Изготовление детали Корпус




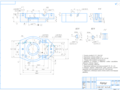
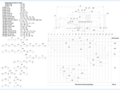
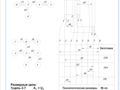
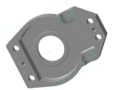
- Добавлен: 24.01.2023
- Размер: 3 MB
- Закачек: 1
Описание
Состав проекта
![]() |
![]() |
![]() ![]() ![]() ![]() |
![]() ![]() |
![]() ![]() ![]() ![]() |
![]() ![]() ![]() |
![]() ![]() ![]() ![]() |
![]() ![]() |
Дополнительная информация
Корпус испр..cdw

Неуказанные литейные радиусы R3.
Неуказанные литейные уклоны по ГОСТ 3212-85.
*Размеры обеспечиваются инструментом.
Обработку по размерам в квадратных скобках производить
совместно с деталью "Крышка".
Детали применять совместно.
Неуказанные предельные отклонения размеров: Js14.
Покрытие наружных поверхностей кроме плоскости разъема:
порошковая эпоксиполиэфирная краска RAL 3000 (красная).
должны пройти пескоструйную
Крышка.m3d

Разм. схема 2.cdw

) цепь 9-5-14-21-15-6-10
+ C 16 - C19 - C20 + C12
) цепь 18-14-21-15-19
) цепь 17-13-21-14-18
) цепь 16-12-1-13-17
Технологические размеры
МОЯ ВЕРСИЯ.doc
Причем Заказчик повысил в последнее время требования как к качеству и количеству так и к срокам изготовления. Пример этому существующая тендерная система как на закупку сырья так и на изготовление продукции (в данном случае металлопродукции).
В результате чего предприятию приходиться разрабатывать и усовершенствовать технологические процессы по обработке принятой к производству детали (изделия) уже в процессе изготовления этой детали (изделия) а так же организовывать новые участки.
В работе рассматриваются: принципы механической обработки включающие: 1) гибкость 2) устойчивость 3) эффективность.
Принцип гибкости - означает его приспособляемость к возможным перестройкам благодаря реорганизации построения оборудования и стандартизации их элементов (на примере одного участка).
Принцип устойчивости - заключается в том что планируемый участок производства должен выполнять основные функции независимо от воздействия на него внутренних и возможных внешних факторов. Это значит что неполадки в отдельных его частях должны быть легко устранимы а работоспособность участка – быстро восстановима.
Эффективность - следует рассматривать как интегральный показатель уровня реализации приведенных выше принципов отнесенного к затратам по организации участка механообработки и его эксплуатации в целом.
В данной работе производится: анализ технологичности детали анализ схем установки и конструкции используемых приспособлений составляется технологический маршрут и назначаются режимы резания а так же проводится нормирование разработанного техпроцесса.
Значительным этапом технического и технологического процесса на заводе является широкое использование в производстве станков с числовым программным управлением:
)многоцелевые обрабатывающие центры;
)токарно-револьверные и токарные станки;
То есть решается проблема высвобождения высококвалифицированных рабочих специального оборудования режущего инструмента. Отпадает необходимость в проектировании и изготовлении специальной оснастки (существуют стандартные детали для оснастки этих станков). Станки с ЧПУ обеспечивают высокую технологическую точность стабильность при изготовлении деталей и узлов.
Большое значение имеет своевременность и высокое качество технико-экономического анализа уже при изготовлении соответствующей продукции с целью выявления и смены экономически неэффективных технологических процессов. Для сравнительного технико-экономического анализа в качестве базовых изделий должны выбираться современные отечественные или зарубежные модели освоенные в производстве имеющие аналогичное эксплуатационное назначение и по возможности близкое к проектируемому.
ТЕХНОЛОГИЧЕСКАЯ ЧАСТЬ
1. Анализ чертежа детали и классификация обрабатываемых поверхностей
Деталь «Корпус» и изготавливается из серого чугуна марки СЧ 15 (химический состав и механические свойства см. табл. 1.1 и 1.2) литьем поэтому конфигурация наружного контура и внутренних поверхностей не вызывает значительных трудностей при получении заготовки. Тем не менее даже при этом формовка должна производиться с применением стержней формирующих внутренние полости.
Химический состав СЧ 18 по ГОСТ 1412-65 %
Механические свойства СЧ 18
С точки зрения механической обработки деталь имеет недостаток: необходима обработка выточек 25 мм (см. рис. 1.1 гл. вид и вид сверху) с внутренней стороны. Обработка этих поверхностей может производиться двумя способами:
– обратными съемными цековками;
– обратными автоматическими цековками.
В первом случае обработку этих поверхностей необходимо выделить в отдельную операцию и выполнять ее на универсальном оборудовании а во втором – потребует применение дорогостоящего режущего инструмента и дополнительных затрат вспомогательного времени на холостые перемещения. Поэтому предлагается заменить эти выточки уступами которые можно обработать концевой фрезой при этом функция которую выполняют эти выточки не нарушится.
В детали «Корпус» имеется ряд резьбовых и крепежных отверстий которые расположены во взаимноперпендикулярных плоскостях что несколько ухудшает технологичность детали с точки зрения обработки ее на многоинструментальных станках с ЧПУ. Но такое расположение отверстий объясняется конструктивными особенностями деталей вызванных условиями работы деталей в узле.
Рис. 1.1. Исходный чертеж детали «Корпус»
В остальном деталь достаточно технологична имеет хорошие базовые поверхности для первоначальных операций и довольно проста по конфигурации. Ко всем обрабатываемым поверхностям имеется свободный доступ режущего инструмента все плоские поверхности могут быть обработаны на проход. Все обрабатываемые поверхности с точки зрения обеспечения точности и шероховатости не представляют технологических трудностей и дают возможность обрабатывать несколько деталей одновременно высокопроизводительными методами.
Для подробного восприятия и детального понимания всех обрабатываемых поверхностей проведем их кодировку согласно кодификатору [1] (см. табл. 1.3) и построим трехмерные модели в 3D-редакторе (см. рис.1.2).
Идентификация обрабатываемых поверхностей
Дополнительные требования
Продолжение табл. 1.3
Рис. 1.2. 3D-модель детали «Корпус»
2. Проверка правильности простановки размеров на чертеже
Проверка правильности простановки размеров производится с помощью графов размерных связей (см. рис. 1.3). Граф на плоскости изображается множеством соответствующих поверхностям вершин соединенных дугами (или ребрами) каждая из которых соответствует размеру с допуском связывающему две поверхности. На графах исходные поверхности формообразование которых завершилось в процессе изготовления заготовки отмечены сдвоенной окружностью. Номер внутри окружности соответствует номеру поверхности. Симметрично расположенные поверхности в частности поверхности вращения на графе отражены двумя вершинами одна из которых – ось симметрии. Для деталей с общей плоскостью симметрии и рядом поверхностей вращения (в том числе и соосных) оси которых лежат в этой плоскости при построении графа размерных связей по оси перпендикулярной плоскости симметрии в необходимом координатном направлении вначале отыскивается базовый элемент и связывается с ним плоскость симметрии комплекса необрабатываемых поверхностей затем эта процедура повторяется для комплекса обрабатываемых поверхностей.
За базовый элемент к которому относится неуказанный допуск симметричности нужно принимать плоскость (ось) симметрии элемента имеющего большую длину в плоскости параллельной плоскости симметрии при одинаковых длинах – плоскость (ось) элемента с допуском размера по более точному квалитету в направлении перпендикулярном плоскости симметрии а при одинаковых длинах и квалитетах – элемента с большим размером в направлении перпендикулярном плоскости симметрии. Если и размеры одинаковы то по технологическим соображениям предпочтение следует отдавать поверхности вращения.
В том случае если имеются соосные поверхности а допуск соосности для них не задан то за базовый элемент принимается ось поверхности имеющей наибольшую длину при одинаковых длинах – ось поверхности с допуском диаметра по более точному квалитету а при одинаковых длинах и квалитетах – ось поверхности с большим диаметром.
После того как найдены базовые элементы симметричности комплексов необрабатываемых и обрабатываемых поверхностей необходимо связать эти поверхности ребром графа и отыскать численное значение допуска симметричности (соосности) согласно ГОСТ25069-81 по таблицам в зависимости от номинального размера и определяющего допуска размера [1]. Под номинальным размером понимается больший из размеров рассматриваемого или базового симметричного элемента (больший из диаметров рассматриваемого или базового элементов). Под номинальным допуском размера понимается допуск размера рассматриваемого или базового симметричного элемента по более грубому квалитету (допуск диаметра рассматриваемого или базового элемента по более грубому квалитету). В том случае если базовыми поверхностями комплекса обработанных и необработанных поверхностей являются оси поверхностей вращения то численное значение допуска предлагается принимать по более жесткому значению либо допуска соосности либо симметричности.
Если размеры на чертеже проставлены правильно то граф размерных связей отвечает следующим требованиям:
) на графе нет оторванных групп вершин (если они есть то это значит что не хватает размеров или технических требований);
) на графе нет замкнутых контуров (если они есть то это значит что проставлены лишние размеры);
) группы исходных и обработанных поверхностей имеют только одну общую дугу.
Рис. 1.3. Эскиз детали «Корпус» с нумерацией поверхностей
Рис. 1.4. Графы размерных связей детали «Корпус»: а) по оси «Z»; б) по оси «X»; в) по оси «Y».
Как видно из построенных графов на рисунке 1.4 на чертеже детали недостает размеров – на графах есть оторванные вершины есть лишние размеры – на графах есть замкнутые контуры и между комплексом обработанных и необработанных поверхностей существует больше одной связи.
Исправленные графы по всем осям представлены на рисунках 1.5 а эскизы деталей после исправления на рисунках 1.6.
Рис. 1.5 Исправленные графы размерных связей детали «Корпус»: а) по оси «Z»; б) по оси «X»; в) по оси «Y».
Рис. 1.6 – Исправленный чертеж детали «Корпус»
3. Методы контроля готовой детали
Основным методом контроля линейных и угловых размеров является метод непосредственной оценки. Значение измеряемой величины получают непосредственно по отсчетному устройству измерительного прибора прямого действия.
Правильный выбор средств измерений имеет важное значение для обеспечения требуемой точности измерений. Средства измерений должны обеспечивать погрешность измерений меньше нормируемой.
Средства измерения выбираем с помощью таблицы 11 [2 c.22] в зависимости от квалитета контролируемого размера.
Для контроля линейных наружных размеров в диапазоне от 18 до 250 мм принимаем штангенциркуль с ценой деления 005 мм по ГОСТ 166 – 80.
Для контроля внутренних линейных размеров в диапазоне от 6 до 50 мм принимаем штангенциркуль с ценой деления 005 мм по ГОСТ 166 – 80 в диапазоне от 25 до 50 мм принимаем индикаторный нутромер с ценой деления 0.002 мм по ГОСТ 9244 – 75.
Параметры шероховатости поверхности оценивают на рабочем месте сравнением с образцами шероховатости – брусками с плоской или цилиндрической поверхностью длиной 30-40 мм и шириной 20 мм с известными значениями параметра шероховатости. Образцы шероховатости комплектуют в наборы.
4. Выбор и описание способа получения заготовки
4.1. Выбор способа методом весовых коэффициентов
)тип производства – серийное
)масса – детали до 50 кг
)группа сложности – 3-я
)параметр шероховатости исходных поверхностей – Ra=25 мкм
)форма детали – корпусная
)максимальный габаритный размер – 230 мм
Значение весовых коэффициентов принимаем по [2].
Значения весовых коэффициентов для данной детали
Номер критерия выбора
Наибольшую сумму коэффициентов набрал метод ЛПФ МФ – литье в песчано-глинистые формы с машинной формовкой.
4.2. Описание принятого метода получения заготовки
Литье в песчано-глинистые формы является наиболее универсальным методом однако изготовление форм требует больших затрат времени. Так набивка 1 м3 формовочной смеси вручную занимает 1.5 – 2 часа а с помощью пневматической трамбовки – 1 час. Применение пескомета снижает время набивки до 6 минут. Встряхивающие машины ускоряют набивку по сравнению с ручной в 15 а прессование – в 20 раз.
При литье в сырые песчаные формы можно получать отливки массой 0.1 2 тонны точностью JT15 – JT18 и шероховатостью до Rz = 80 мкм.
Разработка литейной технологии складывается из нескольких этапов. Основные из них следующие:
-конструирование модели с учетом усадки литейного сплава припусков на механическую обработку напусков литейных уклонов галтелей;
-назначение плоскости разъема модели и выбор положения модели в форме;
-конструирование стержня;
-конструирование стержневого ящика;
-конструирование и расчет литниковой системы и выбор места ее подвода к отливке;
-конструирование всех необходимых приспособлений – шаблонов кондукторов и т.д.
Эскиз литейной формы приведен на рисунке 1.7.
Рис. 1.7 Эскиз литейной формы детали «Корпус»: 1 – верхняя опока; 2 – чаша; 3 – стояк; 4 – шлакоуловитель; 5 – питатель; 6 – стержень; 7 – болван; 8 – армирующий элемент 9 – нижняя опока; 10 – центрирующий штырь.
4.3. Разработка чертежа заготовки
Допуски размеров и припуски на механическую обработку назначаем по ГОСТ 26645 – 85 в зависимости от степени точности отливки. Степень точности отливки 11-11-9.
Эскиз заготовки приведен на рисунке 1.8.
Рис. 1.8 Эскиз заготовки детали «Корпус».
5 Синтез технологического маршрута обработки
Технологический маршрут разрабатываем на основе существующего заводского техпроцесса внося изменения с учетом вновь применяемых многоместных приспособлений.
Технологический маршрут:
Операция 005 Перемещение
Рис. 1.9 Операционный эскиз операции 030
Операция 020 Очистка
Операция 030 Фрезерная с ЧПУ (см. рис. 1.9)
О1 Установить выверить закрепить (2 корпуса и 2 крышки)
О2 Фрезеровать нижнюю поверхность крышки и корпуса
О3 Фрезеровать отверстие в корпусе и крышке
О4 Центровать шесть отверстий
О5 Сверлить 2 отверстия
О6 Сверлить 4 отверстия
Рис. 1.10 Операционный эскиз операция 040
Операция 040 Фрезерная с ЧПУ (см. рис. 1.10)
О2 Фрезеровать верхнюю поверхность крышки и корпуса
О3 Фрезеровать бобышку в корпусе и крышке
О4 Фрезеровать два занижения в корпусе и крышке
О5 Фрезеровать торец крышки и корпуса
О7 Зенковать фаски в 4-х отверстиях
Операция 050 Сверлильная (см. рис. 1.11)
О1 Нарезать резьбу в 4-х отверстиях
Рис. 1.11 Операционный эскиз операция 050
Операция 060 Слесарная
Операция 070 Технологический контроль
Операция 080 Комплектация
Операция 090 Сборочная
Операция 100 Обрубка
Операция 110 Комбинированная (см. рис. 1.12)
О1 Установить 4 детали выверить закрепить
О2 Фрезеровать торец детали
О3 Сверлить 4 отверстия
О4 Зенковать 4 фаски
О5 Нарезать резьбу в 4-х отверстиях
Поворот стола на 180°
Повторить переходы О2-О5
Операция 120 Слесарная
Операция 130 Комбинированная (см. рис. 1.13-1.16)
О2 Расточить отверстие
О3 Расточить фаски в отверстии
О4 Фрезеровать 2 канавки
О5 Центровать 4 отверстия
О6 Центровать отверстие
О7 Сверлить отверстие
О8 Расточить отверстие
О9 Фрезеровать выточку
О10 Фрезеровать канавку
Поворот стола на 90°
Повторить переходы О6-О10
О 11 Открепить деталь верхние прихваты в приспособлении и закрепить с меньшим усилием
О12 Развернуть отверстие
3 Зенкеровать отверстие
4 Развернуть отверстие
Повторить переход О12
Повторить переходы О13 О14
Повернуть стол на 90°
Операция 140 Слесарная
Операция 150 Сверлильная (см. рис. 1.17)
О1 Установить 2 детали в тиски
О2 Сверлить 8 отверстий
О3 Нарезать резьбу в 8-ми отверстиях
Операция 160 Слесарная
Операция 170 Технологический контроль
6. Расчет минимальных припусков
Минимальный припуск рассчитываем как сумму расчётных параметров:
Zmin = RZi-1 + Hi-1 + ri-1
ρi-1 – суммарное отклонение расположения поверхности на предшествующем переходе.
Значение параметров RZ Н r выбираем по таблицам 4.3 4.9 [5 с. 63 71].
Результаты расчётов оформляем в виде таблицы.
Расчёт минимальных припусков
№ поверхности (см. рис. 1.5)
Маршрут обработки поверхности
Расчётные параметры мкм
Минимальный припуск Zmin мм
Фрезерование однокр.
Фрезерование черновое
Растачивание чистовое
Растачивание черновое
7. Размерный анализ технологического процесса
7.1. Размерный анализ маршрута обработки корпуса по оси «В»
Для проведения размерного анализа необходимо построить размерную схему технологического процесса (см. рисунок 1.18 1.20) графы исходных и производных размеров (см. рисунок 1.19 1.21) составить уравнения размерных цепей и решить их (неизвестными являются промежуточные технологические размеры). Анализ технологического процесса проводим только по двум осям т. к. по оси S номинальные значения размеров будут постоянные а допуски на них назначаем по таблицам главы 21 [2].
Рис. 1.18 Размерная схема технологического процесса
В соответствии с размерной схемой составляем графы размерных связей.
Рис. 1.19 Граф исходных и производных размеров
Составляем уравнения размерных цепей:
)цепь 7-2-8z3 = - U2 + U1
)цепь 2-8-1z1 = З1 – U1
)цепь 4-7-2-8-5z2 = U3 – U2 + U1 - З4
Решаем уравнения размерных цепей:
) U2 = A1 = 40-062; принимаем U2=40-062
) U3 = A2 = 20+01; принимаем U3=20+01
) U4 = A = 10+036; принимаем U4=10+036
) U5 = A4 = 13±013; принимаем U5=13±013
) z3min = - U2max + U1min
U1min= U2max+ z3min = 40 + 0.758 = 40.758 мм
U1max = U1min + (U1) = 40.758 + 0.62 = 41.378 мм
Принимаем U1 = 41.4-062
z3max = -U2min + U1max = - 39.38 + 41.378 = 1.998 мм
) z1min = З1min - U1max
З1min= U1max+ z1min = 41378 + 0.86= 42.238 мм
З1max = З1min + (З1) = 42238 + 36 = 45.838 мм
Принимаем З1 = 44.76±18
z1max = З1max - U1min = 45.838 - 40.758 = 5.08 мм
) z2min = U3min – U2max + U1min – З4max
З4max= U3min – U2max + U1min – z2min = 20 - 40 + 40758 – 0.86 = 19898 мм
З4min = З4max - (З4) = 19898 – 32 = 16698 мм
Принимаем З4 = 183±16
z2max = U3max – U2min + U1max – З4min = 20.1 - 39.38 + 41.378 – 16698 = 54 мм
Результаты расчётов сводим в таблицу 1.6.
7.2. Размерный анализ маршрута обработки корпуса по оси «B»
Рис. 1.20 Размерная схема технологического процесса
) цепь 15-21A10 = C19
) цепь 6-15-7p3 = C20 – C21
) цепь 14-21-15p5 = C16 – C19
) цепь 13-21-14p4 = C6 – C16
) цепь 5-14-21-15-6p2 = C17 + C16 – C19 – C20
) цепь 10-6-15-7-11z7 = - C12 + C20 – C21 + C18
) цепь 9-5-14-21-15-6-10z6 = - C11 + C17 + C 16 – C19 – C20 + C12
) цепь 4-14-5p1 = C7 – C17
) цепь 8-4-14-5-9z5 = - C8 + C7 - C 17 + C11
) цепь 2-13-21A5 = - B5 + С6
) цепь 15-21-13-20A6 = C19 – C6 + B3
) цепь 1-13-2z4 = B1 – B5
) цепь 12-1-13p3 = - З2 + B1
) цепь 18-14-21-15-19z10 = - C14 + C16 - C 19 + C15
) цепь 17-13-21-14-18z9 = - B2 + C6 - C 16 + C14
) цепь 21-13-1-22z11 = C6 – B1 + З1
) цепь 16-12-1-13-17z8 = - З3 – З2 + B1 + B2
Рис. 1.21 Граф исходных и производных размеров
Решение уравнений размерных цепей:
) B4 = A7 = 133±0.5; принимаем B4 = 133±0.2
) C21 = A11 = 52.5±0.1; принимаем C21 = 52.5±0.1
) C18 = 2A9 = 16+0.043; принимаем 2C18 = 16+0.043
) C15 = 2A8 = 45+0.062; принимаем 2C15 = 45+0.062
) C19 = A10 = 61±0.3; принимаем C19 = 61±0.1
) Принимаем значения смещения осей:
р1 = р4 = ± 0.03; р2 = р5 = ± 0.02; р3 = р6 = ± 0.01
C20max = C21max + p3max = 52.6 + 0.03 = 52.63 мм
C20min = C21min + p3min = 52.4 – 0.03 = 52.37 мм
Принимаем C5 = 52.5 ± 0.13
) C16max = C19max + p6max = 61.1 + 0.01 = 61.11 мм
C16min = C19min + p6min = 60.9 – 0.01 = 60.89 мм
Принимаем C16 = 61 ± 0.11
) C6max = C16max + p5max = 61.11 + 0.02 = 61.13 мм
C6min = C16min + p5min = 60.89 – 0.02 = 60.87 мм
Принимаем C6 = 61 ± 0.13
) C17max = - C16min + C19max + C20max + p2max = -60.89+61.1+52.63+0.02=52.86 мм
C17min = - C16max + C19min + C20min + p2min = -61.11+60.9+52.37-0.02=52.14 мм Принимаем C17 = 52.5 ± 0.36
) z7min = - C12max + C20min – C21max + C18min
C12max = C20min – C21max + C18min - z7min= 52.37 - 52.6 +8 – 0.076 = 7.694 мм
C12min = C12max - (C12) = 7.694 – 0.035 = 7.659 мм
Принимаем 2C12 = 15.3+0.07
z7max = - C12min + C20max – C21min + C18max = - 7.659+52.63–52.4+8.0215 = 0.593 мм
) z6min = - C11max + C17min + C16min – C19max – C20max + C12min
C11max = C17min + C16min – C19max – C20max + C12min - z6min = 52.14 + 60.89 – 61.1 – - 52.63 + 7.656 – 0.103 = 6.853 мм
C11min = C11max - (C11) = 6.853 - 0.055 = 6.798 мм
Принимаем 2C11 = 13.6+0.11
z6max = - C11min + C17max + C16max – C19min – C20min + C12max=-6.798+52.86+61.11- -60.9-52.37+7.694=1.596 мм
) C7max = C17max + p1max = 52.86 + 0.03 = 52.89 мм
C7min = C17min + p1min = 52.14 – 0.03 = 52.11 мм
Принимаем C7 = 52.5 ± 0.39
) z5min = - C8max + C7min – C17max + C11min
C8max = C7min – C17max + C11min – z5min= 52.11 - 52.86 +6.798 – 0.224 = 5.824 мм
C8min = C8max - (C8) = 5.824 – 0.09 = 5.734 мм
Принимаем 2C8 = 11.5+0.18
z5max = - C8min + C7max – C17min + C11max = - 5.734+52.89–52.86+6.853 = 1.15 мм
) A5max = B5max + C6max
(B5) = (A5) – (C6) = 1.0 – 0.26 = 0.74
B5max = A5max – C6max = 158.5 – 61.13 = 97.37 мм
B5min = B5max - (B5) = 97.37 – 0.74 = 96.63 мм
Принимаем B5 = 97.37-0.74
) A6max = C19max + B3max - C6min
(B3) = (A6) – (C6) - (C19) = 0.62 – 0.26 – 0.2 = 0.16 мм
B3max = A6max – C19max + C6min = 48.31 – 61.1 + 60.87= 48.08 мм
B3min = B3max - (B3) = 48.08 – 0.16 = 47.92 мм
Принимаем B3 = 48±0.08 мм
) z4min = B1min – B5max
B1min = B5max + z4min= 97.37 + 0.78 = 98.15 мм
B1max = B1min + (B1) = 98.15 + 0.87 = 99.02 мм
Принимаем B1 = 98.58±0.44
z4max = B1max – B5min = 99.02–96.63 = 2.39 мм
) З2max = В1max - p4min = 99.02 + 0.03 = 99.05 мм
З2min = B1min - p4max = 98.15 - 0.03 = 98.12 мм
Принимаем З2 = 986 ± 0.47
) z10min = - C14max + C16min – C19max + C15min
C14max = C16min – C19max + C15min – z10min= 60.89 – 61.1 +22.5 – 0.046 = 22.244 мм
C14min = C14max - (C14) = 22.244 – 0.05 = 22.194 мм
Принимаем 2C14 = 44.4+0.1
z10max= - C14min + C16max – C19min + C15max=-22.194+61.11–60.9+22.531= 0.547 мм
) z9min = - B2max + C6min – C16max + C14min
B2max = C6min – C16max + C14min – z9min= 60.87 – 61.11 +22.194 – 0.102 = 21.852 мм
B2min = B2max - (B2) = 21.852 – 0.125 = 21.727 мм
Принимаем 2B2 = 43.5+0.25
z9max= - B2min + C6max – C16min + C14max=-21.727+61.13–60.89+22.244= 0.757 мм
) z11min = - С6max – B1max + З1min
З1min = C6max + B1max + z11min= 61.13 + 99.02 + 0.736 = 160.886 мм
З1max = З1min + (З1) = 160.886 + 5.0 = 165.886 мм
Принимаем З1 = 163.4±2.5
z11max= - C6min – B1min + З1max =-60.87-98.15+165.886= 6.866 мм
) ) z8min = - З3max – З2max + B1min + B2min
З3max = - З2max + B1min + B2min – z8min= -99.05 + 98.15 +21.727 – 0.72 = 20.107 мм
З3min = З3max - (З3) = 20.107 – 4 = 16.107 мм
Принимаем 2З3 = 36.2±2
z8min= - З3min – З2min + B1max + B2max =-16.107-98.12+99.02+21.852= 6.645 мм
Результаты расчётов сводим в таблицу 1.7.
Разм. схема 1.cdw

Корпус.m3d
