Изготовление секции стрелы автомобильного крана




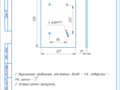
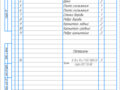
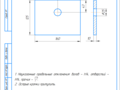
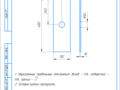
- Добавлен: 25.01.2023
- Размер: 4 MB
- Закачек: 1
Описание
Изготовление секции стрелы автомобильного крана
Состав проекта
![]() |
![]() |
![]() |
![]() ![]() ![]() |
![]() ![]() ![]() ![]() |
![]() ![]() ![]() ![]() |
![]() ![]() ![]() ![]() |
![]() ![]() ![]() ![]() |
![]() ![]() ![]() ![]() |
![]() ![]() ![]() ![]() |
![]() ![]() ![]() ![]() |
![]() ![]() ![]() ![]() |
![]() ![]() ![]() ![]() |
![]() ![]() ![]() ![]() |
![]() ![]() ![]() ![]() |
![]() ![]() ![]() ![]() |
![]() ![]() ![]() ![]() |
![]() ![]() ![]() ![]() |
![]() ![]() ![]() ![]() |
![]() ![]() |
![]() ![]() ![]() |
![]() ![]() ![]() |
![]() ![]() ![]() |
![]() ![]() ![]() |
![]() ![]() ![]() |
Дополнительная информация
УСП.frw

Стенка боковая.cdw

Плита скольжения передняя.cdw

Кронштейн средний.cdw

Швы.frw

Щека.cdw

Стрела СБ.cdw

Плита скольжения задняя.cdw

Пояс верхний.cdw

Спецификация.spw

УСП2.frw

Пояс нижний.cdw

Ребро бороды.cdw

Кронштейн задний.cdw

Стенка бороды.cdw

Ребро кронштейна.cdw

Рекомендуемые чертежи
- 25.01.2023