Машина 1A62




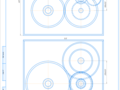
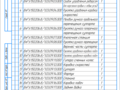
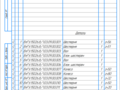
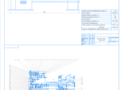
- Добавлен: 25.01.2023
- Размер: 472 KB
- Закачек: 0
Описание
Машина 1A62
Состав проекта
![]() |
![]() |
![]() ![]() ![]() ![]() |
![]() ![]() ![]() |
![]() ![]() ![]() |
![]() ![]() ![]() ![]() |
![]() ![]() ![]() |
![]() ![]() ![]() ![]() |
![]() ![]() ![]() |
![]() ![]() ![]() ![]() |
Дополнительная информация
коробка скоростей 1А62.cdw

Спецификация 1.spw

Коробка 1А62 Свёртка.cdw

Спецификация 2.spw

Лист 1.cdw
