Конструкция редуктора (укр.)




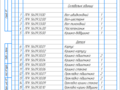
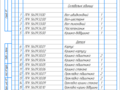
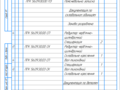
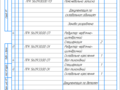
- Добавлен: 24.01.2023
- Размер: 4 MB
- Закачек: 0
Описание
Состав проекта
![]() |
![]() |
![]() |
![]() |
![]() ![]() ![]() |
![]() ![]() ![]() ![]() |
![]() ![]() ![]() ![]() |
![]() ![]() ![]() ![]() |
![]() |
![]() ![]() ![]() ![]() |
![]() ![]() ![]() ![]() |
![]() |
![]() ![]() ![]() |
![]() ![]() ![]() |
![]() ![]() ![]() |
![]() ![]() ![]() |
![]() ![]() ![]() |
![]() ![]() ![]() |
![]() ![]() ![]() |
![]() ![]() ![]() ![]() |
![]() |
![]() ![]() ![]() ![]() |
![]() ![]() ![]() |
![]() |
![]() |
![]() ![]() ![]() |
![]() ![]() ![]() |
![]() ![]() ![]() |
![]() ![]() ![]() |
![]() ![]() ![]() |
![]() ![]() ![]() |
![]() ![]() ![]() ![]() |
![]() ![]() ![]() ![]() |
![]() ![]() ![]() ![]() |
![]() |
![]() ![]() ![]() ![]() |
![]() ![]() ![]() ![]() |
![]() ![]() ![]() ![]() |
![]() |
![]() ![]() ![]() |
![]() |
![]() |
![]() |
![]() |
![]() ![]() ![]() |
![]() |
![]() ![]() ![]() |
![]() |
![]() ![]() ![]() ![]() |
![]() |
![]() ![]() ![]() |
![]() |
![]() |
![]() |
![]() ![]() ![]() ![]() |
![]() |
![]() ![]() ![]() ![]() |
![]() ![]() ![]() ![]() |
![]() |
![]() ![]() ![]() ![]() |
![]() ![]() ![]() ![]() |
![]() ![]() ![]() ![]() |
![]() ![]() ![]() ![]() |
![]() |
![]() ![]() ![]() ![]() |
![]() ![]() ![]() ![]() |
![]() ![]() ![]() ![]() |
![]() ![]() ![]() ![]() |
![]() |
![]() |
![]() ![]() ![]() ![]() |
![]() |
![]() |
![]() ![]() ![]() ![]() |
![]() ![]() ![]() |
![]() ![]() ![]() |
![]() ![]() ![]() |
![]() ![]() ![]() |
![]() ![]() ![]() ![]() |
![]() ![]() ![]() ![]() |
![]() ![]() ![]() ![]() |
![]() ![]() ![]() ![]() |
![]() ![]() ![]() |
![]() ![]() ![]() |
![]() ![]() ![]() |
![]() ![]() ![]() |
![]() ![]() ![]() |
![]() ![]() ![]() |
![]() ![]() ![]() |
![]() ![]() ![]() |
![]() ![]() ![]() |
![]() ![]() ![]() |
![]() ![]() ![]() ![]() |
![]() ![]() ![]() ![]() |
![]() |
![]() |
![]() ![]() ![]() ![]() |
![]() ![]() ![]() |
![]() ![]() ![]() ![]() |
![]() ![]() ![]() ![]() |
![]() ![]() ![]() ![]() |
![]() ![]() ![]() ![]() |
![]() ![]() ![]() ![]() |
![]() |
![]() ![]() ![]() ![]() |
![]() |
![]() ![]() ![]() |
Дополнительная информация
Корпус мой.cdw

Вал- шестерня.cdw

общий Мой.cdw

шестерня Ж.cdw

Коробка моя.cdw

ВАл.cdw

Korobka_skorostei.cdw

КорПУС.cdw

DfVALY.frw

Epiury.frw

КОЛЕСО.cdw

ВАЛ_ШестерняСКЛАД.cdw

Zagalnyi.cdw

ВАЛ МОЙcdw.cdw

rrr.frw

ПГК_56.09.00.00_ЗВcdw.cdw

ПГК_56.09.30.00_СК.cdw

ПГК_56.09.30.00_СП_1.cdw

ПГК_56.09.30.03_СП.cdw

ПГК_56.09.00.00_ПЗ.cdw

ПГК_56.09.30.00_СП_1.cdw

ПГК_56.09.00.00_ПЗ.cdw

ПГК_56.09.30.03_СП.cdw

ПГК_56.09.30.02.cdw

ПГК_56.09.30.01.cdw

ПГК_56.09.30.03_СК.cdw

ПГК_56.09.00.06.cdw

корпус.cdw

Вал- шестерня.cdw

шестерня.cdw

общий.cdw

545.frw

Фрагмент.frw

2626.frw

5.frw

12.frw

Фрагмент1.frw

ВАл.cdw

коробка.cdw

Коробка.cdw

Движок.cdw

Вал-шестерня.cdw

шестерня.cdw

Корпус.cdw

общий.cdw

Вал.cdw

Рекомендуемые чертежи
- 24.01.2023
- 24.01.2023
- 24.01.2023
- 20.08.2014
- 03.05.2023