Кинематический анализ радиально сверлильного станка с проектированием режущего инструмента





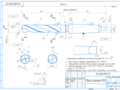
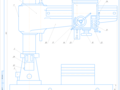
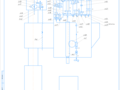
- Добавлен: 25.01.2023
- Размер: 1 MB
- Закачек: 0
Описание
Состав проекта
![]() |
![]() |
![]() ![]() ![]() |
![]() ![]() ![]() |
![]() ![]() ![]() |
![]() ![]() ![]() |
![]() ![]() ![]() |
![]() ![]() ![]() |
![]() ![]() ![]() |
![]() ![]() ![]() |
![]() ![]() ![]() |
![]() ![]() ![]() |
![]() |
![]() ![]() ![]() ![]() |
![]() ![]() ![]() ![]() |
![]() ![]() ![]() ![]() |
![]() ![]() ![]() ![]() |
Дополнительная информация
Введение.docx
Станок — машина для обработки различных материалов. Металлорежущий станок — машина предназначенная для обработки металлических материалов резанием. Основная классификация металлорежущих станков построена по технологическим признакам. В каждую из девяти групп внесены станки по определенному характерному признаку. Сверлильные и расточные станки по классификатору относятся ко второй группе внутри которой их делят на следующие типы: 1 – вертикально-сверлильные станки; 2 – одношпиндельные полуавтоматы; 3 – многошпиндельные полуавтоматы; 4 – координатно-расточные станки; 5 – радиально-сверлильные станки; 6 – горизонтально-расточные; 7 – алмазно-расточные; 8 – горизонтально-сверлильные станки; 9 – разные сверлильные.
Модели станков обозначают буквами и цифрами. Использование классификации позволяет записать модель станка в виде определенного набора цифр и букв. Первая цифра обозначает номер группы вторая — тип последующие одна или две цифры характеризуют какой-либо отличительный параметр. Буква стоящая после первой цифры указывает на модернизацию основной базовой модели станка а буквы в конце — определяют модификацию (класс точности систему управления и др.). В станках с программным управлением в обозначение вводят индексы Ц Т Ф1 Ф4 которые обозначают что этот станок с цикловой (Ц) или оперативной (Т) системами с цикловой индексацией и преднабором координат (Ф1) с позиционной и прямоугольной (Ф2) контурной (ФЗ) и универсальной (Ф4) системами. Иногда станкостроительные заводы отступают от этой классификации но каждому заводу присвоен свой индекс из одной или двух букв после которого проставляется порядковый номер модели станка.
Сверлильные станки предназначены для сверления отверстий нарезания в них резьбы метчиком растачивания и притирки отверстий вырезания дисков из листового материала и т. д. Эти операции выполняют сверлами зенкерами развертками и другими подобными инструментами.
6.docx
Радиально-сверлильный станок модели 2М55 предназначен для широкого применения в промышленности.
Благодаря своей универсальности станок находит применение везде где требуется обработка отверстий - от ремонтного цеха до крупносерийного производства.
На станке можно производить сверление в сплошном материале рассверливание зенкерование развёртывание подрезку торцов нарезку резьбы метчиками и другие подобные операции.
Применение приспособлений и специального инструмента значительно повышает производительность станка и расширяет круг возможных операций позволяя производить на нем выточку внутренних канавок вырезку круглых пластин из листа и т.д. При соответствующей оснастке на станке 2М55 можно производить большинство операций характерных для расточных станков.
Станок имеет двухколонную компоновку станочной части что позволяет создать жесткую конструкцию узла не допускающую смещение оси шпинделя при зажиме колонны. Специальный зажим колонны центрального типа создает тормозной момент гарантирующий высокопроизводительное сверление. Для поворота колонны требуется незначительное усилие на самом малом радиусе сверления что также обеспечивает высокую производительность работы и снижает утомляемость оператора. Широкий диапазон чисел оборотов и подач шпинделя обеспечивает высокопроизводительную работу при любых сочетаниях обрабатываемых материалов инструмента размера и т.д. Преселективное дистанционное электрогидравлическое устройство позволяет менять режимы с предварительным их набором. Станок имеет механизм автоматического выключения при достижении заданной глубины сверления. Уравновешивание шпинделя обеспечивается специальным противовесом допускающим удобную регулировку с рабочего места в случае изменения массы инструмента.
Спецификация Лист 2.doc
Механизм включения подач
Механизм ручного перемещения головки
Привод гидропреселектора
2,Расчет базовых элементов станка!.docx
Металлорежущие станки должны обеспечивать возможность высокопроизводительного изготовления без последующей ручной доводки деталей удовлетворяющих современным непрерывно возрастающим требованиям к точности. Поэтому проектирование станков и их наиболее ответственных деталей и механизмов в частности деталей несущей системы в значительной
степени подчиняется критерию точности. К этому критерию относятся: точность изготовления сохранение точности в работе (обеспечиваемое малостью приведенных упругих температурных деформаций и амплитуд колебаний) и сохранение точности за установленные межремонтные периоды (обеспечиваемое малым износом и короблением от остаточных напряжений).
Несущая система станка образуется совокупностью элементов станка через которые замыкаются силы возникающие между инструментом и заготовкой в процессе резания. К элементам несущей системы рассматриваемым в
настоящем учебном пособии относятся станины и корпусные детали станков.
Несущие системы станков должны обеспечивать и сохранять в течение
срока службы станка возможность обработки с заданными режимами и
требуемой точностью. Исходя из этого основными критериями работоспо-
собности несущей системы являются жесткость а также виброустойчивость в смысле обеспечения возможности устойчивой работы станка при заданных
режимах и ограничения уровня амплитуд вынужденных колебаний
допустимыми пределами.
1 Обоснование вида направляющих станка и выбор материала
В станке применяют направляющие скольжения из серого чугуна выполненные как одно целое с базовой деталью наиболее просты но при интенсивной работе не обеспечивают необходимой долговечности. Их износостойкость повышают закалкой с нагревом токами высокой частоты или газопламенным методом. Закалкой одной из сопряженных поверхностей до HRCa 48—53 можно повысить износостойкость более чем в 2 раза. Легирующие присадки к чугунным направляющим дают повышение износостойкости только при последующей закалке. Значительного повышения износостойкости чугунных направляющих можно добиться применением специальных покрытий. Хромирование направляющих слоем толщиной 25—50 мкм обеспечивает твердость до HRC9 68—72 в 4—5 раз повышает износостойкость и существенно уменьшает коэффициенты трения покоя и трения движения.
По форме поперечного сечения трапециевидные (типа ласточкина хвоста) направляющие.
2 Обоснование конструкции основных базовых элементов и выбор материала.
Фундаментальная плита выполнена из железобетона. Обеспечивая такую же жесткость как и чугунная плита железобетон дает экономию металла примерно на 40—60 %.
Форма сечений вертикальных станин (стоек) если необходимо обеспечить поворот узлов относительно оси стойки вбирают круглой. Материал стойки
СЧ 15. Он обладает хорошими литейными свойствами мало коробится но имеет сравнительно низкие механические свойства.
Траверса выполнена за одно целое вместе с направляющими. Поэтому что бы обеспечить нужные свойства направляющих материал СЧ20.
Спецификация Лист 2(продолжение).doc
Электрооборудование рукава
Электрооборудование головки
7.docx
1 Назначение режущего инструмента
Сверление зенкерование и развертывание являются основными технологическими способами обработки резанием круглых отверстий различной степени точности и с различной шероховатостью обработанной поверхности. Все перечисленные способы относятся к осевой обработке т.е. к лезвийной обработке с вращательным главным движением резания при постоянном радиусе его траектории и движении подачи только вдоль оси главного движения резания.
Сверление — основной способ обработки отверстий в сплошном материале заготовок. Просверленные отверстия как правило не имеют абсолютно правильной цилиндрической формы. Их поперечное сечение имеет форму овала а продольное — небольшую конусность. Диаметры просверленных отверстий всегда больше диаметра сверла которым они обработаны. Разность диаметров сверла и просверленного им отверстия называют разбивкой отверстия. Для стандартных сверл диаметром 10 20 мм разбивка составляет 015 025 мм. Причиной разбивки отверстий являются недостаточная точность заточки сверл и несоосность сверла и шпинделя сверлильного станка.
Сверление отверстий без дальнейшей их обработки проводят тогда когда необходимая точность размеров лежит в пределах 12 14-го квалитетов. Наиболее часто сверлением обрабатывают отверстия для болтовых соединений а также отверстия для нарезания в них внутренней крепежной резьбы (например метчиком).
Зенкерование — это обработка предварительно просверленных отверстий или отверстий изготовленных литьем и штамповкой с целью получения более точных по форме и диаметру чем при сверлении. Точность обработки цилиндрического отверстия после зенкерования — 10 11-й квалитеты.
Развертывание — это завершающая обработка просверленных и зенкерованных отверстий для получения точных по форме и диаметру цилиндрических отверстий (6 9-й квалитеты) с малой шероховатостью Ra 032 125 мкм.
Сверла предназначаются для сверления сквозных или глухих отверстий в деталях обрабатываемых на сверлильных токарно-револьверных и некоторых других станках. В зависимости от конструкции и назначения различают следующие сверла:
Спиральные с цилиндрическим и коническим хвостовиками предназначенные для сверления стали чугуна и других конструкционных материалов;
Оснащенные пластинками из твердых сплавов предназначенные для обработки деталей из чугуна (особенно с литейной коркой) и очень твердой и закаленной стали;
Глубокого сверления (одно- и двустороннего резания) используемые при сверлении отверстий длина которых превышает диаметр в пять раз и более;
Центровочный инструмент (центровочные сверла и зенковки) предназначенный для обработки центровых отверстий обрабатываемых деталей.
Зенкеры предназначены для обработки литых штампованных и предварительно просверленных цилиндрических отверстий с целью улучшения чистоты поверхности и повышения их точности или для подготовки их к дальнейшему развертыванию.
Зенкеры применяют для окончательной обработки отверстий с допуском по 11 12-му квалитетам и обеспечивают параметр шероховатости Rz 20 40 мкм.
Конструктивно зенкеры выполняют хвостовыми цельными хвостовыми сборными с вставными ножами насадными цельными и насадными сборными. Зенкеры изготовляют из быстрорежущей стали или с пластинами твердого сплава напаиваемыми на корпус зенкера или корпус ножей у сборных конструкций. Хвостовые зенкеры (подобно сверлам) крепят с помощью цилиндрических или конических хвостовиков насадные зенкеры имеют коническое посадочное отверстие (конусность 1:30) и торцовую шпонку для предохранения от провертывания при работе.
Развертка — осевой режущий инструмент — предназначена для предварительной и окончательной обработки отверстий с точностью соответствующей 6 11-му квалитетам и шероховатостью поверхности Ra 25 032 мкм.
Развертки подразделяются:
По типу обрабатываемых поверхностей — на цилиндрические и конические;
Способу применения — на ручные и машинные;
Методу крепления на станке — на хвостовые и насадные;
Инструментальному материалу режущей части — на быстрорежущие и оснащенные твердым сплавом;
Конструктивным признакам — на цельные изготовленные из одного инструментального материала; составные неразъемные со сварными хвостовиками; составные неразъемные с припаянными пластинками из твердого сплава и составные разъемные с вставными ножами.
2 Технические требования предъявляемые к инструменту.
Технические требования к осевому режущему инструменту указаны в ГОСТах для каждого инструмента отдельно.
3 Элементы конструкции и геометрические параметры инструмента.
Спиральное сверло (рис.3) состоит из рабочей части включающей режущую часть шейки конического (рис.3 а) или цилиндрического (рис.3 б) хвостовика для крепления сверла в шпинделе станка лапки служащей упором для выбивания сверла из гнезда шпинделя. Режущая часть (рис.3 в) состоит из двух зубьев образованных двумя канавками для отвода стружки; сердцевины— срединной части сверла соединяющей оба зубца; двух передних поверхностей по которым сбегает стружка и которые воспринимают силу резания; двух ленточек — узких полосок по наружному диаметру сверла служащих для его направления и центрирования в отверстии; двух главных режущих лезвий образованных пересечением передних и задних поверхностей и выполняющих основную работу резания; поперечного лезвия или перемычки образованной пересечением обеих задних поверхностей.
Рисунок 3-Элементы геометрические параметры и заточка спиральных сверл: 1 и 10 — лезвия ленточки; 2 и 6 — ленточки; 3 — два режущих лезвия; 4 и 8 — спинки у зубцов; 5 — канавки; 7 — поперечное лезвие; 9 — передняя поверхность.
4 Расчет геометрических параметров инструмента.
Выберем сверло с диаметром 26 с коническим хвостовиком по ГОСТ 10903-77. Основные размеры :
Длина рабочей части мм 130
В ходе выполнения курсового проекта был произведено ознакомление с технологическими возможностями станка устройством и принципом действия станка его кинематической схемой. В ходе курсового проектирования был произведён кинематический расчёт радиально-сверлильного станка модели 2М55 знаменателя геометрического ряда частот расчёт частот каждой ступени построен график частот вращения. Также было произведено ознакомление с правилами эксплуатации и технического обслуживания станка и требованиями безопасности при работе не нём.
При выполнении курсового проекта были использованы знания о кинематике станков построении структурных сеток станков расчёте знаменателя геометрического ряда частот и расчёте частот вращения каждой ступени. При выполнении курсового проекта использовались ГОСТы нормативные документы и справочная литература. А также для разработки чертежей использовалась такая программа как kompas V10.
Глубокий В.И. Металлорежущие станки и промышленные роботы. Ч. 1. Конструирование металлорежущих станков. – Мн. 1988.
Жданович В.В. Техническая эксплуатация технологического оборудования: курсовое и дипломное проектирование В.В. Жданович.- Мн.: «Беларусь» 2006- 278с.:ил.
Локтева С. Е. Станки с программным управлением: Учебн. Пособие для машиностроительных техникумов. – М.: Машиностроение 1979.- 288 с.ил.
Паспорт станка 2М55-Одесса1976.-56 ст.
Чернов Н.Н. Металлорежущие станки: Учебник для машиностроительных техникумов.-3-е изд. перераб. и доп.- М.: «Машиностроение»1978-389 с. ил.
Черпаков Б. И. Альперович Т. А. «Металлорежущие станки» Москва ACADEMIA 2004 г.
ГОСТ 12.1.030-81. Система стандартов безопасности труда. Электробезопасность. Защитное заземление зануление. – Москва: Госстандарт: Межгос. совет по стандартизации метрологии и сертификации 1982.
ГОСТ 12.2.009-99. Система стандартов безопасности труда. Станки металлообрабатывающие. Общие требования безопасности. – Минск: БелГИСС: Межгос. совет по стандартизации метрологии и сертификации 1999.
содержание.docx
1Анализ конструкции современных металлорежущих станков 9
2Назначение и принцип работы станка .10
3Технические характеристики станка 11
4Основные узлы станка 12
5Органы управления станком .13
7Конструктивные особенности станка 14
Расчет базовых элементов станка 17
1Обоснование вида направляющих станка и выбора материала 17
2Обоснование конструкции основных базовых элементов выбор материала ..18
Кинематический анализ станка 19
1Описание кинематической схемы станка 19
1.1Движение резания 19
1.2Движение подачи 19
1.3Вспомогательное движение 20
1.4Кинематический расчет и построение графика частот вращения..20
Указания по эксплуатации и обслуживанию станка 23
Требования техники безопасности и экологии при работе на станке.27
Обоснование экономической эффективности станка 31
Режущий инструмент 32
1Назначение режущего инструмента .32
2Технические требования предъявляемые к инструменту .34
3Элементы конструкции и геометрические параметры инструмента 34
4Расчет геометрических параметров инструмента 35
пункт 4 5!!!.docx
Общие требования безопасности установлены ГОСТ 12.3.002 –75 и включат: устранение непосредственного контакта работающих с исходными материалами заготовками полуфабрикатами готовой продукцией и отходами производства оказывающими вредное действие; замену технологических процессов и операций связанных с возникновением опасных и внедрение производственных факторов процессами и операциями при которых указанные факторы отсутствуют или обладают меньшей интенсивностью; комплексную механизацию и автоматизацию производства; применение дистанционного управления технологического процессами и операциями при наличии опасных и вредных производственных факторов; герметизацию оборудования; применение средств коллективной защиты работающих; рациональную организацию труда и отдыха с целью профилактики монотонности и гиподинамии а также ограничение тяжести труда;
Кроме того безопасность производственных процессов во многом зависит от их организации рациональности планировки цехов и участков и правильности организации рабочих мест выполнения требований безопасности к производственным помещениям хранению транспортированию складированию исходных материалов заготовок и готовой продукции а также к удалению отходов и их утилизации и наконец выполнения требований безопасности предъявляемых к производственному персоналу.
Общие требования безопасности на металлорежущих станках определены ГОСТ 12.3.025 – 80 в соответствии с которым установка обрабатываемых заготовок и снятие готовых деталей во время работы оборудования допускается вне зоны обработки при применении специальных позиционных приспособлений обеспечивающих безопасность работы.
Общие требования техники безопасности к станку:
1 Защитные устройства:
- Ременные передачи расположенные вне корпусов станков и представляющие опасность травмирования должны иметь ограничения для удобства и безопасного открывания при помощи устройств.
- Выступающие при работе за габарит станка внешние торцы сборочных единиц должны окрашиваться под углом 45º чередующимися полосами жёлтого и чёрного цвета.
- Защитные устройства ограждающие зону обработки должны защищать работающего на станке и людей находящихся вблизи станка от отлетающей стружки и СОЖ.
- Защитные устройства не должны вызывать неудобства при работе.
- Поверхность стола защитных устройств станочных принадлежностей и приспособлений не должны иметь острых кромок и заусенцев.
2 Предохранительные и блокирующие устройства:
- Станок должен иметь переходные устройства предотвращающие самопроизвольное опускание шпинделей бабок поперечин.
- Станок должен иметь предохранительные устройства от перегрузки.
- Перемещение сборочных единиц станка должно в крайних положениях ограничиваться устройствами исключающими перебеги за допустимые размеры.
- Устройства закрепления на станке патронов оправок и других съёмных элементов должны исключать самопроизвольное ослабление при работе закрепляемых устройств и сдвигании съёмных элементов при реверсировании вращения.
- В станках имеющих реверсивные приводы главного движения и механизированные подачи должна предусматриваться блокировка
обеспечивающая выключение главного движения не раньше выключения подачи.
3. Органы управления:
- Органы ручного управления должны быть выполнены и расположены так чтобы их использование было удобно и безопасно.
- Рукоятки и другие органы управления станком должны быть снабжены фиксаторами не допускающими самопроизвольных перемещений органов управления.
- Перемещение рукояток при отжиме и зажиме не должны быть направлены в стороны режущего инструмента.
- Расположенное и конструкция органов управления должны исключить задерживание на них стружки.
4 Смазка охлаждение отвод стружки:
- Форма станка и его элементов должны обеспечивать удобный отвод стружки и СОЖ из зоны обработки и удаление стружки со станка.
- Станки следует оборудовать централизованной системой смазки.
- В резервуарах смазочной системы устанавливаемых около станков и расположенных в основании станины должны быть предусмотрены отверстия для откачивания масла насосом.
- Устройства для ввода СОЖ в зону обработки должны обеспечивать возможность удобного и безопасного регулирования их положения надёжной фиксации и необходимость распределения жидкости в зоне резанья.
Электрооборудование защитные меры:
- Каждый станок должен иметь вводный выключатель ручного действия размещённый в безопасном месте.
- На шкафах нишах которые недостаточно ясно показывают что содержат электрическую аппаратуру должны быть помещены предупреждающие знаки электрического напряжения по ГОСТ 12.4.026 – 76.
- Остаточное напряжение у электрического оборудования недопустимо.
- Каждый станок должен иметь орган аварийного отключения красного цвета.
- Металлические части электрических аппаратов с ручным приводом должны быть надёжно соединены с защитной цепью.
- Электрооборудование должно быть защищено нулевой защитой исключающей самопроизвольное включение станка.
- Все металлические части должны быть оснащены легко обозримыми устройствами заземления вблизи от места ввода питающих приводов.
Требования техники безопасности и экологии при работе на станке
Общие и специальные требования по технике безопасности:
Обязанности станочника при работе на станке:
- Перед началом работы убедиться что пуск станка никому не угрожает опасностью.
- Привести в порядок рабочую одежду надеть головной убор.
- Приняв станок убедиться хорошо ли он убран и убрано ли рабочее место.
- О неисправности станка заявить мастеру до устранения неисправности к работе не приступать.
- Приготовить ключи и другие необходимые инструменты не применять крючок с ручкой в виде петли.
Проверить наличие и исправность:
- Ограждений зубчатых колёс валиков приводов а так же токоведущих частей электрической аппаратуры.
1Заземляющих устройств:
- Предохранительных устройств для защиты от стружки СОЖ.
- Устройств для коррекции инструмента.
- Режущего измерительного крепёжного инструмента и приспособлений и разложить их в удобном для использования порядке.
- Если при обработке металла образуется отлетающая стружка то при отсутствии специальных защитных устройств на станке надеть защитные очки.
- Проверить на холостом ходу станок.
- Исправность органов управления.
- Исправность системы смазки и охлаждения.
- Исправность рычагов включения и выключения.
- Для предупреждения кожных заболеваний рук при применении на станках охлаждающих масел и жидкостей перед началом работы смазывать руки специальными пастами и мазями.
- Проверять доброкачественность ручного инструмента при получении его из кладовой.
- Ручка напильника и шабера должна иметь металлическое кольцо предохраняющее его от раскалывания.
- Зубило и другой ударный инструмент должны быть длинной не менее 150 мм кернер – 100 мм не иметь наклёпа на бок.
- Пользоваться режущим инструментом имеющим правильную заточку. Применение неисправного инструмента и приспособлений не допускается.
- Проверить и обеспечить достаточную смазку станка при смазке использовать только соответствующие приспособления.
- Запрещается охлаждать режущий инструмент мокрыми тряпками или щётками.
- Не допускать разбрызгивание масла и жидкости на пол.
- Устанавливать между стенками защитные шиты.
2 Обязанности станочников во время работы:
- Выполнять указания по обслуживанию и уходу за станком изложенные в «Руководстве по станку» а так же требования предупредительных таблиц имеющихся на станке.
- Устанавливать и снимать режущий инструмент только после полного останова станка.
- Не удалять стружку от станка непосредственно руками или инструментом.
- При установке пил для исключения порезов необходимо проявлять максимальную осторожность.
- При установке детали на станок нельзя находиться между деталью и станком.
- При отрезании тяжёлых частей детали или заготовки нельзя придерживать
отрезаемый конец руками.
- Остерегаться заусенцев на обрабатываемых деталях.
3 Обязательно остановить станок и выключить электродвигатель при:
- Уходе от станка даже на короткое время.
- Временном прекращении работы.
- Перерыве подачи электроэнергии.
- Уборке смазке чистке станка.
- Обнаружении неисправности в оборудовании.
- Установке изменении и съёме детали.
При обработке деталей применять режимы резанья указанные в операционной карте для данной детали.
Не превышать установочные режимы резанья без ведома мастера.
Обязанности станочника по окончанию работы:
- Привести в порядок рабочее место убрать со станка стружку инструмент приспособление очистить станок от грязи вытереть и смазать трущиеся части станка аккуратно сложить готовые детали и заготовки.
- Убрать инструмент в отведённые для этого места.
- После окончания работы на станке доложить мастеру о замеченных недостатках имевших место во время работы.
- О всякой замеченной опасности заявить мастеру производственного обучения.
- Вымыть руки тёплой водой принять душ.
Стружку от металлорежущих станков следует убирать только при помощи специальных механизированных средств. Вводной выключатель под нагрузкой не
выключать. Это допустимо только в аварийных случаях. При осмотре или ремонте электроаппаратуры вводной выключатель выключить. Менять скорость и инструмент только при остановке шпинделя. Не использовать инструменты с забитыми и изношенными хвостовиками. Обрабатываемые детали надежно закреплять в приспособлении или на столе станка.
Каждый работник предприятия ответственен за воздействие которое он оказывает на природную среду в результате производственной деятельности. Неотъемлемым условием экологической безопасности является охрана окружающей среды. Воздействие человека на окружающую среду осуществляется следующим образом:
- истощение природных ресурсов в ходе их потребления и преобразования;
- загрязнение окружающей среды отходами производства и потребления.
В результате производственной деятельности оказывается воздействие на:
- истощение природных ресурсов в процессе использования электроэнергии питьевой и технической воды атмосферного воздуха сырья материалов;
- загрязнение вод промышленными сточными водами образующимися в процессе производства в том числе сточными водами содержащими нефтепродукты захоронением опасных отходов производства;
- загрязнение атмосферы от стационарных и передвижных источников вызывая парниковый эффект «кислотные» осадки разрушение озонового слоя оказывая токсическое раздражающее и шумовое воздействие на человека;
- загрязнение почв при обращении с твердыми отходами производства и потребления.
Для сокращения негативного воздействия на окружающую среду организация производства осуществляется на принципах неукоснительного соблюдения законодательных и нормативных требований в области природопользования. На предприятии внедряются природоохранные и экологически безопасные технологические процессы обеспечивающие сохранность и стабильность окружающей среды.
Предотвращение истощения природных ресурсов достигается внедре-
нием энерго- и ресурсосберегающих технологий и оборудования использованием технической воды на технологические нужды систем оборотного водоснабжения учетом всех видов потребляемых предприятием энергоресурсов.
Предотвращение загрязнения атмосферы достигается функционирующим газо-пылеулавливающими установками выполнением законодательных требований в области обращения с озоноразрушающими веществами использованием ограниченного количества фреона оказывающее минимальное воздействие на озоновый слой.
Предотвращение загрязнения почв достигается системой управления процессом обращения с отходами производства и потребления отсутствием мест захоронения отходов производства на территории предприятия утилизацией отходов.
Требования к персоналу в области охраны окружающей среды:
- тщательно осматривать перед началом работ свое рабочее место проверять исправность оборудования систем вентиляции и освещения защитных приспособлений коммуникаций и других средств охраны окружающей среды и производственной санитарии в случае обнаружения нарушений сообщить мастеру;
- эксплуатировать оборудование сооружения коммуникации технические средства защиты в соответствии с технологическими инструкциями и инструкциями по эксплуатации оборудования;
- соблюдать графики остановки чистки ремонта осмотра оборудования очистных установок и коммуникаций;
- докладывать немедленно при обнаружении аварийных сбросов выбросов загрязняющих веществ мастеру и руководствоваться планом ликвидации аварий;
- соблюдать порядок обращения с отходами производства и потребления в соответствии с технологическими документами.
Нарушения требований охраны окружающей среды которые влекут административное и материальное воздействие:
- виновность в выбросе (сбросе) загрязняющих веществ в окружающую среду или несвоевременное принятие мер по этому факту;
- загрязнение и захламление рабочих мест и территории закрепленной за подразделением;
- выполнение технологического процесса при неисправной или не включенной в работу газо-пылеулавливающей установке;
- сжигание отходов производства на территории предприятия;
- эксплуатация автотранспорта с работающим двигателем на территории предприятия и в закрытом помещении необорудованном вытяжной вентиляцией или отсосом от выхлопной трубы;
- хранение кислот едких жидкостей продуктов нефтепереработки в открытых емкостях;
- нерациональное использование или перерасход питьевой технической воды;
- превышение предельно-допустимых концентраций загрязняющих веществ в сточных водах;
- техническая неисправность или не использование оборудования для химической и механической очистки сточных вод;
- мойка и ремонт автотранспорта в не предназначенных для этого местах;
- утечка рабочих растворов вредных веществ из емкостей хранения;
- сброс в системы водоотведения и на землю ГСМ химических растворов эмульсий и других веществ;
- нарушение инструкции «О порядке сбора учета хранения и сдачи на утилизацию ртутьсодержащих люминесцентных ламп»;
- несвоевременный вывоз (вынос) отходов производства от рабочих мест и из цеха;
- складирование хранение захоронение отходов производства и потребления в не предназначенных для этого местах;
- загрязнение захламление земельных участков территории цеха подъездных дорог в том числе отходами производства;
- уничтожение или повреждение зеленых насаждений на территории предприятия и в пределах санитарно-защитной зоны;
- несоблюдение правил производственной санитарии;
- преднамеренное применение неправильных приемов работы в период проведения исследования воздуха рабочей зоны.
общие сведение о мрс.docx
Металлорежущие станки обеспечивают изготовление деталей разнообразной формы с высокой точностью размеров и заданной шероховатостью поверхности. Металлорежущие станки классифицируются по следующим признакам.
По степени специализации: 1—универсальные применяемые для обработки деталей широкой номенклатуры; 2 — специализированные предназначенные для обработки однотипных деталей сходных по конфигурации но имеющие различные размеры; 3 — специальные применяемые для обработки деталей одного типоразмера. Специализированные и специальные станки используют в крупносерийном и массовом производстве а универсальные — в единичном и мелкосерийном производстве.
По точности: нормальной точности — класс Н; повышенной точности — класс П; высокой точности — класс В; особо высокой точности — класс А; прецизионные — класс С.
По массе: легкие — до 1 т средние — до 10 т тяжелые — свыше 10 т. Тяжелые станки в свою очередь делятся на крупные (от 10 до 30 т) тяжелые (от 30 до 100 т) и особо тяжелые (более 100 т).
По виду выполняемых работ и применяемых режущих инструментов все выпускаемые станки согласно классификации делят на девять групп каждая группа разделена на десять типов станков.
Обозначение модели серийно выпускаемых станков состоит из сочетания трех или четырех цифр иногда с добавлением букв. Первая цифра обозначает номер группы по классификационной таблице вторая указывает тип станка. Третья а иногда и четвертая цифра характеризуют параметры станка которые различны для разных групп станков. Буквы указывают на модернизацию или модификацию основной базовой модели станка.
В моделях станков с программным управлением для обозначения степени автоматизации добавляется буква «Ф» с цифрой: Ф1—станки с цифровой индикацией и преднабором координат; Ф2 — станки с позиционными и прямоугольными системами; ФЗ — станки с контурными системами; Ф4 — станки с универсальной системой для позиционной и контурной обработки. Для станков с цикловыми системами программного управления введен индекс Ц.
1Анализ конструкции современных металлорежущих станков аналогичных проектируемому.
Радиально-сверлильные станки ОС4061А и 2А554 предназначены для обработки отверстий преимущественно в крупногабаритных деталях из чугуна сталей и различных сплавов. При обычной компоновке узлов присущих этому типу станков возможно сверление рассверливание зенкерование и нарезание резьбы метчиками. Гильза шпинделя радиально-сверлильных станков имеет механическую подачу остальные позиционирующие движения выполняются с минимальным усилием и в рабочем положении фиксируются гидрозажимами. Сверлильная головка станка на которой расположены все органы управления станком - уравновешена в любой точке горизонтального перемещения. Быстрое изменение режимов резания обеспечивается гидравлическим управлением предварительно выбранных оборотов и подач шпинделя. Конструкция коробки скоростей позволяет осуществлять быстрый реверс оборотов шпинделя станка при нарезке резьбы метчиками выключать механическую подачу при достижении предварительно заданной глубина обработки а также предохраняет узлы и механизмы радиально-сверлильного станка от перегрузок
2Назначение и принцип работы станка
Станок предназначен для сверления зенкерования развертывания нарезания резьбы метчиками и так далее в крупных деталях а при наличии специальных приспособлений — и для операций характерных для расточных станков. На базе станка выпускают станок с ЧПУ 2М55Ф2.
Заготовку закрепляют на фундаментной плите 1 (рисунок 2) или приставном столе 2. В цоколе плиты смонтирована вращающаяся колонна 3 на которой размещен рукав 4 перемещающийся по колонне от механизма подъема 5. Сверлильная головка 6 включающая коробку скоростей и подач перемещается по рукаву вручную. Инструмент можно установить относительно детали поворотом рукава и перемещением по нему сверлильной головки.
Станок имеет преселективное управление переключениями частот вращения и подач.
Фундаментная плита является базовым элементом станка на котором крепятся остальные компоненты и механизмы. Колонна предназначена для крепления рукава который вращается и перемещается по колонне в вертикальном направлении. Рукав предназначен для крепления сверлильной головки с коробкой скоростей и коробкой подач. Коробка подач обеспечивает получение рабочих подач и быстрых перемещений сверлильной головки.
Рисунок 1 – Компоновочная схема радиально- сверлильного станка
3Технические характеристики станка
Класс точности Н по ГОСТ 8-71. Наибольший условный диаметр сверления
(в стали марки 45 по ГОСТ 1050-60) мм 50
Вылет шпинделя от образующей колонны мм
Расстояние от торца шпинделя до плиты мм:
Количество ступеней скоростей шпинделя 21
Пределы скоростей шпинделя обмин от 20 до 2000
Количество ступеней механических подач шпинделя 12
Пределы подач шпинделя ммоб от 0056 до 25
Наибольшая эффективная мощность на шпинделе кВт 40
Наибольший крутящий момент на шпинделе кгссм 7100
Наибольшее усилие подачи кгс 2000
Масса станка кг 4700
4Основные узлы станка
Рисунок 2- Радиально-сверлильный станок 2М55
- фундаментальная плита; 2 – поворотная наружная колонна; 3 – механизм перемещения и зажима траверсы; 4 – траверса; 5 – шпиндельная головка; 6 – приставной стол.
5Органы управления станком
Все органы управления сосредоточены на панели управления сверлильной головки. Предварительный набор частоты вращения и подачи шпинделя а также гидравлическое управление коробками скоростей и подач обеспечивает быстрое изменение режимов.
Фрикционная муфта встроенная в коробку скоростей обеспечивает быстрый реверс при нарезке резьбы и предохраняет коробку скоростей от перегрузок. Шпиндель станка уравновешен в любой точке его перемещения. Штурвальное устройство управления сверлильной головкой имеет возможность выключения механической подачи при достижении заданной глубины сверления.
Реверсирование вращения шпинделя осуществляется переключением двусторонней фрикционной муфтой. Муфта является предохранительной она срабатывает при перегрузке а также отключается при достижении заданной глубины сверления.
Гильза со шпинделем уравновешивается спиральными пружинами которые регулируются вручную рукояткой через червячную передачу. Быстрое перемещение невращающегося шпинделя можно осуществлять от электродвигателя. Тонкую ручную подачу шпинделя можно осуществлять маховичком. Штурвал служит для быстрого ручного перемещения или грубой подачи шпинделя а также для включения и выключения механической подачи.
Перемещение сверлильной головки вдоль траверсы может осуществляться вручную маховичком или от гидромотора.
Вертикальное перемещение траверсы осуществляется от электромотора.. Зажим сверлильной головки на траверсе и траверсы на гильзе осуществляется гидроцилиндрами через рычажные механизмы. Зажим гильзы на колонне осуществляется плунжером-рейкой и передачей винт – гайка.
6Виды движений в станке
Главным движением в радиально-сверлильных станках является вращение шпинделя а движением подачи – осевое перемещение шпинделя вместе с пинолью (гильзой). К вспомогательном движениям относятся: поворот траверсы вместе с поворотной наружной колонной и последующее закрепление на неподвижной внутренней колонне вертикальное перемещение по наружной колонне и закрепление шпиндельной головки на траверсе переключение скоростей и подач шпинделя и т.д.
Горизонтальное перемещение шпиндельной головки по траверсе вручную производят с помощью маховичка и реечной передачи. Механическое вертикальное перемещение траверсы по поворотной колонне осуществляется отдельным электродвигателем. Закрепление траверсы по окончании перемещения а также освобождение траверсы по окончании перемещения происходит автоматически.
Закрепление поворотной наружной колонны на неподвижной внутренней а также закрепление шпиндельной головки на направляющих траверсы происходит с помощью гидромеханизмов управляемых кнопками. Нажим на одну кнопку вызывает закрепление колонны и головки нажим на другую – их освобождение. Сила закрепления регулируется продолжительностью нажима на кнопку. Траверсу с полой колонной поворачивают вручную.
7Конструктивные особенности станка
Станок 2М55 в своей конструкции имеет двухколонную основу станочной части это позволяет создать прочную устойчивую конструкцию узла использование которой не допускает смещение оси шпинделя в случае зажима одной колонны. Дополнительный зажимающий элемент колонны создает тормозящий эффект обеспечивающий высокоточное сверление отверстий. Да разворота колонны необходимо прилагать небольшие усилия на меньшем радиусе сверления это позволяет снизить утомляемость рабочего-оператора а так же повысить производительность операций выполняемых на 2М55. Большой диапазон чисел оборотов и подач шпинделя станка 2М55 позволяет выполнять высокоточную работу при использовании любых инструментов на любой заготовке и с любыми размерами.
Преселективная гидравлическая дистанционная система установленная на станке заметно облегчает выполнение сразу нескольких операций за счет неё можно менять режимы предварительно набрав их. Так же станок оснащен специальными механизмами автоматического выключения в случае завершения процесса сверления с достижением нужной глубины. Шпиндель станка сверлильного 2М55 уравновешивается за счет дополнительных противовесов их регулировка может осуществляется с рабочего места оператора.
Станок 2м55 относится к классу радиально сверлильных станков которые благодаря своей универсальности очень распространены на производстве. Количество основных операций сверлильного станка 2м55 можно значительно расширить применив соответствующую оснастку – станок сможет выполнять операции свойственные расточным станкам.
Основанием радиально сверлильного станка 2м55 служит фундаментная плита с неподвижно закрепленным на ней цоколем. В цоколе смонтирована вращающаяся колонна вращение которой обеспечивается с помощью подшипников. Сверлильная головка станка 2м55 смонтирована на рукаве расположенном на колонне. Благодаря наличию механизма подъема обеспечивается перемещение рукава по колонне.
На радиально-сверлильном 2м55 механизм подъема рукава размещен в корпусе на верхнем торце колонны. Гидромеханическое устройство для зажима колонны и устройство обеспечивающее электропитание для поворотных и подвижных частей станка 2м55 расположены в этом же корпусе.
Сверлильная головка станка 2м55 представляет собой отдельный силовой агрегат состоящий из коробки скоростей механизма подачи шпинделя с противовесом и др. узлов. Перемещение по направляющим сверлильной головки производится вручную фиксирование производится с помощью механизма зажима. Для подачи охлаждающей жидкости к инструменту на сверлильном станке 2м55 предусмотрена насосная установка расположенная в фундаментной плите.
Для обработки деталей небольших деталей на фундаментную плиту станка 2м55 устанавливается стол.
Практически всё управление радиально сверлильным 2м55 (кроме кнопок вводного выключателя и выключателей управления насосом охлаждения) расположено на сверлильной головке.
Конструкцией станка 2м55 предусмотрена возможность регулировки механизмов с изнашивающимися при эксплуатации деталями. Есть возможность произвести регулировку отжима и зажима колонны регулировку зажима рукава регулирование плавного перемещения рукава по колонне регулировку зажима сверлильной головки на направляющих рукава. Есть возможность уменьшения зазора между призматическими направляющими корпуса головки и рукава устранения люфта шпинделя.
3кинематика.docx
1 Описание кинематической схемы станка.
1.1 Главное движение. Шпиндель получает вращение от электродвигателя M1 (N = 55 кВт n = 1500 обмин) через передачу z = 33—39 фрикционную муфту М1 и коробку скоростей с тремя двойными блоками Б1 Б3 Б4 и одним тройным Б2 что обеспечивает 24 теоретических и 21 практических значений частот вращения шпинделя. Блок Б4 может занять положение при котором оба колеса выведены из зацепления; тогда шпиндель легко проворачивается от руки. При переключении муфты М1 происходит реверс шпинделя.
Уравнение кинематической цепи для максимальной частоты вращения шпинделя:
1.2 Движение подачи. От шпинделя через передачу z = 33—54 получает вращение вал VI коробки подач обеспечивающей 12 значений подач при переключении блоков Б5 Б6 и муфты М3 в переборном блоке Б7. При включении специальной регулируемой муфты М4 на валу IX получает вращение червячная передача z = 2—58 и реечное колесо z = 13 перемещающее рейку модулем m= 3 мм нарезанную на гильзе шпинделя XIII.
Уравнение кинематической цепи для минимальной подачи шпинделя:
Для получения максимальной подачи включают муфту М3 тогда:
Специальная регулируемая муфта М4 срабатывает при перегрузке цепи подач или работе на жестком упоре размыкает цепь тонкой ручной подачи при включении механической подачи и включает тонкую ручную подачу при срабатывании перегрузочного устройства. Тонкая ручная подача осуществляется вращением маховика. В положении штурвала «от себя» муфта М5 включается и шпинделю сообщается механическая или тонкая ручная подача. В положении штурвала «на себя» шпинделю можно сообщить грубую ручную подачу. Тонкую настройку на глубину врезания осуществляют по лимбу через червячную передачу z =1 —66.
1.3 Вспомогательные движения.
Перемещение сверлильной головки осуществляют маховиком через колесо z = 16 через накидное колесо z = 24 соединенное с рейкой m = 2 мм неподвижно укрепленной на рукаве. Зажим головки происходит гидравлически.
Вертикальное перемещение рукава происходит от реверсивного электродвигателя М2 (N = 22 кВт n = 1500 обмин) через передачи z = 22—45 16—48 на ходовой винт с шагом Р = 6 мм. Муфта М6 предохраняет привод механизма подъема от перегрузки.
Зажим колонны происходит гидравлически. Рабочий плунжер гидроцилиндра имеет нарезанную зубчатую рейку с z = 17 которая при перемещении плунжера вращает гайку-шестерню z = 50 на валу XIX. При повороте ее по часовой стрелке происходит зажим колонны против часовой стрелки — освобождение колонны.
1.4 Кинематический расчёт.
Количество валов коробки скоростей – 6;
Количество групповых передач – 5;
Количество ступеней вращения шпинделя – 21(24).
По паспорту станка nmin и nmax:
Определение геометрического ряда частот вращения определяется по числу ступеней скорости.
Оно может быть определено из соотношения:
z- число ступеней скоростей вращения шпинделя; z=16.
Из стандартного ряда знаменателей геометрического ряда частот принимаем φ=1.26.
Промежуточные значения частот вращения определяются по следующим формулам: nm
φ- знаменатель геометрического ряда частот.
n2=20126=25225 обмин;
n4=315126=396940 обмин;
n5=40126=50450 обмин;
n7=63126=793880 обмин;
n8=80126=1008100 обмин;
n9=100126=126125 обмин;
n10=125126=1575160 обмин;
n11=160126=2016200 обмин;
n12=200126=252250 обмин;
n13=250126=315 обмин;
n14=315126=3969400 обмин;
n15=400126=504500 обмин;
n16=500126=630 обмин;
n17=630126=7938800 обмин;
n18=800126=10081000 обмин;
n19=1000126=12601250 обмин;
n20=1250126=15751600 обмин;
n21= nmax= 1600126=20162000 обмин.
Структурная сетка.cdw

общий вид станка.cdw

сверления (в стали марки 45 по ГОСТ 1050-60)
Вылет шпинделя от образующей колонны
Расстояние от торца шпинделя до плиты
Количество ступеней скоростей шпинделя 21
Пределы скоростей шпинделя
Пределы подач шпинделя
Наибольшая эффективная мощность на шпинделе
Кинематическая схема .cdw

Sverlo_28.cdw

Сверло должно отвечать требованиям ГОСТ 5756-81
. Маркировать: диаметр сверла. материал режущей части. номер.
Материал режущей части - Р6М5 ГОСТ 19265-73
сталь 45 ГОСТ 1050-74.
Твердость режущей части - 62 65 HRCэ
хвостовика - 30 45 HRCэ.
Рекомендуемые чертежи
- 25.01.2023
- 24.01.2023
- 29.05.2015