Рис.3. Схема расположения припусков.
Припуски на поверхности корпуса
Наименование операции поверхности и их обозначение (см. прил.)
Величина припуска мм
13.Проектирование механических операций.
Разработав маршрут подобрав оборудование и оснастку приступаем к детальной проработке технологических операций. В общем случае содержание операций устанавливают наличием переходов которые могут быть выполнены на выбранном типе станка.
Рассмотрим подробно проектирование операции 020 – многоцелевая.
Согласно технологическому маршруту эта операция осуществляется с одного установа - выполняется обработка 2-х торцов и расположенных вдоль корпуса редуктора отверстий. После окончания обработки с одного торца поворотный стол осуществляет поворот на 180°.
Данная операция выполняется на горизонтальном сверлильно-фрезерно-расточном станке мод. 2204ВМ1Ф4. Базирование осуществляется по предварительно обработанным основанию корпуса редуктора пов. 1 и двум технологическим отверстиям пов. 9 прижим производится с пов. 4.
При данной схеме выполнения операции и на принятом станке можно будет достигнуть заданную точность и шероховатость обрабатываемых поверхностей.
14.Расчет режимов резания сил резания проверка соответствия выбранного оборудования.
Расчет режимов резания для проектируемых операций начинают с изложения исходных данных:
–форма и размеры обрабатываемой поверхности;
–марка и технические свойства материала;
–требования к точности и шероховатости обрабатываемой поверхности;
–способы базирования и закрепления заготовки.
При определении режимов резания используют нормативные данные и рекомендации изложенные в литературе [12]. Результаты режимов резания сводим в таблицу 2.7.
Рассмотрим подробно определение режимов резания на фрезерование основания (переход 1 операция 010).
Произведем расчеты согласно нормативной литературе [12].
Обрабатываемый материал – Сплав АЛ7 ГОСТ 1583-93
Режущий инструмент: фреза концевая 63 Р6М5
Характер заготовки: отливка в кокиль
Припуск на фрезерование основания – 16 мм.
Расчет режимов резания для фрезерования основания:
Определение количества стадий обработки.
По карте 72 выбираем составляющие показатели количества стадий обработки для фрезерования концевой фрезой основания корпуса в зависимости от:
твердости обрабатываемого материала
отношения вылета фрезы к диаметру
отношении ширины фрезерования к диаметру фрезы
Таким образом показатель количества стадий обработки для фрезерования равен
Согласно карте 72 лист 4 поз. 1 инд. б требуемая точность может быть достигнута за одну стадию обработки.
Выбор глубины резания.
Выбор величины глубины резания определяем по карте 75 поз. 8 инд. ж:
Из чего следует что достаточно обработки основания корпуса за один рабочий ход.
Табличное значение подачи на зуб равно (карта 79 поз. 33 инд. ф). Так как условия работы отличаются от нормативных произведем корректировку величины подачи на зуб с учетом поправочных коэффициентов (карта 82) в зависимости от:
материала режущей части фрезы
отношения фактического числа зубьев к нормативному
С учетом поправочных коэффициентов подача принимает значение
Значение подачи допустимой по шероховатости обработанной поверхности (карта 83 поз. 21 инд. в) .
Окончательно принимаем минимальное значение .
Выбор скорости и мощности резания.
Согласно карте 86 поз. 37 инд. д. карте 86 поз. 37 инд. е. .
Поправочные коэффициенты для корректировки табличных значений скорости и мощности резания для измененных условий работы находим согласно карте 86 в зависимости от:
группы обрабатываемого материала
материала режущей части фрезы
периода стойкости режущей части фрезы
отношения фактической ширины фрезерования к нормативной
состояния поверхности заготовки
Окончательно получаем:
Частота вращения шпинделя .
По паспорту станка принимаем ближайшее значение .
С учетом этого фактическая скорость резания равна
Фактическая мощность резания равна
Определение величины силы резани.
По карте 88 поз. 9 инд. ж радиальная составляющая силы резания равна .
Согласно карте 88 поз. 9 инд. з касательная составляющая силы резания .
Поправочные коэффициенты для измененных условий работы в зависимости от:
твердости обрабатываемого материала
Таким образом фактические величины составляющих сил резания равны:
Проверка соответствия выбранного оборудования:
Проведем проверку мощности резания по мощности станка:
NСТ=63кВт – мощность электродвигателя привода вращения шпинделя по паспорту станка;
Аналогичным путем определяем режимы резания для сверления и развертывания двух отверстий результат вычислений заносим в табл. 2.7.
Фрезерование основания
Развертывание отверстий
Аналогично рассчитываются режимы резания и для остальных операций технологического процесса изготовления корпуса редуктора пневмодвигателя. Результаты расчетов заносятся в карты технологических переходов представленные в Приложении.
15.Аналитическое прогнозирование точности и качества обработки поверхностей.
На точность обработки в общем случае оказывает влияние комплекс взаимонезависимых факторов:
–невыполнение принципов совмещения и постоянства баз
–погрешности связанные с неточностью изготовления инструмента ;
–погрешности настройки станка ;
–погрешности установки заготовки в приспособлении ;
–погрешности связанные с температурными деформациями технологической системы СПИД-.;
–погрешности формы связанные с геометрическими неточностями оборудования ;
–рассеивание размеров связанное с методом обработки .;
–недостаточность припусков на обработку.
Проверим обеспечивается ли точность размера при фрезеровании пов.3 на операции 030.
Условие обработки без брака D Тd где
Допуск на выполняемый размер Td = 10 мм.
- суммарная погрешность механической обработки
где - погрешность связанная с деформациями системы СПИД мкм. Для принятых режимов обработки Dg очень мала так как обрабатываемый материал имеет твердость НВ 70..90.
e - погрешность установки для принятой системы обработки = 0 так как технологическая база совпадает с измерительной что свидетельствует о удачно выбранном виде базирования заготовки
- погрешность связанная с неточностью изготовления и износом режущего инструмента Du=6 мкм [11] (стр.74 табл.29).
- погрешность связанная с температурными деформациями технологической системы СПИД мкм. Принимаем DТ = 0 т.к. за время операционного цикла и хорошей податливости заготовки инструмент не успевает разогреться до величин при которых может значительно изменить свои размеры.
- погрешность связанная с геометрическими неточностями оборудования. DФ = 10 мкм [11] (стр.23).
Таким образом суммарная погрешность (мкм) или 0028 что 01 мм.
Вывод: на основании проведенного расчета очевидно что выполняется условие обработки без брака.
Важнейшим показателем определяющим надежность и долговечность изделия является качество поверхностей деталей и машин которое определяется параметрами шероховатости волнистости твердости и др. Основным показателем является параметр шероховатости.
Проведем аналитическое прогнозирование соответствия величины шероховатости полученной согласно проектируемому технологическому процессу изготовления корпуса редуктора при фрезеровании основания изделия пов. 1 на операции 010 – многоцелевой шероховатости поверхности на чертеже Ra = 10 мкм.
По формуле [6 табл. 5 стр. 104]:
где - подача на зуб
- глубина фрезерования
Таким образом при фрезеровании основания корпуса редуктора пневмодвигателя (пов.1) требуемая шероховатость обеспечивается так как 02 мкм 10 мкм.
16.Техническое нормирование.
Техническое нормирование служит инструментом с помощью которого определяют все затраты связанные с изготовлением изделия то есть его себестоимость. Оно служит основой для расчета зарплаты основных и вспомогательных рабочих а также при проектировании нового производства.
Штучное время для операции 010 – многоцелевая будет складываться из штучного времени на фрезерование основания сверление и развертывание двух технологических отверстий. Для нахождения нормы штучного времени воспользуемся справочной литературой [12].
Норма штучного времени определяется по следующей формуле:
- время цикла автоматической работы станка по программе;
- вспомогательное время;
- время на организационное и техническое обслуживание рабочего места отдых и личные потребности.
Время цикла автоматической работы станка по программе складывается из основного времени автоматической работы станка по программе и машинно-вспомогательного времени на автоматическую смену инструмента .
Основное время автоматической работы станка по программе равно
- длина обрабатываемой поверхности (согласно чертежу);
- длина врезания и перебега.
Произведем расчеты и внесем их в табл. 2.8.
Определим машинно-вспомогательного времени на выполнение автоматических вспомогательных ходов.
Исходя из условий минимизации холостых перемещений и соблюдения техники безопасности расстояние от точки «0» до точки «1» выбрано равным или . При фрезеровании второй половины основания корпуса фреза перемещается на величину с подачей холостого хода . Время холостых ходов при сверлении и при развертывании отверстий будет равно. Расстояние от точки «0» до точки «1» равно (). После обработки первого отверстия инструмент перемещается на величину . По окончании обработки второго отверстия для возвращения в точку «0» инструмент должен переместиться на расстояние или .
Таким образом машинно-вспомогательное время на выполнение автоматических вспомогательных ходов и технологические паузы равно:
Определим машинно-вспомогательное время на автоматическую смену инструмента. Для данного станка время при повороте револьверной головки на одну позицию составляет . Для цикла обработки детали необходимо произвести трижды смену инструмента с поворотом револьверной головки на одну позицию. Суммарное время на автоматическую смену инструмента составит .
Вспомогательное время складывается из составляющих:
- вспомогательное время на установку закрепление открепление и снятие детали. (ч.1 карта 13 поз. 44 инд. д. карта 13 поз. 5 инд. е.)
- вспомогательное время связанное с операцией определим по ч. 1 карте 14 поз. 1 4 6 инд. б.: .
- вспомогательное время на произведение контроля
Итого получаем что .
Время на организационное и техническое обслуживание рабочего места отдых и личные потребности приведено в процентах от оперативного времени (ч.1 карта 16 поз. 20) .
Учитывая полученные данные окончательно имеем
Аналогично нормируем все операции технологического процесса. Данные о нормах основного и штучного времени сведены в таблицу 2.9.
17.Проектирование схем технологических наладок оборудования.
Приведем схему технологической наладки для операции 020 – фрезерование торца и полости корпуса растачивание системы отверстий подрезание фасок сверление отверстий в торце корпуса под крепежный элемент.
Исходными данными при проектировании наладки являются:
Название операции – многоцелевая.
Станок на котором выполняется операция – многоцелевой 2204ВМ1Ф4.
Используемое приспособление – фрезерное.
Режущий инструмент: см. п. 2.10.
7 экономическая часть.docx
1.1. Общая характеристика экономики
Машиностроительный комплекс объединяющий девять бывших отраслевых министерств насчитывает в своем составе около 1650 крупных и средних предприятий с численностью работающих более 22 млн. человек. В целом по машиностроительному комплексу и практически по всем направлениям в машиностроении разработаны стратегии и концепции развития на инновационной основе до 2010 г.
Сегодня в России доля машиностроения в общем выпуске промышленной продукции составляет около 20% но в последние годы эта доля перестала расти. В России темпы обновления технологической базы составляют от 01 до 05 % в год а выбытие основных фондов – от 15 до 25 % что во многом определяет технический уровень и конкурентоспособность выпускаемой продукции.
Итоги работы за последние годы подтверждают что факторы роста производства связанные с импорт замещением и активизацией экспорта исчерпываются. Причиной является постепенное сокращение ценового разрыва между импортной и отечественной продукцией вследствие постоянного роста тарифов на энергоносители транспортные перевозки цен на комплектующие изделия и издержек связанных с экономически недостаточным объемом продаж.
В 2011 г. ресурсное обеспечение фундаментальных и прикладных исследований продолжало оставаться недостаточным хотя бюджетное финансирование РАН возросло по сравнению с 2010 г. почти в 15 раза. Оставалась слабой востребованность научной продукции. Основные усилия были направлены главным образом на создание оптимальных условий для развития исследований на поддержку ведущих научных школ сохранение и укрепление кадрового потенциала на интеграцию науки и высшего образования.
В отчетном году научные коллективы продолжали исследования в рамках целевых научно – технических программ программ фундаментальных исследований РАН. Были получены значительные результаты в машиностроении решены некоторые поставленные проблемы намечены и развиты новые пути исследований.
2. Технико-экономическое обоснование (ТЭО)
2.1. Расчет капитальных вложений (инвестиций)
Капитальные вложения (инвестиции) включают в себя единовременные затраты на основное вспомогательное подъемно-транспортное и контрольное оборудование на спецоснастку расходы на строительство необходимых производственных площадей и бытовых помещений.
Капитальные затраты на строительство здания определяются по формуле:
где м2 – площадь производственного здания; тыс. руб. – цена 1 м2 производственных помещений; м2 – площадь служебно-бытовых помещений; тыс. руб. – цена 1 м2 служебно-бытовых помещений;
С учетом загрузки: Kз = 79780*kзаг
kзаг = TS где Т – это суммарное время затрачиваемое на изготовление партии детали S – станкоемкость программы выпуска детали (520000 Станко-часов).
Следовательно kзаг = 1945520000=0000374.
Kз = 79780*0000374=29837 тыс. руб.
Расчет капитальных затрат на создание новой техники или оборудования производят по формуле: Коб = Кпр + Кмон + Книр
где Кпр – прейскурантная стоимость устанавливаемого оборудования руб.; Кмон – затраты на монтаж равные 10-15% от прейскурантной стоимости руб.; Книр – затраты на научно-исследовательские работы отладку оборудования руб.
Рассчитаем капитальные затраты на оборудование:
Прейскурантная стоимость устанавливаемого оборудования.
Цена за единицу тыс. руб.
Коб = (143+143+2)2+(1176+1176+1)7+(1659+1659+3)8+(160+16+3)5+
+(291+291+4)8+(5065+5065+6)34+(1140+114+8)3+(346+346+4)2+
+(265+265+3)74 = 51698 тыс. руб.
С учетом коэффициента загрузки оборудования имеем:
Kоб = 51698*0000374=19335 тыс. руб.
Затраты на приобретение транспортных средств.
где Ктр=150 тыс. руб. – средняя стоимость используемого транспорта.
Кол.тр=5– количество необходимого транспорта (электропогрузчиков грузоподъемностью 2 т).
Ктр= 150 50000374=02805 тыс. руб.
Затраты на инструмент и приспособления берутся как 6% от первоначальных затрат на приобретение оборудования т.е.
Капитальные затраты на хозяйственный инвентарь составляют 2% от первоначальных затрат на приобретение оборудования.
Общие капитальные затраты сведены в таблице 6.2.
Смета капитальных затрат.
В расчёте на весь цех тыс. руб.
Затраты на строительство здания
Затраты на создание новой техники или оборудования
Затраты на приобретение транспортных средств
Затраты на хозяйственный инвентарь
Затраты на инструмент и приспособления
2.2. Расчет себестоимости продукции
Себестоимость продукции включает в себя прямые расходы на технологические цели (затраты на основное сырье вспомогательные материалы электроэнергию) затраты на оплату труда работников предприятия отчисления на социальные нужды амортизацию зданий (сооружений) и оборудования накладные расходы (общепроизводственные и общехозяйственные).
К основным материалам относятся отливки поковки прутковый и листовой прокат метизы трубы полуфабрикаты.
Стоимость сырья и материалов определяется на основании норм расхода каждого вида материалов и цен за вычетом стоимости отходов.отходов составляет примерно 25-35% от черной массы.
Расчётная масса заготовки Мзаг = 536 кг масса готовой детали
Определим ориентировочную стоимость заготовки.
Sзаг – стоимость заготовки при литье в кокиль.
kt kc kb km kn – коэффициенты зависящие от класса точности группы сложности массы материала и объема производства заготовок. Все перечисленные значения принимаем из таблицы 2.6 2.11 3;
Sотх – цена за одну тонну отходов равная 80 тыс. руб.;
Сi= 5 тыс. руб. kt=11 (4 класс точности) km=184 kn=1 (для 3 группы серийности) kc=1 kb=096.
Годовая программа выпуска составляет Nгод = 1500 штгод.
Эм = 7681500 = 115200 руб.
К вспомогательным материалам относятся смазочные масла керосин бензин резина обтирочные материалы материалы для текущего ремонта оборудования. Затраты на вспомогательные материалы определяют исходя из установленных норм расхода на рабочее место и цен.
При укрупненных расчетах затраты на вспомогательные материалы можно брать 152% от стоимости основных материалов:
Звсп.=1152000015 = 1728 руб.
Затраты на основную заработную плату также относятся к переменным расходам.
Производство детали включает в себя как основное производство так и вспомогательное кроме этого – обслуживание и продажа.
Режим работы – двухсменный пятидневный. Длительность смены – 8 часов.
Годовой расход на основную и дополнительную заработную плату станочников на поточной линии на деталь Зст с отчислениями на социальные нужды:
где Тст - часовая тарифная ставка соответствующего разряда по сдельной оплате труда на
Кпд - коэффициент учитывающий премиальные доплаты - 13;
Кдз - коэффициент учитывающий дополнительную зарплату - 11;
Ксн - коэффициент учитывающий отчисления на социальные нужды - 13;
- количество рабочих чел;
Фэф - годовой эффективный фонд времени рабочего (1920 ч).
Часовая тарифная ставка рабочих в соответствии с разрядом.
руб. – зарплата основных рабочих;
руб. – зарплата вспомогательных рабочих.
Заработная плата остальным работникам начисляется помесячно исходя из трудового договора и согласно занимаемой должности.
Затраты на оплату труда сведем в табл. 6.4.
Затраты на оплату труда работающих цеха.
Категория работающих
Количество работающих в цехе чел.
Совокупная зп работающих в цехе тыс. руб.
Вспомогательные рабочие
Расходы на содержание и эксплуатацию оборудования представляем в виде таблицы 6.5.
Смета расходов на содержание и эксплуатацию оборудования.
Амортизация оборудования и транспортных средств
где К стоимость оборудования руб.; На норма амортизации.
Содержание и эксплуатация оборудования и транспортных средств
а) зарплата рабочих по уходу и надзору за оборудованием
б) отчисления на социальные нужды
в) смазочные обтирочные и другие материалы
Фонд основной и дополнительной зарплаты рабочих по уходу и надзору за оборудованием
% от зарплаты вспомогательных рабочих
-10% от зарплаты вспомогательных рабочих
Текущий ремонт оборудования и транспортных средств
-8% балансовой стоимости оборудования и транспортных средств
Внутрицеховое перемещение грузов
% от суммы расходов п.1-3
Износ малоценных и быстроиз нашивающихся инструментов и приспособлений
% балансовой стоимости оборудования и транспортных средств
Цеховые расходы представляем в виде табл. 6.6.
Смета цеховых расходов.
Содержание цехового персонала
Фонд зарплаты цехового персонала (руководители специалисты служащие) с отчислениями на социальные нужды (социальный налог 30 %)
Амортизация зданий сооружений
где К стоимость зданий цехового назначения руб.; На норма амортизации
Содержание зданий и сооружений
Текущий ремонт зданий и сооружений
Расходы по охране труда
% от суммы расходов по предыдущим статьям 1-4
Прочие расходы включающие износ расходы по испытаниям пр.
-15 % от суммы расходов по предыдущим статьям 1-5
Стоимость силовой энергии:
где Рэ установленная мощность всех электродвигателей оборудования (средняя мощность станка в цехе 10 кВт); Ки коэффициент учитывающий использование установленной мощности электродвигателей принимается равным 09; Кмкоэффициент учитывающий использование электродвигателей по машинному времени принимаемый равным 03 08 в зависимости от условий технологического процесса (принимаем Км=05); Кпэ коэффициент учитывающий электропотери в сети (095); коэффициент полезного действия электродвигателей (095); Fg действительный годовой фонд времени работы оборудования 1920 ч;
Цэл стоимость 1 кВт·ч электроэнергии 53 руб.
В целом изменение себестоимости продукции по каждой статье расходов отражается в калькуляции согласно табл. 6.7.
Калькуляция себестоимости детали
На единицу продукции
На годовую программу
Зарплата основных и производственных рабочих с отчислениями на соц. нужды
Затраты на электроэнергию
Отчисления на социальные нужды
Итого цеховая себестоимость
Общезаводские расходы
Итого производственная себестоимость
Внепроизводственные расходы
Определим цену изделия:
2.3. Расчет показателей экономической эффективности проекта
Оценка экономической эффективности проекта может быть осуществлена на основе статических или динамических методов расчета. Применим динамический метод расчета. Динамические методы расчета предполагают учет фактора времени и расчет денежных потоков в различные периоды реализации проекта.
Международная практика в процессе оценки проектов использует несколько обобщающих показателей. К таким показателям относятся: интегральный экономический эффект (чистая текущая стоимость); индекс доходности; внутренний коэффициент эффективности; максимальный денежный отток; период возврата капитальных вложений и срок окупаемости. Интегральный экономический эффект (NPV – Net Present Value of Discounted Cash Flow)
Результаты расчета NPV представим в виде табл. 6.8.
Чистая текущая дисконтированная стоимость (NPV) определяется как разность денежных притоков и оттоков разновременные величины которых приводятся в сопоставимый вид путём приведения к первому году осуществления проекта т.е. путём умножения на соответствующий коэффициент дисконтирования:
где Dпк - чистый денежный поток в течение Т-лет проекта у. е.;
- коэффициент дисконтирования; () () – горизонт расчёта.
NPV = 292649+ 475799 + 428806+ 387688 - 106004= 524902 тыс. руб.
Так как NPV>0 то проект считается эффективным.
Индекс рентабельности определяется как отношение приведенных потоков (ЧДПt) к приведенным оттокам (Кк):
PI = (292649 + 475799 + 428806 + 387688)(106004) = 15
Период возврата инвестиций:
Твозвр = tх + NPVtДДП t + 1
где tх – количество лет с отрицательным эффектом в дисконтированном денежном потоке нарастающем итогом; NPVt – NPV имеющее отрицательный эффект в году tх; ДДПt+1 – дисконтированный денежный поток с положительным эффектом в году (t+1).
Твозвр = 3 + 291592428806= 3+068=368 (года).
Период окупаемости проекта:
где Тинв - период вклада инвестиций лет;
Т= 368 - 2 = 168 (года).
Рис. 6.1. Финансовый профиль проекта.
Денежные потоки проекта тыс. руб.
Инвестиционная деятельность
Финансовая деятельность
1. Выручка от продажи
Чистый денежный поток
Коэффициент дисконтирования
Чистая текущая дисконтированная стоимость
Чистая текущая дисконтированная стоимость нарастающим итогом
2.4. Технико-экономические показатели проекта
Обобщим все рассчитанные данные и занесем их в табл. 6.9.
Годовой выпуск продукции шт.
Объем капвложений тыс. руб.
Количество технического оборудования шт.
Общее количество работающих чел.
- вспомогательные рабочие;
Себестоимость годового выпуска изделий тыс. руб.
Индекс доходности (рентабельности)
Интегральный экономический эффект тыс. руб.
Срок окупаемости лет
Период возврата инвестиций лет
9 Литература.doc
Справочник технолога-машиностроителя : в 2-х т. ред. А. М. Дальский [и др.]. - 5-е изд. испр. - М. : Машиностроение.Т. 2. - 2003. - 943 с.
Анурьев В.И. Справочник конструктора-машиностроителя: в 3-х т. В. И. Анурьев. - 8-е изд. перераб. и доп. - М.: Машиностроение 2001.Т.1. - 2001.- 920 с.
Боровский Г. В. Справочник инструментальщика Г. В. Боровский С. Н. Григорьев А. Р. Маслов. - М.: Машиностроение 2005. - 463 с.
Основы технологии машинострое-ния : учеб. Б. М. Базров. - М.: Машиностроение 2005. - 736 с.
Григорьев С. Н. Инструментальная оснастка станков с ЧПУ: справ. С. Н. Григорьев М. В. Кохомский А. Р. Маслов. - М.: Машиностроение 2006
Гузеев В. И. Режимы резания для токарных и сверлильно-фрезерно-расточных станков с числовым программным управлением: справ. В. И. Гузеев В. А. Батуев И. В. Сурков. - М.: Машиностроение 2005. - 364 с.
Технология машиностроения: учеб. В. В. Клепиков А. Н. Бод-ров. - 2-е изд. испр. и доп. - М.: Форум 2011 ; М. : Форум 2008. - 859 с
Технология машиностроения: учеб. для студентов вузов под ред. Г. Н. Мельникова. - 2-е изд. стереотип. - М.: Изд-во МГТУ им. Н.Э. Баумана 2001 - Т.2: Производство машин. - 2001. - 639 с.
Технология машиностроения: в 2-х т. ред. А. М. Дальский. - М. : МГТУ. Т.1: Основы технологии машиностроения. - 1999. - 564 с.
Чалдаева Л. А. Экономика предприятия: учебник Л. А. Чалдаева; Фин. акад. при Правительстве РФ.-2-е изд. перераб. и доп.- М.: Юрайт2011.- 347 с.
Борисов Е. Ф. Экономика: учебник и практикум для вузовЕ. Ф. Борисов.- М.: Юрайт2010.- 596 с.
Станочные приспособления: Справочник в 2-х томах. Под ред. Б.И. Вардошкина и А.А. Шатилова – М.: Машиностроение 1984.
Конституция Российской Федерации. М.: Изд. «Ось-89» 2002.-48с.
Трудовой кодекс РФ.- М.: ВЦУЖ 2002. – 144 с.
Аттестация рабочих мест по условиям труда (основные нормативно-методические документы) Белгород 2000.-115с.
Безопасность жизнедеятельности: Учебник для вузов С.В. Белов А.В. Ильницкая А.Ф. Козьяков и др.; под общ. ред. С.В. Белова 7-е изд. стер. – М.: Высш. шк. 2007. – 616 с. ISBN 978-5-06-004171-2.
Безопасность производственных процессов на предприятиях машиностроения: учеб.В.В. Сафронов Г.А. Харламов А.Г. Схиртладзе В.Г. Еремин; под ред. Г.А. Харламова. – М.: Новое издание 2006. – 461 с. ISBN 5-94735-099-8
Анурьев В. И. Справочник конструктора-машиностроителя : в 3-х т. В. И. Анурьев. - 8-е изд. перераб. и доп. - М. : Машиностроение 2001. 2. - 2001. - 900 с.
Анурьев В. И.Справочник конструктора-машиностроителя: в 3-х т. В. И. Анурьев. - 8-е изд. перераб. и доп. - М.: Машиностроение 2001. Т. 3. - 2001. - 858 с.
Баранчиков В. И. Обработка специальных материалов в машиностроении: справ. В. И. Баранчиков А. С. Тарапанов Г. А. Харламов. - М.: Машиностроение 2002. - 264 с.
Харламов Г. А. Припуски на механическую обработку: справ. Г. А. Харламов А. С. Тарапанов. - М.: Машиностроение 2006. - 255 с.
Когаев В. П. Расчеты деталей машин и конструкций на прочность и долговечность: справ. В. П. Когаев Н. А. Махутов А. П. Гусенков. - М. : Машиностроение 1985. – 223с.
Проектирование металлорежущих станков и станочных систем. Справочник - учебник в 3 т. [Текст]. Т.2.Ч.2 : Расчет и конструирование узлов и элементов станков. - М.: Машиностроение 1995. - 320 с. - ISBN 5-217-02745-2
Мягков В.Д. Палей М.А. и др. Допуски и посадки: справочник Часть 1.М В 2 частях 8-е издание Политехника 2001.-576 с.
8 Заключение.doc
Заготовку детали в базовом варианте получают из горячекатаного проката круглого профиля этот метод целесообразно применять в массовом и крупносерийном производстве у нас тип производства среднесерийный поэтому данный метод нам не подходит. Был предложен вариант получения заготовки горячей штамповкой на ГКМ или КГШП метод не уступающий по качеству и точности получаемых поверхностей. Рассчитав себестоимость получения заготовок по каждому из методов оказалось что метод получения заготовки горячей штамповки на ГКМ или КГШП.
Ранее существующие операции фрезерования растачивания сверления отверстий и нарезания резьбы в крепёжных отверстиях объединены в одну. Это позволяет вести обработку не меняя оборудование и значительно сокращает вспомогательное время на установку и снятие детали.
Станочное приспособление для выполнения операции фрезерование паза имеет приспособление автоматического закрепления заготовки. Зажим осуществляется за счет разжима пружин которые в свою очередь приводят в движение призмы а открепление приспособления производится перемещения плиты установочной при этом значительно сокращается время закрепления. Механизация привода позволяет сократить вспомогательное время связанное с установкой и снятием заготовки. Таким образом значительно повышается производительность труда и одновременно улучшаются условия работы.
Контрольное приспособление для измерения: 1. радиальное биение поверхности ø110 мм более 008 мм; 2. радиальное биение поверхности ø95 мм более 01 мм; 3. радиальное биение по делительной окружности зуба не более 005мм позволяет определять два первых одновременно что сокращает время на контроль в несколько раз.
Оценивая экономическую эффективность проектируемого варианта следует отметить снижение себестоимости выполнения технологической операции увеличение прибыли по сравнению с базовым вариантом.
В целом можно заключить что при механизации производства автоматизации использования прогрессивных методов получения заготовки прогрессивных методов обработки деталей - повышается производительность труда качество и точность обработки уменьшается трудоёмкость снижаются затраты улучшаются условия труда.
Диплом.doc
ТЕХНОЛОГИЧЕСКАЯ ЧАСТЬ10
1.Исходные данные для проектирования.10
2.Определение типа производства.11
3.Отработка изделия на технологичность и технологический контроль чертежа12
4.Анализ существующего технологического процесса. Выявление его достоинств и недостатков.14
5.Выбор и обоснование способов изготовления заготовок.17
6.Назначение технологических баз.20
7.Выбор способов обработки отдельных поверхностей.21
8.Разработка маршрута механической обработки детали.24
9.Выбор оборудования.29
10.Выбор режущего и вспомогательного инструмента.31
11.Выбор приспособлений и измерительного инструмента36
12.Расчет припусков промежуточных размеров и допусков окончательная корректировка чертежа заготовки.37
13.Проектирование механических операций.42
14.Расчет режимов резания сил резания проверка соответствия выбранного оборудования.43
15.Аналитическое прогнозирование точности и качества обработки поверхностей.47
16.Техническое нормирование.50
17.Проектирование схем технологических наладок оборудования.53
КОНСТРУКТОРСКАЯ ЧАСТЬ54
1.Исходные данные для проектирования станочного приспособления.54
2.Выбор типа приспособления54
3.Выбор схемы станочного приспособления и конструкции установочных деталей.55
4.Расчет сил закрепления заготовки.57
5.Выбор конструкции и размеров зажимных устройств58
6.Расчет погрешности закрепления60
7.Описание конструкции и принципа работы станочного приспособления60
8.Эффективность использования и стоимость технологической оснастки.61
ПРОЕКТИРОВАНИЕ ЦЕХА63
1.Исходные данные для проектирования.63
2.Расчёт количества основного технологического оборудования64
3.Определение состава вспомогательных служб и участков цеха выбор оборудования.65
Расчёт численности и состава работающих.67
4.Расчёт площадей и компоновка оборудования.69
5.Компоновка цеха.73
6.Определение площадей и компоновка служебно-бытовых помещений.74
ЭКОНОМИЧЕСКАЯ ЧАСТЬ76
1.Технико-экономический анализ.76
2.Определение дополнительных капитальных вложений (инвестиций).76
3.Расчет себестоимости продукции77
БЕЗОПАСНОСТЬ ЖИЗНЕДЕЯТЕЛЬНОСТИ85
2.Требования охраны труда к производственным и санитарно-бытовым помещениям86
3.Требования охраны труда к оборудованию и оснастке.88
4.Оздоровление воздушной среды в производственных помещениях.90
5.Меры по снижению уровня шума и вибраций в производственных помещениях.91
6.Производственное освещение. Расчет освещенности цеха.94
7.Электробезопасность. Расчет защитного заземления.96
8.Обеспечение пожарной безопасности.99
СПЕЦИАЛЬНАЯ ЧАСТЬ102
1.Использование трехмерного моделирования для подготовки рабочего чертежа детали.102
2.Выбор системы проектирования.102
3.Трехмерное проектирование корпуса редуктора.103
4.Проектирование плана цеха с использованием библиотеки отрисовки планов зданий и сооружений.104
СПИСОК ЛИТЕРАТУРЫ108
Технический прогресс современного производства во всех отраслях народного хозяйства определяется развитием машиностроения его технический уровнем выпуском продукции с высокими качественными показателями при максимальной эффективности производства. Одним из основных факторов повышения технического уровня машиностроения является внедрение высокоэффективных технологических процессов и конструкторских разработок.
Целью дипломной работы является создание усовершенствованного технологического процесса механической обработки корпуса редуктора пневмодвигателя «Крот-12» с целью получения экономического эффекта за счет внедрения нового оборудования и разработки станочных и контрольных приспособлений.
Рис.1 Корпус редуктора пневмодвигателя «Крот-12»
Назначение и конструкция детали
Корпус является базовой деталью пневмодвигателя установки «Крот-12» предназначенной для гидромеханического разрушения карбонатных отложений на внутренней поверхности различных труб. Установка состоит из двух основных элементов: пневмодвигателя и редуктора.
Корпус редуктора предназначен для размещения в нем передаточного устройства и водяной насадки а также для присоединения гибкого вала.
Внизу корпус имеет коробчатую форму с размерами верхняя половина имеет форму цилиндрической поверхности длиной 105 мм и радиусом 46 мм.
Боковая поверхность является базовой и предназначена для крепления корпуса редуктора к установке. Она выполнена в виде фланца толщиной 10 мм с пятью сквозными отверстиями 7 мм три из которых располагаются на окружности 104 мм (два на горизонтальной оси а одно на вертикальной оси сверху) а два оставшихся располагаются симметрично относительно вертикальной оси корпуса на удалении 6 мм от его боков и 10 мм от его основания.
В корпусе на глубину 46 мм выполнен паз в виде двух пересекающихся цилиндров диаметром 78 мм. Паз предназначен для размещения в нем пары зубчатых колес редуктора. Для данного паза задан допуск биения 16 мкм относительно ступенчатого сквозного отверстия 524745мм выполненного на расстоянии 100 мм от основания и предназначенного для установки подшипникового узла. Ступени отверстия выполняются с шероховатостью 16 мкм по параметру Ra с биением относительно друг друга 16 мкм. Допуск перпендикулярности данных отверстий относительно базовой плоскости 16 мкм. В ступенчатом отверстии выполнены канавки для уплотнительных колец. В нижнем цилиндре паза выполнено глухое отверстие 40 мм глубиной 12 мм для установки подшипника под вал.
С правой стороны корпус имеет форму усеченного конуса на котором имеется 4 отверстия М6 расположенных под углом 45° к осевым линиям на окружности 60 мм для крепления крышки
В отверстии 45мм под углом на расстоянии 10 мм от правого торца корпуса выполнен канал 13мм который сообщается с другим каналом выполненным в виде ступенчатого отверстия 3718222830 и предназначенного для расположения в нем элементов гидроклапана. Данная система каналов предназначена для подвода воды в рубашку гибкого вала.
На заднем торце корпуса расположены 4 отверстия М6-6Н для установки крышки предназначенной для соединения с трубопроводом; на переднем торце так же расположены 4 отверстия М5 для установки крышки под пружину и для соединения с трубопроводом.
Также имеются два отверстия для подвода смазки: первое выполнено в верхней стенке корпуса диаметром М10 куда ввинчивается заглушка; второе 4мм выполнено сквозным через стенку корпуса до ступенчатого отверстия 524745мм. С задней стороны данного ступенчатого отверстия выполнен паз 3516 мм для размещения стопорного элемента.
Нижняя плоскость предназначена для установки корпуса редуктора «Крот-12» на какую-либо поверхность во время его эксплуатации. Для этого на основании корпуса имеется 2 отверстия М6 на расстоянии 64 мм друг от друга и 14 мм от правого торца предназначенные для крепления лап к корпусу.
Корпус пневмодвигателя выполняется из сплава алюминия АЛ7 ГОСТ 1453-93 - сплав предназначенный для изготовления фасонных отливок. АЛ7 - сплав на основе системы алюминий - медь (табл. 1).
Химический состав литейного сплава АЛ-7 ГОСТ 2685-75
Механические свойства сплава.
сопротивление кгсмм2
В - литье в песчаные оболочковые и по выплавляемым моделям. К - литье в кокиль. Т4 - закалка. Т5 - закалка и кратковременное (неполное) искусственное старение;
Для АЛ7 дается характеристика и примерное назначение как сплаву с хорошей обрабатываемостью пониженными свариваемостью и коррозийной стойкостью уровень рабочей температуры 225 0С. Данный сплав применяется для получения отливок несложной формы средненагруженных деталей.
Для уменьшения и перераспределения остаточных напряжений а также для достижения необходимой величины твердости указанной в технических требованиях на чертеже детали отливку подвергают закалке и искусственному старению.
Технологическая часть
1.Исходные данные для проектирования.
Исходными данными для проектирования являются:
–чертеж детали корпус редуктора пневмодвигателя Крот-12;
–годовая программа выпуска - 2500 штгод;
–базовый технологический процесс изготовления корпуса редуктора;
–материал преддипломной практики;
–Техническая научная справочная учебно-методическая литература по технологии машиностроения.
При проектировании данного технологического процесса необходимо учитывать технические требования предъявляемые к детали конструктором которые изложены на чертеже детали.
Твердость получаемой детали должна составлять НВ 70 90. Заготовка - отливка в кокиль группа 1Г по ОСТ 23.4.50 - 73 5 группа сложности точность получаемой отливки 8-3-8-6 по ГОСТ 26645 - 85.
2.Определение типа производства.
Тип производства и соответствующие ему формы организации труда определяют характер технологического процесса и его построение. Ориентируясь по номенклатуре годовой программе и другим характерным признакам (массы изделия габаритных размеров и т. д.) определяется тип производства.
Произведем выбор типа производства по рекомендациям приведенным в [1] позволяющим устанавливать его в зависимости от габаритных размеров массы и годового объема выпуска деталей. По программе выпуска 2500(1 таблица 1) для среднего по массе типа деталей (т=34 кг) данное производство характеризуется как серийное.
Рассчитаем размер партии для условий серийного производства.
гдеа=6-10 - периодичность запуска (необходимость запаса деталей на складах) дни;
N - годовая программа выпуска 2500 шт.год.
Выбор серийности произведем по таблице 3 [1]. По расчетному количеству деталей в серии (99 штук) и отношению данной детали к средним по массе данное производство относится к среднесерийному типу.
3.Отработка изделия на технологичность и технологический контроль чертежа
Чертеж детали «Корпус редуктора» содержит достаточное количество видов разрезов сечений. Размеры на чертеже проставлены правильно и в достаточном количестве. Корпус имеет несколько поверхностей по которым он базируется относительно других деталей важно точное выполнение требований к базовым и основным функциональным поверхностям.
В технических требованиях указаны величины литейных уклонов и радиусов которые на стадии получения заготовки выполняются с целью свободного удаления модели из кокиля. Однако незначительная их величина (литейные уклоны до 2 радиусы до 2 мм) оставшаяся после механической обработки не влияет на эксплуатационные свойства изделия и могут оставаться в указанных пределах.
Технические условия на изготовление корпуса редуктора содержат также требования включающие информацию о наличии дефектов поверхностного слоя и допускаемых их значениях как к обрабатываемым поверхностям (допускаются любые дефекты выводимые припуском на мех. обработку) так и к необрабатываемым (допускаются одиночные газовые раковины 3 мм глубиной до 2 мм в количестве 5на поверхность).
Неуказанные предельные отклонения предельных размеров отверстий и валов 7-ой степени точности соответствуют 14 квалитету точности по ЕСДП СЭВ с полями допусков: для отверстий по Н14 для валов по h14 остальные по .
Размеры обозначенные относятся к справочным то есть к размерам неподлежащим выполнению по данному чертежу и указанных для большего удобства пользования.
Анализ чертежа детали показывает что общее количество размеров на чертеже минимально но достаточно для изготовления и контроля изделия.
Отверстия 40 мм 47 мм 52 мм должны быть обработаны по 7 квалитету точности с шероховатостью 16 Ra. Данные поверхности служат для установки подшипников качения. Согласно рекомендациям справочной литературы [5] (т.1 с. 278) опоры быстровращающихся валов средней точности должны быть обработаны по 7-8 квалитету точности.
Радиальное биение 45 относительно 47 составляет 0016 мм что соответствует 5 степени точности. По [5] (т.1 с. 424) для торцов корпусов высокого давления торцов рам и корпусов гидро- и пневмоприборов радиальное биение отверстий под вал должно соответствовать 4 - 5 степени точности. Аналогично проверим правильность назначения всех остальных допусков на погрешность формы. Шероховатость функциональных поверхностей Ra 16 крепежных отверстий Ra 63 необрабатываемых поверхностей Ra 10.
Корпус имеет форму близкую к параллелепипеду одна сторона которого имеет закругление.
Нетехнологичным элементом представляющим большую сложность обработки является отверстие под углом 60° к основанию. Точная его обработка представляется возможным либо при установке обрабатываемой детали в специальное приспособление либо при базировании корпуса редуктора таким образом чтобы данное отверстие было расположено в горизонтальной плоскости что возможно на станке горизонтальной компоновки с поворотным столом.
Малотехнологичными элементами является множество мелких точных резьбовых отверстий расположенных на торцах и боковых поверхностях корпуса.
Тем не менее в целом все обрабатываемые поверхности с точки зрения обеспечения заданной точности и шероховатости легкости подвода инструмента не представляют технологических трудностей.
4.Анализ существующего технологического процесса. Выявление его достоинств и недостатков.
Производя анализ существующего технологического процесса необходимо выяснить обеспечиваются ли все требования чертежа правильно ли выбраны базы соответствует ли последовательность выполнения операций достижению заданной точности и т. д.
Проанализируем технологический процесс по следующим пунктам:
а)соответствие метода получения заготовки данному масштабу производства её соответствие чертежу по размерам припусков на обработку и технических условий.
Согласно базовому технологическому процессу заготовку корпуса редуктора получают литьем в кокиль. Применяемый метод литья соответствует среднесерийному производству. Заготовка пневмодвигателя имеет несложную фасонную форму средних размеров. Отливка относится к 8 классу размерной точности степень точности поверхностей – 8 класс точности массы – 6.
Точность получаемой отливки 8-3-8-6 по ГОСТ 26645 - 85.
Для улучшения свойств отливки а также для достижения необходимой величины твердости указанной в технических требованиях чертежа изделия (НВ 70-90) в технологическом процессе применяется кратковременное (неполное) искусственное старение которое заключается в нагреве заготовки до с последующим остыванием. В существующем технологическом процессе термообработка выполняется на стадии получения заготовки.
Проверим правильность назначения припусков и допусков на заготовку. Заготовка является обобщенной для различных типов корпусов поэтому имеет завышенные припуски особенно по длине корпуса. Допуски на все размеры назначаются по 14 квалитету что не соответствует рекомендуемым для отливок данного класса точности. Значения литейных уклонов и литейных радиусов - соответствуют действительности.
Коэффициент использования материала имеет среднее значение К=07 что соответствует единичному и мелкосерийному производству. Для средне- и крупносерийного необходимо достигнуть увеличения использования материала. Для более удобного извлечения заготовки из кокиля на заготовке предусмотрены уклоны в сторону плоскости разъема.
В дальнейшем необходимо рассмотреть возможность применения другого способа получения заготовки либо оптимизировать данный вариант путем приближения формы заготовки к форме детали.
б)правильность выбора баз на всех операциях и соблюдение принципа единства баз.
В существующем технологическом процессе обработка корпуса редуктора пневмодвигателя производится при схеме базирования по плоскости и перпендикулярным ей двум отверстиям. Данная схема базирования соблюдается на протяжении практически всего технологического процесса при обработке всех основных функциональных поверхностей.
в)соответствие последовательности операции достижению заданной точности детали.
На первой операции производится обработка основания и двух технологических отверстий. Далее базируясь по основанию и двум отверстиям осуществляем последовательную обработку торцов корпуса редуктора отверстий. После чего базируясь по торцам и основанию получаем отверстие под масленку отверстие под углом к основанию нарезаем резьбу в технологических отверстиях.
Последовательность операций соответствует достижению заданной точности.
г)соответствие оборудования требованиям данной операции по точности габаритным размерам производительности (прогрессивным режимам резания).
На всех операциях механической обработки базового технологического процесса используется многоцелевой сверлильно-фрезерно-расточной станок мод. ГДВ400ПМ1Ф4.
Обработку корпуса редуктора будем производить на горизонтальном сверлильно-фрезерно-расточном станке с автоматической загрузкой инструмента и заготовок мод. 2204ВМ1Ф4. Данный станок предназначен для обработки корпусных деталей с 4-х сторон без переустановки по программе. На станке данной модели можно производить получистовое и чистовое фрезерование различных видов поверхностей фрезами всех типов сверление зенкерование развертывание растачивание нарезание резьбы метчиками.
При этом один рабочий может обслуживать несколько станков что в конечном счете приведет к уменьшению себестоимости детали.
д)оснащенность операции высокопроизводительным режущим и измерительным инструментом и приспособлением.
В качестве режущего инструмента используется универсальный режущий инструмент. В базовом технологическом процессе используются токарные резцы из материала группы ВК8 свёрла фрезы метчики из материала Р6М5. Все выбранные режущие инструменты соответствуют операциям и характеристикам получаемых поверхностей.
В качестве станочного приспособления выбраны тиски что увеличивает время закрепления детали. Для его уменьшения можно применить гидравлический или пневматический привод в тисках или другое приспособление.
Контроль производится только на конечной стадии не производится контроль погрешностей формы. Контроль размеров производится при помощи штангенциркуля точность штангенциркуля составляет 01 мм. Исходя из анализа чертежа очевидно что необходимо для контроля размеров применять более точный измерительный прибор
Таким образом в базовом технологическом процессе следует заменить указанный в базовом тех. процессе станок на многоцелевой станок с ЧПУ 2204ВМ1Ф4 а также дополнить технологический процесс необходимыми данными (выдерживаемые размеры тип и марка режущего инструмента) правильно выбрать контрольное приспособление.
5.Выбор и обоснование способов изготовления заготовок.
Материалом корпуса редуктора пневмодвигателя Крот-12 является алюминиевый сплав АЛ7 ГОСТ 1583-93. Согласно базовому технологическому процессу заготовку корпуса редуктора получают литьем в кокиль.
Отливки в кокиль имеют высокую точность размеров (12 14 квалитеты) и шероховатость поверхности отливки Ra = 5 10 мкм что позволяет уменьшить припуски на обработку резанием в 2-3 раза по сравнению с другими способами получения заготовки. Для отливок в кокиль характерна более плотная мелкозернистая структура металла что повышает их механические свойства на 15%. С учетом выбранного типа материала и массы получаемой отливки многократность использования металлической формы кокиля обеспечивает полное выполнение годовой программы выпуска.
Внутренняя конфигурация отливки должна обеспечиваться с помощью песчаных стержней. Таким образом величина припусков на внутренние поверхности образуемые на этапе получения заготовки будет увеличена по сравнению с припусками на внешние поверхности. Для полной подготовки заготовки после литья выполняется термическая обработка - кратковременное (неполное) искусственное старение так как требования по твердости изготовленной отливки не удовлетворяют условиям указанным на чертеже корпуса редуктора.
В целом данный вид литья соответствует необходимым требованиям к заготовке. Спроектируем заготовку наиболее приближенную к конфигурации детали и сравним ее с базовым вариантом.
К заготовке отливаемой в кокиль предъявляются ряд определенных требований:
–для легкости разъема и извлечения из формы отливка должна иметь минимум выступающих элементов и уклоны в сторону плоскости разъема;
–для создания условий нормального заполнения формы толщина стенок должна быть не менее 3 4 мм.
Определим основные параметры проектируемой заготовки:
класс размерной точности отливки – 8;
степень коробления – 3;
степень точности поверхностей – 8;
шероховатость поверхности Ra 10;
класс точности массы – 6;
литейные уклоны - 2° радиусы - 2 мм;
вес готового изделия – 2615 кг.
С учетом всех предложений к проектированию формы отливки спланируем чертеж заготовки.
Предлагается сравнить имеющийся способ получения заготовки (см. рис. 2б) с базовым (см. рис.2а).
Рис.2 Эскизы заготовок.
Расчет стоимости заготовки при литье в кокиль по базовому и проектируемому вариантам произведем по формуле [4]:
- коэффициенты зависящие от класса точности группы сложности массы материала и объема производства заготовок;
q - масса готовой детали = 2615 кг;
Sотх - цена за одну тонну отходов = 56740 руб;
Все перечисленные значения принимаем из таблиц 2.6 2.11 [Шкред] для отливки из алюминиевого сплава 4-го класса точности 3-ей группы серийности при массе отливки 3 10 кг.
Имеем: Сi=112000 руб .
Таким образом учитывая что масса заготовки равна кг стоимость заготовки при литье в кокиль по проектируемому варианту равна:
При оценке получения отливки в кокиль по базовому варианту необходимо учесть что масса заготовки тогда будет равна кг. Тогда стоимость заготовки по базовому варианту равна:
Экономические расчеты по выбору варианта получения заготовки корпуса редуктора приведем в табл. 3.
Результаты сравнения способов получения заготовки.
Проектируемый вариант
Масса готовой детали кг
Коэффициент использования материала
Стоимость заготовки руб.
*- Экономия (+) или перерасход (-) по второму варианту по сравнению с первым.
Таким образом литье в кокиль по проектируемому варианту целесообразней.
6.Назначение технологических баз.
С целью получения заданной точности и экономичности обработки необходимо соблюдать принцип совмещения технологических баз с конструкторскими и измерительными что позволит исключить погрешность базирования и выполнить размеры с использованием полного поля допуска установленного конструктором. С целью уменьшения погрешностей в расположении поверхностей следует в качестве баз на всех операциях использовать одни и те же поверхности.
Составим эскиз детали корпус редуктора на котором все основные поверхности пронумеруем цифрами (см. прил.)
На первой операции производится обработка основания (пов. 1) и двух отверстий (пов. 9). Базирование осуществляется по поверхности 2 (установочная база) 32 (направляющая база) 4 (опорная и измерительная база).
На второй операции и последующих операциях деталь базируется по поверхности 1 (установочная база) и поверхности двух технологических отверстий 9 (направляющая и центрирующая базы опорная база).
На последующих операциях когда невозможна обработка детали по указанным схемам деталь базируется по поверхностям 2 или 3 (установочная база) 1 или 4 (направляющая база) и 32 (опорная база).
Выбрав такие базы сведем погрешность базирования к минимуму обеспечим снятие равномерного припуска и сведем к минимуму количество операций.
7.Выбор способов обработки отдельных поверхностей.
Некоторые виды поверхностей могут быть обработаны различными способами. Выбор того или иного вида обработки на производстве зависит преимущественно от наличия оборудования оснастки типа и формы организации производства и др. Выбранный метод обработки должен учитывать требования чертежа точность шероховатость массу конфигурацию и жесткость детали метод получения заготовки и т.д.
Согласно чертежу и техническим требованиям к детали обработке подвергаются все поверхности корпуса за исключением наружных боковых (4 32 33).
На первой операции производится обработка технологических баз корпуса: основание пов. 1 два технологических отверстия пов. 9. Точность основания не задана в явном виде поэтому о ней можно судить лишь косвенно по размерам от основания наименьшая точность таких размеров соответствует 8-9 квалитетам. Шероховатость основания Ra 10. Точность технологических отверстий также должна соответствовать 8 квалитету. Согласно нормативной литературе (Карта 724 поз. 1 инд. б. [12]) таких требований по точности можно добиться путем фрезерования основания сверления и развертывания отверстия.
Аналогично произведем анализ всех поверхностей данные сводим в таблицу 4
Способы обработки поверхностей и технологической базы.
Номера и наименование обрабатываемой поверхности
Вид механической обработки
Номер базовой поверхности
- Два технологических отверстия
Сверление и развёртывание
– левый торец корпуса
– правый торец корпуса
– отверстие для установки уплотнения
Растачивание (получистовое и чистовое)
– отверстие под подшипник
(получистовое и чистовое)
– паз под размещение шестерен редуктора
– глухое отверстие под подшипник
– маслоотводящее отверстие
24 – крепежные отверстия
– отверстие для установки втулки
Сверление развертывание
– отверстие для установки
– крепежные отверстия
Сверление и нарезание резьбы
– маслоподводящее отверстие
– крепежное отверстие под масленку
Зенкование нарезание резьбы
– 5 крепежных отверстий
– 4 крепежных отверстия
8.Разработка маршрута механической обработки детали.
Цель разработки технологического маршрута обеспечение наиболее рационального процесса обработки детали заданной точности и качества. При этом указывается содержание и последовательность выполнения технологических операций.
Анализ типовых технологических процессов корпусных деталей показывает что после выполнения заготовительных операций механическую обработку выполняют как правило в следующей последовательности: первоначально осуществляют подготовку баз для последующего использования при основном базировании. При этом возможны две схемы базирования детали на последующих операциях: по трем координатным плоскостям и по двум отверстиям и перпендикулярной им плоскости.
В данном процессе механической обработки основными операциями являются операции фрезерования сверления зенкерования расточка и т.д. Окончательными будут выполняться слесарные операции.
Маршрут механической обработки корпуса редуктора пневмодвигателя разработаем руководствуясь следующими данными:
–метод получения заготовки;
–требования к точности и шероховатости;
–принципа единства и совмещения технологических баз.
С учетом принятых способов обработки поверхностей и рекомендаций литературы [17] составим эскизный вариант маршрута обработки детали (табл.2.3).
Укрупненный технологический маршрут изготовления корпуса пневмодвигателя.
№ операции и пози-ции
Название и содержание операции
Эскиз базирование примечание
Фрезеровать основание пов. 1
Сверлить 2 технологических отверстия отв. пов. 9
Развернуть 2 технологических отверстия отв. пов. 9
Фрезеровать торец корпуса полость углубление 35*14
Расточить начерно отверстия 45 47 52 40согласно эскизу.
Расточить начисто отверстия 45 47 52 40согласно эскизу.
Подрезать фаски согласно эскизу
Сверлить 5 сквозных отверстий в торце корпуса по программе.
Фрезеровать торец корпуса пов. 3
Фрезеровать 2 кольцевые канавки по программе
Фрезеровать паз под стопорный элемент
Сверлить 4 крепежных отверстия.
Нарезать резьбу в 4-х крепежных отверстиях.
Сверлить отверстия 17 27 согласно эскизу
Зенкеровать отверстия 22 30 согласно эскизу
Развернуть отверстия 18 28 окончательно согласно эскизу.
Сверлить маслоотводящее отверстие 9 пов. 21
Сверлить сквозное отверстие 11
Сверлить отверстие 4 на длину 46 согласно эскизу
Сверлить последовательно 4 отверстия 41 под резьбу М5 согласно эскизу
Зенковать фаски согласно эскизу
Нарезать резьбу М10 в маслоотводящем отверстии
Нарезать резьбу М12 согласно эскизу
Нарезать резьбу М5 согласно эскизу.
Фрезеровать углубление 37*8 по программе.
Сверлить 2 отверстия под крепежный элемент
Сверлить сквозное отверстие 11
Сверлить отверстие 4 на длину 46
Зенковать фаски по программе
Нарезать резьбу М4 согласно эскизу
Сверлить сквозное отверстие 7
Сверлить отверстие ступенчатое
Нарезать резьбу под масленку
Сверлить отверстие сквозное 13
Сверлить отверстие сквозное
9.Выбор оборудования.
При выборе оборудования необходимо чтобы металлорежущие станки отвечали ряду требований:
–возможность достижения заданной точности обработки поверхностей
–соответствие рабочей зоны станка габаритам обрабатываемой детали;
–соответствие мощности жесткости и кинематических возможностей станка режимам резания;
–соответствие производительности станка заданной годовой программе выпуска.
Исходя из того что для большинства современных производств выгодно использовать широкопрофильное легко перестраиваемое и точное оборудование необходимым является использование многооперационных станков с ЧПУ.
С учетом вышеприведенных требований к оборудованию окончательно выбираем многоцелевой сверлильно-фрезерно-расточной станок с ЧПУ 2204ВМ1Ф4 т.к. позволяет получить максимальную концентрацию операций. Опишем характеристику выбранного станка.
Техническая характеристика станка 2204ВМ1Ф4:
Размеры рабочей поверхности стола и спутника мм:
Диаметр поворотной части стола мм:
Наибольшие координатные перемещения мм:
Наибольшая масса обрабатываемой детали кг
Конус шпинделя по ГОСТ 15945-70
Частота вращения шпинделя
Рабочая подача шпиндельной головки и стола
Скорость быстрого перемещения
Наибольший допускаемый крутящий момент на шпинделе
Наибольшее усилие подачи Н
Емкость инструментального магазина
Мощность электродвигателя привода вращения шпинделя кВт
Количество управляемых координат:
с одновременным перемещением
Дискретность задания геометрических размеров мм:
по линейным координатам
по круговым координатам
Габаритные размеры мм:
Многоцелевой станок мод. 2204ВМ1Ф4 предназначен для обработки корпусных деталей средних размеров с 4-х сторон без переустановок по программе. На станке данной модели можно производить получистовое и чистовое фрезерование различных видов поверхностей фрезами всех типов сверление зенкерование развертывание растачивание нарезание резьбы метчиками в деталях из стали чугуна цветных металлов и пластмасс.
Класс точности станка В по ГОСТ 8-77.
Категория качества станка – высшая.
Станок оснащен устройством автоматической загрузки и выгрузки изделий предназначенным для установки заготовки на сменные столы (паллеты) и последующей автоматической загрузкой столов на станок а также их выгрузки со станка после окончания обработки. Использование сменных столов позволяет совместить загрузку или выгрузку обработанных изделий с работой станка что существенно сокращает холостые простои повышает эффективность его использования и производительность.
Управление станком – от универсальной комплексной системы ЧПУ “Размер 2М-1300”. Тип системы числового программного управления – комбинированная.
Обработка ведется последовательно различными инструментами в автоматическом цикле поэтому используем его на всех дальнейших операциях.
10.Выбор режущего и вспомогательного инструмента.
Режущий инструмент должен позволять реализовать принятый метод обработки детали на данном оборудовании обеспечивая при этом требуемую точность и шероховатость поверхностей детали при наиболее рациональных и производительных режимах обработки. Для выбора режущего и вспомогательного инструмента исходными данными являются :
а)обрабатываемый материал;
б)величина шероховатости поверхности;
г)присоединительные размеры шпинделя станка.
Произведем выбор режущего и вспомогательного инструмента согласно сборникам.
Рассмотрим операцию 010 – комплексную на ОЦ с ЧПУ. На данной операции производится фрезерование основания корпуса редуктора и отверстий 9: сверление и развертывание. Конец шпинделя станка имеет метрический конус 50 ГОСТ15945-70. Таким образом вспомогательный инструмент должен иметь соответствующий наружный конус.
Согласно рекомендациям прил. 1-4 [12] для цветных сплавов из быстрорежущих сталей следует отдавать предпочтение инструменту из Р6М5 или Р18 для инструмента с твердосплавными пластинами использовать пластины из ВК 4 ВК 6 ВК 8. Исходя из этого выбираем по [3] фрезы сверла и др. инструмент - из Р6М5 или Р18.
Для первой позиции (фрезерование торца пов. 1) по [3] выбираем фрезу концевую 63 коническим хвостовиком конус Морзе 4. Обозначение фрезы: Фреза 2223-0071 ГОСТ17026-71. Вспомогательный инструмент – Втулка 50-5 ОСТ2 П12-7-84.
Для второй позиции (сверление 2 отверстий пов. 9) выбираем сверло Р6М5 42 Сверло 2300-0843 ГОСТ19543-74. Вспомогательный инструмент - Патрон 2-50-4.2-90 ГОСТ 26539-85
Для третьей позиции (развертывание 2-х отверстий пов. 9) принимаем развертку Р6М5 5 Развертка 2363-0721 ГОСТ11172-70. Вспомогательный инструмент - Патрон 2-50-5-90 ГОСТ 26539-85.
Аналогично выбираем инструмент на остальные операции и позиции и сводим в таблицу согласно тех. процесса.
№ операции и позиции
Приспособления и инструмент
Фрезеровать основание пов. 1
Фреза 2223-0071 ГОСТ17026-71
Втулка 50-5 ОСТ2 П12-7-84
Сверло 2300-0843 ГОСТ19543-74
Развернуть 2 технологических отверстия отв. пов. 9.
Развертка 2363-0721 ГОСТ11172-70
Патрон 2-50-5-90 ГОСТ 26539-85
Фрезеровать торец корпуса углубление
Фреза 2223-0015 ГОСТ 17026-71
Втулка 50-4 ОСТ 2 П12-7-84
Расточить отверстия 45 47 52 40 начерно
Резец 2142-0102 ВК8 МН 622-84
Борштанга 6300-0332 МН 2645-81
Втулка 50-4 ОСТ2 П12-7-84
Расточить отверстия 45 47 52 40 начисто.
Резец 2145-0104 ВК8 МН 623-84
Сверлить 5 отверстий в торце корпуса по программе
Сверло 2300-0858 ГОСТ 19543-74
Патрон 2-50-6-90 ГОСТ 26539-85
Фрезеровать кольцевые канавки по программе (пов. )
Фреза 2234-0160 ГОСТ 6648-79
Патрон 2-50-7-90 ГОСТ 26539-85
Фреза 2220-0521 ГОСТ 16225-81
Сверлить 4 отверстия
Сверло 2300-0848 ГОСТ 19543-74
Метчик 2629-2285 ГОСТ 17928-72
Втулка 6143-0103 ГОСТ 15936-70
Сверло 2310-0392 ОСТ 2И20-6-80
Втулка 50-3 ОСТ2 П12-7-84
Развернуть отверстие окончательно
Развертка 2363-0843
Втулка 50-2 ОСТ2 П12-7-84
Фрезеровать отверстия (диаметры 27 30)
Фреза 2223-1311 ГОСТ 23247-78
Развернуть отверстие
Развертка 2363-0865 ГОСТ19268-73
Сверлить маслоотводящее отверстие
Сверло 2300-0888 ГОСТ 19543-74
Патрон 2-50-9-120 ГОСТ 26539-85
Нарезать резьбу в маслоотводящем отверстии
Метчик 2629-2057 ГОСТ 17928-72
Патрон 2-50-10-120 ГОСТ 26539-85
Сверлить 4-е отверстия по программе
Сверло 2300-0842 ГОСТ 19543-74
Патрон 2-50-4-90 ГОСТ 26539-85
Нарезать резьбу по программе
Метчик 2629-2021 ГОСТ 17928-72
Фрезеровать паз по программе
Сверло 2300-0833 ГОСТ 19543-74
Зенковка 2353-0108 ГОСТ 14953-80
Сверлить 4 отверстия по программе
Сверлить сквозное отверстие
Сверло 2300-0868 ГОСТ 19543-74
Патрон 2-50-7-120 ГОСТ 26539-85
Сверло 2310-0390 ОСТ 2И20-6-80
Патрон 2-50-10-150 ГОСТ 26539-85
Сверло 2301-2866 ГОСТ 19546-74
Сверло 2300-0816 ГОСТ 19543-74
Патрон 2-50-2-90 ГОСТ 26539-85
Фреза 2234-0355 ГОСТ 9140-78
Патрон 2-50-6-120 ГОСТ 26539-85
Метчик 2629-2027 ГОСТ 17928-72
11.Выбор приспособлений
и измерительного инструмента
Каждая технологическая операция механической обработки выполняется с использованием станочных приспособлений. Использование приспособлений способствует повышению производительности и точности обработки расширению технологических возможностей оборудования повышению безопасности работы.
На операции 010 (многоцелевая) при обработке основания и двух технологических отверстий деталь базируется по необрабатываемым поверхностям. Корпус устанавливается на боковую поверхность и фиксируется при помощи упоров и прижима.
Для упрощения технологического процесса принятая схема базирования с операции 020 по 030 включительно выполняется при использовании одного приспособления - спутника с базированием на 2-х пальцах (один срезанный) и прижимом с поверхности 4. При переустановке корпуса из-за мягкости материала необходимо заново обрабатывать базы поэтому выгодно использовать приспособление - спутник когда деталь проходит все этапы обработки при данной схеме базирования без переустановки. Такая схема позволяет использовать многопозиционную обработку с применением вращающегося стола. В дальнейшем необходимо точно спроектировать конструкцию приспособления и рассчитать его точность.
При изготовлении корпуса редуктора пневмодвигателя согласно проектируемому технологическому процессу необходимо производить контроль следующих параметров:
Все линейные размеры проставленные на чертеже выполняются с точностью до десятых долей миллиметра. Контроль данных размеров можно производить стандартными измерительными инструментами: Линейка 0-300 ГОСТ 427-75; Штангенциркуль ШЦ-III ГОСТ 166-89 Глубиномер ГИ-100 ГОСТ 7661-67.
Диаметральные размеры выполняются с точностью до десятых долей миллиметра. Контроль этих размеров также можно производить стандартными измерительными инструментами: Нутромер ГОСТ 9244-75;
Контролировать чистоту шероховатости после обработки
Контроль производится при помощи образцов шероховатости поверхности ГОСТ 9378 - 75 или черт. 199 - 0214.
Для контроля резьб М6 - 7Н М10 - 7Н применяется пробка резьбовая 8221 - 3036 - 7Н; ГОСТ 17758 - 72.
12.Расчет припусков промежуточных размеров и допусков окончательная корректировка чертежа заготовки.
Требуется рассчитать припуски на обработку и промежуточные предельные размеры на поверхность корпуса редуктора пневмодвигателя расчетно-аналитическим методом.
Величина промежуточного припуска по этому методу должна быть такой чтобы при его снятии устранялись дефекты поверхностного слоя которые возникли на предшествующих переходах а также погрешности установки обрабатываемой заготовки возникающие на выполняемом переходе.
Заготовка представляет собой отливку массой 3271 кг. Технологический маршрут обработки отверстия 45Н7 состоит из двух стадий обработки: получистового чистового растачивания выполняемых при одной установке обрабатываемой детали.
Корпус редуктора пневмодвигателя базируется на столе станка по предварительно обработанным плоскости основания отливки пов. 1 и двум технологическим отверстиям пов. 9 . Прижим заготовки осуществляется призмой по внешней части корпуса.
Согласно ГОСТ 26645-85 после первого технологического перехода для цветных металлов и сплавов при расчете величину h необходимо исключить. Поэтому для получистового и чистового растачивания указываем только величину Rz (50 и 20 мкм соответственно).
Рассчитаем величину и припусков. Суммарное значение пространственных отклонений для заготовки данного типа определим по формуле .
Коробление отверстия следует учитывать как в диаметральном так и в осевом его сечении. Тогда имеем где
- удельная кривизна заготовок на 1 мм длины;
- диаметр и длина обрабатываемого отверстия соответственно.
Учитывая что суммарное смещение отверстия в отливке относительно наружной ее поверхности представляет геометрическую сумму в двух взаимно перпендикулярных плоскостях получаем
где - допуски на размеры 1036 и 29 по классу точности соответствующий данной отливке [4 табл.2.4]
Тогда суммарное значение пространственного отклонения заготовки
Остаточное пространственное отклонение после чернового растачивания
Известные нам данные вносим в таблицу
Элементы припуска мкм
Расчетный припуск 2Zmin мкм
Предельный размер мм
Предельные значения припусков мкм
Погрешность установки при черновом растачивании
Так как для получения 45 деталь устанавливается в приспособление после обработки основания и при этом деталь не переустанавливается то погрешность базирования детали отсутствует. Таким образом погрешность базирования состоит только из погрешности закрепления.
Погрешность закрепления при установке в зажимное приспособление при базировании по предварительно обработанной плоскости и технологическим отверстиям согласно табл. 4.13 [4] принимаем равной 120 мкм.
Остаточная погрешность установки при чистовом точении . Так как получистовое и чистовое точение производится в одной установке то . Тогда мкм.
Расчет минимальных значений припусков произведем по формуле
Минимальный припуск под растачивание:
Для чистового растачивания
Для получистового растачивания
Значение допуска определяем по таблице согласно допуску на размер. Таким образом для чистового фрезерования для получистового фрезерования для заготовки .
Наименьший предельный размер для
чистового растачивания мм
получистового растачивания мм
Рассчитаем максимальные и минимальные предельные значения припусков:
Для чистового растачивания
Для получистового растачивания
Рис.3 Схема расположения припусков.
Припуски на поверхности корпуса
Наименование операции поверхности и их обозначение (см. прил.)
Величина припуска мм
13.Проектирование механических операций.
Разработав маршрут подобрав оборудование и оснастку приступаем к детальной проработке технологических операций. В общем случае содержание операций устанавливают наличием переходов которые могут быть выполнены на выбранном типе станка.
Рассмотрим подробно проектирование операции 020 – многоцелевая.
Согласно технологическому маршруту эта операция осуществляется с одного установа - выполняется обработка 2-х торцов и расположенных вдоль корпуса редуктора отверстий. После окончания обработки с одного торца поворотный стол осуществляет поворот на 180°.
Операция включает в себя позиций:
Данная операция выполняется на горизонтальном сверлильно-фрезерно-расточном станке мод. 2204ВМ1Ф4. Базирование осуществляется по предварительно обработанным основанию корпуса редуктора пов. 1 и двум технологическим отверстиям пов. 9 прижим производится с пов. 4.
При данной схеме выполнения операции и на принятом станке можно будет достигнуть заданную точность и шероховатость обрабатываемых поверхностей.
14.Расчет режимов резания сил резания
проверка соответствия выбранного оборудования.
Расчет режимов резания для проектируемых операций начинают с изложения исходных данных:
–форма и размеры обрабатываемой поверхности;
–марка и технические свойства материала;
–требования к точности и шероховатости обрабатываемой поверхности;
–способы базирования и закрепления заготовки.
При определении режимов резания используют нормативные данные и рекомендации изложенные в литературе [12]. Результаты режимов резания сводим в таблицу 2.7.
Рассмотрим подробно определение режимов резания на фрезерование основания (переход 1 операция 010).
Произведем расчеты согласно нормативной литературе [12].
Обрабатываемый материал – Сплав АЛ7 ГОСТ 1583-93
Режущий инструмент: фреза концевая 63 Р6М5
Характер заготовки: отливка в кокиль
Припуск на фрезерование основания – 16 мм.
Расчет режимов резания для фрезерования основания:
Определение количества стадий обработки.
По карте 72 выбираем составляющие показатели количества стадий обработки для фрезерования концевой фрезой основания корпуса в зависимости от:
твердости обрабатываемого материала
отношения вылета фрезы к диаметру
отношении ширины фрезерования к диаметру фрезы
Таким образом показатель количества стадий обработки для фрезерования равен
Согласно карте 72 лист 4 поз. 1 инд. б требуемая точность может быть достигнута за одну стадию обработки.
Выбор глубины резания.
Выбор величины глубины резания определяем по карте 75 поз. 8 инд. ж:
Из чего следует что достаточно обработки основания корпуса за один рабочий ход.
Табличное значение подачи на зуб равно (карта 79 поз. 33 инд. ф). Так как условия работы отличаются от нормативных произведем корректировку величины подачи на зуб с учетом поправочных коэффициентов (карта 82) в зависимости от:
материала режущей части фрезы
отношения фактического числа зубьев к нормативному
С учетом поправочных коэффициентов подача принимает значение
Значение подачи допустимой по шероховатости обработанной поверхности (карта 83 поз. 21 инд. в) .
Окончательно принимаем минимальное значение .
Выбор скорости и мощности резания.
Согласно карте 86 поз. 37 инд. д. карте 86 поз. 37 инд. е. .
Поправочные коэффициенты для корректировки табличных значений скорости и мощности резания для измененных условий работы находим согласно карте 86 в зависимости от:
группы обрабатываемого материала
материала режущей части фрезы
периода стойкости режущей части фрезы
отношения фактической ширины фрезерования к нормативной
состояния поверхности заготовки
Окончательно получаем:
Частота вращения шпинделя .
По паспорту станка принимаем ближайшее значение .
С учетом этого фактическая скорость резания равна
Фактическая мощность резания равна
Определение величины силы резани.
По карте 88 поз. 9 инд. ж радиальная составляющая силы резания равна .
Согласно карте 88 поз. 9 инд. з касательная составляющая силы резания .
Поправочные коэффициенты для измененных условий работы в зависимости от:
твердости обрабатываемого материала
Таким образом фактические величины составляющих сил резания равны:
Проверка соответствия выбранного оборудования:
Проведем проверку мощности резания по мощности станка:
NСТ=63кВт – мощность электродвигателя привода вращения шпинделя по паспорту станка;
Аналогичным путем определяем режимы резания для сверления и развертывания двух отверстий результат вычислений заносим в табл. 2.7.
Фрезерование основания
Развертывание отверстий
Аналогично рассчитываются режимы резания и для остальных операций технологического процесса изготовления корпуса редуктора пневмодвигателя. Результаты расчетов заносятся в карты технологических переходов представленные в Приложении.
15.Аналитическое прогнозирование точности и качества обработки поверхностей.
На точность обработки в общем случае оказывает влияние комплекс взаимонезависимых факторов:
–невыполнение принципов совмещения и постоянства баз
–погрешности связанные с неточностью изготовления инструмента ;
–погрешности настройки станка ;
–погрешности установки заготовки в приспособлении ;
–погрешности связанные с температурными деформациями технологической системы СПИД-.;
–погрешности формы связанные с геометрическими неточностями оборудования ;
–рассеивание размеров связанное с методом обработки .;
–недостаточность припусков на обработку.
Проверим обеспечивается ли точность размера при фрезеровании пов.3 на операции 030.
Условие обработки без брака D Тd где
Допуск на выполняемый размер Td = 10 мм.
- суммарная погрешность механической обработки
где - погрешность связанная с деформациями системы СПИД мкм. Для принятых режимов обработки Dg очень мала так как обрабатываемый материал имеет твердость НВ 70..90.
e - погрешность установки для принятой системы обработки = 0 так как технологическая база совпадает с измерительной что свидетельствует о удачно выбранном виде базирования заготовки
- погрешность связанная с неточностью изготовления и износом режущего инструмента Du=6 мкм [11] (стр.74 табл.29).
- погрешность связанная с температурными деформациями технологической системы СПИД мкм. Принимаем DТ = 0 т.к. за время операционного цикла и хорошей податливости заготовки инструмент не успевает разогреться до величин при которых может значительно изменить свои размеры.
- погрешность связанная с геометрическими неточностями оборудования. DФ = 10 мкм [11] (стр.23).
Таким образом суммарная погрешность (мкм) или 0028 что 01 мм.
Вывод: на основании проведенного расчета очевидно что выполняется условие обработки без брака.
Важнейшим показателем определяющим надежность и долговечность изделия является качество поверхностей деталей и машин которое определяется параметрами шероховатости волнистости твердости и др. Основным показателем является параметр шероховатости.
Проведем аналитическое прогнозирование соответствия величины шероховатости полученной согласно проектируемому технологическому процессу изготовления корпуса редуктора при фрезеровании основания изделия пов. 1 на операции 010 – многоцелевой шероховатости поверхности на чертеже Ra = 10 мкм.
По формуле [6 табл. 5 стр. 104]:
где - подача на зуб
- глубина фрезерования
Таким образом при фрезеровании основания корпуса редуктора пневмодвигателя (пов.1) требуемая шероховатость обеспечивается так как 02 мкм 10 мкм.
16.Техническое нормирование.
Техническое нормирование служит инструментом с помощью которого определяют все затраты связанные с изготовлением изделия то есть его себестоимость. Оно служит основой для расчета зарплаты основных и вспомогательных рабочих а также при проектировании нового производства.
Штучное время для операции 010 – многоцелевая будет складываться из штучного времени на фрезерование основания сверление и развертывание двух технологических отверстий. Для нахождения нормы штучного времени воспользуемся справочной литературой [12].
Норма штучного времени определяется по следующей формуле:
- время цикла автоматической работы станка по программе;
- вспомогательное время;
- время на организационное и техническое обслуживание рабочего места отдых и личные потребности.
Время цикла автоматической работы станка по программе складывается из основного времени автоматической работы станка по программе и машинно-вспомогательного времени на автоматическую смену инструмента .
Основное время автоматической работы станка по программе равно
- длина обрабатываемой поверхности (согласно чертежу);
- длина врезания и перебега.
Используя данные табл. произведем расчеты и внесем их в табл. .
Определим машинно-вспомогательного времени на выполнение автоматических вспомогательных ходов.
Исходя из условий минимизации холостых перемещений и соблюдения техники безопасности расстояние от точки «0» до точки «1» выбрано равным или . При фрезеровании второй половины основания корпуса фреза перемещается на величину с подачей холостого хода . Время холостых ходов при сверлении и при развертывании отверстий будет равно. Расстояние от точки «0» до точки «1» равно (). После обработки первого отверстия инструмент перемещается на величину . По окончании обработки второго отверстия для возвращения в точку «0» инструмент должен переместиться на расстояние или .
Таким образом машинно-вспомогательное время на выполнение автоматических вспомогательных ходов и технологические паузы равно:
Определим машинно-вспомогательное время на автоматическую смену инструмента. Для данного станка время при повороте револьверной головки на одну позицию составляет . Для цикла обработки детали необходимо произвести трижды смену инструмента с поворотом револьверной головки на одну позицию. Суммарное время на автоматическую смену инструмента составит .
Вспомогательное время складывается из составляющих:
- вспомогательное время на установку закрепление открепление и снятие детали. (ч.1 карта 13 поз. 44 инд. д. карта 13 поз. 5 инд. е.)
- вспомогательное время связанное с операцией определим по ч. 1 карте 14 поз. 1 4 6 инд. б.: .
- вспомогательное время на произведение контроля
Итого получаем что .
Время на организационное и техническое обслуживание рабочего места отдых и личные потребности приведено в процентах от оперативного времени (ч.1 карта 16 поз. 20) .
Учитывая полученные данные окончательно имеем
Аналогично нормируем все операции технологического процесса. Данные о нормах основного и штучного времени сведены в таблицу 2.9.
17.Проектирование схем технологических наладок оборудования.
Приведем схему технологической наладки для операции 020 – фрезерование торца и полости корпуса растачивание системы отверстий подрезание фасок сверление отверстий в торце корпуса под крепежный элемент.
Исходными данными при проектировании наладки являются:
Название операции – многоцелевая.
Станок на котором выполняется операция – многоцелевой 2204ВМ1Ф4.
Используемое приспособление – фрезерное.
Режущий инструмент: см. п. 2.10
Конструкторская часть
1.Исходные данные для проектирования станочного приспособления.
Исходными данными для проектирования приспособления являются:
–чертежи детали и заготовки с указанием требований к ним;
–технологический процесс выполнения операции разработанный применительно к условиям среднесерийного производства;
–операционные эскизы с указанием промежуточных и окончательных размеров требований к качеству поверхностей;
–годовая программа выпуска изделий: N=2500шт.
Обработку предполагается производить на станке – 2204ВМ1Ф4.
Заготовка детали - отливка из алюминиевого сплава АЛ7 ГОСТ 1583 - 93. Исходя из анализа чертежа поверхности 17 18 41 не обрабатываются и могут служить черновыми базами каковыми и являются на операции 010. На операции 010 подготавливается чистовая технологическая база пов.1 и два отверстия базирования. На операциях 020 и 030 при получении основных элементов детали схема базирования одинакова поэтому предлагается разработать приспособление для этих операций.
2.Выбор типа приспособления
Пользуясь рекомендациями ЕСТПП выбираем подходящий тип станочного приспособления в зависимости от периода производства изделий Тп и коэффициента загрузки:
Кз= Nоп t ш-кFп где:
Nоп - число повторений операций в месяц;
t ш-к – штучно-калькуляционное время;
Fп -100 - месячный фонд времени работы приспособления.
Число повторений операций в месяц определяем по формуле:
N=2500 штгод –годовая программа выпуска.
По графику [8 рис.3] подходящим типом станочного приспособления является УСП.
3.Выбор схемы станочного приспособления и конструкции установочных деталей.
Схема приспособления во многом определяется построением технологической операции и требованиям к ее производительности.
Согласно технологическому процессу ведется многоинструментальная обработка на многоцелевом станке с ЧПУ. Приспособление должно устанавливаться на плиту поворотного приспособления и фиксироваться в определенном положении. При базировании заготовку следует лишать шести степеней свободы. Заготовка корпуса пневмодвигателя после операции 010 имеет уже обработанную поверхность 1 которая и будет служить установочной базой. В качестве направляющих и опорных баз целесообразно использовать обработанные отверстия под монтаж корпуса пневмодвигателя где в технологическом процессе намерено была проведена дополнительная обработка отверстий развертыванием и тем самым повышена точность до Н7. Повышение точности изготовления отверстий служит для уменьшения погрешности установки что тем самым сильно влияет на общую точность изделия в целом.
Рис.4 Схема базирования заготовки в приспособление.
В качестве установочного элемента выбираем плиту УСП. Направляющими элементами являются установочный и срезанный пальцы. Прижим осуществляется с поверхности 4.
Деталь устанавливается в приспособление после обработки основания на операциях 020 и 030 деталь не переустанавливается. Поэтому погрешность базирования детали отсутствует погрешность базирования состоит из погрешности закрепления.
4.Расчет сил закрепления заготовки.
При обработке корпуса пневмодвигателя на фрезерных позициях операции 020 наиболее подходящий тип схемы закрепления заготовки от смещения предложен в [15 стр.69 рис.40]. Эта расчетная схема применима для случая установки на два пальца и перпендикулярную к ним плоскость.
Рис.5 Схема расчета сил закрепления заготовок от смещения
При достаточной жесткости опор и при наличии зажиного устройства второго типа закрепления Q определим как: где
- коэффициент запаса;
- коэффициенты трения заготовки с установочными и зажимными элементами;
Из условий обработки и предохранения базового отверстия от вмятин ромбического пальца сила резания должна восприниматься силой трения на базовой плоскости заготовки т.е. пальцы должны быть полностью загружены. В данном случае f1= f2=016 - коэффициент трения.
Коэффициент запаса k найдем по рекомендациям [15 стр.83].
k=k0× k1× k2× k3× k4× k5× k6
k0-гарантированный коэффициент запаса при зажиме k0=18.
k1-12 - коэффициент учитывающий неравномерность снимаемого припуска.
k2-17 [15 стр.84 табл.12] - коэффициент учитывающий изменение сил резания.
k3-12 - коэффициент учитывающий динамический характер нагрузки при прерывистом резании.
k4-1 - коэффициент характеризующий зажимное устройство с точки зрения непостоянства сил закрепления.
k5-1 - коэффициент характеризующий удобство расположения рукояток в ручных зажимных устройствах.
k6 - 15 - коэффициент учитывающий только при наличии моментов стремящихся повернуть заготовку.
Итого: k=18×12×17×12×1×1×15=66
Из операции 020 выбираем позицию с наибольшей силой резания - позиция 1.
Рx - определяем как: Рx =05× Рz [7 стр.292]
Рx =05×1550 (Н) откуда
5.Выбор конструкции и размеров зажимных устройств
Основное назначение зажимных устройств станочного приспособления - обеспечение надежного контакта заготовки с установочными опорами и предупреждение смещений и вибраций заготовки.
Зажимные устройства приспособления должны:
–быть простыми по конструкции удобными и надежными;
–не препятствовать подводу и отводу инструмента;
–не деформировать заготовки;
–не сдвигать заготовки при закреплении;
–обеспечивать закрепление с минимальными затратами времени;
–обеспечивать равномерный зажим.
В качестве зажимного устройства из узлов УСП выбран прихват 7012-2178 ГОСТ 26680-76. Преимущество данного вида прихвата в применении центрирующей призмы для прижима по цилиндрической поверхности. Это устройство осуществляет как прижим так и повышает устойчивость заготовки.
Рассчитаем достаточна ли сила зажима выбранного устройства. Из теории «деталей машин» найдем минимальный допустимый диаметр шарнирных болтов стягивающих заготовку. Сила стяжки болтов - Q.
Сила передаваемая одному болту: где i- число болтов т.е. i=2.
Расчетная нагрузка на болт:
где коэффициент зависящий от упругих свойств входящих в соединение частей; -усилие затяжки одного болта Н.
Практически можно считать тогда ориентировочно для прокладки из меди - 035. Тогда общее уравнение: ×i
где F-площадь сечения болтов по внутреннему диаметру резьбы м2.
[sp] - допускаемое напряжение при растяжении МПа.
При выборе болта М16 - его сечение F=141 см2=141*10-4 м2 отсюда
что вполне допустимо.
6.Расчет погрешности закрепления
При закреплении из-за контактных деформаций в стыке базовой поверхности с опорной поверхностью заготовка опускается. Изменяется расстояние между измерительной базой и осью инструмента. Появляется погрешность закрепления величину которой определим из выражения [7 с.52 табл.26]:
eз = (КRz × Rz + KHB×HB + C) × (Q10)m × 1Fm
где Rz- показатель шероховатости по ГОСТ 2789-73 Rz = 3.6 * 4 = 14.4 мкм;
НB - твёрдость материала заготовки НВ 80;
F - расчётная площадь контакта заготовки с опорами F = 116 см2 ;
КRz KHB C - коэффициенты которые при обработке заготовок из алюминия соответственно равны: 0016; -00045 и (0776 + 0053*F).
Подставим значения в расчётную формулу:
eз = (0016×144 - 00045×80 + 0776 + 0053×116) × (1598410)06 ×111606
7.Описание конструкции и принципа работы
станочного приспособления
Схема проектируемого приспособления довольно проста не вызывает затруднений при его эксплуатации. Станочное приспособление предназначено для крепления и правильного базирования детали типа "Корпус редуктора" на многоцелевом сверлильно-фрезерно-расточном станке 2204ВМ1Ф4.
На предварительной операции 010 в корпусе редуктора пневмодвигателя обрабатываются основания и два отверстия по которым в последствии будет производиться базирование корпуса в приспособлении.
Заготовка устанавливается на два цилиндрических отверстия с параллельными осями и перпендикулярную к ним плоскость. Преимущества данной схемы базирования заключаются в простоте конструкции приспособления возможности соблюдения постоянства баз на большинстве операций технологического процесса и относительно простая передача и фиксация заготовок на поточных и автоматических линиях.
По сравнению с установкой на шесть точек эта схема обеспечивает большую доступность режущего инструмента к обрабатываемой заготовке. Станочное приспособление устанавливается на стол станка 2204ВМ1Ф4.
Базирование приспособления на столе станка производится по пальцу 2 и шпонке 18. Прижим приспособления осуществляется прижимом 15. Заготовка корпуса пневмодвигателя устанавливается на 2 пальца приспособления и накрывается вилкой 3 на которую в свою очередь накидывают шарнирный болт 8 с гайкой 7. Затем производится затяжка болта 7. Для правильного закрепления следует добавить что прижимная призма 12 должна соблюдать симметричность к своей оси.
8.Эффективность использования и стоимость технологической оснастки.
Рассчитаем стоимость приспособления S руб.по методике [9]:
где К - количество деталей в приспособлении шт.;
Ус - удельная себестоимость руб.
По спецификации к чертежу общее количество деталей в приспособлении равно 21 в том числе оригинальных - 2. Габаритные размеры приспособления не велики а его изготовление не вызовет затруднений. На основании изложенного отнесём приспособление к 1 группе сложности и будем считать что к = 2 т.е. количеству оригинальных деталей. Примем по табл. 2 [20] Ус = 12600. Тогда стоимость приспособления
S = 2 × 12600 = 25200 руб.
Годовая станкоемкость изготовления продукции цеха: 235000 станко-часа.
Программа выпуска: 2500 штгод.
Размер партии: 99 шт.
Тип производства – среднесерийный.
Производимое изделие: корпус редуктора пневмодвигателя “Крот-12”
Масса детали (корпус редуктора): 2615 кг.
Масса заготовки: 3271 кг.
График работы - 2-х сменный.
Исходя из массы детали и годовой программы пользуясь таблицей 3 [19] принимаем тип производства - среднесерийное.
2.Расчёт количества основного технологического оборудования
Определим количество требуемого основного оборудования [19]:
где Тс - станкоёмкость годового объёма выпуска изделий с запасными частями станкочасов;
Фз - средний действительный годовой фонд времени работы оборудования ч (принимаем равным 2030 ч.);
средний коэффициент загрузки оборудования (09) [19];
средний коэффициент использования оборудования (085) [19].
принимается 152 станка в цехе.
В том числе по участку изготовления корпуса редуктора пневмодвигателя:
Станкоёмкость операции - tс равна штучному времени на операцию.
Станкоёмкость годового выпуска корпуса редуктора пневмодвигателя с запасными частями равна:
где N - заданный объём выпуска изделий;
Кзап - коэффициент учитывающий выпуск запасных частей.
tс - станкоёмкость операции (равна штучному времени на операцию).
Учитывая что корпус редуктора пневмодвигателя «Крот-12» согласно проектируемому технологическому процессу обрабатывается на одном и том же станке получаем
принимается 2 многоцелевых станка с ЧПУ 2204ВМ1Ф4.
3.Определение состава вспомогательных служб
и участков цеха выбор оборудования.
Состав механического цеха зависит от объёма выпуска типа и формы производства.
Для среднесерийного производства требуются следующие вспомогательные службы:
-заточное отделение;
-контрольное отделение;
-мастерская для ремонта приспособлений и инструмента;
-площади для сбора и регенерации СОМЖ;
-отделение по переработке стружки;
-инструментально-раздаточная кладовая;
-термическое отделение;
-заготовительное отделение;
-цеховой склад материалов и заготовок;
-промежуточные склады.
Определим общее количество станков заточного отделения [19]:
где Sоп - количество станков основного производства оснащённых режущим инструментом общего назначения; Sон=152 шт.
j1 - коэффициент условной производительности [19] (примем j1=15);
Sсп - количество станков основного производства оснащённых специальным РИ. Sсп=0 шт.
Примем количество станков для заточного отделения равным 8 шт.
Определим количество оборудования для ремонтной базы механика. Согласно таблице 2 [19] для количества основных станков менее 300 количество основных станков ремонтной базы составляет 2% и не менее 6
Sм=0.02·152=304 следовательно принимаем Sм=6 шт.
В мастерской энергетика цеха производят чистку периодический осмотр и ремонт электродвигателей включая пропитку сушку и испытание обмотки смену подшипников перемотку и восстановление катушек восстановление контактов пусковой аппаратуры и прочие работы для поддержания в исправном состоянии оборудования освещения электродвигателей транспортных и подъемных устройств а также санитарной техники цеха. Режущим оборудованием мастерская не комплектуется.
Мастерская для ремонта приспособлений и инструмента
Определим число станков в мастерской по ремонту приспособлений [19]:
где Sмпр - расчётное число станков определяемое в процентах от обслуживаемого оборудования. Для количества станков 152 согласно [19] стр. 8 примем Sмпр=4% от Sпр
j1 - коэффициент условий производительности j1 = 15. тогда имеем:
Sмп=004·Sпр*15=004·152·15=912следовательно принимаем Sмп =10 шт.
Отделение переработки стружки
Может комплектоваться конвейерами для переработки стружки дробилками сепараторами установками для обезжиривания и брикетировочными прессами.
Расчёт численности и состава работающих.
Состав рабочих в цехе включает следующие категории:
- производственные рабочие;
- вспомогательные рабочие;
- инженерно-технические работники (ИТР);
- младший обслуживающий персонал (МОП).
Производственные рабочие
Их количество определяется по формуле для укрупненных расчетов:
гдеОП – количество принятого производственного оборудования
ФЭ - эффективный годовой фонд времени работы оборудования в часах ФЭ = 2030 ч;
ФР - эффективный годовой фонд времени рабочего в часах ФР=1860ч;
– средний коэффициент использования оборудования =085 [19];
кМ – коэффициент многостаночного обслуживания кМ = 105.
принимается 156 производственных рабочих.
Вспомогательные рабочие
Их число определяют по формуле:
NВСП = (035 07)·NПР = 05·156 = 78 чел
принимается 78 вспомогательных рабочих.
Младший обслуживающий персонал (МОП)
NМОП = (002 003)(NПР + NВСП) = 002·(156 + 78) = 568 чел
принимается 6 человек младшего обслуживающего персонала (гардеробщики уборщики бытовых и служебных помещений курьеры и др.)
Их количество принимают равным 13 – 16 % от общего числа рабочих и составляет:
NЦЕХ СЛ = 013(NПР + NВСП) = 013·(156+ 78) = 304 чел
принимается 31 человек цеховых служащих.
Инженерно-технические работники (ИТР)
Их количество принимают равным 115 – 14 % от общего числа рабочих и составляет:
NИТР = 013(NПР + NВСП) = 013·(156 + 78) = 304 чел
принимается 31 человек инженерно-технических работников.
Счетно-конторский персонал
Их количество принимают равным 15 – 2 % от общего числа рабочих и составляет:
NСЧ-КОН = 0015(NПР + NВСП) = 0015·(156 + 78) = 351 чел
принимается 4 человека счетно-конторского персонала.
Общая численность работающих в цехе NОБЩ. = 306 человек.
4.Расчёт площадей и компоновка оборудования.
Укрупнённый расчёт потребных производственных площадей произведём в зависимости от количества и типов применяемого оборудования размеров и массы обрабатываемых деталей применяемых транспортных средств.
Площадь производственных участков равна [19]:
где Sпр - принятое количество производственного оборудования
F - удельная площадь на единицу оборудования (табл. 7 [19]).
Площадь заготовительного отделения [19]:
гдеSЗО – число станков заготовительного отделения SЗО = 5 ст.
FЗО = 30·5 = 150 м2.
Площадь заточного отделения [19]:
где Sз - количество станков заточного отделения. В соответствии с п.3 имеем:
Площадь контрольного отделения [19]:
Fк=002·Fпр=002·2736=5472 м2.
Площадь ремонтной базы механика [19]:
где Sм - количество соответствующего оборудования
Здесь площадь склада запасных частей принимается в размере 28% от площади ремонтной базы [19]: F1=028·Fм=028·195=546 м2
площадь ремонтной мастерской - 40%:F2=04·Fм=04·195=78 м2
площадь распределительной кладовой - 20 %:F3=02·Fм=02·195=39 м2
площадь участка слесарей-монтажников и слесарей по техническому обслуживанию транспортных устройств - 12%: F4=012·Fм=012·195=234 м2.
Определим площадь ремонтной базы энергетика [19]:
Fэ=035·Fм=035×195=6825 м2
в том числе площадь для ремонта оборудования [19]:F1э=02·Fм=02·195=39 м2
площадь участка слесарей [19]: F2э=015·Fм=015·195=2925 м2.
Площадь участка по ремонту приспособлений [19]:
Fрп=Sпр·22=10·22=220 м2.
Площадь участка сбора и регенерации СОЖ [19]:
Fж=005·Fпр=005·2736=1368 м2.
Площадь отделения по переработке стружки [19]:
Fстр=0035·Fпр=0035·2736=9576 м2.
Цеховой склад материалов [19]:
где среднее количество дней хранения материалов на складе
Qг - масса материала годового объёма выпуска
k - коэффициент использования площади
средняя допускаемая нагрузка на единицу площади
.материала годового объёма выпуска Qг:
Примем по рекомендациям ([19] стр. 13) k=03 и тогда с учётом массы крышки передней и годовой программы выпуска получим следующее значение площади склада:
Определим площадь межоперационного и промежуточного складов:
где Qг - масса годового объёма выпуска деталей
- коэффициент учитывающий отходы металла на предыдущих операциях (согласно стр.13 [19] принимается равным 115)
t - число дней межоперационного хранения (принимается равным 2 дня стр. 13 [19])
i - среднее число доставок полуфабрикатов на склад (в соответствии с количеством операций технологического процесса принимаем i=3)
и - средняя допускаемая нагрузка на единицу площади (в обоих случаях принимаем равными 15 кНм2 стр. 13 [19])
и - коэффициенты использования площади принимаемые согласно [19] соответственно 05 и 03
число рабочих дней запаса (принимаем по таблице 3 [19] равным 12).
Таким образом получаем:
Определим площадь инструментально-раздаточных кладовых [19]:
где Fуд - норма площади на один станок основного производства Sпр - количество станков основного производства. По таблице 8 приложения [19] принимаем Fуд=06 тогда:
Площадь кладовой масел [19]:
где S - количество обслуживаемого оборудования. Суммарное количество единиц обслуживаемого оборудования составит:
S=Sпр+Sвсп=152+8+6+10=176 шт.
тогда площадь кладовой составит:
Площадь мастерской по ремонту инвентаря секции по наладке и освоению оборудования согласно рекомендациям [19] стр.14 соответственно равны:
Fри=30 м2 и Fно=50 м2.
Площадь помещения под компрессорные установки [19]:
Fку=0008·Fпр=0008·2736=219 м2.
Площадь под трансформаторные подстанции [19]:
Fтр=001·Fпр=001·2736=2736 м2
но с учётом требования: Fтр50=К (целое число) [19] стр.14 принимаем при К=1 Fтр=50 м2.
Площадь вентиляционных камер [19]:
Fвк=007·Fпр=007·2736=19152 м2.
Таким образом общая площадь цеха без учёта площадей служебно-бытовых помещений равна:
Наиболее распространённой конструкцией зданий для размещения механосборочных цехов согласно [19] являются одноэтажные многопролётные здания прямоугольной формы с полом на бетонном основании и перекрытием поддерживаемым системой колонн образующих пролёты цеха. Выбор основных параметров здания производится с учётом особенностей технологического процесса и определяется рациональным размещением производства и экономичностью строительства достигаемой при применении унифицированных строительных элементов и типовых конструкций.
Для полученной площади здания (см. п. 4.5) наиболее рациональной формой является прямоугольник с соотношением сторон 1:2. принимаем шаг внутренних колонн равным 24 м шаг колонн по периметру здания - 12 м ширину пролёта - 24 м высоту пролёта – 72 м.
С учётом произведённых расчётов основываясь на принципе минимума грузопотоков (стр. 15 [19]) спроектируем компоновочный план цеха. Такому принципу отвечает расположение на плане цеха заточного отделения рядом с инструментально-раздаточной кладовой отделения оперативного контроля – рядом с межоперационной кладовой цеховые склады материалов и заготовок – рядом с заготовительным участком.
Производственная часть механического цеха представляет собой общий зал без перегородок разделенный на отдельные участки магистральными и поперечными проездами (таблица 4 [19]).
К планировке оборудования производственных участков наряду с требованиями эстетики предъявляется ряд производственных и эксплуатационных требований основными из которых являются удобство и безопасность работы. Кроме того должен быть обеспечен удобный подвоз тяжелого инструмента крупных приспособлений и запасных узлов оборудования безопасный подход к станку для смазки и разборки его на месте установки возможность уборки стружки.
При расстановке оборудования должны выдерживаться расстояния между крайними положениями рабочих органов станков между станками и проездами стенами и колоннами.
6.Определение площадей и компоновка служебно-бытовых помещений.
В состав служебно-бытовых помещений цеха входят объекты культурно-бытового назначения и объекты административно-технического назначения. К первым относятся гардеробные с умывальниками душевые туалетные комнаты помещения для личной гигиены комнаты для курения устройства для снабжения питьевой водой столовые медпункты помещения для отдыха. Ко вторым относятся помещения начальников смен мастеров и бригадиров цеховые конторы лаборатории помещения для учебных занятий и пр.
Наибольшую площадь занимают гардеробные. Согласно рекомендациям [19] стр. 18 принимаем для гардеробных шкафчиков размеры 50x50x165 см ширину прохода между шкафами со скамьями 2м между шкафами и стеной - 13 м площадь комнаты для инвентаря - 3м2. Общее количество шкафчиков составит 306
Умывальные разместим в помещении гардеробной. Примем количество умывальников в расчёте 15 чел на 1 умывальник тогда получим общее количество умывальников:
Примем размер одного умывальника 60x40 см ширину прохода - 15 м.
Санузлы располагают равномерно на расстоянии не более 75 м. Площадь комнаты с учётом шлюзов составляет 36 м2.
Медицинский пункт цеха расположим вблизи выхода на первом этаже служебно-бытовых помещений. Принимаем согласно [19] стр. 19 площадь медпункта - 90 м2.
Площадь помещений общественного питания включая подсобные помещения кухни:FОП = 061·NОБЩ. = 061·306 = 186.6 м2.
Площадь помещений для культурного обслуживания (библиотеки учебные комнаты и др.): FК ОБС = 03·NОБЩ. = 03·306 = 91.8 м2.
Площадь служебных помещений (цеховые конторы лаборатории):
FСП = 07·NОБЩ. = 07·306 = 214.2 м2
Конторские помещения для цехового персонала занимающегося технологическим планированием руководством и бухгалтерским учётом расположим на втором этаже служебно-бытовых помещений. При удельных площадях 07 м2 на 1 человека ([19] табл.5) их общая площадь составит:
Площади санитарно-гигиенических помещений примем приблизительно по данным табл. 5 [19]:306316=966.96 м2.
Более точно данные площади определим после их предварительной компоновки с учётом данных приведённых выше.
1.Технико-экономический анализ.
Согласно п.2.5 в проектируемом технологическом процессе изготовления корпуса редуктора пневмодвигателя «Крот-12» используется заготовка измененной конфигурации: масса заготовки уменьшилась на 0401 кг.
За счет изменения структуры технологического процесса и использования современного оборудования время обработки сократилось следовательно трудоемкость изготовления в проектируемом варианте ниже.
2.Определение дополнительных капитальных вложений (инвестиций).
Общие капитальные вложения определяются по формуле [23 стр. 8]:
К = КОБ + КОСН + КЗДН + КПР
гдеКОБ КОСН - затраты на приобретение доставку монтаж наладку оборудования и оснастку руб.;
КЗДН - стоимость необходимых производственных площадей зданий сооружений;
КПР - прочие капитальные вложения например затраты на научно-исследовательские и проектно-конструкторские работы.
гдеаТЗ - процент учитывающий транспортно-заготовительные расходы [23 табл. 2.1 стр. 26];
аМ - процент учитывающий затраты на монтажные работы [23 табл. 2.1 стр. 26];
Ц - договорная цена единицы оборудования руб.;
n - количество технологического оборудования необходимого для выполнения заданного годового объема работ:
N - годовая программа выпуска;
КВН - коэффициент выполнения норм.
Учитывая что согласно проектируемому технологическому процессу обработка корпуса редуктора пневмодвигателя «Крот-12» производится на многоцелевом станке мод. 2204ВМ1Ф4 произведем расчет затрат на приобретение доставку монтаж наладку оборудования следующим образом:
t = 092 ч; N = 2500 шт.; ФД = 2030 ч; КОДН = 1; КВН = 105;
Ц = 274000 руб.; аТЗ = 5%; аМ = 4%;
Таким образом общие затраты на приобретение доставку монтаж наладку оборудования составляют КОБ = 598416 руб.
Затраты на изготовление приспособления используемого на операциях 020 и 030 укрупненно определяются по [17 табл. 17 стр. 426].
Стоимость приспособления:
КОСН = 39·1618 = 63102 руб.
где1618 - коэффициент перевода стоимости на текущий период.
Затраты на проектирование технологических процессов и приспособлений рассчитываются по трудоемкости считая что 1 человеко-час работы разработчика составляет примерно 2912 руб.
Нормы времени на технологические и конструкторские работы приведены в [16 табл. 29 30 стр. 433 435]. Для технологических процессов механической обработки деталей 2 группы сложности нормы времени составляют 1245 ч. Для конструирования технологической оснастки 2 группы сложности нормы времени составляют 785 ч. Тогда затраты на проектирование 59114 руб.
В данных расчетах капитальные вложения на здания и сооружения не учитываются так как внедрение новой техники не связано с изменением необходимой площади зданий и сооружений.
Окончательно дополнительные капитальные вложения:
DК = 598416 + 63102 + 59114 = 59963816 руб.
3.Расчет себестоимости продукции
Для сопоставления текущих затрат на изготовление корпуса долота в условиях базового и проектируемого вариантов необходимо определить технологическую себестоимость. При этом расчет следует производить по изменяющимся элементам затрат к которым могут относиться следующие расходы [23 стр. 11]:
С = ЗМ + ЗСТ + АОБ + АЗД + ЗЭЛ + ЗРИ + ЗР + ЗПОМ
гдеЗМ - затраты на материалы руб.;
ЗСТ - затраты на основную и дополнительную заработную плату с отчислениями на социальные нужды руб.;
АОБ - амортизационные отчисления от стоимости оборудования руб.;
АЗД - амортизационные отчисления от стоимости здания руб.;
ЗЭЛ - затраты на силовую электроэнергию руб.;
ЗРИ - затраты на режущий инструмент руб.;
ЗР - затраты на текущий ремонт и межремонтное обслуживание оборудования руб.;
ЗПОМ - затраты на эксплуатацию производственных и бытовых помещений руб.
Затраты на материалы включают в себя затраты на основные материалы и затраты на вспомогательные.
К основным материалам относятся отливки поковки прутковый и листовой прокат метизы трубы полуфабрикаты.
Стоимость сырья и материалов определяется на основании норм расхода каждого вида материалов и цен за вычетом стоимости отходов.
Расход на основные материалы для изделий на годовую программу:
где НР - норма расхода материала на одно изделие кг;
ЦМ - планово-заготовительная цена 1 кг. руб.;
РО - возвратные отходы кг.;
ЦО - цена 1 кг. отходов руб.;
N - годовая программа выпуска продукции шт.
К вспомогательным расходам относятся смазочные масла керосин бензин резина обтирочные материалы материалы для текущего ремонта оборудования. Затраты на вспомогательные материалы определяют исходя из установленных норм расхода на рабочее место и цен.
При укрупненных расчетах затраты на вспомогательные материалы составляет 15-2% от стоимости основных материалов
По базовому варианту
По проектируемому варианту:
Затраты на основную и дополнительную заработную плату с отчислениями на социальные нужды на годовую программу выпуска определяются по [23 стр. 12]:
гдеtШТ - норма штучного времени на операцию для базового технологического процесса tШТ = 654 мин для проектируемого технологического процесса tШТ = 552 мин
ТСТ - часовая тарифная ставка соответствующего разряда по сдельной оплате труда на
КСП - коэффициент учитывающий премиальные доплаты КСП = 12;
КДЗ - коэффициент учитывающий дополнительную зарплату КДЗ = 13;
КСН - коэффициент учитывающий отчисления на социальные нужды КСН = 126;
n - число операций для базового варианта n = 7 для проектируемого варианта n = 4;
N - годовая программа выпуска N = 2500 шт.
Итого получаем что затраты на основную и дополнительную заработную плату с отчислениями на социальные нужды составляют:
по базовому варианту:
по проектируемому варианту:
Годовые амортизационные отчисления от стоимости оборудования рассчитываются по [23 стр. 13]:
гдеЦ - первоначальная стоимость оборудования руб.;
НА - норма амортизационных отчислений %.
Годовые амортизационные отчисления от стоимости оборудования:
Ц = 924000 руб.; НА = 116% [23 табл. 2.2 стр. 28]
Ц = 598416 руб.; НА = 116% [23 табл. 2.2 стр. 28]
Годовые амортизационные отчисления от стоимости зданий можно не учитывать так как размеры площадей значительно не изменяются от варианта к варианту.
Затраты на силовую электроэнергию на годовую программу выпуска [22 стр. 426]:
гдеNЭ - установленная мощность всех электродвигателей оборудования кВт;
- коэффициенты загрузки станков по времени и по мощности [22 табл. 18 стр. 427] =04;
ЦЭ – цена 1 кВт·ч электроэнергии ЦЭ = 12 руб;
N – годовая программа выпуска N = 2500 шт.
Затраты на силовую электроэнергию на годовую программу выпуска:
по проектному варианту
Затраты на текущий ремонт и межремонтное обслуживание оборудования составляют 3% от стоимости оборудования [16 стр. 424]:
гдеЦ - общая стоимость оборудования ЦБ = руб. по базовому варианту ЦПР = 598416 руб. по проектируемому варианту
ЗР = 003· = 27720 руб.;
ЗР = 003·598416 = 1795248 руб.
Затраты на режущий инструмент принимаются в сумме 1800 руб. на 1 станок [26 стр. 14].
ЗРИ = 1800·3 = 5400 руб.;
ЗРИ = 1800·2 = 3600 руб
Затраты на эксплуатацию производственных и бытовых помещений можно не учитывать так как размеры площадей значительно не изменяются от варианта к варианту.
Таким образом себестоимость изделия корпус долота на годовую программу составит:
С = ++++5400+27720 = 1300793 руб.
По проектируемому варианту
С = ++++3600+1795248= 115366815 руб.
Цеховые расходы принимаются в размере 80% от основной заработной платы производственных рабочих и составляют:
по базовому варианту - 19711039 руб.
по проектируемому варианту - 16636838 руб.
Общезаводские расходы принимаются в размере 67% от основной заработной платы производственных рабочих и составляют: по базовому варианту – 16507994 руб. по проектируемому варианту – 13933352 руб.
Величина внепроизводственных расходов принимается в размере 3% от производственной себестоимости и составляет:
по базовому варианту – 3902379 руб.
по проектируемому варианту – 3413395 руб.
Полная себестоимость продукции (на весь объем продукции):
по базовому варианту 170200712 руб.;
на единицу 6808 руб.;
по проектируемому варианту 1493504руб.;
на единицу 5974 руб.
Данные по себестоимости изготовления корпуса долота на годовую программу выпуска приведены в таблице 5.1.
Себестоимость продукции на годовую программу
Расходы на сырье и материалы
Расходы на основную и
дополнительную заработную
плату рабочих с отчислениями на
Амортизационные отчисления
Расходы на силовую электроэнергию
Расходы на режущий инструмент
Расходы на текущий ремонт
и межремонтное обслуживание
Цеховая себестоимость
Общезаводские расходы
Производственная себестоимость
Внепроизводственные расходы
Полная себестоимость
Прибыль в проектируемом варианте определяется по формуле:
ППР = ПБАЗ + СБАЗ – СПР.
Прибыль в базовом варианте заложена с учетом рентабельности выпуска 20% и составляет:
ПБАЗ = 02·СБАЗ = 02·1702000 = 340400 руб.
ППР = 340400+ 1702000 – 1494000 = 548400 руб.
Оптовая цена продукции в базовом и проектируемом вариантах остается неизменной:
Производительность труда одного рабочего-станочника
гдеn – число рабочих-станочников изготавливающих данную деталь nБ = 3 чел. nПР = 2 чел.;
N – годовой выпуск продукции N = 2500 шт.
Пt Б = 81696·25003 = 680800 руб.
Пt ПР = 81696·25002 = 1021200 руб.
Рентабельность выпуска корпуса редуктора определяется по формуле:
Основные технико-экономические показатели
Годовой экономический эффект определяется по формуле [23 стр. 17]:
ЭГОД = (СБ – СПР) – ЕН·ΔК
гдеЕН – нормативный коэффициент дополнительных капитальных вложений ЕН = 015 [23 стр. 17];
ΔК – дополнительные капитальные вложения ΔК = 59963816 руб.
ЭГОД = (1702000 – 1494000) – 015·59963816 = 118554276руб.
Срок окупаемости дополнительных капитальных вложений [23 стр. 17]:
Сравнительные технико-экономические показатели вариантов технологических процессов изготовления корпуса редуктора приведены в таблице 5.2.
Сравнительные технико-экономические показатели
Годовой выпуск продукции шт.
Товарная продукция тыс. руб.
Число рабочих-станочников
Себестоимость единицы продукции руб.
Производительность труда 1
рабочего-станочника тыс. руб.чел.
Себестоимость годового выпуска
Материалоемкость продукции
Затраты на 1 руб. товарной продукции
Рентабельность продукции %
Балансовая прибыль тыс. руб.
Годовой экономический эффект
Срок окупаемости затрат лет
БЕЗОПАСНОСТЬ ЖИЗНЕДЕЯТЕЛЬНОСТИ
Охрана труда – это система законодательных актов социально-экономических технических и лечебно-профилактических мероприятий обеспечивающих безопасность сохранение здоровья и работоспособности человека в процессе труда.
Задача охраны труда – свести к минимуму вероятность поражения или заболевания работающего с одновременным обеспечением комфортности и максимальной производительности труда.
Охране труда на предприятиях всегда оказывалась большое внимание и являлась общегосударственной задачей. Однако с развитием научно-технического прогресса появляется ряд новых проблем. Повышение технической оснащённости машиностроительных предприятий применение новых материалов конструкций увеличение скоростей и мощности машин оказывает влияние на характер и частоту несчастных случаев и заболеваний па предприятиях. Улучшение условий труда приводит к экономическим и социальным результатам – улучшению здоровья трудящихся повышению степени удовлетворённости трудом укреплению дисциплины повышению производительности труда и т.д.
Современным требованиям научно-технического прогресса может отвечать только всесторонне обоснованная система комплексных задач охраны труда.
2.Требования охраны труда к производственным
и санитарно-бытовым помещениям
На каждого работающего должно приходиться не менее 15 м3 объема и не менее 15 м2 площади помещений. Рабочие места проходы и проезды не должны загромождаться сырьем полуфабрикатами и готовыми изделиями. Граница проходов и рабочих площадок надлежит обозначать видимыми белыми линиями шириной не менее 50 мм.
Использование производственных помещений для принятия пищи запрещается. Все производственные помещения рабочие места и оборудование должны содержаться в чистоте и порядке. Отбросы и мусор должны регулярно собираться и удаляться в специально отведенные для этой цели места. Для отбросов и мусора в производственных помещениях должны быть установлены в доступных и удобных местах мусорные ящики и урны которые должны быть убраны не реже одного раза в день и систематически дезинфицироваться.
Пол стены и потолки рабочих помещений должны содержаться в исправности своевременно ремонтироваться.
Раздевалки гардеробные душевые и другие санитарно-бытовые помещения необходимо периодически подвергать дезинфекции.
Душевые необходимо обеспечивать горячей водой в количестве достаточном для всех рабочих Смесительные приборы должны быть безопасными легко открываться и не подтекать. Температура воды 28 37 °С.
Структура системы охраны труда работающих состоит из трех подсистем (рис.6). Подсистема обеспечения безопасной работы персонала предназначена для эксплуатации и обслуживания металлорежущего оборудования а также профилактики и ликвидации пожаров.
Большое значение в этой системе имеет защита от воздействия механических устройств. Все ременные передачи закрыты кожухами зона обработки на токарных сверлильных зубообрабатывающих станках закрывается в процессе обработки защитными экранами со смотровым окном. Время торможения шпинделя ограничено 5 секундами. Рукоятки и другие органы управления станками должны быть снабжены надежными фиксаторами не допускающими самопроизвольных перемещений органов управления. Двери электрошкафов станков должны закрываться специальными замками.
Защита от стружки о СОЖ должна быть как индивидуальной (очки специальная обувь) а также осуществляться с помощью оградительных устройств.
Рис.6 Структура системы охраны труда.
Должны быть приняты все меры обеспечивающие надежную защиту работающих от любого вида поражения электрическим током.
Пожарная безопасность должна обеспечиваться мерами противопожарной профилактики и активной пожарной защиты включающей систему пожарных гидрантов стационарных пожарных установок автоматических ручных с дистанционным пуском огнетушителями противопожарными щитами с ящиками для песка.
Подсистема обеспечения санитарных условий труда должна включать в себя меры по соблюдению санитарных норм воздушной среды освещенности чистоты рабочих мест защиты рабочих мест от шума вибраций. А также проведение мероприятий по производственной эстетике.
Подсистема обслуживания работающих предназначена для создания нормальных условий работающим путем организации бытового и медицинского обслуживания а также службы общественного питания.
По видам обслуживание должно включать в себя:
Местное – в радиусе 50-90 м от рабочих мест необходимо предусмотреть курительные санитарные узлы питьевые устройства.
Цеховые – в радиусе 200-400 м должен быть предусмотрен комплекс гардеробов умывальников и душевых помещений.
Общезаводские - в радиусе 500-800 м должны быть предусмотрены прачечные химчистки и другие объекты бытового использования.
3.Требования охраны труда к оборудованию
В спроектированном механическом цехе 152 единиц металлорежущего оборудования основного производства. Транспортировка контейнеров с заготовками осуществляется электрокарами.
Отличительной особенностью этих станков является кинематика их рабочих движений. На этих станках инструмент совершает вращение иили выполняет движение подачи.
Основными опасными производственными факторами при эксплуатации станков является образующаяся в процессе резания стружка.
При работе с высокими скоростями резания особое внимание должно быть уделено правильному и надежному закреплению заготовок.
Движущие части представляющие опасность должны быть ограждены. Конструкции ограждающих устройств должны быть прочными надежно крепиться не мешать производственной работе уборке и наладке станка.
Станки следует снабжать экранами защищающими рабочих и окружающих от травмирования или от брызг СОЖ. Конструкция экранов должна быть легкоподвижной и предусматривать возможность чистки смотровых окон от загрязнения. Конструкция станков и их элементов должны способствовать отводу стружки из зоны резания быть удобной для очистки от стружки пыли масла.
Станки на которых вспомогательные перемещения производятся при включении органов главного движения станка необходимо снабжать быстродействующими тормозными устройствами. Рычаги и рукоятки управления должны быть расположены в местах удобных для обслуживания и не требовать значительных перемещений рук рабочего. Местоположение этих органов и рукояток должно исключать возможность случайного включения.
Пусковые педали оборудования должны иметь надежное ограждение или предохранительные устройства исключающие возможность непреднамеренного включения оборудования по какой-либо случайной причине.
Все органы управления эксплуатируемого оборудования должны иметь четкие и ясные надписи и символы указывающие их назначение.
4.Оздоровление воздушной среды в производственных помещениях.
Самочувствие и работоспособность человека зависят от состояния метеорологических характеристик окружающей среды которая определяется основными параметрами:
-относительной влажностью;
-подвижностью воздуха.
Оптимальная температура воздуха в машинном зале составляет 20-22°С влажность 60-65% и скорость движения воздуха в пределах 02т – 04 мс.
Вентиляцией называется комплекс взаимосвязанных устройств и процессов предназначенных для создания организованного воздухообмена с целью обеспечения нормальных метеорологических условий в рабочей зоне помещений.
Вентилирование помещений осуществляется с помощью вентиляционных систем которые по своему назначению подразделяются на три типа:
)Общеобменные – системы которые осуществляют смену воздуха во всем помещении.
)Местные – системы которые обеспечивают улавливание производственных вредностей в местах их выделений и последующее удаление из помещений.
)Смешанные – системы которые выполняют одновременно обе функции.
Устройство в помещении только местной вентиляции недопустимо. Общеобменная вентиляция необходима во всех случаях.
Системы вентиляции по способу побуждения движения воздуха делятся:
-системы с естественным побуждением движения воздуха (аэрация);
-системы с искусственным побуждением движения воздуха (механическая или принудительная вентиляция).
В первом случае причиной перемещения воздуха служат естественные факторы (тепловой напор или движение ветра) во втором – для перемещения воздуха применяют специальные побудители тяги: вентиляторы воздуходувы эжекторы и др.
Вентиляционные установки могут быть приточными и вытяжными. Приточные установки подают свежий воздух в помещении а вытяжные удаляют из помещения отработанные загрязненный воздух. Обычно эти установки действуют совместно образуя приточно-вытяжную систему.
При продолжительной работе с ЭВМ и другими электроустановками воздух в помещении нагревается поэтому для сохранения нормальной температуры необходимо применять принудительную вентиляцию.
В проектируемом цехе нет процессов выделяющих в окружающую среду вредных веществ и следовательно для воздухообмена достаточно свежего воздуха из естественной среды.
5.Меры по снижению уровня шума и вибраций в производственных помещениях.
Шум – это совокупность апериодических звуков различной интенсивности и частоты. С физиологической точки зрения шум – это всякий неблагоприятно воспринимаемый шум. Шум является одним из распространенных и неблагоприятных факторов на производстве.
Интенсивный шум на производстве способствует снижению внимания и увеличению ошибок при выполнении работы. Из-за шума снижается производительность труда и ухудшается качество работы. Шум затрудняет своевременную реакцию работающих на предупредительные сигналы внутрицехового транспорта (автопогрузчики мостовые краны и т. п.) что способствует возникновению несчастных случаев на производстве.
Источником шума в цехе являются машины механизмы агрегаты и другое оборудование цеха. Степень влияния шума зависит от его интенсивности и продолжительности воздействия состояния центральной нервной системы и что очень важно от индивидуальной чувствительности организма к акустическому раздражителю. Вредное воздействие шума отражается на органах слуха оказывает отрицательное влияние на центральную нервную систему и весь организм в целом.
Гигиенические нормативы шума определены ГОСТ 12.1.003–83 и СН 2.2.42.1.8.562–96. Допустимый уровень звука и эквивалентный уровень звука на постоянных рабочих местах и в рабочих зонах в производственных помещениях и на территории предприятий составляет 75-85 дБ.
Понизить уровень шума для обеспечения максимального комфорта и других условий труда позволяет использование мероприятий по борьбе с шумом:
)снижение звуковой мощности источника шума;
)изменение направленности излучения шума;
)акустическая обработка помещений;
)уменьшение шума на пути его распространения;
)применение глушителей шума;
)применение средств индивидуальной защиты (вкладышей наушников шлемов).
Вибрация – это малые механические колебания возникающие в упругих телах. Вибрация относится к факторам обладающим высокой биологической активностью. Действие вибрации зависит от частоты и амплитуды колебаний продолжительности воздействия демпфирующих свойств тканей организма человека явлений резонанса и других условий.
Гигиеническое нормирование вибраций осуществляется по ГОСТ 12.1.012–90 и СН 2.2.42.1.8.566–96.
Вибрация высокой интенсивности при продолжительном воздействии вызывает изменения в нервной и сердечно-сосудистой системах опорно-двигательном аппарате желудочно-кишечном тракте органах равновесия.
Основными методами борьбы с вибрациями машин и оборудования являются:
)снижение виброактивности машин;
)отстройка от резонансных частот;
)вибродемпфирование;
)повышение жесткости системы;
)применение индивидуальных средств защиты (для рук - виброизолирующие рукавицы перчатки вкладыши и прокладки; для ног - виброизолирующая обувь стельки подметки).
Для уменьшения вибраций используются виброизоляция (виброопоры из резины пружины рессоры). При невозможности проведения указанных технических мероприятий обязательно использование индивидуальных средств защиты (виброботинки виброрукавицы и т. д.).
Уровни вибрации на рабочих местах определяются на установке для испытания на нормы точности. Проверка уровня вибрации производится при испытании каждого нового образца оборудования.
Для профилактики профессиональных заболеваний и снижения вредного воздействия шума и вибраций необходимо применять предупредительные меры. Прежде всего они должны учитываться при проектировании строительстве и организации технологического процесса. Шумное с интенсивной вибрацией процессы и оборудование размещается в изолированных помещениях. Для снижения фона отраженного шума стены потолки нужно облицовывать звукопоглощающими материалами. Вращающиеся движущиеся части технологического оборудования являются источниками шума и вибраций поэтому они должны тщательно пригоняться балансироваться смазываться.
6.Производственное освещение. Расчет освещенности цеха.
Освещение рабочего места – важнейший фактор создания нормальных условий труда. Освещение должно отвечать условиям оптимальной работы органов зрения человека. Повышение освещенности как правило ведет к росту производительности труда однако есть предел при котором дальнейшее повышение освещенности такого эффекта уже не дает.
Освещение должно быть равномерным так как перевод взгляда с более освещенной поверхности на менее освещенную вызывает повышенную утомляемость глаза. Светлая отделка потолков стен способствует созданию равномерного распределения световых потоков.
На рабочих поверхностях должны отсутствовать резкие тени прямой и отраженный блеск. Ограничение прямой блесткости достигается уменьшением яркости источников света правильным выбором защитного угла светильника увеличением высоты подвески светильников. Отраженная блесткость устраняется путем использования матовых поверхностей изменением угла наклона рабочей поверхности. Освещение не должно искажать светопередачу. Равномерность цветопередачи обеспечивается использованием комбинированного освещения которое представляет совокупность местного и общего освещения. Осветительная установка должна быть удобной надежной экономной не создавать шума и не быть источником дополнительной опасности.
Освещенность на рабочих местах и поверхностях станков класса П и В должна быть не ниже 400 лк при освещении газоразрядными лампами. Общее искусственное освещение цеха с металлорежущими станками должно быть равным 400 лк при освещении газоразрядными лампами.
В данном разделе производится расчет освещения производственных участков механического цеха. Для расчета рабочего искусственного освещения цеха в качестве исходных данных принимается:
тип источника света: для освещения производственного помещения – лампа дуговая ртутная люминесцентная ДРЛ–400 имеющая величину светового потока ФП = 19000 лм ;
тип системы освещения – комбинированная;
характеристики цеха: длина –96 м ширина – 48 м высота расположения светильников – 96 м;
коэффициент минимальной освещенности равный отношению средней освещенности и минимальной ЕСРЕMIN для ламп ДРЛ z = 115.
Расчет общего равномерного искусственного освещения горизонтальной рабочей поверхности выполняется методом коэффициента использования светового потока.
Световой поток (лм) одной лампы
гдеЕН – нормированная минимальная освещенность по СНиП 23–05–95 ЕН = 200 лк;
S – площадь освещаемого помещения S = 4608 м2;
z – коэффициент неравномерности освещения z = 115;
kЗ – коэффициент запаса kЗ = 15;
И – коэффициент использования светового потока;
N – число светильников в помещении.
Коэффициент использования светового потока И давший название методу расчета определяют по СНиП 23–05–95 в зависимости от типа светильника коэффициентов отражения потолка ρП стены ρC пола ρР размеров помещения определяемых индексом помещения
гдеА – длина помещения в плане А = 96 м;
В – ширина помещения в плане В = 48 м;
НР – высота подвеса светильников над рабочей поверхностью НР = 88 м.
Согласно справочной литературе для коэффициентов отражения потолка ρП = 30% стены ρC = 10% пола ρР = 10% и индекса помещения i = 229 коэффициент использования светового потока И = 06.
Таким образом определяется число светильников в помещении:
Таким образом для освещения проектируемого механического цеха принимается 140 светильника типа УПДДРЛ с лампами ДРЛ–400.
Определяется световой поток
Отклонение потока выбранной лампы ДРЛ–400 (ФП = 19000 лм) от расчетного
что лежит в пределах –10% +20%.
7. Электробезопасность. Расчет защитного заземления.
Цеха промышленного производства как правило оснащены значительным количеством электроустановок. Проектируемый цех не является исключением поэтому достаточное внимание должно уделяться вопросам безопасности при эксплуатации электрооборудования.
Электробезопасность – это система организационных и технических мероприятий и средств обеспечивающих защиту от вредного и опасного воздействия электрического тока электромагнитного поля и статического электричества.
Основными мерами защиты от поражения током является обеспечение недоступности токоведущих частей; электрическое разделение сети; устранение опасности поражения при появлении на корпусах кожухах и других частях электрооборудования; выравнивание потенциала заземления; организация безопасности эксплуатации электроустановок.
Согласно «Правилам устройства электрических установок» сопротивление защитного заземления для установок с напряжением до 1000 В не должно превышать 4 Ом.
Защитным заземлением называется преднамеренное электрическое соединение с землей металлических нетоковедущих частей установок которые могут оказаться под напряжением. Схема заземления приведена на рис.7.
Рис.7 Схема защитного заземления
– внутренний контур заземления; 2 – наружный контур заземления;
– переходное соединение в наружной стене механического цеха;
– заземлитель; 5 – оборудование; 6 – наружная стена цеха.
Для снятия напряжений до безопасной величины относительно земли на металлических частях оборудования необходимо произвести расчет защитного заземления. Защитное заземление состоит из группы заземлителей расположенных непосредственно в земле и соединительной полосы. С их помощью осуществляется надёжное заземление станка.
В качестве заземления используем стальную трубку ø50 мм и длиной 3 м.
Сопротивление трубки:
ρ – удельное сопротивление; ρ=025·104 Ом для 10% влажности;
t – глубина заземления; t=1600 мм;
d – диаметр трубки; d=50 мм;
Количество заземлений в системе:
r1=12 и r2=06 – коэффициенты экранизации;
Соединение заземлений ведем стальной полосой шириной B=5 см и толщиной h=05 см.
a=3 м – шаг заземления;
r=105 – коэффициент удлинения полосы.
Сопротивление полосы:
t0=08 – глубина залегания полосы.
Сопротивление всей системы заземления:
8.Обеспечение пожарной безопасности.
Пожары на предприятиях представляют большую опасность для работающих и могут причинять громадный материальный и моральный ущерб. Вопросы обеспечения пожарной безопасности зданий и сооружений имеют большое значение и утверждены специальными государственными постановлениями и решениями.
Пожарная безопасность может быть обеспечена мерами пожарной профилактики и активной пожарной защиты. Пожарная профилактика включает в себя комплекс мероприятий необходимых для предупреждения возникновения пожара или уменьшения его последствий..
Механический цех относится к категории D т.к. в цехе обрабатываются негорючие материалы в холодном состоянии и все основные конструкции выполнены из несгораемых материалов – железобетона кирпича металлоконструкций.
Основные опасные факторы пожара: открытый огонь искра повышенная температура воздуха и окружающих предметов токсичные продукты горения дым нахождение технологического оборудования под напряжением и т. д.
Мероприятия предупреждающие возникновение пожара на предприятии:
Запрещено разведение открытого огня на всей территории завода и на территории прилегающей к ней ближе чем на 50 м.
На каждом участке установить специальные контейнеры для использованного обдирочного материала отходов ветоши которые регулярно вывозятся.
Регулярно проверять состояние электрической проводки.
Сварочные работы проводить в местах удаленных от легковоспламеняющихся материалов.
Все работники предприятия ознакомляются с приемами тушения пожаров в каждом цехе есть ответственный за противопожарную безопасность.
Курение разрешено только в специально отведенных местах.
Для эвакуации людей и материальных ценностей разрабатывается план эвакуации. Руководителю предприятия предоставлено право налагать дисциплинарные взыскания за нарушения правил и требований пожарной безопасности.
В каждом здании должно быть достаточное количество выходов для обслуживающего персонала.
Для тушения пожаров в начальной стадии внутри зданий предусматриваются внутренние пожарные водопроводы. Внутренний водопровод состоит из вводов водомерных узлов стояков разводящей сети водоразборной и регулирующей аппаратуры.
Внутренние пожарные краны устанавливаются в нишах или шкафчиках у входов на площадках отапливаемых лестничных клеток в коридорах и других доступных местах на высоте 135 м от уровня пола. К пожарным кранам присоединяются рукава со стволами.
Систему внутреннего пожарного водопровода проектируют таким образом чтобы обеспечить бесперебойную и удобную подачу воды из пожарных стволов до прибытия более мощных средств пожарной защиты или тушения пожаров.
Пожарные краны оборудуют пожарными стволами с диаметром насадки 16 мм. Пожарные краны размещают так чтобы компактные струи подаваемые из стволов подключенных к двум соседним кранам соприкасались в наиболее высокой и удаленной точке на границе их взаимодействия.
Рассчитаем необходимое количество огнетушителей для проектируемого цеха:
S – площадь цеха S=4608 м2;
0 м2 – норма площади на один огнетушитель.
Таким образом в проектируемом цехе необходимо установить 46 огнетушителей.
1.Использование трехмерного моделирования для подготовки рабочего чертежа детали.
В дипломном проекте проведено моделирование корпуса редуктора пневмодвигателя с целью получения информации о геометрических и массо-центровочных параметрах а также для анализа возможности получения точной отливки заготовки выбранным способом.
Кроме того в процессе моделирования были проведен анализ исходной конструкторской документации.
Полученные модели деталей можно использовать в дальнейшем для создания и анализа сборочной модели пневмодвигателя «Крот-12М».
2.Выбор системы проектирования.
Общепринятым порядком моделирования твердого тела является последовательное выполнение булевых операций (сложения и вычитания) над объемными примитивами (сферами призмами цилиндрами конусами пирамидами и т.д.). Большинство таких операций были использованы при создании трехмерной модели корпуса радиатора.
В КОМПАС-3D объемные примитивы образуются путем выполнения такого перемещения плоской фигуры в пространстве след от которого определяет форму примитива. При этом получение формы детали во многом может соответствовать известным формообразующим методам используемым в механической обработке путем снятия материала.
Проектирование детали начинается с создания базового тела путем выполнения операции над эскизом (или несколькими эскизами).
При этом доступны следующие типы операций:
вращение эскиза вокруг оси лежащей в плоскости эскиза;
выдавливание эскиза в направлении перпендикулярном плоскости эскиза;
кинематическая операция - перемещение эскиза вдоль указанной направляющей;
построение тела по нескольким сечениям-эскизам.
Каждая операция имеет дополнительные опции позволяющие варьировать правила построения тела.
3.Трехмерное проектирование корпуса редуктора.
На рис.8 показано дерево построения отображающее последовательность операций используемых при создании трехмерной модели детали «Корпус редуктора».
Рис. 8 Последовательность создания модели «Корпус редуктора».
Полученная модель может использоваться для получения моделей сборок и рабочих чертежей а также передаваться в расчетные пакеты для математического анализа и расчетов. Для этого имеется возможность сохранения файлов моделей в форматах IGS SAT X_T X_B STP STEP.
Система КОМПАС-3D позволяет производить расчеты геометрических и массо-центровочных характеристик трехмерных объектов а также сохранение результатов в виде текстовых документы и специальных форматов для дальнейшего использования и анализа.
4.Проектирование плана цеха с использованием библиотеки отрисовки планов зданий и сооружений.
Проектирование механических цехов является одной из трудоемких задач технологической подготовки производства. Это обусловлено и наличием довольно объемных расчетов зависящих от количества различных типов оборудования в цехе количества рабочего персонала вспомогательных служб. Не менее сложной является задача выполнения планировки помещений и производственных участков с последующей подготовкой конструкторской и технологической документации. С целью сокращения сроков данного этапа проектирования рационально применение систем автоматизированного проектирования (САПР). В дипломном проекте в соответствии с заданием предложено использование таких типов систем российской фирмы АСКОН а именно программные средства САПР семейства КОМПАС. Система позволяет провести проектирование с использованием соответствующих модулей и библиотек.
Данная библиотека функционирует в среде КОМПАС-ГРАФИК. Она предназначена для выпуска проектной документации при работе с планировками а также для выпуска поэтажных планов используемых в качестве подосновы при проектировании внутренних инженерных сетей (в частности возможна ее совместная работа с Библиотекой проектирования систем вентиляции или Библиотекой элементов электрических схем).
Пользователь Библиотеки оперирует типичными для специализированных архитектурно-строительных САПР инструментами - такими как колонна стена окно дверь лестница и т.д. Имеется возможность создавать одно- и многослойные стены и перекрытия при их сопряжении Библиотека осуществляет пересчет и корректно представляет узлы примыкания.
Созданные пользователем стили элементов ограждающих конструкций (стен перекрытий и т.п.) а также колонн и прямых лестничных маршей могут быть сохранены как в файле проекта так и в библиотеке стилей что позволяет использовать их в других проектах.
Проектировщику будет полезен и бесплатный продукт поставляемый вместе с Библиотекой отрисовки планов зданий и сооружений: Библиотека типовых узлов строительных конструкций реализованная в виде библиотеки фрагментов КОМПАС. Данная библиотека содержит 70 узлов относящихся к различным конструктивным элементам здания.
Типовые узлы в Библиотеке разбиты на следующие категории:
Состав и утепление фундаментов и стен подвала
Сооружение и утепление пола
Сооружение и утепление стены с кирпичной кладкой
Утепление и оборудование деревянных каркасных стен
Сооружение и утепление скатной крыши
Сооружение и утепление совмещенной крыши
Противопожарная защита
Новые технологии утепления
В дипломном проекте библиотека используется для построения сетки колонн в соответствии с расчетами стеновых панелей планировки участков и вспомогательных помещений расположения дверей и окон.
В итоге получается чертеж плана цеха выполненный в соответствии с требованиями ЕСКД.
Так замена станка мод. ГДВ400ПМ1Ф4 применяемый в базовом технологическом процессе многоцелевым горизонтальным сверлильно-фрезерно-расточным станком мод. 2204ВМ1Ф4 позволила сократить затраты на электроэнергию (за счет меньшей мощности двигателя) улучшить условия труда (за счет меньших габаритов) что в конечном итоге привело к снижению затрат.
Для операций 020 и 030 спроектировано производительное и обеспечивающее необходимую точность станочное приспособление внедрение которого сократило штучное время обработки;
В ходе проектирования была предложена конструкция заготовки наиболее приближенной формы к изделию что позволило сократить расход материала.
Таким образом проведенные в данной работе технологические конструкторские операционно-экономические мероприятия позволили поднять производительность и улучшить условия труда повысить уровень автоматизации механизации и общей культуры производства т.е. поставленные цели были достигнуты.
Методические указания к выполнению курсового проекта по технологии машиностроения для студентов специальности 12.01.00. - Белгород: Изд. БелГТАСМ 2002.
Анурьев В.И. Справочник конструктора-машиностроителя в 3-х томах. - М.: Машиностроение 1980
Справочник технолога-машиностроителя «Обработка металлов резанием»под ред. А.А. Панов и др. - М: Машиностроение 1988 г.
Горбацевич А. Ф. Шкред В. А. Курсовое проектирование по технологии машиностроения. Учебник для вузов. - Минск: Вышэйшая школа 1983 г.
Допуски и посадки: Справочник под ред. В.А. Мягков М.А. Полей и др. - М: Машиностроение 1982 г.
Справочник технолога-машиностроителя т.1 Под ред. А. Г. Косиловой и Р. К. Мещерякова. - М.: Машиностроение 1985
Справочник технолога-машиностроителя т.2 Под ред. А. Г. Косиловой и Р. К. Мещерякова. - М.: Машиностроение 1985
Лебедев Л.В. Начало технологического проектирования: Учебное пособие. - Белгород БТИСМ 1992 г.
Лебедев Л.В. Проектирование технологической оснастки. Метод. указан. - Белгород. БТИСМ 1989 г.
Косилова А. Г. Мещеряков Р. К. Калинин М. А. Точность обработки заготовки и припуски в машиностроении: Справочник технолога. - М.: Машиностроение 1976 г.
Общемашиностроительные нормативы режимов резания для технического нормирования работ на металлорежущих станках. - М.: Машиностроение 1975. - Ч.1 2.
Технология машиностроения (специальная часть): Гусев А.А. и др.- M.: Машиностроение 1986г.
Общемашиностроительные нормативы времени и режимов резания для нормирования работ выполняемых на универсальных и многоцелевых станках с числовым программным управлением. – М.: Экономика 1990. – Ч.1 2.
Безопасность жизнедеятельности Под ред. С. В. Белова. - М.: Высш. шк. 2000 г.
Корсаков В. С. Основы конструирования приспособления: Учебник для вузов. - М.: Машиностроение 1983 г.
Ансеров М.А. Приспособления для металлорежущих станков. Л.: Машиностроение 1973 г.
Охрана труда в машиностроении: Учебник для машиностроительных вузов. Под ред. Е. Я. Юдина С. В. Белова. - М.: Машиностроение 1983
Рязанов В. И. Дуганов В. Я. Методические указания по проектированию механосборочных цехов. - Белгород БелГТАСМ
Справочник контролера машиностроительного завода. Допуски посадки линейные измерения Под ред. А. И. Якушева. - М.: Машиностроение 1980 г.
Белкин И. М. Допуски и посадки (Основные нормы взаимозаменяемости): Учебное пособие для студентов машиностроительных специальностей высших технических заведений. - М.: Машиностроение 1992
Егоров М.Е. Основы проектирования машиностроительных заводов: Учебник для машиностроительных ВУЗов – М.: Высшая школа 1969 г.
Дьяков В. И. Типовые расчеты по электрооборудованию: Метод. пособие. - М.: Высш. шк. 1985
Рудычев А. А. Березняков В. А. Кузнецова И. А. Методические указания к выполнению курсовой работы по дисциплине "Организация производства и менеджмента в машиностроении" для студентов специальности 120100 - Технология машиностроения. - Белгород 1999.
Рекомендуемые чертежи
- 24.01.2023